Unlock Cost Savings: The Ultimate Gasket Material Guide (2025)
Introduction: Navigating the Global Market for gasket material
In the intricate landscape of global commerce, sourcing high-quality gasket material poses a significant challenge for international B2B buyers, particularly those operating in diverse markets such as Africa, South America, the Middle East, and Europe. With numerous options available, selecting the right gasket material that meets specific operational requirements while ensuring compliance with regional standards can be daunting. This guide aims to demystify the complexities of the gasket material market, providing a comprehensive overview of various types—including rubber, silicone, and PTFE—alongside their applications in sectors such as automotive, manufacturing, and construction.
Moreover, we will delve into essential factors such as supplier vetting processes, pricing structures, and logistics considerations tailored to different geographical contexts. By equipping B2B buyers with actionable insights, this guide empowers them to make informed purchasing decisions that optimize both performance and cost-efficiency. Whether you are based in Mexico, the UAE, or elsewhere, understanding the nuances of gasket material sourcing will enable you to navigate the global market with confidence, ensuring that your business remains competitive and compliant in an ever-evolving landscape.
Understanding gasket material Types and Variations
Type Name | Key Distinguishing Features | Primary B2B Applications | Brief Pros & Cons for Buyers |
---|---|---|---|
Aramid Fiber Gaskets | High strength, chemical resistance, and excellent torque retention | Automotive, industrial machinery | Pros: Durable and resilient. Cons: Higher cost compared to other materials. |
EPDM Rubber Gaskets | Excellent weather and ozone resistance, good elasticity | HVAC, plumbing, and automotive applications | Pros: Cost-effective and versatile. Cons: Limited high-temperature resistance. |
PTFE Gaskets | Exceptional chemical resistance, non-stick properties | Chemical processing, food and beverage | Pros: Highly resistant to chemicals. Cons: Can be more expensive and less compressible. |
Cork-Rubber Gaskets | Combination of cork and rubber for flexibility and sealing ability | Automotive, oil and gas applications | Pros: Good compressibility. Cons: May not withstand extreme temperatures. |
Silicone Gaskets | High-temperature resistance and flexibility, often FDA-approved | Food processing, pharmaceuticals | Pros: Safe for food applications. Cons: Less durable than some synthetic options. |
What are the characteristics of Aramid Fiber Gaskets?
Aramid fiber gaskets are known for their high strength and durability, making them ideal for applications that require excellent torque retention and resistance to harsh chemicals. Commonly used in automotive and industrial machinery, these gaskets can withstand extreme conditions, ensuring a reliable seal. When purchasing aramid fiber gaskets, B2B buyers should consider the specific chemical compatibility and temperature ranges relevant to their operations, as well as the initial investment, which may be higher than alternative materials.
Why choose EPDM Rubber Gaskets for your applications?
EPDM rubber gaskets are particularly valued for their excellent resistance to weathering, ozone, and aging. They offer good elasticity and can be used in a variety of applications, including HVAC and plumbing. For B2B buyers, the cost-effectiveness of EPDM makes it an attractive option, but it is crucial to assess the temperature limits of the material as it may not perform well in high-temperature environments. Understanding the application requirements will help in selecting the right EPDM product.
What makes PTFE Gaskets a preferred choice in chemical processing?
PTFE gaskets are renowned for their exceptional chemical resistance and non-stick properties, making them suitable for demanding environments such as chemical processing and food and beverage industries. These gaskets can handle a wide range of temperatures and pressures, but they can be more expensive than other options and may have limitations in compressibility. B2B buyers should evaluate the cost against the long-term benefits of reduced maintenance and downtime when considering PTFE gaskets.
How do Cork-Rubber Gaskets perform in various applications?
Cork-rubber gaskets combine the compressibility of cork with the durability of rubber, providing a flexible sealing solution. They are commonly used in automotive and oil and gas applications where a reliable seal is necessary. While they offer good sealing capabilities, buyers should be aware that cork-rubber gaskets may not withstand extreme temperatures as effectively as synthetic options. Assessing the specific environmental conditions will ensure optimal performance.
What advantages do Silicone Gaskets provide for food processing?
Silicone gaskets are favored in industries such as food processing and pharmaceuticals due to their high-temperature resistance and FDA approval. They are flexible and can maintain a good seal under various conditions. However, while silicone gaskets are safe for food applications, they may not be as durable as some synthetic materials. B2B buyers should consider the specific requirements of their applications, including temperature and chemical exposure, to make informed purchasing decisions.
Key Industrial Applications of gasket material
Industry/Sector | Specific Application of Gasket Material | Value/Benefit for the Business | Key Sourcing Considerations for this Application |
---|---|---|---|
Oil & Gas | Sealing flanges in pipelines | Prevents leaks, ensuring safety and compliance | Material resistance to high pressure and temperature, certification for hazardous materials |
Automotive | Engine gaskets and seals | Enhances performance and fuel efficiency | Compliance with OEM specifications, availability of various thicknesses and materials |
Chemical Processing | Gaskets for reactors and storage tanks | Protects against corrosive substances | Chemical compatibility, temperature tolerance, and certification for food-grade applications |
Power Generation | Gaskets in turbines and generators | Increases operational efficiency | Durability under extreme conditions, custom sizing options |
Water Treatment | Gaskets for pumps and valves in treatment plants | Ensures integrity and longevity of systems | NSF certification for potable water applications, availability of various materials |
How is Gasket Material Used in the Oil & Gas Industry?
In the oil and gas sector, gasket materials are essential for sealing flanges in pipelines and equipment. These gaskets prevent leaks, which can lead to environmental hazards and regulatory non-compliance. Buyers must prioritize materials that withstand high pressure and temperature fluctuations, while also ensuring compliance with safety regulations. For international buyers, sourcing materials that meet local certifications, especially in regions like the Middle East and Africa, is crucial to avoid costly delays and ensure safety.
What Role Does Gasket Material Play in the Automotive Sector?
In the automotive industry, gasket materials are primarily used in engine components, such as cylinder heads and oil pans. High-quality gaskets enhance engine performance, reduce emissions, and improve fuel efficiency. B2B buyers should consider OEM specifications to ensure compatibility with various engine designs. Additionally, the availability of different materials and thicknesses is vital, as it allows for customization based on specific automotive applications, particularly in European and South American markets where vehicle standards may vary.
Why are Gaskets Critical in Chemical Processing?
Chemical processing facilities utilize gasket materials in reactors, storage tanks, and piping systems to prevent leaks of hazardous substances. The right gasket material can provide protection against aggressive chemicals, ensuring safety and compliance with industry regulations. Buyers must focus on chemical compatibility and temperature tolerance when sourcing these materials. Furthermore, certifications for food-grade applications are essential for companies operating in regions like Africa and South America, where regulatory standards may differ.
How Do Gaskets Enhance Power Generation Operations?
In power generation, gaskets are used in turbines and generators to maintain system integrity and efficiency. These gaskets help prevent leaks that can lead to operational inefficiencies and increased maintenance costs. B2B buyers should seek durable materials that perform well under extreme conditions, as well as custom sizing options to fit specific machinery. Understanding local sourcing capabilities in regions like the UAE can aid in reducing lead times and ensuring the timely delivery of essential components.
What is the Importance of Gasket Material in Water Treatment?
Gasket materials play a crucial role in water treatment plants, where they are used in pumps, valves, and filtration systems. These gaskets ensure the integrity and longevity of water systems, preventing leaks that could compromise water quality. Buyers must consider NSF certification for potable water applications, as well as the availability of various materials that can withstand the demands of treatment processes. For international buyers, sourcing from suppliers with a strong track record in compliance is vital to maintaining operational standards and ensuring public health safety.
3 Common User Pain Points for ‘gasket material’ & Their Solutions
Scenario 1: Inconsistent Quality of Gasket Material
The Problem: Many B2B buyers experience frustration when the quality of gasket materials fluctuates, leading to premature failures in sealing applications. This inconsistency can stem from suppliers cutting corners in manufacturing or using subpar raw materials. Buyers in industries such as oil and gas, automotive, or food processing often face the dire consequences of leaks, equipment damage, and increased downtime due to these failures.
The Solution: To combat quality inconsistency, international B2B buyers should focus on sourcing gasket materials from reputable suppliers with established quality assurance processes. Request certifications and test reports that demonstrate compliance with industry standards such as ISO or ASTM. It is also crucial to establish a robust relationship with suppliers, enabling transparent communication regarding material specifications and performance expectations. Implementing a strict incoming quality control process can further ensure that only materials meeting stringent criteria are used in production.
Scenario 2: Difficulty in Selecting the Right Gasket Material for Specific Applications
The Problem: Choosing the appropriate gasket material for specific applications can be overwhelming due to the wide variety of materials available, each with distinct properties. For instance, buyers may struggle to decide between silicone, EPDM, or PTFE gaskets based on factors like temperature resistance, chemical compatibility, or application type. This can lead to improper selections, resulting in leakage, product contamination, or equipment failure, which ultimately affects operational efficiency and costs.
The Solution: Buyers should invest time in understanding the application requirements thoroughly and utilize material data sheets to compare properties. Creating a checklist of factors such as operating temperature, pressure, and exposure to chemicals will aid in narrowing down choices. Furthermore, consulting with technical experts or utilizing suppliers who offer material selection guides and samples can provide valuable insights. Conducting trials with a small batch of the selected material in real operating conditions can also validate the choice before scaling up orders.
Scenario 3: High Costs Associated with Gasket Material Procurement
The Problem: Procurement costs for gasket materials can be a significant burden for international B2B buyers, especially when dealing with fluctuating currency exchange rates, import duties, and shipping costs. Buyers from regions like Africa or South America often find themselves paying exorbitant prices due to limited local suppliers and the high cost of importing quality materials. This situation can lead to budget overruns and affect overall project profitability.
The Solution: To mitigate procurement costs, buyers should consider establishing long-term partnerships with multiple suppliers to negotiate better pricing and terms. Exploring local manufacturing options can also reduce reliance on imports, thus minimizing shipping costs and lead times. Additionally, buyers can benefit from bulk purchasing agreements or collaborative buying initiatives with other businesses in similar sectors to leverage economies of scale. Implementing an inventory management system can help optimize stock levels, reducing the need for urgent, high-cost orders when materials run low.
By addressing these common pain points with informed strategies, B2B buyers can enhance their procurement processes for gasket materials, ultimately leading to improved operational efficiency and reduced costs.
Strategic Material Selection Guide for gasket material
What Are the Key Properties of Common Gasket Materials?
When selecting gasket materials for industrial applications, it is crucial to consider their properties, as these directly influence performance and compatibility with various media. Here, we explore four common gasket materials: EPDM Rubber, PTFE, Aramid Fiber, and Silicone Rubber.
How Does EPDM Rubber Perform in Gasket Applications?
EPDM (Ethylene Propylene Diene Monomer) rubber is renowned for its excellent weather resistance and ability to withstand a wide range of temperatures, typically from -40°F to 300°F (-40°C to 150°C). It exhibits good resistance to steam, water, and many chemicals, making it suitable for outdoor applications and environments with fluctuating temperatures.
Pros:
– High durability and longevity in outdoor environments.
– Cost-effective compared to other materials.
– Good flexibility and resilience.
Cons:
– Limited compatibility with certain oils and fuels.
– Not suitable for high-pressure applications.
Impact on Application: EPDM is often used in automotive and HVAC applications, particularly for sealing and insulation. International buyers should ensure compliance with ASTM standards, particularly for automotive applications.
Why Choose PTFE for Gasket Materials?
PTFE (Polytetrafluoroethylene) is a high-performance material known for its exceptional chemical resistance and temperature tolerance, typically ranging from -450°F to 500°F (-268°C to 260°C). It is non-stick and can handle aggressive chemicals, making it ideal for industries such as pharmaceuticals and food processing.
Pros:
– Inert to most chemicals, including strong acids and bases.
– Excellent thermal stability.
– Low friction properties.
Cons:
– Higher cost compared to rubber-based materials.
– Requires careful handling during installation due to its softness.
Impact on Application: PTFE gaskets are essential in applications involving corrosive substances. Buyers in regions like the Middle East, where chemical processing is prevalent, should verify compliance with relevant industry standards.
What Are the Advantages of Aramid Fiber Gaskets?
Aramid fiber gaskets, such as those made from Garlock BLUE-GARD, offer a unique combination of strength and flexibility. They are designed for high torque retention and can withstand temperatures up to 500°F (260°C) while maintaining low emissions.
Pros:
– High tensile strength and durability.
– Excellent sealing properties under pressure.
– Suitable for a range of applications, including oil and gas.
Cons:
– More expensive than traditional rubber gaskets.
– May require specific installation techniques to avoid damage.
Impact on Application: These gaskets are often used in critical applications where reliability is paramount. International buyers should consider local standards like DIN or JIS for compatibility and performance expectations.
When Should You Use Silicone Rubber for Gaskets?
Silicone rubber is known for its flexibility and high-temperature resistance, typically between -100°F to 500°F (-73°C to 260°C). It is particularly useful in applications that require a high degree of elasticity and resistance to extreme temperatures.
Pros:
– Excellent thermal stability and flexibility.
– Good resistance to UV and ozone exposure.
– Non-toxic and suitable for food-grade applications.
Cons:
– Generally more expensive than standard rubber.
– Limited chemical resistance compared to PTFE.
Impact on Application: Silicone gaskets are commonly used in food processing and pharmaceutical applications. Buyers should ensure that the materials meet FDA or NSF standards, especially in regions with strict food safety regulations.
Summary Table of Gasket Materials
Material | Typical Use Case for gasket material | Key Advantage | Key Disadvantage/Limitation | Relative Cost (Low/Med/High) |
---|---|---|---|---|
EPDM Rubber | Automotive, HVAC | High durability and longevity | Limited oil and fuel compatibility | Low |
PTFE | Chemical processing, pharmaceuticals | Exceptional chemical resistance | Higher cost and requires careful handling | High |
Aramid Fiber | Oil and gas, critical applications | High tensile strength and sealing properties | More expensive, specific installation needed | Med |
Silicone Rubber | Food processing, pharmaceuticals | Excellent thermal stability and flexibility | Limited chemical resistance | Med |
By understanding these materials and their properties, international B2B buyers can make informed decisions that align with their specific application needs, compliance requirements, and budget constraints.
In-depth Look: Manufacturing Processes and Quality Assurance for gasket material
What Are the Key Stages in the Manufacturing Process of Gasket Material?
The manufacturing process of gasket materials encompasses several critical stages that ensure the final product meets the required specifications and performance standards. Understanding these stages is essential for B2B buyers, particularly when sourcing from international suppliers.
Material Preparation
The first stage in gasket manufacturing involves the selection and preparation of raw materials. Various materials, including rubber, fiber, PTFE, and aramid fibers, are commonly used. Depending on the specific application, these materials may undergo pre-treatment processes such as drying, shredding, or mixing with binders and additives to enhance properties like elasticity, temperature resistance, and chemical compatibility.
For instance, aramid fibers may be combined with nitrile rubber to create a composite material that offers improved torque retention and reduced emissions. This blend is crucial for applications in automotive and industrial settings.
How Is Gasket Material Formed?
Once materials are prepared, they move to the forming stage. This involves shaping the gasket material into sheets or pre-cut forms, which can later be assembled into specific gasket configurations.
Key techniques include:
-
Compression Molding: This method is ideal for creating gaskets with complex shapes. Raw materials are placed in a heated mold, where heat and pressure are applied to form the desired shape.
-
Die Cutting: This process involves cutting gasket shapes from sheets using a die, which allows for high precision and repeatability. Die-cut gaskets are often used in mass production for automotive and industrial applications.
-
Water Jet Cutting: For more intricate designs or thicker materials, water jet cutting is utilized. This technique offers high accuracy without introducing heat that could alter the material properties.
What Finishing Techniques Are Applied to Gasket Materials?
After forming, the gaskets undergo finishing processes to enhance their performance and appearance. This may include:
-
Surface Treatment: Gaskets may be treated with coatings to improve resistance to chemicals, heat, or wear.
-
Inspection and Trimming: Gaskets are inspected for defects and trimmed to meet specific size requirements. This is crucial for ensuring a proper fit in their intended applications.
How Is Quality Assurance Implemented in Gasket Manufacturing?
Quality assurance is integral to the manufacturing process of gasket materials. It ensures that products not only meet industry standards but also customer expectations.
Which International Standards Are Relevant for Gasket Quality?
International standards such as ISO 9001 provide a framework for quality management systems. Compliance with ISO 9001 indicates that the manufacturer follows standardized processes that enhance product quality and customer satisfaction.
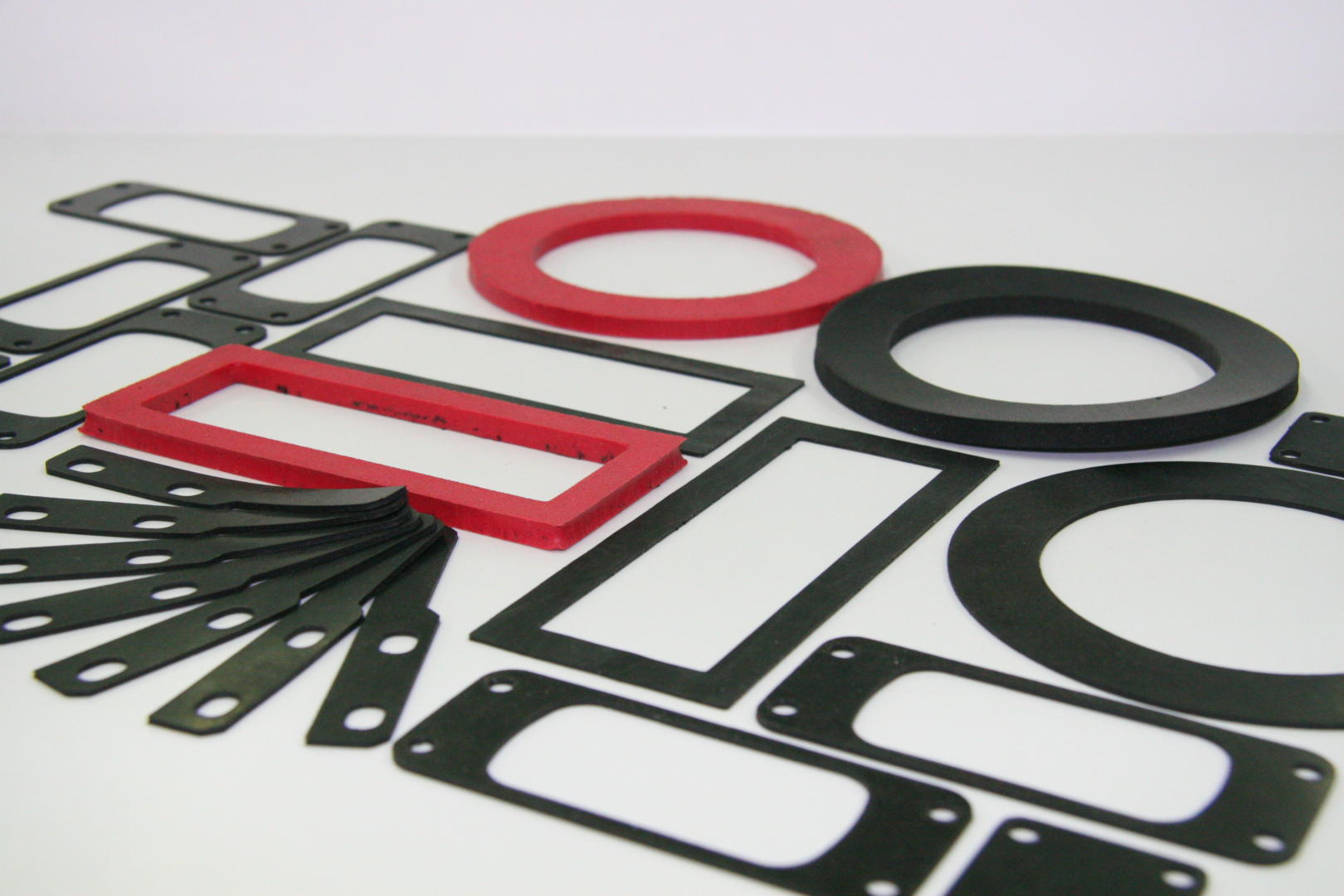
A stock image related to gasket material.
In addition to ISO standards, industry-specific certifications may apply, such as:
-
CE Marking: For products sold within the European Economic Area (EEA), the CE mark indicates conformity with health, safety, and environmental protection standards.
-
API Certification: In industries such as oil and gas, API certifications ensure that gaskets meet stringent requirements for safety and performance.
What Are the Key Quality Control Checkpoints?
Quality control (QC) in gasket manufacturing typically involves several checkpoints throughout the production process:
-
Incoming Quality Control (IQC): This initial stage involves inspecting raw materials upon arrival to ensure they meet specified standards. This prevents defects from entering the production line.
-
In-Process Quality Control (IPQC): Continuous monitoring during the manufacturing process helps identify any deviations from standards in real-time. This includes checking dimensions, material properties, and overall quality at various stages.
-
Final Quality Control (FQC): After production, a thorough inspection of the finished gaskets is conducted. This includes dimensional checks, visual inspections, and performance testing to ensure the final product meets all specifications.
How Can B2B Buyers Verify Supplier Quality Control?
B2B buyers should employ several strategies to verify the quality control practices of potential suppliers, particularly when sourcing internationally:
-
Conduct Supplier Audits: An on-site audit of the supplier’s manufacturing facility can provide valuable insights into their processes, equipment, and adherence to quality standards.
-
Request Quality Assurance Documentation: Buyers should ask for documents that detail the supplier’s quality management system, including ISO certifications, test reports, and inspection records.
-
Engage Third-Party Inspectors: Utilizing third-party inspection services can provide an unbiased assessment of the supplier’s quality control measures and the integrity of the products.
What Testing Methods Are Commonly Used for Gasket Materials?
Various testing methods are employed to ensure the performance and reliability of gasket materials, including:
-
Compression Set Testing: This test measures the gasket’s ability to maintain its shape after prolonged compression, which is crucial for applications under constant pressure.
-
Temperature and Pressure Testing: Gaskets are subjected to extreme temperatures and pressures to evaluate their performance in real-world conditions.
-
Chemical Resistance Testing: Gaskets must be tested against various chemicals to ensure they won’t degrade or fail in their intended environments.
What Are the Specific Quality Control Nuances for International B2B Buyers?
When dealing with international suppliers, particularly from regions like Africa, South America, the Middle East, and Europe, buyers must be aware of specific nuances in quality control:
-
Cultural Differences in Quality Standards: Different regions may have varying interpretations of quality standards. Buyers should ensure that their expectations align with the supplier’s practices.
-
Regulatory Compliance: Understanding local regulations regarding materials and safety is crucial. For example, certain materials may be restricted or require specific certifications in different countries.
-
Logistical Challenges: Ensure that the supplier has robust logistics and quality assurance processes to handle the complexities of international shipping, including customs regulations and transportation safety.
By understanding these manufacturing processes and quality assurance practices, B2B buyers can make informed decisions when sourcing gasket materials, ensuring that they receive high-quality products suited to their specific applications.
Practical Sourcing Guide: A Step-by-Step Checklist for ‘gasket material’
To successfully procure gasket material, it is essential to follow a structured approach that ensures quality and compatibility with your specific needs. This checklist will guide B2B buyers through the critical steps necessary for effective sourcing, particularly for those operating in diverse regions such as Africa, South America, the Middle East, and Europe.
Step 1: Define Your Technical Specifications
Establishing clear technical specifications is the cornerstone of effective gasket sourcing. Consider the application requirements, including temperature, pressure, and chemical compatibility. This will help you determine the right type of gasket material, such as rubber, PTFE, or cork, and ensure that it meets industry standards.
- Key considerations:
- Operating environment (temperature and pressure)
- Chemical exposure and compatibility
Step 2: Research Material Options
Investigate the various gasket materials available in the market to understand their properties and applications. Materials like EPDM, silicone, and aramid fibers offer unique benefits depending on the use case. Familiarizing yourself with these options will enable you to make informed decisions that align with your operational needs.
- Common materials:
- EPDM: Excellent for outdoor applications due to its weather resistance.
- PTFE: Ideal for corrosive environments, particularly in chemical industries.
Step 3: Evaluate Potential Suppliers
Before finalizing a supplier, conduct thorough evaluations to ensure they meet your quality and reliability standards. Request company profiles, certifications, and references. Engaging with suppliers who have a strong reputation in your industry can prevent potential sourcing pitfalls.
- What to assess:
- Supplier certifications (ISO, ASTM, etc.)
- Customer testimonials and case studies
Step 4: Request Samples for Testing
Obtaining samples of gasket materials allows you to evaluate their performance in real-world conditions. Testing samples helps ensure that the material meets your specific requirements for durability and functionality. This step is crucial to avoid costly mistakes in bulk orders.
- Testing parameters:
- Compression set
- Temperature and pressure resistance
Step 5: Verify Compliance with Regulations
Ensure that the gasket materials comply with local and international regulations, especially if they will be used in sensitive applications such as food processing or pharmaceuticals. Non-compliance can lead to legal issues and potential damage to your brand’s reputation.
- Regulatory considerations:
- FDA approvals for food-grade materials
- Environmental regulations for hazardous substances
Step 6: Assess Logistics and Delivery Options
Consider the logistics involved in sourcing gasket materials, including shipping times, costs, and supplier locations. Efficient logistics can significantly impact your project’s timeline and budget. Evaluate whether suppliers can meet your delivery requirements consistently.
- Logistical factors:
- Shipping methods and associated costs
- Supplier proximity to your location
Step 7: Negotiate Terms and Finalize Purchase
Once you’ve identified a suitable supplier and material, engage in negotiations to secure favorable terms. Discuss pricing, payment options, and warranty conditions. A well-negotiated contract can provide added protection and value for your procurement.
- Key negotiation points:
- Bulk order discounts
- Warranty and return policies
By following these steps, international B2B buyers can enhance their sourcing strategy for gasket materials, ensuring they select the most suitable products for their operational needs while minimizing risks.
Comprehensive Cost and Pricing Analysis for gasket material Sourcing
What Are the Key Cost Components in Gasket Material Sourcing?
When sourcing gasket materials, understanding the cost structure is crucial. The primary components include:
-
Materials: The type of gasket material significantly influences the price. Common materials like rubber, PTFE, and aramid fibers vary in cost based on their properties and applications. For instance, high-performance PTFE sheets can range from $274 to over $2,500, depending on thickness and certification.
-
Labor: Labor costs are incurred during manufacturing, cutting, and quality control processes. These costs can fluctuate based on the location of the supplier and the complexity of the production process.
-
Manufacturing Overhead: This includes costs associated with factory operations, utilities, and equipment maintenance. Efficient manufacturing practices can help keep these costs in check.
-
Tooling: Specialized tools and molds may be necessary for custom gasket manufacturing. Investment in tooling can lead to higher upfront costs but may reduce per-unit costs in the long run.
-
Quality Control (QC): Ensuring product quality often requires rigorous testing and inspections, contributing to overall costs. Certifications like ISO or NSF can also add to the price but enhance reliability.
-
Logistics: Transportation costs, including shipping and handling, can vary significantly based on the destination. Incoterms play a vital role in determining who bears these costs and responsibilities.
-
Margin: Suppliers typically add a margin to cover their operational costs and profit. This margin can vary widely based on market competition and supplier relationship dynamics.
How Do Price Influencers Affect Gasket Material Costs?
Several factors can influence the pricing of gasket materials:
-
Volume and Minimum Order Quantity (MOQ): Bulk orders usually result in lower per-unit prices due to economies of scale. Understanding the MOQ is essential for pricing negotiations.
-
Specifications and Customization: Customized gaskets tailored to specific applications will often incur additional costs. Standardized products typically offer more competitive pricing.
-
Material Quality and Certifications: High-quality materials with certifications (e.g., FDA-approved for food applications) may command higher prices but can lead to long-term savings through enhanced performance and durability.
-
Supplier Factors: Supplier reputation, reliability, and geographical location can influence costs. Local suppliers may offer lower shipping costs, while established suppliers might provide better quality assurance.
-
Incoterms: The chosen Incoterms can significantly impact total costs, as they dictate the responsibilities for shipping, insurance, and tariffs between buyer and seller. Understanding these terms is crucial for accurate cost projections.
What Buyer Tips Can Enhance Cost-Efficiency in Gasket Material Sourcing?
To maximize cost-efficiency when sourcing gasket materials, consider the following strategies:
-
Negotiate Wisely: Building a relationship with suppliers can lead to better pricing and terms. Don’t hesitate to negotiate on volume discounts or payment terms.
-
Evaluate Total Cost of Ownership (TCO): Focus not only on the initial purchase price but also on the long-term costs associated with maintenance, replacement, and downtime. High-quality gaskets may have a higher upfront cost but can result in lower TCO.
-
Understand Pricing Nuances for International Buyers: When sourcing from international suppliers, be aware of currency fluctuations, import tariffs, and regional regulations that may affect pricing. Establishing a clear understanding of these factors can prevent unexpected costs.
-
Consider Local Sourcing: For buyers in Africa, South America, the Middle East, and Europe, local suppliers may offer competitive pricing and reduced shipping costs. Assess the quality and availability of local materials before opting for international options.
Conclusion
Navigating the complexities of gasket material sourcing requires a comprehensive understanding of the cost structure, pricing influencers, and effective buyer strategies. By leveraging these insights, international B2B buyers can make informed decisions that lead to cost-effective sourcing solutions. Always remember that prices are indicative and can fluctuate based on market conditions, supplier negotiations, and changes in material costs.
Alternatives Analysis: Comparing gasket material With Other Solutions
In the competitive landscape of industrial sealing solutions, B2B buyers often face the challenge of selecting the right material for their applications. Gasket materials are commonly used for sealing joints in mechanical assemblies, but alternatives may offer distinct advantages based on specific operational needs. This section explores viable alternatives to traditional gasket materials, providing insights that can help international B2B buyers make informed decisions.
How Do Gasket Materials Compare to Alternative Solutions?
Comparison Aspect | Gasket Material | Alternative 1: O-Rings | Alternative 2: Sealing Compounds |
---|---|---|---|
Performance | Effective for static and dynamic seals | Excellent for dynamic sealing; limited to circular applications | Versatile; can fill gaps and provide solid seals |
Cost | Moderate initial cost | Generally lower cost | Varies widely based on formulation |
Ease of Implementation | Requires precise cutting and fitting | Easy to install; minimal tooling | Requires curing time; can be complex |
Maintenance | Low maintenance; long lifespan | Moderate; replacement needed when worn | Moderate; must be reapplied periodically |
Best Use Case | High-pressure applications; flanged joints | Hydraulic systems; rotating shafts | Irregular surfaces; large gaps |
What Are the Advantages and Disadvantages of O-Rings?
O-Rings are a popular alternative to gasket materials, especially in dynamic sealing applications. Their circular shape allows for effective sealing in hydraulic systems and rotating shafts. The primary advantages of O-Rings include their cost-effectiveness and ease of installation, as they typically do not require precise cutting or fitting. However, their use is limited to circular applications, which may restrict their applicability in complex assemblies that require non-circular sealing solutions. Additionally, O-Rings may need regular replacements, depending on the wear and tear in high-friction applications.
How Do Sealing Compounds Perform Compared to Gasket Materials?
Sealing compounds, such as silicone or epoxy-based products, offer a flexible alternative to traditional gasket materials. They can fill irregular gaps and provide a solid seal, making them ideal for non-standard joint configurations. The versatility of sealing compounds allows them to be used in a wide range of applications, including those with fluctuating temperatures and pressures. However, the curing time required for sealing compounds can complicate the implementation process, and they may require periodic reapplication to maintain effectiveness. The cost of sealing compounds can also vary significantly based on their formulation, making budgeting more complex.
Conclusion: How Should B2B Buyers Choose the Right Sealing Solution?
Selecting the right sealing solution requires a thorough understanding of the specific application requirements, including pressure, temperature, and the nature of the substances being sealed. For applications with high-pressure demands or where precise fitment is critical, traditional gasket materials may be the best choice. Conversely, for dynamic systems or irregular surfaces, O-Rings or sealing compounds might provide superior performance. By assessing the performance, cost, ease of implementation, and maintenance needs of each option, B2B buyers can make informed decisions that align with their operational goals and budget constraints.
Essential Technical Properties and Trade Terminology for gasket material
What Are the Key Technical Properties of Gasket Material?
When sourcing gasket materials, understanding specific technical properties is crucial for making informed purchasing decisions. Here are some of the most critical specifications:
-
Material Grade
– Definition: Material grade refers to the classification of the gasket material based on its composition and performance characteristics.
– Importance: Different applications require specific grades for optimal performance. For instance, aramid fiber materials are excellent for high-temperature environments, while EPDM is preferred for outdoor applications due to its resistance to weathering. -
Thickness
– Definition: Thickness is the measurement of the gasket material from one surface to the opposite surface.
– Importance: The thickness of the gasket affects its compressibility and sealing ability. Too thick a gasket may lead to inadequate sealing, while too thin could result in leakage. Understanding the required thickness can prevent costly errors in procurement. -
Tolerance
– Definition: Tolerance indicates the permissible limit of variation in a physical dimension of the gasket material.
– Importance: Maintaining tight tolerances is essential for ensuring that the gasket fits correctly within the assembly. Poor tolerance can lead to uneven sealing and increased wear on equipment, leading to higher maintenance costs. -
Temperature Resistance
– Definition: This property describes the maximum temperature a gasket material can withstand without losing its sealing ability.
– Importance: Gasket materials must be chosen based on the operating temperature of the application. For instance, PTFE gaskets are known for their high-temperature resistance and are suitable for chemical processing industries. -
Chemical Compatibility
– Definition: Chemical compatibility assesses how well a gasket material can resist degradation when exposed to various substances.
– Importance: Selecting the right material that can withstand the chemicals it will encounter is vital to prevent premature failure and ensure safety. For example, PTFE is often chosen for applications involving aggressive solvents. -
Compression Set
– Definition: Compression set measures the ability of the gasket material to return to its original thickness after being compressed.
– Importance: A low compression set value indicates that the gasket will maintain its sealing properties over time, reducing the need for frequent replacements and associated costs.
What Are Common Trade Terms Used in Gasket Material Procurement?
Familiarity with industry-specific terminology can enhance communication and efficiency in the procurement process. Here are some essential terms:
-
OEM (Original Equipment Manufacturer)
– Definition: An OEM is a company that produces parts and equipment that may be marketed by another manufacturer.
– Importance: Understanding OEM specifications is crucial for ensuring that the gasket materials meet the necessary standards for compatibility with existing equipment. -
MOQ (Minimum Order Quantity)
– Definition: MOQ is the smallest quantity of a product that a supplier is willing to sell.
– Importance: Knowing the MOQ helps buyers plan their inventory and budget effectively. It also aids in negotiating favorable terms with suppliers, particularly for smaller businesses. -
RFQ (Request for Quotation)
– Definition: An RFQ is a document that a buyer sends to suppliers requesting pricing and other details for specific products.
– Importance: Issuing an RFQ allows buyers to compare prices and terms from multiple suppliers, ensuring competitive pricing and informed decision-making. -
Incoterms (International Commercial Terms)
– Definition: Incoterms are a set of rules that define the responsibilities of sellers and buyers for the delivery of goods under sales contracts.
– Importance: Understanding Incoterms is essential for international transactions, as they clarify shipping responsibilities, risk transfer, and cost allocation, which can significantly impact overall procurement costs. -
Lead Time
– Definition: Lead time refers to the amount of time it takes for an order to be fulfilled from the moment it is placed.
– Importance: Knowing the lead time helps buyers plan their production schedules and manage inventory effectively. Long lead times may necessitate advanced planning to avoid production delays. -
Certification Standards
– Definition: Certification standards refer to specific criteria that materials must meet to be considered safe and reliable for use in particular applications (e.g., NSF, FDA).
– Importance: Ensuring that gasket materials meet relevant certification standards is critical for compliance and safety, particularly in industries such as food processing and pharmaceuticals.
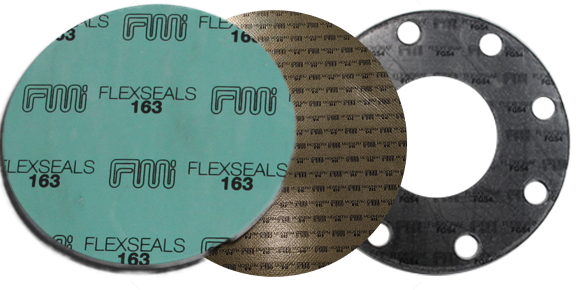
A stock image related to gasket material.
Understanding these technical properties and trade terminologies will empower international B2B buyers to make informed decisions, enhance procurement efficiency, and mitigate risks associated with gasket material sourcing.
Navigating Market Dynamics and Sourcing Trends in the gasket material Sector
What Are the Current Trends Impacting the Gasket Material Market?
The gasket material sector is experiencing significant shifts driven by globalization, technological advancements, and evolving customer demands. Global drivers, such as increasing industrialization in Africa and South America, are creating new markets for gasket materials. Emerging economies are investing heavily in infrastructure, manufacturing, and energy sectors, which are critical consumers of gasket materials. In Europe and the Middle East, stringent regulations on emissions and waste management are pushing manufacturers towards innovative materials that enhance efficiency and performance.
B2B technology trends are also reshaping sourcing strategies. Digital platforms for procurement are making it easier for international buyers to connect with suppliers, ensuring competitive pricing and broader access to diverse gasket materials. Additionally, the rise of e-commerce in the industrial sector is enabling buyers from regions like Mexico and the UAE to source materials directly from manufacturers, reducing lead times and costs. The use of data analytics in supply chain management is helping companies anticipate demand fluctuations, optimize inventory levels, and streamline operations.
As sustainability becomes a priority, buyers are increasingly seeking materials that offer both performance and environmental benefits. This shift is leading to a growing interest in advanced gasket materials, such as those made from recycled or bio-based components, which are gaining traction in the marketplace.
How Is Sustainability Shaping Gasket Material Sourcing?
Sustainability is no longer just a buzzword; it has become a critical factor in the sourcing of gasket materials. The environmental impact of manufacturing processes, including the use of hazardous materials and energy consumption, is under scrutiny. Buyers from Africa, South America, the Middle East, and Europe are prioritizing suppliers who adhere to sustainable practices and can demonstrate a commitment to reducing their carbon footprint.
Ethical sourcing is equally important. Buyers are increasingly looking for supply chains that are transparent and responsible, ensuring that labor practices meet international standards. Certifications such as ISO 14001 for environmental management and Fair Trade for ethical labor practices are becoming essential for suppliers wishing to compete in the global market.
Green certifications are also influencing material choice. Gasket materials that are certified for low emissions, such as NSF 61 for potable water applications or materials compliant with RoHS directives, are gaining favor among environmentally conscious buyers. This trend not only enhances brand reputation but also aligns with regulatory requirements in many regions, making it easier for companies to enter new markets.
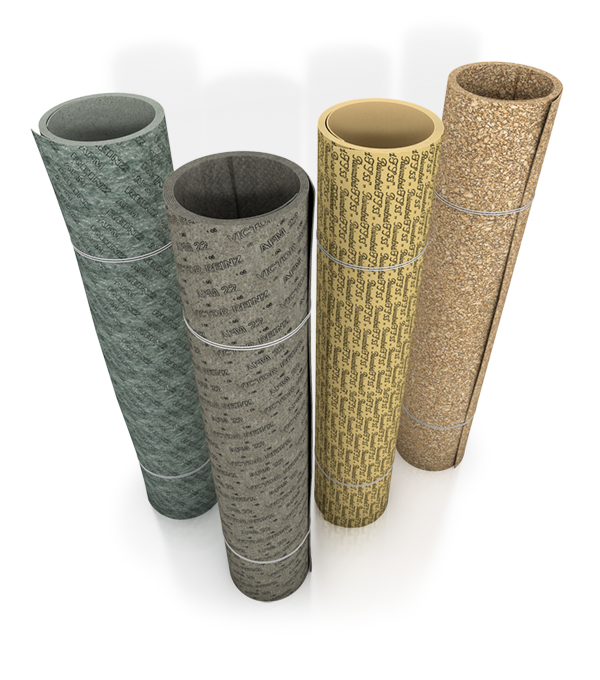
A stock image related to gasket material.
What Is the Historical Context of Gasket Materials in B2B?
The evolution of gasket materials has been marked by advancements in material science and engineering. Initially, gaskets were made from basic materials like cork and rubber, primarily used in simple mechanical applications. As industries advanced, the need for more durable and efficient sealing solutions emerged, leading to the development of composite materials and advanced polymers.
In the late 20th century, the introduction of synthetic materials, such as PTFE (polytetrafluoroethylene) and aramid fibers, revolutionized the gasket industry. These materials offered superior resistance to chemicals and temperature variations, making them essential in high-performance applications across industries like oil and gas, automotive, and aerospace.
Today, the gasket material sector continues to innovate, focusing on improving performance while minimizing environmental impact. The ongoing evolution reflects the industry’s responsiveness to global challenges, including sustainability and the demand for safer, more efficient products. This historical context is crucial for B2B buyers to understand the potential and limitations of various gasket materials available in the market.
Frequently Asked Questions (FAQs) for B2B Buyers of gasket material
-
How do I solve issues with gasket leakage in industrial applications?
To address gasket leakage, begin by identifying the root cause, such as improper installation, material incompatibility, or insufficient torque. Choose a gasket material that suits your specific application—consider factors like temperature, pressure, and the chemicals involved. It’s crucial to follow the manufacturer’s guidelines for installation and maintenance. If problems persist, consult with your supplier for customized solutions or alternative materials that enhance sealing effectiveness. -
What is the best gasket material for high-temperature applications?
For high-temperature applications, materials like PTFE (Polytetrafluoroethylene) and aramid fiber gaskets are often recommended. PTFE withstands extreme temperatures and is chemically resistant, making it ideal for corrosive environments. Aramid fiber gaskets offer excellent torque retention and stability under heat. Always consult technical data sheets to ensure compatibility with your specific conditions before making a purchase. -
How can I determine the right gasket thickness for my application?
The correct gasket thickness is typically determined by the flange surface finish, the material being sealed, and the operating conditions. Generally, thicker gaskets can accommodate more surface irregularities but may compress excessively under high pressure. Consult with your engineering team or gasket supplier to calculate the appropriate thickness based on your specific application requirements, ensuring optimal sealing performance. -
What should I consider when selecting an international supplier for gasket materials?
When selecting a supplier, consider their industry experience, product certifications, and customer reviews. Verify their ability to meet international quality standards, and assess their logistical capabilities, especially if you’re sourcing from Africa, South America, or the Middle East. It’s also essential to inquire about their ability to provide customized solutions and support services, such as technical assistance or training. -
What are the typical minimum order quantities (MOQs) for gasket materials?
MOQs can vary significantly among suppliers and depend on the material type and customization level. Standard gaskets may have lower MOQs, while specialized or custom-made gaskets often require larger orders. Discuss your needs with potential suppliers to negotiate favorable terms, especially if you’re looking to establish a long-term partnership. Many suppliers are willing to accommodate smaller orders for new clients as part of a trial phase. -
What payment terms should I expect when sourcing gasket materials internationally?
Payment terms can differ widely based on supplier policies and the buyer’s relationship with them. Common terms include advance payment, net 30, or even letter of credit for larger orders. For international transactions, consider the added complexity of currency exchange and potential tariffs. Always clarify terms in writing and assess the supplier’s flexibility to accommodate your financial processes, especially if you are operating in regions like Europe or the UAE. -
How can I ensure quality assurance (QA) for gasket materials sourced overseas?
To ensure quality assurance, request product certifications and quality control documentation from your supplier. Consider conducting third-party inspections or audits of the manufacturing facility, especially for critical applications. Establish clear communication channels to address quality concerns and ensure that your supplier adheres to industry standards. A reliable supplier should be open to discussions about QA processes and willing to implement corrective measures if necessary. -
What logistics considerations should I keep in mind when importing gasket materials?
When importing gasket materials, consider shipping times, customs clearance, and potential tariffs that may affect your overall cost. Partner with a logistics provider experienced in international shipping to navigate these challenges effectively. It’s also advisable to track your shipments and maintain open lines of communication with your supplier regarding delivery timelines. Be prepared for any delays, especially when sourcing from regions with varying infrastructure capabilities.
Important Disclaimer & Terms of Use
⚠️ Important Disclaimer
The information provided in this guide, including content regarding manufacturers, technical specifications, and market analysis, is for informational and educational purposes only. It does not constitute professional procurement advice, financial advice, or legal advice.
While we have made every effort to ensure the accuracy and timeliness of the information, we are not responsible for any errors, omissions, or outdated information. Market conditions, company details, and technical standards are subject to change.
B2B buyers must conduct their own independent and thorough due diligence before making any purchasing decisions. This includes contacting suppliers directly, verifying certifications, requesting samples, and seeking professional consultation. The risk of relying on any information in this guide is borne solely by the reader.
Strategic Sourcing Conclusion and Outlook for gasket material
What Are the Key Takeaways for B2B Buyers in Gasket Material Sourcing?
In conclusion, strategic sourcing of gasket materials is essential for international B2B buyers looking to optimize their supply chains and ensure product reliability. Key takeaways include the importance of evaluating material specifications, such as temperature resistance and chemical compatibility, to meet specific operational demands. Buyers should also consider the total cost of ownership, which encompasses not only the purchase price but also long-term performance and maintenance costs.
How Can Buyers Leverage Strategic Sourcing for Competitive Advantage?
By adopting a proactive approach to sourcing, companies can forge strong relationships with suppliers, enabling them to negotiate better terms and gain access to the latest innovations in gasket materials. This is particularly crucial for buyers in regions like Africa, South America, the Middle East, and Europe, where market conditions can vary significantly.
What Is the Future Outlook for Gasket Materials in Global Markets?
Looking ahead, the global demand for high-performance gasket materials is expected to rise, driven by advancements in manufacturing and increasing regulatory standards. B2B buyers should remain vigilant and adaptable, leveraging data analytics and market insights to anticipate trends and make informed sourcing decisions. Engage with suppliers who prioritize sustainability and quality, as these factors will increasingly influence market dynamics. Embrace the opportunity to enhance your sourcing strategy today for a more resilient tomorrow.