The Ultimate Guide to Electric Motor Components (2025)
Introduction: Navigating the Global Market for electric motor components
In the rapidly evolving landscape of the global market for electric motor components, sourcing the right parts can be a daunting challenge for international B2B buyers. With a multitude of options available, from stators and rotors to bearings and brackets, navigating this complex supply chain requires a strategic approach. This comprehensive guide addresses key elements essential for informed purchasing decisions, including an overview of various motor types, their applications across different industries, and insights into supplier vetting processes that ensure quality and reliability.
International B2B buyers, particularly those in Africa, South America, the Middle East, and Europe (including countries like Spain and Poland), will find this guide invaluable. It not only demystifies the components that make up electric motors but also delves into critical considerations such as cost factors, material specifications, and compliance with regional standards. By equipping buyers with actionable insights and a clear understanding of the market dynamics, this guide empowers businesses to make educated decisions that enhance operational efficiency and reduce downtime.
Whether you are looking to upgrade existing machinery or develop new applications, understanding the intricacies of electric motor components is crucial. This guide is your roadmap to successfully navigating the global marketplace, ensuring you can source the right components to meet your business needs.
Understanding electric motor components Types and Variations
Type Name | Key Distinguishing Features | Primary B2B Applications | Brief Pros & Cons for Buyers |
---|---|---|---|
Squirrel-Cage Rotor | Simple design, robust, low maintenance | HVAC systems, industrial machinery | Pros: Cost-effective, reliable. Cons: Limited speed control. |
Permanent Magnet Stator | Utilizes permanent magnets for efficient operation | Electric vehicles, robotics | Pros: High efficiency, compact design. Cons: Higher initial cost. |
Inductor Rotor | Uses electromagnetic induction, typically in AC motors | Pumps, fans, compressors | Pros: Good starting torque. Cons: More complex design. |
Brushless DC Motor | Eliminates brushes, leading to less wear and tear | Consumer electronics, automotive applications | Pros: Higher efficiency, quieter operation. Cons: Higher upfront cost. |
Laminated Core | Reduces energy losses due to eddy currents | Transformers, high-efficiency motors | Pros: Improved performance, reduced heat generation. Cons: More expensive materials. |
What Are the Characteristics of Squirrel-Cage Rotors?
Squirrel-cage rotors are widely recognized for their simple and robust design. They consist of conductive bars shorted at both ends, creating a cage-like structure. This design allows for low maintenance and high reliability, making them suitable for HVAC systems and various industrial applications. When purchasing, buyers should consider the rotor’s efficiency and compatibility with their existing systems, as well as the potential for performance under varying loads.
Why Choose Permanent Magnet Stators?
Permanent magnet stators leverage the magnetic properties of permanent magnets to generate a magnetic field, leading to efficient energy conversion. This type is particularly suitable for electric vehicles and robotics due to its compact size and high efficiency. Buyers should weigh the initial investment against long-term energy savings and performance benefits. Understanding the specific application requirements is crucial for selecting the right stator type.
What Are the Benefits of Inductor Rotors?
Inductor rotors operate using electromagnetic induction, typically found in AC motors. They provide good starting torque, making them ideal for applications like pumps, fans, and compressors. When considering an inductor rotor, B2B buyers should assess the complexity of the motor design and its operational needs, particularly in terms of power supply and load conditions.
How Do Brushless DC Motors Stand Out?
Brushless DC motors are notable for eliminating brushes, which reduces wear and maintenance needs. They are commonly used in consumer electronics and automotive applications due to their higher efficiency and quieter operation compared to traditional brushed motors. For B2B buyers, the focus should be on the cost-benefit analysis, as the initial investment is higher, but the long-term benefits in energy savings and reduced maintenance can be substantial.
What Advantages Do Laminated Cores Offer?
Laminated cores are designed to minimize energy losses from eddy currents, making them essential in high-efficiency motors and transformers. These cores improve overall performance and reduce heat generation, which is critical in applications requiring high reliability. Buyers should consider the material quality and manufacturing standards when sourcing laminated cores, as these factors directly impact performance and longevity.
Key Industrial Applications of electric motor components
Industry/Sector | Specific Application of Electric Motor Components | Value/Benefit for the Business | Key Sourcing Considerations for this Application |
---|---|---|---|
Manufacturing | Automation in production lines | Increased efficiency and reduced labor costs | Quality assurance, supplier reliability, and lead times |
Agriculture | Electric motors in irrigation systems | Enhanced crop yield and resource management | Energy efficiency, durability, and adaptability to local conditions |
Transportation | Electric motors in electric vehicles (EVs) | Sustainability and reduction in operating costs | Compliance with international standards and local regulations |
HVAC | Motors in heating, ventilation, and air conditioning systems | Improved energy efficiency and comfort for users | Energy ratings, compatibility with existing systems, and service support |
Mining | Electric motors in conveyor systems and drilling equipment | Increased productivity and safety in operations | Robustness, maintenance support, and performance under extreme conditions |
How Are Electric Motor Components Used in Manufacturing Automation?
In the manufacturing sector, electric motor components play a crucial role in automating production lines. Motors drive conveyor belts, robotic arms, and other machinery, significantly enhancing operational efficiency and reducing reliance on manual labor. For international buyers, particularly in Africa and South America, sourcing high-quality motors that meet specific performance and durability standards is essential. Additionally, understanding local manufacturing practices and ensuring compatibility with existing systems can help mitigate potential operational disruptions.
What Are the Benefits of Electric Motors in Agricultural Applications?
Electric motors are integral to modern irrigation systems, allowing for precise water distribution and efficient resource management. By automating irrigation, farmers can significantly increase crop yields while conserving water. For buyers in regions like the Middle East, where water scarcity is critical, sourcing energy-efficient motors that can withstand harsh environmental conditions is vital. Moreover, buyers should consider the availability of local support and maintenance services to ensure the longevity of these systems.
How Do Electric Motor Components Enhance Transportation Solutions?
In the transportation industry, electric motors are at the heart of electric vehicles (EVs), providing a sustainable alternative to fossil fuel-powered transportation. The integration of efficient motor components reduces operating costs and lowers carbon emissions, aligning with global sustainability goals. B2B buyers from Europe, particularly in countries like Spain and Poland, must ensure that the motors comply with stringent EU regulations and standards. Additionally, understanding the supply chain for battery systems and charging infrastructure is crucial for a successful transition to electric mobility.
What Role Do Electric Motors Play in HVAC Systems?
Electric motors are essential in heating, ventilation, and air conditioning (HVAC) systems, where they drive fans, compressors, and pumps. High-efficiency motors contribute to lower energy consumption and enhanced comfort in residential and commercial buildings. For international buyers, especially in Europe, sourcing motors that meet energy efficiency ratings can lead to significant cost savings and compliance with environmental regulations. Furthermore, compatibility with existing HVAC systems and access to local maintenance services should be prioritized when selecting suppliers.
How Are Electric Motor Components Critical in Mining Operations?
In the mining sector, electric motors are utilized in conveyor systems and drilling equipment, where they enhance productivity and ensure safety. The robust nature of these motors is essential for operating under extreme conditions, such as high dust levels and temperature fluctuations. B2B buyers in Africa and South America must focus on sourcing motors that offer high reliability and low maintenance requirements to minimize downtime. Additionally, understanding the specific performance metrics required for different mining applications can guide buyers in making informed purchasing decisions.
3 Common User Pain Points for ‘electric motor components’ & Their Solutions
Scenario 1: Difficulty in Selecting the Right Electric Motor Components
The Problem:
B2B buyers often face challenges in selecting the appropriate electric motor components for their specific applications. With numerous types of motors available, including AC and DC motors, each with various stator and rotor configurations, the decision-making process can be overwhelming. Buyers may struggle with ensuring compatibility between components, leading to inefficiencies or even failures in their applications. This is particularly critical for industries in Africa and South America, where the availability of technical resources can be limited, making the wrong choice even more costly.
The Solution:
To effectively address this issue, buyers should conduct a thorough analysis of their application requirements before sourcing components. Begin by defining the motor’s operational parameters, such as voltage, speed, torque, and duty cycle. Utilizing resources such as technical datasheets and manufacturer specifications can help ensure that the chosen components meet these requirements. Collaborating with trusted suppliers who specialize in electric motor components can also provide insights into the best configurations for specific applications. Furthermore, participating in industry forums or webinars can facilitate knowledge sharing and improve decision-making skills.
Scenario 2: High Failure Rates Due to Poor Quality Components
The Problem:
One of the most pressing concerns for B2B buyers is the high failure rate of electric motor components, which can lead to unexpected downtime and increased maintenance costs. This issue is often exacerbated by the procurement of low-quality or counterfeit parts, particularly in regions where regulations may not be as stringent, such as certain Middle Eastern markets. Buyers may find themselves caught in a cycle of replacing parts frequently, which not only strains their budgets but also impacts their overall productivity.
The Solution:
To mitigate the risk of component failure, buyers should prioritize sourcing from reputable manufacturers known for their quality assurance practices. Conducting due diligence on potential suppliers—such as reviewing certifications, quality control processes, and customer feedback—can help ensure that the components are durable and reliable. Additionally, establishing long-term relationships with trusted suppliers can lead to better pricing and access to high-quality products. Implementing a preventive maintenance schedule that includes regular inspections can also help identify wear and tear on components before they lead to failures.
Scenario 3: Inefficient Motor Performance Leading to Increased Energy Costs
The Problem:
International buyers, particularly in Europe where energy efficiency is a significant concern, often experience issues with the performance of electric motors due to suboptimal component selection or installation. Motors that are not operating at their peak efficiency can lead to increased energy consumption, resulting in higher operational costs. This is a critical pain point for businesses looking to enhance sustainability and reduce their carbon footprint while managing expenses.
The Solution:
To improve motor performance and energy efficiency, buyers should consider conducting a comprehensive energy audit of their existing systems. This audit should evaluate the efficiency of the motor and its components in relation to the overall application. Investing in high-efficiency components, such as premium bearings and stators designed for reduced energy loss, can significantly enhance performance. Buyers should also explore the option of variable frequency drives (VFDs) to optimize motor speed and torque according to specific load requirements. Training staff on proper installation and maintenance practices will further ensure that the components are utilized effectively, thereby maximizing energy savings and operational efficiency.
Strategic Material Selection Guide for electric motor components
What Are the Key Materials Used in Electric Motor Components?
When selecting materials for electric motor components, it is crucial to consider their properties, advantages, disadvantages, and the specific needs of international markets. Below, we analyze four common materials used in electric motors: copper, aluminum, silicon steel, and thermoplastics.
How Does Copper Benefit Electric Motor Components?
Copper is widely used in electric motor windings due to its excellent electrical conductivity. With a temperature rating of up to 200°C and good resistance to corrosion, copper ensures efficient energy transfer and durability.
Pros: Copper’s high conductivity allows for smaller wire gauges, reducing overall weight and space requirements. It also has a long lifespan, making it suitable for high-performance applications.
Cons: The primary drawback of copper is its cost, which can be significantly higher than alternatives like aluminum. Additionally, copper is heavier, which may not be ideal for applications where weight is a critical factor.
Impact on Application: Copper’s compatibility with various media makes it suitable for diverse environments, including high-temperature and corrosive settings.
Considerations for International Buyers: Buyers from regions like Africa and South America should consider the availability of copper and its compliance with international standards such as ASTM B3 for copper wire. In Europe, adherence to REACH regulations is also essential.
What Role Does Aluminum Play in Electric Motor Components?
Aluminum is another popular choice for electric motor components, particularly in windings and casings. It is lightweight, with a temperature rating of around 150°C, and offers good corrosion resistance.
Pros: The primary advantage of aluminum is its lower cost compared to copper, making it an attractive option for budget-conscious projects. Its lightweight nature also allows for more compact motor designs.
Cons: However, aluminum has lower conductivity than copper, which may necessitate larger wire sizes to achieve the same performance. Additionally, it can be more susceptible to oxidation, which may affect its long-term reliability.
Impact on Application: Aluminum is suitable for applications where weight savings are crucial, such as in electric vehicles and portable machinery.
Considerations for International Buyers: Buyers should ensure that aluminum components meet relevant standards, such as DIN 17615 in Europe, and consider the material’s performance in specific environmental conditions.
Why Is Silicon Steel Important for Electric Motor Cores?
Silicon steel is predominantly used for the cores of electric motors due to its magnetic properties. It is designed to minimize energy loss through hysteresis and eddy currents, with a typical temperature rating of 120°C.
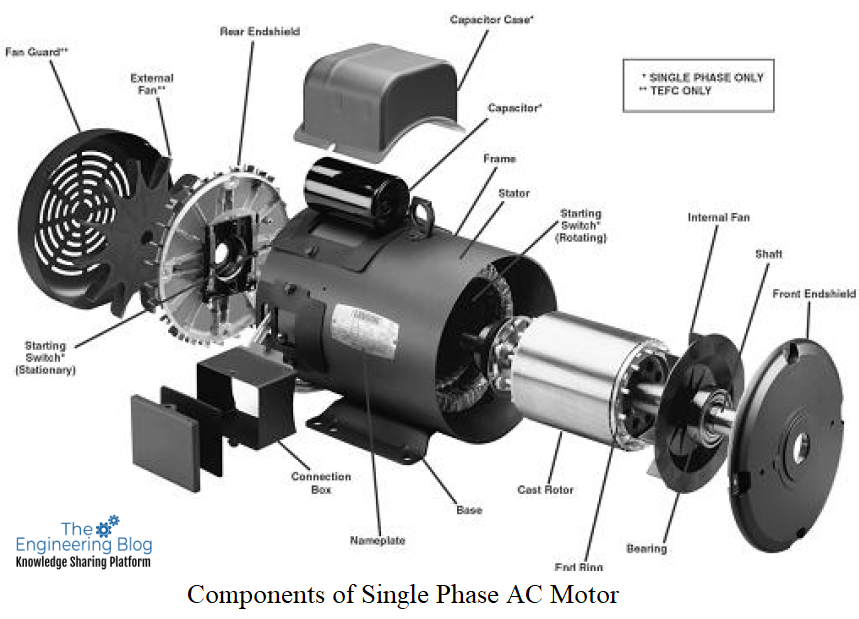
A stock image related to electric motor components.
Pros: The key advantage of silicon steel is its efficiency in magnetic applications, enhancing motor performance and energy efficiency. Its laminated structure reduces energy losses, making it ideal for high-performance motors.
Cons: Silicon steel can be more expensive than conventional steel and may require complex manufacturing processes, increasing production costs.
Impact on Application: This material is particularly effective in induction motors and transformers, where magnetic efficiency is paramount.
Considerations for International Buyers: Compliance with standards such as JIS C 2550 in Japan or ASTM A677 in the U.S. is critical for ensuring quality and performance.
How Do Thermoplastics Enhance Electric Motor Components?
Thermoplastics are increasingly used in electric motor components, particularly for insulation and structural parts. These materials can withstand temperatures up to 150°C and offer excellent chemical resistance.
Pros: Thermoplastics are lightweight, cost-effective, and can be molded into complex shapes, making them versatile for various applications.
Cons: However, they may not provide the same mechanical strength as metals, which can limit their use in high-stress environments.
Impact on Application: Thermoplastics are suitable for non-load-bearing components, such as housings and insulation, where weight and cost savings are essential.
Considerations for International Buyers: Buyers should verify that thermoplastic materials comply with safety standards, such as UL 94 for flammability, especially in regions with stringent regulations.
Summary Table of Material Selection for Electric Motor Components
Material | Typical Use Case for Electric Motor Components | Key Advantage | Key Disadvantage/Limitation | Relative Cost (Low/Med/High) |
---|---|---|---|---|
Copper | Windings and electrical connections | High conductivity and durability | High cost and weight | High |
Aluminum | Windings and casings | Lightweight and cost-effective | Lower conductivity and oxidation risk | Medium |
Silicon Steel | Cores in induction motors | Magnetic efficiency and energy savings | Higher cost and complex manufacturing | High |
Thermoplastics | Insulation and structural components | Lightweight and versatile | Limited mechanical strength | Low |
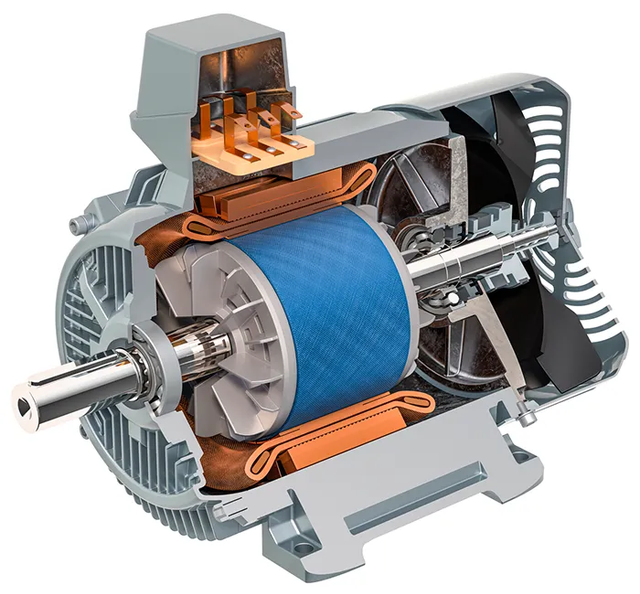
A stock image related to electric motor components.
This guide provides a comprehensive overview of strategic material selection for electric motor components, aiding international B2B buyers in making informed decisions tailored to their specific market needs.
In-depth Look: Manufacturing Processes and Quality Assurance for electric motor components
What Are the Main Stages of Manufacturing Electric Motor Components?
The manufacturing of electric motor components involves several critical stages that ensure the final product meets industry standards and performs efficiently. These stages include material preparation, forming, assembly, and finishing.
How Is Material Prepared for Electric Motor Components?
Material preparation is the foundational step in the manufacturing process. High-quality materials are essential for the performance and longevity of electric motors. Typically, copper and aluminum are used for windings, while silicon steel is employed for the stator and rotor cores.
-
Sourcing Materials: Manufacturers should establish relationships with reputable suppliers to ensure the raw materials meet specific quality standards, such as ASTM or ISO certifications.
-
Quality Control: Incoming materials undergo an Incoming Quality Control (IQC) process to verify dimensions, weight, and material properties. This can include spectrometer analysis for metal composition and mechanical testing for strength.
-
Cutting and Shaping: Raw materials are cut to specified sizes using CNC machines or laser cutting technology, ensuring precision and reducing waste.
What Techniques Are Used in Forming Electric Motor Components?
Forming techniques are essential in shaping the components that will make up the electric motor. Each part requires specific processes:
-
Stator and Rotor Formation: The stator and rotor cores are typically manufactured through processes such as stamping or die-casting. Stamping involves creating thin sheets that are then laminated to reduce energy losses, while die-casting is used for more complex shapes.
-
Winding: For the windings, copper or aluminum wires are wound around the stator and rotor cores. This process can be manual or automated, with computer-controlled machines ensuring uniformity and precision.
-
Insulation Application: Insulating materials, like varnishes or resins, are applied to prevent electrical leakage and ensure safety. This step often involves curing processes that enhance the durability of the insulation.
How Are Electric Motor Components Assembled?
The assembly stage is where all the formed parts come together to create a complete motor. This is a highly coordinated process:
-
Component Alignment: Each part, including bearings, brackets, and the terminal box, is aligned and secured in place. This requires meticulous attention to detail to avoid mechanical failures.
-
Integration of Electrical Components: The electrical connections must be made securely, often involving soldering or crimping wires. Quality assurance at this stage is crucial to prevent electrical failures later on.
-
Final Assembly Checks: Prior to finalization, manufacturers perform In-Process Quality Control (IPQC) to verify that all components fit correctly and function as intended.
What Finishing Processes Are Important for Electric Motor Components?
Finishing processes enhance the durability and aesthetic appeal of electric motor components. They include:
-
Surface Treatment: Components often undergo surface treatments such as anodizing or painting, which help prevent corrosion and improve performance under various environmental conditions.
-
Balancing: Rotors are dynamically balanced to ensure smooth operation at high speeds. This reduces vibration and wear on the bearings.
-
Final Quality Checks: Before packaging, Final Quality Control (FQC) is performed, including functionality tests and visual inspections to detect any surface defects or assembly issues.
Which International Standards and Quality Assurance Practices Should Buyers Be Aware Of?
Quality assurance is critical in the manufacturing of electric motor components, particularly for international B2B buyers. Understanding relevant standards can help ensure that products meet necessary safety and performance benchmarks.
What Are the Key International Standards for Electric Motor Components?
-
ISO 9001: This standard outlines the requirements for a quality management system (QMS). Manufacturers certified under ISO 9001 are likely to maintain consistent quality in their production processes.
-
CE Marking: For buyers in Europe, CE marking indicates that a product meets EU safety, health, and environmental protection standards. This is particularly important for components that will be integrated into machinery or consumer products.
-
API Standards: For electric motors used in the oil and gas industry, adherence to API specifications ensures that components can withstand harsh conditions and operate reliably.
How Can B2B Buyers Verify Supplier Quality Control?
B2B buyers need to implement strategies to verify the quality control processes of their suppliers. This is especially crucial for buyers from Africa, South America, the Middle East, and Europe, where standards may vary significantly.
-
Supplier Audits: Conducting regular audits of suppliers helps verify their adherence to quality standards. This can include reviewing their QMS, material sourcing, and manufacturing processes.
-
Quality Reports: Requesting detailed quality reports can provide insights into a supplier’s performance over time, including defect rates and corrective actions taken.
-
Third-party Inspections: Engaging independent third-party inspection services can offer an unbiased assessment of a supplier’s quality control processes. These inspections often include audits of manufacturing facilities and testing of final products.
What Are the Common Testing Methods for Electric Motor Components?
Testing is an integral part of the quality assurance process. Several common methods are employed to ensure that electric motor components meet performance specifications:
-
Electrical Testing: This includes tests for insulation resistance, dielectric strength, and continuity to ensure that electrical components function correctly without failures.
-
Mechanical Testing: Components are subjected to mechanical tests, including tensile strength and fatigue testing, to assess their durability under operational conditions.
-
Thermal Testing: Given that motors generate heat during operation, thermal testing ensures that components can withstand temperature variations without degradation.
How Do Quality Control Nuances Affect International B2B Transactions?
Understanding the nuances of quality control is vital for international B2B buyers. Factors such as cultural differences, varying standards, and logistical challenges can impact procurement processes.
-
Cultural Considerations: Buyers should be aware that quality perceptions can vary by region. What is considered acceptable in one market may not be in another, necessitating clear communication of expectations.
-
Certification Differences: Different regions may have unique certification requirements. Buyers should ensure that their suppliers meet local standards while also adhering to international benchmarks.
-
Logistical Challenges: Importing components can introduce risks related to quality degradation during transport. Implementing robust logistics strategies can mitigate these risks.
By understanding these manufacturing processes and quality assurance practices, B2B buyers can make informed decisions, ensuring the procurement of high-quality electric motor components that meet their operational needs.
Practical Sourcing Guide: A Step-by-Step Checklist for ‘electric motor components’
Introduction
This practical sourcing guide is designed to assist international B2B buyers in effectively procuring electric motor components. By following this checklist, buyers from Africa, South America, the Middle East, and Europe can ensure they make informed decisions that meet their technical requirements and operational needs.
Step 1: Define Your Technical Specifications
Clearly articulating the technical specifications of the electric motor components you require is vital. This includes understanding the type of motor (AC, DC, or brushless), the necessary power ratings, and operational conditions. Detailed specifications will streamline supplier selection and ensure compatibility with your applications.
Step 2: Research Market Trends and Innovations
Stay updated on the latest trends in electric motor technology and component materials. This knowledge can inform your sourcing decisions, helping you choose suppliers who offer innovative solutions, such as energy-efficient motors or advanced materials that enhance performance. Look for white papers and industry reports that provide insights into emerging technologies.
Step 3: Evaluate Potential Suppliers
Before committing, it’s crucial to vet suppliers thoroughly. Request company profiles, case studies, and references from buyers in a similar industry or region. Key factors to consider include:
– Experience and Expertise: Look for suppliers with a proven track record in manufacturing electric motor components.
– Quality Assurance: Check for certifications such as ISO 9001, which indicate adherence to international quality standards.
Step 4: Assess Manufacturing Capabilities
Understanding a supplier’s manufacturing capabilities is essential to ensure they can meet your volume and quality requirements. Inquire about their production processes, technology, and equipment. Consider the following:
– Capacity and Scalability: Can the supplier scale production if your demand increases?
– Lead Times: What are the typical lead times for orders, and how do they handle urgent requests?
Step 5: Request Samples and Prototypes
Before making a bulk purchase, request samples or prototypes of the components. This allows you to assess the quality, fit, and functionality of the products in your specific application. Pay attention to:
– Material Quality: Ensure that the materials used meet your durability and performance standards.
– Performance Testing: Conduct tests to verify that the components function correctly within your motor system.
Step 6: Negotiate Terms and Pricing
Once you have identified suitable suppliers, negotiate terms and pricing that reflect your budget and expectations. Be clear about your payment terms, delivery schedules, and any warranties or guarantees. Consider:
– Bulk Purchase Discounts: Ask about discounts for larger orders.
– After-Sales Support: Ensure the supplier offers reliable support for installation and maintenance.
Step 7: Establish a Long-Term Partnership
Consider building a long-term relationship with suppliers who meet your needs. A strong partnership can lead to better pricing, priority service, and access to new technologies. Regular communication and feedback can enhance collaboration and ensure continuous improvement in product offerings.
By following this checklist, B2B buyers can navigate the complexities of sourcing electric motor components effectively, ensuring they make strategic decisions that benefit their operations.
Comprehensive Cost and Pricing Analysis for electric motor components Sourcing
What Are the Key Cost Components for Electric Motor Components?
When sourcing electric motor components, understanding the cost structure is crucial for making informed purchasing decisions. The primary cost components include:
-
Materials: The choice of materials significantly impacts the cost. Common materials used in electric motors include copper for windings, silicon steel for cores, and various plastics for insulation. The fluctuating prices of these raw materials can affect overall costs.
-
Labor: Labor costs vary depending on the manufacturing location. Countries with higher labor costs, such as those in Europe, may present higher overall prices compared to regions in Africa or South America where labor costs can be lower.
-
Manufacturing Overhead: This includes costs associated with utilities, rent, and general operational expenses. Efficient production processes can help minimize these costs, impacting the final pricing of motor components.
-
Tooling: Custom tooling for specific motor components can be a significant upfront investment. Understanding the tooling costs is essential, especially for custom specifications that require unique molds or equipment.
-
Quality Control (QC): Implementing rigorous QC processes ensures the reliability and performance of motor components, but it also adds to the overall cost. Buyers should consider the certification standards required in their region, as these can influence both price and quality.
-
Logistics: Transportation costs, including shipping, customs duties, and warehousing, are vital to the total cost. International buyers must factor in these logistics when sourcing components from overseas suppliers.
-
Margin: Supplier margins can vary widely based on market dynamics and competition. Understanding the markup applied by suppliers can help buyers negotiate better pricing.
How Do Price Influencers Affect the Sourcing of Electric Motor Components?
Several factors influence the pricing of electric motor components:
-
Volume and Minimum Order Quantity (MOQ): Higher order volumes typically lead to lower per-unit costs. Negotiating for better pricing based on volume can significantly reduce expenses.
-
Specifications and Customization: Custom specifications can lead to increased costs due to the need for specialized materials or tooling. Buyers should evaluate whether the benefits of customization outweigh the additional costs.
-
Material Quality and Certifications: Components that meet specific industry certifications (e.g., ISO, UL) may cost more but ensure higher reliability and safety. Buyers should weigh the importance of these certifications against their budget constraints.
-
Supplier Factors: The reputation, reliability, and location of the supplier can impact pricing. Established suppliers may offer premium pricing for their proven quality and service, while newer suppliers may provide lower prices to gain market share.
-
Incoterms: Understanding the International Commercial Terms (Incoterms) is essential for international buyers. These terms dictate responsibilities regarding shipping, insurance, and tariffs, which can significantly affect the total landed cost of components.
What Are the Best Buyer Tips for Cost-Efficiency in Sourcing Electric Motor Components?
To maximize cost-efficiency when sourcing electric motor components, consider the following strategies:
-
Negotiate Effectively: Build strong relationships with suppliers and use your purchasing power to negotiate better terms. Discuss potential discounts for bulk purchases or long-term contracts.
-
Evaluate Total Cost of Ownership (TCO): Look beyond the initial purchase price. Consider maintenance costs, energy efficiency, and the lifespan of components when assessing the total cost of ownership.
-
Research Market Trends: Stay informed about market fluctuations in material prices and labor costs. Understanding these trends can provide leverage in negotiations.
-
Leverage Local Suppliers: For buyers in regions like Africa or South America, sourcing from local suppliers can reduce logistics costs and lead times, which can be critical in maintaining production schedules.
-
Be Aware of Pricing Nuances: International buyers should be conscious of currency fluctuations, trade tariffs, and regional economic conditions that may affect pricing. It’s advisable to include these factors in budget planning.
Disclaimer on Indicative Prices
It is important to note that the prices for electric motor components can vary widely based on the factors discussed above. For precise pricing, buyers should consult multiple suppliers and obtain detailed quotes tailored to their specific needs and conditions.
Alternatives Analysis: Comparing electric motor components With Other Solutions
Understanding Alternatives to Electric Motor Components
In the realm of industrial applications, electric motor components are pivotal in converting electrical energy into mechanical energy. However, various alternative technologies and methods can also fulfill similar functions. Understanding these alternatives is crucial for international B2B buyers who seek efficient and cost-effective solutions tailored to their specific needs.
Comparison of Electric Motor Components and Alternatives
Comparison Aspect | Electric Motor Components | Hydraulic Systems | Pneumatic Systems |
---|---|---|---|
Performance | High efficiency, scalable, suitable for diverse applications | Excellent torque at low speeds, powerful for heavy loads | Quick actuation, good for repetitive tasks |
Cost | Moderate initial investment, lower operational costs | High initial costs, higher maintenance expenses | Moderate initial costs, variable operational costs |
Ease of Implementation | Relatively easy to implement, requires electrical infrastructure | Complex installation, needs hydraulic lines and tanks | Simple setup, requires air compressor |
Maintenance | Low maintenance requirements, periodic checks needed | High maintenance due to fluid leaks and pressure checks | Moderate maintenance, potential for air leaks |
Best Use Case | Ideal for applications like electric vehicles, HVAC systems | Best for construction equipment and heavy machinery | Suitable for assembly lines and packaging |
Detailed Breakdown of Alternatives
Hydraulic Systems: What Are Their Advantages and Disadvantages?
Hydraulic systems utilize pressurized fluids to transmit power and are known for their impressive torque output, making them highly effective in heavy machinery and construction equipment. While they excel in power and torque at low speeds, their initial setup costs can be prohibitive. Moreover, the maintenance of hydraulic systems can be a challenge due to potential fluid leaks and the need for regular pressure checks. They are best suited for applications requiring high force and precise control, but their complexity can be a deterrent for some buyers.
Pneumatic Systems: What Are Their Key Benefits and Limitations?
Pneumatic systems operate using compressed air, making them a popular choice for applications that require quick actuation and repetitive tasks. Their setup is relatively straightforward, and they can be easily integrated into existing systems. However, they are generally less powerful than hydraulic systems and may not be suitable for heavy-duty applications. Additionally, the operational costs can vary significantly based on the efficiency of the air compressor used. Pneumatic systems are often ideal for assembly lines and packaging processes, where speed and flexibility are paramount.
How to Choose the Right Solution for Your Business Needs
When selecting between electric motor components and alternative technologies like hydraulic or pneumatic systems, B2B buyers should consider their specific operational requirements, budget constraints, and maintenance capabilities. Electric motors offer a versatile and efficient solution for many applications, particularly where energy efficiency and low maintenance are priorities. Conversely, if the application demands high torque and power, hydraulic systems might be more appropriate, while pneumatic systems can be considered for tasks requiring speed and responsiveness.
Ultimately, the decision should align with the operational goals and infrastructure of the business, ensuring that the chosen technology maximizes efficiency and productivity in their specific context.
Essential Technical Properties and Trade Terminology for electric motor components
What Are the Key Technical Properties of Electric Motor Components?
Understanding the technical properties of electric motor components is essential for B2B buyers, especially when evaluating the quality and compatibility of parts. Here are some critical specifications to consider:
1. Material Grade: Why Does It Matter?
Material grade refers to the classification of the materials used in motor components, such as copper for windings or silicon steel for cores. High-grade materials enhance electrical conductivity, thermal resistance, and overall durability. For international buyers, specifying material grades ensures compliance with local standards and enhances the reliability of the motors in various applications.
2. Tolerance Levels: How Do They Affect Performance?
Tolerance levels indicate the permissible limits of variation in the dimensions of motor components. High precision in manufacturing, often defined in micrometers, is crucial for parts like bearings and shafts, which directly impact performance and efficiency. In markets like Europe and the Middle East, where stringent quality standards are enforced, understanding tolerances can guide buyers in selecting reliable suppliers.
3. Insulation Class: What Protection Do You Need?
The insulation class of electric motor components, such as wires and windings, defines their ability to withstand temperature variations without degrading. Classes range from A (up to 105°C) to H (up to 180°C). For B2B buyers in hot climates, such as parts of Africa and South America, selecting components with appropriate insulation ratings can prevent overheating and extend motor life.
4. Efficiency Ratings: How Do They Impact Costs?
Efficiency ratings, often expressed as a percentage, indicate how effectively a motor converts electrical energy into mechanical energy. Higher efficiency means lower operational costs and reduced energy consumption. Buyers focusing on sustainability or operating in regions with high energy costs should prioritize high-efficiency motors to optimize long-term expenditures.
5. Bearing Type: What Should You Consider?
The type of bearings used in motors, such as ball or roller bearings, affects the motor’s operational smoothness and lifespan. Selecting the right bearing type can minimize friction and wear, which is crucial for applications in demanding environments. Buyers should understand the operational context to choose the most suitable bearing type for their specific needs.
What Are Common Trade Terminology and Jargon in Electric Motor Components?
Familiarity with industry terminology can streamline the purchasing process and ensure clear communication with suppliers. Here are some common terms:
1. OEM (Original Equipment Manufacturer): Why Is It Important?
An OEM is a company that produces parts or equipment that may be marketed by another manufacturer. Understanding whether a supplier is an OEM can help buyers ensure that they are sourcing genuine parts that meet specific quality standards, which is crucial for maintaining equipment performance.
2. MOQ (Minimum Order Quantity): How Does It Affect Your Purchase?
MOQ refers to the smallest quantity of a product that a supplier is willing to sell. This term is vital for B2B buyers, as it can impact inventory management and cash flow. Buyers should negotiate MOQs to align with their demand patterns and avoid excess stock.
3. RFQ (Request for Quotation): What Information Should You Include?
An RFQ is a document sent to suppliers requesting price estimates for specified products or services. Including detailed specifications and quantities in an RFQ helps suppliers provide accurate quotes, facilitating better decision-making for buyers.
4. Incoterms (International Commercial Terms): How Do They Impact Shipping?
Incoterms are internationally recognized rules that define the responsibilities of buyers and sellers in shipping agreements. Understanding these terms, such as FOB (Free on Board) or CIF (Cost, Insurance, Freight), helps buyers clarify shipping costs and liability, which is especially important for international transactions.
5. Lead Time: What Should You Expect?
Lead time refers to the time taken from placing an order to receiving the goods. This metric is crucial for planning production schedules, especially in industries where downtime can be costly. Buyers should inquire about lead times to align their operations with supplier capabilities.
By understanding these technical properties and trade terms, international B2B buyers can make informed purchasing decisions, ensuring they select the right electric motor components for their specific applications.
Navigating Market Dynamics and Sourcing Trends in the electric motor components Sector
What Are the Current Market Dynamics and Key Trends in the Electric Motor Components Sector?
The electric motor components sector is witnessing significant transformation, driven by global demand for energy efficiency and sustainability. As industries across Africa, South America, the Middle East, and Europe adopt electric vehicles and renewable energy technologies, the need for high-quality motor components is surging. Key trends include the increasing adoption of smart manufacturing technologies such as IoT and AI, which enhance operational efficiency and predictive maintenance. Additionally, the rise of customization in motor designs caters to specific industrial applications, enabling buyers to source components that meet unique performance criteria.
International B2B buyers must also be aware of the regional sourcing dynamics. For example, suppliers in Europe, particularly in countries like Spain and Poland, are leading in innovative component manufacturing, focusing on advanced materials and designs that enhance motor performance. Conversely, buyers in Africa and South America may find opportunities in local sourcing to reduce costs and improve supply chain resilience. Understanding these regional differences is crucial for international buyers seeking competitive advantages in procurement.
How Can Sustainability and Ethical Sourcing Shape B2B Relationships in the Electric Motor Components Market?
The environmental impact of electric motor components cannot be overstated, as these components play a pivotal role in achieving energy efficiency in various applications. As sustainability becomes a non-negotiable aspect of business operations, B2B buyers must prioritize ethical sourcing. This involves selecting suppliers who adhere to environmentally friendly practices and demonstrate a commitment to reducing their carbon footprint.
Buyers should seek out green certifications and materials, such as recycled metals and biodegradable insulators, to ensure their supply chains align with sustainability goals. Furthermore, engaging with suppliers that implement circular economy principles can enhance brand reputation and customer loyalty. By prioritizing sustainable sourcing, international B2B buyers not only comply with increasing regulatory requirements but also contribute to a more sustainable future.
What Is the Evolution of the Electric Motor Components Industry and Its Relevance for B2B Buyers?
The evolution of the electric motor components industry has been marked by rapid technological advancements and shifts in consumer demand. Initially, electric motors were primarily used in industrial applications; however, the advent of renewable energy and electric mobility has expanded their application scope significantly. The transition from traditional motors to more efficient, compact designs has also been driven by the need for better energy conservation and performance.
For B2B buyers, understanding this historical context is vital for making informed sourcing decisions. Recognizing the advancements in motor technology can help buyers identify suppliers that are not only established but also innovative. This knowledge can lead to strategic partnerships that enhance operational capabilities and drive competitiveness in an increasingly electrified market. As the industry continues to evolve, staying abreast of these changes will empower buyers to adapt their sourcing strategies effectively.
Frequently Asked Questions (FAQs) for B2B Buyers of electric motor components
1. How do I select the right electric motor components for my application?
Choosing the right electric motor components starts with understanding your specific application requirements. Consider factors such as load capacity, speed, torque, and environmental conditions. Evaluate the types of motors available—AC, DC, or stepper motors—and their respective components like rotors, stators, and bearings. Collaborate with suppliers to ensure the components meet industry standards and regulations. Conducting a thorough technical assessment of each component’s specifications will help you make an informed decision that aligns with your operational needs.
2. What are the key factors to consider when vetting suppliers of electric motor components?
When vetting suppliers, assess their industry experience, certifications, and customer reviews. Ensure they have a robust quality management system in place, such as ISO 9001 certification. Evaluate their production capabilities, lead times, and flexibility for custom orders. It’s also crucial to inquire about their supply chain reliability and logistical capabilities, especially if you are sourcing from different continents. Establishing clear communication channels and understanding their after-sales support can further ensure a successful partnership.
3. What customization options are available for electric motor components?
Many suppliers offer customization options for electric motor components to meet specific performance needs. Customization can include variations in size, material selection, winding configurations, and additional features like integrated sensors or specialized coatings. Before placing an order, discuss your requirements with the supplier to understand their capabilities and any limitations. Custom components may have longer lead times and higher costs, so plan your procurement strategy accordingly to avoid delays.
4. What is the minimum order quantity (MOQ) for electric motor components?
Minimum order quantities (MOQs) for electric motor components can vary significantly among suppliers and depend on the type of component. Commonly, MOQs may range from 50 to 500 units, particularly for specialized or customized parts. However, some suppliers may offer flexibility for smaller orders, especially for ongoing business relationships. It’s essential to clarify MOQ requirements during initial discussions to align your purchasing strategy with supplier capabilities.
5. What payment terms should I expect when sourcing electric motor components internationally?
Payment terms for international sourcing of electric motor components typically vary based on supplier policies and buyer-supplier relationships. Common terms include upfront payment, letter of credit, or payment upon delivery. Some suppliers may offer net 30 or net 60 terms, allowing you to pay within a specified period after receiving the goods. Always negotiate payment terms that suit your cash flow and ensure they are clearly documented in the contract to avoid misunderstandings.
6. How can I ensure quality assurance (QA) when purchasing electric motor components?
To ensure quality assurance, request certifications and quality control documentation from suppliers, such as ISO certifications or third-party testing results. Implement a robust inspection process upon receipt of goods, including visual inspections and functional testing. Establish clear quality criteria before placing orders, and consider conducting audits of the supplier’s facilities if necessary. Maintaining open lines of communication regarding quality issues will help foster a proactive approach to quality management.
7. What logistics considerations should I keep in mind when importing electric motor components?
When importing electric motor components, consider shipping methods, customs regulations, and lead times. Choose between air freight for speed or sea freight for cost-effectiveness based on your urgency and budget. Familiarize yourself with import duties, taxes, and any required documentation, such as bills of lading and commercial invoices. Engage with logistics partners who have experience in handling such components to ensure smooth transportation and compliance with international regulations.
8. How do I handle after-sales support for electric motor components?
After-sales support is critical for ensuring the long-term performance of electric motor components. Establish a clear communication plan with your supplier regarding warranty terms and support services. Ensure they provide technical assistance for installation and troubleshooting issues. Regular maintenance checks and access to replacement parts should also be part of the support package. Building a strong relationship with your supplier can enhance the effectiveness of after-sales support, leading to better operational continuity.
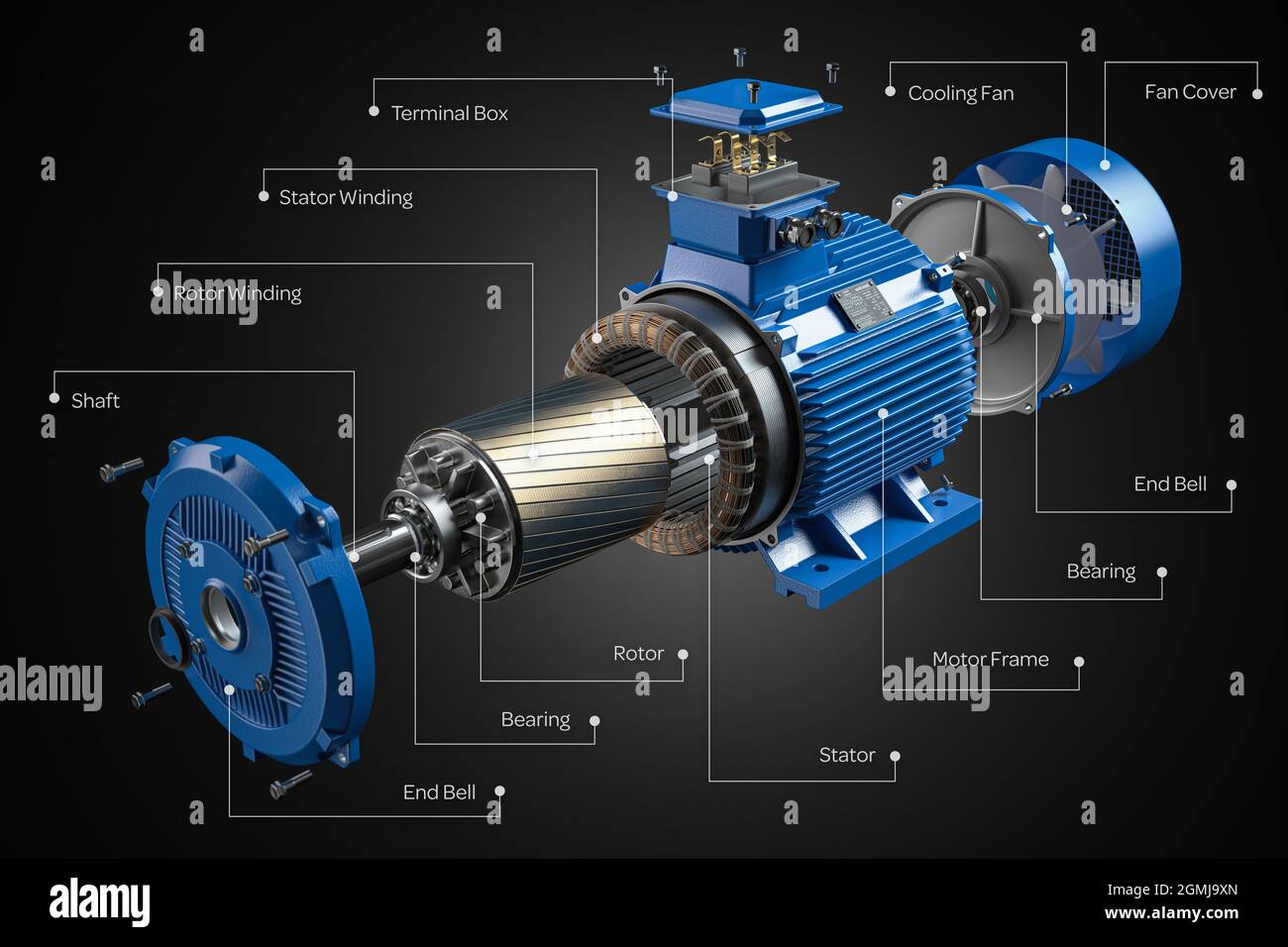
A stock image related to electric motor components.
Important Disclaimer & Terms of Use
⚠️ Important Disclaimer
The information provided in this guide, including content regarding manufacturers, technical specifications, and market analysis, is for informational and educational purposes only. It does not constitute professional procurement advice, financial advice, or legal advice.
While we have made every effort to ensure the accuracy and timeliness of the information, we are not responsible for any errors, omissions, or outdated information. Market conditions, company details, and technical standards are subject to change.
B2B buyers must conduct their own independent and thorough due diligence before making any purchasing decisions. This includes contacting suppliers directly, verifying certifications, requesting samples, and seeking professional consultation. The risk of relying on any information in this guide is borne solely by the reader.
Strategic Sourcing Conclusion and Outlook for electric motor components
As the demand for electric motor components continues to rise globally, understanding the intricacies of strategic sourcing becomes essential for international B2B buyers. The interplay between key components—such as stators, rotors, bearings, and insulation materials—plays a critical role in the performance and efficiency of electric motors. Buyers must prioritize sourcing high-quality materials and components to enhance operational reliability and longevity, particularly in competitive markets across Africa, South America, the Middle East, and Europe.
Strategic sourcing not only enables businesses to optimize costs but also fosters strong supplier relationships, ensuring access to the latest technologies and innovations. By engaging with reputable manufacturers and suppliers, buyers can mitigate risks associated with quality and supply chain disruptions, ultimately enhancing their competitive edge.
Looking ahead, it is crucial for B2B buyers to remain proactive in identifying emerging trends and opportunities within the electric motor component sector. Investing in sustainable practices and understanding regional market dynamics will be key to capitalizing on growth opportunities. International buyers are encouraged to leverage strategic sourcing to navigate challenges and secure a robust supply chain, paving the way for future success in this evolving industry.