Maximize Efficiency: The Ultimate Vane Rotary Guide (2025)
Introduction: Navigating the Global Market for vane rotary
Navigating the complexities of sourcing rotary vane pumps can be a daunting challenge for international B2B buyers, especially in regions like Africa, South America, the Middle East, and Europe. These essential components are pivotal in various industries, yet understanding their specifications, applications, and supplier reliability is crucial for making informed purchasing decisions. This guide serves as a comprehensive resource, covering the diverse types of rotary vane pumps, their operational principles, and the myriad applications they serve, from fuel transfer to chemical handling.
As you delve into the intricacies of rotary vane technology, you will find insights on effective supplier vetting processes, strategies for cost management, and tips for ensuring compatibility with your specific operational needs. By equipping yourself with this knowledge, you can streamline your procurement process, minimize risks, and enhance your operational efficiency. This guide is tailored to empower B2B buyers by providing actionable insights that facilitate smarter, more informed decisions in the global market for rotary vane pumps. Whether you are sourcing for the energy sector in Nigeria, the chemical industry in Brazil, or manufacturing in France, understanding the nuances of these pumps will help you optimize your supply chain and drive business success.
Understanding vane rotary Types and Variations
Type Name | Key Distinguishing Features | Primary B2B Applications | Brief Pros & Cons for Buyers |
---|---|---|---|
Standard Rotary Vane Pump | Eccentric rotor with sliding vanes, self-priming capability | Fuel transfer, chemical handling | Pros: Low maintenance, economical. Cons: Not suitable for high viscosity liquids. |
Oil-Sealed Rotary Vane Pump | Uses oil for lubrication and sealing, operates in vacuum | Vacuum applications, food processing | Pros: Efficient in creating a vacuum. Cons: Requires regular oil maintenance. |
Dry Rotary Vane Pump | Oil-free operation, ideal for sensitive applications | Pharmaceutical, semiconductor industries | Pros: No contamination risk. Cons: Higher initial cost than oil-sealed variants. |
High-Pressure Rotary Vane Pump | Designed for higher pressure applications, robust construction | Hydraulic systems, industrial applications | Pros: Handles high pressure effectively. Cons: More complex and costly. |
Reversible Rotary Vane Pump | Capable of fluid flow in both directions | Loading/unloading, fluid recovery | Pros: Versatile for various applications. Cons: May require additional controls for operation. |
What are the Key Characteristics of Standard Rotary Vane Pumps?
Standard rotary vane pumps are characterized by their use of an eccentrically mounted rotor that allows sliding vanes to extend and retract, creating a series of fluid chambers. These pumps excel in applications involving low to medium viscosity liquids, making them ideal for fuel transfer and chemical handling. When purchasing, buyers should consider the maintenance requirements and the type of media being pumped, as these pumps are not suited for high-viscosity fluids.
How do Oil-Sealed Rotary Vane Pumps Operate?
Oil-sealed rotary vane pumps utilize oil for lubrication and sealing, which enhances their efficiency in vacuum generation. They are commonly employed in food processing and laboratory applications where a stable vacuum is crucial. Buyers should note that while these pumps are efficient, they require regular oil maintenance to prevent contamination and ensure optimal performance. Understanding the specific vacuum requirements of your application will help in selecting the appropriate model.
Why Choose Dry Rotary Vane Pumps?
Dry rotary vane pumps are designed to operate without oil, making them suitable for applications in sensitive industries such as pharmaceuticals and semiconductors. Their oil-free operation eliminates the risk of contamination, a significant advantage in regulated environments. However, buyers should be prepared for a higher initial investment and consider the long-term operational costs, as these pumps may require more frequent replacements of vanes due to wear.
What are the Advantages of High-Pressure Rotary Vane Pumps?
High-pressure rotary vane pumps are engineered to handle demanding applications that require robust construction and the ability to operate under high pressure. They are commonly found in hydraulic systems and various industrial processes. While they provide excellent performance under pressure, potential buyers should be aware of their complexity and higher cost, which can impact the overall budget for equipment procurement.
How do Reversible Rotary Vane Pumps Enhance Versatility?
Reversible rotary vane pumps are unique in their capability to facilitate fluid flow in both directions, making them particularly useful for loading and unloading operations. This versatility allows businesses to maximize efficiency in fluid recovery processes. Buyers should consider the additional controls required for operation and the specific applications to ensure that this type of pump aligns with their operational needs.
Key Industrial Applications of vane rotary
Industry/Sector | Specific Application of Vane Rotary | Value/Benefit for the Business | Key Sourcing Considerations for this Application |
---|---|---|---|
Oil & Gas | Fuel and Lubrication Transfer | Efficient transfer of low to medium viscosity fluids, reducing downtime and maintenance costs. | Ensure compatibility with specific fuels and lubricants; consider regional regulations. |
Chemical Processing | Chemical Handling and Transfer | Reliable movement of chemicals with minimal leakage, enhancing safety and operational efficiency. | Evaluate material compatibility with chemicals; assess the need for explosion-proof designs. |
Food & Beverage | Liquid Transfer in Packaging | Maintains product integrity and hygiene standards during transfer processes. | Focus on food-grade materials; check for compliance with international food safety standards. |
Automotive | Oil and Fluid Management in Manufacturing | Reduces operational costs by allowing for direct and efficient fluid transfer in production lines. | Identify durability and wear resistance; assess the need for easy maintenance and part replacement. |
Pharmaceuticals | Transfer of Solvents and Active Ingredients | Ensures precision in the transfer of sensitive materials, reducing waste and contamination risks. | Verify compliance with pharmaceutical regulations; consider the need for specialized seals and lubricants. |
How is Vane Rotary Used in the Oil & Gas Sector?
In the oil and gas industry, vane rotary pumps are crucial for fuel and lubrication transfer. They efficiently handle low to medium viscosity fluids, which is essential for maintaining operations with minimal downtime. International B2B buyers should consider the pump’s compatibility with specific fuels and lubricants, as well as regional regulations regarding fuel transfer. Ensuring the pump’s durability against corrosive substances is also critical.
What Role Does Vane Rotary Play in Chemical Processing?
In chemical processing, vane rotary pumps are employed for the safe handling and transfer of various chemicals. Their design minimizes leakage, which enhances safety and operational efficiency in environments where hazardous materials are present. Buyers must evaluate the material compatibility of the pump with specific chemicals to prevent degradation. Additionally, assessing the need for explosion-proof designs can be vital, especially in regions with strict safety regulations.
How is Vane Rotary Essential in Food & Beverage Applications?
The food and beverage industry utilizes vane rotary pumps for liquid transfer during packaging processes. These pumps help maintain product integrity and hygiene, essential for compliance with food safety standards. Buyers should focus on sourcing food-grade materials and ensure that the pumps meet international food safety regulations to avoid contamination. Considering the pump’s ability to handle varying viscosities of food products is also important.
Why is Vane Rotary Important for Automotive Manufacturing?
In automotive manufacturing, vane rotary pumps are integral for oil and fluid management. They facilitate direct and efficient fluid transfer in production lines, which helps reduce operational costs. For international buyers, identifying pumps with high durability and wear resistance is essential, as they will be subjected to rigorous usage. Additionally, ease of maintenance and availability of replacement parts can significantly influence the total cost of ownership.
How Do Vane Rotary Pumps Benefit the Pharmaceutical Industry?
Vane rotary pumps are critical in the pharmaceutical sector for the precise transfer of solvents and active ingredients. Their design reduces waste and minimizes contamination risks, which is vital in maintaining product quality. International B2B buyers must verify that pumps comply with stringent pharmaceutical regulations and consider the need for specialized seals and lubricants to ensure safety and efficacy in their applications.
3 Common User Pain Points for ‘vane rotary’ & Their Solutions
Scenario 1: Difficulty in Handling High Viscosity Fluids
The Problem: Many B2B buyers in industries such as food processing and chemicals face the challenge of pumping high viscosity fluids. Common applications include oils, syrups, and thick paints, which can significantly hinder the efficiency of a rotary vane pump. When the viscosity is too high, the sliding vanes struggle to create a proper seal, leading to reduced flow rates, increased wear on the pump, and potentially costly downtime.
The Solution: To effectively handle high viscosity fluids with a rotary vane pump, it is crucial to select a model designed with heating jackets or other heating mechanisms. These features help maintain the fluid at a suitable temperature, enhancing pumpability. When sourcing a pump, inquire specifically about models that offer this option, and consult with manufacturers about fluid temperature ranges and viscosity specifications. Additionally, consider integrating variable frequency drives (VFDs) to control pump speed, allowing for adjustments based on viscosity changes. Regular maintenance schedules should be implemented to inspect and replace vanes as necessary to ensure optimal performance, reducing long-term operational costs.
Scenario 2: Abrasive Material Damage
The Problem: B2B buyers dealing with fluids containing abrasive particles, such as slurries or certain chemical mixtures, often find that traditional rotary vane pumps wear out rapidly due to the abrasive nature of the materials. This results in frequent replacements and higher maintenance costs, which can strain budgets and disrupt operational timelines.
The Solution: To combat the issues associated with abrasive materials, it is essential to choose a rotary vane pump with wear-resistant materials and coatings. Look for pumps that utilize advanced materials such as ceramic or hardened stainless steel for the vanes and cylinder. When specifying a pump, emphasize the need for abrasion resistance and request performance data under similar conditions to your application. Furthermore, consider implementing a pre-filter system to remove larger abrasive particles before they enter the pump, thus extending the life of the pump components. Regular monitoring of pump performance will also help identify wear patterns early, allowing for timely maintenance and part replacements.
Scenario 3: Inefficient Operation in High-Pressure Applications
The Problem: Buyers in industries that require high-pressure applications often struggle with the limitations of standard rotary vane pumps. As pressure increases, the sliding vanes may lose contact with the cylinder walls, leading to decreased efficiency and potential fluid leakage. This inefficiency can result in substantial energy costs and operational disruptions.
The Solution: For high-pressure applications, it is vital to select rotary vane pumps specifically designed to handle elevated pressure levels. These pumps often incorporate features such as reinforced vanes and enhanced sealing technologies. When sourcing a pump, consult with manufacturers about their capabilities in high-pressure scenarios and ensure that the pump is rated for the specific pressure requirements of your application. Additionally, implementing a staged pumping system can help manage fluid flow more efficiently, distributing the pressure load across multiple pumps. Regular pressure testing and maintenance checks will be essential to ensure that the pumps operate within their designated pressure ranges, maintaining efficiency and preventing failures.
Strategic Material Selection Guide for vane rotary
What Are the Key Materials Used in Vane Rotary Pumps?
When selecting materials for vane rotary pumps, B2B buyers must consider various factors, including the operating environment, fluid compatibility, and mechanical properties. Below are analyses of four common materials used in the construction of vane rotary pumps, focusing on their properties, advantages, disadvantages, and specific considerations for international buyers.
How Does Ductile Iron Perform in Vane Rotary Applications?
Key Properties: Ductile iron is known for its excellent tensile strength and toughness, making it suitable for high-stress applications. It typically has a temperature rating of up to 400°F (204°C) and can handle moderate pressures.
Pros & Cons: The durability of ductile iron is a significant advantage, as it can withstand wear and tear over time. However, it is susceptible to corrosion, which can be a limitation in certain applications. Manufacturing complexity is moderate, as ductile iron can be cast into various shapes.
Impact on Application: Ductile iron is compatible with a range of fluids, particularly those that are non-corrosive. However, its use in applications involving aggressive chemicals may require additional protective coatings.
Considerations for International Buyers: Buyers from regions like Africa and the Middle East should ensure compliance with local standards, such as ASTM and ISO, to avoid issues related to material quality and safety.
Why Is Stainless Steel a Preferred Material for Vane Rotary Pumps?
Key Properties: Stainless steel offers excellent corrosion resistance and can operate at higher temperatures (up to 1500°F or 815°C) and pressures compared to ductile iron.
Pros & Cons: The primary advantage of stainless steel is its longevity and resistance to rust, making it suitable for harsh environments. However, it is more expensive than ductile iron and may involve complex manufacturing processes, which can increase lead times.
Impact on Application: Stainless steel is ideal for applications involving corrosive fluids, such as acids or solvents. Its compatibility with a wide variety of media makes it a versatile choice for many industries.
Considerations for International Buyers: In Europe, compliance with standards like DIN and EN is crucial. Buyers should also consider the availability of stainless steel grades in their region to ensure timely procurement.
What Are the Benefits of Carbon Graphite in Vane Rotary Pumps?
Key Properties: Carbon graphite is known for its low friction properties and excellent wear resistance. It can operate effectively at temperatures up to 500°F (260°C) and has good chemical resistance.
Pros & Cons: The primary advantage is its ability to reduce wear on sliding vanes, leading to lower maintenance costs. However, carbon graphite can be brittle, making it less suitable for high-impact applications.
Impact on Application: Carbon graphite is particularly effective in applications involving low-viscosity fluids and can handle some abrasive materials. However, it may not be suitable for high-viscosity or highly abrasive media.
Considerations for International Buyers: Buyers should ensure that the carbon graphite used meets international standards, as variations in quality can affect pump performance.
How Does Aluminum Compare as a Material for Vane Rotary Pumps?
Key Properties: Aluminum is lightweight and has good corrosion resistance, with a temperature rating of up to 400°F (204°C) under normal operating conditions.
Pros & Cons: The lightweight nature of aluminum makes it easy to handle and install. However, it has lower tensile strength compared to ductile iron and stainless steel, which may limit its use in high-stress applications.
Impact on Application: Aluminum is suitable for low-pressure applications and can handle non-corrosive fluids. Its use in high-temperature applications is limited, making it less versatile than other materials.
Considerations for International Buyers: Buyers should check for compliance with local standards and consider the availability of aluminum components in their regions, especially in South America, where sourcing may be a challenge.
Summary Table of Material Selection for Vane Rotary Pumps
Material | Typical Use Case for Vane Rotary | Key Advantage | Key Disadvantage/Limitation | Relative Cost (Low/Med/High) |
---|---|---|---|---|
Ductile Iron | Non-corrosive fluid applications | Excellent durability and strength | Susceptible to corrosion | Medium |
Stainless Steel | Corrosive fluid handling | Superior corrosion resistance | Higher cost and complex manufacturing | High |
Carbon Graphite | Low-viscosity and some abrasive materials | Low friction and wear resistance | Brittle, limiting high-impact applications | Medium |
Aluminum | Low-pressure and non-corrosive applications | Lightweight and easy to handle | Lower tensile strength | Low |
This strategic material selection guide provides valuable insights for international B2B buyers, enabling them to make informed decisions based on their specific operational needs and regional compliance requirements.
In-depth Look: Manufacturing Processes and Quality Assurance for vane rotary
What Are the Key Stages in the Manufacturing Process of Vane Rotary Pumps?
Manufacturing vane rotary pumps involves several critical stages, each essential for ensuring the final product’s performance and reliability. The main stages include material preparation, forming, assembly, and finishing.
Material Preparation: What Materials Are Used for Vane Rotary Pumps?
The choice of materials is fundamental in manufacturing vane rotary pumps. Typically, components are made from ductile iron or stainless steel, chosen for their wear resistance and compatibility with various fluids. Before processing, materials undergo rigorous inspections to verify their quality and suitability for the intended application. This stage may involve cutting, machining, and treating the materials to enhance their properties, such as corrosion resistance.
How Is Forming Carried Out in Vane Rotary Pump Manufacturing?
Forming processes, including casting and machining, are pivotal in shaping the pump components. For instance, the rotor is often cast to achieve the desired geometry, while precision machining is used to create critical tolerances on the sliding vanes and the cylindrical housing. Techniques like CNC machining ensure high accuracy, which is crucial for maintaining the efficiency and reliability of the pump.
What Aspects Are Considered During the Assembly of Vane Rotary Pumps?
The assembly phase is where all individual components come together. This involves aligning the rotor and sliding vanes within the cylindrical housing to create the necessary sealing and operational conditions. During assembly, careful attention is paid to the tolerances and clearances between parts to minimize wear and ensure smooth operation.
What Finishing Processes Are Essential for Vane Rotary Pumps?
Finishing processes, including surface treatment and coating, enhance the durability and performance of the pumps. Surface treatments may involve polishing or applying protective coatings to reduce friction and wear. Additionally, balancing the rotor is crucial to ensure smooth operation and minimize vibrations, which can lead to premature failure.
How Is Quality Assurance Implemented in Vane Rotary Pump Manufacturing?
Quality assurance (QA) is integral to the manufacturing process, ensuring that every pump meets industry standards and customer expectations. International standards like ISO 9001 are commonly adopted to establish a framework for quality management systems.
What International and Industry-Specific Standards Apply to Vane Rotary Pumps?
B2B buyers should familiarize themselves with relevant international standards and certifications, such as CE marking and API (American Petroleum Institute) standards, which indicate compliance with safety and performance criteria. These certifications not only enhance product credibility but also ensure that the pumps are suitable for specific applications, particularly in regulated industries.
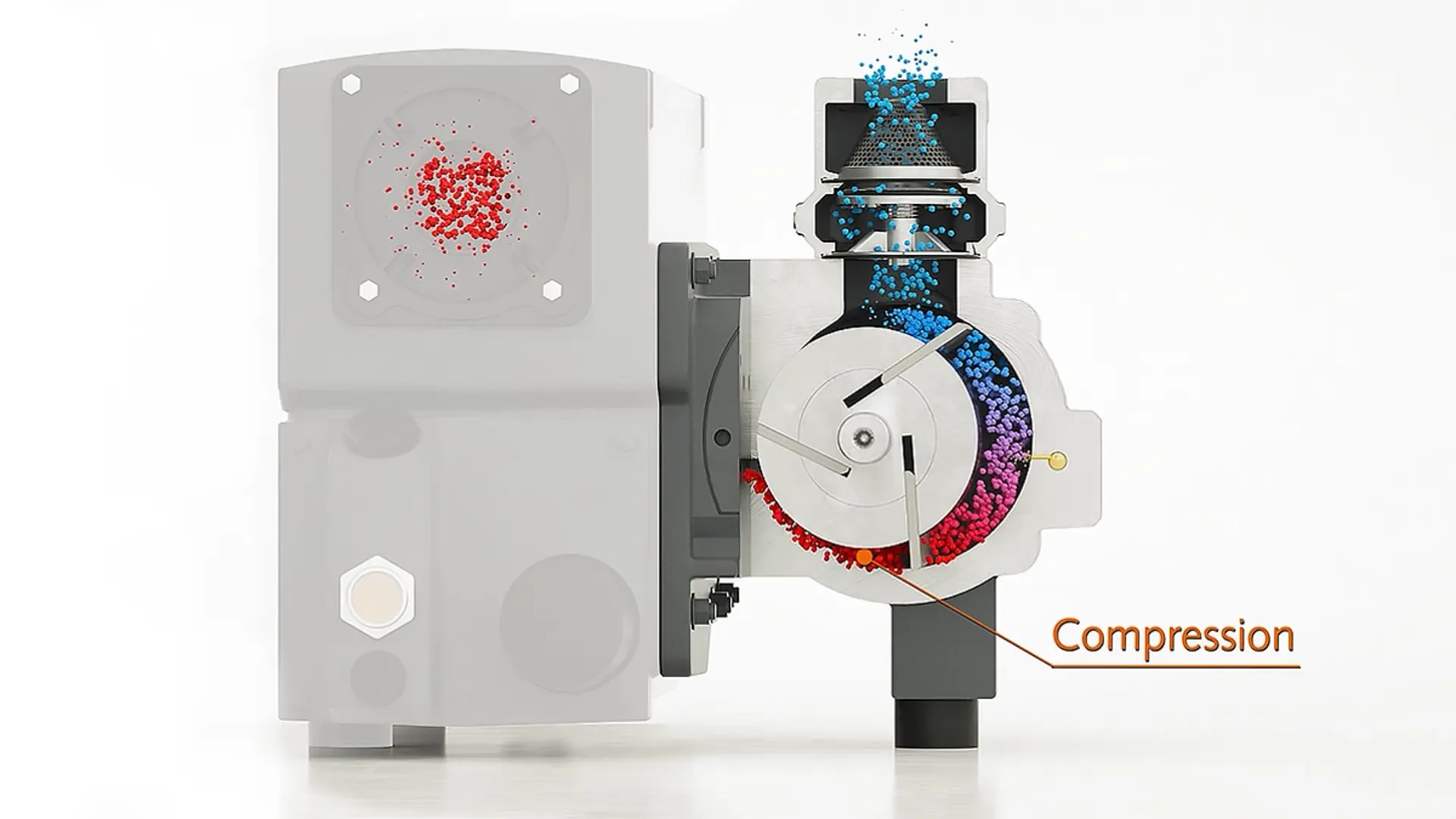
A stock image related to vane rotary.
What Are the Key Quality Control Checkpoints in the Manufacturing Process?
Quality control (QC) involves multiple checkpoints throughout the manufacturing process to identify and rectify issues early.
- Incoming Quality Control (IQC): This stage assesses raw materials upon arrival to ensure they meet specifications.
- In-Process Quality Control (IPQC): Continuous monitoring during the manufacturing process helps catch defects early. This may involve measuring tolerances and inspecting components at various stages.
- Final Quality Control (FQC): Before shipping, the finished pumps undergo rigorous testing to confirm their performance, including pressure tests and flow rate measurements.
What Testing Methods Are Commonly Used for Vane Rotary Pumps?
Common testing methods for vane rotary pumps include hydrostatic testing, performance testing under various load conditions, and endurance testing to simulate long-term use. These tests help ensure that the pumps will perform as expected in real-world applications.
How Can B2B Buyers Verify Supplier Quality Control Practices?
For international B2B buyers, particularly from Africa, South America, the Middle East, and Europe, verifying a supplier’s quality control practices is crucial. Here are some actionable steps:
- Conduct Supplier Audits: Regular audits of potential suppliers can provide insights into their manufacturing processes and adherence to quality standards.
- Request Quality Reports: Suppliers should provide documentation of their quality control processes, including results from IQC, IPQC, and FQC.
- Engage Third-Party Inspectors: Utilizing third-party inspection services can offer an unbiased assessment of the manufacturing and quality assurance processes. This is particularly important for buyers in regions with stringent regulatory requirements.
What Are the Quality Control Nuances for International B2B Buyers?
Navigating quality control nuances can be complex for international buyers. Different regions may have varying compliance requirements, so it’s essential to understand local regulations and certifications. Buyers should also consider language barriers and cultural differences that may affect communication regarding quality standards.
Establishing clear lines of communication with suppliers about expectations and requirements can mitigate misunderstandings. Additionally, leveraging technology for real-time monitoring and reporting can enhance transparency in the supply chain.
Conclusion: How to Ensure Quality in Vane Rotary Pump Procurement
For B2B buyers, particularly in diverse markets like Africa, South America, the Middle East, and Europe, understanding the manufacturing processes and quality assurance practices for vane rotary pumps is vital. By focusing on key manufacturing stages, adhering to international standards, and implementing robust quality control measures, buyers can ensure they procure high-quality, reliable products that meet their operational needs.
Practical Sourcing Guide: A Step-by-Step Checklist for ‘vane rotary’
The following guide serves as a practical checklist for B2B buyers focused on sourcing vane rotary pumps. This guide outlines essential steps to ensure you make an informed purchase that meets your operational needs and regulatory requirements.
Step 1: Define Your Technical Specifications
Establishing precise technical specifications is the foundation of your sourcing process. Identify the type of fluids you will be pumping, their viscosity, and the required flow rate and pressure ratings. This information is crucial, as different vane rotary pumps are designed for specific applications, and using the wrong pump can lead to inefficiencies or equipment failure.
- Fluid Characteristics: Consider the chemical compatibility of the pump materials with the fluids.
- Performance Requirements: Define the desired operating conditions such as temperature and pressure ranges.
Step 2: Research Reliable Manufacturers
Conduct thorough research on manufacturers that specialize in vane rotary pumps. Look for companies with a proven track record in your industry and region, as local support can be invaluable for maintenance and service.
- Industry Reputation: Read reviews and case studies to gauge customer satisfaction.
- Experience: Prioritize manufacturers with extensive experience in producing pumps for your specific application.
Step 3: Evaluate Potential Suppliers
Before making a commitment, it’s crucial to vet suppliers thoroughly. Request company profiles, case studies, and references from buyers in a similar industry or region. This due diligence helps ensure the reliability and quality of the supplier.
- Certifications: Verify that suppliers hold relevant certifications (e.g., ISO 9001) that attest to their quality management systems.
- After-sales Support: Assess the level of technical support and warranty terms offered.
Step 4: Request Detailed Quotes
When you have shortlisted potential suppliers, request detailed quotes that outline pricing, lead times, and terms of sale. This step allows you to compare offers on a like-for-like basis, ensuring transparency in your procurement process.
- Inclusions: Ensure the quote includes shipping, installation, and any other ancillary services.
- Negotiation: Use the quotes as a basis for negotiation to secure the best possible deal.
Step 5: Assess Maintenance and Service Options
Understanding the maintenance requirements and available service options is critical for long-term operational efficiency. Inquire about the frequency of maintenance, availability of spare parts, and support for repairs.
- Service Contracts: Consider if the supplier offers service contracts or ongoing maintenance plans.
- Replacement Parts: Ensure that spare parts are readily available in your region to minimize downtime.
Step 6: Check Compliance with Local Regulations
Ensure that the vane rotary pumps meet local regulations and industry standards in your target market. This is particularly important for sectors like food processing, pharmaceuticals, and chemicals, where compliance is mandatory.
- Documentation: Request compliance documentation, including safety certifications and material safety data sheets (MSDS).
- Local Standards: Familiarize yourself with any specific regional standards that may apply to your operations.
Step 7: Finalize and Place Your Order
After completing your evaluations and ensuring all criteria are met, finalize your decision. Place your order with the selected supplier, ensuring that all terms and conditions are clearly outlined in the purchase agreement.
- Payment Terms: Clarify payment terms and conditions to avoid misunderstandings.
- Delivery Schedule: Confirm the delivery timeline and any penalties for delays to ensure timely project execution.
By following these steps, international B2B buyers can confidently navigate the sourcing process for vane rotary pumps, ensuring that they acquire equipment that aligns with their operational needs and compliance requirements.
Comprehensive Cost and Pricing Analysis for vane rotary Sourcing
What Are the Key Cost Components in Vane Rotary Pump Sourcing?
When sourcing vane rotary pumps, international B2B buyers need to consider several key cost components that contribute to the overall pricing structure. The primary cost elements include:
-
Materials: The choice of materials significantly impacts the cost. Common materials like ductile iron and stainless steel are preferred for their durability and compatibility with various fluids. Higher-quality materials can lead to increased costs but may offer better performance and longevity.
-
Labor: Labor costs vary widely based on geographic location and the complexity of manufacturing processes. Regions with lower labor costs, such as parts of South America and Africa, may present opportunities for cost savings, but buyers must also consider potential trade-offs in quality.
-
Manufacturing Overhead: This includes indirect costs associated with production, such as utilities, rent, and equipment maintenance. Efficient manufacturing practices can help keep these costs down.
-
Tooling: The initial investment in tooling and equipment can be substantial, particularly for custom designs. Buyers should inquire about tooling costs, especially if they require specific modifications to standard pump designs.
-
Quality Control (QC): Ensuring product quality is crucial, especially in industries where pump failure can lead to significant downtime. Buyers should consider the QC processes implemented by suppliers, as robust QC can add to the cost but also reduce long-term risks.
-
Logistics: Shipping and handling costs can vary based on the distance, shipping method, and weight of the pumps. International buyers should factor in potential tariffs and duties, especially when importing from Europe or the Middle East.
-
Margin: Suppliers typically add a margin to cover their costs and profit. This margin can vary based on market competition, supplier reputation, and the buyer’s negotiation power.
How Do Price Influencers Affect Vane Rotary Pump Costs?
Several factors can influence the pricing of vane rotary pumps, impacting the final cost for buyers:
-
Volume/MOQ (Minimum Order Quantity): Purchasing in larger quantities often leads to reduced per-unit costs. Buyers should assess their needs to determine if they can meet MOQ requirements for better pricing.
-
Specifications and Customization: Customization can drive up costs due to the need for specialized materials or design alterations. Buyers should balance their specific requirements with cost implications.
-
Materials Quality and Certifications: High-quality materials and certifications (like ISO standards) can increase costs but may be essential for compliance in certain industries. Buyers must evaluate the necessity of these factors based on their application.
-
Supplier Factors: The supplier’s reputation, reliability, and service quality can affect pricing. Established suppliers may charge a premium, but their experience can lead to better long-term value.
-
Incoterms: Understanding Incoterms is vital for international transactions. They define responsibilities for shipping, insurance, and tariffs, which can significantly influence overall costs.
What Are the Best Buyer Tips for Cost-Efficiency in Vane Rotary Pump Sourcing?
To optimize costs when sourcing vane rotary pumps, buyers should consider the following strategies:
-
Negotiate Effectively: Engage suppliers in discussions to explore flexible pricing options, especially for bulk orders. Understanding the supplier’s cost structure can provide leverage during negotiations.
-
Evaluate Total Cost of Ownership (TCO): Beyond initial purchase prices, consider maintenance, operational costs, and potential downtime. A more expensive pump may offer greater reliability and lower TCO in the long run.
-
Research Pricing Nuances for International Buyers: Different regions may offer varying pricing structures due to local market conditions. Buyers from Africa, South America, the Middle East, and Europe should conduct thorough market research to identify the best sourcing options.
-
Seek Multiple Quotes: Obtaining quotes from multiple suppliers can provide insights into the market rate for vane rotary pumps and help identify the most cost-effective options.
Disclaimer for Indicative Prices
Prices for vane rotary pumps can vary widely based on the factors discussed above. The information provided serves as a general guideline; buyers should conduct their own research and consult with suppliers for accurate and current pricing tailored to their specific needs.
Alternatives Analysis: Comparing vane rotary With Other Solutions
Exploring Alternatives to Vane Rotary Pumps
When considering the best fluid transfer solution for your operations, understanding the alternatives to vane rotary pumps is crucial. Vane rotary pumps offer unique advantages but may not always be the ideal choice depending on specific application requirements. This section will compare vane rotary pumps against two viable alternatives: gear pumps and diaphragm pumps, highlighting their performance, cost, ease of implementation, maintenance needs, and best use cases.
Comparison Aspect | Vane Rotary | Gear Pump | Diaphragm Pump |
---|---|---|---|
Performance | Excellent for low to medium viscosity fluids; struggles with high viscosity and abrasives. | Suitable for a wide range of viscosities; not ideal for shear-sensitive fluids. | Great for shear-sensitive fluids; limited viscosity handling. |
Cost | Moderate initial cost; low operating costs due to efficiency. | Generally lower initial cost; may incur higher maintenance costs. | Higher initial investment; cost-effective in long-term applications. |
Ease of Implementation | Straightforward installation; minimal space required. | Easy installation; requires precise alignment. | More complex setup; requires additional space and may need specialized mounting. |
Maintenance | Low maintenance; vanes can be replaced easily. | Moderate maintenance; gear wear may require frequent inspections. | Low maintenance; diaphragm replacement needed periodically. |
Best Use Case | Fuel transfer, lubrication, chemical handling. | Oil and fuel transfer, food processing. | Pharmaceutical, food & beverage, and hazardous materials handling. |
Detailed Breakdown of Alternatives
What Are Gear Pumps and Their Benefits?
Gear pumps utilize meshing gears to pump fluids, making them efficient for transferring a variety of liquid viscosities. They are particularly well-suited for applications requiring precise flow rates and pressure consistency. The primary advantage of gear pumps is their simplicity and effectiveness in transferring viscous fluids. However, they can generate heat and may not be suitable for shear-sensitive materials, which can affect product quality.
How Do Diaphragm Pumps Compare?
Diaphragm pumps operate by using a flexible diaphragm to create a vacuum that draws fluid into the pump chamber. This technology is particularly beneficial for transferring corrosive or shear-sensitive fluids, making them ideal for applications in the pharmaceutical and food industries. While diaphragm pumps typically have a higher initial cost and may require more space, their ability to handle a wide range of fluids with minimal contamination risks makes them an attractive choice for certain B2B applications.
Conclusion: Choosing the Right Solution for Your Needs
Selecting the right fluid transfer solution ultimately depends on your specific application requirements. Vane rotary pumps are excellent for low to medium viscosity fluids, particularly in fuel transfer and lubrication contexts. However, if your operation involves highly viscous or shear-sensitive fluids, consider gear or diaphragm pumps as viable alternatives. Evaluate factors such as performance needs, budget constraints, maintenance capabilities, and the specific fluid characteristics to make an informed decision that aligns with your operational goals.
Essential Technical Properties and Trade Terminology for vane rotary
What Are the Key Technical Properties of Vane Rotary Pumps?
When selecting a vane rotary pump, understanding its technical specifications is crucial for ensuring optimal performance and longevity. Here are some essential properties to consider:
1. Material Grade: Why Is It Important for Durability?
The material composition of a rotary vane pump significantly impacts its durability and compatibility with various fluids. Common materials include ductile iron and stainless steel, which provide excellent wear resistance and corrosion protection. For B2B buyers, choosing the right material grade can help minimize maintenance costs and extend the pump’s lifespan, especially in harsh operational environments.
2. Tolerance: How Does It Affect Pump Efficiency?
Tolerance refers to the permissible limit of variation in a pump’s dimensions. High precision in manufacturing can reduce the risk of leaks and improve efficiency. B2B buyers must understand the tolerances specified by manufacturers, as tighter tolerances generally indicate better performance and reliability, leading to reduced operational downtime.
3. Maximum Operating Pressure: What Should You Know?
Every vane rotary pump has a specified maximum operating pressure, which indicates the highest pressure the pump can handle effectively. Operating beyond this limit can lead to pump failure or inefficiency. Buyers should assess their specific application needs and ensure that the selected pump meets or exceeds these pressure requirements for optimal performance.
4. Flow Rate: How to Determine the Right Capacity?
Flow rate, measured in liters per minute (LPM) or gallons per minute (GPM), is a critical specification that defines the volume of fluid a pump can move within a given time. Selecting a pump with the right flow rate is essential for meeting operational demands without overloading the system. B2B buyers should calculate their requirements based on application needs and choose a pump that provides the necessary capacity.
5. Viscosity Range: Why Is It Critical for Application Suitability?
The viscosity range indicates the types of fluids a vane rotary pump can effectively handle, typically categorized as low, medium, or high viscosity. Understanding this range is vital for B2B buyers, especially when dealing with various liquids. Choosing a pump outside the recommended viscosity limits can lead to inefficiencies and increased wear on the pump components.
What Are Common Trade Terms Associated with Vane Rotary Pumps?
Understanding industry jargon is essential for effective communication and successful procurement. Here are some common terms relevant to vane rotary pumps:
1. OEM (Original Equipment Manufacturer): What Does It Mean for Your Purchase?
An OEM is a company that produces parts or equipment that may be marketed by another manufacturer. In the context of vane rotary pumps, purchasing from an OEM ensures that buyers receive high-quality products designed specifically for their applications, often accompanied by warranties and service support.
2. MOQ (Minimum Order Quantity): How Does It Impact Your Procurement Strategy?
MOQ refers to the smallest quantity of a product that a supplier is willing to sell. For B2B buyers, understanding MOQs is crucial for budget planning and inventory management. It can influence purchasing decisions, especially for smaller businesses or those testing new products.
3. RFQ (Request for Quotation): Why Is It Essential in the Buying Process?
An RFQ is a document sent to suppliers to request pricing and terms for specific products. For buyers, issuing an RFQ helps gather competitive quotes, enabling informed decision-making based on price, quality, and delivery terms. It is a critical step in ensuring transparency and cost-effectiveness in the procurement process.
4. Incoterms: How Do They Affect International Trade?
Incoterms (International Commercial Terms) are standardized trade terms that define the responsibilities of buyers and sellers in international transactions. Understanding these terms is vital for B2B buyers, as they clarify who is responsible for shipping costs, insurance, and risk during transit, ensuring smooth cross-border transactions.
5. Lead Time: What Should You Consider When Planning Purchases?
Lead time refers to the duration from placing an order to receiving the product. For B2B buyers, understanding lead times is essential for inventory management and project planning. Long lead times can affect operational schedules, making it crucial to factor this into procurement strategies.
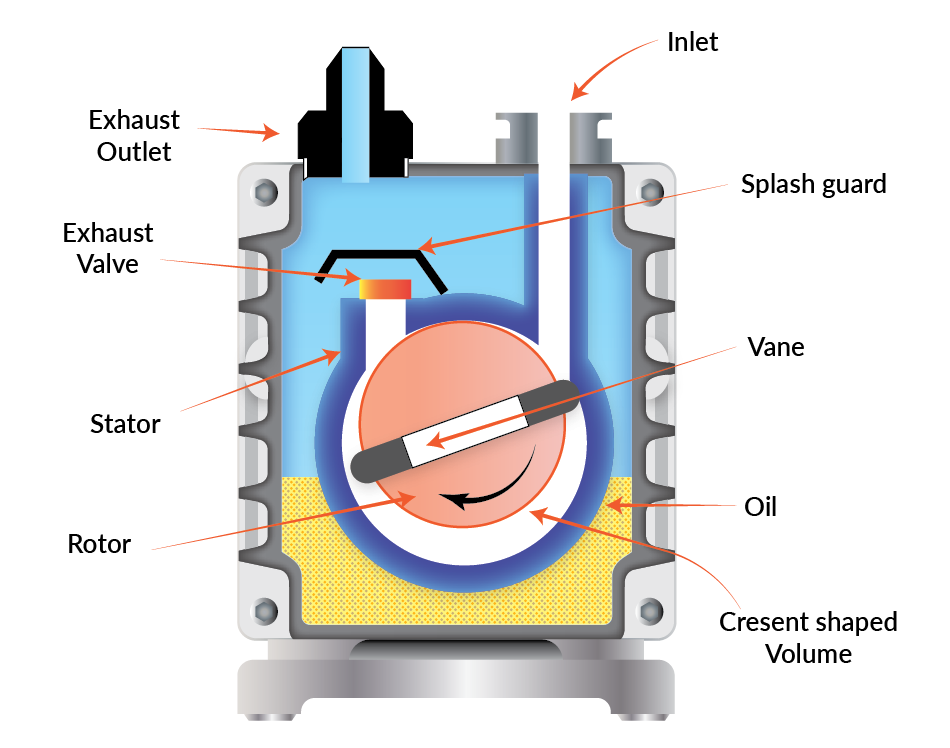
A stock image related to vane rotary.
By familiarizing themselves with these technical properties and trade terms, international B2B buyers can make informed decisions when purchasing vane rotary pumps, ultimately optimizing their operations and ensuring long-term success.
Navigating Market Dynamics and Sourcing Trends in the vane rotary Sector
What Are the Current Trends Influencing the Vane Rotary Market?
The global vane rotary market is witnessing significant growth, driven by the increasing demand for efficient fluid handling solutions across various industries. Key drivers include the rise in energy-efficient technologies, a growing focus on automation, and the need for versatile pumping solutions in sectors such as oil and gas, chemical processing, and food and beverage. In regions like Africa, South America, and the Middle East, where infrastructure development is rapidly evolving, the demand for reliable and low-maintenance pumps is particularly pronounced.
Emerging technologies such as IoT-enabled pump systems are reshaping the market dynamics, allowing for real-time monitoring and predictive maintenance, thus enhancing operational efficiency. B2B buyers from Europe, particularly in France and Germany, are increasingly looking for suppliers that offer smart solutions that integrate seamlessly with existing systems. Additionally, the trend towards digitalization is encouraging buyers to prioritize suppliers that provide comprehensive online support and documentation, facilitating smoother transactions and decision-making processes.
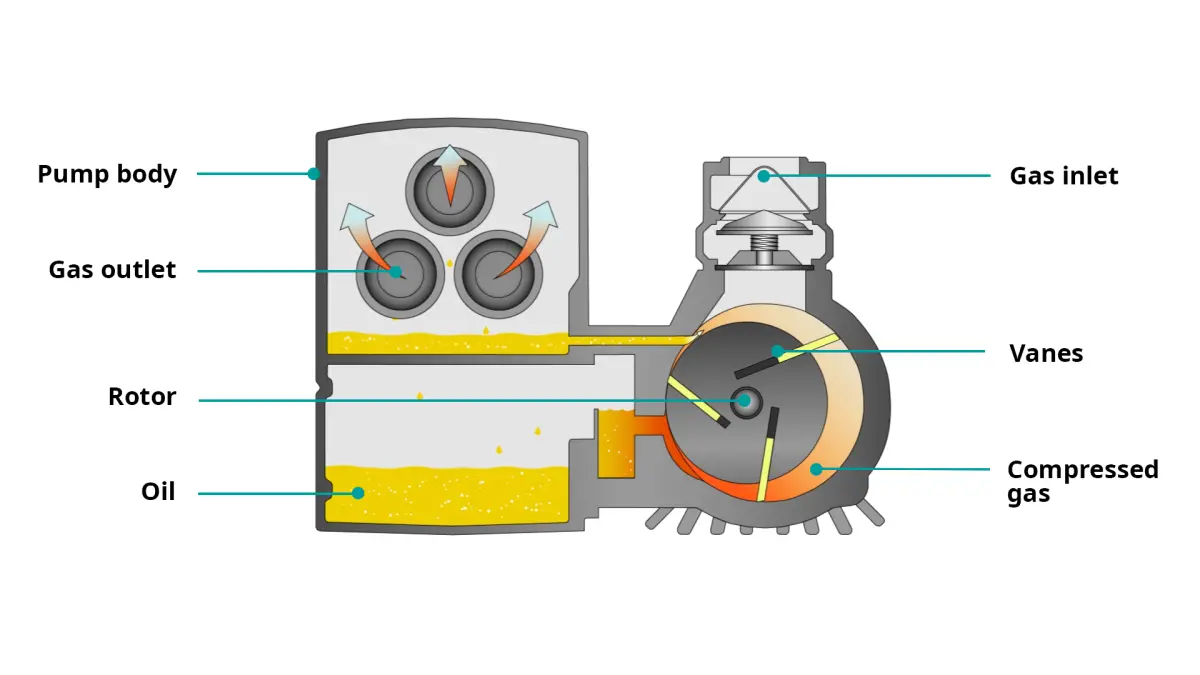
A stock image related to vane rotary.
How Does Sustainability Influence Sourcing Decisions in the Vane Rotary Sector?
Sustainability is becoming a critical factor for international B2B buyers, as the environmental impact of sourcing decisions weighs heavily on corporate reputations and regulatory compliance. In the vane rotary sector, the demand for environmentally friendly materials and processes is rising. Suppliers who prioritize ethical sourcing practices and demonstrate a commitment to sustainability through certifications, such as ISO 14001 or the Global Reporting Initiative (GRI), are increasingly favored by buyers.
Moreover, the use of ‘green’ materials, such as biodegradable lubricants and recyclable components, is gaining traction. Buyers from regions like Europe are particularly attentive to these factors due to stringent environmental regulations. By choosing suppliers that adopt sustainable practices, B2B buyers can enhance their brand image while contributing positively to the environment. This trend also aligns with the global movement towards circular economy principles, where waste is minimized, and materials are reused, thus presenting an opportunity for competitive advantage in the marketplace.
What Is the Historical Context of Vane Rotary Technology?
The vane rotary technology has evolved significantly since its inception in the early 20th century. Initially designed for simple fluid transfer applications, advancements in materials science and engineering have transformed these pumps into versatile solutions capable of handling a wide range of fluids and conditions. The introduction of wear-resistant materials and improved sealing technologies has enhanced the durability and efficiency of vane rotary pumps, making them suitable for more demanding applications.
In recent decades, the integration of electronic controls and monitoring systems has further advanced the technology, allowing for greater precision and reliability. This evolution is crucial for B2B buyers, as modern vane rotary pumps not only offer improved performance but also align with the growing trends in automation and digitalization within industrial processes. Understanding this historical context can help buyers make informed decisions about sourcing and investment in vane rotary technologies.
Frequently Asked Questions (FAQs) for B2B Buyers of vane rotary
-
How do I solve issues with rotary vane pump performance?
To address performance issues with rotary vane pumps, first check the viscosity of the fluid being pumped. High-viscosity liquids can impede the movement of the sliding vanes, leading to reduced efficiency. Consider using heating jackets to maintain fluid temperature and enhance pumpability. Additionally, inspect the vanes for wear or damage, as replacement may be necessary for optimal performance. Regular maintenance, including lubrication checks, can prevent operational problems and prolong pump life. -
What is the best rotary vane pump for chemical handling applications?
The ideal rotary vane pump for chemical handling should be constructed from corrosion-resistant materials such as stainless steel or specialized alloys. Look for models designed for the specific chemicals you plan to handle, as compatibility is crucial. Pumps with adjustable speed control and self-priming capabilities are also advantageous. Brands with a solid reputation for reliability and durability in chemical environments, such as Blackmer or Leybold, are typically recommended by industry professionals. -
What factors should I consider when sourcing rotary vane pumps internationally?
When sourcing rotary vane pumps internationally, consider the supplier’s reputation, product certifications, and compliance with international standards. Evaluate their ability to provide technical support and after-sales service. It’s also essential to assess logistics capabilities, including shipping costs and delivery times to your region. Lastly, verify their experience in your specific industry sector to ensure they understand your unique requirements. -
How can I vet suppliers of rotary vane pumps effectively?
To vet suppliers of rotary vane pumps, start by conducting thorough background research. Look for reviews and testimonials from previous clients, and request references to gauge reliability. Assess their production capabilities and quality control processes, ensuring they follow ISO standards. Additionally, consider visiting their facility if possible or requesting a virtual tour. Engaging in direct communication can also provide insights into their customer service and responsiveness. -
What are the common customization options available for rotary vane pumps?
Many manufacturers offer customization options for rotary vane pumps, including modifications in size, material, and design features tailored to specific applications. Customization may involve adjusting the pump’s capacity, altering inlet/outlet connections, or integrating specialized sealing systems for unique fluids. Discuss your specific requirements with potential suppliers to explore available options. Custom solutions can enhance performance and efficiency in specialized industrial applications. -
What is the minimum order quantity (MOQ) for rotary vane pumps from international suppliers?
Minimum order quantities (MOQs) for rotary vane pumps can vary widely among suppliers, often ranging from one unit to several dozen. Factors influencing MOQ include the supplier’s production capabilities, the complexity of the pump, and your specific customization requests. When negotiating, inquire if the supplier offers flexibility in MOQs, especially for trial orders or initial partnerships. Understanding their MOQ policy can help you manage inventory and cash flow effectively. -
What payment terms should I expect when purchasing rotary vane pumps internationally?
Payment terms for international purchases of rotary vane pumps typically include options such as advance payment, letters of credit, or payment upon delivery. Common practices involve a deposit upfront, followed by the balance upon shipment or delivery. It’s essential to negotiate terms that align with your financial capabilities and risk tolerance. Additionally, consider using secure payment methods to protect your transaction and reduce the risk of fraud. -
How do I ensure quality assurance when sourcing rotary vane pumps?
To ensure quality assurance when sourcing rotary vane pumps, request detailed product specifications and certifications from your supplier. Look for compliance with international standards such as ISO 9001, which indicates a commitment to quality management. You may also want to arrange for third-party inspections or audits of the manufacturing process. Establishing clear quality expectations and maintaining open communication with your supplier throughout the procurement process can help safeguard against quality issues.
Important Disclaimer & Terms of Use
⚠️ Important Disclaimer
The information provided in this guide, including content regarding manufacturers, technical specifications, and market analysis, is for informational and educational purposes only. It does not constitute professional procurement advice, financial advice, or legal advice.
While we have made every effort to ensure the accuracy and timeliness of the information, we are not responsible for any errors, omissions, or outdated information. Market conditions, company details, and technical standards are subject to change.
B2B buyers must conduct their own independent and thorough due diligence before making any purchasing decisions. This includes contacting suppliers directly, verifying certifications, requesting samples, and seeking professional consultation. The risk of relying on any information in this guide is borne solely by the reader.
Strategic Sourcing Conclusion and Outlook for vane rotary
What Are the Key Takeaways for International B2B Buyers in Vane Rotary Sourcing?
As we conclude our exploration of vane rotary pumps, it’s clear that strategic sourcing plays a pivotal role in optimizing operational efficiency and reducing costs. International B2B buyers, particularly from Africa, South America, the Middle East, and Europe, should prioritize pumps that are efficient, low-maintenance, and versatile enough to handle a range of fluids and applications. Understanding the strengths and limitations of rotary vane pumps—such as their suitability for low to medium viscosity liquids and their challenges with high-pressure environments—will empower buyers to make informed decisions that align with their specific needs.
How Can Buyers Leverage Strategic Sourcing for Future Success?
Emphasizing strategic sourcing not only enhances procurement processes but also fosters stronger supplier relationships, ensuring access to high-quality products and services. Buyers are encouraged to engage with manufacturers who demonstrate reliability and innovation, as these partnerships can lead to better pricing, customized solutions, and improved supply chain resilience.
What Is the Future Outlook for Vane Rotary Pumps?
Looking ahead, the demand for efficient and adaptable pumping solutions is expected to rise across various industries. B2B buyers are urged to stay ahead of market trends and technological advancements in rotary vane pumps. By integrating these insights into their sourcing strategies, businesses can enhance operational performance and gain a competitive edge in their respective markets.