Maximize Efficiency: The Ultimate Lab Table Guide (2025)
Introduction: Navigating the Global Market for lab table
Navigating the complexities of sourcing lab tables can be a daunting task for international B2B buyers, especially when considering factors such as functionality, durability, and compliance with local regulations. Whether you are looking to equip a new laboratory or upgrade existing facilities, understanding the diverse range of lab tables available is crucial. This comprehensive guide will explore various types of lab tables, their applications, and essential features like corrosion resistance and adjustable heights, tailored to meet the specific needs of laboratories across Africa, South America, the Middle East, and Europe, including markets like Germany and Colombia.
In this guide, we will provide actionable insights on supplier vetting, helping you identify reliable manufacturers and distributors who can meet your unique specifications. We will also delve into cost considerations, ensuring you are equipped to make informed purchasing decisions that align with your budget and operational requirements. By the end of this guide, you will have a clear understanding of how to navigate the global market for lab tables, empowering you to select the right solutions that enhance productivity and safety in your laboratory environments. Whether you are a seasoned procurement professional or new to the market, this resource is designed to support your journey in making smart, strategic investments in laboratory furniture.
Understanding lab table Types and Variations
Type Name | Key Distinguishing Features | Primary B2B Applications | Brief Pros & Cons for Buyers |
---|---|---|---|
Fixed Height Lab Table | Non-adjustable height, sturdy construction, various tops | Research labs, educational institutions | Pros: Durable, stable; Cons: Limited flexibility in height adjustment. |
Adjustable Height Lab Table | Height can be modified, often ergonomic designs | Versatile lab environments, collaborative spaces | Pros: Customizable for different users; Cons: Typically more expensive. |
Mobile Lab Table | Equipped with casters for easy movement | Temporary labs, mobile testing units | Pros: Flexibility in layout; Cons: May be less stable than stationary tables. |
Chemical-Resistant Lab Table | Special materials that resist corrosion and chemicals | Chemistry labs, pharmaceutical sectors | Pros: Enhanced safety and longevity; Cons: Higher initial investment. |
Multi-Station Workbench | Designed for multiple users, often with storage options | Educational labs, industrial settings | Pros: Maximizes space efficiency; Cons: May require more maintenance and cleaning. |
What Are the Characteristics of Fixed Height Lab Tables?
Fixed height lab tables are designed to provide a stable working surface, typically at a standard height. They are ideal for environments where the tasks performed require consistent height, such as in research labs or educational settings. Buyers should consider the durability of materials used, as these tables often experience heavy use. While they offer stability, the lack of height adjustability can be a limitation for varied user needs.
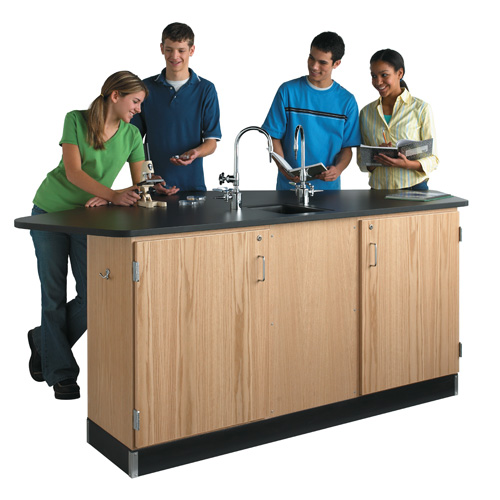
A stock image related to lab table.
Why Choose Adjustable Height Lab Tables for Your Lab?
Adjustable height lab tables cater to diverse user needs by allowing height modifications. This feature is particularly beneficial in collaborative environments where multiple users may require different working heights. When purchasing, consider the mechanism for adjustment, as well as the stability and weight capacity of the table. The investment in adjustable tables can lead to improved ergonomics and user satisfaction, albeit at a higher cost.
How Do Mobile Lab Tables Enhance Laboratory Flexibility?
Mobile lab tables are designed with casters, enabling easy movement within a lab space. They are especially useful in settings where the layout may frequently change or where temporary setups are required, such as in field testing or workshops. Buyers should assess the quality of the wheels and the stability of the table when in motion. While they provide excellent flexibility, mobile tables may sacrifice some stability compared to fixed options.
What Makes Chemical-Resistant Lab Tables Essential?
Chemical-resistant lab tables are constructed from materials that withstand corrosive substances, making them crucial in chemistry and pharmaceutical labs. When selecting these tables, it is important to evaluate the specific chemical resistance of the materials used and the table’s overall durability. Although they may come with a higher price tag, the long-term safety and longevity they provide can justify the investment.
Why Opt for Multi-Station Workbenches in Collaborative Labs?
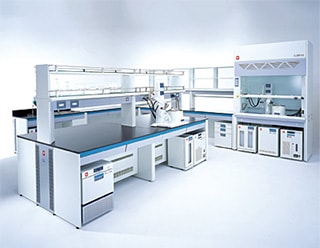
A stock image related to lab table.
Multi-station workbenches are designed to accommodate several users simultaneously, often featuring built-in storage solutions. They are particularly advantageous in educational and industrial settings where multiple experiments or projects are conducted at once. When considering these workbenches, buyers should evaluate the layout and accessibility of storage spaces. While they optimize space usage, they may require more frequent maintenance due to higher user traffic.
Key Industrial Applications of lab table
Industry/Sector | Specific Application of Lab Table | Value/Benefit for the Business | Key Sourcing Considerations for this Application |
---|---|---|---|
Pharmaceutical | Drug formulation and testing | Ensures precision and safety in drug development | Chemical-resistant surfaces, ergonomic designs, and mobility |
Education | STEM education and laboratory training | Facilitates hands-on learning and experimentation | Adjustable height options, durable materials, and safety features |
Food and Beverage | Quality control and testing | Enhances product safety and compliance with regulations | Sanitary materials, easy cleaning surfaces, and storage solutions |
Environmental Testing | Sample analysis and research | Supports accurate data collection for environmental assessments | Robust construction, chemical resistance, and mobility options |
Research and Development (R&D) | Prototype development and material testing | Accelerates innovation and product development | Customizable layouts, modularity, and access to utilities |
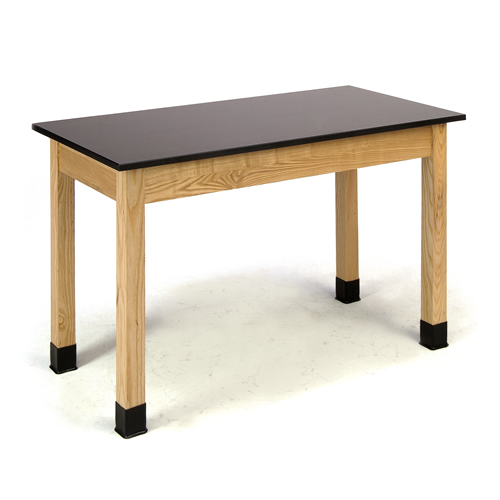
A stock image related to lab table.
How are Lab Tables Used in the Pharmaceutical Sector?
In the pharmaceutical industry, lab tables are vital for drug formulation and testing. These tables often feature chemical-resistant surfaces to safely handle reagents and samples, minimizing contamination risks. International buyers should prioritize ergonomic designs that support long working hours and mobility for easy reconfiguration of lab spaces. Ensuring compliance with safety standards is crucial, especially in regions with stringent regulations.
What Role Do Lab Tables Play in Education?
In educational settings, particularly in STEM programs, lab tables facilitate hands-on learning experiences. These tables can be adjusted in height to accommodate various age groups, promoting inclusivity in laboratory activities. For buyers in Africa and South America, sourcing durable and safe lab tables is essential to withstand the rigors of student use. Additionally, tables with integrated storage solutions help maintain an organized learning environment.
How are Lab Tables Utilized in Food and Beverage Industries?
Lab tables in the food and beverage sector are primarily used for quality control and testing. They must be constructed from sanitary materials that are easy to clean and maintain, ensuring compliance with health regulations. For buyers in the Middle East and Europe, sourcing tables that meet local food safety standards is paramount. Additionally, tables with integrated storage options can streamline workflows in testing environments.
Why Are Lab Tables Important for Environmental Testing?
In environmental testing, lab tables provide a stable platform for sample analysis and research. These tables should be robust and resistant to chemicals, as they often handle hazardous materials. Buyers from Europe and Africa should consider mobility options for flexible lab setups and ensure that the tables can accommodate necessary utilities for specialized testing equipment. Compliance with environmental regulations is also a key consideration.
How Do Lab Tables Support Research and Development?
In R&D settings, lab tables are crucial for prototype development and material testing. They offer customizable layouts that can adapt to various project needs, enhancing collaboration among researchers. International buyers should look for tables that can accommodate specialized equipment and provide access to utilities such as gas and electricity. The ability to easily reconfigure lab spaces is vital for fostering innovation and accelerating product development.
3 Common User Pain Points for ‘lab table’ & Their Solutions
Scenario 1: Difficulty in Choosing the Right Material for Lab Tables
The Problem: B2B buyers often struggle with selecting the appropriate materials for lab tables that can withstand specific laboratory conditions. For instance, in regions where chemical exposure is prevalent, such as in the pharmaceutical or chemical industries, choosing a table that is resistant to corrosion and easy to clean is crucial. Buyers may face uncertainty about the durability of materials like phenolic resin versus stainless steel, leading to potential long-term costs if the wrong choice is made.
The Solution: To effectively address this challenge, buyers should conduct a thorough analysis of their laboratory’s specific needs. Consider the types of chemicals and reagents that will be used on the lab tables. For environments with heavy chemical use, investing in tables with phenolic resin tops can provide better chemical resistance compared to traditional laminate tops. Additionally, buyers should consult with manufacturers or suppliers to obtain detailed specifications regarding the chemical resistance of different materials. Engaging in direct conversations about past performance in similar environments can also help inform their decision. Lastly, opting for suppliers that offer warranties or guarantees on their products can provide added assurance against material failure.
Scenario 2: Space Constraints and Layout Challenges in Laboratories
The Problem: Many laboratories, especially in urban settings or smaller institutions, face significant spatial constraints. B2B buyers may find that standard lab tables do not fit well within their available space, leading to inefficient workflows and overcrowded work areas. Inadequate planning can result in safety hazards and reduced productivity, which is particularly concerning in high-stakes environments such as medical or research labs.
The Solution: To overcome space limitations, buyers should consider investing in modular or customizable lab tables that can be adapted to fit their unique layouts. Prior to purchase, they should assess the dimensions of their workspace and create a detailed floor plan that includes all necessary equipment and workstations. It’s beneficial to involve lab personnel in this planning phase to ensure that the design meets their practical needs. Additionally, choosing tables with adjustable heights or mobile units can offer flexibility in reconfiguring the space as requirements change. Collaborating with suppliers who specialize in laboratory design can yield tailored solutions that maximize efficiency while adhering to safety regulations.
Scenario 3: Compliance with Health and Safety Regulations
The Problem: Navigating the complex landscape of health and safety regulations is a significant pain point for B2B buyers of lab tables. Different regions, particularly in Africa and the Middle East, may have varying compliance requirements regarding laboratory furniture. Buyers may be overwhelmed by the need to ensure that their lab tables meet standards such as fire resistance, chemical safety, and ergonomic design, which can be difficult to verify at the point of sale.
The Solution: To effectively manage compliance issues, buyers should familiarize themselves with both local and international safety standards relevant to laboratory equipment. This includes researching guidelines from organizations such as the International Organization for Standardization (ISO) and local regulatory bodies. When sourcing lab tables, buyers should prioritize manufacturers that provide clear documentation and certifications proving compliance with these standards. It’s also advisable to conduct thorough due diligence by reviewing customer testimonials and case studies that highlight a manufacturer’s track record with compliance. Engaging with a safety consultant during the procurement process can further ensure that all necessary regulations are adhered to, reducing the risk of costly penalties or safety incidents down the line.
Strategic Material Selection Guide for lab table
When selecting materials for laboratory tables, it is crucial to consider their properties, advantages, disadvantages, and how they align with specific applications. Below, we analyze four common materials used in lab tables, providing actionable insights for international B2B buyers, particularly those from Africa, South America, the Middle East, and Europe.
What are the Key Properties of Stainless Steel for Lab Tables?
Stainless steel is renowned for its exceptional durability and corrosion resistance, making it an ideal choice for laboratory environments where chemicals and moisture are prevalent. Its temperature resistance allows it to withstand extreme conditions, which is essential for labs dealing with high-temperature processes.
Pros: Stainless steel is easy to clean and maintain, ensuring hygiene standards are met. It also has a long lifespan, which reduces replacement costs over time.
Cons: The initial cost of stainless steel tables can be high, and they may be prone to scratching, which can compromise their aesthetic appeal.
Impact on Application: Stainless steel is compatible with a wide range of chemicals, making it suitable for various laboratory applications, including biological and chemical labs.
Considerations for International Buyers: Compliance with standards such as ASTM and DIN is important. Buyers should also consider local regulations regarding material sourcing and environmental impact.
How Does Phenolic Resin Perform in Laboratory Settings?
Phenolic resin is a synthetic polymer that offers excellent chemical resistance and durability. It is particularly effective in environments where exposure to harsh chemicals is common.
Pros: Phenolic resin surfaces are non-porous, making them resistant to stains and easy to clean. They also have good thermal stability, which is beneficial for labs that conduct heat-intensive experiments.
Cons: While phenolic resin is durable, it can be more susceptible to chipping and cracking compared to metal options. Additionally, it may have a limited lifespan in extremely high-temperature applications.
Impact on Application: This material is highly suitable for chemistry labs where corrosive substances are handled, as it can withstand a variety of chemicals without degrading.
Considerations for International Buyers: Buyers should ensure that the phenolic resin meets local safety and quality standards, which can vary by region.
What are the Advantages of Laminate Surfaces for Lab Tables?
Laminate surfaces are made from layers of paper or fabric impregnated with resin, creating a durable and aesthetically pleasing surface for lab tables.
Pros: Laminate surfaces are cost-effective and available in various colors and finishes, allowing for customization. They are also easy to clean and resistant to scratches and stains.
Cons: Laminate surfaces may not be as durable as metal options and can be damaged by heat or heavy impacts. They are also less suitable for high-chemical exposure environments.
Impact on Application: Laminate tables are ideal for educational labs or environments where chemical exposure is minimal, making them suitable for classroom settings or light research.
Considerations for International Buyers: Ensure that the laminate meets relevant standards for fire and chemical resistance, especially in regions with strict safety regulations.
Why Choose Wood for Laboratory Tables?
Wood, particularly hardwoods like oak and maple, is a traditional choice for laboratory tables, offering a warm aesthetic and reasonable durability.
Pros: Wood is generally less expensive than metal options and provides a sturdy work surface. It is also easier to work with during installation and customization.
Cons: Wood is susceptible to moisture and chemical damage, which can compromise its integrity over time. It also requires regular maintenance to prevent wear and tear.
Impact on Application: Wooden tables are best suited for labs that do not involve harsh chemicals or high moisture levels, such as educational environments or art labs.
Considerations for International Buyers: Buyers should verify that the wood is sourced sustainably and complies with local regulations regarding chemical treatments and finishes.
Summary Table of Material Selection for Lab Tables
Material | Typical Use Case for lab table | Key Advantage | Key Disadvantage/Limitation | Relative Cost (Low/Med/High) |
---|---|---|---|---|
Stainless Steel | Chemical and biological labs | High durability and corrosion resistance | High initial cost | High |
Phenolic Resin | Chemistry labs with harsh chemicals | Excellent chemical resistance | Prone to chipping | Medium |
Laminate | Educational labs and light research | Cost-effective and customizable | Less durable under heavy use | Low |
Wood | Educational or art labs | Aesthetic appeal and easy customization | Susceptible to moisture damage | Medium |
This guide provides a comprehensive overview of material options for lab tables, enabling international B2B buyers to make informed decisions based on their specific needs and compliance requirements.
In-depth Look: Manufacturing Processes and Quality Assurance for lab table
What Are the Main Stages of Manufacturing Lab Tables?
The manufacturing process of lab tables involves several key stages designed to ensure that the final product meets safety, durability, and functionality standards.
1. Material Preparation
The first stage in the manufacturing process is material preparation. This involves selecting high-quality materials such as stainless steel, hardwoods, or specialized laminates. Suppliers often prioritize corrosion-resistant and chemical-resistant materials due to the demanding environment of laboratories. Before the materials are processed, they undergo rigorous inspection to ensure they meet specified standards.
2. Forming
The next step is forming, where raw materials are cut, shaped, and molded into the desired components of the lab table. Techniques such as laser cutting for metal parts and CNC machining for wooden components are commonly employed. This precision is essential for ensuring that all parts fit together correctly during assembly.
3. Assembly
During assembly, the formed components are joined together. This stage may involve welding for metal frames, glueing and fastening for wooden parts, and installing any necessary fixtures such as sinks, power outlets, or storage options. The assembly process is critical as it directly impacts the durability and functionality of the lab table.
4. Finishing
Finishing is the final stage of manufacturing. This may include sanding, painting, or applying protective coatings to enhance the table’s appearance and longevity. Quality finishes also contribute to safety by providing smooth surfaces that are easy to clean and resistant to chemical spills.
How Is Quality Assurance Implemented in Lab Table Manufacturing?
Quality assurance (QA) is integral to the manufacturing process, ensuring that every lab table produced meets both international and industry-specific standards.
Relevant International Standards for Quality Assurance
International standards such as ISO 9001 play a vital role in the manufacturing process. ISO 9001 sets the criteria for a quality management system, emphasizing a process approach for continuous improvement. Additionally, industry-specific certifications such as CE marking (indicating conformity with health, safety, and environmental protection standards) and API (American Petroleum Institute) standards for oil and gas applications may also be applicable depending on the intended use of the lab table.
What Are the Key Quality Control Checkpoints?
The quality control process typically includes several checkpoints:
-
Incoming Quality Control (IQC): This initial checkpoint involves inspecting raw materials and components before they enter the manufacturing process. Ensuring that materials meet quality specifications helps prevent defects in the final product.
-
In-Process Quality Control (IPQC): During the manufacturing stages, periodic checks are conducted to monitor processes and ensure they adhere to established standards. This can include measuring dimensions and testing the integrity of welded joints.
-
Final Quality Control (FQC): After assembly and finishing, a final inspection is performed to assess the overall quality of the lab table. This may involve functional tests, visual inspections, and ensuring compliance with safety standards.
What Common Testing Methods Are Used for Lab Tables?
Various testing methods are employed to ensure lab tables are safe and functional:
-
Load Testing: Lab tables must withstand specific weight limits. Load testing evaluates the table’s strength and stability under pressure.
-
Chemical Resistance Testing: Given the laboratory environment, tables often undergo chemical exposure tests to assess how well they resist corrosion and damage from various substances.
-
Durability Testing: This includes assessing the wear and tear of surfaces, ensuring that finishes do not degrade under typical lab conditions.
How Can B2B Buyers Verify Supplier Quality Control?
For B2B buyers, particularly those in Africa, South America, the Middle East, and Europe, verifying a supplier’s quality control processes is crucial. Here are actionable steps to ensure quality:
-
Supplier Audits: Conducting regular audits of suppliers can help confirm that they adhere to quality standards and practices. This may include reviewing their manufacturing processes, quality control checkpoints, and compliance with international standards.
-
Requesting Quality Reports: Buyers should request detailed quality assurance reports that outline the procedures followed, testing methods used, and results obtained. This documentation can provide insights into the supplier’s commitment to quality.
-
Third-Party Inspections: Engaging third-party inspection services can add an extra layer of assurance. These independent entities can perform unbiased assessments of the manufacturing processes and final products.
What Are the Quality Control and Certification Nuances for International B2B Buyers?
When purchasing lab tables internationally, buyers must be aware of specific nuances related to quality control and certifications:
-
Compliance with Local Regulations: Different regions may have specific regulations governing laboratory furniture. Buyers should ensure that the products comply with local standards in their respective countries.
-
Understanding Certification Validity: Certifications like CE may vary in validity across different regions. Buyers should confirm that the certifications are recognized in their market.
-
Logistics and Delivery Considerations: Quality assurance does not end at manufacturing. Buyers should also consider how products are packaged and shipped to prevent damage during transit, which can compromise quality.
Conclusion
Understanding the manufacturing processes and quality assurance mechanisms for lab tables is essential for international B2B buyers. By focusing on material preparation, forming, assembly, and finishing, along with rigorous quality control measures, buyers can ensure they select reliable suppliers. Verifying compliance with international standards and engaging in thorough audits will further safeguard investments in laboratory furniture.
Practical Sourcing Guide: A Step-by-Step Checklist for ‘lab table’
When sourcing a lab table, international B2B buyers must navigate various considerations to ensure they select the right product for their specific needs. This guide provides a step-by-step checklist to streamline the procurement process, helping buyers from regions such as Africa, South America, the Middle East, and Europe make informed decisions.
Step 1: Define Your Technical Specifications
Begin by establishing clear technical requirements for your lab table. Consider the intended use, necessary dimensions, and weight capacity. It’s essential to specify the type of material (e.g., stainless steel, phenolic resin) that meets your laboratory’s safety and durability standards.
- Load Bearing Capacity: Ensure the table can support the weight of equipment and materials.
- Chemical Resistance: Select materials that can withstand the specific chemicals used in your lab.
Step 2: Assess Compliance with Local Regulations
Before proceeding with any purchase, verify that the lab table complies with local health and safety regulations. Different regions may have unique standards regarding laboratory furniture, particularly concerning fire safety and chemical exposure.
- Certification: Look for tables that come with certifications indicating compliance with international standards (e.g., ISO, ANSI).
- Local Regulations: Familiarize yourself with any specific requirements in your country or region.
Step 3: Evaluate Potential Suppliers
Conduct thorough research on potential suppliers to ensure they can meet your needs. Request detailed company profiles, product catalogs, and references from other clients in your industry.
- Supplier Reputation: Investigate their track record in supplying quality lab furniture.
- Customer Support: Assess the level of customer service and support they offer post-purchase.
Step 4: Compare Pricing and Value
Gather quotes from multiple suppliers, but remember that the lowest price does not always equate to the best value. Evaluate the overall quality, warranty, and after-sales support included in the price.
- Total Cost of Ownership: Consider long-term costs, including maintenance and potential replacements.
- Warranty Terms: Look for suppliers that offer comprehensive warranties as a sign of confidence in their products.
Step 5: Request Samples or Visit Showrooms
If feasible, request samples or visit showrooms to physically assess the lab tables. This step allows you to evaluate the quality, design, and suitability of the products firsthand.
- Material Quality: Examine the table’s construction and finish to ensure it meets your standards.
- Design Features: Check for practical features like adjustable heights, storage options, and mobility.
Step 6: Finalize Your Order with Clear Terms
Once you have selected a supplier, finalize the order by ensuring all terms are clearly outlined in the contract. This includes payment terms, delivery timelines, and any additional services such as installation.
- Delivery Schedule: Confirm expected delivery dates and any penalties for delays.
- Installation Services: Inquire if the supplier offers installation, especially for complex setups.
Step 7: Establish a Relationship for Future Needs
Building a strong relationship with your supplier can be beneficial for future purchases. Maintain open communication and provide feedback on the products received.
- Ongoing Support: Ensure the supplier is available for future inquiries or maintenance needs.
- Bulk Purchase Discounts: Discuss potential discounts for large orders or repeat purchases to maximize value.
By following this checklist, B2B buyers can effectively navigate the complexities of sourcing lab tables, ensuring they choose the right products for their laboratories while adhering to budgetary and regulatory requirements.
Comprehensive Cost and Pricing Analysis for lab table Sourcing
What Are the Key Cost Components in Lab Table Sourcing?
When sourcing lab tables, understanding the cost structure is critical for B2B buyers. The primary cost components include:
-
Materials: The choice of materials significantly impacts the overall cost. Common materials for lab tables include metal, wood, and various laminates. For instance, stainless steel tables tend to be more expensive due to their durability and corrosion resistance.
-
Labor: Labor costs encompass the wages paid to workers involved in manufacturing. This can vary greatly depending on the region, with labor costs in Europe typically higher than in Africa or South America.
-
Manufacturing Overhead: This includes the indirect costs associated with production, such as utilities, rent, and administrative expenses. It is essential to consider these when evaluating supplier quotes.
-
Tooling: Initial costs for tooling can be substantial, especially for custom designs. High-quality tooling ensures precision and longevity, which may justify the upfront investment.
-
Quality Control (QC): Implementing rigorous QC processes adds to the cost but is crucial for ensuring that the lab tables meet safety and performance standards.
-
Logistics: Shipping and handling costs can vary based on the supplier’s location and the destination. International shipping may require additional fees such as customs duties and taxes.
-
Margin: Suppliers will factor in their desired profit margin, which can range widely based on market conditions and competition.
How Do Price Influencers Affect Lab Table Costs?
Several factors influence the pricing of lab tables, and understanding these can aid in making more informed purchasing decisions:
-
Volume/MOQ (Minimum Order Quantity): Larger orders often lead to lower per-unit costs. Suppliers may offer discounts for bulk purchases, which is an important consideration for institutions or organizations planning extensive lab setups.
-
Specifications and Customization: Custom designs and specifications can increase costs. Buyers should weigh the benefits of customization against the potential price hike.
-
Materials and Quality Certifications: Higher quality materials and certifications (e.g., ISO, ANSI) can lead to increased costs. However, they may also provide long-term savings through durability and reduced maintenance needs.
-
Supplier Factors: Reputation and reliability of suppliers also play a role in pricing. Established suppliers with a proven track record may charge more but offer better service and quality assurance.
-
Incoterms: The terms of shipping and delivery can affect the final cost. Understanding whether prices include shipping, insurance, and duties is crucial for accurate budgeting.
What Buyer Tips Can Enhance Cost Efficiency in Lab Table Sourcing?
For international B2B buyers, particularly those from Africa, South America, the Middle East, and Europe, here are actionable tips to enhance cost efficiency:
-
Negotiate Wisely: Always engage in negotiations with suppliers. Understanding the cost structure allows you to negotiate effectively for better pricing or terms.
-
Consider Total Cost of Ownership (TCO): Evaluate the long-term costs associated with lab tables, including maintenance, durability, and potential need for replacement. Sometimes, a higher upfront cost can lead to lower TCO.
-
Be Aware of Pricing Nuances: Different regions may have varying pricing structures based on local market conditions. For instance, buyers in Germany may encounter different pricing trends compared to those in Colombia or South Africa.
-
Understand Import Regulations: Familiarize yourself with import duties and regulations that could impact the total cost. This knowledge can prevent unexpected expenses.
-
Evaluate Supplier Options: Don’t settle for the first quote. Explore multiple suppliers to compare costs, quality, and service levels. This can help identify the best value for your investment.
Disclaimer on Indicative Prices
Pricing for lab tables can vary significantly based on the factors mentioned above. The prices observed in various sources may be indicative but should not be seen as fixed or all-encompassing. Always request detailed quotes tailored to your specific requirements and conditions.
Alternatives Analysis: Comparing lab table With Other Solutions
Exploring Alternatives to Lab Tables for International B2B Buyers
When considering laboratory furniture, it’s essential to evaluate not just the lab table itself, but also the alternatives that can fulfill similar roles in a lab environment. Each option presents unique advantages and challenges, making it crucial for international B2B buyers—especially from regions like Africa, South America, the Middle East, and Europe—to understand the differences and choose what best aligns with their specific needs.
Comparison of Lab Table with Alternative Solutions
Comparison Aspect | Lab Table | Modular Workstations | Mobile Lab Benches |
---|---|---|---|
Performance | High durability, stable surface | Versatile configurations for various tasks | Flexible design for different setups |
Cost | Moderate ($300-$1,500) | Variable ($500-$2,500) | Moderate to high ($400-$2,000) |
Ease of Implementation | Generally straightforward installation | Requires planning for optimal setup | Easy to set up and relocate |
Maintenance | Low; durable materials | Moderate; may need reconfiguration | Low; easy to clean and maintain |
Best Use Case | Ideal for fixed lab setups | Best for dynamic lab environments | Suitable for educational settings or fieldwork |
Detailed Breakdown of Alternatives
What are Modular Workstations and How Do They Compare to Lab Tables?
Modular workstations provide a flexible and customizable alternative to traditional lab tables. They can be adjusted to accommodate various tasks and workflows, making them ideal for labs that require frequent changes in setup. The primary advantage of modular workstations is their ability to adapt to different laboratory needs, which can enhance productivity. However, they may involve higher initial costs and more complex installation compared to standard lab tables. Buyers should consider whether the flexibility justifies the potential increase in expenditure.
How Do Mobile Lab Benches Offer Flexibility Over Lab Tables?
Mobile lab benches are designed for easy transport and reconfiguration, making them an excellent choice for laboratories that require versatile workspaces. They can be moved to different locations, allowing for collaborative work or changing lab activities. The ease of cleaning and maintenance is another plus, as many models come with durable surfaces resistant to chemicals and spills. On the downside, mobile benches may not provide the same level of stability and durability as fixed lab tables, especially during high-intensity work. Buyers should assess the nature of their lab activities to determine if mobility is a crucial factor.
Conclusion: Choosing the Right Laboratory Solution for Your Needs
Selecting the appropriate laboratory furniture hinges on understanding the specific requirements of your work environment. For international B2B buyers, factors such as workspace flexibility, budget constraints, and maintenance capabilities are critical in the decision-making process. Lab tables excel in stability and durability for fixed setups, while modular workstations and mobile lab benches offer adaptability and ease of movement. Assessing the daily operations and future needs of the laboratory will guide buyers in making an informed choice that aligns with their organizational goals.
Essential Technical Properties and Trade Terminology for lab table
What Are the Essential Technical Properties of Lab Tables?
When investing in lab tables, international B2B buyers must consider several technical properties that can significantly affect usability, safety, and durability in diverse laboratory environments. Here are some critical specifications:
-
Material Grade
– Lab tables are typically constructed from various materials, including stainless steel, phenolic resin, and high-pressure laminate (HPL). Each material has specific properties, such as corrosion resistance, durability, and ease of cleaning. For instance, stainless steel is favored in environments where chemical spills are common, while HPL is often chosen for its aesthetic appeal and lower cost. -
Load Bearing Capacity
– This specification indicates the maximum weight the table can safely support, typically measured in pounds or kilograms. It is crucial for B2B buyers to match the load-bearing capacity with the intended use of the table, especially in laboratories dealing with heavy equipment or multiple users. A load-bearing capacity of at least 600 lb (273 kg) is often recommended for general laboratory use. -
Height Adjustment Mechanism
– Adjustable height tables provide flexibility for various tasks and user preferences. They can be manual or electric, allowing users to switch between sitting and standing positions. This feature is particularly important in educational settings or laboratories where multiple users may require different working heights. -
Chemical Resistance
– Many laboratory tasks involve hazardous substances that can damage furniture. A lab table with a chemically resistant surface can protect the underlying material from corrosion and wear. Buyers should inquire about the chemical resistance ratings of surfaces, especially in laboratories focused on chemistry or biology. -
Vibration Resistance
– In research and testing environments, vibrations can affect the accuracy of results. Lab tables designed with vibration-dampening features minimize disturbances, ensuring stability during sensitive experiments. This is particularly important in fields such as physics or materials science. -
Warranty and Service Life
– A comprehensive warranty is indicative of the manufacturer’s confidence in their product. Buyers should look for tables with warranties covering at least two years, ensuring that any defects or issues can be addressed without incurring additional costs.
What Are Common Trade Terms Associated with Lab Tables?
Understanding industry jargon can greatly enhance the purchasing process. Here are some essential trade terms that B2B buyers should familiarize themselves with:
-
OEM (Original Equipment Manufacturer)
– An OEM is a company that produces parts or equipment that may be marketed by another manufacturer. Buyers should consider OEM products for reliability and compatibility, especially when sourcing lab tables that need to integrate with existing laboratory equipment. -
MOQ (Minimum Order Quantity)
– MOQ refers to the smallest quantity of a product that a supplier is willing to sell. This term is crucial for buyers to understand their budget constraints and inventory needs. For instance, some manufacturers may have an MOQ of 10 units for lab tables, impacting bulk purchasing decisions. -
RFQ (Request for Quotation)
– An RFQ is a document used by buyers to solicit price quotes from suppliers. It typically outlines the specifications of the lab tables required, allowing suppliers to provide accurate pricing. This process is vital for budgeting and comparison shopping among different vendors. -
Incoterms (International Commercial Terms)
– These are internationally recognized rules that define the responsibilities of buyers and sellers in international transactions. Understanding Incoterms helps buyers clarify shipping costs, risks, and delivery timelines, ensuring smooth logistics when importing lab tables from overseas manufacturers. -
Lead Time
– Lead time is the duration from placing an order to receiving the product. In the laboratory setting, knowing the lead time for lab tables can help in planning and avoiding delays in project timelines. Buyers should always confirm lead times with suppliers, especially when working on time-sensitive projects. -
Customization Options
– Many manufacturers offer customization for lab tables, allowing buyers to specify dimensions, materials, and additional features. Understanding the extent of customization available can help buyers tailor products to their specific laboratory needs, enhancing functionality and user experience.
By familiarizing themselves with these technical properties and trade terms, international B2B buyers can make informed decisions when selecting lab tables that best meet their operational requirements.
Navigating Market Dynamics and Sourcing Trends in the lab table Sector
What Are the Current Market Dynamics and Key Trends in the Lab Table Sector?
The global lab table market is experiencing significant growth, driven by increasing demand for laboratory equipment across various sectors, including pharmaceuticals, biotechnology, and education. Key trends shaping the market include the integration of advanced technologies, such as smart lab solutions that enhance efficiency and safety. For international B2B buyers from regions like Africa, South America, the Middle East, and Europe, understanding these trends is crucial.
In Africa, the rise of educational institutions and research facilities is boosting the demand for durable and adaptable lab furniture. In South America, particularly in countries like Colombia, investments in health and safety regulations are leading to a preference for high-quality, chemical-resistant materials. In the Middle East, there is a growing focus on sustainability, with buyers increasingly seeking eco-friendly options. In Europe, countries such as Germany are at the forefront of innovation, with a rising demand for customizable lab tables that meet specific operational needs.
Furthermore, mobility and flexibility are becoming essential features, as more laboratories require workspaces that can adapt to various functions. This shift toward multi-functional lab environments is influencing buyers to seek suppliers that offer modular and adjustable solutions.
How Can Sustainability and Ethical Sourcing Impact Your Lab Table Purchases?
Sustainability is now a key concern for B2B buyers in the lab table sector. The environmental impact of production processes and materials used is under scrutiny, leading to a demand for sustainable practices throughout the supply chain. Ethical sourcing is essential, as buyers look for manufacturers who adhere to fair labor practices and environmental regulations.
Buyers should prioritize suppliers who offer ‘green’ certifications for their lab tables, such as those using recycled materials or low-VOC finishes. Certifications like LEED (Leadership in Energy and Environmental Design) and GreenGuard can guide buyers toward products that minimize environmental impact.
Additionally, opting for furniture made from sustainable materials, such as bamboo or reclaimed wood, can enhance a company’s reputation and align with corporate social responsibility (CSR) goals. The move towards sustainability not only caters to market demands but also reflects positively on a brand’s image, particularly in regions where environmental awareness is rising.
What Is the Historical Context of Lab Tables in B2B Transactions?
The evolution of lab tables can be traced back to the industrial revolution, where the demand for organized and efficient workspaces in scientific research began to grow. Initially, lab tables were basic structures, primarily made from wood. However, advancements in materials science led to the introduction of metal and composite materials, enhancing durability and safety.
Over the decades, lab tables have evolved to meet the changing needs of various industries. The 21st century has seen a surge in technology integration, with features like adjustable heights and built-in utilities becoming standard. This evolution reflects the increasing complexity of laboratory work and the necessity for versatile, functional spaces that cater to modern scientific inquiry.
In conclusion, understanding the current market dynamics, embracing sustainability, and recognizing the historical context of lab tables can significantly enhance sourcing strategies for international B2B buyers in today’s competitive landscape.
Frequently Asked Questions (FAQs) for B2B Buyers of lab table
-
How do I choose the right lab table for my specific needs?
Choosing the right lab table requires assessing your specific laboratory requirements, including the type of work being conducted, space constraints, and the materials needed for safety and durability. Consider the table’s load-bearing capacity, surface material (such as phenolic resin or stainless steel), and whether adjustable height features are necessary. Additionally, evaluate the table’s compatibility with other equipment and storage solutions in your lab to ensure a seamless workflow. -
What are the benefits of customizable lab tables for international buyers?
Customizable lab tables allow you to tailor features to meet specific laboratory needs, enhancing functionality and efficiency. For international buyers, customization can accommodate local safety standards, environmental conditions, and space constraints. It also allows for the selection of materials that resist corrosion or chemical exposure, ensuring durability. Working with suppliers that offer customization options can help you create a lab environment that aligns with your operational goals and user preferences. -
What is the typical lead time for ordering lab tables internationally?
Lead times for ordering lab tables can vary significantly based on the supplier, customization options, and shipping logistics. Generally, expect a lead time of 4 to 12 weeks for production and delivery. For international orders, factors such as customs clearance and local regulations can also affect delivery times. It is advisable to communicate with suppliers early in the process and request a detailed timeline to avoid unexpected delays. -
What should I know about minimum order quantities (MOQs) when sourcing lab tables?
Minimum order quantities (MOQs) can differ among suppliers, often influenced by production capabilities and shipping logistics. For international buyers, understanding MOQs is crucial for budget management and inventory planning. Some suppliers may offer flexible MOQs for first-time buyers or smaller businesses, while others might require larger orders to justify manufacturing costs. Always clarify MOQs upfront and negotiate if your needs fall below the standard requirements. -
How can I verify the quality and safety standards of lab tables from international suppliers?
To ensure the quality and safety of lab tables, request certifications and compliance documentation from suppliers. Look for adherence to international standards such as ISO or ASTM, which indicate rigorous testing and quality assurance processes. Additionally, consider visiting the supplier’s manufacturing facility or seeking third-party inspections to validate their quality control measures. Online reviews and references from other international buyers can also provide insights into the supplier’s reliability. -
What payment terms should I expect when purchasing lab tables internationally?
Payment terms for international purchases can vary widely among suppliers. Common options include upfront payment, partial payment before shipment, or payment upon delivery. It is vital to negotiate terms that align with your cash flow and budget constraints. Consider using secure payment methods such as letters of credit or escrow services to minimize risk. Always clarify currency exchange implications and potential fees associated with international transactions. -
What logistics considerations should I keep in mind when importing lab tables?
Logistics is a critical aspect of importing lab tables, involving shipping methods, customs clearance, and delivery timelines. Identify reliable freight forwarders familiar with laboratory equipment to manage the transportation process efficiently. Ensure that all necessary documentation, such as invoices and packing lists, is prepared for customs. Additionally, factor in potential tariffs and duties when budgeting for your purchase to avoid unexpected costs. -
How do I handle warranty and after-sales support for lab tables sourced internationally?
When sourcing lab tables internationally, it is essential to understand the warranty terms and after-sales support offered by the supplier. Inquire about the duration of the warranty, what it covers, and the process for claiming support. Ensure that the supplier has a responsive customer service team capable of assisting with maintenance or replacement parts. Having a clear understanding of these elements can help you mitigate risks and ensure long-term satisfaction with your investment.
Important Disclaimer & Terms of Use
⚠️ Important Disclaimer
The information provided in this guide, including content regarding manufacturers, technical specifications, and market analysis, is for informational and educational purposes only. It does not constitute professional procurement advice, financial advice, or legal advice.
While we have made every effort to ensure the accuracy and timeliness of the information, we are not responsible for any errors, omissions, or outdated information. Market conditions, company details, and technical standards are subject to change.
B2B buyers must conduct their own independent and thorough due diligence before making any purchasing decisions. This includes contacting suppliers directly, verifying certifications, requesting samples, and seeking professional consultation. The risk of relying on any information in this guide is borne solely by the reader.
Strategic Sourcing Conclusion and Outlook for lab table
As international B2B buyers navigate the complexities of sourcing laboratory tables, understanding the importance of strategic sourcing becomes paramount. By focusing on quality, durability, and functionality, businesses can ensure that their laboratory environments are equipped to handle diverse tasks safely and efficiently. Key factors to consider include the materials used, such as chemical-resistant surfaces and adjustable heights, which cater to various laboratory needs across sectors.
Why is Strategic Sourcing Essential for Lab Tables?
Strategic sourcing not only reduces costs but also enhances the overall value of procurement processes. Buyers from Africa, South America, the Middle East, and Europe must leverage supplier relationships and market insights to identify the best options available. By prioritizing suppliers who offer customizable solutions, companies can better align their laboratory infrastructure with specific operational requirements.
What is the Future Outlook for Lab Table Procurement?
Looking ahead, the demand for high-quality lab tables will continue to grow, driven by advancements in technology and an increasing emphasis on safety and efficiency in laboratories. By remaining proactive and informed, international buyers can seize opportunities to enhance their laboratory capabilities. Engage with suppliers who can provide innovative solutions tailored to your unique needs, ensuring your laboratory remains at the forefront of scientific advancement.