Maximize Savings: The Ultimate Graphite Electrode Guide (2025)
Introduction: Navigating the Global Market for graphite electrode
Navigating the global market for graphite electrodes can be a daunting challenge for international B2B buyers, particularly those from Africa, South America, the Middle East, and Europe, including key markets like Saudi Arabia and Italy. As industries increasingly rely on electric arc furnaces for steel production and other applications, understanding the specifications, types, and sourcing options for graphite electrodes becomes crucial. This guide aims to demystify the complexities of graphite electrode procurement by offering a comprehensive overview of various electrode types, their applications, and critical factors to consider when vetting suppliers.
With the demand for high-performance materials in steelmaking and refining processes escalating, this guide empowers buyers to make informed purchasing decisions. It outlines essential attributes of different grades of graphite electrodes, such as RP, HP, SHP, and UHP, along with their respective performance characteristics and suitability for specific furnace types. Additionally, we delve into cost considerations, market trends, and best practices for supplier evaluation, ensuring that buyers can effectively navigate the competitive landscape. By leveraging the insights provided herein, international B2B buyers can streamline their sourcing processes and enhance operational efficiency, ultimately leading to more sustainable and profitable business practices in their respective markets.
Understanding graphite electrode Types and Variations
Type Name | Key Distinguishing Features | Primary B2B Applications | Brief Pros & Cons for Buyers |
---|---|---|---|
RP Graphite Electrode | Standard grade with moderate electrical conductivity and thermal resistance. | Steelmaking in electric arc furnaces (EAF). | Pros: Cost-effective, widely available. Cons: Limited performance for high-demand applications. |
HP Graphite Electrode | Higher density and electrical conductivity compared to RP. | Used in EAF and ladle furnaces for refining steel. | Pros: Better performance under high temperatures. Cons: Higher cost than RP. |
SHP Graphite Electrode | Super High Power electrodes, designed for higher current applications. | Heavy-duty steel production and large-scale refining. | Pros: Enhanced durability and efficiency. Cons: More expensive, requiring careful selection. |
UHP Graphite Electrode | Ultra High Power electrodes with exceptional density and conductivity. | Specialized applications in EAF and LF (ladle furnaces). | Pros: Optimal performance for demanding environments. Cons: Premium pricing, necessitating high-volume usage to justify costs. |
Male/Female Graphite Electrode | Versatile electrodes designed for specific applications like EDM. | Electrical discharge machining (EDM) and heating elements. | Pros: Customizable for various applications. Cons: May require specialized knowledge for optimal use. |
What are RP Graphite Electrodes and When Should They Be Used?
RP (Regular Power) graphite electrodes are the entry-level choice for electric arc furnaces (EAF) and are suitable for standard steelmaking applications. They provide moderate electrical conductivity and thermal resistance, making them a cost-effective option for businesses looking to optimize their production without incurring high costs. Buyers should consider RP electrodes when their operations do not demand extreme performance levels but still require reliable functionality.
How Do HP Graphite Electrodes Enhance Performance?
HP (High Power) graphite electrodes offer improved density and conductivity over RP options, making them ideal for applications that require a bit more performance, such as refining steel in ladle furnaces. They are particularly useful in environments where higher temperatures and currents are prevalent. Buyers must weigh the benefits of enhanced performance against the increased cost when considering HP electrodes for their operations.
What Advantages Do SHP Graphite Electrodes Offer?
SHP (Super High Power) graphite electrodes are designed for high-demand applications, particularly in heavy-duty steel production. These electrodes can handle greater current loads, resulting in higher efficiency and durability. For B2B buyers in regions with advanced steelmaking processes, investing in SHP electrodes may be justified despite their higher price due to the potential for increased productivity and lower long-term operational costs.
Why Choose UHP Graphite Electrodes for Specialized Applications?
UHP (Ultra High Power) graphite electrodes are the premium option for businesses requiring the highest levels of performance in electric arc and ladle furnaces. With exceptional density and conductivity, they are specifically engineered to withstand extreme operational conditions. While they come at a premium price, businesses that rely on high-volume production will find that the benefits in efficiency and reduced downtime can offset the initial investment.
How Do Male/Female Graphite Electrodes Fit into Various Applications?
Male/Female graphite electrodes are specialized tools primarily used in electrical discharge machining (EDM) and other heating applications. Their unique design allows for customization based on specific operational needs, making them versatile for various industries. Buyers should consider these electrodes when looking for tailored solutions, though they may require specialized knowledge for effective implementation.
Key Industrial Applications of graphite electrode
Industry/Sector | Specific Application of Graphite Electrode | Value/Benefit for the Business | Key Sourcing Considerations for this Application |
---|---|---|---|
Steel Manufacturing | Electric Arc Furnaces (EAF) | Efficient melting of scrap metal for recycling | Quality of electrodes, size specifications, and thermal resistance |
Foundry and Casting | Ladle Furnaces | Refinement of molten steel | Purity levels, electrode diameter, and consistency in performance |
Aerospace and Defense | High-Temperature Applications | Manufacturing of components requiring high thermal stability | Sourcing certified suppliers, compliance with industry standards |
Electronics and Semiconductor | Anodes for Electrochemical Processes | Improved conductivity and durability in applications | Material grade, resistance to wear, and electrical conductivity |
Renewable Energy | Fuel Cell Components | Enhanced performance and efficiency in energy conversion | Specific material requirements, availability, and sourcing logistics |
How Are Graphite Electrodes Used in Steel Manufacturing?
In the steel manufacturing sector, graphite electrodes are predominantly utilized in Electric Arc Furnaces (EAF). These electrodes enable the efficient melting of scrap metal at temperatures exceeding 1600°C, facilitating the recycling process. For international buyers, particularly from regions like Africa and South America, sourcing high-quality electrodes that meet specific size and thermal resistance requirements is crucial. The efficiency of the EAF directly impacts operational costs and sustainability efforts, making the choice of electrode vital for business success.
What Role Do Graphite Electrodes Play in Foundry and Casting?
In foundry and casting applications, graphite electrodes are essential for ladle furnaces, where they are used to refine molten steel. The electrodes help maintain temperature and composition, ensuring quality in the final product. Buyers from the Middle East and Europe should consider the purity levels and diameter specifications of the electrodes, as these factors significantly affect the performance and reliability of the refining process. Ensuring consistency in electrode performance can reduce production downtime and improve product quality.
How Are Graphite Electrodes Beneficial in Aerospace and Defense?
In the aerospace and defense industries, graphite electrodes are employed in high-temperature applications, such as the manufacturing of engine components. Their ability to withstand extreme thermal conditions while maintaining structural integrity makes them indispensable. B2B buyers in this sector, particularly from Europe, must prioritize sourcing from certified suppliers to ensure compliance with stringent industry standards. The durability and performance of these electrodes directly influence the safety and efficacy of aerospace components.
How Do Graphite Electrodes Enhance Electronics and Semiconductor Applications?
Graphite electrodes serve as anodes in electrochemical processes within the electronics and semiconductor sectors. Their high electrical conductivity and resistance to wear enhance the performance and longevity of various electronic components. International buyers, especially from regions like Africa and South America, should focus on the material grade and sourcing logistics to guarantee timely delivery and consistent quality. The choice of electrode can significantly impact the efficiency of production processes in this rapidly evolving industry.
What Advantages Do Graphite Electrodes Offer in Renewable Energy?
In the renewable energy sector, graphite electrodes are critical components in fuel cells, where they improve performance and efficiency in energy conversion processes. Buyers must consider specific material requirements and the availability of electrodes to support their projects effectively. With the global shift towards sustainable energy solutions, sourcing high-quality graphite electrodes can provide a competitive edge in developing innovative energy technologies.
3 Common User Pain Points for ‘graphite electrode’ & Their Solutions
Scenario 1: Difficulty in Sourcing High-Quality Graphite Electrodes
The Problem: B2B buyers often encounter challenges in sourcing high-quality graphite electrodes that meet their specific requirements. This is particularly true for industries in Africa and South America, where suppliers may not consistently adhere to international quality standards. As a result, companies risk purchasing substandard products that can lead to inefficiencies in their electric arc furnaces, affecting production capacity and increasing operational costs.
The Solution: To overcome sourcing challenges, buyers should conduct thorough supplier evaluations. Look for manufacturers with ISO certifications and strong reputations in the industry, such as Tokai Carbon or Orient Carbon Graphite. Consider visiting production facilities or arranging for third-party inspections to verify quality before placing large orders. Additionally, request samples to assess the electrodes’ performance characteristics, such as electrical conductivity and thermal resistance, against your operational needs. Establishing long-term relationships with reliable suppliers can also provide more consistent access to high-quality electrodes, helping to stabilize production processes.
Scenario 2: Inadequate Technical Specifications Leading to Equipment Failures
The Problem: Many B2B buyers struggle with understanding the technical specifications of graphite electrodes, which can lead to improper usage or equipment failures. For instance, a company in the Middle East might select an electrode that cannot handle the required current density, resulting in overheating and premature failure in electric arc furnaces. This not only disrupts production but can also incur significant repair costs and downtime.
The Solution: Buyers should invest in training for their procurement teams and technical staff to better understand the specifications of graphite electrodes, such as resistance, thermal expansion, and mechanical strength. Consult with manufacturers to get detailed datasheets that outline the performance metrics of their products. Furthermore, leverage industry resources and attend workshops or webinars focusing on graphite electrode applications. By ensuring that the selected electrodes match the specific needs of your furnace type—whether AC or DC—companies can enhance operational efficiency and reduce the risk of equipment failures.
Scenario 3: Rising Costs and Supply Chain Disruptions
The Problem: International B2B buyers are increasingly facing rising costs and supply chain disruptions related to graphite electrodes. Factors like geopolitical tensions, fluctuating raw material prices, and logistics issues can cause significant delays and price increases, impacting the overall cost structure of production. Companies in Europe may find themselves paying significantly more for electrodes than they did previously, squeezing profit margins.
The Solution: To mitigate the impact of rising costs, buyers should consider diversifying their supplier base across different regions, such as sourcing from both local and international suppliers. This strategy not only helps in maintaining competitive pricing but also reduces dependency on a single source, minimizing the risk of supply chain disruptions. Additionally, buyers can explore bulk purchasing agreements or long-term contracts to lock in favorable pricing. Implementing just-in-time inventory management can also help in reducing holding costs and ensuring that you have the right amount of stock without overcommitting financially. Engaging in regular market analysis can assist in forecasting price trends, allowing companies to make more informed purchasing decisions.
Strategic Material Selection Guide for graphite electrode
When selecting materials for graphite electrodes, understanding the properties, advantages, and limitations of each type is crucial for international B2B buyers. This guide analyzes several common materials used in the production of graphite electrodes, focusing on their performance characteristics, application impacts, and specific considerations for buyers from diverse regions.
What Are the Key Properties of Different Graphite Electrode Materials?
1. Regular Power (RP) Graphite Electrodes
Key Properties: RP graphite electrodes are characterized by their moderate electrical conductivity and thermal resistance. They typically operate at temperatures up to 3000°C and have a bulk density of 1.58-1.70 g/cm³.
Pros & Cons: The primary advantage of RP electrodes is their cost-effectiveness, making them suitable for less demanding applications. However, they are less durable than higher-grade electrodes, which can lead to higher replacement costs in high-performance environments.
Impact on Application: RP electrodes are commonly used in steelmaking and foundries where the melting requirements are moderate. They may not be suitable for applications requiring high current densities or extreme thermal conditions.
Considerations for International Buyers: Buyers should ensure compliance with regional standards such as ASTM and DIN. In regions like Europe and the Middle East, where quality assurance is paramount, RP electrodes may be less favored compared to UHP grades.
2. High Power (HP) Graphite Electrodes
Key Properties: HP electrodes offer improved electrical conductivity and can withstand higher temperatures (up to 3500°C). Their density ranges from 1.65 to 1.76 g/cm³, making them suitable for more demanding applications.
Pros & Cons: HP electrodes provide a balance between performance and cost. They are more durable than RP electrodes but come at a higher price point. The manufacturing process is more complex, which can affect lead times.
Impact on Application: These electrodes are ideal for electric arc furnaces (EAF) and ladle refining furnaces, where higher efficiency and reduced electrode consumption are critical.
Considerations for International Buyers: Buyers from Africa and South America should consider local availability and import regulations, as HP electrodes may be subject to tariffs or trade restrictions.
3. Ultra High Power (UHP) Graphite Electrodes
Key Properties: UHP graphite electrodes are designed for extreme conditions, capable of operating at temperatures exceeding 4000°C. They possess a high bulk density (1.68-1.75 g/cm³) and low specific resistance (4.2-5.5 μΩm).
Pros & Cons: The main advantage of UHP electrodes is their exceptional performance in high-demand applications, leading to lower operational costs over time. However, they are the most expensive option and require sophisticated manufacturing techniques.
Impact on Application: UHP electrodes are essential in high-capacity EAFs and other applications where maximum efficiency and minimal downtime are critical.
Considerations for International Buyers: Buyers in regions with stringent environmental regulations, such as Europe, must ensure that UHP electrodes meet all compliance standards. Additionally, the higher initial investment may be justified by long-term savings in operational costs.
Summary Table of Material Selection for Graphite Electrodes
Material | Typical Use Case for graphite electrode | Key Advantage | Key Disadvantage/Limitation | Relative Cost (Low/Med/High) |
---|---|---|---|---|
Regular Power (RP) | Steelmaking, foundries | Cost-effective for moderate applications | Less durable, higher replacement costs | Low |
High Power (HP) | Electric arc furnaces, ladle refining | Good balance of performance and cost | More expensive, complex manufacturing | Medium |
Ultra High Power (UHP) | High-capacity electric arc furnaces | Exceptional performance in extreme conditions | Highest cost, requires advanced manufacturing | High |
By understanding the properties and implications of different graphite electrode materials, international B2B buyers can make informed decisions that align with their operational needs and regional compliance requirements.
In-depth Look: Manufacturing Processes and Quality Assurance for graphite electrode
What Are the Key Stages in the Manufacturing Process of Graphite Electrodes?
The manufacturing of graphite electrodes involves several crucial stages that ensure the production of high-quality products capable of withstanding extreme conditions in electric arc furnaces. Understanding these stages can help B2B buyers in Africa, South America, the Middle East, and Europe make informed decisions when selecting suppliers.
1. Material Preparation: What Raw Materials Are Used?
The primary raw materials for graphite electrodes include petroleum coke, pitch coke, and coal tar pitch. These materials are selected for their high carbon content and low ash content, which are critical for performance in electric arc furnaces.
- Screening and Crushing: The raw materials are screened and crushed to achieve the desired particle size.
- Mixing: The crushed materials are then mixed with a binder (coal tar pitch) to create a homogeneous paste.
2. Forming: How Are Graphite Electrodes Shaped?
The forming stage involves several methods to shape the electrodes:
- Extrusion: The paste is extruded through a die to form long rods, which can be cut to desired lengths.
- Molding: Alternatively, the paste can be pressed into molds to create specific shapes.
- Isostatic Pressing: This technique applies uniform pressure from all sides, resulting in denser and more uniform electrodes.
What Finishing Techniques Are Used in Graphite Electrode Production?
Finishing processes are essential for enhancing the properties of graphite electrodes.
- Baking: The formed electrodes are baked at high temperatures (around 1000-1200°C) to carbonize the binder and strengthen the structure.
- Graphitization: Further heating to temperatures exceeding 2500°C transforms the carbon structure into a crystalline form, significantly improving electrical conductivity.
- Machining: Final shaping and surface finishing are done using CNC machines to ensure precise dimensions and surface quality.
What Are the Key Quality Assurance Standards for Graphite Electrodes?
Quality assurance is crucial in ensuring that graphite electrodes meet international standards. B2B buyers should be aware of the following standards:
- ISO 9001: This standard focuses on quality management systems and is widely recognized across industries. Suppliers adhering to ISO 9001 demonstrate a commitment to consistent quality.
- CE Marking: For products sold in the European Economic Area, CE marking indicates compliance with health, safety, and environmental protection standards.
- API Standards: In industries like oil and gas, adherence to API standards may also be relevant.
How Are Quality Control Checkpoints Implemented During Production?
Quality control (QC) is implemented at various checkpoints during the manufacturing process to ensure product integrity.
1. Incoming Quality Control (IQC)
During IQC, raw materials are inspected for quality before production begins. This includes checking for:
- Chemical Composition: Ensuring materials meet specified carbon and ash content.
- Physical Properties: Assessing particle size and moisture content.
2. In-Process Quality Control (IPQC)
IPQC monitors the production process to catch any deviations in real-time. Common practices include:
- Temperature Monitoring: Ensuring baking and graphitization temperatures are within specified ranges.
- Dimensional Checks: Regularly measuring electrode dimensions during machining.
3. Final Quality Control (FQC)
FQC involves comprehensive testing of finished products to validate performance. Key tests include:
- Electrical Conductivity Testing: Measuring the electrical resistance to ensure it meets specifications.
- Mechanical Testing: Evaluating bending strength, thermal expansion, and density.
How Can B2B Buyers Verify Supplier Quality Control Practices?
International B2B buyers should take proactive steps to verify the quality control practices of potential suppliers.
1. Conduct Supplier Audits
Performing audits allows buyers to assess the supplier’s quality management systems firsthand. Key areas to focus on include:
- Documentation: Review quality management documentation and compliance records.
- Production Processes: Observe manufacturing processes and QC checkpoints.
2. Request Quality Assurance Reports
Buyers should request detailed quality assurance reports from suppliers. These reports should include:
- Test Results: Documentation of test results for batches of electrodes.
- Certification Copies: Copies of certifications for compliance with international standards.
3. Engage Third-Party Inspection Services
Utilizing third-party inspection services can provide an unbiased evaluation of a supplier’s quality practices. These services can conduct:
- Pre-shipment Inspections: Ensuring that products meet specifications before shipment.
- Random Sampling: Conducting random sampling of products for testing against quality standards.
What Nuances Should International Buyers Consider Regarding Quality Control?
International buyers, especially from regions like Africa, South America, the Middle East, and Europe, should consider specific nuances in quality control:
- Regulatory Compliance: Different regions may have varying regulatory requirements. Understanding these can prevent compliance issues.
- Cultural Differences: Different business cultures may affect communication about quality expectations. Clear communication and documented agreements are essential.
- Logistics and Supply Chain Factors: Consider how logistical challenges may impact delivery times and quality assurance.
Conclusion: Ensuring Quality in Graphite Electrode Procurement
For B2B buyers in the graphite electrode market, understanding the manufacturing processes and quality assurance practices is vital. By focusing on supplier audits, quality certifications, and compliance with international standards, buyers can ensure they are partnering with reliable suppliers that deliver high-quality products suitable for their applications in electric arc furnaces and beyond.
Practical Sourcing Guide: A Step-by-Step Checklist for ‘graphite electrode’
To successfully procure graphite electrodes for your business, it’s crucial to follow a structured approach. This guide provides a step-by-step checklist to help international B2B buyers, particularly from Africa, South America, the Middle East, and Europe, navigate the sourcing process effectively.
Step 1: Define Your Technical Specifications
Establishing clear technical specifications is essential for ensuring that the graphite electrodes meet your operational needs. Consider the type of furnace you are using—AC, DC, or LF—and the required electrode size and grade.
- Electrode Types: Choose between RP, HP, SHP, and UHP electrodes based on your melting and refining processes.
- Performance Metrics: Evaluate parameters such as thermal conductivity, density, and resistance to ensure optimal performance.
Step 2: Identify Potential Suppliers
Begin by researching and compiling a list of suppliers who specialize in graphite electrodes. Look for companies with a strong reputation and experience in your specific industry.
- Industry Networks: Utilize trade shows, industry associations, and online platforms to find reputable suppliers.
- Regional Focus: Prioritize suppliers who understand the market dynamics and regulations in your region, whether it be in Africa, Europe, or the Middle East.
Step 3: Evaluate Supplier Certifications
Before proceeding, it’s critical to verify the certifications and quality standards of potential suppliers. This step ensures that you are sourcing from reliable partners.
- Quality Certifications: Look for ISO certifications or other relevant quality management systems that indicate adherence to industry standards.
- Compliance with Regulations: Ensure that suppliers meet local regulations regarding environmental and safety standards.
Step 4: Request Samples and Test Quality
Once you have shortlisted suppliers, request samples of the graphite electrodes. Testing these samples will help you assess their quality and suitability for your operations.
- Performance Testing: Conduct tests to check for thermal conductivity, electrical resistance, and durability under high temperatures.
- Feedback Loop: Engage your technical team to evaluate the samples and provide feedback before making a bulk purchase.
Step 5: Review Pricing and Payment Terms
Pricing is a vital aspect of sourcing graphite electrodes. Compare quotes from different suppliers while considering the total cost of ownership, which includes shipping and handling.
- Transparent Pricing: Ensure that suppliers provide a detailed breakdown of costs, including any hidden fees.
- Payment Flexibility: Discuss payment terms and conditions, including deposit requirements and credit options, to find a mutually beneficial arrangement.
Step 6: Negotiate Contracts and Terms
Once you’ve selected a supplier, proceed to negotiate the terms of the contract. This step is crucial for establishing a clear understanding of expectations and responsibilities.
- Delivery and Lead Times: Specify delivery schedules and lead times to avoid operational disruptions.
- Warranty and Support: Include warranty clauses and after-sales support to ensure you receive assistance in case of product issues.
Step 7: Establish a Relationship for Future Orders
Building a strong relationship with your supplier can lead to better service, pricing, and collaboration in the long run. Consider regular communication and feedback as part of this relationship.
- Long-term Partnerships: Explore opportunities for bulk purchasing or exclusive agreements that could benefit both parties.
- Continuous Improvement: Work with your supplier to identify areas for product improvement or innovation that can enhance your operations.
By following this checklist, B2B buyers can streamline the procurement process for graphite electrodes, ensuring they make informed decisions that align with their operational needs and business goals.
Comprehensive Cost and Pricing Analysis for graphite electrode Sourcing
What Are the Key Cost Components in Graphite Electrode Sourcing?
When sourcing graphite electrodes, understanding the cost structure is essential for international B2B buyers. The primary cost components include:
-
Materials: Graphite itself is the primary material, and its price can vary significantly based on purity, origin, and market demand. High-quality graphite, especially for ultra-high power (UHP) electrodes, typically incurs higher costs.
-
Labor: Labor costs can differ based on the manufacturing location. Regions with lower labor costs may offer a competitive advantage, but this must be balanced against quality and expertise.
-
Manufacturing Overhead: This includes costs associated with production facilities, equipment depreciation, and energy consumption. Efficient production processes can help minimize these costs.
-
Tooling: Custom tooling for specific electrode shapes or sizes can add to the upfront costs. Buyers should consider whether standard sizes meet their needs to avoid unnecessary expenditures.
-
Quality Control (QC): Rigorous QC processes ensure product reliability and performance. While this adds to costs, it is essential for preventing defects that could lead to operational issues.
-
Logistics: Shipping and handling costs can be substantial, particularly for bulky items like graphite electrodes. Factors like distance, mode of transport, and customs duties should be factored into the total cost.
-
Margin: Suppliers will include a profit margin in their pricing, which can vary based on their operational costs and market competition.
How Do Price Influencers Affect Graphite Electrode Costs?
Several factors can influence the pricing of graphite electrodes:
-
Volume/MOQ (Minimum Order Quantity): Larger orders often qualify for volume discounts, reducing the cost per unit. Buyers should assess their needs to optimize order sizes.
-
Specifications and Customization: Customized electrodes designed for specific applications may carry a premium. Buyers should evaluate if customization is necessary or if standard options suffice.
-
Materials and Quality Certifications: The quality of graphite and the presence of certifications (ISO, ASTM, etc.) can significantly impact pricing. Higher quality materials may lead to enhanced performance but will increase costs.
-
Supplier Factors: The supplier’s reputation, production capacity, and location can affect pricing. Established suppliers may charge more due to their reliability and quality assurance processes.
-
Incoterms: The chosen Incoterms (e.g., FOB, CIF) will determine who bears the costs and risks at various stages of the shipping process. Buyers should clarify these terms to avoid unexpected expenses.
What Buyer Tips Can Help Optimize Graphite Electrode Costs?
B2B buyers can implement several strategies to optimize their graphite electrode sourcing costs:
-
Effective Negotiation: Engage suppliers in discussions about pricing, especially when placing large orders. Building a good relationship can lead to better terms and conditions.
-
Focus on Cost-Efficiency: Evaluate the Total Cost of Ownership (TCO) rather than just the purchase price. Consider factors such as maintenance, durability, and energy efficiency of the electrodes.
-
Understand Pricing Nuances: Different regions may experience fluctuations in graphite prices due to local demand and supply conditions. Buyers from Africa, South America, the Middle East, and Europe should stay informed about market trends to make timely purchasing decisions.
-
Leverage Local Suppliers: Whenever possible, consider sourcing from local suppliers to reduce shipping costs and lead times. Local suppliers may also have a better understanding of regional requirements and standards.
Disclaimer on Indicative Prices
Prices for graphite electrodes can fluctuate due to market conditions, currency exchange rates, and changes in raw material costs. It is advisable for buyers to obtain current quotes and conduct thorough market research before finalizing their purchases.
Alternatives Analysis: Comparing graphite electrode With Other Solutions
When evaluating the use of graphite electrodes in industrial applications, it’s essential for B2B buyers to consider alternative solutions that can achieve similar outcomes. Understanding the strengths and weaknesses of these alternatives can help in making informed decisions that align with specific operational needs and budget constraints.
Comparison Aspect | Graphite Electrode | Carbon Electrode | Copper Electrode |
---|---|---|---|
Performance | High thermal conductivity; withstands extreme heat (up to 1600℃) | Good conductivity but lower heat resistance | Excellent conductivity; low thermal resistance |
Cost | Moderate to high cost, influenced by raw material prices | Generally lower cost, but performance can vary | Higher initial investment but longer lifespan |
Ease of Implementation | Requires specialized equipment for installation | Easier to handle and install | More straightforward installation with common tools |
Maintenance | Requires regular monitoring and replacement due to wear | Less frequent replacement | Minimal maintenance but can require periodic checks |
Best Use Case | Ideal for electric arc furnaces and steel refining | Suitable for lower temperature applications | Preferred in applications requiring precision and less heat |
What Are the Advantages and Disadvantages of Using Carbon Electrodes?
Carbon electrodes serve as a cost-effective alternative to graphite electrodes in specific applications. They offer good electrical conductivity and are particularly effective in processes that do not require extreme temperatures. However, carbon electrodes generally have lower thermal resistance, which may limit their effectiveness in high-heat applications such as electric arc furnaces. While they are easier to handle and install, their performance may not meet the demands of industries focused on high efficiency and durability.
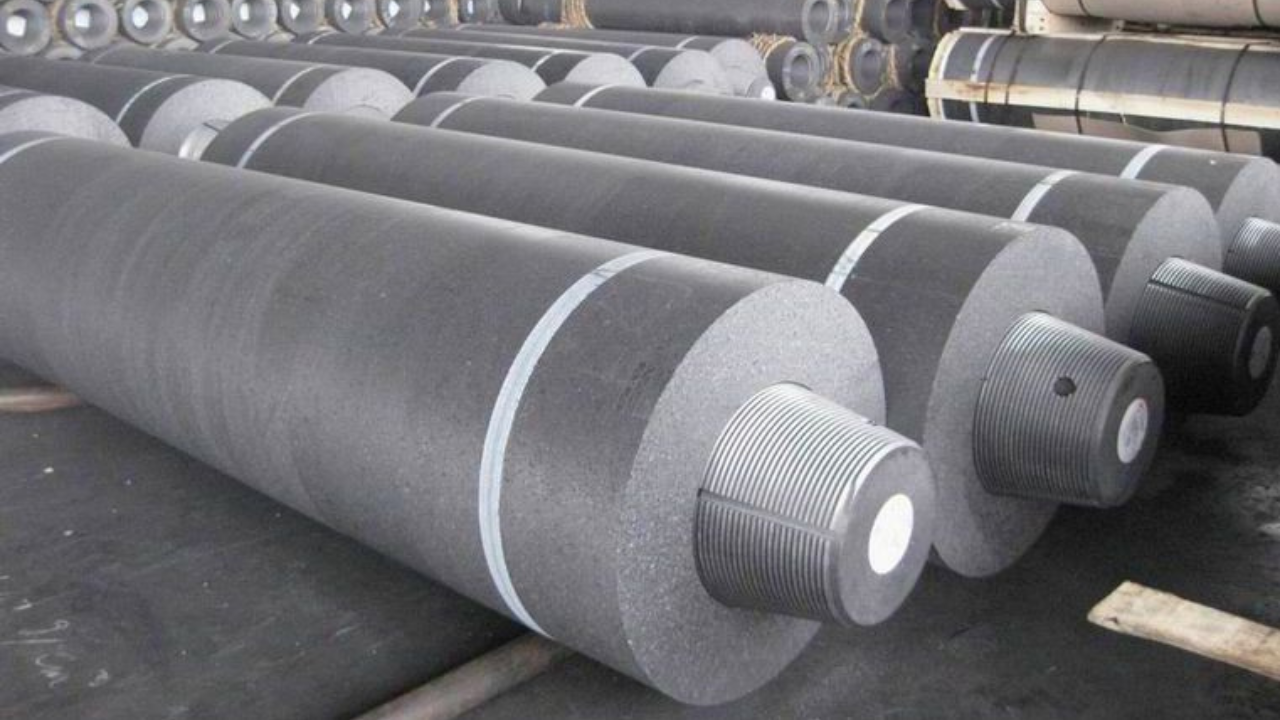
A stock image related to graphite electrode.
How Do Copper Electrodes Compare in Performance and Cost?
Copper electrodes are known for their exceptional electrical conductivity, making them suitable for applications that require precise energy transfer. Their installation is straightforward, often requiring common tools, which can reduce labor costs. However, copper electrodes have a higher initial investment, and while they do not require frequent maintenance, they may not withstand the extreme conditions found in electric arc furnaces as effectively as graphite electrodes. This trade-off makes copper electrodes a viable choice for industries where precision and efficiency are paramount but may not be suitable for high-temperature environments.
Conclusion: How to Choose the Right Electrode Solution for Your Needs?
When selecting the appropriate electrode solution, B2B buyers should consider the specific requirements of their operations, including temperature thresholds, cost constraints, and ease of use. Graphite electrodes remain the industry standard for high-temperature applications due to their robust performance and durability. However, alternatives like carbon and copper electrodes can provide cost-effective solutions for less demanding environments. By evaluating the performance characteristics, costs, and application suitability of each option, buyers can make strategic decisions that enhance operational efficiency while managing budgets effectively.
Essential Technical Properties and Trade Terminology for graphite electrode
What Are the Key Technical Properties of Graphite Electrodes?
Graphite electrodes are vital components in electric arc furnaces (EAF) and other metallurgical processes. Understanding their technical properties is essential for international B2B buyers, particularly those in Africa, South America, the Middle East, and Europe, as these specifications directly influence performance, efficiency, and cost-effectiveness.
1. Material Grade
Graphite electrodes are classified into different grades based on their electrical and thermal conductivity, mechanical strength, and thermal resistance. The most common grades include RP (Regular Power), HP (High Power), SHP (Super High Power), and UHP (Ultra High Power). Each grade is optimized for specific applications, with UHP electrodes designed for higher efficiency in EAFs. Selecting the correct material grade is crucial for ensuring optimal operational performance and minimizing downtime.
2. Diameter and Length Specifications
The diameter and length of graphite electrodes vary widely, typically ranging from 14 inches (350 mm) to 32 inches (800 mm) in diameter and lengths from 1.5 meters to 3 meters. The appropriate size depends on the furnace type (AC or DC) and the specific melting requirements. Accurate diameter and length specifications ensure compatibility with equipment and can significantly affect the melting efficiency and energy consumption.
3. Bulk Density
Bulk density, measured in grams per cubic centimeter (g/cm³), is an important property that indicates the material’s compactness and strength. Typical values range from 1.58 to 1.76 g/cm³ for various grades. Higher bulk density often correlates with better performance under extreme conditions, making it a key factor for buyers concerned about electrode longevity and operational stability.
4. Electrical Resistance
Electrical resistance, expressed in micro-ohm meters (μΩm), is critical for the effective conduction of electricity during the melting process. Lower resistance values (e.g., 4.2 to 8.5 μΩm) imply better conductivity and efficiency in power consumption. Understanding electrical resistance helps buyers select electrodes that will minimize operational costs and improve melting efficiency.
5. Bending Strength and Young’s Modulus
Bending strength, measured in megapascals (MPa), indicates the ability of the electrode to withstand mechanical stress during operation. Typical values range from 10 to 18 MPa, depending on the grade. Young’s modulus, also expressed in gigapascals (GPa), reflects the material’s stiffness. These mechanical properties are crucial for ensuring that the electrodes can endure the harsh conditions within a furnace without failure, thus impacting production continuity.
What Are Common Trade Terminologies in Graphite Electrode Transactions?
Understanding trade terminology is vital for smooth B2B transactions in the graphite electrode industry. Here are some essential terms that buyers should be familiar with:
1. OEM (Original Equipment Manufacturer)
OEM refers to companies that manufacture components used in the production of other products. In the context of graphite electrodes, an OEM may supply electrodes specifically designed for a particular furnace model. Knowing the OEM can help buyers ensure compatibility and performance.
2. MOQ (Minimum Order Quantity)
MOQ is the minimum number of units a supplier is willing to sell in a single order. This term is crucial for buyers, as understanding the MOQ helps manage inventory levels and budget constraints. It can vary significantly depending on the supplier and the type of graphite electrode being ordered.
3. RFQ (Request for Quotation)
An RFQ is a document sent by buyers to suppliers requesting pricing and other terms for specific products. It is a common practice in B2B transactions, allowing buyers to compare offers and select the best value for their needs.
4. Incoterms (International Commercial Terms)
Incoterms are a set of predefined commercial terms published by the International Chamber of Commerce (ICC). They define the responsibilities of buyers and sellers regarding shipping, insurance, and tariffs. Familiarity with Incoterms helps buyers understand their obligations and costs associated with international shipping.
5. Lead Time
Lead time refers to the period between placing an order and receiving the goods. In the graphite electrode industry, lead times can vary based on production schedules and shipping logistics. Understanding lead times is essential for effective project planning and inventory management.
By familiarizing themselves with these technical properties and trade terminologies, B2B buyers can make informed decisions, ensuring they select the right graphite electrodes for their operational needs.
Navigating Market Dynamics and Sourcing Trends in the graphite electrode Sector
What Are the Current Market Dynamics and Key Trends in the Graphite Electrode Sector?
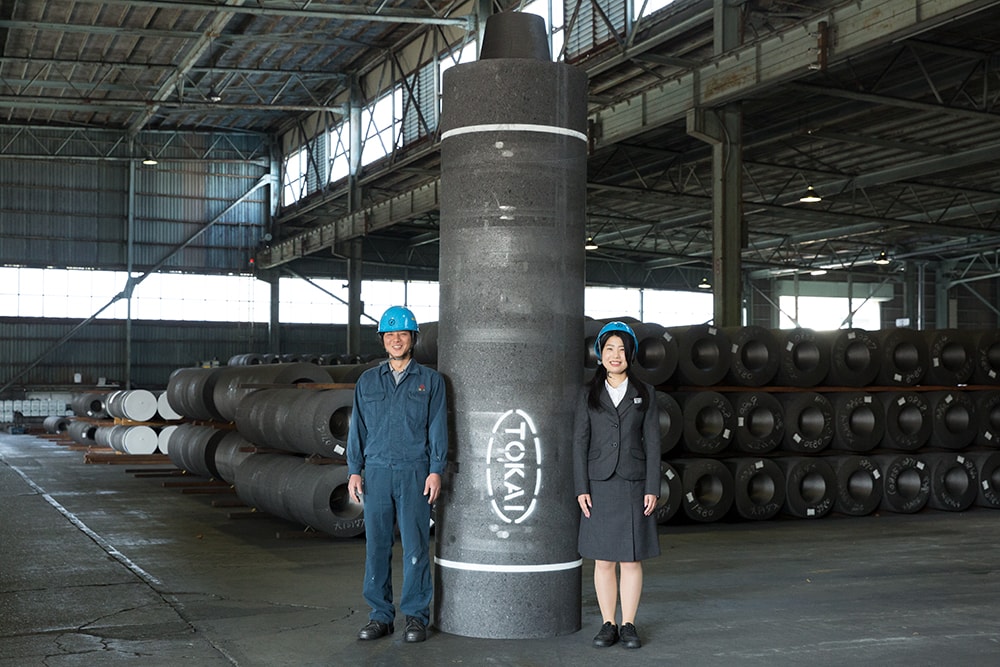
A stock image related to graphite electrode.
The graphite electrode market is experiencing significant shifts driven by several global factors. One of the primary drivers is the increasing demand for electric arc furnace (EAF) steel production, which is prevalent in regions such as Africa and South America, where recycling of scrap metal is becoming more critical. The rise in electric vehicle (EV) manufacturing also contributes to the demand for high-quality graphite electrodes used in battery production.
Emerging technologies, such as advanced manufacturing techniques and enhanced material processing, are transforming sourcing trends. For instance, the development of ultra-high power (UHP) graphite electrodes capable of withstanding higher temperatures and electrical currents is reshaping procurement strategies for international buyers. Additionally, the integration of digital tools for supply chain management is becoming increasingly important, enabling buyers to track materials more effectively and ensure timely delivery.
Market dynamics are also influenced by geopolitical factors, particularly in the Middle East and Europe, where trade agreements and tariffs can impact pricing and availability. Buyers from regions like Saudi Arabia and Italy must navigate these complexities while ensuring they source from reliable suppliers who can meet their specific production requirements.
How Important Is Sustainability and Ethical Sourcing in the Graphite Electrode Industry?
Sustainability is a growing concern for B2B buyers in the graphite electrode sector. The environmental impact of graphite mining and production processes can be significant, necessitating an emphasis on ethical sourcing practices. Buyers are increasingly prioritizing suppliers who demonstrate a commitment to reducing their carbon footprint and minimizing waste.
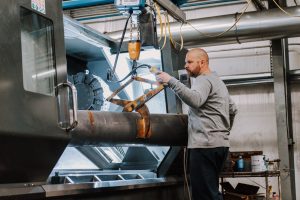
A stock image related to graphite electrode.
The importance of ethical supply chains cannot be overstated. Many companies are seeking suppliers with certifications that validate their sustainability efforts, such as ISO 14001 for environmental management systems or specific certifications for ‘green’ materials. These certifications not only enhance a company’s reputation but also align with the growing consumer demand for environmentally responsible products.
In addition to certifications, the use of recycled materials in the production of graphite electrodes is becoming more common. This practice not only reduces the need for new raw materials but also supports circular economy principles, appealing to B2B buyers focused on sustainability.
What Is the Historical Context of Graphite Electrodes in B2B Applications?
The evolution of graphite electrodes can be traced back to the early 20th century when they were first utilized in electric arc furnaces. Initially, the electrodes were smaller and less efficient, but advancements in material science and manufacturing techniques have led to significant improvements over the decades.
By the 1980s, the demand for higher efficiency and performance resulted in the development of different grades of graphite electrodes, including RP (Regular Power), HP (High Power), and UHP (Ultra High Power). This evolution has enabled industries, particularly steel manufacturing, to leverage the benefits of recycling scrap metal while achieving higher operational efficiencies. Today, the continued innovation in electrode design and materials reflects the ongoing needs of B2B buyers for reliable and high-performing products in a competitive marketplace.
Frequently Asked Questions (FAQs) for B2B Buyers of graphite electrode
-
How do I choose the right graphite electrode for my electric arc furnace?
Choosing the right graphite electrode depends on several factors, including the type of furnace (AC or DC), the steelmaking process, and specific operational requirements. For AC furnaces, electrodes typically range from 16 to 28 inches in diameter, while DC furnaces require larger electrodes, up to 32 inches. Consider the maximum current density your application requires, as well as the electrode’s thermal and electrical properties. Consulting with suppliers who understand your specific needs can also help ensure you make the right choice. -
What are the different types of graphite electrodes available?
Graphite electrodes are categorized into four main types: Regular Power (RP), High Power (HP), Super High Power (SHP), and Ultra High Power (UHP). Each type varies in terms of electrical conductivity and thermal resistance, making them suitable for different applications. RP electrodes are commonly used for lower power applications, while UHP electrodes are ideal for high-demand environments like steel refining. Assess your furnace’s requirements to determine which type will optimize performance and efficiency. -
What customization options are available for graphite electrodes?
Many suppliers offer customization options for graphite electrodes, including size, shape, and specific material properties tailored to your application. You may request electrodes with specific diameters or lengths, or those that meet particular thermal and electrical specifications. Discussing your exact requirements with potential suppliers will help you understand the available customization options and the impact on performance, ultimately ensuring that the electrodes fit your operational needs. -
What are the typical minimum order quantities (MOQ) for graphite electrodes?
Minimum order quantities for graphite electrodes can vary significantly by supplier and region. Generally, MOQs range from a few tons to several dozen tons, depending on the electrode type and customization required. If you are a smaller operation or just starting, it’s advisable to communicate your needs directly with suppliers, as some may be flexible with their MOQs, especially for repeat customers or bulk orders. -
What payment terms should I expect when sourcing graphite electrodes internationally?
Payment terms for international orders of graphite electrodes typically include options such as advance payment, letters of credit, or open account terms, depending on the supplier’s policies and your relationship with them. It’s crucial to clarify these terms early in negotiations to avoid any misunderstandings. Additionally, consider the currency fluctuations and exchange rates that could impact your costs when dealing with international suppliers. -
How can I ensure the quality of graphite electrodes before purchase?
To ensure the quality of graphite electrodes, request certifications and test reports from suppliers that comply with international quality standards. Conducting audits or inspections at the manufacturing site can also be beneficial. Additionally, consider asking for samples before placing a large order to assess the product’s performance in your specific applications. Building relationships with reputable suppliers who prioritize quality assurance can significantly reduce risks. -
What logistics considerations should I keep in mind when importing graphite electrodes?
When importing graphite electrodes, consider logistics factors such as shipping methods, lead times, and customs regulations in your country. Work with suppliers who have experience in international shipping to help navigate any potential challenges. Additionally, ensure that you have a clear understanding of delivery timelines and costs, including any import duties or taxes that may apply. Effective communication with your supplier and logistics partner can help streamline the process. -
What are the common applications of graphite electrodes in various industries?
Graphite electrodes are primarily used in electric arc furnaces for steel production, but they also have applications in other industries such as aluminum smelting, ferroalloy production, and the manufacturing of various alloys. Their high thermal conductivity and electrical resistance make them suitable for refining metals in ladle furnaces and for use in applications requiring high-temperature resistance. Understanding the specific needs of your industry will help you leverage the benefits of graphite electrodes effectively.
Important Disclaimer & Terms of Use
⚠️ Important Disclaimer
The information provided in this guide, including content regarding manufacturers, technical specifications, and market analysis, is for informational and educational purposes only. It does not constitute professional procurement advice, financial advice, or legal advice.
While we have made every effort to ensure the accuracy and timeliness of the information, we are not responsible for any errors, omissions, or outdated information. Market conditions, company details, and technical standards are subject to change.
B2B buyers must conduct their own independent and thorough due diligence before making any purchasing decisions. This includes contacting suppliers directly, verifying certifications, requesting samples, and seeking professional consultation. The risk of relying on any information in this guide is borne solely by the reader.
Strategic Sourcing Conclusion and Outlook for graphite electrode
What Are the Key Takeaways for Strategic Sourcing of Graphite Electrodes?
In conclusion, the strategic sourcing of graphite electrodes is pivotal for international B2B buyers across various industries, especially in regions like Africa, South America, the Middle East, and Europe. Understanding the different types of electrodes—RP, HP, SHP, and UHP—and their specific applications in electric arc furnaces and ladle refining processes is essential. This knowledge enables buyers to select the most suitable products that align with their operational needs, ultimately enhancing efficiency and reducing costs.
How Can International Buyers Optimize Their Sourcing Strategies?
Moreover, the importance of establishing reliable supplier relationships cannot be overstated. Engaging with manufacturers that prioritize innovation and quality, such as those producing larger and more efficient electrodes, can significantly impact production capabilities. By leveraging global networks and fostering partnerships, businesses can navigate market fluctuations and secure competitive pricing, especially in regions with emerging industrial sectors.
What Does the Future Hold for Graphite Electrode Sourcing?
Looking ahead, the demand for high-quality graphite electrodes is expected to grow, driven by advancements in steel production technologies and an increasing focus on sustainability. International buyers should proactively explore new sourcing strategies, consider diversification of supply chains, and stay informed about industry trends. Embracing these approaches will not only enhance operational resilience but also position businesses favorably in a rapidly evolving market landscape.