The Ultimate Guide to Size Reduction Equipment For Pharmaceutical Industry (2025)
Introduction: Navigating the Global Market for size reduction equipment for pharmaceutical industry
In an increasingly competitive global marketplace, sourcing the right size reduction equipment for the pharmaceutical industry is a critical challenge for B2B buyers. With the demand for high-quality, consistent products rising, selecting machinery that effectively processes raw materials while maintaining strict quality standards becomes paramount. This guide serves as a comprehensive resource, exploring various types of size reduction equipment—including mills, grinders, and pulverizers—alongside their applications, supplier vetting processes, and cost considerations.
International buyers from Africa, South America, the Middle East, and Europe, including regions like Mexico and Spain, will find actionable insights tailored to their unique market dynamics. Understanding the nuances of material properties, desired particle sizes, and operational efficiencies is essential for making informed purchasing decisions. This guide aims to empower you with the knowledge necessary to navigate supplier options, ensuring that you select equipment that aligns with your production needs and regulatory requirements.
By delving into the intricacies of size reduction technology and its implications for pharmaceutical manufacturing, this guide not only simplifies the procurement process but also enhances your operational efficiency and product quality. Equip yourself with the insights needed to thrive in the global market, making strategic choices that propel your business forward.
Understanding size reduction equipment for pharmaceutical industry Types and Variations
Type Name | Key Distinguishing Features | Primary B2B Applications | Brief Pros & Cons for Buyers |
---|---|---|---|
Crushers | Heavy-duty machines for breaking large materials | Initial size reduction in pharmaceuticals | Pros: Efficient for large chunks; Cons: Limited to coarse sizes. |
Grinders | Intermediate to fine grinding capabilities | Producing powders for formulations | Pros: Versatile; can achieve fine particle sizes; Cons: May require multiple passes. |
Pulverizers | Very fine particle size reduction | Creating powders for tablets and capsules | Pros: Essential for uniformity; Cons: Higher energy consumption. |
Cutting Mills | Mechanical cutting of soft to medium-hard materials | Preparation of raw materials in formulations | Pros: Effective for fibrous materials; Cons: Limited for hard materials. |
High Shear Mixers | Emulsification and homogenization of mixtures | Mixing active pharmaceutical ingredients | Pros: Ensures uniformity; Cons: Complexity in operation and maintenance. |
What Are Crushers and Their Role in Size Reduction?
Crushers are robust machines designed to break down large chunks of materials into smaller pieces, making them ideal for the initial stages of size reduction in the pharmaceutical industry. These machines can handle hard materials and are typically used to prepare feed for further processing. When purchasing crushers, B2B buyers should consider factors like the material’s hardness and the desired output size, as well as the machine’s throughput capacity to ensure it meets production demands.
How Do Grinders Contribute to Pharmaceutical Processing?
Grinders are versatile machines that excel in reducing materials to intermediate and fine particle sizes. They are commonly used in the pharmaceutical sector to produce powders necessary for drug formulations. Buyers should evaluate the grinder’s ability to achieve the desired particle fineness and consider whether multiple passes through the machine are needed for optimal results. The choice of grinder can significantly impact product quality and processing efficiency.
Why Are Pulverizers Essential for Pharmaceutical Production?
Pulverizers are designed for achieving very fine particle sizes, which are crucial in pharmaceutical applications where uniformity is paramount. They are particularly effective for creating powders needed in tablet and capsule manufacturing. B2B buyers must consider the energy efficiency and potential wear on components when selecting pulverizers, as these factors can influence operational costs and maintenance requirements.
What Are Cutting Mills and Their Application in the Industry?
Cutting mills utilize mechanical action to cut soft to medium-hard materials, making them suitable for preparing raw materials that require size reduction before formulation. They are particularly effective for fibrous materials, allowing for efficient processing. When purchasing cutting mills, buyers should assess the machine’s capacity and suitability for the specific materials they intend to process, as well as the ease of cleaning and maintenance.
How Do High Shear Mixers Enhance Pharmaceutical Manufacturing?
High shear mixers play a critical role in emulsifying and homogenizing mixtures, ensuring that active pharmaceutical ingredients are uniformly distributed. These mixers are vital for creating consistent formulations, which is essential for product efficacy. Buyers should be aware of the complexity of operation and maintenance associated with high shear mixers, as well as the necessity for precision in controlling mixing parameters to achieve the desired product consistency.
Key Industrial Applications of size reduction equipment for pharmaceutical industry
Industry/Sector | Specific Application of Size Reduction Equipment for Pharmaceutical Industry | Value/Benefit for the Business | Key Sourcing Considerations for this Application |
---|---|---|---|
Pharmaceutical Manufacturing | Grinding active pharmaceutical ingredients (APIs) into fine powders | Enhanced bioavailability and uniformity in dosage forms | Material properties, desired particle size, and equipment compatibility |
Nutraceuticals | Milling herbal extracts for supplement production | Improved extraction efficiency and product consistency | Compliance with regulatory standards and quality control measures |
Biotechnology | Homogenizing cell cultures for vaccine production | Increased yield and consistency in bioprocessing | Equipment scalability, ease of cleaning, and validation processes |
Cosmetics | Reducing particle size of cosmetic ingredients for creams and lotions | Better texture and absorption in end products | Material compatibility, hygiene standards, and energy efficiency |
Research & Development | Preparing samples for analytical testing | Accurate and reproducible results in experiments | Equipment precision, sample feed size adaptability, and ease of use |
How Is Size Reduction Equipment Used in Pharmaceutical Manufacturing?
In pharmaceutical manufacturing, size reduction equipment is vital for grinding active pharmaceutical ingredients (APIs) into fine powders. This process enhances bioavailability, ensuring that drugs are effectively absorbed in the body. For international buyers, particularly from regions like Africa and South America, understanding the material properties and desired particle size is crucial for selecting the right equipment. Compliance with local regulations regarding equipment standards is also a key consideration.
What Role Does Size Reduction Equipment Play in Nutraceuticals?
In the nutraceuticals sector, size reduction equipment is used for milling herbal extracts, significantly improving extraction efficiency and ensuring product consistency. This is particularly important for international B2B buyers in the Middle East and Europe, who must adhere to stringent quality control measures and regulatory standards. Buyers should focus on sourcing equipment that can handle diverse materials while maintaining the integrity of active compounds.
How Does Size Reduction Equipment Benefit Biotechnology?
Biotechnology applications, such as vaccine production, utilize size reduction equipment for homogenizing cell cultures. This process increases yield and consistency in bioprocessing, which is critical for meeting production demands. Buyers from Europe and Africa should consider equipment scalability and ease of cleaning to ensure compliance with stringent biomanufacturing standards. Validation processes must also be a priority when selecting suitable machinery.
What Is the Importance of Size Reduction in Cosmetics?
In the cosmetics industry, size reduction equipment is essential for reducing the particle size of ingredients used in creams and lotions. This results in better texture and absorption in final products, enhancing customer satisfaction. Buyers from South America and the Middle East should prioritize sourcing equipment that meets hygiene standards and is compatible with various materials to ensure high-quality formulations.
How Is Size Reduction Equipment Used in Research & Development?
In research and development, size reduction equipment is crucial for preparing samples for analytical testing. It ensures accurate and reproducible results, which are vital for product development and quality assurance. International buyers should look for equipment that offers precision and adaptability to different sample feed sizes. Additionally, ease of use is an important factor to facilitate efficient laboratory workflows.
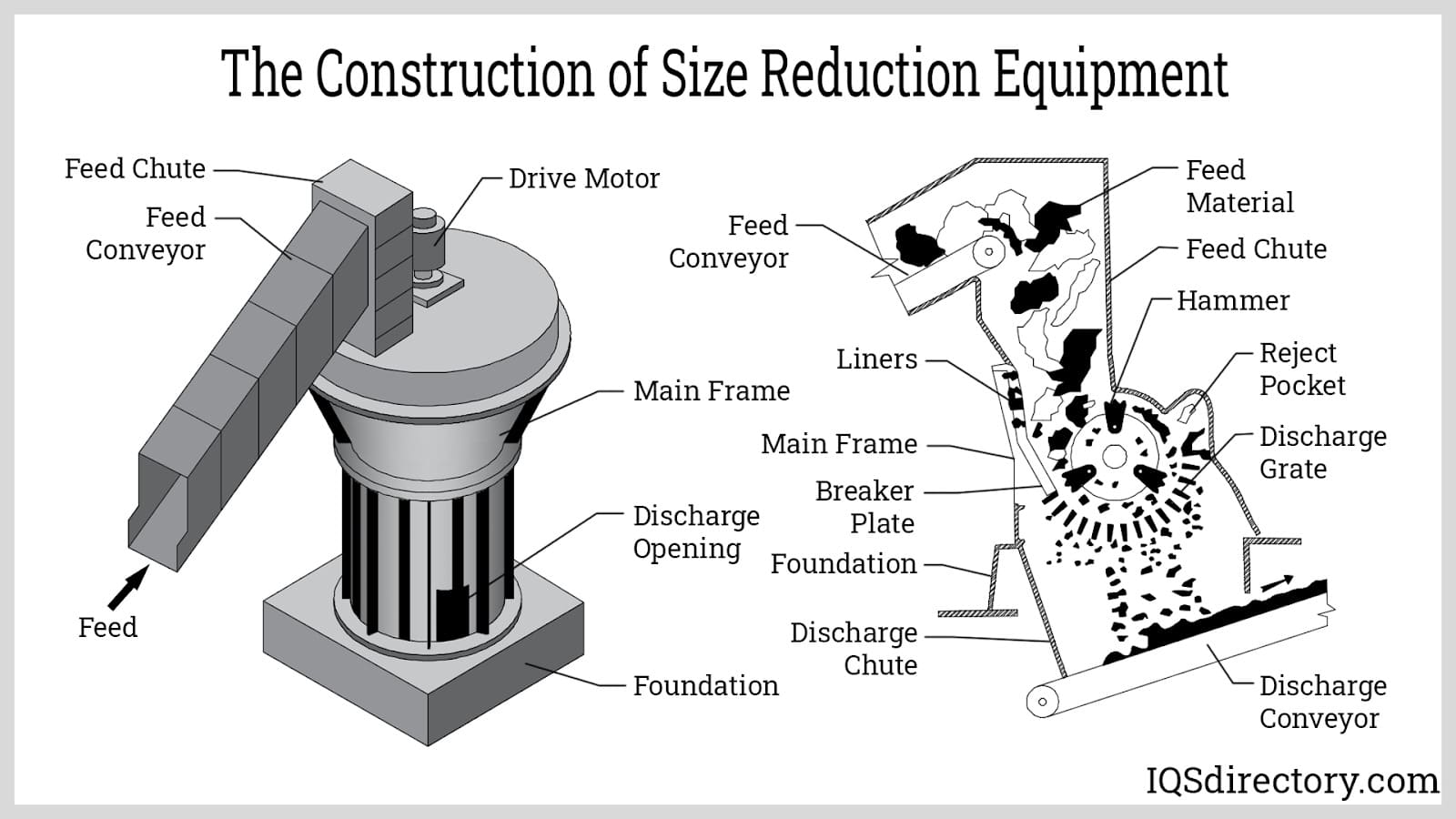
A stock image related to size reduction equipment for pharmaceutical industry.
3 Common User Pain Points for ‘size reduction equipment for pharmaceutical industry’ & Their Solutions
Scenario 1: Difficulty in Achieving Consistent Particle Size Distribution
The Problem:
B2B buyers in the pharmaceutical industry often grapple with the challenge of achieving a consistent particle size distribution when using size reduction equipment. This inconsistency can lead to variations in the dissolution rates of active pharmaceutical ingredients (APIs), impacting both efficacy and regulatory compliance. Buyers may find themselves frustrated when different batches of material yield varying particle sizes, forcing them to conduct additional testing or rework processes, which increases costs and time.
The Solution:
To address this issue, it is crucial to invest in high-quality, precision-engineered size reduction equipment that is tailored to the specific materials being processed. Buyers should conduct a thorough assessment of their materials, focusing on properties such as hardness, moisture content, and friability. Utilizing advanced milling technologies like air jet mills or roller mills can ensure that the desired particle size is achieved consistently. Additionally, incorporating inline particle size analysis tools can provide real-time feedback, allowing for immediate adjustments to milling parameters. Buyers should also establish a robust quality control protocol that includes regular calibration of equipment to maintain performance standards.
Scenario 2: Equipment Downtime and Maintenance Costs
The Problem:
Frequent breakdowns and high maintenance costs associated with size reduction equipment can severely impact production schedules in the pharmaceutical industry. Buyers often face the dilemma of choosing between lower-cost equipment that may lack durability and higher-end machines that promise longevity but come with a hefty price tag. This creates an ongoing struggle to balance initial investment with operational efficiency, ultimately leading to productivity losses and increased overhead.
The Solution:
To mitigate these challenges, buyers should prioritize sourcing equipment from reputable manufacturers known for durability and reliability. Conducting a lifecycle cost analysis before purchasing can provide insights into long-term savings versus initial costs. Moreover, implementing a proactive maintenance strategy is essential. This includes scheduling regular maintenance checks and employing predictive maintenance technologies that utilize IoT sensors to monitor equipment health. By investing in training for operators on proper equipment use and maintenance, organizations can significantly reduce the risk of downtime caused by user error. Establishing a relationship with suppliers for ongoing support and spare parts availability can also ensure that any issues are addressed swiftly, minimizing disruptions.
Scenario 3: Regulatory Compliance Challenges
The Problem:
The pharmaceutical industry is heavily regulated, with stringent guidelines governing the manufacturing processes, including size reduction. Buyers often struggle with ensuring that their equipment meets local and international regulatory standards. Non-compliance can lead to costly fines, product recalls, and damage to brand reputation. Many buyers may feel overwhelmed by the complexity of these regulations and the need for equipment that can adapt to changing compliance requirements.
The Solution:
To navigate regulatory compliance, it is essential for buyers to thoroughly research and understand the relevant guidelines applicable in their region, such as those set forth by the FDA in the United States or EMA in Europe. Selecting size reduction equipment that is designed with compliance in mind is crucial. Buyers should look for features such as easy cleaning capabilities, validation documentation, and materials that meet sanitary standards. Engaging with suppliers who offer equipment that has been certified for compliance can simplify the procurement process. Additionally, investing in training for staff on compliance standards and best practices will ensure that everyone involved in the production process is aware of their responsibilities. Regular audits and continuous improvement initiatives can further solidify compliance and enhance overall product quality.
Strategic Material Selection Guide for size reduction equipment for pharmaceutical industry
What Are the Key Materials for Size Reduction Equipment in the Pharmaceutical Industry?
Selecting the right materials for size reduction equipment is crucial in the pharmaceutical industry, as it directly affects product quality, compliance, and operational efficiency. Below are analyses of four common materials used in size reduction equipment, focusing on their properties, advantages, disadvantages, and considerations for international B2B buyers.
Stainless Steel: The Industry Standard for Durability and Corrosion Resistance
Key Properties: Stainless steel is renowned for its excellent corrosion resistance, high-temperature tolerance, and mechanical strength. It is often rated for temperatures up to 500°F (260°C) and can withstand various pressures, making it suitable for diverse pharmaceutical applications.
Pros & Cons: The primary advantage of stainless steel is its durability and resistance to rust and corrosion, which is critical in maintaining hygiene and product integrity. However, it can be more expensive than other materials, and the manufacturing process may involve complex machining, which can increase lead times.
Impact on Application: Stainless steel is compatible with most pharmaceutical media, ensuring that it does not react with active ingredients. Its non-porous surface also facilitates easy cleaning and maintenance, essential for compliance with strict pharmaceutical standards.
Considerations for International Buyers: Buyers from regions like Africa, South America, the Middle East, and Europe should ensure that the stainless steel used meets international standards such as ASTM A240 or EN 10088. Compliance with local regulations regarding material safety and hygiene is also crucial.
Carbon Steel: A Cost-Effective Alternative with Limitations
Key Properties: Carbon steel is known for its high tensile strength and ability to withstand mechanical stress. However, it is less resistant to corrosion and may require protective coatings or treatments to enhance its durability.
Pros & Cons: The main advantage of carbon steel is its lower cost compared to stainless steel, making it an attractive option for budget-conscious buyers. However, its susceptibility to rust and corrosion can pose risks in pharmaceutical applications, potentially compromising product quality.
Impact on Application: Carbon steel is suitable for dry materials but may not be ideal for wet processes or products sensitive to contamination. Buyers must consider the nature of their materials when opting for carbon steel.
Considerations for International Buyers: Compliance with standards such as ASTM A36 is essential. Additionally, buyers should evaluate the need for protective coatings to ensure compatibility with pharmaceutical media, especially in humid environments.
Polypropylene: A Versatile Plastic Option for Specific Applications
Key Properties: Polypropylene is a lightweight, chemically resistant plastic that can withstand temperatures up to 200°F (93°C). It is often used in applications requiring a non-reactive surface.
Pros & Cons: The key advantage of polypropylene is its resistance to a wide range of chemicals, making it suitable for various pharmaceutical applications. However, its lower temperature tolerance compared to metals may limit its use in high-heat processes.
Impact on Application: Polypropylene is ideal for applications involving corrosive substances, as it does not leach harmful chemicals into the product. However, its mechanical strength is inferior to metals, which may affect its longevity in high-stress environments.
Considerations for International Buyers: Buyers should verify compliance with standards such as FDA regulations for materials in contact with pharmaceuticals. Understanding local regulations regarding plastic materials is also critical.
Ceramic: High Performance for Specific Size Reduction Needs
Key Properties: Ceramic materials are known for their hardness and wear resistance, making them suitable for grinding and milling applications. They can withstand high temperatures and are chemically inert.
Pros & Cons: The primary advantage of ceramics is their longevity and ability to maintain sharp edges, which enhances performance in size reduction. However, ceramics can be brittle and may break under excessive mechanical stress, leading to higher replacement costs.
Impact on Application: Ceramics are ideal for grinding hard materials and are often used in processes requiring high precision. Their inert nature ensures that they do not contaminate pharmaceutical products.
Considerations for International Buyers: Buyers must ensure that ceramic materials comply with relevant standards, such as ISO 12647 for manufacturing processes. Understanding the specific application requirements is essential to avoid issues related to brittleness.
Summary Table of Material Selections
Material | Typical Use Case for Size Reduction Equipment for Pharmaceutical Industry | Key Advantage | Key Disadvantage/Limitation | Relative Cost (Low/Med/High) |
---|---|---|---|---|
Stainless Steel | General size reduction of various pharmaceutical products | Excellent corrosion resistance | Higher cost and complex machining | High |
Carbon Steel | Cost-effective size reduction for dry materials | Lower cost | Susceptible to rust and corrosion | Medium |
Polypropylene | Non-reactive applications for sensitive materials | Chemical resistance | Limited temperature tolerance | Low |
Ceramic | Grinding hard materials requiring precision | High wear resistance | Brittle and can break under stress | Medium |
By understanding these materials’ properties, advantages, and limitations, international B2B buyers can make informed decisions that align with their operational needs and compliance requirements in the pharmaceutical industry.
In-depth Look: Manufacturing Processes and Quality Assurance for size reduction equipment for pharmaceutical industry
What Are the Main Stages of Manufacturing Size Reduction Equipment for the Pharmaceutical Industry?
The manufacturing process of size reduction equipment for the pharmaceutical industry encompasses several key stages: material preparation, forming, assembly, and finishing. Each stage requires meticulous attention to detail to ensure that the final product meets stringent industry standards.
How Is Material Prepared for Size Reduction Equipment?
Material preparation begins with the careful selection of raw materials, which must meet specific criteria for durability, resistance to corrosion, and compatibility with pharmaceutical substances. Common materials include stainless steel and high-grade plastics, which are selected for their ability to withstand harsh cleaning processes and minimize contamination risks.
Once selected, the materials undergo pre-treatment processes, such as cutting and surface finishing, to prepare them for forming. This stage may include grinding or milling the raw materials into smaller, manageable sizes, ensuring uniformity and consistency.
What Techniques Are Used in Forming Size Reduction Equipment?
The forming stage involves various techniques, including casting, machining, and welding. Each technique is chosen based on the design specifications and the type of equipment being manufactured.
- Casting: This method is often used for creating complex shapes that are difficult to achieve through machining. It is essential for producing components like hoppers and casings.
- Machining: Precision machining is critical in shaping components to exact specifications, especially for parts that require tight tolerances, such as rotors and stators in high shear mixers.
- Welding: For parts that need to be assembled into larger structures, welding techniques ensure structural integrity while maintaining the properties of the materials used.
How Is Assembly Conducted for Size Reduction Equipment?
The assembly stage integrates various components into a complete system. This process typically involves:
- Component Alignment: Each component must be precisely aligned to ensure optimal performance and minimize wear during operation.
- Fastening: Using screws, bolts, or welding, components are securely fastened to withstand operational stresses.
- Integration of Controls: Modern size reduction equipment often includes electronic controls for monitoring and adjusting settings. These systems must be integrated seamlessly into the mechanical components.
What Finishing Techniques Are Applied to Size Reduction Equipment?
Finishing processes enhance the durability and aesthetic appeal of the equipment. Common techniques include:
- Surface Treatment: Processes like passivation and electropolishing are used to improve corrosion resistance and reduce contamination risks.
- Coating: Applying protective coatings can enhance wear resistance and facilitate cleaning, which is vital in the pharmaceutical industry.
- Quality Inspection: After finishing, each piece undergoes rigorous inspection to ensure that it meets quality and safety standards.
What Quality Assurance Standards Are Relevant for Size Reduction Equipment?
Quality assurance (QA) is paramount in the manufacturing of size reduction equipment for the pharmaceutical industry. Compliance with international standards, such as ISO 9001, ensures that manufacturers maintain a quality management system that enhances customer satisfaction and product quality.
How Do Industry-Specific Standards Like CE and API Impact Quality Assurance?
In addition to ISO standards, equipment designed for the pharmaceutical sector must also adhere to industry-specific standards. The CE mark indicates compliance with European safety, health, and environmental protection standards, while API (American Petroleum Institute) certifications may apply to certain types of machinery used in the processing of pharmaceuticals.
What Are the Key Quality Control Checkpoints in Manufacturing?
Effective quality control (QC) involves several checkpoints throughout the manufacturing process:
- Incoming Quality Control (IQC): Raw materials are inspected upon arrival to ensure they meet specified standards.
- In-Process Quality Control (IPQC): Ongoing checks during manufacturing help identify defects early, reducing waste and rework.
- Final Quality Control (FQC): The finished equipment undergoes comprehensive testing to ensure it meets all design specifications and regulatory requirements.
What Testing Methods Are Commonly Used in Quality Assurance?
Common testing methods for size reduction equipment include:
- Performance Testing: Evaluating the equipment’s ability to reduce particle size effectively under specified conditions.
- Durability Testing: Assessing how well the equipment withstands operational stresses over time.
- Cleaning Validation: Ensuring that the equipment can be cleaned effectively to prevent contamination.
How Can B2B Buyers Verify Supplier Quality Control?
For international B2B buyers, particularly those in Africa, South America, the Middle East, and Europe, verifying a supplier’s quality control processes is crucial. Here are actionable steps to consider:
- Supplier Audits: Conducting on-site audits allows buyers to evaluate the supplier’s manufacturing practices, quality management systems, and compliance with relevant standards.
- Requesting Quality Reports: Buyers should ask for detailed QC reports that outline testing results, compliance with standards, and corrective actions taken in case of deviations.
- Third-Party Inspections: Engaging third-party inspection services can provide unbiased evaluations of the supplier’s quality assurance processes and product reliability.
What Nuances Should International Buyers Consider Regarding Quality Control?
International buyers need to be aware of specific nuances in quality control that can affect their purchasing decisions:
- Regulatory Differences: Different regions may have varying regulations regarding pharmaceutical manufacturing. Understanding these can help buyers ensure compliance in their local markets.
- Cultural Factors: Cultural attitudes towards quality and safety can differ significantly. Building strong relationships with suppliers can facilitate better communication regarding quality expectations.
- Logistical Considerations: When sourcing from abroad, logistical challenges can affect quality. Buyers should consider the implications of transport, storage, and handling on the equipment’s integrity.
In summary, a comprehensive understanding of the manufacturing processes and quality assurance practices for size reduction equipment is essential for international B2B buyers in the pharmaceutical industry. By focusing on these areas, buyers can make informed decisions that enhance their operational efficiency and product quality.
Practical Sourcing Guide: A Step-by-Step Checklist for ‘size reduction equipment for pharmaceutical industry’
In the pharmaceutical industry, the procurement of size reduction equipment is essential for ensuring product quality, efficiency, and compliance with regulatory standards. This step-by-step guide is designed to assist international B2B buyers from regions such as Africa, South America, the Middle East, and Europe in sourcing the right equipment effectively.
Step 1: Define Your Technical Specifications
Begin by clearly outlining the technical requirements of the size reduction equipment needed for your specific applications. Consider factors such as the type of material (hard, soft, fibrous), desired particle size, and throughput requirements. Documenting these specifications ensures that suppliers understand your needs and can provide suitable solutions.
- Material Properties: Understand the hardness, moisture content, and abrasiveness of the materials you will be processing.
- Particle Size Requirements: Specify the final fineness you need to achieve, which will guide the selection of appropriate machinery.
Step 2: Conduct Market Research on Equipment Types
Different types of size reduction equipment serve varying functions. Conduct thorough market research to identify which equipment—such as crushers, grinders, or pulverizers—best fits your needs. Understanding the available options allows you to make informed decisions.
- Types of Equipment: Familiarize yourself with equipment like ball mills for fine grinding or high shear mixers for emulsifying materials.
- Applications: Investigate how similar companies in your industry utilize specific equipment for their processes.
Step 3: Evaluate Potential Suppliers
Before making a purchase, it’s crucial to vet suppliers thoroughly. Look for suppliers with a proven track record in the pharmaceutical sector, as they will be more attuned to industry-specific requirements and standards.
- Request Documentation: Ask for company profiles, product certifications, and case studies from previous clients.
- Check References: Reach out to other businesses in your region that have purchased similar equipment to gauge supplier reliability and service quality.
Step 4: Verify Compliance with Regulatory Standards
Pharmaceutical manufacturing is heavily regulated. Ensure that the equipment meets all relevant compliance standards, such as GMP (Good Manufacturing Practices) and FDA regulations, to avoid costly delays or fines.
- Certification Verification: Request documentation proving that the equipment complies with international safety and quality standards.
- Supplier Reputation: Investigate the supplier’s history with regulatory bodies and their ability to provide compliant equipment.
Step 5: Assess After-Sales Support and Training
After-sales support is vital for maintaining equipment efficiency and longevity. Evaluate the level of support offered by the supplier, including training for your staff on equipment operation and maintenance.
- Training Programs: Ensure the supplier provides comprehensive training sessions to familiarize your team with the equipment.
- Maintenance Services: Inquire about the availability of ongoing support and maintenance contracts to keep the machinery in optimal condition.
Step 6: Compare Costs and Financing Options
Cost is a critical factor in procurement. Compare not only the purchase price but also the total cost of ownership, including installation, maintenance, and operational expenses. Explore financing options that may be available to spread the cost over time.
- Total Cost of Ownership: Consider all associated costs to avoid unexpected expenses later.
- Financing Solutions: Look for suppliers offering flexible payment terms or leasing options that align with your budget.
Step 7: Make an Informed Decision
After gathering all necessary information and evaluating your options, make a well-informed decision. Consider all aspects, including technical specifications, supplier reliability, compliance, support, and cost, to choose the best equipment for your needs.
- Final Evaluation: Review all gathered data and feedback from your team to ensure a consensus on the best choice.
- Contract Review: Before signing, ensure that all terms, warranties, and service agreements are clearly outlined in the contract.
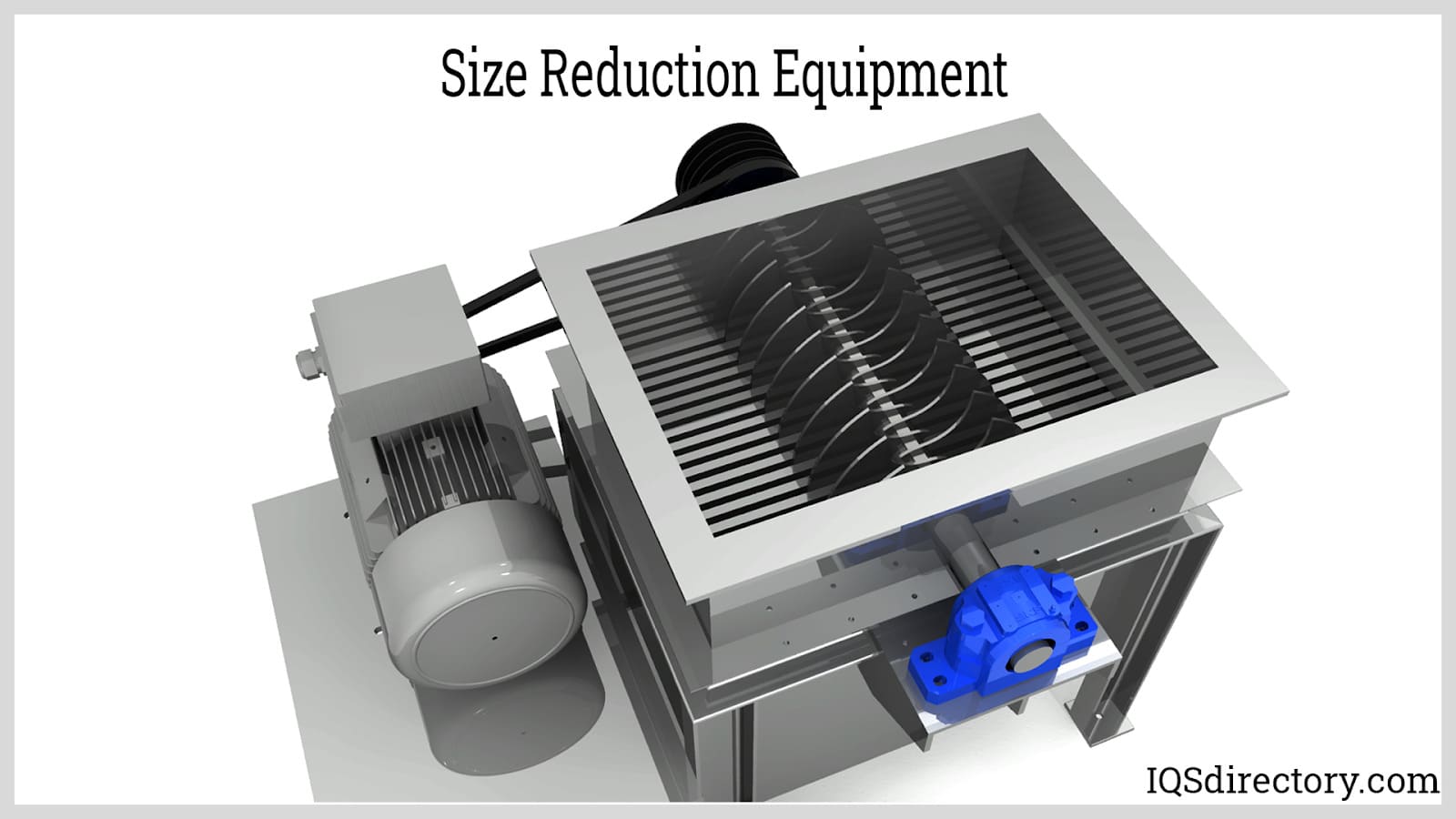
A stock image related to size reduction equipment for pharmaceutical industry.
By following this comprehensive checklist, B2B buyers in the pharmaceutical industry can successfully navigate the procurement process for size reduction equipment, ensuring they select the best solutions tailored to their specific needs.
Comprehensive Cost and Pricing Analysis for size reduction equipment for pharmaceutical industry Sourcing
What Are the Key Cost Components in Sourcing Size Reduction Equipment for the Pharmaceutical Industry?
When evaluating the costs associated with size reduction equipment, several critical components come into play. The primary cost components include:
-
Materials: The type of raw materials used in manufacturing the equipment significantly influences the overall cost. Higher-grade materials, such as stainless steel or specialized alloys, often come at a premium but offer better durability and compliance with pharmaceutical standards.
-
Labor: Labor costs encompass both direct labor involved in manufacturing and indirect labor associated with design, engineering, and support roles. Skilled labor is essential for precision engineering, particularly in custom equipment tailored to specific pharmaceutical applications.
-
Manufacturing Overhead: This includes expenses such as utilities, depreciation of equipment, and facility costs. Efficient manufacturing processes can help minimize these overheads, thereby reducing the overall cost of the equipment.
-
Tooling: Tooling costs relate to the necessary molds and dies used in the manufacturing process. Custom tooling can increase initial costs but may lead to better fitting and more efficient production runs.
-
Quality Control (QC): In the pharmaceutical industry, stringent QC measures are essential to ensure compliance with regulatory standards. The costs associated with testing, certification, and documentation can be substantial but are critical for maintaining product integrity.
-
Logistics: Shipping and handling costs must also be factored in, particularly for international shipments. These costs can vary widely based on the destination, shipment size, and chosen logistics provider.
-
Margin: Suppliers typically add a margin to their costs, which can vary based on their market position, reputation, and the level of service they provide.
How Do Volume and Customization Affect Pricing for Size Reduction Equipment?
Pricing for size reduction equipment can be heavily influenced by order volume and customization requirements.
-
Volume/MOQ (Minimum Order Quantity): Bulk orders generally lead to lower per-unit costs. Suppliers often provide discounts for larger orders, making it more cost-effective for buyers planning extensive use of the equipment.
-
Specifications and Customization: Custom equipment designed to meet specific application needs may incur additional costs. Buyers should clearly communicate their specifications to receive accurate quotes. Customization can include adjustments in size, material, and functionality, which can lead to variations in pricing.
What Factors Should International B2B Buyers Consider When Sourcing Size Reduction Equipment?
International buyers, particularly from regions such as Africa, South America, the Middle East, and Europe, should consider several factors that can influence their purchasing decisions:
-
Supplier Factors: Assessing the supplier’s reputation, experience, and past performance is crucial. Suppliers with a history of delivering high-quality, reliable equipment may command higher prices, but the investment is often justified by reduced downtime and maintenance costs.
-
Quality and Certifications: Compliance with international standards (e.g., ISO, GMP) is essential in the pharmaceutical industry. Equipment that meets these certifications may have higher upfront costs but can save buyers from costly compliance issues down the line.
-
Incoterms: Understanding the agreed terms of shipping and delivery is vital. Different Incoterms can significantly affect the total landed cost of the equipment, including insurance, freight, and customs duties.
What Are Effective Negotiation and Cost-Efficiency Strategies for Buyers?
To achieve cost efficiency and favorable pricing, buyers should employ strategic negotiation techniques:
-
Total Cost of Ownership (TCO): Buyers should consider not just the initial purchase price but the total cost of ownership, which includes maintenance, operational costs, and potential downtime. Equipment that is slightly more expensive upfront may prove more economical over its lifespan.
-
Leverage Relationships: Building long-term relationships with suppliers can lead to better pricing and terms. Suppliers may be more willing to offer discounts or favorable terms to loyal customers.
-
Market Research: Conduct thorough market research to understand prevailing prices and trends. This knowledge can empower buyers during negotiations, helping them to identify fair pricing benchmarks.
Disclaimer on Indicative Prices
It is important to note that prices for size reduction equipment can vary widely based on specific requirements, market conditions, and supplier negotiations. Buyers should seek detailed quotes tailored to their unique needs and circumstances.
Alternatives Analysis: Comparing size reduction equipment for pharmaceutical industry With Other Solutions
Understanding Alternatives to Size Reduction Equipment in the Pharmaceutical Industry
In the pharmaceutical sector, the need for effective size reduction is critical for achieving desired product characteristics, enhancing bioavailability, and optimizing manufacturing processes. While traditional size reduction equipment, such as mills and grinders, is widely used, several alternative technologies can also achieve similar objectives. This analysis will provide a comparative overview to help international B2B buyers identify the best solution for their specific needs.
Comparison of Size Reduction Solutions
Comparison Aspect | Size Reduction Equipment For Pharmaceutical Industry | Alternative 1: High Shear Mixers | Alternative 2: Ultrasound-assisted Extraction |
---|---|---|---|
Performance | High efficiency in producing fine particles; customizable for various materials | Excellent for emulsification and uniform mixing; not primarily focused on particle size | Effective for extracting compounds from solids; can reduce particle size indirectly |
Cost | Varies widely based on type and capacity; initial investment can be high | Moderate cost; may require additional equipment for particle size reduction | Generally lower cost; equipment is often versatile for other applications |
Ease of Implementation | Requires specialized setup and training; longer installation times | Easier to integrate into existing processes; quicker to operate | Simple setup; often compatible with existing workflows |
Maintenance | Regular maintenance required for optimal performance; parts can be costly | Low to moderate maintenance; fewer moving parts | Minimal maintenance required; easy to clean and operate |
Best Use Case | Ideal for high-volume production requiring precise particle size | Best for formulations requiring emulsification and homogenization | Suitable for extracting active ingredients from solid materials with minimal size reduction needs |
Pros and Cons of Each Alternative
What are the advantages and disadvantages of High Shear Mixers?
High shear mixers excel in applications where emulsification and uniform mixing are essential, making them a valuable tool in pharmaceutical formulations. They can produce consistent mixtures quickly, allowing for efficient processing. However, they are not primarily designed for size reduction, which may necessitate additional equipment to achieve the desired particle size. This could lead to increased capital investment and operational complexity.
How does Ultrasound-assisted Extraction compare?
Ultrasound-assisted extraction is a cost-effective method that leverages ultrasonic waves to enhance the extraction of compounds from solid matrices. This technique can indirectly lead to size reduction by breaking down cell walls and facilitating the release of active ingredients. Its simplicity and versatility make it appealing for companies looking to optimize processes without significant investment. However, it may not provide the same level of particle size control as dedicated size reduction equipment, which could impact product quality in certain applications.
Conclusion: How to Choose the Right Size Reduction Solution for Your Needs
Selecting the appropriate size reduction technology depends on various factors including the specific requirements of the pharmaceutical products being developed, budget constraints, and operational capabilities. B2B buyers should conduct a thorough analysis of their production needs, considering both the advantages and limitations of each alternative. Engaging with equipment suppliers for demonstrations and assessments can also provide valuable insights, helping ensure that the chosen solution aligns with the strategic goals of the organization. Ultimately, the right choice will enhance efficiency, product quality, and profitability in the competitive pharmaceutical landscape.
Essential Technical Properties and Trade Terminology for size reduction equipment for pharmaceutical industry
What Are the Key Technical Properties of Size Reduction Equipment in the Pharmaceutical Industry?
When selecting size reduction equipment for the pharmaceutical sector, understanding the technical specifications is crucial for ensuring operational efficiency and product quality. Here are essential properties to consider:
-
Material Grade
The material used in the construction of size reduction machinery (such as stainless steel or special alloys) directly impacts durability, corrosion resistance, and compliance with pharmaceutical regulations. Equipment made from high-grade materials ensures long-term performance and minimizes contamination risks. -
Particle Size Distribution (PSD)
This specification defines the range and frequency of particle sizes produced by the equipment. In pharmaceuticals, achieving a specific PSD is vital for drug efficacy and bioavailability. Equipment must be capable of producing consistent and uniform particle sizes to meet stringent industry standards. -
Capacity and Throughput
The capacity refers to the volume of material the equipment can process within a specific time frame. Understanding the throughput is essential for aligning equipment capabilities with production demands, ensuring that the size reduction process does not become a bottleneck in the manufacturing workflow. -
Power Consumption and Efficiency
Evaluating the power requirements and energy efficiency of size reduction equipment is essential for cost management. Energy-efficient machines not only reduce operational costs but also contribute to sustainable practices, which are increasingly important in global markets. -
Tolerance Levels
Tolerance indicates the acceptable variations in size and dimensions of the output particles. In pharmaceutical applications, tight tolerances are critical to ensure consistent dosage and effectiveness of the final product. Equipment with precise tolerances minimizes waste and rework. -
Cleaning and Maintenance Features
The ease of cleaning and maintenance is a vital property, especially in the pharmaceutical industry where hygiene is paramount. Equipment designed for quick disassembly and effective cleaning can significantly reduce downtime and improve compliance with regulatory standards.
What Are Common Trade Terms Used in Size Reduction Equipment Transactions?
Navigating the procurement of size reduction equipment involves familiarity with industry jargon. Here are some key terms:
-
OEM (Original Equipment Manufacturer)
An OEM refers to a company that produces parts or equipment that may be marketed by another manufacturer. For buyers, engaging with reputable OEMs ensures quality and reliability in the equipment purchased. -
MOQ (Minimum Order Quantity)
MOQ specifies the smallest quantity of a product that a supplier is willing to sell. Understanding MOQ is crucial for international buyers to manage inventory levels and minimize overstock costs. -
RFQ (Request for Quotation)
An RFQ is a document issued by a buyer to solicit price offers from suppliers for specific equipment or services. It is an essential step in the procurement process, allowing buyers to compare costs and features from different suppliers. -
Incoterms (International Commercial Terms)
These are standardized trade terms that define the responsibilities of buyers and sellers in international transactions. Familiarity with Incoterms helps buyers understand shipping costs, risks, and delivery obligations, which can significantly influence total acquisition costs. -
Lead Time
Lead time refers to the period from placing an order to receiving the equipment. Knowledge of lead times is critical for planning and ensuring that production schedules are met without delays.
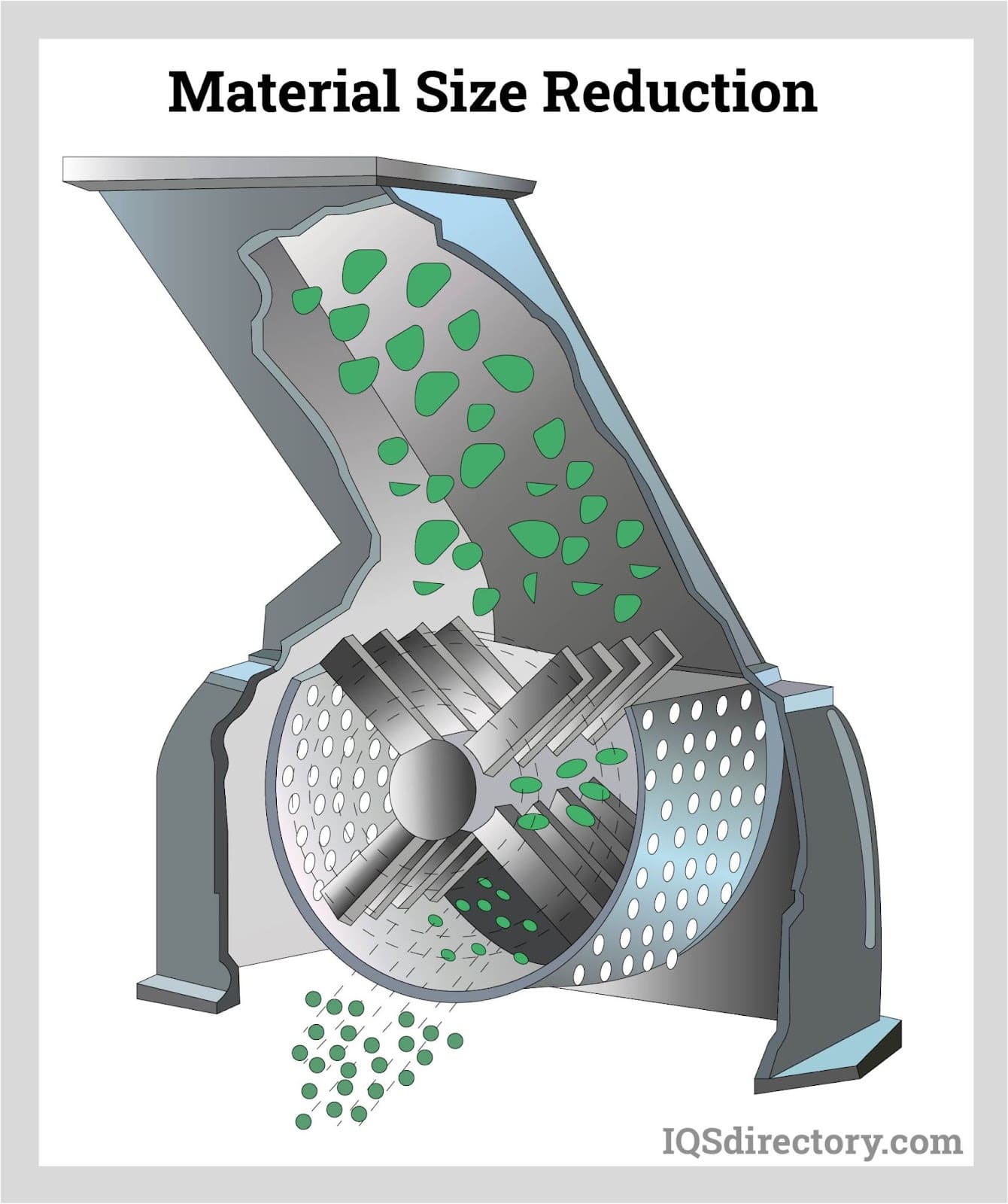
A stock image related to size reduction equipment for pharmaceutical industry.
- Warranty and Service Agreements
These terms outline the support provided by the manufacturer post-purchase, including repairs, maintenance, and replacement of parts. Understanding warranty terms helps buyers assess the long-term value and reliability of the equipment.
By grasping these technical properties and trade terms, international B2B buyers can make informed decisions when sourcing size reduction equipment for the pharmaceutical industry, ultimately leading to more efficient operations and enhanced product quality.
Navigating Market Dynamics and Sourcing Trends in the size reduction equipment for pharmaceutical industry Sector
What Are the Current Market Dynamics and Key Trends in Size Reduction Equipment for the Pharmaceutical Industry?
The global size reduction equipment market for the pharmaceutical industry is witnessing significant growth driven by several factors. Increased demand for high-quality pharmaceuticals, particularly in emerging markets across Africa, South America, and the Middle East, is propelling manufacturers to invest in advanced size reduction technologies. Enhanced focus on efficient production processes and product quality has led to the adoption of high-shear mixers, pulverizers, and cutting mills that improve the consistency and effectiveness of drug formulations.
Furthermore, the rise of personalized medicine is fostering a demand for flexible and scalable production capabilities. B2B buyers are increasingly looking for equipment that can easily adapt to varying batch sizes and formulations. Technological advancements such as automation and data integration in machinery are also becoming crucial for optimizing production efficiency and ensuring compliance with regulatory standards. For international buyers, particularly from regions like Europe and Latin America, understanding these trends is vital for making informed purchasing decisions.
The market is also influenced by the growing emphasis on sustainability and ethical sourcing. Buyers are increasingly prioritizing suppliers who demonstrate a commitment to environmentally friendly practices and materials, which is reshaping sourcing strategies. This shift is particularly pronounced in regions such as Spain and Mexico, where regulatory frameworks and consumer expectations are driving the demand for sustainable manufacturing practices.
How Is Sustainability Impacting Sourcing Trends in Size Reduction Equipment?
Sustainability is becoming a cornerstone of sourcing strategies in the pharmaceutical sector, significantly impacting the choice of size reduction equipment. The environmental impact of manufacturing processes has led to a greater focus on energy-efficient and low-emission technologies. Equipment manufacturers are responding by developing machines that minimize waste and energy consumption, appealing to B2B buyers who prioritize eco-friendly solutions.
Ethical sourcing is also gaining traction, with businesses increasingly scrutinizing their supply chains to ensure compliance with environmental regulations and social responsibility standards. This shift is prompting buyers to seek out suppliers who can provide certifications for green materials and processes, such as ISO 14001 for environmental management systems or other relevant eco-labels. In regions like Africa and the Middle East, where regulatory environments are evolving, the pressure for ethical sourcing is becoming more pronounced.
Moreover, the use of recyclable materials in the manufacturing of size reduction equipment is a growing trend. By opting for equipment made from sustainable materials, buyers can not only reduce their carbon footprint but also align their operations with the global push for a circular economy. This alignment is particularly important for pharmaceutical companies that are increasingly held accountable for their environmental impact.
How Has the Size Reduction Equipment Market Evolved Over Time?
The evolution of size reduction equipment in the pharmaceutical industry reflects broader technological advancements and changing market needs. Initially, size reduction processes were predominantly manual and labor-intensive, relying on basic mechanical devices. However, as the pharmaceutical industry grew and regulatory demands increased, there was a significant shift towards automation and precision in size reduction techniques.
The introduction of sophisticated machinery, such as high-shear mixers and advanced pulverizers, has transformed the way pharmaceuticals are produced. These innovations not only enhance efficiency but also ensure a higher degree of product uniformity and quality. Over the years, manufacturers have increasingly incorporated digital technologies into their operations, allowing for real-time monitoring and data analysis, which further enhances the decision-making process for B2B buyers.
As the market continues to evolve, the focus remains on developing equipment that meets stringent regulatory requirements while also addressing sustainability concerns. This ongoing transformation underscores the importance of staying informed about technological advancements and market dynamics for international buyers seeking to optimize their sourcing strategies in the pharmaceutical sector.
Frequently Asked Questions (FAQs) for B2B Buyers of size reduction equipment for pharmaceutical industry
-
How do I choose the right size reduction equipment for my pharmaceutical needs?
Choosing the right size reduction equipment involves assessing the properties of your materials, such as hardness, moisture content, and desired particle size. For pharmaceuticals, precision is crucial; therefore, equipment like ball mills or pulverizers may be ideal for achieving fine particle sizes. Additionally, consider the scale of production and whether batch or continuous processing fits your operational needs. It’s advisable to consult with suppliers who can provide tailored recommendations based on your specific application requirements. -
What is the best size reduction equipment for achieving fine particle sizes in pharmaceuticals?
For achieving fine particle sizes in pharmaceuticals, pulverizers and high shear mixers are often the best choices. Pulverizers, such as disc mills or vibratory disc mills, can produce very fine powders essential for effective formulation. High shear mixers, on the other hand, are excellent for emulsifying and homogenizing mixtures, ensuring uniformity in product quality. It’s essential to evaluate the specific characteristics of your materials to determine which equipment will yield the best results. -
What are the common payment terms in international B2B transactions for size reduction equipment?
Common payment terms in international B2B transactions often include options like Letter of Credit (LC), advance payment, or open account terms. For larger purchases, LCs provide security for both buyer and seller, while advance payments may be requested for custom equipment. It’s crucial to negotiate terms upfront and consider factors like currency fluctuations, transaction fees, and the supplier’s payment history to ensure a smooth financial arrangement. -
How can I vet suppliers of size reduction equipment for the pharmaceutical industry?
Vetting suppliers involves several steps: check their industry experience, certifications (such as ISO), and client testimonials. Conducting site visits can provide insights into their manufacturing processes and quality control measures. Additionally, ensure they have a robust after-sales service and support system. Engaging in discussions about their technology and equipment customization capabilities can also reveal their expertise and reliability. -
What are the minimum order quantities (MOQ) typically required when purchasing size reduction equipment?
Minimum order quantities (MOQ) for size reduction equipment can vary significantly based on the supplier and the type of equipment. Many manufacturers have MOQs for custom equipment, while standard models may have lower or no minimums. It’s advisable to discuss your specific needs with potential suppliers, as some may offer flexibility on MOQs depending on your project scale and future orders. -
What logistics considerations should I keep in mind when importing size reduction equipment?
When importing size reduction equipment, consider shipping methods, customs regulations, and potential tariffs. Ensure that the equipment meets local compliance standards to avoid delays. Collaborate with logistics providers experienced in handling industrial equipment to facilitate smooth transport. Additionally, factor in lead times for production and delivery, as these can impact your overall project timeline. -
How does quality assurance (QA) play a role in the procurement of size reduction equipment?
Quality assurance is critical in the procurement of size reduction equipment, particularly in the pharmaceutical sector where product consistency is paramount. Ensure that suppliers implement rigorous QA processes, including material inspections and performance testing. Request documentation of compliance with industry standards, such as Good Manufacturing Practices (GMP), to validate their commitment to quality. Regular audits of the supplier’s facilities can also provide assurance of their adherence to quality protocols. -
What customization options are available for size reduction equipment in the pharmaceutical industry?
Customization options for size reduction equipment can include modifications in size, capacity, and material compatibility to suit specific pharmaceutical applications. Some suppliers offer tailored solutions, such as unique grinding tool designs or special coatings to handle corrosive materials. Engaging with suppliers early in the procurement process can help you identify available customization options that meet your precise operational needs and regulatory requirements.
Important Disclaimer & Terms of Use
⚠️ Important Disclaimer
The information provided in this guide, including content regarding manufacturers, technical specifications, and market analysis, is for informational and educational purposes only. It does not constitute professional procurement advice, financial advice, or legal advice.
While we have made every effort to ensure the accuracy and timeliness of the information, we are not responsible for any errors, omissions, or outdated information. Market conditions, company details, and technical standards are subject to change.
B2B buyers must conduct their own independent and thorough due diligence before making any purchasing decisions. This includes contacting suppliers directly, verifying certifications, requesting samples, and seeking professional consultation. The risk of relying on any information in this guide is borne solely by the reader.
Strategic Sourcing Conclusion and Outlook for size reduction equipment for pharmaceutical industry
In the rapidly evolving pharmaceutical industry, strategic sourcing of size reduction equipment is critical for optimizing production efficiency and product quality. By understanding the diverse types of equipment—from crushers and grinders to homogenizers and cutting mills—buyers can make informed decisions that align with their specific processing needs. The key takeaway for international B2B buyers is to prioritize equipment that not only meets operational requirements but also enhances overall productivity and compliance with industry standards.
As markets in Africa, South America, the Middle East, and Europe continue to expand, the demand for high-quality size reduction equipment is expected to rise. Buyers should consider long-term partnerships with reputable suppliers that offer both cutting-edge technology and robust support services. This strategic approach not only mitigates risks associated with equipment failure but also fosters innovation within production processes.
Looking ahead, the integration of advanced technologies such as automation and data analytics will likely reshape the landscape of size reduction equipment. International B2B buyers are encouraged to stay ahead of these trends by engaging with suppliers that are committed to continuous improvement and sustainability. Embrace the opportunity to enhance your operations through strategic sourcing—your next step towards achieving competitive advantage in the pharmaceutical market awaits.