The Ultimate Guide to Dc Electric Motor Parts (2025)
Introduction: Navigating the Global Market for dc electric motor parts
In the fast-evolving landscape of global commerce, sourcing high-quality DC electric motor parts presents a unique set of challenges for international B2B buyers. From ensuring compatibility to navigating varied regulations across regions such as Africa, South America, the Middle East, and Europe, the complexities can be daunting. This guide serves as a comprehensive resource that empowers businesses to make informed purchasing decisions by covering essential aspects including types of DC motor parts, their applications, supplier vetting processes, and cost considerations.
Understanding the intricacies of DC motor components—like armatures, stators, commutators, and brushes—is crucial for optimizing performance and reliability in various applications, ranging from industrial machinery to consumer electronics. This guide not only outlines the technical specifications and functionalities of each component but also provides strategic insights into the procurement process, ensuring that buyers can confidently select the right products for their operational needs.
Moreover, by addressing common pitfalls and offering best practices for supplier evaluation, this resource is designed to help businesses mitigate risks and enhance supply chain efficiency. Whether you are a buyer in Egypt looking for robust parts for mining equipment or a company in Argentina sourcing components for automotive applications, this guide is tailored to support your journey in navigating the global market for DC electric motor parts.
Understanding dc electric motor parts Types and Variations
Type Name | Key Distinguishing Features | Primary B2B Applications | Brief Pros & Cons for Buyers |
---|---|---|---|
Brushed DC Motors | Simple design with brushes and commutators; cost-effective. | Automotive, robotics, and small machinery. | Pros: Easy to control; Cons: Shorter lifespan due to brush wear. |
Brushless DC Motors | No brushes; uses electronic controllers; higher efficiency. | HVAC systems, drones, and electric vehicles. | Pros: Longer lifespan; Cons: More complex and costly to implement. |
Permanent Magnet DC Motors | Uses permanent magnets for the magnetic field; compact size. | Consumer electronics and portable tools. | Pros: High efficiency; Cons: Limited torque at high speeds. |
Series Wound DC Motors | High starting torque; field winding in series with armature. | Cranes, electric trains, and traction applications. | Pros: Excellent for high-load applications; Cons: Speed varies with load. |
Shunt Wound DC Motors | Field winding in parallel with armature; stable speed. | Industrial applications and conveyor systems. | Pros: Consistent speed under varying loads; Cons: Lower starting torque. |
What Are the Key Characteristics of Brushed DC Motors?
Brushed DC motors are characterized by their straightforward design, which includes brushes and a commutator. This simplicity makes them cost-effective and easy to control, making them suitable for applications in automotive, robotics, and small machinery. However, the brushes wear over time, which can lead to maintenance issues and a shorter lifespan. Buyers should consider the balance between initial cost and long-term maintenance when selecting this type.
How Do Brushless DC Motors Stand Out?
Brushless DC motors eliminate the need for brushes by using electronic controllers, which enhances their efficiency and reliability. They are particularly well-suited for applications in HVAC systems, drones, and electric vehicles where performance and longevity are critical. While they come with a higher upfront cost and complexity, the advantages of longer lifespan and reduced maintenance make them a preferred choice for many industrial applications.
What Are the Advantages of Permanent Magnet DC Motors?
Permanent magnet DC motors utilize permanent magnets to create the magnetic field, resulting in a compact design that is highly efficient. These motors are commonly found in consumer electronics and portable tools where space and weight are at a premium. While they provide high efficiency, buyers should be aware that their torque output can be limited at high speeds, which may affect performance in certain applications.
What Makes Series Wound DC Motors Ideal for High-Load Applications?
Series wound DC motors are designed with the field winding connected in series with the armature, providing high starting torque. This feature makes them ideal for applications such as cranes, electric trains, and other traction applications. While they excel in high-load scenarios, buyers should consider that the speed of these motors can vary significantly with the load, which may impact operational consistency.
Why Choose Shunt Wound DC Motors for Industrial Use?
Shunt wound DC motors have their field winding connected in parallel with the armature, allowing for a more stable speed under varying loads. This stability makes them particularly suitable for industrial applications such as conveyor systems. Despite their lower starting torque compared to series wound motors, their consistent performance under load is a significant advantage for buyers looking for reliability in their operations.
Key Industrial Applications of dc electric motor parts
Industry/Sector | Specific Application of dc electric motor parts | Value/Benefit for the Business | Key Sourcing Considerations for this Application |
---|---|---|---|
Manufacturing | Conveyor Systems | Enhances efficiency in material handling | Quality of motor parts to ensure durability under heavy loads |
Agriculture | Irrigation Systems | Improves water distribution and crop yield | Compatibility with existing systems and environmental resistance |
Automotive | Electric Vehicle (EV) Components | Supports sustainable transport solutions | Availability of specialized parts for EV applications |
Mining | Hoisting Equipment | Increases safety and efficiency in material lifting | Compliance with safety standards and reliability under harsh conditions |
HVAC | Ventilation and Air Conditioning Systems | Enhances energy efficiency and comfort | Energy ratings and maintenance requirements for optimal performance |
How Are DC Electric Motor Parts Used in Manufacturing Applications?
In the manufacturing sector, DC electric motor parts are integral to conveyor systems, which streamline the movement of materials and products through various stages of production. By ensuring reliable operation, these components reduce downtime and improve overall productivity. International B2B buyers, particularly from regions like South America and Africa, should focus on sourcing high-quality brushes and commutators that can withstand the rigors of continuous operation, emphasizing durability and maintenance support.
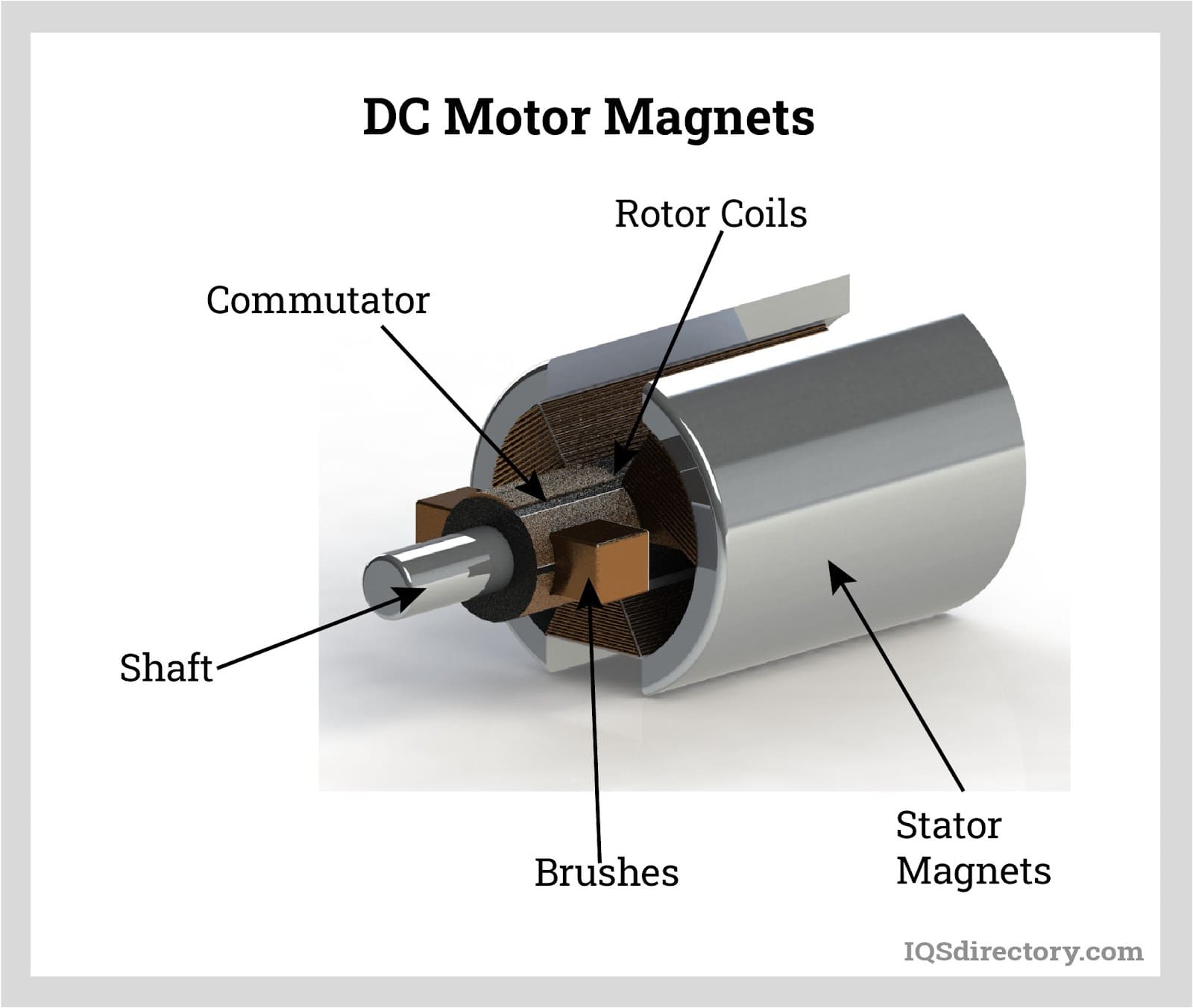
A stock image related to dc electric motor parts.
What Role Do DC Electric Motor Parts Play in Agriculture?
In agriculture, DC electric motor parts are vital for irrigation systems, where they help to automate water distribution across fields. This automation not only conserves water but also maximizes crop yield by ensuring timely irrigation. Buyers in the Middle East and Africa should prioritize sourcing motors that are resistant to environmental factors such as humidity and dust, ensuring longevity and efficiency in diverse climates.
How Are DC Electric Motor Parts Essential for Electric Vehicles?
The automotive industry is witnessing a significant shift towards electric vehicles (EVs), where DC electric motor parts are crucial for components such as electric drive systems. These parts enable efficient energy conversion, contributing to the overall performance of EVs. B2B buyers in Europe and South America must consider sourcing specialized components that meet stringent environmental regulations and performance standards, ensuring compatibility with modern EV technology.
What Applications Do DC Electric Motor Parts Have in Mining?
In the mining sector, DC electric motor parts are essential for hoisting equipment used to lift heavy materials from deep underground. These motors provide the necessary torque and reliability to ensure safe operations in challenging environments. International buyers, particularly from regions with extensive mining operations like South America, should ensure that the sourced components comply with safety standards and are designed for high-load applications to enhance operational safety and efficiency.
How Do DC Electric Motor Parts Improve HVAC Systems?
DC electric motor parts are crucial in HVAC systems for ventilation and air conditioning applications. They enhance energy efficiency by providing precise control over airflow and temperature regulation. Buyers in Europe and the Middle East should focus on sourcing energy-efficient motors that align with sustainability goals, as well as considering the long-term maintenance needs to ensure optimal performance in varying climates.
3 Common User Pain Points for ‘dc electric motor parts’ & Their Solutions
Scenario 1: Sourcing Quality DC Electric Motor Parts to Avoid Downtime
The Problem:
International B2B buyers often face the challenge of sourcing high-quality DC electric motor parts, particularly in regions like Africa and South America where the availability of reliable suppliers can be limited. Poor-quality parts can lead to frequent motor failures, resulting in significant downtime and financial losses. Buyers may struggle with identifying reputable manufacturers, which compounds the issue of selecting the right parts that meet specific operational requirements. The risk of receiving subpar components can also lead to safety hazards in industrial applications.
The Solution:
To mitigate these challenges, buyers should conduct thorough research to identify established suppliers with a proven track record in the DC electric motor parts market. This involves seeking out manufacturers that provide detailed product specifications, certifications, and customer testimonials. Utilize platforms such as industry trade shows or online marketplaces that specialize in industrial components to network with reputable suppliers. Establishing long-term partnerships with reliable suppliers can ensure consistent quality and availability of parts. Additionally, consider ordering samples or conducting small test purchases to evaluate the quality before committing to larger orders. Regular communication with suppliers can help buyers stay informed about new products and innovations in the market.
Scenario 2: Understanding Technical Specifications for Optimal Performance
The Problem:
B2B buyers often encounter difficulties in understanding the technical specifications of DC electric motor parts, such as armatures, commutators, and brushes. This lack of clarity can lead to incorrect part selection, which can compromise the performance and efficiency of the motor. For buyers in the Middle East and Europe, where compliance with specific industrial standards is essential, misunderstanding these specifications can result in costly operational failures and compliance issues.
The Solution:
To address this issue, buyers should invest time in educating themselves about the core components of DC motors and their specifications. Engaging with technical resources, such as manufacturer catalogs, online webinars, or industry publications, can provide valuable insights into the nuances of motor components. Furthermore, collaborating with engineers or technical experts during the procurement process can ensure that the chosen parts align with the specific operational needs of the application. When sourcing parts, request detailed technical documentation and support from suppliers, and don’t hesitate to ask for clarification on specifications. This proactive approach will help ensure that the selected components enhance motor performance and reliability.
Scenario 3: Preventing Maintenance Issues Through Proper Part Selection
The Problem:
Maintenance challenges are a common pain point for B2B buyers managing DC electric motors. Inconsistent maintenance practices, often due to using incorrect or low-quality parts, can lead to increased wear and tear on motors. This is particularly critical in industries such as mining and manufacturing in regions like South America and Africa, where motor reliability is paramount. Failure to maintain motors effectively can result in unplanned downtime, increased repair costs, and diminished operational efficiency.
The Solution:
To prevent maintenance-related issues, buyers should prioritize the selection of high-quality, compatible parts that are specifically designed for their DC motors. Implementing a regular maintenance schedule that includes inspections and timely replacements of wear items, such as brushes and commutators, is crucial. Buyers can work with their suppliers to establish maintenance kits that include all necessary parts, along with guidelines on replacement intervals based on operational usage. Investing in training for maintenance personnel on best practices for inspecting and replacing motor components can also significantly enhance the longevity and reliability of DC motors. Furthermore, leveraging technology such as condition monitoring systems can provide real-time insights into motor health, allowing for proactive maintenance and timely part replacement.
Strategic Material Selection Guide for dc electric motor parts
What Are the Key Materials Used in DC Electric Motor Parts?
When selecting materials for DC electric motor parts, it is essential to consider their properties, advantages, and limitations. This analysis will focus on four common materials: copper, carbon, steel, and aluminum. Each material has unique characteristics that influence performance, durability, and cost, making them suitable for specific applications.
How Does Copper Impact Performance in DC Electric Motor Parts?
Copper is widely recognized for its excellent electrical conductivity, making it a preferred choice for windings and commutators in DC motors. Its high thermal conductivity allows for efficient heat dissipation, which is critical in high-performance applications. However, copper is susceptible to corrosion, particularly in humid environments, which can affect its longevity.
Pros: High conductivity, excellent thermal properties, and good mechanical strength.
Cons: Higher cost compared to alternatives and potential corrosion issues.
Impact on Application: Copper’s conductivity makes it ideal for applications requiring efficient power transfer.
Considerations for International Buyers: Compliance with standards like ASTM B170 is crucial, especially in regions with varying environmental conditions.
What Role Does Carbon Play in DC Electric Motor Components?
Carbon, particularly in the form of carbon brushes, is essential for maintaining electrical contact within DC motors. Carbon brushes are self-lubricating and exhibit low friction, which minimizes wear on the commutator. They can operate effectively at high temperatures, making them suitable for demanding applications.
Pros: Durability, low friction, and high-temperature resistance.
Cons: Limited lifespan under extreme conditions and potential for electrical noise.
Impact on Application: Carbon brushes are suitable for applications where consistent electrical contact is critical.
Considerations for International Buyers: Buyers should ensure adherence to international standards such as JIS B 2301 for brush specifications.
Why Is Steel a Common Choice for Structural Components in DC Motors?
Steel is often used for the armature and stator due to its strength and durability. It provides structural integrity and can withstand high mechanical stress. However, the type of steel used can significantly impact performance, as different grades offer varying levels of corrosion resistance and magnetic properties.
Pros: High strength, durability, and good magnetic properties.
Cons: Heavier than alternatives and can be prone to rust without proper treatment.
Impact on Application: Steel is ideal for applications requiring robust structural components.
Considerations for International Buyers: Compliance with DIN standards for steel grades is essential, especially in European markets.
How Does Aluminum Compare for Weight-Sensitive Applications?
Aluminum is favored in applications where weight is a critical factor. It is lightweight and has good electrical conductivity, although not as high as copper. Aluminum is also resistant to corrosion, making it suitable for outdoor applications.
Pros: Lightweight, corrosion-resistant, and cost-effective.
Cons: Lower conductivity than copper and may require special handling during manufacturing.
Impact on Application: Ideal for portable devices or applications where weight savings are crucial.
Considerations for International Buyers: Buyers should verify compliance with ASTM standards for aluminum products, particularly in aerospace and automotive sectors.
Summary Table of Material Selection for DC Electric Motor Parts
Material | Typical Use Case for dc electric motor parts | Key Advantage | Key Disadvantage/Limitation | Relative Cost (Low/Med/High) |
---|---|---|---|---|
Copper | Windings and commutators | Excellent electrical conductivity | Susceptible to corrosion | High |
Carbon | Brushes | Self-lubricating, low friction | Limited lifespan under extreme conditions | Medium |
Steel | Armature and stator | High strength and durability | Heavier and prone to rust | Medium |
Aluminum | Lightweight components | Lightweight and corrosion-resistant | Lower conductivity than copper | Low |
This strategic material selection guide provides international B2B buyers with essential insights into the materials used in DC electric motor parts, enabling informed decisions based on performance requirements and regional considerations.
In-depth Look: Manufacturing Processes and Quality Assurance for dc electric motor parts
What Are the Main Stages of Manufacturing DC Electric Motor Parts?
The manufacturing process of DC electric motor parts involves several key stages, each critical to ensuring the final product meets performance and quality standards. Here’s a breakdown of the main stages:
1. Material Preparation
Material preparation is the foundational stage where raw materials are selected based on their properties and suitability for specific motor components. Common materials include high-grade steel for armatures, copper for windings, and carbon or graphite for brushes.
- Key Techniques:
- Material Selection: Choose materials that meet specific mechanical and electrical properties to enhance performance.
- Heat Treatment: Employ processes such as annealing to improve ductility and reduce brittleness in metals.
2. Forming
Forming processes shape the raw materials into the desired components. This stage includes various techniques, depending on the part being manufactured.
- Key Techniques:
- Stamping and Die-Casting: Used for creating armature laminations and housings.
- Winding: Involves wrapping copper wire around the armature to create electromagnetic fields, which is crucial for motor function.
3. Assembly
The assembly stage integrates the various components into a functioning motor. This step is critical for ensuring that all parts fit together correctly and operate as intended.
- Key Techniques:
- Precision Alignment: Ensuring that the armature and stator are correctly aligned to prevent mechanical failures.
- Soldering and Welding: Used to connect electrical components securely and ensure good electrical conductivity.
4. Finishing
The finishing stage involves processes that enhance the appearance and functionality of the motor parts. It includes surface treatments and final inspections.
- Key Techniques:
- Coating: Application of protective coatings to prevent corrosion and enhance durability.
- Balancing: This ensures that rotating parts are balanced, reducing vibrations during operation.
How Is Quality Assurance Implemented in the Manufacturing of DC Electric Motor Parts?
Quality assurance (QA) is a critical aspect of the manufacturing process for DC electric motor parts. It ensures that products meet international standards and customer expectations. Below are the key elements of QA.
Relevant International Standards for Quality Assurance
Several international standards guide the quality assurance processes in manufacturing. Notable among them are:
- ISO 9001: This standard focuses on quality management systems (QMS) and is essential for ensuring consistent quality across manufacturing processes.
- CE Marking: Indicates compliance with European safety, health, and environmental protection standards.
- API Standards: Relevant for motors used in the oil and gas industry, ensuring they meet specific operational requirements.
What Are the Key Quality Control Checkpoints in Manufacturing?
Quality control (QC) checkpoints are essential in monitoring and maintaining product quality throughout the manufacturing process.
1. Incoming Quality Control (IQC)
This checkpoint assesses the quality of raw materials before they enter the production line.
- Key Actions:
- Verify supplier documentation and material certifications.
- Conduct physical inspections and tests to ensure materials meet specifications.
2. In-Process Quality Control (IPQC)
During the manufacturing process, continuous monitoring is crucial to identify any defects early.
- Key Actions:
- Regular inspections at various stages of production.
- Use of statistical process control (SPC) to analyze production data and identify trends.
3. Final Quality Control (FQC)
The FQC stage involves comprehensive testing and inspection of the finished products before they are shipped.
- Key Actions:
- Perform functional testing to ensure motors operate as intended.
- Conduct visual inspections for surface defects and assembly errors.
How Can B2B Buyers Verify Supplier Quality Control?
For international B2B buyers, particularly in regions such as Africa, South America, the Middle East, and Europe, verifying a supplier’s quality control processes is crucial. Here are actionable insights for buyers:
1. Conduct Supplier Audits
Request to conduct on-site audits of potential suppliers. This helps buyers assess the manufacturing environment, quality control measures, and compliance with international standards.
2. Review Quality Assurance Documentation
Ask suppliers for their quality assurance documentation, including certificates for ISO 9001, CE marking, and any other relevant certifications. This provides insights into their commitment to quality.
3. Utilize Third-Party Inspection Services
Engaging third-party inspection services can provide an unbiased assessment of the supplier’s quality control processes. These services can conduct pre-shipment inspections and testing to ensure compliance with specifications.
What Common Testing Methods Are Used in Quality Assurance?
Various testing methods are employed to ensure the quality and reliability of DC electric motor parts. Some of the common methods include:
- Electrical Testing: Measures the electrical properties of components to ensure they meet specified performance standards.
- Mechanical Testing: Evaluates the strength and durability of parts through stress tests and fatigue testing.
- Thermal Testing: Assesses how components perform under varying temperature conditions, crucial for applications in extreme environments.
What Are the QC and Certification Nuances for International B2B Buyers?
International B2B buyers must be aware of specific nuances related to quality control and certification:
- Regional Compliance: Ensure that products meet the regulatory standards of the destination country. For instance, products exported to Europe must comply with CE marking requirements.
- Cultural Considerations: Understanding cultural differences can impact quality perceptions and expectations. Engaging local experts can aid in navigating these nuances.
- Documentation and Traceability: Maintain thorough records of all quality control processes and certifications to streamline customs and regulatory compliance in different regions.
By understanding the manufacturing processes and quality assurance protocols for DC electric motor parts, international B2B buyers can make informed decisions, ensuring they procure high-quality components that meet their operational requirements.
Practical Sourcing Guide: A Step-by-Step Checklist for ‘dc electric motor parts’
In the ever-evolving landscape of international trade, sourcing DC electric motor parts requires a strategic approach to ensure efficiency, reliability, and cost-effectiveness. This guide provides a step-by-step checklist designed specifically for B2B buyers from regions such as Africa, South America, the Middle East, and Europe. By following these steps, you can streamline your procurement process and make informed decisions.
Step 1: Define Your Technical Specifications
Establishing clear technical specifications is the foundation of effective sourcing. Identify the specific components you need, such as carbon brushes, armatures, or commutators, and determine their dimensions, materials, and performance standards. This clarity will help you communicate your requirements to potential suppliers and ensure that the parts you receive meet your operational needs.
- Consider application requirements: Different industries may have unique demands, such as temperature tolerance or load capacity.
- Documentation: Prepare detailed specifications documents to share with suppliers.
Step 2: Research and Identify Potential Suppliers
Conduct thorough research to compile a list of potential suppliers. Utilize online platforms, industry directories, and trade shows to gather information about manufacturers and distributors specializing in DC motor parts.
- Check supplier reviews: Look for feedback from previous clients to gauge reliability and quality.
- Network with industry peers: Leverage connections to obtain recommendations for trustworthy suppliers.
Step 3: Evaluate Supplier Certifications and Compliance
Before finalizing any partnerships, verify that suppliers possess the necessary certifications and comply with industry standards. This step is crucial to ensure the quality and safety of the parts you will be sourcing.
- ISO certifications: Suppliers with ISO 9001 or similar certifications demonstrate a commitment to quality management.
- Regulatory compliance: Ensure that the products meet the legal requirements of your region, especially for international transactions.
Step 4: Request Quotes and Compare Pricing
Once you have shortlisted potential suppliers, request quotes that outline pricing, lead times, and payment terms. Comparing these quotes will help you identify the most cost-effective options while ensuring quality.
- Consider total cost of ownership: Evaluate not just the upfront cost but also shipping, customs, and potential maintenance expenses.
- Negotiate terms: Don’t hesitate to discuss pricing and terms to secure the best deal.
Step 5: Assess Quality Assurance Processes
Understanding a supplier’s quality assurance processes is vital for ensuring the longevity and performance of the parts. Inquire about testing protocols, quality control measures, and warranty policies.
- Request documentation: Ask for quality assurance certificates or test results for the parts you intend to purchase.
- On-site inspections: If feasible, arrange for visits to the supplier’s facility to observe their manufacturing and quality control processes.
Step 6: Establish Communication Channels
Effective communication is key to a successful sourcing relationship. Ensure that you establish clear lines of communication with your chosen supplier to facilitate timely updates and issue resolution.
- Designate points of contact: Identify primary contacts on both sides to streamline communication.
- Regular updates: Schedule regular check-ins to discuss order status, potential issues, or changes in specifications.
Step 7: Plan for Logistics and Delivery
Finally, consider the logistics involved in transporting the parts from the supplier to your location. Factor in shipping methods, customs clearance, and delivery timelines to avoid disruptions in your operations.
- Choose reliable logistics partners: Work with freight forwarders experienced in handling international shipments of industrial components.
- Contingency plans: Develop backup plans for delays or issues that may arise during shipping.
By following this checklist, international B2B buyers can enhance their sourcing strategy for DC electric motor parts, ensuring they acquire high-quality components that meet their specific needs.
Comprehensive Cost and Pricing Analysis for dc electric motor parts Sourcing
What Are the Key Cost Components for DC Electric Motor Parts?
When sourcing DC electric motor parts, understanding the cost structure is crucial for international B2B buyers. The primary cost components include:
-
Materials: The type of materials used in production significantly affects costs. For instance, high-quality copper for windings or specialized carbon for brushes can increase costs but may enhance performance and longevity.
-
Labor: Labor costs vary widely based on geographic location and the skill level required for manufacturing. Countries with lower labor costs may offer competitive pricing, but it is essential to consider the potential trade-offs in quality.
-
Manufacturing Overhead: This includes utilities, rent, and equipment maintenance costs. Efficient factories may have lower overhead, allowing for more competitive pricing.
-
Tooling: The cost of molds and tools used in production can be a significant upfront investment. Custom parts often require specialized tooling, which can raise initial costs but may yield better-quality products.
-
Quality Control (QC): Implementing robust QC processes ensures that parts meet specifications and standards, thereby preventing costly returns and replacements. This can add to the overall cost but is essential for maintaining customer satisfaction.
-
Logistics: Transportation and shipping costs can vary based on the supplier’s location and the chosen shipping method. Understanding Incoterms is crucial, as they define responsibilities for shipping, insurance, and tariffs.
-
Margin: Suppliers will add a profit margin to their costs, which can vary based on market demand, competition, and the uniqueness of the product.
How Do Price Influencers Impact Sourcing Decisions for DC Electric Motor Parts?
Several factors influence the pricing of DC electric motor parts, and buyers should consider these when negotiating:
-
Volume and Minimum Order Quantity (MOQ): Larger orders often come with discounts. Understanding the supplier’s MOQ can help buyers optimize their purchasing strategy.
-
Specifications and Customization: Customized parts or those with specific performance characteristics typically cost more. Buyers should clearly define their requirements to avoid unexpected costs.
-
Material Quality and Certifications: Higher quality materials and recognized certifications (like ISO standards) may lead to higher costs but can result in better performance and reliability.
-
Supplier Factors: The reputation and reliability of the supplier can influence pricing. Established suppliers may charge a premium for their perceived quality and service levels.
-
Incoterms: Different Incoterms can affect the overall cost by determining who is responsible for shipping, insurance, and tariffs. Understanding these terms can lead to significant savings.
What Are Effective Buyer Tips for Negotiating Prices on DC Electric Motor Parts?
International B2B buyers can employ several strategies to achieve cost efficiency:
-
Negotiate Terms: Always negotiate not just the price but also payment terms, lead times, and delivery schedules. Flexibility in these areas can lead to better overall value.
-
Consider Total Cost of Ownership (TCO): Evaluate the TCO instead of just the upfront cost. This includes maintenance, energy consumption, and potential downtime costs associated with the parts.
-
Research Market Prices: Stay informed about current market prices for DC motor parts. This knowledge can empower buyers during negotiations and help them identify fair pricing.
-
Leverage Relationships: Building strong relationships with suppliers can lead to better pricing and favorable terms in the long run. Suppliers are often more willing to negotiate with buyers who demonstrate loyalty and reliability.
-
Factor in Regional Differences: Buyers from Africa, South America, the Middle East, and Europe should consider regional manufacturing capabilities and costs, as these can significantly affect pricing and availability.
Conclusion and Disclaimer on Pricing
While the insights provided here offer a comprehensive overview of the cost structure and pricing dynamics for DC electric motor parts, it is essential to note that prices can fluctuate based on market conditions, supplier capabilities, and specific buyer requirements. Engaging in thorough research and maintaining open communication with suppliers will enhance the procurement process and lead to more favorable outcomes.
Alternatives Analysis: Comparing dc electric motor parts With Other Solutions
In the ever-evolving landscape of industrial solutions, it is vital for B2B buyers to explore various alternatives to traditional products. This section focuses on comparing DC electric motor parts with alternative technologies, offering insights that can assist international buyers, particularly from regions like Africa, South America, the Middle East, and Europe, in making informed decisions.
Comparison Table of DC Electric Motor Parts and Alternatives
Comparison Aspect | Dc Electric Motor Parts | Brushless DC Motor (BLDC) | Stepper Motor |
---|---|---|---|
Performance | High torque at low speeds | High efficiency, smooth operation | Precise positioning |
Cost | Generally lower initial cost | Higher upfront cost but longer lifespan | Moderate cost |
Ease of Implementation | Straightforward installation | Requires complex control systems | Simple to integrate |
Maintenance | Regular brush replacement required | Minimal maintenance, no brushes | Low maintenance |
Best Use Case | General-purpose applications | Robotics, HVAC systems | 3D printers, CNC machines |
What are the Pros and Cons of Brushless DC Motors?
Brushless DC Motors (BLDC) represent a significant technological advancement over traditional DC motors. The absence of brushes eliminates friction, leading to greater efficiency and a longer lifespan. This makes BLDC motors ideal for applications requiring high reliability and performance, such as robotics and HVAC systems. However, the initial cost is higher compared to traditional DC motors, and their installation can be more complex due to the need for advanced control systems. For B2B buyers focused on high-efficiency applications and willing to invest upfront, BLDC motors are a compelling alternative.
How Do Stepper Motors Compare?
Stepper motors excel in applications requiring precise control over position and speed. They operate by dividing a full rotation into a series of discrete steps, allowing for accurate movement without the need for feedback systems. This makes them ideal for CNC machines and 3D printers where precision is paramount. The cost of stepper motors is moderate, and they are relatively easy to integrate into existing systems. However, they may not deliver the same torque as traditional DC motors at low speeds, which can limit their application in some industrial scenarios. B2B buyers should consider stepper motors for projects that prioritize precision over raw power.
Conclusion: How Can B2B Buyers Choose the Right Solution?
When evaluating the best solution for their specific needs, international B2B buyers should consider several factors, including performance requirements, budget constraints, ease of implementation, and maintenance capabilities. While DC electric motor parts offer a reliable and cost-effective solution for general applications, alternatives like brushless DC motors and stepper motors provide unique advantages that may better serve specific use cases. By carefully analyzing these options, buyers can ensure they select a solution that aligns with their operational goals and enhances their overall efficiency.
Essential Technical Properties and Trade Terminology for dc electric motor parts
What Are the Essential Technical Properties of DC Electric Motor Parts?
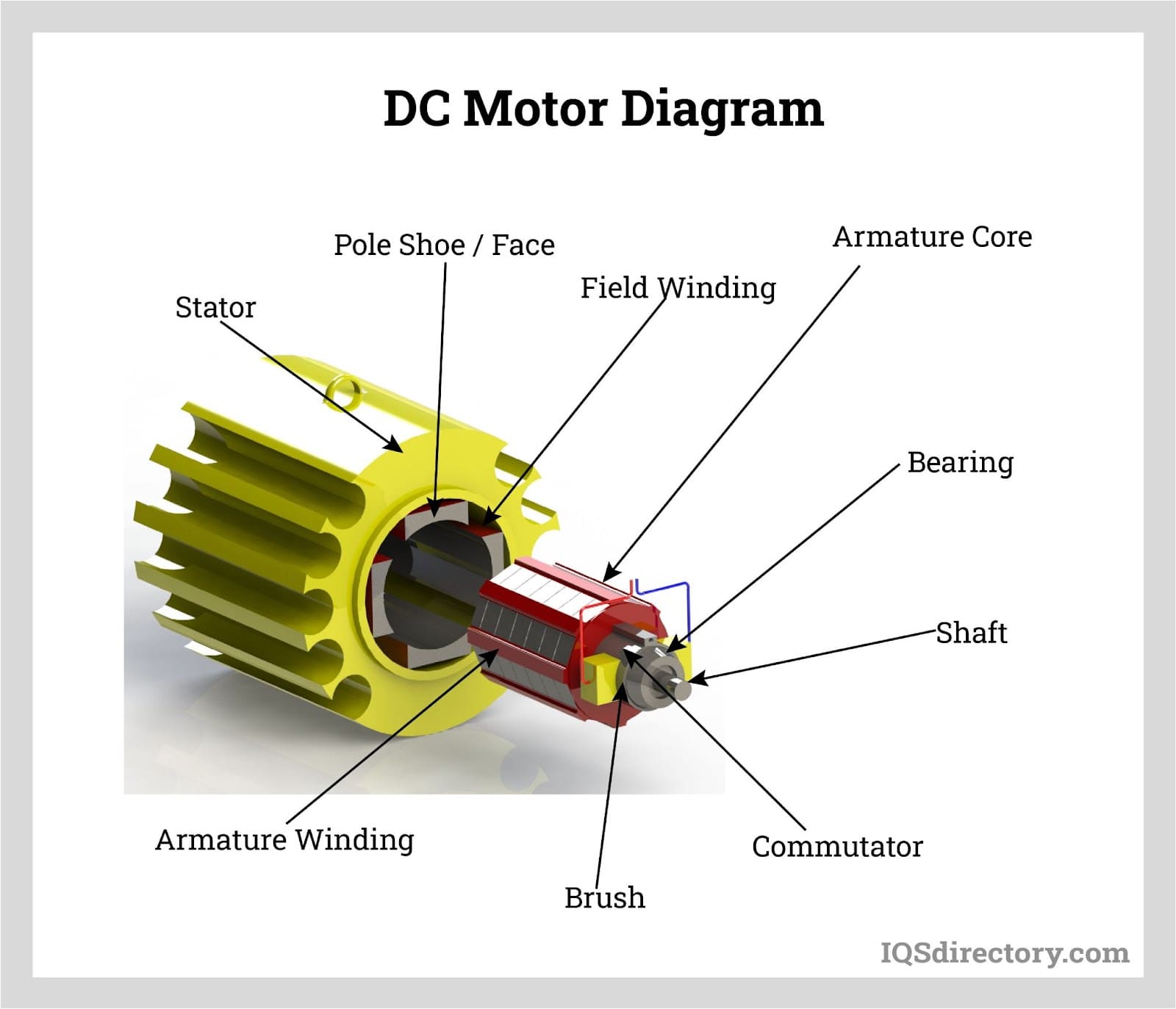
A stock image related to dc electric motor parts.
Understanding the technical properties of DC electric motor parts is crucial for B2B buyers, especially those in regions like Africa, South America, the Middle East, and Europe. Here are several key specifications that play a vital role in ensuring the performance and reliability of these components.
What Material Grades Are Commonly Used in DC Motor Parts?
-
Copper Wire: Used primarily in armature windings, copper offers excellent electrical conductivity, which is essential for efficient motor operation. The purity and gauge of copper wire can significantly affect motor performance, making it vital for buyers to specify these characteristics in their orders.
-
Carbon Brushes: Typically made from a composite of carbon and graphite, these brushes are crucial for maintaining electrical contact with the commutator. Buyers should pay attention to the hardness and density of the brushes, as these properties influence wear rates and conductivity.
-
Steel for Commutators: The commutator segments are often made from high-grade copper, but the supporting structure may be steel. The choice of steel grade impacts the commutator’s durability and resistance to mechanical stress during operation.
-
Insulation Materials: Insulation is critical for preventing electrical shorts and ensuring safety. Common materials include mica and thermoplastics, which should meet specific thermal and electrical resistance criteria.
Why Are Tolerances Important in DC Motor Parts?
Tolerances refer to the allowable variations in dimensions and characteristics of components. In DC motors, tight tolerances are essential for ensuring that parts fit together correctly, preventing mechanical failures and ensuring smooth operation. For instance, armature windings must be precisely aligned to optimize magnetic fields, while commutators must fit snugly with brushes to maintain consistent electrical contact.
What Are Common Trade Terms Used in DC Electric Motor Parts Procurement?
Navigating the trade terminology is equally important for B2B buyers. Understanding these terms can streamline purchasing processes and improve communication with suppliers.
-
OEM (Original Equipment Manufacturer): This term refers to companies that produce parts that are used in another company’s end product. For buyers, working with OEMs can ensure high-quality components that meet specific standards required for their applications.
-
MOQ (Minimum Order Quantity): This is the minimum quantity of a product that a supplier is willing to sell. Understanding MOQ is crucial for buyers to manage inventory levels and costs, especially when dealing with specialized DC motor parts.
-
RFQ (Request for Quotation): An RFQ is a document sent to suppliers to solicit price quotes for specific products. For international buyers, crafting a detailed RFQ can help ensure competitive pricing and clarify specifications, leading to better purchasing decisions.
-
Incoterms (International Commercial Terms): These are standardized trade terms that define the responsibilities of buyers and sellers in international transactions. Familiarity with Incoterms can help buyers avoid misunderstandings regarding shipping, insurance, and customs duties.
-
Lead Time: This term refers to the amount of time it takes from placing an order to receiving the goods. Understanding lead time is critical for B2B buyers to manage production schedules and inventory effectively.
-
Warranty and Service Agreements: These terms outline the conditions under which a supplier will repair or replace defective parts. Buyers should pay close attention to these agreements to ensure they are protected against potential failures.
By grasping these essential technical properties and trade terminologies, B2B buyers can make informed decisions that enhance the reliability and efficiency of their DC motor applications, ultimately leading to better operational outcomes.
Navigating Market Dynamics and Sourcing Trends in the dc electric motor parts Sector
What Are the Current Market Dynamics and Key Trends in the DC Electric Motor Parts Sector?
The global market for DC electric motor parts is witnessing significant growth driven by increasing demand for energy-efficient solutions across various industries. Key trends include the integration of advanced technologies such as IoT and AI, which enhance monitoring and performance optimization of electric motors. Additionally, there is a rising focus on automation and robotics in manufacturing processes, particularly in sectors like automotive, aerospace, and renewable energy. For B2B buyers in regions such as Africa, South America, the Middle East, and Europe, understanding these dynamics is crucial for strategic sourcing.
Emerging sourcing trends also highlight the need for suppliers who offer not only high-quality components but also rapid delivery and flexible order quantities. The shift towards online procurement platforms has made it easier for international buyers to access a wider range of products and suppliers. Furthermore, regional variations in demand are notable; for instance, countries in Africa are increasingly investing in electric infrastructure, while European nations push for sustainability in manufacturing. Buyers must stay informed about local market conditions and supplier capabilities to make informed purchasing decisions.
How Are Sustainability and Ethical Sourcing Impacting the DC Electric Motor Parts Market?
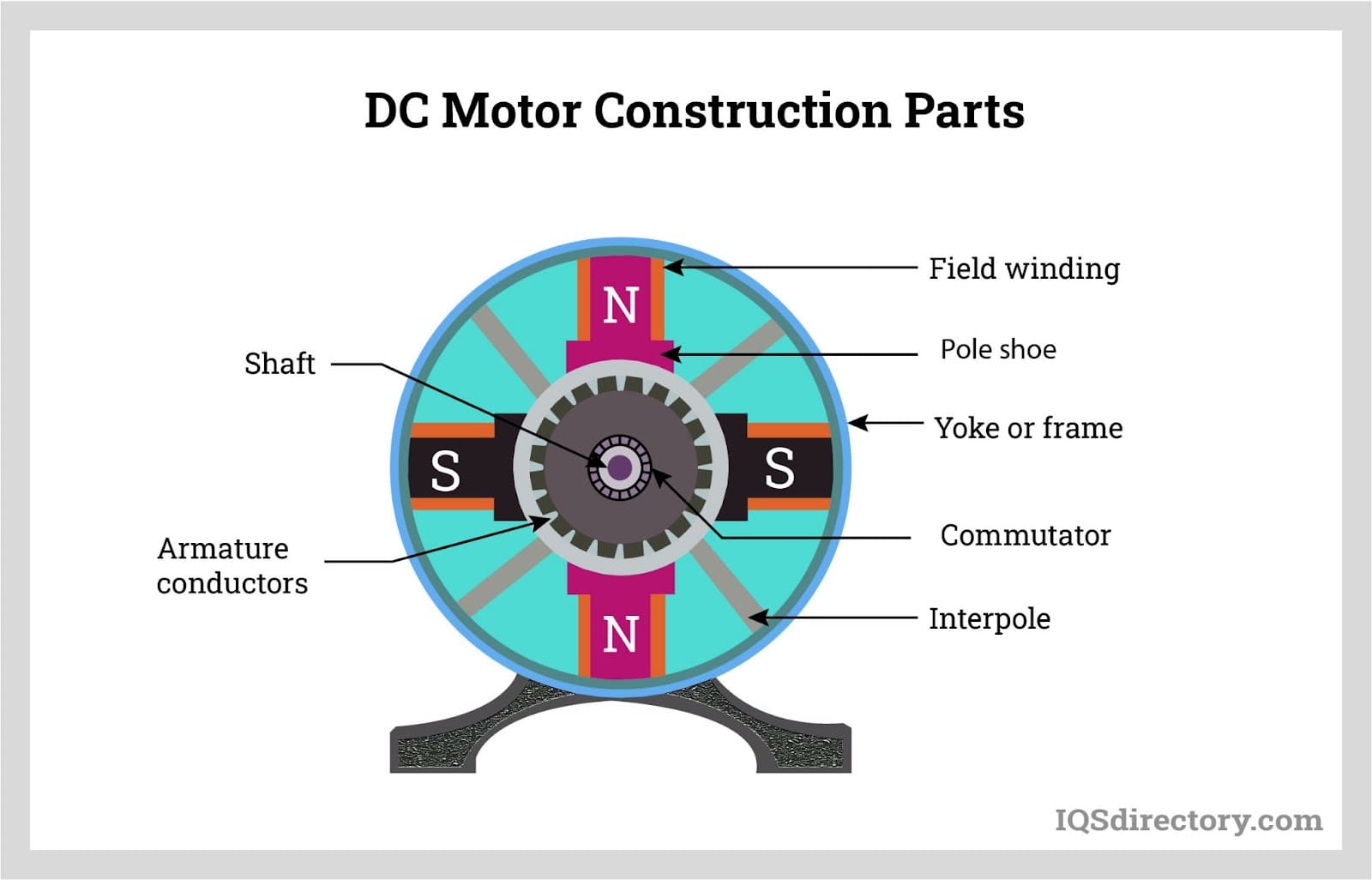
A stock image related to dc electric motor parts.
Sustainability is becoming a pivotal factor in the sourcing of DC electric motor parts. As global awareness of environmental issues grows, buyers are increasingly prioritizing suppliers that adhere to sustainable practices. This includes sourcing materials responsibly and minimizing waste in production processes. The environmental impact of the electric motor parts industry is significant, as traditional manufacturing methods can lead to high carbon footprints and resource depletion.
Ethical supply chains are gaining traction, emphasizing transparency and social responsibility in sourcing practices. B2B buyers should seek suppliers who hold certifications such as ISO 14001 for environmental management and other “green” credentials that guarantee sustainable sourcing. Additionally, materials such as recycled metals and eco-friendly composites are becoming more prevalent in the production of motor parts. By prioritizing sustainability and ethical sourcing, international buyers can not only comply with regulatory standards but also enhance their brand reputation and appeal to environmentally-conscious consumers.
What Is the Evolution of the DC Electric Motor Parts Sector and Its Relevance for B2B Buyers?
The evolution of the DC electric motor parts sector can be traced back to the early 19th century, with significant advancements occurring throughout the 20th century as industries began to recognize the potential of electric motors in various applications. The transition from traditional mechanical systems to electric-driven solutions marked a major turning point, leading to enhanced efficiency and reduced operational costs.
In recent years, the advent of digital technologies has further transformed the sector, enabling manufacturers to innovate and improve the performance of DC motors and their components. For B2B buyers, this historical context is essential as it highlights the ongoing advancements in motor technology, which can directly impact procurement strategies and supplier selection. Understanding the trajectory of the market helps buyers anticipate future trends and make informed decisions that align with their operational goals.
Frequently Asked Questions (FAQs) for B2B Buyers of dc electric motor parts
-
How do I solve common issues with DC motor parts?
To address common issues like excessive wear on brushes or poor motor performance, regular maintenance is key. This includes inspecting the commutator for wear, ensuring proper brush alignment, and replacing worn brushes timely. Additionally, using high-quality replacement parts can enhance performance. For international buyers, understanding local sourcing options for these components can help mitigate downtime. Establishing a maintenance schedule can also prevent minor issues from escalating into significant problems. -
What is the best type of carbon brush for my DC motor application?
The ideal carbon brush varies based on the specific requirements of your DC motor application. For general industrial use, carbon brushes with a medium hardness are typically recommended, as they provide good conductivity and wear resistance. If your application involves high speeds or temperatures, consider graphite brushes, which offer lower friction. Consult with suppliers to understand the best materials available based on your operational conditions, and request samples for testing before placing larger orders. -
How can I effectively vet suppliers of DC electric motor parts?
When vetting suppliers, prioritize those with a proven track record in the industry. Check for certifications, such as ISO standards, which indicate quality assurance processes. Request references from previous clients, and conduct background checks to assess reliability. Additionally, consider suppliers that offer a warranty on their parts, as this reflects confidence in their products. Engaging in direct communication can also provide insights into their customer service approach and responsiveness. -
What are the typical minimum order quantities (MOQs) for DC motor parts?
MOQs can vary significantly based on the type of DC motor parts and the supplier. Generally, manufacturers may set MOQs ranging from 10 to 100 units for standard parts, while custom components might have higher MOQs. It is advisable to discuss your specific needs with suppliers to negotiate MOQs that align with your operational requirements. Some suppliers may be flexible, especially for initial orders or trial runs, so it’s worth exploring options. -
What payment terms should I expect when purchasing DC motor parts internationally?
Payment terms can differ based on the supplier’s policies and your negotiation. Common terms include upfront payments, a percentage deposit with the balance upon delivery, or net 30/60 days after invoice receipt. For international transactions, consider using secure payment methods such as letters of credit or escrow services to protect against fraud. Always clarify terms in your contract to avoid misunderstandings and ensure timely payments. -
How do I ensure quality assurance (QA) for DC motor parts?
Quality assurance should start with selecting reputable suppliers known for their rigorous QA processes. Request documentation such as test reports, quality certifications, and compliance with international standards. Additionally, consider implementing your own QA checks upon receipt of goods, including visual inspections and functional tests. Establishing a feedback loop with your suppliers can also help address any quality issues promptly and ensure continuous improvement. -
What logistics considerations should I be aware of when sourcing DC motor parts?
Logistics play a critical role in international sourcing. Assess shipping options, including air versus sea freight, based on your budget and urgency. Understand customs regulations in your country to avoid delays or additional costs. Partnering with a reliable freight forwarder can simplify the shipping process and help navigate complex documentation. Additionally, consider lead times and plan your orders accordingly to maintain inventory levels without disrupting operations. -
Can I customize DC motor parts to meet specific requirements?
Yes, many suppliers offer customization options for DC motor parts, including specific dimensions, materials, and performance characteristics. When considering customization, clearly outline your requirements and engage in discussions with potential suppliers to explore their capabilities. Keep in mind that custom parts may have longer lead times and higher costs, so factor these into your planning. Request prototypes or samples before committing to larger orders to ensure the custom parts meet your expectations.
Important Disclaimer & Terms of Use
⚠️ Important Disclaimer
The information provided in this guide, including content regarding manufacturers, technical specifications, and market analysis, is for informational and educational purposes only. It does not constitute professional procurement advice, financial advice, or legal advice.
While we have made every effort to ensure the accuracy and timeliness of the information, we are not responsible for any errors, omissions, or outdated information. Market conditions, company details, and technical standards are subject to change.
B2B buyers must conduct their own independent and thorough due diligence before making any purchasing decisions. This includes contacting suppliers directly, verifying certifications, requesting samples, and seeking professional consultation. The risk of relying on any information in this guide is borne solely by the reader.
Strategic Sourcing Conclusion and Outlook for dc electric motor parts
In the evolving landscape of DC electric motor parts, strategic sourcing has emerged as a critical component for international B2B buyers. By understanding the intricate relationships between core components such as armatures, commutators, and brushes, buyers can make informed decisions that enhance performance and reliability. Prioritizing quality and supplier partnerships can significantly reduce downtime and maintenance costs, especially in industries reliant on efficient motor operation.
Why Is Strategic Sourcing Important for DC Motor Parts?
Investing in strategic sourcing allows businesses to leverage global supply chains, optimizing procurement processes while ensuring access to high-quality materials. This is particularly essential for buyers in Africa, South America, the Middle East, and Europe, where local suppliers may vary in capability and reliability.
What Should International Buyers Focus On Moving Forward?
As we look ahead, international buyers must remain proactive in identifying suppliers who not only offer competitive pricing but also demonstrate a commitment to innovation and quality assurance. Engaging with suppliers that provide comprehensive support, including maintenance and technical expertise, will be key to maintaining operational efficiency.
In conclusion, the future of DC motor parts sourcing is bright for those willing to adapt and invest in strategic partnerships. Now is the time to explore new opportunities and elevate your procurement strategy to ensure sustained growth and success in your operations.