Maximize Efficiency: The Ultimate DC Motor Sourcing Guide (2025)
Introduction: Navigating the Global Market for dc motor
In today’s global market, sourcing high-quality DC motors presents a unique challenge for international B2B buyers, particularly those in Africa, South America, the Middle East, and Europe. With a multitude of options available, finding the right supplier who offers reliable products at competitive prices can be daunting. This comprehensive guide demystifies the complexities of the DC motor market, covering essential topics such as types of DC motors, their applications across various industries, and effective supplier vetting strategies.
As you navigate through this guide, you will gain insights into the diverse applications of DC motors, from agricultural equipment and warehouse automation to portable medical devices and renewable energy solutions. Understanding the specifications, such as voltage ratings and torque capabilities, will empower you to make informed decisions tailored to your operational needs. Additionally, we delve into the cost factors associated with purchasing DC motors, enabling you to establish budget expectations and negotiate better deals.
This guide serves as an essential resource for international B2B buyers, equipping you with the knowledge to confidently select DC motors that align with your business requirements. By leveraging the insights provided, you can streamline your sourcing process, ensure product quality, and ultimately enhance your competitive edge in the global market.
Understanding dc motor Types and Variations
Type Name | Key Distinguishing Features | Primary B2B Applications | Brief Pros & Cons for Buyers |
---|---|---|---|
Permanent Magnet DC Motor (PMDC) | High efficiency, compact size, and high starting torque | Agricultural equipment, warehouse automation | Pros: Cost-effective, reliable performance. Cons: Limited to specific speed controls. |
Series DC Motor | High starting torque, speed varies with load | Electric vehicles, cranes, and hoists | Pros: Simple design, excellent for heavy loads. Cons: Poor speed regulation under varying loads. |
Shunt DC Motor | Constant speed, independent of load variations | Industrial machinery, conveyors | Pros: Good speed regulation, versatile. Cons: More complex design, higher maintenance. |
Compound DC Motor | Combines series and shunt features for better performance | Elevators, winches, and heavy-duty machinery | Pros: High torque and speed control. Cons: Higher initial cost and complexity. |
Brushless DC Motor (BLDC) | No brushes, higher efficiency, and longer lifespan | Robotics, HVAC systems, and electric bikes | Pros: Reduced maintenance, high efficiency. Cons: Higher cost and requires specialized controls. |
What are the Characteristics of Permanent Magnet DC Motors (PMDC)?
Permanent Magnet DC Motors (PMDC) are known for their compact design and high efficiency. They utilize permanent magnets to create a magnetic field, allowing for a simpler construction compared to other DC motors. PMDC motors are particularly suited for applications requiring high starting torque and adjustable speed, making them ideal for agricultural equipment and warehouse automation. When purchasing PMDC motors, buyers should consider voltage ratings, torque requirements, and compatibility with speed control systems to ensure optimal performance in their specific applications.
How Do Series DC Motors Perform in Different Applications?
Series DC Motors are characterized by their ability to deliver high starting torque, which makes them suitable for applications like electric vehicles and cranes. Their speed varies with the load, providing a robust solution for heavy-duty tasks. However, this can be a double-edged sword; while they excel under heavy loads, they struggle with speed regulation when the load changes. B2B buyers should assess the load characteristics and operational demands of their applications to determine if a series motor is the right choice.
What Makes Shunt DC Motors a Versatile Choice for Industries?
Shunt DC Motors offer constant speed operation, which is largely independent of load variations, making them a versatile choice for industrial machinery and conveyor systems. This type of motor is designed for applications where consistent speed is critical. While they provide good speed regulation, shunt motors are more complex and may require higher maintenance. Buyers should weigh the benefits of speed stability against the potential for increased upkeep when considering shunt motors for their operations.
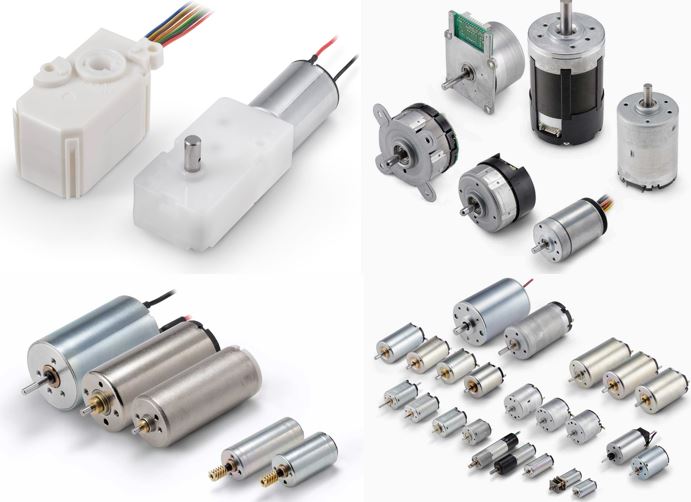
A stock image related to dc motor.
Why Choose Compound DC Motors for Heavy-Duty Applications?
Compound DC Motors combine the features of both series and shunt motors, providing excellent torque and speed control. They are particularly effective in applications such as elevators, winches, and other heavy-duty machinery where both high torque and speed regulation are necessary. However, their complexity and higher initial costs may deter some buyers. It is essential for B2B purchasers to analyze their specific needs and operational budgets when evaluating compound motors.
What are the Advantages of Brushless DC Motors (BLDC)?
Brushless DC Motors (BLDC) are recognized for their high efficiency and longevity due to the absence of brushes, which reduces wear and tear. These motors are commonly used in robotics, HVAC systems, and electric bikes. While they may come with a higher upfront cost and require specialized controls, the reduced maintenance needs and enhanced performance can justify the investment. B2B buyers should consider their application requirements and long-term operational costs when looking into BLDC motors.
Key Industrial Applications of dc motor
Industry/Sector | Specific Application of dc motor | Value/Benefit for the Business | Key Sourcing Considerations for this Application |
---|---|---|---|
Agriculture | Automated Irrigation Systems | Enhances efficiency and precision in water usage, reducing costs. | Look for motors with low voltage options suitable for solar power. |
Warehouse Automation | Automated Guided Vehicles (AGVs) | Improves operational efficiency and reduces labor costs. | Ensure motors support adjustable speed and high starting torque. |
Medical Equipment | Portable Medical Devices | Provides reliable and quiet operation for sensitive applications. | Select motors with compact designs and low-voltage capabilities. |
Manufacturing | Conveyor Systems | Increases production speed and reliability in material handling. | Choose motors with continuous duty ratings for heavy workloads. |
Renewable Energy | Solar Tracking Systems | Maximizes energy capture by adjusting panel angles. | Sourcing should focus on durability and compatibility with solar setups. |
How Are DC Motors Used in Agriculture for Automated Irrigation Systems?
In agriculture, DC motors are integral to automated irrigation systems, providing precise control over water delivery. These motors enable farmers to optimize water usage, which is crucial in regions facing water scarcity. By sourcing low-voltage PMDC motors, particularly those compatible with solar power, agricultural buyers can ensure sustainability and efficiency in their operations. High starting torque and adjustable speed features are essential for adapting to varying field conditions.
What Role Do DC Motors Play in Warehouse Automation with Automated Guided Vehicles (AGVs)?
DC motors are vital in the operation of Automated Guided Vehicles (AGVs) within warehouse settings. They power the movement of these vehicles, which transport goods efficiently throughout the facility. The ability to adjust speed and torque allows AGVs to navigate complex layouts and handle different load sizes. For international buyers, sourcing motors that provide high reliability and efficiency can significantly lower operational costs while enhancing productivity.
How Are DC Motors Utilized in Portable Medical Devices?
In the medical sector, DC motors are used in portable medical devices, such as ventilators and infusion pumps. These motors are favored for their quiet operation and compact size, which are critical in sensitive healthcare environments. Buyers should prioritize sourcing motors that offer low-voltage options and high efficiency to ensure the safety and reliability of medical devices. Additionally, compatibility with various power sources, including batteries, is a key consideration.
What Benefits Do DC Motors Provide in Manufacturing Conveyor Systems?
DC motors are commonly employed in conveyor systems within manufacturing environments, where they facilitate the continuous movement of materials. By utilizing DC motors with high torque and continuous duty ratings, manufacturers can enhance production efficiency and reliability. Buyers should consider the specific torque and speed requirements of their application to ensure optimal performance. Additionally, sourcing motors that are easy to integrate with existing systems can streamline operations.
How Do DC Motors Enhance Renewable Energy Solutions in Solar Tracking Systems?
In renewable energy applications, particularly solar tracking systems, DC motors play a crucial role by adjusting the angle of solar panels to maximize sunlight exposure. This capability significantly increases energy capture and efficiency. Buyers interested in this application should focus on sourcing durable DC motors that can withstand outdoor conditions and are compatible with solar energy systems. Ensuring that the motors have robust performance metrics is essential for long-term reliability in energy generation.
3 Common User Pain Points for ‘dc motor’ & Their Solutions
Scenario 1: Sourcing Reliable DC Motors for Harsh Environments
The Problem: Many B2B buyers operating in sectors such as agriculture, mining, or renewable energy face the challenge of sourcing DC motors that can withstand harsh environmental conditions. These motors often encounter dust, moisture, and extreme temperatures, which can lead to premature failure and increased maintenance costs. Buyers are concerned about selecting the right motor that not only performs reliably but also adheres to local regulations and standards, especially when sourcing from international suppliers.
The Solution: To overcome this challenge, buyers should prioritize the selection of DC motors that are specifically designed for rugged applications. Look for motors with high ingress protection (IP) ratings, such as IP65 or higher, which indicate resistance to dust and water. Additionally, consider sourcing from manufacturers that provide detailed specifications regarding temperature ranges and environmental compatibility. It is also advisable to work with suppliers who offer robust customer support and warranty options, ensuring that any issues can be addressed promptly. Conducting thorough research on suppliers, including reviews and case studies from similar industries, can help mitigate risks associated with international sourcing.
Scenario 2: Managing Power Supply Variability in DC Motor Applications
The Problem: In regions with inconsistent power supply, such as some parts of Africa and South America, B2B buyers often struggle with the performance of DC motors due to voltage fluctuations and power quality issues. These inconsistencies can lead to motor overheating, reduced lifespan, and operational inefficiencies, which can be costly for businesses relying on continuous operation.
The Solution: Buyers should invest in DC motors that come with built-in voltage regulation features or those that can be paired with reliable DC power supply solutions, such as battery management systems or DC-DC converters. Sourcing motors that have a wide operating voltage range (e.g., 12V to 180V) will provide more flexibility in varying conditions. Additionally, implementing surge protection devices and voltage stabilizers can help safeguard the motors from power spikes and dips. Collaborating with local electrical engineers to design a robust power management system tailored to the specific operational environment can further enhance performance and reliability.
Scenario 3: Customization Needs for Specific Applications
The Problem: Many businesses require DC motors tailored to specific applications, such as automated machinery or robotics, but often find that off-the-shelf products do not meet their unique requirements. This can lead to inefficiencies and delays in production if the motors do not integrate well with existing systems or fail to deliver the necessary torque and speed.
The Solution: To address this customization challenge, buyers should engage with manufacturers that offer bespoke solutions for DC motors. Providing detailed specifications about the required performance characteristics—such as torque, speed, and duty cycle—can facilitate the development of a motor that fits seamlessly into the intended application. Additionally, consider suppliers who are willing to work collaboratively during the design phase, allowing for adjustments based on testing results. Exploring options such as gear motors or incorporating features like encoders for precise control can also enhance functionality. Establishing a strong communication channel with the manufacturer throughout the development process ensures that the final product aligns with operational goals and minimizes the risk of compatibility issues.
Strategic Material Selection Guide for dc motor
What Are the Common Materials Used in DC Motors?
When selecting materials for DC motors, international B2B buyers must consider various factors, including performance, cost, and compliance with industry standards. The following analysis explores four common materials used in DC motors: copper, aluminum, steel, and plastic composites. Each material has unique properties and implications for performance and application.
How Does Copper Impact DC Motor Performance?
Copper is widely used in the windings of DC motors due to its excellent electrical conductivity. It has a high melting point (approximately 1,984°F or 1,085°C) and can withstand significant thermal stress, making it suitable for high-performance applications.
Pros: Copper’s high conductivity allows for efficient energy transfer, reducing energy losses and improving overall motor efficiency. It also exhibits good corrosion resistance, particularly when coated.
Cons: The primary drawback of copper is its cost, which is higher than aluminum. Additionally, its weight can be a disadvantage in applications where weight reduction is critical.
Impact on Application: Copper is ideal for applications requiring high torque and speed, such as electric vehicles and industrial machinery. However, buyers must ensure compliance with international standards like ASTM B170 for copper wire.
What Role Does Aluminum Play in DC Motors?
Aluminum is another popular material for DC motor construction, particularly for housing and rotor components. It has a lower density compared to copper, which makes it an attractive option for lightweight applications.
Pros: Aluminum is cost-effective and offers good thermal conductivity. It is also more resistant to corrosion than copper when treated, making it suitable for outdoor applications.
Cons: While aluminum has decent electrical conductivity, it is not as efficient as copper. It also has a lower melting point (approximately 1,221°F or 660°C), which may limit its use in high-temperature environments.
Impact on Application: Aluminum is often used in portable devices and automotive applications where weight savings are crucial. Buyers should consider compliance with standards such as ASTM B221 for aluminum extrusions.
Why Is Steel Used in DC Motor Components?
Steel is commonly used for the structural components of DC motors, such as the frame and shaft. It provides excellent mechanical strength and durability.
Pros: Steel is highly durable and can withstand significant mechanical stress, making it suitable for heavy-duty applications. It is also relatively inexpensive compared to other metals.
Cons: Steel is heavier than both copper and aluminum, which may not be suitable for applications requiring lightweight designs. Additionally, it is prone to corrosion unless properly treated or coated.
Impact on Application: Steel is ideal for applications in harsh environments, such as mining or agriculture. International buyers should ensure compliance with standards like ASTM A36 for carbon structural steel.
How Do Plastic Composites Enhance DC Motor Design?
Plastic composites are increasingly used in DC motors for non-structural components, such as housings and insulators. They offer a unique combination of properties that can enhance motor performance.
Pros: Plastic composites are lightweight, corrosion-resistant, and can be molded into complex shapes, allowing for design flexibility. They also provide good electrical insulation.
Cons: The primary limitation is their lower mechanical strength compared to metals, which may restrict their use in high-stress applications. Additionally, they may have lower thermal resistance.
Impact on Application: Plastic composites are suitable for consumer electronics and applications where weight and insulation are critical. Buyers should consider compliance with UL standards for electrical components.
Summary Table of Material Selection for DC Motors
Material | Typical Use Case for dc motor | Key Advantage | Key Disadvantage/Limitation | Relative Cost (Low/Med/High) |
---|---|---|---|---|
Copper | Electric vehicles, industrial machinery | High electrical conductivity | High cost, heavier than aluminum | High |
Aluminum | Portable devices, automotive | Lightweight, cost-effective | Lower conductivity than copper, lower melting point | Medium |
Steel | Heavy-duty applications (mining, agriculture) | Excellent mechanical strength | Heavier, prone to corrosion | Low |
Plastic Composites | Consumer electronics, insulation | Lightweight, corrosion-resistant | Lower mechanical strength, thermal resistance | Medium |
This strategic material selection guide aims to equip international B2B buyers with actionable insights to make informed decisions when sourcing DC motors, ensuring compliance with local standards while optimizing performance for their specific applications.
In-depth Look: Manufacturing Processes and Quality Assurance for dc motor
What Are the Key Stages in the Manufacturing Process of DC Motors?
The manufacturing process of DC motors is a sophisticated procedure that involves multiple stages, each crucial for ensuring the final product meets the required specifications and performance standards. The main stages include material preparation, forming, assembly, and finishing.
Material Preparation
The first stage is material preparation, which involves sourcing high-quality raw materials such as copper for windings, steel for the rotor, and various plastics for insulation. International B2B buyers should ensure that suppliers provide material certifications to verify the quality of the components. For instance, checking for compliance with standards like ASTM (American Society for Testing and Materials) can offer insights into material integrity.
Forming Techniques Used in DC Motor Manufacturing
The forming stage typically involves machining processes like stamping, winding, and shaping the rotor and stator.
- Stamping: This is used to create the laminated cores of the motor, reducing eddy current losses.
- Winding: Precision winding techniques are employed to wrap copper wire around the rotor and stator. Automated winding machines often enhance consistency and reduce human error.
- Injection Molding: For parts like housings and end caps, injection molding ensures that components are produced with tight tolerances and minimal defects.
Buyers should inquire about the machinery and technologies used in these processes, as advanced manufacturing techniques can significantly affect the performance and longevity of the motors.
How Is Assembly Conducted in DC Motor Manufacturing?
The assembly stage combines all individual components into a complete motor. This process includes:
- Component Placement: Automated and manual methods are used to place the rotor, stator, brushes, and other components.
- Soldering and Bonding: Electrical connections are established through soldering, and structural integrity is ensured using adhesives or mechanical fastening.
- Alignment and Testing: As components are assembled, alignment is crucial for motor performance. Misalignment can lead to increased wear and reduced efficiency.
B2B buyers should consider the level of automation in the assembly process, as highly automated lines can improve consistency and reduce the risk of defects.
What Finishing Techniques Are Important for DC Motors?
The finishing stage involves several treatments that enhance the motor’s performance and durability. Key techniques include:
- Surface Treatment: This may involve coating components with corrosion-resistant materials to extend the motor’s lifespan, especially in harsh environments.
- Balancing: Dynamic balancing of the rotor is essential to minimize vibrations during operation, which can lead to premature failure.
- Quality Checks: Final inspections are conducted to ensure that all components meet specified tolerances and performance metrics.
What Quality Assurance Measures Are Essential for DC Motors?
Quality assurance (QA) is vital in ensuring that DC motors perform reliably and safely. International standards and industry-specific certifications play a crucial role in this process.
What International Standards Should B2B Buyers Be Aware Of?
One of the most recognized international standards for quality management is ISO 9001. Compliance with this standard indicates that a manufacturer has established a robust quality management system (QMS) focused on customer satisfaction and continuous improvement.
In addition to ISO 9001, industry-specific certifications such as CE (Conformité Européenne) for European markets and API (American Petroleum Institute) certifications for motors used in oil and gas applications are critical. These certifications assure buyers that products meet necessary safety and performance standards.
What Are the Key Quality Control Checkpoints in DC Motor Manufacturing?
Quality control (QC) in DC motor manufacturing typically involves several checkpoints:
- Incoming Quality Control (IQC): This stage checks raw materials and components upon arrival. Ensuring that suppliers adhere to specifications is crucial for maintaining product quality.
- In-Process Quality Control (IPQC): During manufacturing, various tests are performed to monitor processes and detect defects early. This can include dimensional inspections and electrical tests.
- Final Quality Control (FQC): After assembly, motors undergo comprehensive testing, including performance evaluations under load conditions, insulation resistance tests, and thermal imaging to identify potential overheating issues.
How Can B2B Buyers Verify Supplier Quality Control Practices?
For international B2B buyers, verifying a supplier’s quality control practices is essential. Here are some actionable strategies:
- Audits: Conducting on-site audits allows buyers to assess manufacturing processes, QC measures, and compliance with international standards.
- Quality Reports: Request detailed quality reports from suppliers that outline QC practices, including metrics on defect rates and corrective actions taken.
- Third-Party Inspections: Engaging third-party inspection services can provide an unbiased evaluation of a supplier’s quality control systems, offering additional assurance.
What Are the QC and Certification Nuances for International B2B Buyers?
When sourcing DC motors internationally, particularly from regions like Africa, South America, the Middle East, and Europe, buyers should be aware of specific nuances in quality control and certification:
- Regional Standards: Different countries may have unique regulations and standards. Buyers should familiarize themselves with these to ensure compliance and avoid penalties.
- Supply Chain Transparency: Knowing the entire supply chain, from raw material sourcing to final assembly, can help buyers assess risks and ensure quality.
- Cultural Considerations: Understanding cultural differences in business practices can facilitate smoother negotiations and foster better relationships with suppliers.
By focusing on these manufacturing processes and quality assurance measures, B2B buyers can make informed decisions, ensuring they procure reliable and high-quality DC motors suitable for their specific applications.
Practical Sourcing Guide: A Step-by-Step Checklist for ‘dc motor’
The following practical sourcing guide is designed to assist B2B buyers in procuring DC motors effectively. By adhering to this checklist, international buyers—especially those from Africa, South America, the Middle East, and Europe—can ensure they make informed decisions that meet their operational needs.
Step 1: Define Your Technical Specifications
Start by outlining the specific requirements for the DC motor you need. Consider factors such as voltage rating, power output, torque, and RPM.
– Key considerations: Are you looking for low-voltage motors for battery-powered applications or higher voltage for industrial machinery? Understanding your needs ensures that the motor you select is suitable for your applications, such as agriculture or automation.
Step 2: Research Different Types of DC Motors
Familiarize yourself with the various types of DC motors available in the market, including Permanent Magnet DC (PMDC) motors and Brushless DC motors.
– Why it matters: Each type has unique characteristics, such as efficiency and operational longevity, which can significantly impact your application. For example, PMDC motors offer high starting torque and efficiency, making them ideal for portable medical devices or warehouse automation.
Step 3: Evaluate Potential Suppliers
Before making a purchase, it’s essential to assess the credibility and reliability of potential suppliers.
– What to look for: Request company profiles, product catalogs, and customer references. Check for certifications relevant to your industry standards, such as ISO or CE certifications, to ensure compliance and quality.
Step 4: Request Quotes and Compare Pricing
After identifying potential suppliers, request detailed quotations for the motors you are interested in.
– Comparison criteria: Look beyond the price; assess shipping costs, lead times, and payment terms. This comprehensive analysis helps you understand the total cost of ownership, which is crucial for budgeting.
Step 5: Ask About Warranty and Support Services
Inquire about the warranty terms and after-sales support provided by the supplier.
– Importance: A robust warranty and support service can protect your investment and ensure that you have assistance in case of operational issues or product defects. Knowing the supplier’s response times and service capabilities is vital for maintaining operational continuity.
Step 6: Verify Supply Chain Logistics
Ensure that the supplier can meet your logistical needs, particularly if you are sourcing from a different continent.
– Logistics considerations: Consider factors such as shipping times, customs clearance, and local regulations. Suppliers who can efficiently handle logistics will minimize potential delays in your project timelines.
Step 7: Finalize the Purchase Agreement
Once you have chosen a supplier, review and finalize the purchase agreement carefully.
– Key elements to check: Ensure that all terms regarding delivery, payment, and warranty are clearly outlined. This step is crucial to avoid misunderstandings that could impact your operations later on.
By following this checklist, B2B buyers can make well-informed decisions when sourcing DC motors, ultimately leading to more successful procurement outcomes.
Comprehensive Cost and Pricing Analysis for dc motor Sourcing
What Are the Key Cost Components in DC Motor Sourcing?
When sourcing DC motors, understanding the various cost components is crucial for international B2B buyers. The primary cost components include:
-
Materials: The choice of materials significantly influences the cost. High-quality copper for windings, rare earth magnets for efficiency, and durable housing materials can increase initial costs but enhance performance and longevity.
-
Labor: Labor costs vary by region and can affect the overall price of DC motors. Countries with higher labor costs may result in more expensive products, while manufacturers in regions with lower labor costs could offer competitive pricing.
-
Manufacturing Overhead: This includes costs associated with production facilities, equipment depreciation, and utilities. Efficient manufacturing processes can help reduce overhead costs, ultimately benefiting the buyer.
-
Tooling: Custom tooling for specific motor designs or configurations can lead to higher upfront costs. However, these costs may be amortized over large production runs, making them more manageable per unit.
-
Quality Control (QC): Investing in robust QC processes ensures product reliability and compliance with international standards. While this may increase costs, it can prevent costly failures and recalls in the long run.
-
Logistics: Shipping and handling costs vary based on the distance from the supplier to the buyer. Understanding the Incoterms (International Commercial Terms) can help buyers manage these costs effectively.
-
Margin: Supplier profit margins can vary widely based on market dynamics and competition. Buyers should be aware of the typical margins in their industry to negotiate effectively.
How Do Price Influencers Affect DC Motor Costs?
Several factors can influence the pricing of DC motors, especially in the international market:
-
Volume/MOQ (Minimum Order Quantity): Larger orders typically result in lower per-unit costs. Buyers should consider their requirements and negotiate MOQs to optimize pricing.
-
Specifications and Customization: Custom features or specifications can significantly impact pricing. Buyers should weigh the benefits of customization against potential cost increases.
-
Materials Quality and Certifications: Higher quality materials and necessary certifications (e.g., ISO, CE) can lead to increased costs but ensure reliability and compliance with international standards.
-
Supplier Factors: The reputation, reliability, and production capabilities of the supplier can influence pricing. Established suppliers may command higher prices due to their perceived quality and service levels.
-
Incoterms: Understanding shipping terms and responsibilities (e.g., FOB, CIF) is essential. Different terms can lead to variations in overall costs, impacting budgeting and negotiations.
What Are the Best Buyer Tips for Cost-Efficiency in DC Motor Sourcing?
To maximize value and minimize costs when sourcing DC motors, consider the following tips:
-
Negotiate Effectively: Leverage your purchasing power by negotiating with suppliers. Discuss volume discounts, payment terms, and potential for future business to secure favorable pricing.
-
Evaluate Total Cost of Ownership (TCO): Beyond the initial purchase price, consider maintenance, energy consumption, and potential downtime costs. A slightly higher upfront cost may be justified by lower operational costs over time.
-
Understand Pricing Nuances for International Buyers: Be aware of currency fluctuations, import duties, and regional market conditions that can affect pricing. Engaging with local experts or consultants can provide valuable insights into specific regional challenges.
-
Seek Multiple Quotes: Obtaining quotes from several suppliers allows for comparison and negotiation leverage. Look for suppliers that offer transparent pricing structures, as this can facilitate better decision-making.
-
Build Relationships with Suppliers: Establishing long-term relationships can lead to better pricing, preferential treatment, and improved communication, ultimately benefiting the sourcing process.
Disclaimer on Indicative Prices
Prices for DC motors can vary widely based on specifications, supplier relationships, and market conditions. The information provided here serves as a guideline, and buyers should conduct thorough research and due diligence to obtain accurate pricing for their specific needs.
Alternatives Analysis: Comparing dc motor With Other Solutions
Understanding the Importance of Alternative Solutions to DC Motors
When considering motor solutions for various applications, it’s crucial to evaluate alternatives to DC motors. Although DC motors offer several advantages such as high starting torque and controllable speed, other technologies may be better suited for specific needs, especially for international B2B buyers from diverse regions like Africa, South America, the Middle East, and Europe. This section compares DC motors with two viable alternatives: AC motors and stepper motors, focusing on performance, cost, ease of implementation, maintenance, and best use cases.
Comparison Table of DC Motors and Alternatives
Comparison Aspect | DC Motor | AC Motor | Stepper Motor |
---|---|---|---|
Performance | High efficiency, good torque at low speeds | Reliable for continuous operation | Precise control over position and speed |
Cost | Moderate initial cost | Generally lower cost for high power | Higher initial cost compared to DC motors |
Ease of Implementation | Requires specific controllers | Easier to integrate with standard power | Complex setup with controllers needed |
Maintenance | Moderate; brushes may wear out | Low; fewer moving parts | Moderate; requires calibration |
Best Use Case | Adjustable speed applications | High-power, continuous applications | Applications needing precise positioning |
Pros and Cons of Each Alternative
AC Motors: Are They a Cost-Effective Alternative?
AC motors utilize alternating current to operate, making them a popular choice for many industrial applications. They are generally more cost-effective than DC motors when it comes to high-power applications, as they can deliver substantial torque and are often easier to integrate into existing power systems. However, they may lack the precision control that DC motors provide, especially in applications requiring variable speed. Additionally, AC motors can be less efficient at low speeds, which may not suit all applications.
Stepper Motors: When Precision is Paramount
Stepper motors are designed for applications where precise control of position and speed is essential. They excel in scenarios like 3D printing and CNC machinery, where exact movements are critical. However, they come with a higher upfront cost and require more complex controllers compared to DC motors. Maintenance can be moderate, as they may need regular calibration to maintain their precision. For B2B buyers looking to invest in technologies that require exacting standards, stepper motors may offer significant advantages despite the higher initial investment.
How to Choose the Right Motor Solution for Your Needs
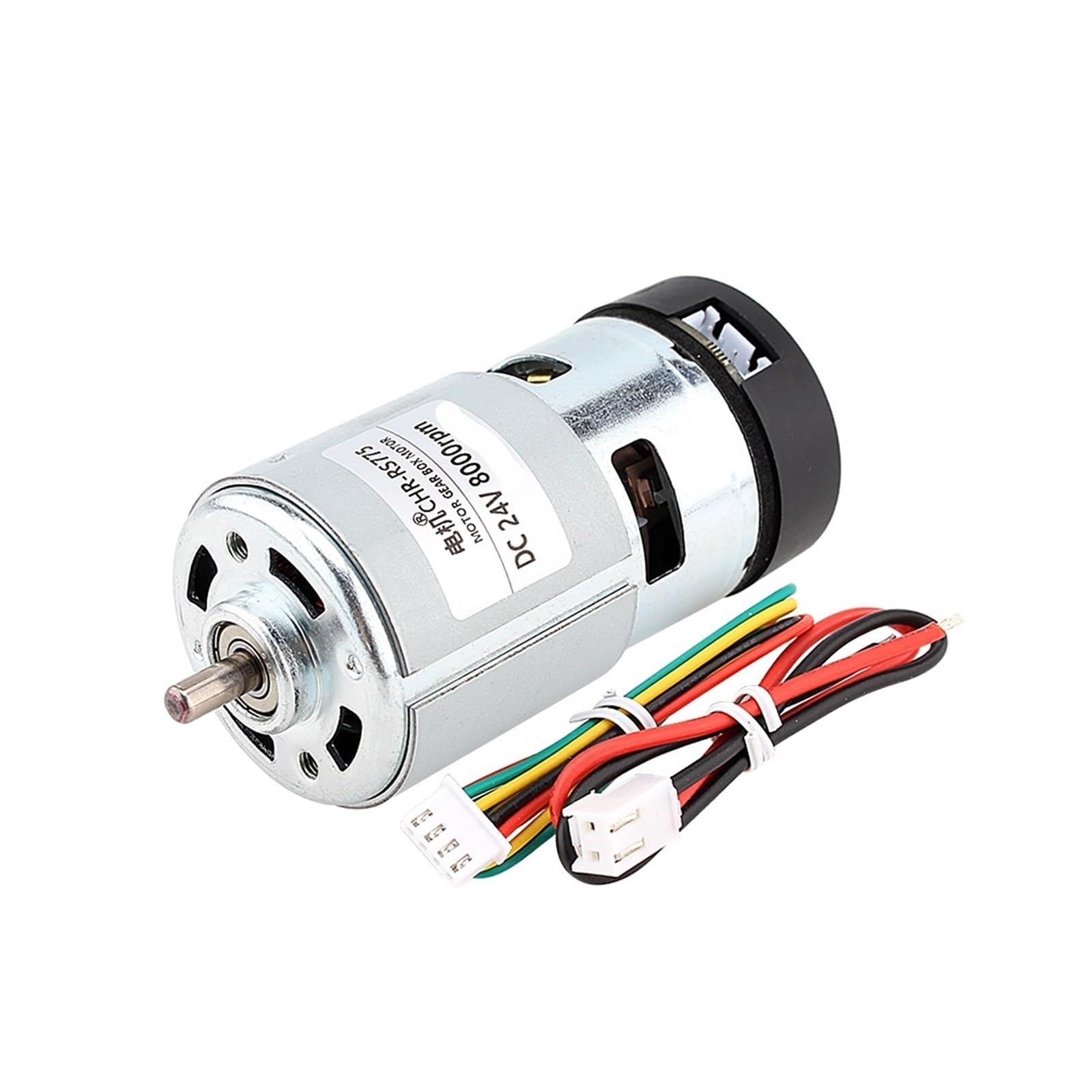
A stock image related to dc motor.
Selecting the right motor solution depends on various factors, including the specific requirements of your application, budget constraints, and the desired level of control. For applications requiring high torque and adjustable speed, DC motors may be the best choice. Conversely, if your operations involve high-power requirements with less emphasis on speed variability, AC motors could be more cost-effective. On the other hand, if your project demands precise control over movements, stepper motors may be worth the investment. Ultimately, understanding the nuances of each motor type will empower B2B buyers to make informed decisions that align with their operational goals and regional market conditions.
Essential Technical Properties and Trade Terminology for dc motor
What Are the Key Technical Properties of DC Motors?
When considering the purchase of DC motors for various applications, it’s essential to understand their critical technical properties. These specifications not only influence the motor’s performance but also its suitability for specific applications, particularly in sectors like agriculture, manufacturing, and renewable energy.
1. Voltage Rating
The voltage rating of a DC motor indicates the maximum voltage it can handle. Common ratings include low voltage (12V, 24V) and standard voltages (90V, 130V). For B2B buyers, selecting the correct voltage is crucial for compatibility with power sources, especially in battery-operated or solar-powered devices. Using a motor with an incorrect voltage can lead to inefficiency or motor failure.
2. Torque
Torque is a measure of the rotational force the motor can provide and is typically expressed in ounce-inches (oz-in) or Newton-meters (Nm). High starting torque is particularly important for applications requiring immediate acceleration, such as conveyors or agricultural machinery. B2B buyers should evaluate torque requirements based on the load conditions of their specific applications to ensure optimal performance.
3. Speed (RPM)
The revolutions per minute (RPM) rating indicates how fast the motor can turn. Different applications may require varying speeds; for example, warehouse automation robots may need high RPMs for quick movements, while more controlled applications may require lower speeds. Understanding the required speed helps buyers select a motor that matches their operational needs.
4. Duty Cycle
Duty cycle describes the motor’s operational time versus rest time, often expressed as a percentage. Continuous duty motors can operate without interruption, while intermittent duty motors are designed for periodic use. This specification is vital for buyers to ensure that the motor can handle the demands of their application without overheating or suffering from wear.
5. Frame Size
Frame size is a critical specification that affects the motor’s physical dimensions and mounting compatibility. A motor must fit into the designated space in machinery or equipment. Buyers should verify that the frame size aligns with their design requirements, especially when retrofitting or integrating new motors into existing systems.
6. Efficiency Rating
Efficiency ratings indicate how effectively a motor converts electrical energy into mechanical energy. Higher efficiency motors lead to lower energy consumption and can provide significant cost savings over time. For international buyers, especially in regions with high energy costs, selecting a motor with a superior efficiency rating is a smart investment.
What Are Common Trade Terms Used in the DC Motor Industry?
Understanding industry terminology is crucial for effective communication and negotiation in B2B transactions. Here are some common terms that buyers should be familiar with:
1. OEM (Original Equipment Manufacturer)
An OEM is a company that produces parts or equipment that may be marketed by another manufacturer. In the context of DC motors, OEMs often supply motors that are integrated into larger systems or machinery. Buyers should ensure they are dealing with reputable OEMs to guarantee quality and compatibility.
2. MOQ (Minimum Order Quantity)
MOQ refers to the smallest number of units that a supplier is willing to sell. This term is vital for buyers looking to manage inventory costs effectively. Understanding the MOQ helps businesses plan their purchases and avoid excess inventory.
3. RFQ (Request for Quotation)
An RFQ is a document sent to suppliers asking for pricing information on specific products or services. It is a standard practice in B2B transactions, enabling buyers to compare offers and negotiate better terms. Crafting a clear RFQ can lead to more accurate quotes and better supplier relationships.
4. Incoterms (International Commercial Terms)
Incoterms are a series of pre-defined commercial terms published by the International Chamber of Commerce. They outline the responsibilities of buyers and sellers in international transactions, including shipping costs, insurance, and risk management. Familiarity with Incoterms is essential for B2B buyers, especially when sourcing motors from international suppliers.
5. Lead Time
Lead time refers to the time taken from placing an order to receiving the goods. Understanding lead times can help businesses manage their production schedules and inventory levels. Buyers should inquire about lead times during negotiations to align their operational needs with supplier capabilities.
6. Warranty
A warranty is a guarantee provided by the manufacturer regarding the condition of the product. In the context of DC motors, warranties can cover defects in materials and workmanship. Buyers should always clarify warranty terms before finalizing a purchase to ensure protection against potential failures.
By grasping these technical properties and industry terms, international B2B buyers can make informed decisions when sourcing DC motors, ultimately enhancing their operational efficiency and product quality.
Navigating Market Dynamics and Sourcing Trends in the dc motor Sector
What Are the Key Market Dynamics and Trends in the DC Motor Sector?
The global DC motor market is experiencing significant growth driven by several factors. The increasing demand for automation in various industries such as manufacturing, agriculture, and logistics is propelling the adoption of DC motors, particularly in regions like Africa, South America, the Middle East, and Europe. These motors are favored for their efficiency, high starting torque, and ability to operate in variable speed applications. Moreover, the rise of renewable energy solutions, such as solar and battery-powered systems, is further enhancing the demand for low-voltage DC motors, which are critical for sustainable energy applications.
Emerging trends in the B2B landscape include the integration of smart technologies in motor designs, such as IoT capabilities that allow for remote monitoring and control. This advancement not only improves operational efficiency but also provides valuable data analytics for predictive maintenance. Additionally, the focus on modular designs is gaining traction, enabling buyers to customize their motor solutions based on specific application requirements. International buyers should also be aware of the growing trend toward local sourcing to mitigate supply chain disruptions and reduce lead times, particularly in light of recent global events.
How Can B2B Buyers Emphasize Sustainability and Ethical Sourcing in DC Motors?
Sustainability is becoming a cornerstone of B2B purchasing decisions, particularly in the DC motor sector. The environmental impact of manufacturing processes, including energy consumption and waste production, is under scrutiny. Buyers should prioritize suppliers that demonstrate a commitment to sustainable practices, such as using eco-friendly materials and minimizing carbon footprints in their production processes.
Ethical sourcing is equally important, as it ensures that materials are obtained responsibly and that labor practices meet ethical standards. Look for suppliers who hold certifications like ISO 14001 for environmental management and ISO 45001 for occupational health and safety. Furthermore, certifications related to green materials, such as RoHS (Restriction of Hazardous Substances), can signal a supplier’s commitment to reducing harmful substances in their products. By focusing on these criteria, international B2B buyers can enhance their corporate social responsibility (CSR) profiles and align with global sustainability goals.
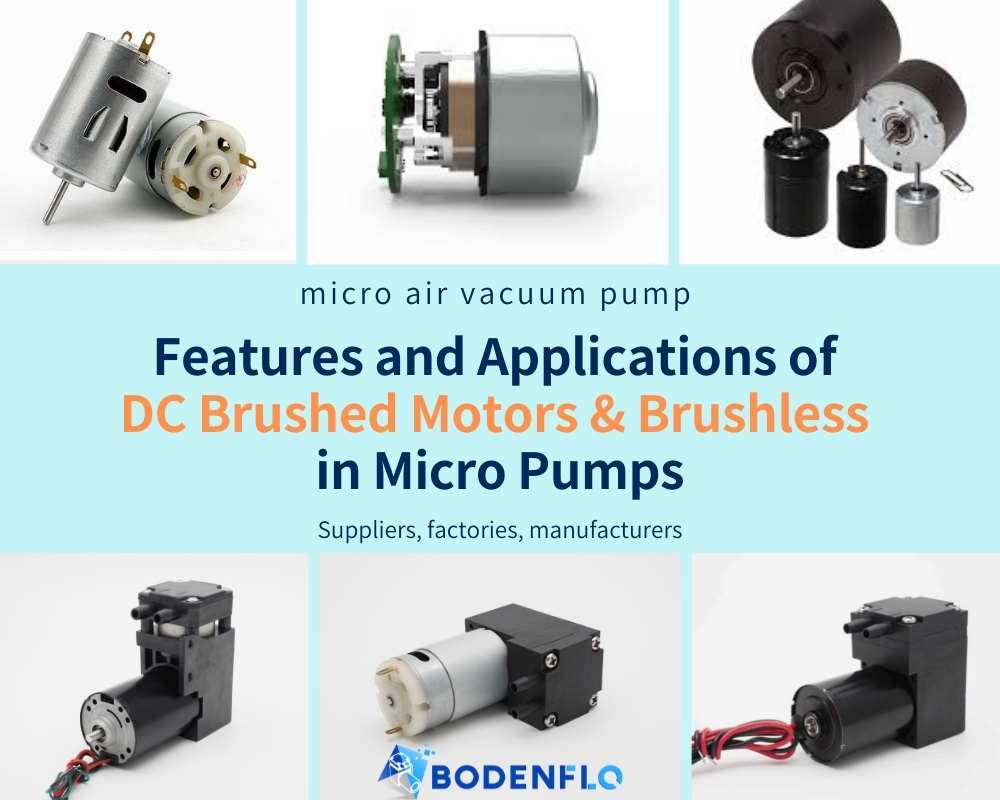
A stock image related to dc motor.
How Has the DC Motor Sector Evolved Over Time?
The evolution of DC motors can be traced back to the late 19th century when they were first developed for various industrial applications. Initially, these motors were bulky and inefficient, but advancements in materials and design technology have led to significant improvements in performance and efficiency. The introduction of permanent magnet DC (PMDC) motors revolutionized the market, offering higher efficiency and compact designs that are now prevalent in modern applications.
In recent decades, the shift toward automation and digitalization has further transformed the sector. The development of electronic speed controllers has enabled precise control over motor functions, enhancing the versatility of DC motors in applications ranging from robotics to renewable energy systems. As the market continues to grow, ongoing innovations in motor technology, such as brushless designs and smart connectivity, are set to redefine the landscape for international B2B buyers seeking cutting-edge solutions.
Frequently Asked Questions (FAQs) for B2B Buyers of dc motor
-
How do I choose the right DC motor for my application?
Selecting the appropriate DC motor involves assessing your specific application requirements, such as torque, speed, power supply voltage, and physical dimensions. Consider whether you need a permanent magnet DC (PMDC) motor for high efficiency and starting torque or a brushed DC motor for simple control. Additionally, evaluate the environmental conditions—like temperature and humidity—that the motor will operate in. Collaborate with suppliers who can provide detailed specifications and recommendations based on your unique needs. -
What is the best voltage for a DC motor in solar applications?
For solar-powered systems, low-voltage DC motors, typically operating at 12V or 24V, are ideal due to their compatibility with battery systems. These motors are designed to maximize efficiency and are often used in portable devices, agricultural equipment, and remote applications. When selecting a motor, ensure it matches the voltage output of your solar panels and batteries to optimize performance and energy management. -
What factors should I consider when vetting a DC motor supplier?
When vetting suppliers, evaluate their industry experience, product range, and customer reviews. Look for suppliers who offer certifications such as ISO 9001, indicating quality management systems. Request samples to assess the quality and performance of their motors in your specific applications. Additionally, consider their ability to provide technical support, customization options, and responsiveness to inquiries, which are critical for long-term partnerships. -
What are the typical minimum order quantities (MOQ) for DC motors?
Minimum order quantities can vary widely among suppliers, typically ranging from a few units to several hundred, depending on the motor type and supplier’s policies. For bulk orders, suppliers may offer better pricing and flexible payment terms. Always confirm MOQs before finalizing an agreement, especially if you are testing a new product line or entering a new market. -
How can I customize a DC motor to meet my specific needs?
Many manufacturers offer customization options for DC motors, including adjustments to voltage, speed ratings, and mounting configurations. When discussing your needs with suppliers, provide detailed specifications about your application, including any environmental factors and performance requirements. Customization can also extend to integrating encoders, brakes, and gear ratios to enhance functionality and fit your system design. -
What payment terms are common in international B2B transactions for DC motors?
Payment terms can vary by supplier and region, but common practices include partial upfront payments with the balance due upon delivery or after installation. Letters of credit are also frequently used in international transactions to ensure security for both parties. Establish clear terms early in negotiations to avoid misunderstandings and ensure smooth transaction processes. -
How do I ensure quality assurance (QA) for my DC motor purchases?
To ensure quality assurance, request documentation such as test reports, certifications, and compliance with international standards (like CE or UL). Consider suppliers who provide a warranty or guarantee on their products, as this reflects confidence in their quality. Additionally, regular audits and inspections can be conducted to verify the manufacturing processes and final product quality. -
What logistics considerations should I keep in mind when importing DC motors?
When importing DC motors, consider shipping methods, customs regulations, and lead times. Ensure that you understand tariffs and duties applicable to your shipments. Collaborating with experienced logistics partners can help navigate these complexities and optimize shipping routes. Additionally, plan for storage and distribution in your local market to minimize delays and manage inventory effectively.
Important Disclaimer & Terms of Use
⚠️ Important Disclaimer
The information provided in this guide, including content regarding manufacturers, technical specifications, and market analysis, is for informational and educational purposes only. It does not constitute professional procurement advice, financial advice, or legal advice.
While we have made every effort to ensure the accuracy and timeliness of the information, we are not responsible for any errors, omissions, or outdated information. Market conditions, company details, and technical standards are subject to change.
B2B buyers must conduct their own independent and thorough due diligence before making any purchasing decisions. This includes contacting suppliers directly, verifying certifications, requesting samples, and seeking professional consultation. The risk of relying on any information in this guide is borne solely by the reader.
Strategic Sourcing Conclusion and Outlook for dc motor
What Are the Key Takeaways for International B2B Buyers of DC Motors?
In conclusion, strategic sourcing of DC motors is essential for international B2B buyers seeking to enhance operational efficiency and competitiveness. Understanding the various types of DC motors, such as permanent magnet and gearmotors, enables businesses to select the right solutions tailored to their specific applications—be it in agriculture, warehouse automation, or renewable energy sectors. Emphasizing high efficiency, adjustable speed capabilities, and compact designs can significantly improve performance in demanding environments.
How Can Strategic Sourcing Impact Your Business?
The value of strategic sourcing lies in its ability to reduce costs while ensuring high-quality components that meet regulatory standards and operational needs. By leveraging local suppliers in Africa, South America, the Middle East, and Europe, companies can optimize their supply chains, mitigate risks, and respond swiftly to market demands.
What’s Next for B2B Buyers in the DC Motor Market?
Looking ahead, the demand for advanced DC motor technologies will continue to rise as industries evolve toward automation and sustainability. International B2B buyers are encouraged to stay informed about emerging trends and innovations in the DC motor sector. Engaging with reliable suppliers and exploring collaborative opportunities can pave the way for future growth and success. Take the next step in your sourcing strategy today—invest in quality DC motors that will drive your business forward.