The Ultimate Guide to Perforated Metal Panels (2025)
Introduction: Navigating the Global Market for perforated metal panels
Navigating the global market for perforated metal panels presents a unique challenge for international B2B buyers, particularly when sourcing materials that meet specific performance and aesthetic requirements. Whether you are based in Africa, South America, the Middle East, or Europe, understanding the diverse types and applications of perforated metal is crucial for making informed purchasing decisions. This comprehensive guide delves into the various forms of perforated metal panels, including aluminum, stainless steel, and carbon steel, highlighting their uses in architectural design, filtration systems, and industrial applications.
Buyers will gain insights into the latest trends in perforated metal, which not only serves functional purposes—such as ventilation and sound dampening—but also enhances the visual appeal of structures. We will discuss strategies for vetting suppliers, comparing costs, and ensuring quality compliance, which are essential for effective procurement. Additionally, the guide addresses logistical considerations, including shipping and local regulations, that can impact your sourcing process.
By empowering B2B buyers with actionable insights and expert knowledge, this guide aims to streamline your decision-making process, ultimately enhancing your project’s success. From understanding the nuances of different perforation patterns to evaluating supplier capabilities, you will be equipped with the tools necessary to navigate the competitive landscape of the perforated metal market effectively.
Understanding perforated metal panels Types and Variations
Type Name | Key Distinguishing Features | Primary B2B Applications | Brief Pros & Cons for Buyers |
---|---|---|---|
Round Perforated Panels | Circular holes, varying diameters, high aesthetic appeal | Architectural facades, ventilation screens | Pros: Versatile design; Cons: May require custom sizing. |
Square Perforated Panels | Square holes, uniform spacing, excellent for sound absorption | Acoustic panels, safety guards | Pros: Efficient sound control; Cons: Limited aesthetic options. |
Slotted Perforated Panels | Rectangular slots, elongated openings, enhanced airflow | Grilles, filters, machinery guards | Pros: High airflow; Cons: Less visual appeal. |
Hexagonal Perforated Panels | Unique hexagonal shapes, modern look, effective filtration | Decorative applications, fencing | Pros: Distinctive design; Cons: May not be as structurally strong. |
Designer Perforated Panels | Custom patterns, artistic designs, often made from premium materials | High-end architectural projects, art installations | Pros: Unique aesthetics; Cons: Higher cost and lead time. |
What Are the Characteristics of Round Perforated Panels?
Round perforated panels feature circular holes that can vary in diameter, allowing for a wide range of design possibilities. These panels are often used in architectural facades and ventilation systems due to their ability to blend functionality with aesthetics. When purchasing, buyers should consider the specific size and spacing of holes, as well as the material used, to ensure they meet project requirements.
How Do Square Perforated Panels Offer Sound Absorption?
Square perforated panels are known for their uniform hole pattern, which provides excellent sound absorption properties. This makes them ideal for applications such as acoustic panels and safety guards. When evaluating square panels, B2B buyers should focus on the gauge of the material and the percentage of open area to optimize sound control while maintaining structural integrity.
What Advantages Do Slotted Perforated Panels Provide?
Slotted perforated panels are characterized by elongated openings that facilitate enhanced airflow and drainage. They are frequently used in grilles, filters, and machinery guards. Buyers should assess the slot dimensions and spacing, as these factors significantly influence airflow efficiency and overall performance in their intended applications.
Why Choose Hexagonal Perforated Panels for Decorative Needs?
Hexagonal perforated panels offer a modern and stylish alternative to traditional shapes. Their unique design is not only visually appealing but also effective for filtration in various applications, including decorative fencing. When considering hexagonal panels, buyers should evaluate the material’s strength and the panel’s installation requirements to ensure they meet aesthetic and functional goals.
What Makes Designer Perforated Panels Unique?
Designer perforated panels are tailored to feature custom patterns and artistic designs, making them suitable for high-end architectural projects and art installations. They are typically made from premium materials and can significantly enhance the visual appeal of any structure. Buyers should be prepared for higher costs and longer lead times, as these panels often require specialized manufacturing processes.
Key Industrial Applications of perforated metal panels
Industry/Sector | Specific Application of Perforated Metal Panels | Value/Benefit for the Business | Key Sourcing Considerations for this Application |
---|---|---|---|
Architecture & Construction | Facades and Wall Panels | Enhances aesthetics while providing ventilation | Material selection (aluminum, steel), design flexibility, and sustainability certifications. |
Automotive Manufacturing | Grilles and Ventilation Covers | Improves airflow and reduces heat accumulation | Custom hole patterns, durability against environmental factors, and compliance with industry standards. |
Oil & Gas | Safety Barriers and Fencing | Ensures safety while allowing visibility | Corrosion resistance, compliance with safety regulations, and availability of large sheets. |
Environmental Engineering | Filtration Systems | Enhances filtration efficiency for air and liquids | Material compatibility with specific filtration needs, open area percentage, and maintenance requirements. |
Retail & Display | Decorative Screens and Partitions | Creates visually appealing environments and divides spaces | Design options, strength-to-weight ratio, and ease of installation. |
How Are Perforated Metal Panels Used in Architecture & Construction?
In the architecture and construction industry, perforated metal panels are extensively used for facades and wall systems. These panels not only enhance the visual appeal of buildings but also provide necessary ventilation, contributing to energy efficiency. International buyers, particularly from Europe and the Middle East, should consider factors such as material selection (aluminum vs. steel) and sustainability certifications when sourcing these panels to align with local building regulations and aesthetic standards.
What Are the Applications in Automotive Manufacturing?
Automotive manufacturers utilize perforated metal panels for grilles and ventilation covers, which are essential for improving airflow and reducing heat build-up in vehicles. Buyers from Africa and South America must focus on custom hole patterns and materials that withstand harsh conditions. Ensuring durability and compliance with automotive industry standards is crucial for maintaining safety and performance.
How Is Perforated Metal Used in the Oil & Gas Sector?
In the oil and gas sector, perforated metal panels serve as safety barriers and fencing, providing visibility while ensuring protection in hazardous environments. International B2B buyers should prioritize sourcing materials that exhibit corrosion resistance and compliance with strict safety regulations, particularly in the Middle East where environmental conditions can be extreme. The ability to provide large sheets for extensive coverage is also a vital consideration.
What Role Do Perforated Panels Play in Environmental Engineering?
Perforated metal panels are critical in environmental engineering, specifically in filtration systems for air and liquid applications. These panels enhance filtration efficiency, making them essential for wastewater treatment facilities and air purification systems. Buyers from South America and Africa should assess the material compatibility with specific filtration needs and the open area percentage required for optimal performance. Maintenance requirements also play a significant role in the sourcing decision.
How Are Perforated Metal Panels Beneficial for Retail & Display?
In the retail and display sector, perforated metal panels are used for decorative screens and partitions, creating visually appealing environments that enhance customer experience. Buyers, especially from Europe, should consider design options and the strength-to-weight ratio when sourcing these panels, as ease of installation can significantly impact project timelines. The versatility of these panels allows for creative applications, making them a popular choice in retail design.
3 Common User Pain Points for ‘perforated metal panels’ & Their Solutions
Scenario 1: Difficulty in Selecting the Right Material for Perforated Metal Panels
The Problem: B2B buyers often face challenges when it comes to selecting the appropriate material for perforated metal panels. With options like aluminum, stainless steel, and carbon steel available, each material comes with its own set of properties such as weight, corrosion resistance, and aesthetic appeal. For buyers in regions with diverse climates, such as the Middle East’s heat and humidity or South America’s variable weather, choosing the right material is crucial. Misalignment in material selection can lead to premature wear, increased maintenance costs, and ultimately a negative impact on project timelines.
The Solution: To effectively navigate this challenge, buyers should conduct a thorough analysis of the environmental conditions their panels will be exposed to. For example, if the panels are intended for outdoor use in coastal areas, opting for stainless steel or coated aluminum may be more advantageous due to their superior corrosion resistance. Collaborating with suppliers who offer detailed product specifications and environmental performance data can provide critical insights. Buyers should also consider working with engineering consultants who specialize in material science to assess the long-term durability and functionality of the materials in question. Engaging in this level of due diligence can significantly mitigate risks associated with poor material choices.
Scenario 2: Managing Customization Needs for Unique Applications
The Problem: Many B2B buyers need perforated metal panels that are customized to fit specific applications, such as architectural designs or specialized filtration systems. However, the customization process can often be cumbersome, with potential delays in production and shipping leading to project holdups. Buyers may also struggle with understanding the technical specifications required for their custom designs, which can result in miscommunications with manufacturers and costly errors.
The Solution: Buyers should begin the customization process by clearly defining their project requirements, including dimensions, hole size, and spacing. Utilizing design software or CAD tools can help visualize how the perforated panels will fit within the overall project scope. Once specifications are established, engaging manufacturers early in the design process can ensure that they are capable of meeting the custom requirements. Establishing a communication plan that includes regular updates and feedback loops can further streamline the process. Additionally, buyers should inquire about prototyping options to evaluate the panel’s performance before full-scale production, reducing the risk of errors and enhancing overall satisfaction.
Scenario 3: Overcoming Cost and Budget Constraints
The Problem: Budget constraints are a common pain point for B2B buyers looking to procure perforated metal panels, especially for large-scale projects. Buyers often find themselves torn between quality and cost, leading to compromises that can affect both the project’s integrity and long-term sustainability. In regions like Africa or South America, where economic conditions may fluctuate, securing the best pricing while ensuring high-quality materials becomes even more challenging.
The Solution: To address budgetary limitations, buyers should explore a multi-sourcing strategy that includes evaluating different suppliers and manufacturers from various regions. This approach allows for price comparisons and can uncover cost-effective options without sacrificing quality. Additionally, buyers should negotiate terms that allow for bulk purchasing discounts or seek out alternative materials that still meet project specifications but are more budget-friendly. Incorporating lifecycle cost analysis into the procurement process can also provide a clearer picture of long-term savings versus upfront costs. This proactive financial strategy ensures that buyers are not only staying within budget but also making informed decisions that benefit the project in the long run.
Strategic Material Selection Guide for perforated metal panels
When selecting perforated metal panels for various applications, the choice of material plays a pivotal role in determining performance, durability, and suitability for specific environments. Below is an analysis of four common materials used in perforated metal panels, focusing on their key properties, advantages, disadvantages, and considerations for international B2B buyers.
What are the Key Properties of Aluminum Perforated Metal Panels?
Aluminum is a lightweight, corrosion-resistant material that is often used in architectural applications. It has a good strength-to-weight ratio and can withstand moderate temperatures, making it suitable for both indoor and outdoor environments. Aluminum panels can also be anodized or painted, enhancing their aesthetic appeal and further improving corrosion resistance.
Pros:
– Excellent corrosion resistance, ideal for humid or coastal environments.
– Lightweight, which reduces transportation costs.
– Easy to fabricate and install, allowing for complex designs.
Cons:
– Lower strength compared to steel, which may limit its use in high-load applications.
– Higher initial cost compared to some other materials.
Impact on Application:
Aluminum panels are particularly effective in applications requiring ventilation and light diffusion, such as facades and screens. They are compatible with various media, including air and light.
Considerations for International Buyers:
Buyers should ensure compliance with local building codes and standards, such as ASTM or DIN, particularly concerning fire safety and structural integrity. In regions like the UAE, where high temperatures are prevalent, selecting aluminum with adequate thermal resistance is crucial.
How Does Stainless Steel Compare for Perforated Metal Panels?
Stainless steel is renowned for its exceptional strength and corrosion resistance, making it suitable for demanding environments, including industrial and marine applications. It can withstand high temperatures and pressures, which is beneficial for applications like filtration and exhaust systems.
Pros:
– Superior durability and resistance to corrosion, even in harsh environments.
– High strength, making it suitable for structural applications.
– Aesthetic appeal, available in various finishes.
Cons:
– Higher cost compared to aluminum and carbon steel.
– Heavier weight can increase transportation costs and installation complexity.
Impact on Application:
Stainless steel panels are ideal for applications requiring high durability and resistance to aggressive media, such as chemicals or high-temperature gases.
Considerations for International Buyers:
Buyers should verify the grade of stainless steel (e.g., 304 vs. 316) to ensure it meets specific environmental conditions. Compliance with international standards is essential, especially in Europe, where stringent regulations may apply.
What Are the Advantages of Carbon Steel for Perforated Metal Panels?
Carbon steel is a cost-effective option for perforated metal panels, widely used in construction and industrial applications. It offers good strength and can be treated for corrosion resistance through galvanization or painting.
Pros:
– Lower cost, making it an attractive option for large-scale projects.
– Good strength-to-weight ratio, suitable for various structural applications.
– Versatile, with various finishes available.
Cons:
– Prone to corrosion if not properly treated, limiting its use in outdoor applications.
– Heavier than aluminum, which can increase shipping costs.
Impact on Application:
Carbon steel panels are commonly used in structural applications, such as building facades and industrial partitions, where cost efficiency is a priority.
Considerations for International Buyers:
Buyers should consider local climate conditions and the necessity for corrosion protection. Compliance with standards such as JIS in Japan or ASTM in the USA is vital for ensuring product quality.
Why Choose Galvanized Steel for Perforated Metal Panels?
Galvanized steel is carbon steel that has been coated with zinc to enhance its corrosion resistance. This material is particularly suited for outdoor applications where exposure to moisture is a concern.
Pros:
– Excellent corrosion resistance due to the zinc coating.
– Cost-effective compared to stainless steel.
– Good strength and durability.
Cons:
– The zinc coating can wear off over time, especially in harsh environments.
– Limited aesthetic appeal compared to aluminum or stainless steel.
Impact on Application:
Galvanized steel panels are ideal for outdoor applications, such as fencing and roofing, where weather resistance is necessary.
Considerations for International Buyers:
Ensure that the galvanization process meets local standards and that the material is suitable for the specific environmental conditions of the region, particularly in humid or coastal areas.
Summary Table of Material Selection for Perforated Metal Panels
Material | Typical Use Case for perforated metal panels | Key Advantage | Key Disadvantage/Limitation | Relative Cost (Low/Med/High) |
---|---|---|---|---|
Aluminum | Architectural facades, screens | Lightweight and corrosion-resistant | Lower strength than steel | Medium |
Stainless Steel | Industrial applications, filtration systems | Superior strength and durability | Higher cost | High |
Carbon Steel | Structural applications, partitions | Cost-effective and versatile | Prone to corrosion | Low |
Galvanized Steel | Outdoor applications, roofing | Excellent corrosion resistance | Zinc coating can wear off | Medium |
This guide provides a strategic overview of material selection for perforated metal panels, helping international B2B buyers make informed decisions based on specific application needs and regional considerations.
In-depth Look: Manufacturing Processes and Quality Assurance for perforated metal panels
What Are the Main Stages in the Manufacturing Process of Perforated Metal Panels?
The manufacturing process for perforated metal panels involves several critical stages, each essential for ensuring the final product meets the required specifications for quality and performance. The primary stages include material preparation, forming, assembly, and finishing.
Material Preparation: Selecting the Right Material for Your Needs
The first step in the manufacturing process is selecting the appropriate base material. Common materials for perforated metal panels include aluminum, stainless steel, carbon steel, and galvanized steel. Each material offers distinct advantages depending on the application, such as corrosion resistance in harsh environments or aesthetic appeal in architectural applications.
Once the material is selected, it is cut to size using techniques like laser cutting or shearing. This initial sizing is crucial as it sets the foundation for the subsequent perforation and forming processes.
How Is the Forming Process Executed for Perforated Metal Panels?
The forming stage involves creating the desired perforations in the metal sheets. This is typically achieved through various techniques, including:
- Punching: This method uses a die to create holes of various shapes and sizes. The process can produce intricate designs, making it popular for decorative panels.
- Laser Cutting: For more complex patterns, laser cutting offers precision and flexibility. It is ideal for projects requiring custom designs and can handle various materials.
- Waterjet Cutting: This technique employs high-pressure water mixed with abrasives to cut through metal. It is especially useful for thicker materials and minimizes heat-affected zones, preserving material integrity.
After perforation, the panels may undergo additional forming processes, such as bending or rolling, to achieve specific shapes or configurations.
What Quality Assurance Measures Are Essential for Perforated Metal Panels?
Quality assurance (QA) in the manufacturing of perforated metal panels is critical to ensuring that the final products meet international standards and client specifications. Key QA measures include adherence to international standards, inspection checkpoints, and testing methods.
Which International Standards Are Relevant for Perforated Metal Panels?
For international B2B buyers, understanding relevant quality standards is essential. The most recognized standard is ISO 9001, which outlines the requirements for a quality management system. Compliance with ISO 9001 ensures that manufacturers consistently provide products that meet customer and regulatory requirements.
Additionally, industry-specific certifications such as CE marking in Europe and API standards in the oil and gas sector can provide added assurance of quality and safety.
What Are the Key Quality Control Checkpoints in the Manufacturing Process?
Quality control checkpoints are integrated at various stages of the manufacturing process to ensure product quality:
-
Incoming Quality Control (IQC): This stage involves inspecting raw materials before they enter production. Buyers should ensure that suppliers conduct rigorous IQC to verify that incoming materials meet specified standards.
-
In-Process Quality Control (IPQC): During manufacturing, continuous monitoring is necessary. This can include checks on perforation accuracy, dimensions, and surface quality.
-
Final Quality Control (FQC): Once the panels are completed, a thorough inspection ensures that all specifications are met. This can include visual inspections, dimensional checks, and functional testing based on the intended use of the panels.
What Testing Methods Are Commonly Used to Ensure Quality in Perforated Metal Panels?
Testing methods vary based on application but typically include:
- Dimensional Inspection: Verifying that the panels meet specified dimensions and tolerances.
- Material Testing: Conducting tensile tests and hardness tests to ensure that the material properties meet standards.
- Surface Finish Testing: Assessing the quality of surface treatments to ensure durability and aesthetic appeal.
How Can B2B Buyers Verify Supplier Quality Control Processes?
For international B2B buyers, especially those from Africa, South America, the Middle East, and Europe, verifying a supplier’s quality control processes is vital for building trust and ensuring product reliability. Here are some strategies:
-
Conduct Audits: Regular audits of suppliers can provide insights into their quality management systems. This can help buyers assess compliance with international standards and internal quality protocols.
-
Request Quality Reports: Buyers should ask for detailed reports on quality control processes, including results from IQC, IPQC, and FQC. These reports can provide transparency into the supplier’s operations.
-
Engage Third-Party Inspectors: Utilizing third-party inspection services can provide an unbiased assessment of the manufacturing process and final products. This is particularly beneficial for buyers unfamiliar with local suppliers.
What Are the Quality Control Nuances for International B2B Buyers?
B2B buyers operating in different regions may face unique challenges related to quality control. For example, suppliers in emerging markets may have different operational standards compared to those in Europe or North America. Buyers should consider:
-
Cultural Differences: Understanding local manufacturing practices and cultural attitudes towards quality can provide insights into potential challenges.
-
Regulatory Requirements: Ensure that suppliers are aware of and compliant with local and international regulations that may affect product quality.
-
Communication: Establishing clear communication channels with suppliers can facilitate better understanding and adherence to quality expectations.
By focusing on these aspects of manufacturing processes and quality assurance, B2B buyers can make informed decisions when sourcing perforated metal panels, ultimately ensuring that they receive high-quality products that meet their specific needs.
Practical Sourcing Guide: A Step-by-Step Checklist for ‘perforated metal panels’
In the competitive landscape of international procurement, especially for specialized products like perforated metal panels, having a clear sourcing strategy is essential. This checklist is designed to guide B2B buyers through the critical steps necessary for effective sourcing, ensuring quality, compliance, and value for your investment.
Step 1: Define Your Technical Specifications
Understanding your project requirements is the foundation of successful procurement. Identify the specific dimensions, materials (such as aluminum, stainless steel, or carbon steel), hole sizes, and patterns needed for your application.
– Consider: The environment where the panels will be used (e.g., outdoor vs. indoor), as this can influence material selection and coating requirements for durability.
Step 2: Research Potential Suppliers
A thorough research phase is vital to identify reliable suppliers. Look for manufacturers with a proven track record in producing high-quality perforated metal panels.
– Tip: Utilize industry directories and trade shows to gather a list of potential suppliers. Focus on those with experience in your target regions, such as Africa, South America, or Europe, as they may better understand local regulations and market conditions.
Step 3: Evaluate Supplier Capabilities
Before committing to a supplier, assess their production capabilities and quality control processes. Inquire about their manufacturing methods, lead times, and customization options.
– Ask: What certifications do they hold? Are they ISO certified or compliant with other international standards relevant to your industry? This ensures that they meet quality benchmarks.
Step 4: Request Samples and Specifications
Always request product samples to evaluate the quality of the perforated metal panels firsthand. This step is crucial for assessing the finish, durability, and overall appearance.
– Important: Check for detailed specifications, including load-bearing capacity, corrosion resistance, and aesthetic qualities. This information is vital for making an informed decision.
Step 5: Verify Supplier Certifications
Ensure that your selected suppliers have the necessary certifications and meet regulatory standards. This step is particularly crucial for international transactions.
– Look for: Certifications like CE marking in Europe, or local compliance documentation in Africa or the Middle East, which can indicate adherence to safety and quality standards.
Step 6: Compare Pricing and Terms
Gather and compare quotes from multiple suppliers. Look beyond just the price; consider factors like shipping costs, payment terms, and warranty conditions.
– Consider: The total cost of ownership, which includes not only the purchase price but also potential shipping fees, taxes, and any customs duties applicable in your region.
Step 7: Establish Communication Channels
Effective communication with your supplier is essential for a smooth procurement process. Ensure that you have established clear lines of communication for updates on production, shipping, and any potential issues.
– Ensure: That there is a dedicated point of contact who can promptly address your queries and keep you informed throughout the sourcing process.
By following this practical sourcing checklist, international B2B buyers can navigate the complexities of procuring perforated metal panels more effectively, ensuring a successful outcome that meets their project needs.
Comprehensive Cost and Pricing Analysis for perforated metal panels Sourcing
What Are the Key Cost Components for Perforated Metal Panels?
When sourcing perforated metal panels, understanding the breakdown of costs is crucial for international B2B buyers. The primary cost components include:
-
Materials: The choice of material significantly impacts pricing. Common materials for perforated panels include aluminum, stainless steel, carbon steel, and galvanized steel. Each material has its own cost implications, with aluminum generally being more expensive than carbon steel due to its lightweight and corrosion-resistant properties.
-
Labor: Labor costs can vary based on the region and complexity of the perforation process. Skilled labor may be required for intricate designs or specialized applications, which can drive up costs.
-
Manufacturing Overhead: This includes expenses related to factory operation, such as utilities, equipment maintenance, and production facility costs. These overheads are often factored into the unit price of perforated panels.
-
Tooling Costs: Custom tooling for unique perforation patterns adds to the initial investment. If a buyer requires a specific design, the upfront tooling costs should be evaluated in relation to the expected volume of orders.
-
Quality Control (QC): Implementing stringent QC processes ensures that the panels meet industry standards and specifications. While this may increase upfront costs, it helps avoid long-term expenses related to product failures or recalls.
-
Logistics: Shipping and handling costs can vary widely based on the distance from the supplier, weight of the panels, and chosen Incoterms. International buyers must account for potential tariffs and customs duties, which can significantly impact overall costs.
-
Margin: Suppliers will mark up the base costs to ensure profitability. Understanding typical margins in the industry can help buyers negotiate better deals.
How Do Price Influencers Affect Perforated Metal Panel Costs?
Several factors can influence the pricing of perforated metal panels, particularly for international buyers:
-
Volume and Minimum Order Quantity (MOQ): Suppliers often provide discounts for bulk purchases. Understanding the MOQ can help buyers determine whether they can leverage volume pricing.
-
Specifications and Customization: Custom designs or specifications, such as hole size and pattern, can increase costs. Buyers should weigh the benefits of customization against its impact on pricing.
-
Materials and Quality Certifications: Higher quality materials and certifications (such as ISO or ASTM) can lead to higher prices. Buyers should assess whether the added costs align with their project requirements.
-
Supplier Factors: The reputation and reliability of the supplier can affect pricing. Established suppliers may charge a premium for their brand and quality assurance.
-
Incoterms: The chosen Incoterms dictate who bears shipping costs and risks, impacting total expenditure. Buyers should clarify these terms to avoid unexpected expenses.
What Buyer Tips Can Help Achieve Cost Efficiency?
For international B2B buyers, particularly in regions like Africa, South America, the Middle East, and Europe, several strategies can enhance cost efficiency:
-
Negotiate Terms: Engage suppliers in discussions about pricing, payment terms, and delivery schedules. Many suppliers are willing to negotiate to secure large contracts.
-
Total Cost of Ownership (TCO): Evaluate not just the purchase price but also the TCO, which includes maintenance, installation, and operational costs over the product’s lifecycle. Sometimes, a higher initial investment can yield lower long-term costs.
-
Research Local Suppliers: Depending on the project location, sourcing from local suppliers may reduce shipping costs and lead times. This can be particularly advantageous for urgent projects.
-
Stay Informed on Market Trends: Understanding current market conditions, such as material shortages or price fluctuations, can help buyers make informed purchasing decisions.
Disclaimer on Indicative Prices
While prices for perforated metal panels can vary widely based on the factors discussed, it is important to note that specific pricing is subject to change based on market conditions, supplier negotiations, and order specifications. Buyers should always request updated quotes from multiple suppliers to ensure competitive pricing.
Alternatives Analysis: Comparing perforated metal panels With Other Solutions
Exploring Alternatives to Perforated Metal Panels for B2B Buyers
In the quest for effective architectural and industrial solutions, perforated metal panels are often considered for their unique blend of aesthetics and functionality. However, various alternatives may also meet the needs of international B2B buyers, particularly those operating in Africa, South America, the Middle East, and Europe. Below, we compare perforated metal panels with two viable alternatives: expanded metal mesh and solid metal sheets with cut-outs.
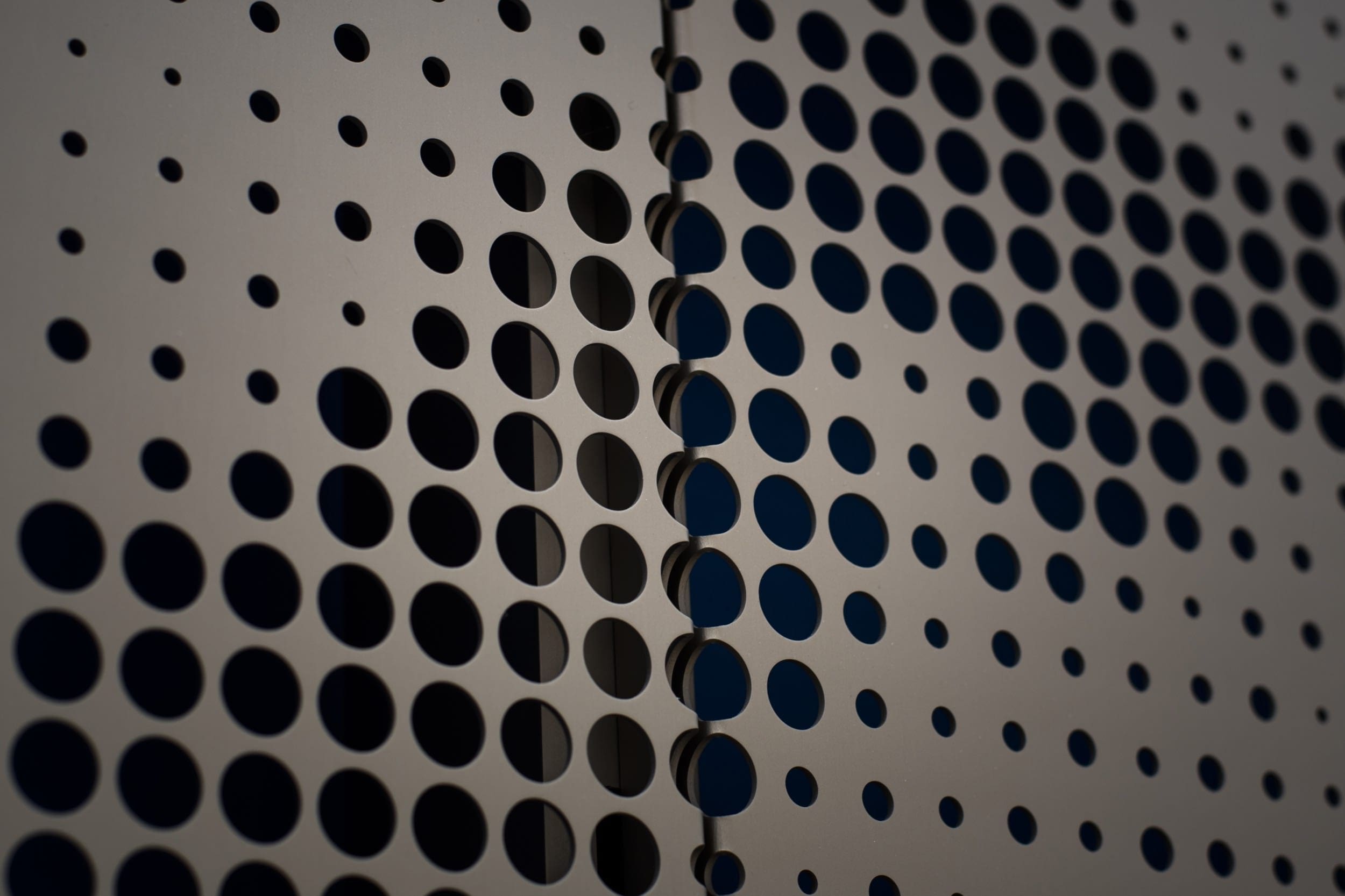
A stock image related to perforated metal panels.
Comparison Table of Perforated Metal Panels and Alternatives
Comparison Aspect | Perforated Metal Panels | Expanded Metal Mesh | Solid Metal Sheets with Cut-Outs |
---|---|---|---|
Performance | High strength-to-weight ratio; excellent for ventilation and filtration | Good airflow; flexible designs | Strong and durable; limited airflow |
Cost | Moderate; varies by material and perforation pattern | Generally lower; cost-effective | Higher due to customization |
Ease of Implementation | Moderate; requires specific tools for installation | Easy; typically pre-fabricated | Moderate; complex cutting required |
Maintenance | Low; durable and corrosion-resistant | Low; similar durability | Moderate; may require painting |
Best Use Case | Architectural features, sound barriers, filtration | Walkways, safety barriers | Decorative elements, structural support |
Detailed Breakdown of Alternatives
What Are the Advantages and Disadvantages of Expanded Metal Mesh?
Expanded metal mesh is a versatile alternative that allows for excellent airflow while maintaining structural integrity. Its manufacturing process creates a uniform mesh pattern that can be used in various applications, from walkways to safety barriers. The primary advantage is its cost-effectiveness; it is often cheaper than perforated panels and requires less complex installation. However, it may not provide the same level of aesthetic appeal or customization options, making it less suitable for high-end architectural projects.
How Do Solid Metal Sheets with Cut-Outs Compare to Perforated Panels?
Solid metal sheets with cut-outs present a strong alternative, particularly for applications requiring substantial strength and structural support. They can be customized with intricate designs, offering a unique aesthetic appeal. However, the cost tends to be higher due to the additional cutting and finishing processes involved. Furthermore, solid sheets may limit airflow and are less effective for applications requiring ventilation or filtration. This makes them more suitable for decorative elements or structural components rather than functional barriers.
Conclusion: How Should B2B Buyers Choose the Right Solution?
When selecting the appropriate solution between perforated metal panels and their alternatives, B2B buyers should consider their specific project requirements. Factors such as performance needs, budget constraints, ease of installation, and maintenance expectations play a crucial role. For projects prioritizing aesthetics and airflow, perforated panels may be ideal. Conversely, for cost-sensitive applications or where structural integrity is paramount, expanded metal mesh or solid sheets with cut-outs could offer better value. Understanding these nuances allows buyers to make informed decisions that align with their operational goals and project specifications.
Essential Technical Properties and Trade Terminology for perforated metal panels
What Are the Key Technical Properties of Perforated Metal Panels?
When considering perforated metal panels for your projects, understanding their technical properties is crucial for making informed purchasing decisions. Here are some essential specifications that B2B buyers should be aware of:
-
Material Grade
The material grade of perforated metal panels determines their strength, durability, and suitability for various applications. Common materials include aluminum, carbon steel, stainless steel, and galvanized steel. Each material offers unique benefits; for instance, stainless steel is ideal for corrosive environments, while aluminum is lightweight and resistant to oxidation. -
Hole Size and Pattern
The hole size and pattern directly influence the panel’s aesthetic appeal and functional capabilities. Common patterns include round, square, slotted, and hexagonal holes. The size of the holes affects ventilation, light diffusion, and structural integrity. For example, larger holes provide better airflow but may reduce the panel’s overall strength. -
Gauge (Thickness)
The gauge of the metal panel refers to its thickness, which is crucial for determining load-bearing capacity and resistance to bending or deformation. Thicker gauges are typically more robust and suitable for structural applications, while thinner gauges may be more cost-effective for decorative purposes. -
Open Area Percentage
This specification indicates the ratio of the hole area to the total panel area, expressed as a percentage. A higher open area percentage allows for greater airflow and visibility, making it ideal for applications such as facades and screens. Conversely, a lower percentage may be preferable for privacy or sound insulation. -
Tolerance
Tolerance refers to the allowable deviation from specified dimensions and is vital for ensuring that panels fit properly in their intended applications. Tight tolerances are particularly important in architectural applications where precision is critical for aesthetics and functionality. -
Finish Options
The finish of perforated metal panels can enhance both appearance and performance. Options include powder coating, anodizing, and galvanizing. Each finish provides different benefits, such as corrosion resistance or aesthetic enhancement, which can influence the panel’s lifespan and maintenance requirements.
What Common Trade Terms Should International Buyers Know?
Understanding industry jargon is essential for effective communication and negotiation. Here are some common terms that buyers should familiarize themselves with:
-
OEM (Original Equipment Manufacturer)
This term refers to companies that manufacture products that are then sold under another brand’s name. When sourcing perforated metal panels, knowing whether the supplier is an OEM can help buyers gauge product quality and reliability. -
MOQ (Minimum Order Quantity)
MOQ specifies the smallest quantity of a product that a supplier is willing to sell. This is particularly important for B2B buyers as it impacts inventory costs and project planning. Understanding MOQ can help negotiate better terms and avoid excess inventory. -
RFQ (Request for Quotation)
An RFQ is a formal document sent to suppliers requesting a price quote for specific quantities and specifications. This process is critical for obtaining competitive pricing and ensuring that all potential suppliers are evaluated on the same criteria. -
Incoterms (International Commercial Terms)
Incoterms are a set of predefined commercial terms published by the International Chamber of Commerce that clarify the responsibilities of buyers and sellers in international transactions. Familiarity with these terms helps in understanding shipping costs, insurance, and risk management. -
Lead Time
This term refers to the time taken from placing an order until its delivery. Understanding lead times is crucial for project planning, especially when sourcing materials from international suppliers, as it can impact project timelines. -
Certification Standards
Various certification standards (e.g., ISO, ASTM) ensure that perforated metal panels meet specific quality and safety requirements. Awareness of these certifications can help buyers ensure that their materials comply with local regulations and industry standards.
By understanding these technical properties and trade terms, international B2B buyers from regions such as Africa, South America, the Middle East, and Europe can make informed decisions, ensuring successful procurement of perforated metal panels for their projects.
Navigating Market Dynamics and Sourcing Trends in the perforated metal panels Sector
What Are the Key Market Dynamics and Trends Affecting Perforated Metal Panels?
The global market for perforated metal panels is experiencing significant growth, driven by increasing demand across various sectors such as construction, automotive, and architectural design. Notably, the rise in urbanization, especially in Africa and South America, is fueling the need for innovative building materials that offer both functionality and aesthetic appeal. Additionally, the growing emphasis on energy efficiency and sustainability is encouraging the adoption of perforated metal panels, which facilitate ventilation and natural light, thus reducing reliance on artificial lighting and HVAC systems.
Emerging technologies in manufacturing, such as advanced CNC machining and laser cutting, are enhancing the precision and customization of perforated metal products. This is particularly beneficial for international buyers seeking tailored solutions that meet specific design and functional requirements. Moreover, digital platforms are increasingly being used for sourcing and procurement, allowing buyers in Europe and the Middle East to easily compare products, suppliers, and prices, streamlining the purchasing process.
In terms of market dynamics, fluctuating raw material prices, particularly steel and aluminum, are a concern for buyers. Suppliers must be transparent about pricing structures and offer competitive rates to maintain market share. Additionally, geopolitical factors and trade regulations can impact sourcing strategies, making it crucial for B2B buyers to stay informed about the global supply chain landscape.
How Is Sustainability Influencing Sourcing Decisions for Perforated Metal Panels?
Sustainability is a pivotal consideration for B2B buyers in the perforated metal panel sector. The environmental impact of manufacturing processes and the materials used plays a significant role in sourcing decisions. Buyers are increasingly prioritizing suppliers that demonstrate a commitment to sustainable practices, such as utilizing recycled materials and implementing energy-efficient manufacturing processes.
Ethical sourcing is becoming a competitive differentiator. Buyers are seeking suppliers who can provide transparency in their supply chains, ensuring that the materials used in their perforated panels are sourced responsibly. Certifications such as LEED (Leadership in Energy and Environmental Design) and ISO 14001 (Environmental Management Systems) are becoming essential for suppliers to showcase their environmental credentials.
Additionally, the demand for “green” materials is on the rise. Perforated panels made from aluminum and other recyclable materials not only contribute to reduced environmental footprints but also appeal to a growing segment of environmentally conscious consumers and businesses. By investing in sustainable products, B2B buyers can enhance their brand reputation and align with global sustainability goals.
What Historical Developments Have Shaped the Perforated Metal Panels Market?
The evolution of perforated metal panels can be traced back to their initial use in industrial applications for ventilation and filtration. Over the decades, advancements in manufacturing techniques have transformed perforated metals into versatile design elements, suitable for a wide range of applications, from architectural facades to decorative interiors. The introduction of computer-aided design (CAD) in the late 20th century allowed for unprecedented customization in hole patterns and sizes, making perforated panels a favorite among architects and designers.
In recent years, the market has shifted towards integrating sustainable practices in production, driven by heightened awareness of environmental issues. This evolution has not only expanded the application of perforated metal panels but has also positioned them as key components in modern, eco-friendly designs. As a result, the historical context of perforated metal panels reflects a significant transition from utilitarian function to aesthetic and sustainable value, aligning with contemporary market demands and consumer expectations.
Frequently Asked Questions (FAQs) for B2B Buyers of perforated metal panels
-
How do I choose the right perforated metal panel for my project?
Selecting the right perforated metal panel involves considering the intended application, material type, hole size, pattern, and thickness. For example, aluminum panels are lightweight and corrosion-resistant, making them ideal for architectural applications. If sound attenuation is a priority, consider panels with smaller holes and higher open area percentages. It’s also important to consult with suppliers about customization options that align with your project’s specific requirements. -
What are the common applications of perforated metal panels in various industries?
Perforated metal panels are widely used across industries for applications such as architectural facades, ventilation screens, security barriers, and decorative elements. In the construction sector, they provide aesthetic appeal and functionality. In manufacturing, they serve as filters for sound, light, and airflow. Understanding your industry’s specific needs can guide you in selecting the appropriate panel type. -
What customization options are available for perforated metal panels?
Customization options for perforated metal panels can include variations in hole size, spacing, and shape, as well as different materials like stainless steel, aluminum, or carbon steel. Some manufacturers also offer finishing options such as powder coating or anodizing to enhance aesthetics and durability. Discussing your specific design needs with suppliers can help ensure the final product meets your project specifications. -
What is the minimum order quantity (MOQ) for perforated metal panels?
Minimum order quantities (MOQ) can vary significantly depending on the supplier and the specific product. Some manufacturers may have an MOQ of as low as 10 panels, while others might require orders of several hundred or more. Always confirm the MOQ with potential suppliers early in the procurement process to avoid any surprises and to ensure that your order aligns with their production capabilities. -
How do I vet suppliers for perforated metal panels in international markets?
Vetting suppliers involves assessing their reputation, quality of products, and compliance with international standards. Look for suppliers with certifications like ISO or those that are members of recognized industry associations. Request references from previous clients and review their product samples. Additionally, consider visiting their facilities if possible or using third-party verification services to ensure reliability. -
What are the typical payment terms for international purchases of perforated metal panels?
Payment terms can vary widely between suppliers but often include options such as upfront payment, partial payment upon order confirmation, and the balance upon delivery. Letter of credit (LC) is another common method for securing transactions in international trade. Always negotiate payment terms that protect your interests, and ensure they align with your cash flow management strategies. -
What quality assurance (QA) measures should I expect from suppliers?
Reputable suppliers should have established quality assurance measures to ensure that their products meet specified standards. This can include material testing, dimensional checks, and visual inspections. Ask potential suppliers about their QA processes, certifications, and whether they provide inspection reports or guarantees for their perforated metal panels. -
How should I manage logistics when sourcing perforated metal panels internationally?
Managing logistics involves coordinating shipping, customs clearance, and delivery timelines. Work with suppliers who have experience in international shipping to ensure compliance with local regulations. It’s crucial to choose reliable freight forwarders and consider insurance options for your shipment. Additionally, maintaining clear communication with your supplier about shipping schedules can help mitigate delays and unexpected costs.
Important Disclaimer & Terms of Use
⚠️ Important Disclaimer
The information provided in this guide, including content regarding manufacturers, technical specifications, and market analysis, is for informational and educational purposes only. It does not constitute professional procurement advice, financial advice, or legal advice.
While we have made every effort to ensure the accuracy and timeliness of the information, we are not responsible for any errors, omissions, or outdated information. Market conditions, company details, and technical standards are subject to change.
B2B buyers must conduct their own independent and thorough due diligence before making any purchasing decisions. This includes contacting suppliers directly, verifying certifications, requesting samples, and seeking professional consultation. The risk of relying on any information in this guide is borne solely by the reader.
Strategic Sourcing Conclusion and Outlook for perforated metal panels
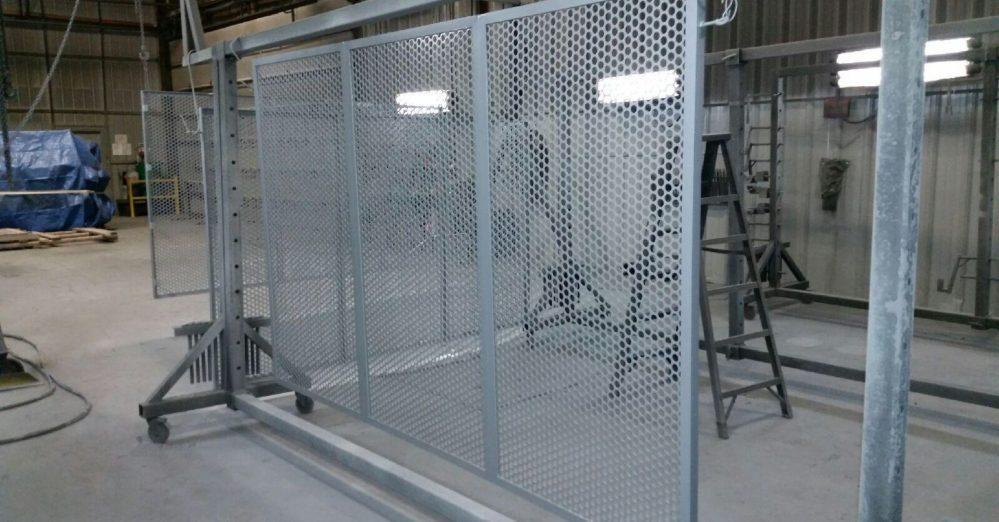
A stock image related to perforated metal panels.
As the global demand for perforated metal panels continues to rise, strategic sourcing becomes paramount for international B2B buyers. In regions such as Africa, South America, the Middle East, and Europe, understanding the diverse applications of perforated metals—from architectural designs to filtration systems—can enhance procurement strategies. Buyers should prioritize suppliers that offer a wide range of materials, including aluminum, stainless steel, and carbon steel, to ensure they meet specific project requirements while optimizing cost efficiency.
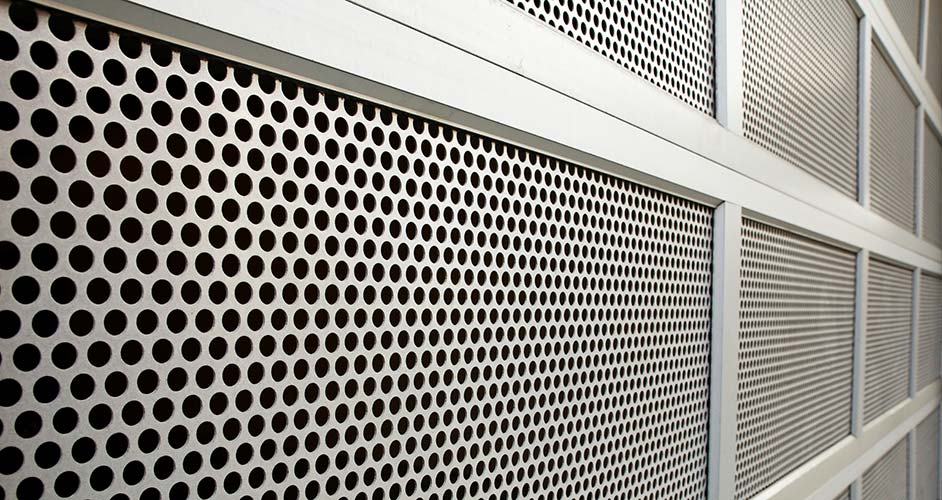
A stock image related to perforated metal panels.
Investing in high-quality perforated metal not only improves aesthetic appeal but also enhances functionality, providing ventilation and sound filtration in various settings. Additionally, establishing long-term relationships with reputable manufacturers can lead to better pricing, reliable supply chains, and innovative solutions tailored to unique needs.
Looking ahead, B2B buyers should stay informed about advancements in perforation technology and sustainable practices within the industry. By proactively seeking partnerships and embracing new developments, businesses can position themselves competitively in the market. The future of perforated metal panels is bright, and those who leverage strategic sourcing will undoubtedly benefit from enhanced project outcomes and increased market presence.