Maximize Efficiency: The Ultimate Pressure Vessel Guide (2025)
Introduction: Navigating the Global Market for pressure vessel
In today’s competitive landscape, sourcing pressure vessels that meet stringent safety and regulatory standards can be a daunting challenge for international B2B buyers. As industries across Africa, South America, the Middle East, and Europe expand, the demand for reliable, high-quality pressure vessels—essential for storing and transporting gases and liquids under pressure—continues to grow. This comprehensive guide serves as a vital resource for navigating the complexities of the global pressure vessel market, covering essential topics such as types, applications, supplier vetting, and cost analysis.
International buyers will find actionable insights tailored to their specific needs, whether they are operating in the oil and gas, chemical, or energy sectors. With a focus on understanding the unique requirements of various industries, this guide empowers B2B buyers to make informed purchasing decisions. It addresses critical questions about compliance with international standards, material selection, and the latest innovations in pressure vessel technology, including the potential of composite materials.
By leveraging the knowledge contained within this guide, buyers from regions like Egypt and Mexico can confidently evaluate suppliers, assess pricing structures, and select the most suitable pressure vessels for their operations. Ultimately, this resource aims to streamline the procurement process, minimize risks, and enhance operational efficiency in an increasingly interconnected global market.
Understanding pressure vessel Types and Variations
Type Name | Key Distinguishing Features | Primary B2B Applications | Brief Pros & Cons for Buyers |
---|---|---|---|
Process Vessel | Designed for storage and processing of liquids | Petrochemical facilities, oil & gas production | Pros: Versatile, suitable for various processes. Cons: Requires regular maintenance. |
Autoclave | High-pressure, high-temperature cylindrical vessel | Sterilization in pharmaceuticals, food industry | Pros: Effective sterilization. Cons: High initial cost. |
High-Pressure Vessel | Built to withstand extreme pressures and corrosive environments | Chemical reactors, supercritical extraction | Pros: Durable and reliable. Cons: Complex design increases cost. |
Heat Exchanger | Transfers heat between fluids | Energy, food, pharmaceuticals | Pros: Energy-efficient, reduces operational costs. Cons: Requires precise design for specific applications. |
Vacuum Tank | Operates under negative pressure | Waste management, chemical processing | Pros: Effective for air/fluid filtration. Cons: Limited to specific applications. |
What Are the Characteristics of Process Vessels?
Process vessels are fundamental in industries such as petrochemicals and oil and gas. They are designed to hold and store liquids under pressure while facilitating integrated operations. The versatility of process vessels allows them to be used for various applications, including mixing, separating, and storing chemicals. Buyers should consider the vessel’s material, capacity, and compatibility with the substances it will store, as these factors significantly impact performance and safety.
How Do Autoclaves Serve Various Industries?
Autoclaves are specialized pressure vessels that operate at high temperatures and pressures, making them essential in sterilization processes in the pharmaceutical and food industries. Their cylindrical shape ensures uniform pressure distribution, enhancing safety and efficiency. When purchasing autoclaves, B2B buyers should evaluate their capacity, temperature range, and compliance with safety standards to ensure they meet the specific needs of their operations.
What Makes High-Pressure Vessels Unique?
High-pressure vessels are engineered to endure extreme pressures and corrosive environments, commonly used in chemical reactors and supercritical extraction systems. They are typically constructed from durable materials like stainless steel, which adds to their longevity. B2B buyers must assess the vessel’s design, material specifications, and operational limits to ensure it aligns with their production requirements and safety regulations.
Why Are Heat Exchangers Important for B2B Operations?
Heat exchangers are critical in transferring heat between fluids, utilized across various sectors, including energy, food processing, and pharmaceuticals. Their design significantly influences operational efficiency, as they can help reduce energy costs. When selecting a heat exchanger, businesses should consider thermal properties, flow rates, and maintenance requirements to optimize performance and achieve cost savings.
How Do Vacuum Tanks Function in Industrial Applications?
Vacuum tanks operate under negative pressure, making them ideal for applications in waste management and chemical processing. They are designed to filter air or fluids effectively, which is crucial for maintaining operational efficiency in various industries. Buyers should focus on the tank’s capacity, materials used, and compatibility with their specific applications to ensure optimal performance and reliability.
Key Industrial Applications of pressure vessel
Industry/Sector | Specific Application of Pressure Vessel | Value/Benefit for the Business | Key Sourcing Considerations for this Application |
---|---|---|---|
Oil & Gas | Gas storage and transportation vessels | Ensures safe and efficient storage of volatile substances | Compliance with international safety standards; material durability |
Chemical Manufacturing | Chemical reactors for high-pressure reactions | Enables complex chemical processes while maintaining safety | Material compatibility with chemicals; regulatory certifications |
Energy (Power Generation) | Reactor Pressure Vessels (RPVs) for nuclear power plants | Critical for safe containment of nuclear reactions | High reliability standards; resistance to extreme conditions |
Food & Beverage | Autoclaves for sterilization processes | Ensures product safety and extends shelf life | Certification for food safety; material specifications for hygiene |
Water Treatment | Pressure tanks for water distribution | Enhances water pressure management and system efficiency | Sizing based on system requirements; corrosion resistance materials |
How Are Pressure Vessels Used in the Oil & Gas Industry?
In the oil and gas sector, pressure vessels are crucial for the safe storage and transportation of gases and liquids under high pressure. These vessels help manage volatile substances, reducing the risk of leaks and accidents. Buyers from Africa and the Middle East should ensure that their sourced vessels comply with international safety standards, such as those set by ASME, to avoid costly failures. Additionally, the choice of materials, like carbon steel or stainless steel, is vital for durability and corrosion resistance in harsh environments.
What Role Do Pressure Vessels Play in Chemical Manufacturing?
Pressure vessels in chemical manufacturing, such as reactors, facilitate high-pressure chemical reactions essential for producing various products. These vessels allow companies to conduct complex processes safely while maximizing efficiency. B2B buyers, especially from South America, should prioritize sourcing vessels that meet specific material compatibility requirements to prevent reactions with stored chemicals. Regulatory certifications and adherence to safety standards are also critical to ensure operational safety.
How Are Reactor Pressure Vessels Used in Energy Generation?
Reactor Pressure Vessels (RPVs) are integral to nuclear power plants, containing the core and coolant while withstanding extreme temperatures and pressures. The reliability of these vessels is paramount, as they serve as the main barrier against radioactive leaks. Buyers from Europe need to focus on suppliers who adhere to stringent quality and safety standards, given the critical nature of this equipment. Additionally, sourcing from manufacturers with proven expertise in nuclear applications is essential.
Why Are Autoclaves Important in the Food & Beverage Sector?
Autoclaves are pressure vessels used for sterilizing food products, ensuring safety and extending shelf life. By using high-pressure steam, they effectively eliminate pathogens and spoilage organisms. For B2B buyers in regions like Africa, sourcing autoclaves requires attention to food safety certifications and compliance with hygiene standards. Material specifications must also ensure that the vessels can withstand repeated high-temperature cycles without degradation.
How Do Pressure Tanks Enhance Water Treatment Systems?
Pressure tanks are essential in water treatment processes, maintaining optimal pressure levels for distribution systems. They help manage fluctuations in water demand, ensuring a steady supply. Buyers in South America should consider the sizing of these tanks based on specific system requirements and opt for materials that resist corrosion. Additionally, sourcing pressure tanks that meet local regulations will enhance system reliability and efficiency, ultimately benefiting the community served.
3 Common User Pain Points for ‘pressure vessel’ & Their Solutions
Scenario 1: Navigating Compliance with Pressure Vessel Regulations
The Problem: For B2B buyers, especially in regions like Africa and South America, understanding and adhering to the myriad of regulations governing pressure vessels can be overwhelming. Buyers often face the challenge of ensuring that their pressure vessels comply with local and international standards, such as the ASME Boiler and Pressure Vessel Code or API 510. Non-compliance can lead to costly fines, project delays, and severe safety risks.
The Solution: To navigate compliance effectively, B2B buyers should establish a thorough understanding of the relevant standards applicable to their industry and region. This begins by conducting a comprehensive regulatory assessment to identify the necessary certifications required for their specific pressure vessels. Engaging with experienced suppliers who have a proven track record in regulatory compliance is crucial. Buyers should prioritize vendors who offer documentation and guidance on the compliance process, including installation, maintenance, and inspection requirements. Additionally, investing in training for staff responsible for pressure vessel operations can enhance compliance awareness and adherence.
Scenario 2: Managing the Risk of Pressure Vessel Failures
The Problem: Pressure vessel failures can have catastrophic consequences, including environmental damage, safety hazards, and financial losses. B2B buyers in the oil and gas sectors in the Middle East often struggle with the risk of equipment failure due to improper maintenance or inadequate design specifications. Such incidents not only disrupt operations but can also tarnish a company’s reputation.
The Solution: To mitigate the risk of pressure vessel failures, buyers should implement a robust maintenance strategy that includes regular inspections and testing as outlined by the API 510 guidelines. Collaborating with qualified engineers to conduct risk assessments and develop a maintenance schedule tailored to their specific operational conditions is essential. Furthermore, investing in advanced monitoring technologies, such as pressure and temperature sensors, can provide real-time data to detect anomalies before they escalate into failures. Buyers should also consider sourcing pressure vessels from manufacturers who provide warranties and service agreements, ensuring ongoing support and reliability.
Scenario 3: Overcoming Sizing and Specification Challenges for Pressure Vessels
The Problem: Selecting the correct size and specifications for a pressure vessel can be a daunting task for B2B buyers, particularly in Europe, where precision is critical. Misjudging the required capacity or pressure ratings can lead to inefficiencies, increased operational costs, or even project failure. Buyers often feel overwhelmed by the technical jargon and complex calculations needed to ensure they choose the right vessel for their applications.
The Solution: To overcome sizing and specification challenges, B2B buyers should start by engaging with engineering experts who specialize in pressure vessels. Collaborating with these professionals allows buyers to clarify their operational needs, including the types of fluids being stored, temperature ranges, and pressure requirements. Using detailed process flow diagrams and operational data can help in accurately determining the necessary dimensions and specifications. Buyers should also take advantage of simulation software tools that can predict performance under various scenarios, ensuring the selected vessel meets both current and future demands. Additionally, establishing a clear line of communication with manufacturers about specific requirements can facilitate customized solutions that enhance operational efficiency.
Strategic Material Selection Guide for pressure vessel
What Are the Key Materials Used in Pressure Vessel Construction?
When selecting materials for pressure vessels, international B2B buyers must consider various factors, including the specific application, environmental conditions, and regulatory compliance. Here, we analyze four common materials used in pressure vessel construction: carbon steel, stainless steel, aluminum, and composite materials.
How Does Carbon Steel Perform in Pressure Vessel Applications?
Key Properties: Carbon steel is known for its high strength and excellent toughness, making it suitable for high-pressure applications. It typically has a temperature rating of up to 400°C (752°F) and can withstand pressures exceeding 15 psi.
Pros & Cons: The primary advantage of carbon steel is its cost-effectiveness and durability. However, it is prone to corrosion, especially in aggressive environments, which may necessitate additional protective coatings or treatments. Manufacturing complexity is moderate, as carbon steel is widely available and easy to work with.
Impact on Application: Carbon steel is compatible with a wide range of media, including water, oil, and gas. However, it may not be suitable for corrosive chemicals without proper treatment.
Considerations for International Buyers: Buyers from regions like Africa and South America should ensure compliance with local standards, such as ASTM or DIN. Additionally, understanding the local climate’s impact on corrosion can influence the choice of protective measures.
What Are the Benefits of Using Stainless Steel in Pressure Vessels?
Key Properties: Stainless steel offers excellent corrosion resistance and can operate at temperatures up to 800°C (1472°F) and pressures exceeding 15 psi. Its composition includes chromium, which enhances its resistance to oxidation.
Pros & Cons: The key advantage of stainless steel is its longevity and low maintenance requirements. However, it is significantly more expensive than carbon steel, and its manufacturing processes can be complex, requiring specialized equipment.
Impact on Application: Stainless steel is ideal for applications involving corrosive substances, such as chemicals and pharmaceuticals. Its compatibility with a variety of media makes it a versatile choice.
Considerations for International Buyers: Buyers in Europe and the Middle East should be aware of the various grades of stainless steel and their specific applications. Compliance with international standards like ASME and API is crucial for ensuring safety and reliability.
How Does Aluminum Compare as a Material for Pressure Vessels?
Key Properties: Aluminum is lightweight and has a good strength-to-weight ratio, with temperature ratings typically up to 200°C (392°F) and pressure capabilities around 15 psi.
Pros & Cons: The main advantage of aluminum is its lightweight nature, which can lead to reduced transportation costs. However, it has lower strength compared to steel and can be more susceptible to fatigue and corrosion, especially in marine environments.
Impact on Application: Aluminum is suitable for low-pressure applications and is often used in food and beverage industries due to its non-reactive nature. However, it may not be appropriate for high-pressure or high-temperature applications.
Considerations for International Buyers: Buyers in regions like South America should consider the specific applications and whether aluminum meets the necessary safety and performance standards. Local regulations may dictate the use of certain materials in specific industries.
What Role Do Composite Materials Play in Pressure Vessel Design?
Key Properties: Composite materials, such as fiberglass reinforced plastic (FRP), offer high strength and excellent corrosion resistance, with temperature ratings up to 120°C (248°F) and pressures around 15 psi.
Pros & Cons: The primary advantage of composites is their lightweight nature and resistance to corrosion, making them suitable for harsh environments. However, they are typically more expensive to manufacture and may require specialized handling during installation.
Impact on Application: Composites are ideal for applications involving aggressive chemicals or environments, such as in the chemical processing or marine industries. However, their use in high-pressure applications is limited.
Considerations for International Buyers: Buyers from the Middle East and Africa should be aware of the evolving standards for composite materials and their acceptance in various industries. Understanding local market trends can help in making informed decisions.
Summary Table of Material Selection for Pressure Vessels
Material | Typical Use Case for Pressure Vessel | Key Advantage | Key Disadvantage/Limitation | Relative Cost (Low/Med/High) |
---|---|---|---|---|
Carbon Steel | Oil & gas storage | Cost-effective and durable | Prone to corrosion | Low |
Stainless Steel | Chemical processing | Excellent corrosion resistance | Higher cost and complex manufacturing | High |
Aluminum | Food and beverage applications | Lightweight and low transport costs | Lower strength and fatigue issues | Medium |
Composite Materials | Chemical processing in harsh environments | High corrosion resistance | Expensive and specialized handling | High |
This strategic material selection guide provides essential insights for international B2B buyers, helping them choose the right materials for their pressure vessel applications while considering cost, performance, and compliance with local regulations.
In-depth Look: Manufacturing Processes and Quality Assurance for pressure vessel
What Are the Main Stages in the Manufacturing Process of Pressure Vessels?
The manufacturing process of pressure vessels involves several critical stages that ensure the final product meets safety and performance standards. These stages include material preparation, forming, assembly, and finishing.
How Is Material Prepared for Pressure Vessel Manufacturing?
Material preparation is the first step in manufacturing pressure vessels. The most commonly used materials are carbon steel and stainless steel, chosen for their strength and resistance to corrosion. During this stage, raw materials are sourced, inspected for quality, and cut to the required dimensions. This step often involves the use of advanced software for precision cutting, ensuring that the material meets specifications for thickness and composition.
What Forming Techniques Are Used in Pressure Vessel Manufacturing?
Once the materials are prepared, they undergo forming, which can be achieved through various techniques such as rolling, bending, or forging. For cylindrical pressure vessels, plates are typically rolled into a cylinder and welded together. The use of Computer Numerical Control (CNC) machinery enhances precision in forming, reducing the likelihood of defects. Depending on the vessel design, additional techniques such as hydroforming may be employed to achieve complex shapes while maintaining material integrity.
How Is Assembly Conducted in Pressure Vessel Manufacturing?
Assembly is a crucial stage where the formed components are joined to create the pressure vessel. This process usually involves welding, which must be performed by certified welders following strict guidelines. The welds are tested for quality through non-destructive testing (NDT) methods, such as ultrasonic testing or radiographic inspection, to ensure they can withstand the internal pressures expected during operation.
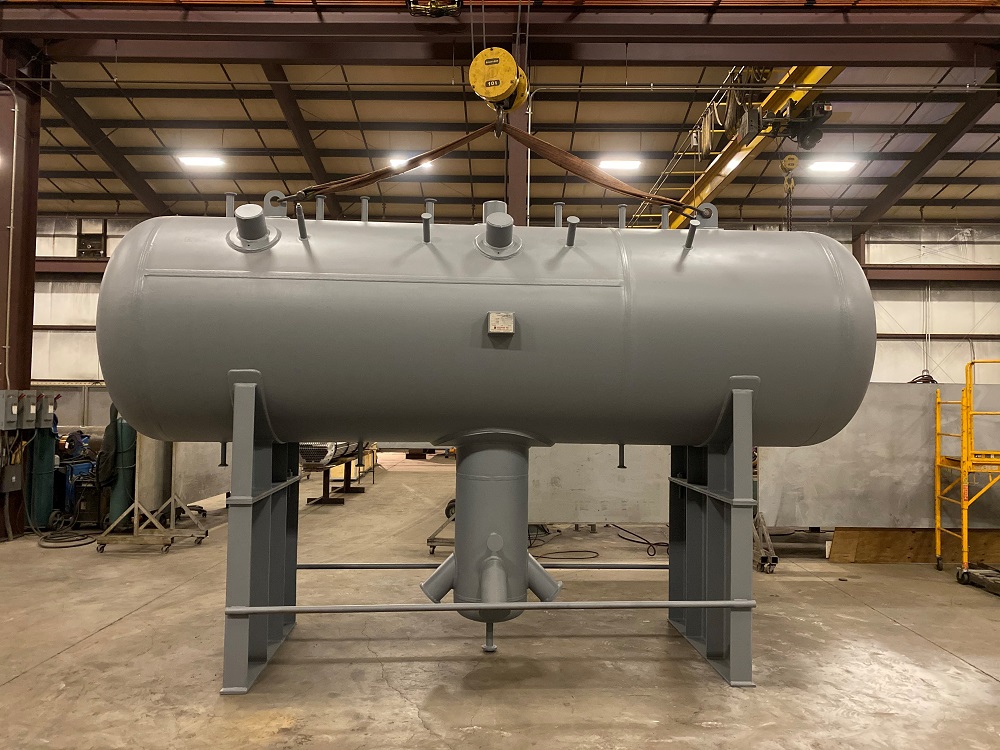
A stock image related to pressure vessel.
What Finishing Processes Are Essential for Pressure Vessels?
The final stage, finishing, involves surface treatment, coating, and painting to enhance the vessel’s durability and resistance to environmental factors. Surface treatments may include sandblasting or passivation, which helps prevent corrosion. Additionally, pressure vessels may undergo pressure testing to verify their performance under operational conditions. This testing is crucial for ensuring compliance with international safety standards.
What Quality Assurance Standards Are Relevant for Pressure Vessels?
Quality assurance (QA) is vital in the manufacturing of pressure vessels, ensuring that they meet stringent safety and performance standards. Various international standards govern this process, including ISO 9001, which provides a framework for quality management systems.
How Do International and Industry-Specific Standards Influence Quality Control?
In addition to ISO 9001, pressure vessels must comply with industry-specific standards such as the ASME Boiler and Pressure Vessel Code (BPVC) in the United States and the European Pressure Equipment Directive (PED) in Europe. These standards dictate design, fabrication, inspection, and testing protocols, ensuring that pressure vessels can safely operate under high pressures and temperatures.
What Are the Key Quality Control Checkpoints in Pressure Vessel Manufacturing?
To ensure the integrity of pressure vessels, several quality control checkpoints are established throughout the manufacturing process:
- Incoming Quality Control (IQC): This step involves inspecting raw materials upon delivery to verify that they meet specified standards.
- In-Process Quality Control (IPQC): During the manufacturing stages, ongoing inspections are conducted to monitor the quality of welding, forming, and assembly processes.
- Final Quality Control (FQC): Before shipping, the completed pressure vessel undergoes rigorous testing, including pressure tests and NDT methods, to confirm its compliance with safety standards.
How Can B2B Buyers Verify Supplier Quality Control Processes?
For international B2B buyers, particularly those in Africa, South America, the Middle East, and Europe, verifying a supplier’s quality control processes is crucial. Here are effective methods to achieve this:
What Audit Processes Can Buyers Implement to Ensure Supplier Compliance?
Buyers can conduct supplier audits, which involve visiting the manufacturing facility to assess quality control measures and manufacturing practices firsthand. This process includes reviewing documentation related to quality management systems, certifications, and test results.
How Can Buyers Leverage Reports and Third-Party Inspections?
Requesting quality assurance reports and certifications from suppliers can provide insight into their compliance with international standards. Additionally, engaging third-party inspection agencies to evaluate the manufacturing process can offer an unbiased assessment of quality control practices.
What Nuances Should International Buyers Consider Regarding Quality Control?
International buyers should be aware of regional variations in quality assurance practices and standards. For example, while European standards may emphasize specific safety regulations, manufacturers in Africa or South America may adhere to different local standards. It’s essential for buyers to communicate their specific quality requirements clearly and ensure that suppliers can meet them.
How Can Buyers Navigate Certification Nuances Across Regions?
Understanding the certification requirements in different regions is crucial. For instance, pressure vessels exported to Europe must comply with CE marking, while those intended for the U.S. market must adhere to ASME standards. Buyers should request documentation that verifies compliance with the relevant certification standards for their region.
Conclusion
The manufacturing processes and quality assurance measures for pressure vessels are intricate and heavily regulated. International B2B buyers must not only understand these processes but also actively engage in verifying supplier quality controls. By implementing thorough audits, requesting documentation, and understanding regional standards, buyers can ensure that they procure safe and reliable pressure vessels tailored to their operational needs.
Practical Sourcing Guide: A Step-by-Step Checklist for ‘pressure vessel’
In the competitive landscape of international B2B sourcing, procuring pressure vessels requires careful consideration and strategic planning. This guide provides a step-by-step checklist to ensure that buyers, particularly from Africa, South America, the Middle East, and Europe, can make informed decisions while navigating the complexities of this critical equipment.
Step 1: Define Your Technical Specifications
Before engaging with suppliers, it’s essential to clearly outline your technical requirements. This includes the type of pressure vessel needed (e.g., storage, heat exchanger), the materials (such as carbon steel or stainless steel), and the specific pressure and temperature ratings. Clearly defined specifications help prevent miscommunication and ensure that the final product meets your operational needs.
- Consider the application: Identify the industry standards relevant to your sector, such as ASME or API.
- Determine size and capacity: Specify the dimensions and volume that the pressure vessel must accommodate.
Step 2: Research Compliance and Safety Standards
Pressure vessels are subject to stringent safety regulations. Familiarize yourself with the relevant compliance standards applicable in your region and industry. For example, the ASME Boiler and Pressure Vessel Code (BPVC) outlines critical safety guidelines.
- Identify local regulations: Ensure that your supplier adheres to local and international standards.
- Check for certifications: Look for ISO certifications or other relevant safety certifications that demonstrate a supplier’s commitment to quality and safety.
Step 3: Evaluate Potential Suppliers
Thoroughly vet potential suppliers to ensure reliability and quality. Request company profiles, case studies, and references from buyers in similar industries or regions. This step is vital in establishing trust and verifying the supplier’s capability to meet your specifications.
- Assess supplier experience: Look for suppliers with a proven track record in manufacturing pressure vessels.
- Seek customer feedback: Investigate reviews and testimonials from previous clients to gauge satisfaction levels.
Step 4: Request Detailed Quotes and Proposals
Once you’ve narrowed down your list of potential suppliers, request detailed quotes and proposals. This should include pricing, lead times, and any additional services like installation or maintenance.
- Compare costs: Evaluate quotes not just on price, but also on the value offered, including warranty and after-sales support.
- Clarify terms and conditions: Ensure you understand payment terms, delivery schedules, and any penalties for late delivery.
Step 5: Conduct Site Visits and Factory Audits
If feasible, arrange site visits to the manufacturing facilities of your shortlisted suppliers. This firsthand observation can provide critical insights into the supplier’s production capabilities and quality control processes.
- Inspect production processes: Ensure that the supplier employs modern manufacturing techniques and adheres to quality standards.
- Evaluate workforce competency: Meet with engineers and technicians to assess their expertise and commitment to quality.
Step 6: Negotiate Terms and Finalize Agreements
Once you’ve selected a supplier, negotiate terms that reflect your needs while also protecting your interests. This includes pricing, delivery timelines, and warranty conditions.
- Be clear about expectations: Clearly communicate your expectations for product performance and support.
- Document everything: Ensure that all agreements are documented to avoid future disputes.
Step 7: Plan for Quality Assurance and Inspection
Before accepting delivery of the pressure vessel, establish a plan for quality assurance and inspection. This should involve pre-delivery inspections and testing to ensure compliance with your specifications.
- Engage third-party inspectors: Consider hiring independent inspectors to verify that the pressure vessel meets all required standards.
- Create a checklist for acceptance: Develop a checklist to ensure all specifications and safety standards are met upon delivery.
By following this comprehensive sourcing checklist, B2B buyers can navigate the complexities of procuring pressure vessels effectively, ensuring that they make informed decisions that support their operational needs and compliance requirements.
Comprehensive Cost and Pricing Analysis for pressure vessel Sourcing
What Are the Key Cost Components in Pressure Vessel Sourcing?
Understanding the cost structure of pressure vessels is essential for international B2B buyers. The primary cost components include materials, labor, manufacturing overhead, tooling, quality control (QC), logistics, and supplier margins.
-
Materials: The choice of materials significantly impacts the overall cost. Common materials include carbon steel, stainless steel, and increasingly, composite materials. The selection is often driven by the application and required pressure ratings. For instance, high-pressure vessels typically require more durable materials, leading to higher costs.
-
Labor: Skilled labor is necessary for the design, fabrication, and assembly of pressure vessels. Labor costs can vary significantly based on geographic location and the complexity of the project. Regions with a skilled workforce might offer better quality but at a premium price.
-
Manufacturing Overhead: This includes costs associated with equipment maintenance, utilities, and factory space. Efficient manufacturing processes can lower these costs, making it crucial to evaluate the supplier’s operational efficiency.
-
Tooling: Custom tooling for specific designs can add significant costs to the project. Buyers should consider whether the tooling is reusable for future orders, as this can mitigate costs in the long run.
-
Quality Control (QC): Rigorous QC processes are essential for ensuring compliance with safety standards. Costs associated with inspections and certifications can add to the price but are necessary to avoid costly failures.
-
Logistics: Transportation costs can fluctuate based on the distance from the manufacturing site to the buyer’s location. International buyers must factor in customs duties and import taxes, which can significantly affect the total cost.
-
Margin: Supplier margins vary based on competition, brand reputation, and market demand. It’s beneficial to understand the market landscape to negotiate effectively.
What Influences Pressure Vessel Pricing for International Buyers?
Several factors influence pricing beyond the basic cost components, particularly for buyers from Africa, South America, the Middle East, and Europe.
-
Volume and Minimum Order Quantity (MOQ): Larger orders often come with volume discounts. Understanding the supplier’s MOQ can provide leverage in negotiations.
-
Specifications and Customization: Custom designs or specific certifications can lead to higher costs. It’s essential to clearly define requirements to avoid unexpected expenses.
-
Material Selection: The choice of material not only impacts the upfront cost but also the long-term durability and maintenance costs. Buyers should consider the Total Cost of Ownership (TCO) when selecting materials.
-
Quality and Certifications: Compliance with international standards, such as the ASME Boiler and Pressure Vessel Code, can increase costs. However, these certifications are crucial for safety and reliability.
-
Supplier Factors: The reputation and reliability of suppliers can significantly impact pricing. Established suppliers may charge more due to their experience and the quality assurance they provide.
-
Incoterms: Understanding the Incoterms (International Commercial Terms) is critical for determining who bears the cost of shipping, insurance, and customs duties. Choosing the right Incoterm can lead to cost savings.
How Can International B2B Buyers Negotiate Effectively?
Negotiation is a vital aspect of sourcing pressure vessels. Here are actionable tips:
- Research and Benchmark: Gather data on market prices and competitor offerings to inform your negotiations.
- Be Transparent: Clearly communicate your needs and constraints to suppliers. This can foster a collaborative approach to pricing.
- Leverage Relationships: Building long-term relationships with suppliers can lead to better pricing and terms in future contracts.
- Consider Total Cost of Ownership: Evaluate the long-term costs associated with maintenance, operation, and potential downtime rather than focusing solely on upfront costs.
Disclaimer on Pricing
The prices of pressure vessels can vary widely based on the factors discussed. It is advisable for international buyers to obtain detailed quotations from multiple suppliers to ensure competitive pricing and to factor in all potential costs associated with sourcing.
Alternatives Analysis: Comparing pressure vessel With Other Solutions
Exploring Alternatives to Pressure Vessels: A Comparative Analysis
In the realm of industrial applications, pressure vessels serve as critical components for storing and transporting gases and liquids under pressure. However, various alternatives can be employed depending on specific operational needs, budget constraints, and application requirements. This section provides an in-depth comparison of pressure vessels with two viable alternatives: Heat Exchangers and Storage Tanks.
Comparison Table: Pressure Vessel vs. Alternatives
Comparison Aspect | Pressure Vessel | Heat Exchanger | Storage Tank |
---|---|---|---|
Performance | High performance under extreme pressures | Efficient heat transfer between fluids | Good for bulk storage of liquids/gases |
Cost | Generally higher due to materials and standards | Moderate, depending on complexity | Lower initial investment |
Ease of Implementation | Requires specialized knowledge for installation | Can be complex but manageable with skilled labor | Easier installation, often pre-fabricated |
Maintenance | Regular inspections needed for safety compliance | Requires periodic cleaning and checks | Minimal maintenance, primarily checking for leaks |
Best Use Case | Ideal for high-pressure applications in chemical and energy sectors | Best for processes requiring heat transfer | Suitable for bulk storage of liquids and gases |
In-Depth Analysis of Alternatives
What are Heat Exchangers and Their Advantages?
Heat exchangers are devices designed to transfer heat between two or more fluids without mixing them. They are widely utilized in industries such as food processing, pharmaceuticals, and energy production. The primary advantage of heat exchangers lies in their ability to efficiently manage thermal energy, thereby reducing operational costs associated with heating and cooling processes. However, they may not be suitable for high-pressure applications like pressure vessels, and their complexity can require specialized installation and maintenance knowledge.
How Do Storage Tanks Compare?
Storage tanks are large containers used to hold liquids or gases at atmospheric pressure. They are typically more cost-effective than pressure vessels, making them an attractive option for bulk storage needs in industries such as agriculture, water treatment, and oil storage. The simplicity of their design allows for easier installation and maintenance. However, storage tanks are limited in their application, as they cannot accommodate the high pressures that pressure vessels can safely handle. Thus, they are not ideal for situations requiring containment of pressurized gases or liquids.
Conclusion: How to Choose the Right Solution for Your Needs
When deciding between pressure vessels and their alternatives, B2B buyers must assess their specific operational requirements, including the nature of the materials being stored, pressure levels, and thermal management needs. While pressure vessels are essential for high-pressure applications, alternatives like heat exchangers and storage tanks offer distinct benefits that could align better with certain business models and budget considerations. By carefully evaluating these aspects, international buyers from regions such as Africa, South America, the Middle East, and Europe can make informed decisions that enhance efficiency and safety in their operations.
Essential Technical Properties and Trade Terminology for pressure vessel
What Are the Essential Technical Properties of Pressure Vessels?
When considering the procurement of pressure vessels, understanding their technical specifications is crucial for ensuring safety, compliance, and functionality in various applications. Below are some key properties that international B2B buyers should be aware of:
1. Material Grade: Why Is It Important?
Pressure vessels are primarily constructed from metals such as carbon steel, stainless steel, and occasionally aluminum or composite materials. The choice of material affects the vessel’s resistance to corrosion, temperature, and pressure. For example, stainless steel is favored in industries that handle corrosive substances due to its durability. Buyers must evaluate the material grade according to the specific environmental conditions and media the vessel will encounter.
2. Design Pressure: What Does It Indicate?
Design pressure refers to the maximum pressure that a pressure vessel is designed to withstand during its operational lifecycle. It is critical for ensuring that the vessel can safely contain its contents without risk of failure. Understanding the design pressure helps buyers assess whether a vessel meets their operational requirements and complies with industry standards.
3. Tolerance and Thickness: How Do They Affect Performance?
Tolerance and wall thickness are vital in determining a pressure vessel’s structural integrity. Thicker walls can withstand higher pressures, but they also add weight and cost. Tolerances must be adhered to for safety and performance, as deviations can lead to catastrophic failures. Buyers should consider the balance between material costs and required performance specifications.
4. Temperature Rating: Why Is This Specification Critical?
The temperature rating indicates the maximum temperature at which a pressure vessel can operate safely. This specification is crucial in industries like oil and gas, where high temperatures are common. Buyers need to ensure that the selected pressure vessel can handle the thermal conditions of their specific applications to avoid malfunctions.
5. Inspection and Testing Standards: What Should Buyers Know?
Pressure vessels are subject to various inspection and testing standards, such as the ASME Boiler and Pressure Vessel Code (BPVC). Compliance with these standards ensures that the vessel meets safety and quality benchmarks. Buyers should inquire about the certification of the vessels and the inspection processes undertaken by manufacturers.
What Are the Common Trade Terms Related to Pressure Vessels?
Understanding industry jargon can greatly enhance the procurement process for pressure vessels. Here are several common terms that B2B buyers should familiarize themselves with:
1. OEM (Original Equipment Manufacturer): What Does It Mean?
An OEM is a company that manufactures products that are used as components in another company’s end product. In the context of pressure vessels, working with an OEM can ensure that the buyer receives high-quality, compliant vessels designed specifically for their application.
2. MOQ (Minimum Order Quantity): Why Is This Relevant?
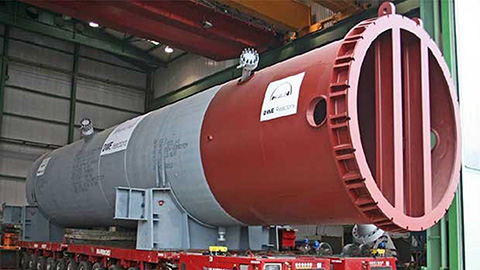
A stock image related to pressure vessel.
MOQ refers to the smallest quantity of a product that a supplier is willing to sell. Understanding MOQ is essential for budgeting and inventory management, as it can impact the overall cost of procurement. Buyers from Africa, South America, the Middle East, and Europe should negotiate MOQs that align with their operational needs.
3. RFQ (Request for Quotation): How Should It Be Used?
An RFQ is a document sent to suppliers to solicit price quotes for specific products or services. When purchasing pressure vessels, an RFQ allows buyers to compare pricing, terms, and specifications from multiple suppliers, facilitating better decision-making.
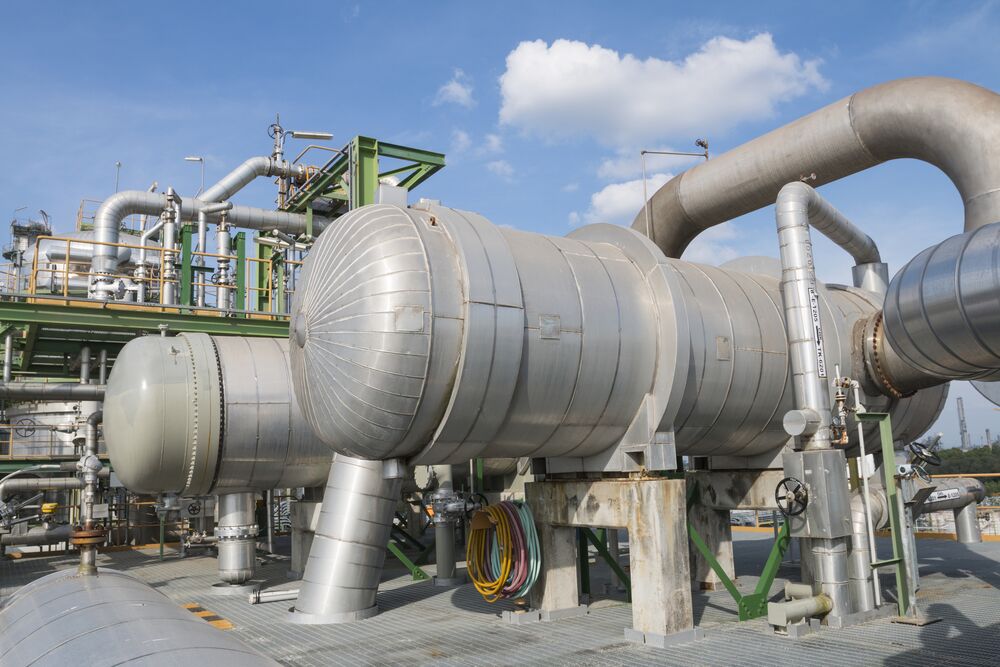
A stock image related to pressure vessel.
4. Incoterms (International Commercial Terms): What Do They Cover?
Incoterms are standardized international trade terms that define the responsibilities of buyers and sellers regarding the delivery of goods. Familiarity with Incoterms is essential for understanding shipping costs, insurance, and liability, which can significantly impact the total cost of acquiring pressure vessels.
5. ASME BPVC (American Society of Mechanical Engineers Boiler and Pressure Vessel Code): Why Is It Important?
The ASME BPVC is a set of standards governing the design, fabrication, and inspection of pressure vessels. Compliance with these standards is often a requirement in many industries, making it crucial for buyers to ensure that their suppliers adhere to these regulations for safety and reliability.
By understanding these technical properties and trade terminologies, B2B buyers can make informed decisions when sourcing pressure vessels, ensuring they meet both operational and regulatory requirements.
Navigating Market Dynamics and Sourcing Trends in the pressure vessel Sector
What Are the Current Market Dynamics and Key Trends in the Pressure Vessel Sector?
The pressure vessel market is poised for significant growth, driven by increased investments across various industries, including oil and gas, chemicals, and energy. International B2B buyers should note that the global demand for pressure vessels is influenced by factors such as industrial expansion, the push for renewable energy, and stringent safety regulations. For instance, the oil and gas sector continues to rely heavily on pressure vessels for high-temperature and high-pressure processes, while the chemical industry is seeing an uptick in the use of specialized vessels for complex chemical reactions.
Emerging technologies are reshaping the sourcing landscape. The rise of Industry 4.0 is introducing smart manufacturing practices and IoT-enabled pressure vessels, which enhance monitoring capabilities and predictive maintenance. Buyers should consider suppliers who are investing in these technologies, as they can provide enhanced performance and reliability. Additionally, the transition to composite materials is gaining traction, offering lighter and more corrosion-resistant alternatives to traditional steel. This trend is particularly relevant for buyers in regions like Africa and South America, where cost-effective solutions are essential.
Market dynamics are also shifting due to geopolitical factors and trade agreements. Buyers in the Middle East and Europe must navigate complexities arising from tariffs and international regulations, making it crucial to partner with suppliers who understand local compliance requirements. By staying informed about these trends, B2B buyers can make strategic sourcing decisions that align with their operational needs.
How Can Sustainability and Ethical Sourcing Impact B2B Buying Decisions in the Pressure Vessel Sector?
Sustainability is increasingly becoming a critical consideration in the pressure vessel sector. The environmental impact of manufacturing processes and materials used in pressure vessels cannot be overlooked. Buyers are now looking for suppliers who prioritize eco-friendly practices, such as minimizing waste and reducing carbon footprints. This shift is particularly pronounced in regions like Europe, where regulatory frameworks encourage sustainable manufacturing.
Ethical sourcing plays a vital role in establishing robust supply chains. B2B buyers should seek suppliers who adhere to ethical labor practices and transparent sourcing methods. Certifications such as ISO 14001 for environmental management and ASME certification for safety and quality assurance are indicators of a supplier’s commitment to sustainability. Additionally, materials such as recycled steel and bio-composites are gaining popularity, providing buyers with options that align with their sustainability goals.
By prioritizing suppliers with strong sustainability credentials, B2B buyers can not only reduce their environmental impact but also enhance their corporate reputation. This alignment with sustainability can be a deciding factor for clients and stakeholders who are increasingly aware of corporate responsibility.
What Is the Brief Evolution of the Pressure Vessel Market?
The evolution of the pressure vessel market reflects broader industrial advancements. Initially developed for steam boilers in the 19th century, pressure vessels have transformed significantly with the advent of modern engineering techniques and materials. The introduction of stringent safety standards, such as the ASME Boiler and Pressure Vessel Code, has been pivotal in shaping design and manufacturing practices.
As industries evolved, so did the applications of pressure vessels. Today, they are integral to various sectors, including energy, pharmaceuticals, and food processing. The shift towards high-performance materials, such as composites and advanced alloys, highlights the industry’s response to the demand for more efficient and durable solutions. Understanding this evolution is essential for B2B buyers as it provides context for current trends and future innovations in the pressure vessel market.
Frequently Asked Questions (FAQs) for B2B Buyers of pressure vessel
-
How do I choose the right pressure vessel for my industry?
Selecting the appropriate pressure vessel depends on several factors, including the type of fluid (gas or liquid), operating pressure and temperature, and specific industry requirements. For industries like oil and gas, chemical, and energy, consider the material (carbon steel vs. stainless steel) and design specifications (e.g., spherical or cylindrical). Consult with manufacturers about compliance with relevant standards (like ASME) and ensure the vessel can handle your specific operational conditions. -
What are the key safety standards for pressure vessels?
Pressure vessels must adhere to strict safety standards to ensure reliability and prevent catastrophic failures. The American Society of Mechanical Engineers (ASME) Boiler and Pressure Vessel Code is a widely recognized standard, particularly Section VIII, which governs design, construction, and inspection. Depending on your region, you may also need to comply with local regulations, such as the European Pressure Equipment Directive (PED) or API standards in the oil and gas sector. -
What should I consider when vetting international suppliers of pressure vessels?
When sourcing pressure vessels from international suppliers, evaluate their certifications, production capabilities, and experience in your industry. Request references and case studies to assess their reliability and customer satisfaction. Consider their compliance with international standards and their ability to provide necessary documentation for shipping and customs. It’s also important to check their after-sales support and warranty terms to ensure long-term partnership viability. -
How can I customize a pressure vessel to meet my specific needs?
Customization options for pressure vessels often include adjustments in size, shape, material, and design features like insulation or internal components. Engage with your supplier early in the design process to discuss your unique requirements. Most manufacturers can provide tailored solutions but be prepared for potential changes in lead times and costs associated with custom designs. Ensure to review the technical specifications and compliance with applicable standards. -
What is the minimum order quantity (MOQ) for pressure vessels?
The MOQ for pressure vessels can vary significantly based on the manufacturer and the complexity of the design. For standard models, MOQs may be lower, while customized vessels often have higher minimums due to the specific production requirements. It’s advisable to communicate your needs clearly with potential suppliers to understand their MOQ policies and negotiate terms that align with your project scale. -
What payment terms should I expect when sourcing pressure vessels internationally?
Payment terms for international transactions can vary by supplier, but common practices include a percentage upfront (typically 30-50%) with the balance due upon delivery or after inspection. Some suppliers may offer letter of credit (LC) options for added security. Always clarify payment terms before finalizing contracts to avoid misunderstandings and ensure that your financial processes align with your cash flow requirements. -
How do I ensure quality assurance (QA) for pressure vessels?
To ensure quality assurance for pressure vessels, request a detailed QA plan from your supplier, including inspection and testing processes. Look for suppliers that conduct regular audits and adhere to international standards, such as ISO 9001. Additionally, consider third-party inspections during production and before shipment to verify compliance with your specifications and industry standards, providing an added layer of assurance. -
What logistics considerations should I be aware of when importing pressure vessels?
Logistics for importing pressure vessels involve several factors, including shipping methods, customs clearance, and handling requirements due to their size and weight. Work with experienced freight forwarders familiar with handling industrial equipment to navigate regulations and ensure timely delivery. Additionally, factor in local regulations for storage and installation, especially in regions with stringent safety codes, to avoid costly delays.
Important Disclaimer & Terms of Use
⚠️ Important Disclaimer
The information provided in this guide, including content regarding manufacturers, technical specifications, and market analysis, is for informational and educational purposes only. It does not constitute professional procurement advice, financial advice, or legal advice.
While we have made every effort to ensure the accuracy and timeliness of the information, we are not responsible for any errors, omissions, or outdated information. Market conditions, company details, and technical standards are subject to change.
B2B buyers must conduct their own independent and thorough due diligence before making any purchasing decisions. This includes contacting suppliers directly, verifying certifications, requesting samples, and seeking professional consultation. The risk of relying on any information in this guide is borne solely by the reader.
Strategic Sourcing Conclusion and Outlook for pressure vessel
As international B2B buyers navigate the complexities of sourcing pressure vessels, strategic sourcing emerges as a critical factor in optimizing procurement processes. By understanding the diverse applications and materials used in pressure vessels—such as the predominance of steel in the oil and gas sector and the growing interest in composite materials—buyers can make informed decisions that align with their operational needs and sustainability goals.
How Can Strategic Sourcing Enhance Your Procurement of Pressure Vessels?
Investing in strategic sourcing not only ensures compliance with rigorous safety standards, such as the ASME Boiler and Pressure Vessel Code but also fosters relationships with reputable manufacturers who prioritize quality and reliability. This approach can mitigate risks associated with supply chain disruptions, particularly in regions like Africa, South America, the Middle East, and Europe, where market dynamics are rapidly evolving.
What Does the Future Hold for Pressure Vessel Procurement?
Looking ahead, the pressure vessel market is poised for growth, driven by technological advancements and increased investment across various industries. Buyers are encouraged to leverage these trends by exploring innovative designs and materials that enhance performance and safety. As you consider your procurement strategies, prioritize partnerships with suppliers that demonstrate a commitment to quality, sustainability, and technological innovation. Embrace this opportunity to not only secure essential equipment but to also position your organization as a leader in your industry.