Optimize Your Storage: The Ultimate Pallet Racking Guide (2025)
Introduction: Navigating the Global Market for pallet racking
In the fast-paced world of logistics and warehousing, sourcing the right pallet racking solutions can be a daunting challenge for B2B buyers, especially in diverse markets across Africa, South America, the Middle East, and Europe. With a plethora of options available, understanding the various types of pallet racking systems and their specific applications is crucial for optimizing storage efficiency and ensuring seamless operations. This guide provides a comprehensive overview of pallet racking, from selective and drive-in systems to cantilever and mobile racking, catering to the unique needs of different industries.
Navigating the complexities of supplier vetting, cost considerations, and installation requirements can be overwhelming. However, this guide empowers international B2B buyers by equipping them with the knowledge necessary to make informed purchasing decisions. By breaking down the essential factors involved in selecting the right pallet racking system, buyers can confidently assess their options and align them with their operational goals.
Whether you are a warehouse manager in Turkey seeking to maximize your space or a logistics director in South Africa looking to streamline inventory management, this resource aims to enhance your understanding of pallet racking solutions. Ultimately, the insights provided will facilitate a smoother procurement process, ensuring that your investment in pallet racking yields optimal returns and supports your business’s growth trajectory.
Understanding pallet racking Types and Variations
Type Name | Key Distinguishing Features | Primary B2B Applications | Brief Pros & Cons for Buyers |
---|---|---|---|
Selective Pallet Racking | Direct access to each pallet; adjustable levels | Warehousing, retail, distribution | Pros: Easy access, flexible; Cons: Lower density storage compared to others. |
Drive-In/Drive-Through Racking | High-density storage; forklifts drive into racks | Cold storage, bulk storage | Pros: Maximizes space, efficient for large volumes; Cons: Limited access for inventory management. |
Push Back Racking | Pallets stored on wheeled carts; FIFO system | Food distribution, manufacturing | Pros: Efficient use of space, good for fast-moving items; Cons: More complex installation. |
Mobile Racking | Racks mounted on mobile bases; compact storage | Archive storage, libraries | Pros: Maximizes space, flexible layout; Cons: Higher initial investment, maintenance required. |
Cantilever Racking | Designed for long items; open design | Lumber yards, furniture storage | Pros: Easy access for long products, customizable; Cons: Less stable for smaller items. |
What are the Characteristics of Selective Pallet Racking?
Selective pallet racking is the most common type of racking system, known for its straightforward design that allows direct access to each pallet. This system features adjustable levels, accommodating various pallet sizes and weights, making it suitable for diverse industries such as warehousing, retail, and distribution. B2B buyers should consider their inventory turnover rates and the need for quick access to products when choosing this type of racking.
How Does Drive-In/Drive-Through Racking Work?
Drive-in and drive-through racking systems offer high-density storage solutions, allowing forklifts to drive directly into the racks. This design is particularly beneficial for cold storage and bulk storage applications, where space optimization is critical. Buyers should weigh the benefits of maximizing storage against the potential drawbacks of limited accessibility for inventory management, especially for businesses with a diverse product range.
What are the Advantages of Push Back Racking?
Push back racking utilizes a wheeled cart system, allowing pallets to be loaded from the front and pushed back into the rack. This system supports a first-in, first-out (FIFO) inventory management approach, making it ideal for industries like food distribution and manufacturing. When considering push back racking, B2B buyers should assess the complexity of installation and maintenance against the efficiency gains in space utilization and inventory flow.
Why Choose Mobile Racking Systems?
Mobile racking systems are mounted on mobile bases, enabling aisles to be created or closed as needed. This flexibility is perfect for archive storage and libraries, where maximizing floor space is essential. Buyers should consider the higher initial investment and maintenance requirements against the significant space-saving benefits and adaptability this system provides.
What are the Key Features of Cantilever Racking?
Cantilever racking is specifically designed for storing long items such as lumber or furniture. Its open design allows for easy access and customization based on the length of the items being stored. B2B buyers should evaluate the stability of the system for various product sizes and the potential need for additional safety features when selecting cantilever racking for their operations.
Key Industrial Applications of pallet racking
Industry/Sector | Specific Application of Pallet Racking | Value/Benefit for the Business | Key Sourcing Considerations for this Application |
---|---|---|---|
Retail | Storing Seasonal Merchandise | Optimizes space and improves inventory management | Consider height and load capacity based on product types |
Food and Beverage | Cold Storage Solutions | Maintains product integrity and reduces spoilage | Ensure racking is compatible with refrigeration systems |
Automotive | Parts and Component Storage | Increases efficiency in parts retrieval and inventory | Look for heavy-duty options with high load capacities |
E-commerce | Fulfillment Center Operations | Streamlines order processing and shipping logistics | Focus on modular designs to adapt to changing needs |
Pharmaceuticals | Secure Storage for Sensitive Products | Enhances security and compliance with regulations | Prioritize racks with safety features and easy access |
How is Pallet Racking Used in Retail for Seasonal Merchandise Storage?
In the retail sector, pallet racking is instrumental for managing seasonal merchandise. Retailers can utilize adjustable pallet racks to accommodate fluctuating inventory levels, allowing for efficient space usage during peak seasons. This system enhances inventory visibility and accessibility, reducing the time staff spend locating products. Buyers should consider the height and load capacity of the racks to match the specific types of merchandise, ensuring optimal performance throughout the year.
What are the Benefits of Pallet Racking in Food and Beverage Cold Storage?
Pallet racking systems in the food and beverage industry are crucial for cold storage applications. They help maintain product integrity by providing organized and efficient storage solutions that minimize spoilage. By using racks designed for cold environments, businesses can enhance their operational efficiency while ensuring compliance with health regulations. Buyers must ensure that the racking is compatible with refrigeration systems and can withstand the unique conditions of cold storage.
How Does Pallet Racking Improve Efficiency in Automotive Parts Storage?
In the automotive sector, pallet racking is used extensively for storing parts and components. This application allows for quick retrieval and efficient inventory management, which is vital for maintaining production schedules. Heavy-duty pallet racks can handle the substantial weight of automotive parts, ensuring safety and reliability. Buyers should focus on sourcing options with high load capacities and robust designs to accommodate the demands of this fast-paced industry.
Why is Pallet Racking Essential for E-commerce Fulfillment Centers?
E-commerce businesses rely heavily on pallet racking for their fulfillment center operations. The ability to quickly process orders and efficiently store products is vital in meeting customer expectations. Pallet racks facilitate streamlined workflows, reducing the time from order placement to shipment. When sourcing, buyers should consider modular designs that allow for easy reconfiguration as inventory needs change, ensuring adaptability in a rapidly evolving market.
How Does Pallet Racking Enhance Security in Pharmaceutical Storage?
In the pharmaceutical industry, pallet racking is employed for secure storage of sensitive products. These systems not only organize inventory but also enhance security and compliance with stringent regulations. Racks equipped with safety features help mitigate risks associated with product handling and storage. Buyers must prioritize sourcing racking solutions that offer both security and ease of access, ensuring that sensitive products are well-protected while remaining readily available for distribution.
3 Common User Pain Points for ‘pallet racking’ & Their Solutions
Scenario 1: Inadequate Space Utilization in Warehouses
The Problem: Many B2B buyers, particularly those operating in regions with high real estate costs like Europe and parts of the Middle East, struggle with maximizing warehouse space. Inefficient layouts lead to wasted vertical space and hinder productivity. As businesses grow and product lines expand, the need for an adaptable storage solution becomes critical. Buyers often find themselves with a disorganized inventory, which not only complicates retrieval but also increases operational costs.
The Solution: To combat inadequate space utilization, buyers should consider implementing selective pallet racking systems. These systems allow for efficient vertical storage, enabling warehouses to utilize height effectively. When sourcing pallet racking, buyers should look for customizable options that allow for different heights and widths based on their specific inventory needs. Additionally, incorporating accessories such as wire decking can enhance visibility and airflow, making it easier to track inventory levels. It’s advisable to perform a thorough analysis of current inventory and future projections to select the appropriate racking system that can scale with business growth.
Scenario 2: Safety Hazards and Compliance Issues
The Problem: Safety is a paramount concern in warehouse operations, and improper pallet racking setups can lead to accidents and injuries. Many businesses face challenges with compliance to safety regulations, especially in regions with stringent laws like South Africa and Turkey. Buyers may find their existing racking systems are not only unsafe but also fail to meet industry standards, putting their workforce at risk and potentially leading to costly fines.
The Solution: To enhance safety and compliance, businesses should invest in high-quality pallet racking systems that meet or exceed safety standards. Buyers should prioritize systems that include features such as column protectors and safety mesh to prevent accidents from falling products. Regular training for warehouse staff on safe loading and unloading practices is also crucial. Furthermore, conducting routine inspections of racking systems can identify potential hazards before they become critical issues. Engaging with reputable suppliers who provide certifications and documentation for safety compliance will ensure that the selected pallet racking meets all necessary regulations.
Scenario 3: Difficulty in Inventory Management and Accessibility
The Problem: Another common pain point is the difficulty in managing and accessing inventory stored on pallet racks. Many businesses experience delays in order fulfillment due to inefficient retrieval processes. This is particularly prevalent in regions like South America, where logistical challenges can exacerbate issues with stock rotation and accessibility. Buyers often find their employees spending excessive time locating items, leading to reduced productivity and customer dissatisfaction.
The Solution: To streamline inventory management, businesses should consider implementing a first-in, first-out (FIFO) system using pallet racking designed for easy access. This can include drive-in or push-back racking systems that allow for multiple pallets to be stored in-depth, ensuring that older stock is used first. Buyers should also leverage technology, such as warehouse management systems (WMS), to track inventory levels and automate retrieval processes. Investing in barcode scanning or RFID technology can further enhance accuracy in inventory management, making it easier to locate products quickly. Regular audits of inventory can help maintain organization and ensure that the pallet racking system remains efficient and effective.
Strategic Material Selection Guide for pallet racking
When selecting materials for pallet racking systems, international B2B buyers must consider various factors that influence performance, durability, and cost-effectiveness. Below is an analysis of four common materials used in pallet racking, focusing on their properties, advantages, disadvantages, and specific considerations for buyers from Africa, South America, the Middle East, and Europe.
What are the Key Properties of Steel in Pallet Racking?
Steel is the most widely used material for pallet racking due to its strength and durability. Key properties include:
- Temperature Rating: Steel can withstand high temperatures, making it suitable for warehouses with fluctuating climates.
- Corrosion Resistance: Galvanized steel offers enhanced corrosion resistance, ideal for humid or coastal environments.
Pros: Steel pallet racks are robust and can support heavy loads, with a typical load capacity of up to 5,000 lbs per level. They are also easy to maintain and can be customized with various accessories.
Cons: The primary downside is the higher initial cost compared to other materials. Additionally, manufacturing complexity can lead to longer lead times.
Impact on Application: Steel is compatible with various media, including chemicals and food products, provided it is properly coated to prevent corrosion.
Considerations for International Buyers: Compliance with standards such as ASTM and EN is crucial. Buyers should ensure that the steel used meets local regulations, especially in regions with stringent safety requirements.
How Does Aluminum Perform in Pallet Racking Applications?
Aluminum is another viable option for pallet racking, particularly in environments where weight reduction is essential.
- Temperature Rating: Aluminum can perform well in both high and low temperatures, making it versatile for different climates.
- Corrosion Resistance: Naturally resistant to corrosion, aluminum is ideal for humid environments.
Pros: Lightweight and easy to assemble, aluminum racks can be relocated easily, making them suitable for dynamic warehouse environments.
Cons: Aluminum has a lower load capacity compared to steel, typically around 2,000 lbs per level, which may limit its use in heavy-duty applications. Additionally, it tends to be more expensive.
Impact on Application: Aluminum is particularly effective in industries that require frequent changes in layout or where space optimization is a priority.
Considerations for International Buyers: Buyers should verify that aluminum racks comply with local standards and assess the suitability for specific applications, especially in regions with varying regulatory requirements.
What are the Benefits of Using Composite Materials for Pallet Racking?
Composite materials, such as engineered wood or plastic, are gaining popularity in pallet racking systems.
- Temperature Rating: Composites can perform well in moderate temperature ranges but may not be suitable for extreme conditions.
- Corrosion Resistance: Many composite materials are resistant to moisture and decay, making them ideal for specific applications.
Pros: These materials are often lighter and can be more cost-effective than steel or aluminum. They also offer good aesthetic appeal.
Cons: The load capacity is generally lower, often around 1,500 lbs per level, which limits their use in heavy-duty settings. Additionally, they may require more maintenance over time.
Impact on Application: Composites are suitable for lighter loads and environments where aesthetics are important, such as retail spaces.
Considerations for International Buyers: Ensure compliance with local safety standards, particularly in regions with specific regulations regarding fire safety and material durability.
What Role Does Plastic Play in Pallet Racking Solutions?
Plastic is less common but can be used in specific applications, such as for lightweight or temporary storage solutions.
- Temperature Rating: Plastic can withstand a range of temperatures, but extreme heat may lead to deformation.
- Corrosion Resistance: Highly resistant to chemicals and moisture, making it suitable for various applications.
Pros: Plastic racks are lightweight and easy to clean, making them ideal for certain industries like food processing.
Cons: The load capacity is significantly lower, often around 1,000 lbs per level, which limits their use in heavy-duty environments. They are also less durable than metal options.
Impact on Application: Plastic racks are best suited for environments that require cleanliness and hygiene, such as laboratories or food storage.
Considerations for International Buyers: Buyers should ensure that plastic materials meet local health and safety regulations, especially in food-related applications.
Summary Table of Material Selection for Pallet Racking
Material | Typical Use Case for pallet racking | Key Advantage | Key Disadvantage/Limitation | Relative Cost (Low/Med/High) |
---|---|---|---|---|
Steel | Heavy-duty storage in warehouses | High load capacity and durability | Higher initial cost and complexity | High |
Aluminum | Dynamic environments requiring mobility | Lightweight and corrosion-resistant | Lower load capacity than steel | Medium |
Composite | Aesthetic applications or lighter loads | Cost-effective and visually appealing | Limited load capacity | Medium |
Plastic | Clean environments like food processing | Easy to clean and lightweight | Very low load capacity | Low |
This strategic material selection guide provides actionable insights for international B2B buyers, ensuring they make informed decisions that align with their operational needs and compliance requirements.
In-depth Look: Manufacturing Processes and Quality Assurance for pallet racking
What Are the Key Stages in the Manufacturing Process of Pallet Racking?
The manufacturing process of pallet racking is a multi-stage operation that ensures the durability and reliability of the final product. Understanding these stages can help international B2B buyers make informed purchasing decisions.
1. Material Preparation
The first step in the manufacturing process is the selection and preparation of raw materials. Common materials used in pallet racking include high-grade steel, which is favored for its strength and durability. Manufacturers typically source steel from certified suppliers to ensure quality.
Once the steel is acquired, it undergoes processes such as cutting and bending to prepare it for further shaping. The steel pieces are cut to specific lengths and widths according to the design specifications. This ensures consistency and accuracy in the final product.
2. Forming Techniques Used in Pallet Racking Production
Forming is a critical stage where the prepared materials are shaped into the components of the pallet racking system. Key techniques include:
-
Roll Forming: This process involves feeding flat steel into a series of rollers that progressively shape it into the desired profile. Roll forming is efficient for producing long sections of racking components, such as beams and uprights.
-
Welding: After forming, parts are welded together to create robust connections. Various welding methods, such as MIG and TIG welding, may be employed to ensure structural integrity.
-
Punching and Notching: These techniques are used to create holes and slots in the steel components, allowing for easy assembly and adjustment of shelves.
3. Assembly Process for Pallet Racking Systems
Once all components are formed, the assembly stage begins. This involves:
-
Pre-assembly: Components are temporarily fitted together to check for alignment and fit.
-
Final Assembly: The components are assembled into complete racking systems. This stage often includes the installation of accessories like wire decking, row spacers, and safety guards.
-
Quality Checks During Assembly: Manufacturers typically conduct quality checks at this stage to ensure that all parts meet specifications and standards.
4. Finishing Techniques for Enhanced Durability
The finishing process adds protective coatings to the assembled pallet racks. Common techniques include:
-
Powder Coating: This is a popular method that provides a durable, weather-resistant finish. It involves applying a powder that is then cured under heat to create a tough coating.
-
Galvanization: For environments prone to corrosion, galvanization is essential. The steel is coated with zinc to enhance its resistance to rust and chemical damage.
How Is Quality Assurance Implemented in Pallet Racking Manufacturing?
Quality assurance (QA) is critical in the manufacturing of pallet racking systems to ensure safety and performance standards are met. B2B buyers should be aware of the various quality assurance practices and international standards that manufacturers adhere to.
Relevant International Standards for Pallet Racking
Manufacturers often comply with several international standards to maintain quality and safety:
-
ISO 9001: This standard outlines a framework for quality management systems (QMS) and is widely adopted across industries. It emphasizes continuous improvement and customer satisfaction.
-
CE Marking: In Europe, CE marking indicates that a product meets EU safety, health, and environmental protection standards. This is particularly relevant for B2B buyers in Europe and ensures that the pallet racking systems are compliant with EU regulations.
-
American National Standards Institute (ANSI): In the United States, ANSI standards set guidelines for safety and performance, which can also be beneficial for international buyers.
What Are the Key QC Checkpoints in Pallet Racking Manufacturing?
Quality control (QC) is performed at various checkpoints throughout the manufacturing process:
-
Incoming Quality Control (IQC): This stage involves inspecting raw materials upon delivery to ensure they meet specified standards.
-
In-Process Quality Control (IPQC): During the manufacturing process, routine checks are conducted to verify that production methods and components adhere to quality standards.
-
Final Quality Control (FQC): After assembly, a comprehensive inspection is performed to ensure that the finished pallet racking systems meet all specifications and safety requirements.
Common Testing Methods for Pallet Racking Systems
Several testing methods are employed to ensure the quality and safety of pallet racking systems:
-
Load Testing: This involves applying weights to the racking system to ensure it can handle specified loads without failure.
-
Impact Testing: This assesses the structural integrity of the racking system under potential impact scenarios, which is crucial for safety.
-
Corrosion Resistance Testing: For coated systems, tests are conducted to ensure that finishes withstand environmental factors without degrading.
How Can B2B Buyers Verify Supplier Quality Control Practices?
International B2B buyers must take proactive steps to verify the quality control practices of their suppliers. Here are actionable strategies:
-
Supplier Audits: Conducting on-site audits of manufacturers can provide insights into their production processes, quality control measures, and adherence to international standards.
-
Requesting Quality Reports: Buyers should ask suppliers for detailed quality reports that document their manufacturing processes, quality checks, and any certifications obtained.
-
Third-Party Inspections: Engaging third-party inspection services can offer an unbiased assessment of the manufacturer’s capabilities and compliance with quality standards.
What Are the Quality Control and Certification Nuances for International B2B Buyers?
B2B buyers from Africa, South America, the Middle East, and Europe should be aware of certain nuances when it comes to quality control and certifications:
-
Regional Standards Variability: Different regions may have varying standards and certifications. Buyers should familiarize themselves with local regulations and compliance requirements.
-
Documentation Requirements: Ensure that all certifications and quality documentation are available in a language that is understandable and accessible.
-
Cultural Considerations: Understanding cultural differences in business practices can facilitate smoother negotiations and partnerships with manufacturers.
By comprehensively understanding the manufacturing processes and quality assurance measures for pallet racking systems, international B2B buyers can make informed decisions that align with their operational needs and compliance requirements.
Practical Sourcing Guide: A Step-by-Step Checklist for ‘pallet racking’
When sourcing pallet racking for your business, it’s vital to follow a systematic approach to ensure you meet your operational needs while optimizing costs. This guide provides a practical checklist tailored for international B2B buyers, especially those from Africa, South America, the Middle East, and Europe.
Step 1: Define Your Technical Specifications
Understanding your specific requirements is the first step in the sourcing process. Define the dimensions, load capacity, and configuration of the pallet racking systems needed based on your inventory types and storage space.
- Dimensions: Measure your warehouse space to determine the height, width, and depth of the racks.
- Load Capacity: Assess the weight of the pallets to ensure the racking can safely support them, keeping in mind future inventory growth.
Step 2: Research Different Types of Pallet Racking
There are various types of pallet racking systems available, each designed for specific needs. Research options such as selective, drive-in, and push-back racking.
- Selective Racking: Ideal for maximizing space while allowing easy access to each pallet.
- Drive-In Racking: Suitable for high-density storage but requires careful inventory management.
Step 3: Evaluate Potential Suppliers
Before committing, it’s crucial to vet suppliers thoroughly. Request company profiles, case studies, and references from buyers in a similar industry or region to ensure their reliability.
- Certifications: Verify if the supplier adheres to international safety and quality standards.
- Experience: Look for suppliers with proven experience in your specific market or region.
Step 4: Request Quotes and Compare Prices
Obtain quotes from multiple suppliers to understand the market rates. This will help you identify competitive pricing while ensuring you don’t compromise on quality.
- Cost Breakdown: Ask for a detailed quote that includes installation, delivery, and any additional accessories.
- Discounts: Inquire about bulk purchase discounts or financing options that may be available.
Step 5: Assess After-Sales Support and Warranty Options
A reliable after-sales support system is essential for maintenance and repairs. Check the warranty terms and the support offered by the supplier after installation.
- Warranty Duration: Look for warranties that cover both materials and workmanship.
- Support Services: Ensure the supplier provides installation support and ongoing maintenance services.
Step 6: Plan for Installation and Compliance
Once you’ve selected a supplier, plan for the installation of the pallet racking. Ensure that the installation complies with local safety regulations and standards.
- Professional Installation: Consider hiring professionals for installation to avoid safety risks and ensure compliance.
- Safety Training: Provide training for your staff on how to safely operate and maintain the racking systems.
Step 7: Monitor and Evaluate Performance
After installation, continuously monitor the performance of the pallet racking system. Gather feedback from your staff on its functionality and make adjustments as necessary.
- Inventory Management: Regularly assess how the racking system supports your inventory flow and make modifications to optimize space utilization.
- Safety Audits: Conduct periodic safety audits to ensure compliance with regulations and to identify any potential hazards.
By following this checklist, B2B buyers can streamline their sourcing process for pallet racking, ensuring they select the best systems to meet their operational needs while maximizing safety and efficiency.
Comprehensive Cost and Pricing Analysis for pallet racking Sourcing
What Are the Key Cost Components in Pallet Racking Sourcing?
When considering pallet racking sourcing, it is essential to understand the cost structure that influences overall pricing. The primary cost components include:
-
Materials: This is typically the largest component of the cost structure. Common materials used in pallet racking systems include steel and wire decking. The choice of materials significantly affects durability and price.
-
Labor: Labor costs encompass the wages for workers involved in manufacturing, assembly, and installation of the racking systems. Labor costs may vary based on the region and skill level required.
-
Manufacturing Overhead: This includes indirect costs such as utilities, rent for manufacturing facilities, and administrative expenses. Efficient manufacturing processes can reduce these costs, positively impacting pricing.
-
Tooling: Tooling costs refer to the expenses associated with the equipment and machinery used in production. Advanced machinery may lead to higher initial costs but can enhance efficiency and reduce long-term expenses.
-
Quality Control (QC): Ensuring the safety and reliability of pallet racking systems involves costs for quality assurance processes. Compliance with international safety standards can further increase these costs.
-
Logistics: This encompasses transportation and warehousing costs. Depending on the supplier’s location and the buyer’s destination, logistics can significantly influence the final price.
-
Margin: Suppliers typically add a profit margin to cover their operational costs and ensure profitability. This margin can vary widely depending on competition and market demand.
How Do Price Influencers Affect Pallet Racking Costs?
Several factors can influence the pricing of pallet racking systems:
-
Volume/MOQ (Minimum Order Quantity): Larger orders often qualify for discounts, making it more cost-effective to procure in bulk. Buyers should assess their storage needs to determine optimal order sizes.
-
Specifications and Customization: Custom-built solutions may incur additional costs. Buyers should clearly define their requirements to avoid unexpected expenses.
-
Materials and Quality Certifications: Higher-quality materials and certifications that comply with international safety standards often come with a higher price tag. Buyers must balance quality with budget constraints.
-
Supplier Factors: The reputation, reliability, and geographical location of suppliers can impact pricing. Established suppliers with a track record of quality and service may command higher prices.
-
Incoterms: Understanding Incoterms is crucial for international buyers. The chosen terms can affect shipping costs, responsibilities, and risks involved in the transaction.
What Buyer Tips Can Enhance Cost-Efficiency in Pallet Racking Sourcing?
To optimize costs in pallet racking sourcing, buyers should consider the following strategies:
-
Negotiation: Engage suppliers in discussions about pricing, especially for larger orders. Leverage competitive quotes from multiple suppliers to negotiate better terms.
-
Total Cost of Ownership (TCO): Evaluate not just the purchase price but the overall TCO, which includes installation, maintenance, and potential replacement costs. A cheaper initial price may lead to higher long-term expenses if quality is compromised.
-
Pricing Nuances for International Buyers: Buyers from Africa, South America, the Middle East, and Europe should be aware of currency fluctuations and import duties that can significantly affect the total cost. Additionally, understanding local market conditions can lead to better sourcing decisions.
-
Supplier Relationships: Building long-term relationships with suppliers can lead to better pricing, priority service, and insights into new products or technologies.
Conclusion: Understanding the Indicative Prices for Pallet Racking
Prices for pallet racking systems can vary significantly based on the above factors. For example, standard pallet racks can range from $400 to over $800 depending on size, material, and features. It is important for buyers to conduct thorough market research and consider all cost components to make informed purchasing decisions. Always consult with suppliers for the most accurate and current pricing, as this content serves only as a general guideline.
Alternatives Analysis: Comparing pallet racking With Other Solutions
Understanding Alternatives to Pallet Racking
When it comes to optimizing warehouse storage, pallet racking is a popular choice for many businesses. However, several alternative solutions may better suit specific operational needs, especially for international B2B buyers in diverse markets such as Africa, South America, the Middle East, and Europe. Understanding the advantages and disadvantages of each option can help businesses make informed decisions about their storage systems.
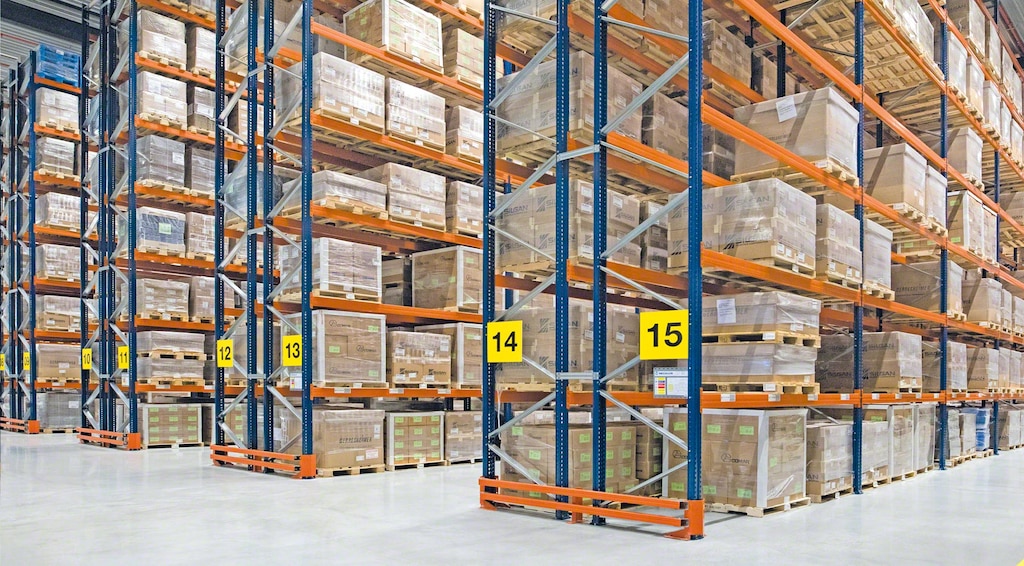
A stock image related to pallet racking.
Comparison Table: Pallet Racking vs. Alternatives
Comparison Aspect | Pallet Racking | Mobile Shelving Units | Vertical Lift Modules |
---|---|---|---|
Performance | High load capacity (up to 5,000 lbs/level) | Moderate load capacity, optimized for space | High density storage, automated retrieval |
Cost | Moderate initial investment, quick ROI | Higher initial cost due to automation | High investment, but reduces labor costs over time |
Ease of Implementation | Easy to assemble and customize | Requires professional installation | Complex installation, needs space planning |
Maintenance | Low maintenance, easy to inspect | Moderate maintenance, mechanical parts may wear | Requires regular servicing for automation |
Best Use Case | General warehousing, heavy loads | Limited space environments, high turnover items | Automated warehouses, high-density storage needs |
What Are the Benefits and Drawbacks of Mobile Shelving Units?
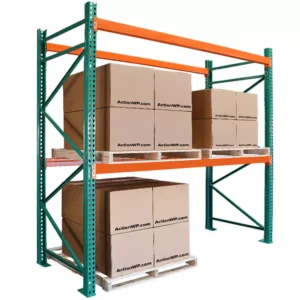
A stock image related to pallet racking.
Mobile shelving units are an excellent alternative for businesses with limited space. These units are designed to move on tracks, allowing users to access only the aisles they need at any given time, maximizing available space. The primary advantage is their ability to store a significant number of items in a compact area, which can lead to a reduced footprint and lower rent costs. However, the initial investment is typically higher, and they may require professional installation. Additionally, while they improve space efficiency, they may not support the same weight as traditional pallet racking.
How Do Vertical Lift Modules Enhance Warehouse Efficiency?
Vertical lift modules (VLMs) are an automated storage solution that utilizes vertical space to store items. These systems are particularly advantageous for companies that prioritize speed and efficiency in their inventory management. VLMs retrieve items automatically, which can significantly reduce the time employees spend searching for products. However, the investment required for VLMs can be substantial, making them less accessible for smaller businesses or those with limited budgets. Furthermore, they require careful planning and space consideration during installation.
Conclusion: How Can B2B Buyers Choose the Right Storage Solution?
Selecting the right storage solution depends on various factors, including budget, available space, and specific operational needs. For businesses with heavy loads and ample space, pallet racking remains a strong contender due to its cost-effectiveness and scalability. However, for companies facing space constraints, mobile shelving units may provide a more efficient alternative. On the other hand, businesses focused on automation and high-density storage might find vertical lift modules to be the best fit despite the higher investment. By carefully evaluating these alternatives, B2B buyers can choose a storage solution that aligns with their operational goals and financial capabilities.
Essential Technical Properties and Trade Terminology for pallet racking
What Are the Key Technical Properties of Pallet Racking?
When selecting pallet racking systems, understanding the essential technical properties is crucial for ensuring efficient storage and safety in your warehouse operations. Here are some critical specifications to consider:
1. Material Grade
Pallet racks are typically made from steel, which can vary in grade. Higher-grade steel offers increased strength and durability, essential for supporting heavy loads. For B2B buyers, investing in high-grade materials can reduce maintenance costs and enhance the longevity of the racking system, making it a cost-effective choice over time.
2. Load Capacity
Load capacity refers to the maximum weight each shelf can hold. This is usually measured in pounds per pair of beams. For instance, many pallet racks can support up to 5,000 lbs per pair. Understanding the load capacity is vital for ensuring that the racking system can accommodate your inventory without risk of collapse, thereby ensuring workplace safety and operational efficiency.
3. Beam Height and Levels
The height of the beams and the number of levels in a pallet racking system can greatly affect storage density. Common beam heights range from 3.5 inches to 6 inches, with various configurations allowing for multiple levels. B2B buyers should assess their vertical storage needs, as optimizing space can lead to significant cost savings in warehousing.
4. Tolerance
Tolerance in pallet racking refers to the allowable deviation in dimensions during manufacturing. A tighter tolerance often indicates better quality control, resulting in a more stable and safer racking system. For B2B buyers, selecting racks with precise tolerances can prevent misalignment issues that could jeopardize safety and efficiency.
5. Powder Coating
Many pallet racks come with a powder-coated finish that enhances resistance to corrosion and scratches. This feature is particularly important in environments where humidity or exposure to chemicals is a concern. Investing in powder-coated racks can lead to lower maintenance costs and prolonged system life, making it a wise choice for B2B buyers.
What Are Common Trade Terms in Pallet Racking?
Navigating the world of pallet racking involves understanding specific trade terminology that can affect purchasing decisions. Here are some key terms every buyer should know:
1. OEM (Original Equipment Manufacturer)
An OEM produces parts or equipment that are sold by another company under its brand. When purchasing pallet racks, understanding whether you are buying directly from an OEM or a distributor can impact pricing and warranty considerations.
2. MOQ (Minimum Order Quantity)
MOQ refers to the minimum number of units a supplier is willing to sell. For international buyers, knowing the MOQ can help in budgeting and logistics planning. It’s essential to balance your inventory needs with the supplier’s requirements to avoid excess costs.
3. RFQ (Request for Quotation)
An RFQ is a formal document used to solicit price quotes from suppliers. For B2B buyers, issuing an RFQ allows for comparison of pricing, lead times, and terms from multiple vendors, enabling informed purchasing decisions.
4. Incoterms (International Commercial Terms)
Incoterms are a set of international rules that define the responsibilities of buyers and sellers regarding shipping and freight. Understanding these terms can help buyers from different regions, such as Africa and South America, navigate logistics and reduce risks associated with international trade.
5. Lead Time
Lead time is the amount of time from placing an order to receiving the product. For businesses that rely heavily on timely inventory management, understanding lead times is crucial for maintaining operational efficiency and customer satisfaction.
6. Customization
Customization refers to the ability to tailor pallet racking solutions to specific business needs, such as unique dimensions or additional features. B2B buyers should consider customization options to optimize their storage solutions for specific operational requirements.
In summary, grasping the essential technical properties and trade terminology related to pallet racking is vital for making informed purchasing decisions. By understanding these aspects, international B2B buyers can enhance their warehouse operations while ensuring safety and efficiency.
Navigating Market Dynamics and Sourcing Trends in the pallet racking Sector
What Are the Current Market Dynamics and Key Trends in the Pallet Racking Sector?
The pallet racking market is evolving rapidly, driven by the increasing demands of e-commerce, automation, and the need for efficient inventory management. Global trends indicate a shift towards modular and customizable pallet racking systems that can adapt to diverse warehouse environments, especially in emerging markets like Africa and South America. As businesses expand their operations, the requirement for scalable storage solutions becomes critical. In regions such as the Middle East and Turkey, investments in logistics and infrastructure are propelling demand for high-density storage systems, which can maximize warehouse space.
Technological advancements are also reshaping the sourcing landscape. Automated storage and retrieval systems (ASRS) and Internet of Things (IoT) integrations enable real-time inventory tracking and enhance operational efficiency. International B2B buyers should consider suppliers that offer innovative solutions, such as adjustable racking systems and advanced safety features, to meet their unique operational needs. Moreover, the rise of online platforms for sourcing equipment allows buyers from different regions to access a broader range of suppliers, fostering competitive pricing and improved negotiation terms.
How Is Sustainability Reshaping B2B Sourcing for Pallet Racking?
Sustainability is becoming a non-negotiable aspect of B2B sourcing in the pallet racking sector. As businesses face increasing scrutiny regarding their environmental impact, the demand for sustainable practices and materials is on the rise. Buyers are now prioritizing suppliers that utilize recycled materials and environmentally-friendly production processes. For instance, pallet racks made from steel, which can be recycled at the end of their life cycle, are gaining popularity.
Ethical sourcing is also pivotal. Companies are expected to maintain transparency throughout their supply chains, ensuring that materials are sourced responsibly. Certifications such as the Forest Stewardship Council (FSC) for wood products and ISO 14001 for environmental management systems are increasingly sought after by international buyers. By aligning with suppliers that adhere to these standards, businesses can enhance their brand reputation while contributing positively to the environment.
What Is the Historical Context of Pallet Racking Development?
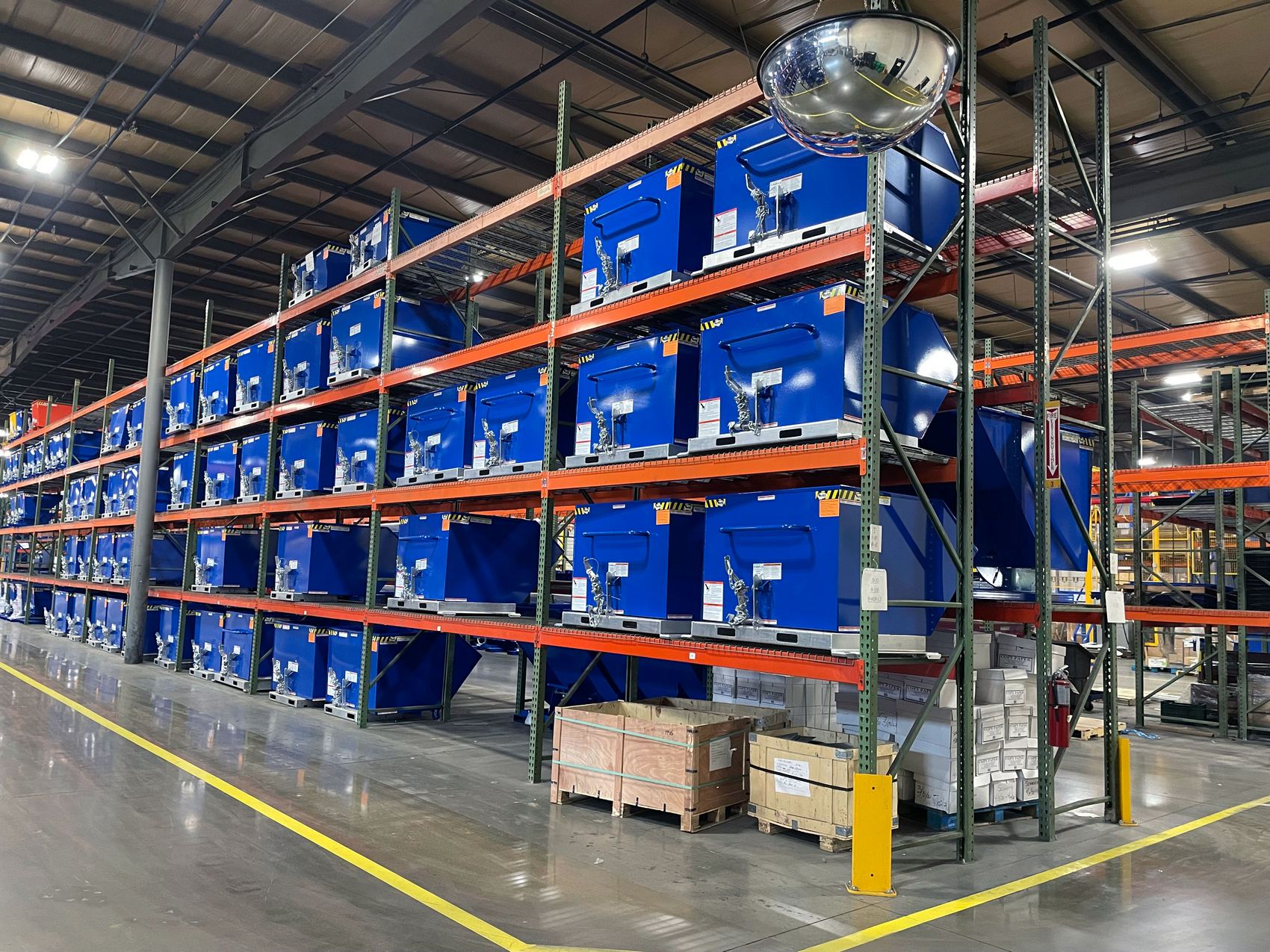
A stock image related to pallet racking.
The evolution of pallet racking systems dates back to the mid-20th century when the need for efficient warehouse storage solutions began to grow alongside industrialization. Initially, simple wooden shelves were used, but as logistics and inventory management became more complex, the demand for robust metal racking systems surged. The introduction of standardized pallet sizes and the development of various racking types, such as selective, drive-in, and push-back racking, allowed for greater flexibility and efficiency in storage.
Today, pallet racking continues to evolve with advancements in technology and a growing focus on sustainability, making it a crucial element in modern supply chains. For international B2B buyers, understanding this historical context can provide valuable insights into current market offerings and future trends. By leveraging this knowledge, buyers can make informed decisions that align with their operational goals and sustainability commitments.
Frequently Asked Questions (FAQs) for B2B Buyers of pallet racking
-
How do I solve the issue of limited warehouse space with pallet racking?
To maximize limited warehouse space, consider investing in adjustable pallet racking systems. These systems allow you to customize the height and width of the racks based on your specific storage needs. Additionally, utilizing multi-tiered racking can effectively increase vertical storage without expanding your footprint. Implementing a FIFO (First In, First Out) inventory management system can also enhance space efficiency by ensuring that older stock is used first, reducing clutter. -
What is the best pallet racking system for heavy loads?
For heavy loads, selective pallet racking is often the best choice due to its robust construction and ability to handle substantial weight, typically up to 5,000 lbs per level. Teardrop racking systems are particularly popular, offering easy assembly and the flexibility to adjust shelf heights. Consider the load capacity of your products and the specific dimensions of your warehouse to ensure optimal safety and efficiency. -
How can I assess the reliability of a pallet racking supplier?
To assess the reliability of a pallet racking supplier, start by checking their industry reputation through online reviews and testimonials. Verify their certifications, such as compliance with safety standards like ANSI/RMI or SEMA. Request references from previous clients and evaluate their experience with international shipments, especially if you are sourcing from regions like Europe or South America. Additionally, inquire about their customer service and after-sales support to ensure ongoing assistance. -
What are the typical payment terms for international pallet racking purchases?
Payment terms for international pallet racking purchases often vary by supplier but typically include options such as a letter of credit, advance payment, or net 30/60 terms. It’s crucial to negotiate terms that align with your cash flow management while ensuring protection against potential risks. Always review the supplier’s payment policy and consider using escrow services for larger transactions to secure your investment until the goods are received and inspected. -
How can I customize pallet racking to fit my specific business needs?
Customization options for pallet racking include adjusting height, width, and load capacity to accommodate specific products. Many suppliers offer additional accessories like wire decking, column protectors, and row spacers to enhance functionality. When discussing your requirements with suppliers, provide detailed information about your inventory types and storage processes to ensure the proposed solutions meet your operational needs effectively. -
What is the minimum order quantity (MOQ) for pallet racking systems?
The minimum order quantity (MOQ) for pallet racking systems can vary significantly based on the supplier and the type of racking. While some suppliers may allow single-unit purchases, others might require bulk orders to offer competitive pricing. When sourcing internationally, it’s advisable to discuss your needs upfront to negotiate favorable terms and avoid overcommitting to large quantities that may not align with your immediate requirements. -
What quality assurance measures should I look for when sourcing pallet racking?
When sourcing pallet racking, ensure the supplier has a robust quality assurance process in place. Look for certifications such as ISO 9001, which indicates adherence to quality management standards. Request documentation of load testing and safety inspections to confirm the racking meets required standards. Additionally, inquire about warranties and return policies, which can provide further assurance of product quality and reliability. -
How can I manage logistics when importing pallet racking from abroad?
To effectively manage logistics when importing pallet racking, collaborate closely with your supplier to understand shipping timelines and methods. Choose a reliable freight forwarder familiar with customs regulations in your country to streamline the import process. Ensure that all necessary documentation, such as bills of lading and commercial invoices, is prepared accurately to avoid delays. It’s also beneficial to plan for storage upon arrival to facilitate smooth unloading and installation.
Important Disclaimer & Terms of Use
⚠️ Important Disclaimer
The information provided in this guide, including content regarding manufacturers, technical specifications, and market analysis, is for informational and educational purposes only. It does not constitute professional procurement advice, financial advice, or legal advice.
While we have made every effort to ensure the accuracy and timeliness of the information, we are not responsible for any errors, omissions, or outdated information. Market conditions, company details, and technical standards are subject to change.
B2B buyers must conduct their own independent and thorough due diligence before making any purchasing decisions. This includes contacting suppliers directly, verifying certifications, requesting samples, and seeking professional consultation. The risk of relying on any information in this guide is borne solely by the reader.
Strategic Sourcing Conclusion and Outlook for pallet racking
How Can Strategic Sourcing Enhance Your Pallet Racking Solutions?
In summary, strategic sourcing for pallet racking systems is essential for B2B buyers looking to optimize warehouse efficiency and inventory management. By understanding the diverse range of pallet racking options available—from selective to drive-in systems—buyers can tailor their storage solutions to their specific operational needs. The ability to adapt and scale these systems can significantly enhance logistics performance, particularly in regions experiencing rapid economic growth, such as Africa and South America.
Investing in high-quality pallet racks not only ensures safety under heavy loads but also promotes excellent stock control and fast return on investment (ROI). As international buyers navigate the complexities of sourcing, it’s crucial to prioritize suppliers who offer flexibility, reliability, and comprehensive support.
What’s Next for International B2B Buyers?
As you embark on your pallet racking procurement journey, consider leveraging the insights gained from this guide to make informed decisions. Engage with suppliers who understand the unique challenges of your market, whether in the Middle East or Europe, and explore innovative solutions that align with your business objectives. Embrace strategic sourcing as a pathway to enhance your operational capabilities and position your business for future growth.