Unlock Cost Savings: The Complete Guide to Hydra Presses (2025)
Introduction: Navigating the Global Market for hydra presses
In an increasingly interconnected world, sourcing the right hydra presses can be a daunting challenge for international B2B buyers, particularly those in Africa, South America, the Middle East, and Europe. The complexity of selecting the ideal hydraulic press—whether for manufacturing, waste management, or compacting applications—requires a thorough understanding of specifications, capabilities, and market options. This comprehensive guide addresses critical aspects of hydra presses, including various types, applications across industries, supplier vetting processes, and cost considerations, ensuring that buyers can navigate this diverse landscape with confidence.
Understanding the intricate features and functionalities of hydra presses is essential for making informed purchasing decisions. Buyers will benefit from insights into the latest technological advancements, such as automated systems and digital controls, which enhance productivity and efficiency. Additionally, this guide highlights the importance of aligning press specifications with operational needs, which can vary significantly across regions and industries.
By providing a robust framework for evaluating suppliers and their offerings, this guide empowers B2B buyers to make strategic decisions that can lead to increased productivity and cost savings. Whether you are in Johannesburg, Buenos Aires, Riyadh, or Berlin, the insights shared here will help streamline your sourcing process and ensure that you select the right hydra press for your business needs.
Understanding hydra presses Types and Variations
Type Name | Key Distinguishing Features | Primary B2B Applications | Brief Pros & Cons for Buyers |
---|---|---|---|
Hydraulic Press | Ranges from 20 to 1,000 tons, versatile configurations | Metal stamping, plastic forming, waste management | Pros: High force application, adaptable. Cons: Requires maintenance and space. |
Electro-Mechanical Press | Combines hydraulic force with digital control systems | Precision compacting, automotive parts production | Pros: High precision, low operating costs. Cons: Higher initial investment. |
Hydra-Mechanical Press | Operates with mechanical and hydraulic principles | Heavy-duty applications, metal forming | Pros: Robust construction, efficient for large jobs. Cons: Limited speed compared to hydraulic presses. |
Hydra-Press for Waste Management | Designed for compacting and dewatering waste materials | Waste treatment facilities, recycling operations | Pros: Efficient waste reduction, minimizes disposal costs. Cons: Specialized use may limit versatility. |
Remanufactured Hydra Press | Refurbished machines with updated components | Cost-sensitive operations, small to medium production | Pros: Cost-effective, reliable performance. Cons: May lack the latest technology features. |
What are the Characteristics of Hydraulic Presses?
Hydraulic presses are characterized by their extensive range of capacities, from 20 to 1,000 tons, making them suitable for various industrial applications. They are highly versatile and can be configured for tasks such as metal stamping, plastic forming, and even waste management. When purchasing a hydraulic press, B2B buyers should consider factors such as maintenance requirements, space constraints, and the specific applications they intend to use the press for.
How Do Electro-Mechanical Presses Differ?
Electro-mechanical presses integrate hydraulic force with advanced digital control systems, allowing for precise operations. They are ideal for applications requiring high accuracy, such as automotive parts production and precision compacting. While they offer lower operating costs over time, buyers must weigh the initial investment against potential savings in operational efficiency and reduced waste.
What Makes Hydra-Mechanical Presses Suitable for Heavy-Duty Tasks?
Hydra-mechanical presses utilize a combination of mechanical and hydraulic principles, making them particularly effective for heavy-duty applications like metal forming. Their robust construction ensures durability under intense working conditions. Buyers should consider the specific needs of their operations, including the types of materials being processed and the desired speed of production, when evaluating these machines.
How Do Hydra-Presses Benefit Waste Management Operations?
Hydra-presses designed for waste management excel in compacting and dewatering waste materials, thus playing a crucial role in resource recovery and environmental sustainability. These machines significantly reduce the volume of waste, leading to lower disposal costs. However, their specialized nature means they may not be as versatile for other applications, which buyers should consider based on their operational needs.
What are the Advantages of Choosing Remanufactured Hydra Presses?
Remanufactured hydra presses present a cost-effective solution for companies looking to upgrade their machinery without the high costs associated with new equipment. These refurbished machines come with updated components and can deliver reliable performance similar to new models. Buyers should ensure that the remanufacturing process meets industry standards to guarantee the longevity and efficiency of their investment.
Key Industrial Applications of hydra presses
Industry/Sector | Specific Application of Hydra Presses | Value/Benefit for the Business | Key Sourcing Considerations for this Application |
---|---|---|---|
Manufacturing | Metal Stamping and Forming | Enhanced precision and efficiency in producing metal components | Capacity, tonnage requirements, and automation options |
Waste Management | Waste Compaction and Dewatering | Reduced waste volume and improved resource recovery | Equipment durability, hydraulic power, and maintenance support |
Automotive | Component Assembly and Testing | Improved production efficiency and consistent quality control | Custom tooling options, safety features, and cycle speed |
Construction | Material Compaction for Concrete Forming | Increased structural integrity and reduced material costs | Platen size, adjustable shut height, and operational flexibility |
Plastic and Rubber Industry | Thermoforming and Die-Cutting | Faster production cycles and reduced labor costs | Tonnage adjustments, control panel features, and safety devices |
How Are Hydra Presses Used in Manufacturing for Metal Stamping and Forming?
In the manufacturing sector, particularly in metal stamping and forming, hydra presses are crucial for producing components with high precision. These presses can handle various materials, allowing manufacturers to create intricate designs while maintaining quality control. The ability to adjust tonnage and cycle times caters to different production needs, making them versatile for international buyers. Companies in Africa and South America may seek hydra presses that offer robust support and service options, ensuring minimal downtime and operational efficiency.
What Role Do Hydra Presses Play in Waste Management?
Hydra presses are instrumental in waste management, particularly for waste compaction and dewatering. These machines utilize hydraulic force to compress waste materials, significantly reducing their volume and making disposal more manageable. In regions like the Middle East, where waste management is a growing concern, investing in efficient hydra presses can lead to substantial cost savings and environmental benefits. Buyers should consider the machine’s hydraulic power and durability to ensure long-term performance in challenging conditions.
How Are Hydra Presses Enhancing Automotive Component Assembly?
In the automotive industry, hydra presses facilitate component assembly and testing, ensuring that parts fit together accurately and function as intended. The precision of these presses helps in maintaining quality standards, which is critical in automotive manufacturing. International buyers, especially in Europe, should look for presses with advanced automation options to streamline operations and improve productivity. Safety features are also essential, given the high-speed nature of automotive assembly lines.
How Do Hydra Presses Improve Construction Material Compaction?
In construction, hydra presses are used for material compaction, particularly in concrete forming applications. These presses ensure that materials are compacted uniformly, enhancing the structural integrity of buildings and reducing the amount of raw material needed. Buyers from South Africa and other developing regions should prioritize presses with adjustable shut heights and large platen sizes to accommodate various project requirements. Operational flexibility is key, as construction projects often demand quick adjustments to meet specific job site conditions.
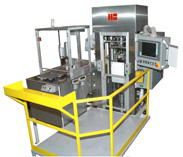
A stock image related to hydra presses.
What Benefits Do Hydra Presses Provide in the Plastic and Rubber Industry?
In the plastic and rubber industry, hydra presses are primarily used for thermoforming and die-cutting processes. These machines allow for rapid production cycles, which can significantly reduce labor costs and improve output. For international buyers, particularly in emerging markets, understanding the specific control features and safety devices available with these presses is crucial for ensuring optimal performance and compliance with local regulations. The ability to customize tooling options can also provide a competitive advantage in product development.
3 Common User Pain Points for ‘hydra presses’ & Their Solutions
Scenario 1: Inconsistent Pressing Results Affecting Production Quality
The Problem: Many B2B buyers of hydra presses encounter issues with inconsistent pressing results, leading to defective products and increased waste. This inconsistency often stems from improper setup or calibration, which can be exacerbated by the use of outdated or poorly maintained equipment. Buyers in regions with limited access to technical support may struggle to achieve the precise tonnage and cycle times required for their specific applications, resulting in costly production delays and potential loss of clients.
The Solution: To overcome this challenge, buyers should invest in hydra presses with advanced digital control systems that allow for easy setup and monitoring. These systems typically feature touch-screen interfaces that enable operators to store and recall specific part setups, ensuring consistent performance across batches. Additionally, regular maintenance schedules should be established, including inspections of hydraulic fluid levels and seals, to maintain optimal function. For buyers in regions like Africa or South America, seeking suppliers that offer remote technical support and training can enhance operational consistency and reduce the risk of production errors.
Scenario 2: High Operational Costs Due to Inefficiency
The Problem: Operational inefficiencies can significantly inflate production costs for businesses utilizing hydra presses. In many cases, outdated equipment or a lack of automation leads to longer cycle times and increased labor costs. Buyers may find that their current presses do not have features like automated part removal or real-time monitoring, which can optimize workflow and reduce manual intervention.
The Solution: Buyers should prioritize the acquisition of hydra presses that integrate automation capabilities and advanced monitoring technologies. Models equipped with features such as automatic gauging systems, part removal robots, and data collection for cycle times can streamline operations and enhance productivity. For instance, investing in a press that utilizes a compact “plug and play” design with remote access for troubleshooting can drastically cut down on downtime. By assessing total cost of ownership (TCO) rather than just the initial purchase price, buyers can identify long-term savings associated with modern, efficient machinery.
Scenario 3: Safety Concerns and Compliance Challenges
The Problem: Safety is a critical concern for B2B buyers, particularly in industries that involve heavy machinery like hydra presses. Buyers often face challenges ensuring compliance with local and international safety standards, which can vary significantly across regions such as Europe, the Middle East, and Africa. Failure to comply can result in fines, operational halts, or worse—serious injuries to workers.
The Solution: To address safety concerns, buyers should focus on sourcing hydra presses that come equipped with comprehensive safety features, such as two-hand anti-tie-down switches and emergency stop controls. It’s essential to conduct a thorough risk assessment before purchasing equipment and to ensure that all operators are trained on safety protocols. Additionally, buyers can leverage the expertise of suppliers who offer compliance documentation and guidance on meeting local regulations. Engaging in regular safety audits and implementing a culture of safety within the organization can further mitigate risks and ensure a safer working environment.
Strategic Material Selection Guide for hydra presses
What Are the Common Materials Used in Hydra Presses?
When selecting materials for hydra presses, international B2B buyers must consider several factors, including performance properties, application suitability, and compliance with regional standards. Below, we analyze four common materials used in the construction of hydra presses, focusing on their key properties, advantages, disadvantages, and specific considerations for buyers from Africa, South America, the Middle East, and Europe.
How Does Steel Perform in Hydra Press Applications?
Steel is the most prevalent material used in hydra presses due to its excellent mechanical properties. It offers high tensile strength, making it suitable for high-pressure applications. Steel can withstand temperatures ranging from -40°C to 400°C, depending on the alloy, and exhibits good corrosion resistance when properly treated.
Pros: Steel’s durability and strength make it ideal for heavy-duty applications. It is readily available and can be manufactured into complex shapes.
Cons: The primary downside is its susceptibility to corrosion if not adequately protected, which can lead to increased maintenance costs. Additionally, steel can be heavier, impacting the overall weight of the press.
Impact on Application: Steel’s compatibility with various hydraulic fluids makes it a versatile choice for different applications, including metal forming and waste management.
Considerations for International Buyers: Compliance with standards such as ASTM A36 or DIN 17100 is crucial. Buyers should also consider local sourcing options to minimize costs and ensure timely delivery.
What Role Does Aluminum Play in Hydra Press Construction?
Aluminum is increasingly used in hydra presses, especially for components requiring lightweight properties without compromising strength. It has a lower density than steel, making it easier to handle, and exhibits good corrosion resistance, particularly when anodized.
Pros: The lightweight nature of aluminum allows for easier installation and reduced energy consumption during operation. Its corrosion resistance is beneficial in humid environments.
Cons: Aluminum generally has a lower tensile strength compared to steel, which may limit its use in high-pressure applications. It can also be more expensive than steel.
Impact on Application: Aluminum is suitable for applications where weight savings are critical, such as portable presses or in industries like automotive and aerospace.
Considerations for International Buyers: Buyers should ensure compliance with standards such as ASTM B221 or JIS H4000. The availability of aluminum may vary by region, impacting procurement strategies.
Why Is Cast Iron a Preferred Material for Some Hydra Presses?
Cast iron is known for its excellent wear resistance and ability to dampen vibrations, making it a popular choice for the frames of hydra presses. It can withstand high pressures and has good thermal stability.
Pros: The rigidity of cast iron contributes to the stability of the press during operation, enhancing precision. It is also cost-effective for large components.
Cons: Cast iron is brittle and can fracture under excessive stress. It is also heavier than both steel and aluminum, which may affect mobility.
Impact on Application: Cast iron is particularly effective in applications requiring stability and precision, such as metal stamping and forming.
Considerations for International Buyers: Compliance with standards such as ASTM A48 is essential. Buyers should also evaluate local suppliers for cast iron components to ensure quality and cost-effectiveness.
How Does Composite Material Enhance Hydra Press Performance?
Composite materials, such as carbon fiber reinforced polymers, are emerging in the hydra press market for specific applications. These materials offer high strength-to-weight ratios and excellent corrosion resistance.
Pros: Composites are lightweight and can be tailored for specific performance characteristics, making them ideal for specialized applications.
Cons: The manufacturing process for composites can be complex and expensive. They may also have limitations in high-temperature applications.
Impact on Application: Composites are suitable for applications requiring high precision and low weight, such as in the aerospace and automotive sectors.
Considerations for International Buyers: Buyers should ensure that composite materials meet relevant standards and certifications. The availability of these materials may vary, requiring careful planning for procurement.
Summary Table of Material Selection for Hydra Presses
Material | Typical Use Case for hydra presses | Key Advantage | Key Disadvantage/Limitation | Relative Cost (Low/Med/High) |
---|---|---|---|---|
Steel | Heavy-duty applications | High tensile strength | Susceptible to corrosion | Medium |
Aluminum | Lightweight components | Lightweight and corrosion-resistant | Lower tensile strength | High |
Cast Iron | Frames for stability | Excellent wear resistance | Brittle and heavy | Medium |
Composite | Specialized applications | High strength-to-weight ratio | Complex manufacturing process | High |
In conclusion, selecting the right material for hydra presses involves balancing performance characteristics, application requirements, and regional compliance standards. Understanding these factors will help international B2B buyers make informed decisions that align with their operational needs and market conditions.
In-depth Look: Manufacturing Processes and Quality Assurance for hydra presses
What Are the Main Stages of Manufacturing Hydra Presses?
The manufacturing process of hydra presses is complex and involves several critical stages that ensure the machines meet high-quality standards. Understanding these stages will help B2B buyers assess the reliability and efficiency of potential suppliers.
Material Preparation
The first step in manufacturing hydra presses is material preparation, which involves sourcing high-quality raw materials, typically steel and hydraulic components. Suppliers should provide certifications that verify the material’s grade and origin. Buyers should look for suppliers who maintain strict quality controls in material selection to avoid issues such as premature wear or structural failure.
Forming Techniques
Once materials are prepared, the next stage involves forming, which can include processes such as stamping, bending, and welding. Advanced techniques like CNC machining are often employed to ensure precision in parts that require tight tolerances. Buyers should inquire about the technology and machinery used in the forming process, as modern equipment can significantly enhance the accuracy and consistency of components.
Assembly Process
The assembly stage is where individual components are put together to form the final product. This process typically involves skilled technicians who adhere to specific assembly protocols to ensure that all parts fit correctly and function as intended. Buyers should verify whether the assembly process includes checks for alignment and fit, as these factors are crucial for the operational efficiency of hydra presses.
Finishing Touches
Finishing involves surface treatments such as painting, coating, or galvanization to enhance durability and aesthetics. The finishing process also includes final adjustments and testing of hydraulic systems to ensure optimal performance. Buyers should ask about the finishing techniques used, as these can affect both the longevity and maintenance requirements of the equipment.
How is Quality Assurance Implemented in Hydra Press Manufacturing?
Quality assurance (QA) is a vital aspect of the manufacturing process for hydra presses, ensuring that products meet international standards and customer expectations.
What International Standards Should Buyers Consider?
For B2B buyers, understanding the relevant international standards is essential. Many manufacturers comply with ISO 9001, which focuses on quality management systems. Additionally, industry-specific certifications such as CE marking for European markets or API standards for oil and gas applications provide further assurance of quality.
What Are the Key Quality Control Checkpoints?
Quality control (QC) involves multiple checkpoints throughout the manufacturing process:
-
Incoming Quality Control (IQC): This initial checkpoint ensures that raw materials meet specified quality standards before production begins. Buyers should inquire about the criteria used to accept or reject materials.
-
In-Process Quality Control (IPQC): During manufacturing, inspections are conducted at various stages to catch defects early. This can include checks on dimensions, functionality, and assembly integrity.
-
Final Quality Control (FQC): Once assembly is complete, a comprehensive inspection is performed. This includes functional testing of hydraulic systems and operational checks to ensure the machine meets performance specifications.
Which Testing Methods Are Commonly Used in Hydra Press Manufacturing?
B2B buyers should be aware of the various testing methods employed to ensure the reliability and safety of hydra presses:
-
Hydraulic Testing: This method assesses the integrity of hydraulic systems by applying pressure and checking for leaks. It is crucial for ensuring operational safety.
-
Load Testing: Simulating real-world conditions, load testing verifies that the press can handle specified loads without deforming or failing.
-
Performance Testing: This involves evaluating cycle times, speed, and efficiency to ensure the press meets operational requirements.
How Can B2B Buyers Verify Supplier Quality Control?
Verification of a supplier’s quality control processes is essential for making informed purchasing decisions. Here are several strategies:
-
Supplier Audits: Conducting on-site audits allows buyers to assess manufacturing facilities, quality control processes, and compliance with international standards firsthand.
-
Requesting Quality Reports: Buyers should request documentation that outlines the results of IQC, IPQC, and FQC tests. Comprehensive reports can provide insights into the supplier’s commitment to quality.
-
Third-Party Inspections: Engaging independent third-party inspectors can provide an unbiased evaluation of the manufacturing process and product quality.
What Are the Quality Control and Certification Nuances for International Buyers?
When dealing with international suppliers, particularly those in Africa, South America, the Middle East, and Europe, several nuances come into play:
-
Understanding Regional Standards: Different regions may have varying standards and certifications. Buyers should familiarize themselves with local regulations to ensure compliance.
-
Language Barriers: Communication can sometimes hinder quality assurance efforts. Buyers should ensure that all documentation, including quality reports and certifications, is available in a language they understand.
-
Cultural Differences: Different cultures may approach quality and manufacturing processes differently. Building strong relationships with suppliers can facilitate better understanding and adherence to quality expectations.
Conclusion
For B2B buyers considering the purchase of hydra presses, understanding the intricacies of manufacturing processes and quality assurance is vital. By focusing on material preparation, forming techniques, assembly, and finishing, as well as ensuring compliance with international standards and rigorous QC checkpoints, buyers can make more informed decisions. Verifying supplier quality through audits, reports, and independent inspections will further enhance the likelihood of successful procurement. With this knowledge, international buyers can confidently navigate the complexities of sourcing hydra presses that meet their operational needs.
Practical Sourcing Guide: A Step-by-Step Checklist for ‘hydra presses’
In the competitive landscape of international B2B procurement, particularly for machinery like hydra presses, a structured approach is crucial. This checklist serves as a practical guide to help buyers navigate the sourcing process effectively, ensuring that they make informed decisions that align with their operational needs and budget constraints.
Step 1: Define Your Technical Specifications
Clearly outline the technical specifications required for your hydra press. Consider factors such as tonnage capacity, platen size, and cycle speed. This step is essential to ensure that the press meets your production needs and integrates seamlessly with existing equipment.
- Tonnage Capacity: Determine the maximum force needed for your applications, as hydra presses can range from 20 to 1000 tons.
- Platen Size: Identify the dimensions required for your specific projects to prevent future operational bottlenecks.
Step 2: Identify Your Application Needs
Understanding the primary application of the hydra press will guide your sourcing decisions. Different presses are suited for various tasks, such as metal forming, plastic thermoforming, or waste management.
- Material Types: Clarify whether you will be pressing metals, plastics, or other materials.
- Process Requirements: Consider if you need features like automatic gauging systems or advanced safety controls.
Step 3: Evaluate Potential Suppliers
Before making a commitment, it’s crucial to vet suppliers thoroughly. Look for established manufacturers with a solid reputation in the industry.
- Supplier Profiles: Request company backgrounds, product catalogs, and case studies that demonstrate their expertise.
- References: Seek testimonials or references from other businesses in your region or industry to gauge reliability and service quality.
Step 4: Assess Compliance and Certifications
Verify that the suppliers meet international safety and quality standards. Compliance with certifications such as ISO can be indicative of a supplier’s commitment to quality and safety.
- Safety Standards: Check for certifications relevant to your region, such as CE marking in Europe or ANSI standards in the U.S.
- Quality Assurance: Ensure that the supplier has a documented quality control process in place.
Step 5: Request Detailed Quotes
Once you have shortlisted suppliers, request detailed quotes that encompass all costs involved, including shipping, installation, and training.
- Breakdown of Costs: Ensure quotes include itemized pricing for the equipment, accessories, and any additional services.
- Warranty and Support: Inquire about warranty terms and after-sales support, as these can significantly impact long-term operational costs.
Step 6: Conduct a Site Visit or Virtual Tour
If feasible, visiting the supplier’s facility can provide valuable insights into their operations. Alternatively, request a virtual tour to observe their manufacturing processes and quality assurance measures.
- Production Capabilities: Assess their production capabilities and lead times to ensure they can meet your demands.
- Technology and Equipment: Evaluate the technology and machinery used in production to ensure they align with modern manufacturing practices.
Step 7: Finalize the Contract
Once you’ve completed due diligence, finalize the contract with clear terms regarding delivery, payment, and service agreements.
- Legal Review: Consider having a legal expert review the contract to ensure all terms are fair and transparent.
- Payment Terms: Establish clear payment terms that protect your interests while being agreeable to the supplier.
By following this structured checklist, international B2B buyers can streamline their sourcing process for hydra presses, reducing risks and ensuring they select the most suitable equipment for their operational needs.
Comprehensive Cost and Pricing Analysis for hydra presses Sourcing
What Are the Key Cost Components in Hydra Press Sourcing?
When sourcing hydra presses, understanding the cost structure is crucial for international B2B buyers. The primary components that contribute to the overall cost include:
-
Materials: The cost of raw materials varies significantly based on the type of press and specifications. High-grade steel and hydraulic components typically represent a substantial portion of the material costs. Buyers should consider sourcing from regions with lower material costs without compromising quality.
-
Labor: Labor costs can fluctuate based on geographic location. In regions like Africa and South America, labor may be less expensive, but the skill level and availability of specialized workers should be assessed. In contrast, Europe may offer higher labor costs but potentially greater expertise in precision engineering.
-
Manufacturing Overhead: This includes costs associated with factory operations, utilities, and maintenance. Efficient manufacturing processes can lead to lower overhead costs, which is a key consideration when evaluating suppliers.
-
Tooling: Custom tooling can add to the initial setup costs. Buyers should inquire about tooling options and whether the supplier can accommodate specific needs without excessive charges.
-
Quality Control (QC): Implementing rigorous QC measures can increase costs but is essential for ensuring product reliability. Buyers should evaluate the supplier’s quality certifications and testing protocols to gauge the level of QC involved.
-
Logistics: Shipping costs can vary widely based on the supplier’s location and the chosen shipping method. International buyers should be aware of potential customs fees and import taxes that can impact total costs.
-
Margin: Suppliers typically apply a profit margin on top of the base costs. Understanding the typical margin in the hydra press market can aid buyers in recognizing fair pricing.
How Do Price Influencers Affect Hydra Press Costs?
Several factors can significantly influence the pricing of hydra presses:
-
Volume/MOQ (Minimum Order Quantity): Larger orders often lead to discounts. International buyers should assess their production needs to leverage better pricing through bulk purchases.
-
Specifications and Customization: Custom features increase costs. Buyers should clearly define their requirements to avoid unnecessary expenses related to modifications.
-
Materials Used: The choice of materials directly affects pricing. High-performance materials may incur higher costs but can enhance the press’s durability and efficiency.
-
Quality and Certifications: Suppliers with recognized quality certifications (e.g., ISO) may charge a premium. However, this often translates to better reliability and performance.
-
Supplier Factors: The supplier’s reputation and history can influence pricing. Established suppliers may have higher prices but offer better support and service.
-
Incoterms: Understanding Incoterms (International Commercial Terms) is vital for determining who bears the shipping costs and risks during transit. This can impact the total landed cost of the equipment.
What Are the Best Buyer Tips for Cost-Efficiency?
For international B2B buyers, particularly from Africa, South America, the Middle East, and Europe, employing strategic purchasing methods can lead to significant cost savings:
-
Negotiate Terms: Always negotiate pricing, payment terms, and delivery schedules. Building a rapport with suppliers can lead to favorable conditions.
-
Consider Total Cost of Ownership (TCO): Evaluate not just the purchase price but also maintenance, operational costs, and potential downtime. A lower upfront cost might lead to higher long-term expenses.
-
Research Multiple Suppliers: Obtain quotes from various suppliers to compare pricing and terms. This can provide leverage in negotiations and help identify the best overall value.
-
Leverage Local Expertise: Engage with local partners or consultants who understand the regional market dynamics. They can provide insights into effective sourcing strategies and potential cost-saving opportunities.
-
Stay Informed on Pricing Trends: Monitor industry trends and price fluctuations in the hydra press market. Understanding market dynamics can help buyers make informed purchasing decisions.
Disclaimer on Indicative Prices
Prices for hydra presses can vary widely based on specifications, supplier location, and market conditions. It’s essential for buyers to conduct thorough research and obtain detailed quotes tailored to their specific needs before making a purchase decision.
Alternatives Analysis: Comparing hydra presses With Other Solutions
When considering the purchase of hydraulic equipment, B2B buyers must evaluate various solutions available in the market. While hydra presses are a robust option for many applications, alternative technologies can also fulfill similar roles, often with distinct advantages and drawbacks. Understanding these alternatives can help buyers make informed decisions tailored to their specific operational needs.
Comparison Aspect | Hydra Presses | Electro-Mechanical Presses | Mechanical Presses |
---|---|---|---|
Performance | High force application with adjustable tonnage; effective for various materials | High precision with repeatable performance; ideal for light to medium applications | High-speed operation with robust performance; suited for heavy-duty tasks |
Cost | Moderate to high initial investment; long-term savings on maintenance | Typically lower initial costs; potential higher operational costs | Generally lower cost; potential for higher maintenance due to wear |
Ease of Implementation | Requires specialized setup; user training needed | Plug-and-play design; easy to operate | Standard setup; requires skilled operators |
Maintenance | Moderate maintenance needs; durable components | Low maintenance; advanced digital controls | High maintenance due to mechanical wear; regular checks necessary |
Best Use Case | Ideal for plastic thermoforming and die-cutting | Best for precision compacting in lighter materials | Excellent for high-volume, heavy-duty stamping |
What are the advantages and disadvantages of Electro-Mechanical Presses?
Electro-mechanical presses are gaining popularity due to their cost-effectiveness and precision. They operate using electric motors to drive the press, which allows for a high degree of control over the pressing process. This technology is particularly advantageous for applications requiring consistent pressure and speed, such as in the production of small, intricate components. However, they may not be suitable for heavy-duty tasks, as their capacity is generally lower than that of hydra presses. Additionally, the reliance on electronic systems may lead to higher operational costs if technical issues arise.
How do Mechanical Presses compare to Hydra Presses?
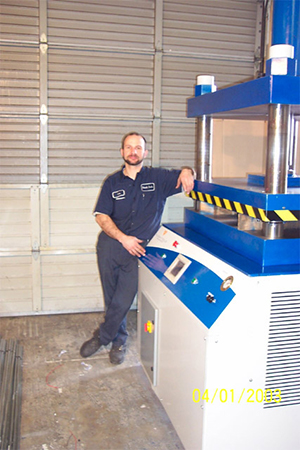
A stock image related to hydra presses.
Mechanical presses, known for their durability and high-speed operation, are often favored in industries requiring heavy-duty stamping and forming applications. They can produce parts at a rapid rate and are ideal for high-volume production runs. However, the mechanical components are subject to wear and tear, leading to higher maintenance requirements compared to hydra presses. While the initial investment may be lower, the long-term costs can increase due to maintenance and replacement parts.
Conclusion: How should B2B buyers choose the right solution for their needs?
When choosing between hydra presses and alternative technologies, B2B buyers should consider their specific operational requirements, including production volume, material types, and budget constraints. Hydra presses excel in applications requiring high force and flexibility, while electro-mechanical and mechanical presses may be more suitable for precision tasks or heavy-duty operations, respectively. By assessing the performance, cost, ease of implementation, and maintenance needs of each option, buyers can select the most appropriate solution that aligns with their production goals and operational efficiency.
Essential Technical Properties and Trade Terminology for hydra presses
What Are the Key Technical Properties of Hydra Presses?
When considering the purchase of hydra presses, understanding specific technical properties is crucial for ensuring the right fit for your production needs. Here are some essential specifications to consider:
-
Tonnage Capacity
– Tonnage capacity refers to the maximum force a hydra press can exert, typically measured in tons. Common capacities range from 4 tons to over 1,000 tons. The capacity needed depends on the material being processed and the complexity of the operations. For buyers in sectors like automotive or heavy manufacturing, selecting a press with the appropriate tonnage ensures efficiency and avoids equipment damage. -
Platen Size
– Platen size indicates the dimensions of the pressing surface. A standard size, such as 36″ x 48″, is common, but custom sizes may be required for specific applications. A larger platen allows for processing larger materials, which is particularly beneficial for manufacturers in industries like aerospace or construction where component sizes can vary significantly. -
Shut Height
– The shut height represents the distance between the upper and lower platens when the press is closed. Typical ranges are between 2″ and 12″. Understanding this measurement is essential for ensuring that the hydra press can accommodate the thickness of the materials being processed, thus impacting production efficiency. -
Cycle Time
– Cycle time refers to the duration it takes for the press to complete one full operation cycle. Options like continuous, single, or dwell cycles can greatly affect productivity. For businesses focused on high-volume production, a shorter cycle time can significantly increase throughput, making it a critical factor in purchasing decisions. -
Control Systems
– Modern hydra presses often feature advanced digital control systems, such as SIEMENS PC-based controls, allowing for precise adjustments and monitoring of operations. This capability can enhance operational efficiency and reduce downtime, important for international buyers looking to optimize production processes. -
Safety Features
– Safety features, including two-hand anti-tie-down switches and emergency stop mechanisms, are vital for ensuring workplace safety. Compliance with international safety standards can protect your workforce and minimize liability, making it a key consideration for buyers across different regions.
What Are Common Trade Terms Related to Hydra Presses?
In addition to understanding the technical specifications, familiarity with industry jargon can facilitate smoother negotiations and transactions. Here are several important trade terms:
-
OEM (Original Equipment Manufacturer)
– This term refers to companies that produce parts or equipment that may be marketed by another manufacturer. For B2B buyers, sourcing from reputable OEMs can ensure quality and compatibility with existing systems. -
MOQ (Minimum Order Quantity)
– MOQ specifies the smallest amount of a product that a supplier is willing to sell. Understanding MOQ is crucial for inventory management and budgeting, particularly for businesses in regions with varying demand levels. -
RFQ (Request for Quotation)
– An RFQ is a formal document sent to suppliers requesting pricing and terms for specific products or services. For international buyers, issuing RFQs can help compare offers and negotiate better terms. -
Incoterms (International Commercial Terms)
– These are standardized terms used in international shipping to define the responsibilities of buyers and sellers. Familiarity with Incoterms can help mitigate risks related to shipping costs and delivery timelines, which is particularly beneficial for businesses operating across borders. -
Lead Time
– Lead time refers to the time taken from placing an order to delivery. For B2B buyers, understanding lead times can aid in project planning and inventory management, ensuring that production schedules are met without delays. -
Warranty and After-Sales Support
– This term encompasses the guarantees provided by manufacturers regarding the performance of their equipment and the support offered post-purchase. Buyers should prioritize suppliers who offer comprehensive warranty terms and accessible after-sales service, ensuring long-term operational reliability.
By equipping yourself with knowledge of both technical properties and trade terminology, you can make informed purchasing decisions that align with your business goals.
Navigating Market Dynamics and Sourcing Trends in the hydra presses Sector
What Are the Current Market Dynamics and Key Trends in the Hydra Presses Sector?
The hydra presses market is experiencing significant transformations driven by technological advancements, increased automation, and a growing emphasis on efficiency and productivity. The demand for hydraulic presses is being fueled by the expanding manufacturing sectors across Africa, South America, the Middle East, and Europe. Key trends include the integration of IoT capabilities, enabling real-time monitoring and predictive maintenance, which enhance operational efficiency and reduce downtime. Additionally, the use of energy-efficient hydraulic systems is becoming prevalent, driven by the need for cost savings and sustainability.
In emerging markets, international B2B buyers are increasingly looking for versatile machines that can accommodate various applications, from metal stamping to plastic forming. The shift towards automation, including robotic part removal systems, is also evident, as manufacturers seek to minimize labor costs and improve production rates. As global supply chains evolve, B2B buyers must remain adaptable, leveraging local partnerships and sourcing options to enhance their operational resilience in a competitive landscape.
How Can Sustainability and Ethical Sourcing Impact B2B Buyers in the Hydra Presses Sector?
Sustainability is a critical consideration for international B2B buyers, particularly in the hydra presses sector, where the environmental impact of manufacturing processes is under scrutiny. The industry is moving towards greener practices, with many manufacturers adopting eco-friendly materials and processes that reduce waste and energy consumption. Buyers should prioritize suppliers who demonstrate commitment to sustainability through certifications such as ISO 14001 or adherence to the European Union’s Eco-Design Directive.
Ethical sourcing is equally important, as buyers increasingly seek transparency in their supply chains. This includes understanding the sourcing of raw materials, labor practices, and the overall environmental footprint of the production process. B2B buyers can enhance their brand reputation by collaborating with suppliers who prioritize ethical practices, which can also lead to improved customer loyalty and satisfaction.
What Is the Brief Evolution of Hydra Presses and Their Importance in the B2B Context?
Hydra presses have evolved significantly since their inception, transitioning from simple mechanical devices to sophisticated hydraulic machines equipped with advanced control systems. Initially used in basic manufacturing processes, the introduction of programmable logic controllers (PLCs) and digital interfaces has transformed their functionality, making them adaptable for various applications. This evolution is crucial for B2B buyers, as modern hydra presses offer enhanced precision, efficiency, and versatility, enabling companies to meet diverse production demands.
The ongoing development of hydraulic press technology reflects broader trends in manufacturing, including the move towards automation and smart manufacturing. For B2B buyers, investing in state-of-the-art hydra presses not only optimizes production capabilities but also aligns with the industry’s shift towards sustainable practices, providing a competitive edge in a rapidly changing market landscape.
Frequently Asked Questions (FAQs) for B2B Buyers of hydra presses
-
How do I solve issues related to the maintenance of hydra presses?
Maintaining hydra presses is crucial for ensuring longevity and optimal performance. Regular inspections, lubrication of moving parts, and checking hydraulic fluid levels are essential. It’s also advisable to establish a routine for cleaning the press and its components to prevent build-up that can lead to malfunctions. Engaging with the manufacturer for guidance on maintenance schedules and acquiring genuine spare parts can further enhance reliability. If issues persist, consider consulting with a qualified technician who specializes in hydraulic systems. -
What is the best type of hydra press for high-volume production?
For high-volume production, consider hydraulic presses with automated features and higher tonnage capacities, typically ranging from 200 to 1,000 tons. Look for models that offer quick change tooling options, high-speed operation, and robust safety features. Brands that integrate advanced digital controls for monitoring and adjusting parameters in real-time can significantly boost efficiency. Always assess your specific production requirements, including material types and cycle times, to select the most suitable press. -
How can I effectively vet suppliers of hydra presses?
When vetting suppliers, start by reviewing their industry reputation through online reviews, case studies, and customer testimonials. Request references and check their experience with international shipping and compliance with local regulations in your region. Evaluate their quality control processes and certifications, such as ISO standards. Additionally, consider their after-sales support, warranty offerings, and responsiveness to inquiries. Engaging in direct communication with potential suppliers can also provide insight into their reliability and professionalism. -
What are the typical payment terms for purchasing hydra presses internationally?
Payment terms for international purchases can vary widely based on supplier policies and buyer-seller relationships. Common terms include 30% deposit upon order confirmation, with the balance due prior to shipping or upon delivery. Letters of credit (LC) are often used for larger transactions to mitigate risks. Always clarify payment methods, currency exchange implications, and potential additional fees with suppliers to avoid misunderstandings. Establishing clear payment agreements in advance will help facilitate smoother transactions. -
What are the customization options available for hydra presses?
Customization options for hydra presses can include adjustments in tonnage capacity, platen sizes, and additional features such as automated part removal systems or integrated data collection. Many manufacturers also offer specialized tooling for specific applications, such as deep drawing or precision stamping. When discussing customization, ensure that the supplier understands your operational needs and can provide tailored solutions. It’s advisable to request prototypes or demonstrations if possible to validate the effectiveness of custom features. -
How do I ensure quality assurance when sourcing hydra presses?
To ensure quality assurance, request detailed product specifications and manufacturing standards from your supplier. Conduct factory visits if feasible or arrange for third-party inspections during the production process. Verify that the manufacturer follows strict quality control protocols and holds relevant certifications, such as ISO 9001. Additionally, consider implementing a trial run of the press to assess its performance before final acceptance. Establishing a clear return policy in case of defects can also safeguard your investment. -
What logistics considerations should I keep in mind when importing hydra presses?
When importing hydra presses, consider the logistics of shipping, including freight costs, shipping times, and customs clearance procedures. It’s important to choose a reliable freight forwarder familiar with heavy machinery transport and regulations in your destination country. Ensure that all necessary documentation, such as commercial invoices and certificates of origin, is prepared for smooth customs processing. Be aware of potential import duties and taxes, and factor these into your overall budget to avoid unexpected expenses. -
What are the common applications of hydra presses in different industries?
Hydra presses are versatile and widely used across various industries, including automotive, aerospace, and manufacturing. Common applications include metal stamping, plastic thermoforming, and material compaction for waste management. In the automotive sector, they are essential for producing parts like brackets and panels. In waste management, hydra presses efficiently compact and dewater waste materials. Understanding the specific applications relevant to your industry will help you select the right press and maximize its utility in your operations.
Important Disclaimer & Terms of Use
⚠️ Important Disclaimer
The information provided in this guide, including content regarding manufacturers, technical specifications, and market analysis, is for informational and educational purposes only. It does not constitute professional procurement advice, financial advice, or legal advice.
While we have made every effort to ensure the accuracy and timeliness of the information, we are not responsible for any errors, omissions, or outdated information. Market conditions, company details, and technical standards are subject to change.
B2B buyers must conduct their own independent and thorough due diligence before making any purchasing decisions. This includes contacting suppliers directly, verifying certifications, requesting samples, and seeking professional consultation. The risk of relying on any information in this guide is borne solely by the reader.
Strategic Sourcing Conclusion and Outlook for hydra presses
What Are the Key Takeaways for B2B Buyers of Hydra Presses?
Strategic sourcing of hydra presses is essential for B2B buyers aiming to enhance operational efficiency and productivity. These versatile machines are not only pivotal in manufacturing processes but also offer adaptability across various industries, including automotive, aerospace, and environmental management. By understanding the specifications and capabilities of different models—ranging from 20 to 1,000 tons—buyers can select the right equipment to meet their unique production demands.
How Does Strategic Sourcing Impact Cost Efficiency?
Investing in the right hydra press can lead to significant cost savings through improved production rates and reduced waste. Moreover, leveraging remanufactured options can provide a cost-effective alternative without compromising quality. Buyers should prioritize suppliers who offer comprehensive support, including maintenance and automation options, to maximize the longevity and performance of their presses.
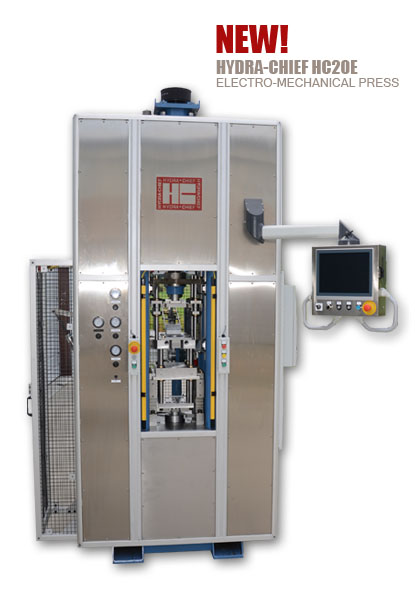
A stock image related to hydra presses.
What Should International Buyers Consider Moving Forward?
As the market for hydra presses evolves, international buyers from Africa, South America, the Middle East, and Europe should remain proactive in their sourcing strategies. Engaging with manufacturers who prioritize innovation and sustainable practices will be crucial in navigating future challenges. By fostering strong supplier relationships and continuously assessing technological advancements, buyers can ensure they remain competitive in an increasingly globalized market. Embrace the future of manufacturing by strategically sourcing your hydra presses today—your operational success depends on it.