Optimize Your Process: The Ultimate Screw Conveyor Guide (2025)
Introduction: Navigating the Global Market for screw conveyor
In today’s fast-paced global market, sourcing efficient and reliable screw conveyors can be a daunting challenge for international B2B buyers. The intricacies of bulk material handling require an understanding of various conveyor types and their specific applications across different industries. This comprehensive guide addresses the complexities of selecting the right screw conveyor for your needs, encompassing a broad spectrum of topics, including types of screw conveyors, their applications, supplier vetting processes, and cost considerations.
For buyers in Africa, South America, the Middle East, and Europe—regions characterized by diverse industrial requirements—this guide serves as an essential resource. It empowers you to make informed purchasing decisions by providing actionable insights into the unique features and advantages of various conveyor systems. Whether you are looking for horizontal, inclined, or shaftless screw conveyors, understanding their operational efficiencies will help you optimize your processes and enhance productivity.
Moreover, this guide emphasizes the importance of supplier vetting, ensuring that you partner with manufacturers who offer not only quality products but also reliable support and expertise. By navigating the global market for screw conveyors with the information presented herein, you can confidently select the best solutions tailored to your operational needs, ultimately driving success in your business endeavors.
Understanding screw conveyor Types and Variations
Type Name | Key Distinguishing Features | Primary B2B Applications | Brief Pros & Cons for Buyers |
---|---|---|---|
Horizontal Screw Conveyors | Most common type; designed for horizontal transport; various sizes and materials. | Food processing, agriculture, and chemical industries. | Pros: Versatile, cost-effective. Cons: Limited incline capacity. |
Inclined Screw Conveyors | Operates at angles up to 45 degrees; efficiency decreases with higher angles. | Waste management, mining, and construction. | Pros: Space-saving design. Cons: Higher energy consumption at steep angles. |
Shaftless Screw Conveyors | No central shaft; allows for higher capacity and reduced wear. | Handling sticky, caked, or abrasive materials. | Pros: Reduced maintenance, flexible design. Cons: Typically higher initial cost. |
Vertical Screw Conveyors | Designed for vertical transport; compact footprint; efficient space utilization. | Chemical processing, grain handling, and bulk material storage. | Pros: Efficient for high lifts. Cons: More complex installation. |
Flexible Screw Conveyors | Can be routed at various angles; handles a wide range of materials. | Food, pharmaceuticals, and plastics industries. | Pros: Customizable and mobile. Cons: May require more frequent cleaning. |
What are the Characteristics of Horizontal Screw Conveyors?
Horizontal screw conveyors are the most widely used type, primarily designed to transport bulk materials from one process point to another. They are available in various sizes, lengths, and materials, making them highly versatile for industries like food processing and agriculture. When purchasing, buyers should consider the material characteristics, as trough loading can vary based on the material’s density and abrasiveness. This type is cost-effective, but its inability to handle steep inclines is a limitation for certain applications.
How Do Inclined Screw Conveyors Function?
Inclined screw conveyors operate at angles from slightly above horizontal to 45 degrees. They are particularly useful in waste management and mining, where space is often constrained. However, as the angle increases, efficiency decreases, necessitating higher horsepower to overcome gravity. Buyers should assess the specific angle and material characteristics to ensure optimal performance, as the design must accommodate these variables. While they save space, the energy costs can be higher compared to horizontal systems.
What Makes Shaftless Screw Conveyors Unique?
Shaftless screw conveyors have no central shaft, which allows them to handle higher capacities without the wear associated with traditional designs. They are ideal for sticky or abrasive materials, making them a preferred choice in industries like waste management and food processing. When considering a shaftless conveyor, buyers should evaluate the initial investment against long-term maintenance savings, as their design reduces wear and tear significantly.
Why Choose Vertical Screw Conveyors?
Vertical screw conveyors are specifically engineered for vertical transport, providing an efficient solution for bulk material handling in industries such as chemical processing and grain handling. Their compact footprint allows for effective space utilization, but installation can be more complex. Buyers must consider the height of lift required and ensure that the conveyor is designed to handle the specific material being transported. While they offer high efficiency for vertical lifts, the complexity can lead to higher installation costs.
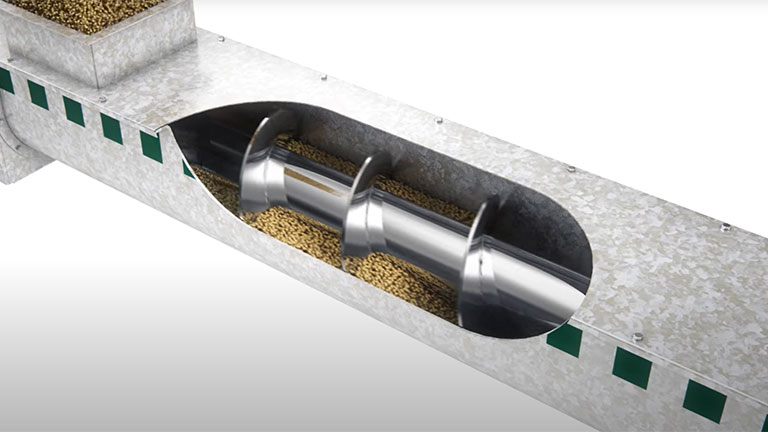
A stock image related to screw conveyor.
How Do Flexible Screw Conveyors Adapt to Various Needs?
Flexible screw conveyors are adaptable systems that can be routed at various angles, making them suitable for a wide range of materials, including powders and granules. Their mobility and customizable design make them a popular choice in food, pharmaceutical, and plastics industries. Buyers should consider the need for frequent cleaning and maintenance, as these conveyors can be more challenging to clean compared to fixed systems. Their versatility, however, often outweighs these concerns, particularly in dynamic production environments.
Key Industrial Applications of screw conveyor
Industry/Sector | Specific Application of Screw Conveyor | Value/Benefit for the Business | Key Sourcing Considerations for this Application |
---|---|---|---|
Food and Beverage | Transporting flour and sugar in processing plants | Enhances efficiency and reduces contamination risk | Compliance with food safety standards; material selection for hygiene |
Agriculture | Conveying seeds and fertilizers in bulk | Improves handling speed and reduces waste | Durability against abrasive materials; capacity requirements |
Mining and Minerals | Moving ore and aggregates from extraction sites | Increases operational efficiency and safety | Customization for harsh environments; maintenance support |
Plastics and Polymers | Feeding plastic resins into molding machines | Ensures precise material flow and minimizes downtime | Compatibility with various resin types; energy efficiency |
Waste Management | Transporting recycled materials and waste | Streamlines waste processing and enhances recycling rates | Enclosed systems to prevent spillage; adaptability to different materials |
How is Screw Conveyor Used in Food and Beverage Industries?
In the food and beverage sector, screw conveyors are crucial for transporting bulk ingredients like flour and sugar. These conveyors ensure the efficient movement of materials while minimizing contamination risks, as they can be designed to meet stringent food safety standards. Buyers should focus on sourcing conveyors made from food-grade materials and consider features such as easy cleaning and maintenance to comply with hygiene regulations.
What Role Does Screw Conveyor Play in Agriculture?
Screw conveyors are extensively used in agriculture for the bulk handling of seeds and fertilizers. They improve the speed of material transport, reducing waste and ensuring that products are delivered to processing areas efficiently. International buyers, particularly from regions like Africa and South America, should consider the durability of the conveyor systems against abrasive materials and the capacity to handle varying loads.
Why is Screw Conveyor Essential in Mining and Minerals?
In the mining industry, screw conveyors facilitate the movement of ore and aggregates from extraction points to processing facilities. They significantly enhance operational efficiency while ensuring worker safety by minimizing spillage and material handling risks. Buyers in this sector should prioritize customization options to withstand harsh environments and seek suppliers who offer robust maintenance support for uninterrupted operations.
How Does Screw Conveyor Improve Processes in Plastics and Polymers?
Screw conveyors are integral in the plastics industry for feeding plastic resins into molding machines. They ensure a precise flow of materials, which is vital for maintaining production efficiency and minimizing downtime. For international buyers, especially in Europe, it’s essential to consider compatibility with various resin types and the energy efficiency of the conveyor systems to optimize operational costs.
In What Ways Does Screw Conveyor Enhance Waste Management Efforts?
In waste management, screw conveyors are utilized to transport recycled materials and waste efficiently. They streamline processing and enhance recycling rates by ensuring that materials are moved quickly and safely. Buyers should look for enclosed conveyor systems to prevent spillage and consider how adaptable the system is to handle diverse materials, which is especially important in regions with varied waste streams.
3 Common User Pain Points for ‘screw conveyor’ & Their Solutions
Scenario 1: Inefficient Material Flow in Diverse Environments
The Problem: Many B2B buyers face challenges with the efficient movement of bulk materials, especially in environments that require flexibility and adaptability. For instance, in industries like agriculture or food processing, materials can vary significantly in texture and moisture content. This inconsistency can lead to blockages or inefficient flow in traditional screw conveyor systems, causing delays in production and increased operational costs. Buyers often struggle to find a solution that accommodates both free-flowing and non-free-flowing materials without the risk of separation or contamination.
The Solution: To address this issue, investing in a flexible screw conveyor is highly recommended. These systems are designed to handle a wide range of materials, including those that tend to pack, cake, or smear. When sourcing a flexible screw conveyor, ensure that it is constructed with rugged materials and has a design that minimizes contact with seals and bearings. This not only improves the longevity of the equipment but also enhances operational efficiency.
Buyers should consult with manufacturers to specify the right diameter and geometry of the screw based on the characteristics of the materials being handled. Additionally, integrating flow promotion devices can significantly improve the handling of non-free-flowing materials, ensuring a steady supply to the conveyor and minimizing downtime.
Scenario 2: Excessive Wear and Maintenance Costs
The Problem: A common concern among B2B buyers is the high wear and tear on screw conveyor components, leading to frequent maintenance and replacement costs. Industries handling abrasive materials, such as mining or recycling, often report accelerated degradation of their equipment, which can result in unexpected downtime and increased operational costs. Buyers may find it challenging to select a screw conveyor that balances durability with cost-effectiveness.
The Solution: To mitigate excessive wear, it is crucial to choose a screw conveyor specifically designed for handling abrasive materials. Opt for materials such as stainless steel or specialized alloys that offer higher resistance to abrasion. When contacting suppliers, inquire about custom design options that include features such as thicker troughs and enhanced screw configurations tailored to abrasive materials.
Furthermore, implementing a proactive maintenance schedule can significantly extend the lifespan of the equipment. Regular inspections and timely replacement of worn parts can prevent sudden breakdowns. Buyers should also consider investing in wear-resistant liners for the conveyor troughs, which can provide an additional layer of protection against abrasive wear and reduce overall maintenance costs.
Scenario 3: Difficulty in Sourcing Customized Solutions
The Problem: Many international B2B buyers encounter obstacles when attempting to source customized screw conveyor solutions that meet their specific operational needs. This challenge is particularly pronounced in regions like Africa and South America, where suppliers may not offer the necessary flexibility in design or configuration. Buyers may find themselves limited to standard options that do not align with their unique material handling requirements.
The Solution: To overcome the challenge of sourcing customized solutions, it is essential to engage with manufacturers that offer a comprehensive range of options and are open to customization. Start by clearly defining your material handling requirements, including the types of materials, flow rates, and any environmental considerations such as dust control or temperature fluctuations.
When evaluating suppliers, prioritize those who provide a collaborative design process, allowing for modifications in screw geometry, conveyor length, and material of construction. Additionally, consider manufacturers with a proven track record of delivering custom solutions for various industries. Establishing a strong relationship with a reliable supplier can lead to tailored solutions that enhance efficiency and performance while ensuring that your specific needs are met without compromise.
Strategic Material Selection Guide for screw conveyor
When selecting materials for screw conveyors, it’s essential to consider various factors that affect performance, durability, and cost. This guide analyzes four common materials used in screw conveyor construction: carbon steel, stainless steel, plastic, and aluminum. Each material has distinct properties, advantages, and limitations that can significantly impact operational efficiency and suitability for specific applications.
What Are the Key Properties of Carbon Steel for Screw Conveyors?
Carbon steel is one of the most widely used materials for screw conveyors due to its strength and cost-effectiveness. It typically has a temperature rating of up to 400°F (204°C) and can withstand moderate pressure levels. However, it is prone to corrosion, especially in humid or abrasive environments, which can lead to premature wear.
Pros: Carbon steel is durable and offers a low initial cost, making it a popular choice for many applications. Its strength allows it to handle heavy loads effectively.
Cons: The main drawback is its susceptibility to rust and corrosion, which can be mitigated by coatings or galvanization but may increase costs. It may not be suitable for food-grade applications without proper treatment.
How Does Stainless Steel Perform in Screw Conveyors?
Stainless steel is renowned for its corrosion resistance, making it ideal for applications involving moisture or corrosive materials. It can handle temperatures up to 1,500°F (815°C) and is often used in food processing, pharmaceuticals, and chemical industries.
Pros: Its durability and resistance to corrosion make it a long-lasting option. Stainless steel is also easy to clean, which is crucial for maintaining hygiene in food-related applications.
Cons: The primary limitation is its higher cost compared to carbon steel. Additionally, it may require specialized welding techniques, increasing manufacturing complexity.
What Are the Benefits of Using Plastic in Screw Conveyors?
Plastic materials, such as polyethylene and polypropylene, are gaining popularity in screw conveyor applications, especially for handling non-abrasive, lightweight materials. They are typically rated for temperatures ranging from -40°F to 180°F (-40°C to 82°C).
Pros: Plastics are lightweight, resistant to corrosion, and can be manufactured in various colors for easy identification. They are also less expensive than metals and can be molded into complex shapes.
Cons: Plastic may not withstand high temperatures or heavy loads as effectively as metal. It is also less suitable for abrasive materials, which can lead to wear and tear over time.
Why Choose Aluminum for Screw Conveyors?
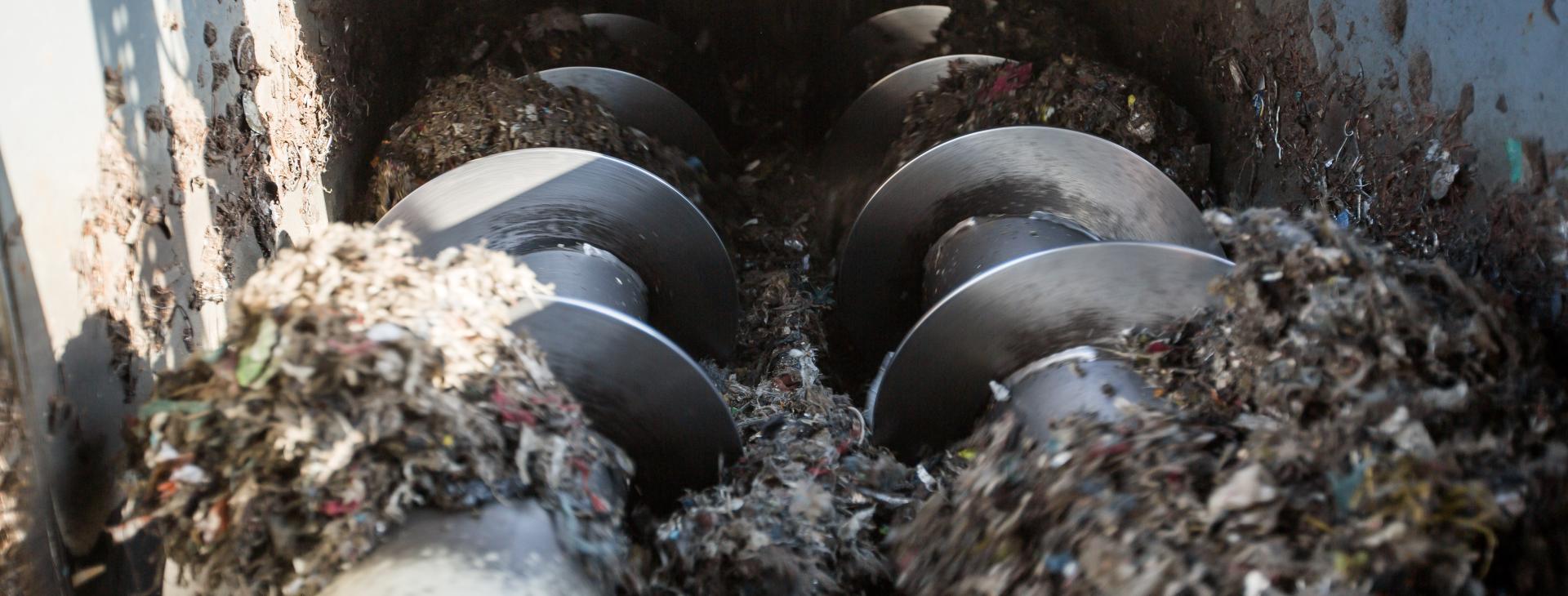
A stock image related to screw conveyor.
Aluminum is a lightweight, corrosion-resistant material that is often used in applications requiring portability and ease of installation. It can handle temperatures up to 500°F (260°C) and is suitable for a variety of materials, including grains and powders.
Pros: The lightweight nature of aluminum makes it easy to install and move, which is advantageous in dynamic environments. It also provides good corrosion resistance and can be anodized for additional protection.
Cons: Aluminum is generally more expensive than carbon steel and may not be as strong, making it less suitable for heavy-duty applications. Its susceptibility to dents and scratches can also be a concern in harsh environments.
Considerations for International B2B Buyers
When selecting materials for screw conveyors, international buyers, particularly from Africa, South America, the Middle East, and Europe, should consider compliance with local standards such as ASTM, DIN, or JIS. Understanding the specific requirements for materials used in food processing or hazardous environments is crucial. Additionally, preferences for local suppliers or manufacturers who can provide after-sales support and service should be taken into account to ensure smooth operations.
Material | Typical Use Case for screw conveyor | Key Advantage | Key Disadvantage/Limitation | Relative Cost (Low/Med/High) |
---|---|---|---|---|
Carbon Steel | General bulk material handling | Cost-effective and durable | Prone to corrosion | Low |
Stainless Steel | Food processing and pharmaceuticals | Excellent corrosion resistance | Higher cost and manufacturing complexity | High |
Plastic | Lightweight, non-abrasive materials | Lightweight and easy to mold | Limited temperature and load capacity | Medium |
Aluminum | Portable applications | Lightweight and corrosion-resistant | More expensive and less strong | Medium |
This strategic material selection guide provides a comprehensive overview of the most common materials used in screw conveyors, helping international B2B buyers make informed decisions tailored to their specific operational needs and regional standards.
In-depth Look: Manufacturing Processes and Quality Assurance for screw conveyor
What Are the Main Stages of Screw Conveyor Manufacturing?
The manufacturing process of screw conveyors involves several crucial stages, each designed to ensure efficiency, durability, and performance. Here’s a breakdown of the typical manufacturing stages:
Material Preparation: What Types of Materials Are Used?
The first step in the manufacturing process is material selection and preparation. Common materials for screw conveyors include carbon steel, stainless steel, and plastic composites. Each material has unique properties suitable for specific applications. For instance, stainless steel is often chosen for its resistance to corrosion and hygiene, making it ideal for food and pharmaceutical applications.
After selecting the appropriate material, it undergoes treatment processes such as cutting and surface finishing to enhance durability. This may involve processes like annealing or hardening to improve the material’s performance under load.
How Is the Forming Process Executed?
The forming stage is where the basic components of the screw conveyor are shaped. This often involves techniques such as:
-
Rolling: This process shapes the steel into a trough or tube, forming the housing for the screw conveyor. Rollers are used to bend the material into the desired shape while maintaining uniform thickness.
-
Machining: After rolling, components may require precise machining to create screw flights, shafts, and other fittings. CNC (Computer Numerical Control) machines are commonly used for their precision and ability to produce complex geometries.
-
Welding: For many screw conveyors, parts such as the flight and shaft need to be welded together. The welding techniques used can vary, with TIG (Tungsten Inert Gas) and MIG (Metal Inert Gas) being popular choices due to their strength and reliability.
What Is Involved in the Assembly Process?
Once the components are formed, assembly takes place. This stage involves:
-
Aligning and Fitting: Ensuring that all components fit together seamlessly. This may require adjustments to ensure proper alignment and functionality.
-
Fastening: Using bolts, nuts, and other fastening methods to secure components together. The choice of fasteners can affect the overall durability and maintenance of the screw conveyor.
-
Installation of Drive Systems: The drive mechanism is installed, which may include motors and gear reducers. This is a critical step, as the efficiency of the screw conveyor heavily relies on the drive system’s performance.
What Finishing Techniques Are Commonly Used?
The finishing stage is where the screw conveyor is prepared for operation. This may involve:
-
Surface Treatments: Processes such as painting, galvanizing, or powder coating are applied to enhance corrosion resistance and provide an appealing appearance.
-
Quality Checks: Before leaving the factory, each unit undergoes final inspections to ensure all components meet design specifications and quality standards.
How Is Quality Assurance Implemented in Screw Conveyor Manufacturing?
Quality assurance (QA) is paramount in screw conveyor manufacturing, ensuring that each product meets stringent standards for performance and safety. Here are some key aspects of QA:
What International Standards Should B2B Buyers Be Aware Of?
Understanding international standards is crucial for B2B buyers. Key standards include:
-
ISO 9001: This standard outlines the criteria for a quality management system. Manufacturers adhering to ISO 9001 demonstrate a commitment to quality and continuous improvement.
-
CE Marking: In Europe, CE marking indicates that the product complies with EU safety, health, and environmental protection standards.
-
API Standards: For screw conveyors used in the oil and gas industry, adhering to American Petroleum Institute (API) standards is essential for safety and reliability.
What Are the QC Checkpoints During Manufacturing?
Quality control checkpoints are established at various stages of the manufacturing process:
-
Incoming Quality Control (IQC): This involves inspecting raw materials upon arrival to ensure they meet specified standards.
-
In-Process Quality Control (IPQC): Quality checks are conducted during the manufacturing process to identify defects early, minimizing waste and rework.
-
Final Quality Control (FQC): The final inspection ensures that the completed screw conveyor meets all specifications before shipment.
What Testing Methods Are Used for Screw Conveyors?
To validate the performance and safety of screw conveyors, manufacturers employ several testing methods, including:
-
Load Testing: Ensuring that the screw conveyor can handle the expected load without failure.
-
Vibration Testing: Assessing the conveyor’s stability and performance under operational conditions.
-
Leak Testing: For enclosed systems, ensuring there are no leaks that could compromise material integrity.
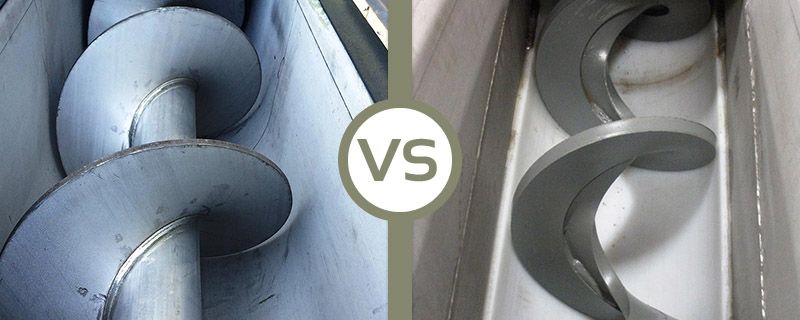
A stock image related to screw conveyor.
How Can B2B Buyers Verify Supplier Quality Control?
For international B2B buyers, especially those from regions such as Africa, South America, the Middle East, and Europe, verifying a supplier’s quality control practices is vital. Here are actionable steps:
What Should Buyers Look for in Supplier Audits and Reports?
-
Supplier Audits: Conducting audits on potential suppliers can provide insight into their manufacturing processes, quality control practices, and adherence to international standards.
-
Quality Reports: Requesting documentation that outlines quality control measures, testing results, and compliance with standards can help assess a supplier’s reliability.
How Can Third-party Inspections Enhance Confidence?
Engaging third-party inspection services offers an unbiased assessment of the supplier’s manufacturing and quality control processes. This can include:
-
Certification Verification: Ensuring that the supplier holds relevant certifications (e.g., ISO, CE).
-
On-site Inspections: A third-party inspector can evaluate the manufacturing process, check compliance with specifications, and assess the quality of finished products.
What Are the QC and Certification Nuances for International Buyers?
Understanding the nuances of quality control and certification is essential for international buyers:
-
Regional Compliance: Different regions may have specific compliance requirements. For instance, CE marking is mandatory in Europe, while other regions may have different standards.
-
Cultural Considerations: Buyers should be aware of cultural differences in business practices that may affect communication and expectations regarding quality.
-
Documentation Requirements: Ensure that all necessary documentation is provided, including compliance certificates, test reports, and warranties, to facilitate smooth international transactions.
By navigating the manufacturing processes and quality assurance measures effectively, B2B buyers can make informed decisions when sourcing screw conveyors, ensuring they select reliable suppliers that meet their operational needs.
Practical Sourcing Guide: A Step-by-Step Checklist for ‘screw conveyor’
The procurement of screw conveyors can significantly impact your operational efficiency and material handling processes. This practical sourcing guide offers a step-by-step checklist designed for international B2B buyers in Africa, South America, the Middle East, and Europe. By following these steps, you can ensure that you select the right screw conveyor solution tailored to your specific needs.
Step 1: Define Your Technical Specifications
Before reaching out to suppliers, clearly outline the technical requirements for your screw conveyor. Consider factors such as the type of material being conveyed, the distance and elevation of the conveyor, and the required capacity. Understanding these parameters will help you communicate effectively with potential suppliers and ensure they can meet your needs.
- Material Characteristics: Is the material free-flowing or does it tend to pack or cake?
- Operational Environment: Will the conveyor operate in a dusty, corrosive, or hazardous environment?
Step 2: Assess Your Budget and Total Cost of Ownership
Establish a budget that not only covers the initial purchase price but also considers maintenance, energy consumption, and potential downtime. Understanding the total cost of ownership (TCO) will help you make a more informed decision and avoid unexpected expenses later.
- Energy Efficiency: Look for conveyors with low horsepower motors that reduce operational costs.
- Maintenance Requirements: Consider the ease of maintenance and availability of replacement parts.
Step 3: Evaluate Potential Suppliers
Conduct thorough research on potential suppliers to gauge their reliability and expertise. Request company profiles, case studies, and references from other buyers, particularly those in your region or industry. A reputable supplier should have a solid track record and be able to demonstrate their capability through past projects.
- Certifications and Standards: Verify any industry certifications or compliance with international standards.
- Experience: Look for suppliers with extensive experience in manufacturing screw conveyors suitable for your specific materials.
Step 4: Request Quotes and Compare Offerings
Once you have shortlisted potential suppliers, request detailed quotes that outline specifications, pricing, and lead times. Comparing these quotes will help you identify the best value for your investment. Ensure that each quote includes all relevant costs, including shipping and installation.
- Customization Options: Inquire if the supplier offers custom solutions to meet your specific requirements.
- Warranty and Support: Check what warranties are provided and the level of after-sales support available.
Step 5: Conduct Site Visits or Virtual Demonstrations
If feasible, visit the supplier’s manufacturing facility or request a virtual demonstration of their products. Observing the production process and the equipment in action can provide valuable insights into the quality and reliability of the screw conveyors.
- Quality Assurance Processes: Look for evidence of rigorous quality control measures in place.
- Operational Testing: Ask about testing procedures for the screw conveyors to ensure performance and reliability.
Step 6: Finalize the Purchase Agreement
Once you’ve selected a supplier, carefully review the purchase agreement. Ensure that all terms, including delivery schedules, payment terms, and warranty conditions, are clearly stated. A well-defined agreement will help protect your interests and facilitate a smooth transaction.
- Delivery Timelines: Confirm the expected delivery date and any penalties for delays.
- Payment Terms: Understand the payment structure and options available to you.
By following this comprehensive checklist, you can streamline the sourcing process and make an informed decision when procuring screw conveyors, ultimately enhancing your operational efficiency and productivity.
Comprehensive Cost and Pricing Analysis for screw conveyor Sourcing
What Are the Key Cost Components in Screw Conveyor Sourcing?
When sourcing screw conveyors, understanding the cost structure is essential for international B2B buyers. The primary cost components include:
-
Materials: The type of materials used—such as stainless steel, carbon steel, or specialized alloys—significantly impacts the cost. High-quality materials often increase initial expenses but can lead to lower maintenance costs over time.
-
Labor: Labor costs can vary by region and are influenced by local wage standards. For instance, sourcing from regions with lower labor costs, such as some South American countries, may reduce overall expenses.
-
Manufacturing Overhead: This includes costs related to facilities, utilities, and equipment. Efficient manufacturing processes can lower overhead, which may be reflected in the pricing.
-
Tooling: Custom tooling requirements for specific applications can add to the initial costs. Buyers should assess whether a standard design can meet their needs to avoid additional tooling expenses.
-
Quality Control (QC): Implementing stringent QC processes is critical, especially for applications in industries like food processing or pharmaceuticals. While this may increase costs, it ensures product reliability and compliance with international standards.
-
Logistics: Shipping and handling costs are vital considerations, particularly for international buyers. Factors such as distance, shipping method, and local customs regulations can significantly influence the final price.
-
Margin: Suppliers will typically add a margin to cover their operational costs and profit. Understanding the margin structure can help buyers negotiate better deals.
How Do Price Influencers Affect Screw Conveyor Costs?
Several factors can influence the pricing of screw conveyors:
-
Volume and Minimum Order Quantity (MOQ): Larger orders often benefit from volume discounts. Buyers should evaluate their long-term needs to negotiate favorable terms.
-
Specifications and Customization: Custom designs tailored to specific applications may lead to higher prices. Buyers should assess whether off-the-shelf solutions are viable to minimize costs.
-
Material Quality and Certifications: Premium materials and certifications (e.g., ISO, CE) can drive up costs but may be necessary for compliance in certain regions, especially in Europe.
-
Supplier Factors: The reputation and reliability of the supplier can affect pricing. Established suppliers may charge more due to their proven quality and service, but they also reduce risks associated with sourcing.
-
Incoterms: The choice of Incoterms (International Commercial Terms) can impact total costs. Buyers should understand terms like FOB (Free on Board) or CIF (Cost, Insurance, Freight) to manage shipping costs effectively.
What Tips Can Help Buyers Optimize Costs When Sourcing Screw Conveyors?
For international buyers, particularly from Africa, South America, the Middle East, and Europe, several strategies can help optimize costs:
-
Negotiate Wisely: Leverage your purchasing power by negotiating terms with suppliers. Highlighting potential future orders can incentivize suppliers to offer better pricing.
-
Consider Total Cost of Ownership (TCO): Evaluate not just the purchase price but also long-term operational costs, including maintenance, energy consumption, and potential downtime. This holistic view can lead to better purchasing decisions.
-
Understand Pricing Nuances for International Transactions: Be aware of currency fluctuations and their impact on pricing. Establishing fixed pricing agreements may mitigate risks associated with currency volatility.
-
Research Local Suppliers: Explore local manufacturers in your region to reduce logistics costs. Local sourcing may also lead to faster turnaround times and easier communication.
-
Stay Informed About Market Trends: Keeping up with industry trends and material costs can help buyers make informed decisions and negotiate effectively.
Disclaimer on Indicative Prices
Prices for screw conveyors can vary significantly based on the aforementioned factors. It’s important for buyers to request quotes tailored to their specific needs and circumstances. This approach ensures a more accurate understanding of potential costs involved in sourcing screw conveyors.
Alternatives Analysis: Comparing screw conveyor With Other Solutions
When considering bulk material handling solutions, evaluating alternatives to screw conveyors can provide valuable insights for B2B buyers in diverse regions such as Africa, South America, the Middle East, and Europe. Each solution has its unique advantages and limitations, making it essential to understand how they compare in terms of performance, cost, ease of implementation, maintenance, and best use cases. Below is a detailed comparison of screw conveyors with two viable alternatives: Flexible Screw Conveyors and Pneumatic Conveyors.
Comparison Aspect | Screw Conveyor | Flexible Screw Conveyor | Pneumatic Conveyor |
---|---|---|---|
Performance | Efficient for free-flowing and semi-fluid materials; limited incline ability. | Handles a wide range of materials; highly adaptable to layout. | Excellent for lightweight and fine materials; high speed but may require more energy. |
Cost | Generally cost-effective; lower initial investment for horizontal systems. | Higher upfront cost due to versatility and customization options. | Can be expensive due to complex systems and energy consumption. |
Ease of Implementation | Straightforward installation; requires space for horizontal or inclined layouts. | Flexible installation; can fit into tight spaces and complex layouts. | Installation can be complex; requires careful consideration of pressure and air supply. |
Maintenance | Moderate maintenance; regular inspection needed for wear and tear. | Low maintenance; fewer moving parts reduce wear and downtime. | High maintenance; requires monitoring of air pressure and system integrity. |
Best Use Case | Ideal for continuous, bulk material handling in stable environments. | Suitable for varied materials and applications, especially in limited spaces. | Best for transporting lightweight, powdered, or granular materials over long distances. |
What Are the Advantages and Disadvantages of Flexible Screw Conveyors?
Flexible screw conveyors are designed to handle a wide variety of materials, from large pellets to fine powders, making them incredibly versatile. Their primary advantage is the ability to convey materials at different angles and through tight spaces, which is beneficial for operations with limited layouts. However, they can be more expensive upfront than traditional screw conveyors, and their performance may decline with very heavy or abrasive materials. Additionally, while they require less maintenance, they may not be the best choice for heavy-duty applications.
How Do Pneumatic Conveyors Compare to Screw Conveyors?
Pneumatic conveyors utilize air pressure to transport materials, making them excellent for lightweight and fine materials. They are particularly efficient for long-distance transport and can move materials through complex piping systems. However, the initial setup can be complex and costly, and they require a reliable air supply to function effectively. Maintenance can also be a challenge, as the system must be monitored for pressure and potential leaks. While pneumatic systems excel in certain applications, they may not provide the same level of reliability for bulk materials as screw conveyors.
How Should B2B Buyers Choose the Right Solution for Their Needs?
When selecting the right conveying solution, B2B buyers should consider several factors, including the specific material type, layout constraints, and budgetary considerations. For businesses handling free-flowing bulk materials in stable environments, screw conveyors often provide a cost-effective and reliable solution. Conversely, if flexibility and adaptability are paramount, especially in limited spaces, flexible screw conveyors may be the better choice. Finally, for operations requiring the transport of lightweight or fine materials over long distances, pneumatic conveyors can offer significant advantages, despite their higher costs and maintenance needs. Ultimately, the decision should align with the operational goals and material characteristics of the business.
Essential Technical Properties and Trade Terminology for screw conveyor
What are the Key Technical Properties of Screw Conveyors?
When considering screw conveyors for bulk material handling, understanding their technical properties is crucial for making informed purchasing decisions. Here are some essential specifications that B2B buyers should be aware of:
1. Material Grade
The material grade of a screw conveyor affects its durability and resistance to wear. Common materials include carbon steel, stainless steel, and other alloys. For instance, stainless steel is ideal for corrosive environments, while carbon steel is suitable for general applications. Choosing the right material grade can significantly impact the lifespan and maintenance costs of the equipment.
2. Tolerance
Tolerance refers to the permissible limit of variation in a physical dimension or measured value. In screw conveyors, tight tolerances are essential for optimal performance and efficiency. For example, a well-calibrated screw pitch ensures that bulk materials are conveyed smoothly without blockages. Ensuring the correct tolerances can minimize operational disruptions and enhance overall efficiency.
3. Capacity
Capacity indicates the volume of material a screw conveyor can handle over a specific period. It is often measured in cubic meters per hour (m³/h) or tons per hour (TPH). Selecting a conveyor with the right capacity is vital to meet production demands without overloading the system, which can lead to breakdowns and increased wear.
4. Incline Angle
The incline angle of a screw conveyor can range from horizontal to vertical. Different angles affect the efficiency and horsepower requirements of the conveyor. For instance, conveyors inclined beyond 20 degrees may require additional power to overcome gravity. Understanding the incline angle is essential for optimizing energy consumption and ensuring effective material flow.
5. Screw Diameter and Pitch
The diameter and pitch of the screw influence the flow rate and efficiency of the conveyor. Larger diameters can handle heavier loads, while pitch affects the material’s movement speed. A shorter pitch may be necessary for denser materials to prevent packing. Selecting the right dimensions can significantly enhance operational efficiency and reduce energy costs.
What are Common Trade Terms Used in Screw Conveyor Transactions?
Familiarity with industry jargon can facilitate smoother transactions and negotiations in the screw conveyor market. Here are some common terms:
1. OEM (Original Equipment Manufacturer)
An OEM is a company that manufactures products that are sold under another company’s brand. Understanding whether you are dealing with an OEM can help buyers assess product quality and reliability, as OEMs often adhere to strict manufacturing standards.
2. MOQ (Minimum Order Quantity)
MOQ refers to the smallest number of units a supplier is willing to sell. This is particularly important for international buyers as it can affect inventory levels and cash flow. Knowing the MOQ helps in planning purchases effectively, especially in regions with varying demand.
3. RFQ (Request for Quotation)
An RFQ is a document that a buyer sends to suppliers to request pricing and terms for specific products or services. For international buyers, issuing an RFQ can lead to better pricing and terms by allowing multiple suppliers to bid for the business.
4. Incoterms (International Commercial Terms)
Incoterms are a set of predefined commercial terms that define the responsibilities of buyers and sellers in international transactions. They cover aspects such as shipping, insurance, and tariffs, which are crucial for international buyers to understand to avoid unexpected costs and liabilities.
5. Lead Time
Lead time is the time taken from placing an order to the delivery of the product. This is particularly important for businesses operating on tight schedules. Knowing the lead time can help buyers plan their production schedules and manage supply chain risks effectively.
Understanding these technical properties and trade terms will empower B2B buyers, particularly from Africa, South America, the Middle East, and Europe, to make informed decisions in the screw conveyor market, ultimately leading to better operational outcomes and cost efficiencies.
Navigating Market Dynamics and Sourcing Trends in the screw conveyor Sector
What Are the Current Market Dynamics and Key Trends Influencing Screw Conveyors?
The screw conveyor market is witnessing significant growth driven by increased industrial automation and the rising demand for bulk material handling across various sectors, including agriculture, food processing, and construction. International B2B buyers from regions like Africa, South America, the Middle East, and Europe, particularly Italy and Mexico, are increasingly seeking reliable and efficient solutions that can handle diverse materials. The adoption of advanced technologies, such as IoT and AI, is reshaping how screw conveyors are designed and operated, leading to enhanced efficiency, predictive maintenance, and real-time monitoring capabilities.
Emerging trends include the rise of flexible screw conveyors, which can accommodate a broader range of materials and configurations. These systems are particularly advantageous in industries that handle both free-flowing and non-free-flowing materials, offering versatility and reduced maintenance needs. Furthermore, suppliers are increasingly focusing on customization options to meet specific operational requirements, enabling buyers to optimize their material handling processes. As sustainability becomes a priority, many manufacturers are also integrating eco-friendly practices into their production, offering “green” conveyor solutions that align with global environmental goals.
How Does Sustainability Impact Sourcing Decisions in the Screw Conveyor Sector?
Sustainability is a critical factor for international B2B buyers in the screw conveyor market, as companies increasingly prioritize environmental responsibility in their sourcing strategies. The environmental impact of bulk material handling equipment can be significant, with energy consumption and material waste being key considerations. Buyers are now more inclined to partner with manufacturers who demonstrate a commitment to sustainable practices, such as using recyclable materials and minimizing energy usage during production.
Ethical sourcing is also gaining traction, as businesses aim to ensure that their supply chains are transparent and responsible. Buyers should look for suppliers that hold certifications such as ISO 14001 for environmental management and utilize sustainable materials in their products. Additionally, the incorporation of energy-efficient drive systems in screw conveyors not only reduces operational costs but also aligns with corporate sustainability goals. By prioritizing suppliers with a focus on sustainability, B2B buyers can enhance their brand reputation and meet the growing consumer demand for environmentally friendly products.
How Has the Screw Conveyor Industry Evolved Over Time?
The screw conveyor industry has undergone significant evolution since its inception, adapting to the changing needs of various sectors. Initially designed for simple material transport, screw conveyors have transformed into highly sophisticated systems that leverage advanced engineering and materials technology. Over the decades, manufacturers have introduced various types of screw conveyors, including horizontal, inclined, and vertical designs, each tailored to specific applications and material characteristics.
The incorporation of automation and smart technologies has further revolutionized the industry, allowing for improved efficiency, reliability, and data-driven insights. Today, screw conveyors are not only integral to bulk handling operations but also play a pivotal role in supporting sustainable practices across industries. As the market continues to evolve, B2B buyers can expect ongoing innovations that enhance performance while addressing environmental and operational challenges.
Frequently Asked Questions (FAQs) for B2B Buyers of screw conveyor
-
How do I solve issues with material flow in screw conveyors?
To address material flow problems in screw conveyors, first assess the characteristics of the bulk material, such as moisture content, particle size, and flowability. Adjust the screw pitch and diameter to optimize the flow rate. Additionally, consider the conveyor’s incline—lowering the incline can improve efficiency. Implementing flow promotion devices like vibratory feeders can also help with non-free-flowing materials. Regular maintenance and inspection of the conveyor system are crucial to ensure it operates smoothly and to identify any wear or damage that could impede performance. -
What is the best type of screw conveyor for handling sticky materials?
For sticky materials, flexible screw conveyors are often the best choice due to their ability to handle both free-flowing and non-free-flowing materials without separation. They feature a rugged design that minimizes contact with bearings and seals, which can become clogged. Additionally, consider using a shaftless screw conveyor as it can effectively transport sticky materials without the risk of jamming. Ensure the conveyor is equipped with appropriate discharge systems to prevent build-up at the discharge point. -
How can I customize a screw conveyor for my specific application?
Customization of screw conveyors can be achieved by varying the diameter, pitch, and material of the screw, as well as the type of trough (U-trough vs. tubular). Many manufacturers offer modular designs that allow you to interchange components such as hoppers and drive systems based on your material characteristics and process requirements. Discuss your specific needs with suppliers who can provide tailored solutions, including mobile configurations for flexibility in your operations. -
What minimum order quantities (MOQs) should I expect when sourcing screw conveyors?
Minimum order quantities for screw conveyors can vary significantly among manufacturers and depend on the complexity of the design. Generally, MOQs may range from a single unit for standard models to larger quantities for customized solutions. It’s advisable to communicate your requirements directly with suppliers to negotiate MOQs, especially if you are a first-time buyer or looking to establish a long-term partnership. Some suppliers may offer flexibility for international buyers to accommodate varying market demands. -
What payment terms are typically offered by screw conveyor suppliers?
Payment terms can vary by supplier but commonly include options like upfront deposits (often 30-50% of the total cost) with the balance due upon delivery or installation. Some suppliers may offer net payment terms (e.g., net 30 or net 60 days) for established customers. International buyers should inquire about the possibility of using letters of credit or escrow services for larger transactions to ensure secure payment. Always clarify terms in advance to prevent misunderstandings. -
How do I vet suppliers when sourcing screw conveyors internationally?
Vetting suppliers involves conducting thorough due diligence, including checking their industry reputation, certifications, and customer reviews. Request references from previous clients and assess their experience with international shipping. Evaluate their manufacturing capabilities and quality assurance processes to ensure compliance with international standards. Engaging third-party inspection services can also provide additional assurance regarding product quality and supplier reliability. -
What logistics considerations should I keep in mind when importing screw conveyors?
When importing screw conveyors, consider factors such as shipping methods, lead times, and customs regulations. Choose a reliable logistics partner experienced in handling industrial equipment to ensure timely delivery. Understand the import duties and taxes applicable in your country, as these can significantly impact overall costs. Additionally, plan for potential delays by accounting for customs clearance and transportation times when scheduling your operations. -
What quality assurance practices should I expect from screw conveyor manufacturers?
Reputable screw conveyor manufacturers typically implement rigorous quality assurance practices, including material testing, performance evaluations, and compliance with industry standards. Look for suppliers who offer warranties and post-sale support, indicating confidence in their products. Request documentation of their quality control processes and certifications, such as ISO 9001, to ensure they adhere to high manufacturing standards. Regular audits and inspections can also provide peace of mind regarding the quality of the equipment you are sourcing.
Important Disclaimer & Terms of Use
⚠️ Important Disclaimer
The information provided in this guide, including content regarding manufacturers, technical specifications, and market analysis, is for informational and educational purposes only. It does not constitute professional procurement advice, financial advice, or legal advice.
While we have made every effort to ensure the accuracy and timeliness of the information, we are not responsible for any errors, omissions, or outdated information. Market conditions, company details, and technical standards are subject to change.
B2B buyers must conduct their own independent and thorough due diligence before making any purchasing decisions. This includes contacting suppliers directly, verifying certifications, requesting samples, and seeking professional consultation. The risk of relying on any information in this guide is borne solely by the reader.
Strategic Sourcing Conclusion and Outlook for screw conveyor
What Are the Key Takeaways for B2B Buyers in Screw Conveyor Sourcing?
In the evolving landscape of bulk material handling, strategic sourcing of screw conveyors is paramount for optimizing operational efficiency. International B2B buyers, particularly in Africa, South America, the Middle East, and Europe, must prioritize suppliers that offer customizable solutions tailored to specific material characteristics and handling requirements. Understanding the diverse types of screw conveyors—from horizontal to vertical and inclined—can significantly enhance process efficiency and reduce long-term costs.
How Can Strategic Sourcing Benefit Your Business?
Implementing a strategic sourcing approach enables businesses to leverage competitive pricing, ensure reliability, and foster long-term partnerships with manufacturers who possess the necessary expertise and technological advancements. Buyers should focus on suppliers that emphasize quality craftsmanship, robust design, and comprehensive support services. This proactive approach not only mitigates risks associated with equipment failure but also aligns with sustainability goals by optimizing energy consumption and minimizing waste.
What’s Next for International B2B Buyers?
As the demand for efficient bulk handling solutions continues to grow, staying informed about the latest innovations in screw conveyor technology is essential. Engage with trusted suppliers, attend industry trade shows, and participate in webinars to stay ahead of market trends. The future of screw conveyor sourcing lies in strategic partnerships that drive operational excellence and foster innovation. Begin your journey today by evaluating potential suppliers and aligning their offerings with your unique business needs.