Ultimate Guide to Sourcing the US Plug Shape (2025)
Introduction: Navigating the Global Market for us plug shape
Navigating the complexities of sourcing the right US plug shape can be a significant challenge for international B2B buyers, particularly those operating in diverse regions such as Africa, South America, the Middle East, and Europe. Understanding the intricacies of electrical standards, including the prevalent types A and B plugs, is essential for ensuring compatibility with electrical devices and avoiding potential hazards. This guide provides a thorough exploration of the US plug shape, covering the technical specifications, applications, and the critical considerations needed for successful procurement.
As businesses increasingly expand their operations globally, the demand for reliable power solutions has surged. Buyers will find detailed insights into supplier vetting processes, enabling them to identify reputable manufacturers and distributors of travel adaptors and voltage converters. Additionally, the guide outlines cost factors associated with various plug types, helping to empower informed purchasing decisions.
Whether you are a company in Egypt needing to equip your workforce with compatible devices or a French firm looking to import electrical equipment, this comprehensive resource is tailored to meet the needs of international buyers. By addressing key questions and providing actionable insights, this guide aims to facilitate seamless transactions and enhance operational efficiency in the global marketplace.
Understanding us plug shape Types and Variations
Type Name | Key Distinguishing Features | Primary B2B Applications | Brief Pros & Cons for Buyers |
---|---|---|---|
Type A | Two flat parallel pins | Small appliances, chargers | Pros: Widely used, inexpensive; Cons: No grounding, limited compatibility. |
Type B | Two flat parallel pins + one grounding pin | Larger appliances, industrial equipment | Pros: Grounding for safety, more stable; Cons: Slightly bulkier, higher cost. |
Universal | Multiple plug configurations | Travel adapters, international trade | Pros: Versatile, convenient for global use; Cons: May compromise on safety standards. |
Type C | Two round pins | Electronics, travel appliances (less common in USA) | Pros: Common in Europe, fits many devices; Cons: Not standard in USA, requires additional adapters. |
Type G | Three rectangular pins | UK appliances, specialized equipment | Pros: High safety standards, robust; Cons: Not compatible with US sockets without adapters. |
What are the Characteristics of Type A Plugs?
Type A plugs feature two flat parallel pins and are commonly used for smaller electrical devices such as chargers and personal electronics. They are prevalent in the USA and are often the go-to choice for international travelers bringing devices from regions with similar plug types. B2B buyers should consider the limited grounding capabilities of Type A plugs, which can pose safety risks when used with higher wattage appliances.
How Does Type B Differ from Type A?
Type B plugs include the same two flat parallel pins as Type A but add a grounding pin for enhanced safety. This grounding feature makes Type B plugs suitable for larger appliances and industrial equipment that require a stable connection to prevent electrical hazards. B2B buyers should prioritize Type B for any equipment that will be used continuously or requires high power, as it provides a safer and more reliable connection.
Why Choose Universal Adapters for International Trade?
Universal adapters accommodate multiple plug types, making them ideal for businesses involved in international trade or travel. These adapters are particularly useful for companies that frequently send employees abroad or import/export goods. However, buyers should be cautious about safety standards, as some universal adapters may not meet the rigorous requirements of specific devices.
What are the Applications of Type C Plugs in the USA?
While Type C plugs are not standard in the USA, they feature two round pins and are widely used in Europe. B2B buyers importing European equipment should consider investing in adapters or converters to ensure compatibility. The versatility of Type C plugs can be advantageous for businesses with a diverse range of electronic devices, but they require additional planning for safe usage in the US market.
When Should You Consider Type G Plugs?
Type G plugs, characterized by three rectangular pins, are primarily used in the UK and some regions of the Middle East. They are known for their robust safety features, making them suitable for high-power equipment. However, B2B buyers should be aware that using Type G devices in the USA necessitates a proper adapter, which may complicate logistics and increase costs.
Key Industrial Applications of us plug shape
Industry/Sector | Specific Application of us plug shape | Value/Benefit for the Business | Key Sourcing Considerations for this Application |
---|---|---|---|
Consumer Electronics | Charging devices like smartphones and laptops | Ensures compatibility and convenience for travelers and business professionals | Look for dual voltage ratings and travel adaptors that cater to various plug types. |
Hospitality | Powering guest room appliances (kettles, TVs) | Enhances guest experience by allowing use of personal devices | Ensure adaptors are readily available for international guests, and consider safety standards. |
Construction & Engineering | Tools and equipment requiring US plug shapes | Facilitates the use of specialized equipment, ensuring operational efficiency | Verify the voltage and amperage requirements of tools to avoid overload. |
Healthcare | Medical devices and equipment for international patients | Guarantees functionality and safety of critical devices | Source adaptors that comply with medical standards and ensure compatibility with patient devices. |
Event Management | Audio-visual equipment for conferences and events | Provides seamless integration of technology, enhancing event quality | Assess power needs and ensure adequate adaptors are on hand for diverse equipment. |
How is the ‘US Plug Shape’ Used in Consumer Electronics?
In the consumer electronics sector, the US plug shape is critical for charging devices like smartphones and laptops. International B2B buyers from regions such as Africa and South America must ensure that their devices are compatible with US outlets, especially when traveling or conducting business in the United States. This often involves sourcing dual voltage rated chargers that can accommodate the 120V supply without the need for converters. The value lies in the convenience it provides to business professionals who rely on their devices for communication and productivity during travel.
What Role Does the ‘US Plug Shape’ Play in Hospitality?
In the hospitality industry, the US plug shape is essential for powering guest room appliances such as kettles, televisions, and charging stations. Hotels catering to international guests need to provide adaptors that fit these plug types to enhance the guest experience. Failure to do so may lead to dissatisfaction and poor reviews. B2B buyers in this sector should prioritize sourcing high-quality travel adaptors that meet safety standards, ensuring that they can accommodate a variety of international plugs while maintaining a focus on guest comfort.
How is the ‘US Plug Shape’ Relevant to Construction & Engineering?
In construction and engineering, the US plug shape is used for various tools and equipment that require compatibility with US outlets. This is particularly important for international contractors and engineers who may bring their own equipment to US job sites. Sourcing the correct adaptors is vital to avoid equipment malfunction or damage due to voltage discrepancies. Businesses should ensure that they verify the voltage and amperage requirements of their tools to prevent overload and ensure compliance with local electrical standards.
Why is the ‘US Plug Shape’ Important in Healthcare?
In healthcare, the US plug shape is crucial for the operation of medical devices and equipment used for international patients. Hospitals and clinics must ensure that their devices are compatible with US electrical standards to guarantee patient safety and device functionality. B2B buyers in this sector should focus on sourcing adaptors that comply with medical standards and can accommodate a wide range of devices. This not only ensures reliability but also enhances the overall quality of care provided to patients from various regions.
How Does the ‘US Plug Shape’ Benefit Event Management?
In event management, the US plug shape is vital for powering audio-visual equipment used during conferences and events. Event planners must ensure they have the necessary adaptors to accommodate diverse equipment brought in by international speakers or vendors. This facilitates seamless integration of technology, enhancing the quality of the event. B2B buyers should assess the power needs of all equipment in advance and ensure that adequate adaptors are sourced to avoid technical difficulties during events, thereby ensuring a smooth and professional experience.
3 Common User Pain Points for ‘us plug shape’ & Their Solutions
Scenario 1: Navigating Different Voltage Requirements in the US
The Problem: International B2B buyers often face significant challenges when using electrical appliances designed for different voltage standards. For example, a company from Egypt may import machinery that operates on 220V, only to find that the US outlets provide a standard voltage of 120V. This mismatch can lead to equipment malfunction or even permanent damage, resulting in costly repairs or replacements, downtime, and lost productivity.
The Solution: To prevent voltage-related issues, it is crucial for buyers to understand their equipment’s voltage requirements before exporting to the US. Conduct thorough research on the appliances’ specifications and determine if they are dual voltage (typically marked as ‘INPUT: 100-240V’). If the equipment is not dual voltage, sourcing a high-quality voltage converter or transformer is essential. When selecting a converter, ensure it has the appropriate power rating (measured in watts) for your devices. Additionally, consider purchasing equipment designed for the US market, which can reduce complications and increase efficiency. Partnering with reliable suppliers who can provide compatible equipment can also save time and reduce risk.
Scenario 2: Compatibility with US Plug Types A and B
The Problem: Many international companies overlook the specific plug types used in the US. For example, a South American business may send staff with laptops that have a Type C plug. Upon arrival, they discover that they cannot plug their devices into US outlets, causing significant inconvenience during crucial meetings or events. This lack of compatibility can hinder operations and create a negative impression on clients and partners.
The Solution: To avoid compatibility issues, B2B buyers should invest in universal travel adapters that accommodate multiple plug types, including A and B. Before travel, check the plug type of each device, and ensure that all employees are equipped with the necessary adapters. Additionally, consider bulk purchasing adapters and providing them to staff as part of travel kits. For companies that frequently operate in the US, sourcing electrical equipment with native US plug types could streamline processes and reduce the risk of incompatibility. Establishing relationships with local suppliers can also facilitate easier access to compatible products.
Scenario 3: Ensuring Safety with Grounding Requirements
The Problem: Safety is a paramount concern when it comes to electrical devices. A business from Europe might use appliances with two-pin plugs, which are not grounded. In the US, devices requiring grounding typically utilize Type B plugs. If these devices are connected to a non-grounded outlet, it poses serious risks, including electrical shocks or fires. This can lead to potential liability issues for companies that do not adhere to safety standards.
The Solution: To ensure safety compliance, B2B buyers should prioritize equipment that meets US safety standards, particularly for devices requiring grounding. When sourcing electrical products, verify that they are marked as double-insulated or include grounding features. If using non-grounded devices, only utilize travel adapters that are specifically rated for such appliances and ensure they are used in conjunction with devices that have adequate safety ratings. Additionally, consider consulting with a local electrician familiar with US regulations to assess the safety of your devices and make necessary adjustments before use. Regular audits of electrical equipment can also help identify potential hazards and maintain compliance with safety standards.
Strategic Material Selection Guide for us plug shape
What Are the Common Materials Used for US Plug Shapes?
When selecting materials for US plug shapes, international B2B buyers must consider various factors, including electrical performance, durability, and compliance with international standards. Below are analyses of four common materials used in the manufacture of US plug shapes, focusing on their properties, advantages, disadvantages, and specific considerations for buyers from regions such as Africa, South America, the Middle East, and Europe.
Which Materials Are Suitable for US Plug Shapes?
1. Polycarbonate (PC)
Key Properties:
Polycarbonate is a high-performance thermoplastic known for its excellent impact resistance and thermal stability. It can withstand temperatures ranging from -40°C to 120°C, making it suitable for various environmental conditions.
Pros & Cons:
Polycarbonate is highly durable and resistant to UV radiation, which enhances its longevity. However, it can be more expensive than other plastics, and its manufacturing process may require specialized equipment, increasing overall production costs.
Impact on Application:
Due to its high dielectric strength, polycarbonate is compatible with electrical applications, ensuring safe insulation. Its resistance to heat makes it ideal for plugs that may be exposed to higher temperatures during operation.
Considerations for International Buyers:
Buyers should ensure that polycarbonate components meet relevant standards such as UL (Underwriters Laboratories) and IEC (International Electrotechnical Commission) certifications. Compliance with these standards is crucial for market acceptance in regions like Europe and the Middle East.
2. Thermoplastic Elastomer (TPE)
Key Properties:
TPE combines the properties of rubber and plastic, offering flexibility and resilience. It operates effectively within a temperature range of -30°C to 80°C.
Pros & Cons:
The flexibility of TPE allows for easy molding into intricate shapes, making it ideal for ergonomic designs. However, TPE can have lower heat resistance compared to other materials, which may limit its application in high-temperature environments.
Impact on Application:
TPE’s flexibility and durability make it suitable for plugs that require frequent handling and connection. Its excellent electrical insulation properties ensure safety in various applications.
Considerations for International Buyers:
Buyers should verify that TPE materials comply with ASTM standards, especially regarding electrical safety and environmental impact. This is particularly important for buyers in Europe, where stringent regulations on materials are enforced.
3. Nylon
Key Properties:
Nylon is a synthetic polymer known for its strength and durability. It can withstand temperatures up to 120°C and has good chemical resistance.
Pros & Cons:
Nylon is relatively inexpensive and offers excellent mechanical properties, making it suitable for high-stress applications. However, it can be susceptible to moisture absorption, which may affect its electrical properties over time.
Impact on Application:
Nylon’s strength makes it ideal for structural components of plugs, ensuring they can withstand physical stress. Its chemical resistance allows for compatibility with various environments.
Considerations for International Buyers:
International buyers should ensure that nylon components meet the necessary fire safety standards, such as UL 94, especially for applications in regions with strict fire regulations, like Europe.
4. Metal (Copper and Brass)
Key Properties:
Copper and brass are commonly used for the conductive parts of plugs due to their excellent electrical conductivity and corrosion resistance.
Pros & Cons:
Metal components provide superior electrical performance and durability. However, they can be more expensive and may require additional coatings to prevent corrosion.
Impact on Application:
The use of metal in plugs ensures efficient power transfer and reduces the risk of overheating. This is critical for appliances that draw significant current.
Considerations for International Buyers:
Buyers must ensure that metal components comply with international standards regarding conductivity and corrosion resistance. This is particularly relevant for buyers in humid regions, such as parts of Africa and South America, where corrosion can be a significant issue.
Summary Table of Material Selection for US Plug Shapes
Material | Typical Use Case for US Plug Shape | Key Advantage | Key Disadvantage/Limitation | Relative Cost (Low/Med/High) |
---|---|---|---|---|
Polycarbonate | Insulation and housing | High impact resistance | Higher manufacturing costs | Medium |
Thermoplastic Elastomer (TPE) | Flexible components | Excellent flexibility and durability | Lower heat resistance | Medium |
Nylon | Structural components | Cost-effective and strong | Moisture absorption issues | Low |
Metal (Copper/Brass) | Conductive parts | Superior electrical conductivity | Higher cost and corrosion potential | High |
This strategic material selection guide provides actionable insights for international B2B buyers, ensuring they can make informed decisions when sourcing materials for US plug shapes.
In-depth Look: Manufacturing Processes and Quality Assurance for us plug shape
What are the Main Stages in the Manufacturing Process of US Plug Shapes?
The manufacturing process of US plug shapes, specifically Type A and Type B plugs, involves several critical stages. Understanding these stages is essential for international B2B buyers looking to ensure quality and reliability in their electrical components.
Material Preparation: What Materials are Used for US Plug Manufacturing?
The first step in the manufacturing process is material preparation. Common materials for US plugs include:
- Plastic: Used for the outer casing, typically made from polycarbonate or nylon for durability and insulation.
- Metal: Copper or brass is often used for the pins due to its excellent conductivity and resistance to corrosion.
- Rubber: Sometimes used for insulation or to provide a non-slip grip.
These materials must meet specific standards to ensure safety and compliance with international regulations. Suppliers should provide material safety data sheets (MSDS) to verify material quality.
Forming: How are US Plugs Shaped?
The forming process involves shaping the prepared materials into the desired plug configurations. This typically includes:
- Injection Molding: A common technique for creating the plastic casing. Pellets of plastic are heated and injected into molds to form the outer shell.
- Stamping and Die-Cutting: Used for shaping metal components like pins. This involves cutting and shaping metal sheets into the required dimensions.
Precision is crucial during this stage to ensure that the plugs fit securely into sockets without risk of electrical failure.
Assembly: What Steps are Involved in Plug Assembly?
After forming, the next step is assembly, where the individual components are brought together. This usually includes:
- Pin Insertion: Metal pins are inserted into the molded plastic casing. This may involve automatic or manual processes depending on the production scale.
- Screwing and Welding: Pins may be secured using screws or welding techniques to ensure a robust connection.
- Quality Checks: As plugs are assembled, preliminary quality checks should be conducted to catch defects early in the process.
Efficient assembly processes can significantly impact production costs and lead times, which are critical for B2B buyers.
Finishing: How is Quality Ensured in the Final Product?
The finishing stage involves several processes to enhance the plug’s appearance and functionality:
- Polishing: The surface of the plug is polished to remove any imperfections and improve aesthetics.
- Coating: A protective coating may be applied to enhance durability and resistance to wear.
- Final Inspection: Before packaging, plugs undergo a final inspection to ensure they meet all specifications and standards.
What International Quality Standards Should B2B Buyers Consider?
Quality assurance is paramount in the manufacturing of electrical components. B2B buyers should be familiar with several international standards that apply to US plug shapes.
Which International Standards Are Relevant for US Plugs?
- ISO 9001: This standard focuses on quality management systems, ensuring that manufacturers maintain consistent quality in their processes.
- CE Marking: Required in the European Union, CE marking indicates that a product meets health, safety, and environmental protection standards.
- UL Certification: Underwriters Laboratories (UL) certification indicates that the product has been tested for safety and performance.
These certifications provide assurance to buyers that the products meet stringent safety and quality standards.
What are the Key Quality Control Checkpoints in Manufacturing?
Quality control (QC) is integral to the manufacturing process, and it typically involves several checkpoints:
How is Incoming Quality Control (IQC) Conducted?
Incoming Quality Control (IQC) occurs before production begins. This involves:
- Material Inspection: Assessing raw materials for compliance with specifications.
- Supplier Audits: Verifying that suppliers meet quality standards and have the necessary certifications.
B2B buyers can request IQC reports to ensure materials used in manufacturing are of high quality.
What is In-Process Quality Control (IPQC)?
In-Process Quality Control (IPQC) monitors production processes to catch defects early. This includes:
- Monitoring Equipment: Ensuring machines are calibrated and functioning correctly.
- Random Sampling: Taking samples from production batches for testing.
B2B buyers can inquire about IPQC practices to understand how manufacturers maintain quality during production.
How is Final Quality Control (FQC) Performed?
Final Quality Control (FQC) involves a comprehensive assessment of the finished products. This typically includes:
- Visual Inspection: Checking for physical defects or damage.
- Functional Testing: Verifying that the plugs operate correctly under voltage and load conditions.
Buyers should request FQC reports to confirm that products have passed all necessary tests before shipment.
How Can B2B Buyers Verify Supplier Quality Control?
For international B2B buyers, verifying a supplier’s quality control processes is crucial for ensuring product reliability.
What Methods Can Buyers Use to Assess Supplier QC?
- Audits: Conducting on-site audits can provide insights into a manufacturer’s QC processes and compliance with international standards.
- Documentation: Requesting quality control documentation, including IQC, IPQC, and FQC reports, can help buyers evaluate the supplier’s commitment to quality.
- Third-party Inspections: Engaging third-party inspection services can provide an unbiased assessment of the manufacturer’s quality assurance practices.
What QC and Certification Nuances Should International Buyers Be Aware Of?
When sourcing US plugs, international buyers from regions like Africa, South America, the Middle East, and Europe should be mindful of specific nuances:
- Regional Regulations: Different regions have unique regulations and standards that manufacturers must comply with. For example, CE marking in Europe versus UL certification in the US.
- Supply Chain Transparency: Understanding the entire supply chain, from raw materials to finished products, can help buyers assess quality risks.
- Cultural Differences: Different regions may have varying approaches to quality control and manufacturing practices. Buyers should be aware of these differences when communicating with suppliers.
By understanding these manufacturing processes and quality assurance practices, international B2B buyers can make informed decisions when sourcing US plug shapes, ensuring they receive high-quality, reliable products that meet their specific needs.
Practical Sourcing Guide: A Step-by-Step Checklist for ‘us plug shape’
To ensure a successful procurement process for US plug shapes, B2B buyers need a structured approach that addresses technical specifications, supplier qualifications, and logistical considerations. This checklist serves as a practical guide for international buyers, particularly from Africa, South America, the Middle East, and Europe, to facilitate their sourcing decisions effectively.
Step 1: Define Your Technical Specifications
Clearly outline the technical requirements for the US plug shape you need. This includes identifying the plug types (Type A and Type B), voltage compatibility (120V), and frequency (60Hz). Understanding these specifications will help you avoid compatibility issues with electrical devices, ensuring safety and functionality in the intended applications.
Step 2: Research Regulatory Compliance
Before sourcing, verify that the plugs comply with relevant international and local electrical safety standards. In the US, this includes certifications such as UL (Underwriters Laboratories) or ETL (Electrical Testing Laboratories). Compliance ensures that the products meet safety requirements and can help avoid potential liabilities.
Step 3: Evaluate Potential Suppliers
Thoroughly vet potential suppliers to ensure they can meet your needs. Request detailed company profiles, client testimonials, and case studies that illustrate their experience with similar products. Look for suppliers that have a proven track record in exporting to your region, as this indicates familiarity with international shipping regulations and challenges.
Step 4: Assess Manufacturing Capabilities
Investigate the manufacturing capabilities of your shortlisted suppliers. Ensure they have the necessary equipment and quality control processes to produce the US plug shapes to your specifications. A reliable manufacturer should also offer flexibility in production to accommodate varying order sizes.
Step 5: Request Samples for Testing
Before finalizing any orders, request samples of the US plug shapes. Conduct thorough testing to confirm that the products meet your technical specifications and safety standards. This step is crucial to ensure that the plugs will function correctly with your devices and are safe for use.
Step 6: Discuss Pricing and Payment Terms
Engage in discussions regarding pricing structures and payment terms with your selected suppliers. Look for transparency in pricing to avoid hidden costs. Consider negotiating terms that allow for favorable payment schedules, which can help manage cash flow effectively.
Step 7: Plan for Logistics and Delivery
Finally, establish a clear logistics plan for shipping and delivery. Discuss shipping options, lead times, and potential customs duties with your suppliers. Having a well-defined logistics strategy will minimize delays and ensure that you receive your products on time, ready for distribution or use.
By following this checklist, B2B buyers can streamline their sourcing process for US plug shapes, ensuring they make informed decisions that align with their technical needs and business objectives.
Comprehensive Cost and Pricing Analysis for us plug shape Sourcing
What Are the Key Cost Components in Sourcing US Plug Shapes?
When sourcing US plug shapes, understanding the cost structure is crucial for B2B buyers, especially those operating in diverse regions like Africa, South America, the Middle East, and Europe. The primary cost components include:
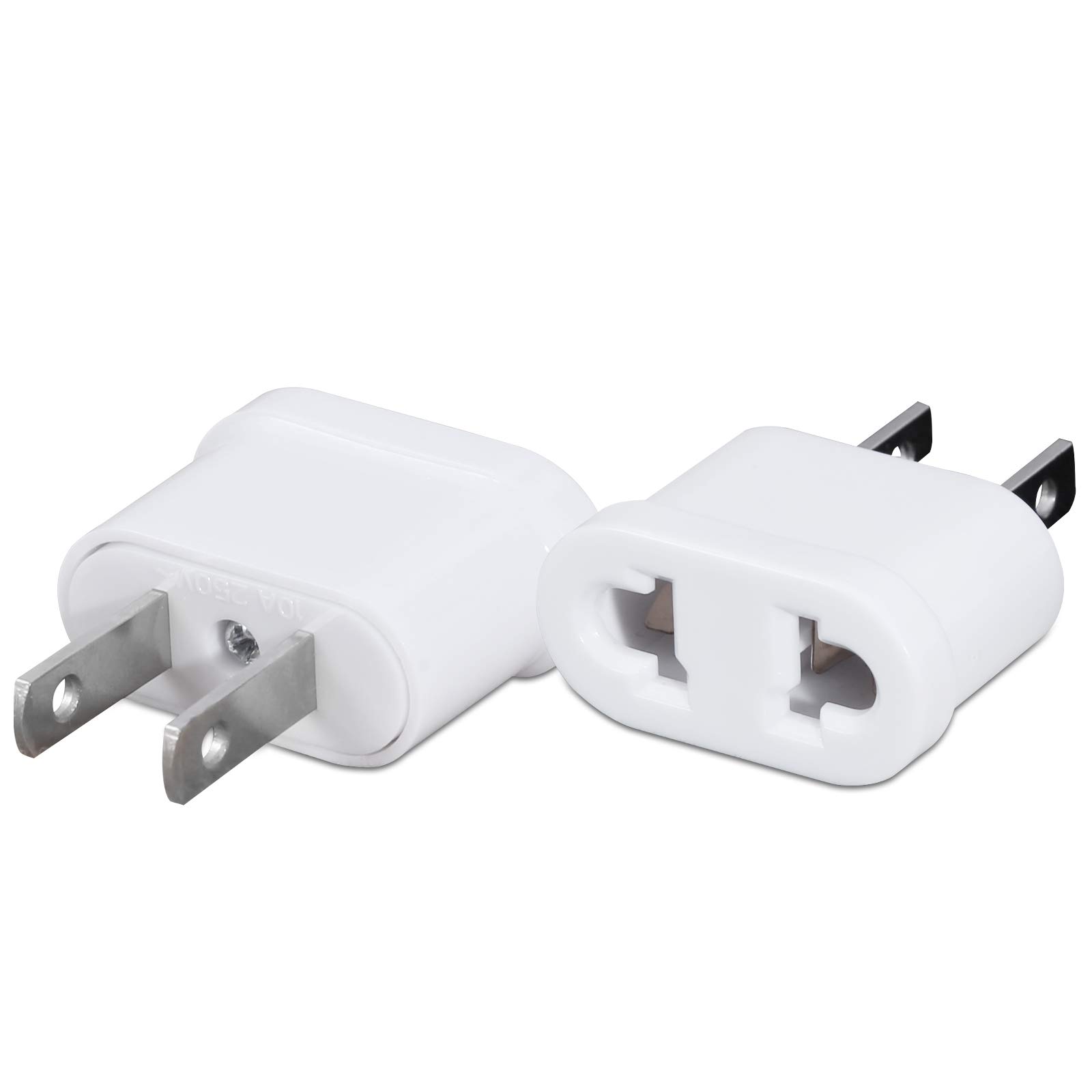
A stock image related to us plug shape.
-
Materials: The choice of materials significantly affects the cost. High-quality plastics and metals that meet safety standards can be more expensive but are essential for durability and compliance.
-
Labor: Labor costs can vary greatly depending on the manufacturing location. Regions with lower labor costs may offer competitive pricing, but buyers should consider the trade-off between cost and quality.
-
Manufacturing Overhead: This includes expenses related to utilities, equipment depreciation, and facility costs. Efficient manufacturing processes can help reduce these overheads, impacting the final pricing.
-
Tooling: Initial tooling costs for molds and dies can be substantial, particularly for custom designs. However, these costs are amortized over production runs, making them less significant for larger orders.
-
Quality Control (QC): Ensuring that products meet international safety standards requires investment in quality control processes. This includes testing for electrical safety, which can add to the overall cost.
-
Logistics: Shipping costs can fluctuate based on the distance from the manufacturer to the buyer’s location, as well as the chosen Incoterms. Air freight is faster but more expensive than sea freight.
-
Margin: Suppliers will typically apply a margin to cover their costs and profit. Understanding the expected margin can help buyers negotiate better pricing.
How Do Price Influencers Impact Sourcing Decisions?
Several factors influence the pricing of US plug shapes, which international buyers should consider:
-
Volume/MOQ (Minimum Order Quantity): Larger orders generally attract lower unit prices due to economies of scale. Buyers should assess their projected demand to negotiate favorable terms.
-
Specifications and Customization: Custom designs or specific certifications (like UL or CE) can increase costs. Buyers should weigh the need for customization against budget constraints.
-
Materials and Quality Certifications: Higher-quality materials and certifications for safety standards can raise the price but are essential for compliance in certain markets.
-
Supplier Factors: The reputation and reliability of the supplier can influence pricing. Established suppliers with good track records may charge more but can offer peace of mind regarding quality and delivery.
-
Incoterms: The choice of Incoterms (e.g., FOB, CIF) affects the total landed cost of goods. Buyers should understand their implications to make informed decisions about shipping responsibilities and costs.
What Are Effective Buyer Tips for Cost-Efficiency?
International B2B buyers can implement several strategies to enhance cost efficiency when sourcing US plug shapes:
-
Negotiation: Engage in discussions with suppliers about pricing and payment terms. Establishing a good relationship can lead to better deals and flexibility.
-
Total Cost of Ownership (TCO): Consider all costs associated with sourcing, including shipping, customs duties, and potential returns. A lower initial price may not always lead to overall savings.
-
Market Research: Conduct thorough research on multiple suppliers to compare pricing and quality. Leveraging industry contacts or trade shows can provide insights into competitive pricing.
-
Supplier Diversification: Avoid relying on a single supplier. Diversifying your supplier base can mitigate risks and provide leverage in negotiations.
-
Stay Informed on Regulatory Changes: Keeping abreast of changes in import regulations and safety standards in your target markets can help avoid unexpected costs.
Disclaimer on Indicative Prices
Please note that prices for US plug shapes can vary widely based on the factors outlined above. The estimates provided in this analysis are indicative and may not reflect current market conditions. Buyers are encouraged to obtain quotes from multiple suppliers to ensure competitive pricing.
Alternatives Analysis: Comparing us plug shape With Other Solutions
Introduction to Alternative Solutions for Electrical Connections
In the realm of international business, particularly for B2B buyers engaging in cross-border transactions, understanding the nuances of electrical connections is crucial. The US plug shapes, specifically Type A and Type B, are commonly used in the United States, but they are not the only options available. Buyers must consider alternatives that could provide better compatibility, cost-effectiveness, or convenience based on their specific needs. This section evaluates the US plug shapes against alternative solutions, helping businesses make informed decisions.
Comparison Table of US Plug Shape Against Alternatives
Comparison Aspect | Us Plug Shape | Universal Travel Adapter | European Plug Type (Type C) |
---|---|---|---|
Performance | Reliable for US voltage | Versatile across regions | Efficient for EU standards |
Cost | Generally low | Moderate (varies widely) | Low to moderate |
Ease of Implementation | Simple for US appliances | Easy to use, but can be bulky | Direct fit for EU devices |
Maintenance | Low maintenance | Occasional wear and tear | Very low |
Best Use Case | US domestic use | International travel | EU domestic and regional use |
Detailed Breakdown of Alternative Solutions
Universal Travel Adapter: Is It Worth It?
Universal travel adapters are designed to accommodate various plug types, making them a flexible solution for international travelers. Their major advantage lies in their ability to connect devices from multiple countries, thus eliminating the need for multiple adapters. However, while they offer versatility, they can sometimes be bulky and may not fit easily into tight spaces. Additionally, they do not convert voltage, so users must ensure their devices are compatible with local voltage standards to avoid damage.
European Plug Type (Type C): A European Standard
Type C plugs are widely used across Europe and are known for their simple design, featuring two round pins. They are efficient and reliable for devices that operate on the European electrical system, which typically runs on 230V at 50Hz. The Type C plug is advantageous for businesses operating in Europe, as it eliminates the need for additional adapters when using European equipment. However, for businesses that frequently operate in the US, the lack of compatibility with US plug shapes necessitates a conversion solution.
Conclusion: Choosing the Right Solution for Your Needs
When selecting the right electrical connection solution, B2B buyers must consider their operational regions, the compatibility of their devices, and the frequency of international travel. The US plug shapes are optimal for domestic use, while universal travel adapters provide flexibility for global operations. Conversely, European plugs are best suited for businesses focusing on the European market. Ultimately, understanding these alternatives allows international buyers to make informed decisions that enhance their operational efficiency while minimizing costs and technical issues.
Essential Technical Properties and Trade Terminology for us plug shape
What Are the Key Technical Properties of US Plug Shapes?
When dealing with the US plug shape, understanding its essential technical properties is crucial for international B2B buyers. Here are the key specifications that should be considered:
-
Plug Types: What Are Type A and Type B?
– Type A: This plug features two flat parallel pins and is commonly used in devices that do not require grounding.
– Type B: This design includes two flat parallel pins and a grounding pin, making it suitable for devices that require an earth connection. Knowing which plug type is required can prevent compatibility issues when sourcing electrical appliances. -
Voltage Rating: Why Is 120V Important?
– The standard voltage in the USA is 120V, with a frequency of 60Hz. Understanding this is vital for buyers sourcing electrical equipment, as using appliances designed for different voltage standards can lead to malfunction or damage. Ensure that the equipment you import can operate safely at this voltage. -
Material Specifications: What Materials Are Used in US Plugs?
– Common materials for US plug manufacturing include polycarbonate and thermoplastic rubber (TPR). Polycarbonate is often used for its durability and resistance to heat, while TPR provides flexibility and safety. Selecting plugs made from high-quality materials can enhance the longevity and safety of the electrical devices you distribute. -
Amperage Rating: What Does It Indicate?
– Plugs typically have a maximum amperage rating, often 15A for Type A and 20A for Type B. This rating indicates how much current the plug can handle safely. Understanding this specification is critical to ensure that the devices you import do not exceed the plug’s limits, thereby avoiding potential hazards. -
Certifications: Why Are UL and CSA Important?
– Look for certifications from organizations like Underwriters Laboratories (UL) and the Canadian Standards Association (CSA). These certifications indicate that the plugs meet specific safety and performance standards, which is particularly important for B2B buyers focused on quality assurance and compliance with local regulations.
What Common Trade Terms Should B2B Buyers Know Regarding US Plugs?
Navigating the trade landscape requires familiarity with specific jargon. Here are essential terms relevant to sourcing US plugs:
-
OEM (Original Equipment Manufacturer):
– This term refers to companies that produce parts or equipment that may be marketed by another manufacturer. Understanding OEM relationships can help buyers negotiate better pricing and ensure they are getting reliable products. -
MOQ (Minimum Order Quantity):
– The MOQ is the smallest quantity of a product that a supplier is willing to sell. This is crucial for buyers to know, as it affects inventory costs and the ability to test new products in smaller markets. -
RFQ (Request for Quotation):
– An RFQ is a standard business process to invite suppliers to bid on specific products or services. For B2B buyers, issuing RFQs can help compare pricing and terms, ensuring that they receive the best deal for US plugs. -
Incoterms (International Commercial Terms):
– These are predefined commercial terms used in international transactions that clarify the responsibilities of buyers and sellers. Understanding Incoterms like FOB (Free On Board) or CIF (Cost, Insurance, and Freight) can help buyers navigate shipping and logistics more effectively. -
CE Marking:
– This certification indicates that a product complies with EU safety standards. While primarily relevant for European markets, awareness of CE marking is useful for international buyers to ensure their products meet global safety requirements.
By grasping these technical properties and trade terms, international B2B buyers can make informed decisions when sourcing US plug shapes, ensuring compliance, safety, and compatibility with their electrical equipment.
Navigating Market Dynamics and Sourcing Trends in the us plug shape Sector
What Are the Key Market Trends in the US Plug Shape Sector?
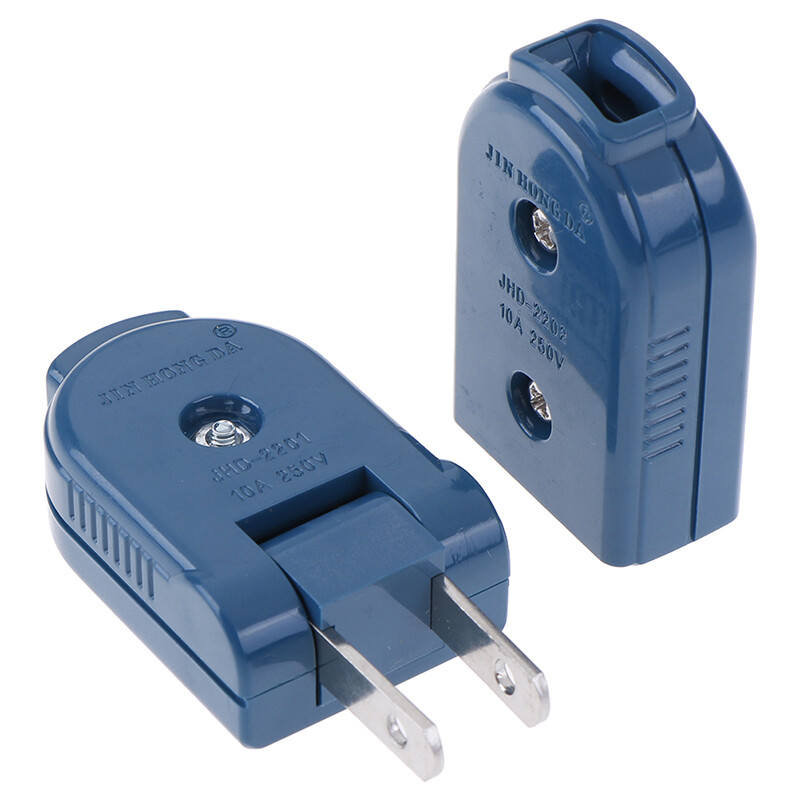
A stock image related to us plug shape.
The US plug shape sector is witnessing significant evolution driven by global demand for connectivity and the proliferation of electronic devices. Key trends include the increasing adoption of dual-voltage appliances, which cater to a broader international market. As international travel and commerce expand, the need for compatible power solutions is paramount. B2B buyers from Africa, South America, the Middle East, and Europe should focus on sourcing products that comply with Type A and Type B standards, given their prevalence in the US market.
Additionally, the rise of smart technologies is influencing product development. Manufacturers are integrating smart features into adapters, enhancing user experience while ensuring safety and compliance with electrical standards. Emerging technologies, such as IoT-enabled devices, are also driving demand for adaptable power solutions that can cater to varied voltage and frequency requirements.
Another important market dynamic is the shift towards online procurement channels. International buyers are increasingly leveraging e-commerce platforms to source plug shape products, benefiting from competitive pricing and a wider selection. This trend underscores the importance of establishing robust digital marketing strategies to reach potential buyers effectively.
How Is Sustainability Influencing Sourcing Trends for US Plug Shapes?
Sustainability and ethical sourcing are becoming crucial considerations for B2B buyers in the US plug shape sector. The environmental impact of electrical products, including their lifecycle and end-of-life disposal, is under scrutiny. Companies are now prioritizing suppliers that demonstrate commitment to sustainable practices, such as using recycled materials and minimizing waste during production.
Certifications such as Energy Star and RoHS (Restriction of Hazardous Substances) are increasingly important in verifying the environmental credentials of products. Buyers should consider sourcing from manufacturers that hold these certifications, ensuring that they align with global sustainability goals.
Moreover, the demand for eco-friendly materials is rising. Buyers should seek products made from biodegradable or recyclable materials, which not only reduce environmental impact but also appeal to a growing segment of environmentally-conscious consumers. Establishing partnerships with suppliers who share these values can enhance a company’s reputation and customer loyalty.
What Is the Brief History of US Plug Shape Development?
The evolution of the US plug shape can be traced back to the early 20th century when electricity became widespread. The Type A and Type B plugs were standardized in the 1920s, aiming to enhance safety and compatibility across devices. Type A, featuring two flat parallel pins, was designed for basic appliances, while Type B, with an additional grounding pin, was introduced to address safety concerns associated with higher-power devices.
Over the decades, the designs have remained relatively unchanged, but advancements in materials and safety features have significantly improved their efficacy. Today, the US plug shape sector stands at a crossroads, influenced by technological innovations and shifting consumer expectations, making it essential for international B2B buyers to stay informed about these developments for effective sourcing strategies.
Conclusion
As the US plug shape sector continues to evolve, international B2B buyers must navigate these dynamics with a strategic approach. By understanding market trends, prioritizing sustainability, and recognizing the historical context, buyers can make informed decisions that align with their business objectives while meeting the growing demands of a global marketplace.
Frequently Asked Questions (FAQs) for B2B Buyers of us plug shape
-
How do I solve compatibility issues with US plug shapes when sourcing electrical products?
To address compatibility issues with US plug shapes, first, confirm the plug type required for your appliances—Type A and Type B are the standards in the USA. When sourcing products, communicate clearly with suppliers about the plug specifications needed. Consider investing in universal adapters or discuss the possibility of customizing products to include the appropriate plug type. Additionally, ensure that your supplier provides detailed product specifications and compliance certifications for safety standards applicable in the US market. -
What is the best voltage and frequency for electrical appliances designed for the US market?
The standard voltage in the USA is 120V with a frequency of 60Hz. When sourcing electrical appliances for the US market, it’s crucial to ensure they are designed to operate at this voltage and frequency. Look for dual voltage appliances (rated for 110-240V) if you plan to distribute them in multiple markets. This flexibility can enhance product appeal and reduce the need for additional voltage converters, making it easier for end-users to utilize these products safely. -
What are the key factors to consider when vetting suppliers for US plug shape products?
When vetting suppliers for products with US plug shapes, consider factors such as compliance with safety standards (e.g., UL certification), manufacturing capabilities, and experience in exporting to the US. Request samples to test product quality and ensure they meet local regulations. It’s also advisable to check references or reviews from other international buyers and to understand the supplier’s logistics capabilities, including shipping options and lead times. -
How can I customize products with US plug shapes for my target market?
Customization can be achieved by communicating specific requirements to your supplier during the product design phase. Options may include modifying plug types, voltage ratings, or even packaging to cater to local preferences. Ensure you collaborate closely with your supplier to understand the technical feasibility of these modifications. It’s also beneficial to conduct market research to identify any unique demands or trends in your target market that could inform your customization choices. -
What are the minimum order quantities (MOQ) typically required for US plug shape products?
Minimum order quantities for US plug shape products vary significantly by supplier and product type. Generally, MOQs can range from 50 to several hundred units, depending on the manufacturer’s production scale and the complexity of the product. When negotiating with suppliers, be clear about your needs and seek flexibility in MOQs, especially if you are a new buyer or testing a new market. Discussing potential trial orders may also be a viable option. -
What payment terms should I expect when sourcing US plug shape products from international suppliers?
Payment terms can vary widely among suppliers. Common arrangements include upfront payments, partial payments (e.g., 30% deposit and 70% upon delivery), or letters of credit. It’s crucial to establish clear payment terms upfront to mitigate risks. Consider using payment platforms that offer buyer protection or escrow services, especially when dealing with new suppliers. Always ensure that payment terms align with your cash flow and risk tolerance. -
How do I ensure quality assurance (QA) for US plug shape products?
Quality assurance can be ensured by establishing a comprehensive QA process that includes pre-production samples, regular inspections during production, and final product testing. Specify quality standards that align with US regulations, such as ANSI or UL certifications. Consider hiring third-party inspection services to verify product quality before shipment. Maintaining open communication with your supplier throughout the production process can also help address any issues promptly. -
What logistics considerations should I keep in mind when importing US plug shape products?
When importing US plug shape products, consider factors such as shipping methods (air freight vs. sea freight), customs regulations, and potential tariffs. Ensure that your supplier provides all necessary documentation, such as invoices and certificates of origin, to facilitate smooth customs clearance. It’s also wise to work with logistics partners familiar with international shipping to navigate potential challenges and optimize delivery times to your target market.
Important Disclaimer & Terms of Use
⚠️ Important Disclaimer
The information provided in this guide, including content regarding manufacturers, technical specifications, and market analysis, is for informational and educational purposes only. It does not constitute professional procurement advice, financial advice, or legal advice.
While we have made every effort to ensure the accuracy and timeliness of the information, we are not responsible for any errors, omissions, or outdated information. Market conditions, company details, and technical standards are subject to change.
B2B buyers must conduct their own independent and thorough due diligence before making any purchasing decisions. This includes contacting suppliers directly, verifying certifications, requesting samples, and seeking professional consultation. The risk of relying on any information in this guide is borne solely by the reader.
Strategic Sourcing Conclusion and Outlook for us plug shape
In navigating the complexities of sourcing products compatible with the U.S. plug shape, international B2B buyers must prioritize understanding the specific requirements associated with plug types A and B. This includes recognizing the standard voltage of 120V and frequency of 60Hz, which are critical for the safe operation of electrical appliances. Buyers should ensure that their devices are either dual voltage rated or compatible with voltage converters when necessary.
Why Is Strategic Sourcing Essential for U.S. Plug Compatibility?
Strategic sourcing is pivotal in optimizing procurement processes and mitigating risks related to electrical compatibility. By establishing strong supplier relationships and understanding local regulations, businesses can streamline their operations and ensure product safety. This approach not only reduces costs but also enhances market competitiveness, particularly in regions such as Africa, South America, the Middle East, and Europe.
What Does the Future Hold for International B2B Buyers?
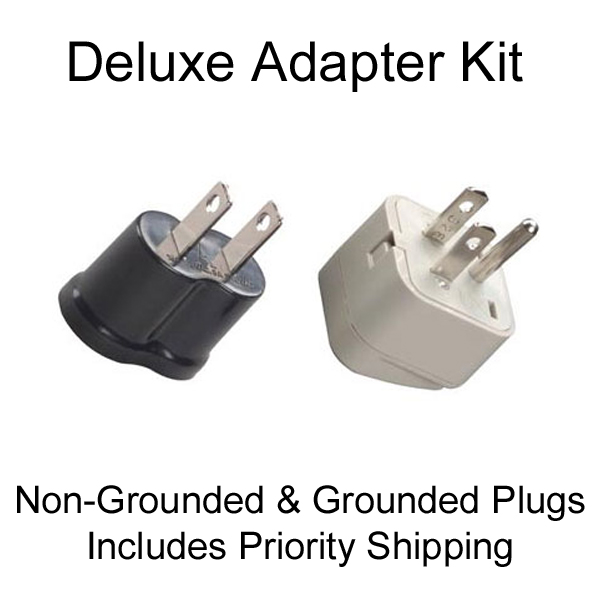
A stock image related to us plug shape.
As global trade continues to evolve, the demand for compatible electrical solutions will only increase. International buyers should stay informed about technological advancements and regulatory changes that could impact sourcing decisions. By proactively addressing these factors, businesses can position themselves favorably in the marketplace.
In conclusion, embracing a strategic sourcing mindset will empower international B2B buyers to navigate the nuances of U.S. plug shapes effectively. Engage with reliable suppliers today to secure your operational needs and stay ahead in an ever-changing market landscape.