Maximize Efficiency: The Complete Guide to DC Output (2025)
Introduction: Navigating the Global Market for dc output
Navigating the global market for DC output can be a complex task for international B2B buyers, especially when ensuring reliable and efficient power supply solutions. With the rise of electronic devices across various industries, sourcing a suitable DC power supply that meets specific voltage and current requirements is crucial. This comprehensive guide delves into the myriad types of DC outputs, including programmable and industrial power supplies, and their diverse applications, from powering sensitive laboratory equipment to supporting large-scale manufacturing processes.
International buyers from regions such as Africa, South America, the Middle East, and Europe, including countries like Colombia and Egypt, face unique challenges when vetting suppliers and understanding market dynamics. This guide equips you with actionable insights, covering essential criteria for evaluating suppliers, cost considerations, and best practices for ensuring compliance with local regulations. By offering a deep understanding of the specifications and features that matter most, we empower you to make informed purchasing decisions that align with your operational needs.
Whether you are looking to enhance your production capabilities or streamline your electronics testing processes, this guide serves as a valuable resource for navigating the complexities of sourcing DC output solutions in a global marketplace.
Understanding dc output Types and Variations
Type Name | Key Distinguishing Features | Primary B2B Applications | Brief Pros & Cons for Buyers |
---|---|---|---|
Linear DC Power Supply | Simple design, low noise, excellent regulation | Laboratory equipment, medical devices | Pros: Stable output, minimal ripple; Cons: Less efficient, larger size. |
Switching DC Power Supply | High efficiency, compact design, adjustable output | Telecommunications, industrial automation | Pros: Energy-efficient, lightweight; Cons: Higher noise levels, complexity. |
Programmable DC Power Supply | Customizable output settings, digital control | Research & development, testing environments | Pros: Versatile, precise control; Cons: Higher cost, requires technical expertise. |
High Voltage DC Power Supply | Capable of delivering high voltages with safety features | Power testing, industrial machinery | Pros: Suitable for demanding applications; Cons: Safety concerns, larger size. |
DC-DC Converter | Converts one DC voltage to another, compact and efficient | Renewable energy systems, electric vehicles | Pros: Versatile, enhances system efficiency; Cons: Limited output range, potential for heat generation. |
What are the Characteristics of Linear DC Power Supplies?
Linear DC power supplies are characterized by their straightforward design and low noise output. They provide a stable voltage with minimal ripple, making them ideal for sensitive applications such as laboratory equipment and medical devices. When purchasing, buyers should consider the required voltage and current ratings, as well as the size and weight, which can be larger compared to other types. While they are reliable, their efficiency is lower, leading to potential energy waste.
How Do Switching DC Power Supplies Differ?
Switching DC power supplies utilize high-frequency switching technology to convert power, resulting in high efficiency and compact designs. They are commonly used in telecommunications and industrial automation due to their ability to adjust output voltage dynamically. Buyers should evaluate the noise levels and complexity of these supplies, as they can introduce electromagnetic interference. Despite their advantages in size and efficiency, understanding the specific application requirements is crucial to mitigate potential drawbacks.
What Makes Programmable DC Power Supplies Unique?
Programmable DC power supplies offer customizable output settings controlled through digital interfaces, making them suitable for research and testing environments. Their versatility allows for precise adjustments to voltage and current, which is beneficial for experimental setups. Buyers should consider the programming capabilities and whether the system integrates well with existing equipment. Although they tend to be more expensive, the investment can lead to significant time savings and enhanced testing accuracy.
Why Choose High Voltage DC Power Supplies?
High voltage DC power supplies are designed to deliver elevated voltage levels safely, which is essential for power testing and operating industrial machinery. These supplies often come equipped with protective features to ensure safety during operation. Buyers must assess the voltage requirements and safety protocols, as high voltage can pose risks if not handled correctly. While they are indispensable for specific applications, their larger footprint may limit placement options.
What are the Benefits of Using DC-DC Converters?
DC-DC converters are designed to convert one DC voltage level to another, offering high efficiency in a compact format. They are particularly useful in renewable energy systems and electric vehicles, where optimizing power usage is critical. Buyers should evaluate the output range and thermal management capabilities, as these converters can generate heat. Their versatility makes them an attractive option, but understanding the specific needs of the application will ensure the right choice is made.
Key Industrial Applications of dc output
Industry/Sector | Specific Application of dc output | Value/Benefit for the Business | Key Sourcing Considerations for this Application |
---|---|---|---|
Renewable Energy | Solar Power Systems | Efficient energy conversion and storage | Ensure compatibility with local grid standards and regulations. |
Automotive | Electric Vehicle Charging Stations | Fast and reliable charging solutions | Look for durable power supplies with high voltage capabilities. |
Telecommunications | Data Center Operations | Stable power supply for continuous operation | Consider redundancy and scalability for future growth. |
Industrial Automation | Robotics and Control Systems | Enhanced precision and reliability in operations | Evaluate the power supply’s response time and load handling. |
Medical Equipment | Diagnostic and Monitoring Devices | Accurate and consistent performance for patient care | Compliance with health regulations and safety standards is critical. |
How is DC Output Used in Renewable Energy Applications?
In the renewable energy sector, particularly in solar power systems, DC output is crucial for converting solar energy into usable electricity. Solar panels generate DC electricity, which must be managed and converted for storage in batteries or for use in the grid. This application addresses challenges like energy efficiency and grid compatibility. For international buyers, especially in regions like Africa and South America where solar energy is abundant, sourcing reliable and efficient DC power supplies that comply with local regulations is essential for maximizing energy output and ensuring system longevity.
What Role Does DC Output Play in Automotive Charging Stations?
DC output is integral to electric vehicle (EV) charging stations, providing fast and efficient charging solutions. Unlike AC charging, which can take hours, DC fast chargers significantly reduce charging time, enhancing user convenience and promoting EV adoption. For buyers in the automotive sector across the Middle East and Europe, it is vital to select robust power supplies that can handle high voltage and current levels, ensuring safety and reliability. Additionally, understanding local infrastructure and grid requirements will aid in the efficient deployment of these systems.
How is DC Output Critical for Telecommunications Data Centers?
In telecommunications, DC output powers data center operations, ensuring that servers and networking equipment function without interruption. A stable power supply is critical for maintaining uptime and preventing data loss. Buyers in this sector should prioritize sourcing DC power supplies with high reliability and redundancy features, especially in regions with fluctuating power quality. As data demands grow, scalability in power solutions will also be a key consideration for future-proofing investments.
Why is DC Output Important for Industrial Automation?
In industrial automation, DC output is essential for powering robotics and control systems that require precise voltage and current for optimal performance. This application helps solve issues related to equipment reliability and operational efficiency. International buyers, particularly in Europe and the Middle East, must assess the power supply’s response time and load handling capabilities to ensure they meet the specific demands of their automation systems. Investing in high-quality DC power supplies can lead to significant productivity gains and reduced downtime.
How Does DC Output Benefit Medical Equipment?
DC output plays a vital role in the operation of diagnostic and monitoring devices in the healthcare sector. These devices require a consistent and accurate power supply to function correctly, directly impacting patient care quality. For B2B buyers in the medical field, especially in developing regions like Africa, sourcing DC power supplies that comply with stringent health regulations and safety standards is non-negotiable. Ensuring reliability in power supply not only enhances device performance but also upholds patient safety and care standards.
3 Common User Pain Points for ‘dc output’ & Their Solutions
Scenario 1: Inconsistent DC Output Causes Equipment Failure
The Problem: One of the most common challenges faced by international B2B buyers, particularly in regions with fluctuating power stability like Africa and South America, is the inconsistency of DC output. Equipment that relies on a stable power supply can malfunction or even get damaged if the voltage or current is not regulated properly. This inconsistency can lead to costly downtimes, repair expenses, and a significant loss of productivity, making it imperative for businesses to find a reliable solution.
The Solution: To address this issue, businesses should invest in high-quality programmable DC power supplies that offer features like voltage regulation and current limiting. These devices ensure that the output remains stable even when input power fluctuates. Buyers should look for suppliers that provide detailed specifications and allow for customization based on specific application needs. Additionally, implementing a power conditioning system can help filter out noise and transients, ensuring that the equipment receives clean power. Regular maintenance and calibration of the power supply are also essential to ensure long-term reliability.
Scenario 2: Complex Integration with Existing Systems
The Problem: Many B2B buyers face difficulties integrating new DC output devices with their existing systems. This is particularly prevalent in industries like manufacturing and telecommunications, where legacy systems are common. The lack of compatibility can lead to increased integration costs, delays, and frustration among technical teams who struggle to make everything work seamlessly together.
The Solution: To overcome integration challenges, buyers should prioritize selecting DC output devices that are designed with compatibility in mind. This includes ensuring that the voltage levels and connector types match existing equipment. Working closely with suppliers who provide comprehensive technical support can also facilitate smoother integration. Additionally, opting for modular DC power supplies can allow for easier scalability and adaptation to future technological advancements. It may also be beneficial to engage with system integrators who specialize in bridging the gap between new technology and legacy systems to streamline the process.
Scenario 3: Lack of Technical Expertise in Selection and Use
The Problem: In many regions, especially in emerging markets like parts of Africa and South America, there is often a lack of technical expertise available to make informed decisions regarding the selection and use of DC output devices. This knowledge gap can result in purchasing the wrong equipment, leading to inefficiencies and increased operational costs.
The Solution: To mitigate this issue, B2B buyers should seek out suppliers that offer comprehensive training and support services. This can include workshops, webinars, and detailed product documentation that educate users on the specifications and applications of DC power supplies. Additionally, engaging with manufacturers who provide a consultation service can help buyers identify the right equipment for their specific needs. Investing in ongoing training for technical staff can also enhance their understanding of power supply systems, ensuring they can make informed decisions and maintain optimal operational efficiency. Finally, leveraging online resources and industry forums can provide valuable insights and peer support to navigate the complexities of DC output applications.
Strategic Material Selection Guide for dc output
When selecting materials for DC output applications, international B2B buyers must consider various factors, including performance characteristics, cost implications, and regional compliance standards. Below is an analysis of four common materials used in DC output applications, focusing on their properties, advantages, disadvantages, and specific considerations for buyers from Africa, South America, the Middle East, and Europe.
What Are the Key Properties of Copper for DC Output Applications?
Copper is one of the most widely used materials in electrical applications due to its excellent electrical conductivity and thermal properties. It can withstand high temperatures and has a good resistance to corrosion, making it suitable for various environments.
- Pros: High conductivity ensures minimal energy loss, and its malleability allows for easy fabrication into wires and connectors.
- Cons: Copper is relatively expensive compared to other metals and can corrode if not properly insulated, particularly in humid or saline environments.
- Impact on Application: Copper is ideal for applications requiring high current flow, such as in power distribution systems and electronic devices.
- Considerations for Buyers: Compliance with international standards like ASTM B170 (for copper wire) is essential. Buyers should also consider local availability and cost fluctuations.
How Does Aluminum Compare as a Material for DC Output?
Aluminum is a lightweight alternative to copper, often used in applications where weight is a critical factor. It offers good conductivity, though not as high as copper, and has excellent resistance to corrosion.
- Pros: Lower cost and weight compared to copper, making it suitable for large-scale installations and applications where weight savings are crucial.
- Cons: Aluminum has a lower conductivity, which may necessitate larger wire sizes to achieve the same performance as copper.
- Impact on Application: Commonly used in overhead power lines and large electrical installations where weight and cost are significant factors.
- Considerations for Buyers: Ensure compliance with standards like ASTM B231 for aluminum conductors. Local market conditions may affect pricing and availability.
What Are the Benefits of Using Stainless Steel in DC Output Systems?
Stainless steel is known for its exceptional strength and corrosion resistance, making it suitable for harsh environments, including chemical processing and marine applications.
- Pros: High durability and resistance to corrosion, ensuring long-term performance in challenging conditions.
- Cons: Higher manufacturing complexity and cost compared to copper and aluminum, which may limit its use in budget-sensitive projects.
- Impact on Application: Ideal for applications that require robust materials, such as connectors and enclosures in corrosive environments.
- Considerations for Buyers: Compliance with international standards like ASTM A240 is crucial. Buyers should evaluate the total cost of ownership, considering maintenance and replacement cycles.
Why Choose Thermoplastic Materials for DC Output Applications?
Thermoplastics, such as polyvinyl chloride (PVC) and polyethylene (PE), are often used for insulation and protective casings in DC output applications. They offer good electrical insulation properties and are lightweight.
- Pros: Cost-effective and easy to mold into complex shapes, providing flexibility in design.
- Cons: Limited thermal resistance compared to metals, which can lead to failure in high-temperature environments.
- Impact on Application: Suitable for insulation of wires and connectors in low to moderate temperature applications.
- Considerations for Buyers: Ensure compliance with standards like UL 94 for flammability. Regional preferences for specific types of thermoplastics may also influence material choice.
Summary Table of Material Selection for DC Output
Material | Typical Use Case for dc output | Key Advantage | Key Disadvantage/Limitation | Relative Cost (Low/Med/High) |
---|---|---|---|---|
Copper | Power distribution systems | High conductivity reduces energy loss | Expensive and prone to corrosion | High |
Aluminum | Overhead power lines | Lightweight and cost-effective | Lower conductivity requires larger sizes | Medium |
Stainless Steel | Connectors and enclosures in harsh environments | Exceptional strength and corrosion resistance | Higher manufacturing complexity and cost | High |
Thermoplastics | Insulation for wires and connectors | Cost-effective and flexible in design | Limited thermal resistance | Low |
This strategic material selection guide provides B2B buyers with essential insights into the properties and applications of various materials for DC output. Understanding these factors will facilitate informed decision-making, ensuring that the chosen materials meet both performance and regulatory requirements.
In-depth Look: Manufacturing Processes and Quality Assurance for dc output
What Are the Main Stages in the Manufacturing Process of DC Output Devices?
The manufacturing process of DC output devices encompasses several critical stages, each of which plays a vital role in ensuring product reliability and performance. These stages include material preparation, forming, assembly, and finishing.
-
Material Preparation: The initial stage involves sourcing high-quality raw materials, which may include metals, plastics, and electronic components. Suppliers should provide certifications of material quality to ensure compliance with international standards. Proper handling and storage of these materials are essential to prevent contamination or damage.
-
Forming: During this phase, raw materials are shaped into components. This can involve machining, stamping, or molding processes, depending on the design specifications of the DC output device. Advanced technologies such as CNC machining and 3D printing are increasingly used for precision and efficiency. Buyers should inquire about the technology used by suppliers to assess the potential for defects in component formation.
-
Assembly: Once components are formed, they are assembled into the final product. This stage may include soldering, wiring, and integration of electronic circuits. Automated assembly lines are often employed to enhance accuracy and reduce human error. B2B buyers should evaluate the assembly process for automation levels, as this can significantly impact production consistency.
-
Finishing: The final stage involves surface treatments, painting, and quality checks before packaging. This step not only enhances aesthetics but also improves durability and resistance to environmental factors. Finishing processes should comply with industry standards to ensure product longevity.
How Is Quality Assurance Implemented in DC Output Manufacturing?
Quality assurance (QA) is integral to the manufacturing of DC output devices, ensuring that products meet both customer expectations and regulatory requirements. The QA process typically adheres to international standards such as ISO 9001 and may also involve industry-specific certifications like CE and API.
- International and Industry-Specific Standards:
– ISO 9001: This standard focuses on quality management systems and is crucial for companies looking to improve their operational processes. Compliance indicates that a manufacturer is committed to quality and customer satisfaction.
– CE Marking: For products marketed in Europe, CE marking ensures that the product meets EU safety, health, and environmental protection requirements.
– API Standards: For manufacturers in the oil and gas sector, API standards ensure that the products are suitable for use in potentially hazardous environments.
What Are the Key Quality Control Checkpoints During Manufacturing?
Quality control (QC) involves several checkpoints throughout the manufacturing process to ensure that each stage meets specified standards. These checkpoints typically include:
-
Incoming Quality Control (IQC): At this initial stage, materials and components are inspected upon arrival at the manufacturing facility. This includes checking for defects, measuring dimensions, and reviewing certificates of conformity from suppliers.
-
In-Process Quality Control (IPQC): Throughout the manufacturing process, regular inspections are conducted to monitor production quality. This can involve functional testing of components, visual inspections, and verifying adherence to specifications.
-
Final Quality Control (FQC): Before products are packaged and shipped, a final inspection is performed. This may include comprehensive testing of electrical performance, safety checks, and ensuring compliance with relevant standards. B2B buyers should request FQC reports to verify product quality before purchase.
What Testing Methods Are Commonly Used in DC Output Quality Assurance?
Various testing methods are employed to ensure the quality and reliability of DC output devices. Common testing techniques include:
-
Electrical Testing: This involves measuring voltage, current, and resistance to ensure that the device operates within specified parameters. Functional testing is also critical to verify that the device performs as intended under load conditions.
-
Environmental Testing: Products may be subjected to extreme temperatures, humidity, and vibration to assess durability and reliability in real-world conditions. This testing is particularly important for products intended for use in harsh environments.
-
Safety Testing: Compliance with safety standards is paramount. This can include tests for insulation resistance, dielectric strength, and short-circuit protection to prevent hazards during operation.
How Can B2B Buyers Verify Supplier Quality Control Processes?
For international B2B buyers, especially those from regions such as Africa, South America, the Middle East, and Europe, verifying a supplier’s quality control processes is essential. Here are actionable steps buyers can take:
-
Supplier Audits: Conducting regular audits of potential suppliers allows buyers to assess their manufacturing processes, quality control measures, and compliance with relevant standards. Audits should include reviews of documentation, production methods, and employee training.
-
Requesting Quality Reports: Buyers should ask suppliers for detailed quality reports that outline the results of IQC, IPQC, and FQC processes. These reports should provide insights into defect rates, corrective actions taken, and overall product quality.
-
Third-Party Inspections: Engaging third-party inspection services can provide an unbiased assessment of supplier quality. These inspections can cover various aspects, from material quality to final product performance.
-
Understanding Regional Certification Nuances: Buyers should be aware of specific certifications and standards that apply in their region. For example, products sold in the EU must meet CE requirements, while those in certain industries may require API certifications. Understanding these nuances can help buyers navigate the complexities of international procurement.
Conclusion
The manufacturing processes and quality assurance practices for DC output devices are critical considerations for B2B buyers. By understanding the main stages of manufacturing, key quality control checkpoints, and effective verification methods, buyers can make informed decisions and ensure they source reliable and compliant products. Engaging with suppliers who prioritize quality assurance will ultimately lead to successful partnerships and high-quality outcomes.
Practical Sourcing Guide: A Step-by-Step Checklist for ‘dc output’
In today’s fast-paced global market, sourcing reliable DC output solutions is crucial for businesses in diverse sectors, particularly for international B2B buyers from regions such as Africa, South America, the Middle East, and Europe. This guide provides a step-by-step checklist to streamline your procurement process, ensuring that you select the right products for your needs.
Step 1: Define Your Technical Specifications
Understanding your requirements is the foundation of effective sourcing. Clearly outline the voltage, current, and power needs for your application. Consider factors such as:
– Load Type: Identify whether you need a constant voltage or a constant current supply.
– Regulation Needs: Determine the acceptable voltage fluctuations for your application to ensure consistent performance.
Step 2: Research Potential Suppliers
Thorough research is vital to identify reliable suppliers. Look for manufacturers or distributors with a solid reputation in the industry. Key aspects to investigate include:
– Experience and Expertise: Check how long they have been in the DC power supply market.
– Product Range: Ensure they offer a variety of products that meet your specifications, including programmable and high-voltage options.
Step 3: Evaluate Supplier Certifications
Before finalizing a supplier, verify their certifications to ensure compliance with international standards. This step is crucial for:
– Quality Assurance: Certifications like ISO 9001 indicate a commitment to quality management.
– Safety Standards: Look for compliance with safety regulations relevant to your industry, such as CE marking in Europe or UL certification in North America.
Step 4: Request Product Samples
Obtaining samples allows you to assess the quality and performance of the DC output solutions firsthand. This process should include:
– Testing: Evaluate the samples in your operational environment to ensure they meet your technical specifications.
– Compatibility Checks: Ensure the products integrate seamlessly with your existing systems and equipment.
Step 5: Review Pricing and Payment Terms
Cost is a significant factor in procurement. Request detailed pricing from multiple suppliers and compare offers. Consider:
– Total Cost of Ownership: Factor in shipping, taxes, and potential tariffs, especially for international purchases.
– Payment Flexibility: Inquire about payment terms and financing options that may ease cash flow concerns.
Step 6: Assess Customer Support and Warranty Options
Strong customer support can significantly impact your satisfaction with the product. Look for suppliers who offer:
– Technical Support: Ensure they provide assistance during installation and troubleshooting.
– Warranty Policies: Understand the warranty terms to protect your investment in case of product failures.
Step 7: Finalize Your Order and Monitor Delivery
Once you have selected a supplier, finalize your order with clear specifications and timelines. During delivery:
– Tracking: Stay in communication with the supplier to track the shipment.
– Inspection Upon Arrival: Verify that the delivered products match your order specifications and are free from damage.
By following this checklist, B2B buyers from diverse regions can confidently navigate the sourcing process for DC output solutions, ensuring they select products that meet their operational needs while establishing strong supplier relationships.
Comprehensive Cost and Pricing Analysis for dc output Sourcing
What Are the Key Cost Components in DC Output Sourcing?
Understanding the cost structure of DC output sourcing is crucial for international B2B buyers. The primary components influencing costs include:
-
Materials: The quality and type of materials used in manufacturing DC power supplies can significantly affect the price. High-quality components such as capacitors and transformers may increase initial costs but can lead to better performance and longevity.
-
Labor: Labor costs vary by region and can impact overall pricing. Countries with higher labor costs may offer products with better craftsmanship and quality assurance, while lower-cost regions may lead to savings but potentially at the expense of quality.
-
Manufacturing Overhead: This includes costs related to utilities, rent, and equipment maintenance. Efficient manufacturing processes can help keep these costs down, which can be beneficial for the buyer.
-
Tooling: For custom or specialized DC output products, tooling costs can be significant. Buyers should consider whether the tooling costs are amortized over a larger order volume.
-
Quality Control (QC): Investing in rigorous QC processes ensures reliability and compliance with international standards, which can affect pricing but ultimately save costs related to returns or failures.
-
Logistics: Shipping and handling fees are particularly relevant for international buyers. Factors such as distance, mode of transport, and customs duties can add to the overall cost.
-
Margin: Suppliers typically build a margin into their pricing to ensure profitability. Understanding the competitive landscape can help buyers negotiate better terms.
How Do Pricing Influencers Affect DC Output Costs?
Several factors can influence the pricing of DC output products:
-
Volume/MOQ (Minimum Order Quantity): Larger orders often lead to lower per-unit costs. Buyers should assess their needs against supplier MOQs to optimize pricing.
-
Specifications and Customization: Custom solutions tailored to specific applications may incur additional costs. Buyers should weigh the benefits of customization against the potential price increase.
-
Materials: The choice of materials can dramatically affect price. For example, using higher-grade or specialized materials for demanding applications can lead to a higher initial investment but may provide better long-term value.
-
Quality and Certifications: Products that meet international standards or hold certifications may command higher prices. However, these certifications can be crucial for compliance and reliability in sensitive markets.
-
Supplier Factors: The reputation and reliability of the supplier can affect pricing. Established suppliers with a track record of quality may charge a premium, while newer suppliers may offer lower prices to gain market share.
-
Incoterms: Understanding the terms of sale is vital for international transactions. Incoterms dictate who is responsible for shipping, insurance, and tariffs, impacting the total landed cost.
What Are Effective Buyer Tips for Negotiating DC Output Prices?
For B2B buyers, especially those in regions such as Africa, South America, the Middle East, and Europe, effective negotiation and cost management strategies are essential:
-
Negotiation: Leverage volume purchases and long-term contracts to negotiate better pricing. Establishing a good relationship with suppliers can also lead to more favorable terms.
-
Cost-Efficiency: Analyze the Total Cost of Ownership (TCO), not just the upfront costs. Consider factors such as energy efficiency, maintenance, and potential downtime when evaluating products.
-
Pricing Nuances for International Buyers: Be aware of currency fluctuations and international shipping costs. These can significantly impact the final price and should be factored into budgeting.
-
Research and Compare: Conduct thorough market research to compare prices and specifications across multiple suppliers. This can provide leverage in negotiations and help identify the best value options.
Disclaimer
The prices mentioned in this analysis are indicative and can fluctuate based on market conditions, supplier negotiations, and other external factors. Always consult with suppliers for the most accurate and updated pricing information tailored to your specific requirements.
Alternatives Analysis: Comparing dc output With Other Solutions
When evaluating solutions for electrical power supply needs, it’s crucial to consider alternatives to direct current (DC) output. The right choice can significantly impact efficiency, cost, and overall system performance. In this analysis, we will compare DC output with two viable alternatives: alternating current (AC) output and battery-based power solutions.
Comparison Table of DC Output and Alternatives
Comparison Aspect | DC Output | Alternating Current (AC) Output | Battery-Based Power Solutions |
---|---|---|---|
Performance | Stable and precise voltage | Variable voltage, frequency issues | Limited by battery life and capacity |
Cost | Moderate initial investment | Generally lower infrastructure costs | Higher upfront costs for quality batteries |
Ease of Implementation | Requires specific design and setup | Widely compatible with existing infrastructure | Needs careful selection and maintenance |
Maintenance | Low maintenance requirements | Moderate maintenance for transformers and wiring | Regular replacement and charging needed |
Best Use Case | Sensitive electronic equipment | General power distribution | Portable applications, remote locations |
What Are the Pros and Cons of Alternating Current (AC) Output?
Alternating current (AC) output is a common power solution that serves as an alternative to DC output. AC is widely used in power grids and is suitable for general applications. One of the key advantages of AC is its ability to be easily transformed to different voltages, making it versatile for various applications, from residential to industrial. However, AC can experience voltage drops and interference, particularly over long distances. Its variable nature may not be ideal for sensitive electronic devices that require stable power.
How Do Battery-Based Power Solutions Compare?
Battery-based power solutions offer a portable and flexible alternative to DC output. These systems are particularly useful in remote locations or applications where grid power is unavailable. The primary advantages of battery systems include independence from the grid and the ability to store energy for later use. However, they come with limitations, such as finite capacity and the need for regular maintenance, including charging and eventual replacement. The initial investment for high-quality battery systems can also be significant, making them less appealing for some buyers.
Conclusion: How Should B2B Buyers Choose the Right Solution?
For international B2B buyers—especially from regions like Africa, South America, the Middle East, and Europe—selecting the appropriate power supply solution requires careful consideration of specific needs and applications. Companies must assess factors such as the nature of their equipment, budget constraints, and maintenance capabilities. DC output is ideal for applications demanding stable and precise voltage, while AC output may serve broader infrastructure needs. Battery solutions are best suited for portable or remote applications but require careful management. Ultimately, aligning the choice with operational demands and financial viability will lead to a more efficient and effective power supply strategy.
Essential Technical Properties and Trade Terminology for dc output
What Are the Essential Technical Properties of DC Output?
When selecting DC output power supplies, understanding the technical specifications is crucial for ensuring compatibility and efficiency in your applications. Here are some key properties to consider:
1. Output Voltage Range
The output voltage range indicates the minimum and maximum voltage levels the power supply can provide. For example, a power supply with a range of 0-10V allows for flexibility in powering devices that require different voltage levels. This is particularly important for B2B buyers in industries like manufacturing or telecommunications, where precise voltage is critical for the operation of sensitive equipment.
2. Current Rating (Amperage)
The current rating specifies the maximum amount of current the power supply can deliver without risking damage. Understanding this rating helps businesses avoid overloading the power supply, which can lead to failures and increased costs. For instance, a power supply rated at 5A should not be used to power devices that draw more current than this limit.
3. Regulation (Voltage and Current)
Voltage and current regulation refer to the power supply’s ability to maintain a constant output despite variations in input voltage or load conditions. Good regulation is essential for applications requiring stable power, such as precision testing equipment. Buyers should look for specifications indicating low ripple and noise levels, which can affect sensitive electronics.
4. Efficiency Rating
Efficiency is a measure of how much input power is converted into usable output power. A higher efficiency rating (typically over 80%) means less energy waste, leading to cost savings and reduced heat generation. This is particularly important for companies looking to minimize operational costs and enhance sustainability.
5. Temperature Coefficient
This specification indicates how much the output voltage changes with temperature variations. A low temperature coefficient is desirable, especially in environments with fluctuating temperatures. This is critical for B2B buyers in regions with extreme climates, as it ensures consistent performance.
6. Isolation Voltage
Isolation voltage refers to the voltage level that can be applied between the input and output without causing a breakdown. It is a vital safety feature that protects sensitive equipment from electrical surges and failures. Buyers should ensure that the isolation voltage meets or exceeds the requirements of their applications.
What Are Common Trade Terms in the DC Output Industry?
Understanding trade terminology can greatly improve communication and negotiation processes in the B2B sector. Here are several important terms to be aware of:
1. OEM (Original Equipment Manufacturer)
An OEM refers to a company that produces parts or equipment that may be marketed by another manufacturer. In the context of DC output supplies, businesses often source components from OEMs to integrate into their products. Understanding OEM relationships can help buyers streamline their supply chain.
2. MOQ (Minimum Order Quantity)
MOQ indicates the smallest number of units a supplier is willing to sell. This term is crucial for B2B buyers as it impacts inventory management and cost efficiency. Knowing the MOQ can help businesses plan their purchases and avoid excess inventory costs.
3. RFQ (Request for Quotation)
An RFQ is a formal request sent to suppliers to obtain pricing and terms for specific products or services. For international buyers, especially in diverse regions like Africa and South America, submitting an RFQ can help ensure competitive pricing and favorable terms.
4. Incoterms (International Commercial Terms)
Incoterms are a series of predefined commercial terms published by the International Chamber of Commerce, used in international transactions. They define the responsibilities of buyers and sellers regarding shipping, insurance, and tariffs. Understanding Incoterms is essential for international B2B buyers to navigate logistics effectively.
5. Lead Time
Lead time refers to the amount of time it takes from placing an order to receiving the goods. In industries reliant on timely delivery, such as manufacturing, understanding lead times can help businesses plan their production schedules and inventory levels.
6. Warranty Period
The warranty period is the duration during which a product is guaranteed to be free from defects. For B2B buyers, knowing the warranty terms can influence purchasing decisions, as it reflects the manufacturer’s confidence in their product’s reliability.
By familiarizing yourself with these essential properties and trade terms related to DC output, you can make informed decisions that align with your business’s operational needs and strategic goals.
Navigating Market Dynamics and Sourcing Trends in the dc output Sector
What Are the Current Market Dynamics and Key Trends in the DC Output Sector?
The global market for DC output devices is experiencing significant growth, driven by advancements in technology and increasing demand across various sectors. Key trends include the rise of renewable energy systems, where DC power supplies are crucial for solar energy applications, and the increasing use of electric vehicles (EVs), which rely heavily on DC charging infrastructure. Furthermore, the ongoing digital transformation is pushing industries towards automation and smart technologies, necessitating reliable DC power supplies for everything from sensors to robotics.
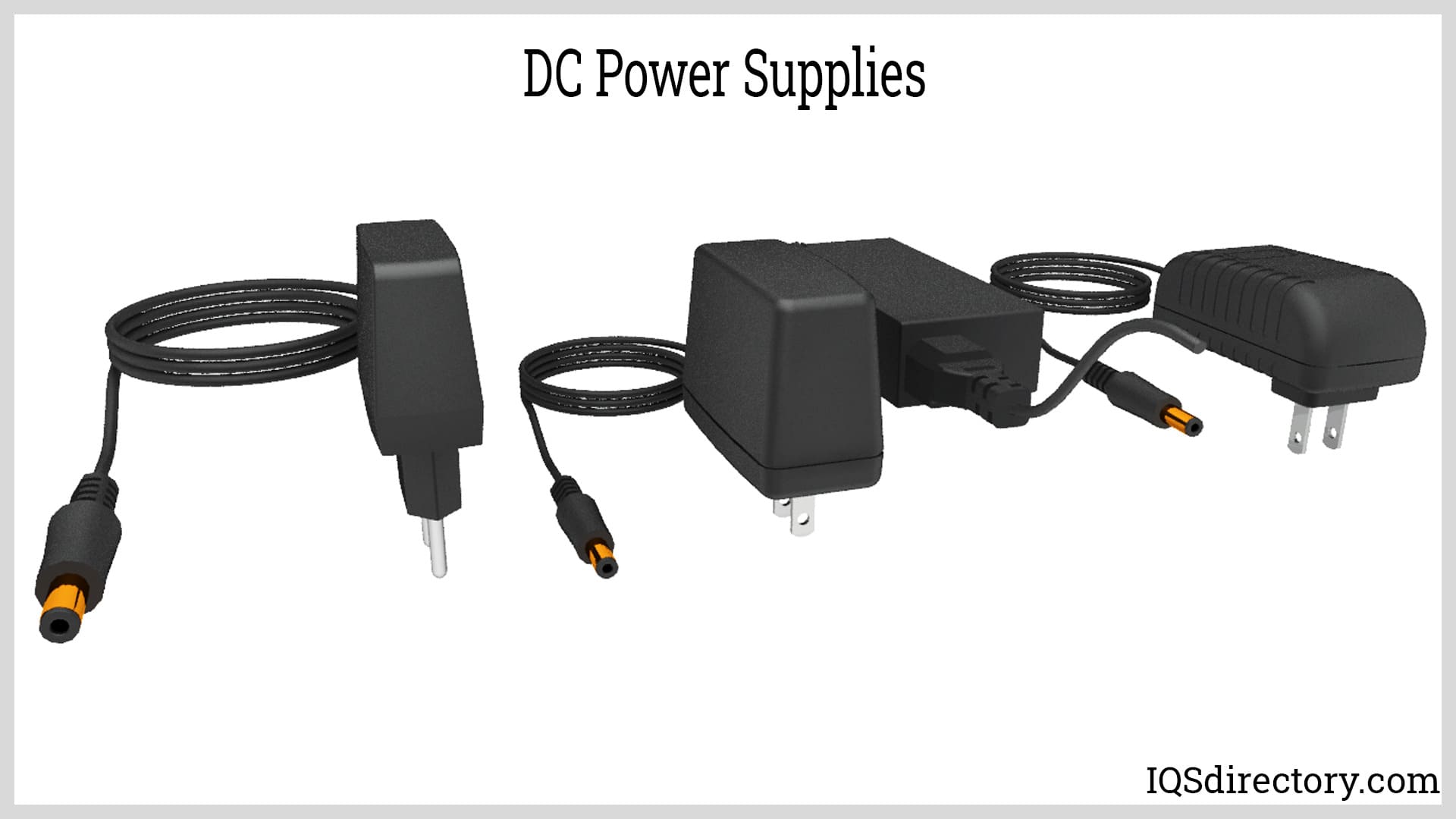
A stock image related to dc output.
International B2B buyers, particularly in regions like Africa, South America, the Middle East, and Europe, should consider the implications of these trends on sourcing strategies. The transition to more sophisticated DC power systems is leading to a demand for programmable and modular power supplies, which offer flexibility and efficiency. Additionally, the focus on energy efficiency and high-performance standards is pushing manufacturers to innovate, thus providing buyers with a wider range of options. It is essential for businesses to stay informed about these dynamics to make educated purchasing decisions and to align their sourcing strategies with market demands.
How Can International Buyers Prioritize Sustainability and Ethical Sourcing in DC Output?
As global awareness of environmental issues grows, sustainability and ethical sourcing have become paramount in the B2B sector, including the DC output market. Buyers must be aware of the environmental impact of their purchases, focusing on suppliers that minimize waste and utilize sustainable materials. This includes sourcing products that are designed for energy efficiency, as these can significantly reduce the overall carbon footprint of operations.
Moreover, certifications such as Energy Star, RoHS, and ISO 14001 can serve as indicators of a supplier’s commitment to sustainability. Buyers should prioritize partnerships with manufacturers who not only comply with these standards but also engage in ethical practices throughout their supply chains. This not only enhances brand reputation but also meets the increasing demand from consumers for environmentally responsible products.
What is the Brief Evolution and History of DC Output Technology?
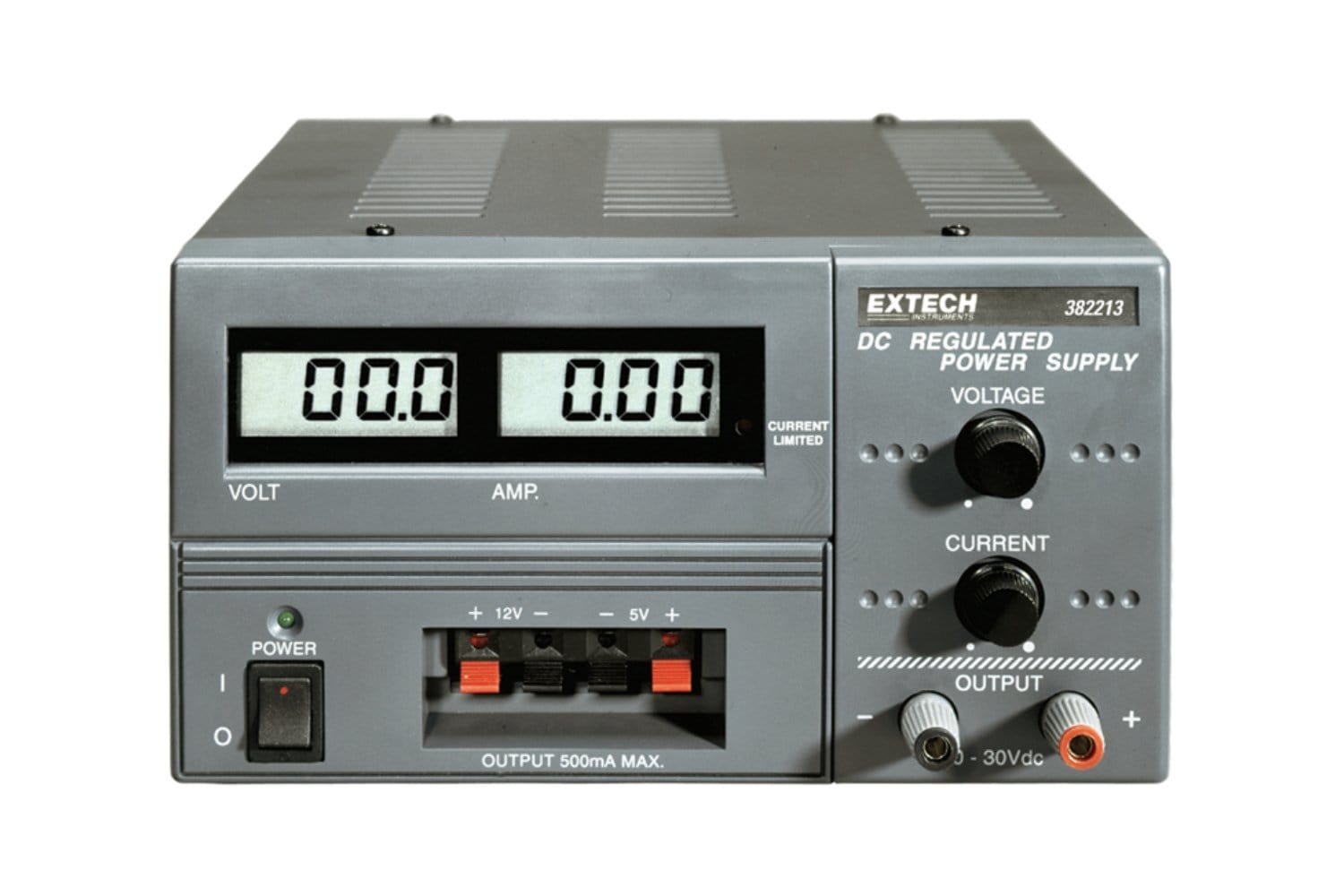
A stock image related to dc output.
The evolution of DC output technology has been closely linked to advancements in electrical engineering and the increasing reliance on electronics across industries. Initially, DC power supplies were primarily used in basic applications, but the demand for more reliable and efficient power sources has driven innovation. Over the past few decades, the introduction of switching power supplies revolutionized the sector by offering compact designs and improved efficiency compared to traditional linear power supplies.
Today, the focus has shifted towards high-performance and programmable DC power supplies that cater to complex applications, including telecommunications, automotive, and renewable energy systems. This evolution highlights the necessity for international B2B buyers to remain adaptive and informed about technological advancements to ensure their sourcing strategies align with the latest market developments.
Frequently Asked Questions (FAQs) for B2B Buyers of dc output
-
How do I solve the issue of inconsistent DC output voltage?
To address inconsistent DC output voltage, first verify the specifications of your power supply. Ensure it meets the requirements of your application, as inadequate power supply ratings can lead to fluctuations. If the supply is suitable, check for potential issues such as loose connections, faulty cables, or damaged components in your circuit. Implementing a voltage regulator may also stabilize the output. For international buyers, sourcing from reputable suppliers with quality assurance processes can mitigate these issues. -
What is the best type of DC power supply for industrial applications?
For industrial applications, a programmable DC power supply is often the best choice. These supplies offer adjustable voltage and current settings, enabling precise control over the output, which is essential for testing and development purposes. Look for features like high efficiency, low noise, and robust thermal management. Suppliers that offer customizable options can provide units tailored to your specific requirements, which is particularly beneficial for businesses operating in diverse environments across regions like Africa and South America. -
How can I vet suppliers for DC output products internationally?
When vetting suppliers for DC output products, conduct thorough research on their reputation and reliability. Look for certifications such as ISO 9001, which indicates adherence to quality management standards. Request references from previous clients and check for reviews or testimonials. Engage in direct communication to assess their responsiveness and customer service. Additionally, consider suppliers that provide detailed product specifications and have a transparent supply chain, which is crucial for international transactions. -
What are the common customization options available for DC power supplies?
Customization options for DC power supplies often include adjustable voltage and current ranges, output connectors, and built-in protection features like over-voltage and over-current protections. Some manufacturers also offer programmable settings, allowing users to create specific output profiles. Additionally, consider options for enhanced thermal management or compact designs suited for space-constrained environments. Engaging with suppliers early in the procurement process can help you identify the best customization options for your operational needs. -
What minimum order quantities (MOQs) should I expect when sourcing DC output products?
Minimum order quantities (MOQs) for DC output products can vary widely depending on the supplier and product type. Typically, you may encounter MOQs ranging from 10 to 100 units for standard products. However, manufacturers may offer flexibility for first-time buyers or bulk orders. It’s advisable to communicate your requirements directly with suppliers to negotiate MOQs that align with your business needs. For international buyers, understanding MOQs can help in planning logistics and inventory management effectively.
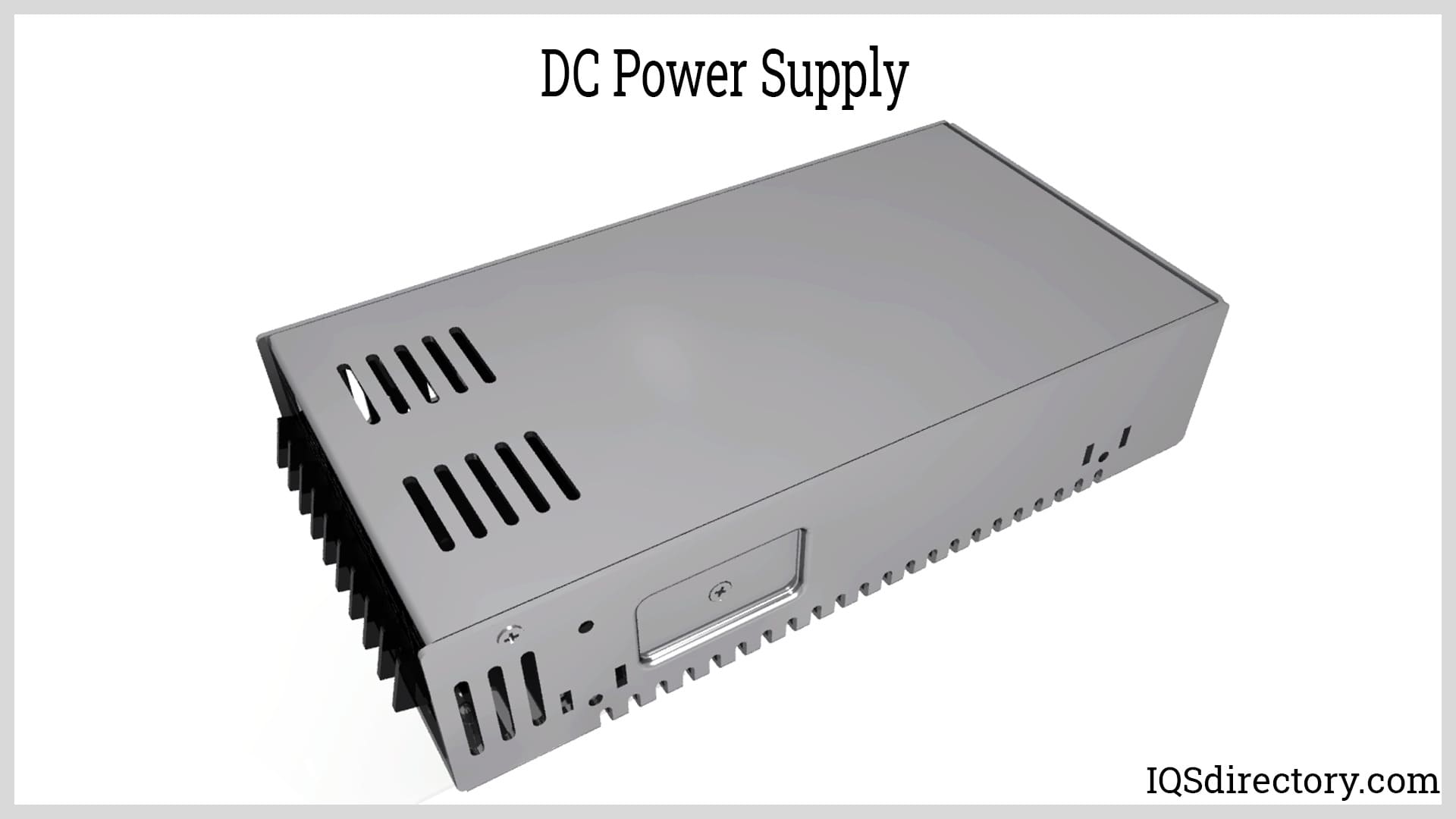
A stock image related to dc output.
-
What payment terms are standard in international B2B transactions for DC output products?
Standard payment terms in international B2B transactions often include options like net 30, net 60, or advance payment, depending on the supplier’s policies and the buyer’s creditworthiness. Many suppliers may request a deposit upfront, especially for large orders or customizations. It’s essential to clarify payment methods accepted, such as wire transfers, credit cards, or letters of credit. Establishing clear payment terms upfront can prevent misunderstandings and ensure smoother transactions across borders. -
How can I ensure quality assurance (QA) when sourcing DC output products?
To ensure quality assurance when sourcing DC output products, request documentation that verifies compliance with international standards like CE, RoHS, or UL certifications. Engage suppliers that conduct rigorous testing on their products, including performance under various loads and environmental conditions. Additionally, consider on-site inspections or third-party audits to evaluate the manufacturing processes. Establishing a clear QA agreement with your supplier can help maintain high standards and build trust in your supply chain. -
What logistics considerations should I keep in mind when importing DC output products?
When importing DC output products, consider factors such as shipping methods, lead times, and customs regulations. Choose a reliable freight forwarder familiar with your destination country’s import procedures to minimize delays. Evaluate the total landed cost, including duties and taxes, to ensure it aligns with your budget. Additionally, ensure that the products are packaged securely to prevent damage during transit. Proactive logistics planning can significantly enhance the efficiency of your supply chain and reduce unexpected costs.
Important Disclaimer & Terms of Use
⚠️ Important Disclaimer
The information provided in this guide, including content regarding manufacturers, technical specifications, and market analysis, is for informational and educational purposes only. It does not constitute professional procurement advice, financial advice, or legal advice.
While we have made every effort to ensure the accuracy and timeliness of the information, we are not responsible for any errors, omissions, or outdated information. Market conditions, company details, and technical standards are subject to change.
B2B buyers must conduct their own independent and thorough due diligence before making any purchasing decisions. This includes contacting suppliers directly, verifying certifications, requesting samples, and seeking professional consultation. The risk of relying on any information in this guide is borne solely by the reader.
Strategic Sourcing Conclusion and Outlook for dc output
What Are the Key Takeaways for International B2B Buyers on DC Output?
In conclusion, understanding the nuances of DC output is critical for international B2B buyers, especially those operating in emerging markets like Africa and South America, as well as established regions such as Europe and the Middle East. A strategic sourcing approach enables buyers to not only identify reliable suppliers but also negotiate favorable terms that align with their specific power supply needs. Key considerations include the compatibility of DC power supplies with existing systems, the importance of quality assurance, and the need for robust after-sales support.
How Can Strategic Sourcing Enhance Your Procurement Process?
Investing in strategic sourcing for DC power supplies can yield significant long-term benefits. It allows businesses to mitigate risks associated with supply chain disruptions while ensuring access to the latest technologies that enhance operational efficiency. By fostering relationships with reputable suppliers, buyers can also stay ahead of market trends and adapt to evolving technological demands.
What’s Next for B2B Buyers in the DC Power Supply Market?
As the demand for reliable DC power continues to grow, now is the time for international buyers to engage proactively with suppliers. By leveraging strategic sourcing, companies can secure competitive pricing and superior products that drive business success. Take the initiative today to evaluate your sourcing strategies and explore new partnerships that will empower your operations in an increasingly electrified future.