Unlock Cost Savings: The Complete Metal Shredder Guide (2025)
Introduction: Navigating the Global Market for metal shredder
Navigating the global market for metal shredders poses a significant challenge for international B2B buyers, particularly those from Africa, South America, the Middle East, and Europe. As industries increasingly seek sustainable solutions for waste management, sourcing the right metal shredder becomes crucial. This guide aims to demystify the complexities surrounding metal shredders, covering essential aspects such as types, applications, supplier vetting, and cost considerations. Whether you are looking for heavy-duty shredders to process steel and aluminum or specialized units for electronic waste, understanding the various options available can empower your purchasing decisions.
In a world where efficiency and sustainability are paramount, selecting the right shredding equipment not only enhances operational productivity but also significantly reduces waste disposal costs. This comprehensive guide provides actionable insights tailored to the unique needs of international buyers. It equips you with the knowledge necessary to evaluate potential suppliers, ensuring that you invest in reliable machinery that meets both regulatory standards and operational demands.
By following this guide, businesses in regions like Argentina and Turkey can make informed decisions that align with their specific market requirements and sustainability goals, ultimately driving profitability and operational excellence. Whether you’re a seasoned buyer or new to the industry, this resource will serve as your roadmap to navigating the metal shredder market effectively.
Understanding metal shredder Types and Variations
Type Name | Key Distinguishing Features | Primary B2B Applications | Brief Pros & Cons for Buyers |
---|---|---|---|
Single-Shaft Shredders | High-speed operation, single rotor design | General metal recycling, small scrap processing | Pros: Efficient for smaller volumes; Cons: Limited to softer metals. |
Twin-Shaft Shredders | Low-speed, high-torque operation, dual rotor configuration | Heavy-duty scrap metal processing | Pros: Handles tough materials; Cons: Higher initial investment. |
Industrial Metal Shredders | Versatile, robust construction, customizable knife systems | Large-scale recycling, e-waste, automotive parts | Pros: High throughput; Cons: Requires significant space and power. |
Mobile Metal Shredders | Portable units, often mounted on trucks | On-site metal recycling, construction sites | Pros: Flexibility and mobility; Cons: May have lower throughput. |
Granulators | Smaller, more precise cutting mechanisms | Fine metal shredding, preparation for recycling | Pros: Ideal for precision; Cons: Slower processing speed. |
What Are the Characteristics of Single-Shaft Shredders?
Single-shaft shredders are designed for high-speed operation and feature a single rotor that rotates against a fixed bed knife. This design is particularly effective for processing softer metals and smaller volumes of scrap. B2B buyers looking for efficient solutions for general metal recycling or small scrap processing will find these shredders suitable. However, they may not be ideal for thicker materials, which could limit their application scope.
How Do Twin-Shaft Shredders Stand Out?
Twin-shaft shredders operate at low speeds but with high torque, employing a dual rotor configuration to handle tougher materials effectively. This makes them the go-to choice for heavy-duty scrap metal processing, including steel and aluminum. For B2B buyers in industries dealing with significant metal waste, these shredders provide robust performance. The downside is their higher initial investment, but the long-term durability and efficiency often justify the costs.
What Makes Industrial Metal Shredders Versatile?
Industrial metal shredders are characterized by their robust construction and customizable knife systems, enabling them to process a wide variety of materials, from e-waste to automotive parts. Their high throughput makes them suitable for large-scale recycling operations. B2B buyers should consider their space and power requirements, as these machines often need significant infrastructure. The investment is worthwhile for businesses looking to maximize recycling efficiency.
Why Consider Mobile Metal Shredders?
Mobile metal shredders are designed for portability, often mounted on trucks to facilitate on-site metal recycling. This flexibility is especially beneficial for construction sites or remote locations where transporting scrap is impractical. While they provide the advantage of mobility, buyers should be aware that these units may have lower throughput compared to stationary models, making them suitable for specific applications where flexibility is paramount.
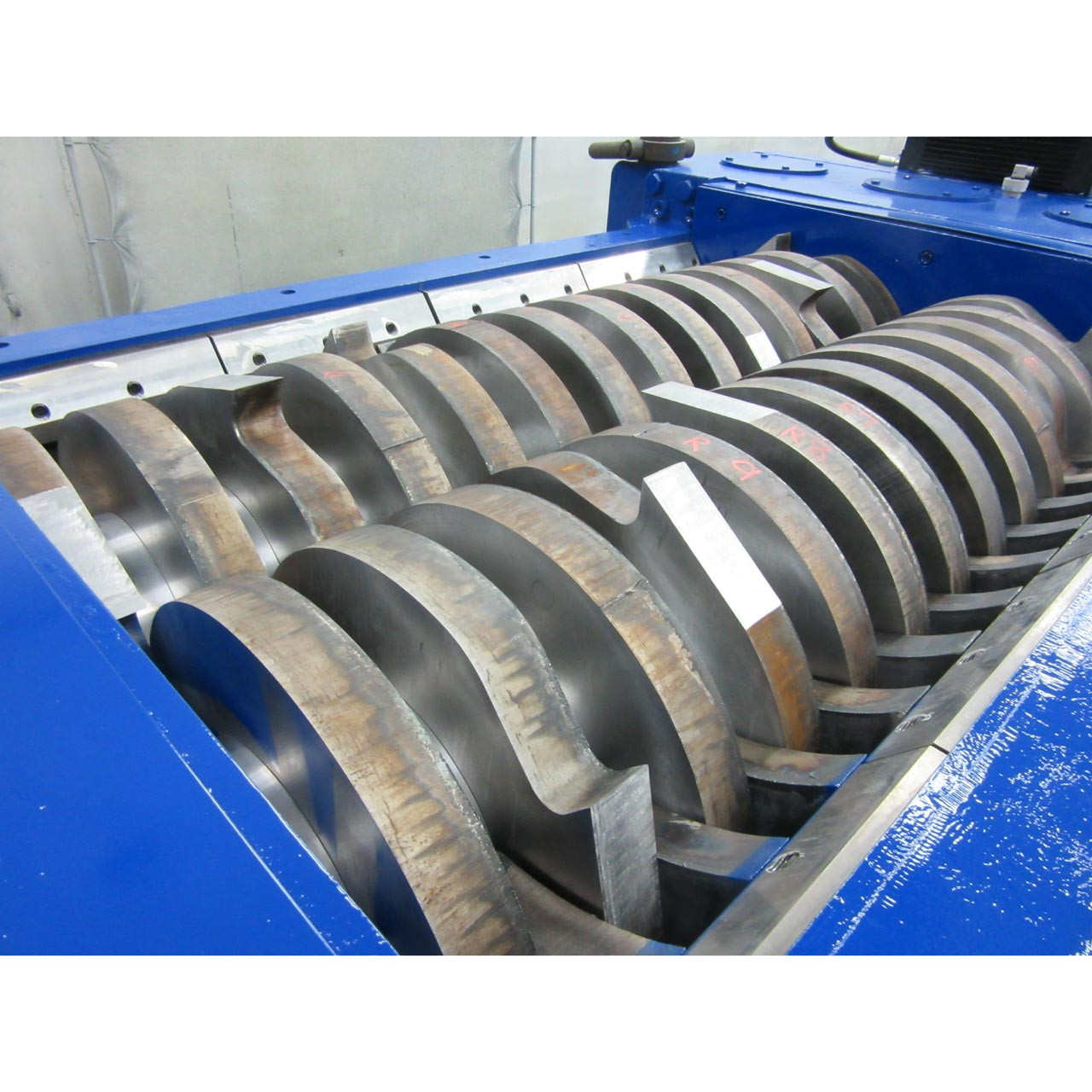
A stock image related to metal shredder.
What Are the Advantages of Granulators?
Granulators are smaller shredding machines that focus on precision cutting, making them ideal for fine metal shredding and preparing materials for recycling. They are particularly useful in applications where a specific shred size is required. However, their processing speed is generally slower compared to other types of shredders. B2B buyers looking for precision and specific output sizes will find granulators valuable, but they should also consider their operational speed in relation to overall production goals.
Key Industrial Applications of metal shredder
Industry/Sector | Specific Application of Metal Shredder | Value/Benefit for the Business | Key Sourcing Considerations for this Application |
---|---|---|---|
Automotive Recycling | Shredding end-of-life vehicles (ELVs) | Reduces waste volume, recovers valuable metals for resale | Capacity, shred size, and compatibility with various materials |
Construction & Demolition | Processing scrap metal from construction sites | Efficient waste management, promotes recycling initiatives | Durability, ease of maintenance, and throughput capacity |
Electronics Recycling | Shredding e-waste like circuit boards and hard drives | Safe disposal of hazardous materials, recovery of precious metals | Compliance with regulations, shred size, and energy efficiency |
Manufacturing | Shredding metal scrap from production processes | Minimizes disposal costs, improves material recovery rates | Customization options, operational efficiency, and machine reliability |
Metal Fabrication | Recycling metal offcuts and trimmings | Reduces production waste, enhances sustainability efforts | Versatility in handling different metal types, maintenance requirements |
How is Metal Shredder Used in Automotive Recycling?
In the automotive recycling sector, metal shredders are vital for processing end-of-life vehicles (ELVs). These machines efficiently break down vehicles into manageable scrap, allowing for the recovery of valuable metals such as aluminum and steel. By reducing the waste volume, companies can significantly enhance their profitability while promoting sustainable practices. International buyers, especially from regions like Africa and South America, should consider the shredder’s capacity and shred size to meet local regulatory requirements and market demands.
What Role Does Metal Shredding Play in Construction & Demolition?
Metal shredders are essential for managing scrap metal generated from construction and demolition activities. By processing this waste, companies can efficiently recycle materials, thereby minimizing landfill contributions and promoting environmental sustainability. For international buyers, particularly in the Middle East and Europe, sourcing shredders with high durability and ease of maintenance is crucial to ensure continuous operation in challenging environments and to handle the bulkiness of construction debris.
How is Metal Shredder Essential in Electronics Recycling?
In the electronics recycling industry, metal shredders are used to process e-waste, such as circuit boards and hard drives. These shredders help safely dispose of hazardous materials while recovering precious metals like gold and copper. Compliance with stringent regulations regarding e-waste disposal is a significant consideration for buyers in regions like Europe and South America. Therefore, selecting shredders that ensure effective size reduction and energy efficiency is critical for successful operations.
How Do Metal Shredders Benefit Manufacturing Operations?
Manufacturers utilize metal shredders to process scrap generated during production, effectively minimizing disposal costs and enhancing material recovery rates. By shredding metal offcuts, businesses can recycle materials for reuse in production, thereby improving their bottom line. For international buyers, particularly in emerging markets like Africa and South America, it is essential to evaluate customization options and operational efficiency to ensure that the shredding system aligns with specific manufacturing needs.
Why is Metal Shredding Important in Metal Fabrication?
In metal fabrication, shredders are employed to recycle metal trimmings and offcuts, reducing production waste and promoting sustainability. This process not only helps in conserving resources but also supports companies in meeting their corporate social responsibility goals. Buyers, especially from regions with growing environmental regulations, should focus on shredders capable of handling various metal types and ensuring minimal downtime through reliable maintenance practices.
3 Common User Pain Points for ‘metal shredder’ & Their Solutions
Scenario 1: Inefficient Material Processing in Metal Recycling
The Problem: Many B2B buyers in the metal recycling industry face the challenge of inefficient processing of scrap metals, leading to low productivity and increased operational costs. For instance, companies may find that their current shredders are unable to handle the volume of metal waste generated, causing bottlenecks in the recycling process. This inefficiency can result in higher labor costs and extended processing times, ultimately impacting profitability.
The Solution: To overcome this issue, buyers should consider investing in high-capacity metal shredders that are specifically designed for their volume requirements. When sourcing a shredder, it is crucial to evaluate its throughput capabilities, which should align with your business’s operational needs. For example, the Shred-Tech ST-400 industrial shredder offers throughput options ranging from 1 to over 3 tons per hour, making it suitable for various capacities. Additionally, selecting a machine with customizable knife configurations can optimize shred size and improve downstream processing efficiency. Regular maintenance and periodic performance evaluations of the shredding equipment can further enhance productivity and reduce unplanned downtime, allowing for smoother operations.
Scenario 2: High Operating Costs Due to Equipment Downtime
The Problem: B2B buyers often encounter high operating costs due to frequent equipment downtime caused by maintenance issues. Metal shredders are subjected to heavy wear and tear, especially when processing tough materials like steel and aluminum. This downtime can lead to increased labor expenses and lost revenue opportunities, as the recycling process grinds to a halt while repairs are conducted.
The Solution: To mitigate these costs, businesses should prioritize the selection of shredders known for their durability and low maintenance requirements. For example, choosing a shredder with a robust design, such as the TASKMASTER® twin-shaft shredder, can significantly reduce maintenance frequency. Additionally, implementing a proactive maintenance schedule that includes regular inspections and timely replacement of wear parts can help preemptively address potential issues. Training operational staff on proper handling and usage of the shredders is also vital to prolonging equipment lifespan and minimizing operational disruptions. Investing in quality spare parts from reputable suppliers ensures that repairs can be executed quickly without compromising the shredder’s performance.
Scenario 3: Challenges in Handling Diverse Metal Types
The Problem: International B2B buyers often struggle with shredding a wide variety of metal types, which can complicate the recycling process. For example, companies that handle both ferrous and non-ferrous metals may find that their existing shredders lack the versatility needed to effectively process different materials. This limitation can result in suboptimal shred sizes, increased contamination rates, and ultimately lower profitability.
The Solution: To address this challenge, buyers should consider investing in versatile shredders that can efficiently handle multiple metal types. Metal shredders like those from Franklin Miller are designed to manage a broad range of applications, including steel drums, aluminum scrap, and even electronic waste. When specifying a shredder, it is essential to look for features such as adjustable cutting configurations and the ability to switch between different knife profiles. Furthermore, integrating a modular shredding system can allow businesses to easily adapt to changing material streams and market demands. Regular training for operators on how to best utilize the shredder’s features can enhance the efficiency of the shredding process and ensure the highest quality output for recycling.
Strategic Material Selection Guide for metal shredder
What Are the Key Materials Used in Metal Shredders?
When selecting a metal shredder, understanding the materials used in its construction is crucial for optimizing performance and ensuring longevity. Here, we analyze four common materials: Carbon Steel, Stainless Steel, Cast Iron, and Alloy Steel. Each material has unique properties, advantages, and limitations that can significantly impact operational efficiency, especially for international B2B buyers.
How Does Carbon Steel Perform in Metal Shredders?
Key Properties: Carbon steel is known for its high tensile strength and hardness, making it suitable for heavy-duty applications. It typically has a temperature rating up to 400°F and can withstand moderate pressure.
Pros & Cons: The primary advantage of carbon steel is its durability and cost-effectiveness, making it a popular choice for shredder blades. However, it is prone to corrosion if not properly treated, which can lead to premature wear. Additionally, manufacturing complexity can increase if specialized treatments are required.
Impact on Application: Carbon steel blades are effective for shredding various metals, including aluminum and steel, but may require additional coatings or treatments for optimal performance in humid or corrosive environments.
Considerations for International Buyers: Buyers from regions like Africa and South America should ensure compliance with local corrosion resistance standards, as untreated carbon steel may not withstand environmental conditions in these areas.
What Are the Benefits of Using Stainless Steel in Metal Shredders?
Key Properties: Stainless steel offers excellent corrosion resistance and can handle high temperatures, making it ideal for diverse applications. It typically has a pressure rating that allows it to withstand significant operational stress.
Pros & Cons: The key advantage of stainless steel is its longevity and reduced maintenance needs due to its resistance to rust. However, it comes at a higher cost compared to carbon steel and can be more challenging to machine, which may increase manufacturing complexity.
Impact on Application: Stainless steel is particularly suited for shredding applications involving food-grade materials or environments requiring strict hygiene standards, such as medical waste.
Considerations for International Buyers: Buyers in Europe and the Middle East should be aware of specific standards (like ASTM and DIN) for stainless steel grades to ensure compliance with industry regulations.
Why Choose Cast Iron for Metal Shredders?
Key Properties: Cast iron is known for its excellent wear resistance and ability to absorb vibrations, which can enhance shredder performance. It typically has a lower tensile strength compared to steel but excels in compressive strength.
Pros & Cons: The primary advantage of cast iron is its durability and ability to withstand heavy loads, making it suitable for stationary shredders. However, it is brittle and can crack under high-impact conditions, which limits its application in mobile shredders.
Impact on Application: Cast iron is often used in the construction of shredder frames and housings, providing stability and support for heavy-duty operations.
Considerations for International Buyers: Buyers in regions with high temperatures or seismic activity, such as parts of South America and the Middle East, should consider the structural integrity of cast iron under such conditions.
What Are the Advantages of Alloy Steel in Metal Shredders?
Key Properties: Alloy steel combines various elements to enhance specific properties, such as toughness and wear resistance. It typically maintains high strength at elevated temperatures and has a good pressure rating.
Pros & Cons: The main advantage of alloy steel is its versatility and performance in demanding applications. However, it can be more expensive to produce and may require specialized machining techniques.
Impact on Application: Alloy steel is often used in high-performance shredders designed for processing tough materials like heavy metals and electronic waste.
Considerations for International Buyers: Buyers should consider the specific alloy composition to ensure it meets local standards and application requirements, especially in Europe where regulations may be stricter.
Summary Table of Material Selection for Metal Shredders
Material | Typical Use Case for Metal Shredder | Key Advantage | Key Disadvantage/Limitation | Relative Cost (Low/Med/High) |
---|---|---|---|---|
Carbon Steel | Heavy-duty shredding of metals | Cost-effective and durable | Prone to corrosion without treatment | Low |
Stainless Steel | Food-grade and medical waste shredding | Excellent corrosion resistance | Higher cost and machining complexity | High |
Cast Iron | Shredder frames and housings | Good wear resistance and stability | Brittle and can crack under impact | Medium |
Alloy Steel | High-performance shredding applications | Versatile and high-performance | More expensive and specialized machining required | High |
This strategic material selection guide provides international B2B buyers with essential insights to make informed decisions when investing in metal shredders, ensuring they choose the most suitable materials for their specific needs and operational environments.
In-depth Look: Manufacturing Processes and Quality Assurance for metal shredder
What Are the Key Stages in the Manufacturing Process of Metal Shredders?
The manufacturing process of metal shredders involves several critical stages designed to ensure both efficiency and quality. Understanding these stages is essential for international B2B buyers, particularly those in Africa, South America, the Middle East, and Europe, as they can influence purchasing decisions and operational efficiency.
1. Material Preparation
The first stage of manufacturing metal shredders is material preparation. This involves sourcing high-quality raw materials such as hardened steel for the cutting blades and robust metals for the body of the shredder. Suppliers often follow specific material specifications to ensure durability and performance. Buyers should inquire about the type of materials used and their origin, as this can impact the shredder’s longevity and operational costs.
2. Forming Techniques
Once materials are prepared, the next step is forming. This typically includes processes like machining, welding, and casting. Advanced CNC (Computer Numerical Control) machining is commonly used for precision cutting and shaping of components. For instance, the cutting blades may undergo special heat treatment processes to enhance their hardness and resistance to wear. B2B buyers should consider the forming techniques used, as they directly affect the shredder’s performance and maintenance needs.
3. Assembly Process
The assembly stage is where all the components come together. This includes the integration of the drive system, cutting chamber, and control panels. Manufacturers often employ skilled technicians to ensure that each part is correctly assembled to maintain operational integrity. It’s advisable for buyers to ask about the assembly protocols and whether they include any automated systems for quality assurance, as this can significantly impact the final product’s reliability.
4. Finishing Techniques
Finishing processes such as surface treatment, painting, and coating are vital for enhancing the shredder’s durability and corrosion resistance. These treatments not only improve aesthetics but also protect against wear and tear during operation. Buyers should inquire about the types of finishes used and their expected lifespan, as this can influence maintenance schedules and costs.
How Is Quality Assurance Implemented in Metal Shredder Manufacturing?
Quality assurance (QA) is crucial in the manufacturing of metal shredders, ensuring that each unit meets international standards and customer expectations. For B2B buyers, understanding the QA processes in place can help mitigate risks associated with purchasing equipment.
International Standards and Certifications to Look For
Manufacturers often adhere to internationally recognized standards such as ISO 9001, which outlines the requirements for a quality management system. Additionally, certifications like CE mark (for compliance with European safety standards) and API (American Petroleum Institute) standards are important for equipment used in specific industries. Buyers should always verify these certifications when assessing potential suppliers.
Key Quality Control Checkpoints
Quality control (QC) is integrated at various checkpoints throughout the manufacturing process:
-
Incoming Quality Control (IQC): This stage involves inspecting raw materials upon arrival to ensure they meet specified standards.
-
In-Process Quality Control (IPQC): During assembly and production, various tests are conducted to monitor the manufacturing process. This includes visual inspections and performance tests to identify any defects early.
-
Final Quality Control (FQC): Once the shredder is assembled, a thorough final inspection is conducted. This may involve operational tests to ensure that the machine performs as intended under load.
What Common Testing Methods Are Used in Metal Shredder Quality Assurance?
Testing methods play a significant role in ensuring the reliability and performance of metal shredders. Manufacturers typically employ a variety of testing techniques to validate their products.
-
Functional Testing: This involves operating the shredder under various conditions to ensure it meets performance specifications. It checks for issues such as excessive noise, vibration, or failure to process materials effectively.
-
Durability Testing: Many manufacturers conduct stress tests to simulate long-term use. This helps to identify potential failure points before the product reaches the market.
-
Material Testing: Testing the hardness, tensile strength, and wear resistance of materials used in the shredder components is crucial. This ensures that the materials can withstand the rigors of shredding operations.
How Can B2B Buyers Verify Supplier Quality Control?
For international B2B buyers, especially those from regions like Africa and South America, verifying a supplier’s quality control practices is essential. Here are actionable steps to consider:
-
Conduct Audits: Request to perform on-site audits of the manufacturing facilities. This allows buyers to assess the production environment and QC practices firsthand.
-
Request Quality Reports: Suppliers should provide documentation of their quality control processes, including IQC, IPQC, and FQC results. This transparency can help buyers gauge the reliability of the supplier.
-
Third-Party Inspections: Engaging third-party inspection services can add an extra layer of assurance. These organizations can conduct independent assessments of the manufacturing process and final products.
What Are the Quality Control Nuances for International B2B Buyers?
Navigating the international market presents unique challenges for B2B buyers. Understanding the nuances of quality control can help in making informed purchasing decisions.
-
Cultural and Regulatory Differences: Buyers should be aware that quality standards may vary by region. For example, European standards might be stricter than those in other areas. Understanding these differences can help buyers set appropriate expectations.
-
Language Barriers: Communication can be a challenge when dealing with international suppliers. It’s advisable to have clear, documented communication regarding quality expectations and standards.
-
Post-Purchase Support: Quality assurance does not end with the sale. Buyers should inquire about the supplier’s after-sales support, including spare parts availability and service options, to ensure long-term satisfaction with the equipment.
By understanding these manufacturing processes and quality assurance practices, B2B buyers can make informed decisions when selecting metal shredders that meet their operational needs and compliance requirements.
Practical Sourcing Guide: A Step-by-Step Checklist for ‘metal shredder’
Introduction
Navigating the procurement of a metal shredder can be complex, especially for international B2B buyers from diverse regions such as Africa, South America, the Middle East, and Europe. This checklist provides a structured approach to ensure you make informed decisions when sourcing a metal shredder, maximizing efficiency and profitability while minimizing risks.
Step 1: Define Your Technical Specifications
Before engaging with suppliers, clearly outline the technical specifications required for your metal shredder. Consider factors such as the types of metals you will process, the desired throughput capacity, and the end product size.
– Throughput: Identify the volume of metal you need to shred daily or weekly.
– Metal Types: Ensure the shredder is capable of handling the specific metals relevant to your operations, such as aluminum, steel, or copper.
Step 2: Research Supplier Credentials
Investigate potential suppliers thoroughly to ensure they have the necessary expertise and reliability. Look for manufacturers with a proven track record in the industry and positive customer testimonials.
– Certifications: Check for industry certifications (ISO, CE) that validate their manufacturing processes.
– Experience: Assess their years of operation and case studies of previous installations, especially in your geographical region.
Step 3: Evaluate Potential Suppliers
Before making a commitment, vet suppliers rigorously. Request detailed company profiles, case studies, and references from similar industries or regions.
– Site Visits: If feasible, conduct site visits to verify their operations and meet the team behind the technology.
– Customer Support: Evaluate their after-sales support and maintenance services, which are crucial for long-term operational success.
Step 4: Compare Machine Features and Performance
Analyze the features of different metal shredders to determine which best fits your operational needs. Look for key performance indicators such as energy efficiency, maintenance requirements, and ease of use.
– Cutting Technology: Assess the type of cutting mechanism used (e.g., rotary, twin-shaft) and its suitability for your applications.
– Durability: Examine the materials used in construction to ensure longevity and robustness under heavy use.
Step 5: Request Quotes and Analyze Costs
Obtain detailed quotes from multiple suppliers and break down costs for a comprehensive comparison. Look beyond the initial purchase price to consider total cost of ownership, including installation, maintenance, and operational costs.
– Financing Options: Inquire about financing options or leasing plans that can ease cash flow concerns.
– Warranty and Service Plans: Understand warranty terms and what service plans are available to protect your investment.
Step 6: Assess Compliance with Local Regulations
Ensure that the metal shredder you choose complies with local regulations regarding waste disposal and recycling. This is particularly important in regions with stringent environmental laws.
– Environmental Impact: Consider the shredder’s energy consumption and emissions to align with sustainability goals.
– Regulatory Standards: Confirm that the supplier is knowledgeable about and compliant with local and international standards.
Step 7: Finalize the Purchase and Plan Installation
Once you’ve chosen a supplier, finalize the purchase agreement, ensuring all terms are clear. Plan for installation by coordinating with the supplier to align timelines and responsibilities.
– Training: Ensure that your team receives adequate training on the new equipment to maximize its efficiency.
– Support Structure: Establish a support structure for ongoing maintenance and troubleshooting to prevent operational downtime.
By following this checklist, international B2B buyers can make informed decisions when sourcing metal shredders, ensuring they select the right equipment for their specific needs.
Comprehensive Cost and Pricing Analysis for metal shredder Sourcing
What Are the Key Cost Components for Metal Shredder Sourcing?
When sourcing metal shredders, international B2B buyers must understand the various cost components that contribute to the overall price. These typically include:
- Materials: The quality of materials used in manufacturing metal shredders significantly impacts costs. High-grade steel and advanced alloys ensure durability and performance but come at a higher price.
- Labor: Skilled labor is essential in the assembly and quality control of shredders. Labor costs can vary widely by region, influencing total expenses, particularly in countries with higher wage standards.
- Manufacturing Overhead: This includes costs related to facility operations, utilities, and maintenance of manufacturing equipment. Efficient production processes can help mitigate these overhead costs.
- Tooling: Initial tooling costs for creating custom or specialized shredders can be substantial. Buyers should inquire about tooling expenses when considering customized options.
- Quality Control (QC): Ensuring the shredders meet specific industry standards requires rigorous QC processes, which can add to the overall cost.
- Logistics: Transportation costs, including shipping and customs duties, can significantly affect the final price, especially for international buyers. Factors such as distance and mode of transport play a crucial role here.
- Margin: Suppliers typically add a margin to cover their operational costs and profit. Understanding the typical margins in the market can help buyers negotiate better deals.
How Do Price Influencers Affect Metal Shredder Costs?
Several factors influence the pricing of metal shredders, which B2B buyers should consider:
- Volume and Minimum Order Quantity (MOQ): Higher purchase volumes often lead to discounts, making it crucial for buyers to negotiate favorable terms based on their anticipated needs.
- Specifications and Customization: Custom features or specifications can raise costs. Buyers should clearly define their requirements to avoid unexpected expenses.
- Material Quality and Certifications: Shredders that meet specific industry certifications (e.g., ISO) may cost more but can ensure reliability and compliance with local regulations.
- Supplier Factors: The reputation and reliability of the supplier can affect pricing. Established suppliers may charge a premium for their products due to brand trust and proven performance.
- Incoterms: The agreed shipping terms (Incoterms) can influence the total cost. Buyers should be aware of who bears the cost and risk at various points in the shipping process.
What Are the Best Buyer Tips for Negotiating Metal Shredder Prices?
When sourcing metal shredders, particularly in markets like Africa, South America, the Middle East, and Europe, buyers can leverage several strategies:
- Negotiate: Engage in discussions to negotiate prices, especially if committing to larger orders. Suppliers may offer volume discounts or favorable payment terms.
- Focus on Cost-Efficiency: Evaluate the total cost of ownership (TCO), which includes initial purchase price, maintenance, operational efficiency, and potential resale value. A lower initial price may not always equate to better value if the machine is prone to breakdowns.
- Understand Pricing Nuances: Familiarize yourself with the local market conditions and common pricing practices in the supplier’s country. This knowledge can empower you during negotiations.
- Conduct Supplier Research: Investigate multiple suppliers and their offerings. Comparing specifications, warranties, and after-sales support can reveal better options that may not be the cheapest upfront.
- Consider Long-Term Partnerships: Building a relationship with a reliable supplier can lead to better terms and pricing over time, as trust and mutual understanding grow.
Final Thoughts on Pricing for Metal Shredder Sourcing
While the costs associated with sourcing metal shredders can vary widely based on multiple factors, understanding these dynamics will empower B2B buyers to make informed purchasing decisions. It is essential to approach negotiations with a comprehensive understanding of the cost structure, price influencers, and effective negotiation strategies to optimize investments in metal shredding equipment.
Disclaimer: The prices and cost structures mentioned are indicative and may vary based on specific circumstances and market conditions. Always consult with suppliers for the most accurate and current pricing information.
Alternatives Analysis: Comparing metal shredder With Other Solutions
When considering the best solution for metal recycling and waste management, international B2B buyers must evaluate various technologies and methods available in the market. Metal shredders are a common choice, but alternative solutions can offer different advantages depending on specific operational needs. This section compares metal shredders with two viable alternatives: hydraulic compactors and granulators.
Comparison Table of Metal Shredder and Alternatives
Comparison Aspect | Metal Shredder | Hydraulic Compactor | Granulator |
---|---|---|---|
Performance | High throughput, can process various metals efficiently | Moderate performance, suited for dense materials | High precision in size reduction, best for smaller pieces |
Cost | Moderate to high initial investment; lower operating costs | Lower initial investment; moderate operating costs | Moderate initial investment; higher maintenance costs |
Ease of Implementation | Requires specialized installation and training | Easier to install and operate | Requires training for optimal operation |
Maintenance | Regular maintenance needed; parts can be expensive | Low maintenance, occasional hydraulic checks | Higher maintenance due to wear on blades |
Best Use Case | Ideal for large-scale metal recycling operations | Best for waste management in construction or industrial settings | Suitable for producing consistent granule sizes for recycling |
What Are the Advantages and Disadvantages of Hydraulic Compactors?
Hydraulic compactors offer a cost-effective alternative for B2B buyers looking to manage dense materials efficiently. Their ability to compress waste into manageable sizes makes them particularly useful in construction and industrial settings where space is limited. However, while they excel in compacting, their performance in shredding metal is limited, which may not meet the needs of businesses focused on metal recycling. Additionally, while initial costs are lower, ongoing operational costs can increase based on hydraulic fluid maintenance.
How Do Granulators Differ from Metal Shredders?
Granulators are designed for high-precision size reduction, making them ideal for applications requiring uniform granule sizes, such as in plastic and metal recycling. They are particularly effective for smaller pieces of material, thus enabling better downstream processing. However, granulators generally have higher maintenance costs due to blade wear and require more frequent replacements. While the initial investment is moderate, the ongoing costs can add up, making this option less appealing for large-scale operations focusing solely on metal recycling.
How to Choose the Right Solution for Your Business Needs?
Selecting the right solution for metal processing depends on several factors, including the scale of operations, the type of materials being processed, and budget constraints. For businesses primarily focused on metal recycling, metal shredders provide unmatched performance and efficiency. However, if the goal is to manage waste in a more compact form, hydraulic compactors may serve better. On the other hand, for applications requiring precise granule sizes, granulators could be the optimal choice. B2B buyers should carefully analyze their specific requirements, weigh the pros and cons of each alternative, and choose the solution that aligns with their operational goals and financial considerations.
Essential Technical Properties and Trade Terminology for metal shredder
What Are the Key Technical Properties of Metal Shredders?
When considering a metal shredder for your business, understanding its technical specifications is crucial for making an informed purchasing decision. Here are some essential properties to evaluate:
1. Material Grade
Material grade refers to the quality and type of materials used in the construction of the shredder. High-grade steel and durable alloys are preferred as they enhance the shredder’s longevity and operational efficiency. For B2B buyers, investing in a shredder with superior material grade can lead to reduced maintenance costs and increased uptime, maximizing productivity.
2. Throughput Capacity
Throughput capacity indicates the volume of material a shredder can process within a specific timeframe, often measured in tons per hour. Knowing the throughput capacity is vital for buyers to match their operational needs. A shredder with a higher throughput can significantly improve efficiency in metal recycling operations, allowing businesses to handle larger volumes of scrap metal and thus increase profitability.
3. Cutting Chamber Size
The cutting chamber size impacts the shredder’s ability to handle various material sizes. A larger cutting chamber can accommodate bulkier loads and a wider range of materials, from steel drums to aluminum sheets. For international buyers, especially in regions with diverse waste types, selecting a shredder with an appropriately sized cutting chamber ensures versatility and efficiency in processing.
4. Knife Configuration
Knife configuration refers to the design and arrangement of the cutting blades within the shredder. Different configurations can optimize shredding for various materials, affecting the final shred size. Understanding knife options is critical for B2B buyers to ensure that the shredder meets their specific recycling requirements, as the right configuration can enhance both efficiency and output quality.
5. Drive System Power
The power of the drive system, often measured in horsepower (HP), determines how effectively the shredder can operate under heavy loads. A more powerful drive system allows the shredder to tackle tougher materials without bogging down, which is essential for high-volume recycling operations. Buyers should consider their material types and expected processing volumes when evaluating drive system power.
What Common Trade Terms Should B2B Buyers Know?
Navigating the world of metal shredders involves understanding various industry-specific terms. Here are some critical trade terms that every buyer should be familiar with:
1. OEM (Original Equipment Manufacturer)
An OEM is a company that produces parts or equipment that may be marketed by another manufacturer. In the context of metal shredders, buyers should consider purchasing from reputable OEMs to ensure quality and reliability in their machinery.
2. MOQ (Minimum Order Quantity)
MOQ refers to the smallest quantity of a product that a supplier is willing to sell. This is important for B2B buyers who may need to plan their budgets and inventory levels accordingly. Understanding MOQ can help businesses negotiate better terms and manage their supply chain effectively.
3. RFQ (Request for Quotation)
An RFQ is a document that a buyer sends to suppliers to request price quotes for specific products or services. For buyers in the metal shredding industry, issuing an RFQ can help compare costs and features among different manufacturers, ensuring they receive the best value for their investment.
4. Incoterms (International Commercial Terms)
Incoterms are a set of predefined commercial terms published by the International Chamber of Commerce (ICC) that clarify the responsibilities of buyers and sellers in international transactions. Familiarity with Incoterms can help B2B buyers from Africa, South America, the Middle East, and Europe navigate shipping costs, risks, and logistics more effectively.
5. Service Level Agreement (SLA)
An SLA is a contract that outlines the expected level of service between a service provider and a client. In the context of metal shredders, SLAs can define maintenance schedules, response times for repairs, and performance benchmarks, providing peace of mind for buyers concerned about operational continuity.
By grasping these technical properties and trade terms, international B2B buyers can make informed decisions that enhance their metal recycling operations, optimize investments, and improve overall business efficiency.
Navigating Market Dynamics and Sourcing Trends in the metal shredder Sector
What Are the Key Market Dynamics and Trends in the Metal Shredder Sector?
The global metal shredder market is currently driven by the increasing demand for metal recycling and waste management solutions. As urbanization and industrial activities grow in Africa, South America, the Middle East, and Europe, the amount of scrap metal generated is rising. This surge in scrap metal is a result of various factors, including the expansion of manufacturing sectors and infrastructure projects. Additionally, the push for sustainability and circular economy principles is compelling businesses to adopt metal shredding as a means to recycle valuable materials efficiently.
Emerging technologies such as IoT-enabled shredders and automation are revolutionizing the industry. These advancements allow for real-time monitoring of shredder performance, predictive maintenance, and enhanced operational efficiencies. For international B2B buyers, particularly from regions like Argentina and Turkey, investing in technologically advanced shredders can lead to significant cost reductions and increased throughput. Furthermore, partnerships with local suppliers and manufacturers can enhance sourcing strategies by providing tailored solutions that meet specific regional needs.
How Can Sustainability and Ethical Sourcing Impact the Metal Shredder Market?
The environmental impact of metal shredders cannot be overstated, as they play a crucial role in reducing landfill waste and conserving natural resources. For B2B buyers, understanding the sustainability credentials of their suppliers is essential. Ethical sourcing is becoming increasingly important, with businesses prioritizing suppliers that adhere to environmentally friendly practices and use sustainable materials. Certifications such as ISO 14001 for environmental management systems can serve as valuable indicators of a supplier’s commitment to sustainability.
Moreover, as regulations around waste disposal tighten globally, companies that invest in sustainable shredding solutions will not only comply with legal requirements but also enhance their brand reputation. Buyers should look for shredders that offer energy-efficient operation and low emissions, contributing to a reduced carbon footprint. The use of recycled materials in manufacturing shredders is another trend gaining traction, as it aligns with the principles of the circular economy and appeals to environmentally conscious consumers.
What Is the Brief History and Evolution of Metal Shredders in the B2B Context?
The evolution of metal shredders dates back to the late 19th century when the industrial revolution necessitated efficient waste disposal methods. Early shredders were manually operated and limited in capacity, primarily designed for small-scale operations. As industries grew, so did the need for more robust shredding solutions. The introduction of electric-powered shredders in the mid-20th century marked a significant turning point, enhancing shredding speed and efficiency.
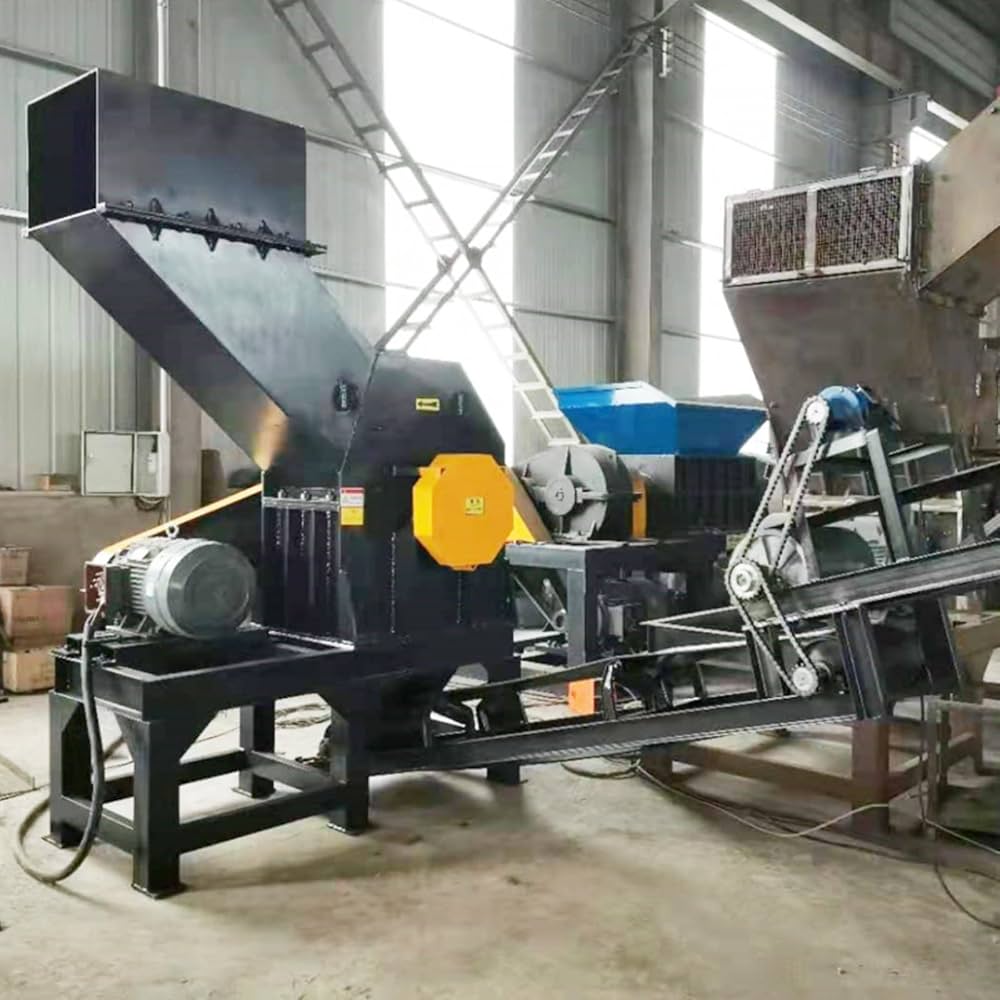
A stock image related to metal shredder.
In recent decades, the focus has shifted towards automation and advanced engineering, leading to the development of high-capacity, high-efficiency shredders capable of handling diverse materials. Today’s shredders are designed not only for efficiency but also for sustainability, reflecting a broader industry trend towards responsible waste management. For B2B buyers, understanding this historical context can aid in making informed decisions about purchasing advanced shredding technologies that align with contemporary market demands.
Frequently Asked Questions (FAQs) for B2B Buyers of metal shredder
-
How do I choose the right metal shredder for my business needs?
Selecting the appropriate metal shredder involves assessing your specific requirements, such as the type of metals you will be shredding (steel, aluminum, etc.), the volume of material, and desired shred size. Evaluate the shredder’s throughput capacity, as machines can vary from light-duty (up to 1 ton/hour) to heavy-duty (over 3 tons/hour). Additionally, consider maintenance needs and operational costs. Consulting with manufacturers for expert recommendations based on your operational goals can also provide valuable insights. -
What is the best type of metal shredder for recycling operations?
The best type of metal shredder for recycling operations depends on the types of materials you handle. Heavy-duty twin-shaft shredders are often preferred for their efficiency in processing a wide range of metals, including steel drums and electronic waste. Look for shredders with customizable knife configurations and robust construction to withstand continuous operation. Additionally, consider features like low noise and heat generation, which can enhance workplace safety and comfort. -
How can I verify the credibility of metal shredder suppliers?
To verify the credibility of suppliers, conduct thorough research on their company history, customer reviews, and industry certifications. Request references from previous clients and check their track record in delivering quality equipment. Engage in direct communication to assess their customer service responsiveness and expertise. Additionally, visiting their manufacturing facility or trade shows can provide firsthand insight into their operations and product quality. -
What customization options are available for metal shredders?
Many manufacturers offer customization options for metal shredders, allowing you to tailor the machine to your specific needs. Customizations may include modifications to shred size, knife configurations, and additional features such as conveyors or hoppers. It’s essential to discuss your requirements with the supplier to understand the extent of customization they offer and any associated costs. This ensures that the shredder fits seamlessly into your operational workflow. -
What are the typical minimum order quantities (MOQs) for metal shredders?
Minimum order quantities for metal shredders can vary significantly by manufacturer and the complexity of the machine. Some suppliers may have MOQs as low as one unit for standard models, while custom or specialized machines may require higher MOQs. It’s advisable to clarify MOQs during initial discussions with potential suppliers and explore options for bulk purchasing or financing if needed. -
What payment terms should I expect when purchasing a metal shredder?
Payment terms for metal shredders typically include a deposit upon order confirmation, with the balance due upon delivery or installation. Some suppliers may offer financing options or installment plans, especially for larger orders. It’s crucial to negotiate terms that align with your cash flow and budget constraints. Additionally, ensure that any payment agreements are documented in the purchase contract to avoid misunderstandings. -
How is quality assurance handled for metal shredders?
Quality assurance for metal shredders is usually managed through rigorous testing and inspection processes during manufacturing. Reputable suppliers will provide documentation, including performance reports and certifications that verify the machine’s compliance with industry standards. It’s beneficial to inquire about the specific QA procedures a supplier follows and request information on warranties and after-sales support, which can further assure the reliability of the equipment. -
What logistics considerations should I keep in mind for importing a metal shredder?
When importing a metal shredder, consider logistics factors such as shipping methods, customs regulations, and potential tariffs. Work with freight forwarders experienced in heavy machinery to ensure safe transport. Additionally, confirm that the supplier provides adequate packaging and handling instructions to prevent damage during transit. Understanding local regulations regarding equipment imports in your region can also streamline the process and avoid delays.
Important Disclaimer & Terms of Use
⚠️ Important Disclaimer
The information provided in this guide, including content regarding manufacturers, technical specifications, and market analysis, is for informational and educational purposes only. It does not constitute professional procurement advice, financial advice, or legal advice.
While we have made every effort to ensure the accuracy and timeliness of the information, we are not responsible for any errors, omissions, or outdated information. Market conditions, company details, and technical standards are subject to change.
B2B buyers must conduct their own independent and thorough due diligence before making any purchasing decisions. This includes contacting suppliers directly, verifying certifications, requesting samples, and seeking professional consultation. The risk of relying on any information in this guide is borne solely by the reader.
Strategic Sourcing Conclusion and Outlook for metal shredder
As the global market for metal shredders continues to evolve, international B2B buyers must recognize the importance of strategic sourcing to optimize their recycling operations. Key takeaways include understanding the diverse applications of shredders, from processing various metals to handling industrial waste, which can significantly enhance operational efficiency and profitability. By investing in high-quality machinery tailored to specific needs, businesses can minimize downtime and maximize throughput.
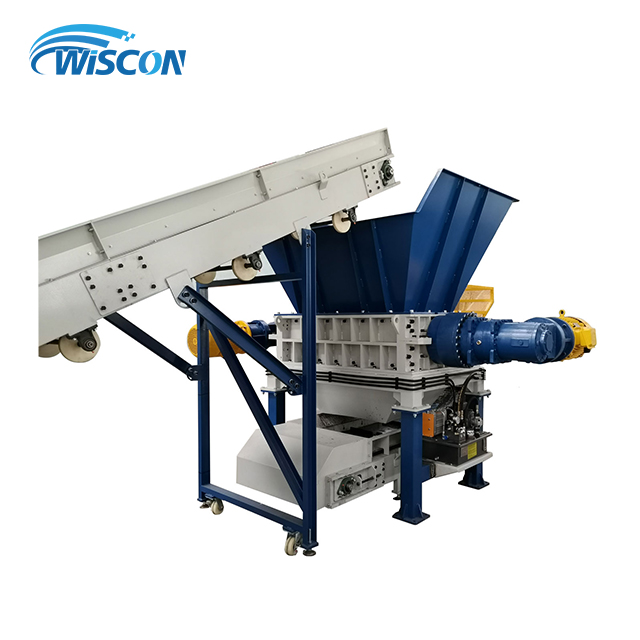
A stock image related to metal shredder.
What are the future trends in the metal shredding industry for B2B buyers? As sustainability becomes increasingly prioritized across regions—especially in Africa, South America, the Middle East, and Europe—companies must adapt to regulatory changes and consumer demands for eco-friendly practices. This not only involves sourcing advanced shredding technology but also considering the lifecycle impacts of equipment.
In conclusion, international B2B buyers are encouraged to evaluate their metal shredding needs and explore innovative solutions that align with their operational goals. By leveraging strategic sourcing, businesses can position themselves as leaders in the recycling sector, paving the way for sustainable growth and profitability in the coming years. Engage with trusted suppliers today to ensure your operations are equipped for the future.