Mastering the Components of a CNC Machine for Optimal
Introduction: Navigating the Global Market for components of a cnc machine
In the rapidly evolving landscape of global manufacturing, the components of CNC (Computer Numerical Control) machines stand at the forefront of innovation and efficiency. These intricate machines are the backbone of modern production, enabling manufacturers to achieve unparalleled precision and consistency. For international B2B buyers, especially those from regions like Africa, South America, the Middle East, and Europe, understanding the core components of CNC machines is not just beneficial—it’s essential for making informed sourcing decisions.
This guide delves deep into the various components that constitute CNC machines, including the Computer Control Unit, drive systems, input/output devices, and the machine tool itself. Each section will cover critical aspects such as types of components, materials used, manufacturing and quality control processes, leading suppliers, cost considerations, and market trends. Additionally, we will address frequently asked questions to equip buyers with the knowledge needed to navigate this complex landscape.
By empowering B2B buyers with comprehensive insights, this guide aims to streamline the procurement process and enhance strategic decision-making. Whether you are a manufacturer in Kenya looking to upgrade your machinery or a buyer in Brazil seeking reliable suppliers, understanding the intricacies of CNC machine components will provide a competitive edge in the global market.
Understanding components of a cnc machine Types and Variations
Type Name | Key Distinguishing Features | Primary B2B Applications | Brief Pros & Cons for Buyers |
---|---|---|---|
Machine Control Unit (MCU) | Processes G-code, converts to electrical signals; coordinates machine movements. | Aerospace, automotive, and electronics industries. | Pros: High precision; Cons: Complexity may require skilled operators. |
Drive System | Comprises motors (stepper or servo) and mechanisms for motion; ensures accurate tool movement. | Manufacturing of intricate parts and assemblies. | Pros: High reliability; Cons: Initial investment can be high. |
Feedback System | Utilizes sensors to monitor position and movement; ensures real-time adjustments. | Quality control in precision machining. | Pros: Enhances accuracy; Cons: Maintenance can be costly. |
Input/Output Devices | Includes keyboards, displays, and communication interfaces for program input/output. | Any CNC machining operation requiring programming. | Pros: User-friendly; Cons: May require updates for compatibility. |
Cooling System | Manages heat and lubrication during machining; critical for maintaining performance. | Metalworking, woodworking, and plastic machining. | Pros: Extends tool life; Cons: Additional maintenance required. |
Machine Control Unit (MCU)
The Machine Control Unit serves as the brain of the CNC machine, interpreting G-code and converting it into electrical signals that direct the machine’s movements. This component is essential for ensuring precision in applications across industries such as aerospace and automotive. Buyers should consider the MCU’s compatibility with their existing systems and the level of technical expertise required for operation, as a more complex MCU may necessitate additional training for staff.
Drive System
The Drive System is responsible for the movement of machine components, incorporating motors and mechanisms like lead screws or ball screws. Its primary role is to ensure accurate positioning of tools during machining processes. This component is critical for industries that require high precision, such as manufacturing intricate parts. Buyers should evaluate the drive system’s reliability, as well as the cost of potential replacements or upgrades, to ensure long-term operational efficiency.
Feedback System
This system monitors the CNC machine’s position and movement through sensors, providing real-time data for adjustments. A robust feedback system is crucial for maintaining accuracy in precision machining applications. For B2B buyers, understanding the feedback system’s technology is important, as it can impact both the quality of output and the overall maintenance costs. Investing in advanced feedback systems may lead to better performance but could also involve higher initial costs.
Input/Output Devices
Input/Output devices facilitate communication between operators and the CNC machine, allowing for the entry of programming instructions and receiving operational feedback. These devices can include keyboards, displays, and network connections. For buyers, the usability and compatibility of these devices with existing systems are key considerations. While user-friendly interfaces can enhance productivity, it’s important to account for potential updates or replacements as technology evolves.
Cooling System
The Cooling System plays a vital role in maintaining the CNC machine’s performance by managing heat and lubrication during machining processes. This component is particularly important in metalworking, woodworking, and plastic machining applications, where excessive heat can lead to tool wear and reduced accuracy. Buyers should consider the maintenance requirements and costs associated with the cooling system, as well as its impact on the overall efficiency and longevity of the CNC machine.
Related Video: How milling on a 4-axis CNC machine works
Key Industrial Applications of components of a cnc machine
Industry/Sector | Specific Application of components of a cnc machine | Value/Benefit for the Business | Key Sourcing Considerations for this Application |
---|---|---|---|
Aerospace | Precision machining of aircraft components | Enhanced safety and reliability of aircraft | Certification standards, material specifications, and lead times |
Automotive | Production of engine components and parts | Improved efficiency and reduced production costs | Quality control measures, scalability, and technology compatibility |
Electronics | Fabrication of circuit boards and enclosures | High precision and reduced waste | Supplier reliability, technological support, and customization options |
Metal Fabrication | Custom parts manufacturing for various applications | Flexibility in production and quick turnaround | Material availability, machine compatibility, and lead times |
Medical Devices | Creation of surgical instruments and implants | High precision and compliance with health standards | Certification for medical use, material properties, and traceability |
Aerospace
In the aerospace industry, components of CNC machines are crucial for the precision machining of aircraft parts, such as turbine blades and landing gear. These components ensure that parts meet strict safety and performance standards, significantly enhancing the reliability of the aircraft. International buyers, particularly from regions like Africa and South America, should prioritize suppliers who adhere to rigorous certification standards and can provide detailed material specifications, as well as reasonable lead times to avoid delays in production.
Automotive
CNC machines play a vital role in the automotive sector, particularly in the production of engine components and intricate parts like gearboxes. The precision offered by CNC technology leads to improved efficiency and reduced production costs, making it an attractive option for manufacturers. Buyers in Europe and the Middle East should consider quality control measures and the scalability of the supplier’s operations to ensure they can meet fluctuating demands without compromising on quality or timelines.
Electronics
The electronics industry relies heavily on CNC machines for fabricating circuit boards and enclosures. The precision achieved through CNC machining reduces waste and enhances product quality, which is critical in a sector where small tolerances can lead to significant issues. B2B buyers should focus on supplier reliability and the availability of technological support to ensure seamless integration into their existing production processes, as well as options for customization to meet specific project needs.
Metal Fabrication
CNC machines are essential in metal fabrication for producing custom parts across various applications, from construction to machinery. The flexibility offered by CNC technology allows for quick turnarounds and the ability to adapt to different project requirements. For international buyers, key considerations include the availability of raw materials, compatibility with existing machinery, and the supplier’s ability to meet lead times to avoid project delays.
Medical Devices
In the medical device industry, the creation of surgical instruments and implants demands the highest levels of precision and compliance with health regulations. CNC machines are instrumental in achieving these standards, ensuring that products are safe and effective for patient use. Buyers should prioritize suppliers who possess the necessary certifications for medical-grade materials and can provide traceability for all components, ensuring adherence to stringent health regulations in their respective markets.
Related Video: CNC Machine Working Process 5 Axis Machining Metal & Aluminium Aerospace
Strategic Material Selection Guide for components of a cnc machine
When selecting materials for CNC machine components, international B2B buyers must consider various factors including performance characteristics, cost implications, and regional compliance standards. Below is an analysis of four common materials used in CNC machine components, focusing on their properties, advantages, disadvantages, and specific considerations for international buyers.
Aluminum Alloys
Aluminum alloys are widely used in CNC machining due to their excellent strength-to-weight ratio and good machinability. They typically have a temperature rating of up to 200°C and are resistant to corrosion, making them suitable for various environments.
Pros:
– Lightweight and easy to machine, which reduces manufacturing complexity.
– Good corrosion resistance, extending the lifespan of components.
– Cost-effective for mass production.
Cons:
– Lower strength compared to steel, which may limit its use in high-stress applications.
– Can be more expensive than some lower-grade materials, depending on the alloy.
Impact on Application:
Aluminum is commonly used in components like machine frames and housings. Its lightweight nature makes it ideal for applications where weight savings are crucial, such as in aerospace or mobile machinery.
Considerations for International Buyers:
Buyers in regions like Africa and South America should be aware of the specific aluminum alloy standards (e.g., ASTM B221) and ensure compliance with local regulations regarding material sourcing and environmental impact.
Steel Alloys
Steel alloys are the backbone of CNC machinery due to their exceptional strength and durability. They can withstand high temperatures and pressures, making them suitable for heavy-duty applications.
Pros:
– High tensile strength and toughness, ideal for demanding applications.
– Versatile with various grades available for different uses.
– Generally lower cost compared to high-performance alloys.
Cons:
– Heavier than aluminum, which can be a disadvantage in certain applications.
– Susceptible to corrosion unless treated or alloyed with corrosion-resistant elements.
Impact on Application:
Steel is often used for components such as shafts, gears, and structural frames. Its ability to handle high loads makes it a preferred choice in automotive and industrial applications.
Considerations for International Buyers:
Buyers should ensure compliance with international standards such as DIN or JIS for steel quality and specifications. Additionally, understanding local market conditions can help in sourcing quality steel at competitive prices.
Plastics (e.g., Nylon, PTFE)
Plastics, particularly engineering-grade plastics like Nylon and PTFE, are increasingly used in CNC applications due to their lightweight properties and resistance to wear and chemicals.
Pros:
– Excellent resistance to corrosion and chemicals, making them suitable for harsh environments.
– Lightweight, which can reduce overall machine weight.
– Good machinability and lower manufacturing costs in some cases.
Cons:
– Lower mechanical strength compared to metals, limiting their use in load-bearing applications.
– Temperature sensitivity, as some plastics may deform under high heat.
Impact on Application:
Plastics are often used for components such as bearings, bushings, and non-structural parts where weight and corrosion resistance are prioritized.
Considerations for International Buyers:
Buyers should be aware of the specific grades and standards for engineering plastics, such as ASTM D638 for tensile properties. Compliance with local environmental regulations regarding plastic use and disposal is also essential.
Titanium Alloys
Titanium alloys are renowned for their high strength-to-weight ratio and excellent corrosion resistance, making them ideal for specialized applications in aerospace and medical devices.
Pros:
– Exceptional strength and durability, suitable for high-performance applications.
– Excellent corrosion resistance, even in extreme environments.
– Biocompatible, making it suitable for medical applications.
Cons:
– High cost and complex manufacturing processes can limit its use.
– More challenging to machine compared to aluminum and steel.
Impact on Application:
Titanium is often used in high-stress components such as aerospace fittings and medical implants, where performance and reliability are critical.
Considerations for International Buyers:
Buyers must consider compliance with international standards such as ASTM F136 for titanium used in medical applications. Additionally, understanding the supply chain for titanium, which can be limited in certain regions, is crucial.
Summary Table
Material | Typical Use Case for components of a cnc machine | Key Advantage | Key Disadvantage/Limitation | Relative Cost (Low/Med/High) |
---|---|---|---|---|
Aluminum Alloys | Machine frames, housings | Lightweight and corrosion-resistant | Lower strength than steel | Medium |
Steel Alloys | Shafts, gears, structural frames | High strength and toughness | Susceptible to corrosion | Low |
Plastics | Bearings, bushings | Excellent corrosion resistance | Lower mechanical strength | Low |
Titanium Alloys | Aerospace fittings, medical implants | Exceptional strength and corrosion resistance | High cost and complex machining | High |
This strategic material selection guide provides valuable insights for international B2B buyers, enabling informed decisions that align with their specific application needs and regional considerations.
In-depth Look: Manufacturing Processes and Quality Assurance for components of a cnc machine
Understanding Manufacturing Processes for CNC Machine Components
The manufacturing of CNC machine components involves a series of meticulous processes designed to ensure precision and quality. Each stage of production—from material preparation to finishing—plays a crucial role in determining the overall performance of the CNC machines.
Main Stages of Manufacturing
-
Material Preparation
– Selection of Materials: Common materials used in CNC components include metals (like aluminum, steel, and titanium), plastics, and composites. B2B buyers should focus on suppliers that provide high-grade materials that meet industry standards.
– Cutting and Shaping: Raw materials are cut into manageable sizes through processes such as sawing, shearing, or laser cutting. This step often requires CNC machines themselves to ensure accuracy. -
Forming
– Machining Processes: This stage includes various techniques such as milling, turning, and drilling. CNC machines are programmed to perform these tasks with high precision, allowing for complex geometries and tight tolerances.
– Casting and Forging: For specific components, especially those requiring high strength, casting or forging may be employed. Buyers should inquire about the methods used to ensure they align with their quality requirements. -
Assembly
– Sub-assembly and Final Assembly: Components are assembled in stages. Initially, sub-assemblies are created, which are then combined into the final product. This step may involve mechanical fastening, welding, or adhesive bonding, depending on the component.
– Integration of Systems: The integration of control systems, motors, and feedback devices is crucial for the operational efficiency of CNC machines. Buyers should ensure that the supplier has robust assembly procedures to minimize errors. -
Finishing
– Surface Treatment: Processes like anodizing, painting, or polishing enhance the durability and appearance of components. This step is vital for preventing corrosion and wear.
– Inspection and Testing: Before the final product is dispatched, it undergoes rigorous inspection and testing to ensure it meets specified tolerances and standards.
Quality Assurance in Manufacturing
Quality assurance is integral to the manufacturing process, ensuring that each component meets international and industry-specific standards.
Relevant International Standards
- ISO 9001: This standard outlines requirements for a quality management system (QMS) and is essential for suppliers aiming to provide consistent quality. Buyers should prioritize suppliers with ISO 9001 certification.
- CE Marking: For products sold in the European market, CE marking indicates compliance with safety, health, and environmental protection standards.
- API Standards: For components used in oil and gas industries, API (American Petroleum Institute) standards ensure quality and safety.
Quality Control Checkpoints
-
Incoming Quality Control (IQC): This stage involves the inspection of raw materials upon arrival. Suppliers should have protocols in place to verify the quality of incoming materials against specifications.
-
In-Process Quality Control (IPQC): Continuous monitoring during the manufacturing process helps catch defects early. Techniques such as statistical process control (SPC) can be beneficial in this stage.
-
Final Quality Control (FQC): Before shipping, components undergo final inspections and testing to ensure they meet all quality standards. This includes functional testing and dimensional checks.
Common Testing Methods
- Dimensional Inspection: Measuring the physical dimensions of components against specified tolerances using tools like calipers and micrometers.
- Functional Testing: Ensuring that components perform as intended under simulated operational conditions.
- Non-Destructive Testing (NDT): Techniques like ultrasonic testing and magnetic particle testing help identify defects without damaging the components.
Verifying Supplier Quality Control
B2B buyers need to implement strategies to verify the quality control processes of their suppliers. Here are actionable methods:
-
Supplier Audits: Conducting on-site audits of potential suppliers can provide insights into their manufacturing processes and quality assurance practices. Focus on their adherence to international standards and their internal QC processes.
-
Requesting Quality Reports: Suppliers should provide documentation of their quality control procedures, inspection reports, and certifications. Regular reporting can help build trust.
-
Third-Party Inspections: Engaging third-party quality inspection services can offer an unbiased assessment of the supplier’s manufacturing capabilities and quality control measures. This is particularly important for buyers in regions with less stringent local regulations.
QC and Certification Nuances for International Buyers
For B2B buyers from regions like Africa, South America, the Middle East, and Europe, understanding the nuances of quality control and certification is crucial:
-
Regional Standards Compliance: Different regions may have varying compliance requirements. Buyers should ensure that suppliers are familiar with and can meet the regulatory standards specific to their market.
-
Cultural and Communication Considerations: Misunderstandings can arise from cultural differences in business practices. Establishing clear communication channels and understanding local business customs can enhance collaboration.
-
Logistics and Supply Chain Reliability: Quality assurance is not just about the manufacturing process; it also extends to logistics. Buyers should evaluate the supplier’s ability to deliver components on time and in compliance with quality standards.
In conclusion, a comprehensive understanding of manufacturing processes and quality assurance is essential for B2B buyers in the CNC machine component industry. By focusing on these areas, buyers can make informed decisions, ensuring that they partner with suppliers capable of delivering high-quality products that meet their specific needs.
Comprehensive Cost and Pricing Analysis for components of a cnc machine Sourcing
When sourcing components for CNC machines, understanding the comprehensive cost structure and pricing dynamics is crucial for international B2B buyers. This analysis will explore the key cost components, price influencers, and practical tips for negotiating favorable terms, particularly for buyers from Africa, South America, the Middle East, and Europe.
Cost Components of CNC Machine Components
-
Materials: The primary cost driver is the materials used in CNC components, including metals (aluminum, steel), plastics, and composites. Material prices can fluctuate based on market demand and availability, impacting overall costs.
-
Labor: Labor costs encompass both direct labor (workers assembling the components) and indirect labor (management and support staff). Regions with higher labor costs can affect the pricing of components, making it essential to consider the supplier’s location.
-
Manufacturing Overhead: This includes costs related to facilities, utilities, equipment depreciation, and administrative expenses. Efficient manufacturing processes can help mitigate these costs, potentially leading to lower prices for buyers.
-
Tooling: Tooling costs involve the creation and maintenance of molds and tools necessary for production. Custom tooling can significantly increase initial costs but may lead to better quality and precision in the long run.
-
Quality Control (QC): Ensuring component quality through rigorous QC processes adds to the cost but is vital for maintaining performance and reducing defects. Certifications (e.g., ISO) can also influence pricing.
-
Logistics: Shipping and transportation costs are especially critical for international buyers. Factors such as distance, shipping method, and import duties can all affect the final price.
-
Margin: Suppliers typically include a profit margin in their pricing. Understanding the standard margins in different regions can help buyers negotiate better deals.
Price Influencers
-
Volume/MOQ: Minimum Order Quantities (MOQs) can vary significantly by supplier. Higher volumes often lead to discounted prices, making bulk purchases more cost-effective.
-
Specifications/Customization: Customized components can lead to higher costs. Buyers should weigh the need for specific features against budget constraints.
-
Materials: The choice of materials directly impacts the price. For instance, high-grade materials may offer enhanced performance but come at a premium.
-
Quality/Certifications: Suppliers with recognized certifications may charge more due to the assurance of quality. However, this can be a worthwhile investment for critical applications.
-
Supplier Factors: The supplier’s reputation, reliability, and production capabilities can influence pricing. Established suppliers may command higher prices but often offer better service and quality assurance.
-
Incoterms: Understanding Incoterms (International Commercial Terms) is essential for clarifying responsibilities for shipping, risks, and costs. This knowledge can prevent unexpected expenses.
Buyer Tips
-
Negotiation: Leverage your purchasing power by negotiating terms based on volume and long-term relationships. Don’t hesitate to ask for discounts, especially for bulk orders.
-
Cost-Efficiency: Analyze Total Cost of Ownership (TCO), which includes purchase price, maintenance, and operational costs over the component’s lifecycle. This holistic view can guide purchasing decisions.
-
Pricing Nuances: Be aware of regional pricing differences. For instance, components sourced from Europe may have higher prices due to labor and material costs, while suppliers in Asia might offer competitive pricing due to lower overhead.
-
Research Suppliers: Conduct thorough research on potential suppliers, including reviews and references. This due diligence can help identify reliable partners who offer competitive pricing and quality.
-
Local Regulations: Familiarize yourself with local import regulations and tariffs that may affect the overall cost when sourcing from international suppliers.
Disclaimer
Prices for CNC machine components can vary widely based on the factors discussed above. The information provided serves as a guideline and may not reflect current market conditions. Always conduct thorough market research and supplier comparisons before making purchasing decisions.
Spotlight on Potential components of a cnc machine Manufacturers and Suppliers
This section looks at several manufacturers active in the ‘components of a cnc machine’ market. This is a representative sample for illustrative purposes; B2B buyers must conduct extensive due diligence before any transaction. Information is synthesized from public sources and general industry knowledge.
Essential Technical Properties and Trade Terminology for components of a cnc machine
Key Technical Properties of CNC Machine Components
Understanding the critical specifications of CNC machine components is essential for international B2B buyers, as these properties significantly influence machine performance, durability, and cost-effectiveness.
-
Material Grade
– Definition: This refers to the specific classification of materials used in the construction of CNC machine components, such as steel, aluminum, and plastics.
– B2B Importance: Selecting the right material grade affects the machine’s strength, weight, and resistance to wear and tear. Buyers must ensure that components are made from materials suitable for their specific application to guarantee longevity and performance. -
Tolerance
– Definition: Tolerance indicates the permissible limit of variation in a physical dimension of a component. It is usually expressed as a range (e.g., ±0.01 mm).
– B2B Importance: Precision is crucial in CNC machining. Buyers should prioritize components with tight tolerances to ensure the final product meets quality standards, especially in industries like aerospace and automotive where precision is non-negotiable. -
Load Capacity
– Definition: This refers to the maximum load a component can bear without failure, which is critical for moving parts like spindles and tables.
– B2B Importance: Understanding load capacity helps buyers select components that can handle the operational demands of their specific applications, preventing breakdowns and costly downtime. -
Rotational Speed
– Definition: This is the maximum speed at which a spindle or motor can operate, typically measured in RPM (revolutions per minute).
– B2B Importance: High rotational speeds can enhance productivity but may also affect the quality of the machined part. Buyers should match the rotational speed to their machining needs to balance efficiency and output quality.
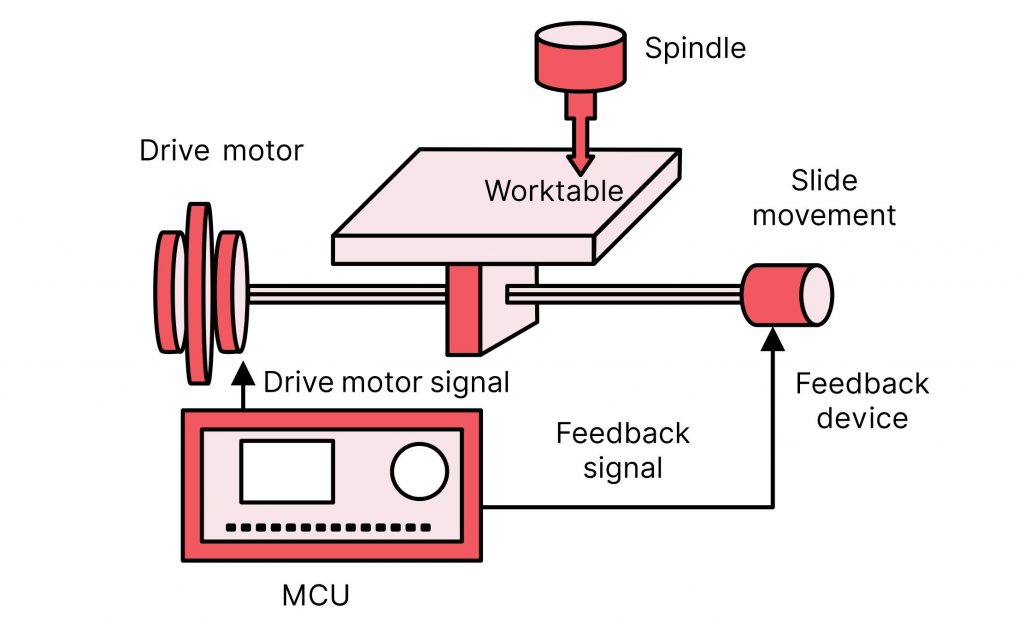
Illustrative Image (Source: Google Search)
- Surface Finish
– Definition: Surface finish refers to the texture of the surface of a component, often expressed in terms of roughness (Ra value).
– B2B Importance: A smoother finish can reduce friction and wear, improving the overall efficiency and lifespan of the machine. Buyers should specify surface finish requirements based on the intended use of the machined parts.
Common Trade Terms in CNC Machining
Familiarity with industry jargon is crucial for effective communication and negotiation in the B2B space. Here are some essential terms:
-
OEM (Original Equipment Manufacturer)
– Definition: A company that produces parts and equipment that may be marketed by another manufacturer.
– Importance: Understanding the role of OEMs helps buyers identify reputable suppliers and ensure they are purchasing high-quality components designed for specific machines. -
MOQ (Minimum Order Quantity)
– Definition: The smallest quantity of a product that a supplier is willing to sell.
– Importance: Knowing the MOQ is vital for budgeting and inventory management, especially for businesses in regions with fluctuating demand. -
RFQ (Request for Quotation)
– Definition: A document sent to suppliers requesting pricing and terms for specific products or services.
– Importance: An RFQ allows buyers to compare prices and terms from multiple suppliers, facilitating informed decision-making.
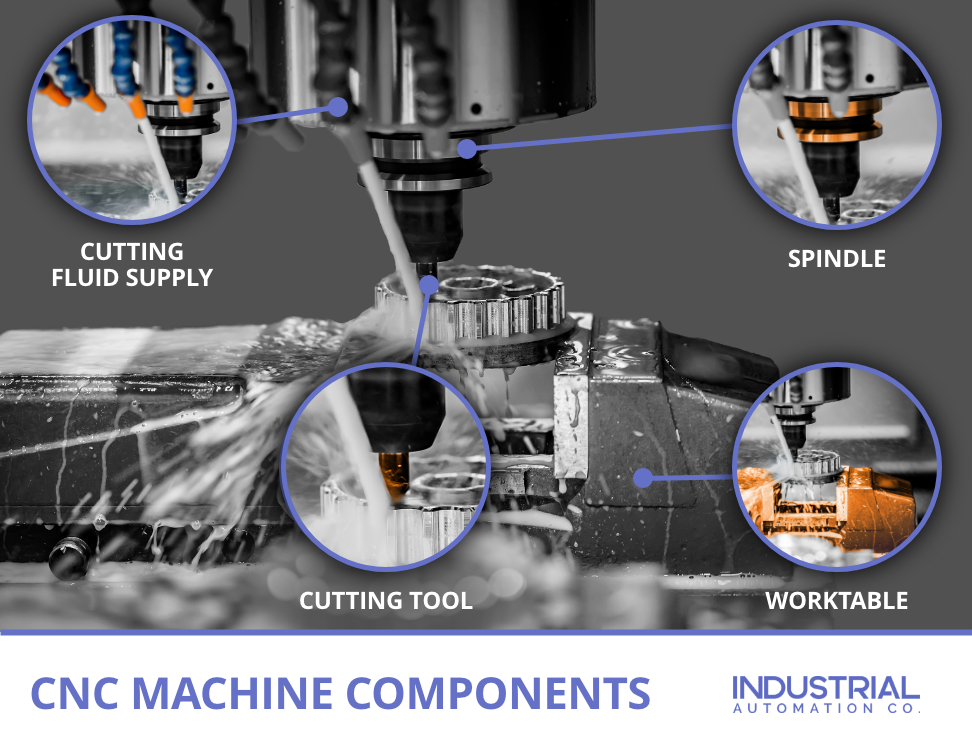
Illustrative Image (Source: Google Search)
-
Incoterms (International Commercial Terms)
– Definition: A set of predefined international trade terms that clarify the responsibilities of buyers and sellers.
– Importance: Understanding Incoterms helps buyers navigate shipping, risk, and insurance responsibilities, which is especially critical in cross-border transactions. -
Lead Time
– Definition: The amount of time from when an order is placed until it is fulfilled.
– Importance: Buyers must be aware of lead times to plan their production schedules effectively and avoid delays in their manufacturing processes. -
Tact Time
– Definition: The maximum allowable time to produce a product to meet customer demand.
– Importance: Tact time helps buyers assess whether a CNC machine can meet their production goals, ensuring they choose the right equipment for their operational needs.
By understanding these technical properties and trade terms, international B2B buyers can make informed decisions when sourcing CNC machine components, ultimately enhancing their operational efficiency and competitiveness in the market.
Navigating Market Dynamics, Sourcing Trends, and Sustainability in the components of a cnc machine Sector
Market Overview & Key Trends
The global CNC machine components market is experiencing dynamic growth, driven by technological advancements and increasing automation in manufacturing processes. Key drivers include the rising demand for high-precision parts across industries such as aerospace, automotive, and electronics. International B2B buyers, particularly from regions like Africa, South America, the Middle East, and Europe, are increasingly seeking suppliers that can offer not only quality components but also innovative solutions that enhance productivity and reduce operational costs.
Emerging trends in sourcing include a shift towards digital platforms for procurement, allowing buyers to access a wider range of suppliers and compare prices more efficiently. Additionally, the rise of Industry 4.0 is leading to the integration of IoT and AI in CNC machine operations, compelling buyers to consider suppliers who are at the forefront of these technologies. Moreover, the need for customization is growing, as manufacturers look for components that can be tailored to specific applications, emphasizing the importance of flexibility in supplier relationships.
Another significant trend is the focus on local sourcing to mitigate supply chain disruptions. This is particularly relevant for B2B buyers in Africa and South America, where logistics challenges can affect timely delivery. Buyers are advised to build strategic partnerships with local suppliers who understand regional demands and can provide faster service. Overall, being attuned to these trends will empower buyers to make informed decisions and leverage the latest innovations in CNC machine components.
Sustainability & Ethical Sourcing in B2B
Sustainability has become a critical consideration in the sourcing of CNC machine components. The environmental impact of manufacturing processes is under scrutiny, leading buyers to prioritize suppliers who adopt sustainable practices. This includes using eco-friendly materials, minimizing waste, and implementing energy-efficient production methods. For instance, components made from recycled metals or biodegradable materials are increasingly in demand, reflecting a broader commitment to reducing carbon footprints.
Ethical sourcing is equally important. B2B buyers should seek suppliers that uphold fair labor practices and adhere to strict ethical standards throughout their supply chains. Certifications such as ISO 14001 (Environmental Management) and ISO 45001 (Occupational Health and Safety) serve as indicators of a supplier’s commitment to sustainability and ethical operations. By prioritizing suppliers with these certifications, international buyers can ensure that their sourcing practices align with their corporate social responsibility goals.
Furthermore, transparency in the supply chain is essential. Buyers are encouraged to conduct due diligence and engage with suppliers who can provide insights into their sourcing practices and material origins. This not only fosters trust but also contributes to the broader goal of creating a sustainable manufacturing ecosystem that benefits all stakeholders involved.
Brief Evolution/History
The evolution of CNC technology can be traced back to the 1950s, when the first numerical control systems were developed, allowing for automated machining processes. Initially, these systems relied on punched tape for programming, but as computing technology advanced, the introduction of computer numerical control revolutionized the industry. By the 1980s, CNC machines had become more accessible, leading to widespread adoption across various sectors.
Today, CNC machines are integral to modern manufacturing, characterized by enhanced precision, speed, and flexibility. The continuous advancements in software and hardware have enabled manufacturers to produce increasingly complex components, driving innovation in the CNC machine components market. For international B2B buyers, understanding this evolution highlights the importance of partnering with suppliers who are equipped to meet the demands of an ever-changing landscape, ensuring they remain competitive in their respective markets.
Related Video: Incoterms for beginners | Global Trade Explained
Frequently Asked Questions (FAQs) for B2B Buyers of components of a cnc machine
-
What criteria should I use to vet suppliers of CNC machine components?
When vetting suppliers, prioritize their industry experience, reputation, and customer reviews. Verify their certifications, such as ISO standards, which ensure quality management systems. Request references from previous clients, especially those in your region, to assess reliability. Additionally, consider their production capabilities, response times, and after-sales support. Engaging in a trial order can also help gauge their performance before making larger commitments. -
Can CNC components be customized to specific requirements?
Yes, many suppliers offer customization options for CNC components. Discuss your specific needs regarding dimensions, materials, and functionality with potential suppliers. Ensure they have the technical expertise to accommodate your requests. It’s advisable to request prototypes or samples to verify that the customized components meet your specifications before placing a bulk order. -
What are the typical minimum order quantities (MOQs) and lead times for CNC components?
MOQs for CNC components can vary widely depending on the supplier and the complexity of the parts. Commonly, MOQs may range from 10 to 100 units. Lead times also depend on the supplier’s production capacity and the complexity of the order, typically ranging from 2 to 8 weeks. Always clarify these terms upfront to avoid delays in your production schedule. -
What payment terms are common when sourcing CNC machine components internationally?
Payment terms can vary by supplier and region. Common practices include upfront payments, a deposit with the balance upon delivery, or net payment terms (e.g., net 30 or net 60). For international transactions, consider using secure payment methods such as letters of credit, PayPal, or bank transfers to mitigate risks. Always ensure that payment terms are clearly stated in the contract to prevent misunderstandings. -
How can I ensure quality assurance and certifications for CNC components?
To ensure quality, request documentation of certifications from suppliers, such as ISO 9001 or other relevant industry standards. Inquire about their quality control processes, including inspection methods and testing protocols. Consider conducting third-party inspections or audits, especially for significant orders, to verify compliance with your quality standards before shipment. -
What logistics considerations should I keep in mind when importing CNC components?
When importing CNC components, factor in shipping costs, customs duties, and lead times for delivery. Choose reliable logistics partners who are experienced in handling industrial equipment. Ensure that suppliers provide adequate packaging to prevent damage during transit. Also, be aware of the import regulations in your country to avoid delays or penalties at customs. -
How should disputes over quality or delivery issues be handled?
Establish a clear dispute resolution process in your contract before engaging with suppliers. Communicate issues promptly and provide evidence (photos, inspection reports) to support your claims. It’s often beneficial to negotiate an amicable resolution, but if necessary, consider mediation or arbitration as outlined in your agreement. Maintaining a professional relationship can facilitate smoother negotiations during disputes. -
What trends should I be aware of when sourcing CNC components internationally?
Stay informed about advancements in CNC technology, such as increased automation and smart manufacturing solutions. Sustainability is becoming a key focus, so consider suppliers who implement eco-friendly practices. Additionally, be aware of global supply chain disruptions and geopolitical factors that may affect availability and pricing. Networking with industry peers can provide valuable insights into emerging trends and supplier recommendations.
Important Disclaimer & Terms of Use
⚠️ Important Disclaimer
The information provided in this guide, including content regarding manufacturers, technical specifications, and market analysis, is for informational and educational purposes only. It does not constitute professional procurement advice, financial advice, or legal advice.
While we have made every effort to ensure the accuracy and timeliness of the information, we are not responsible for any errors, omissions, or outdated information. Market conditions, company details, and technical standards are subject to change.
B2B buyers must conduct their own independent and thorough due diligence before making any purchasing decisions. This includes contacting suppliers directly, verifying certifications, requesting samples, and seeking professional consultation. The risk of relying on any information in this guide is borne solely by the reader.
Strategic Sourcing Conclusion and Outlook for components of a cnc machine
In conclusion, strategic sourcing for CNC machine components is essential for international B2B buyers aiming to enhance operational efficiency and product quality. Understanding the intricate parts of a CNC machine—such as the Machine Control Unit, Drive System, and Feedback Systems—enables buyers to make informed decisions that align with their manufacturing needs. By prioritizing reliable suppliers and integrating advanced technologies, businesses can minimize downtime and ensure precision in production.
Buyers from Africa, South America, the Middle East, and Europe should consider leveraging local networks and global partnerships to source high-quality components. This approach not only fosters competitive pricing but also enhances supply chain resilience against global disruptions.
As the demand for automated precision manufacturing continues to rise, investing in the right CNC components will be pivotal for staying ahead in the competitive landscape. Now is the time to engage with suppliers who understand your unique market challenges and can provide tailored solutions. Embrace this opportunity to elevate your manufacturing capabilities and drive sustainable growth in your operations.