The Ultimate Guide to Shell & Tube Type Heat Exchanger (2025)
Introduction: Navigating the Global Market for shell & tube type heat exchanger
Navigating the global market for shell & tube type heat exchangers can be a daunting task for international B2B buyers, particularly when considering the diverse applications and the technical specifications involved. As industries across Africa, South America, the Middle East, and Europe (such as Italy and the UK) seek efficient thermal management solutions, sourcing the right heat exchanger becomes critical to ensuring operational efficiency and compliance with local standards. This comprehensive guide delves into the various types of shell & tube heat exchangers, their applications across different sectors, and essential factors to consider when vetting suppliers.
From understanding the intricacies of fixed tubesheet, U-tube, and floating head designs to evaluating performance metrics and material compatibility, this guide equips B2B buyers with actionable insights. We will also explore cost considerations, maintenance practices, and the importance of after-sales support, ensuring you make informed purchasing decisions.
By addressing common challenges and providing clarity on the procurement process, this guide empowers international buyers to confidently navigate the complexities of sourcing shell & tube heat exchangers, ultimately enhancing their project outcomes and fostering long-term supplier relationships. Whether you are establishing a new facility or upgrading existing equipment, the knowledge gained from this resource will be invaluable in optimizing your investment in heat exchange technology.
Understanding shell & tube type heat exchanger Types and Variations
Type Name | Key Distinguishing Features | Primary B2B Applications | Brief Pros & Cons for Buyers |
---|---|---|---|
Fixed Tubesheet Exchanger | Tubesheets are welded to the shell; simple design; limited accessibility | Petrochemical and chemical industries | Pros: Cost-effective; easy to manufacture. Cons: Limited cleaning options; thermal stress issues. |
U-Tube Exchanger | U-shaped tubes allow for thermal expansion; removable bundle | Power generation and HVAC applications | Pros: Flexible design; good for clean fluids. Cons: Difficult internal cleaning; more expensive than fixed types. |
Floating Head Exchanger | Tubesheet allows for movement; suitable for high thermal expansion | Oil & gas and refrigeration sectors | Pros: Easy maintenance; accommodates thermal expansion. Cons: Higher initial cost; complex design. |
Double-Wall Tube Heat Exchanger | Contains two walls for enhanced safety; reduces risk of leaks | Pharmaceutical and food processing | Pros: High safety standards; prevents contamination. Cons: Higher manufacturing cost; bulkier design. |
Enhanced Surface Tube Exchanger | Tubes designed for higher heat transfer efficiency | HVAC systems and industrial processes | Pros: Improved efficiency; compact design. Cons: Higher upfront costs; specific fluid compatibility required. |
What are the characteristics of Fixed Tubesheet Exchangers?
Fixed tubesheet exchangers feature a straightforward design with tubesheets welded to the shell, making them suitable for applications where the fluids are not expected to cause fouling. They are commonly used in petrochemical and chemical industries due to their economical construction. However, buyers should be aware that while they are cost-effective, the limited cleaning options can lead to maintenance challenges, especially under high thermal stress.
Why choose U-Tube Exchangers for your operations?
U-tube exchangers are designed with U-shaped tubes that allow for thermal expansion, making them ideal for power generation and HVAC applications where temperature fluctuations are common. Their removable bundle design facilitates maintenance, but it’s important for buyers to consider that internal cleaning can be difficult, and they are typically more expensive than fixed types. This design is best suited for clean fluids to minimize fouling.
What makes Floating Head Exchangers a viable option?
Floating head exchangers feature a design that allows one end of the tubesheet to move, accommodating thermal expansion and making them suitable for oil & gas and refrigeration applications. Their ease of maintenance is a significant advantage, but buyers should note that the initial costs are higher due to the complex design. They offer flexibility in operation, making them a preferred choice for systems with significant temperature variations.
How do Double-Wall Tube Heat Exchangers ensure safety?
Double-wall tube heat exchangers are designed with two walls, enhancing safety by reducing the risk of leaks and contamination, which is crucial in pharmaceutical and food processing industries. While they provide high safety standards, their manufacturing costs are typically higher, and they can be bulkier than traditional designs. Buyers must weigh the benefits of safety and compliance against the increased investment.
Why consider Enhanced Surface Tube Exchangers for efficiency?
Enhanced surface tube exchangers are tailored for high heat transfer efficiency, making them an excellent choice for HVAC systems and various industrial processes. Their compact design allows for space-saving installations, but buyers should be aware of the higher upfront costs and ensure that the fluids used are compatible with the specific enhancements. This type of exchanger is ideal for applications requiring maximized thermal performance.
Key Industrial Applications of shell & tube type heat exchanger
Industry/Sector | Specific Application of shell & tube type heat exchanger | Value/Benefit for the Business | Key Sourcing Considerations for this Application |
---|---|---|---|
Petrochemical | Heat recovery in crude oil refining processes | Enhances energy efficiency and reduces operational costs | Compliance with TEMA standards, material selection for corrosion resistance |
Power Generation | Feedwater heating in steam power plants | Improves thermal efficiency and overall plant performance | Custom designs for high pressures and temperatures, maintenance accessibility |
HVAC and Refrigeration | Chilled water systems for commercial buildings | Provides effective cooling, leading to lower energy costs | Space constraints, ease of installation, and maintenance requirements |
Food and Beverage | Pasteurization processes for liquid products | Ensures product safety and extends shelf life | Regulatory compliance, hygienic design, and material certification |
Marine and Offshore | Cooling systems for engines and machinery on vessels | Enhances reliability and extends equipment lifespan | Durability under harsh conditions, lightweight materials, and compact design |
How is Shell & Tube Heat Exchanger Used in the Petrochemical Industry?
In the petrochemical sector, shell & tube heat exchangers are integral for heat recovery during crude oil refining. They allow for the efficient transfer of heat between fluids, thereby enhancing energy efficiency and reducing operational costs. Buyers in this industry should prioritize compliance with TEMA standards and ensure the selection of materials that offer high corrosion resistance, given the harsh chemicals involved in the processes.
What Role Does Shell & Tube Heat Exchanger Play in Power Generation?
In power generation, these heat exchangers are commonly used for feedwater heating in steam power plants. By recovering heat from exhaust gases or steam, they significantly improve thermal efficiency and enhance overall plant performance. International buyers should consider custom designs that can withstand high pressures and temperatures, ensuring accessibility for maintenance to avoid costly downtimes.
How Are Shell & Tube Heat Exchangers Applied in HVAC and Refrigeration?
In HVAC and refrigeration applications, shell & tube heat exchangers are used in chilled water systems for commercial buildings. They effectively transfer heat, providing reliable cooling solutions that lead to lower energy costs. When sourcing these units, buyers must account for space constraints and ease of installation, as well as maintenance requirements to ensure long-term efficiency.
What is the Importance of Shell & Tube Heat Exchangers in Food and Beverage Processing?
In the food and beverage industry, shell & tube heat exchangers are crucial for pasteurization processes, ensuring the safety and extending the shelf life of liquid products. The design must meet regulatory compliance standards, and buyers should look for hygienic designs and certified materials to ensure product safety and quality.
How Do Shell & Tube Heat Exchangers Benefit Marine and Offshore Applications?
In marine and offshore environments, shell & tube heat exchangers are vital for cooling systems in engines and machinery. They enhance reliability and extend the lifespan of equipment under harsh conditions. Buyers should focus on sourcing exchangers made from durable, lightweight materials with compact designs to optimize space and performance in these challenging environments.
3 Common User Pain Points for ‘shell & tube type heat exchanger’ & Their Solutions
Scenario 1: Inefficient Heat Transfer Leading to Increased Operational Costs
The Problem: A manufacturing plant in South America has been experiencing significant inefficiencies with its shell and tube heat exchanger, resulting in higher energy consumption and operational costs. The plant’s management suspects that the heat exchanger is not performing optimally due to fouling, which reduces the heat transfer efficiency. This not only leads to wasted energy but can also cause production delays and increased maintenance costs.
The Solution: To address this issue, it is crucial for the plant to implement a regular maintenance schedule that includes cleaning the heat exchanger to remove fouling deposits. Additionally, buyers should consider investing in advanced monitoring systems that can provide real-time data on the performance of the heat exchanger. These systems can alert operators to potential fouling before it becomes a significant issue, allowing for timely cleaning. When sourcing a new unit, consider models with enhanced surface tubes or those designed for easier access to cleaning, which can improve performance and reduce downtime. Collaborating with manufacturers that offer tailored solutions based on specific operational requirements can also ensure that the selected heat exchanger meets the plant’s unique needs.
Scenario 2: Choosing the Right Material for Diverse Applications
The Problem: An engineering firm in the Middle East is tasked with designing a new heat exchanger for a petrochemical plant. However, they are facing challenges in selecting the appropriate materials that can withstand the harsh operating conditions, including high temperatures and corrosive fluids. The wrong choice could lead to premature failure, costly replacements, and extended downtime.
The Solution: To mitigate this risk, it is essential for buyers to conduct a thorough materials compatibility analysis before procurement. This includes considering factors such as thermal conductivity, corrosion resistance, and the specific properties of the fluids being processed. Engaging with suppliers who specialize in shell and tube heat exchangers can provide valuable insights into the latest material innovations, such as advanced alloys or coatings designed for extreme environments. Additionally, buyers should request case studies or references from suppliers to understand how similar applications were handled, ensuring that the selected materials will perform reliably over time. Taking advantage of custom manufacturing options can also help in achieving the best fit for specific operational challenges.
Scenario 3: Navigating Regulatory Compliance and Standards
The Problem: A European company is looking to purchase a shell and tube heat exchanger for a new facility but is overwhelmed by the various industry standards and regulations that need to be met. Non-compliance could lead to legal issues and operational interruptions, making it imperative to ensure that the selected unit adheres to all relevant guidelines.
The Solution: Buyers should start by familiarizing themselves with the applicable standards in their region, such as those set by the Tubular Exchanger Manufacturers Association (TEMA) or local regulatory bodies. Engaging with suppliers who have a proven track record of compliance can simplify this process. It is advisable to ask for documentation that outlines how the heat exchanger meets these standards and to conduct due diligence on the supplier’s certifications. Furthermore, collaborating with engineering consultants who specialize in regulatory compliance can provide peace of mind and ensure that all necessary criteria are met from the design phase through to installation. By prioritizing compliance at the outset, companies can avoid costly delays and ensure the smooth operation of their systems.
Strategic Material Selection Guide for shell & tube type heat exchanger
What Are the Key Materials for Shell & Tube Heat Exchangers?
When selecting materials for shell and tube heat exchangers, international B2B buyers must consider the properties, advantages, and limitations of various materials. Here, we analyze four common materials used in these heat exchangers: carbon steel, stainless steel, copper alloys, and titanium. Each material has distinct characteristics that affect performance, durability, and suitability for specific applications.
How Does Carbon Steel Perform in Shell & Tube Heat Exchangers?
Key Properties: Carbon steel is known for its high strength and excellent thermal conductivity. It typically withstands pressures up to 2000 psi and temperatures up to 400°F (204°C).
Pros & Cons: Carbon steel is cost-effective and easy to manufacture. However, it is prone to corrosion, especially in humid or acidic environments, which can lead to failure over time. This material is best suited for applications involving non-corrosive fluids.
Impact on Application: Carbon steel is ideal for applications in oil and gas, where the media is less aggressive. However, it may not be suitable for industries like food processing or pharmaceuticals due to hygiene concerns.
Considerations for International Buyers: Buyers from regions like Africa and South America should ensure compliance with local corrosion standards. ASTM A106 and A53 are common specifications for carbon steel pipes.
What Advantages Does Stainless Steel Offer?
Key Properties: Stainless steel is highly resistant to corrosion and can handle temperatures up to 1500°F (815°C) and pressures exceeding 3000 psi, depending on the grade.
Pros & Cons: Its durability and resistance to oxidation make stainless steel a preferred choice for many industries. However, it is more expensive than carbon steel and can be more complex to fabricate.
Impact on Application: Stainless steel is ideal for applications involving corrosive fluids, such as in chemical processing or marine environments. Its hygienic properties also make it suitable for food and beverage applications.
Considerations for International Buyers: Compliance with standards such as ASTM A312 or EN 10216 is crucial for buyers in Europe and the Middle East, where stringent regulations govern material quality.
What Role Do Copper Alloys Play in Heat Exchangers?
Key Properties: Copper alloys, such as brass and bronze, offer excellent thermal conductivity and corrosion resistance. They can typically handle temperatures up to 400°F (204°C) and pressures around 1500 psi.
Pros & Cons: The high thermal efficiency of copper alloys makes them suitable for applications requiring rapid heat transfer. However, they are more expensive than carbon steel and can be susceptible to dezincification in certain environments.
Impact on Application: Copper alloys are commonly used in HVAC systems and refrigeration applications where efficient heat transfer is critical.
Considerations for International Buyers: Buyers should be aware of local regulations regarding the use of copper, especially in potable water systems. Compliance with standards like ASTM B88 is important for ensuring safety and quality.
Why Choose Titanium for Shell & Tube Heat Exchangers?
Key Properties: Titanium is known for its outstanding corrosion resistance and can withstand temperatures up to 1000°F (538°C) and pressures exceeding 3000 psi.
Pros & Cons: While titanium is highly durable and lightweight, it is also significantly more expensive and challenging to fabricate than other materials.
Impact on Application: Titanium is ideal for harsh environments, such as seawater applications or chemical processing, where other materials may fail.
Considerations for International Buyers: Buyers from Europe and the Middle East should ensure compliance with ASTM B338 or equivalent standards, as titanium applications often require rigorous quality checks.
Summary Table of Material Selection for Shell & Tube Heat Exchangers
Material | Typical Use Case for Shell & Tube Type Heat Exchanger | Key Advantage | Key Disadvantage/Limitation | Relative Cost (Low/Med/High) |
---|---|---|---|---|
Carbon Steel | Oil and gas applications | Cost-effective | Prone to corrosion | Low |
Stainless Steel | Chemical processing, food and beverage | High corrosion resistance | Higher manufacturing complexity | High |
Copper Alloys | HVAC and refrigeration | Excellent thermal conductivity | Susceptible to dezincification | Medium |
Titanium | Seawater applications, chemical processing | Outstanding corrosion resistance | High cost and fabrication difficulty | High |
This guide serves as a strategic resource for international B2B buyers, ensuring informed material selection for shell and tube heat exchangers tailored to specific applications and regional compliance requirements.
In-depth Look: Manufacturing Processes and Quality Assurance for shell & tube type heat exchanger
What Are the Key Stages in the Manufacturing Process of Shell & Tube Heat Exchangers?
The manufacturing process of shell and tube heat exchangers involves several critical stages that ensure the final product meets industry standards for performance and durability. Here’s a detailed breakdown of each stage:
-
Material Preparation
The first step involves selecting the appropriate materials based on the intended application and environmental conditions. Common materials include carbon steel, stainless steel, and special alloys that offer resistance to corrosion and high temperatures. After selection, materials undergo processes such as cutting and surface treatment to prepare them for forming. -
Forming
This stage encompasses the shaping of components, primarily the shell and tubes. Techniques such as cold rolling, welding, and bending are employed to achieve the desired geometries. For instance, tubes may be produced using seamless or welded methods depending on the required specifications. Precision in forming is essential to ensure optimal heat transfer efficiency and structural integrity. -
Assembly
In the assembly stage, the formed components are brought together to create the heat exchanger. This includes fitting the tube bundle into the shell, installing baffles to direct fluid flow, and securing the headers. Effective assembly techniques are crucial, as they influence the exchanger’s performance and maintenance accessibility. -
Finishing
The final manufacturing stage includes surface finishing treatments such as passivation and painting to enhance corrosion resistance and aesthetic appeal. Additionally, the heat exchanger undergoes various pressure tests to ensure it can withstand operational conditions without leaks.
How Is Quality Assurance Implemented in Shell & Tube Heat Exchanger Manufacturing?
Quality assurance (QA) is a vital aspect of the manufacturing process for shell and tube heat exchangers. It ensures that the products meet both international standards and specific customer requirements.
-
International Standards and Certifications
Compliance with international standards such as ISO 9001 is critical for manufacturers. This certification demonstrates a commitment to quality management systems, ensuring consistent quality in manufacturing processes. Industry-specific standards, such as CE marking for European markets and API standards for oil and gas applications, also play a crucial role in quality assurance. -
Quality Control Checkpoints
The QA process includes several key checkpoints:
- Incoming Quality Control (IQC): Raw materials are inspected upon arrival to ensure they meet specified standards. This includes checking for material grades and dimensions.
- In-Process Quality Control (IPQC): During manufacturing, periodic inspections are conducted to monitor the quality of the forming and assembly processes. Techniques such as visual inspections and dimensional checks are commonly employed.
- Final Quality Control (FQC): Once assembly is complete, the entire unit undergoes a comprehensive inspection. This may involve pressure testing, non-destructive testing (NDT), and functional tests to verify performance.
- Common Testing Methods for Quality Assurance
Various testing methods are employed to ensure the reliability and efficiency of shell and tube heat exchangers:
- Hydrostatic Testing: This method checks for leaks and structural integrity under pressure.
- Radiographic Testing: Used to inspect weld quality and detect internal flaws.
- Ultrasonic Testing: Measures wall thickness and identifies any potential corrosion or defects in the material.
How Can International B2B Buyers Verify Supplier Quality Control?
B2B buyers, especially those from diverse regions such as Africa, South America, the Middle East, and Europe, should adopt several strategies to verify the quality control processes of suppliers:
-
Supplier Audits
Conducting on-site audits allows buyers to assess the manufacturer’s processes, equipment, and quality management systems firsthand. This provides an opportunity to evaluate adherence to international standards and operational best practices. -
Quality Assurance Reports
Requesting detailed QA reports from suppliers can provide insights into their quality control measures, testing results, and compliance with industry standards. These documents are essential for understanding the reliability of the products being offered. -
Third-Party Inspections
Engaging third-party inspection agencies can offer an independent assessment of the manufacturing process and product quality. These agencies can perform various tests and provide certification that the products meet specified standards. -
Certifications and Documentation
Buyers should request copies of relevant certifications and documentation that demonstrate compliance with international and industry-specific standards. This includes ISO certifications, CE markings, and any other applicable quality assurance documentation.
What Are the Specific Quality Control Nuances for B2B Buyers in Different Regions?
International B2B buyers need to be aware of regional nuances in quality control and regulations:
-
Africa
Buyers should consider the varying levels of manufacturing capabilities across different African countries. It is advisable to partner with suppliers that have established international certifications and a proven track record. -
South America
In countries like Brazil and Argentina, compliance with local standards (e.g., INMETRO certification) is crucial. Buyers should ensure that suppliers are familiar with these regulations. -
Middle East
The Middle East markets often prioritize certifications related to energy efficiency and environmental standards. Buyers should ensure that suppliers can meet these specific requirements. -
Europe (e.g., Italy, UK)
In Europe, compliance with CE marking and adherence to EU directives on safety and environmental impact is mandatory. Buyers should focus on suppliers that can demonstrate full compliance with these stringent regulations.
Conclusion
Understanding the manufacturing processes and quality assurance measures for shell and tube heat exchangers is essential for international B2B buyers. By focusing on detailed manufacturing stages, rigorous quality assurance practices, and regional nuances, buyers can make informed decisions when selecting suppliers. This comprehensive approach not only ensures the reliability of the heat exchangers but also aligns with the specific needs and regulatory requirements of different markets.
Practical Sourcing Guide: A Step-by-Step Checklist for ‘shell & tube type heat exchanger’
In this practical sourcing guide, we aim to equip international B2B buyers, particularly from Africa, South America, the Middle East, and Europe, with a step-by-step checklist for procuring shell & tube type heat exchangers. This guide will help you navigate the complexities of selecting the right equipment that meets your operational needs while ensuring compliance with industry standards.
Step 1: Define Your Technical Specifications
Before initiating the procurement process, clearly outline your technical requirements. Consider factors such as the fluids being processed, temperature and pressure conditions, and the desired heat transfer efficiency.
– Key considerations:
– Determine if you need a fixed tubesheet, U-tube, or floating head design based on maintenance accessibility and thermal expansion requirements.
– Specify material compatibility, especially if corrosive substances are involved.
Step 2: Research Industry Standards and Regulations
Understanding the relevant industry standards is crucial for compliance and safety. Different sectors may require adherence to specific guidelines such as those set by the Tubular Exchanger Manufacturers Association (TEMA).
– Important points:
– Familiarize yourself with TEMA designations for shell & tube heat exchangers.
– Review any regional regulations that might impact your procurement, particularly in your target markets in Africa, South America, the Middle East, and Europe.
Step 3: Evaluate Potential Suppliers
Before committing, it’s crucial to vet suppliers thoroughly. Request company profiles, case studies, and references from buyers in a similar industry or region.
– What to look for:
– Supplier certifications (ISO, TEMA compliance).
– Experience in your specific industry, especially if you operate in specialized sectors like petrochemicals or power generation.
Step 4: Request Quotes and Compare Pricing
Once you have a shortlist of potential suppliers, request detailed quotes for your specified heat exchanger models.
– Comparison factors:
– Analyze not just the price but also the terms of warranty, maintenance services, and lead times.
– Ensure all quotes include similar specifications for an accurate comparison.
Step 5: Verify Quality Assurance Processes
Quality assurance is vital for the longevity and reliability of your heat exchangers.
– Key aspects to check:
– Inquire about the quality control measures in place during manufacturing.
– Look for third-party testing certifications to ensure the products meet performance standards.
Step 6: Negotiate Terms and Conditions
Negotiating favorable terms can lead to significant savings and better service.
– Focus areas:
– Discuss payment terms, delivery schedules, and after-sales support.
– Ensure clarity on responsibilities related to installation, maintenance, and potential repair services.
Step 7: Finalize the Purchase Agreement
After confirming that the supplier meets all your requirements, finalize the purchase agreement.
– Important elements:
– Ensure all specifications, delivery timelines, and warranties are documented.
– Review the cancellation and return policies to protect your interests.
By following this structured approach, international B2B buyers can make informed decisions when sourcing shell & tube type heat exchangers, ultimately leading to improved operational efficiency and compliance with industry standards.
Comprehensive Cost and Pricing Analysis for shell & tube type heat exchanger Sourcing
What Are the Key Cost Components in Sourcing Shell & Tube Heat Exchangers?
When sourcing shell and tube heat exchangers, understanding the various cost components is crucial. The main factors include:
-
Materials: The choice of materials significantly affects cost. Common materials include carbon steel, stainless steel, and specialized alloys for corrosive environments. High-quality materials are essential for durability and efficiency but can raise upfront costs.
-
Labor: Labor costs can vary based on location and the complexity of the manufacturing process. Skilled labor is often required for assembly and quality control, which can add to the overall cost.
-
Manufacturing Overhead: This includes expenses related to factory operations, utilities, and equipment maintenance. Efficient manufacturing processes can help reduce these overheads.
-
Tooling: The initial investment in tooling for specialized designs can be substantial. However, this cost can be amortized over large production runs, making it more manageable for high-volume orders.
-
Quality Control (QC): Ensuring the heat exchangers meet industry standards (like TEMA) involves rigorous QC processes. These costs should be factored into the overall budget.
-
Logistics: Transportation and shipping costs can vary greatly, especially for international shipments. Factors such as Incoterms and shipping methods influence the final price.
-
Margin: Suppliers typically add a margin to cover business expenses and profit. Understanding supplier pricing strategies can help buyers negotiate better deals.
How Do Price Influencers Affect Shell & Tube Heat Exchanger Costs?
Several factors can influence the pricing of shell and tube heat exchangers:
-
Volume/MOQ (Minimum Order Quantity): Higher order volumes often lead to lower per-unit costs. Suppliers may offer discounts for bulk orders, which can be a significant advantage for large projects.
-
Specifications and Customization: Custom designs or specific performance requirements can increase costs. Buyers should assess whether customization is necessary or if standard models can meet their needs.
-
Material Quality and Certifications: Higher quality materials and necessary certifications (such as ASME or ISO) add to costs but are essential for compliance and reliability, especially in regulated industries.
-
Supplier Factors: The reputation and reliability of the supplier can impact pricing. Established suppliers may charge more due to their proven track record, while newer companies might offer lower prices to gain market share.
-
Incoterms: Understanding the terms of delivery (e.g., FOB, CIF) is crucial for assessing total costs. The choice of Incoterms can affect shipping costs, insurance, and responsibility during transit.
What Are Effective Buyer Tips for Cost-Efficiency?
For international B2B buyers, particularly from Africa, South America, the Middle East, and Europe, the following tips can enhance cost-efficiency:
-
Negotiate Effectively: Don’t hesitate to negotiate pricing, especially for large orders. Suppliers may have room to adjust prices, especially if they know you are considering multiple suppliers.
-
Consider Total Cost of Ownership (TCO): Analyze the long-term costs associated with the heat exchangers, including maintenance, energy consumption, and potential downtime. This holistic view can justify higher upfront costs for more efficient units.
-
Be Aware of Pricing Nuances: Currency fluctuations, local tariffs, and taxes can all impact the final price. Stay informed about these factors, especially when dealing with international suppliers.
-
Build Relationships with Suppliers: Establishing a good relationship with suppliers can lead to better pricing, priority service, and increased flexibility in negotiations.
Disclaimer on Indicative Prices
Prices for shell and tube heat exchangers can vary widely based on the factors discussed above. It’s essential for buyers to request detailed quotes from multiple suppliers to ensure they are receiving competitive offers that reflect their specific requirements.
Alternatives Analysis: Comparing shell & tube type heat exchanger With Other Solutions
Understanding the Importance of Alternatives in Heat Exchange Solutions
When considering the best heat exchange solution for industrial applications, it’s crucial to explore alternatives to the widely used shell and tube type heat exchangers. While shell and tube exchangers offer versatility and robustness, other technologies may provide distinct advantages in specific applications or operational contexts. This analysis will compare shell and tube heat exchangers with plate heat exchangers and air-cooled heat exchangers, highlighting their respective strengths and weaknesses.
Comparison Table of Heat Exchanger Solutions
Comparison Aspect | Shell & Tube Type Heat Exchanger | Plate Heat Exchanger | Air-Cooled Heat Exchanger |
---|---|---|---|
Performance | High thermal efficiency; good for high pressure and temperature applications. | Excellent heat transfer efficiency; compact design. | Suitable for low-pressure applications; relies on ambient air for cooling. |
Cost | Generally higher initial cost but lower operational costs due to durability. | Lower initial cost, but may require more frequent maintenance. | Cost-effective for installation; no water source needed but may incur higher operational costs. |
Ease of Implementation | Complex installation requiring skilled labor; larger footprint. | Easier to install; smaller footprint, requires less space. | Simple installation; can be placed in various locations without water access. |
Maintenance | Requires regular maintenance; cleaning can be labor-intensive. | Easier to clean and maintain; plates can be removed for thorough cleaning. | Minimal maintenance required; however, cleaning of fins may be necessary. |
Best Use Case | Ideal for high-temperature and high-pressure applications, such as petrochemical and power generation industries. | Best for food processing, pharmaceuticals, and HVAC applications where space is limited. | Suitable for cooling applications in remote areas or where water resources are scarce. |
In-Depth Analysis of Alternative Solutions
What Are the Advantages and Disadvantages of Plate Heat Exchangers?
Plate heat exchangers consist of a series of thin plates that create channels for fluids to pass through, promoting efficient heat transfer. The primary advantage of this design is its compact size, making it ideal for applications with space constraints. They also offer excellent thermal efficiency and are easier to clean, as the plates can be disassembled for maintenance. However, plate heat exchangers may not withstand as high pressure and temperature as shell and tube models, making them less suitable for certain industrial applications.
How Do Air-Cooled Heat Exchangers Compare?
Air-cooled heat exchangers utilize ambient air to dissipate heat, eliminating the need for cooling water. This makes them an excellent choice for locations where water supply is limited or expensive. They are also cost-effective in terms of installation, as they require less infrastructure compared to water-cooled systems. However, their performance can be affected by environmental conditions, leading to less efficiency in hotter climates, and they may incur higher operational costs in terms of energy consumption.
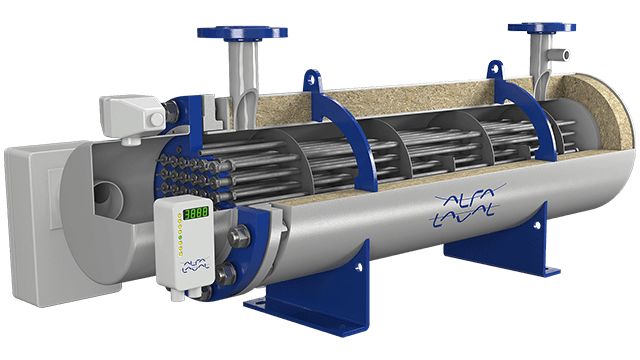
A stock image related to shell & tube type heat exchanger.
Conclusion: Choosing the Right Heat Exchanger for Your Needs
When selecting a heat exchanger, B2B buyers must consider various factors, including application requirements, budget constraints, and operational conditions. Shell and tube heat exchangers are robust solutions for high-demand environments, while plate heat exchangers provide space-saving benefits and ease of maintenance. Air-cooled heat exchangers offer unique advantages in water-scarce settings but may not be suitable for all applications. By carefully evaluating the specific needs and constraints of their operations, buyers from Africa, South America, the Middle East, and Europe can make informed decisions that optimize efficiency and cost-effectiveness in their heat exchange processes.
Essential Technical Properties and Trade Terminology for shell & tube type heat exchanger
What Are the Essential Technical Properties of Shell & Tube Heat Exchangers?
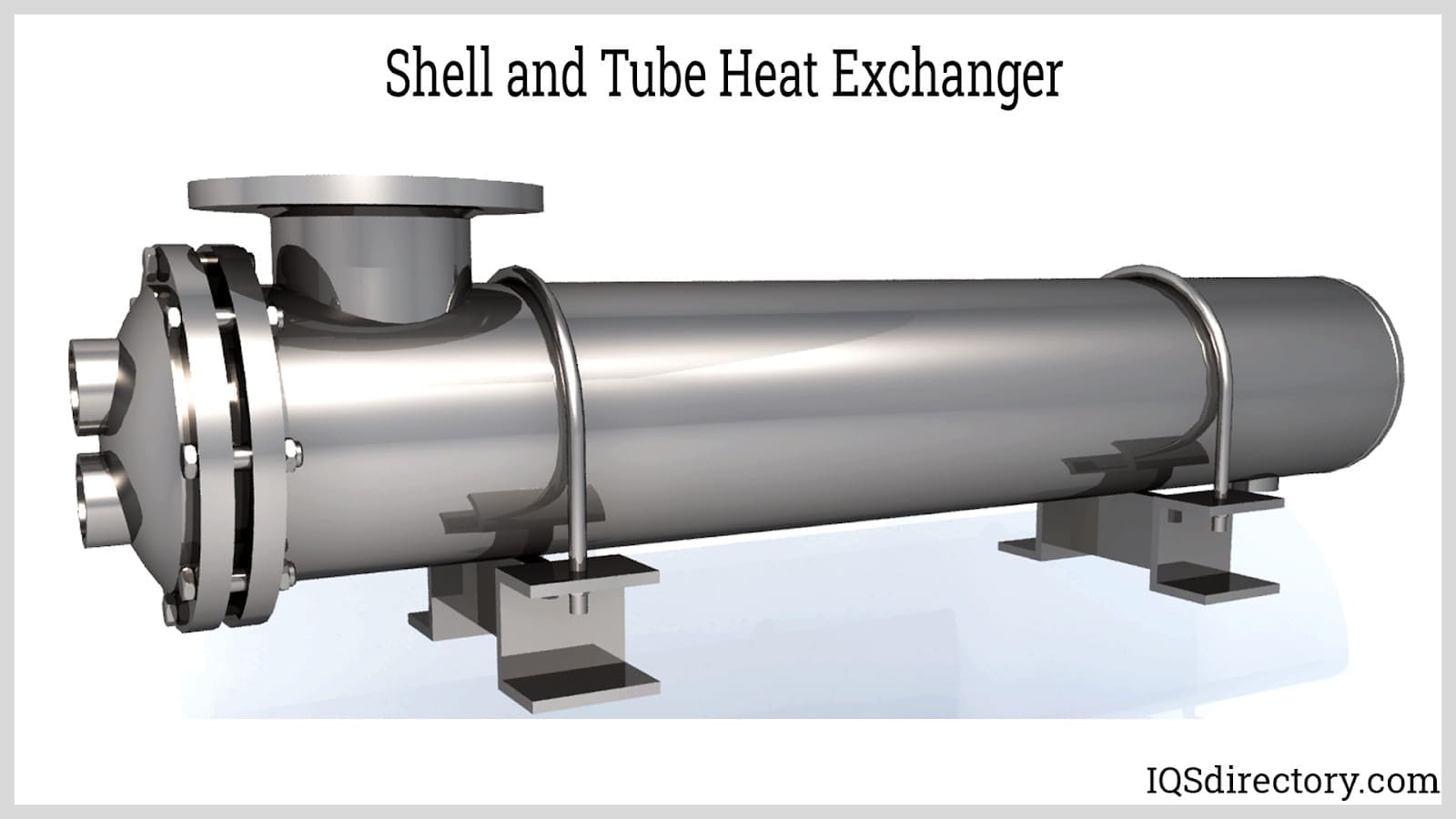
A stock image related to shell & tube type heat exchanger.
When selecting a shell & tube heat exchanger for industrial applications, understanding key technical properties is crucial for ensuring optimal performance and longevity. Here are some critical specifications to consider:
1. Material Grade
The choice of material directly impacts durability and thermal efficiency. Common materials include stainless steel, carbon steel, and titanium. Stainless steel is favored for its corrosion resistance and strength, making it suitable for a variety of fluids and temperatures. For B2B buyers, specifying the right material grade is essential to match operational conditions and regulatory standards, particularly in industries like petrochemicals or food processing.
2. Pressure Rating
Shell & tube heat exchangers are designed to operate under specific pressure conditions, often classified into various pressure ratings (e.g., ANSI Class 150, 300). Understanding the pressure rating is vital for safety and functionality, as it affects the design and cost. Buyers should ensure that the exchanger meets the pressure requirements of their process to avoid failures and downtime.
3. Heat Transfer Area
The effectiveness of a heat exchanger is largely determined by its heat transfer area, which is influenced by the number and size of tubes. A larger heat transfer area typically leads to better thermal performance. B2B buyers should consider their heating or cooling requirements to select a unit that optimizes energy efficiency while minimizing operational costs.
4. Tolerance and Clearance
Tolerance specifications pertain to the allowable variations in dimensions, which can affect the performance and installation of the heat exchanger. Clearance refers to the space between the tubes and the shell, which can influence the flow dynamics. Accurate tolerances are critical for ensuring proper assembly and operation, thus preventing leaks or efficiency losses.
5. Flow Arrangement
Heat exchangers can utilize various flow arrangements—such as parallel, counterflow, or crossflow—that impact thermal efficiency. Counterflow arrangements are often preferred as they provide higher heat transfer rates. Understanding flow arrangement options helps B2B buyers select the most efficient design for their specific applications.
What Are Common Trade Terms Related to Shell & Tube Heat Exchangers?
Navigating the procurement process for shell & tube heat exchangers involves familiarity with industry jargon. Here are several common terms that B2B buyers should know:
1. OEM (Original Equipment Manufacturer)
An OEM is a company that produces parts and equipment that may be marketed by another manufacturer. Understanding whether your supplier is an OEM can assure quality and compatibility with existing systems, which is crucial for seamless integration and maintenance.
2. MOQ (Minimum Order Quantity)
MOQ refers to the minimum number of units a supplier is willing to sell. Knowing the MOQ helps buyers manage inventory and budgeting effectively, especially in regions where logistics may increase costs.
3. RFQ (Request for Quotation)
An RFQ is a document sent to suppliers to solicit price quotes for specific products or services. Crafting a detailed RFQ ensures that suppliers provide accurate pricing and lead times, which is essential for planning and cost management.
4. Incoterms (International Commercial Terms)
Incoterms are internationally recognized terms that define the responsibilities of buyers and sellers in international transactions. Familiarity with these terms helps buyers understand shipping costs, risks, and delivery obligations, ensuring compliance and reducing potential disputes.
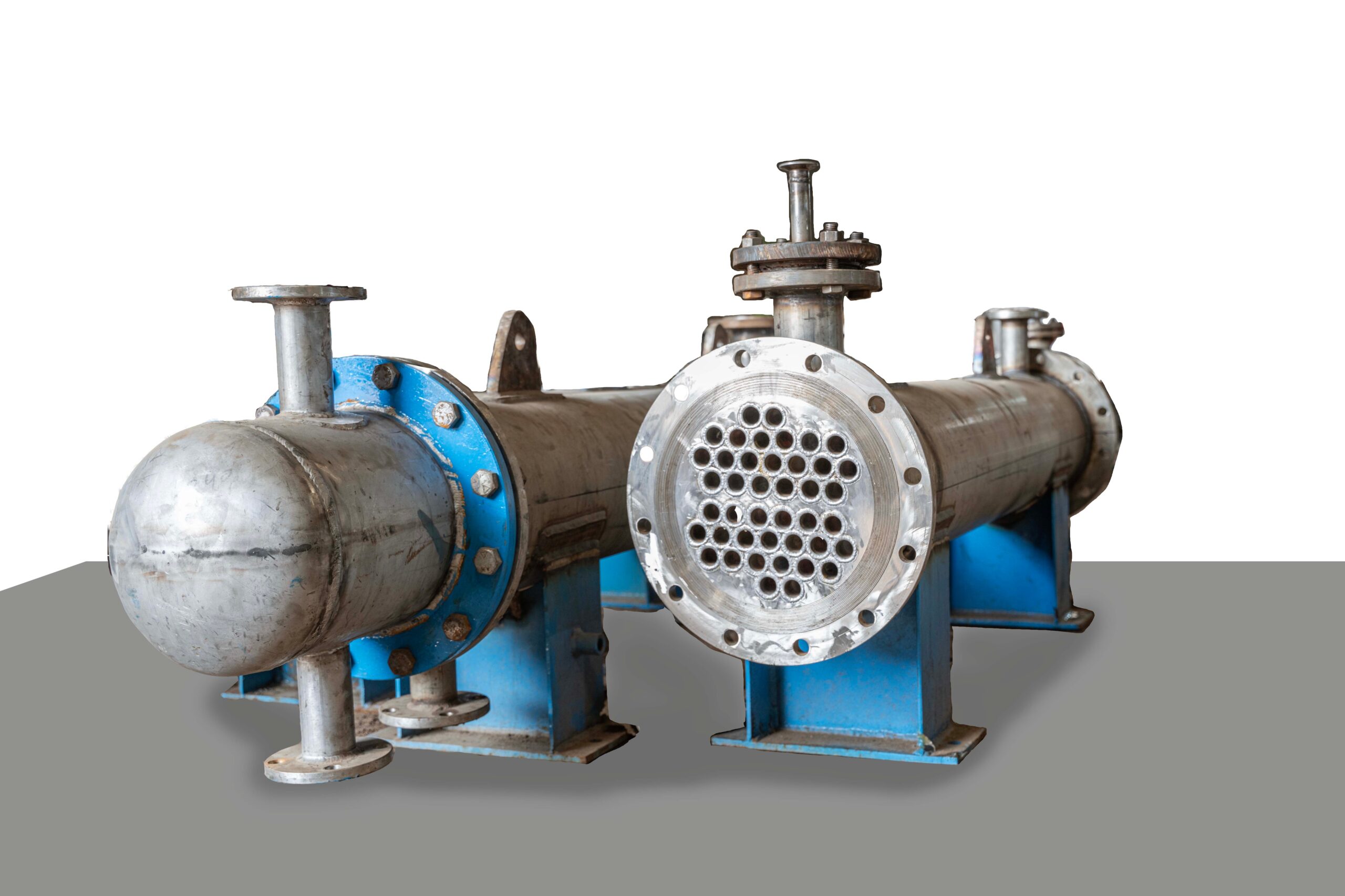
A stock image related to shell & tube type heat exchanger.
5. TEMA (Tubular Exchanger Manufacturers Association) Standards
TEMA standards provide guidelines for the design and manufacture of shell & tube heat exchangers. Familiarity with these standards can help buyers ensure that they are selecting products that meet industry benchmarks for quality and performance.
Understanding these technical properties and trade terms will empower B2B buyers to make informed decisions when procuring shell & tube heat exchangers, ultimately enhancing operational efficiency and reducing costs.
Navigating Market Dynamics and Sourcing Trends in the shell & tube type heat exchanger Sector
What Are the Key Market Dynamics Influencing Shell & Tube Heat Exchangers?
The global shell & tube heat exchanger market is experiencing robust growth driven by several factors. Increasing energy efficiency demands and stringent regulations on emissions are pushing industries to adopt advanced thermal management solutions. Key sectors such as petrochemicals, power generation, and HVAC are particularly influential, with the demand for custom-engineered solutions rising significantly. For international B2B buyers from Africa, South America, the Middle East, and Europe, understanding regional market dynamics is crucial. In Europe, for instance, the push for sustainability is shaping purchasing decisions, while in emerging markets like Africa and South America, the focus is often on cost-effectiveness and reliability.
Moreover, the rise of Industry 4.0 is introducing advanced technologies into sourcing trends. Digital platforms and IoT capabilities are enabling predictive maintenance and real-time monitoring, reducing downtime and optimizing operational efficiencies. As a result, B2B buyers are increasingly seeking suppliers who can provide integrated solutions that combine hardware with smart technology. This trend is particularly relevant in the Middle East, where investment in smart infrastructure is on the rise.
How Is Sustainability Shaping Sourcing Decisions for Shell & Tube Heat Exchangers?
Sustainability is becoming a paramount consideration for B2B buyers in the shell & tube heat exchanger sector. The environmental impact of manufacturing and operating these units is under scrutiny, leading to a growing emphasis on ethical sourcing practices. Buyers are increasingly prioritizing suppliers who demonstrate a commitment to reducing their carbon footprint through the use of renewable materials and energy-efficient processes.
Certifications such as ISO 14001 for environmental management and the use of green materials are becoming essential benchmarks for suppliers. For instance, manufacturers that utilize recyclable alloys or implement waste reduction strategies in their production processes are more likely to attract discerning buyers. Furthermore, the shift towards sustainable design principles is leading to innovations in heat exchanger technology, such as enhanced surface tubes that improve thermal performance while using fewer resources.
As international buyers navigate their sourcing decisions, they should engage with suppliers who offer transparency in their supply chains and can provide documentation on sustainability initiatives. This not only ensures compliance with regulatory standards but also aligns with the ethical expectations of stakeholders.
What Is the Historical Evolution of Shell & Tube Heat Exchangers?
The shell & tube heat exchanger has a rich history, evolving significantly since its inception in the early 20th century. Initially designed for basic heating and cooling applications, advancements in materials science and engineering have transformed these exchangers into sophisticated devices capable of handling extreme temperatures and pressures. The introduction of TEMA standards in the 1950s provided a framework for design and performance, further enhancing their reliability and efficiency.
Over the decades, innovations such as the development of U-tube and floating head designs have expanded the versatility of shell & tube heat exchangers. These enhancements have allowed for easier maintenance and improved thermal performance, making them indispensable in industries ranging from oil and gas to food processing. Today, as industries face new challenges in energy efficiency and sustainability, the evolution of shell & tube heat exchangers continues, driven by the need for more effective and environmentally friendly solutions.
Frequently Asked Questions (FAQs) for B2B Buyers of shell & tube type heat exchanger
-
How do I determine the right shell & tube heat exchanger for my application?
To select the appropriate shell & tube heat exchanger, assess your specific application requirements, including the type of fluids involved (liquid or gas), temperature and pressure conditions, and the heat transfer efficiency needed. Consult with manufacturers about their offerings and ensure they provide units that comply with industry standards, such as TEMA. Additionally, consider factors like maintenance accessibility and the potential for fouling, which can influence your choice between fixed tubesheet, U-tube, or floating head designs. -
What are the common materials used in shell & tube heat exchangers?
Shell & tube heat exchangers can be constructed from various materials depending on the application and operating conditions. Common materials include carbon steel for general applications, stainless steel for corrosive environments, and specialized alloys for high-temperature or high-pressure situations. When sourcing, inquire about the supplier’s material certifications and ensure they meet international standards to guarantee durability and performance. -
What is the typical lead time for ordering a custom shell & tube heat exchanger?
The lead time for a custom shell & tube heat exchanger can vary significantly based on complexity, design specifications, and supplier capabilities. Generally, expect a timeframe of 6 to 12 weeks from order confirmation to delivery. For urgent needs, some suppliers offer expedited services, but this may come at an additional cost. Always discuss timelines upfront with your supplier to align your project schedules. -
What are the minimum order quantities (MOQ) for shell & tube heat exchangers?
Minimum order quantities for shell & tube heat exchangers can vary by manufacturer and product type. While some suppliers may accommodate single units for specialized applications, others might require MOQs of 5 to 10 units for standard models. It’s essential to communicate your needs during the initial discussions and explore options for bulk purchasing, which can often lead to cost savings. -
How do I assess the quality assurance measures of a heat exchanger supplier?
To evaluate a supplier’s quality assurance measures, request information about their certifications (e.g., ISO 9001) and their adherence to industry standards like TEMA. Inquire about their manufacturing processes, inspection methods, and testing protocols for heat exchangers. Additionally, seek references or case studies from previous clients to assess their satisfaction with product quality and after-sales support. -
What payment terms should I expect when purchasing shell & tube heat exchangers?
Payment terms for shell & tube heat exchangers typically vary by supplier and may include options such as full payment upfront, a deposit with balance upon delivery, or net 30/60 days terms for established customers. It’s advisable to negotiate terms that align with your cash flow and project timelines. Always review contracts carefully to understand any penalties for late payments or upfront costs. -
What logistics considerations should I keep in mind when sourcing heat exchangers internationally?
When sourcing shell & tube heat exchangers internationally, consider logistics aspects such as shipping methods, customs clearance, and delivery timelines. Evaluate the supplier’s experience with international shipping and their ability to handle documentation for customs. Additionally, factor in potential tariffs and taxes that may affect the overall cost. It’s prudent to work with a logistics partner familiar with importing industrial equipment to streamline the process. -
Can I customize the design of my shell & tube heat exchanger?
Yes, many manufacturers offer customization options for shell & tube heat exchangers to meet specific operational requirements. Customizations can include size adjustments, material selection, and modifications to enhance thermal performance or facilitate maintenance. When discussing your project with potential suppliers, provide detailed specifications and inquire about their capabilities to ensure they can deliver a product that meets your unique needs.
Important Disclaimer & Terms of Use
⚠️ Important Disclaimer
The information provided in this guide, including content regarding manufacturers, technical specifications, and market analysis, is for informational and educational purposes only. It does not constitute professional procurement advice, financial advice, or legal advice.
While we have made every effort to ensure the accuracy and timeliness of the information, we are not responsible for any errors, omissions, or outdated information. Market conditions, company details, and technical standards are subject to change.
B2B buyers must conduct their own independent and thorough due diligence before making any purchasing decisions. This includes contacting suppliers directly, verifying certifications, requesting samples, and seeking professional consultation. The risk of relying on any information in this guide is borne solely by the reader.
Strategic Sourcing Conclusion and Outlook for shell & tube type heat exchanger
What Are the Key Takeaways for International B2B Buyers?
The strategic sourcing of shell and tube heat exchangers presents significant opportunities for international B2B buyers across Africa, South America, the Middle East, and Europe. Understanding the various types—fixed tubesheet, U-tube, and floating head exchangers—allows buyers to select the most appropriate design for their specific applications, enhancing operational efficiency and reducing long-term costs. Additionally, familiarity with TEMA standards ensures compliance and quality assurance in procurement processes.
How Can Strategic Sourcing Enhance Your Procurement Strategy?
Emphasizing strategic sourcing not only streamlines procurement but also fosters relationships with reliable suppliers. Buyers should evaluate suppliers based on their capabilities to offer customized solutions, including new units, replacement parts, and maintenance services. This holistic approach can mitigate risks associated with equipment failure and ensure sustained performance.
What Does the Future Hold for Shell and Tube Heat Exchangers?
As industries evolve, the demand for efficient thermal management systems will grow. Investing in advanced shell and tube heat exchangers, particularly those with enhanced surface designs for improved thermal performance, will be crucial. B2B buyers are encouraged to explore innovative technologies and sustainable practices in their sourcing strategies.
In conclusion, as global markets become increasingly interconnected, the need for reliable and efficient heat exchangers is paramount. Engage with qualified suppliers today to future-proof your operations and capitalize on emerging trends in heat exchange technology.