The Ultimate Guide to Dc Motor Direct Current (2025)
Introduction: Navigating the Global Market for dc motor direct current
Navigating the global market for DC motors can be a daunting task for international B2B buyers, particularly in regions such as Africa, South America, the Middle East, and Europe. With the growing demand for efficient and reliable direct current (DC) motors across various industries—from automotive to robotics—buyers face the challenge of sourcing the right products that meet specific operational needs and compliance standards. This guide aims to demystify the complexities of the DC motor market by offering a comprehensive overview of the types of DC motors available, their applications, and essential factors to consider when vetting suppliers.
Within this guide, you will find detailed insights into the different types of DC motors, including brushed, brushless, and stepper motors, along with their respective advantages and ideal use cases. We will also explore critical aspects such as pricing structures, quality assurance, and the importance of supplier reliability. By empowering buyers with actionable strategies and informed decision-making tools, this guide serves as a vital resource for international B2B buyers seeking to navigate the intricacies of the DC motor market effectively. Whether you are operating in Argentina, Mexico, or elsewhere, understanding these elements will facilitate smarter purchasing decisions that align with your business goals and operational requirements.
Understanding dc motor direct current Types and Variations
Type Name | Key Distinguishing Features | Primary B2B Applications | Brief Pros & Cons for Buyers |
---|---|---|---|
Brushed DC Motors | Utilize brushes and commutators for current switching | Automotive, robotics, and industrial tools | Pros: Simple design, cost-effective. Cons: Shorter lifespan due to brush wear. |
Brushless DC Motors | Use electronic commutation, eliminating brushes | HVAC systems, drones, and electric vehicles | Pros: Longer lifespan, higher efficiency. Cons: Higher initial cost. |
Shunt DC Motors | Field windings connected in parallel with the armature | Manufacturing equipment, conveyors | Pros: Good speed regulation. Cons: Lower starting torque. |
Series DC Motors | Field windings connected in series with the armature | Cranes, elevators, and traction systems | Pros: High starting torque. Cons: Speed regulation can be challenging. |
Permanent Magnet DC Motors | Use permanent magnets for the magnetic field | Toys, home appliances, and small machinery | Pros: Compact, lightweight. Cons: Limited torque at high speeds. |
What Are the Key Characteristics of Brushed DC Motors?
Brushed DC motors are characterized by their use of brushes and a commutator to switch current direction in the armature winding. This design is straightforward and cost-effective, making it a popular choice for various applications, especially in automotive and robotic sectors. However, buyers should consider the shorter lifespan due to brush wear, which can lead to increased maintenance costs over time.
How Do Brushless DC Motors Differ in Functionality?
Brushless DC motors eliminate the need for brushes by using electronic commutation, which enhances durability and efficiency. They are suitable for applications requiring precision and reliability, such as HVAC systems and electric vehicles. While the initial investment is higher, the long-term savings on maintenance and energy efficiency can justify the cost for B2B buyers looking for sustainable solutions.
What Makes Shunt DC Motors Suitable for Industrial Applications?
Shunt DC motors have their field windings connected in parallel with the armature, which allows for effective speed regulation. This feature makes them ideal for manufacturing equipment and conveyor systems where consistent speed is crucial. However, they may provide lower starting torque, which could be a disadvantage in applications requiring high initial force.
Why Are Series DC Motors Preferred for Heavy-Duty Applications?
Series DC motors connect their field windings in series with the armature, resulting in high starting torque. This characteristic makes them particularly suitable for heavy-duty applications like cranes and elevators. Despite their advantages, buyers should be aware that speed regulation can be challenging, which may necessitate additional control systems for certain applications.
What Are the Advantages of Permanent Magnet DC Motors?
Permanent magnet DC motors use permanent magnets to generate the magnetic field, resulting in a compact and lightweight design. They are commonly found in toys, home appliances, and small machinery where space and weight are critical factors. However, their torque may be limited at high speeds, making them less suitable for applications requiring consistent high performance. B2B buyers should assess the specific requirements of their projects when considering this motor type.
Key Industrial Applications of dc motor direct current
Industry/Sector | Specific Application of dc motor direct current | Value/Benefit for the Business | Key Sourcing Considerations for this Application |
---|---|---|---|
Automotive | Electric Vehicle (EV) Powertrains | Enhanced energy efficiency and performance | Supplier reliability, motor efficiency ratings |
Manufacturing | Conveyor Systems | Improved material handling and process automation | Load capacity, durability, and maintenance support |
Robotics | Automated Guided Vehicles (AGVs) | Increased operational efficiency and flexibility | Precision control, integration with existing systems |
HVAC Systems | Ventilation and Air Conditioning | Energy savings and improved climate control | Voltage compatibility, noise levels, and size |
Consumer Electronics | Electric Tools and Appliances | Higher performance and user satisfaction | Safety standards, power requirements, and warranty |
How Are DC Motors Used in the Automotive Sector?
In the automotive industry, DC motors play a pivotal role in electric vehicle (EV) powertrains. They are responsible for converting electrical energy from batteries into mechanical energy, driving the wheels efficiently. This application addresses the growing demand for sustainable transportation solutions, particularly in regions like Europe and South America, where environmental regulations are tightening. International buyers should consider sourcing high-efficiency motors that comply with local standards and offer robust performance under varying climatic conditions.
What Role Do DC Motors Play in Manufacturing?
DC motors are integral to conveyor systems in manufacturing, facilitating the movement of materials between production stages. By automating these processes, businesses can significantly enhance productivity and reduce labor costs. This is especially beneficial for manufacturers in Africa and South America, where labor costs may be higher. Buyers should prioritize sourcing motors that can handle specific load capacities and are designed for continuous operation to minimize downtime.
How Are DC Motors Enhancing Robotics Applications?
In the robotics sector, DC motors are essential for powering automated guided vehicles (AGVs). These vehicles rely on precise motor control to navigate production environments and transport goods, increasing efficiency and reducing human error. For international buyers, especially in the Middle East and Europe, it is crucial to ensure that the sourced motors provide excellent torque control and can integrate seamlessly with existing robotic systems.
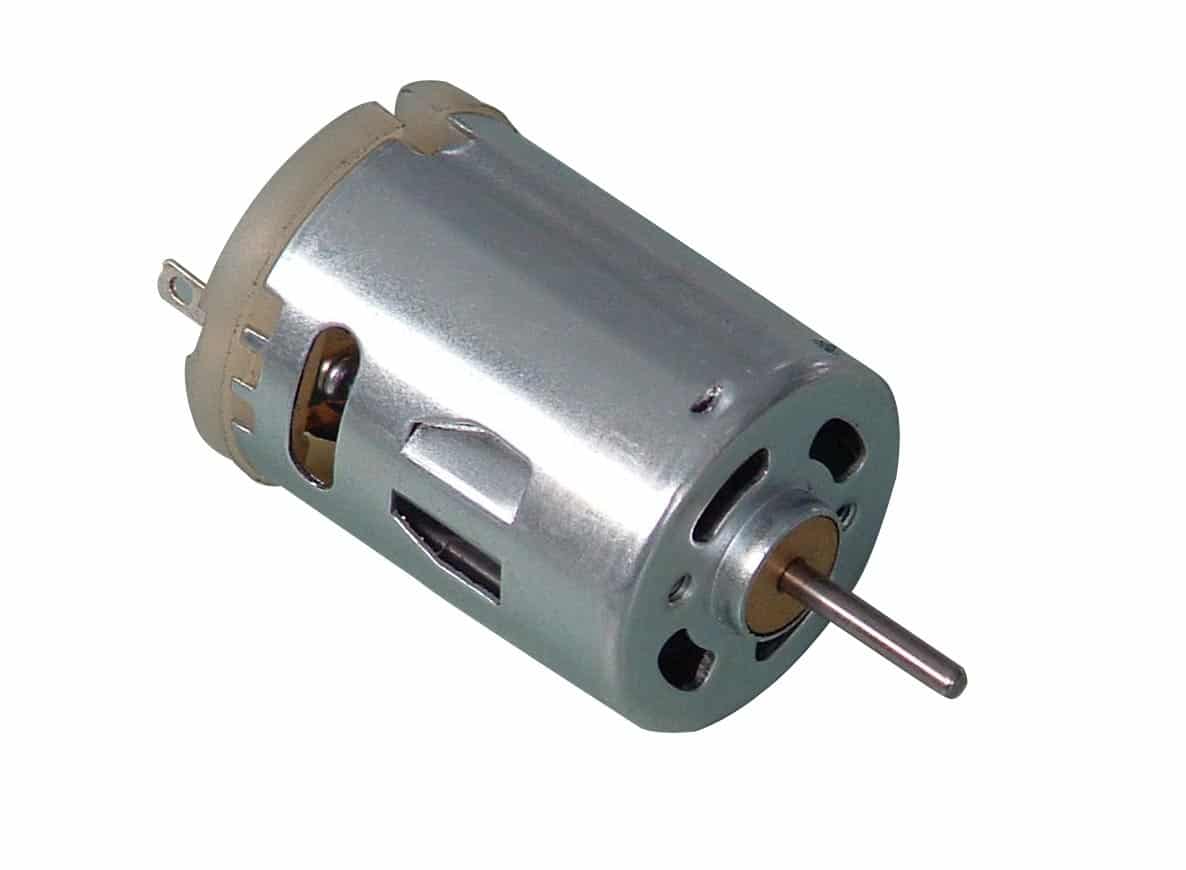
A stock image related to dc motor direct current.
Why Are DC Motors Important in HVAC Systems?
DC motors are commonly employed in HVAC systems for ventilation and air conditioning applications. They help regulate airflow and maintain temperature efficiently, leading to significant energy savings. This is particularly relevant in regions with extreme climates, such as the Middle East. Buyers should focus on sourcing motors that meet energy efficiency standards and have low noise levels, as these factors directly impact user satisfaction and operational costs.
How Do DC Motors Benefit Consumer Electronics?
In consumer electronics, DC motors are vital for powering electric tools and appliances, enhancing their performance and user experience. They enable precise control over device operations, which is crucial for customer satisfaction. For B2B buyers in South America and Africa, sourcing motors that meet safety standards and specific power requirements is essential to ensure compliance and reliability in the end products.
3 Common User Pain Points for ‘dc motor direct current’ & Their Solutions
Scenario 1: Ensuring Compatibility with Existing Systems
The Problem: One of the most pressing issues for B2B buyers when sourcing DC motors is ensuring compatibility with existing systems. In regions like Africa and South America, where infrastructure may vary significantly, mismatched voltage and current ratings can lead to operational failures. Buyers often find themselves purchasing a motor that doesn’t integrate well with their equipment, causing delays and unexpected costs.
The Solution: To avoid compatibility issues, it’s crucial to conduct a thorough assessment of the existing systems before making a purchase. Start by documenting the voltage and current specifications of the systems where the DC motor will be installed. Additionally, consult with manufacturers or suppliers about the specific requirements of your setup, as they can offer insight into which motor types—such as brushed or brushless—will perform best. Utilizing simulation tools or software can also help visualize how the new motor will interact with your current machinery, ensuring a seamless integration. Furthermore, consider sourcing motors that offer adjustable voltage or multi-voltage capabilities to accommodate various operational environments.
Scenario 2: Managing Operational Efficiency and Performance
The Problem: Many international B2B buyers face challenges related to the operational efficiency of DC motors. In industries ranging from manufacturing to transportation, the performance of these motors can significantly affect productivity. Buyers often encounter issues like overheating, inefficient power consumption, and inadequate torque output, which can lead to machinery downtimes and increased operational costs.
The Solution: To enhance operational efficiency, buyers should prioritize the selection of high-quality DC motors with specific performance ratings suited for their application. Look for motors with advanced features, such as thermal protection and variable speed drives, which can optimize performance and reduce energy consumption. Conducting regular maintenance checks and monitoring motor performance metrics can also help identify inefficiencies before they escalate. Implementing smart monitoring technologies, such as IoT sensors, can provide real-time data on motor performance, allowing for timely interventions that maximize productivity. Additionally, consider engaging with suppliers who offer tailored solutions and ongoing support for optimizing motor performance in your specific industrial context.
Scenario 3: Navigating the Supply Chain for Timely Delivery
The Problem: Supply chain disruptions can pose significant challenges for B2B buyers of DC motors, particularly in regions like the Middle East and Europe, where geopolitical factors can impact shipping and delivery times. Buyers often experience delays that hinder project timelines, resulting in lost revenue and strained client relationships.
The Solution: To navigate these supply chain challenges, buyers should develop relationships with multiple suppliers to create a diversified procurement strategy. Engaging with local suppliers can reduce lead times and shipping costs, while also providing the opportunity for face-to-face consultations regarding specific requirements. Buyers can also consider implementing just-in-time (JIT) inventory management practices to better align procurement with project timelines, minimizing the risk of overstocking or shortages. Additionally, utilizing digital procurement platforms can enhance visibility into inventory levels and streamline the ordering process. By establishing clear communication channels with suppliers regarding expected delivery timelines and potential risks, buyers can better manage their operations and mitigate the impact of supply chain uncertainties.
Strategic Material Selection Guide for dc motor direct current
When selecting materials for DC motors, international B2B buyers must consider a variety of factors, including the properties of the materials, their suitability for specific applications, and compliance with regional standards. Here’s a detailed analysis of four common materials used in DC motor construction.
What Are the Key Properties of Copper in DC Motors?
Copper is one of the most widely used materials in DC motors, particularly for windings and connections. Its excellent electrical conductivity (approximately 59.6 x 10^6 S/m) allows for efficient energy transfer, which is critical for motor performance. Additionally, copper has a high melting point (around 1,984°F or 1,085°C) and good thermal conductivity, making it suitable for high-temperature applications.
Pros & Cons:
Copper is highly durable and resistant to corrosion, which enhances the longevity of the motor. However, it is relatively expensive compared to alternatives like aluminum, and its weight can be a disadvantage in applications where reducing mass is crucial.
Impact on Application:
Copper is compatible with a wide range of media and environments, making it a versatile choice for various applications. Its high conductivity ensures that motors can operate efficiently, even under heavy loads.
Considerations for International Buyers:
Buyers from regions such as Africa and South America should ensure that their suppliers comply with international standards like ASTM B170 for copper wire. Additionally, understanding the local availability and pricing trends for copper can aid in cost-effective procurement.
Why Is Aluminum a Popular Choice for DC Motors?
Aluminum is increasingly used in DC motors, especially for the rotor and housing components. It has a lower density than copper, making it a lightweight alternative, which is particularly advantageous in portable applications.
Pros & Cons:
Aluminum is less expensive than copper and offers good corrosion resistance, especially when anodized. However, its electrical conductivity is only about 61% that of copper, which may impact performance in high-load scenarios.
Impact on Application:
Aluminum is suitable for applications requiring weight reduction, such as automotive and aerospace. Its compatibility with various environments is also beneficial, although it may require additional treatment to enhance its durability.
Considerations for International Buyers:
Buyers in Europe and the Middle East should be aware of European standards like EN 60228 for conductors. Understanding the local market dynamics for aluminum can also help in making informed purchasing decisions.
How Does Steel Contribute to the Durability of DC Motors?
Steel is commonly used for the structural components of DC motors, such as the frame and shaft. Its high tensile strength and durability make it an ideal choice for heavy-duty applications.
Pros & Cons:
Steel is relatively inexpensive and offers excellent mechanical properties, including resistance to wear and deformation. However, it is prone to corrosion, which can be a significant drawback in humid or corrosive environments unless properly treated.
Impact on Application:
Steel is suitable for applications requiring robust construction, such as industrial machinery. However, its weight can be a disadvantage in applications where weight is a critical factor.
Considerations for International Buyers:
Buyers should ensure that the steel used complies with relevant standards, such as ASTM A36 for structural steel. Understanding local regulations regarding material sourcing and environmental impact can also guide purchasing decisions.
What Role Does Plastic Play in DC Motor Applications?
Plastics, particularly engineered thermoplastics, are often used for non-structural components in DC motors, such as housings and insulation. They are lightweight and can be molded into complex shapes.
Pros & Cons:
Plastics offer excellent corrosion resistance and can be produced at a lower cost than metals. However, they generally have lower mechanical strength and thermal stability compared to metals, which may limit their use in high-stress applications.
Impact on Application:
Plastics are suitable for applications where weight reduction and corrosion resistance are priorities, such as in consumer electronics. However, their performance may be compromised in high-temperature or high-load scenarios.
Considerations for International Buyers:
Buyers should consider compliance with standards like ISO 9001 for quality management systems. Additionally, understanding the specific types of plastics available in local markets can facilitate better material selection.
Summary Table of Material Selection for DC Motors
Material | Typical Use Case for dc motor direct current | Key Advantage | Key Disadvantage/Limitation | Relative Cost (Low/Med/High) |
---|---|---|---|---|
Copper | Windings and connections | Excellent electrical conductivity | High cost | High |
Aluminum | Rotor and housing components | Lightweight and cost-effective | Lower conductivity | Medium |
Steel | Structural components | High strength and durability | Prone to corrosion | Low |
Plastic | Non-structural components | Corrosion-resistant and lightweight | Lower mechanical strength | Low |
This strategic material selection guide provides international B2B buyers with actionable insights into the properties, advantages, and limitations of various materials used in DC motors, helping them make informed decisions tailored to their specific regional needs and applications.
In-depth Look: Manufacturing Processes and Quality Assurance for dc motor direct current
What Are the Main Stages of Manufacturing DC Motors?
The manufacturing process of direct current (DC) motors is a complex interplay of precision engineering and quality control. It typically involves several key stages, including material preparation, forming, assembly, and finishing. Understanding these processes can help B2B buyers evaluate suppliers and ensure that they are sourcing high-quality products.
How Is Material Prepared for DC Motor Manufacturing?
Material preparation is the first step in manufacturing DC motors. This involves selecting high-grade materials, such as copper for windings, silicon steel for the stator and rotor, and various plastics for insulation. The quality of these materials directly affects the motor’s efficiency and lifespan.
- Material Selection: Ensure suppliers use materials that meet international standards, such as ASTM or ISO specifications. This is particularly important for buyers in Africa, South America, the Middle East, and Europe, where varying material quality can impact performance.
- Material Testing: Before production, materials undergo testing to verify their mechanical and electrical properties. Techniques such as tensile testing, hardness testing, and electrical conductivity tests are commonly employed.
What Techniques Are Used in Forming DC Motors?
Forming is the next critical stage where the prepared materials are shaped into components. This stage includes several techniques:
- Stamping and Machining: The stator and rotor cores are typically produced through stamping processes. Precision machining is then used to create the necessary slots for windings and to achieve the desired dimensions.
- Winding: The winding process is crucial. Automated winding machines are often employed to wrap copper wire around the stator and rotor. This step requires high precision to ensure the correct number of turns and tension, which directly influences motor performance.
How Is the Assembly Process Conducted?
Assembly is where various components come together to form the complete DC motor. This stage involves:
- Component Assembly: The rotor is inserted into the stator, and the winding connections are made. This process often involves automated systems to ensure accuracy.
- Integration of Electronic Components: For brushless DC motors, electronic controllers are integrated during this phase. This requires specialized knowledge to ensure proper functionality and reliability.
What Finishing Processes Are Required for DC Motors?
Finishing processes are essential for enhancing the motor’s durability and performance. Key finishing techniques include:
- Coating: Motors may receive protective coatings to prevent corrosion and wear. This is particularly important for motors used in harsh environments, common in industries across Africa and the Middle East.
- Final Inspection: After finishing, each motor undergoes a final inspection to check for defects or inconsistencies. This step is crucial for ensuring that only high-quality products reach the market.
How Is Quality Assurance Implemented in DC Motor Manufacturing?
Quality assurance (QA) is vital in the manufacturing of DC motors. It ensures that products meet both international and industry-specific standards, which is crucial for B2B buyers.
What International Standards Are Relevant for DC Motors?
International standards such as ISO 9001 play a significant role in quality management systems across industries. For DC motors, compliance with these standards ensures consistency in manufacturing processes.
- ISO 9001: This standard focuses on meeting customer expectations and delivering satisfaction. Suppliers certified to this standard have demonstrated their ability to consistently provide products that meet quality requirements.
- CE Marking: In Europe, CE marking indicates compliance with health, safety, and environmental protection standards. Buyers in Europe should verify that their suppliers have this certification.
What Are the Common QC Checkpoints in DC Motor Manufacturing?
Quality control checkpoints are integrated throughout the manufacturing process. Key checkpoints include:
- Incoming Quality Control (IQC): This involves inspecting raw materials and components upon arrival at the manufacturing facility. Ensuring that incoming materials meet specified standards is critical.
- In-Process Quality Control (IPQC): During manufacturing, processes are monitored to detect any deviations from established procedures. Regular checks help identify issues early, preventing defects from progressing.
- Final Quality Control (FQC): This last step involves comprehensive testing of the finished motors to ensure they meet performance specifications. Common tests include electrical testing, thermal testing, and vibration analysis.
What Testing Methods Are Commonly Used for DC Motors?
Testing is integral to quality assurance, ensuring that DC motors perform as expected under various conditions. Common testing methods include:
- Electrical Testing: Verification of electrical characteristics such as voltage, current, and resistance is essential. This helps ensure that the motor operates efficiently and safely.
- Performance Testing: Motors are subjected to load tests to assess their performance under realistic operating conditions. This includes measuring torque, speed, and temperature.
- Durability Testing: Long-term reliability is critical, particularly for motors used in demanding applications. Testing under accelerated conditions helps predict the lifespan of the motor.
How Can B2B Buyers Verify Supplier Quality Control?
For B2B buyers, especially those from regions like Africa and South America, verifying a supplier’s quality control processes is crucial for ensuring product reliability. Here are several strategies:
- Supplier Audits: Conducting audits of potential suppliers can provide insights into their manufacturing processes and quality control measures. This is particularly important when sourcing from regions with varying manufacturing standards.
- Quality Assurance Reports: Requesting QA reports can offer additional confidence. These reports should detail the results of testing and inspections conducted throughout the manufacturing process.
- Third-Party Inspections: Engaging third-party inspection services can provide an unbiased assessment of a supplier’s quality control practices. This can be particularly valuable for international transactions where local standards may differ.
What Are the QC and Certification Nuances for International B2B Buyers?
International buyers must navigate various nuances related to quality control and certification when sourcing DC motors. Some important considerations include:
- Regional Standards: Understanding regional standards is crucial. For example, what is acceptable in Europe may not be sufficient in Africa or South America. Buyers should familiarize themselves with local regulations and standards.
- Cultural Differences: Different regions may have varying approaches to quality control. Building relationships and open communication with suppliers can help bridge these gaps.
- Documentation: Ensure that suppliers provide all necessary documentation, including certifications, testing results, and compliance statements. This documentation is essential for validating quality and compliance with international standards.
By understanding the manufacturing processes and quality assurance measures related to DC motors, B2B buyers can make informed decisions, ensuring that they source reliable and high-quality products tailored to their specific needs.
Practical Sourcing Guide: A Step-by-Step Checklist for ‘dc motor direct current’
To assist international B2B buyers in effectively sourcing direct current (DC) motors, this guide provides a structured checklist. Each step highlights key considerations and actions to ensure a successful procurement process.
Step 1: Define Your Technical Specifications
Before beginning your search, clearly outline the technical requirements of the DC motor you need. Consider factors such as voltage, current rating, power output, and size.
– Why it matters: Precise specifications help avoid confusion and ensure that the motor will meet your operational needs.
– What to look for: Create a detailed list that includes the type of application (e.g., automotive, industrial machinery) and any environmental conditions (e.g., temperature, humidity) the motor will face.
Step 2: Research Different Types of DC Motors
Familiarize yourself with the various types of DC motors available, such as brushed, brushless, shunt, and series motors.
– Why it matters: Understanding the differences will help you choose the most suitable motor for your application.
– What to look for: Evaluate the advantages and disadvantages of each type, considering factors like efficiency, maintenance needs, and performance under load.
Step 3: Evaluate Potential Suppliers
Thoroughly vet potential suppliers to ensure they meet your quality and reliability standards.
– Why it matters: Partnering with a reputable supplier minimizes the risk of receiving subpar products that could impact your operations.
– What to look for: Request company profiles, product catalogs, and references from other buyers in your region or industry. Check for certifications that demonstrate compliance with international standards.
Step 4: Request Samples or Prototypes
Before finalizing your order, request samples or prototypes of the DC motors you are considering.
– Why it matters: Testing a sample allows you to verify the motor’s performance and compatibility with your systems.
– What to look for: Assess the sample for quality, performance metrics, and any specific features that are critical for your application.
Step 5: Negotiate Terms and Pricing
Once you have identified a suitable supplier, engage in negotiations regarding pricing, delivery timelines, and payment terms.
– Why it matters: Effective negotiation can lead to better pricing and more favorable terms that enhance your procurement budget.
– What to look for: Ensure that the terms are clear and mutually beneficial, and consider including clauses for after-sales support or warranties.
Step 6: Verify Compliance with Local Regulations
Ensure that the DC motors meet the local regulations and standards in your country or region.
– Why it matters: Non-compliance can lead to legal issues or delays in your project.
– What to look for: Confirm that the motors have the necessary certifications for safety and environmental standards applicable in your market.
Step 7: Establish a Long-term Relationship with the Supplier
After completing the initial purchase, focus on building a long-term relationship with your chosen supplier.
– Why it matters: A strong partnership can lead to better service, priority in supply chains, and potential discounts on future orders.
– What to look for: Maintain open communication and provide feedback on product performance, which can help the supplier improve their offerings.
By following this checklist, international B2B buyers can navigate the complexities of sourcing DC motors, ensuring they select the right products for their specific needs while fostering strong supplier relationships.
Comprehensive Cost and Pricing Analysis for dc motor direct current Sourcing
What Are the Key Cost Components in DC Motor Sourcing?
When sourcing DC motors, it’s essential to understand the various cost components that contribute to the total price. The primary cost components include:
-
Materials: The quality of materials directly influences the motor’s performance and durability. Common materials used in DC motors include copper for windings, steel for the stator, and various composites for housing. Sourcing high-quality materials can lead to better performance but may increase initial costs.
-
Labor: Labor costs vary significantly by region. In countries with lower labor costs, such as those in parts of Africa and South America, you might find competitive pricing. However, skilled labor for complex assembly can still be a significant factor regardless of location.
-
Manufacturing Overhead: This includes costs related to facilities, utilities, and equipment maintenance. Overhead can vary based on the manufacturing location and efficiency of the production process.
-
Tooling: Custom tooling for specific motor designs can significantly impact initial costs. For high-volume orders, investing in specialized tooling can yield long-term savings.
-
Quality Control (QC): Rigorous QC processes ensure that motors meet required standards, especially when dealing with international suppliers. The cost of QC can vary based on the complexity of the motor and the certifications required.
-
Logistics: Shipping and handling costs must be considered, particularly for international shipments. Factors such as distance, shipping method, and customs duties can significantly affect the overall cost.
-
Margin: Supplier margins can vary based on their pricing strategy, market conditions, and the competitive landscape. Understanding the margin structure can provide insights into potential negotiation points.
How Do Price Influencers Affect DC Motor Costs?
Several factors can influence the pricing of DC motors:
-
Volume/MOQ (Minimum Order Quantity): Larger orders typically attract discounts, allowing for more favorable pricing. International buyers should assess their needs carefully to leverage bulk purchasing advantages.
-
Specifications and Customization: Custom motors designed to meet specific requirements may incur additional costs. Buyers should balance their needs for customization with budget constraints.
-
Materials and Quality Certifications: Motors that meet specific industry standards (e.g., ISO, CE certifications) may command higher prices due to the assurance of quality and reliability. Buyers should weigh the importance of certifications against cost.
-
Supplier Factors: The reputation and experience of the supplier can affect pricing. Established suppliers may charge more due to their reliability and quality assurance.
-
Incoterms: Understanding Incoterms (International Commercial Terms) is crucial for international buyers. These terms determine who bears the cost and risk at various points in the shipping process and can influence overall pricing.
What Are Essential Tips for Negotiating DC Motor Prices?
For international B2B buyers, particularly from Africa, South America, the Middle East, and Europe, here are some actionable tips for negotiating better prices on DC motors:
-
Conduct a Total Cost of Ownership (TCO) Analysis: Evaluate not just the purchase price but also long-term costs associated with maintenance, energy consumption, and potential downtime. This comprehensive view can inform negotiations.
-
Leverage Relationships: Building strong relationships with suppliers can lead to better terms and potential discounts. Regular communication and feedback can foster trust and collaboration.
-
Be Transparent About Your Needs: Clearly communicate your specifications and requirements to suppliers. This transparency can help them provide more accurate quotes and avoid misunderstandings that could lead to additional costs.
-
Negotiate Payment Terms: Flexible payment terms can improve cash flow. Consider negotiating for extended payment periods or discounts for early payments.
-
Stay Informed About Market Trends: Understanding current market conditions, including material costs and supply chain challenges, can provide leverage in negotiations. Being well-informed allows buyers to make data-driven decisions.
Conclusion and Disclaimer
While the above insights provide a foundational understanding of the cost structure and pricing dynamics for DC motors, prices can vary widely based on market conditions and specific supplier agreements. It’s advisable to conduct thorough research and engage in direct discussions with suppliers to obtain the most accurate and relevant pricing information tailored to your needs.
Alternatives Analysis: Comparing dc motor direct current With Other Solutions
When evaluating electric motor solutions, it is essential for B2B buyers to consider alternatives to direct current (DC) motors. Each technology has unique advantages and disadvantages that can affect operational efficiency, cost, and overall performance in various applications. This section compares DC motors with two viable alternatives: AC motors and stepper motors.
Comparison Aspect | Dc Motor Direct Current | AC Motor | Stepper Motor |
---|---|---|---|
Performance | High torque at low speeds; variable speed control | Generally higher efficiency at high speeds; less torque at low speeds | Precise control of position and speed; limited torque compared to DC motors |
Cost | Moderate initial cost; lower long-term maintenance costs | Generally lower initial cost; higher operational costs due to energy consumption | Higher initial cost; potential savings in operational costs due to precision |
Ease of Implementation | Simple to implement; requires DC power supply | Widely used and easy to source; compatible with AC power supply | More complex due to control requirements; may need additional drivers |
Maintenance | Requires periodic brush replacement; lower overall maintenance | Generally low maintenance; can be subject to wear in high-load conditions | Minimal maintenance; robust in design |
Best Use Case | Applications requiring high torque at low speeds, like elevators | High-speed applications like fans and pumps | Applications requiring precise positioning, like 3D printers |
What Are the Pros and Cons of AC Motors as an Alternative to DC Motors?
AC motors are a popular alternative to DC motors, particularly due to their simplicity and efficiency at higher speeds. They are generally less expensive to purchase and maintain, making them an attractive option for many industrial applications. However, they can be less effective in applications requiring high torque at low speeds, which may necessitate the use of a gearbox or other mechanical solutions to achieve the desired performance.
How Do Stepper Motors Compare to DC Motors?
Stepper motors offer precise control over positioning and speed, making them ideal for applications that require high accuracy, such as robotics and CNC machinery. They can operate in open-loop control systems, eliminating the need for complex feedback mechanisms. However, stepper motors typically have lower torque compared to DC motors and can struggle in applications requiring rapid acceleration or high load, which may limit their applicability in certain industrial settings.
How Can B2B Buyers Choose the Right Solution for Their Needs?
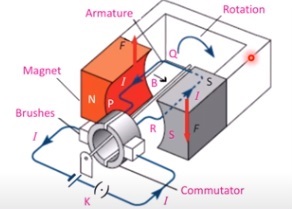
A stock image related to dc motor direct current.
When selecting between DC motors, AC motors, and stepper motors, B2B buyers should first assess their specific application requirements, including torque, speed, and precision needs. Cost considerations, including both initial and long-term operational expenses, are also critical. Additionally, understanding the ease of implementation and maintenance requirements can help buyers make informed decisions that align with their operational goals. By carefully weighing these factors, businesses can choose the most effective motor solution to meet their unique demands.
Essential Technical Properties and Trade Terminology for dc motor direct current
What Are the Key Technical Properties of DC Motors?
When considering the procurement of direct current (DC) motors, understanding their technical specifications is critical for ensuring compatibility with your applications. Here are some essential properties to evaluate:
1. Torque Rating
Torque is a measure of rotational force produced by the motor. It is vital for applications requiring specific movement or load handling. A higher torque rating generally indicates a motor’s ability to handle heavier loads, which is especially important in industries such as manufacturing and automotive. Buyers should assess the torque requirements of their applications to select a motor that meets or exceeds these needs.
2. Speed Rating (RPM)
The speed rating, measured in revolutions per minute (RPM), indicates how fast the motor can operate. Different applications may require different speeds; for instance, conveyor belts may need consistent low speeds, while fans may require higher RPMs. Understanding the required speed can help buyers choose the right motor for their specific operational requirements.
3. Voltage and Current Specifications
DC motors operate at specific voltage and current levels. These specifications determine the motor’s efficiency and performance. For instance, a motor operating at 12V will behave differently compared to one rated for 24V. Buyers should ensure compatibility with their power supply systems to avoid operational failures or inefficiencies.
4. Material Grade
The materials used in a DC motor affect its durability, heat resistance, and overall performance. Common materials include copper for windings and various grades of steel for the casing. High-grade materials can lead to longer service life and reduced maintenance costs, which is crucial for businesses looking to minimize downtime.
5. Duty Cycle
The duty cycle defines the operational time versus rest time of the motor. It is usually expressed as a percentage. Motors with a higher duty cycle are designed for continuous operation, while those with a lower duty cycle may be suited for intermittent use. Understanding duty cycles helps buyers select motors that align with their operational patterns, enhancing efficiency and longevity.
What Are Common Trade Terms Related to DC Motors?
Familiarity with industry terminology can streamline the procurement process and enhance communication with suppliers. Here are several important terms:
1. OEM (Original Equipment Manufacturer)
OEM refers to a company that produces parts or equipment that may be marketed by another manufacturer. In the context of DC motors, understanding whether a supplier is an OEM can help buyers ensure they are sourcing high-quality, reliable products. OEMs often provide better support and warranties.
2. MOQ (Minimum Order Quantity)
MOQ is the smallest number of units a supplier is willing to sell. Knowing the MOQ helps businesses plan their purchases and manage inventory effectively. For international buyers, particularly in Africa and South America, understanding MOQs can aid in budget management and supply chain planning.
3. RFQ (Request for Quotation)
An RFQ is a standard business process used to invite suppliers to bid on specific products or services. When purchasing DC motors, issuing an RFQ allows buyers to compare prices, lead times, and other terms from multiple vendors, ensuring they secure the best deal.
4. Incoterms (International Commercial Terms)
Incoterms are a series of predefined commercial terms published by the International Chamber of Commerce (ICC). They define the responsibilities of buyers and sellers in international transactions. Understanding Incoterms is crucial for international B2B buyers, as they govern shipping, insurance, and tariffs, impacting overall costs.
5. Lead Time
Lead time refers to the time taken from placing an order to the delivery of the product. For businesses relying on timely delivery of DC motors for production, understanding lead times helps in planning and minimizing disruptions. It’s advisable for buyers to clarify lead times during the procurement process to align with their operational schedules.
By grasping these technical properties and trade terms, international B2B buyers can make informed decisions, ensuring they select the right DC motors that meet their specific needs while navigating the complexities of global procurement.
Navigating Market Dynamics and Sourcing Trends in the dc motor direct current Sector
What Are the Current Market Dynamics and Key Trends Affecting the DC Motor Sector?
The global demand for DC motors is experiencing significant growth, driven by the increased automation across various industries such as automotive, aerospace, and manufacturing. International B2B buyers, particularly from Africa, South America, the Middle East, and Europe, should be aware of the following key trends shaping the market:
-
Technological Advancements: The integration of IoT and AI technologies is revolutionizing how DC motors are utilized. Smart motors equipped with sensors allow for real-time monitoring and predictive maintenance, thereby reducing downtime and enhancing operational efficiency.
-
Growing Demand for Energy Efficiency: As businesses strive to minimize operational costs and carbon footprints, energy-efficient DC motors are becoming a priority. These motors not only consume less power but also exhibit higher performance levels, making them an attractive option for industries aiming to meet sustainability goals.
-
Customization and Flexibility: B2B buyers are increasingly seeking tailored solutions that meet specific operational requirements. Manufacturers are responding by offering customizable DC motors that can be adapted for various applications, from small electronic devices to large industrial machines.
-
Emerging Markets: Countries in Africa and South America are witnessing a surge in industrialization, creating a robust market for DC motors. This growth presents opportunities for international buyers to source competitively priced motors while also supporting local economies.
-
Supply Chain Optimization: With global supply chain disruptions, companies are re-evaluating their sourcing strategies. Diversifying suppliers and focusing on local sourcing can mitigate risks and ensure a more resilient supply chain.
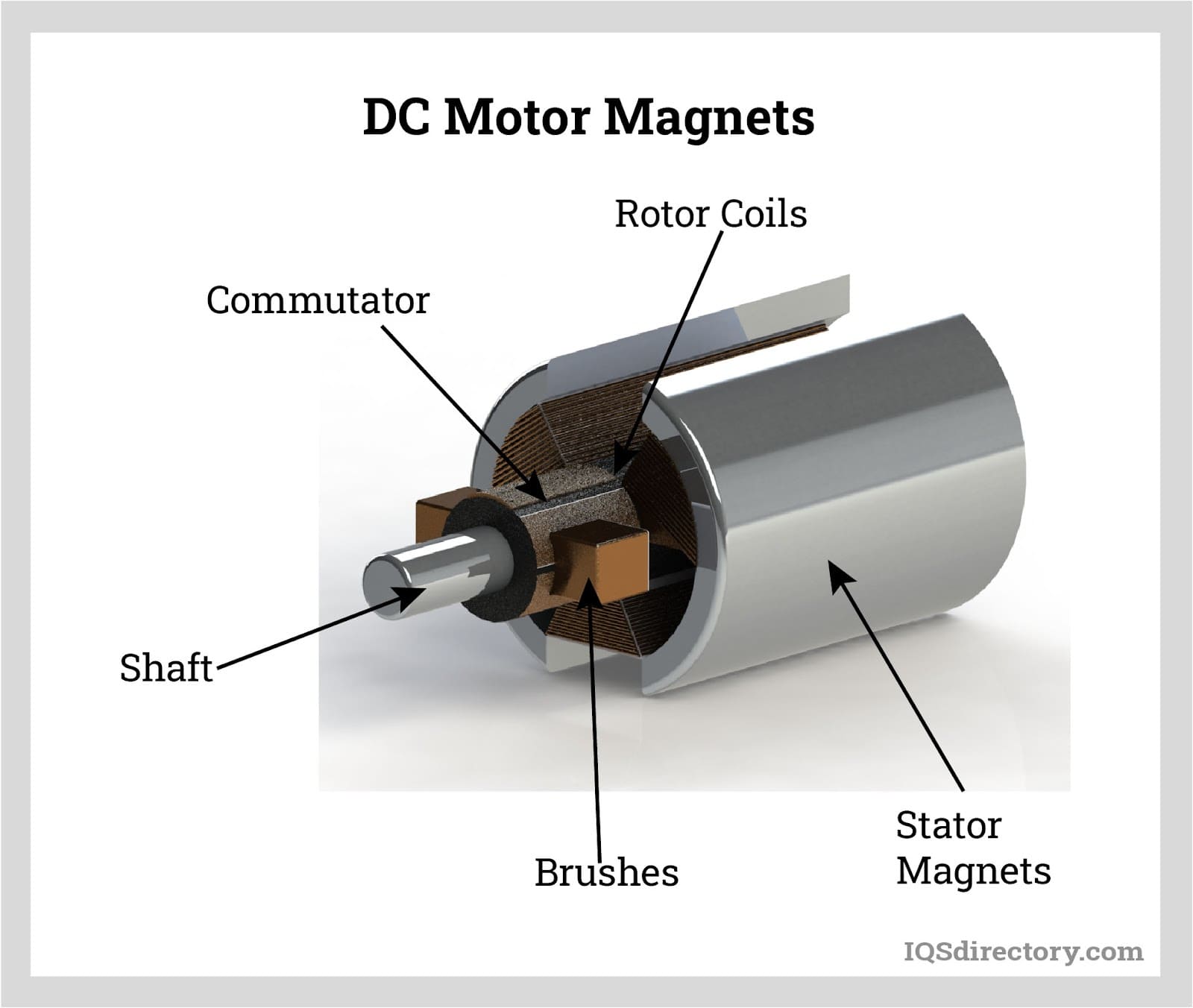
A stock image related to dc motor direct current.
How Can Sustainability and Ethical Sourcing Impact B2B Buyers in the DC Motor Sector?
Sustainability is becoming a critical consideration for B2B buyers of DC motors. The environmental impact of sourcing materials and manufacturing processes cannot be overlooked. Here are some ways sustainability and ethical sourcing play a role:
-
Environmental Regulations: Many countries are implementing stricter environmental regulations that require manufacturers to adopt sustainable practices. Buyers should prioritize suppliers who comply with these regulations, as it will ensure they are aligned with local and international standards.
-
Importance of Ethical Supply Chains: Companies are increasingly held accountable for their supply chain practices. Buyers should seek manufacturers that provide transparency in their sourcing processes, ensuring that materials are obtained ethically and sustainably.
-
Green Certifications and Materials: Certifications such as ISO 14001 (Environmental Management) and RoHS (Restriction of Hazardous Substances) are indicators of a manufacturer’s commitment to sustainability. Buyers should inquire about these certifications when sourcing DC motors, as they reflect a commitment to reducing environmental impact.
-
Lifecycle Considerations: Sustainable sourcing goes beyond initial production. B2B buyers should consider the entire lifecycle of the motor, including energy consumption during use and end-of-life recycling options, ensuring that they are making environmentally responsible choices.
What is the Brief Evolution of DC Motors Relevant to B2B Buyers?
The evolution of DC motors is significant for understanding their current applications and market dynamics. Initially developed in the early 19th century, DC motors have undergone considerable transformation. The first practical DC motor, invented by Frank Julian Sprague in 1886, paved the way for electric trolleys and elevators, revolutionizing transportation and urban infrastructure.
Over the years, advancements in materials, manufacturing processes, and control technologies have led to the development of various types of DC motors, including brushed and brushless variants. The transition from traditional brushed motors to brushless designs has improved efficiency and reduced maintenance needs, making them increasingly popular in industrial applications.
For B2B buyers, understanding this historical context provides insights into the reliability, advancements, and applications of DC motors, enabling informed purchasing decisions that align with modern technological needs and sustainability goals.
Frequently Asked Questions (FAQs) for B2B Buyers of dc motor direct current
-
How do I choose the right DC motor for my application?
Selecting the appropriate DC motor involves considering several factors, including torque requirements, speed, voltage, and the specific application. Assess the load characteristics and operational environment—whether it’s for industrial machinery, automotive, or consumer electronics. Additionally, consider the motor type (brushed or brushless) based on maintenance needs and efficiency. Collaborate with suppliers to ensure the motor specifications align with your operational requirements, and request samples to test performance in real-world conditions. -
What are the key benefits of using brushless DC motors over brushed motors?
Brushless DC motors offer enhanced durability and efficiency compared to brushed motors due to the absence of brushes, which wear out over time. They typically provide better speed control, lower maintenance costs, and increased lifespan, making them ideal for applications requiring high reliability. Additionally, brushless motors operate quieter and generate less heat, which can be beneficial in sensitive environments. For international buyers, these advantages can translate into long-term cost savings and improved operational efficiency. -
What customization options are available for DC motors?
Many manufacturers offer customization options for DC motors, including specific voltage ratings, size, mounting configurations, and winding types. Buyers can also request features such as integrated encoders for speed feedback, specific shaft configurations, and unique insulation materials for harsh environments. When sourcing, ensure to communicate your requirements clearly to potential suppliers, and inquire about their capabilities for custom orders to meet your specific needs. -
What is the minimum order quantity (MOQ) for DC motors?
The minimum order quantity for DC motors varies by manufacturer and product type. Generally, MOQs can range from a few units to several hundred or more, depending on production capabilities and material costs. For international buyers, it’s crucial to discuss MOQs upfront with suppliers, as lower MOQs may be available for standardized products. Additionally, some suppliers may offer flexibility on MOQs for repeat customers or larger projects. -
What payment terms should I negotiate when sourcing DC motors?
Payment terms can vary widely among suppliers, but common options include payment in advance, net 30, or net 60 days after delivery. It’s advisable to negotiate terms that balance your cash flow needs with the supplier’s requirements. Additionally, consider using secure payment methods such as letters of credit or escrow services for larger transactions. Always clarify these terms in your purchase agreement to avoid misunderstandings and ensure timely delivery. -
How can I ensure quality assurance (QA) for DC motors?
To ensure quality assurance for DC motors, request detailed specifications and quality control certifications from suppliers. Many manufacturers conduct routine testing, including performance, thermal, and electromagnetic tests, to verify product quality. Consider visiting the manufacturing facility or requesting third-party inspections before shipment. Establishing a clear QA process in your contract can help ensure that the motors meet your standards and reduce the risk of defects. -
What logistical considerations should I keep in mind when importing DC motors?
Logistics play a crucial role in importing DC motors, particularly regarding shipping methods, customs regulations, and delivery timelines. Assess whether air freight or sea freight is more suitable for your needs based on cost and urgency. Additionally, familiarize yourself with import duties, taxes, and any required documentation to avoid delays. Partnering with a reliable freight forwarder can streamline the process and help navigate complex international shipping regulations. -
How do I vet potential suppliers for DC motors?
Vetting suppliers is essential to ensure reliability and product quality. Start by researching their company history, customer reviews, and industry reputation. Request references and case studies from past clients to gauge their experience. Additionally, consider their production capabilities, certifications (ISO, CE), and after-sales support. Engaging in direct communication and visiting the facility, if possible, can provide further assurance of their reliability and alignment with your business standards.
Important Disclaimer & Terms of Use
⚠️ Important Disclaimer
The information provided in this guide, including content regarding manufacturers, technical specifications, and market analysis, is for informational and educational purposes only. It does not constitute professional procurement advice, financial advice, or legal advice.
While we have made every effort to ensure the accuracy and timeliness of the information, we are not responsible for any errors, omissions, or outdated information. Market conditions, company details, and technical standards are subject to change.
B2B buyers must conduct their own independent and thorough due diligence before making any purchasing decisions. This includes contacting suppliers directly, verifying certifications, requesting samples, and seeking professional consultation. The risk of relying on any information in this guide is borne solely by the reader.
Strategic Sourcing Conclusion and Outlook for dc motor direct current
What Are the Key Takeaways for B2B Buyers of DC Motors?
In the rapidly evolving landscape of direct current (DC) motors, strategic sourcing emerges as a crucial factor for B2B buyers aiming to optimize their procurement processes. Understanding the different types of DC motors—such as brushed, brushless, shunt, and series—enables buyers to make informed decisions tailored to their specific applications. Leveraging the strengths of each motor type can significantly enhance operational efficiency, reduce maintenance costs, and improve product performance.
How Can Strategic Sourcing Enhance Your Supply Chain?
Investing in strategic sourcing not only helps streamline your supply chain but also fosters strong relationships with reputable suppliers across diverse markets, including Africa, South America, the Middle East, and Europe. By prioritizing suppliers with proven track records in quality and innovation, businesses can mitigate risks associated with supply disruptions and fluctuating costs.
What Does the Future Hold for DC Motor Procurement?
As industries increasingly prioritize automation and energy efficiency, the demand for advanced DC motors is set to rise. International buyers are encouraged to stay ahead of market trends by adopting a proactive approach to sourcing. Engaging with suppliers who offer cutting-edge technologies and sustainable solutions will be vital in maintaining a competitive edge.
Embrace the opportunity to enhance your sourcing strategy today—partner with suppliers who can not only meet your current needs but also support your future growth in the dynamic world of DC motors.