Optimize Costs: The Complete Guide to Motor Electric DC (2025)
Introduction: Navigating the Global Market for motor electric dc
In today’s fast-paced industrial landscape, sourcing reliable motor electric DC solutions can pose significant challenges for international B2B buyers, particularly in regions such as Africa, South America, the Middle East, and Europe. As businesses strive for efficiency and performance, understanding the nuances of DC motors—including their types, applications, and cost structures—becomes crucial. This comprehensive guide serves as an essential resource, outlining the various types of DC motors available, their specific applications across industries, and strategies for effective supplier vetting.
The global market for DC motors is diverse, with options ranging from permanent magnet DC (PMDC) motors to brushless DC (BLDC) variants, each offering unique benefits tailored to specific operational needs. In this guide, we delve into the key features and functionalities of these motors, as well as their suitability for applications in sectors such as agriculture, automation, and renewable energy systems. Moreover, we provide insights into the cost implications and maintenance considerations that can influence purchasing decisions.
By equipping international buyers with actionable knowledge and practical strategies, this guide empowers them to make informed decisions, ensuring they select the right motor solutions that align with their operational goals and market demands. Whether you are a buyer in the UAE looking for high-performance motors for industrial applications or a South American firm exploring energy-efficient solutions, this guide will be your roadmap in navigating the global DC motor market effectively.
Understanding motor electric dc Types and Variations
Type Name | Key Distinguishing Features | Primary B2B Applications | Brief Pros & Cons for Buyers |
---|---|---|---|
Permanent Magnet DC Motor | High efficiency, compact size, and simple control | Robotics, medical devices, agricultural equipment | Pros: Cost-effective, high starting torque. Cons: Limited speed range. |
Brushless DC Motor (BLDC) | No brushes, high efficiency, and longer lifespan | Automotive, power tools, HVAC systems | Pros: Less maintenance, high reliability. Cons: Higher initial cost. |
Series Wound DC Motor | High starting torque and speed control | Cranes, elevators, and traction applications | Pros: Excellent for high torque applications. Cons: Less efficient at low speeds. |
Shunt Wound DC Motor | Stable speed under varying loads | Industrial machinery, conveyor systems | Pros: Good speed regulation. Cons: More complex control required. |
Gear Motor | Integrated gear reduction for increased torque | Packaging, automation, and conveyor systems | Pros: Compact design, high torque output. Cons: Potentially higher wear on gears. |
What are the Characteristics of Permanent Magnet DC Motors?
Permanent Magnet DC (PMDC) motors are known for their high efficiency and compact design, making them suitable for applications requiring reliable performance in limited spaces. They operate on low voltage, which is ideal for battery-powered and solar applications. The key B2B purchasing considerations include the motor’s torque and speed characteristics, as well as its compatibility with existing control systems. Buyers should evaluate the motor’s performance in terms of starting torque and efficiency to ensure it meets their operational needs.
How Do Brushless DC Motors Compare to Other Types?
Brushless DC motors (BLDC) eliminate the need for brushes, resulting in reduced maintenance and longer operational life. They are characterized by high efficiency and precise speed control, making them ideal for applications in automotive and power tool industries. When considering a BLDC for purchase, B2B buyers should assess the motor’s efficiency ratings, operational noise levels, and initial cost, as these factors can significantly impact long-term operational costs and performance.
What are the Advantages of Series Wound DC Motors?
Series wound DC motors are designed for applications requiring high starting torque and speed control, making them suitable for cranes and elevators. They are particularly effective in scenarios where heavy loads must be moved quickly. However, buyers should be aware that these motors are less efficient at lower speeds and may require more robust control systems. Evaluating the torque requirements of specific applications is crucial for buyers when considering this type of motor.
Why Choose Shunt Wound DC Motors for Industrial Applications?
Shunt wound DC motors offer stable speed under varying load conditions, making them a popular choice for industrial machinery and conveyor systems. They provide excellent speed regulation, which is essential for processes requiring consistent operational parameters. B2B buyers should consider the complexity of control systems required for shunt wound motors, as well as their operational environment, to ensure they select the right motor for their specific needs.
What are the Benefits of Using Gear Motors in Automation?
Gear motors combine a motor with a gear reduction system to increase torque output, making them ideal for packaging, automation, and conveyor systems. Their compact design allows for space-saving installations, while their high torque output is essential for driving heavy loads. When purchasing gear motors, B2B buyers should consider the potential wear on gears and the overall efficiency of the system, as these factors can influence maintenance costs and operational longevity.
Key Industrial Applications of motor electric dc
Industry/Sector | Specific Application of motor electric dc | Value/Benefit for the Business | Key Sourcing Considerations for this Application |
---|---|---|---|
Agriculture | Automated irrigation systems | Improved efficiency and reduced labor costs | Voltage specifications, environmental conditions |
Warehouse Automation | Automated Guided Vehicles (AGVs) | Enhanced operational efficiency and safety | Load capacity, speed control, and maintenance needs |
Medical Devices | Portable medical equipment (e.g., infusion pumps) | Reliability and precision in patient care | Compliance with medical standards, power supply |
Automotive | Electric vehicle (EV) components | High torque and performance in compact designs | Durability, weight considerations, and cost |
Industrial Equipment | Conveyor systems and assembly lines | Consistent torque and adjustable speed capabilities | Size constraints, control options, and maintenance |
How Are DC Motors Used in Agriculture for Automated Irrigation Systems?
In the agricultural sector, motor electric DC is vital for automated irrigation systems. These motors enable precise control over water distribution, ensuring crops receive the right amount of water at the right time. This application significantly reduces labor costs and increases efficiency, particularly in regions with water scarcity. International buyers should consider voltage specifications and the ability to operate in various environmental conditions when sourcing these motors.
What Role Do DC Motors Play in Warehouse Automation with AGVs?
Automated Guided Vehicles (AGVs) are increasingly utilized in warehouse automation, relying on motor electric DC for their drive systems. These motors provide the necessary torque for navigating heavy loads efficiently while ensuring smooth operation at low speeds. The use of AGVs can enhance operational efficiency and safety, especially in high-demand environments. Buyers should prioritize specifications related to load capacity, speed control, and maintenance needs to ensure optimal performance.
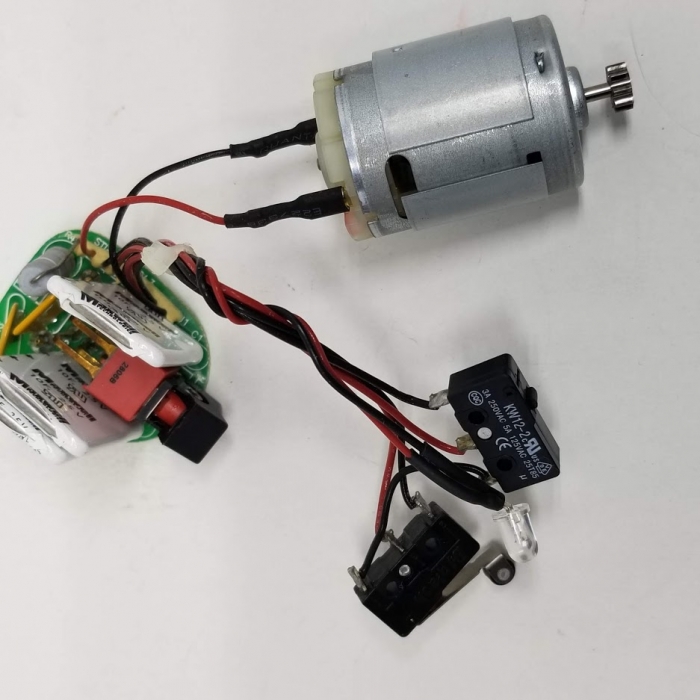
A stock image related to motor electric dc.
How Are DC Motors Essential in Portable Medical Devices?
In the medical field, motor electric DC is crucial for the functionality of portable medical devices, such as infusion pumps. These motors offer reliable and precise control, essential for patient care in various settings, including hospitals and home care. The compact design of DC motors allows for easy integration into medical equipment. Buyers in this sector must ensure compliance with strict medical standards and consider the power supply requirements when sourcing these motors.
How Are DC Motors Used in Electric Vehicle Components?
The automotive industry increasingly relies on motor electric DC for electric vehicle (EV) components. These motors provide high torque and efficient performance in a compact size, making them ideal for powering various vehicle functions. The adoption of DC motors contributes to the overall performance and efficiency of EVs, appealing to a growing market focused on sustainable transportation solutions. Buyers should consider durability, weight constraints, and overall cost when sourcing these components.
Why Are DC Motors Important in Conveyor Systems and Assembly Lines?
In industrial settings, motor electric DC is widely used in conveyor systems and assembly lines, where consistent torque and adjustable speed are essential. These motors facilitate smooth operation, allowing for precise control over production processes. This capability is particularly valuable in industries with high throughput demands. Buyers should pay close attention to size constraints, control options, and maintenance requirements to ensure the selected motors meet their operational needs effectively.
3 Common User Pain Points for ‘motor electric dc’ & Their Solutions
Scenario 1: High Maintenance Costs for DC Motors
The Problem:
B2B buyers frequently face the challenge of high maintenance costs associated with DC motors, particularly due to the need for regular brush replacements and repairs. This is especially true in industries such as manufacturing and logistics, where downtime can lead to significant losses. For companies in regions like Africa and South America, where access to spare parts and skilled technicians may be limited, this issue can be exacerbated. The financial burden of constant maintenance not only impacts operational efficiency but also affects the overall profitability of projects.
The Solution:
To mitigate high maintenance costs, buyers should consider investing in Brushless DC (BLDC) motors, which eliminate the need for brushes, thereby reducing wear and maintenance needs. When sourcing motors, it’s crucial to evaluate the total cost of ownership rather than just the initial purchase price. Buyers should seek suppliers that provide comprehensive warranty and service agreements to ensure long-term support. Additionally, investing in training for local technicians on the upkeep of these motors can further reduce dependency on external maintenance services. Properly specifying the required torque, speed, and environmental conditions for the motor will also ensure that the selected product operates efficiently, minimizing the risk of premature failure.
Scenario 2: Power Supply Compatibility Issues
The Problem:
Another common pain point for B2B buyers is ensuring compatibility between DC motors and existing power supply systems. Many operations, especially in regions with inconsistent power supply, struggle with integrating DC motors into their infrastructure. For instance, buyers in the Middle East may find their equipment is not optimized for the fluctuating voltage levels common in their electrical grids. This often leads to performance issues, reduced efficiency, and even damage to the motor over time.
The Solution:
To address power supply compatibility issues, buyers should prioritize sourcing DC motors that are designed for a range of voltage inputs. It’s advisable to work with manufacturers who offer motors with flexible voltage ratings and built-in protection against voltage spikes. Additionally, implementing robust power management systems can help stabilize the voltage supplied to the motor. Buyers should conduct thorough compatibility assessments before purchasing, which includes measuring voltage and current variations in their existing infrastructure. Consulting with an electrical engineer during the selection process can ensure that the chosen motor meets specific operational requirements and power conditions.
Scenario 3: Limited Technical Support and Knowledge Gaps
The Problem:
Limited access to technical support and knowledge gaps regarding DC motor applications can pose significant hurdles for B2B buyers, particularly in emerging markets. Companies may struggle to find reliable technical assistance for installation, configuration, and troubleshooting. This is particularly critical in Europe, where regulatory standards can vary widely and compliance is essential for operational legitimacy. The lack of expertise can lead to incorrect applications, resulting in inefficient operations and costly failures.
The Solution:
To overcome these challenges, buyers should seek partnerships with manufacturers and distributors that provide extensive technical support and training programs. Engaging suppliers who offer on-site consultation and personalized training can empower teams with the knowledge needed to effectively utilize DC motors. Additionally, investing in online resources such as webinars, instructional videos, and user manuals can enhance understanding and operational capabilities. Buyers should also consider joining industry groups or forums where they can share experiences and seek advice from peers facing similar challenges. This collaborative approach will enhance their operational knowledge and improve overall motor application success.
Strategic Material Selection Guide for motor electric dc
What Are the Key Materials Used in Electric DC Motors?
When selecting materials for electric DC motors, several factors influence performance, durability, and cost. Below, we analyze four common materials used in the manufacturing of these motors, focusing on their properties, advantages, disadvantages, and implications for international B2B buyers.
1. Copper: The Preferred Choice for Windings
Key Properties: Copper is known for its excellent electrical conductivity, thermal conductivity, and resistance to corrosion. It can operate efficiently under high temperatures, making it suitable for motor applications that require robust performance.
Pros & Cons: The primary advantage of copper is its superior conductivity, which enhances the motor’s efficiency and reduces energy losses. However, copper is relatively expensive compared to alternatives like aluminum, and its weight can increase the overall mass of the motor, impacting applications where weight is a critical factor.
Impact on Application: Copper windings are crucial in applications requiring high torque and speed control, such as robotics and automotive systems. Its compatibility with various media makes it versatile across different industries.
Considerations for International Buyers: Buyers should ensure compliance with international standards such as ASTM B170 for copper quality. In regions like Africa and South America, where raw material availability may vary, sourcing reliable suppliers is essential.
2. Aluminum: A Cost-Effective Alternative
Key Properties: Aluminum is lighter than copper and has good electrical conductivity, though not as high as copper. It is resistant to corrosion, especially when anodized, and can withstand moderate temperatures.
Pros & Cons: The main advantage of aluminum is its lower cost and weight, making it a popular choice for applications where reducing mass is critical. However, its lower conductivity means that motors made with aluminum may be less efficient and require larger wire gauges, which can complicate design.
Impact on Application: Aluminum is often used in applications like portable power tools and consumer electronics, where weight savings are essential. Its resistance to corrosion makes it suitable for outdoor applications.
Considerations for International Buyers: Buyers should be aware of the varying quality of aluminum based on regional standards. Compliance with standards such as ASTM B221 is vital, especially in markets like the Middle East, where environmental conditions can affect material performance.
3. Steel: The Backbone of Motor Frames
Key Properties: Steel offers high tensile strength and durability, making it an excellent choice for motor frames. It can withstand high pressures and impacts, and when treated, it can resist corrosion.
Pros & Cons: The strength of steel provides excellent structural integrity, ensuring the motor can handle harsh environments. However, steel is heavier than other materials, which can limit its use in lightweight applications. Additionally, the cost of high-quality steel can be significant.
Impact on Application: Steel frames are commonly used in industrial motors, where durability is paramount. They are also suitable for applications in harsh environments, such as mining and construction.
Considerations for International Buyers: Buyers should consider the availability of quality steel in their regions. Compliance with standards like DIN 17100 is crucial, particularly in Europe, where stringent quality requirements exist.
4. Plastics: The Future of Lightweight Components
Key Properties: Engineering plastics, such as polycarbonate and nylon, are increasingly used in non-load-bearing components of DC motors. They are lightweight, resistant to corrosion, and can be molded into complex shapes.
Pros & Cons: The primary advantage of plastics is their weight and design flexibility, allowing for innovative motor designs. However, they typically have lower strength and thermal resistance compared to metals, which may limit their use in high-stress applications.
Impact on Application: Plastics are often used in consumer electronics and low-power applications where weight and design are more critical than strength.
Considerations for International Buyers: Buyers should ensure that the plastics used meet international safety and performance standards, such as UL 94 for flammability. In regions like Africa and South America, sourcing reliable suppliers that adhere to these standards is essential.
Summary Table of Material Selection for Electric DC Motors
Material | Typical Use Case for motor electric dc | Key Advantage | Key Disadvantage/Limitation | Relative Cost (Low/Med/High) |
---|---|---|---|---|
Copper | Windings in high-efficiency motors | Superior electrical conductivity | Higher cost and weight | High |
Aluminum | Portable tools and consumer electronics | Cost-effective and lightweight | Lower conductivity | Medium |
Steel | Industrial motors | High strength and durability | Heavier and potentially more costly | Medium to High |
Plastics | Non-load-bearing components | Lightweight and design flexibility | Lower strength and thermal resistance | Low |
This guide serves as a foundational resource for international B2B buyers, enabling informed decisions when selecting materials for electric DC motors, considering performance, cost, and compliance with regional standards.
In-depth Look: Manufacturing Processes and Quality Assurance for motor electric dc
What Are the Main Stages of Manufacturing Electric DC Motors?
The manufacturing process for electric DC motors involves several critical stages that ensure the final product meets industry standards and customer expectations. The primary stages include:
-
Material Preparation: This initial stage involves sourcing high-quality materials such as copper for windings, permanent magnets, and steel for the motor casing. Material quality is crucial since it directly impacts the motor’s efficiency and durability. Suppliers should provide certifications for material properties to ensure compliance with international standards.
-
Forming: In this phase, raw materials are shaped into the required components. Techniques such as stamping, machining, and injection molding are commonly used to create parts like the rotor, stator, and housing. Precision in this step is essential, as even minor deviations can lead to performance issues.
-
Assembly: This stage involves the integration of individual components into a complete motor. Automated assembly lines are often employed to enhance efficiency and consistency. During assembly, particular attention is paid to the alignment of the rotor and stator, as misalignment can affect torque and speed control.
-
Finishing: The final stage includes surface treatments such as painting, coating, or plating to enhance corrosion resistance and aesthetics. This step may also involve the installation of additional components such as encoders or brakes, depending on the motor’s intended application.
Which Key Techniques Are Utilized in DC Motor Manufacturing?
Manufacturers employ various techniques to optimize the performance and longevity of DC motors:
-
Winding Techniques: Utilizing automated winding machines can enhance the precision of coil windings, which is critical for achieving the desired electromagnetic properties.
-
Quality Machining: CNC (Computer Numerical Control) machining is often used for creating highly precise parts. This technology reduces human error and ensures consistency across production batches.
-
Magnetization: For permanent magnet DC motors, effective magnetization processes are essential. Techniques such as pulse magnetization ensure that magnets achieve optimal strength, which is vital for performance.
-
Testing and Calibration: Each motor undergoes a series of tests to verify functionality. Calibration adjustments may be made to ensure the motor operates within specified parameters.
What Quality Assurance Practices Are Essential for DC Motors?
Quality assurance (QA) is critical in the manufacturing of DC motors to ensure reliability and performance. Key practices include:
-
International Standards Compliance: Compliance with standards such as ISO 9001 ensures that the manufacturing process meets international quality management criteria. For specific applications, adherence to CE (Conformité Européenne) or API (American Petroleum Institute) standards may also be necessary.
-
Quality Control Checkpoints: Effective QC involves several checkpoints:
- Incoming Quality Control (IQC): Inspecting raw materials before production to ensure they meet specifications.
- In-Process Quality Control (IPQC): Continuous monitoring during the manufacturing process to catch defects early.
-
Final Quality Control (FQC): Comprehensive testing of the finished product to confirm it meets performance criteria.
-
Common Testing Methods: Testing methods include electrical testing, thermal cycling, and vibration analysis. These tests help identify potential failures and ensure that the motors can withstand operational stresses.
How Can B2B Buyers Verify Supplier Quality Control?
International B2B buyers must implement strategies to verify the quality assurance practices of potential suppliers. Here are actionable steps:
-
Conduct Audits: Regularly audit suppliers to evaluate their manufacturing processes and quality control systems. This can be done on-site or through third-party inspection services.
-
Request Quality Reports: Suppliers should provide detailed quality reports, including test results and compliance certifications. This documentation can be crucial for understanding product reliability.
-
Engage Third-Party Inspectors: Utilizing third-party inspection services can offer an unbiased assessment of the supplier’s quality control practices. These inspectors can conduct random checks and provide comprehensive reports on compliance and quality.
What Are the Quality Control and Certification Nuances for International Buyers?
For buyers in regions such as Africa, South America, the Middle East, and Europe, understanding the nuances of quality control and certification is vital:
-
Regional Standards: Be aware of local regulations and standards that may differ from international norms. For instance, products sold in the EU must comply with CE marking, while different certifications may apply in the Middle East.
-
Supplier Certification: Ensure that suppliers are certified by recognized organizations, indicating adherence to quality management systems. Certifications such as ISO 9001 or industry-specific certifications can provide assurance of quality.
-
Cultural Considerations: Understand cultural differences in business practices and communication styles. Building strong relationships with suppliers can enhance transparency and facilitate better cooperation in quality assurance efforts.
Conclusion
For international B2B buyers, particularly those from Africa, South America, the Middle East, and Europe, understanding the manufacturing processes and quality assurance practices of DC motors is essential for making informed purchasing decisions. By focusing on supplier verification, international standards compliance, and robust quality control practices, buyers can ensure they source reliable and high-performance products that meet their operational needs.
Practical Sourcing Guide: A Step-by-Step Checklist for ‘motor electric dc’
In the competitive landscape of international B2B sourcing, procuring electric DC motors requires a strategic approach to ensure you receive the best value and quality for your investment. This checklist provides a step-by-step guide tailored for buyers from Africa, South America, the Middle East, and Europe, aiming to streamline your sourcing process.
Step 1: Define Your Technical Specifications
Establishing clear technical specifications is critical when sourcing electric DC motors. Consider factors such as voltage requirements (e.g., low-voltage options for battery-operated applications), power output, torque, speed ranges, and any specific mounting or environmental constraints. A well-defined specification not only aids in identifying suitable products but also helps in communicating your needs effectively with suppliers.
Step 2: Research Market Trends and Technologies
Understanding the latest trends in DC motor technology can significantly influence your purchasing decision. For instance, advancements in brushless DC (BLDC) motors offer benefits like higher efficiency and lower maintenance costs compared to traditional brushed motors. Conduct market research to compare the advantages of different motor types and their applications in your industry.
Step 3: Evaluate Potential Suppliers
Before committing to a supplier, it’s essential to conduct a thorough evaluation. Look for suppliers with a proven track record in manufacturing DC motors, especially those who can provide case studies or references from similar industries. Consider checking their certifications (e.g., ISO) and quality assurance processes to ensure they meet international standards.
- Key Questions to Ask:
- What are your quality control measures?
- Can you provide examples of similar projects you’ve handled?
Step 4: Request Samples for Testing
Always request samples of the DC motors you intend to purchase. Testing samples can provide insights into the motor’s performance in real-world applications, ensuring they meet your operational requirements. This step is particularly important for high-stakes applications where performance reliability is crucial.
Step 5: Negotiate Terms and Pricing
Effective negotiation can lead to significant cost savings. Discuss pricing, payment terms, and delivery schedules with potential suppliers. Be clear about your budget constraints and explore options for bulk purchasing discounts or long-term contracts to secure better rates.
Step 6: Assess After-Sales Support and Warranty
Consider the level of after-sales support offered by suppliers. A reliable supplier should provide comprehensive support, including installation guidance, troubleshooting assistance, and warranty terms. Understanding the warranty details can help mitigate risks associated with product performance and longevity.
Step 7: Finalize Contracts with Clear Terms
Once you’ve selected a supplier, ensure that all agreements are documented in a formal contract. The contract should outline all terms, including specifications, pricing, delivery timelines, and after-sales support. Clear documentation protects both parties and minimizes the potential for disputes.
By following this checklist, international B2B buyers can navigate the complexities of sourcing electric DC motors more effectively, leading to informed decisions and successful procurement outcomes.
Comprehensive Cost and Pricing Analysis for motor electric dc Sourcing
What Are the Key Cost Components in Sourcing Electric DC Motors?
When sourcing electric DC motors, understanding the cost structure is essential for B2B buyers. The primary cost components include:
-
Materials: The quality and type of materials used, such as copper for windings and rare earth metals for permanent magnets, can significantly affect costs. Higher-grade materials usually yield better performance but come at a premium.
-
Labor: Labor costs can vary based on the region of manufacturing. Countries with lower labor costs may offer more competitive pricing but could compromise on quality or lead times.
-
Manufacturing Overhead: This includes costs associated with factory operations, utilities, and administrative expenses. Efficient manufacturing processes can help reduce overhead, thus lowering overall costs.
-
Tooling: The cost of molds, dies, and other tools necessary for production is also a factor. Custom tooling for specific designs can increase initial costs but may lead to savings in mass production.
-
Quality Control (QC): Implementing robust QC measures ensures product reliability but adds to the overall cost. Buyers should weigh the benefits of stringent QC against potential savings from lower QC standards.
-
Logistics: Shipping and handling costs are often overlooked but can significantly impact the total cost, especially for international transactions. Consideration of warehousing and transportation logistics is crucial.
-
Margin: Suppliers generally apply a profit margin that reflects their operational costs and market conditions. This margin can vary widely based on the supplier’s reputation and the product’s complexity.
How Do Price Influencers Impact the Cost of Electric DC Motors?
Several factors influence the pricing of electric DC motors:
-
Volume/MOQ: Suppliers often offer better pricing for bulk orders. Understanding the minimum order quantities (MOQ) can lead to cost savings for larger purchases.
-
Specifications and Customization: Custom specifications can increase costs due to the need for specialized materials or manufacturing processes. Buyers should evaluate if standard products meet their needs before opting for custom solutions.
-
Materials: The choice of materials directly impacts pricing. For instance, opting for standard copper windings instead of high-performance materials can reduce costs.
-
Quality and Certifications: Motors that meet international quality standards (e.g., ISO, CE) may be priced higher but are often more reliable. Investing in certified products can minimize maintenance costs in the long run.
-
Supplier Factors: Supplier reputation, reliability, and service can influence pricing. Established suppliers may charge more but often provide better support and warranty options.
-
Incoterms: Understanding the terms of delivery (e.g., FOB, CIF) is crucial. These terms can affect total landed costs, including shipping, insurance, and customs duties.
What Are Essential Buyer Tips for Cost-Efficiency in Electric DC Motor Sourcing?
B2B buyers can adopt several strategies to optimize costs when sourcing electric DC motors:
-
Negotiation: Always negotiate terms and pricing with suppliers. Establishing long-term relationships can lead to better deals and discounts.
-
Cost-Efficiency: Analyze the Total Cost of Ownership (TCO), including purchase price, maintenance, and operational costs. A lower initial price may not always be the best option if it leads to higher long-term expenses.
-
Pricing Nuances for International Buyers: Buyers from Africa, South America, the Middle East, and Europe should consider currency fluctuations and local import regulations. These factors can add complexity to pricing and should be factored into negotiations.
-
Research and Compare: Spend time researching various suppliers and products. Obtaining multiple quotes will provide insights into fair pricing and help identify the best value.
-
Leverage Technology: Utilize online platforms and tools to compare specifications and prices of electric DC motors. This can streamline the sourcing process and enhance decision-making.
Disclaimer on Indicative Prices
Prices for electric DC motors can vary significantly based on the discussed factors. Therefore, it is advisable to conduct thorough market research and consult multiple suppliers to obtain the most accurate and competitive pricing for your specific needs.
Alternatives Analysis: Comparing motor electric dc With Other Solutions
The decision-making process for selecting an appropriate motor technology is crucial for businesses seeking efficiency and reliability in their operations. While motor electric DC (Direct Current) motors offer specific advantages, it’s essential to consider viable alternatives that may better suit particular applications or operational needs. Below, we compare motor electric DC with two primary alternatives: AC motors and Brushless DC (BLDC) motors.
Comparison Table of Motor Electric DC and Alternatives
Comparison Aspect | Motor Electric DC | AC Motors | Brushless DC Motors (BLDC) |
---|---|---|---|
Performance | High starting torque; smooth operation at low speeds | Good for high-speed applications; variable speed with AC drives | High efficiency; excellent speed control and torque at low speeds |
Cost | Generally higher initial costs; maintenance costs due to brushes | Lower initial costs; variable based on application | Moderate costs; typically lower maintenance than brushed motors |
Ease of Implementation | Requires specific controllers and power supply; easy for small-scale applications | Widely available; simpler integration in many existing systems | More complex setup; requires compatible controllers |
Maintenance | Higher maintenance due to brush replacement | Lower maintenance; fewer parts subject to wear | Minimal maintenance; no brushes to replace |
Best Use Case | Adjustable speed applications, battery-operated devices | General purpose, industrial applications, HVAC systems | Robotics, electric vehicles, and precision applications |
Understanding the Pros and Cons of Alternatives
What are the Advantages and Disadvantages of AC Motors?
AC motors are widely recognized for their versatility and lower initial costs. They are suitable for a variety of applications, particularly in industrial settings where high-speed performance is required. The ease of integration with existing systems and lower maintenance requirements make them an attractive option. However, they may not provide the same level of torque at low speeds as DC motors, which can limit their effectiveness in applications requiring precise speed control.
How Do Brushless DC Motors Compare to Motor Electric DC?
Brushless DC motors offer several advantages over traditional DC motors, particularly in terms of efficiency and maintenance. They operate without brushes, significantly reducing wear and the need for replacement parts, thus ensuring longer operational life and reliability. BLDC motors excel in applications requiring precise speed and torque control, making them ideal for robotics and electric vehicles. However, they typically involve more complex systems and higher initial costs, which can be a consideration for budget-conscious buyers.
How Should B2B Buyers Choose the Right Motor Solution?
When selecting the right motor technology, B2B buyers must consider their specific operational requirements, including performance needs, budget constraints, and maintenance capabilities. If the application demands high torque at low speeds, motor electric DC may be the best choice. In contrast, for applications where initial costs are a concern and high-speed performance is necessary, AC motors could be more suitable. Meanwhile, for high-efficiency operations requiring precise control, Brushless DC motors present a compelling alternative. Assessing these factors will enable businesses to make informed decisions that align with their long-term operational goals.
Essential Technical Properties and Trade Terminology for motor electric dc
What Are the Key Technical Properties of Electric DC Motors?
Understanding the essential technical properties of electric DC motors is crucial for international B2B buyers, especially when sourcing products from diverse markets in Africa, South America, the Middle East, and Europe. Here are some critical specifications to consider:
-
Voltage Rating
The voltage rating indicates the electrical potential required to operate the motor efficiently. Common ratings include 12V, 24V, 90V, and 180V. Understanding the voltage rating helps buyers determine compatibility with their power supply systems, especially in regions where low-voltage systems are prevalent, such as in battery-powered applications. -
Torque
Torque is a measure of rotational force and is critical for applications requiring significant power output. It is usually expressed in ounce-inches (oz-in) or Newton-meters (Nm). High torque ratings are essential for applications like conveyor systems and robotics, where consistent performance is required under varying loads. -
Speed (RPM)
The revolutions per minute (RPM) rating indicates how fast the motor can spin. This specification is crucial for buyers looking for motors that can achieve specific operational speeds in applications such as packaging machinery or automated assembly lines. -
Duty Cycle
The duty cycle defines how long a motor can operate before needing a cooldown period. It is typically expressed as a percentage. Motors designed for continuous duty can run for extended periods without overheating, which is vital for applications in industrial settings. -
Efficiency
Efficiency measures how well a motor converts electrical energy into mechanical energy. A higher efficiency rating translates to lower operational costs and reduced energy consumption, making it a critical factor for environmentally-conscious companies and those operating in regions with high energy costs.
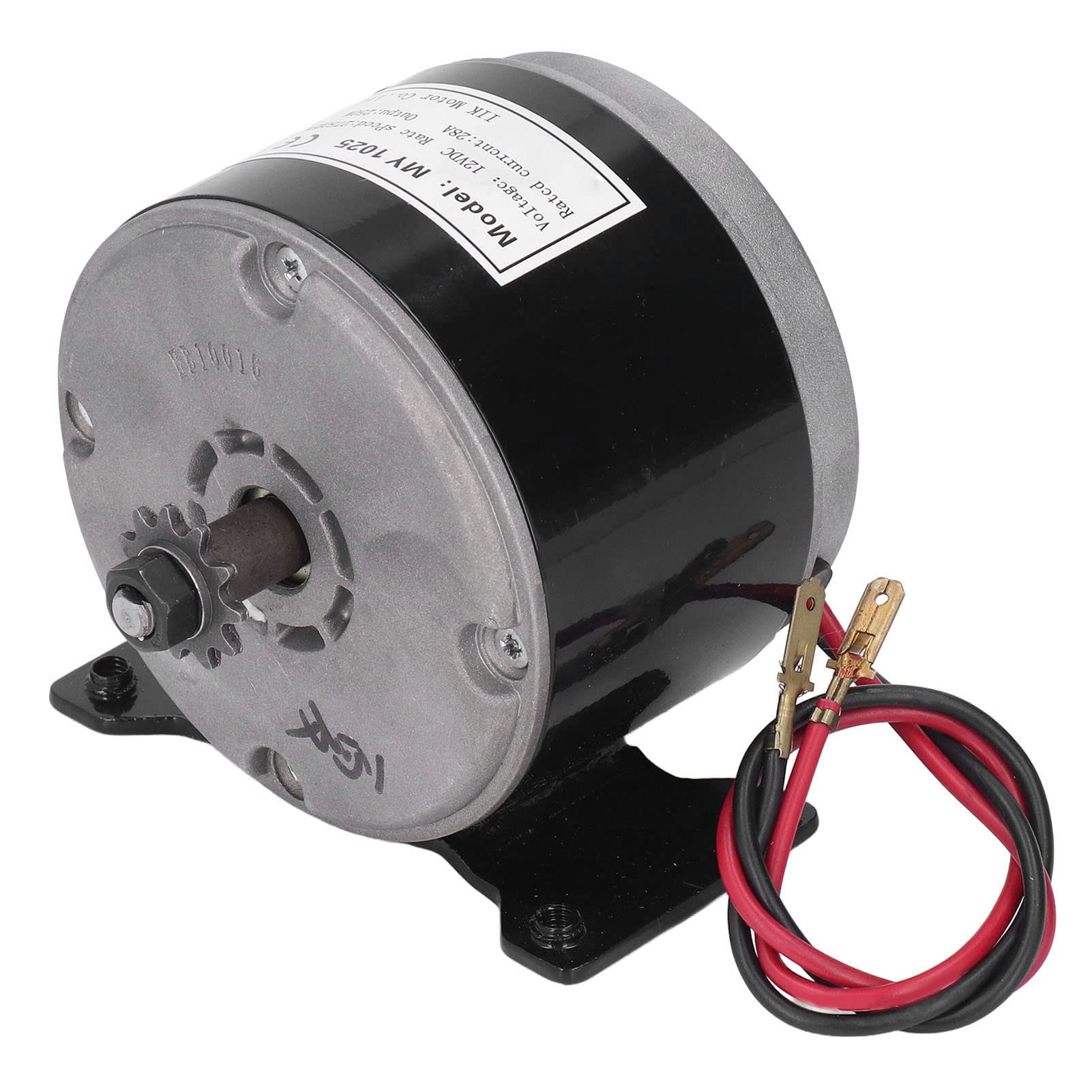
A stock image related to motor electric dc.
- Material Grade
The material used in motor construction, particularly the rotor and stator, affects durability and performance. High-grade materials like copper and specialized alloys enhance thermal conductivity and reduce wear, thereby extending the motor’s lifespan and reliability.
What Are Common Trade Terms in the DC Motor Industry?
Familiarity with industry-specific jargon can streamline communication and negotiation processes. Here are some essential terms for B2B buyers:
-
OEM (Original Equipment Manufacturer)
OEMs produce parts and equipment that are sold under another company’s brand. For buyers, sourcing from OEMs often ensures quality and reliability, as these manufacturers adhere to strict industry standards. -
MOQ (Minimum Order Quantity)
MOQ refers to the smallest quantity of a product that a supplier is willing to sell. Understanding the MOQ is vital for budgeting and inventory management, especially for businesses in emerging markets where capital may be limited. -
RFQ (Request for Quotation)
An RFQ is a formal document sent to suppliers to request pricing for specific products. This process is essential for obtaining competitive pricing and ensuring that all potential suppliers meet the technical requirements. -
Incoterms (International Commercial Terms)
Incoterms define the responsibilities of buyers and sellers in international trade. Familiarity with these terms helps buyers understand shipping responsibilities, insurance, and risk during transportation, which is especially relevant for companies importing motors from different continents. -
Lead Time
Lead time is the duration from placing an order to receiving the product. Understanding lead times can help businesses plan their production schedules and manage customer expectations effectively. -
Aftermarket Support
Aftermarket support refers to services provided after the sale, such as maintenance, spare parts, and technical assistance. Strong aftermarket support is crucial for companies that rely on the continuous operation of their equipment.
Conclusion
Navigating the technical properties and trade terminology of electric DC motors is essential for international B2B buyers. By understanding these specifications and terms, buyers can make informed decisions that align with their operational needs and market conditions.
Navigating Market Dynamics and Sourcing Trends in the motor electric dc Sector
What Are the Current Market Dynamics and Key Trends in the DC Motor Sector?
The global market for DC motors is witnessing significant growth, driven by the increasing demand for energy-efficient solutions across various industries, including automotive, manufacturing, and renewable energy. As international B2B buyers from regions like Africa, South America, the Middle East, and Europe seek to enhance operational efficiencies, the focus on high-performance motors that offer adjustable speed and high starting torque is becoming paramount. Emerging technologies, such as brushless DC (BLDC) motors, are gaining traction due to their superior efficiency, lower maintenance costs, and reduced noise levels compared to traditional brushed DC motors.
In terms of sourcing trends, buyers are increasingly looking for suppliers that can provide customized solutions tailored to specific applications, such as agricultural equipment and warehouse automation systems. Additionally, the integration of advanced digital technologies, including IoT and AI, is transforming the supply chain landscape, enabling real-time monitoring and predictive maintenance. This shift not only enhances operational efficiencies but also supports data-driven decision-making for buyers in diverse markets.
Moreover, geopolitical factors and economic fluctuations are influencing sourcing strategies. Buyers are advised to diversify their supplier base to mitigate risks associated with supply chain disruptions. This approach is particularly relevant for buyers in regions with varying levels of infrastructure development, where local sourcing may present unique opportunities for cost savings and faster delivery times.
How Can B2B Buyers Address Sustainability and Ethical Sourcing in the DC Motor Sector?
Sustainability is becoming a critical consideration for B2B buyers in the DC motor sector. The environmental impact of manufacturing processes, including carbon emissions and waste generation, is prompting companies to prioritize sustainable practices. Buyers should seek suppliers that implement eco-friendly manufacturing processes, such as energy-efficient production methods and the use of recyclable materials.
Ethical sourcing is also gaining traction, with buyers increasingly focused on supply chain transparency. This includes ensuring that suppliers adhere to fair labor practices and comply with environmental regulations. Buyers can enhance their credibility and appeal to environmentally conscious consumers by partnering with suppliers who possess ‘green’ certifications, such as ISO 14001 or Energy Star ratings.
Furthermore, the shift towards renewable energy sources, like solar and wind power, is influencing the demand for low-voltage PMDC motors, which are ideal for battery-operated and off-grid applications. By investing in sustainable technologies and ethical supply chains, B2B buyers can not only contribute to environmental conservation but also align their operations with global sustainability goals.
What Is the Evolution of the DC Motor Industry and Its Relevance for B2B Buyers?
The DC motor industry has evolved significantly since its inception in the late 19th century. Initially, these motors were primarily used in basic applications, but advancements in technology have expanded their utility across various sectors. The introduction of permanent magnet DC motors (PMDC) and brushless DC motors (BLDC) has revolutionized the market, offering enhanced efficiency and performance.
For B2B buyers, understanding the historical context of DC motors is essential for making informed purchasing decisions. The shift from traditional brushed motors to advanced alternatives reflects broader trends in energy efficiency and automation. This evolution highlights the importance of selecting suppliers that stay abreast of technological advancements and can provide innovative solutions to meet the demands of modern applications.
In summary, the dynamics of the DC motor market are shaped by technological innovations, sustainability considerations, and shifting buyer preferences. By staying informed and strategically navigating these trends, international B2B buyers can optimize their sourcing strategies and position themselves for success in an increasingly competitive landscape.
Frequently Asked Questions (FAQs) for B2B Buyers of motor electric dc
-
How do I choose the right DC motor for my application?
Choosing the right DC motor involves considering several factors, including the required voltage, torque, speed, and the specific application needs. For instance, if your application requires high starting torque and adjustable speed, a Permanent Magnet DC (PMDC) motor may be ideal. Assess your operational environment, such as temperature and humidity, and consider whether you need a low-voltage model for battery-powered applications. Consulting with manufacturers about your specific requirements can help ensure you select a motor that meets your performance criteria. -
What are the key benefits of using DC motors in industrial applications?
DC motors offer numerous advantages in industrial applications, including smooth operation, high starting torque, and precise speed control. They are particularly beneficial in environments requiring variable speed and load conditions, such as conveyor systems or robotics. Additionally, their simple design facilitates easy integration with battery power, making them suitable for off-grid applications. While they may incur higher maintenance costs due to brush replacement, their performance in specific applications can justify these expenses. -
What should I consider when vetting suppliers for DC motors?
When vetting suppliers, focus on their reputation, experience in the industry, and product quality. Look for suppliers who provide detailed product specifications and have a track record of reliability. Request samples to assess motor performance, and inquire about certifications that ensure compliance with international standards. Additionally, evaluate their customer service and support capabilities, as prompt communication and assistance can be crucial for resolving any issues post-purchase. -
What are the typical minimum order quantities (MOQs) for DC motors?
MOQs for DC motors can vary widely depending on the supplier and the type of motor. Some manufacturers may have low MOQs for standard models, while custom motors may require larger orders. It’s advisable to discuss your specific needs with potential suppliers to understand their policies. If you’re a smaller buyer, consider looking for distributors or suppliers who specialize in smaller quantities to meet your requirements without excessive inventory costs.
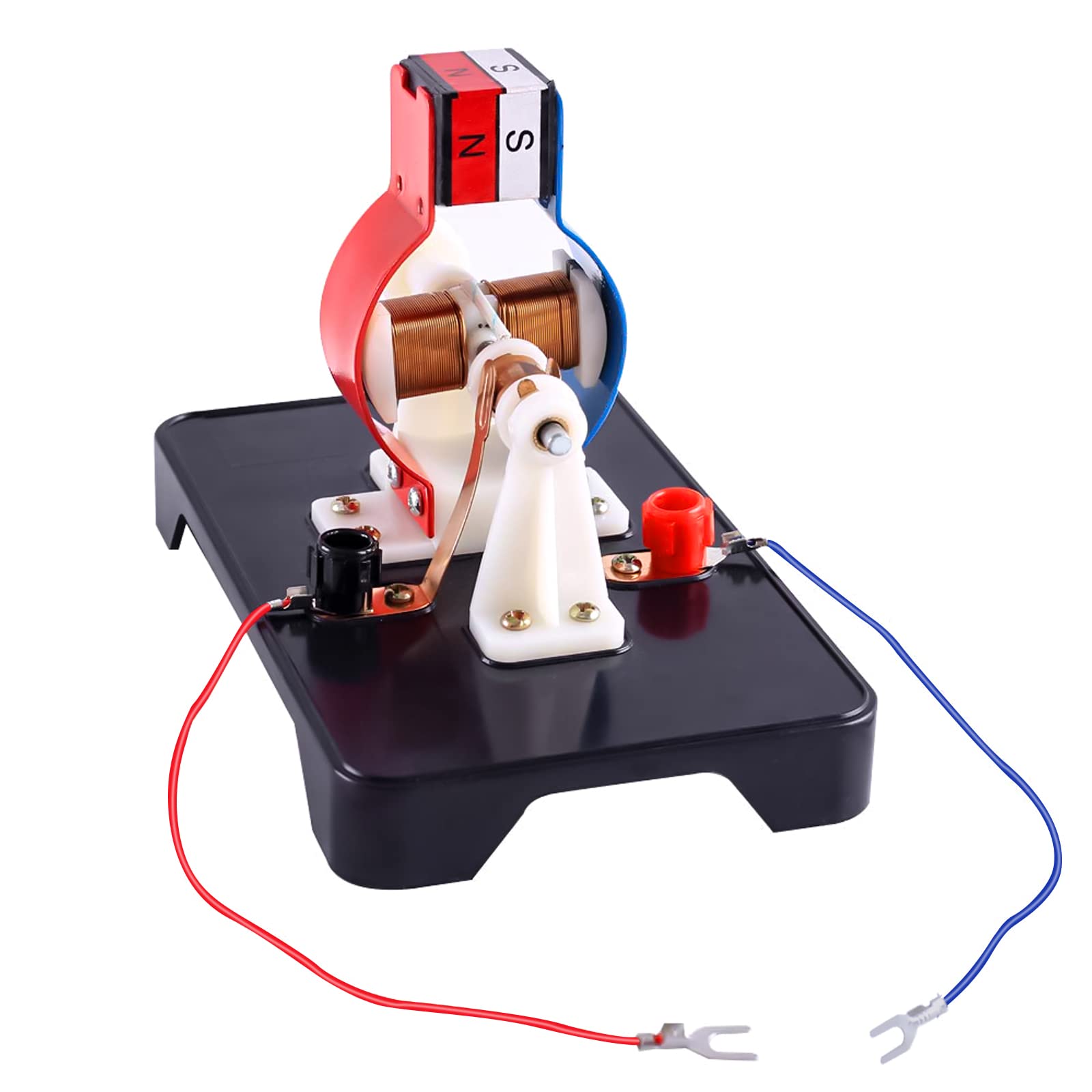
A stock image related to motor electric dc.
-
How can I customize a DC motor for my specific needs?
Customization options for DC motors often include adjustments to voltage ratings, torque specifications, and physical dimensions. Many suppliers offer the ability to tailor motors to fit unique application requirements, such as adding encoders for precise speed control or modifying windings for specific operational environments. Engage with your supplier early in the design process to discuss your needs and evaluate potential solutions, ensuring that the final product aligns with your application’s demands. -
What payment terms are common for international B2B transactions?
Payment terms can vary, but common practices include partial upfront payments with the balance due upon delivery, or payment via letters of credit to secure both parties. Ensure clarity on the payment schedule, currency, and any additional costs like taxes or shipping fees. It’s prudent to negotiate terms that protect your investment, especially in international transactions where risks may be higher. Always document agreements to avoid misunderstandings. -
What quality assurance measures should I expect from DC motor suppliers?
Reliable suppliers typically implement strict quality assurance (QA) processes, including testing motors for performance, durability, and safety compliance. Expect to see certifications such as ISO 9001 or IEC standards that indicate adherence to quality management principles. Ask about the testing procedures they employ and whether they provide warranties or guarantees for their products. A solid QA framework not only assures product quality but also minimizes the risk of failures in your applications. -
How do I manage logistics for sourcing DC motors internationally?
Managing logistics for international sourcing involves understanding shipping regulations, customs requirements, and potential tariffs. Collaborate with logistics partners who have experience in handling industrial shipments to streamline the process. Ensure that you have clear documentation, including commercial invoices and packing lists, to facilitate customs clearance. Additionally, consider the lead times for production and shipping, and plan accordingly to avoid delays in your project timelines.
Important Disclaimer & Terms of Use
⚠️ Important Disclaimer
The information provided in this guide, including content regarding manufacturers, technical specifications, and market analysis, is for informational and educational purposes only. It does not constitute professional procurement advice, financial advice, or legal advice.
While we have made every effort to ensure the accuracy and timeliness of the information, we are not responsible for any errors, omissions, or outdated information. Market conditions, company details, and technical standards are subject to change.
B2B buyers must conduct their own independent and thorough due diligence before making any purchasing decisions. This includes contacting suppliers directly, verifying certifications, requesting samples, and seeking professional consultation. The risk of relying on any information in this guide is borne solely by the reader.
Strategic Sourcing Conclusion and Outlook for motor electric dc
In the realm of strategic sourcing for motor electric DC, international buyers must prioritize quality, efficiency, and adaptability to stay competitive. The insights gathered throughout this guide emphasize the importance of selecting the right DC motor types—such as Permanent Magnet DC (PMDC) and Brushless DC (BLDC) motors—tailored for specific applications. These motors offer advantages like high starting torque, compact designs, and efficient power management, particularly in regions with limited energy resources, such as Africa and South America.
How Can Strategic Sourcing Enhance Your Supply Chain?
By leveraging strategic sourcing, buyers can cultivate long-term partnerships with reliable suppliers, ensuring access to advanced technologies and cost-effective solutions. This practice not only mitigates risks associated with supply chain disruptions but also enhances the overall performance of motor systems in diverse applications ranging from warehouse automation to renewable energy solutions.
What Does the Future Hold for DC Motors?
As industries evolve, the demand for efficient and sustainable motor solutions will continue to rise. Buyers from the Middle East and Europe should be proactive in exploring innovations in DC motor technology, such as enhanced control systems and energy-efficient designs. By doing so, they can position themselves at the forefront of the market, ready to capitalize on emerging opportunities. Engaging with suppliers who emphasize R&D and sustainability will be crucial in this dynamic landscape.
Take the initiative to reassess your sourcing strategies today and align with partners that share your vision for innovation and efficiency in the motor electric DC sector.