Maximize Efficiency: The Complete Lubrication System Guide (2025)
Introduction: Navigating the Global Market for lubrication system
Navigating the global market for lubrication systems can pose significant challenges for international B2B buyers, particularly in regions like Africa, South America, the Middle East, and Europe. With diverse applications ranging from heavy machinery to automotive engines, selecting the right lubrication solution is crucial for optimizing operational efficiency and reducing equipment wear. This guide aims to demystify the complexities of lubrication systems by exploring various types, their applications, and best practices for supplier vetting and cost analysis.
By providing actionable insights into the intricacies of lubrication systems, this comprehensive resource empowers B2B buyers to make informed purchasing decisions. Whether you are sourcing automatic lubrication systems for industrial machinery or specialized greases for extreme conditions, understanding the nuances of lubrication technology is vital. The guide will delve into the essential components, such as metering pumps and hose reels, and offer strategic advice on evaluating suppliers to ensure reliability and quality.
In an ever-evolving global market, having access to this knowledge will not only enhance your procurement strategies but also contribute to the longevity and performance of your equipment. Join us as we equip you with the tools necessary to navigate the lubrication systems market effectively and confidently.
Understanding lubrication system Types and Variations
Type Name | Key Distinguishing Features | Primary B2B Applications | Brief Pros & Cons for Buyers |
---|---|---|---|
Manual Lubrication Systems | Requires human intervention for lubrication | Construction machinery, automotive repair, small equipment | Pros: Lower initial cost, straightforward setup. Cons: Labor-intensive, prone to human error. |
Automatic Lubrication Systems | Delivers lubricant at set intervals without manual input | Heavy machinery, manufacturing plants, conveyor systems | Pros: Reduces downtime, consistent lubrication. Cons: Higher upfront cost, requires maintenance. |
Centralized Lubrication Systems | Integrates multiple lubrication points into one system | Large industrial facilities, fleet maintenance, mining | Pros: Efficient, reduces maintenance time. Cons: Complex installation, higher initial investment. |
Grease Lubrication Systems | Uses grease instead of oil for lubrication | Heavy-duty vehicles, industrial machinery, marine equipment | Pros: Better for high-load applications, longer-lasting. Cons: More difficult to manage in terms of temperature. |
Oil Lubrication Systems | Utilizes oil for lubrication, often in engines | Automotive engines, compressors, turbines | Pros: Easier to distribute, effective cooling. Cons: Requires regular monitoring and replacement. |
What Are the Characteristics of Manual Lubrication Systems?
Manual lubrication systems rely on personnel to apply lubricants to machinery, making them straightforward and cost-effective. They are suitable for smaller equipment or environments where machinery is less complex. However, this method can be labor-intensive and prone to inconsistencies due to human error. Buyers should consider the potential for increased labor costs and downtime when evaluating this option.
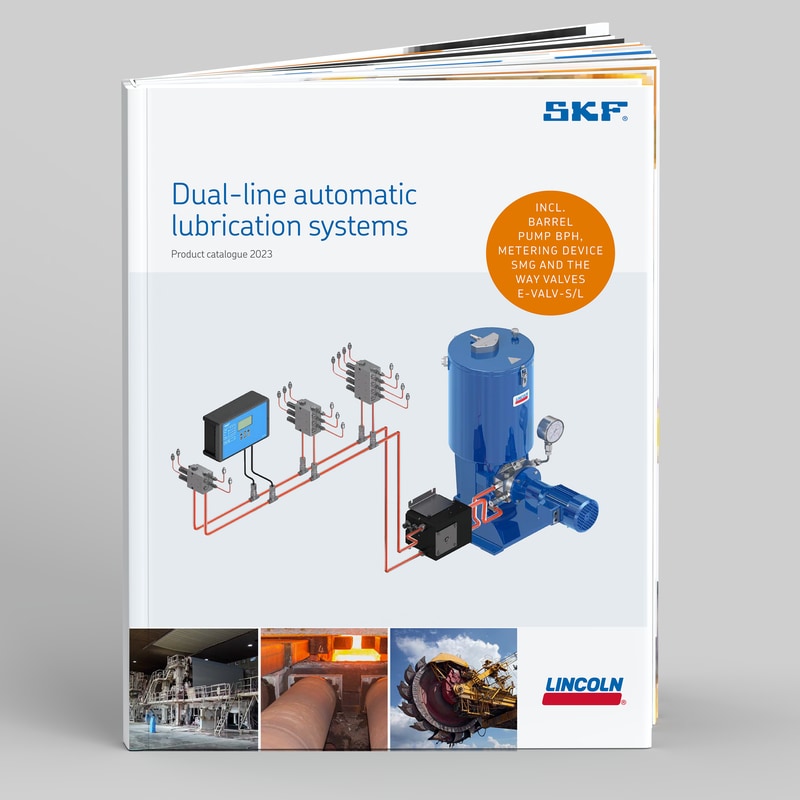
A stock image related to lubrication system.
How Do Automatic Lubrication Systems Improve Efficiency?
Automatic lubrication systems provide a continuous supply of lubricant to machinery at predetermined intervals, reducing the need for manual intervention. These systems are ideal for heavy machinery and industrial applications where consistent lubrication is critical to performance and longevity. The main purchasing considerations include the system’s compatibility with existing machinery and its maintenance requirements, as these systems can have a higher upfront cost.
Why Choose Centralized Lubrication Systems?
Centralized lubrication systems consolidate multiple lubrication points into a single system, enhancing efficiency in large industrial facilities. They are particularly beneficial in environments where machinery operates continuously, such as mining and fleet maintenance. Buyers should evaluate the complexity of installation and the system’s capability to integrate with existing equipment, as these factors can impact long-term operational efficiency.
What Are the Benefits of Grease Lubrication Systems?
Grease lubrication systems employ thicker lubricants, making them ideal for high-load applications such as heavy-duty vehicles and industrial machinery. They provide superior protection against wear and can last longer than oil-based systems. However, buyers must consider the challenges of managing temperature and flow, as grease can become less effective in extreme conditions. Understanding the specific requirements of the application is essential for selecting the right grease type.
How Do Oil Lubrication Systems Function in Automotive Applications?
Oil lubrication systems are commonly found in automotive engines, compressors, and turbines, utilizing oil to reduce friction and heat. They are effective at distributing lubricant uniformly across moving parts and are easier to monitor than grease systems. However, they require regular maintenance and oil changes, which can add to operational costs. Buyers should assess their maintenance capabilities and the specific lubricant requirements for their machinery to ensure optimal performance.
Key Industrial Applications of lubrication system
Industry/Sector | Specific Application of lubrication system | Value/Benefit for the Business | Key Sourcing Considerations for this Application |
---|---|---|---|
Manufacturing | Automatic lubrication systems for machinery | Reduced downtime and maintenance costs | Reliability of components, compatibility with existing systems |
Construction | Lubrication for heavy machinery like excavators | Enhanced equipment lifespan and performance | Availability of local suppliers, ease of installation |
Automotive | Engine lubrication systems | Improved engine efficiency and longevity | Specifications compliance, oil quality standards |
Food Processing | Food-grade lubrication systems for conveyors | Compliance with safety regulations and reduced wear | Certification of lubricants, temperature resistance |
Mining | Lubrication for conveyor belts and crushers | Increased operational efficiency and reduced failure | Durability under harsh conditions, cost-effectiveness |
How Are Automatic Lubrication Systems Used in Manufacturing?
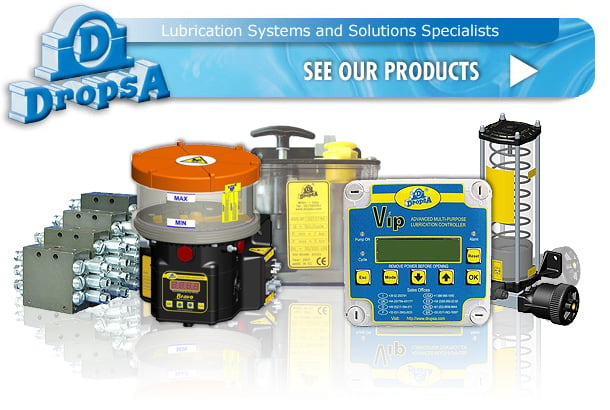
A stock image related to lubrication system.
In the manufacturing sector, automatic lubrication systems are deployed to ensure consistent lubrication of machinery, reducing friction and wear. These systems are crucial for high-speed operations, where manual lubrication may lead to delays and increased downtime. For international buyers, sourcing reliable components that can integrate seamlessly with existing machinery is essential. Factors such as the system’s reliability and the availability of after-sales support should be prioritized to ensure long-term efficiency.
What Role Does Lubrication Play in Heavy Machinery for Construction?
Heavy machinery, such as excavators and bulldozers, requires regular lubrication to maintain optimal performance. Automatic lubrication systems can deliver grease to various pivot points and bearings, enhancing equipment lifespan and reducing the frequency of maintenance. Buyers from regions like Africa and South America must consider local supplier availability and the ease of installation when sourcing these systems, as well as the need for lubricants that can withstand harsh environmental conditions.
How Are Engine Lubrication Systems Essential for the Automotive Industry?
In the automotive sector, engine lubrication systems are vital for maintaining engine efficiency and longevity. These systems circulate oil to lubricate moving parts, reducing friction and preventing wear. International buyers should focus on sourcing high-quality lubricants that meet specific vehicle manufacturer requirements. Additionally, understanding regional oil quality standards and ensuring compliance can help mitigate issues related to engine performance and reliability.
Why Are Food-Grade Lubrication Systems Critical in Food Processing?
Food processing facilities utilize food-grade lubrication systems for equipment like conveyors to ensure safety and compliance with health regulations. These lubricants prevent contamination while minimizing wear on machinery. Buyers should prioritize sourcing lubricants that are certified for food safety and assess their temperature resistance properties, especially in hot processing environments. Choosing suppliers with a strong reputation for quality can help ensure operational safety and efficiency.
How Does Lubrication Impact Mining Equipment Operations?
In the mining industry, lubrication systems are crucial for maintaining the functionality of conveyor belts and crushers. These systems mitigate wear and tear caused by abrasive materials, thus increasing operational efficiency and reducing the likelihood of equipment failure. Buyers in this sector should focus on sourcing durable lubrication systems that can withstand harsh conditions, including dust and moisture. Cost-effectiveness and long-term reliability are also significant considerations for procurement strategies.
3 Common User Pain Points for ‘lubrication system’ & Their Solutions
Scenario 1: Inefficient Lubrication Leads to Machinery Downtime
The Problem:
For many B2B buyers, particularly those in manufacturing and heavy industries, the challenge of maintaining machinery performance is paramount. Inefficient lubrication systems can lead to excessive wear and tear on critical components, resulting in unexpected machinery downtime. This not only disrupts production schedules but also incurs significant costs related to repairs and lost revenue. Buyers may find themselves struggling to manage lubrication intervals manually, which can lead to inconsistencies and human error in maintenance routines.
The Solution:
To combat this issue, consider investing in an automatic lubrication system. These systems are designed to deliver precise amounts of lubricant at set intervals, ensuring that machinery components receive consistent lubrication without the need for manual intervention. When sourcing an automatic lubrication system, assess the specific requirements of your machinery—such as load capacity, operating environment, and the types of lubricants needed. Collaborate with suppliers who can offer tailored solutions, including integration support and ongoing maintenance services. Additionally, implementing a lubrication management software can help track lubricant usage and maintenance schedules, further enhancing operational efficiency.
Scenario 2: Difficulty in Selecting the Right Lubricant
The Problem:
B2B buyers often encounter confusion when selecting the appropriate lubricant for different machinery applications. Factors such as temperature, load conditions, and compatibility with existing lubricants can complicate the decision-making process. This uncertainty can lead to using incorrect lubricants, resulting in equipment failure, increased friction, and costly repairs. Buyers may also face challenges in sourcing high-quality lubricants that meet industry standards, particularly in regions with limited access to specialized suppliers.
The Solution:
To mitigate these challenges, buyers should conduct a comprehensive lubricant compatibility analysis. Begin by reviewing the machinery manufacturer’s specifications, which often provide detailed guidance on the appropriate lubricants for various components. Engage with reputable lubricant manufacturers or distributors who can provide samples and technical data sheets to help assess product suitability. Additionally, consider leveraging the expertise of a lubrication consultant to guide you in selecting the right lubricant based on your specific operating conditions. Establishing relationships with multiple suppliers can also enhance your access to a diverse range of high-quality lubricants, ensuring that you have the right products on hand when needed.
Scenario 3: Manual Lubrication Processes are Time-Consuming and Error-Prone
The Problem:
In many organizations, manual lubrication processes are still prevalent, often resulting in time-consuming maintenance routines. B2B buyers may struggle with the logistical challenges of scheduling lubrication tasks, training personnel, and ensuring that all machinery is adequately lubricated. This manual approach is not only inefficient but also increases the risk of human error, leading to inconsistent lubrication and potential equipment failures.
The Solution:
Transitioning to a centralized lubrication system can significantly streamline the lubrication process. These systems allow multiple machines to be lubricated from a single point, reducing the time and labor required for maintenance. When implementing a centralized lubrication system, assess the layout of your facility to determine the best configuration for piping and access points. Collaborate with a qualified supplier to design a system that meets your specific needs, including the type of lubricant, delivery methods, and maintenance schedules. Additionally, invest in training for your staff to ensure they understand how to operate and maintain the new system effectively. By automating and centralizing lubrication processes, you can improve efficiency, reduce downtime, and enhance the longevity of your machinery.
Strategic Material Selection Guide for lubrication system
What Are the Key Materials Used in Lubrication Systems?
When selecting materials for lubrication systems, international B2B buyers must consider various factors, including performance properties, cost, and application suitability. Below, we analyze four common materials used in lubrication systems: metals, polymers, ceramics, and composite materials.
How Do Metals Perform in Lubrication Systems?
Key Properties: Metals such as steel and aluminum are often used in components like pumps, fittings, and reservoirs due to their high strength and durability. They typically have excellent temperature and pressure ratings, making them suitable for high-performance applications.
Pros & Cons: Metals offer high durability and resistance to wear, but they can be prone to corrosion if not properly treated. The manufacturing complexity can vary; for example, precision components require advanced machining. While metals are generally more expensive than polymers, their longevity can justify the initial investment.
Impact on Application: Metals are compatible with a wide range of lubricants, including oils and greases, but their performance can be affected by the lubricant’s viscosity and chemical composition. Buyers should ensure that the selected metal can withstand the operational conditions of their specific application.
Considerations for International Buyers: Compliance with international standards such as ASTM and DIN is crucial. Buyers in regions like Africa and the Middle East should also consider local environmental conditions that may affect metal performance.
What Role Do Polymers Play in Lubrication Systems?
Key Properties: Polymers, including various types of plastics, are often used for seals, gaskets, and hoses. They exhibit good chemical resistance and can operate effectively at lower temperatures.
Pros & Cons: The primary advantage of polymers is their lightweight nature and resistance to corrosion. However, they may not withstand high temperatures or pressures as effectively as metals. The manufacturing process is generally less complex, leading to lower costs.
Impact on Application: Polymers can be suitable for non-pressurized lubrication systems and applications involving less aggressive media. Buyers must ensure that the selected polymer is compatible with the lubricants used, as some may degrade over time.
Considerations for International Buyers: Buyers should verify compliance with relevant safety and environmental regulations in their regions. In Europe, for instance, REACH compliance is essential for polymers used in industrial applications.
How Do Ceramics Enhance Lubrication Systems?
Key Properties: Ceramics are known for their exceptional hardness and wear resistance, making them ideal for high-load applications. They can operate at elevated temperatures and have excellent corrosion resistance.
Pros & Cons: The main advantage of ceramics is their durability and ability to maintain performance in harsh environments. However, they can be brittle and may require careful handling during installation. The cost of ceramics is generally higher compared to metals and polymers.
Impact on Application: Ceramics are particularly effective in applications where metal fatigue is a concern, such as in high-speed machinery. Their compatibility with various lubricants makes them versatile, but buyers should consider the specific operational conditions.
Considerations for International Buyers: Buyers need to assess the availability of ceramic components in their regions, as supply chains can differ significantly. Compliance with international standards is also essential for ensuring quality and reliability.
What Are the Benefits of Composite Materials in Lubrication Systems?
Key Properties: Composite materials combine the strengths of different materials, offering tailored properties such as improved strength-to-weight ratios and enhanced corrosion resistance.
Pros & Cons: Composites can be engineered for specific applications, making them highly versatile. However, they may come with higher manufacturing costs and complexity. The long-term durability can also vary based on the specific composite formulation.
Impact on Application: Composites can be used in various lubrication system components, including bearings and seals, where traditional materials may fall short. Compatibility with different lubricants is a crucial factor to consider.
Considerations for International Buyers: Understanding the specific composite material properties is vital for ensuring compatibility with local environmental conditions. Buyers should also look for certifications that guarantee the material’s performance under local regulations.
Summary Table of Material Selection for Lubrication Systems
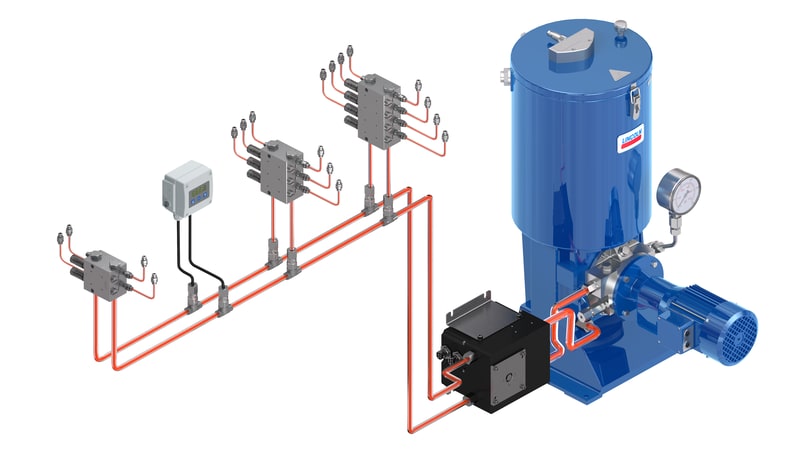
A stock image related to lubrication system.
Material | Typical Use Case for lubrication system | Key Advantage | Key Disadvantage/Limitation | Relative Cost (Low/Med/High) |
---|---|---|---|---|
Metals | Pumps, fittings, reservoirs | High strength and durability | Prone to corrosion without treatment | High |
Polymers | Seals, gaskets, hoses | Lightweight and corrosion-resistant | Limited high-temperature performance | Medium |
Ceramics | High-load applications | Exceptional hardness and wear resistance | Brittle and costly | High |
Composites | Bearings, seals | Tailored properties and versatility | Higher manufacturing complexity | Medium to High |
This strategic material selection guide provides B2B buyers with essential insights to make informed decisions when sourcing lubrication system components, ensuring optimal performance and compliance with relevant standards.
In-depth Look: Manufacturing Processes and Quality Assurance for lubrication system
What Are the Main Stages of Manufacturing Lubrication Systems?
Manufacturing lubrication systems involves several critical stages that ensure the final product meets performance and quality requirements. Understanding these stages helps B2B buyers assess potential suppliers and their capabilities.
Material Preparation: What Raw Materials Are Used?
The first step in the manufacturing process is material preparation, where raw materials such as metals, plastics, and rubber are sourced and prepared. Common materials include:
- Metals: Steel and aluminum are frequently used for components like pumps, tanks, and fittings due to their strength and durability.
- Plastics: Used for housings and seals, these materials are chosen for their resistance to chemicals and temperature variations.
- Greases and Oils: The lubricants themselves are formulated using various additives to enhance performance characteristics, such as viscosity, thermal stability, and pressure resistance.
B2B buyers should inquire about the sourcing of these materials, as quality and consistency are paramount for long-term performance.
How Are Lubrication Systems Formed?
After material preparation, the next stage is forming, which typically involves machining, molding, or extrusion processes. Key techniques include:
- CNC Machining: This technique is essential for creating precise components that fit together perfectly. It reduces tolerances and ensures that parts are made to specifications.
- Injection Molding: Commonly used for plastic components, this process allows for high-volume production and complex shapes.
- Extrusion: This technique is used for producing continuous lengths of material, such as hoses and tubes, which are integral to lubrication systems.
Understanding these forming processes can help buyers determine the manufacturing capabilities and technological sophistication of potential suppliers.
What Assembly Techniques Are Used in Lubrication System Manufacturing?
Once components are formed, the assembly stage begins. This process is crucial for ensuring that all parts function harmoniously. Key assembly techniques include:
- Manual Assembly: Skilled technicians often perform the assembly of intricate systems, ensuring that components are fitted and tested correctly.
- Automated Assembly: For high-volume products, automation can enhance efficiency and consistency, reducing the chance of human error.
- Quality Control During Assembly: Checkpoints are established to ensure that each step meets specifications, allowing for immediate corrective actions if issues arise.
B2B buyers should assess the assembly capabilities of suppliers to ensure they can produce reliable and high-quality lubrication systems.
What Finishing Processes Are Important for Lubrication Systems?
Finishing processes enhance the durability and aesthetic of the lubrication systems. Common techniques include:
- Surface Treatment: Processes like anodizing or powder coating are applied to metal components to improve corrosion resistance and durability.
- Testing and Calibration: Final assembly often includes testing systems under operational conditions to ensure that they meet performance standards. Calibration of metering pumps and flow rates is crucial for precision applications.
B2B buyers should ensure that suppliers have robust finishing processes to guarantee the longevity and reliability of their lubrication systems.
How Is Quality Assurance Implemented in Lubrication System Manufacturing?
Quality assurance (QA) is a critical aspect of manufacturing lubrication systems, ensuring that products meet industry standards and customer specifications.
What International Standards Should B2B Buyers Consider?
International standards such as ISO 9001 are fundamental for ensuring consistent quality management systems. Additionally, industry-specific certifications like API (American Petroleum Institute) and CE (Conformité Européenne) mark products as compliant with relevant regulations and safety requirements.
B2B buyers should prioritize suppliers with these certifications, as they indicate a commitment to quality and reliability.
What Are the Key Quality Control Checkpoints?
Quality control (QC) checkpoints are integral to the manufacturing process and include:
- Incoming Quality Control (IQC): Raw materials are inspected upon receipt to ensure they meet specifications.
- In-Process Quality Control (IPQC): Ongoing inspections during the manufacturing process help identify defects early, minimizing waste and rework.
- Final Quality Control (FQC): The finished product undergoes rigorous testing to ensure it meets all performance and safety standards before shipping.
Understanding these checkpoints allows B2B buyers to evaluate the thoroughness of a supplier’s quality assurance process.
What Testing Methods Are Commonly Used for Lubrication Systems?
Testing methods for lubrication systems are varied, depending on the specific components and their intended applications. Common testing methods include:
- Pressure Testing: Ensures that the system can withstand operational pressures without leaking.
- Flow Rate Testing: Verifies that the system delivers the correct amount of lubricant under various conditions.
- Temperature Resistance Testing: Assesses how well components perform under extreme temperatures, which is critical for certain applications.
B2B buyers should request detailed testing reports to verify that suppliers adhere to these standards.
How Can B2B Buyers Verify Supplier Quality Control?
Verifying a supplier’s quality control measures is essential for B2B buyers, especially those in international markets. Key strategies include:
- Supplier Audits: Conducting regular audits of suppliers can help assess their adherence to quality standards and manufacturing processes.
- Requesting Documentation: Buyers should ask for certificates of compliance, quality assurance reports, and test results to ensure that products meet the required standards.
- Third-Party Inspections: Engaging independent third-party inspectors to evaluate manufacturing practices and product quality can provide an objective assessment.
What Are the Quality Control Nuances for International B2B Buyers?
International B2B buyers should be aware of specific nuances in quality control when sourcing lubrication systems:
- Cultural Differences: Understanding local manufacturing practices and quality expectations can help bridge gaps in communication and expectations.
- Regulatory Compliance: Different regions may have unique regulations regarding manufacturing processes, safety standards, and environmental considerations. Buyers should be well-informed about these requirements to avoid compliance issues.
By leveraging these insights, B2B buyers can make informed decisions when selecting suppliers for lubrication systems, ensuring they receive high-quality products that meet their operational needs.
Practical Sourcing Guide: A Step-by-Step Checklist for ‘lubrication system’
In this section, we will provide a comprehensive checklist for B2B buyers seeking to procure lubrication systems. This guide is tailored to international buyers, particularly from Africa, South America, the Middle East, and Europe, ensuring a streamlined process that aligns with regional needs and standards.
Step 1: Define Your Technical Specifications
Establishing clear technical specifications is crucial for ensuring the lubrication system meets your operational needs. Consider the types of machinery or vehicles that require lubrication, the environmental conditions they operate in, and the types of lubricants needed (oil, grease, etc.). This will help you communicate effectively with suppliers and avoid costly misalignments.
Step 2: Assess Application Requirements
Understanding the specific applications of the lubrication system is vital. Different industries such as automotive, manufacturing, and heavy machinery may have unique requirements. Identify if you need automatic lubrication systems or manual options, and ensure that the chosen system can handle the load and environmental factors specific to your operations.
Step 3: Evaluate Potential Suppliers
Before committing, it’s crucial to vet suppliers thoroughly. Request detailed company profiles, case studies, and references from buyers in similar industries or regions. Look for suppliers with experience in your specific application and those who can provide evidence of successful installations.
- Key Considerations:
- Review their customer feedback and ratings.
- Ensure they have experience in your geographical market.
Step 4: Verify Supplier Certifications and Compliance
Ensure that the suppliers you consider are compliant with international standards and certifications relevant to lubrication systems. This includes ISO certifications, safety standards, and environmental regulations. Compliance not only assures quality but also minimizes risks associated with legal liabilities.
Step 5: Request Detailed Proposals and Quotations
Once you have shortlisted suppliers, request detailed proposals that outline their offerings, including technical specifications, pricing, delivery timelines, and warranty terms. A comprehensive proposal allows for better comparison and helps you make an informed decision.
- What to Compare:
- Total cost of ownership (including installation and maintenance).
- Warranty and support services offered.
Step 6: Conduct Site Visits or Virtual Tours
If possible, conduct site visits to the supplier’s facilities or request virtual tours. This gives you insight into their manufacturing processes and quality control measures. Observing their operations can also enhance your confidence in their ability to deliver a reliable lubrication system.
Step 7: Negotiate Terms and Finalize the Contract
Once you’ve selected a supplier, engage in negotiations to finalize the terms of the contract. Be clear about your expectations regarding delivery, installation, maintenance, and support. Ensure that all agreements are documented to protect both parties.
By following this checklist, B2B buyers can effectively navigate the procurement process for lubrication systems, ensuring they select the right solution tailored to their specific operational needs.
Comprehensive Cost and Pricing Analysis for lubrication system Sourcing
What Are the Key Cost Components in Lubrication System Sourcing?
When sourcing lubrication systems, understanding the cost structure is essential for international B2B buyers. The primary cost components include:
-
Materials: The type of lubricant, whether oil or grease, significantly impacts costs. Specialty lubricants designed for extreme conditions or high-temperature applications tend to be more expensive. Additionally, the quality and source of raw materials can vary, affecting pricing.
-
Labor: Labor costs encompass not only the workforce needed for manufacturing but also installation and maintenance. In regions with higher labor costs, such as parts of Europe, this can significantly impact the overall cost.
-
Manufacturing Overhead: This includes expenses related to utilities, equipment depreciation, and factory management. Efficient manufacturing processes can help reduce overhead, which in turn lowers the overall price for buyers.
-
Tooling: The initial investment in tools and machinery can be substantial, particularly for custom lubrication systems. Buyers should consider the tooling costs when evaluating suppliers, especially for bespoke solutions.
-
Quality Control (QC): Ensuring that lubrication systems meet industry standards requires rigorous testing and quality assurance processes. These QC measures can add to the cost but are crucial for preventing failures in demanding applications.
-
Logistics: Shipping costs can vary dramatically based on distance, mode of transport, and any import/export tariffs. International buyers must factor in logistics, especially when sourcing from regions with complex customs regulations.
-
Margin: Supplier profit margins can vary based on market demand and competition. Understanding the typical margins within your specific industry can aid in negotiations.
How Do Price Influencers Affect Lubrication System Costs?
Several factors can influence the pricing of lubrication systems significantly:
-
Volume/MOQ (Minimum Order Quantity): Larger orders often lead to lower per-unit costs. Buyers should negotiate MOQs that align with their operational needs to optimize pricing.
-
Specifications and Customization: Custom-designed lubrication systems will generally incur higher costs due to the additional engineering and production requirements. Buyers should clearly define their specifications upfront to avoid unexpected costs.
-
Materials: The choice of lubricant materials (synthetic vs. conventional) and the use of additional components (like automated systems) can affect pricing. High-performance materials may command premium prices but can lead to cost savings through enhanced performance and longevity.
-
Quality and Certifications: Systems that meet specific industry certifications (ISO, API, etc.) often come at a premium but ensure compliance and reliability. Buyers should assess the value of these certifications in relation to their operational requirements.
-
Supplier Factors: The reputation and reliability of the supplier can also affect pricing. Established suppliers may charge more due to brand trust but often provide better service and support.
-
Incoterms: The choice of Incoterms (International Commercial Terms) can significantly impact the total landed cost of lubrication systems. Buyers should negotiate terms that minimize risks and costs associated with shipping and customs.
What Are Effective Buyer Tips for Cost-Efficiency in Lubrication Systems?
To maximize cost-efficiency when sourcing lubrication systems, international B2B buyers should consider the following strategies:
-
Negotiate: Always engage in negotiations with suppliers. Leverage factors such as order volume, payment terms, and long-term partnerships to obtain better pricing.
-
Evaluate Total Cost of Ownership (TCO): Instead of focusing solely on the initial purchase price, consider the TCO, which includes maintenance, operational efficiency, and potential downtime costs. A higher upfront investment may yield lower operational costs over time.
-
Understand Pricing Nuances: Be aware of regional pricing dynamics. Buyers from Africa, South America, the Middle East, and Europe should consider local market conditions, currency fluctuations, and logistics costs when evaluating offers from suppliers across different regions.
-
Request Indicative Prices: Given the variability in costs based on customization and specifications, requesting indicative pricing from multiple suppliers can provide a benchmark for negotiations. Always clarify that prices are subject to change based on final specifications.
By adopting these insights and strategies, international B2B buyers can make informed decisions when sourcing lubrication systems, ensuring they achieve both quality and value.
Alternatives Analysis: Comparing lubrication system With Other Solutions
Exploring Alternatives to Traditional Lubrication Systems
When considering maintenance solutions for machinery and equipment, lubrication systems often stand out as the primary choice. However, various alternatives may offer unique advantages depending on the specific needs of your operations. This section delves into the comparison of lubrication systems against two alternative solutions: Grease Gun Systems and Self-Lubricating Bearings. By evaluating these options, international B2B buyers can make informed decisions tailored to their operational requirements.
Comparison Table
Comparison Aspect | Lubrication System | Grease Gun System | Self-Lubricating Bearings |
---|---|---|---|
Performance | High efficiency and reliability; suitable for complex machinery | Effective for localized lubrication; manual application needed | Minimal maintenance; continuous lubrication without external sources |
Cost | Higher initial investment; lower long-term costs due to efficiency | Lower upfront cost; requires regular manual effort | Moderate cost; longer lifespan reduces replacement frequency |
Ease of Implementation | Installation complexity; requires setup of pumps and lines | Simple to use; can be implemented in various settings | Easy installation; integrates into existing systems without modification |
Maintenance | Requires regular checks and system maintenance | Regular refilling necessary; less maintenance than full systems | Very low maintenance; designed for long-term use |
Best Use Case | Heavy industrial applications; large machinery with multiple lubrication points | Smaller machinery; less critical lubrication points | Applications where maintenance access is challenging or downtime needs to be minimized |
Detailed Breakdown of Alternatives
What Are the Advantages and Disadvantages of Grease Gun Systems?
Grease gun systems are manual tools designed to apply grease to machinery, ideal for smaller or less critical lubrication needs. Their primary advantage lies in their low cost and straightforward operation. However, they require frequent manual intervention, which can lead to inconsistent lubrication if not managed properly. This may result in increased wear and tear on machinery over time, especially in high-demand environments.
How Do Self-Lubricating Bearings Enhance Machinery Longevity?
Self-lubricating bearings are engineered to provide continuous lubrication without the need for external systems. They are particularly beneficial in applications where maintenance access is limited or where downtime must be minimized. The primary advantage is their ability to reduce friction and wear over time, thus extending the lifespan of machinery components. However, their initial cost can be higher compared to traditional bearings, and they may not be suitable for all applications, particularly those requiring high load capacities.
Conclusion: How Can B2B Buyers Choose the Right Solution for Their Needs?
When selecting the appropriate lubrication solution, B2B buyers must consider several factors, including the specific operational requirements, budget constraints, and maintenance capabilities. For high-demand industrial settings with complex machinery, a traditional lubrication system may provide the best long-term investment despite its higher upfront costs. Conversely, for smaller machinery or environments with limited access, grease gun systems or self-lubricating bearings could offer practical, cost-effective alternatives. Ultimately, understanding the unique needs of your operations will guide you to the most effective lubrication strategy.
Essential Technical Properties and Trade Terminology for lubrication system
What Are the Key Technical Properties of Lubrication Systems?
In the realm of lubrication systems, understanding essential technical properties is vital for making informed purchasing decisions. Here are some critical specifications that B2B buyers should consider:
1. Viscosity Grade
Viscosity refers to a fluid’s resistance to flow. It is a critical property as it affects the lubricant’s ability to create a film between moving parts. The viscosity grade, often indicated by SAE (Society of Automotive Engineers) numbers, dictates how well the lubricant will perform under varying temperature conditions. For instance, a lubricant with a lower viscosity will flow more easily in cold conditions, while a higher viscosity is preferred for high-temperature operations. Selecting the correct viscosity is crucial for maximizing equipment efficiency and longevity.
2. Operating Temperature Range
Each lubricant has a specified temperature range within which it can perform optimally. Exceeding this range can lead to lubricant breakdown and equipment failure. Understanding the operating temperature range is essential for ensuring that the lubrication system can withstand the conditions it will face in specific environments, particularly in regions with extreme temperatures, such as the Middle East or Southern Africa.
3. Additive Package
Lubricants often contain additives that enhance their performance. These may include anti-wear agents, antioxidants, and detergents. The choice of additives can significantly impact the lubricant’s effectiveness in preventing corrosion, reducing friction, and maintaining cleanliness within the system. Buyers should assess the additive package to ensure it aligns with their operational requirements and environmental standards.
4. Base Oil Type
The base oil is the primary component of any lubricant, and its type can influence performance characteristics. Common types include mineral oils, synthetic oils, and bio-based oils. Synthetic oils, for instance, provide superior thermal stability and lower volatility, making them ideal for high-performance applications. Understanding the base oil type helps buyers choose lubricants that best suit their machinery and operational conditions.
5. NLGI Grade
The National Lubricating Grease Institute (NLGI) grade indicates the consistency of grease. This specification is crucial when selecting lubricants for applications where grease must remain in place, such as bearings and gears. A higher NLGI grade means thicker grease, which can be beneficial in high-load applications. Buyers need to match the NLGI grade with their equipment requirements to ensure proper lubrication.
What Are the Common Trade Terms in the Lubrication Industry?
Familiarity with industry jargon is essential for effective communication and negotiation in the lubrication systems market. Here are several common terms:
1. OEM (Original Equipment Manufacturer)
An OEM refers to a company that produces parts or equipment that may be marketed by another manufacturer. In lubrication systems, understanding OEM specifications ensures compatibility and performance standards are met. Buyers should inquire about OEM certifications when selecting lubricants for specific machinery.
2. MOQ (Minimum Order Quantity)
MOQ represents the smallest quantity of a product that a supplier is willing to sell. For international buyers, understanding MOQ is critical for managing inventory costs and ensuring that they can meet their operational needs without overcommitting financially.
3. RFQ (Request for Quotation)
An RFQ is a document sent to suppliers requesting a price quote for specific products or services. This process is vital for B2B buyers to compare pricing, availability, and terms from multiple suppliers, helping them make informed purchasing decisions.
4. Incoterms (International Commercial Terms)
Incoterms are standardized trade terms that define the responsibilities of buyers and sellers in international transactions. They clarify who is responsible for shipping, insurance, and tariffs. Familiarity with Incoterms is essential for international buyers to avoid misunderstandings and ensure smooth logistics.
5. TCO (Total Cost of Ownership)
TCO is a financial estimate designed to help buyers understand the direct and indirect costs of a product or service over its entire lifecycle. In lubrication systems, TCO considers the costs of purchasing, operating, and maintaining the lubrication solution, allowing for a comprehensive assessment of value.
By grasping these technical properties and trade terms, international B2B buyers can enhance their decision-making processes, ensuring they select the most suitable lubrication systems for their operational needs.
Navigating Market Dynamics and Sourcing Trends in the lubrication system Sector
What are the Current Market Dynamics and Key Trends in the Lubrication System Sector?
The lubrication system sector is experiencing transformative changes driven by technological advancements and shifting market demands. Global trends indicate a growing emphasis on automation and smart technologies, allowing for enhanced efficiency in lubrication processes. International B2B buyers, particularly from Africa, South America, the Middle East, and Europe, should be aware of the increasing adoption of automatic lubrication systems. These systems reduce manual labor, minimize downtime, and ensure consistent lubrication, which is crucial for maintaining machinery longevity.
Emerging technologies, such as IoT (Internet of Things) integration, are also reshaping the landscape. Connected lubrication systems enable real-time monitoring of lubricant levels and performance, allowing for predictive maintenance and reducing the risk of equipment failure. This trend is particularly relevant for industries like manufacturing, automotive, and construction, where operational efficiency is paramount.
Furthermore, the global push for sustainability is influencing sourcing trends. Buyers are increasingly prioritizing suppliers who offer environmentally friendly lubricants and systems. This shift is not only regulatory-driven but also stems from the growing awareness of corporate responsibility among businesses in Africa, South America, the Middle East, and Europe. Understanding these dynamics can help international buyers make informed decisions that align with their operational goals and sustainability commitments.
How Can Sustainability and Ethical Sourcing Impact the Lubrication System Sector?
Sustainability is becoming a crucial factor in the lubrication system sector, with environmental impacts prompting significant changes in sourcing practices. The production and disposal of traditional lubricants can pose environmental challenges, leading to increased scrutiny from regulatory bodies and consumers alike. Thus, international B2B buyers must consider sourcing lubricants that comply with stringent environmental regulations while also minimizing their ecological footprint.
Ethical sourcing is equally important. Buyers should prioritize suppliers who demonstrate a commitment to sustainable practices, such as using renewable resources or biodegradable materials in their lubricants. Certifications like ISO 14001 or eco-labels can serve as indicators of a supplier’s environmental management practices. In regions like the Middle East and Europe, where regulatory frameworks are becoming more stringent, such certifications can provide a competitive edge.
Moreover, the demand for ‘green’ lubricants—those formulated with environmentally friendly materials—continues to rise. These products not only reduce environmental impact but also appeal to a growing segment of environmentally conscious consumers. By integrating sustainability and ethical sourcing into their procurement strategies, international buyers can contribute to a more responsible supply chain while enhancing their brand reputation.
What is the Brief Evolution and History of Lubrication Systems?
The evolution of lubrication systems dates back to ancient civilizations, where natural oils and fats were employed to reduce friction in simple machines. As industrialization progressed in the 18th and 19th centuries, the need for more effective lubrication systems became apparent. The introduction of steam engines and heavy machinery necessitated advancements in lubrication technology, leading to the development of grease and oil-based lubricants.
By the mid-20th century, automatic lubrication systems emerged, revolutionizing the way machinery was maintained. These systems allowed for continuous lubrication without the need for manual intervention, significantly improving efficiency and equipment lifespan. Today, the sector is characterized by a diverse range of lubrication solutions, including advanced automatic systems and eco-friendly lubricants, reflecting the ongoing commitment to innovation and sustainability in industrial practices.
As the lubrication system sector continues to evolve, international B2B buyers must stay informed about historical trends and current advancements to make strategic purchasing decisions that align with their operational needs and sustainability goals.
Frequently Asked Questions (FAQs) for B2B Buyers of lubrication system
-
How do I solve lubrication system failures in heavy machinery?
To address lubrication system failures in heavy machinery, start by conducting a thorough inspection of the system. Check for leaks, blockages, and worn-out components like hoses and pumps. Regular maintenance, including timely oil changes and filter replacements, is crucial. Implement an automatic lubrication system to ensure consistent delivery of lubricants to critical points, reducing human error and improving machinery longevity. Additionally, consider using high-quality lubricants suitable for specific operating conditions to enhance performance. -
What is the best lubrication system for industrial applications?
The best lubrication system for industrial applications largely depends on the specific machinery and operational requirements. Automatic lubrication systems, such as centralized systems that deliver grease or oil to multiple points, are often ideal for large-scale operations. They minimize downtime and maintenance efforts. For high-temperature environments, opt for specialized lubricants designed to withstand extreme conditions. Evaluate your machinery’s load requirements and operating environment to select the most effective system. -
How can I vet suppliers for lubrication systems in international trade?
When vetting suppliers for lubrication systems in international trade, start by researching their reputation and experience in the industry. Look for certifications and compliance with international standards. Request references from previous clients and evaluate their feedback. It’s also wise to assess their manufacturing capabilities and quality control processes. Conducting a site visit or virtual audit can provide insight into their operations and reliability. Finally, consider their financial stability and ability to meet your specific needs in terms of customization and support. -
What customization options are available for lubrication systems?
Many suppliers offer customization options for lubrication systems to meet specific operational needs. This can include adjustments in the size and type of reservoirs, pump configurations, and the type of lubricant used. Additionally, you can customize the system’s control mechanisms, such as timers for automatic lubrication cycles. Discuss your requirements with potential suppliers to explore available customization options that align with your operational goals and machinery specifications. -
What are the minimum order quantities (MOQ) for lubrication systems?
Minimum order quantities (MOQ) for lubrication systems can vary significantly between suppliers. Some manufacturers may have low MOQs, allowing you to test products with minimal investment, while others might require larger orders to ensure cost-effectiveness. It’s essential to clarify MOQs upfront during negotiations and consider your budget and storage capabilities. If you’re a smaller buyer, look for suppliers who offer flexible purchasing options or explore group buying opportunities with other businesses. -
What payment terms should I expect when sourcing lubrication systems internationally?
Payment terms for international purchases of lubrication systems can vary widely among suppliers. Common arrangements include advance payments, payment upon shipment, or net payment terms (e.g., net 30 or net 60). It’s crucial to discuss payment terms early in negotiations to avoid misunderstandings. Additionally, consider using secure payment methods such as letters of credit or escrow services to protect your investment. Ensure that the terms align with your cash flow requirements and risk tolerance. -
How do I ensure quality assurance for lubrication systems?
To ensure quality assurance for lubrication systems, request detailed specifications and testing certifications from your suppliers. Many reputable manufacturers adhere to ISO standards and other quality management systems. Conduct thorough inspections upon receipt of the products and implement regular maintenance checks to ensure optimal performance. Additionally, consider establishing a quality assurance agreement that outlines expectations and responsibilities for both parties to maintain high standards throughout the product lifecycle. -
What logistical considerations should I keep in mind when importing lubrication systems?
When importing lubrication systems, consider logistics factors such as shipping methods, customs regulations, and delivery timelines. Choose reliable shipping partners with experience in handling industrial equipment. Understand the import duties and taxes applicable in your region to avoid unexpected costs. It’s also essential to have a clear plan for storage and installation upon arrival. Communicate with your supplier to coordinate shipping schedules and ensure that all documentation is in order for a smooth customs clearance process.
Important Disclaimer & Terms of Use
⚠️ Important Disclaimer
The information provided in this guide, including content regarding manufacturers, technical specifications, and market analysis, is for informational and educational purposes only. It does not constitute professional procurement advice, financial advice, or legal advice.
While we have made every effort to ensure the accuracy and timeliness of the information, we are not responsible for any errors, omissions, or outdated information. Market conditions, company details, and technical standards are subject to change.
B2B buyers must conduct their own independent and thorough due diligence before making any purchasing decisions. This includes contacting suppliers directly, verifying certifications, requesting samples, and seeking professional consultation. The risk of relying on any information in this guide is borne solely by the reader.
Strategic Sourcing Conclusion and Outlook for lubrication system
What Are the Key Takeaways for International B2B Buyers in Lubrication Systems?
In conclusion, strategic sourcing of lubrication systems is crucial for international B2B buyers, particularly those operating in diverse markets such as Africa, South America, the Middle East, and Europe. A well-implemented lubrication system not only enhances equipment longevity but also significantly reduces maintenance costs and operational downtime. By selecting the right lubrication solutions tailored to specific applications—be it automatic systems for heavy machinery or specialized greases for extreme conditions—companies can optimize their operational efficiency and reliability.
How Can Buyers Leverage Strategic Sourcing for Competitive Advantage?
Investing in high-quality lubricants and efficient lubrication systems can yield substantial returns. Buyers should prioritize partnerships with reputable suppliers who offer comprehensive support and expertise in lubrication technology. This collaboration ensures access to the latest innovations and best practices in lubrication management, enabling companies to stay ahead in a competitive landscape.
What Does the Future Hold for Lubrication Systems in Global Markets?
Looking ahead, the lubrication industry is poised for growth driven by advancements in technology and an increasing emphasis on sustainability. Buyers should remain vigilant about emerging trends, such as the integration of IoT for predictive maintenance and the adoption of eco-friendly lubricants. By embracing these innovations, international B2B buyers can enhance their operational capabilities and contribute to a more sustainable future.
Engage with your suppliers today to assess how you can enhance your lubrication strategies and ensure your operations remain efficient and competitive in the evolving global market.