The Ultimate Guide to Hydraulics And Pneumatics (2025)
Introduction: Navigating the Global Market for hydraulics and pneumatics
In an increasingly interconnected world, sourcing efficient hydraulic and pneumatic solutions is pivotal for businesses aiming to enhance productivity and streamline operations. As international B2B buyers from regions such as Africa, South America, the Middle East, and Europe seek to navigate the complexities of the global market, understanding the nuances of hydraulics and pneumatics becomes essential. This comprehensive guide delves into various types of hydraulic and pneumatic systems, their applications across industries, and the critical considerations for supplier vetting and cost assessment.
The world of hydraulics and pneumatics is vast, encompassing a wide range of technologies, from hydraulic lifts and presses to pneumatic conveying systems. Each type serves unique purposes and presents distinct advantages, making it crucial for buyers to align their specific needs with the right solutions. By exploring the detailed sections on system functionality, application suitability, and supplier reliability, this guide empowers B2B buyers to make informed purchasing decisions that can drive operational efficiency and reduce costs.
Moreover, understanding the global landscape of hydraulic and pneumatic suppliers is key to ensuring quality and reliability. With actionable insights tailored to the unique challenges faced by buyers in diverse markets, this guide serves as a valuable resource for enhancing procurement strategies and fostering successful partnerships in the hydraulic and pneumatic sectors.
Understanding hydraulics and pneumatics Types and Variations
Type Name | Key Distinguishing Features | Primary B2B Applications | Brief Pros & Cons for Buyers |
---|---|---|---|
Hydraulic Press | Uses liquid pressure to shape materials | Metal forming, automotive, manufacturing | Pros: High force output, precision; Cons: Slower operation |
Pneumatic Cylinder | Utilizes compressed air for force generation | Automation, packaging, material handling | Pros: Fast operation, less maintenance; Cons: Lower force output |
Hydraulic Lift | Lifts heavy loads using hydraulic fluid | Warehousing, construction, automotive repair | Pros: High load capacity; Cons: Requires more space |
Pneumatic Conveying | Transfers materials through air pressure | Food processing, pharmaceuticals, plastics | Pros: Clean, efficient; Cons: Limited to lighter materials |
Scissor Lift | Compact design for vertical lifting | Maintenance, construction, warehousing | Pros: Space-saving, versatile; Cons: Limited height capability |
What Are the Characteristics of a Hydraulic Press?
Hydraulic presses are powerful machines that utilize Pascal’s principle to exert force on materials using hydraulic fluid. They are ideal for applications requiring significant pressure, such as metal forming and automotive parts manufacturing. When purchasing a hydraulic press, consider factors like force output, cycle time, and the types of materials you will be working with. Their high precision and ability to handle heavy loads make them an excellent choice for industries that prioritize accuracy and strength.
How Do Pneumatic Cylinders Function in B2B Applications?
Pneumatic cylinders operate by converting compressed air into linear motion, making them suitable for tasks that require quick and repetitive actions. They are commonly found in automation and material handling applications. When selecting a pneumatic cylinder, buyers should assess the required speed, stroke length, and load capacity. Their fast operation and lower maintenance needs make them appealing for businesses looking to enhance efficiency, although they may not deliver the same force as hydraulic systems.
What Makes Hydraulic Lifts Essential for Heavy Loads?
Hydraulic lifts are designed to raise heavy loads with the help of hydraulic fluid. These systems are prevalent in warehouses, construction sites, and automotive repair shops. When considering a hydraulic lift, it’s essential to evaluate the lift capacity, footprint, and power source. Their ability to handle substantial weights makes them indispensable in environments where safety and efficiency are critical, though they require more space compared to pneumatic alternatives.
How Does Pneumatic Conveying Enhance Material Transfer?
Pneumatic conveying systems utilize air pressure to transport bulk materials, making them suitable for industries like food processing and pharmaceuticals. Buyers should consider the type of materials being conveyed, system layout, and air pressure requirements. The cleanliness and efficiency of pneumatic systems are significant advantages, especially in industries where contamination is a concern. However, their capacity is limited to lighter materials, which may not suit all operational needs.
Why Choose Scissor Lifts for Vertical Movement?
Scissor lifts are compact platforms that provide vertical lifting capabilities, making them ideal for maintenance and construction tasks. Key considerations for B2B buyers include maximum height, load capacity, and mobility features. Their space-saving design and versatility make them a popular choice for businesses that need to maximize operational efficiency in confined spaces. However, their height limitations can restrict use in certain applications, so evaluating specific needs is crucial.
Key Industrial Applications of hydraulics and pneumatics
Industry/Sector | Specific Application of hydraulics and pneumatics | Value/Benefit for the Business | Key Sourcing Considerations for this Application |
---|---|---|---|
Construction | Hydraulic Lifts and Scissor Lifts | Enhanced safety and efficiency in lifting operations | Reliability of components, load capacity, and maintenance support |
Manufacturing | Pneumatic Conveying Systems | Increased speed and efficiency in material handling | Compatibility with existing systems, energy efficiency, and scalability |
Automotive | Hydraulic Presses for Metal Forming | High precision and quality in part manufacturing | Material compatibility, pressure ratings, and supplier reliability |
Mining and Heavy Equipment | Hydraulic Excavators | Greater power and control for heavy-duty operations | Durability, service availability, and parts accessibility |
Food and Beverage | Pneumatic Actuators for Packaging Machinery | Improved hygiene and speed in processing and packaging | Compliance with safety standards, ease of cleaning, and energy consumption |
How Are Hydraulic Lifts and Scissor Lifts Used in Construction?
In the construction sector, hydraulic lifts and scissor lifts are essential for safely raising materials and personnel to various heights. These systems provide controlled lifting, ensuring that heavy loads can be moved efficiently without compromising safety. International buyers should consider the reliability of components, the lift’s load capacity, and the availability of maintenance support, particularly in regions like Africa and South America where service networks may be less established.
What Role Do Pneumatic Conveying Systems Play in Manufacturing?
Pneumatic conveying systems are widely used in manufacturing to transport bulk materials like powders and granules. By utilizing compressed air, these systems facilitate the fast and efficient movement of materials between processing centers, significantly increasing production speed. B2B buyers must assess the compatibility of these systems with existing equipment, their energy efficiency, and scalability to meet future production demands, especially in rapidly growing markets in Europe and the Middle East.
How Are Hydraulic Presses Utilized in the Automotive Industry?
Hydraulic presses are critical in the automotive industry for metal forming processes, such as stamping and shaping components. They provide the high precision and force required to manufacture quality parts that meet stringent industry standards. Buyers should evaluate the material compatibility, pressure ratings, and the reliability of suppliers to ensure optimal performance and minimize downtime, particularly in regions with varying industrial capabilities.
Why Are Hydraulic Excavators Important for Mining and Heavy Equipment?
In the mining sector, hydraulic excavators are invaluable for their ability to handle heavy loads with precision and control. These machines rely on hydraulics to provide the necessary power for digging and moving materials, which is crucial in challenging environments. When sourcing hydraulic equipment, businesses must prioritize durability, service availability, and parts accessibility to ensure efficient operations, especially in remote locations common in Africa and South America.
How Do Pneumatic Actuators Enhance Food and Beverage Processing?
Pneumatic actuators are increasingly used in the food and beverage industry for packaging machinery, where speed and hygiene are paramount. These systems enable quick actuation while minimizing contamination risks, ensuring compliance with health standards. Buyers should focus on compliance with safety regulations, ease of cleaning, and energy consumption when selecting pneumatic solutions, particularly in European markets where regulatory standards are stringent.
3 Common User Pain Points for ‘hydraulics and pneumatics’ & Their Solutions
Scenario 1: Inefficiencies in Hydraulic System Performance
The Problem: Many B2B buyers encounter performance inefficiencies in hydraulic systems, often leading to increased operational costs and downtime. Common issues include unexpected leaks, overheating, or insufficient power output. These inefficiencies can stem from inadequate system design, improper fluid selection, or lack of routine maintenance. For companies in sectors such as manufacturing or construction, these challenges can halt production and affect timelines, leading to lost revenue and damaged client relationships.
The Solution: To address these issues, it is crucial to conduct a thorough assessment of the hydraulic system’s design and components. Begin by selecting the appropriate hydraulic fluids that match the operational temperature and viscosity requirements of your equipment. Regularly scheduled maintenance, including fluid checks, filter replacements, and seal inspections, is essential. Consider investing in condition-monitoring technologies that can provide real-time data on system performance, enabling proactive maintenance. Additionally, collaborating with a reputable supplier who specializes in hydraulic solutions can help ensure that you are sourcing high-quality components tailored to your specific needs. This strategic approach can enhance system performance, reduce downtime, and ultimately lead to cost savings.
Scenario 2: Complexity in Pneumatic System Integration
The Problem: Integrating pneumatic systems into existing machinery can be a daunting task for B2B buyers, especially when dealing with multiple suppliers and components. Often, companies face compatibility issues between different brands or models of pneumatic devices, leading to installation delays and increased costs. This complexity can hinder the scalability of operations and frustrate engineering teams who must troubleshoot integration problems rather than focus on innovation.
The Solution: To simplify pneumatic system integration, prioritize sourcing components from a single manufacturer that offers a comprehensive line of products. This approach ensures compatibility and simplifies the procurement process. Before purchasing, engage with engineering consultants or suppliers who can assist in designing a custom solution that meets your specific operational requirements. Additionally, consider utilizing modular pneumatic systems that allow for easier upgrades and adjustments as your business evolves. Implementing a standardized training program for your team on the operation and maintenance of these systems can also enhance efficiency and reduce integration-related challenges.
Scenario 3: Challenges in Sourcing High-Quality Components
The Problem: International B2B buyers often struggle with sourcing high-quality hydraulic and pneumatic components, particularly in emerging markets in Africa and South America. Fluctuating supply chains, inconsistent quality control, and varying regulatory standards can make it difficult to procure reliable parts that meet specific industry requirements. This uncertainty can lead to project delays and increased costs, as companies may need to re-purchase components or face operational disruptions due to equipment failures.
The Solution: To mitigate sourcing challenges, establish strong relationships with trusted suppliers who have a proven track record in your industry. Look for suppliers that provide detailed product specifications, certifications, and quality assurance processes. Consider diversifying your supplier base to include both local and international vendors, which can enhance supply chain resilience. Participating in industry trade shows can also provide valuable networking opportunities and insights into new products and technologies. Furthermore, conducting thorough due diligence on potential suppliers, including site visits and quality audits, can ensure that you are making informed decisions that align with your operational goals. By implementing these strategies, you can enhance your sourcing process, ensure component reliability, and maintain the integrity of your hydraulic and pneumatic systems.
Strategic Material Selection Guide for hydraulics and pneumatics
What Are the Key Materials Used in Hydraulics and Pneumatics?
When selecting materials for hydraulic and pneumatic systems, understanding the properties, advantages, and limitations of each material is crucial for ensuring optimal performance. Below, we analyze four common materials used in these systems: steel, aluminum, plastic, and rubber.
How Does Steel Perform in Hydraulic and Pneumatic Systems?
Key Properties: Steel is renowned for its strength and durability, with a high-temperature rating and excellent pressure resistance. It typically withstands pressures up to 3000 psi or more, depending on the grade.
Pros & Cons: The primary advantage of steel is its robustness, making it suitable for high-pressure applications. However, its weight can be a disadvantage in mobile or lightweight applications. Additionally, steel can be prone to corrosion unless treated or coated, which may increase manufacturing complexity.
Impact on Application: Steel is compatible with various hydraulic fluids, including petroleum-based oils and water-based fluids. However, users must consider corrosion resistance, especially in humid or corrosive environments.
Considerations for International Buyers: Buyers from regions like Africa and South America should ensure compliance with international standards such as ASTM A106 for seamless steel pipes. In Europe, adherence to EN standards is crucial for safety and performance.
What Advantages Does Aluminum Offer in Hydraulic and Pneumatic Applications?
Key Properties: Aluminum is lightweight and has good corrosion resistance, with temperature ratings typically up to 200°C. It can handle moderate pressures, generally around 1500 psi.
Pros & Cons: The lightweight nature of aluminum makes it ideal for applications where weight is a concern, such as in aerospace or portable equipment. However, its lower strength compared to steel limits its use in high-pressure applications. Additionally, aluminum can be more expensive than steel.
Impact on Application: Aluminum is compatible with many fluids but is not recommended for use with certain solvents or aggressive chemicals.
Considerations for International Buyers: Buyers should verify compliance with standards such as ASTM B221 for aluminum extrusions. In the Middle East, familiarity with local standards can aid in selecting suitable aluminum grades.
How Do Plastics Compare in Hydraulic and Pneumatic Systems?
Key Properties: Plastics, particularly thermoplastics like PVC and nylon, offer excellent chemical resistance and can operate effectively at lower pressures (up to 1000 psi) and temperatures (up to 80°C).
Pros & Cons: The main advantage of plastics is their lightweight and corrosion resistance, making them suitable for various applications, including food processing and pharmaceuticals. However, their lower pressure ratings and potential for deformation under high temperatures can limit their use.
Impact on Application: Plastics are ideal for non-aggressive fluids but may not be suitable for high-pressure hydraulic systems.
Considerations for International Buyers: Compliance with standards such as FDA regulations for food-grade applications is essential, particularly for buyers in Europe and the Middle East.
What Role Does Rubber Play in Hydraulic and Pneumatic Systems?
Key Properties: Rubber is flexible and can withstand pressures up to 3000 psi, with temperature ratings generally between -40°C and 100°C, depending on the type.
Pros & Cons: Rubber’s flexibility makes it ideal for seals and gaskets, providing excellent leak-proof capabilities. However, it can degrade over time when exposed to certain chemicals and UV light, which may necessitate more frequent replacements.
Impact on Application: Rubber is compatible with a wide range of fluids, but users must select the appropriate type (e.g., nitrile, neoprene) based on the specific application.
Considerations for International Buyers: Buyers should ensure that rubber components meet relevant standards, such as ISO 9001 for quality management, especially in Europe and the Middle East.
Summary Table of Material Selection for Hydraulics and Pneumatics
Material | Typical Use Case for hydraulics and pneumatics | Key Advantage | Key Disadvantage/Limitation | Relative Cost (Low/Med/High) |
---|---|---|---|---|
Steel | High-pressure hydraulic systems | High strength and durability | Heavy and prone to corrosion | Medium |
Aluminum | Lightweight applications, aerospace | Lightweight and corrosion-resistant | Lower strength than steel | High |
Plastic | Non-aggressive fluid applications | Excellent chemical resistance | Limited pressure and temperature ratings | Low |
Rubber | Seals and gaskets in various systems | Flexibility and leak-proof capabilities | Degrades with exposure to certain chemicals | Medium |
This strategic material selection guide provides B2B buyers with essential insights into the materials commonly used in hydraulic and pneumatic systems, enabling informed decisions that align with their specific application requirements and regional standards.
In-depth Look: Manufacturing Processes and Quality Assurance for hydraulics and pneumatics
What Are the Main Stages of Manufacturing Hydraulics and Pneumatics?
Manufacturing hydraulic and pneumatic components involves a series of well-defined stages to ensure efficiency and quality. Understanding these stages can help B2B buyers in Africa, South America, the Middle East, and Europe make informed decisions when sourcing components.
Material Preparation: How Are Raw Materials Selected and Processed?
The manufacturing process begins with material preparation, where high-quality raw materials, such as metals (steel, aluminum) and polymers, are selected based on their mechanical properties. These materials are then cut, cleaned, and sometimes treated to enhance their durability. For instance, steel components may undergo heat treatment to improve strength, while aluminum parts might be anodized for corrosion resistance.
Forming Techniques: What Methods Are Used to Shape Components?
Once materials are prepared, various forming techniques are employed to shape the components. Key methods include:
- Forging: This technique uses controlled pressure to shape metals, ensuring high strength and durability. It is commonly used for parts like hydraulic cylinders and fittings.
- Machining: CNC (Computer Numerical Control) machining is prevalent for creating precise parts. It allows for intricate designs and tight tolerances, essential for pneumatic valves and actuators.
- Injection Molding: Used primarily for plastic components, this method involves injecting molten plastic into a mold. It’s efficient for producing large volumes of parts, such as pneumatic connectors.
These forming techniques are critical in determining the performance and reliability of hydraulic and pneumatic systems.
Assembly Processes: How Are Components Joined Together?
The assembly stage involves the integration of various components into a final product. This may include:
- Welding: Often used for metal parts, welding ensures strong joints that can withstand high pressures.
- Bolting and Fastening: Mechanical fastening methods are common for components that require maintenance or replacement.
- Sealing: Proper sealing is crucial to prevent leaks in hydraulic systems. O-rings and gaskets are commonly used to ensure airtight and watertight seals.
Attention to detail during assembly is vital, as any oversight can lead to system failures.
Finishing: What Treatments Are Applied for Quality Assurance?
The final stage of manufacturing includes finishing processes that enhance the appearance and functionality of the components. These may include:
- Surface Treatment: Techniques like plating, painting, or powder coating are applied to protect against corrosion and wear.
- Quality Inspections: Before shipment, components undergo inspections to ensure they meet specified standards.
Finishing not only improves aesthetics but also significantly impacts the longevity and reliability of hydraulic and pneumatic systems.
What Quality Assurance Practices Are Essential in Hydraulics and Pneumatics Manufacturing?
Quality assurance (QA) is critical in the manufacturing of hydraulic and pneumatic components, ensuring that products meet both international and industry-specific standards.
Which International Standards Should Buyers Be Aware Of?
International standards such as ISO 9001 provide a framework for quality management systems, ensuring consistent quality across manufacturing processes. Other relevant standards include:
- CE Marking: Indicates compliance with European safety standards, crucial for buyers in Europe.
- API Standards: American Petroleum Institute standards are essential for components used in oil and gas applications.
Understanding these standards helps buyers assess the credibility and reliability of suppliers.
What Are the Key Quality Control Checkpoints?
Quality control (QC) involves several checkpoints throughout the manufacturing process:
- Incoming Quality Control (IQC): Raw materials are inspected upon arrival to ensure they meet specified standards.
- In-Process Quality Control (IPQC): Ongoing inspections during manufacturing help identify defects early in the process.
- Final Quality Control (FQC): The finished products undergo rigorous testing to ensure they meet functional and safety standards.
These checkpoints are crucial for maintaining the integrity of hydraulic and pneumatic systems.
What Common Testing Methods Are Utilized?
Several testing methods are employed to verify the quality and performance of hydraulic and pneumatic components:
- Pressure Testing: Ensures that components can withstand the required pressure without leaks.
- Functional Testing: Validates that the component operates as intended under simulated operational conditions.
- Durability Testing: Assesses the lifespan of components under various stress conditions.
Implementing these tests helps mitigate risks associated with system failures, providing peace of mind for buyers.
How Can B2B Buyers Verify Supplier Quality Control?
For international B2B buyers, especially those from regions like Africa and South America, verifying a supplier’s quality control measures is crucial. Here are actionable steps:
Conducting Supplier Audits: What Should Buyers Look For?
Performing on-site audits allows buyers to evaluate a supplier’s manufacturing processes and quality control measures firsthand. Key areas to assess include:
- Equipment and Technology: Modern machinery often correlates with higher quality outputs.
- Quality Management Systems: Verify compliance with international standards like ISO 9001.
- Employee Training: Well-trained staff contribute to better quality outcomes.
Reviewing Quality Control Reports: What Information Is Valuable?
Requesting quality control reports can provide insights into a supplier’s QA performance. Look for:
- Defect Rates: Low defect rates indicate robust QC processes.
- Testing Results: Documentation of pressure tests, functional tests, and durability tests should be provided.
- Compliance Certifications: Ensure the supplier holds relevant certifications for the markets they serve.
Utilizing Third-Party Inspections: How Can Buyers Ensure Objectivity?
Engaging third-party inspection services can offer an unbiased evaluation of a supplier’s quality control practices. These services can conduct:
- Random Sample Testing: Assessing a random selection of products can provide insights into overall quality.
- Factory Audits: Comprehensive audits by third-party experts can reveal potential issues that may not be apparent during a supplier audit.
By following these steps, B2B buyers can make informed decisions and mitigate risks associated with sourcing hydraulic and pneumatic components.
Conclusion: Why Quality Assurance Matters for International Buyers
In the world of hydraulics and pneumatics, understanding manufacturing processes and implementing rigorous quality assurance practices are essential for ensuring reliable and efficient components. By knowing what to look for and how to verify supplier capabilities, international B2B buyers can confidently source high-quality products that meet their operational needs.
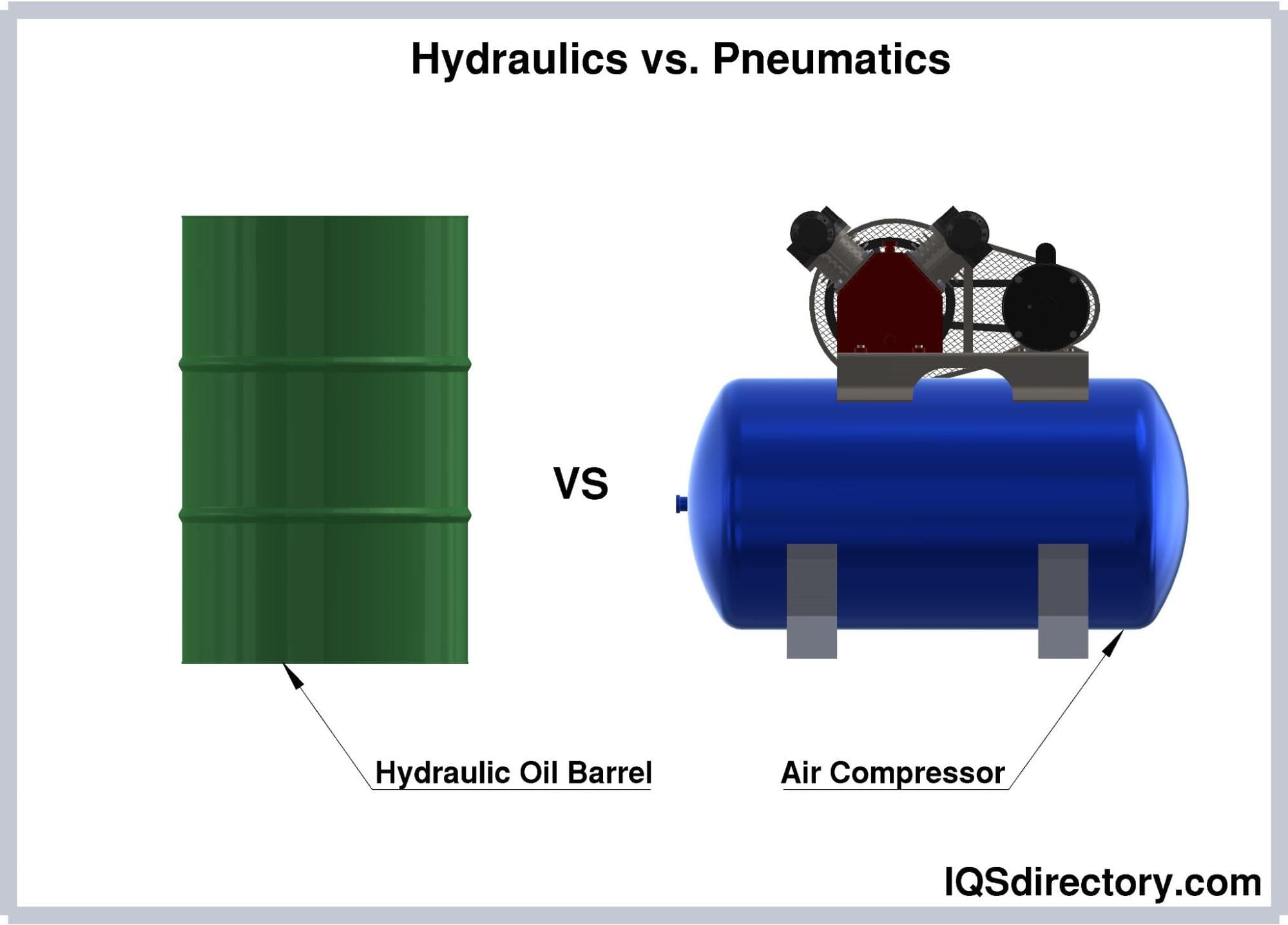
A stock image related to hydraulics and pneumatics.
Practical Sourcing Guide: A Step-by-Step Checklist for ‘hydraulics and pneumatics’
Introduction
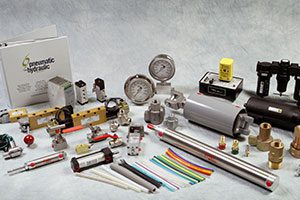
A stock image related to hydraulics and pneumatics.
Navigating the procurement of hydraulics and pneumatics components can be complex, especially for international B2B buyers. This guide provides a practical checklist to streamline your sourcing process, ensuring you make informed decisions that align with your operational needs and budget considerations.
Step 1: Define Your Technical Specifications
Understanding your specific requirements is crucial before starting the sourcing process. Define the type of hydraulic or pneumatic systems you need, including load capacities, pressure ratings, and operating environments.
– Considerations: Identify whether your application demands high precision (favoring hydraulics) or faster operation (favoring pneumatics).
Step 2: Identify Suitable Suppliers
Conduct thorough research to compile a list of potential suppliers in the hydraulics and pneumatics sector. Look for manufacturers and distributors with a solid reputation in your target markets, especially in regions like Africa, South America, the Middle East, and Europe.
– Resources: Utilize industry directories, trade shows, and online platforms to discover suppliers that specialize in your required components.
Step 3: Evaluate Supplier Certifications
Before moving forward, verify that your chosen suppliers hold relevant certifications and comply with international standards such as ISO or API. This step is vital for ensuring product quality and reliability.
– Verification: Request documentation to confirm certifications and check for any industry-specific compliance requirements that may apply to your sector.
Step 4: Request Product Samples
Obtaining samples allows you to assess the quality and compatibility of the components with your systems. This step is essential for verifying that the products meet your specifications and performance expectations.
– Evaluation: Test the samples under real-world conditions to ensure they operate effectively within your application.
Step 5: Assess Pricing and Payment Terms
Once you have identified potential suppliers and assessed their products, compare pricing structures and payment terms. Understanding the total cost, including shipping and taxes, is crucial for budgeting.
– Negotiation: Don’t hesitate to negotiate terms that are favorable to your business, such as bulk discounts or extended payment periods.
Step 6: Check References and Customer Feedback
Gather insights from previous customers about their experiences with the suppliers you are considering. This step can reveal critical information regarding reliability, customer service, and post-sale support.
– Questions to Ask: Inquire about delivery times, product performance, and how the supplier handled any issues that arose.
Step 7: Plan for After-Sales Support and Maintenance
Ensure that your selected supplier offers robust after-sales support, including maintenance services and spare parts availability. This support is crucial for minimizing downtime and ensuring the longevity of your hydraulic and pneumatic systems.
– Service Agreements: Discuss potential service contracts that can provide regular maintenance and quicker response times for repairs.
By following these steps, B2B buyers can effectively navigate the complexities of sourcing hydraulics and pneumatics, leading to successful procurement outcomes tailored to their operational needs.
Comprehensive Cost and Pricing Analysis for hydraulics and pneumatics Sourcing
What Are the Key Cost Components in Hydraulics and Pneumatics Sourcing?
When sourcing hydraulic and pneumatic systems, understanding the cost structure is crucial for international B2B buyers. The primary cost components include materials, labor, manufacturing overhead, tooling, quality control (QC), logistics, and profit margins.
-
Materials: The choice of materials significantly impacts the overall cost. Hydraulic systems often utilize high-strength steel or aluminum, while pneumatics may rely on lighter materials. The price fluctuations in raw materials can directly influence pricing.
-
Labor: Labor costs vary widely based on geographic location. For instance, labor costs may be lower in regions like Africa compared to Europe. However, skilled labor for specialized assembly can command higher wages, affecting total costs.
-
Manufacturing Overhead: This includes indirect costs such as utilities, rent, and administrative expenses. Efficient manufacturing processes can help lower these overheads, thus reducing prices.
-
Tooling: The initial investment in tooling is significant, especially for custom solutions. Buyers should consider the amortization of tooling costs over large production runs to better understand long-term pricing.
-
Quality Control (QC): Implementing stringent QC measures ensures product reliability but can add to costs. Certifications (e.g., ISO) also require compliance and can influence pricing.
-
Logistics: Shipping and handling costs can vary depending on the distance, mode of transport, and Incoterms agreed upon. For international buyers, understanding these variables is essential for accurate budgeting.
-
Margin: Supplier margins can differ significantly based on market positioning and competition. Buyers should assess whether the pricing reflects the quality and service provided.
How Do Price Influencers Affect Hydraulics and Pneumatics Costs?
Several factors influence the pricing of hydraulic and pneumatic systems, making it essential for buyers to conduct thorough market research.
-
Volume and Minimum Order Quantity (MOQ): Bulk purchases often lead to discounted pricing. Understanding MOQs can help buyers negotiate better deals, especially for large-scale projects.
-
Specifications and Customization: Custom solutions tailored to specific applications can lead to higher prices. Buyers should evaluate whether the customization is necessary or if standard products can meet their needs.
-
Materials and Quality Certifications: Higher quality materials and certifications often come at a premium. Buyers should weigh the benefits of quality against budget constraints.
-
Supplier Factors: Supplier reliability and reputation can impact pricing. Established suppliers may charge more due to their track record, but they often provide better service and product quality.
-
Incoterms: The choice of Incoterms affects logistics costs and risk distribution. Buyers should be familiar with terms like FOB (Free on Board) and CIF (Cost, Insurance, and Freight) to make informed decisions.
What Are the Best Practices for Negotiating Prices in Hydraulics and Pneumatics Sourcing?
Effective negotiation strategies can lead to better pricing and terms for B2B buyers.
-
Research and Benchmarking: Before entering negotiations, buyers should benchmark prices and understand industry standards. This knowledge empowers them to negotiate from a position of strength.
-
Focus on Total Cost of Ownership (TCO): Buyers should consider not just the upfront costs but also maintenance, operational costs, and potential downtime. A lower initial price may not always equate to better value.
-
Leverage Relationships: Building strong relationships with suppliers can lead to better deals and preferential treatment. Long-term partnerships often result in more favorable terms.
-
Be Clear on Requirements: Clearly defined specifications can reduce miscommunication and help prevent additional costs due to changes or customizations.
-
Consider Payment Terms: Negotiating favorable payment terms can improve cash flow and overall purchasing strategy.
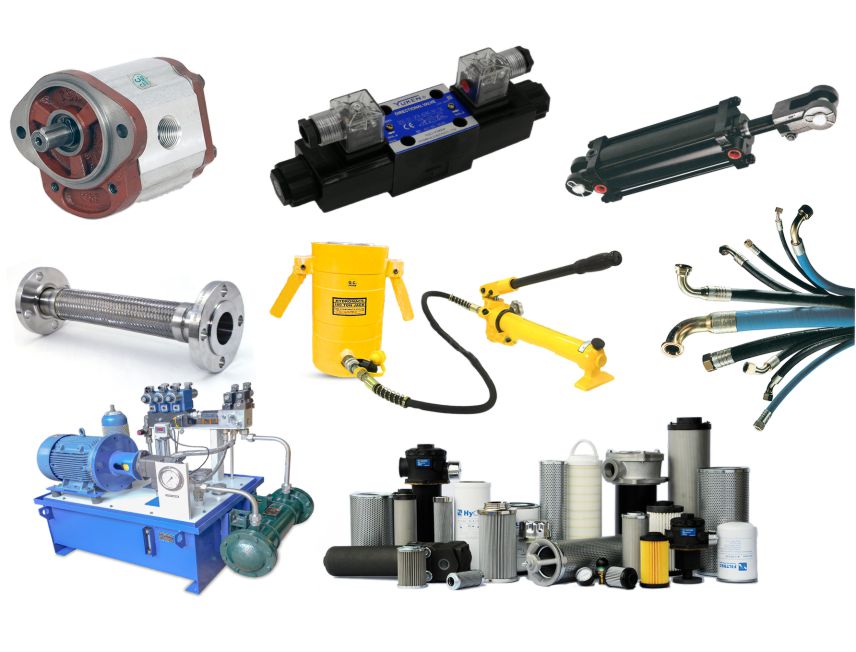
A stock image related to hydraulics and pneumatics.
Conclusion
Understanding the comprehensive cost structure and pricing dynamics in hydraulics and pneumatics sourcing is essential for international B2B buyers, particularly from regions like Africa, South America, the Middle East, and Europe. By analyzing cost components, recognizing price influencers, and employing effective negotiation strategies, buyers can optimize their sourcing processes and ensure better value for their investments. Always remember that prices can fluctuate, and it is advisable to consult multiple suppliers to gather a range of indicative prices before making purchasing decisions.
Alternatives Analysis: Comparing hydraulics and pneumatics With Other Solutions
Introduction: Exploring Alternatives to Hydraulics and Pneumatics
When considering fluid power systems, hydraulics and pneumatics are often at the forefront due to their efficiency and versatility. However, various alternative technologies can also fulfill similar roles in industrial applications. Understanding these alternatives can help international B2B buyers make informed decisions based on specific needs, operational environments, and financial constraints. This analysis compares hydraulics and pneumatics with electric drives and mechanical systems to provide a comprehensive overview of viable options.
Comparison Table: Hydraulics and Pneumatics vs Alternatives
Comparison Aspect | Hydraulics And Pneumatics | Electric Drives | Mechanical Systems |
---|---|---|---|
Performance | High power, precise control | Good for moderate loads | Limited by physical dimensions |
Cost | Moderate initial investment | Higher initial costs, lower operational costs | Lower upfront costs, but high maintenance |
Ease of Implementation | Requires specialized setup | Straightforward integration | Simple installation |
Maintenance | Regular maintenance needed | Minimal, mostly electrical checks | Moderate, depends on wear and tear |
Best Use Case | Heavy-duty applications | Automation in production | General applications requiring basic movement |
Detailed Breakdown of Alternatives
What Are the Pros and Cons of Electric Drives?
Electric drives utilize electric motors to produce mechanical motion, making them suitable for various applications. One significant advantage is their ability to provide precise control with minimal noise and vibration, enhancing the working environment. Additionally, electric drives have lower ongoing operational costs compared to hydraulic systems, primarily due to their energy efficiency. However, they may have higher initial costs and may not perform as well in heavy-load applications, where hydraulic systems excel. Electric drives are best for automation tasks in manufacturing settings, where precision and reliability are paramount.
How Do Mechanical Systems Compare to Hydraulics and Pneumatics?
Mechanical systems rely on gears, levers, and other physical components to transmit force. They are generally less expensive to install and maintain than hydraulic and pneumatic systems, making them appealing for simpler applications. However, mechanical systems can be limited by their physical size and the forces they can handle. They may not provide the same level of power or precision as hydraulics or pneumatics. Mechanical systems are ideal for general applications where heavy lifting is not a primary requirement, such as conveyor systems in manufacturing.
Conclusion: How to Choose the Right Solution for Your Needs
Selecting the appropriate power transmission system involves evaluating the specific requirements of your application, including load capacity, required precision, environmental conditions, and budget constraints. Hydraulics and pneumatics are excellent for heavy-duty applications requiring high power and precise control, while electric drives offer energy efficiency and lower operational costs. Mechanical systems provide a cost-effective solution for simpler tasks but may lack the strength and precision needed for more demanding applications. By carefully analyzing these factors, B2B buyers can make informed decisions that align with their operational goals and financial strategies.
Essential Technical Properties and Trade Terminology for hydraulics and pneumatics
What Are the Essential Technical Properties of Hydraulics and Pneumatics?
Understanding the technical properties of hydraulic and pneumatic systems is crucial for international B2B buyers seeking efficient solutions. Here are several key specifications to consider:
1. Material Grade: Why Is It Important for Performance?
The material used in hydraulic and pneumatic components, such as cylinders, valves, and hoses, directly affects durability and performance. Common materials include steel, aluminum, and various plastics, each offering different strength, weight, and corrosion resistance properties. For instance, using high-grade steel can ensure that components withstand high pressures without failure, which is particularly vital in heavy-duty applications.
2. Tolerance Levels: How Do They Impact Precision?
Tolerance levels refer to the allowable variation in dimensions of components. In hydraulic and pneumatic systems, tight tolerances are essential for ensuring proper fit and function. For example, a hydraulic cylinder with a tolerance of ±0.01 mm will perform more reliably than one with ±0.5 mm, as the former will reduce leakage and improve efficiency. Buyers should prioritize suppliers who can meet specific tolerance requirements to ensure optimal performance.
3. Operating Pressure: What Should You Know About System Limits?
Operating pressure is a critical specification that indicates the maximum pressure a hydraulic or pneumatic system can safely handle. This is measured in bar or psi. Buyers must choose systems that can operate within the required pressure ranges for their applications to prevent failures and ensure safety. For example, a hydraulic press used in metal forming may require a system rated for 200 bar, while a pneumatic actuator may only need 6 bar.
4. Flow Rate: How Does It Affect System Efficiency?
Flow rate, measured in liters per minute (L/min) or cubic feet per minute (CFM), indicates how much fluid can move through the system. A higher flow rate can lead to faster operation but may require larger and more expensive components. Buyers should assess their operational needs to strike a balance between speed and cost, ensuring that the flow rate aligns with the application’s requirements.
5. Temperature Range: Why Is It Critical for System Longevity?
Temperature range specifies the operational limits within which hydraulic or pneumatic systems can function effectively. Extreme temperatures can lead to fluid degradation or seal failure. Buyers must ensure that the components they select can withstand the environmental conditions of their application, particularly in regions with harsh climates, such as parts of Africa or the Middle East.
What Are Common Trade Terms in Hydraulics and Pneumatics?
Familiarity with industry terminology can enhance communication and negotiation for international B2B buyers. Here are key terms to understand:
1. OEM (Original Equipment Manufacturer): Why Is It Key in Sourcing?
OEM refers to companies that manufacture parts or equipment that are sold under another company’s brand. Understanding whether a supplier is an OEM can help buyers ensure they are sourcing high-quality components that meet industry standards, which is crucial for maintaining system reliability.
2. MOQ (Minimum Order Quantity): How Does It Affect Your Purchasing Strategy?
MOQ indicates the smallest quantity a supplier is willing to sell. This term is particularly important for businesses looking to manage inventory costs. Understanding MOQs can help buyers negotiate better terms, especially when sourcing components for large-scale operations.
3. RFQ (Request for Quotation): How Can It Streamline Procurement?
An RFQ is a document sent to suppliers to request pricing for specific products or services. Including detailed specifications in an RFQ can lead to more accurate quotes, enabling buyers to make informed decisions based on cost and quality comparisons.
4. Incoterms: What Role Do They Play in International Trade?
Incoterms define the responsibilities of buyers and sellers regarding shipping costs, risk, and insurance. Familiarity with these terms is vital for international transactions, as they clarify who is liable for costs and risks at various stages of the shipping process.
By understanding these essential technical properties and trade terminology, international B2B buyers can make more informed decisions, ensuring they select the right hydraulic and pneumatic solutions for their specific needs.
Navigating Market Dynamics and Sourcing Trends in the hydraulics and pneumatics Sector
What Are the Current Market Dynamics and Key Trends in the Hydraulics and Pneumatics Sector?
The hydraulics and pneumatics market is undergoing significant transformation, driven by advancements in technology and changing industrial needs. Key global drivers include the rise of automation, increased demand for energy-efficient systems, and a growing emphasis on safety standards. In regions like Africa and South America, the expansion of manufacturing sectors and infrastructure projects has spurred demand for hydraulic and pneumatic systems, while in Europe and the Middle East, there is a notable shift towards smart manufacturing technologies.
Emerging B2B tech trends include the integration of IoT (Internet of Things) into hydraulic and pneumatic systems, enabling real-time monitoring and predictive maintenance. This not only enhances operational efficiency but also reduces downtime, a critical factor for international buyers. Additionally, the trend toward modular systems allows for greater customization and flexibility, catering to the diverse needs of various industries, from automotive to construction.
For international B2B buyers, understanding these dynamics is crucial. Buyers should look for suppliers that offer innovative solutions, such as smart hydraulic systems or energy-efficient pneumatic equipment. Sourcing decisions should also consider suppliers’ capabilities in adapting to local regulations and standards, which can vary significantly across regions.
How Can Sustainability and Ethical Sourcing Impact B2B Decisions in the Hydraulics and Pneumatics Sector?
Sustainability is becoming a pivotal concern in the hydraulics and pneumatics sector. The environmental impact of hydraulic fluids and pneumatic systems, particularly regarding oil spills and emissions, necessitates a shift towards more sustainable practices. B2B buyers are increasingly seeking suppliers that prioritize eco-friendly materials and processes.
Ethical sourcing is equally important, as companies face pressure to ensure that their supply chains are transparent and responsible. This includes sourcing components from manufacturers that adhere to environmental regulations and labor standards. Certifications such as ISO 14001 (Environmental Management) and ISO 45001 (Occupational Health and Safety) are gaining traction among buyers looking to validate the sustainability of their suppliers.
The use of biodegradable hydraulic fluids and recyclable pneumatic components is a growing trend. Buyers should engage with suppliers who invest in ‘green’ technologies and materials, as these efforts not only reduce environmental footprints but can also lead to cost savings through improved energy efficiency.
What Is the Brief Evolution of Hydraulics and Pneumatics in the B2B Market?
The evolution of hydraulics and pneumatics has been marked by significant technological advancements since their inception. The hydraulic press, developed in the 18th century, laid the groundwork for modern hydraulic systems, enabling the application of powerful forces with minimal effort. As industries evolved, so did the need for more precise and efficient systems, leading to the development of pneumatic technologies in the early 20th century.
The introduction of digital controls and automation in the late 20th century revolutionized both hydraulics and pneumatics, enhancing their precision and efficiency. Today, the integration of IoT and smart technologies represents the latest phase in their evolution, allowing for real-time data analysis and improved operational control. This historical context is vital for B2B buyers, as it highlights the continuous innovation and adaptability within the sector, underscoring the importance of partnering with forward-thinking suppliers.
Frequently Asked Questions (FAQs) for B2B Buyers of hydraulics and pneumatics
-
How do I solve hydraulic system leakage issues?
To address hydraulic system leakage, first conduct a thorough inspection of all components, including hoses, fittings, and seals, to identify the source of the leak. Ensure that all connections are properly tightened, as loose fittings can lead to significant leaks. Replace any worn-out seals or damaged hoses immediately to prevent further fluid loss. Additionally, consider using a hydraulic fluid with superior leak resistance. Regular maintenance checks can help detect issues early, reducing downtime and costs associated with leaks. -
What is the best pneumatic actuator for heavy-duty applications?
For heavy-duty applications, the best pneumatic actuator is typically a double-acting cylinder, which provides power in both directions. Look for actuators with a higher bore size and stroke length to accommodate greater loads. Additionally, consider features such as shock absorbers and adjustable speed controls for enhanced performance. Brands known for reliability in heavy-duty applications include SMC, Parker, and Festo. Always assess the specific requirements of your application, including environmental conditions and space constraints, before making a selection. -
What are the key factors to consider when sourcing hydraulic components internationally?
When sourcing hydraulic components internationally, key factors include the supplier’s reputation, compliance with international standards, and their ability to provide timely delivery. Research potential suppliers through industry reviews, certifications, and customer testimonials. Additionally, consider the availability of after-sales support and warranty terms. Understanding local regulations and import duties is crucial, as these can significantly impact your total cost. Establish clear communication channels to discuss customization needs and ensure quality control measures are in place. -
How do I ensure the quality of hydraulic and pneumatic products?
To ensure product quality, request certifications such as ISO 9001 from suppliers, which indicate adherence to quality management standards. Conduct factory audits if feasible, or engage third-party inspection services to verify product specifications before shipment. Always ask for samples to test compatibility with your existing systems. Establish a clear quality assurance process that includes testing protocols upon receipt of goods. This proactive approach minimizes the risk of defects and operational disruptions. -
What are the typical minimum order quantities (MOQs) for hydraulic and pneumatic components?
Minimum order quantities (MOQs) for hydraulic and pneumatic components can vary significantly based on the supplier and the specific product type. Generally, MOQs range from 50 to 500 units for standard components. Custom products or specialized parts may require higher MOQs due to the costs associated with tooling and production setup. Always clarify MOQs upfront during negotiations, and consider the potential for bulk purchasing discounts, which can lead to cost savings in the long term. -
What payment terms should I negotiate with international suppliers?
When negotiating payment terms with international suppliers, aim for conditions that minimize risk while maintaining cash flow. Common terms include a 30% deposit upfront with the balance due upon delivery or after inspection. Consider using letters of credit for larger transactions, as they provide security for both parties. Additionally, inquire about early payment discounts that can offer savings. Establishing a good relationship with your supplier can also lead to more favorable terms over time. -
How can I effectively manage logistics for importing hydraulic and pneumatic equipment?
Effective logistics management for importing hydraulic and pneumatic equipment involves thorough planning and coordination. Start by selecting a reliable freight forwarder familiar with your destination country’s import regulations. Ensure that all necessary documentation, such as bills of lading and customs declarations, is accurate and complete. Consider using a Just-In-Time (JIT) inventory system to minimize storage costs and ensure timely delivery. Regular communication with your supplier and freight forwarder can help address potential issues proactively. -
What are the most common applications for hydraulics and pneumatics in various industries?
Hydraulics are commonly used in industries requiring high force applications, such as construction (excavators, lifts), manufacturing (presses, molding machines), and automotive (braking systems). Pneumatics, on the other hand, are often utilized in settings requiring rapid movement and clean operations, such as packaging, food processing, and assembly lines. Understanding the specific applications in your industry can help you choose the right system and components, ensuring optimal efficiency and performance.
Important Disclaimer & Terms of Use
⚠️ Important Disclaimer
The information provided in this guide, including content regarding manufacturers, technical specifications, and market analysis, is for informational and educational purposes only. It does not constitute professional procurement advice, financial advice, or legal advice.
While we have made every effort to ensure the accuracy and timeliness of the information, we are not responsible for any errors, omissions, or outdated information. Market conditions, company details, and technical standards are subject to change.
B2B buyers must conduct their own independent and thorough due diligence before making any purchasing decisions. This includes contacting suppliers directly, verifying certifications, requesting samples, and seeking professional consultation. The risk of relying on any information in this guide is borne solely by the reader.
Strategic Sourcing Conclusion and Outlook for hydraulics and pneumatics
As the global market for hydraulics and pneumatics continues to evolve, strategic sourcing remains crucial for international B2B buyers. Understanding the nuances between hydraulic and pneumatic systems—such as their operational principles, advantages, and ideal applications—empowers businesses to make informed decisions that enhance efficiency and productivity. Buyers from Africa, South America, the Middle East, and Europe should prioritize partnerships with reputable suppliers who offer comprehensive solutions, ensuring that they can access quality components tailored to their specific needs.
What are the benefits of effective strategic sourcing in hydraulics and pneumatics? By fostering strong supplier relationships, companies can achieve cost savings, improve supply chain reliability, and gain access to innovative technologies. This is particularly important in regions where infrastructure development is rapidly advancing, creating a demand for high-quality hydraulic and pneumatic solutions.
Looking ahead, the integration of smart technologies and sustainability practices in hydraulic and pneumatic systems will reshape the landscape. International B2B buyers are encouraged to stay proactive and explore these emerging trends to enhance their competitive edge. Engage with suppliers who are aligned with your strategic goals and ready to support your business in navigating the complexities of this dynamic industry.