The Ultimate Guide to Shell And Heat Exchanger (2025)
Introduction: Navigating the Global Market for shell and heat exchanger
Navigating the complexities of sourcing shell and heat exchangers can be a daunting task for international B2B buyers, particularly those from regions like Africa, South America, the Middle East, and Europe. With varying industry standards and supplier capabilities, finding the right heat exchanger that meets specific operational requirements while balancing cost-effectiveness is crucial. This guide addresses key challenges in the global market, providing comprehensive insights into the different types of shell and heat exchangers, their applications across diverse industries, and essential factors to consider during supplier vetting.
In this guide, you will discover the various classifications of shell and tube heat exchangers, including fixed tubesheet, U-tube, and floating head designs, each tailored for unique applications and operating conditions. We delve into critical considerations such as thermal performance, material selection, and maintenance requirements, enabling buyers to make informed decisions based on their specific needs. Additionally, we offer actionable insights on evaluating suppliers, understanding pricing structures, and navigating regulatory standards, ensuring a smooth procurement process.
By leveraging the knowledge contained in this guide, B2B buyers will be empowered to identify reliable suppliers, optimize their procurement strategies, and ultimately enhance their operational efficiency through the effective use of shell and heat exchangers. This resource aims to facilitate better purchasing decisions and contribute to the growth and sustainability of your business in a competitive global landscape.
Understanding shell and heat exchanger Types and Variations
Type Name | Key Distinguishing Features | Primary B2B Applications | Brief Pros & Cons for Buyers |
---|---|---|---|
Fixed Tubesheet Exchanger | Welded tubesheet for simple construction; limited cleaning access | Petrochemical, power plants | Pros: Economical; easy to manufacture. Cons: Difficult to clean; limited thermal expansion handling. |
U-Tube Exchanger | Flexible tube arrangement; allows for thermal expansion | Oil refining, chemical processing | Pros: Easy maintenance; good for clean fluids. Cons: Difficult internal cleaning; larger footprint. |
Floating Head Exchanger | Allows for thermal expansion; removable tube bundle | HVAC systems, refrigeration | Pros: Versatile; easier to clean. Cons: More complex design; potentially higher costs. |
Plate Heat Exchanger | Compact design with thin plates; high efficiency | Food processing, pharmaceuticals | Pros: Space-saving; excellent heat transfer. Cons: Limited pressure handling; may require frequent cleaning. |
Air-Cooled Heat Exchanger | Uses air to cool fluids; no water required | Power generation, HVAC | Pros: Water conservation; lower operational costs. Cons: Dependent on ambient conditions; larger size needed for efficiency. |
What Are the Characteristics of Fixed Tubesheet Exchangers?
Fixed tubesheet exchangers feature a design where the tubesheet is welded to the shell, making them a straightforward and economical choice for many industrial applications. These exchangers are primarily utilized in the petrochemical and power generation sectors due to their ability to handle high pressures and temperatures. Buyers should consider that while they are easy to manufacture, the cleaning process is limited to chemical methods, which can be a drawback in applications where fouling is a concern.
How Do U-Tube Exchangers Offer Flexibility?
U-tube exchangers are designed with tubes that are bent into a U-shape, allowing for thermal expansion without imposing stress on the materials. This flexibility makes them suitable for oil refining and chemical processing where variations in temperature and pressure are common. While they are advantageous for maintenance and cleaning, particularly for clean fluids, buyers must be aware that internal cleaning can be challenging, which may necessitate additional downtime and cost.
What Makes Floating Head Exchangers a Popular Choice?
Floating head exchangers are characterized by a design that permits the tubesheet at one end to float, accommodating thermal expansion. This feature makes them highly versatile for HVAC systems and refrigeration applications. The ability to remove the tube bundle for cleaning significantly enhances their maintenance profile. However, the complexity of the design may lead to higher initial costs, so buyers should weigh these factors against the long-term operational benefits.
Why Choose Plate Heat Exchangers for Compact Applications?
Plate heat exchangers utilize a series of thin plates to facilitate heat transfer, making them ideal for industries such as food processing and pharmaceuticals where space is at a premium. Their compact design allows for high thermal efficiency, but they may not handle high pressures as effectively as shell and tube designs. Buyers should consider the frequency of cleaning required, as fouling can impact efficiency and necessitate more maintenance.
What Are the Benefits of Air-Cooled Heat Exchangers?
Air-cooled heat exchangers operate by using air to cool fluids, eliminating the need for water, which can be particularly advantageous in regions with limited water resources. They are commonly used in power generation and HVAC applications. While they contribute to lower operational costs and are environmentally friendly, their efficiency can be affected by ambient conditions, and they may require a larger physical footprint compared to water-cooled systems. Buyers should evaluate these trade-offs in the context of their specific needs.
Key Industrial Applications of shell and heat exchanger
Industry/Sector | Specific Application of Shell and Heat Exchanger | Value/Benefit for the Business | Key Sourcing Considerations for this Application |
---|---|---|---|
Petrochemical Industry | Heat exchange in crude oil processing | Efficient thermal management enhances yield and reduces costs | Compliance with TEMA standards, material compatibility, and durability |
Power Generation | Feedwater heating in steam power plants | Increases efficiency of power generation, reducing fuel costs | Pressure ratings, thermal performance, and maintenance requirements |
HVAC Systems | Cooling and heating in commercial buildings | Optimizes energy consumption and enhances comfort levels | Size, energy efficiency ratings, and installation requirements |
Food and Beverage Processing | Pasteurization and cooling processes | Ensures product safety and quality while minimizing energy use | Food-grade materials, cleaning ease, and regulatory compliance |
Chemical Manufacturing | Heat recovery in chemical reactions | Improves process efficiency and reduces waste heat emissions | Custom designs for specific chemical processes and safety standards |
How is Shell and Heat Exchanger Used in the Petrochemical Industry?
In the petrochemical industry, shell and tube heat exchangers are vital for crude oil processing, facilitating heat exchange between various fluids involved in refining. These exchangers enhance thermal management, allowing for effective heat recovery and minimizing energy consumption. Buyers in this sector should prioritize compliance with TEMA standards, ensuring the materials used can withstand corrosive environments and high pressures. Additionally, durability is crucial to prevent unexpected downtime and maintenance costs.
What Role Do Shell and Heat Exchangers Play in Power Generation?
Shell and tube heat exchangers are extensively used in steam power plants for feedwater heating, which is essential for improving overall plant efficiency. By pre-heating the water before it enters the boiler, these exchangers help reduce fuel consumption and operational costs. International buyers must consider pressure ratings and thermal performance when sourcing these systems, as they directly impact the efficiency and reliability of power generation processes.
How Are Shell and Heat Exchangers Utilized in HVAC Systems?
In HVAC systems, shell and tube heat exchangers are employed for both heating and cooling applications in commercial buildings. They optimize energy consumption by efficiently transferring heat between different fluids, contributing to enhanced comfort and reduced operational costs. Buyers should focus on the size and energy efficiency ratings of these exchangers to ensure they meet the specific requirements of their facilities while also considering installation logistics.
In What Ways Are Shell and Heat Exchangers Important in Food and Beverage Processing?
In the food and beverage industry, shell and tube heat exchangers are crucial for processes such as pasteurization and cooling. They ensure product safety by effectively managing heat transfer, which is essential for killing harmful bacteria while maintaining product quality. Buyers must source heat exchangers made from food-grade materials and consider ease of cleaning and regulatory compliance to meet industry standards.
How Do Shell and Heat Exchangers Contribute to Chemical Manufacturing?
In chemical manufacturing, shell and tube heat exchangers facilitate heat recovery during various chemical reactions, improving process efficiency and reducing waste heat emissions. This not only enhances productivity but also aligns with sustainability goals by minimizing energy waste. Buyers should look for custom designs tailored to specific chemical processes, ensuring that safety standards are met to prevent hazardous incidents.
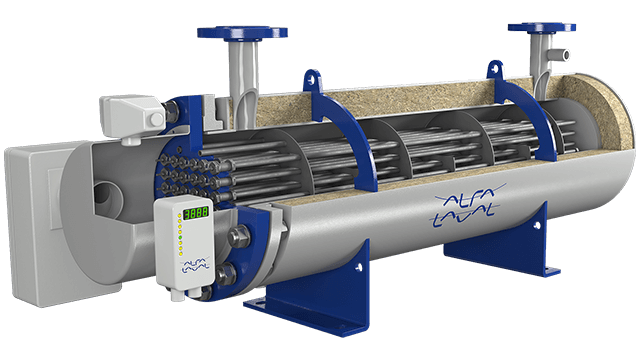
A stock image related to shell and heat exchanger.
3 Common User Pain Points for ‘shell and heat exchanger’ & Their Solutions
Scenario 1: Inefficient Heat Transfer Leading to Increased Operational Costs
The Problem: Many B2B buyers struggle with heat exchangers that do not perform efficiently due to fouling, inadequate design, or the wrong choice of materials. This inefficiency can lead to increased energy consumption and operational costs, particularly in industries such as petrochemicals and power generation. For instance, a company in Saudi Arabia may find that its shell and tube heat exchangers are unable to maintain optimal temperature differentials, leading to higher energy bills and reduced productivity.
The Solution: To address this issue, buyers should conduct a thorough performance assessment of their existing heat exchangers. This includes evaluating flow rates, temperatures, and the specific heat transfer coefficients of the fluids involved. Investing in enhanced surface tubes can significantly improve thermal performance, as these designs increase the surface area available for heat transfer without requiring larger units. Additionally, regular maintenance schedules should be established, incorporating chemical cleaning techniques to remove fouling deposits. By sourcing heat exchangers that comply with TEMA standards, buyers can ensure they are selecting robust designs optimized for their specific application, ultimately lowering operational costs.
Scenario 2: Frequent Downtime Due to Maintenance Challenges
The Problem: Frequent maintenance and unexpected downtime are common pain points for B2B buyers utilizing shell and tube heat exchangers. For example, a manufacturing plant in Brazil might face disruptions due to the need for regular inspections and repairs, particularly if the current equipment lacks accessibility for cleaning or replacement of parts. This can lead to lost revenue and decreased customer satisfaction due to delayed production timelines.
The Solution: Buyers should prioritize designs that offer easy access for maintenance. Floating head exchangers, for instance, allow for simple removal of the tube bundle for cleaning and inspection, reducing downtime significantly. When sourcing new units, it is essential to inquire about the ease of maintenance and whether the design allows for quick access to critical components. Furthermore, implementing a predictive maintenance program using sensors to monitor performance can preemptively identify issues before they necessitate significant downtime. This proactive approach not only extends the lifespan of the heat exchangers but also enhances overall operational efficiency.
Scenario 3: Compliance with International Standards and Local Regulations
The Problem: Navigating the compliance landscape for shell and tube heat exchangers can be daunting for international B2B buyers, especially those in regions with stringent safety and environmental regulations, such as Europe and the Middle East. A company in the UAE may find itself facing penalties or operational halts due to non-compliance with local standards, which can stem from using outdated technology or improper installation.
The Solution: To mitigate compliance-related challenges, buyers must stay informed about both international standards (like ASME, TEMA) and local regulations. Partnering with suppliers who have a strong track record in regulatory compliance is crucial. When selecting shell and tube heat exchangers, buyers should verify that the products are certified and meet the relevant standards for their industry. Moreover, engaging in thorough training for installation and operational staff can ensure that the equipment is used according to prescribed guidelines, thereby reducing the risk of compliance issues. Collaborating with engineering consultants who specialize in heat transfer technologies can also provide insights into best practices that align with regulatory requirements, ensuring smooth operations and peace of mind.
Strategic Material Selection Guide for shell and heat exchanger
What Are the Key Properties of Common Materials Used in Shell and Heat Exchangers?
When selecting materials for shell and heat exchangers, it’s crucial to consider their properties that directly impact performance, including temperature and pressure ratings, corrosion resistance, and thermal conductivity. Below are analyses of four common materials used in the construction of shell and tube heat exchangers.
How Does Carbon Steel Perform in Shell and Heat Exchangers?
Key Properties: Carbon steel is known for its high strength and excellent thermal conductivity. It can withstand high temperatures and pressures, making it suitable for various applications.
Pros & Cons: Carbon steel is relatively low-cost and widely available, which makes it a popular choice. However, it has limited corrosion resistance, which can lead to premature failure in corrosive environments. Its manufacturing processes are straightforward, but it may require additional coatings or treatments for specific applications.
Impact on Application: Carbon steel is best used in applications involving clean water or oil. Its susceptibility to rust and corrosion means it is not ideal for applications involving acidic or saline environments.
Considerations for International Buyers: Buyers in regions with high humidity or corrosive environments, such as coastal areas in Africa or South America, should consider the need for protective coatings. Compliance with ASTM standards is essential for ensuring quality and safety.
What Are the Advantages of Stainless Steel in Heat Exchangers?
Key Properties: Stainless steel offers excellent corrosion resistance and can handle high temperatures and pressures. It is also known for its durability and strength.
Pros & Cons: The primary advantage of stainless steel is its resistance to corrosion, making it suitable for a wide range of fluids, including those that are acidic or saline. However, it comes at a higher cost compared to carbon steel and can be more complex to manufacture due to its toughness.
Impact on Application: Stainless steel is ideal for applications in the food and beverage industry, petrochemical processing, and pharmaceuticals, where cleanliness and corrosion resistance are paramount.
Considerations for International Buyers: Buyers should ensure compliance with international standards such as DIN and JIS. The higher initial investment may be justified by the long-term savings on maintenance and replacement.
How Do Copper and Copper Alloys Enhance Heat Transfer?
Key Properties: Copper has excellent thermal conductivity, making it highly effective for heat transfer applications. It also offers good corrosion resistance, particularly in water-based applications.
Pros & Cons: The main advantage of copper is its superior heat transfer efficiency, which can lead to reduced energy costs. However, it is more expensive than carbon steel and can be prone to corrosion in certain environments, such as those containing ammonia or chlorides.
Impact on Application: Copper is commonly used in applications requiring high thermal efficiency, such as HVAC systems and refrigeration. Its compatibility with various fluids makes it versatile, but care must be taken to avoid corrosive environments.
Considerations for International Buyers: Buyers should be aware of the specific environmental conditions in their region. Compliance with relevant standards is crucial, and the higher cost may be offset by energy savings over time.
What Role Does Alloy Steel Play in High-Pressure Applications?
Key Properties: Alloy steel is designed to withstand high pressures and temperatures, making it suitable for demanding applications. It combines elements like chromium and molybdenum to enhance its properties.
Pros & Cons: The key advantage of alloy steel is its strength and toughness, which make it ideal for high-pressure applications. However, it is more expensive than carbon steel and may require specialized fabrication techniques.
Impact on Application: Alloy steel is commonly used in the oil and gas industry, where high-pressure and high-temperature conditions are prevalent. Its durability ensures a longer lifespan in challenging environments.
Considerations for International Buyers: Buyers must ensure that alloy steel components meet specific industry standards, such as ASTM A335 for high-temperature service. The investment in alloy steel can yield significant long-term benefits in terms of reliability and safety.
Summary Table of Material Selection for Shell and Heat Exchangers
Material | Typical Use Case for Shell and Heat Exchanger | Key Advantage | Key Disadvantage/Limitation | Relative Cost (Low/Med/High) |
---|---|---|---|---|
Carbon Steel | Water and oil applications | Low cost and high strength | Limited corrosion resistance | Low |
Stainless Steel | Food processing, petrochemical applications | Excellent corrosion resistance | Higher cost and manufacturing complexity | High |
Copper | HVAC and refrigeration systems | Superior thermal conductivity | Higher cost and corrosion in certain environments | Med |
Alloy Steel | Oil and gas industry | High strength for high-pressure use | More expensive and complex fabrication | High |
This strategic material selection guide provides valuable insights for international B2B buyers looking to optimize their shell and heat exchanger applications, ensuring compliance with regional standards and enhancing operational efficiency.
In-depth Look: Manufacturing Processes and Quality Assurance for shell and heat exchanger
What Are the Key Stages in Manufacturing Shell and Tube Heat Exchangers?
Manufacturing shell and tube heat exchangers involves several critical stages, each ensuring the efficiency and reliability of the final product. Here’s a breakdown of these stages:
Material Preparation: What Materials Are Used in Heat Exchanger Manufacturing?
The choice of materials is fundamental to the performance of shell and tube heat exchangers. Common materials include carbon steel, stainless steel, and special alloys, depending on the application and operating conditions. The materials must be resistant to corrosion, pressure, and temperature fluctuations.
Before manufacturing begins, raw materials undergo rigorous inspection to ensure they meet specified standards. This includes checking for chemical composition and mechanical properties. Quality assurance at this stage is crucial, as subpar materials can lead to failures and safety hazards later on.
Forming: How Are Components Shaped for Heat Exchangers?
The forming process involves several techniques to shape the components of the heat exchanger. Key methods include:
- Rolling: Used to form the shell and tube sheets, ensuring precise dimensions and structural integrity.
- Bending: Applied to create the necessary curvature in the tubes, especially in U-tube designs, which allow for thermal expansion.
- Welding: Essential for joining components, especially in fixed tubesheet exchangers. Advanced welding techniques, such as TIG (Tungsten Inert Gas) welding, are often employed to achieve strong, leak-proof joints.
Each of these techniques requires skilled operators and advanced machinery to maintain consistency and quality.
Assembly: What Are the Steps in Assembling Shell and Tube Heat Exchangers?
The assembly of shell and tube heat exchangers is a meticulous process, typically involving:
- Tube Bundle Installation: The tube bundle is inserted into the shell, ensuring proper alignment and spacing.
- Header Attachment: The front and rear headers are installed, which facilitate the entry and exit of fluids.
- Baffle Installation: Baffles are strategically placed to direct fluid flow and enhance heat transfer efficiency.
Throughout the assembly process, it’s vital to maintain cleanliness to prevent contamination that could affect performance.
Finishing: What Quality Checks Are Conducted During the Finishing Process?
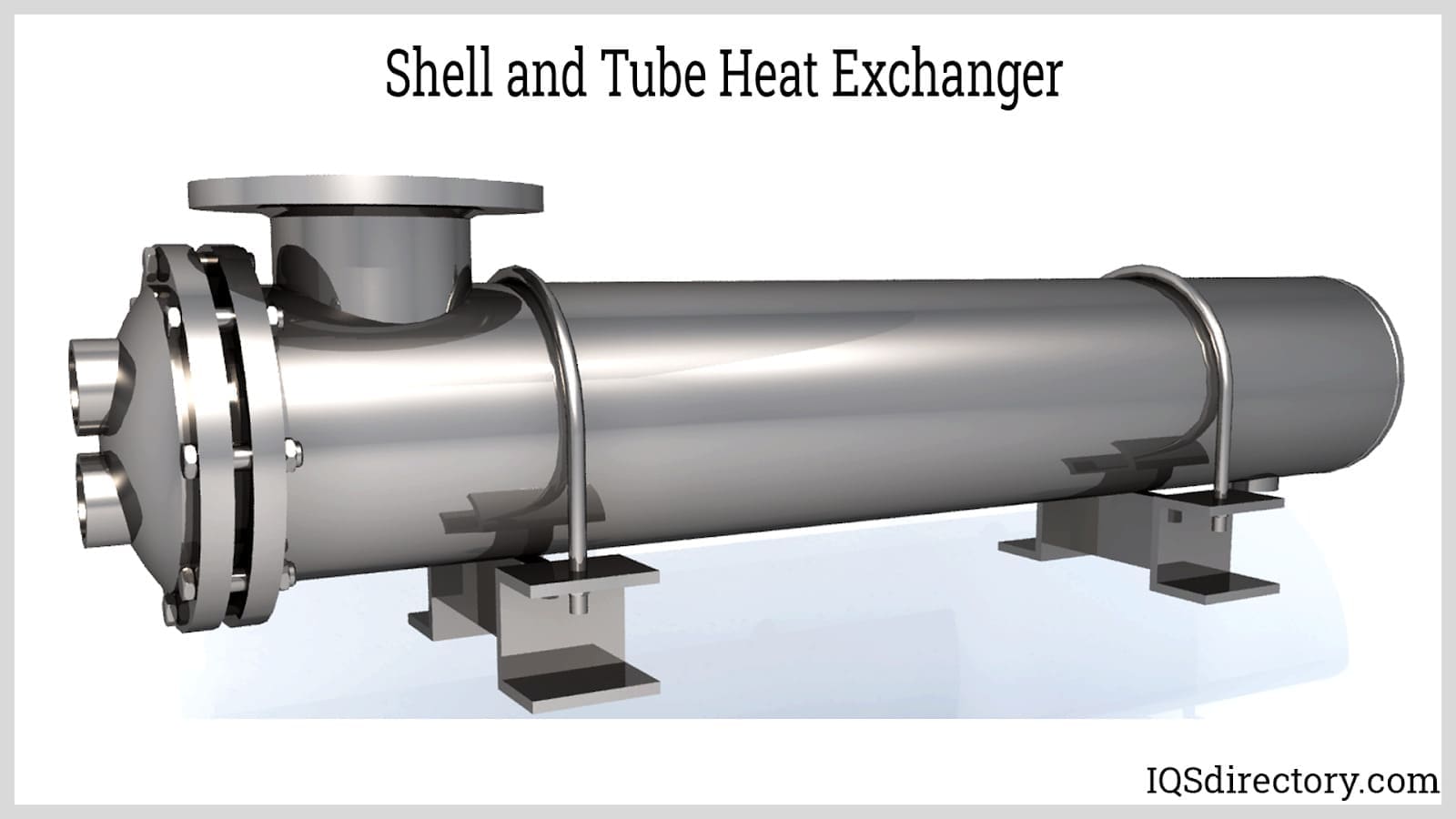
A stock image related to shell and heat exchanger.
The finishing stage often includes surface treatments, such as passivation for stainless steel components, to enhance corrosion resistance. Additionally, thorough inspections are conducted to ensure that all components fit together correctly and that there are no defects.
What International Quality Standards Apply to Heat Exchanger Manufacturing?
Quality assurance in manufacturing shell and tube heat exchangers is governed by various international standards. Key certifications include:
- ISO 9001: This standard ensures that manufacturers have a quality management system in place, focusing on customer satisfaction and continuous improvement.
- CE Marking: Required for products sold in the European Economic Area, indicating compliance with health, safety, and environmental protection standards.
- API Standards: Particularly relevant in the oil and gas industry, these standards ensure that equipment meets strict safety and performance criteria.
These certifications not only enhance product credibility but also help B2B buyers assess potential suppliers.
What Are the Quality Control Checkpoints in Heat Exchanger Manufacturing?
Quality control (QC) is an integral part of the manufacturing process, encompassing several checkpoints:
- Incoming Quality Control (IQC): At this stage, raw materials and components are inspected upon arrival. This includes checking specifications against orders and conducting material tests.
- In-Process Quality Control (IPQC): During the manufacturing process, operators conduct regular inspections to ensure adherence to specifications and identify defects early.
- Final Quality Control (FQC): Once the heat exchanger is assembled, a comprehensive inspection is performed, often including non-destructive testing (NDT) methods like ultrasonic testing or radiography to detect any hidden flaws.
How Can B2B Buyers Verify Supplier Quality Control Processes?
For international B2B buyers, especially those from Africa, South America, the Middle East, and Europe, verifying a supplier’s quality control processes is essential. Here are actionable steps:
- Request Documentation: Ask for detailed quality assurance plans, including inspection and testing reports, to understand their QC processes.
- Conduct Audits: If possible, perform on-site audits to assess the manufacturing facility’s practices firsthand. This can reveal the supplier’s commitment to quality.
- Third-Party Inspections: Consider hiring third-party inspection services to evaluate the heat exchangers before shipment. This adds an extra layer of assurance regarding the product’s quality.
What Testing Methods Are Commonly Used for Shell and Tube Heat Exchangers?
Testing methods play a crucial role in ensuring the reliability of shell and tube heat exchangers. Common testing methods include:
- Hydrostatic Testing: This involves filling the heat exchanger with water and pressurizing it to check for leaks. It is a critical test for ensuring the integrity of welded joints.
- Leak Testing: Using methods such as air or helium leak testing, manufacturers can identify any potential leaks that could compromise performance.
- Performance Testing: This assesses the heat exchanger’s ability to transfer heat effectively under specified conditions, ensuring it meets operational requirements.
What Quality Control Nuances Should International B2B Buyers Be Aware Of?
For international buyers, understanding regional compliance and quality control nuances is crucial. Different regions may have specific regulations and standards that must be adhered to. For instance:
- Cultural Differences: Buyers should be aware of varying practices in quality assurance across different countries. In some regions, informal checks may be more common than formal processes.
- Language Barriers: Technical documentation may be available only in local languages, making it essential for buyers to have reliable translators or local representatives.
- Regulatory Changes: Regulations can change frequently, especially in sectors like oil and gas. Buyers should stay informed about the latest standards in the regions where they operate.
By understanding these factors, B2B buyers can make more informed decisions when selecting suppliers for shell and tube heat exchangers, ensuring they receive high-quality products that meet their operational needs.
Practical Sourcing Guide: A Step-by-Step Checklist for ‘shell and heat exchanger’
Introduction
Navigating the procurement of shell and heat exchangers can be complex, especially for international B2B buyers from diverse regions such as Africa, South America, the Middle East, and Europe. This practical sourcing guide provides a systematic checklist to ensure you make informed purchasing decisions tailored to your specific industrial needs.
Step 1: Define Your Technical Specifications
Establishing precise technical specifications is essential for sourcing the right shell and heat exchanger. Consider factors such as the type of fluids involved, operating temperatures, and pressure requirements. This ensures compatibility with your existing systems and helps avoid costly modifications later.
- Fluid Types: Identify whether you will be working with single-phase or two-phase fluids, as this impacts the design and efficiency.
- Material Requirements: Specify materials that can withstand the corrosive nature of the fluids you are dealing with, such as stainless steel or carbon steel.
Step 2: Understand Industry Standards and Regulations
Familiarize yourself with relevant industry standards and regulations that govern heat exchangers in your region. This is crucial to ensure compliance and safety in your operations.
- TEMA Standards: For shell and tube exchangers, refer to the Tubular Exchanger Manufacturers Association (TEMA) standards for design and performance.
- Local Regulations: Investigate local compliance requirements that may affect installation, maintenance, or operational safety.
Step 3: Evaluate Potential Suppliers
Before committing to a supplier, it is vital to conduct thorough evaluations. Request detailed company profiles, including case studies and references from clients in your industry.
- Supplier Experience: Look for suppliers with a proven track record in your specific sector, whether it be petrochemical, power generation, or HVAC.
- Technical Support: Assess the level of technical support they provide post-purchase, which is crucial for troubleshooting and maintenance.
Step 4: Request Detailed Quotations
Obtain detailed quotations from shortlisted suppliers to compare pricing and specifications. A well-structured quotation should outline all costs, including shipping, installation, and any after-sales support.
- Breakdown of Costs: Ensure the quotation includes a breakdown of costs associated with materials, labor, and delivery timelines.
- Warranty Information: Clarify warranty terms and conditions to understand the supplier’s commitment to quality.
Step 5: Inspect Quality Certifications
Verifying the quality certifications of potential suppliers is key to ensuring that the heat exchangers meet industry standards. Look for ISO certifications or other relevant quality management system certifications.
- Production Quality: Suppliers should adhere to strict quality control processes during manufacturing.
- Testing Procedures: Inquire about the testing procedures they utilize to ensure the performance and reliability of their products.
Step 6: Negotiate Terms of Purchase
Once you have selected a supplier, negotiate the terms of purchase, focusing on payment options, delivery timelines, and installation services. Clear agreements on these aspects can prevent misunderstandings later.
- Payment Terms: Discuss flexible payment options that may be available, especially for large orders.
- Delivery Schedule: Confirm a realistic delivery schedule that aligns with your project timelines to avoid delays.
Step 7: Plan for Installation and Maintenance
Finally, ensure you have a plan for the installation and ongoing maintenance of the shell and heat exchanger. This includes training for your staff and establishing a routine maintenance schedule.
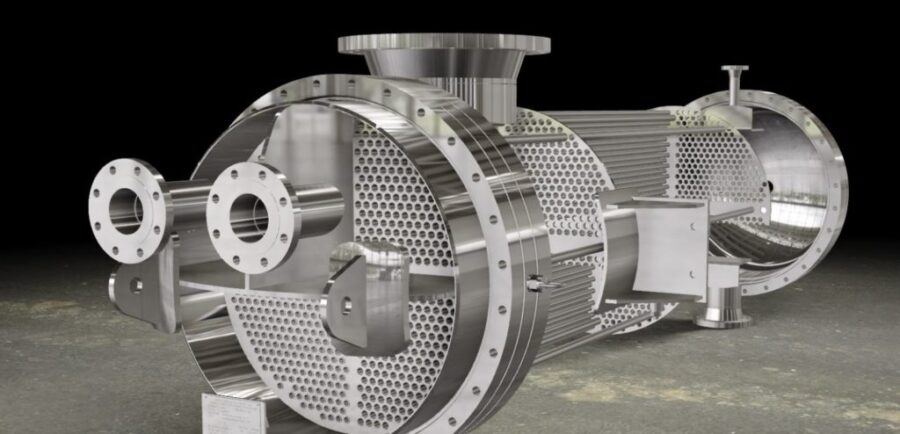
A stock image related to shell and heat exchanger.
- Staff Training: Verify if the supplier provides training for your personnel to ensure safe and efficient operation.
- Maintenance Plans: Discuss potential maintenance contracts to keep the equipment running optimally and extend its lifespan.
By following this checklist, B2B buyers can streamline the procurement process for shell and heat exchangers, ensuring they select the right equipment for their operational needs while minimizing risks associated with poor sourcing decisions.
Comprehensive Cost and Pricing Analysis for shell and heat exchanger Sourcing
What are the Key Cost Components for Shell and Heat Exchanger Sourcing?
When sourcing shell and heat exchangers, understanding the comprehensive cost structure is crucial for B2B buyers, particularly in regions like Africa, South America, the Middle East, and Europe. The primary cost components include:
-
Materials: The choice of materials significantly affects pricing. Common materials include stainless steel, carbon steel, and copper, with stainless steel typically commanding a premium due to its corrosion resistance and durability.
-
Labor: Labor costs vary by region and can be influenced by local wage standards. Skilled labor is essential for assembly and quality control, particularly for custom designs.
-
Manufacturing Overhead: This encompasses costs associated with running the manufacturing facility, including utilities, equipment depreciation, and indirect labor.
-
Tooling: Specialized tooling may be required for custom designs or specific manufacturing processes, impacting overall costs.
-
Quality Control (QC): Implementing rigorous QC processes ensures compliance with international standards, which may increase initial costs but reduce long-term risks.
-
Logistics: Transportation and shipping costs can vary widely based on distance, shipping methods, and Incoterms. Buyers should factor in these costs when assessing total pricing.
-
Margin: Suppliers typically add a markup to cover their costs and profit, which can vary based on market conditions and competition.
How Do Price Influencers Affect Shell and Heat Exchanger Costs?
Several factors influence the pricing of shell and heat exchangers:
-
Volume and Minimum Order Quantity (MOQ): Higher order volumes often lead to reduced per-unit costs. Buyers should negotiate MOQs that align with their production needs.
-
Specifications and Customization: Custom designs or specific performance requirements can increase costs. Buyers should weigh the need for customization against the potential price increase.
-
Material Choices: The selection of materials not only affects the initial purchase price but also the long-term maintenance costs. For instance, while copper may be cheaper initially, its susceptibility to corrosion can lead to higher maintenance costs.
-
Quality and Certifications: Equipment that meets international quality certifications (like ISO) may come at a higher price but ensures reliability and compliance with safety standards.
-
Supplier Factors: Reputation and reliability of suppliers can influence pricing. Established suppliers may offer better warranties and customer support, justifying a higher cost.
-
Incoterms: Understanding Incoterms is essential for clarifying responsibilities for shipping, insurance, and tariffs, which can significantly affect total costs.
What Buyer Tips Can Enhance Cost-Efficiency in Sourcing?
International B2B buyers can implement several strategies to enhance cost-efficiency when sourcing shell and heat exchangers:
-
Negotiation: Engage in thorough negotiations with suppliers. Highlighting potential for larger orders or long-term partnerships can yield discounts.
-
Total Cost of Ownership (TCO): Consider the TCO, which includes purchase price, installation, maintenance, and potential downtime. A lower upfront cost may not always equate to savings in the long run.
-
Understanding Pricing Nuances: Be aware of regional pricing variations. For instance, suppliers in Europe may have different pricing structures compared to those in Africa or South America due to labor and material costs.
-
Leverage Local Partnerships: Building relationships with local distributors or agents can provide insights into regional pricing trends and help negotiate better terms.
-
Evaluate Supplier Reliability: Focus not only on price but also on supplier reliability, delivery times, and after-sales support. A slightly higher price may be justified by enhanced service quality.
Disclaimer on Indicative Prices
The prices for shell and heat exchangers can fluctuate based on numerous factors, including market conditions and raw material costs. It is advisable for buyers to conduct thorough market research and obtain multiple quotes to ensure they are making informed purchasing decisions.
Alternatives Analysis: Comparing shell and heat exchanger With Other Solutions
When considering heat transfer solutions, it’s essential to evaluate the various technologies available in the market. Shell and tube heat exchangers are widely used due to their versatility and efficiency. However, several alternative solutions exist that may better suit specific applications or operational needs. This analysis will compare shell and tube heat exchangers with plate heat exchangers and air-cooled chillers, highlighting key aspects that B2B buyers should consider.
Comparison Table of Heat Transfer Solutions
Comparison Aspect | Shell and Tube Heat Exchanger | Plate Heat Exchanger | Air-Cooled Chiller |
---|---|---|---|
Performance | High efficiency, suitable for high pressure and temperature applications | Excellent thermal efficiency, compact design | Good for large cooling loads, efficient in hot climates |
Cost | Moderate initial investment, but lower operational costs | Lower initial cost, potential for higher maintenance costs | Higher initial investment, but operational costs can vary |
Ease of Implementation | Requires more space and specialized installation | Easier to install in tight spaces | Requires sufficient space for airflow and installation |
Maintenance | Regular maintenance needed, but easier access for cleaning | Requires frequent inspection, potential for fouling | Minimal maintenance, but needs regular checks on fans and refrigerants |
Best Use Case | Petrochemical and power industries | Food processing, HVAC applications | Industrial cooling, large buildings, and process cooling |
In-Depth Analysis of Alternatives
What are the benefits and drawbacks of Plate Heat Exchangers?
Plate heat exchangers (PHEs) offer a compact design that can achieve high thermal efficiency due to their large surface area relative to volume. They are particularly advantageous in applications where space is at a premium, such as in food processing and HVAC systems. However, they can require more frequent maintenance due to fouling, especially if the fluids have particulate matter. Additionally, while they are generally less expensive upfront, the costs can escalate if frequent cleaning or repairs are needed.
How do Air-Cooled Chillers compare to Shell and Tube Heat Exchangers?
Air-cooled chillers are ideal for large cooling applications, particularly in hot climates where they can efficiently reject heat to the atmosphere. They offer the benefit of reduced water usage compared to water-cooled systems, making them suitable for areas with water scarcity. However, their initial investment is typically higher, and operational costs can vary depending on ambient temperatures and system load. Unlike shell and tube heat exchangers, air-cooled chillers may require more space for proper airflow, and their efficiency can decrease as outdoor temperatures rise.
Conclusion: How can B2B buyers choose the right heat transfer solution?
Choosing the right heat transfer solution depends on various factors including application requirements, budget constraints, and maintenance capabilities. For high-pressure and temperature applications, shell and tube heat exchangers may be the best fit, especially in industries like petrochemicals. Conversely, for applications requiring compact designs or frequent thermal cycling, plate heat exchangers could be more suitable. Finally, air-cooled chillers are an excellent choice for large-scale cooling needs, particularly in regions where water is scarce. B2B buyers should assess their unique operational needs, infrastructure, and long-term goals to make an informed decision that aligns with their business objectives.
Essential Technical Properties and Trade Terminology for shell and heat exchanger
What Are the Key Technical Properties of Shell and Heat Exchangers?
When selecting a shell and tube heat exchanger for industrial applications, understanding its technical specifications is crucial for ensuring optimal performance and longevity. Here are several critical specifications to consider:
1. Material Grade
The material grade of both the shell and the tubes is paramount. Common materials include stainless steel, carbon steel, and titanium. Stainless steel (e.g., AISI 316) is often preferred for its corrosion resistance and durability in harsh environments. For international B2B buyers, selecting the right material grade can prevent costly failures and maintenance issues, particularly in industries like petrochemicals and food processing where cleanliness and corrosion resistance are vital.
2. Design Pressure and Temperature
The design pressure and temperature ratings indicate the maximum operating conditions the heat exchanger can withstand. For instance, a unit rated for 150 psi and 300°C is suitable for high-pressure applications. B2B buyers must ensure that the heat exchanger’s specifications align with the operational requirements of their processes to avoid premature equipment failure and safety hazards.
3. Heat Transfer Efficiency
The efficiency of heat transfer is influenced by the design of the tube arrangement and the type of fluids used. Enhanced surface tubes can improve heat transfer rates significantly. Buyers should look for performance data such as the overall heat transfer coefficient (U-value) to assess energy efficiency, which can lead to substantial cost savings over time.
4. Tolerance and Clearance
Tolerance levels in manufacturing define how much variation is acceptable in the dimensions of the heat exchanger components. Adequate clearance is essential for thermal expansion and maintenance. For B2B buyers, understanding tolerances can help in selecting compatible components and ensuring proper installation, which is crucial for maximizing efficiency and longevity.
5. Flow Arrangement
Heat exchangers can be designed for counterflow, parallel flow, or crossflow arrangements, affecting their efficiency and application suitability. Counterflow designs typically offer higher efficiency due to a more effective temperature gradient. Buyers should consider their specific application requirements when selecting the flow arrangement to optimize performance.
What Are the Common Trade Terms Used in Shell and Heat Exchanger Transactions?
Navigating the procurement of shell and tube heat exchangers involves familiarizing oneself with industry jargon. Here are some essential terms that international B2B buyers should understand:
1. OEM (Original Equipment Manufacturer)
An OEM refers to a company that produces parts or equipment that may be marketed by another manufacturer. For buyers, working with OEMs can ensure the quality and compatibility of components, particularly in industries with strict regulatory standards.
2. MOQ (Minimum Order Quantity)
MOQ is the smallest number of units a supplier is willing to sell. Understanding MOQ is critical for B2B buyers to manage inventory and budget effectively, especially when dealing with high-cost equipment like heat exchangers.
3. RFQ (Request for Quotation)
An RFQ is a document issued by a buyer to solicit price quotes from suppliers for specific goods or services. For international buyers, a well-prepared RFQ can expedite the procurement process and ensure that all necessary specifications are included, leading to accurate and comparable quotes.
4. Incoterms (International Commercial Terms)
Incoterms are a set of rules that define the responsibilities of buyers and sellers in international transactions. Familiarity with Incoterms, such as FOB (Free On Board) or CIF (Cost, Insurance, and Freight), is essential for B2B buyers to understand the logistics and costs associated with shipping and delivery.
5. Lead Time
Lead time refers to the time it takes from placing an order until the goods are delivered. Understanding lead times is crucial for B2B buyers to plan their operations and avoid production delays, especially in industries where timing is critical.
By grasping these technical properties and trade terms, international B2B buyers can make informed decisions that enhance operational efficiency and reduce costs in their applications involving shell and tube heat exchangers.
Navigating Market Dynamics and Sourcing Trends in the shell and heat exchanger Sector
What Are the Current Market Dynamics and Key Trends in the Shell and Heat Exchanger Sector?
The global shell and heat exchanger market is significantly influenced by various drivers, including the increasing demand for efficient thermal management solutions across industries such as petrochemicals, power generation, and HVAC. The market is projected to grow at a compound annual growth rate (CAGR) of approximately 6% over the next five years. Key trends include the adoption of advanced materials that enhance thermal efficiency and the integration of IoT technologies for predictive maintenance and operational efficiency. Buyers from Africa, South America, the Middle East, and Europe should note the regional differences in regulatory standards and market demands, particularly in the petrochemical sectors of Saudi Arabia and the oil-rich regions of South America.
Emerging technologies such as enhanced surface tubes and compact designs are gaining traction, allowing for more effective heat transfer while reducing space requirements. Furthermore, the growing emphasis on sustainability is driving innovations in heat exchanger design, leading to energy-efficient products that align with global energy conservation goals. Buyers should focus on suppliers who can provide customization options to meet specific operational needs while adhering to local standards, which can differ significantly across regions.
How Can Sustainability and Ethical Sourcing Impact B2B Buyers in the Shell and Heat Exchanger Sector?
Sustainability is becoming an essential consideration for B2B buyers in the shell and heat exchanger market. The environmental impact of manufacturing processes and the materials used in production are under scrutiny. Buyers are increasingly prioritizing suppliers who demonstrate a commitment to reducing their carbon footprint, whether through the use of recycled materials or energy-efficient manufacturing processes. This shift not only enhances corporate social responsibility (CSR) profiles but also meets the growing consumer demand for sustainable practices.
Ethical sourcing is equally critical, as it ensures that materials are obtained in a manner that respects both the environment and the communities involved. Certifications such as ISO 14001 for environmental management systems and LEED (Leadership in Energy and Environmental Design) for sustainable building practices are becoming essential for suppliers aiming to maintain competitiveness in the market. Buyers should seek partnerships with manufacturers who are transparent about their sourcing practices and who can provide proof of compliance with sustainability standards.
What Is the Brief Evolution and Historical Context of the Shell and Heat Exchanger Industry?
The shell and heat exchanger technology has undergone significant evolution since its inception in the early 20th century. Initially developed for steam generation and power applications, the design and manufacturing processes have advanced dramatically, driven by the need for greater efficiency and versatility. The introduction of standards by organizations like the Tubular Exchanger Manufacturers Association (TEMA) has standardized nomenclature and design practices, facilitating better communication and procurement processes among international buyers.
As industries continue to innovate, the focus has shifted toward enhancing heat transfer efficiency and minimizing energy consumption. This evolution reflects broader trends in industrialization and the increasing importance of thermal management in various applications, from petrochemicals to HVAC systems. Understanding this historical context can help B2B buyers appreciate the technological advancements that have led to the current state of the market, enabling more informed sourcing decisions.
Frequently Asked Questions (FAQs) for B2B Buyers of shell and heat exchanger
-
How do I select the right shell and tube heat exchanger for my application?
Choosing the right shell and tube heat exchanger involves assessing several factors including the type of fluids, temperature and pressure requirements, and space constraints. Consider the thermal performance, compatibility with the fluid properties, and maintenance accessibility. Additionally, evaluate the design standards such as TEMA, which provides guidelines on construction and performance. Collaborating with a knowledgeable supplier can help you navigate these variables and select an exchanger that meets your specific needs. -
What is the best material for a shell and tube heat exchanger in corrosive environments?
In corrosive environments, stainless steel is often the best material due to its excellent resistance to corrosion and high temperatures. For more aggressive chemicals, materials like titanium or specialized alloys may be necessary. It’s crucial to assess the fluid composition and operating conditions to ensure the selected material will maintain integrity over time. Consulting with manufacturers who offer customized solutions can also help in selecting the right material for your specific application. -
What are the common applications of shell and tube heat exchangers in various industries?
Shell and tube heat exchangers are widely used in industries such as petrochemical, power generation, and HVAC. They serve functions like heating or cooling fluids, condensing steam, and recovering waste heat. In the petrochemical sector, they often handle crude oil and its derivatives, while in power plants, they are crucial for processes like feedwater heating. Understanding your industry’s specific requirements will help you identify the most suitable applications for these heat exchangers. -
What factors should I consider when vetting suppliers of shell and tube heat exchangers?
When vetting suppliers, consider their experience in your industry, the quality certifications they hold (such as ISO), and their compliance with international standards like TEMA. Look for suppliers who offer customized solutions and have a solid track record of reliability and customer service. Additionally, evaluate their logistical capabilities, including shipping options and delivery times, especially for international transactions, to ensure they can meet your project deadlines. -
What are the typical minimum order quantities (MOQs) for shell and tube heat exchangers?
Minimum order quantities can vary significantly based on the supplier and the customization of the heat exchangers. Standard units may have lower MOQs, while customized or specialty units often require larger orders. It’s advisable to discuss your specific needs with potential suppliers to understand their MOQ policies. Some suppliers may offer flexibility in MOQs, especially for long-term partnerships or contracts. -
What payment terms are common in international B2B transactions for heat exchangers?
Payment terms for international transactions often include options like advance payment, letters of credit, or payment upon delivery. The choice of terms can depend on factors such as the supplier’s policy, the buyer’s creditworthiness, and the nature of the transaction. It’s crucial to negotiate clear terms that protect both parties and facilitate smooth transactions. Additionally, ensure that any currency exchange risks are considered in the agreement. -
How can I ensure quality assurance (QA) for my shell and tube heat exchanger order?
To ensure quality assurance, request detailed documentation from the supplier, including material certifications, inspection reports, and compliance with industry standards. Consider conducting pre-shipment inspections and engaging third-party quality assurance agencies if necessary. Establishing a clear QA process in your contract can also help mitigate risks and ensure that the delivered products meet your specifications and performance criteria. -
What logistics considerations should I keep in mind when importing heat exchangers?
Logistics for importing heat exchangers require careful planning around shipping methods, customs clearance, and potential tariffs. Choose a reliable freight forwarder who understands the complexities of international shipping. Ensure that all necessary documentation, such as bills of lading and customs declarations, are prepared in advance. Additionally, consider the lead times for production and shipping to avoid delays in your project timeline.
Important Disclaimer & Terms of Use
⚠️ Important Disclaimer
The information provided in this guide, including content regarding manufacturers, technical specifications, and market analysis, is for informational and educational purposes only. It does not constitute professional procurement advice, financial advice, or legal advice.
While we have made every effort to ensure the accuracy and timeliness of the information, we are not responsible for any errors, omissions, or outdated information. Market conditions, company details, and technical standards are subject to change.
B2B buyers must conduct their own independent and thorough due diligence before making any purchasing decisions. This includes contacting suppliers directly, verifying certifications, requesting samples, and seeking professional consultation. The risk of relying on any information in this guide is borne solely by the reader.
Strategic Sourcing Conclusion and Outlook for shell and heat exchanger
What Are the Key Takeaways for International B2B Buyers in Shell and Heat Exchanger Procurement?
In conclusion, strategic sourcing of shell and heat exchangers offers significant advantages for international B2B buyers, particularly in regions like Africa, South America, the Middle East, and Europe. Understanding the specific needs of your application—be it petrochemical, power generation, or HVAC—enables the selection of the right type of heat exchanger. Leveraging TEMA standards can ensure compatibility and reliability, which are crucial for maintaining operational efficiency.
How Can Strategic Sourcing Enhance Your Competitive Edge?
Investing in high-quality shell and tube heat exchangers can significantly reduce maintenance costs and enhance energy efficiency, ultimately improving the bottom line. Furthermore, establishing strong relationships with reputable suppliers can lead to better pricing, faster delivery times, and access to advanced technologies.
What’s Next for International B2B Buyers?
As the demand for energy-efficient solutions continues to rise, the market for shell and heat exchangers is poised for growth. Buyers should stay informed about emerging trends and innovations in heat exchange technology to remain competitive. Engaging in proactive sourcing strategies will not only optimize procurement processes but also foster long-term partnerships that can adapt to changing market dynamics. Now is the time to evaluate your sourcing strategies and seize opportunities to enhance operational performance and sustainability.