Optimize Costs: The Ultimate Cable Reeling Guide (2025)
Introduction: Navigating the Global Market for cable reeling
Navigating the complexities of sourcing the right cable reeling solutions can be a significant challenge for international B2B buyers, particularly in regions such as Africa, South America, the Middle East, and Europe. With a plethora of options available, including various types of reeling cables designed for heavy-duty applications, it is crucial to identify products that not only meet operational demands but also ensure long-term reliability. This comprehensive guide delves into the diverse types of cable reeling solutions, their applications across industries, and best practices for supplier vetting, ensuring that buyers are equipped with the knowledge necessary for informed purchasing decisions.
Understanding the specifications, such as temperature resistance, mechanical load capacities, and material durability, is essential for selecting the appropriate cable reeling products for specific applications, from cranes to transport systems. Furthermore, this guide addresses critical factors influencing cost and performance, allowing buyers to balance quality with budget constraints effectively.
By providing actionable insights and expert recommendations, this guide empowers B2B buyers to navigate the global market for cable reeling with confidence. Whether you are in Indonesia, Kenya, or elsewhere, the information presented here will help streamline your procurement process, ensuring that you choose the most suitable reeling solutions for your business needs.
Understanding cable reeling Types and Variations
Type Name | Key Distinguishing Features | Primary B2B Applications | Brief Pros & Cons for Buyers |
---|---|---|---|
Motor-Driven Cable Reels | Automated winding, designed for high-load applications | Cranes, mining equipment, industrial machines | Pros: High efficiency, less manual labor. Cons: Higher initial cost, requires power source. |
Spring-Driven Cable Reels | Manual operation, uses spiral springs for cable retraction | Hoists, transport systems, agricultural equipment | Pros: Cost-effective, low maintenance. Cons: Limited to lighter loads, manual setup required. |
Portable Power Reeling Cables | Flexible, lightweight design, suitable for retractable applications | Events, stage lighting, temporary installations | Pros: Easy to transport, versatile. Cons: Less durable for heavy-duty use. |
High-Temperature Reeling Cables | Specially designed to withstand extreme temperatures | Aerospace, military, specialized industrial uses | Pros: High resistance to heat, reliable in extreme conditions. Cons: Specialized, potentially higher costs. |
Control Cables for Reeling | Multi-conductor design for data and power transfer | Robotics, automation, crane control systems | Pros: Efficient data transfer, versatile. Cons: Complex installation, higher technical requirements. |
What are the Characteristics of Motor-Driven Cable Reels?
Motor-driven cable reels are engineered for high-load applications, providing automated winding and unwinding of cables. They are ideal for industries where efficiency is paramount, such as construction, mining, and heavy machinery. When considering a motor-driven reel, buyers should evaluate the power requirements and installation space. While they offer significant labor savings and operational efficiency, the upfront costs and dependency on a power source can be drawbacks.
How Do Spring-Driven Cable Reels Operate?
Spring-driven cable reels operate using a manual mechanism powered by spiral springs. They are commonly used in applications where lighter loads are involved, such as in hoists and agricultural equipment. Buyers appreciate their cost-effectiveness and low maintenance needs. However, it is essential to consider that they may not be suitable for heavy-duty applications and require manual operation, which could be a limitation in high-demand environments.
What Makes Portable Power Reeling Cables Unique?
Portable power reeling cables are designed for flexibility and ease of transport, making them ideal for temporary installations at events or for stage lighting. Their lightweight nature allows for quick setup and breakdown, catering to industries that require mobility. Buyers should consider their specific application needs, as while they provide versatility, they may not withstand the rigors of heavy-duty use.
Why Choose High-Temperature Reeling Cables?
High-temperature reeling cables are specifically formulated to endure extreme heat, making them suitable for aerospace and military applications. These cables are essential in environments where conventional cables might fail. Buyers must assess the temperature ratings and specific application requirements, as these specialized cables often come with a higher price tag but provide critical reliability in challenging conditions.
What are Control Cables for Reeling Applications?
Control cables designed for reeling are multi-conductor cables that facilitate both power and data transfer. These cables are crucial in automation systems, robotics, and crane control, ensuring seamless operation. When purchasing control cables, businesses should evaluate their technical requirements and installation complexities. Although they offer high efficiency in data transfer, their intricate installation process can be a barrier for some users.
Key Industrial Applications of cable reeling
Industry/Sector | Specific Application of Cable Reeling | Value/Benefit for the Business | Key Sourcing Considerations for this Application |
---|---|---|---|
Manufacturing | Power supply for automated machinery | Enhanced efficiency and reduced downtime | Durability, flexibility, and compatibility with machinery |
Construction | Crane operations for lifting heavy materials | Increased safety and productivity on site | Load capacity, weather resistance, and installation ease |
Entertainment | Stage lighting and sound systems | Reliable performance during events | Flexibility, ease of handling, and heat resistance |
Mining | Power and control cables for heavy equipment | Improved operational reliability in harsh environments | Resistance to abrasion, chemical exposure, and tensile strength |
Agriculture | Control cables for automated irrigation systems | Increased crop yield and resource efficiency | Environmental resistance and customizability for specific needs |
How is Cable Reeling Used in Manufacturing and What Problems Does It Solve?
In the manufacturing sector, cable reeling systems are crucial for supplying power to automated machinery, such as robotic arms and conveyor belts. These systems minimize cable wear and prevent tangling, thereby enhancing operational efficiency. For international buyers, especially from regions like Africa and South America, sourcing durable and flexible cables that can withstand vibrations and impacts is essential. Buyers should consider the specific environmental conditions of their operations, including temperature extremes and potential exposure to chemicals.
What Role Does Cable Reeling Play in Construction?
In construction, cable reeling is primarily used to support crane operations, allowing for the safe lifting of heavy materials. This application not only boosts productivity but also enhances safety by ensuring that cables are managed efficiently. Buyers in the Middle East and Europe must focus on sourcing cables with high load capacities and weather resistance to accommodate various site conditions, including extreme temperatures and moisture levels. Additionally, ease of installation and maintenance should be prioritized to minimize downtime on construction sites.
How is Cable Reeling Essential in the Entertainment Industry?
The entertainment industry employs cable reeling systems for stage lighting and sound equipment, where reliability is paramount during live events. These systems facilitate quick setup and breakdown, ensuring that performances run smoothly without technical hitches. For buyers in Europe and South America, it’s critical to source cables that are not only flexible but also capable of withstanding high temperatures generated by lighting equipment. Customization options may also be necessary to meet the specific requirements of different venues.
How is Cable Reeling Applied in Mining Operations?
In mining, cable reeling plays a vital role in supplying power and control signals to heavy equipment, such as excavators and drilling rigs. The harsh environments of mines demand cables that can resist abrasion and chemical exposure while maintaining tensile strength. International buyers, particularly from regions with significant mining activity, should prioritize sourcing cables that are specifically designed for these conditions. Understanding the operational demands and environmental challenges is essential for ensuring that the selected cables provide long-term reliability.
What is the Importance of Cable Reeling in Agriculture?
In agriculture, cable reeling is used in automated irrigation systems, where it facilitates the control of water supply to crops. This application not only increases crop yield but also enhances resource efficiency, which is crucial in regions facing water scarcity. Buyers from Africa and South America should seek cables that offer environmental resistance and are customizable to meet specific irrigation needs. Ensuring that these cables can withstand outdoor conditions and provide reliable performance is essential for maximizing agricultural productivity.
3 Common User Pain Points for ‘cable reeling’ & Their Solutions
Scenario 1: Frequent Cable Damage in Harsh Environments
The Problem: B2B buyers in industries such as mining, construction, and agriculture often face challenges with cable durability. In environments where heavy machinery operates, cables are subjected to high levels of abrasion, extreme temperatures, and exposure to chemicals. This leads to frequent cable damage, resulting in costly downtime and repairs. For buyers in regions like Africa or South America, where infrastructure might be less stable, ensuring the reliability of electrical systems is critical.
The Solution: To mitigate cable damage, it is essential to select high-quality reeling cables specifically designed for harsh conditions. Look for cables with robust insulation materials that can withstand extreme temperatures and resist chemicals, such as TPC’s Thermo-Trex® High Temp Reeling Cable. Buyers should also consider cables with enhanced flexibility and abrasion resistance, like those reinforced with aramid fibers. When sourcing, request samples and conduct thorough testing in your specific operational environment to ensure compatibility. Additionally, implement regular maintenance checks to identify wear early and replace cables before they fail, minimizing downtime and disruption.
Scenario 2: Inefficiencies in Cable Management Systems
The Problem: Many companies struggle with inefficient cable management, particularly in facilities where heavy machinery and moving parts are involved. Cables that are poorly organized can lead to tangling, snags, and operational hazards, which can be particularly concerning in fast-paced environments such as logistics and manufacturing in the Middle East and Europe. This not only affects productivity but also increases the risk of accidents and equipment failure.
The Solution: Implementing an efficient cable management system begins with selecting the right type of cable reels. Consider motor-driven cable reels for high-usage applications, as they provide consistent retraction and can handle multiple cables without tangling. Ensure that the reels are sized appropriately for your operational needs, considering factors like the length of cable and the frequency of use. Investing in automated cable management solutions, such as those that incorporate sensors for real-time monitoring, can further enhance efficiency. Training staff on proper cable handling techniques and scheduling regular maintenance of the cable reels can also prevent issues before they arise.
Scenario 3: Difficulty in Custom Cable Solutions
The Problem: International buyers often encounter a lack of tailored solutions when sourcing cable reeling products. Many standard cables do not meet specific operational requirements, leading to poor performance and potential safety hazards. This is particularly relevant for industries in South America and Africa, where local manufacturers may not offer the customization options needed for unique applications, such as specialized machinery or environmental conditions.
The Solution: To address this challenge, buyers should partner with manufacturers who offer bespoke cable solutions. Engage with suppliers like SAB Cable or Stemmann-Technik, who can create cables optimized for specific applications. Provide detailed specifications regarding the mechanical loads, environmental conditions, and operational expectations. Utilize the expertise of these manufacturers to develop a solution that meets your exact needs, whether it’s incorporating specific shielding materials or customizing cable lengths. Building strong relationships with suppliers ensures that you have access to the latest innovations and can quickly adapt to changing operational demands, enhancing overall efficiency and safety.
Strategic Material Selection Guide for cable reeling
What are the Key Materials Used in Cable Reeling Applications?
When selecting materials for cable reeling applications, it is crucial to consider the specific requirements of the environment and the intended use. Here, we analyze four common materials used in cable reeling, focusing on their properties, advantages, disadvantages, and implications for international B2B buyers.
How Does PVC Perform in Cable Reeling Applications?
Key Properties: Polyvinyl Chloride (PVC) is known for its excellent electrical insulation properties, temperature resistance (up to 70°C), and good mechanical strength. It is also resistant to many chemicals and has a low moisture absorption rate.
Pros & Cons: PVC is cost-effective and easy to manufacture, making it a popular choice for a variety of applications. However, it has limitations in high-temperature environments, as prolonged exposure to temperatures above its rating can lead to degradation. Additionally, PVC is less flexible than other materials, which may affect its performance in dynamic applications.
Impact on Application: PVC is suitable for indoor applications and environments where exposure to chemicals is minimal. However, it may not be the best choice for outdoor applications in regions with extreme temperatures or UV exposure.
Considerations for International Buyers: Buyers from regions like Africa and South America should ensure that PVC cables meet local compliance standards (e.g., ASTM, IEC) to avoid issues with quality and safety.
What Advantages Does Rubber Offer for Cable Reeling?
Key Properties: Rubber cables are known for their excellent flexibility, high-temperature resistance (up to 90°C), and superior abrasion resistance. They also provide good electrical insulation and are resistant to oil and chemicals.
Pros & Cons: The primary advantage of rubber cables is their durability and flexibility, making them ideal for dynamic applications. However, they can be more expensive to produce than PVC cables and may require more complex manufacturing processes.
Impact on Application: Rubber is particularly well-suited for outdoor and industrial applications where exposure to harsh conditions is common, such as in construction or mining.
Considerations for International Buyers: Buyers should check for certifications and compliance with local standards, especially in regions with stringent safety regulations. The higher cost may also be a consideration for budget-sensitive projects.
Why Choose Thermoplastic Elastomers (TPE) for Cable Reeling?
Key Properties: Thermoplastic elastomers combine the flexibility of rubber with the processing advantages of plastics. They have a high-temperature rating (up to 120°C) and excellent resistance to UV light and ozone.
Pros & Cons: TPEs offer great flexibility and durability, making them suitable for a wide range of applications. However, they tend to be more expensive than PVC and may not be as readily available in all markets.
Impact on Application: TPE is ideal for applications that require both flexibility and resistance to environmental factors, making it a strong candidate for outdoor use.
Considerations for International Buyers: Buyers should evaluate the availability of TPE in their region and consider the cost implications. Compliance with international standards is essential, particularly in Europe, where regulations can be stringent.
What Role Does Steel Play in Cable Reeling Systems?
Key Properties: Steel is known for its high tensile strength and durability. It is resistant to various mechanical stresses and can withstand extreme environmental conditions.
Pros & Cons: The primary advantage of steel is its strength and long lifespan. However, it is heavier and more expensive than other materials and can be prone to corrosion if not properly treated.
Impact on Application: Steel is often used in the construction of cable reels and supports for heavy-duty applications, such as cranes and industrial machinery.
Considerations for International Buyers: Buyers must ensure that steel components meet local standards for safety and performance. Corrosion resistance treatments may be necessary in humid or coastal environments, which is particularly relevant for buyers in regions like the Middle East.
Summary Table of Material Selection for Cable Reeling
Material | Typical Use Case for Cable Reeling | Key Advantage | Key Disadvantage/Limitation | Relative Cost (Low/Med/High) |
---|---|---|---|---|
PVC | Indoor electrical applications | Cost-effective and easy to manufacture | Limited high-temperature performance | Low |
Rubber | Outdoor and industrial applications | Excellent flexibility and durability | Higher manufacturing costs | High |
Thermoplastic Elastomers | Flexible outdoor applications | High temperature and UV resistance | More expensive and less available | Medium |
Steel | Heavy-duty cable reels and supports | High tensile strength and durability | Heavier and prone to corrosion | High |
This guide provides a comprehensive overview of materials used in cable reeling applications, offering actionable insights for international B2B buyers. By understanding the properties and implications of each material, buyers can make informed decisions that align with their specific needs and compliance requirements.
In-depth Look: Manufacturing Processes and Quality Assurance for cable reeling
What Are the Main Stages in the Manufacturing Process of Cable Reeling?
Manufacturing cable reeling products involves several critical stages that ensure the final product meets rigorous performance and safety standards. Understanding these stages is essential for B2B buyers, particularly those in regions like Africa, South America, the Middle East, and Europe, where operational conditions may vary significantly.
1. Material Preparation
The first step in manufacturing cable reels involves selecting and preparing materials. High-quality raw materials such as copper, aluminum, and specialized polymers are typically sourced. Buyers should verify the origin of these materials, as they can significantly impact performance. For instance, using copper with high conductivity can enhance the efficiency of power transmission.
The preparation phase also includes cutting materials to precise lengths and treating them to resist environmental factors like corrosion and abrasion. This is particularly crucial for cables intended for heavy-duty applications, where resilience against mechanical stress is vital.
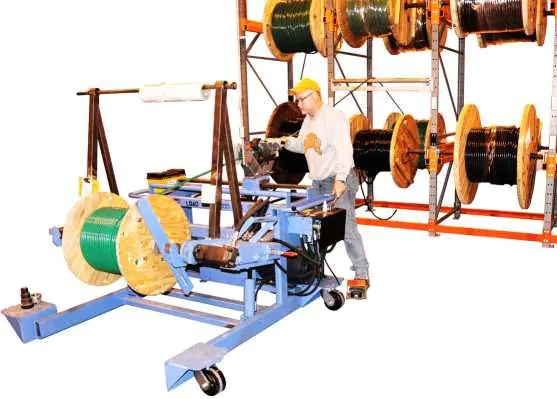
A stock image related to cable reeling.
2. Forming Techniques: How Are Cable Reels Shaped?
Once materials are prepared, the forming stage begins. This typically involves processes such as extrusion, molding, and stamping.
- Extrusion is commonly used for creating the insulation and outer jackets of cables. Here, heated materials are forced through a die to achieve desired shapes.
- Molding can be employed for creating components of the cable reels themselves, ensuring they can withstand the rigors of tension and flexing during operation.
- Stamping is often used for the metal parts of the reels, ensuring they are robust enough to handle heavy loads without deformation.
Buyers should inquire about the specific forming techniques used by manufacturers, as these can impact the durability and functionality of the final product.
3. Assembly: How Are Components Brought Together?
The assembly stage combines all the manufactured components into a cohesive unit. This includes attaching the cable to the reel, securing connectors, and integrating any necessary electronic components.
During assembly, manufacturers may employ automated systems to enhance precision and efficiency. However, manual assembly is also common, particularly for complex configurations that require a high degree of craftsmanship.
Quality assurance at this stage is crucial. Buyers should look for suppliers who implement strict assembly protocols to minimize errors and ensure that all components function seamlessly together.
4. Finishing: What Final Touches Ensure Quality?
The finishing stage includes processes such as surface treatment, painting, and quality checks. Surface treatments often involve applying coatings that enhance durability, such as galvanization or powder coating, which can protect against environmental factors.
This stage also involves the application of branding and labeling, which can be important for compliance with international standards. B2B buyers should ensure that the finishing processes align with their branding and quality requirements.
What Quality Assurance Standards Are Relevant for Cable Reeling?
Quality assurance in cable reeling manufacturing is critical to ensure safety, reliability, and compliance with international standards. Here are the key standards and checkpoints that buyers should consider:
1. International Standards: What Should Buyers Look For?
ISO 9001 is one of the most recognized international standards for quality management systems. It ensures that manufacturers consistently provide products that meet customer and regulatory requirements. Buyers should verify whether potential suppliers are certified to ISO 9001, as this indicates a commitment to quality.
Additionally, industry-specific standards such as CE marking (for European markets) and API (American Petroleum Institute) standards for oil and gas applications can be relevant. Ensuring compliance with these standards is crucial for operational safety and regulatory adherence.
2. What Are the Key Quality Control Checkpoints?
Quality control is typically structured around several checkpoints throughout the manufacturing process:
-
Incoming Quality Control (IQC): This checkpoint assesses the quality of raw materials before they are used in production. It helps identify any material defects early in the process.
-
In-Process Quality Control (IPQC): During manufacturing, IPQC ensures that the processes are followed correctly, and any deviations are addressed immediately. This may involve regular inspections and measurements.
-
Final Quality Control (FQC): At the end of the manufacturing process, FQC involves comprehensive testing of the final products to ensure they meet all specifications and standards.
B2B buyers should ask suppliers about their quality control protocols and how they document these processes.
How Can B2B Buyers Verify Supplier Quality Control?
Verifying a supplier’s quality control measures is essential for B2B buyers, especially when dealing with international suppliers. Here are some actionable steps:
1. Conduct Supplier Audits: What Should Be Included?
Audits can provide deep insights into a supplier’s manufacturing processes and quality control systems. Buyers should develop a checklist that includes:
- Review of certifications (ISO, CE, etc.)
- Examination of quality control documentation
- Interviews with quality assurance personnel
- Observations of the manufacturing floor and processes
2. Request Quality Control Reports: What Information Should They Contain?
Buyers should request detailed quality control reports that outline the results of IQC, IPQC, and FQC. These reports should include information on:
- Testing methods used (e.g., tensile strength, thermal resistance)
- Failure rates and corrective actions taken
- Compliance with relevant standards
3. Engage Third-Party Inspectors: Why Is This Important?
Employing third-party inspection services can provide an unbiased assessment of a supplier’s quality control processes. These inspectors can conduct thorough evaluations and provide reports that help mitigate risks associated with international sourcing.
What Are the Quality Control Nuances for International B2B Buyers?
For international B2B buyers, particularly from regions like Africa and South America, understanding local manufacturing practices and international standards is vital. Buyers should consider:
- Cultural Differences: Different regions may have varying approaches to quality control. Understanding these nuances can help in negotiations and setting expectations.
- Logistics and Supply Chain Risks: Ensure that suppliers have robust logistics and supply chain management systems to minimize disruptions and maintain quality standards.
- Regulatory Compliance: Be aware of local regulations that may affect quality assurance processes and product specifications.
In summary, a thorough understanding of the manufacturing processes and quality assurance measures for cable reeling is crucial for B2B buyers. By focusing on these areas, buyers can make informed decisions that align with their operational needs and quality standards.
Practical Sourcing Guide: A Step-by-Step Checklist for ‘cable reeling’
The purpose of this practical sourcing guide is to assist B2B buyers in efficiently procuring cable reeling solutions that meet their operational needs. By following this checklist, buyers can ensure they are making informed decisions, selecting reliable suppliers, and acquiring products that align with their technical specifications.
Step 1: Define Your Technical Specifications
Understanding your specific needs is crucial before engaging with suppliers. Identify the type of cable reeling required based on your operational context—consider factors such as load capacity, environmental conditions, and application type (e.g., cranes, hoists, or agricultural equipment).
– Key Considerations:
– Mechanical load requirements
– Environmental resistance (temperature, moisture, chemicals)
Step 2: Research Potential Suppliers
Explore various suppliers specializing in cable reeling products. Look for companies with a proven track record in your industry and region, as local expertise can significantly influence product suitability and service efficiency.
– What to Look For:
– Established reputation and industry experience
– Availability of product variations tailored to your needs
Step 3: Evaluate Product Quality and Compliance
Quality assurance is paramount in cable reeling solutions. Request certifications that demonstrate compliance with international standards, such as ISO or IEC, to ensure safety and reliability.
– Focus Areas:
– Material durability and resistance to wear
– Flexibility and lifespan under operational stress
Step 4: Request Samples or Prototypes
Before finalizing a purchase, obtain samples or prototypes of the cable reeling products. This allows you to assess performance in real-world conditions and determine compatibility with your existing systems.
– Benefits of Testing:
– Validation of technical claims made by the supplier
– Identification of any potential issues before bulk ordering
Step 5: Verify Supplier Certifications
Confirm that your chosen supplier holds the necessary certifications and industry accreditations. This step helps mitigate risks related to quality and compliance, ensuring that you partner with a reputable vendor.
– Important Certifications:
– Quality management systems (e.g., ISO 9001)
– Specific industry certifications relevant to your sector
Step 6: Negotiate Terms and Conditions
Once you have identified a suitable supplier, engage in negotiations regarding pricing, delivery timelines, and warranty terms. Clear agreements will help prevent misunderstandings and ensure that both parties have aligned expectations.
– Considerations:
– Payment terms and conditions
– After-sales support and maintenance agreements
Step 7: Plan for After-Sales Support and Maintenance
Ensure your supplier offers robust after-sales support, including maintenance services and readily available spare parts. This is crucial for minimizing downtime and extending the lifespan of your cable reeling systems.
– What to Confirm:
– Availability of technical support and training
– Long-term partnership opportunities for future needs
By following this step-by-step checklist, international B2B buyers can streamline the procurement process for cable reeling solutions, ensuring they select products that are reliable, compliant, and tailored to their specific operational requirements.
Comprehensive Cost and Pricing Analysis for cable reeling Sourcing
What Are the Key Cost Components in Cable Reeling Sourcing?
Understanding the cost structure of cable reeling is essential for B2B buyers to make informed purchasing decisions. The primary components of cost include:
-
Materials: The choice of materials significantly impacts the overall cost. High-quality compounds and conductors, such as copper or specialized polymers for insulation, can increase upfront costs but enhance durability and performance, especially under extreme conditions.
-
Labor: Labor costs encompass the wages paid to skilled workers involved in manufacturing, assembly, and quality control. In regions with higher labor costs, such as Europe, the final price may reflect these expenses more significantly than in lower-cost regions like parts of Africa or South America.
-
Manufacturing Overhead: This includes expenses related to factory operations, such as utilities, equipment maintenance, and facility costs. Efficient manufacturing processes can mitigate these overheads, affecting overall pricing.
-
Tooling: Custom tooling for specialized cable designs or sizes can lead to higher initial costs. However, these costs may be amortized over larger production runs, making it economically viable for bulk orders.
-
Quality Control (QC): Implementing strict QC measures ensures that the products meet safety and performance standards, which may increase costs but ultimately provides long-term savings by reducing failure rates and warranty claims.
-
Logistics: Shipping, handling, and storage costs can vary significantly based on geographic location and supplier. For international buyers, understanding Incoterms is crucial to estimate these costs accurately.
-
Margin: Supplier margins can vary based on market conditions, competition, and the perceived value of the product. Higher margins may be justified by superior quality or added services.
How Do Price Influencers Affect Cable Reeling Costs?
Various factors can influence pricing and should be considered by international buyers:
-
Volume and Minimum Order Quantity (MOQ): Larger orders often qualify for volume discounts, significantly lowering the unit price. Buyers should negotiate MOQs that balance their needs with supplier capabilities.
-
Specifications and Customization: Custom cables tailored to specific applications typically incur higher costs due to specialized materials and manufacturing processes. Buyers must weigh the benefits of customization against cost implications.
-
Materials and Quality Certifications: The type of materials used and certifications (such as UL or CE) can significantly affect pricing. High-quality materials may incur higher costs but provide added assurance of performance and reliability.
-
Supplier Factors: The supplier’s reputation, reliability, and geographic location can influence pricing. Established suppliers may charge a premium for their brand, but their reliability can also reduce risks for buyers.
-
Incoterms: Understanding the terms of shipment is essential for cost calculations. Terms like CIF (Cost, Insurance, and Freight) or FOB (Free on Board) dictate who is responsible for shipping costs and risks at different stages, impacting the total landed cost.
What Buyer Tips Can Enhance Cost-Efficiency in Cable Reeling Sourcing?
For international B2B buyers, particularly from Africa, South America, the Middle East, and Europe, several strategies can optimize costs:
-
Negotiation: Engage suppliers in discussions about pricing, especially for bulk orders. Highlighting potential long-term relationships can lead to favorable terms.
-
Total Cost of Ownership (TCO): Evaluate not just the purchase price but also factors like maintenance, durability, and potential downtime costs. Investing in higher-quality cables may yield savings over time.
-
Research and Compare Suppliers: Conduct thorough research on multiple suppliers to compare pricing structures, quality, and service levels. Utilize online marketplaces and industry contacts to gather insights.
-
Leverage Local Partnerships: For buyers in regions like Africa and South America, collaborating with local distributors or manufacturers can reduce logistics costs and lead times.
-
Stay Informed About Market Trends: Keep abreast of shifts in material costs, labor rates, and international trade policies that could affect pricing. This knowledge can help in planning purchases and negotiations.
Disclaimer on Indicative Prices
It is important to note that prices for cable reeling can vary widely based on market conditions, specific requirements, and supplier negotiations. Always request quotes directly from suppliers to obtain accurate and current pricing tailored to your specific needs.
Alternatives Analysis: Comparing cable reeling With Other Solutions
When considering the best solution for managing cables in industrial applications, B2B buyers must evaluate various options. Cable reeling is a popular choice due to its reliability and efficiency, but there are viable alternatives that may better suit specific needs. This section provides a comparative analysis of cable reeling against other methods, helping international buyers make informed decisions.
Comparison Aspect | Cable Reeling | Pneumatic Cable Management Systems | Fixed Cable Trays |
---|---|---|---|
Performance | High flexibility and durability; suitable for dynamic applications. | Excellent for heavy-duty environments; can handle high loads. | Reliable for static installations; limited mobility. |
Cost | Moderate initial investment with low maintenance costs. | Higher upfront costs; often requires professional installation. | Lower upfront costs but may incur higher maintenance over time. |
Ease of Implementation | Relatively easy to install; requires minimal space. | Complex installation; requires specialized knowledge. | Simple installation; adaptable to various layouts. |
Maintenance | Low maintenance; periodic checks recommended. | Moderate maintenance; requires regular air supply checks. | Low maintenance; periodic inspections needed. |
Best Use Case | Ideal for mobile applications in cranes or construction sites. | Best for environments with heavy machinery and high cable loads. | Suited for permanent installations in warehouses or manufacturing facilities. |
What Are the Advantages and Disadvantages of Pneumatic Cable Management Systems?
Pneumatic cable management systems utilize air pressure to operate and manage cables. They are particularly effective in environments that experience high mechanical loads, such as manufacturing and heavy machinery operations. The advantages include the ability to handle substantial weights and the elimination of manual handling, which enhances safety. However, the higher initial investment and the complexity of installation can be drawbacks, especially for businesses with limited budgets or those that lack specialized installation teams.
How Do Fixed Cable Trays Compare to Cable Reeling Systems?
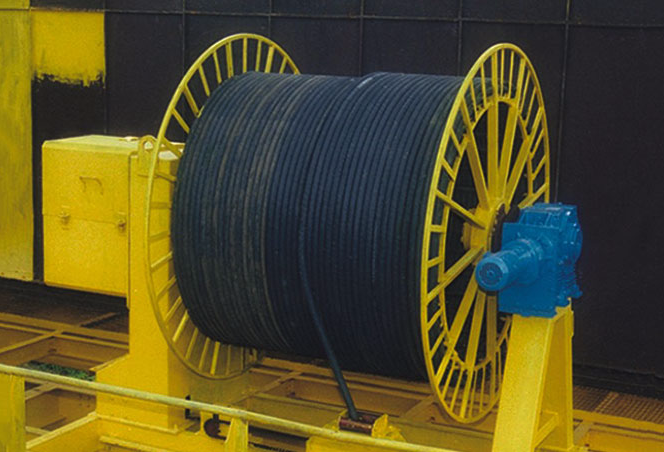
A stock image related to cable reeling.
Fixed cable trays provide a structured method for routing cables in a permanent manner. They are cost-effective for installations where mobility is not a priority. The main advantage of cable trays is their adaptability to various layouts and ease of installation, making them a popular choice for many industrial settings. However, they lack the flexibility that cable reeling offers, especially in dynamic environments where cables need to be frequently adjusted or retracted. Maintenance can be more frequent with cable trays due to dust accumulation and wear over time.
Conclusion: How Can B2B Buyers Choose the Right Cable Management Solution?
Selecting the right cable management solution depends on the specific needs of the operation. For dynamic environments where cables are frequently moved, cable reeling is often the most effective choice. Conversely, for fixed installations, cable trays may provide a more economical and straightforward solution. Pneumatic systems are ideal for heavy-duty applications but require careful consideration of the initial investment and installation complexity. B2B buyers should assess their operational requirements, budget constraints, and long-term maintenance capabilities to determine the most suitable option for their cable management needs.
Essential Technical Properties and Trade Terminology for cable reeling
What Are the Key Technical Properties of Cable Reeling?
Understanding the technical specifications of cable reeling is essential for international B2B buyers looking to optimize their operations. Here are several critical properties to consider:
1. Material Grade
The material used in cable reeling significantly impacts durability and performance. Common materials include rubber, thermoplastics, and polyurethane, each offering varying resistance to environmental factors such as oil, chemicals, and temperature extremes. For instance, high-quality thermoplastic elastomers can provide enhanced flexibility and resistance to abrasion, making them ideal for heavy-duty applications.
2. Flex Life
Flex life refers to the number of bends a cable can endure before failure. It is crucial for applications involving repetitive movements, such as cranes and hoists. A longer flex life reduces maintenance costs and downtime, thus enhancing operational efficiency. Buyers should evaluate flex life ratings to ensure the chosen cable meets the specific demands of their application.
3. Break Strength
Break strength indicates the maximum load a cable can handle before breaking. This property is particularly important for high-tension applications, where cables are subjected to significant pulling forces. For instance, cables with a break strength of 4,000 pounds or more are suitable for heavy lifting and reeling operations. Understanding this specification helps buyers select cables that can safely support their operational loads.
4. Operating Temperature Range
Cables are often exposed to extreme temperatures, affecting their performance and lifespan. It’s essential to choose cables with an appropriate operating temperature range. For example, high-temperature cables can withstand temperatures up to 200°C (392°F), making them ideal for applications in hot environments. Selecting cables with the right temperature tolerance is vital for maintaining safety and functionality.
5. Shielding Options
Cable shielding, often made from copper (Cu) or aluminum, protects against electromagnetic interference (EMI) and enhances signal integrity. This is particularly relevant in environments with heavy machinery where electrical noise can disrupt operations. Buyers should assess their specific needs regarding shielding to ensure optimal performance of their cable systems.
What Trade Terminology Should International Buyers Understand?
Familiarity with industry jargon is crucial for effective communication and negotiation in the B2B market. Here are some common terms that buyers should know:
1. OEM (Original Equipment Manufacturer)
An OEM refers to a company that produces parts or equipment that may be marketed by another manufacturer. Understanding OEM relationships is essential for buyers looking to source cables that meet specific equipment standards and compatibility.
2. MOQ (Minimum Order Quantity)
MOQ indicates the smallest quantity of a product that a supplier is willing to sell. Knowing the MOQ is vital for buyers to plan their purchases effectively, especially in international trade, where shipping costs and tariffs can impact overall expenses.
3. RFQ (Request for Quotation)
An RFQ is a document sent to suppliers requesting a price quote for specific products. This process allows buyers to compare prices and terms from various suppliers, ensuring they receive competitive offers. Crafting a clear RFQ can lead to better supplier responses and negotiations.
4. Incoterms (International Commercial Terms)
Incoterms are a series of predefined commercial terms published by the International Chamber of Commerce (ICC) that clarify the responsibilities of buyers and sellers in international transactions. Familiarity with Incoterms like FOB (Free on Board) or CIF (Cost, Insurance, and Freight) is essential for international buyers to understand their obligations regarding shipping and delivery.
5. Lead Time
Lead time refers to the time taken from placing an order to its delivery. Understanding lead times helps buyers plan their inventory and production schedules effectively. In industries where timing is critical, knowing the lead time can prevent costly delays in project execution.
By grasping these technical properties and trade terminologies, international B2B buyers can make informed decisions, ensuring their cable reeling applications are both efficient and cost-effective.
Navigating Market Dynamics and Sourcing Trends in the cable reeling Sector
What Are the Key Market Trends in the Cable Reeling Sector?
The global cable reeling market is experiencing significant growth, driven by advancements in technology and increasing demand across various industries, including construction, manufacturing, and entertainment. Key trends include the rising adoption of automation and smart technologies in cable management systems, which enhance efficiency and reduce operational costs. Additionally, the expansion of renewable energy projects, particularly in Africa and South America, is leading to a surge in demand for high-quality reeling cables capable of withstanding harsh environmental conditions. International B2B buyers should pay close attention to suppliers that offer customized solutions tailored to specific applications, as this trend is becoming increasingly relevant in meeting diverse regional requirements.
Emerging technologies such as IoT (Internet of Things) integration in cable reeling systems are also gaining traction. These innovations enable real-time monitoring and predictive maintenance, thereby minimizing downtime. As the market becomes more competitive, buyers from regions like the Middle East and Europe are encouraged to evaluate suppliers not only based on price but also on the technological sophistication of their products. Understanding these dynamics will empower B2B buyers to make informed sourcing decisions that align with their operational needs and long-term strategic goals.
How Does Sustainability Impact Sourcing in the Cable Reeling Industry?
The importance of sustainability in the cable reeling sector cannot be overstated. With growing awareness about environmental impacts, B2B buyers are increasingly prioritizing suppliers who demonstrate a commitment to sustainable practices. This encompasses the use of eco-friendly materials, reduced carbon footprints, and ethical sourcing of raw materials. Buyers from Africa, South America, and the Middle East should consider suppliers with certifications such as ISO 14001, which indicates effective environmental management systems.
Moreover, the trend toward using recyclable and biodegradable materials in cable manufacturing is gaining momentum. Manufacturers are responding to this demand by developing cables that not only meet performance standards but also minimize environmental impact. When sourcing cable reeling solutions, international buyers should inquire about the sustainability practices of potential suppliers, including their waste management strategies and energy consumption during production. This commitment to sustainability not only enhances brand reputation but also meets the growing consumer demand for responsible sourcing.
What Is the Historical Context of Cable Reeling Technology?
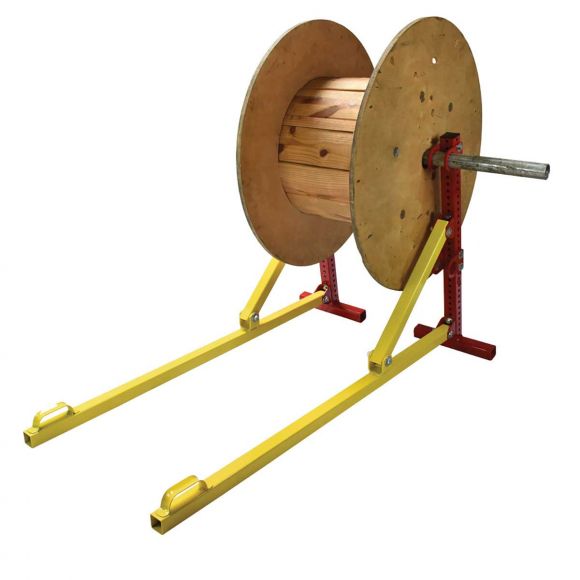
A stock image related to cable reeling.
The evolution of cable reeling technology can be traced back to the early 20th century when the need for efficient cable management became apparent with the rise of electrical engineering and construction. Initially, cable reels were primarily manual, but as industries evolved, so did the technology. The introduction of motorized and automated cable reels in the latter half of the century significantly improved operational efficiency, allowing for quicker deployment and retraction of cables.
In recent years, the focus has shifted towards customization and durability, with manufacturers developing specialized cables that can withstand extreme conditions and heavy mechanical loads. This historical context highlights the sector’s ongoing innovation and adaptability, which is crucial for B2B buyers seeking reliable and advanced cable reeling solutions in today’s market. Understanding this evolution not only provides insight into current product offerings but also helps buyers anticipate future trends and technologies in the cable reeling industry.
Frequently Asked Questions (FAQs) for B2B Buyers of cable reeling
-
How do I solve cable reeling issues caused by abrasion and environmental factors?
To address abrasion and environmental challenges in cable reeling, choose cables designed with high-quality compounds that resist wear and tear. Look for options with features like oil and chemical resistance, high-temperature tolerance, and reinforced structures. Suppliers often provide customization options to fit specific operational conditions, so engage with manufacturers to ensure the selected cable meets the demands of your environment, such as extreme temperatures or exposure to hazardous materials. -
What is the best cable reeling solution for heavy-duty applications?
For heavy-duty applications, such as cranes or mining operations, consider using aramid-reinforced cables. These cables offer higher break strength and durability under tension, making them suitable for extreme mechanical loads. Multi-conductor cables like Super-Trex® are designed specifically for payout and retractile applications, providing flexibility and longevity. Always consult with suppliers about load specifications and environmental conditions to determine the best fit for your needs. -
How can I verify the reliability of a cable reeling supplier?
To verify the reliability of a cable reeling supplier, conduct thorough research by reviewing their industry reputation, certifications, and customer testimonials. Check if they have experience in your specific application area, such as industrial or agricultural use. Request samples of their products and inquire about their quality assurance processes. It’s also beneficial to assess their responsiveness and willingness to provide customized solutions, as this indicates a commitment to customer satisfaction. -
What are the minimum order quantities (MOQs) for cable reeling products?
Minimum order quantities (MOQs) for cable reeling products can vary significantly by supplier and product type. While some manufacturers may accept low MOQs for standard items, custom solutions often require larger orders. It’s advisable to directly communicate with potential suppliers to understand their MOQ policies. This helps in planning your procurement strategy, especially if you are looking to balance inventory costs with your operational needs. -
What payment terms should I expect when sourcing cable reeling products internationally?
Payment terms for international purchases can differ widely based on supplier policies and the nature of the transaction. Common practices include upfront payment, partial payment upon order confirmation, and the balance upon delivery. Letters of credit (LCs) are also a popular option to secure transactions. Always negotiate terms that align with your financial capabilities and consider using escrow services for large orders to mitigate risks. -
How can I ensure quality assurance in my cable reeling purchases?
To ensure quality assurance in your cable reeling purchases, request detailed product specifications, certifications, and test results from suppliers. Many reputable manufacturers will provide documentation outlining their quality control processes. Additionally, consider implementing a third-party inspection service to evaluate the products before shipment, especially for bulk orders. Establishing a clear communication channel with the supplier about quality expectations is crucial for long-term partnership success. -
What logistics considerations should I keep in mind for international shipping of cable reeling products?
When planning for international shipping of cable reeling products, consider factors such as shipping routes, customs regulations, and import duties. Work with logistics providers experienced in handling industrial equipment to ensure compliance and minimize delays. Additionally, factor in lead times for production and shipping when placing orders. Choosing a reliable freight forwarder can also help streamline the process and manage documentation efficiently. -
What customization options are available for cable reeling products?
Most manufacturers offer customization options for cable reeling products to meet specific operational needs. This can include variations in cable length, conductor size, shielding types, and insulation materials. Some suppliers may also provide tailored solutions for unique applications, such as high-temperature environments or specialized machinery. Engaging in a detailed discussion with the supplier about your requirements will help in designing a product that perfectly fits your operational context.
Important Disclaimer & Terms of Use
⚠️ Important Disclaimer
The information provided in this guide, including content regarding manufacturers, technical specifications, and market analysis, is for informational and educational purposes only. It does not constitute professional procurement advice, financial advice, or legal advice.
While we have made every effort to ensure the accuracy and timeliness of the information, we are not responsible for any errors, omissions, or outdated information. Market conditions, company details, and technical standards are subject to change.
B2B buyers must conduct their own independent and thorough due diligence before making any purchasing decisions. This includes contacting suppliers directly, verifying certifications, requesting samples, and seeking professional consultation. The risk of relying on any information in this guide is borne solely by the reader.
Strategic Sourcing Conclusion and Outlook for cable reeling
In the evolving landscape of cable reeling solutions, strategic sourcing remains pivotal for international B2B buyers, especially from regions like Africa, South America, the Middle East, and Europe. By prioritizing high-quality, durable reeling cables designed to withstand extreme conditions, buyers can enhance operational efficiency and reduce long-term costs. Key considerations include selecting cables that resist abrasion, flexing, and environmental stresses, as well as ensuring compatibility with specific applications such as cranes, hoists, and agricultural equipment.
Investing in reliable reeling solutions not only boosts productivity but also safeguards against costly downtimes. Collaborating with reputable manufacturers who offer customized solutions can further optimize performance to meet unique operational needs.
As we look to the future, the demand for advanced cable reeling technologies is expected to grow, driven by increased industrialization and infrastructure projects globally. B2B buyers are encouraged to stay ahead of trends and innovations in cable technology. Engage with industry experts and suppliers to explore tailored solutions that align with your business objectives. The right strategic sourcing approach can empower your operations, ensuring you remain competitive in a dynamic marketplace.