Unlock Cost Savings: The Ultimate Powdered Metal Guide (2025)
Introduction: Navigating the Global Market for powdered metal
Navigating the complexities of the global market for powdered metal can be a daunting task for international B2B buyers. With a myriad of options available, sourcing high-quality powdered metal components that meet specific application requirements poses significant challenges. This guide serves as a comprehensive resource for understanding the nuances of powdered metal manufacturing, including various types of metals, their applications, and the essential steps for supplier vetting.
Key topics covered in this guide include the intricacies of the powdered metallurgy process, the advantages of using powdered metals over traditional manufacturing methods, and how to assess costs effectively. Additionally, it delves into the environmental benefits of powdered metal production, making it an attractive option for sustainability-conscious businesses across Africa, South America, the Middle East, and Europe, including emerging markets like Nigeria and Thailand.
By equipping B2B buyers with actionable insights and best practices, this guide empowers informed purchasing decisions. Whether you are looking for tailored solutions for complex geometries or seeking cost-effective alternatives to traditional machining, understanding the powdered metal landscape is crucial for gaining a competitive edge in your industry. With this knowledge, you can streamline your sourcing process and enhance the quality of your products, ultimately driving your business’s success in the global market.
Understanding powdered metal Types and Variations
Type Name | Key Distinguishing Features | Primary B2B Applications | Brief Pros & Cons for Buyers |
---|---|---|---|
Stainless Steel Powder | Excellent corrosion resistance, high strength | Automotive, Aerospace, Medical Devices | Pros: Durable, versatile; Cons: Higher cost than ferrous powders. |
Iron Powder | Cost-effective, good machinability | Construction, Tooling, Automotive | Pros: Economical; Cons: Prone to corrosion without coatings. |
Copper Powder | High thermal and electrical conductivity | Electrical components, Heat exchangers | Pros: Excellent conductivity; Cons: Expensive, less strength than steel. |
Bronze Powder | Good corrosion resistance, high wear resistance | Marine applications, Bearings, Gears | Pros: Durable and resistant to wear; Cons: Can be costly. |
Soft Magnetic Powder | Tailored magnetic properties, suitable for high-frequency applications | Transformers, Electric Motors | Pros: Customizable magnetic properties; Cons: Limited to specific applications. |
What Are the Characteristics of Stainless Steel Powder?
Stainless steel powder is renowned for its exceptional corrosion resistance and mechanical strength, making it ideal for critical applications in industries such as automotive, aerospace, and medical devices. Its ability to maintain structural integrity under harsh conditions adds to its appeal. When considering purchasing stainless steel powder, buyers should evaluate the specific grade required for their application, as the material properties can vary significantly between different stainless steel alloys.
Why Choose Iron Powder for Cost-Effective Solutions?
Iron powder is a popular choice in various industries due to its cost-effectiveness and good machinability. It is widely used in construction, tooling, and automotive applications. Buyers should consider the need for additional surface treatments to prevent corrosion, as untreated iron can rust easily. The balance between cost and performance makes iron powder an attractive option for high-volume production runs where budget constraints are a priority.
How Does Copper Powder Enhance Electrical Applications?
Copper powder stands out for its high thermal and electrical conductivity, making it particularly beneficial for electrical components and heat exchangers. Its applications span from electrical connectors to advanced thermal management systems. Buyers should weigh the higher cost of copper powder against its superior performance in electrical applications, ensuring that the specific conductivity requirements of their projects justify the investment.
What Advantages Does Bronze Powder Offer in Marine Applications?
Bronze powder is characterized by its good corrosion resistance and high wear resistance, making it suitable for marine applications, bearings, and gears. Its durability under challenging environmental conditions is a significant benefit for industries that require reliability. When purchasing bronze powder, buyers should consider its cost compared to other materials, as well as the specific properties needed to meet application demands.
Why Is Soft Magnetic Powder Important for Electrical Components?
Soft magnetic powder is specifically designed to provide tailored magnetic properties, making it suitable for high-frequency applications such as transformers and electric motors. This type of powder allows manufacturers to optimize performance in critical electrical components. Buyers should assess the specific magnetic characteristics required for their applications, as well as the potential trade-offs in terms of material costs and performance capabilities.
Key Industrial Applications of powdered metal
Industry/Sector | Specific Application of Powdered Metal | Value/Benefit for the Business | Key Sourcing Considerations for this Application |
---|---|---|---|
Automotive | Engine Components (e.g., gears, bearings) | Enhanced durability and performance under high stress | Availability of high-quality alloys; compliance with industry standards |
Aerospace | Structural Components (e.g., brackets, frames) | Weight reduction without compromising strength | Certification for aerospace-grade materials; reliable supply chain |
Medical Devices | Surgical Instruments and Implants | High precision and biocompatibility | Regulatory compliance; customization capabilities for specific applications |
Electronics | Connectors and Switches | Improved electrical conductivity and reduced size | Material compatibility with electronic components; high-volume production capabilities |
Industrial Equipment | Tools and Machinery Parts | Extended tool life and reduced maintenance costs | Availability of specific powder types; ability to handle large production runs |
How is Powdered Metal Used in Automotive Applications?
In the automotive sector, powdered metal is widely used for manufacturing engine components such as gears and bearings. These parts benefit from the high strength and durability of powdered metal, which can withstand the rigorous demands of engine operations. For international buyers, particularly those in Africa and South America, sourcing high-quality alloys that meet automotive standards is critical. Buyers must ensure that their suppliers can provide materials that offer both performance and cost-effectiveness.
What are the Aerospace Applications of Powdered Metal?
Aerospace applications leverage powdered metal for structural components like brackets and frames. The ability to produce lightweight yet strong parts is essential for improving fuel efficiency and overall aircraft performance. International B2B buyers in the aerospace sector must prioritize suppliers that are certified for aerospace-grade materials, ensuring compliance with stringent safety and quality regulations. Additionally, the reliability of the supply chain is crucial due to the high costs associated with aircraft components.
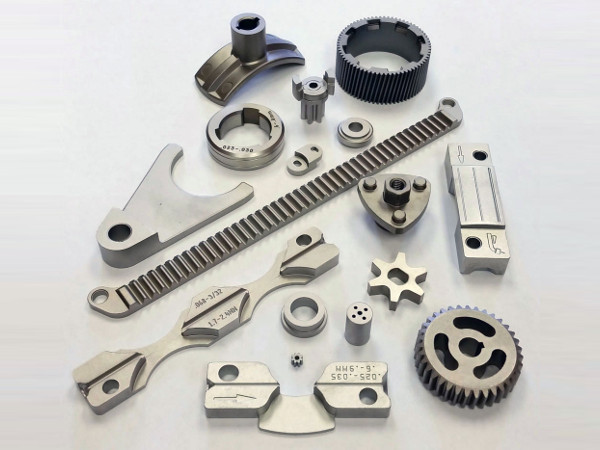
A stock image related to powdered metal.
How is Powdered Metal Beneficial in Medical Device Manufacturing?
Powdered metal plays a significant role in the production of surgical instruments and implants, where precision and biocompatibility are paramount. The customization capabilities of powdered metal allow for the creation of complex geometries tailored to specific medical applications. For buyers in the Middle East and Europe, it’s essential to partner with suppliers who understand the regulatory landscape and can provide materials that meet medical standards, ensuring safety and efficacy in their applications.
What are the Electronics Sector Applications of Powdered Metal?
In the electronics industry, powdered metal is utilized in the production of connectors and switches, where improved electrical conductivity and reduced size are critical. The net-shape manufacturing process allows for the creation of intricate designs that traditional methods may not achieve. Buyers from Europe and Africa should focus on suppliers who can offer materials compatible with electronic components while maintaining high-volume production capabilities to meet market demands.
How is Powdered Metal Applied in Industrial Equipment?
In industrial equipment, powdered metal is used to manufacture tools and machinery parts that require extended tool life and reduced maintenance costs. The unique properties of powdered metal contribute to the durability and performance of these components in demanding environments. For B2B buyers in South America and Africa, sourcing specific powder types that align with their operational needs is vital, as is the ability to handle large production runs efficiently.
3 Common User Pain Points for ‘powdered metal’ & Their Solutions
Scenario 1: Difficulty Achieving Desired Material Properties
The Problem:
Many B2B buyers face challenges when it comes to selecting powdered metal materials that meet specific mechanical properties for their applications. For instance, a manufacturer in Nigeria might require high corrosion resistance for components used in coastal environments, but struggles to find the right alloy blend that provides both strength and durability. This difficulty can lead to costly production delays and increased scrap rates if the wrong material is chosen.
The Solution:
To address this challenge, buyers should conduct thorough material property assessments before sourcing powdered metals. Engage with suppliers who offer customizable solutions and can provide detailed material property data, such as tensile strength, ductility, and corrosion resistance. It’s beneficial to utilize simulation software to model how different powder blends will perform in actual applications. Additionally, consider small-scale trials with different materials to evaluate performance before committing to large orders. This proactive approach can help ensure that the selected powdered metal meets all necessary specifications, reducing the risk of production issues.
Scenario 2: Inconsistent Quality Across Production Batches
The Problem:
Another common pain point for international B2B buyers is the inconsistency in the quality of powdered metal parts across different production batches. For example, a buyer in Brazil might order a specific component, but due to variations in powder quality or sintering conditions, the parts produced in different batches may not meet the required tolerances or surface finishes. This inconsistency can lead to increased rework costs and impact the overall quality of the end product.
The Solution:
To mitigate quality inconsistencies, it’s crucial to establish robust quality assurance protocols with your suppliers. Buyers should request detailed documentation of the manufacturing process, including powder production methods, compaction pressures, and sintering temperatures. Additionally, implementing strict incoming inspection procedures for raw materials can help ensure that only high-quality powders are used. Collaborating with suppliers to develop standardized operating procedures can further enhance consistency. Periodic audits of the supplier’s processes can also help maintain quality control across production batches, ensuring that every part meets the specified requirements.
Scenario 3: Understanding the Cost Implications of Powdered Metal Manufacturing
The Problem:
B2B buyers often find themselves grappling with the perceived high costs of powdered metal manufacturing compared to traditional methods. A buyer from the Middle East, for instance, may hesitate to switch to powdered metal due to initial investment concerns, fearing that the long-term savings will not justify the upfront costs. This hesitation can prevent them from capitalizing on the unique benefits of powdered metal parts, such as reduced waste and greater design flexibility.
The Solution:
To better understand the cost implications, buyers should perform a comprehensive cost-benefit analysis that considers both short-term and long-term factors. Begin by evaluating the total cost of ownership, which includes not only material costs but also labor, energy consumption, and potential scrap rates. Engaging with suppliers to obtain detailed quotes that break down all costs can provide clearer insights. Additionally, explore case studies or testimonials from other companies that have successfully transitioned to powdered metal, highlighting the long-term savings achieved. By focusing on the overall efficiency and potential cost savings over time, buyers can make informed decisions that align with their financial objectives while leveraging the advantages of powdered metal technology.
Strategic Material Selection Guide for powdered metal
What Are the Most Common Materials Used in Powdered Metal Manufacturing?
When selecting materials for powdered metal components, it is crucial for international B2B buyers to understand the properties, advantages, and limitations of various metal powders. Here, we analyze four common materials: Iron, Stainless Steel, Bronze, and Copper. Each material has unique characteristics that influence product performance, manufacturing complexity, and cost, making them suitable for different applications.
How Does Iron Powder Perform in Powdered Metal Applications?
Key Properties: Iron powder is known for its excellent magnetic properties and high tensile strength. It can withstand moderate temperatures and pressures, making it suitable for various mechanical applications.
Pros & Cons: Iron is relatively inexpensive and widely available, which reduces costs for manufacturers. However, it is prone to rust and corrosion if not treated or alloyed properly, which can limit its suitability for outdoor or humid environments.
Impact on Application: Iron powder is often used in automotive parts and magnetic components. Its compatibility with various lubricants and coatings can enhance its performance in specific applications.
Considerations for International Buyers: Buyers should be aware of compliance with standards such as ASTM A532 for wear-resistant cast iron. In regions like Africa and South America, the availability of high-quality iron powder can vary, impacting sourcing decisions.
What Are the Advantages of Using Stainless Steel Powder?
Key Properties: Stainless steel powder is renowned for its exceptional corrosion resistance and high-temperature performance. It maintains strength and durability even in harsh environments.
Pros & Cons: The primary advantage of stainless steel is its resistance to oxidation and corrosion, making it ideal for applications in the food and medical industries. However, it is more expensive than other metals and can complicate the manufacturing process due to its hardness.
Impact on Application: Stainless steel components are commonly used in applications requiring hygiene and durability, such as medical devices and food processing equipment.
Considerations for International Buyers: Buyers must consider compliance with standards such as ASTM A276 for stainless steel. In Europe, there is a strong preference for materials that meet stringent safety and environmental regulations.
Why Choose Bronze Powder for Your Powdered Metal Needs?
Key Properties: Bronze powder is characterized by its excellent wear resistance and low friction properties. It can operate effectively under high loads and offers good corrosion resistance.
Pros & Cons: Bronze is often used in applications requiring low friction, such as bearings and bushings. Its downside is that it can be more expensive than iron and may require additional machining to achieve desired tolerances.
Impact on Application: Bronze is particularly effective in marine applications due to its resistance to seawater corrosion, making it a preferred choice for components in boats and ships.
Considerations for International Buyers: Buyers should look for compliance with JIS standards in Japan or DIN standards in Europe, as these can affect the acceptance of bronze components in various markets.
What Are the Key Benefits of Copper Powder in Powdered Metal?
Key Properties: Copper powder boasts excellent thermal and electrical conductivity, making it ideal for electrical applications. It also has good corrosion resistance, particularly in non-oxidizing environments.
Pros & Cons: The main advantage of copper is its conductivity, which is essential for electrical components. However, it is relatively expensive and can be prone to oxidation, which may necessitate protective coatings.
Impact on Application: Copper powder is commonly used in electrical contacts, connectors, and other electronic components where conductivity is critical.
Considerations for International Buyers: Compliance with standards such as ASTM B193 for copper wire and other electrical components is essential. Buyers in regions like the Middle East should also consider local sourcing capabilities and market preferences.
Summary Table of Material Selection for Powdered Metal
Material | Typical Use Case for Powdered Metal | Key Advantage | Key Disadvantage/Limitation | Relative Cost (Low/Med/High) |
---|---|---|---|---|
Iron | Automotive parts, magnetic components | Cost-effective and widely available | Prone to rust and corrosion | Low |
Stainless Steel | Medical devices, food processing | Exceptional corrosion resistance | Higher cost and manufacturing complexity | High |
Bronze | Bearings, marine applications | Excellent wear resistance | More expensive and requires machining | Medium |
Copper | Electrical contacts, connectors | Excellent thermal and electrical conductivity | Prone to oxidation and relatively expensive | High |
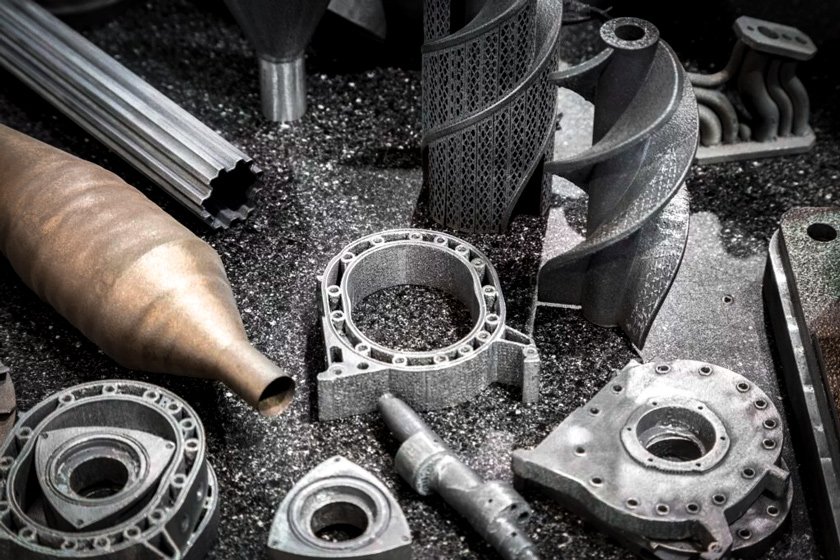
A stock image related to powdered metal.
This strategic material selection guide provides valuable insights for B2B buyers in diverse regions, allowing for informed decisions based on application needs, material properties, and compliance requirements.
In-depth Look: Manufacturing Processes and Quality Assurance for powdered metal
What Are the Key Manufacturing Processes for Powdered Metal?
Understanding the manufacturing processes of powdered metal is essential for international B2B buyers seeking high-quality components. The process involves several key stages, including material preparation, forming, assembly, and finishing. Each stage plays a critical role in determining the final product’s quality and performance.
How Is Material Prepared for Powdered Metal Production?
The first step in powdered metal manufacturing is material preparation, which involves producing metal powders from various sources. The primary techniques include:
-
Atomization: This method involves melting metal and then disintegrating it into fine droplets using high-energy jets of gas or liquid. This allows for precise control over the powder’s particle size and morphology.
-
Mechanical Alloying: This technique combines different metal powders using mechanical forces, resulting in a homogeneous mixture suitable for specific applications.
-
Chemical Reduction: Metals can be extracted from ores through chemical processes, yielding powders that can be blended with other materials.
Once the powder is produced, it may be blended with lubricants and alloying agents to enhance its properties, ensuring a uniform mix that meets the desired specifications.
What Are the Forming Techniques Used in Powdered Metal Manufacturing?
The forming process is crucial for achieving the desired shape and density of the powdered metal components. Key techniques include:
-
Compaction: The prepared metal powder is placed into a die and compacted under high pressure. This creates a “green” part that resembles the final product but requires further processing to achieve full strength.
-
Sintering: The compacted parts are then heated in a controlled atmosphere furnace to bond the particles together without melting them fully. The sintering temperature is critical, typically just below the melting point of the metal, to ensure optimal mechanical properties.
-
Secondary Operations: After sintering, parts may undergo various secondary operations such as machining, heat treatment, and surface finishing to enhance their performance characteristics.
What Quality Assurance Measures Are Essential for Powdered Metal Components?
Quality assurance (QA) is a vital aspect of the powdered metal manufacturing process, ensuring that the final products meet international standards and customer expectations. B2B buyers should be aware of the following QA measures:
Which International Standards Should Buyers Consider?
International standards such as ISO 9001 provide a framework for quality management systems, ensuring that manufacturers consistently meet customer and regulatory requirements. Additionally, industry-specific certifications like CE and API may be relevant depending on the application, especially for parts used in medical, automotive, or aerospace industries.
What Are the Key Quality Control Checkpoints in Powdered Metal Manufacturing?
Quality control (QC) involves several checkpoints throughout the manufacturing process to ensure that each component meets specified standards:
-
Incoming Quality Control (IQC): This stage involves inspecting raw materials and powders upon arrival to ensure they meet specified requirements.
-
In-Process Quality Control (IPQC): Continuous monitoring during the compaction and sintering processes helps identify any deviations from quality standards in real-time.
-
Final Quality Control (FQC): After the finishing processes, the final products undergo rigorous testing and inspections to confirm they meet all specifications.
What Testing Methods Are Commonly Used in Quality Control?
Various testing methods can be employed to verify the quality of powdered metal components:
-
Dimensional Inspection: Tools such as calipers and coordinate measuring machines (CMM) are used to ensure that parts meet specified tolerances.
-
Mechanical Testing: This includes tensile testing, hardness testing, and fatigue testing to evaluate the mechanical properties of the components.
-
Microstructure Analysis: Techniques such as scanning electron microscopy (SEM) can be used to assess the particle morphology and bonding quality achieved during sintering.
How Can B2B Buyers Verify Supplier Quality Assurance Practices?
B2B buyers should adopt a proactive approach to verify the quality assurance practices of their suppliers:
-
Supplier Audits: Conducting regular audits of the manufacturing facilities can provide insights into the supplier’s quality management systems and compliance with international standards.
-
Quality Reports: Requesting detailed quality reports and certifications from suppliers can help assess their commitment to quality assurance.
-
Third-Party Inspections: Engaging third-party inspectors can provide an unbiased assessment of the supplier’s processes and the quality of the finished products.
What QC Considerations Are Important for International B2B Buyers?
For international buyers, particularly those from Africa, South America, the Middle East, and Europe, several QC nuances must be considered:
-
Cultural and Regulatory Differences: Understanding regional differences in quality expectations and regulatory requirements can help buyers make informed decisions about suppliers.
-
Logistics and Supply Chain Management: Quality assurance does not end with production; ensuring that products are transported and stored correctly is vital to maintaining their integrity.
-
Local Support and Communication: Establishing clear lines of communication with suppliers can facilitate quicker resolutions to any quality issues that arise.
Conclusion: Ensuring Quality in Powdered Metal Manufacturing
Investing time in understanding the manufacturing processes and quality assurance measures for powdered metal can significantly enhance the purchasing decisions of B2B buyers. By focusing on these areas, buyers can ensure they partner with reputable suppliers, leading to successful procurement strategies and high-quality components tailored to their specific needs.
Practical Sourcing Guide: A Step-by-Step Checklist for ‘powdered metal’
To help international B2B buyers effectively procure powdered metal, this guide provides a structured checklist to streamline the sourcing process. Whether you’re from Africa, South America, the Middle East, or Europe, following these actionable steps will ensure that you select the right materials and suppliers for your specific needs.
Step 1: Define Your Technical Specifications
Understanding your requirements is crucial for sourcing powdered metal. Identify the specific types of alloys (e.g., stainless steel, brass, or copper) and mechanical properties (e.g., strength, hardness) that are essential for your application. This clarity will help you communicate effectively with suppliers and ensure they can meet your needs.
- Consider the application: Different industries may require varying specifications, so tailor your requirements accordingly.
- Document your needs: Create a detailed technical sheet to share with potential suppliers for accurate quotes.
Step 2: Research and Identify Reputable Suppliers
Finding reliable suppliers is essential for ensuring quality and consistency in your materials. Use online platforms, industry directories, and trade shows to compile a list of potential vendors.
- Check for industry certifications: Look for suppliers with certifications such as ISO 9001 to ensure quality management practices.
- Review their experience: Prioritize suppliers who have a proven track record in your specific industry or similar applications.
Step 3: Evaluate Supplier Capabilities
Assessing a supplier’s manufacturing capabilities will help you determine if they can meet your technical specifications. Request detailed information about their production processes, equipment, and material sourcing.
- Inquire about their technology: Understand the methods used for powder production and sintering, as these significantly affect the final product’s quality.
- Ask for samples: Request samples of their powdered metal to evaluate material quality and performance characteristics.
Step 4: Verify Supplier Certifications
Before making any commitments, verify that your selected suppliers hold relevant certifications that demonstrate compliance with industry standards.
- Look for environmental certifications: Since powdered metal manufacturing is recognized as a green technology, suppliers should have certifications related to sustainability.
- Request documentation: Ensure they can provide proof of their certifications and quality control measures.
Step 5: Assess Pricing and Terms
Understanding the pricing structure and payment terms is vital for budgeting your project effectively. Request quotes from multiple suppliers and compare them based on the total cost of ownership.
- Consider hidden costs: Ask about additional fees for shipping, handling, or custom orders that may affect your final costs.
- Negotiate terms: Don’t hesitate to discuss payment terms, lead times, and bulk order discounts to find the best deal.
Step 6: Evaluate Customer Support and Communication
Effective communication with your supplier can make or break your sourcing experience. Assess how responsive and helpful potential suppliers are during your initial interactions.
- Test their responsiveness: Reach out with inquiries and gauge how quickly they address your questions or concerns.
- Assess their support resources: Look for suppliers that offer technical support or consultative services to assist you in material selection and application.
Step 7: Finalize Your Order and Establish a Relationship
Once you have selected a supplier, finalize your order and establish a clear line of communication for future interactions. Building a strong relationship with your supplier can lead to better service and support.
- Set clear expectations: Define delivery timelines, quality expectations, and payment schedules in your agreement.
- Maintain open communication: Regularly check in with your supplier to discuss any changes in requirements or feedback on their products.
By following this checklist, you can navigate the complexities of sourcing powdered metal and ensure that your procurement process is efficient, cost-effective, and aligned with your business needs.
Comprehensive Cost and Pricing Analysis for powdered metal Sourcing
What Are the Key Cost Components in Powdered Metal Sourcing?
When sourcing powdered metal, understanding the cost structure is essential for international B2B buyers. The primary components of the cost include:
-
Materials: The cost of raw metal powders—like iron, copper, and alloys—can vary significantly based on market prices and availability. For buyers in Africa and South America, fluctuations in local currency can further impact material costs.
-
Labor: Labor costs encompass the wages of skilled workers involved in the manufacturing process, including those handling compaction and sintering. Regions with higher labor costs, such as parts of Europe, may see this reflected in the final pricing.
-
Manufacturing Overhead: This includes costs associated with factory maintenance, utilities, and administrative expenses. Efficient production processes in regions with advanced technology can help reduce overhead, thus affecting the overall price.
-
Tooling: Investment in specialized tooling for the production of specific parts can be substantial. Custom tooling may be necessary for unique specifications, impacting the initial setup costs.
-
Quality Control (QC): Ensuring that products meet quality standards requires rigorous testing and inspection, which can add to the overall cost. Buyers should inquire about the quality certifications held by suppliers, as these can influence pricing.
-
Logistics: Transportation and shipping costs are crucial, especially for international buyers. Factors such as distance, shipping methods, and customs duties can significantly affect the total cost.
-
Margin: Suppliers will add their profit margins to cover their expenses and risks. Understanding the market landscape can help buyers gauge a fair margin.
How Do Price Influencers Impact Powdered Metal Costs?
Several factors can influence the pricing of powdered metal components:
-
Volume/MOQ: Minimum order quantities (MOQ) can affect pricing. Higher volumes typically lead to lower per-unit costs due to economies of scale. Buyers should assess their needs carefully to optimize costs.
-
Specifications and Customization: Custom specifications can drive up costs, particularly if unique materials or complex geometries are required. Buyers need to balance between customization and cost-effectiveness.
-
Material Selection: The choice of materials directly influences cost. High-performance alloys may command a premium price, while more common materials might be more economical.
-
Quality and Certifications: Suppliers with ISO certifications or other quality assurances may charge higher prices, reflecting their commitment to quality. Buyers should weigh the benefits of higher-quality components against potential cost savings.
-
Supplier Factors: The reputation and reliability of suppliers can impact pricing. Established suppliers may charge more due to their track record, while emerging suppliers might offer competitive pricing to gain market share.
-
Incoterms: Understanding Incoterms (International Commercial Terms) is crucial for international transactions. These terms dictate responsibilities regarding shipping, insurance, and tariffs, affecting the overall cost structure.
What Tips Can Help Buyers Negotiate Better Prices for Powdered Metal?
-
Negotiate Based on Volume: Leverage bulk purchasing to negotiate better prices. Suppliers are often willing to offer discounts for larger orders.
-
Consider Total Cost of Ownership (TCO): While the upfront price is important, consider the long-term costs associated with the part’s performance, maintenance, and potential failures. A higher-quality part might save money over time.
-
Research Market Prices: Stay informed about market trends and material prices to strengthen negotiation positions. Knowledge of current prices allows buyers to challenge inflated quotes effectively.
-
Explore Multiple Suppliers: Engaging with multiple suppliers can yield competitive pricing and better terms. It also provides insight into the market landscape and potential alternatives.
-
Understand Regional Variations: For international buyers, be aware of regional pricing dynamics. Factors like local labor costs, material availability, and logistics can greatly influence pricing.
-
Review Contracts Carefully: Pay attention to the fine print in contracts, especially regarding payment terms, delivery schedules, and penalties for delays. Clarifying these details can prevent unexpected costs.
Conclusion
Understanding the comprehensive cost structure and pricing factors associated with powdered metal sourcing is crucial for international B2B buyers. By being informed and strategic, buyers can optimize their purchasing decisions, ensuring they secure high-quality components at competitive prices while maintaining a focus on total cost efficiency.
Alternatives Analysis: Comparing powdered metal With Other Solutions
Understanding Alternative Manufacturing Solutions to Powdered Metal
When evaluating manufacturing processes for metal components, international B2B buyers must consider various alternatives to powdered metal. Each method has distinct advantages and drawbacks that can significantly impact performance, cost, and suitability for specific applications. This analysis compares powdered metal with two viable alternatives: casting and machining, helping buyers make informed decisions that align with their operational needs.
Comparison Table of Manufacturing Alternatives
Comparison Aspect | Powdered Metal | Casting | Machining |
---|---|---|---|
Performance | High strength, complex geometries | Good for large parts, variable strength | Excellent precision, variable surface finish |
Cost | Cost-effective for high volumes | Lower initial costs, but higher waste | Higher labor and material costs, especially for complex shapes |
Ease of Implementation | Requires specialized equipment, but efficient for mass production | Relatively easy, requires molds | Requires skilled labor and precision tools |
Maintenance | Low, durable parts with minimal wear | Moderate, can require repairs | High, ongoing tool replacement and maintenance |
Best Use Case | High-volume production of custom parts | Large, simple shapes like engine blocks | Precision components, low-volume runs |
What Are the Advantages and Disadvantages of Casting?
Casting is a widely used manufacturing method where molten metal is poured into a mold and allowed to solidify.
Pros:
– Cost-effective for large parts: Casting can be economical for producing large components due to lower initial costs for the molds.
– Versatility in materials: It accommodates a wide range of metals and alloys, making it suitable for various applications.
Cons:
– Variable strength: The quality and strength of cast parts can vary significantly based on the cooling process and mold design, leading to potential inconsistencies.
– Waste generation: Casting often results in excess material waste, which can increase overall costs in low-volume production settings.
What Are the Benefits and Limitations of Machining?
Machining involves removing material from a solid block to achieve desired shapes and specifications, typically using tools like lathes and mills.
Pros:
– Precision: Machining offers exceptional accuracy and surface finish, making it ideal for critical applications requiring tight tolerances.
– Flexibility: It can be used for both large and small production runs, accommodating a variety of shapes and designs.
Cons:
– Higher costs: The labor-intensive nature of machining results in higher costs, particularly for complex components.
– Material waste: Machining often leads to significant waste, especially when starting from larger blocks of material, which can be a concern for budget-conscious buyers.
How Can B2B Buyers Choose the Right Manufacturing Solution?
Selecting the appropriate manufacturing method requires careful consideration of various factors including the intended application, production volume, and budget constraints. Buyers should assess the specific requirements of their projects, such as the complexity of the part, desired material properties, and long-term performance needs. Powdered metal offers a compelling option for high-volume, custom parts with tight tolerances, while casting and machining may be better suited for different scenarios. Ultimately, the choice hinges on balancing performance expectations with cost efficiency and production capabilities.
Essential Technical Properties and Trade Terminology for powdered metal
What Are the Key Technical Properties of Powdered Metal?
Understanding the technical properties of powdered metal is crucial for B2B buyers to ensure that the products meet their specific application requirements. Here are some essential properties to consider:
What is Material Grade and Why Is It Important?
Material grade refers to the classification of the metal based on its chemical composition and physical properties. For powdered metals, common grades include stainless steel, bronze, copper, and iron. Selecting the appropriate material grade is vital for ensuring that the finished component has the necessary strength, corrosion resistance, and durability for its intended application. Buyers should consider the specific conditions in which the part will operate, including temperature, pressure, and exposure to chemicals.
How Do Tolerances Affect Product Quality?
Tolerance is the permissible limit of variation in a physical dimension. In powdered metal manufacturing, tight tolerances (often ±0.001 inches) can significantly impact product performance and assembly compatibility. High precision is particularly important in industries like automotive and aerospace, where even minor deviations can lead to operational failures. Understanding tolerances helps buyers assess the quality of potential suppliers and ensure that parts will fit seamlessly into their systems.
What Are the Benefits of Density in Powdered Metal?
Density refers to the mass per unit volume of the powdered metal. Higher density often leads to improved mechanical properties, such as strength and wear resistance. This is particularly important for applications that require high-performance components, such as gears and bearings. Buyers should inquire about the density specifications of the powdered metal products to ensure they meet the demands of their specific applications.
Why is Sintering Temperature a Critical Factor?
Sintering temperature is the heat level at which the compacted powder is fused together. This temperature affects the final mechanical properties of the parts, including hardness and tensile strength. Different materials require specific sintering temperatures for optimal performance. Buyers should consider the sintering capabilities of their suppliers to ensure that they can produce parts that meet the required specifications.
How Do Secondary Operations Enhance Powdered Metal Parts?
Secondary operations refer to additional processes that enhance the properties of powdered metal parts after initial manufacturing. These can include heat treatments, machining, and surface finishing. Understanding these operations is essential for buyers looking to customize parts for specific applications, as they can significantly impact performance characteristics such as surface finish and corrosion resistance.
What Are Common Trade Terms Used in Powdered Metal Industry?
Familiarizing yourself with industry jargon can help streamline communication with suppliers and enhance procurement strategies. Here are some key terms:
What Does OEM Mean in the Context of Powdered Metal?
OEM stands for Original Equipment Manufacturer. This term refers to companies that produce parts for other companies to sell under their brand. In the powdered metal industry, understanding whether a supplier is an OEM can influence purchasing decisions, as OEMs often have established reputations for quality and reliability.
What is MOQ and Why Should Buyers Care?
MOQ, or Minimum Order Quantity, is the smallest number of units that a supplier is willing to sell. This is particularly important for B2B buyers as it can affect inventory management and cash flow. Understanding the MOQ can help buyers negotiate better terms and ensure that they are not overcommitting to a supplier.
How Do RFQs Facilitate Purchasing Decisions?
RFQ stands for Request for Quotation. This is a formal process where buyers solicit price quotes from suppliers for specific quantities of powdered metal components. Using RFQs helps buyers compare prices, lead times, and terms from multiple suppliers, enabling informed purchasing decisions.
What Are Incoterms and Their Relevance to International Trade?
Incoterms are international commercial terms that define the responsibilities of buyers and sellers in the shipping process. Understanding these terms is crucial for international B2B buyers as they clarify who bears the risk and cost at various stages of the transaction. Familiarity with Incoterms can prevent misunderstandings and ensure smoother logistics.
By grasping these essential technical properties and trade terminologies, international B2B buyers can navigate the powdered metal landscape with greater confidence and make informed purchasing decisions.
Navigating Market Dynamics and Sourcing Trends in the powdered metal Sector
What Are the Current Market Dynamics in the Powdered Metal Sector?
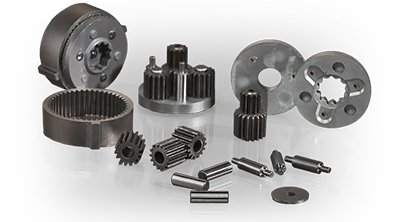
A stock image related to powdered metal.
The powdered metal (PM) sector is experiencing significant growth driven by several global factors. As industries increasingly demand lightweight and high-strength components, PM technology is rising to meet these needs. The automotive, aerospace, and medical sectors are particularly influential, pushing for more efficient manufacturing processes and innovative material solutions. Emerging trends include the adoption of advanced manufacturing technologies such as 3D printing and automation, which enhance production efficiency and customization capabilities.
International B2B buyers, especially from regions like Africa, South America, the Middle East, and Europe, should be aware of the increasing emphasis on local sourcing and short supply chains. This trend not only reduces lead times but also mitigates risks associated with global logistics disruptions. Additionally, the rise of digital platforms for sourcing and procurement is transforming how companies engage with suppliers, enabling better transparency and decision-making. Buyers should look for suppliers who leverage technology to provide real-time data and insights into inventory and delivery timelines.
How Does Sustainability Influence Sourcing in the Powdered Metal Industry?
Sustainability is a crucial consideration for B2B buyers in the powdered metal sector. The PM process is inherently eco-friendly, utilizing over 97% of raw materials and generating minimal waste. This makes it an attractive option for companies looking to reduce their environmental footprint. However, it’s essential for buyers to scrutinize their supply chains for ethical practices and sustainability certifications.
Buyers should seek suppliers who prioritize sustainable sourcing of materials, such as those utilizing recycled metal powders or adhering to strict environmental standards. Certifications like ISO 14001 can indicate a supplier’s commitment to environmental management. Ethical sourcing not only aligns with corporate social responsibility goals but also resonates with increasingly eco-conscious consumers and businesses. Companies that demonstrate transparency in their sourcing practices can gain a competitive edge in the market.
What Is the Historical Context of Powdered Metal Manufacturing?
The powdered metal industry has evolved significantly over the past century. Initially, PM was primarily used for producing simple components and was limited by technological constraints. However, advancements in metallurgy and manufacturing processes, including atomization and sintering, have expanded the capabilities of PM.
Today, the technology allows for the production of complex geometries and tailored material properties, making it viable for high-performance applications across various industries. This evolution has positioned powdered metal as a critical player in modern manufacturing, offering cost-effective and efficient alternatives to traditional methods like casting and machining. International B2B buyers can leverage this historical context to understand the reliability and potential of powdered metal components in their operations.
Frequently Asked Questions (FAQs) for B2B Buyers of powdered metal
-
How do I choose the right powdered metal supplier for my business needs?
When selecting a powdered metal supplier, consider their experience, manufacturing capabilities, and industry certifications. Look for suppliers that specialize in your specific application, whether it’s automotive, aerospace, or medical. Request samples to evaluate the quality of their products and assess their customization options. Additionally, check their sustainability practices, as environmentally friendly suppliers can reduce your company’s carbon footprint. Establishing communication regarding lead times, customer service, and support will ensure a strong partnership moving forward. -
What factors should I consider when determining the minimum order quantity (MOQ) for powdered metal?
The MOQ for powdered metal can vary based on the supplier, material type, and manufacturing process. Consider factors such as your project scope, budget, and storage capabilities. Suppliers may offer lower MOQs for standard materials but may require higher quantities for custom blends. Always discuss your needs upfront to negotiate favorable terms, and evaluate the potential for future orders to maximize cost efficiency. Understanding your production cycles will also help in determining the right MOQ for your business. -
What are the typical payment terms for international powdered metal suppliers?
Payment terms can differ significantly among international suppliers, often ranging from 30 to 90 days after invoice. Some may require a deposit upfront, especially for custom orders, while others might offer net payment options. It’s essential to clarify these terms during negotiations and consider utilizing secure payment methods such as letters of credit or escrow services to protect your investment. Understanding currency exchange rates and potential fees is also crucial for international transactions. -
How can I ensure quality assurance when sourcing powdered metal?
Quality assurance in powdered metal sourcing can be achieved by selecting suppliers with recognized certifications such as ISO 9001. Request detailed documentation of their quality control processes, including material testing and inspection procedures. Engage in regular communication with the supplier about your quality expectations and consider conducting audits or site visits if feasible. Additionally, implementing a robust incoming inspection process on your end can help maintain the integrity of the materials received. -
What customization options are available for powdered metal components?
Powdered metal allows for extensive customization, including variations in material blends, geometries, and surface finishes. Discuss your specific application requirements with potential suppliers to explore available options, such as heat treatment, coatings, or impregnation processes. Many suppliers can create custom alloys to meet unique mechanical properties or performance standards. Collaborate closely during the design phase to ensure the end product aligns with your specifications. -
What are the key logistical considerations when importing powdered metal?
When importing powdered metal, consider logistics related to shipping, customs clearance, and storage. Engage with suppliers who have experience in international shipping to streamline the process. Understand the regulations and tariffs that may apply to your specific materials in both the exporting and importing countries. Additionally, ensure that you have suitable storage facilities that comply with safety regulations, as some powdered metals may require specific handling procedures. -
How does the powdered metal manufacturing process differ from traditional methods?
Powdered metal manufacturing utilizes a unique process of compaction and sintering, allowing for the production of complex shapes with minimal waste. Unlike traditional methods such as forging or casting, PM can achieve tighter tolerances and superior surface finishes without extensive machining. This process also enables the use of a wider range of materials and allows for the creation of custom alloys tailored to specific applications, making it a versatile and cost-effective solution for high-volume production. -
What industries benefit most from using powdered metal components?
Powdered metal components are widely used across various industries, including automotive, aerospace, medical devices, and electronics. The versatility of powdered metallurgy allows for the production of high-strength parts that meet the demanding performance requirements of these sectors. Industries benefit from the cost savings, reduced material waste, and ability to create complex geometries that are difficult to achieve with traditional manufacturing methods. Understanding your industry’s specific needs can help you leverage powdered metal solutions effectively.
Important Disclaimer & Terms of Use
⚠️ Important Disclaimer
The information provided in this guide, including content regarding manufacturers, technical specifications, and market analysis, is for informational and educational purposes only. It does not constitute professional procurement advice, financial advice, or legal advice.
While we have made every effort to ensure the accuracy and timeliness of the information, we are not responsible for any errors, omissions, or outdated information. Market conditions, company details, and technical standards are subject to change.
B2B buyers must conduct their own independent and thorough due diligence before making any purchasing decisions. This includes contacting suppliers directly, verifying certifications, requesting samples, and seeking professional consultation. The risk of relying on any information in this guide is borne solely by the reader.
Strategic Sourcing Conclusion and Outlook for powdered metal
What Are the Key Takeaways for International B2B Buyers in Powdered Metal?
In summary, the powdered metal industry offers significant advantages for international B2B buyers, particularly in regions like Africa, South America, the Middle East, and Europe. The strategic sourcing of powdered metal components can lead to substantial cost savings—up to 70%—due to improved material utilization and reduced energy consumption. The ability to customize alloys and achieve complex geometries means that businesses can obtain parts tailored to their specific needs, enhancing both performance and reliability.
How Can Strategic Sourcing Enhance Your Supply Chain?
Strategic sourcing in powdered metal not only streamlines production but also ensures access to high-quality, consistent parts that can meet exacting tolerances. This is crucial for industries that rely on precision, such as automotive, aerospace, and medical devices. By establishing strong relationships with trusted suppliers, buyers can mitigate risks associated with fluctuating material costs and supply chain disruptions, particularly in emerging markets.
What Should You Consider Moving Forward?
As you look to the future, consider the growing importance of sustainability in manufacturing. The environmentally friendly nature of powdered metallurgy, which utilizes over 97% of input materials, aligns well with global trends toward greener practices. Engage with suppliers who prioritize sustainability and innovation to ensure your operations remain competitive.
In conclusion, embracing powdered metal solutions can position your business for success in a rapidly evolving marketplace. Take action now by exploring partnerships with leading manufacturers to leverage these advantages and drive your business forward.