Optimize Efficiency: The Complete V Belt Drive Guide (2025)
Introduction: Navigating the Global Market for v belt drive
Navigating the global market for V belt drives poses unique challenges for international B2B buyers, especially those operating in diverse regions like Africa, South America, the Middle East, and Europe. Sourcing reliable V belt drives that meet specific operational demands while ensuring cost-effectiveness can be daunting. This guide is designed to demystify the complexities of V belt drive sourcing, offering a thorough exploration of various types, applications, and best practices in supplier vetting.
Throughout this guide, you will discover detailed insights into the different categories of V belts, including automotive, industrial, and specialty belts, along with their respective applications. You’ll learn how to assess suppliers for quality assurance, understand pricing structures, and evaluate the total cost of ownership to make informed purchasing decisions. Additionally, the guide addresses region-specific considerations, including compliance with local standards and logistical challenges that may affect procurement.
By leveraging this comprehensive resource, B2B buyers will gain the knowledge needed to navigate the intricacies of the V belt drive market confidently. Whether you are based in the UAE, Argentina, or elsewhere, this guide will empower you to make strategic decisions that enhance operational efficiency and drive business success.
Understanding v belt drive Types and Variations
Type Name | Key Distinguishing Features | Primary B2B Applications | Brief Pros & Cons for Buyers |
---|---|---|---|
Classic V-Belt | Traditional design with a trapezoidal cross-section | General machinery, HVAC systems | Pros: Cost-effective, widely available. Cons: Limited power transmission efficiency. |
Cogged V-Belt | Features notches for increased flexibility | Agricultural equipment, automotive engines | Pros: Better grip, reduced slippage. Cons: Higher cost compared to classic belts. |
Banded V-Belt | Multiple belts joined together for increased strength | Heavy-duty machinery, conveyor systems | Pros: Handles higher loads, reduces vibration. Cons: Bulkier, may require special pulleys. |
Wedge V-Belt | Wider and narrower profile for high-load applications | Industrial machinery, pumps | Pros: Enhanced power transmission, durable. Cons: Requires precise alignment. |
Metric V-Belt | Designed to meet international sizing standards | European machinery, automotive applications | Pros: Compatible with global equipment, precise fit. Cons: Limited availability in some regions. |
What are the Characteristics of Classic V-Belts?
Classic V-belts are the most common type of belt drive used in various machinery. They have a trapezoidal cross-section, which allows them to fit snugly into the grooves of pulleys, ensuring effective power transmission. These belts are widely used in HVAC systems and general industrial applications due to their cost-effectiveness and availability. However, they may not be the best choice for high-efficiency applications, as their power transmission capabilities are limited compared to other variations.
Why Choose Cogged V-Belts for Your Applications?
Cogged V-belts feature notches along their length, which enhance their flexibility and grip. This design allows them to bend around pulleys more easily, making them ideal for applications requiring high performance, such as agricultural machinery and automotive engines. While they offer superior grip and reduced slippage, buyers should consider their higher cost compared to classic V-belts. This investment may be justified by the increased efficiency and longevity in demanding applications.
What are the Advantages of Banded V-Belts?
Banded V-belts consist of multiple individual belts that are joined together, providing increased strength and stability. They are particularly suited for heavy-duty machinery and conveyor systems where high load capacity and vibration reduction are critical. The primary advantage of banded V-belts is their ability to handle larger loads without slipping. However, their bulkier design may necessitate specialized pulleys, which could increase overall system costs.
When to Use Wedge V-Belts in Your Operations?
Wedge V-belts have a narrower profile that allows them to transmit more power than standard V-belts. They are commonly used in industrial machinery and pumps where high-load applications are prevalent. The benefits of using wedge V-belts include enhanced durability and power transmission capabilities. However, precise alignment is crucial; misalignment can lead to premature wear and failure, which buyers should factor into their purchasing decisions.
How Do Metric V-Belts Fit into International Sourcing?
Metric V-belts are designed according to international sizing standards, making them essential for equipment manufactured in Europe and other regions. Their standardized sizing ensures compatibility with a wide range of machinery, making them a reliable choice for international B2B buyers. While they provide a precise fit and are often preferred for their compatibility with global equipment, availability may be limited in certain markets, requiring buyers to plan their sourcing strategies accordingly.
Key Industrial Applications of v belt drive
Industry/Sector | Specific Application of V Belt Drive | Value/Benefit for the Business | Key Sourcing Considerations for this Application |
---|---|---|---|
Manufacturing | Power transmission in conveyor systems | Enhanced efficiency in material handling | Quality, durability, and compatibility with existing systems |
Agriculture | Drive systems for agricultural machinery | Increased productivity and reduced downtime | Resistance to environmental factors and wear |
Automotive | Engine power transmission in vehicles | Reliable performance and maintenance savings | OEM specifications and quality certifications |
Mining | Equipment drive systems for extraction processes | Improved operational efficiency and safety | Load capacity, heat resistance, and supplier reliability |
Food Processing | Conveyor systems for food handling | Compliance with hygiene standards and efficiency | Food-grade materials and ease of cleaning |
How is V Belt Drive Used in Manufacturing?
In the manufacturing sector, v belt drives are integral to power transmission in conveyor systems. These systems facilitate the efficient movement of materials, reducing manual handling and increasing throughput. V belts provide reliable operation, minimizing downtime due to maintenance. For international B2B buyers, especially in regions like Africa and South America, sourcing high-quality v belts that can withstand local environmental conditions, such as humidity and dust, is crucial to ensure consistent performance.
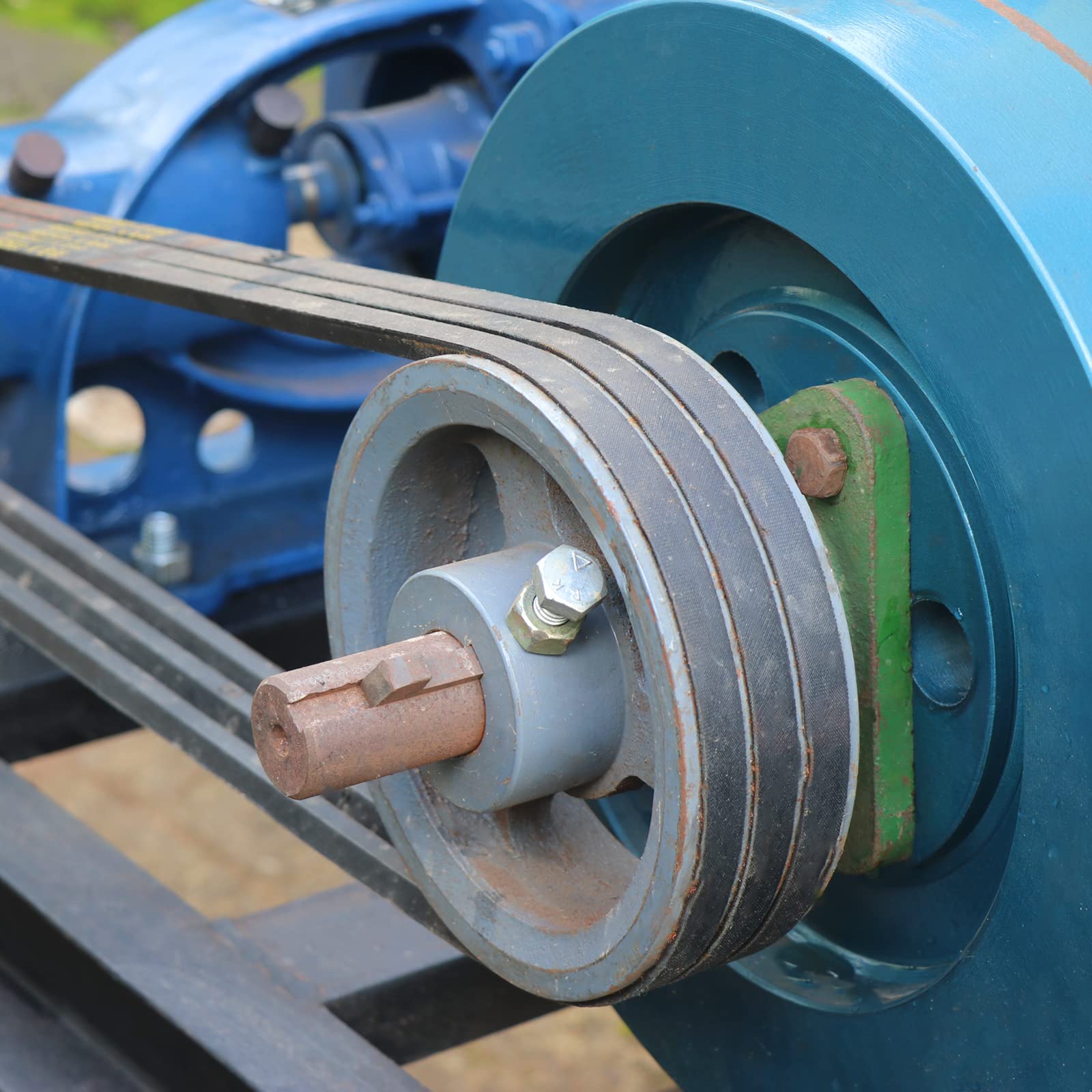
A stock image related to v belt drive.
What Role Does V Belt Drive Play in Agriculture?
V belt drives are widely used in agricultural machinery, such as tractors and harvesters, to transmit power from the engine to various components like augers and plows. This application enhances productivity by ensuring that machinery operates smoothly and efficiently, which is vital during critical harvest periods. Buyers from the Middle East and Europe should consider v belts that offer resistance to wear and environmental factors, such as UV exposure and extreme temperatures, to maximize the lifespan of their equipment.
How is V Belt Drive Essential in Automotive Applications?
In the automotive industry, v belt drives are crucial for engine power transmission, connecting components like alternators, water pumps, and air conditioning units. This application ensures that vehicles operate efficiently while reducing fuel consumption. For B2B buyers in Europe, sourcing v belts that meet OEM specifications is essential for maintaining vehicle performance and ensuring compliance with regulatory standards. Quality certifications and durability are key factors in the purchasing decision.
How Does V Belt Drive Benefit the Mining Sector?
In mining, v belt drives are used in equipment such as crushers and conveyors to facilitate the extraction and transportation of minerals. This application improves operational efficiency and safety by providing reliable power transmission even in harsh environments. Buyers from South America and Africa should prioritize sourcing v belts with high load capacity and heat resistance to withstand the demanding conditions typical of mining operations.
What is the Importance of V Belt Drive in Food Processing?
In the food processing industry, v belt drives are employed in conveyor systems to handle food products efficiently while adhering to strict hygiene standards. This application is crucial for maintaining product quality and operational efficiency. For international B2B buyers, especially in regions like the UAE, sourcing v belts made from food-grade materials that are easy to clean and resistant to contamination is essential for compliance with food safety regulations.
3 Common User Pain Points for ‘v belt drive’ & Their Solutions
Scenario 1: Frequent V-Belt Breakdowns
The Problem:
Many B2B buyers in industries ranging from manufacturing to agriculture experience frequent breakdowns of v-belt drives. This often leads to unexpected downtime, resulting in lost productivity and increased operational costs. Factors such as improper installation, misalignment of pulleys, or the use of low-quality belts can exacerbate these issues. Buyers may feel frustrated as they invest in what they believe are high-quality belts only to face repeated failures, disrupting their operations and affecting their bottom line.
The Solution:
To mitigate the risk of frequent v-belt breakdowns, it is essential to ensure proper installation and maintenance. Buyers should invest in comprehensive training for their maintenance teams on the correct installation procedures, including checking pulley alignment and tension settings. It’s also crucial to select the right type of v-belt for the specific application, considering factors such as load capacity, environmental conditions, and operating speeds.
Additionally, sourcing belts from reputable suppliers who offer quality assurance and warranty can enhance reliability. Regularly scheduled maintenance checks should be implemented to identify potential issues before they lead to failure. This proactive approach not only extends the lifespan of the v-belts but also significantly reduces the risk of unexpected breakdowns.
Scenario 2: Incompatibility with Existing Equipment
The Problem:
Another common pain point for B2B buyers is the incompatibility of new v-belt drives with existing equipment. This is particularly prevalent in industries that have older machinery or have made incremental upgrades over the years. Buyers may find that standard v-belt sizes do not fit their equipment or that the new belts do not perform adequately due to mismatched specifications, leading to inefficiencies and additional costs.
The Solution:
To address compatibility issues, buyers should conduct a thorough assessment of their existing equipment before sourcing new v-belt drives. This involves measuring the dimensions of the pulleys and checking the manufacturer’s specifications for the equipment. By consulting with suppliers who offer a wide range of v-belt options, including custom sizes and configurations, buyers can ensure they find the right fit.
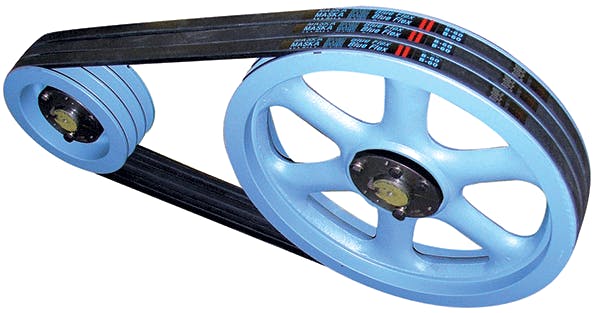
A stock image related to v belt drive.
Moreover, leveraging technology such as CAD software can aid in visualizing the fitment of different belt options with existing machinery. Suppliers should also provide detailed product specifications, including material properties and performance ratings, to help buyers make informed decisions. Establishing a collaborative relationship with suppliers can facilitate better recommendations and help identify suitable alternatives that enhance compatibility and performance.
Scenario 3: Lack of Knowledge on V-Belt Types and Applications
The Problem:
Many international B2B buyers, especially those new to the industry or operating in less technologically advanced regions, struggle with the diverse range of v-belt types and their specific applications. This knowledge gap can lead to the selection of inappropriate belts, resulting in poor performance and premature wear. Buyers may feel overwhelmed by the technical jargon and specifications, making it challenging to make informed purchasing decisions.
The Solution:
To combat this lack of knowledge, B2B buyers should invest in educational resources and training programs for their teams. Engaging with suppliers who provide detailed guidance on the various types of v-belts—such as banded, cogged, and double-angle belts—and their specific applications can empower buyers to make better choices.
Additionally, creating a decision matrix that outlines the operational requirements, including load, speed, and environmental conditions, can serve as a valuable reference. Online platforms and webinars hosted by manufacturers can also provide insights into best practices and new technologies in v-belt drives. By fostering an environment of continuous learning and collaboration with suppliers, buyers can enhance their understanding and improve their overall operational efficiency.
Strategic Material Selection Guide for v belt drive
When selecting materials for V-belt drives, international B2B buyers must consider various properties and performance characteristics that can significantly impact their applications. Below is an analysis of four common materials used in V-belt drives, focusing on their key properties, advantages, disadvantages, and considerations for buyers in diverse global markets.
What Are the Key Properties of Rubber V-Belts?
Rubber is the most common material used for V-belts due to its excellent elasticity and flexibility. Rubber V-belts typically have high temperature and pressure ratings, making them suitable for a wide range of applications. They also exhibit good resistance to wear and tear, which is crucial for longevity.
Pros:
– Durability: Rubber V-belts can withstand significant wear over time.
– Cost-Effectiveness: Generally, rubber belts are less expensive than other materials.
– Versatility: Suitable for various applications, including automotive and industrial machinery.
Cons:
– Temperature Sensitivity: Rubber can degrade at extreme temperatures, limiting its use in high-heat environments.
– Chemical Resistance: Not all rubber formulations are resistant to oils and solvents.
Impact on Application:
Rubber V-belts are widely used in automotive and industrial applications where flexibility and cost are paramount. However, they may not be suitable for applications involving aggressive chemicals.
Considerations for International Buyers:
Buyers in regions like Africa and South America should ensure compliance with local standards (such as ASTM) for rubber materials, especially in automotive applications.
How Do Polyurethane V-Belts Compare in Performance?
Polyurethane (PU) V-belts are increasingly popular due to their superior durability and resistance to abrasion and chemicals. They maintain performance in a wider temperature range compared to rubber.
Pros:
– Chemical Resistance: PU belts are resistant to oils, solvents, and other chemicals.
– Longevity: They offer extended service life due to their robust nature.
Cons:
– Higher Cost: PU belts generally come at a higher price point than rubber alternatives.
– Limited Flexibility: They can be less flexible, which may affect performance in certain applications.
Impact on Application:
These belts are ideal for applications requiring high durability and exposure to harsh chemicals, making them suitable for industries such as food processing and pharmaceuticals.
Considerations for International Buyers:
Buyers in Europe and the Middle East should verify compliance with EU regulations regarding material safety and performance standards.
What Advantages Do Kevlar-Reinforced V-Belts Offer?
Kevlar-reinforced V-belts are designed for high-performance applications where strength and low stretch are critical. Kevlar provides exceptional tensile strength and resistance to wear.
Pros:
– High Strength: Kevlar belts can handle heavy loads without stretching.
– Temperature Stability: They perform well in high-temperature environments.
Cons:
– Cost: Kevlar belts are among the most expensive options available.
– Manufacturing Complexity: The production process can be more complex, leading to longer lead times.
Impact on Application:
These belts are often used in heavy machinery and high-performance automotive applications where reliability and strength are crucial.
Considerations for International Buyers:
Buyers should be aware of the need for specific certifications and compliance with industry standards, particularly in sectors like mining and construction.
Why Choose Metal V-Belts for Certain Applications?
Metal V-belts, often made from steel or other alloys, are used in applications requiring high strength and durability. They are particularly effective in environments where rubber or PU belts may wear out quickly.
Pros:
– Durability: Metal belts can last significantly longer than rubber or PU options.
– High Load Capacity: They can handle heavy loads and extreme conditions.
Cons:
– Weight: Metal belts are heavier, which can affect overall system efficiency.
– Cost: They tend to be more expensive than traditional rubber belts.
Impact on Application:
Metal V-belts are suitable for industrial applications where high strength is necessary, such as in conveyor systems and heavy machinery.
Considerations for International Buyers:
Buyers should ensure compliance with relevant manufacturing standards, such as DIN or JIS, particularly in regions with stringent industrial regulations.
Summary Table of Material Selection for V-Belt Drives
Material | Typical Use Case for V Belt Drive | Key Advantage | Key Disadvantage/Limitation | Relative Cost (Low/Med/High) |
---|---|---|---|---|
Rubber | Automotive, general industrial | Cost-effective and durable | Temperature sensitivity | Low |
Polyurethane (PU) | Food processing, pharmaceuticals | Chemical resistance and longevity | Higher cost | Med |
Kevlar | Heavy machinery, high-performance | High strength and low stretch | Expensive and complex to manufacture | High |
Metal | Industrial conveyor systems | Extremely durable and high load capacity | Heavier and more costly | High |
This strategic material selection guide provides international B2B buyers with essential insights into V-belt materials, helping them make informed decisions based on their specific needs and regional standards.
In-depth Look: Manufacturing Processes and Quality Assurance for v belt drive
What Are the Key Manufacturing Processes for V-Belt Drives?
The manufacturing of V-belt drives involves several critical stages that ensure the product meets the required performance and quality standards. Understanding these processes can help B2B buyers evaluate suppliers and make informed purchasing decisions.
How Is Material Prepared for V-Belt Manufacturing?
Material preparation is the first step in the V-belt manufacturing process. Typically, high-quality rubber compounds, synthetic materials, and reinforcing fibers (such as polyester or aramid) are selected based on the application requirements.
- Material Selection: The choice of materials significantly impacts the durability and performance of the V-belts. For instance, belts intended for heavy-duty applications may require high-tensile strength materials that can withstand extreme stress and temperature variations.
- Compounding: This stage involves mixing raw materials with additives that enhance properties such as wear resistance, heat resistance, and flexibility.
What Are the Key Forming Techniques for V-Belts?
Once the materials are prepared, the next stage involves forming the V-belts into their final shape.
- Extrusion: The rubber compound is extruded into the desired profile. This technique allows for the production of consistent and uniform V-belt shapes.
- Molding: Some manufacturers utilize molding techniques, especially for cogged belts, to create intricate designs that enhance grip and reduce slippage.
- Curing: The formed belts undergo a curing process (vulcanization) to enhance their mechanical properties and ensure they retain their shape under operational stresses.
How Are V-Belts Assembled and Finished?
The assembly and finishing stages are crucial for ensuring that V-belts are ready for the market and can perform reliably.
- Assembly: For banded V-belts, multiple belts may be assembled together using adhesives or mechanical methods to create a single unit that provides enhanced power transmission.
- Finishing: This includes trimming excess material, applying protective coatings, and ensuring that the belts meet specific dimensional tolerances.
What Quality Assurance Standards Are Relevant for V-Belt Production?
Quality assurance is vital in the manufacturing process of V-belts. Several international and industry-specific standards guide the quality control measures that manufacturers must adhere to.
How Does ISO 9001 Impact V-Belt Manufacturing?
ISO 9001 is an internationally recognized standard that outlines the criteria for a quality management system. Compliance with ISO 9001 ensures that manufacturers maintain consistent quality throughout their production processes, from material selection to final inspection.
- Documentation and Procedures: Manufacturers are required to document their processes, maintain records, and implement corrective actions when necessary.
- Continuous Improvement: ISO 9001 promotes a culture of continuous improvement, which can lead to enhanced product quality and customer satisfaction.
What Other Certifications Should B2B Buyers Look For?
In addition to ISO 9001, other certifications relevant to V-belt manufacturing include:
- CE Marking: Indicates conformity with health, safety, and environmental protection standards for products sold within the European Economic Area.
- API Standards: Relevant for V-belts used in the oil and gas industry, ensuring they meet specific performance criteria.
What Are the Key Quality Control Checkpoints in V-Belt Production?
Quality control (QC) checkpoints are essential to ensure that V-belts meet the required specifications. These checkpoints typically include:
- Incoming Quality Control (IQC): Raw materials are inspected upon arrival to ensure they meet specified quality standards.
- In-Process Quality Control (IPQC): During production, random samples are tested to ensure that the manufacturing process is producing belts within the required specifications.
- Final Quality Control (FQC): Finished products undergo a comprehensive inspection that includes dimensional checks, performance testing, and visual inspections for defects.
What Testing Methods Are Commonly Used for V-Belts?
Various testing methods are employed to evaluate the performance and durability of V-belts. These may include:
- Tensile Testing: Measures the strength and elasticity of the belt material.
- Wear Testing: Assesses how well the belt withstands wear under operational conditions.
- Heat Resistance Testing: Evaluates how the belt performs under high-temperature environments.
How Can B2B Buyers Verify Supplier Quality Control Practices?
B2B buyers must ensure that their suppliers adhere to stringent quality control practices. Here are some actionable steps:
- Supplier Audits: Conduct regular audits of suppliers to assess their manufacturing processes and quality control systems. This can include on-site visits and reviews of their documentation.
- Request Quality Reports: Ask suppliers for their quality control reports, which should detail their testing methods and results.
- Third-Party Inspections: Engage independent third-party inspectors to evaluate the quality of the products before shipment.
What Are the Unique QC Considerations for International B2B Buyers?
International B2B buyers, particularly from regions like Africa, South America, the Middle East, and Europe, face unique challenges when it comes to quality control.
- Regulatory Compliance: Ensure that the products comply with local regulations and standards in your region, which may differ significantly from those in the supplier’s country.
- Cultural Differences: Be aware of cultural differences that may affect communication and expectations regarding quality standards.
- Logistical Challenges: Consider the potential logistical issues that may arise during shipping and handling, which can impact product quality upon arrival.
Conclusion
Understanding the manufacturing processes and quality assurance practices for V-belt drives is essential for B2B buyers looking to source reliable products. By focusing on material preparation, forming techniques, and quality control measures, buyers can ensure they partner with suppliers who meet their stringent requirements. Moreover, verifying compliance with international standards and conducting thorough audits will help mitigate risks and enhance the overall supply chain integrity.
Practical Sourcing Guide: A Step-by-Step Checklist for ‘v belt drive’
In today’s competitive landscape, sourcing the right V-belt drive is critical for ensuring operational efficiency and reliability in industrial applications. This guide provides a systematic checklist for international B2B buyers from regions like Africa, South America, the Middle East, and Europe. Follow these steps to make informed procurement decisions.
Step 1: Define Your Technical Specifications
Establishing precise technical specifications is the cornerstone of a successful procurement process. Consider factors such as the type of V-belt required (e.g., banded, bandless, cogged), dimensions, and material composition. Understanding the operational environment—like temperature ranges and load capacities—will help you narrow down the options effectively.
- Identify Application Needs: Determine where the V-belt will be used, such as in conveyor systems or automotive applications.
- Consult Equipment Manuals: Refer to machinery manuals to ensure compatibility with existing systems.
Step 2: Conduct Market Research for Suppliers
Investing time in market research can yield a list of credible suppliers who specialize in V-belt drives. Look for companies with a solid track record and positive reviews from other B2B buyers in your industry.
- Utilize Online Directories: Platforms like IQS Directory and trade shows can provide insights into reputable manufacturers and distributors.
- Check Industry Forums: Engage with industry forums and networks to gather recommendations and feedback on suppliers.
Step 3: Evaluate Potential Suppliers
Before making a commitment, thoroughly vet potential suppliers. This includes analyzing their production capabilities, quality control measures, and customer service track record.
- Request Company Profiles: Ask for detailed information about the supplier’s history, product range, and production processes.
- Seek References: Reach out to existing clients, especially those in similar industries, to gain insights into their experiences.
Step 4: Verify Certifications and Compliance
Ensure that your selected suppliers adhere to international quality standards and certifications. This not only guarantees product quality but also compliance with local regulations.
- Look for ISO Certifications: Suppliers should ideally have ISO 9001 certifications or equivalent, indicating their commitment to quality management.
- Check for Industry-Specific Standards: Depending on your region and industry, certifications like CE or ANSI might be necessary.
Step 5: Request Samples for Testing
Before finalizing your order, request samples of the V-belts you are considering. Testing these samples in real operational conditions will provide valuable insights into their performance and durability.
- Conduct Performance Tests: Evaluate the samples under simulated operational conditions to assess their efficiency and longevity.
- Analyze Fit and Compatibility: Ensure that the samples fit seamlessly with your machinery and meet your specifications.
Step 6: Negotiate Terms and Conditions
Once you have selected a supplier, engage in negotiations to ensure favorable terms that align with your budget and operational needs.
- Discuss Payment Terms: Clarify payment options, including any potential discounts for bulk purchases.
- Address Delivery Timelines: Set clear expectations regarding lead times and delivery schedules to avoid operational disruptions.
Step 7: Establish a Long-Term Relationship
Building a strong relationship with your supplier can lead to better service, favorable pricing, and access to new products in the future.
- Regular Communication: Maintain open lines of communication to discuss performance, feedback, and future needs.
- Consider Partnership Opportunities: Explore collaborative opportunities that can enhance both parties’ operational efficiencies.
By following this checklist, international B2B buyers can streamline their procurement process for V-belt drives, ensuring they select products that meet their technical requirements while building strong supplier relationships.
Comprehensive Cost and Pricing Analysis for v belt drive Sourcing
What Are the Key Cost Components in V-Belt Drive Sourcing?
When sourcing v-belt drives, understanding the cost structure is crucial. The primary cost components include:
-
Materials: The type of material used in v-belts, such as rubber, synthetic composites, or Kevlar, significantly impacts the cost. Higher-quality materials typically result in better performance and longer life but may come at a premium.
-
Labor: The labor costs associated with manufacturing vary by region. Countries with higher labor costs may influence overall pricing, while regions with lower wages might offer more competitive pricing.
-
Manufacturing Overhead: This includes costs related to utilities, facility maintenance, and administrative expenses. Efficient manufacturing processes can help reduce these costs, allowing suppliers to offer more competitive pricing.
-
Tooling: The initial investment in tooling can be substantial, especially for custom v-belt designs. However, this cost can be amortized over larger production runs, making it essential to consider minimum order quantities (MOQs).
-
Quality Control (QC): Ensuring that v-belts meet industry standards requires a robust QC process. This can add to the overall manufacturing cost but is crucial for maintaining product reliability and customer satisfaction.
-
Logistics: Shipping costs, including packaging, handling, and transport, can vary significantly based on the supplier’s location and the buyer’s destination. Incoterms can also influence these costs, determining who bears the risk and cost during transportation.
-
Margin: Supplier margins can vary widely based on competition, brand reputation, and market conditions. Understanding these margins can help buyers negotiate better pricing.
How Do Price Influencers Affect V-Belt Drive Costs?
Several factors influence the pricing of v-belt drives:
-
Volume and Minimum Order Quantities (MOQs): Ordering in bulk typically leads to lower per-unit costs. Suppliers often have tiered pricing models, so negotiating for larger quantities can be beneficial.
-
Specifications and Customization: Custom v-belts tailored to specific machinery or applications can incur additional costs. Buyers should weigh the benefits of customization against potential price increases.
-
Material Quality and Certifications: Higher quality materials and certifications (e.g., ISO standards) may raise costs but can lead to increased efficiency and reduced maintenance, ultimately affecting the total cost of ownership.
-
Supplier Factors: The supplier’s reputation, reliability, and service quality can impact pricing. Established suppliers may command higher prices due to perceived quality and service levels.
-
Incoterms: Understanding the implications of different Incoterms is essential for international buyers. They dictate who is responsible for shipping costs and risks, impacting the total landed cost of the product.
What Tips Can Buyers Use to Negotiate Better Pricing?
International B2B buyers, especially from Africa, South America, the Middle East, and Europe, can use several strategies to optimize their sourcing costs:
-
Negotiate Volume Discounts: Engage suppliers in discussions about bulk purchasing to unlock better pricing. Be prepared to provide forecasts to support your negotiation.
-
Evaluate Total Cost of Ownership (TCO): Instead of focusing solely on the purchase price, consider the long-term costs associated with maintenance, efficiency, and potential downtime. A slightly higher initial cost can lead to savings over the product’s lifespan.
-
Understand Pricing Nuances: Be aware of regional pricing trends and currency fluctuations that can affect costs. This knowledge can provide leverage during negotiations.
-
Build Relationships with Suppliers: Developing strong relationships can lead to better pricing, priority service, and insights into upcoming discounts or new product offerings.
-
Request Multiple Quotes: Always seek quotes from multiple suppliers to compare pricing and terms. This can help identify the best overall deal.
Disclaimer on Indicative Prices
Pricing for v-belt drives can vary significantly based on the factors mentioned above. It is essential for buyers to conduct thorough market research and obtain multiple quotes to ensure they receive the best value for their investment.
Alternatives Analysis: Comparing v belt drive With Other Solutions
When considering power transmission solutions, international B2B buyers must evaluate various options to find the most suitable system for their operations. This analysis compares V-belt drives against two viable alternatives: flat belts and timing belts. Understanding the strengths and weaknesses of each solution can help organizations make informed decisions tailored to their specific operational requirements.
Comparison Aspect | V Belt Drive | Flat Belts | Timing Belts |
---|---|---|---|
Performance | High efficiency, good grip | Moderate efficiency, lower grip | High precision, minimal slippage |
Cost | Moderate initial investment | Generally lower cost | Higher initial cost, lower long-term maintenance |
Ease of Implementation | Relatively easy to install | Simple installation process | Requires precise alignment |
Maintenance | Moderate, regular checks needed | Low maintenance | Low maintenance, but replacement can be complex |
Best Use Case | General-purpose industrial use | Light-duty applications, conveyor systems | Automotive engines, high precision machinery |
What Are the Advantages and Disadvantages of Flat Belts Compared to V Belt Drives?
Flat belts are a widely used alternative that excels in transporting materials over short distances. Their construction allows for a lower profile and a positive grip, making them ideal for conveyor systems. However, while flat belts have a lower initial cost and simpler installation, they may not provide the same level of efficiency and grip as V-belt drives, especially in heavy-duty applications. Additionally, flat belts can be prone to slippage when subjected to high loads, making them less suitable for applications requiring high torque.
How Do Timing Belts Compare to V Belt Drives?
Timing belts offer a unique solution, particularly in applications requiring synchronization, such as in automotive engines. Their toothed design enables precise movement between components, reducing the risk of slippage. While timing belts have a higher initial cost, they often require less maintenance and provide longer service life due to their robust construction. However, their installation demands precise alignment, which can be a drawback for some users. In contrast to V-belt drives, timing belts are best suited for high-precision tasks rather than general power transmission.
How Can B2B Buyers Choose the Right Solution for Their Needs?
Selecting the most suitable power transmission solution requires a careful assessment of operational needs and constraints. B2B buyers should consider the specific requirements of their applications, including load capacity, space limitations, and maintenance capabilities. For general-purpose use, V-belt drives provide a balanced option with good efficiency and moderate maintenance. In contrast, flat belts might be more appropriate for lighter applications, while timing belts are ideal for high-precision requirements, particularly in automotive or machinery contexts. By thoroughly evaluating these alternatives, buyers can make strategic decisions that align with their operational goals and budget constraints.
Essential Technical Properties and Trade Terminology for v belt drive
What Are the Essential Technical Properties of V-Belt Drives?
When selecting V-belt drives, understanding their technical properties is crucial for ensuring optimal performance and longevity in various applications. Here are key specifications to consider:
1. Material Grade
V-belts are typically made from rubber, polyurethane, or composite materials. The choice of material affects durability, flexibility, and resistance to environmental factors such as heat, oil, and abrasion. For B2B buyers, selecting the right material grade can significantly impact operational efficiency and maintenance costs.
2. Width and Length Specifications
V-belts come in various widths and lengths, which are critical for ensuring a proper fit within machinery. Common widths include 1/2”, 5/8”, and 1”. The length is usually specified in inches or millimeters and must match the pulleys’ diameters to prevent slippage and wear. Accurate measurements are essential for achieving maximum power transmission efficiency.
3. Tension and Tolerance Levels
Tension refers to the amount of force applied to the V-belt, which affects its grip on the pulleys. Tolerance levels indicate acceptable variations in dimensions during manufacturing. For international buyers, understanding these parameters ensures that the belts will perform reliably in their specific applications without premature failure.
4. Temperature Resistance
Different applications may expose V-belts to varying temperature ranges. Selecting belts with appropriate heat resistance properties is vital to prevent degradation over time. This is particularly important for industries in hot climates, such as those found in parts of Africa and the Middle East.
5. Load Capacity
V-belts are rated for specific load capacities, which indicate the maximum load they can handle without failure. This specification is critical for B2B buyers to ensure that the V-belt can support the operational demands of their machinery without risking breakdowns.
6. Belt Type
Various types of V-belts are available, including classic, cogged, and banded designs. Each type serves different applications and load requirements. Understanding the characteristics of each belt type helps buyers make informed decisions aligned with their operational needs.
What Are Common Trade Terms Related to V-Belt Drives?
Understanding industry terminology is essential for effective communication and successful procurement. Here are some commonly used terms in the V-belt drive market:
1. OEM (Original Equipment Manufacturer)
This term refers to companies that manufacture products that are sold under another company’s brand name. For B2B buyers, knowing whether a V-belt is an OEM product can assure them of its quality and compatibility with existing equipment.
2. MOQ (Minimum Order Quantity)
MOQ is the smallest quantity of a product that a supplier is willing to sell. Understanding MOQ is important for international buyers, as it can affect inventory management and cash flow.
3. RFQ (Request for Quotation)
An RFQ is a document sent to suppliers requesting pricing and terms for specific quantities of products. This is a critical step for B2B buyers to ensure they receive competitive pricing and terms that align with their budget and operational requirements.
4. Incoterms (International Commercial Terms)
These are predefined commercial terms published by the International Chamber of Commerce (ICC) that dictate the responsibilities of buyers and sellers in international trade. Familiarity with Incoterms is essential for buyers in Africa, South America, the Middle East, and Europe to understand shipping responsibilities, risks, and costs.
5. Lead Time
Lead time refers to the time it takes from placing an order until it is delivered. This is a crucial factor for B2B buyers who need to plan their operations and inventory levels accordingly.
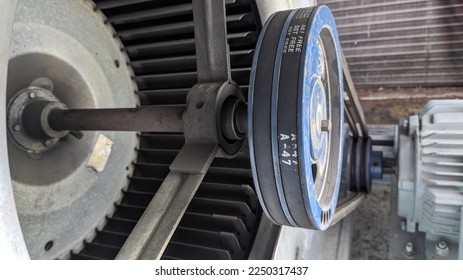
A stock image related to v belt drive.
6. Cross-Reference Numbers
Cross-reference numbers are unique identifiers that allow buyers to find equivalent products from different manufacturers. This is particularly useful for buyers looking to compare options and ensure compatibility with existing systems.
By understanding these essential technical properties and trade terminology, international B2B buyers can make informed decisions when sourcing V-belt drives, ultimately leading to improved operational efficiency and cost savings.
Navigating Market Dynamics and Sourcing Trends in the v belt drive Sector
What Are the Key Market Dynamics and Trends in the V-Belt Drive Sector?
The global V-belt drive market is witnessing robust growth, driven by increasing automation across various industries, including manufacturing, agriculture, and construction. As international B2B buyers from regions like Africa, South America, the Middle East, and Europe (notably the UAE and Argentina) navigate this landscape, they should be aware of several key trends.
Firstly, the shift towards higher efficiency and reliability in power transmission systems is paramount. Many manufacturers are investing in advanced materials and technologies that enhance the durability and performance of V-belts. Buyers should look for suppliers that offer high-quality options, such as Kevlar-reinforced V-belts, which provide greater tensile strength and resistance to wear.
Secondly, the rise of Industry 4.0 is influencing sourcing trends, with a growing emphasis on digitalization and smart manufacturing. B2B buyers can benefit from suppliers who utilize IoT (Internet of Things) technologies in their production processes, enabling real-time tracking of inventory and performance metrics. This not only helps in optimizing maintenance schedules but also in reducing downtime and operational costs.
Moreover, the increasing importance of customization in V-belt solutions is noteworthy. Buyers are encouraged to engage with manufacturers that can provide tailored solutions to meet specific operational needs, enhancing overall efficiency.
How Can Sustainability and Ethical Sourcing Impact B2B Buyers in the V-Belt Drive Sector?
Sustainability is becoming a critical consideration in the V-belt drive sector, as environmental impacts are scrutinized more than ever. B2B buyers must prioritize suppliers who adopt sustainable practices, such as using eco-friendly materials and processes that minimize waste.
Ethical sourcing is also gaining traction, with buyers seeking transparency in their supply chains. This involves understanding the sourcing of raw materials and ensuring that suppliers adhere to ethical labor practices. Certifications such as ISO 14001 for environmental management and Fair Trade can serve as indicators of a supplier’s commitment to sustainability.
Furthermore, the use of “green” materials in V-belt production, like recycled rubber or bio-based polymers, is increasingly favored. Buyers should actively inquire about the environmental certifications of products and consider suppliers who demonstrate a commitment to reducing their carbon footprint.
What Is the Historical Context of V-Belt Drives Relevant to B2B Buyers?
The history of V-belt drives can be traced back to the early 20th century when they were introduced as an efficient means of power transmission. Initially used in automotive applications, their versatility quickly led to widespread adoption in various industrial sectors. Over the decades, advancements in materials and manufacturing processes have significantly improved the performance and lifespan of V-belts.
For B2B buyers, understanding this evolution is crucial. It highlights the importance of selecting suppliers with a proven track record and innovative capabilities. As the market continues to evolve with technological advancements and sustainability initiatives, buyers should align themselves with manufacturers who are not only knowledgeable about the history of V-belts but are also at the forefront of future developments in the sector.
Frequently Asked Questions (FAQs) for B2B Buyers of v belt drive
-
How do I solve common issues with V-belt drives?
To resolve issues with V-belt drives, first identify the problem: slippage, wear, or misalignment. Regularly inspect the belts for wear and tear, ensuring they are properly tensioned. If slippage occurs, check the pulleys for alignment and surface conditions. In cases of excessive noise or vibration, consider replacing worn belts or pulleys. Implementing a preventive maintenance schedule will help avoid most common problems, ensuring a longer lifespan and optimal performance of your V-belt drive. -
What is the best V-belt drive type for heavy-duty applications?
For heavy-duty applications, banded V-belts are often the best choice due to their ability to handle higher loads without slippage. These belts are constructed with multiple layers, increasing their strength and durability. Additionally, cogged V-belts can be beneficial for applications requiring high torque and speed, as their design allows for better flexibility and grip. Always evaluate your specific application requirements, such as load capacity and environmental conditions, to select the most suitable type. -
How can I effectively vet V-belt suppliers in international markets?
Vetting suppliers involves several key steps: research their reputation through online reviews, ask for references from other clients, and verify their certifications and compliance with international standards. Additionally, consider their production capabilities, lead times, and quality assurance processes. Engaging in communication to gauge their responsiveness and customer service can also provide insights into their reliability. If possible, visit their facilities to inspect production practices firsthand, ensuring they align with your quality expectations. -
What are the typical minimum order quantities (MOQ) for V-belt drives?
Minimum order quantities for V-belt drives can vary widely based on the supplier and the specific type of belts required. Generally, MOQs can range from 100 to 1,000 units for standard products. However, for customized V-belts or specialized applications, MOQs may be higher. Always discuss your needs with the supplier to negotiate favorable terms, especially if you are a smaller buyer or seeking a trial order to evaluate product quality. -
What payment terms should I expect when sourcing V-belt drives internationally?
Payment terms for international transactions can vary by supplier and region. Common terms include a percentage upfront (typically 30-50%) with the balance due upon delivery or a letter of credit. It’s essential to clarify these terms before committing to an order. Additionally, consider using secure payment methods that provide buyer protection, such as PayPal or escrow services, to mitigate risks associated with international transactions. -
How can I ensure quality assurance when sourcing V-belt drives?
To ensure quality assurance, request detailed specifications and certifications from your supplier, including ISO standards or equivalent. Implement a quality control process that includes inspecting samples before full production and conducting random inspections during shipment. Consider third-party inspection services that specialize in manufacturing and logistics. Establishing clear communication regarding quality expectations will help ensure the final products meet your requirements. -
What logistics considerations should I keep in mind when importing V-belt drives?
Logistics considerations include shipping methods, customs clearance, and potential tariffs or duties associated with importing V-belt drives. Choose a shipping method that balances cost and delivery speed, such as sea freight for large orders or air freight for urgent needs. Familiarize yourself with local customs regulations and paperwork required to avoid delays. Working with a freight forwarder can streamline this process, ensuring compliance and efficient handling of your shipments. -
Can I customize V-belt drives to meet specific application needs?
Yes, many suppliers offer customization options for V-belt drives to cater to specific application requirements. Customizations can include adjustments in size, material, or design features to enhance performance in particular environments. When discussing customization with suppliers, provide detailed specifications and application scenarios to facilitate the design process. Keep in mind that custom orders may have higher MOQs and longer lead times, so plan accordingly.
Important Disclaimer & Terms of Use
⚠️ Important Disclaimer
The information provided in this guide, including content regarding manufacturers, technical specifications, and market analysis, is for informational and educational purposes only. It does not constitute professional procurement advice, financial advice, or legal advice.
While we have made every effort to ensure the accuracy and timeliness of the information, we are not responsible for any errors, omissions, or outdated information. Market conditions, company details, and technical standards are subject to change.
B2B buyers must conduct their own independent and thorough due diligence before making any purchasing decisions. This includes contacting suppliers directly, verifying certifications, requesting samples, and seeking professional consultation. The risk of relying on any information in this guide is borne solely by the reader.
Strategic Sourcing Conclusion and Outlook for v belt drive
What Are the Key Takeaways for B2B Buyers in V-Belt Drive Sourcing?
In the evolving landscape of power transmission, strategic sourcing of V-belt drives offers significant advantages for international B2B buyers, particularly in Africa, South America, the Middle East, and Europe. Understanding the diverse types of V-belts—such as banded, cogged, and metric options—enables companies to select products tailored to their specific operational needs, ensuring optimal performance and longevity. Additionally, focusing on suppliers that prioritize quality, such as those offering OE-grade materials and maintenance-free solutions, can lead to reduced downtime and lower operational costs.
How Can Strategic Sourcing Enhance Supply Chain Efficiency?
Effective strategic sourcing not only streamlines procurement processes but also fosters strong supplier relationships, which are essential for timely and reliable delivery. For buyers in regions like the UAE and Argentina, leveraging local and international suppliers can mitigate risks associated with supply chain disruptions, enhancing resilience.
What’s Next for International B2B Buyers of V-Belt Drives?
As industries continue to innovate, the demand for advanced V-belt technology will only grow. Buyers are encouraged to stay informed about emerging trends and advancements in materials and designs that can further enhance efficiency and sustainability. By prioritizing strategic sourcing and collaborating with knowledgeable suppliers, businesses can position themselves for success in a competitive market. Embrace this opportunity to optimize your V-belt drive sourcing strategy and ensure your operations are equipped for future challenges.