Streamline Operations: The Ultimate Palletizing Robot Guide (2025)
Introduction: Navigating the Global Market for palletizing robot
Navigating the complexities of sourcing a palletizing robot can be daunting for international B2B buyers, especially in diverse markets across Africa, South America, the Middle East, and Europe. With varying local regulations, technological standards, and supplier landscapes, the challenge lies in identifying a solution that not only meets operational needs but also aligns with budget constraints and efficiency goals. This guide serves as a comprehensive resource, covering essential aspects such as types of palletizing robots, their applications across different industries, and critical factors for supplier vetting.
In this guide, buyers will explore the distinct categories of palletizing robots, from high-speed systems designed for rapid throughput to collaborative robots that work alongside human operators. Additionally, we delve into the importance of understanding total cost of ownership, including initial investment, maintenance, and potential return on investment. By offering actionable insights and strategies for making informed purchasing decisions, this guide empowers businesses to enhance their operations and streamline logistics processes.
Ultimately, this resource aims to demystify the palletizing robot market, providing B2B buyers with the knowledge needed to select the right technology and supplier for their unique requirements. Whether you are based in the UAE, Turkey, or any other region, understanding these dynamics will position your business for success in an increasingly automated world.
Understanding palletizing robot Types and Variations
Type Name | Key Distinguishing Features | Primary B2B Applications | Brief Pros & Cons for Buyers |
---|---|---|---|
High-Speed Palletizers | Fast cycle times, optimized for medium payloads (up to 40 kg) | Food and beverage, consumer goods | Pros: Increased throughput; Cons: Higher initial cost. |
Heavy-Duty Palletizers | Supports payloads from 120 kg to 1,300 kg, robust design | Manufacturing, logistics, automotive | Pros: Handles heavy loads; Cons: Requires more space. |
Collaborative Robots (Cobots) | Designed for safe human interaction, easy to program and deploy | Small to medium-sized enterprises | Pros: Flexible, safe; Cons: Lower payload capacity. |
Custom Robotic Systems | Tailored solutions for specific applications, advanced technology | Niche markets, specialized industries | Pros: Fully optimized for specific tasks; Cons: Longer lead time. |
Mobile Palletizing Robots | Portable design, can be moved between locations | Warehousing, distribution centers | Pros: Versatile and space-saving; Cons: May have limited payload capacity. |
What Are the Characteristics of High-Speed Palletizers?
High-speed palletizers are engineered for rapid operation, typically achieving cycle times of up to 56 cycles per minute. They are ideal for medium payloads, making them a perfect fit for industries such as food and beverage, where efficiency is crucial. When considering a high-speed palletizer, B2B buyers should evaluate their production volume, as these systems can significantly enhance throughput. However, the initial investment can be substantial, necessitating a careful cost-benefit analysis.
How Do Heavy-Duty Palletizers Stand Out?
Heavy-duty palletizers are built to handle substantial payloads ranging from 120 kg to 1,300 kg. Their robust design makes them suitable for demanding applications in manufacturing, logistics, and the automotive sector. B2B buyers should consider their space constraints, as these machines often require a larger footprint. While they offer exceptional load handling capabilities, the higher upfront costs and maintenance needs must also be factored into the purchasing decision.
Why Choose Collaborative Robots (Cobots)?
Collaborative robots, or cobots, are designed for safe interaction with human workers, making them an excellent choice for small to medium-sized enterprises. Their ease of programming and deployment allows for quick integration into existing workflows. Buyers should assess their specific operational needs, as cobots typically have lower payload capacities compared to traditional palletizers. However, their flexibility and safety features can lead to significant productivity gains in environments where human oversight is necessary.
What Are the Advantages of Custom Robotic Systems?
Custom robotic systems provide tailored solutions for unique operational challenges, utilizing advanced technology to optimize performance. These systems are particularly beneficial in niche markets and specialized industries where standard solutions may not suffice. B2B buyers should be prepared for a longer lead time, as custom solutions require detailed planning and design. While they can offer unparalleled efficiency for specific tasks, the investment may be higher compared to off-the-shelf options.
How Do Mobile Palletizing Robots Enhance Flexibility?
Mobile palletizing robots are designed for portability, allowing them to be easily moved between different areas of a facility. This adaptability makes them ideal for warehousing and distribution centers that require flexibility in their operations. Buyers should consider the trade-offs, as mobile robots may come with limited payload capacities. However, their space-saving designs and versatility can lead to improved operational efficiency, particularly in environments facing fluctuating demands.
Key Industrial Applications of palletizing robot
Industry/Sector | Specific Application of palletizing robot | Value/Benefit for the Business | Key Sourcing Considerations for this Application |
---|---|---|---|
Food and Beverage | High-speed palletizing of packaged goods | Increased throughput, reduced labor costs, and minimized risk of contamination. | Need for hygiene compliance, temperature resistance, and energy efficiency. |
Consumer Goods | Mixed palletizing for varied product sizes | Enhanced flexibility in production lines and optimized space utilization. | Customization options for grippers and adaptability to product variations. |
Pharmaceuticals | Precise palletizing for sensitive products | Improved accuracy in order fulfillment and compliance with regulations. | Consideration for cleanroom standards and robotic integration with existing systems. |
Logistics and Warehousing | Automated palletizing for shipping and storage | Streamlined operations, reduced handling time, and increased accuracy in inventory management. | Scalability of the system and compatibility with existing warehouse management systems. |
Automotive | Heavy load palletizing for parts and components | Enhanced efficiency in assembly lines and reduced downtime. | Robustness of the robotic system to handle heavy payloads and integration with conveyor systems. |
What are the Key Industrial Applications of Palletizing Robots?
How are palletizing robots used in the Food and Beverage Industry?
In the food and beverage sector, palletizing robots are employed to automate the stacking of packaged goods onto pallets for storage and shipping. They address challenges such as high-volume production, labor shortages, and hygiene standards. Buyers in this industry should prioritize robots that meet food safety regulations, have easy-to-clean designs, and can operate in cold storage environments to ensure product integrity.
What role do palletizing robots play in Consumer Goods?
Palletizing robots in consumer goods manufacturing facilitate mixed palletizing, where different product sizes and shapes are stacked on the same pallet. This flexibility allows businesses to respond quickly to market demands while optimizing warehouse space. International buyers should consider the robot’s adaptability to various product types and the availability of customizable grippers to handle diverse packaging formats.
Why are palletizing robots crucial for Pharmaceuticals?
In the pharmaceutical industry, palletizing robots are essential for accurately stacking sensitive products such as vials and medications. They help improve order accuracy and compliance with strict regulatory standards. Buyers need to ensure that the robots are designed for cleanroom environments and can integrate seamlessly with existing packaging and distribution systems to maintain product safety and efficacy.
How do palletizing robots enhance Logistics and Warehousing operations?
Palletizing robots are increasingly used in logistics and warehousing to automate the loading and unloading of goods. They reduce manual handling, streamline operations, and improve inventory accuracy. For B2B buyers, it is crucial to assess the scalability of the palletizing system and its compatibility with current warehouse management systems to ensure a smooth transition and ongoing efficiency.
What advantages do palletizing robots provide in the Automotive sector?
In automotive manufacturing, palletizing robots are used to handle heavy loads of parts and components efficiently. They enhance production line efficiency by reducing manual labor and minimizing downtime. Buyers should focus on the robot’s capability to manage heavy payloads and its integration potential with existing conveyor systems to optimize workflow and productivity.
3 Common User Pain Points for ‘palletizing robot’ & Their Solutions
Scenario 1: Integration Challenges with Existing Systems
The Problem: Many B2B buyers, particularly in manufacturing and logistics, face significant challenges when integrating new palletizing robots into their existing systems. The complexities arise from outdated machinery, incompatible software, or the sheer scale of operations that require a tailored approach. For instance, a company may have a legacy conveyor system that does not support modern robotic interfaces, leading to potential downtime and increased costs during the transition phase.
The Solution: To effectively overcome integration challenges, start by conducting a thorough audit of your current systems. Collaborate with the palletizing robot supplier to identify the compatibility of their technology with your existing infrastructure. Seek solutions that offer modular designs and flexible programming options, allowing for easier integration. For instance, companies like KUKA provide detailed documentation and support for integrating their robots into various environments. Additionally, consider investing in simulation software to visualize the integration process before implementation. This proactive approach can save time and reduce errors, ensuring a smoother transition and maximizing your return on investment.
Scenario 2: High Initial Investment and Cost Justification
The Problem: The upfront cost of purchasing and installing palletizing robots can be daunting for B2B buyers, especially in regions where capital is limited or operational budgets are tight. Companies may struggle to justify the investment, fearing that the return on investment (ROI) may not materialize quickly enough. This is particularly true in emerging markets in Africa and South America, where businesses often operate on slimmer margins.
The Solution: To address this financial concern, it’s crucial to develop a clear and comprehensive business case that outlines the long-term benefits of palletizing robots. Begin by analyzing current operational costs associated with manual palletizing, such as labor, errors, and inefficiencies. Use this data to project potential savings and productivity improvements. Suppliers like MMCI Automation offer financing options, such as leasing or phased payment plans, which can alleviate immediate cash flow concerns. Furthermore, consider pilot projects or incremental automation, where you can start with a single robotic unit and scale as you see the benefits. This strategy not only reduces initial financial strain but also allows for a more measured evaluation of ROI.
Scenario 3: Maintenance and Downtime Concerns
The Problem: Maintenance and potential downtime associated with robotic systems can be significant pain points for B2B buyers. Companies worry about the reliability of palletizing robots, fearing that unexpected breakdowns could disrupt production schedules and lead to substantial financial losses. This concern is especially pronounced in industries with high throughput demands, such as food and beverage or pharmaceuticals.
The Solution: To mitigate maintenance concerns, select palletizing robots known for their durability and low maintenance needs. For example, KUKA’s palletizing systems are designed with long-wear components, reducing the frequency of required maintenance. Additionally, work with suppliers that offer comprehensive training programs for your staff, ensuring that your team is equipped to perform routine checks and minor repairs. Investing in predictive maintenance technologies can also provide early warnings for potential issues, allowing for proactive measures before a breakdown occurs. Creating a strong relationship with your supplier for ongoing support and parts availability will further enhance your operational reliability. By taking these steps, you can significantly reduce downtime and maintain continuous productivity.
Strategic Material Selection Guide for palletizing robot
What are the Key Materials Used in Palletizing Robots?
When selecting a palletizing robot, the choice of materials plays a crucial role in determining performance, durability, and overall operational efficiency. Below, we analyze four common materials used in the construction of palletizing robots, focusing on their properties, advantages, disadvantages, and considerations for international B2B buyers.
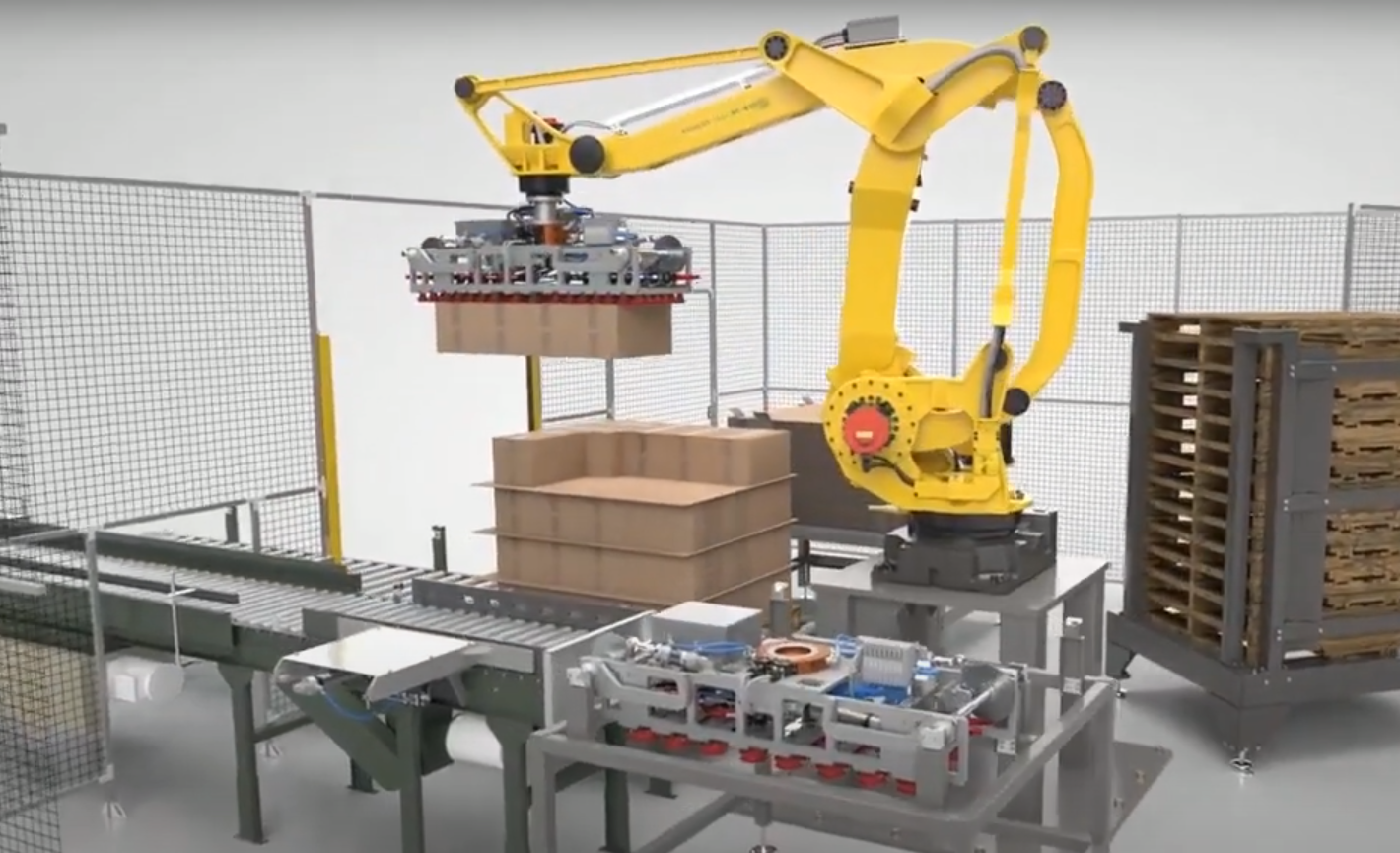
A stock image related to palletizing robot.
How Does Steel Impact the Performance of Palletizing Robots?
Key Properties: Steel is known for its high tensile strength and durability, making it suitable for heavy-duty applications. It can withstand high temperatures and pressures, and its corrosion resistance can be enhanced with coatings.
Pros & Cons: The primary advantage of steel is its strength and longevity, which reduces the need for frequent replacements. However, it is heavier than other materials, which can affect the robot’s speed and agility. Additionally, the manufacturing process can be complex and costly.
Impact on Application: Steel is ideal for environments where heavy loads are common, such as in the automotive and construction industries. Its robustness allows it to handle various media, including heavy boxes and pallets.
Considerations for International Buyers: Compliance with standards such as ASTM and DIN is essential, especially in Europe and the Middle East. Buyers should also consider the availability of high-quality steel in their region to avoid delays in procurement.
What Role Does Aluminum Play in Palletizing Robot Design?
Key Properties: Aluminum is lightweight and has good corrosion resistance, making it suitable for applications where mobility is essential. It can also be anodized to enhance its protective qualities.
Pros & Cons: The lightweight nature of aluminum allows for faster operation of the robot, which can improve throughput. However, it is less durable than steel, which may lead to higher maintenance costs in the long run.
Impact on Application: Aluminum is commonly used in food and beverage industries where hygiene and weight are critical. Its resistance to corrosion makes it suitable for environments with moisture.
Considerations for International Buyers: Buyers in regions with high humidity, like parts of South America and the Middle East, should prioritize aluminum options. Compliance with food safety standards is also crucial in these markets.
Why is Plastic Used in Certain Palletizing Robot Components?
Key Properties: Engineering plastics are lightweight, have good chemical resistance, and can be molded into complex shapes. They are also non-corrosive and can withstand various temperatures.
Pros & Cons: The main advantage of plastic is its versatility and ease of manufacturing, which can lead to lower costs. However, plastics may not support heavy loads as effectively as metals, limiting their use in high-capacity applications.
Impact on Application: Plastic components are often used in grippers and other non-structural parts of palletizing robots, particularly in industries like consumer goods where weight and handling are critical.
Considerations for International Buyers: Buyers should ensure that the plastics used comply with local environmental regulations and standards, especially in Europe, where sustainability is a significant concern.
How Does Composite Material Enhance Palletizing Robots?
Key Properties: Composites combine materials like carbon fiber and resin to create a lightweight yet strong structure. They offer excellent fatigue resistance and can be tailored for specific applications.
Pros & Cons: Composites provide high strength-to-weight ratios, making them ideal for high-speed applications. However, they can be more expensive and complex to manufacture compared to traditional materials.
Impact on Application: Composites are well-suited for high-speed palletizing robots in industries like electronics and pharmaceuticals, where precision and speed are paramount.
Considerations for International Buyers: Buyers should be aware of the availability of composite materials in their regions, as well as any specific certifications required for their applications.
Summary of Material Selection for Palletizing Robots
Material | Typical Use Case for palletizing robot | Key Advantage | Key Disadvantage/Limitation | Relative Cost (Low/Med/High) |
---|---|---|---|---|
Steel | Heavy-duty applications (automotive, construction) | High strength and durability | Heavy weight affects speed | High |
Aluminum | Food and beverage industries | Lightweight and corrosion-resistant | Less durable than steel | Medium |
Plastic | Grippers and non-structural components | Versatile and cost-effective | Limited load capacity | Low |
Composite | High-speed applications (electronics, pharmaceuticals) | High strength-to-weight ratio | Expensive and complex to manufacture | High |
This strategic material selection guide provides international B2B buyers with critical insights into the materials used in palletizing robots, enabling informed decisions based on their specific operational needs and regional considerations.
In-depth Look: Manufacturing Processes and Quality Assurance for palletizing robot
What Are the Main Manufacturing Processes for Palletizing Robots?
Manufacturing palletizing robots involves a series of well-coordinated stages designed to ensure efficiency and quality. The main stages include material preparation, forming, assembly, and finishing. Each stage utilizes specific techniques and technologies to produce robots that meet industrial standards and customer requirements.
How Is Material Prepared for Palletizing Robots?
The first step in the manufacturing process is material preparation. This involves sourcing high-quality raw materials, such as metals and plastics, which are critical for the robot’s structural integrity and performance. Suppliers typically perform material testing to verify that the materials meet necessary specifications.
Once sourced, materials undergo cutting and shaping processes using advanced machinery like laser cutters and CNC machines. These technologies ensure precise dimensions and tolerances that are essential for the robot’s assembly and functionality.
What Forming Techniques Are Used in Palletizing Robot Production?
The forming stage involves converting raw materials into usable components. This may include processes such as stamping, forging, and injection molding. Each technique is chosen based on the specific part being produced:
- Stamping: Commonly used for metal components, stamping allows for the mass production of identical parts with high precision.
- Forging: This method enhances the strength of metal components through deformation, making it suitable for load-bearing parts of the robot.
- Injection Molding: Utilized for producing plastic components, this technique enables complex shapes and designs that are lightweight yet durable.
These forming techniques ensure that the components can withstand the operational demands of palletizing tasks, such as heavy lifting and rapid movements.
What Happens During the Assembly of Palletizing Robots?
The assembly stage is where the individual components come together to form a complete robot. This process typically involves several key steps:
- Sub-assembly: Components are first assembled into smaller units, such as robotic arms and control systems. This helps streamline the final assembly process.
- Integration of Electronics: Advanced electronics, including sensors and controllers, are integrated into the robot. This stage is crucial for enabling the robot to perform complex tasks and respond to real-time data.
- Testing During Assembly: As components are assembled, initial testing is conducted to ensure each part functions correctly. This might include mechanical tests to check for movement precision and electronic tests for system responsiveness.
By conducting these tests during assembly, manufacturers can identify and rectify issues early in the process, reducing the risk of failures later on.
How Is the Finishing Process Handled for Palletizing Robots?
The finishing stage involves several processes aimed at enhancing the robot’s aesthetics and durability. This includes:
- Surface Treatment: Techniques such as powder coating or anodizing are applied to protect against corrosion and wear. These treatments also improve the robot’s visual appeal.
- Final Assembly and Calibration: After surface treatments, the robots undergo final assembly, where all components are brought together. Calibration is performed to ensure that the robot operates within specified parameters.
- Quality Assurance Checks: Final inspections are conducted to verify that the robot meets all design specifications and operational standards.
This meticulous attention to finishing is vital for ensuring longevity and reliability in demanding environments.
What Quality Assurance Standards Are Relevant for Palletizing Robots?
Quality assurance is critical in the manufacturing of palletizing robots to ensure they meet international standards and customer expectations. Several key standards are relevant:
- ISO 9001: This international standard outlines the criteria for a quality management system (QMS). Manufacturers must demonstrate their ability to consistently provide products that meet customer and regulatory requirements.
- CE Marking: For products sold in Europe, CE marking indicates compliance with health, safety, and environmental protection standards.
- API Standards: For robots used in specific industries like oil and gas, adherence to API standards ensures that the equipment can operate safely and efficiently in those environments.
These standards not only enhance product quality but also provide buyers with assurance regarding the reliability and safety of the robots.
What Are the Key Quality Control Checkpoints in Palletizing Robot Manufacturing?
Quality control (QC) is integrated into various stages of the manufacturing process, with specific checkpoints established to maintain high standards:
- Incoming Quality Control (IQC): This initial checkpoint involves inspecting raw materials and components upon arrival. Any defective materials are rejected, ensuring that only quality inputs enter the production line.
- In-Process Quality Control (IPQC): Throughout the assembly process, random inspections and tests are conducted to verify that components meet specifications. This proactive approach helps catch defects early, reducing waste and rework.
- Final Quality Control (FQC): Once the robot is fully assembled, comprehensive testing is performed to assess functionality, safety, and compliance with relevant standards. This includes load testing, precision checks, and operational simulations.
By implementing these QC checkpoints, manufacturers can ensure that their palletizing robots consistently meet quality expectations.
How Can B2B Buyers Verify Supplier Quality Control Processes?
International B2B buyers must ensure that their suppliers adhere to stringent quality control processes. Here are some actionable insights for verifying supplier QC:
-
Conduct Audits: Regular audits of suppliers can reveal their adherence to quality standards and manufacturing processes. Buyers should assess the supplier’s QMS and ensure compliance with ISO 9001 and other relevant standards.
-
Request Quality Reports: Suppliers should provide documentation, including inspection reports and certifications, to prove compliance with international standards. This transparency helps buyers assess the supplier’s commitment to quality.
-
Engage Third-Party Inspectors: Utilizing third-party inspection services can provide an unbiased assessment of the supplier’s manufacturing processes and quality control measures. This is particularly beneficial for buyers from regions with less rigorous local standards.
-
Evaluate Certifications: Buyers should verify that suppliers possess relevant certifications, such as CE marking or API standards. These certifications indicate that the supplier’s products meet recognized international safety and quality benchmarks.
-
Assess Supplier Reputation: Researching the supplier’s track record in the industry can provide insights into their reliability and commitment to quality. Reviews and testimonials from previous clients can be valuable indicators.
By following these steps, B2B buyers can ensure they partner with reputable suppliers who prioritize quality in their manufacturing processes. This diligence is particularly crucial for international buyers from diverse regions, ensuring that their investments in palletizing robots yield reliable and effective solutions.
Practical Sourcing Guide: A Step-by-Step Checklist for ‘palletizing robot’
The purpose of this guide is to provide international B2B buyers with a structured approach to sourcing palletizing robots. This checklist is designed to help you make informed decisions that align with your operational needs, budget constraints, and future growth prospects.
Step 1: Define Your Technical Specifications
Establishing clear technical specifications is the first step in your sourcing journey. Consider the payload capacity, reach, and speed requirements that align with your operational needs. For instance, if you handle heavy products, look for robots with higher load capacities, such as those capable of lifting up to 1,300 kg.
- Payload Requirements: Determine the weight of the products to be palletized.
- Operational Speed: Assess the required cycle times to meet your throughput targets.
Step 2: Evaluate Supplier Certifications
Before engaging with potential suppliers, verify their certifications and compliance with international standards. Certifications such as ISO 9001 for quality management systems and ISO 13485 for medical devices can indicate a supplier’s commitment to quality and safety.
- Industry Compliance: Ensure they meet specific industry standards relevant to your sector.
- Sustainability Practices: Assess their commitment to environmentally friendly manufacturing processes.
Step 3: Assess Integration Capabilities
Consider how well the palletizing robot will integrate with your existing systems. Evaluate the compatibility with your current production lines, software, and equipment.
- Control Systems: Check if the robot can easily interface with your existing automation systems.
- Physical Space: Measure the available space to accommodate the robot’s footprint and operational requirements.
Step 4: Request Detailed Proposals
Once you have shortlisted potential suppliers, request detailed proposals that outline specifications, pricing, and service agreements. A comprehensive proposal should include information on installation, training, and after-sales support.
- Cost Breakdown: Look for clarity in pricing, including hidden costs like maintenance and spare parts.
- Delivery Timeline: Ensure that the timeline for delivery and installation aligns with your operational deadlines.
Step 5: Review Customer References and Case Studies
Request references from previous clients who have implemented similar palletizing solutions. Learning from their experiences can provide insights into the supplier’s reliability and performance.
- Industry Similarity: Focus on references from companies in your industry or similar operational contexts.
- Performance Metrics: Ask about improvements in efficiency, throughput, and ROI post-installation.
Step 6: Consider Ongoing Support and Maintenance
Evaluate the level of support and maintenance that suppliers offer after installation. A strong support structure can minimize downtime and ensure the robot operates at peak efficiency.
- Service Level Agreements (SLAs): Look for clear terms regarding response times and support availability.
- Training Programs: Ensure that comprehensive training is provided for your staff to operate and maintain the robot effectively.
Step 7: Plan for Scalability and Future Needs
Finally, consider the future scalability of the palletizing robot. As your business grows, your automation needs may evolve. Choose a solution that can adapt to changing demands without requiring complete replacement.
- Modularity: Look for robots that can be easily upgraded or expanded.
- Adaptability: Assess how well the robot can handle different products or packaging types.
By following this checklist, you can make a well-informed decision when sourcing palletizing robots, ensuring that the solution you choose aligns with your operational goals and long-term strategy.
Comprehensive Cost and Pricing Analysis for palletizing robot Sourcing
What Are the Key Cost Components in Palletizing Robot Sourcing?
When sourcing palletizing robots, international B2B buyers must consider several key cost components that contribute to the overall price. These include:
-
Materials: The choice of materials significantly impacts the cost. High-quality components, such as advanced sensors and durable robotic arms, are essential for ensuring reliability and performance but come at a premium.
-
Labor: The labor costs associated with manufacturing and assembly can vary widely based on the supplier’s location. Countries with higher labor costs may charge more, while regions with lower labor rates can provide more competitive pricing.
-
Manufacturing Overhead: This includes costs related to the production facility, utilities, and administrative expenses. Buyers should inquire about how these costs are calculated and factored into the final pricing.
-
Tooling: Specialized tooling for custom applications can increase initial costs but may be necessary for specific operational requirements. Understanding the tooling costs upfront can help in budgeting.
-
Quality Control (QC): Rigorous testing and quality assurance processes are critical to ensure that the robots perform as expected. Buyers should consider the QC measures taken by the manufacturer and how they influence pricing.
-
Logistics: Shipping costs can vary significantly based on the distance, shipping method, and Incoterms agreed upon. Buyers should factor in these logistics costs when evaluating the total expenditure.
-
Margin: The profit margin that suppliers build into their pricing can vary. Understanding the market dynamics and typical margins in the industry can aid in negotiation.
How Do Price Influencers Affect the Cost of Palletizing Robots?
Several factors can influence the pricing of palletizing robots, which buyers need to consider:
-
Volume and Minimum Order Quantity (MOQ): Purchasing in larger volumes can lead to discounts. Buyers should assess their needs and negotiate MOQs to achieve better pricing.
-
Specifications and Customization: Custom features or specific configurations tailored to unique operational needs can increase costs. Buyers should evaluate the necessity of these customizations against their budget.
-
Materials and Quality Certifications: The quality of materials used can affect both performance and price. Suppliers may offer certifications (e.g., ISO) that add credibility but can also raise costs.
-
Supplier Factors: Established suppliers with a strong reputation may charge higher prices due to perceived reliability and support. However, newer or less-known suppliers may offer competitive pricing at the risk of less proven performance.
-
Incoterms: The agreed-upon Incoterms can significantly influence logistics costs. Understanding the responsibilities for shipping and delivery can help buyers negotiate more favorable terms.
What Are Effective Buyer Tips for Negotiating Palletizing Robot Prices?
International buyers, particularly from regions like Africa, South America, the Middle East, and Europe, should consider the following tips for effective negotiation and cost-efficiency:
-
Understand Total Cost of Ownership (TCO): Evaluate not just the purchase price but also long-term costs, including maintenance, energy consumption, and potential downtime. A higher upfront cost may lead to lower TCO if the robot is more efficient.
-
Leverage Local Insights: Buyers in regions like the UAE and Turkey can benefit from local market insights, which may help in negotiating better terms or understanding regional pricing trends.
-
Build Relationships with Suppliers: Establishing strong relationships can lead to better negotiation outcomes. Suppliers may offer preferential pricing or additional support to valued customers.
-
Request Detailed Quotes: Ensure quotes break down all cost components, allowing for clearer comparisons between suppliers. This transparency can aid in negotiations.
-
Consider Long-Term Partnerships: Engaging in long-term contracts may provide stability in pricing and better service agreements. Suppliers may be more willing to negotiate favorable terms for committed buyers.
Disclaimer on Indicative Prices
It is important to note that prices for palletizing robots can vary widely based on the factors mentioned above. The indicative starting prices for robotic palletizers can range from $100,000 to over $175,000, depending on specifications and additional features. Buyers are encouraged to conduct thorough market research and obtain multiple quotes to ensure they are receiving competitive pricing tailored to their specific needs.
Alternatives Analysis: Comparing palletizing robot With Other Solutions
Understanding Alternatives to Palletizing Robots
When considering automation solutions for palletizing, it’s essential to evaluate various alternatives to palletizing robots. This analysis will help international B2B buyers identify the most suitable solution for their operational needs, taking into account factors like performance, cost, and ease of implementation. Below, we compare palletizing robots with two viable alternatives: manual palletizing and automated conveyor systems.
Comparison Table of Palletizing Solutions
Comparison Aspect | Palletizing Robot | Manual Palletizing | Automated Conveyor Systems |
---|---|---|---|
Performance | High speed, precision, and repeatability | Lower speed, human error potential | Moderate speed, depends on system design |
Cost | High initial investment; long-term savings | Low initial cost; higher labor costs | Moderate cost; ongoing maintenance needed |
Ease of Implementation | Requires technical expertise for setup | Simple setup; no specialized skills needed | Requires integration with existing systems |
Maintenance | Low maintenance; long intervals | High maintenance; frequent breaks | Moderate maintenance; depends on complexity |
Best Use Case | High-volume production with consistency | Low to moderate volume; flexible tasks | Continuous flow applications in various industries |
Detailed Breakdown of Alternatives
What Are the Benefits and Drawbacks of Manual Palletizing?
Manual palletizing involves human labor for stacking products onto pallets. While this method has a low initial cost and requires no specialized equipment, it is labor-intensive and can lead to higher long-term operational costs due to wages and potential human error. In regions like Africa and South America, where labor costs might be lower, manual palletizing may initially seem attractive. However, as demand grows and production scales up, the scalability and efficiency of manual processes often become limiting factors.
How Do Automated Conveyor Systems Compare?
Automated conveyor systems facilitate the movement of products and can include features for palletizing. They offer moderate speeds and can be customized to fit various production lines. However, their effectiveness is highly dependent on the design of the system and the types of products being handled. While they require a moderate investment, ongoing maintenance can be a concern, especially in harsh industrial environments. Automated conveyor systems may be ideal for continuous flow applications, but they lack the precision and flexibility of robotic solutions.
Making the Right Choice: How to Decide Between Palletizing Robots and Alternatives
Choosing the right palletizing solution involves assessing your specific operational needs, including production volume, product types, and available budget. For high-volume operations that prioritize speed and precision, palletizing robots are typically the best choice, despite their higher upfront costs. Alternatively, businesses with lower volume needs or those operating in regions with inexpensive labor may find manual palletizing more feasible. Automated conveyor systems provide a middle ground but may require careful consideration regarding integration and maintenance.
Ultimately, the best approach is to conduct a thorough analysis of your operational goals and constraints, ensuring that the selected solution aligns with your business’s long-term objectives.
Essential Technical Properties and Trade Terminology for palletizing robot
What Are the Essential Technical Properties of a Palletizing Robot?
When considering the purchase of a palletizing robot, understanding its technical properties is crucial for making informed decisions that align with operational needs. Here are some key specifications to consider:
1. Payload Capacity
Payload capacity refers to the maximum weight a robot can handle. Ranging from 40 kg to over 1,300 kg, selecting a robot with the appropriate payload capacity is vital for ensuring it can efficiently manage your specific products without risking damage or operational failures. For industries in Africa, South America, the Middle East, and Europe, understanding your product weights is essential for selecting the right robot.
2. Reach
The reach of a palletizing robot indicates the maximum distance its arm can extend to pick or place items. Robots with reaches of up to 3,601 mm are designed to operate in larger workspaces, making them ideal for high-density warehouse environments. A robot with a suitable reach can minimize the need for additional equipment, thereby reducing overall operational costs.
3. Cycle Time
Cycle time measures how long it takes for a robot to complete a full operation cycle, including picking, moving, and placing items. Short cycle times improve throughput and efficiency, making it crucial for operations with high demand. For B2B buyers, understanding the cycle time helps in forecasting productivity levels and return on investment (ROI).
4. Precision and Repeatability
Precision refers to the robot’s ability to accurately position items, while repeatability indicates how consistently it can perform the same task. High precision and repeatability are essential for maintaining product quality, especially in industries like food and beverage or pharmaceuticals, where exact stacking is crucial.
5. Energy Efficiency
Energy efficiency in robotic systems not only impacts operational costs but also reflects a commitment to sustainable practices. Selecting robots designed with energy-efficient components can lead to significant savings over time, which is especially beneficial for companies operating in regions where energy costs are high.
6. Maintenance Requirements
The maintenance frequency and complexity of a palletizing robot are critical factors in ensuring long-term operational efficiency. Robots with low-wear drive trains and extended maintenance intervals help reduce downtime and associated costs, allowing businesses to maximize their automation investments.
What Common Trade Terminology Should B2B Buyers Know?
Understanding industry jargon is essential for effective communication and negotiation in the procurement process. Here are some common terms related to palletizing robots:
1. OEM (Original Equipment Manufacturer)
An OEM is a company that produces parts or equipment that may be marketed by another manufacturer. In the context of robotic systems, partnering with reputable OEMs ensures high-quality components, which is crucial for reliability and performance.
2. MOQ (Minimum Order Quantity)
MOQ refers to the smallest quantity of a product that a supplier is willing to sell. For B2B buyers, knowing the MOQ helps in planning purchases and inventory management, ensuring that procurement aligns with production needs.
3. RFQ (Request for Quotation)
An RFQ is a document sent to suppliers asking for pricing and terms for specific products or services. This is a critical step in the purchasing process, as it allows buyers to compare costs and terms from multiple suppliers, facilitating better decision-making.
4. Incoterms (International Commercial Terms)
Incoterms are a set of international rules that define the responsibilities of sellers and buyers in international transactions. Understanding these terms helps buyers clarify shipping costs, risk transfer, and insurance, which is particularly important when sourcing equipment globally.
5. Turnkey Solutions
A turnkey solution refers to a complete package that includes design, installation, and support, allowing businesses to implement automation with minimal effort. For international buyers, seeking suppliers that offer turnkey solutions can streamline the procurement process and ensure faster implementation.
6. Cobot (Collaborative Robot)
Cobots are designed to work alongside human operators safely. They are increasingly popular in palletizing applications due to their flexibility and ease of integration into existing workflows. Understanding the benefits of cobots can help buyers assess whether they need traditional industrial robots or collaborative solutions.
By familiarizing yourself with these technical properties and trade terms, you can make more informed decisions regarding palletizing robots, ensuring that your investment aligns with your operational goals and market demands.
Navigating Market Dynamics and Sourcing Trends in the palletizing robot Sector
What Are the Current Market Dynamics and Key Trends in the Palletizing Robot Sector?
The global market for palletizing robots is experiencing significant growth, driven by the increasing need for automation in manufacturing and logistics sectors. B2B buyers from regions such as Africa, South America, the Middle East, and Europe are particularly influenced by several key trends. Firstly, the rising labor costs and skill shortages in these regions compel companies to adopt automated solutions to enhance operational efficiency. Additionally, advancements in robotics technology, including collaborative robots (cobots), are making it easier for businesses to integrate automation into their existing workflows.
Another emerging trend is the customization of palletizing solutions. Manufacturers are now offering tailored systems that cater to specific industry needs, whether for food and beverage, pharmaceuticals, or consumer goods. This flexibility allows businesses to optimize their production lines and improve throughput. The increasing emphasis on Industry 4.0 technologies, such as IoT and AI, is also transforming the palletizing landscape, enabling real-time data analytics and predictive maintenance, which are essential for maximizing operational uptime.
Moreover, international buyers should be aware of the importance of vendor reliability and post-sale support when sourcing palletizing robots. As these systems become more complex, ongoing maintenance and technical support are crucial for ensuring seamless operations.
How Does Sustainability and Ethical Sourcing Impact the Palletizing Robot Industry?
Sustainability has become a focal point for many international B2B buyers, influencing their sourcing decisions in the palletizing robot sector. The environmental impact of manufacturing processes and the demand for greener solutions are prompting companies to prioritize sustainable practices. Buyers are increasingly seeking suppliers who incorporate eco-friendly materials and energy-efficient technologies into their robotic systems.
Ethical sourcing also plays a significant role in decision-making. Companies are more inclined to partner with manufacturers that adhere to ethical supply chain practices, ensuring fair labor conditions and responsible sourcing of materials. Certifications such as ISO 14001 (Environmental Management) and the use of recyclable materials are becoming critical factors for buyers looking to align their operations with global sustainability goals.
In addition, the push for ‘green’ certifications is shaping the market. Manufacturers that can demonstrate compliance with environmental standards not only enhance their brand reputation but also attract environmentally-conscious buyers. This trend is particularly pronounced in regions like Europe, where regulatory frameworks are increasingly stringent.
What Is the Brief Evolution and History of the Palletizing Robot Market?
The evolution of palletizing robots has been marked by significant technological advancements since their inception in the late 20th century. Initially, palletizing was a labor-intensive process, heavily reliant on manual handling. The introduction of the first industrial robots in the 1960s revolutionized this process, paving the way for automated palletizing solutions.
As technology progressed, the development of more sophisticated robotic systems allowed for greater flexibility and efficiency. The emergence of collaborative robots in the 2010s represented a paradigm shift, enabling robots to work alongside human operators safely. This evolution has not only improved productivity but has also opened new avenues for automation in various sectors, making palletizing robots an essential component of modern supply chains.
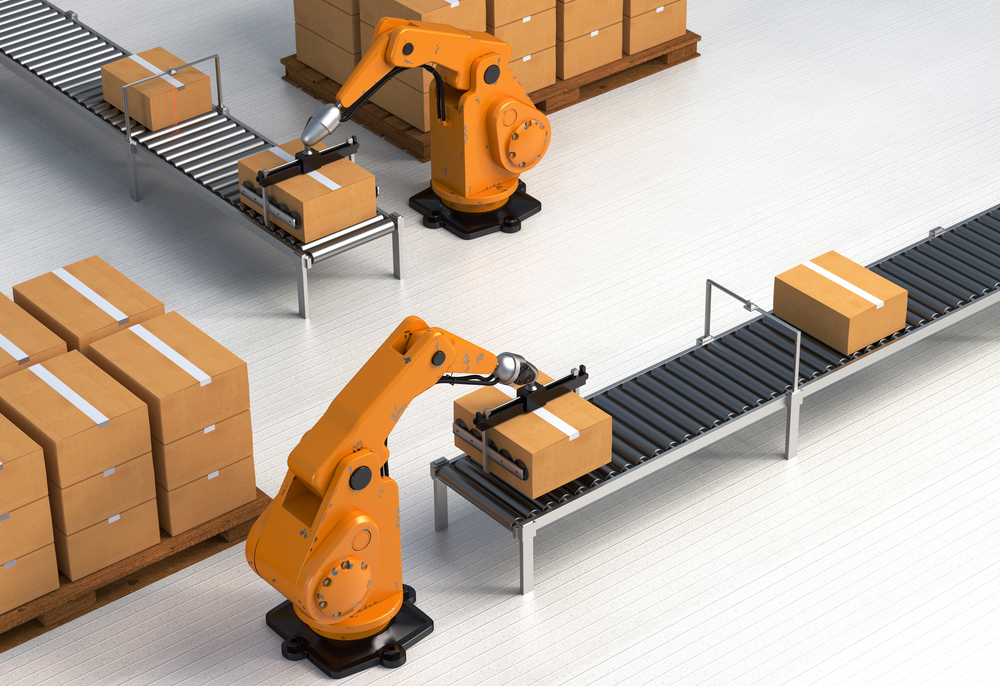
A stock image related to palletizing robot.
International B2B buyers today benefit from a rich history of innovation in the palletizing robot sector, allowing them to choose from a diverse range of solutions tailored to their specific operational needs. Understanding this historical context can help buyers make informed decisions when investing in automation technology.
Frequently Asked Questions (FAQs) for B2B Buyers of palletizing robot
-
How do I solve the challenge of integrating a palletizing robot into my existing production line?
Integrating a palletizing robot requires a thorough analysis of your current production setup. Start by documenting your existing processes and identifying bottlenecks. Collaborate with your supplier to conduct a reachability test and plan the cell layout for optimal workflow. Ensure that the robot’s gripper is tailored to your products. Finally, safeguard your automation application to comply with safety standards, followed by proper programming and testing before full deployment. -
What is the best palletizing robot for high-speed applications?
For high-speed applications, consider models like the KR QUANTEC PA series, which offer rapid cycle times and precision for medium to heavy payloads. These robots are designed for high throughput and can handle a variety of product types efficiently. Evaluate your specific requirements regarding payload capacity, cycle speed, and integration compatibility to select the most suitable model for your operation. -
How can I ensure the quality and reliability of a palletizing robot before purchase?
To ensure quality and reliability, research the manufacturer’s reputation and review customer testimonials. Request technical specifications and performance data, and consider visiting a facility where the robots are operational. Many suppliers also offer factory acceptance tests (FAT) where you can see the robots in action with your products, allowing you to assess their performance under real conditions before finalizing your purchase. -
What customization options are available for palletizing robots?
Customization options for palletizing robots typically include different gripper designs, programming features, and safety solutions tailored to specific product types. Additionally, you can choose between various payload capacities and operational speeds. Discuss your unique requirements with suppliers, as many offer bespoke solutions to enhance efficiency and integrate seamlessly into your existing systems. -
What are the typical minimum order quantities (MOQ) for palletizing robots?
Minimum order quantities for palletizing robots can vary significantly based on the supplier and the complexity of the system. Generally, for standard models, MOQs might start at one unit, while customized solutions may require a higher minimum. It is advisable to negotiate with suppliers, especially for larger projects, to find a mutually beneficial arrangement that accommodates your budget and operational needs.
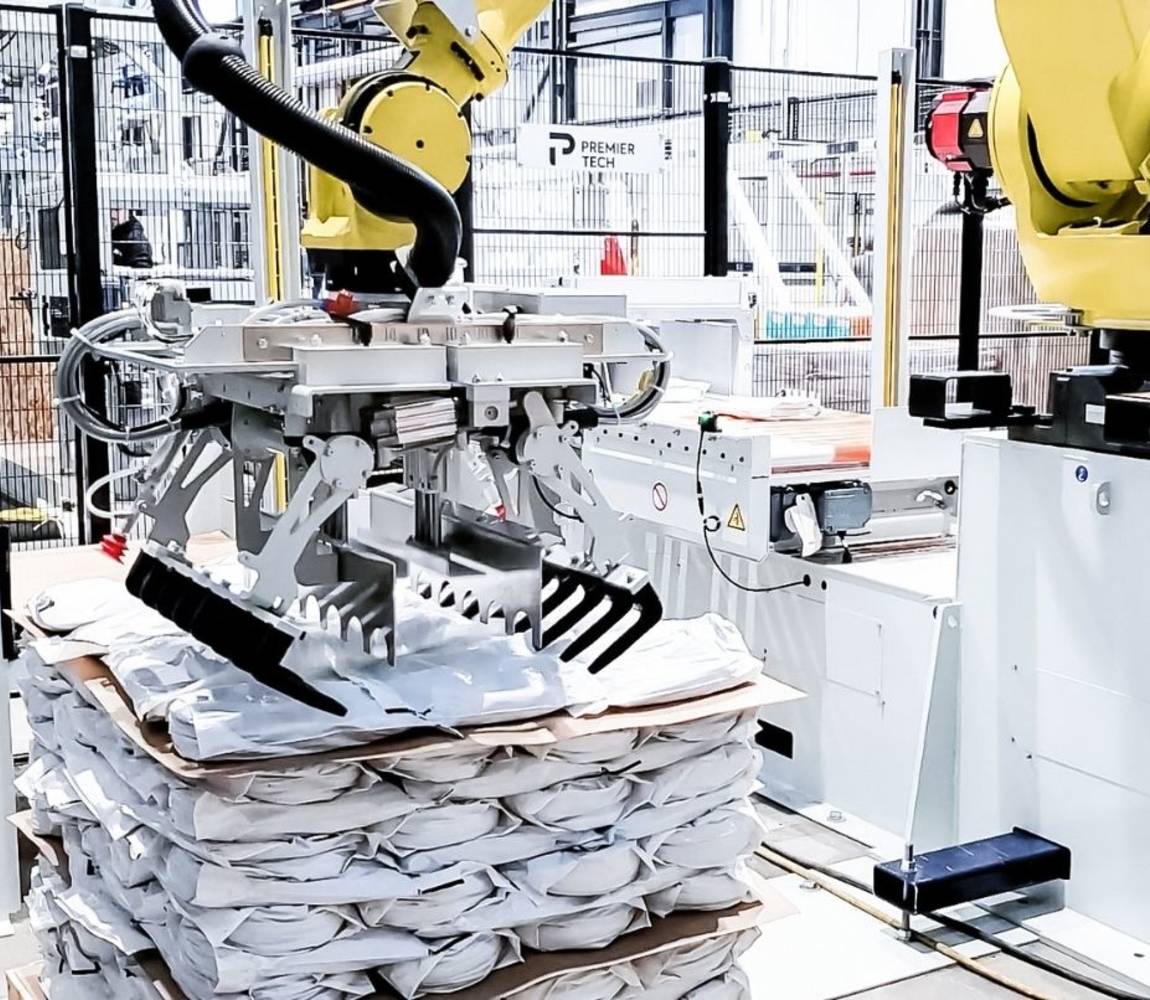
A stock image related to palletizing robot.
-
What payment terms can I expect when sourcing a palletizing robot?
Payment terms can vary widely among suppliers, but typical arrangements include upfront deposits followed by milestone payments based on project phases. Some suppliers may offer financing options or leasing programs, which can be beneficial for managing cash flow. Always clarify payment terms upfront and ensure they align with your financial capabilities and project timelines. -
How can I assess the logistics and delivery options for a palletizing robot?
When assessing logistics, consider factors such as shipping costs, delivery timelines, and customs regulations specific to your region. Request detailed shipping information from suppliers, including packaging methods and transport routes. It’s also essential to understand the installation process and whether the supplier provides on-site support for setup and integration, which can impact overall delivery efficiency. -
What should I know about after-sales support for palletizing robots?
After-sales support is crucial for maintaining operational efficiency. Ensure that your supplier offers comprehensive support services, including installation, training, and ongoing maintenance. Check for warranty options and the availability of spare parts. A robust after-sales support system can significantly reduce downtime and enhance the longevity of your palletizing investment, making it a critical factor in your purchasing decision.
Important Disclaimer & Terms of Use
⚠️ Important Disclaimer
The information provided in this guide, including content regarding manufacturers, technical specifications, and market analysis, is for informational and educational purposes only. It does not constitute professional procurement advice, financial advice, or legal advice.
While we have made every effort to ensure the accuracy and timeliness of the information, we are not responsible for any errors, omissions, or outdated information. Market conditions, company details, and technical standards are subject to change.
B2B buyers must conduct their own independent and thorough due diligence before making any purchasing decisions. This includes contacting suppliers directly, verifying certifications, requesting samples, and seeking professional consultation. The risk of relying on any information in this guide is borne solely by the reader.
Strategic Sourcing Conclusion and Outlook for palletizing robot
What Are the Key Takeaways for B2B Buyers Considering Palletizing Robots?
In conclusion, the strategic sourcing of palletizing robots presents a unique opportunity for international B2B buyers to enhance efficiency and productivity in their operations. As highlighted, the advanced capabilities of modern palletizing solutions—such as high-speed operation, low maintenance requirements, and flexibility to integrate with existing systems—make them indispensable in meeting growing market demands. Buyers from regions like Africa, South America, the Middle East, and Europe should prioritize suppliers who offer tailored solutions that align with their specific industry needs, whether it’s handling heavy loads or optimizing space in a facility.
How Can Strategic Sourcing Drive Competitive Advantage?
Investing in palletizing robots not only streamlines processes but also significantly reduces labor costs and error rates. The emphasis on collaborative robots (cobots) and automated systems allows for a more agile manufacturing environment, which is crucial for maintaining a competitive edge. As companies navigate supply chain challenges and labor shortages, the value of strategic sourcing becomes even more pronounced.
What Should B2B Buyers Do Next?
Looking ahead, B2B buyers are encouraged to engage with reputable manufacturers and integrators who can provide comprehensive support, from system design to ongoing maintenance. Embrace the potential of automation by exploring customized solutions that suit your operational needs. By making informed sourcing decisions today, you can position your business for sustained growth and resilience in an ever-evolving market landscape.