Maximize Efficiency: The Ultimate Drum Mixer Guide (2025)
Introduction: Navigating the Global Market for drum mixer
In today’s competitive landscape, sourcing the right drum mixer can be a daunting challenge for international B2B buyers. Whether you’re in Africa, South America, the Middle East, or Europe, the complexities of selecting a mixer that meets your specific operational needs and budgetary constraints cannot be underestimated. This guide aims to streamline your purchasing process by providing a comprehensive overview of drum mixers, including various types, applications, and critical considerations for supplier vetting and cost analysis.
Drum mixers are essential in industries such as chemical processing, food and beverage, and pharmaceuticals, where consistent product quality is paramount. Understanding the different mounting options—such as bung mount, clamp mount, and lid mount—can significantly influence your mixing efficiency and reduce transfer waste. Furthermore, we delve into key factors such as power source compatibility, viscosity handling capabilities, and safety standards, particularly in regions with specific regulatory requirements.
By equipping you with actionable insights and practical strategies, this guide empowers B2B buyers to make informed decisions. You’ll gain clarity on how to assess suppliers, compare products effectively, and ultimately select a drum mixer that aligns with your operational goals and enhances productivity. Navigate the global market with confidence and ensure your investment in mixing technology drives your business success.
Understanding drum mixer Types and Variations
Type Name | Key Distinguishing Features | Primary B2B Applications | Brief Pros & Cons for Buyers |
---|---|---|---|
Bung Mount Mixer | Threads into standard 2″ NPT bung fittings; compact design | Ideal for closed drum mixing | Pros: Space-saving, reduces contamination risk. Cons: Limited to drum types with bung fittings. |
Drum Clamp Mixer | Attaches to the side of drums; versatile for open or closed | Suitable for a variety of liquids | Pros: Flexibility in use, easy to install. Cons: May require extra support for larger volumes. |
Drum Lid Mixer | Mounted on the lid, designed for low shear agitation | Mixing viscous or sensitive fluids | Pros: Minimizes splashing, effective for delicate mixing. Cons: Can be more expensive than clamp options. |
Drum Bracket Mixer | Secured with brackets for stability; accommodates larger drums | Heavy-duty mixing applications | Pros: Stability for high-viscosity materials. Cons: More complex installation process. |
Explosion-Proof Mixer | Designed for hazardous environments; robust construction | Chemical and pharmaceutical sectors | Pros: Safety in volatile settings, high reliability. Cons: Higher initial investment required. |
What Are the Characteristics of Bung Mount Mixers?
Bung mount mixers are specifically designed to thread directly into standard 2″ NPT bung fittings found on drums. This compact design allows for efficient mixing within closed containers, making them ideal for applications where contamination must be minimized. When considering a bung mount mixer, buyers should evaluate the compatibility with their existing drum types and the type of materials being mixed, as this mixer is limited to specific drum configurations.
How Do Drum Clamp Mixers Offer Versatility?
Drum clamp mixers attach to the side of drums, allowing for mixing in both open and closed containers. This versatility makes them suitable for a wide range of liquid types, from low to high viscosity. Buyers should consider their specific mixing needs, including the volume and viscosity of the materials, as well as the ease of installation and mobility. Drum clamp mixers provide a balance of flexibility and efficiency, making them a popular choice for many industries.
What Makes Drum Lid Mixers Suitable for Sensitive Mixing?
Drum lid mixers are mounted on the drum lid and are designed to provide low shear agitation, making them particularly effective for mixing sensitive fluids or viscous materials. This type of mixer minimizes splashing and ensures thorough blending without damaging the product. Buyers should assess the specific mixing requirements of their applications, as well as the budget, since drum lid mixers can be more expensive than clamp-mounted alternatives.
Why Choose Drum Bracket Mixers for Heavy-Duty Applications?
Drum bracket mixers are designed to provide stability during the mixing process, making them suitable for heavy-duty applications and larger drum sizes. They utilize brackets for secure attachment, which is essential when dealing with high-viscosity materials. Buyers should consider the space and installation requirements, as these mixers may require a more complex setup compared to other types. Their stability and efficiency make them a reliable choice for industrial mixing needs.
What Are the Benefits of Explosion-Proof Mixers?
Explosion-proof mixers are constructed to operate safely in hazardous environments where flammable materials are present. These mixers are essential for industries such as chemicals and pharmaceuticals, where safety is paramount. Buyers must weigh the higher initial investment against the critical safety benefits provided by these mixers. For businesses operating in volatile settings, explosion-proof mixers are a necessary investment for compliance and risk management.
Key Industrial Applications of drum mixer
Industry/Sector | Specific Application of Drum Mixer | Value/Benefit for the Business | Key Sourcing Considerations for this Application |
---|---|---|---|
Chemical Manufacturing | Mixing of chemical compounds in drums | Reduces transfer waste and improves mixing efficiency | Compatibility with drum sizes, viscosity of chemicals, and explosion-proof options if necessary. |
Food and Beverage | Blending ingredients for sauces and dressings | Ensures uniform consistency and quality control | Hygiene standards, material compatibility, and ease of cleaning. |
Pharmaceuticals | Preparing formulations in bulk | Enhances product homogeneity and compliance with regulations | Certification for pharmaceutical use, mixing speed, and power source options. |
Paint and Coatings | Homogenizing paints and coatings | Improves color consistency and reduces settling | Ability to handle varying viscosities, impeller design, and energy efficiency. |
Agriculture | Mixing fertilizers and pesticides | Optimizes nutrient distribution for better crop yield | Chemical resistance, safety features, and power requirements. |
How is a Drum Mixer Used in Chemical Manufacturing?
In the chemical manufacturing sector, drum mixers are essential for blending various chemical compounds directly in their storage containers. This process minimizes transfer waste and optimizes the mixing of high-viscosity liquids. For international buyers, particularly in regions like Africa and the Middle East, sourcing mixers that meet specific safety and compatibility standards is crucial. Buyers should consider explosion-proof options to comply with local regulations, especially when working with volatile chemicals.
What Role Does a Drum Mixer Play in the Food and Beverage Industry?
Drum mixers are widely used in the food and beverage industry for blending ingredients such as sauces, dressings, and marinades. The ability to achieve a uniform consistency is paramount for maintaining product quality. Buyers from South America and Europe should prioritize mixers that adhere to hygiene standards and are constructed from food-grade materials. Easy disassembly and cleaning features are also vital to ensure compliance with food safety regulations.
Why is Drum Mixing Important in Pharmaceuticals?
In the pharmaceutical industry, drum mixers are utilized for preparing bulk formulations, ensuring that active ingredients are evenly distributed throughout the mixture. This uniformity is critical for product efficacy and regulatory compliance. Buyers need to focus on mixers that are certified for pharmaceutical use, with features that accommodate varying mixing speeds and power sources. Additionally, understanding local regulations regarding mixer specifications is essential for compliance.
How Do Drum Mixers Enhance Paint and Coatings Production?
In paint and coatings production, drum mixers play a vital role in homogenizing materials to achieve consistent color and texture. This process reduces settling and ensures that the final product meets quality standards. Buyers should consider mixers capable of handling a range of viscosities, as well as those with efficient impeller designs that minimize energy consumption. Understanding the specific requirements of local markets in Europe and South America can also guide sourcing decisions.
What Benefits Do Drum Mixers Offer in Agriculture?
In agriculture, drum mixers are commonly used to blend fertilizers and pesticides, ensuring that nutrients are evenly distributed for optimal crop yield. The need for chemical resistance and safety features is paramount, especially for international buyers dealing with hazardous materials. Additionally, energy efficiency and compatibility with local power sources should be key considerations when sourcing drum mixers for agricultural applications.
3 Common User Pain Points for ‘drum mixer’ & Their Solutions
Scenario 1: Inefficient Mixing Processes Lead to Production Delays
The Problem: Many manufacturers, especially those in sectors like chemicals and food processing, struggle with inefficient mixing processes when using drum mixers. When products are not mixed thoroughly, it can lead to inconsistencies in product quality, which may result in rework or waste. For instance, a company in South America faced significant delays due to inadequate mixing, causing their production line to halt while they addressed quality control issues. This not only impacted their output but also strained relationships with clients who relied on timely deliveries.
The Solution: To overcome this challenge, B2B buyers should invest in drum mixers that are specifically designed for their product viscosity and mixing requirements. When sourcing a drum mixer, it is crucial to evaluate the following: the mixer’s power, the type of impeller used, and the mounting method. For high-viscosity products, consider using gear-driven mixers that provide better torque and mixing efficiency. Additionally, utilizing a bung mount or lid mount mixer can minimize splashing and material waste. Consulting with manufacturers or suppliers to tailor the mixer specifications to your operational needs can ensure that mixing processes become efficient, reducing downtime and improving overall production consistency.
Scenario 2: Safety Concerns with Hazardous Materials
The Problem: Companies dealing with hazardous materials, such as chemicals or flammable substances, often face significant safety concerns during the mixing process. For example, a manufacturing facility in the Middle East experienced an incident where the mixer’s open design led to fumes escaping, creating a hazardous environment for workers. Such scenarios can not only endanger employee safety but also lead to regulatory compliance issues, potentially resulting in fines or operational shutdowns.
The Solution: To enhance safety when using drum mixers for hazardous materials, B2B buyers should consider explosion-proof and sealed mixers. These mixers prevent the escape of fumes and reduce the risk of ignition, ensuring a safer working environment. Additionally, implementing proper training for operators on the safe use of these mixers and regular maintenance checks can further mitigate risks. Buyers should also look for mixers equipped with safety features, such as automatic shut-off controls and pressure relief valves, to enhance operational safety. Engaging with suppliers who specialize in safety-compliant equipment will help in sourcing the right solutions tailored for hazardous material mixing.
Scenario 3: Inadequate Support and Maintenance Resources
The Problem: Many B2B buyers face challenges related to inadequate support and maintenance for their drum mixers, particularly in regions with limited access to technical expertise. For instance, a company in Africa found itself unable to troubleshoot mixer issues due to a lack of local service technicians. This resulted in prolonged downtimes and increased repair costs, negatively affecting their production schedules and profitability.
The Solution: To address these challenges, it is essential for buyers to choose drum mixers from reputable manufacturers that provide comprehensive support services, including installation, training, and ongoing maintenance. Buyers should inquire about the availability of local service representatives and the manufacturer’s commitment to training their staff. Additionally, sourcing mixers that come with clear documentation and online support resources can empower operators to handle minor issues independently. Investing in a maintenance agreement with the supplier can also ensure timely service and reduce unexpected downtimes. When engaging with suppliers, ask about their service network and customer support options, as this can significantly impact the long-term reliability of your mixing operations.
Strategic Material Selection Guide for drum mixer
When selecting materials for drum mixers, international B2B buyers must consider various factors that impact performance, durability, and compatibility with specific applications. Below are analyses of four common materials used in drum mixer construction, focusing on their properties, advantages, disadvantages, and specific considerations for buyers from Africa, South America, the Middle East, and Europe.
What Are the Key Properties of Stainless Steel for Drum Mixers?
Stainless steel is renowned for its excellent corrosion resistance, high tensile strength, and ability to withstand extreme temperatures. It is particularly suitable for mixing applications involving aggressive chemicals or high-viscosity materials. The material’s non-reactive nature makes it ideal for food-grade applications, ensuring that no contaminants leach into the product.
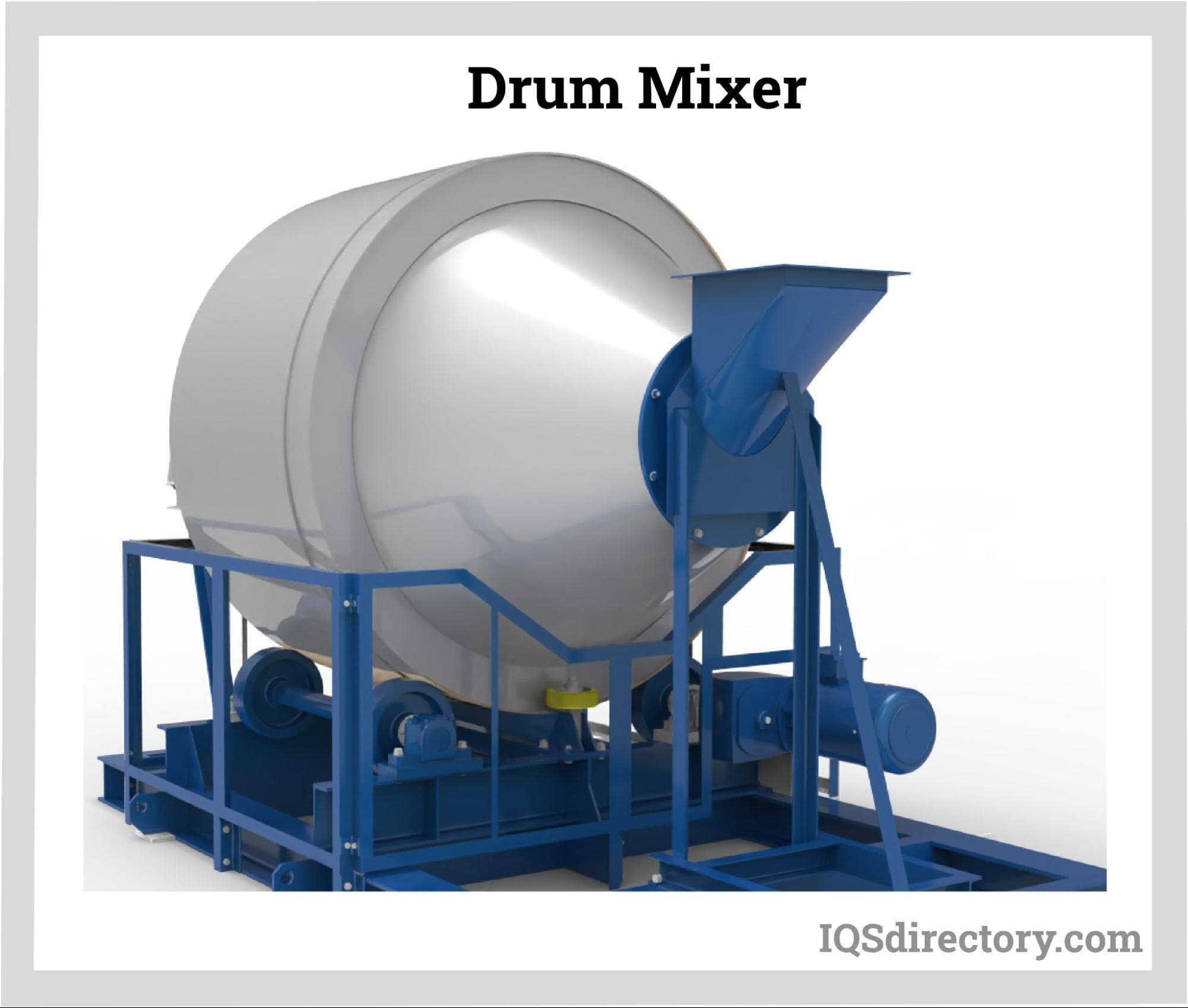
A stock image related to drum mixer.
Pros: Stainless steel offers exceptional durability and longevity, making it a cost-effective choice in the long run. Its resistance to rust and staining ensures minimal maintenance and a clean operating environment.
Cons: The primary drawback is its higher initial cost compared to other materials. Additionally, manufacturing complexities can arise due to the need for specialized welding techniques.
Impact on Application: Stainless steel is compatible with a wide range of media, including corrosive liquids and food products, making it versatile for various industries.
Considerations for International Buyers: Compliance with international standards such as ASTM and DIN is crucial, especially in regions with stringent regulations like Europe. Buyers should also consider local sourcing options to reduce costs and lead times.
How Does Polypropylene Compare as a Material for Drum Mixers?
Polypropylene is a lightweight, cost-effective thermoplastic that offers good chemical resistance, making it suitable for mixing less aggressive materials. It is commonly used in applications where weight savings and lower costs are priorities.
Pros: The material is affordable and easy to mold, leading to lower manufacturing costs. Its resistance to a variety of chemicals makes it suitable for many applications.
Cons: Polypropylene has lower temperature resistance compared to metals, which can limit its use in high-heat applications. Additionally, it may not be suitable for mixing highly viscous materials.
Impact on Application: It is ideal for mixing non-corrosive liquids, but its limitations in temperature and viscosity must be considered.
Considerations for International Buyers: Buyers should verify that the polypropylene used meets relevant safety and quality standards, particularly in regions like the Middle East where regulations can be strict.
What Advantages Does Aluminum Offer for Drum Mixers?
Aluminum is lightweight yet strong, making it a popular choice for portable drum mixers. It offers good corrosion resistance, particularly when anodized, and can handle moderate temperatures and pressures.
Pros: The lightweight nature of aluminum facilitates easy handling and transport. Its cost is generally lower than stainless steel, while still offering good performance.
Cons: Aluminum is less durable than stainless steel and can suffer from pitting in highly corrosive environments. Its temperature limitations may also restrict its use in certain applications.
Impact on Application: Aluminum is suitable for mixing applications that do not involve aggressive chemicals or extreme temperatures.
Considerations for International Buyers: Buyers should ensure that the aluminum used is of a grade suitable for their specific application and complies with local standards, especially in regions like Africa where material quality can vary.
Why Choose Carbon Steel for Drum Mixers?
Carbon steel is a strong and durable material often used in industrial applications. It is less expensive than stainless steel and can be coated to improve corrosion resistance.
Pros: The material is robust and cost-effective, making it a popular choice for heavy-duty applications. Coatings can enhance its performance in corrosive environments.
Cons: Carbon steel is prone to rust if not properly coated or maintained, which can lead to shorter lifespans in harsh conditions. Its weight can also be a disadvantage for portable applications.
Impact on Application: Suitable for mixing applications that require strength but may not be ideal for corrosive substances unless adequately protected.
Considerations for International Buyers: Buyers should be aware of the need for protective coatings and maintenance, especially in humid or corrosive environments prevalent in certain regions.
Summary Table of Material Selection for Drum Mixers
Material | Typical Use Case for Drum Mixer | Key Advantage | Key Disadvantage/Limitation | Relative Cost (Low/Med/High) |
---|---|---|---|---|
Stainless Steel | Food and chemical processing | Excellent corrosion resistance | Higher initial cost | High |
Polypropylene | Mixing non-corrosive liquids | Cost-effective and lightweight | Limited temperature resistance | Low |
Aluminum | Portable mixers for moderate applications | Lightweight and easy to handle | Less durable in corrosive environments | Medium |
Carbon Steel | Heavy-duty industrial mixing | Strong and cost-effective | Prone to rust without coatings | Medium |
By considering these materials and their properties, international B2B buyers can make informed decisions that align with their operational needs and compliance requirements.
In-depth Look: Manufacturing Processes and Quality Assurance for drum mixer
What Are the Key Stages in the Manufacturing Process of Drum Mixers?
The manufacturing process of drum mixers involves several critical stages to ensure that the final product meets industry standards and customer expectations. Understanding these stages can help B2B buyers make informed decisions when selecting suppliers.
Material Preparation: What Materials Are Commonly Used?
The initial stage of manufacturing drum mixers involves the careful selection and preparation of materials. Most drum mixers are constructed from high-quality metals like stainless steel and carbon steel, which provide durability and resistance to corrosion. Additionally, some components may be made from specialized polymers to enhance performance and reduce maintenance needs.
During this phase, materials undergo a thorough inspection to verify their quality and suitability for the intended application. Any defects or inconsistencies are addressed before proceeding to the next stage.
How Are Drum Mixers Formed and Assembled?
Once the materials are prepared, they are subjected to various forming techniques, including cutting, welding, and machining. CNC (Computer Numerical Control) machining is commonly employed to achieve precise dimensions and tolerances. This technology ensures that each component fits together seamlessly, which is crucial for optimal performance.
After forming, the assembly process begins. Components such as motors, impellers, and mounting brackets are carefully assembled to create the final mixer unit. This stage often involves the use of robotic automation to enhance accuracy and reduce human error.
What Finishing Techniques Are Employed in Drum Mixer Manufacturing?
The finishing stage of drum mixer manufacturing is essential for improving aesthetic appeal and enhancing performance. Common finishing techniques include:
- Surface Treatment: Processes such as powder coating, anodizing, or galvanizing are used to protect against corrosion and wear, especially in harsh environments.
- Quality Control Measures: Each finished product undergoes visual inspections to identify any surface defects or inconsistencies.
These finishing techniques not only contribute to the product’s longevity but also ensure compliance with international standards.
How Is Quality Assurance Implemented in Drum Mixer Production?
Quality assurance (QA) is vital in the manufacturing process to ensure that drum mixers meet the required specifications and standards. This involves implementing quality control (QC) checkpoints at various stages of production.
What Are the Relevant International Standards for Drum Mixers?
Many manufacturers adhere to international standards such as ISO 9001, which outlines requirements for a quality management system. Additionally, industry-specific certifications like CE (Conformité Européenne) for European markets or API (American Petroleum Institute) standards for oil and gas applications are crucial for ensuring product reliability and safety.
B2B buyers should inquire about these certifications when assessing potential suppliers to ensure compliance with relevant regulations in their regions.
What Are the Key Quality Control Checkpoints in Drum Mixer Manufacturing?
Quality control checkpoints play a significant role in maintaining the integrity of the manufacturing process. Key checkpoints include:
- Incoming Quality Control (IQC): This stage involves inspecting raw materials upon arrival to ensure they meet specified standards before production begins.
- In-Process Quality Control (IPQC): During the manufacturing process, ongoing inspections are conducted to monitor production quality and address any issues immediately.
- Final Quality Control (FQC): Before the drum mixers are shipped, a comprehensive final inspection is conducted to verify that all units meet the required specifications and standards.
What Common Testing Methods Are Used for Drum Mixers?
Testing methods are essential for validating the performance and safety of drum mixers. Common testing procedures include:
- Performance Testing: Assessing the mixer’s efficiency in blending materials of varying viscosities.
- Durability Testing: Simulating prolonged use to evaluate the mixer’s longevity and resistance to wear.
- Safety Testing: Ensuring that the equipment meets safety standards to minimize risks during operation.
Buyers should request documentation of these tests to verify that the products they intend to purchase have been rigorously evaluated.
How Can B2B Buyers Verify Supplier Quality Control Measures?
B2B buyers can take several steps to verify the quality control measures of potential suppliers:
- Supplier Audits: Conducting on-site audits allows buyers to assess manufacturing processes, quality control systems, and compliance with international standards.
- Quality Assurance Reports: Requesting detailed reports on quality assurance practices can provide insights into the supplier’s commitment to maintaining high standards.
- Third-party Inspections: Engaging third-party inspectors can offer an unbiased evaluation of the supplier’s operations and product quality.
What Are the QC Certification Nuances for International B2B Buyers?
When dealing with suppliers across different regions, B2B buyers must understand the nuances of quality control certifications. For instance:
- In Europe, the CE mark indicates conformity with health, safety, and environmental protection standards. Buyers in Europe should prioritize suppliers with this certification.
- In Africa and South America, local regulations may differ significantly, and buyers should ensure suppliers comply with regional standards.
By being aware of these nuances, buyers can make more informed decisions and mitigate risks associated with quality issues.
Conclusion: Why Is Understanding Manufacturing and Quality Assurance Crucial for B2B Buyers?
In conclusion, a comprehensive understanding of the manufacturing processes and quality assurance practices for drum mixers is essential for B2B buyers. By focusing on material preparation, forming techniques, assembly, finishing, and rigorous quality control measures, buyers can ensure they select reliable suppliers that meet their specific needs. Additionally, familiarity with international standards and effective verification methods enhances the procurement process, ultimately leading to better operational efficiency and product satisfaction.
Practical Sourcing Guide: A Step-by-Step Checklist for ‘drum mixer’
The following is a practical sourcing guide designed for B2B buyers looking to procure drum mixers. This checklist outlines essential steps to ensure you choose the right equipment tailored to your specific operational needs.
Step 1: Define Your Technical Specifications
Identifying your technical requirements is crucial for selecting the appropriate drum mixer. Consider factors such as the type of materials you will be mixing (e.g., low vs. high viscosity), the volume of the drums (commonly 55-gallon), and the desired mixing intensity. Knowing these specifications helps narrow down your options and prevents costly mismatches.
- Material Compatibility: Ensure the mixer can handle the chemical properties of the materials being mixed.
- Mixing Method: Determine if you need a clamp mount, bung mount, or lid mount mixer based on your mixing environment.
Step 2: Research Market Options
Conduct thorough market research to understand the various drum mixer options available. Explore different brands, models, and suppliers to identify the best fit for your needs.
- Supplier Reputation: Look for suppliers with a strong reputation in your industry.
- Product Range: Ensure the supplier offers a variety of models to choose from.
Step 3: Evaluate Potential Suppliers
Before making a commitment, vet potential suppliers thoroughly. Request company profiles, case studies, and references from buyers in a similar industry or region.
- Ask for Certifications: Verify that the supplier adheres to industry standards and has the necessary certifications.
- Check Reviews: Read customer reviews to gauge the reliability and performance of their drum mixers.
Step 4: Request Quotes and Compare Pricing
Once you have shortlisted potential suppliers, request detailed quotes for the drum mixers that meet your specifications. Comparing pricing is essential for budget management.
- Inclusions in Quotes: Ensure quotes include shipping costs, warranty details, and after-sales support.
- Price Versus Value: Consider the overall value rather than just the price; sometimes, a higher-priced option may offer better longevity or efficiency.
Step 5: Assess After-Sales Support and Service
Understanding the after-sales support available is crucial for long-term satisfaction with your purchase. Evaluate the supplier’s service offerings and response times.
- Warranty Terms: Inquire about warranty coverage and what it includes.
- Technical Support: Ensure that the supplier offers accessible technical support for troubleshooting.
Step 6: Conduct a Final Review
Before finalizing your purchase, conduct a comprehensive review of all gathered information. Confirm that the selected drum mixer aligns with your operational needs and budget constraints.
- Cross-Check Specifications: Revisit your initial specifications to ensure the chosen model meets all requirements.
- Final Negotiations: Don’t hesitate to negotiate the terms if necessary, especially if you are placing a large order.
Step 7: Place Your Order
Once all criteria are met and satisfaction is achieved, proceed with placing your order. Ensure that you receive a confirmation that details your purchase agreement.
- Document Everything: Keep records of all transactions, communications, and agreements for future reference.
- Follow Up: Stay in touch with the supplier for updates on your order status and delivery schedule.
Following this checklist will help ensure a smooth procurement process for your drum mixer, allowing you to make an informed decision that best meets your operational needs.
Comprehensive Cost and Pricing Analysis for drum mixer Sourcing
What Are the Key Cost Components in Drum Mixer Sourcing?
When sourcing drum mixers, B2B buyers must consider several cost components that significantly influence the overall price. These components include:
-
Materials: The type of materials used in manufacturing drum mixers directly impacts the cost. High-quality stainless steel or specialized alloys for corrosion resistance may elevate prices compared to standard materials.
-
Labor: Labor costs can vary based on the region of production. For instance, sourcing from countries with lower labor costs may reduce the overall price, but this could also affect quality and lead times.
-
Manufacturing Overhead: This includes costs associated with factory operations, such as utilities, equipment maintenance, and administrative expenses. Efficient production processes can help keep these costs down.
-
Tooling: The initial investment in molds and machinery can be substantial, especially for custom or specialized mixers. Buyers should inquire about tooling costs if they require unique specifications.
-
Quality Control (QC): Investing in rigorous QC processes ensures that the mixers meet industry standards. While this may add to the cost, it can prevent future issues and enhance reliability.
-
Logistics: Transportation costs, including shipping and handling, can vary significantly based on the distance from the manufacturer to the buyer. Import duties and customs fees must also be factored in, particularly for international buyers.
-
Margin: Suppliers typically include a profit margin in their pricing. Understanding the industry standard margins can aid buyers in negotiating better prices.
How Do Price Influencers Affect Drum Mixer Costs?
Several factors can influence the pricing of drum mixers, particularly for international B2B buyers:
-
Volume/MOQ (Minimum Order Quantity): Larger orders often attract bulk discounts, which can significantly reduce the per-unit cost. Buyers should assess their needs and consider consolidating orders to leverage volume pricing.
-
Specifications and Customization: Custom features such as specialized impeller designs or unique power sources can increase costs. Buyers should weigh the benefits of customization against the additional costs.
-
Materials and Quality Certifications: Higher-grade materials and compliance with international quality certifications (like ISO or CE) can elevate prices. However, these investments are often justified by longer service life and better performance.
-
Supplier Factors: The supplier’s reputation, production capacity, and financial stability can influence pricing. Established suppliers may charge a premium for reliability and service.
-
Incoterms: Understanding Incoterms (International Commercial Terms) is crucial for international buyers. These terms define the responsibilities of buyers and sellers regarding shipping, insurance, and tariffs, which can affect the overall cost.
What Tips Can Help Buyers Optimize Drum Mixer Costs?
B2B buyers should consider the following tips to optimize costs and enhance value in their drum mixer sourcing:
-
Negotiate Effectively: Establish clear communication with suppliers and be prepared to negotiate prices based on volume and long-term partnership potential. Highlighting your commitment to ongoing business can encourage suppliers to offer better pricing.
-
Evaluate Total Cost of Ownership (TCO): Beyond the initial purchase price, consider maintenance, operational efficiency, and potential downtime costs. A higher upfront investment in a durable, high-quality mixer could yield significant savings over time.
-
Understand Pricing Nuances for International Buyers: Buyers from regions such as Africa, South America, the Middle East, and Europe should be aware of fluctuations in exchange rates, tariffs, and shipping costs. These factors can dramatically affect the total landed cost of equipment.
-
Seek Multiple Quotes: Don’t settle for the first quote. Obtaining multiple quotes from different suppliers can provide a clearer picture of the market price and help identify the best deal.
-
Stay Informed About Market Trends: Keeping abreast of market conditions, such as supply chain disruptions or material shortages, can help buyers anticipate price changes and make informed purchasing decisions.
Disclaimer on Indicative Prices
Prices for drum mixers can vary widely based on the aforementioned factors and are subject to change. The prices mentioned in various sources should be considered indicative, and buyers are encouraged to conduct thorough market research and obtain quotes tailored to their specific requirements.
Alternatives Analysis: Comparing drum mixer With Other Solutions
When evaluating the best solution for mixing liquids in industrial applications, it’s essential to consider not only the drum mixer but also alternative technologies that may fulfill similar roles. This analysis will help international B2B buyers, particularly in Africa, South America, the Middle East, and Europe, make informed decisions based on their specific operational needs.
Comparison Table of Mixing Solutions
Comparison Aspect | Drum Mixer | Inline Mixer | Portable Mixer |
---|---|---|---|
Performance | Efficient for low to medium viscosity | Suitable for high viscosity and continuous flow | Good for small batches and field use |
Cost | Moderate initial investment | Higher upfront costs | Generally lower cost |
Ease of Implementation | Simple to set up and use | Requires installation and plumbing | Highly portable, minimal setup needed |
Maintenance | Low maintenance, easy to clean | Moderate, may require professional service | Low maintenance, easy to clean |
Best Use Case | Ideal for batch processing in drums | Best for continuous production lines | Excellent for temporary or small-scale operations |
What Are the Advantages and Disadvantages of an Inline Mixer?
Inline mixers are designed for continuous mixing processes and can handle various viscosities, making them a robust alternative to drum mixers. Their main advantage is their ability to integrate seamlessly into existing piping systems, providing consistent results without the need for batch processing. However, the initial investment can be significantly higher, and they require more complex installation and maintenance procedures. Inline mixers are best suited for companies that need a constant supply of mixed materials and have the infrastructure to support them.
How Does a Portable Mixer Compare to a Drum Mixer?
Portable mixers are excellent for applications where flexibility is crucial, such as in small batch production or on-site mixing. They are generally less expensive than drum mixers and are easy to transport, making them suitable for various locations. However, they may not provide the same level of mixing efficiency for larger volumes and can be less effective for high-viscosity materials. Portable mixers are ideal for companies looking for versatility and cost-effectiveness without the need for a permanent installation.
Conclusion: How Should International B2B Buyers Choose the Right Mixing Solution?
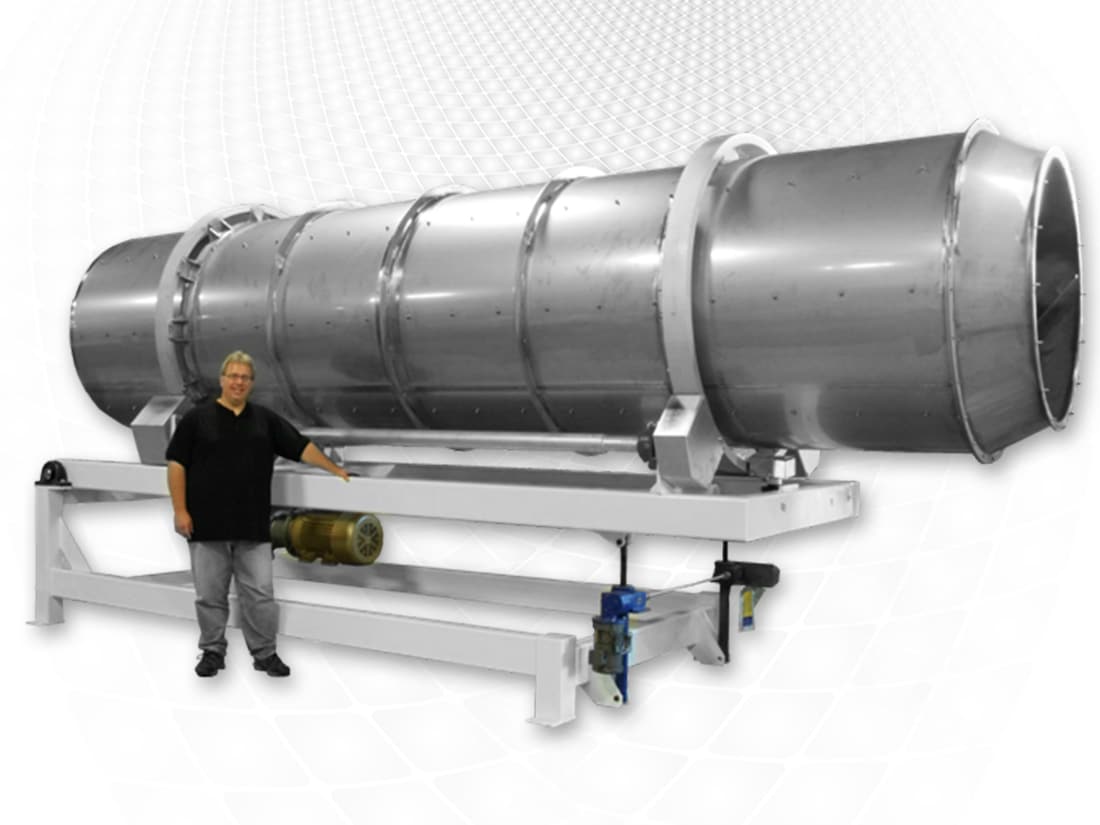
A stock image related to drum mixer.
When selecting the appropriate mixing solution, international B2B buyers should assess their specific needs, including batch size, viscosity of materials, and operational context. Drum mixers are often the go-to choice for companies processing materials in 55-gallon drums, offering a balance of performance and cost-effectiveness. However, for operations requiring continuous mixing or flexibility, inline and portable mixers present viable alternatives. Evaluating the total cost of ownership, including maintenance and operational efficiency, will further guide buyers in making the best decision for their mixing needs.
Essential Technical Properties and Trade Terminology for drum mixer
What Are the Key Technical Properties of Drum Mixers for B2B Buyers?
Understanding the technical properties of drum mixers is crucial for B2B buyers to make informed purchasing decisions. Here are some essential specifications to consider:
-
Material Grade
Drum mixers are typically constructed from materials like stainless steel, aluminum, or high-grade plastics. The choice of material affects durability, corrosion resistance, and suitability for specific applications. For instance, stainless steel is ideal for chemical processing due to its resistance to corrosion, making it a preferred choice for industries in the Middle East and Africa that deal with harsh environments. -
Power Source
The power source of a drum mixer can be electric, pneumatic, or hydraulic. Each has its advantages; electric mixers are often more efficient and easier to maintain, while pneumatic mixers are preferred in environments where electrical hazards exist. Understanding the power requirements helps buyers ensure compatibility with existing equipment and operational needs. -
Viscosity Rating
Drum mixers are designed to handle various viscosity levels, indicated in centipoise (cps). Knowing the viscosity of the materials being mixed allows buyers to select the appropriate mixer type. For example, a mixer capable of handling high-viscosity liquids will be necessary for industries such as food processing or cosmetics, prevalent in South America and Europe. -
Mounting Type
There are several mounting options available for drum mixers, including bung mount, clamp mount, and bracket mount. Each type offers different advantages depending on the drum design and mixing requirements. For example, bung-mounted mixers allow for mixing without exposing the contents to the air, which is beneficial for sensitive materials. -
Impeller Design
The impeller design significantly influences mixing efficiency and effectiveness. Impellers can be classified as low-shear or high-shear, depending on the application. Low-shear impellers are suitable for gentle mixing, while high-shear impellers are necessary for emulsifying or dispersing materials. Buyers must consider the nature of their products when selecting an impeller type. -
Speed Control
Variable speed control allows for greater flexibility in the mixing process. Being able to adjust the mixer speed according to the viscosity of the material can enhance product quality. Buyers in industries such as pharmaceuticals or chemicals, where precise formulations are critical, should prioritize mixers with adjustable speed settings.
What Are Common Trade Terms Related to Drum Mixers?
Familiarity with industry terminology can greatly aid B2B buyers in negotiations and procurement processes. Here are some key terms to know:
-
OEM (Original Equipment Manufacturer)
This term refers to companies that produce equipment that may be marketed by another company. Understanding OEM relationships can help buyers identify trusted suppliers and assess product quality, especially when sourcing mixers for specific applications. -
MOQ (Minimum Order Quantity)
MOQ refers to the smallest quantity of a product that a supplier is willing to sell. For international buyers, knowing the MOQ is essential for budgeting and ensuring they meet supplier requirements. This is particularly relevant for buyers from regions like Africa and South America, where import costs can be significant. -
RFQ (Request for Quotation)
An RFQ is a document sent to suppliers requesting pricing for specified goods or services. Issuing an RFQ can help buyers compare prices and ensure they receive competitive offers, which is crucial for managing costs in competitive markets. -
Incoterms (International Commercial Terms)
These are a series of pre-defined commercial terms published by the International Chamber of Commerce, which clarify the responsibilities of buyers and sellers in international trade. Familiarity with Incoterms can help buyers from Europe, Africa, and the Middle East navigate shipping logistics and responsibilities effectively. -
Lead Time
Lead time refers to the amount of time it takes from placing an order until the product is received. Understanding lead times is essential for inventory management and ensuring timely project completion, especially in industries where delays can be costly. -
Warranty Period
The warranty period is the duration during which the manufacturer guarantees the product against defects. Knowing the warranty terms helps buyers assess the long-term value and reliability of their investment in drum mixers, which is crucial for maintaining operational efficiency.
By grasping these technical properties and trade terms, B2B buyers can enhance their procurement strategies and make informed decisions that align with their operational needs.
Navigating Market Dynamics and Sourcing Trends in the drum mixer Sector
What Are the Key Market Dynamics and Trends in the Drum Mixer Sector?
The drum mixer market is experiencing significant growth, driven by various global factors. As industries worldwide seek to enhance efficiency and reduce operational costs, the trend of mixing directly in the original drums is becoming more prevalent. This method minimizes transfer waste and capital investment, making it an attractive choice for manufacturers across sectors such as chemicals, food and beverage, and pharmaceuticals. For international B2B buyers, particularly in regions like Africa, South America, the Middle East, and Europe, understanding these dynamics is crucial for making informed sourcing decisions.
Emerging technologies are also shaping the drum mixer landscape. The integration of IoT (Internet of Things) for real-time monitoring and control is gaining traction, enabling manufacturers to optimize their mixing processes. Additionally, automation is becoming increasingly important, with advanced mixers featuring programmable settings that cater to specific product requirements. This shift towards automation not only improves consistency but also enhances safety in production environments.
Another notable trend is the growing demand for customized solutions. As diverse industries require mixers tailored to their unique applications, suppliers are expanding their product lines to include various mounting methods and impeller types. Buyers from diverse markets must evaluate their specific needs and seek suppliers who offer flexible and adaptable solutions.
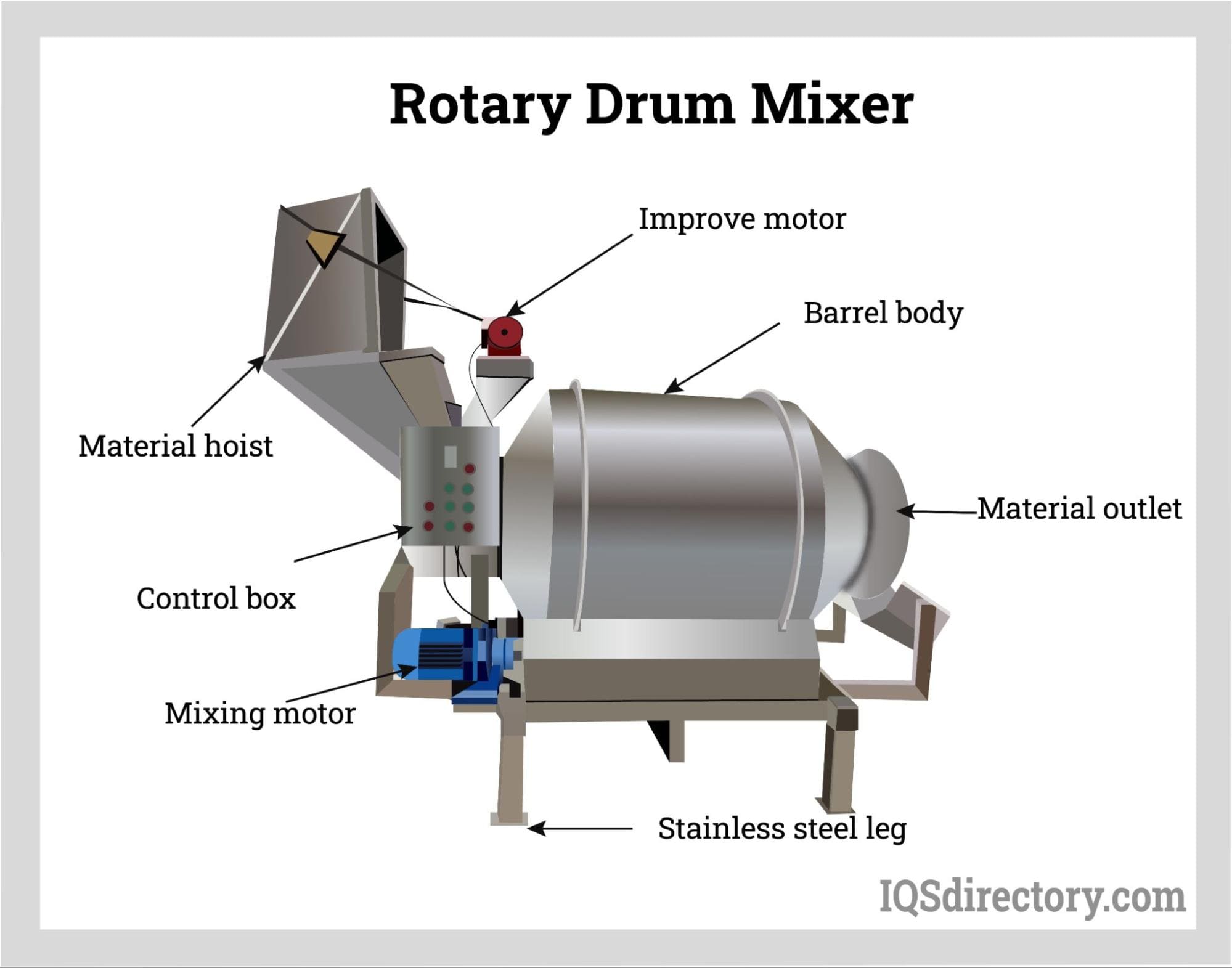
A stock image related to drum mixer.
How Is Sustainability Influencing B2B Sourcing in the Drum Mixer Sector?
Sustainability is becoming a central focus for B2B buyers in the drum mixer sector. As environmental regulations tighten and consumers become more environmentally conscious, companies are compelled to adopt sustainable practices throughout their supply chains. For international buyers, particularly those in emerging markets, this means prioritizing suppliers who demonstrate a commitment to reducing their environmental impact.
One critical aspect of sustainable sourcing is the use of eco-friendly materials and processes in manufacturing drum mixers. Buyers should look for products that incorporate recyclable materials and energy-efficient manufacturing processes. Additionally, suppliers with green certifications, such as ISO 14001, can provide assurance of their environmental management practices.
Ethical sourcing is equally important. Buyers are encouraged to conduct thorough due diligence on their suppliers to ensure that labor practices are ethical and that the production processes do not harm local communities. By prioritizing sustainability and ethical sourcing, businesses not only enhance their brand reputation but also align with the values of an increasingly discerning consumer base.
How Has the Drum Mixer Sector Evolved Over Time?
The evolution of the drum mixer sector reflects broader technological advancements and changing market demands. Initially, drum mixers were basic mechanical devices designed primarily for mixing low-viscosity liquids. However, as industries began to diversify and the need for more complex mixing solutions emerged, manufacturers responded by developing a range of innovative mixers capable of handling various viscosities and product types.
In recent years, the introduction of electric and pneumatic-powered mixers has transformed the sector, providing users with greater efficiency and control. The development of specialized impeller designs has further enhanced mixing capabilities, allowing for improved performance in challenging applications. This evolution continues to shape the offerings available to international B2B buyers, who must stay informed about the latest technological advancements and market trends to make effective sourcing decisions.
Frequently Asked Questions (FAQs) for B2B Buyers of drum mixer
-
How do I choose the right drum mixer for my specific needs?
Choosing the right drum mixer involves understanding your material’s viscosity, the drum type, and the desired mixing outcome. For high-viscosity liquids, consider gear-driven mixers that provide more torque. If you’re dealing with low-viscosity materials, direct drive mixers may suffice. Additionally, evaluate the mounting options—bung mount, clamp mount, or lid mount—based on your operational requirements. Always consult with suppliers to get advice tailored to your specific applications and materials. -
What is the best drum mixer for high-viscosity materials?
For high-viscosity materials, a gear-driven drum mixer is often the best choice. These mixers provide higher torque and are capable of effectively blending thick substances. Look for models with adjustable speed settings to accommodate varying material densities. It’s also crucial to consider impeller design; a high-shear impeller can enhance mixing efficiency. Brands offering custom solutions may provide models specifically designed for your unique materials, ensuring optimal performance. -
What should I consider when sourcing drum mixers internationally?
When sourcing drum mixers internationally, consider the reliability of the supplier, their production capabilities, and compliance with international standards. Evaluate their experience with exporting to your region, particularly in terms of customs regulations. Request product certifications and quality assurance documentation. It’s also important to assess shipping logistics and timelines, as well as potential tariffs or duties that may apply to your order, which can affect overall costs. -
How can I ensure quality when purchasing a drum mixer from a new supplier?
To ensure quality when purchasing from a new supplier, conduct a thorough vetting process. Start by requesting samples or detailed specifications of the drum mixer. Ask for references from previous clients, especially those in your industry. Verify the supplier’s certifications and quality assurance practices, and consider visiting their manufacturing facility if feasible. Additionally, establish clear communication channels to address any concerns and confirm their commitment to quality throughout the production process. -
What are the typical minimum order quantities (MOQs) for drum mixers?
Minimum order quantities (MOQs) for drum mixers can vary widely depending on the supplier and the complexity of the product. Generally, manufacturers may set MOQs ranging from 10 to 50 units for standard models. Custom or specialized drum mixers may have higher MOQs due to the additional resources required for production. Always discuss MOQs with suppliers upfront and negotiate terms that align with your business needs and inventory management strategies. -
What payment terms are common for international drum mixer purchases?
Common payment terms for international drum mixer purchases typically include options such as advance payment, letter of credit (LC), or payment upon delivery. Many suppliers may require a deposit (often 30-50%) upfront, with the balance due before shipping or upon receipt of goods. It’s crucial to clarify these terms in advance and ensure they align with your cash flow capabilities. Additionally, consider using secure payment methods to protect your investment. -
How can I handle logistics and shipping for drum mixers purchased overseas?
Handling logistics and shipping for overseas drum mixers involves careful planning and coordination with your supplier. Discuss preferred shipping methods—air freight is faster but more expensive, while sea freight is cost-effective for larger orders. Work with freight forwarders experienced in handling industrial equipment to navigate customs clearance and ensure compliance with local regulations. Always factor in lead times and potential delays, especially in peak shipping seasons, to avoid disruptions in your supply chain. -
What is the warranty and support typically offered with drum mixers?
Warranties and support for drum mixers vary by manufacturer but generally cover defects in materials and workmanship. Most suppliers offer warranties ranging from one to three years. It’s vital to inquire about the specifics of the warranty, including any exclusions or conditions. Additionally, check if the supplier provides technical support, replacement parts, or maintenance services post-purchase. Establishing a good relationship with your supplier can facilitate smoother support and service interactions in the future.
Important Disclaimer & Terms of Use
⚠️ Important Disclaimer
The information provided in this guide, including content regarding manufacturers, technical specifications, and market analysis, is for informational and educational purposes only. It does not constitute professional procurement advice, financial advice, or legal advice.
While we have made every effort to ensure the accuracy and timeliness of the information, we are not responsible for any errors, omissions, or outdated information. Market conditions, company details, and technical standards are subject to change.
B2B buyers must conduct their own independent and thorough due diligence before making any purchasing decisions. This includes contacting suppliers directly, verifying certifications, requesting samples, and seeking professional consultation. The risk of relying on any information in this guide is borne solely by the reader.
Strategic Sourcing Conclusion and Outlook for drum mixer
In conclusion, strategic sourcing of drum mixers is essential for international B2B buyers aiming to enhance operational efficiency and reduce costs. Understanding the diverse range of drum mixers available—such as bung mount, clamp mount, and lid mount mixers—enables businesses to select the most suitable equipment for their specific applications, whether dealing with low or high-viscosity liquids. Furthermore, investing in mixers that minimize transfer waste while maximizing productivity can significantly impact the bottom line.
How Can Strategic Sourcing of Drum Mixers Benefit Your Business?
By leveraging strategic sourcing, companies can negotiate better pricing, ensure quality, and establish reliable supply chains. This is particularly crucial for buyers in regions like Africa, South America, the Middle East, and Europe, where local sourcing may be limited.
What Should You Consider for Future Investments in Drum Mixers?
As you look towards the future, consider the advancements in mixer technology that promise greater energy efficiency and improved mixing capabilities. This proactive approach not only prepares your business for upcoming market demands but also positions you as a leader in your sector.
We encourage you to engage with suppliers to explore tailored solutions that meet your unique requirements and drive your business forward in an increasingly competitive landscape.