Unlock Cost Savings: The Ultimate Blow Molding Guide (2025)
Introduction: Navigating the Global Market for blow molding
Navigating the complexities of sourcing blow molding solutions can be a daunting task for international B2B buyers, especially in regions like Africa, South America, the Middle East, and Europe. As businesses strive to meet increasing demand for efficient and cost-effective manufacturing processes, understanding the nuances of blow molding becomes crucial. This guide delves into the various types of blow molding—extrusion blow molding, injection blow molding, and injection stretch blow molding—highlighting their applications across industries such as automotive, packaging, and agriculture.
Moreover, it provides an in-depth analysis of the materials commonly used in blow molding, offering insights into their suitability for different applications. This guide also emphasizes the importance of supplier vetting, helping buyers identify reliable manufacturers who can meet their specific needs while ensuring quality and compliance with international standards.
By equipping buyers with actionable insights into cost structures, production capabilities, and the latest advancements in blow molding technology, this resource empowers informed purchasing decisions. Whether you are based in France looking to enhance your product line or in South Africa seeking innovative packaging solutions, this comprehensive guide serves as your essential roadmap in the global market for blow molding, helping you navigate challenges and seize opportunities effectively.
Understanding blow molding Types and Variations
Type Name | Key Distinguishing Features | Primary B2B Applications | Brief Pros & Cons for Buyers |
---|---|---|---|
Extrusion Blow Molding (EBM) | Uses a continuous tube of plastic; lower cost per part | Packaging, automotive parts, containers | Pros: Cost-effective for high volumes; versatile. Cons: Limited complexity in shapes. |
Injection Blow Molding (IBM) | Combines injection molding with blow molding; high precision | Bottles, jars, and specialized containers | Pros: High precision; excellent for complex designs. Cons: Higher tooling costs. |
Injection Stretch Blow Molding (ISBM) | Involves stretching the preform; creates strong, clear parts | Beverage bottles, high-end packaging | Pros: Superior strength and clarity; ideal for high-performance applications. Cons: More complex process. |
Reheat Blow Molding | Involves reheating preforms; allows for complex shapes | Specialty containers, custom designs | Pros: Design flexibility; can use recycled materials. Cons: Slower production speed. |
Multi-layer Blow Molding | Uses multiple materials for enhanced properties | Food and pharmaceutical packaging | Pros: Barrier properties; tailored material combinations. Cons: More complex and costly setup. |
What Are the Key Characteristics of Extrusion Blow Molding (EBM)?
Extrusion Blow Molding (EBM) is characterized by its ability to produce hollow plastic parts from a continuous tube of melted plastic, which is then inflated into a mold. This method is particularly suitable for high-volume production runs, making it ideal for applications such as packaging and automotive components. B2B buyers should consider EBM for its cost-effectiveness at scale, although they should be aware of its limitations in producing highly intricate shapes compared to other methods.
How Does Injection Blow Molding (IBM) Stand Out?
Injection Blow Molding (IBM) integrates the precision of injection molding with the inflation aspect of blow molding. This process is best for producing bottles and containers that require intricate designs and high dimensional accuracy. B2B purchasers looking for high-quality products with complex geometries may find IBM advantageous, despite the higher tooling costs. The precision achieved through IBM can significantly enhance product performance, making it a preferred choice for specialized applications.
What Advantages Does Injection Stretch Blow Molding (ISBM) Offer?
Injection Stretch Blow Molding (ISBM) stands out for its ability to produce strong, clear products, particularly for beverage containers. This process stretches the preform during inflation, resulting in enhanced strength and clarity. B2B buyers in industries requiring high-performance packaging, such as beverages and cosmetics, will appreciate ISBM for its ability to meet rigorous standards. However, the complexity of the ISBM process can lead to higher production costs, making it essential for buyers to evaluate their specific needs before choosing this method.
Why Choose Reheat Blow Molding for Custom Designs?
Reheat Blow Molding is notable for its flexibility in creating complex shapes by reheating preforms before they are blown into molds. This method is particularly suited for specialty containers and custom designs, allowing for innovative product development. B2B buyers should consider this option when they require unique shapes or wish to utilize recycled materials. However, the slower production speed might not be ideal for large-scale manufacturing needs.
What Is the Benefit of Multi-layer Blow Molding?
Multi-layer Blow Molding employs multiple materials to enhance product properties, such as barrier functions, which are crucial in food and pharmaceutical packaging. This method allows manufacturers to tailor material combinations to meet specific requirements, making it a valuable option for B2B buyers focused on quality and performance. However, the setup for multi-layer processes can be more complex and costly, necessitating careful consideration of budget and production capabilities.
Key Industrial Applications of blow molding
Industry/Sector | Specific Application of Blow Molding | Value/Benefit for the Business | Key Sourcing Considerations for this Application |
---|---|---|---|
Packaging | Production of plastic bottles | Cost-effective mass production of containers | Material compatibility, sustainability certifications |
Automotive | Manufacturing fuel tanks and ducts | Lightweight components that enhance fuel efficiency | Compliance with safety standards, durability under stress |
Agriculture | Creation of irrigation systems and tanks | Improved water management and resource efficiency | Resistance to UV and chemicals, availability of sizes |
Consumer Goods | Development of cosmetic and household product containers | Attractive designs that enhance market appeal | Customization options, rapid prototyping capabilities |
Medical Devices | Production of IV bags and pharmaceutical containers | High standards of hygiene and safety | Certification requirements, material biocompatibility |
How is Blow Molding Used in the Packaging Industry?
In the packaging sector, blow molding is predominantly used for producing plastic bottles and containers for beverages, cleaning products, and personal care items. This method offers an efficient means of creating lightweight, durable, and recyclable packaging solutions. For international buyers, particularly in regions like Africa and South America, sourcing blow-molded packaging requires careful consideration of material compatibility, ensuring that the chosen plastics meet regulatory standards for food safety and sustainability.
What Role Does Blow Molding Play in the Automotive Industry?
The automotive industry utilizes blow molding to manufacture various components such as fuel tanks, air ducts, and other lightweight parts. This process helps reduce vehicle weight, thereby improving fuel efficiency and overall performance. Buyers must consider compliance with strict safety standards and the durability of materials under extreme conditions. Sourcing from manufacturers with a proven track record in automotive applications is essential for ensuring product reliability.
How Does Blow Molding Benefit the Agriculture Sector?
In agriculture, blow molding is employed to create essential components like irrigation tanks, fluid reservoirs, and other bulk containers. These products help in efficient water management, crucial for sustainable farming practices. When sourcing blow-molded agricultural products, buyers should prioritize materials resistant to UV rays and chemicals, as these factors significantly impact the longevity and performance of irrigation systems.
Why is Blow Molding Important for Consumer Goods?
The consumer goods sector benefits from blow molding through the production of aesthetically pleasing and functional containers for cosmetics, detergents, and other household products. This process allows for intricate designs that enhance product appeal and marketability. Buyers should look for suppliers that offer customization options and rapid prototyping capabilities to meet specific branding needs and market trends.
How is Blow Molding Applied in the Medical Device Industry?
In the medical device sector, blow molding is crucial for manufacturing items like IV bags and pharmaceutical containers, where hygiene and safety are paramount. The materials used must comply with stringent health regulations and be biocompatible. International buyers in the medical field must ensure that their suppliers meet certification requirements and can provide materials that guarantee patient safety and product integrity.
3 Common User Pain Points for ‘blow molding’ & Their Solutions
Scenario 1: Difficulty in Achieving Consistent Wall Thickness in Blow Molding
The Problem:
B2B buyers often face challenges with achieving consistent wall thickness in blow-molded products. This inconsistency can lead to structural weaknesses, increased material waste, and ultimately, product failures. For manufacturers producing items like bottles or containers, uneven walls can compromise product integrity, resulting in costly recalls and damage to brand reputation. Buyers may feel frustrated, especially when they need to meet stringent industry standards or customer expectations for quality.
The Solution:
To mitigate wall thickness variability, it’s essential to invest in high-quality molds and precise manufacturing processes. One effective approach is to collaborate with suppliers who utilize advanced simulation software during the mold design phase. This software can predict how the material will behave under different conditions, allowing for adjustments before production begins. Additionally, implementing real-time monitoring systems during the blow molding process can help detect inconsistencies immediately, enabling corrective actions to be taken before large batches are produced. Buyers should also consider discussing specific material properties with their suppliers, as selecting the right polymer can significantly influence wall thickness control.
Scenario 2: Limited Design Flexibility in Blow Molded Products
The Problem:
Buyers often encounter limitations with design flexibility when using blow molding for complex parts. The inability to create intricate features or unique shapes can restrict innovation and product differentiation. This challenge is particularly evident in industries such as consumer goods, where packaging aesthetics and functionality are critical. When a design requires features like handles or custom textures, buyers may feel boxed in by the constraints of traditional blow molding processes.
The Solution:
To enhance design flexibility, buyers should explore the use of advanced blow molding techniques such as injection stretch blow molding (ISBM). This method not only allows for more complex shapes but also provides improved material strength and clarity. Additionally, collaborating with mold designers who have experience in creating custom molds can lead to innovative solutions tailored to specific needs. Utilizing rapid prototyping technologies, such as 3D printing for mold production, can also expedite the design process, allowing for quick iterations and adjustments. This approach enables buyers to test designs more effectively before committing to full-scale production.
Scenario 3: High Initial Costs of Blow Molding Setup
The Problem:
One of the most significant barriers for B2B buyers considering blow molding is the high initial setup costs associated with machinery and tooling. This can be a particular pain point for small to medium-sized enterprises (SMEs) looking to scale production but facing budget constraints. The financial burden of acquiring specialized equipment and molds can lead to hesitation in adopting blow molding as a manufacturing solution, limiting growth opportunities.
The Solution:
To address high initial costs, buyers should consider partnering with suppliers who offer low-volume production runs or contract manufacturing services. This allows companies to leverage blow molding capabilities without the need for significant upfront investments. Additionally, exploring options for shared tooling or co-investment in mold development can help distribute costs among multiple buyers. Another viable strategy is to utilize 3D printed molds for initial prototypes or small batches, which significantly reduces tooling costs and lead times. As production volumes increase, transitioning to traditional molds becomes a more economically viable option. Buyers should also conduct a thorough cost-benefit analysis to understand the long-term savings associated with blow molding compared to other manufacturing processes.
Strategic Material Selection Guide for blow molding
Which Materials are Commonly Used in Blow Molding?
Blow molding is a versatile manufacturing process that relies heavily on the selection of appropriate materials. Understanding the properties, advantages, disadvantages, and applications of these materials is crucial for international B2B buyers, particularly those from Africa, South America, the Middle East, and Europe. Here, we analyze four common materials used in blow molding: Polyethylene (PE), Polypropylene (PP), Polyethylene Terephthalate (PET), and Polyvinyl Chloride (PVC).
What are the Key Properties of Polyethylene (PE) for Blow Molding?
Polyethylene is one of the most widely used materials in blow molding, particularly in the production of bottles and containers. It exhibits excellent chemical resistance, low moisture absorption, and good impact strength. PE is available in various densities, including low-density polyethylene (LDPE) and high-density polyethylene (HDPE), which offer different properties.
Pros: PE is cost-effective, lightweight, and has a high resistance to impact and chemicals. Its flexibility allows for the production of a wide range of shapes and sizes.
Cons: However, PE has lower temperature resistance compared to other materials, which may limit its application in high-temperature environments. Additionally, it can be less suitable for products requiring high clarity or rigidity.
Impact on Application: PE is ideal for packaging applications, especially in food and beverage sectors, due to its safety and compliance with food-grade standards.
Considerations for International Buyers: Buyers should ensure compliance with local standards such as ASTM or DIN, especially in food-related applications. The availability of recycled PE is also a growing concern in many regions.
How Does Polypropylene (PP) Perform in Blow Molding Applications?
Polypropylene is another popular choice in blow molding, known for its versatility and strength. It has a higher melting point than PE, making it suitable for applications that require heat resistance.
Pros: PP offers excellent chemical resistance, low density, and good fatigue resistance. It is also more rigid than PE, which can be advantageous in certain applications.
Cons: The main limitation of PP is its susceptibility to UV degradation, which can affect outdoor applications unless treated with stabilizers. Additionally, it may have a higher cost compared to PE.
Impact on Application: PP is commonly used in automotive components, household goods, and packaging, particularly for products that require a balance of strength and flexibility.
Considerations for International Buyers: Buyers should be aware of the specific grades of PP available and their compliance with regional standards. The cost of UV stabilizers can also influence overall project budgets.
What Advantages Does Polyethylene Terephthalate (PET) Offer?
PET is renowned for its clarity, strength, and recyclability, making it a preferred material for beverage containers and packaging.
Pros: PET has excellent barrier properties against moisture and gases, which is crucial for food and beverage applications. Its high strength-to-weight ratio also enhances product durability.
Cons: The primary drawback of PET is its higher processing temperatures, which can complicate the manufacturing process and increase costs. Additionally, it may not be suitable for all chemical environments.
Impact on Application: PET is widely used in the beverage industry for bottles and jars due to its safety and recyclability.
Considerations for International Buyers: Compliance with food safety regulations is essential, particularly in Europe, where standards can be stringent. Buyers should also consider the availability of recycled PET in their sourcing decisions.
Why Choose Polyvinyl Chloride (PVC) for Blow Molding?
PVC is less common in blow molding but is used for specific applications, particularly in construction and plumbing.
Pros: PVC is highly durable, resistant to corrosion, and can be produced in various colors and finishes. Its rigidity makes it ideal for structural applications.
Cons: However, PVC has lower impact resistance compared to other materials and can be more challenging to recycle. Additionally, it may release harmful chemicals during processing.
Impact on Application: PVC is often used in pipes, fittings, and other construction-related products where durability is paramount.
Considerations for International Buyers: Buyers should be aware of the environmental regulations regarding PVC, particularly in Europe, where there is increasing pressure to reduce the use of harmful substances.
Summary Table of Material Selection for Blow Molding
Material | Typical Use Case for Blow Molding | Key Advantage | Key Disadvantage/Limitation | Relative Cost (Low/Med/High) |
---|---|---|---|---|
Polyethylene (PE) | Bottles, containers, packaging | Cost-effective and lightweight | Lower temperature resistance | Low |
Polypropylene (PP) | Automotive parts, household goods | Excellent chemical resistance | Susceptible to UV degradation | Medium |
Polyethylene Terephthalate (PET) | Beverage bottles, food containers | High clarity and recyclability | Higher processing temperatures | Medium |
Polyvinyl Chloride (PVC) | Pipes, fittings, construction | Highly durable and corrosion-resistant | Lower impact resistance | Medium |
Understanding these materials and their properties will assist B2B buyers in making informed decisions that align with their product requirements and regional compliance standards.
In-depth Look: Manufacturing Processes and Quality Assurance for blow molding
What Are the Key Stages in the Blow Molding Manufacturing Process?
Blow molding is an intricate manufacturing process that involves several distinct stages to produce high-quality hollow plastic parts. Understanding these stages is crucial for B2B buyers, especially those sourcing from or within regions like Africa, South America, the Middle East, and Europe.
1. Material Preparation
The blow molding process starts with material selection and preparation. Common materials include high-density polyethylene (HDPE), polypropylene (PP), and polyethylene terephthalate (PET). The chosen polymer is typically delivered in pellet form and must be dried to remove any moisture, which can adversely affect the molding process.
Once dried, the pellets are fed into a hopper and heated until they reach a molten state. This heating process is critical, as the temperature must be accurately controlled to ensure the material becomes pliable enough for the subsequent stages. Mismanagement during this phase can lead to defects in the final product.
2. Forming: How Is the Blow Molding Process Executed?
The forming stage is where the actual shaping of the hollow parts occurs. Depending on the type of blow molding being used—extrusion blow molding (EBM), injection blow molding (IBM), or injection stretch blow molding (ISBM)—the process will vary slightly:
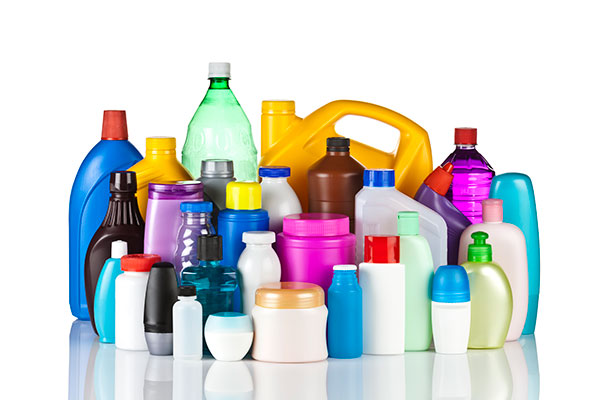
A stock image related to blow molding.
-
Extrusion Blow Molding (EBM): A continuous tube of plastic, known as a parison, is extruded and then inflated within a mold to form the desired shape. EBM is often chosen for simpler designs due to its lower production costs.
-
Injection Blow Molding (IBM): This method involves injecting molten plastic into a mold to form a preform, which is then inflated in a second mold. IBM is ideal for producing complex shapes with higher precision.
-
Injection Stretch Blow Molding (ISBM): Similar to IBM, ISBM stretches the preform before inflation, resulting in improved clarity and strength, making it suitable for high-performance applications like beverage containers.
Regardless of the method, maintaining consistent pressure and temperature during the inflation process is critical for achieving uniform wall thickness and preventing defects.
3. Assembly: What Happens After Molding?
After the blow molding process, the newly formed parts typically undergo a trimming process to remove any excess material. This stage may also include additional assembly processes if the final product requires joining multiple components or adding features such as handles or closures.
In some cases, secondary operations such as printing, labeling, or surface treatments may be performed to enhance the product’s functionality or aesthetics. It’s essential for B2B buyers to confirm that suppliers can accommodate these additional requirements.
4. Finishing: How Is Quality Enhanced Post-Manufacturing?
The finishing stage focuses on ensuring that the blow-molded parts meet the required specifications and quality standards. This may involve further quality control checks, surface polishing, or application of protective coatings.
What Quality Assurance Practices Should B2B Buyers Expect in Blow Molding?
Quality assurance (QA) is a vital component of the blow molding process, ensuring that the final products are reliable and meet international and industry-specific standards.
Relevant International Standards: What Should Buyers Know?
For B2B buyers, particularly those from diverse regions, understanding relevant quality standards is crucial. Key international standards include:
-
ISO 9001: This standard outlines the criteria for a quality management system and is applicable to any organization, regardless of size or industry. It emphasizes a process approach and the importance of continuous improvement.
-
CE Marking: For products sold in the European Economic Area, CE marking indicates conformity with health, safety, and environmental protection standards.
-
API Standards: Particularly for buyers in the oil and gas industry, API (American Petroleum Institute) standards ensure that products meet specific performance and safety criteria.
Quality Control Checkpoints: Where Are the Key Areas of Focus?
Quality control in blow molding typically involves multiple checkpoints throughout the manufacturing process:
-
Incoming Quality Control (IQC): This initial stage involves inspecting raw materials to ensure they meet the specified standards before production begins.
-
In-Process Quality Control (IPQC): During the forming stage, real-time monitoring of temperature, pressure, and material flow is essential to prevent defects from occurring.
-
Final Quality Control (FQC): After production, a thorough inspection of the finished products is conducted. This includes dimensional checks, visual inspections, and functional tests to ensure compliance with specifications.
What Testing Methods Are Commonly Used in Blow Molding Quality Assurance?
To ensure that blow-molded products meet the required quality standards, various testing methods are employed:
-
Dimensional Inspection: This involves measuring the physical dimensions of the finished parts to ensure they match the specifications.
-
Mechanical Testing: Tests such as tensile strength, impact resistance, and burst pressure are conducted to evaluate the material’s performance under stress.
-
Visual Inspection: A thorough visual examination is performed to detect surface defects, color inconsistencies, or other visual flaws.
How Can B2B Buyers Verify Supplier Quality Control?
To ensure that their suppliers maintain high standards of quality, B2B buyers should consider the following verification methods:
-
Supplier Audits: Conducting regular audits allows buyers to assess the supplier’s adherence to quality standards, production processes, and compliance with relevant certifications.
-
Quality Reports: Requesting detailed quality reports that outline inspection results, testing outcomes, and any corrective actions taken can provide valuable insights into the supplier’s quality control practices.
-
Third-party Inspections: Engaging third-party inspection services can provide an unbiased assessment of the supplier’s processes and product quality. This is especially critical for international buyers who may face language barriers or cultural differences.
What Are the Quality Control Nuances for International B2B Buyers?
For international B2B buyers, especially those in Africa, South America, the Middle East, and Europe, understanding local regulations and cultural nuances is vital for ensuring effective quality control. Buyers should be aware of:
-
Regional Standards: Different regions may have specific standards and regulations that must be adhered to. Understanding these can help avoid compliance issues.
-
Cultural Considerations: Building strong relationships with suppliers can facilitate better communication regarding quality expectations and processes.
By comprehensively understanding the manufacturing processes and quality assurance practices associated with blow molding, B2B buyers can make informed decisions, ensuring they procure high-quality products that meet their specific needs.
Practical Sourcing Guide: A Step-by-Step Checklist for ‘blow molding’
To effectively procure blow molding services and products, international B2B buyers must navigate a structured approach. This step-by-step checklist is designed to ensure that you make informed decisions while sourcing blow molding solutions, particularly for industries across Africa, South America, the Middle East, and Europe.
Step 1: Define Your Technical Specifications
Clearly outline the technical specifications of the blow-molded products you require. This includes dimensions, material types, and design intricacies. By having a precise set of requirements, you can communicate effectively with potential suppliers and ensure they can meet your needs.
- Materials: Specify if you need high-density polyethylene (HDPE), polypropylene (PP), or polyethylene terephthalate (PET).
- Design Complexity: Consider whether your product demands intricate designs or if simpler forms will suffice.
Step 2: Research and Identify Potential Suppliers
Conduct thorough research to identify suppliers specializing in blow molding. Look for companies with a proven track record in your specific industry. This will help you shortlist suppliers who can fulfill your requirements effectively.
- Industry Experience: Check how long suppliers have been in business and their experience with similar products.
- Geographic Considerations: Consider suppliers located close to your operations to reduce shipping costs and lead times.
Step 3: Evaluate Supplier Capabilities
Assess the capabilities of potential suppliers to ensure they have the right technology and processes in place for your project. This includes examining their blow molding techniques, production capacity, and quality control measures.
- Technology: Inquire about the types of blow molding they employ (EBM, IBM, ISBM) and their suitability for your needs.
- Production Capacity: Ensure the supplier can handle your required production volume without compromising quality.
Step 4: Request Samples and Prototypes
Before finalizing your decision, request samples or prototypes of the products you intend to order. This step is crucial for evaluating the supplier’s quality and how well their capabilities align with your specifications.
- Quality Assessment: Inspect the samples for consistency in wall thickness and overall finish.
- Functionality Testing: Ensure that the prototypes meet the functional requirements of your intended application.
Step 5: Verify Certifications and Compliance
It’s essential to verify that your chosen supplier holds the necessary certifications and complies with industry standards. This ensures that the products are safe, reliable, and meet regulatory requirements.
- ISO Certifications: Look for ISO 9001 or other relevant certifications that indicate a commitment to quality management.
- Material Compliance: Confirm that the materials used are compliant with local regulations, especially if you are in regulated industries like food and beverage.
Step 6: Negotiate Terms and Conditions
Once you have selected a supplier, negotiate terms and conditions that protect your interests. This includes pricing, payment terms, delivery schedules, and warranties.
- Pricing Transparency: Ensure that the pricing structure is clear and includes all associated costs.
- Delivery Commitments: Agree on realistic delivery timelines to avoid disruptions in your supply chain.
Step 7: Establish a Clear Communication Plan
Finally, establish a communication plan with your supplier to ensure ongoing collaboration. Regular updates and open lines of communication can help address any issues that arise during production.
- Point of Contact: Designate a point of contact for both parties to streamline communication.
- Feedback Loop: Set up regular meetings or reports to discuss progress and any potential challenges.
By following this structured checklist, international B2B buyers can effectively navigate the complexities of sourcing blow molding solutions, ensuring they secure high-quality products that meet their specific needs.
Comprehensive Cost and Pricing Analysis for blow molding Sourcing
What Are the Key Cost Components in Blow Molding?
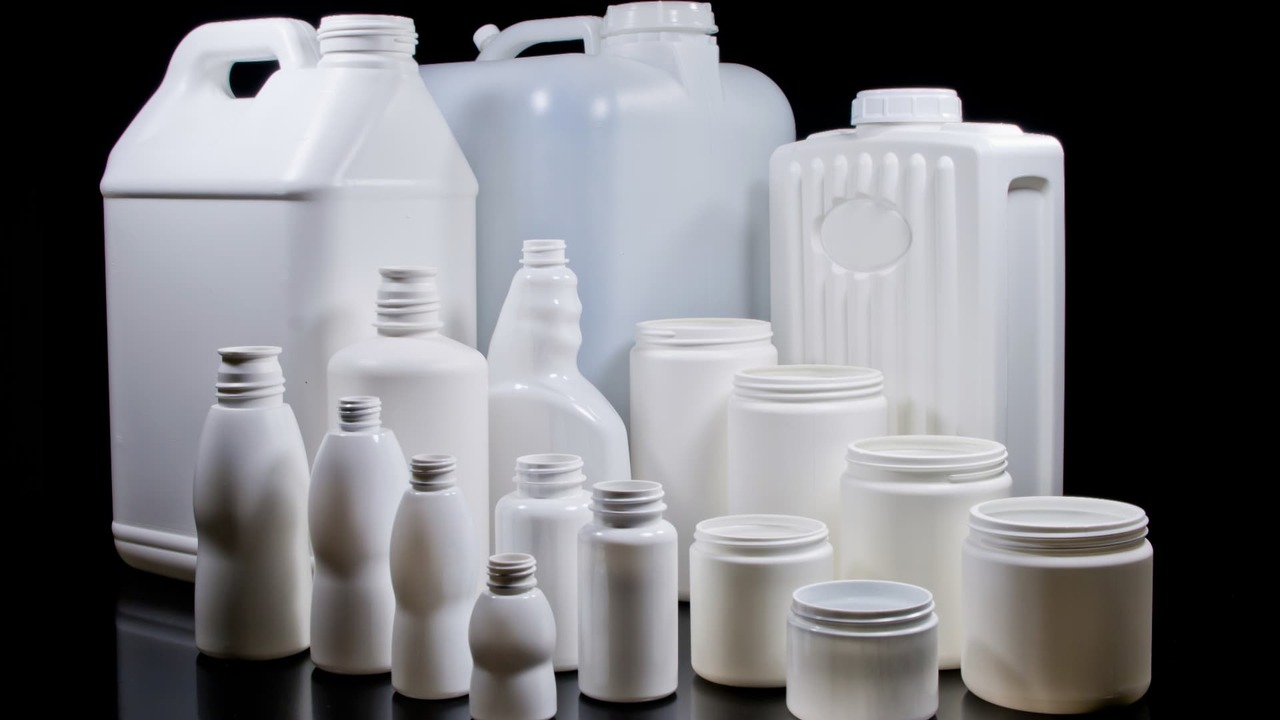
A stock image related to blow molding.
When considering blow molding for manufacturing hollow plastic parts, it is essential to understand the various cost components involved. This analysis includes materials, labor, manufacturing overhead, tooling, quality control (QC), logistics, and the supplier’s margin.
-
Materials: The choice of polymers significantly affects the cost. Common materials include polyethylene (PE), polypropylene (PP), and polyethylene terephthalate (PET). Prices can fluctuate based on market demand and availability, which can vary by region, particularly in Africa and South America.
-
Labor: Labor costs can vary widely depending on the region and skill level required. In emerging markets, labor may be less expensive, but the need for skilled technicians for quality control and machinery operation can increase costs.
-
Manufacturing Overhead: This includes costs associated with running the facility, utilities, and maintenance. For international buyers, understanding local regulations and operational efficiencies can help mitigate these expenses.
-
Tooling: Blow molding requires specific molds, which can be a significant upfront investment. While the initial tooling costs can be high, they are amortized over large production runs. Custom molds for complex designs can further escalate costs.
-
Quality Control (QC): Maintaining quality is crucial in blow molding, especially for sectors like packaging and automotive. Implementing rigorous QC processes incurs additional costs, but they are vital for ensuring product reliability and compliance with industry standards.
-
Logistics: Transportation and shipping costs can vary depending on location, shipping method, and Incoterms chosen. International buyers should consider these factors when sourcing from different regions.
-
Margin: Suppliers typically include a profit margin in their pricing, which can vary based on market competition, supplier reputation, and the complexity of the order.
What Influences Pricing in Blow Molding?
Understanding the key factors that influence pricing can help buyers make informed decisions:
-
Volume/MOQ (Minimum Order Quantity): Larger orders generally reduce the per-unit cost. Negotiating favorable terms for higher volumes can lead to significant savings.
-
Specifications and Customization: Custom designs and specific material requirements can increase costs. Buyers should clearly define their needs to avoid unexpected expenses.
-
Material Selection: The choice of material not only affects the cost but also the final product’s quality and durability. Buyers should weigh the cost against performance requirements.
-
Quality and Certifications: Products requiring specific certifications (e.g., FDA approval for food packaging) may incur additional costs. Ensure suppliers can meet these requirements to avoid costly delays.
-
Supplier Factors: The supplier’s reputation, location, and experience can influence pricing. Established suppliers may charge more but offer reliability and quality assurance.
-
Incoterms: Understanding the chosen Incoterms is critical for international transactions. These terms dictate responsibilities for shipping costs, risk, and insurance, impacting the total landed cost.
What Are the Best Negotiation and Cost-Efficiency Tips for Buyers?
B2B buyers, particularly from Africa, South America, the Middle East, and Europe, should consider the following tips to optimize their sourcing strategy:
-
Negotiate Terms: Leverage your purchasing power to negotiate better terms, especially for large orders. Establishing long-term relationships with suppliers can lead to favorable pricing.
-
Evaluate Total Cost of Ownership (TCO): Beyond the initial purchase price, consider maintenance, logistics, and potential downtime costs. TCO analysis provides a comprehensive view of the financial implications of sourcing decisions.
-
Understand Pricing Nuances: Be aware of regional pricing variations and the impact of currency fluctuations on costs. International buyers should factor in these elements when negotiating.
-
Seek Multiple Quotes: Obtaining quotes from several suppliers helps establish a competitive pricing baseline. Use this information to negotiate better deals.
-
Invest in Quality: While lower costs are appealing, investing in quality materials and suppliers can lead to long-term savings through reduced failures and rework.
Disclaimer on Indicative Prices
Please note that pricing for blow molding services can vary widely based on numerous factors, including material costs, order volume, and supplier capabilities. It is advisable for buyers to conduct thorough market research and obtain multiple quotes to ensure they receive competitive pricing tailored to their specific needs.
Alternatives Analysis: Comparing blow molding With Other Solutions
Understanding Alternatives to Blow Molding
As international B2B buyers explore manufacturing options, it’s essential to compare blow molding with other viable solutions. Each method has its unique advantages and limitations, making it crucial for buyers to assess which process aligns best with their product requirements, production volume, and budget constraints. This section will provide a detailed comparison of blow molding with rotational molding and injection molding, helping buyers make informed decisions.
Comparison Aspect | Blow Molding | Rotational Molding | Injection Molding |
---|---|---|---|
Performance | Excellent for hollow, thin-walled shapes; limited wall thickness control | Good for large, seamless parts; higher design freedom | High precision; ideal for complex geometries |
Cost | Cost-effective for large volumes; higher initial tooling costs | Lower tooling costs; suitable for low-volume runs | High initial costs; economical for high volume |
Ease of Implementation | Requires specific machinery; moderate complexity | Simpler setup; less specialized equipment needed | Complex machinery required; high expertise needed |
Maintenance | Moderate maintenance; wear on molds over time | Low maintenance; molds last longer | High maintenance due to complexity and wear |
Best Use Case | Ideal for bottles, containers, and hollow parts in large quantities | Best for toys, tanks, and large industrial products | Perfect for detailed parts in automotive and consumer goods |
In-Depth Analysis of Alternatives
What Are the Advantages and Disadvantages of Rotational Molding?
Rotational molding is an alternative that excels in producing large, hollow, and seamless parts. The primary advantage of this method is its design freedom, allowing for complex geometries that blow molding may struggle to achieve. Additionally, rotational molding typically features lower tooling costs, making it an attractive option for low-volume production runs or projects with frequent design changes. However, it may not be as efficient for high-volume production compared to blow molding, and cycle times are generally longer.
How Does Injection Molding Compare to Blow Molding?
Injection molding is another popular alternative, particularly known for its high precision and ability to create intricate designs. This method is best suited for applications requiring tight tolerances and complex features, making it ideal for automotive components and consumer products. However, injection molding comes with higher initial costs and requires specialized machinery, which can be a barrier for small to mid-sized manufacturers. While it offers excellent production rates for high volumes, the cost-effectiveness diminishes for lower production runs.
Making the Right Choice for Your Manufacturing Needs
For international B2B buyers, the choice between blow molding, rotational molding, and injection molding hinges on specific project requirements. If the goal is to produce large quantities of hollow parts efficiently, blow molding is often the best option. Conversely, for projects requiring intricate designs or lower production volumes, rotational molding or injection molding may provide better value.
Ultimately, understanding the unique characteristics of each method will empower buyers to select the most appropriate solution that meets their production needs, budget, and desired product quality. By carefully evaluating the advantages and disadvantages of each alternative, businesses can enhance their manufacturing strategies and drive successful outcomes.
Essential Technical Properties and Trade Terminology for blow molding
What Are the Key Technical Properties of Blow Molding?
Understanding the essential technical properties involved in blow molding is critical for international B2B buyers. These specifications not only influence product quality but also affect the overall production process and cost-efficiency.
1. Material Grade
The choice of material grade is paramount in blow molding. Common materials include high-density polyethylene (HDPE), polyethylene terephthalate (PET), and polypropylene (PP). Each material has unique properties such as chemical resistance, tensile strength, and thermal stability. Selecting the appropriate material grade ensures that the final product meets specific application requirements, such as durability and compliance with industry standards. For instance, PET is widely used in beverage containers due to its clarity and strength.
2. Wall Thickness Tolerance
Wall thickness tolerance refers to the allowable variation in the thickness of the molded part. It is crucial in applications where structural integrity and performance are essential, such as automotive or packaging components. A tighter tolerance can improve strength and reduce the risk of failure under stress. However, achieving precise wall thickness can be challenging in blow molding, which may impact cost and production efficiency. Buyers should communicate their tolerance requirements clearly to manufacturers to avoid costly rework.
3. Dimensional Accuracy
Dimensional accuracy is the degree to which the produced part matches the intended design specifications. In blow molding, maintaining dimensional accuracy is vital for ensuring that parts fit together correctly in assemblies. Poor dimensional accuracy can lead to increased scrap rates and higher production costs. Buyers should specify their dimensional requirements in detail during the procurement process to ensure that manufacturers can meet their needs.
4. Cycle Time
Cycle time is the total time taken to produce one part from start to finish, including heating, molding, and cooling. Reducing cycle time is essential for improving productivity and lowering manufacturing costs. Buyers should inquire about the cycle times of different blow molding processes (EBM, IBM, ISBM) to determine which method aligns best with their production volume and urgency.
5. Surface Finish Quality
Surface finish quality refers to the texture and appearance of the final product. Depending on the application, a smooth or textured surface may be required. For instance, consumer products may necessitate a polished finish for aesthetic appeal, while industrial components may prioritize functionality over appearance. Understanding the desired surface finish helps buyers communicate their requirements effectively to manufacturers.
What Are Common Trade Terms in Blow Molding?
Familiarizing yourself with industry jargon can enhance communication and negotiation with suppliers and manufacturers.
1. OEM (Original Equipment Manufacturer)
An OEM is a company that produces parts or equipment that may be marketed by another manufacturer. In the context of blow molding, buyers often collaborate with OEMs to create custom-designed components that meet their specifications. Understanding OEM relationships can help buyers leverage the expertise of manufacturers in achieving high-quality products.
2. MOQ (Minimum Order Quantity)
MOQ is the smallest quantity of a product that a supplier is willing to sell. This term is crucial for B2B buyers, particularly in international markets, as it can impact the overall cost and feasibility of orders. Buyers should negotiate MOQs based on their production needs and budget constraints to optimize their supply chain.
3. RFQ (Request for Quotation)
An RFQ is a document issued by a buyer to solicit price quotes from suppliers for specific products or services. For blow molding, an RFQ should include detailed specifications such as material grade, dimensions, and tolerances to ensure accurate quotes. This process helps buyers compare costs and make informed purchasing decisions.
4. Incoterms (International Commercial Terms)
Incoterms are internationally recognized terms that define the responsibilities of buyers and sellers in international transactions. These terms clarify aspects such as shipping costs, insurance, and risk transfer. Understanding Incoterms is essential for B2B buyers to navigate logistics and ensure compliance with trade regulations.
5. Lead Time
Lead time refers to the period from placing an order to receiving the finished product. It encompasses manufacturing and shipping times. Buyers should consider lead times when planning their production schedules to avoid delays. Clear communication with suppliers about expected lead times can help mitigate potential disruptions in the supply chain.
By understanding these technical properties and trade terms, international B2B buyers can make informed decisions, optimize their manufacturing processes, and enhance collaboration with suppliers in the blow molding industry.
Navigating Market Dynamics and Sourcing Trends in the blow molding Sector
What Are the Key Trends and Dynamics in the Global Blow Molding Market?
The blow molding industry is witnessing significant growth driven by various global factors. The demand for lightweight and sustainable packaging solutions in sectors like consumer goods, automotive, and agriculture is propelling the market forward. As international B2B buyers from regions such as Africa, South America, the Middle East, and Europe seek efficient manufacturing processes, blow molding stands out due to its cost-effectiveness and ability to produce hollow plastic parts at scale. Notably, the rise of e-commerce is influencing packaging needs, leading to increased demand for innovative blow-molded products.
Emerging technologies such as 3D printing are also reshaping the blow molding landscape. By allowing for rapid prototyping and the production of complex mold designs, these technologies can significantly reduce lead times and tooling costs. Buyers should consider suppliers who leverage such technologies to stay competitive. Additionally, automation in blow molding processes enhances efficiency and reduces labor costs, making it a vital consideration for businesses aiming to optimize production.
International buyers should also pay attention to regional market dynamics. For example, the European Union’s stringent regulations on plastic waste management have resulted in a shift towards recyclable and biodegradable materials. In contrast, markets in Africa and South America are experiencing a surge in demand for affordable packaging solutions, presenting unique opportunities for suppliers who can offer tailored solutions.
How Does Sustainability and Ethical Sourcing Impact the Blow Molding Sector?
Sustainability is increasingly becoming a focal point for international B2B buyers. The blow molding sector is responding to environmental concerns by adopting sustainable practices and materials. The use of recyclable plastics such as PET and HDPE is on the rise, as these materials have lower environmental impacts compared to traditional options. Buyers should prioritize suppliers who offer ‘green’ certifications and transparent sourcing practices, ensuring that their products not only meet quality standards but also contribute to sustainable development.
Ethical sourcing is equally important, especially in regions where supply chain transparency can be challenging. Buyers should seek partners who adhere to ethical labor practices and environmental regulations. Certifications such as ISO 14001 for environmental management and the Global Recycled Standard (GRS) can serve as indicators of a supplier’s commitment to sustainability.
In addition, many manufacturers are investing in the development of biodegradable materials for blow molding applications. This innovation is crucial for reducing plastic waste and aligns with the global shift towards a circular economy. By engaging with suppliers focused on sustainable practices, B2B buyers can enhance their brand reputation and meet the growing consumer demand for eco-friendly products.
What Is the Historical Context of Blow Molding Relevant to B2B Buyers?
Blow molding, a process that dates back to the early 20th century, has evolved significantly to meet modern manufacturing needs. Initially developed for glass production, the technique transitioned to plastic in the 1930s, paving the way for mass production of hollow plastic items. The introduction of various blow molding techniques—extrusion, injection, and stretch blow molding—has expanded the capabilities of manufacturers, allowing for the creation of more complex and durable products.
Understanding this evolution is essential for B2B buyers, as it highlights the industry’s adaptability and innovation. The continuous advancements in blow molding technology, particularly in automation and material science, demonstrate the sector’s commitment to improving efficiency and sustainability. This historical perspective can guide buyers in making informed decisions about sourcing and partnerships, ensuring they align with suppliers who are forward-thinking and equipped to meet future challenges.
Conclusion
In summary, navigating the blow molding sector requires an understanding of market dynamics, sustainability trends, and the historical context of the industry. International B2B buyers must remain vigilant about emerging technologies and ethical sourcing practices to ensure they partner with suppliers who align with their business goals and values. By prioritizing these factors, buyers can enhance their competitive edge in a rapidly evolving marketplace.
Frequently Asked Questions (FAQs) for B2B Buyers of blow molding
-
How do I choose the right blow molding supplier for my business needs?
Selecting a blow molding supplier requires careful evaluation of their capabilities, quality standards, and industry experience. Start by researching suppliers who specialize in your specific product type and have a proven track record in your target market. Request samples of their previous work to assess quality, and check references or reviews from other clients. Additionally, consider their production capacity, lead times, and whether they can accommodate your customization requirements. Engaging in direct communication can also provide insights into their responsiveness and customer service. -
What are the typical minimum order quantities (MOQ) for blow molding products?
Minimum order quantities for blow molding can vary significantly depending on the supplier, the complexity of the design, and the materials used. Generally, MOQs can range from a few hundred to several thousand units. For international buyers, it’s essential to discuss MOQs during initial negotiations, as some suppliers may offer flexibility for first-time orders or pilot runs. Understanding the implications of MOQs on your inventory and cash flow is crucial, especially in emerging markets where demand may fluctuate. -
What payment terms should I expect when sourcing blow molding services internationally?
Payment terms for international sourcing can vary widely based on the supplier’s policies and the nature of the transaction. Common arrangements include advance payments, letter of credit, or payment upon delivery. It’s advisable to negotiate terms that balance risk and cash flow for both parties. Ensure that payment methods are secure and preferably include options for dispute resolution. Additionally, consider the currency exchange rates and any potential fees that may arise from international transactions. -
How can I ensure the quality of blow molded products before shipment?
To ensure quality, establish clear quality assurance (QA) protocols with your supplier before production begins. This includes defining specifications for dimensions, material properties, and surface finishes. Request pre-production samples to evaluate the quality and adherence to your standards. Many suppliers offer inspection reports and certifications; consider hiring third-party inspection services to verify compliance with international standards. Regular communication and updates during the production process can help address any issues early on. -
What are the advantages of blow molding compared to other manufacturing processes?
Blow molding is highly efficient for producing hollow plastic parts, offering cost advantages for large-scale production. It allows for complex shapes with seamless construction, reducing the need for assembly and enhancing durability. The process is adaptable to various materials, including PET and HDPE, making it suitable for diverse applications, from packaging to automotive components. When compared to methods like injection molding, blow molding typically has lower tooling costs, making it a compelling choice for businesses looking to scale production economically. -
How does the choice of material impact the blow molding process?
The choice of material significantly influences both the blow molding process and the final product characteristics. Common materials such as polyethylene, polypropylene, and PET each have unique thermal properties and processing requirements. For instance, PET is often used for bottles due to its strength and clarity, while HDPE is favored for its durability. Selecting the appropriate material not only affects production efficiency but also impacts product performance, sustainability, and cost. It’s essential to collaborate with your supplier to select the best material for your specific application. -
What logistics considerations should I keep in mind when importing blow molded products?
Logistics play a critical role in the successful import of blow molded products. Consider factors such as shipping methods, customs regulations, and lead times. Work with suppliers who have experience in international shipping to ensure compliance with all necessary documentation, including bills of lading and certificates of origin. Additionally, factor in warehousing solutions and distribution channels in your target market to streamline delivery. Planning for potential delays and understanding local regulations can help mitigate risks associated with international logistics. -
What customization options are available in blow molding for my specific product needs?
Blow molding offers a range of customization options to meet specific product requirements. This includes variations in size, shape, wall thickness, and surface finishes. You can also incorporate features such as handles, spouts, or embossed logos. Collaborate closely with your supplier during the design phase to explore the full range of customization possibilities, ensuring that your product meets both functional and aesthetic criteria. Utilizing advanced technologies like 3D modeling can facilitate more complex designs and quicker iterations, enhancing your product’s market competitiveness.
Important Disclaimer & Terms of Use
⚠️ Important Disclaimer
The information provided in this guide, including content regarding manufacturers, technical specifications, and market analysis, is for informational and educational purposes only. It does not constitute professional procurement advice, financial advice, or legal advice.
While we have made every effort to ensure the accuracy and timeliness of the information, we are not responsible for any errors, omissions, or outdated information. Market conditions, company details, and technical standards are subject to change.
B2B buyers must conduct their own independent and thorough due diligence before making any purchasing decisions. This includes contacting suppliers directly, verifying certifications, requesting samples, and seeking professional consultation. The risk of relying on any information in this guide is borne solely by the reader.
Strategic Sourcing Conclusion and Outlook for blow molding
What Are the Key Takeaways for Strategic Sourcing in Blow Molding?
In conclusion, strategic sourcing in blow molding is essential for international B2B buyers aiming to optimize production costs and enhance product quality. The process offers significant advantages, including cost-effectiveness, design flexibility, and the capability to create seamless structures that meet diverse industry needs. Understanding the distinctions among extrusion blow molding, injection blow molding, and injection stretch blow molding allows buyers to make informed decisions tailored to their specific applications.
How Can B2B Buyers Benefit from Market Trends?
As the global demand for sustainable and innovative packaging solutions rises, leveraging advancements in technologies like 3D printing for mold creation can further reduce costs and lead times. Buyers from Africa, South America, the Middle East, and Europe should actively engage with suppliers who are adopting these technologies to stay competitive in their markets.
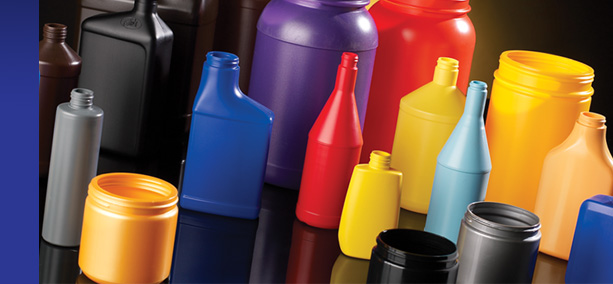
A stock image related to blow molding.
What Is the Future Outlook for Blow Molding?
Looking ahead, the blow molding industry is poised for growth as manufacturers continue to invest in sustainable practices and materials. By establishing strategic partnerships with reliable suppliers and staying informed about market trends, international B2B buyers can position themselves for success in an evolving landscape. Now is the time to explore these opportunities and enhance your sourcing strategy to meet the demands of tomorrow’s market.