Unlock Cost Savings: The Ultimate Urethane Molding Guide (2025)
Introduction: Navigating the Global Market for urethane molding
In today’s competitive landscape, sourcing high-quality urethane molding solutions can be a daunting task for international B2B buyers. As businesses strive to create durable and versatile products, understanding the nuances of urethane casting becomes essential. This guide is designed to help you navigate the complexities of urethane molding, covering critical aspects such as types of materials, applications, supplier vetting processes, and cost considerations.
Whether you are based in Africa, South America, the Middle East, or Europe—countries like Italy and Saudi Arabia—this comprehensive resource aims to empower you with the knowledge needed to make informed purchasing decisions. Urethane molding offers a unique balance between flexibility and production quality, making it ideal for low-volume runs and prototype development. By exploring the various options available, including the benefits of using urethane over traditional methods like injection molding, you will be equipped to select suppliers that align with your specific project requirements.
Moreover, this guide delves into the latest advancements in materials and technologies, providing insights into how to leverage these innovations for your business. Ultimately, our goal is to simplify the sourcing process, enabling you to find reliable partners and achieve your production goals with confidence.
What are the Key Benefits of Urethane Molding for B2B Buyers?
Understanding the advantages of urethane molding can help you determine its fit for your projects.
How to Identify Reputable Urethane Molding Suppliers?
Learn the best practices for vetting suppliers to ensure quality and reliability.
What Are the Cost Implications of Urethane Molding?
Explore pricing structures and factors that influence the overall cost of urethane casting.
Understanding urethane molding Types and Variations
Type Name | Key Distinguishing Features | Primary B2B Applications | Brief Pros & Cons for Buyers |
---|---|---|---|
General Purpose Urethane | Impact-resistant, versatile, ABS-like properties, Shore D 76-80 | Enclosure housings, concept models | Pros: Cost-effective, good surface finish. Cons: Limited flexibility for specialized applications. |
Rigid Clear Urethane | High transparency, matte or high-gloss finishes, Shore D 80 | Optical components, display cases, cosmetic products | Pros: Excellent aesthetics, durable. Cons: Higher production cost than opaque options. |
Rubber-Like Polyurethane | High elongation, Shore A 25-95, flexible and durable | Seals, gaskets, soft-touch components | Pros: Good flexibility and resilience. Cons: Limited hardness options for rigid applications. |
Polycarbonate-Like Urethane | High impact resistance, mimics polycarbonate properties, Shore D 82-86 | Automotive parts, protective housings | Pros: Strong and durable. Cons: Not suitable for extreme thermal environments. |
Glass-Filled Nylon-Like Urethane | High performance, USP Class VI compliant, Shore D 85 | Medical devices, high-stress mechanical components | Pros: Excellent strength and impact resistance. Cons: More expensive due to specialized materials. |
What are the characteristics of General Purpose Urethane?
General Purpose Urethane is a widely utilized type of urethane molding that offers a balance of strength and versatility. With a Shore hardness rating of 76-80, it is impact-resistant and can mimic the properties of ABS plastic, making it suitable for a variety of applications, including enclosure housings and concept models. B2B buyers should consider this option for projects requiring reliable performance without the need for specialized features, as it is often more cost-effective than other materials.
How does Rigid Clear Urethane stand out?
Rigid Clear Urethane is distinguished by its high transparency and finish options, ranging from matte to high gloss. With a Shore hardness of 80, it is ideal for applications where aesthetics are paramount, such as optical components, display cases, and cosmetic products. Buyers should weigh the benefits of its visual appeal against the potentially higher production costs compared to opaque materials, especially if the application demands high clarity.
Why choose Rubber-Like Polyurethane for your projects?
Rubber-Like Polyurethane is characterized by its high elongation and flexibility, with a Shore hardness ranging from 25 to 95. This type is particularly suited for applications requiring seals, gaskets, and soft-touch components. For B2B buyers, the key consideration is the material’s ability to provide resilience and flexibility, making it an excellent choice for products that undergo significant wear and tear.
What makes Polycarbonate-Like Urethane a preferred option?
Polycarbonate-Like Urethane offers high impact resistance and mimics the properties of polycarbonate, with a Shore hardness between 82-86. This makes it suitable for demanding applications such as automotive parts and protective housings. Buyers should note that while it provides excellent strength, it may not be the best choice for environments with extreme thermal conditions, and its performance should be evaluated based on specific project requirements.
When should you opt for Glass-Filled Nylon-Like Urethane?
Glass-Filled Nylon-Like Urethane is a high-performance option that is USP Class VI compliant, making it ideal for medical devices and high-stress mechanical components. With a Shore hardness of 85, it offers exceptional strength and impact resistance. B2B buyers should consider this material when high durability is critical, but they should also be prepared for a higher cost associated with its specialized properties.
Key Industrial Applications of urethane molding
Industry/Sector | Specific Application of Urethane Molding | Value/Benefit for the Business | Key Sourcing Considerations for this Application |
---|---|---|---|
Automotive | Production of custom gaskets and seals | Enhanced durability and resistance to wear | Ensure compatibility with automotive standards and regulations. |
Medical Devices | Manufacturing of surgical models | High precision and biocompatibility | Verify compliance with health regulations and material safety standards. |
Consumer Electronics | Creation of electronic housings | Cost-effective production with excellent finish | Look for suppliers with rapid prototyping capabilities. |
Aerospace | Production of lightweight components | Reduced weight with high strength-to-weight ratio | Source materials that meet aerospace specifications. |
Construction and Fixtures | Development of durable outdoor products | Long-lasting performance in harsh environments | Consider sourcing from local suppliers for quicker delivery times. |
How is Urethane Molding Used in the Automotive Industry?
Urethane molding plays a critical role in the automotive industry, particularly in the production of custom gaskets and seals. These components are essential for preventing leaks and ensuring the overall integrity of vehicles. Urethane’s durability and resistance to wear make it an ideal choice for automotive applications. For international buyers, especially from regions like Africa and South America, it’s crucial to source materials that comply with local automotive standards and regulations to avoid costly rework and ensure safety.
What Are the Applications of Urethane Molding in Medical Devices?
In the medical sector, urethane molding is extensively used to manufacture surgical models and prototypes. These models require high precision and biocompatibility to meet stringent health regulations. Urethane offers the flexibility and detail needed to accurately replicate complex anatomical structures. Buyers from the Middle East and Europe should prioritize suppliers that adhere to health safety standards to ensure the reliability and safety of medical devices.
How Does Urethane Molding Benefit Consumer Electronics?
Urethane molding is increasingly utilized in the consumer electronics sector for creating electronic housings. This method allows for cost-effective production while providing a high-quality finish that is visually appealing. The versatility of urethane enables the creation of parts that can withstand varying environmental conditions. For B2B buyers in Europe, particularly in Italy, it is essential to partner with suppliers who have rapid prototyping capabilities to meet the fast-paced demands of the electronics market.
In What Ways is Urethane Molding Used in Aerospace Applications?
In aerospace, urethane molding is used to produce lightweight components that are crucial for improving fuel efficiency. The strength-to-weight ratio of urethane makes it an excellent material choice for this industry. International buyers should focus on sourcing materials that meet specific aerospace specifications to ensure safety and performance. Additionally, understanding the certification process for materials can help streamline procurement.
How is Urethane Molding Applied in Construction and Outdoor Products?
Urethane molding is ideal for developing durable outdoor products, such as fixtures and protective casings. The material’s ability to withstand harsh environmental conditions ensures long-lasting performance, making it a preferred choice for construction applications. For buyers in regions with extreme weather, such as the Middle East, it’s beneficial to source from local suppliers to reduce lead times and shipping costs. Ensuring that the materials are suitable for outdoor use is crucial for maximizing the longevity of the products.
3 Common User Pain Points for ‘urethane molding’ & Their Solutions
Scenario 1: High Costs of Prototyping and Production
The Problem:
B2B buyers often face significant financial constraints when it comes to prototyping and small-batch production. Traditional methods like injection molding require high initial tooling costs and long lead times, making them unsuitable for businesses needing flexibility and speed. For companies in regions like Africa and South America, where budget limitations are common, these costs can hinder the ability to innovate or respond to market demands effectively.
The Solution:
Switching to urethane molding offers a cost-effective alternative for creating prototypes and small production runs. Urethane casting requires less investment in tooling compared to injection molding, allowing for a quicker turnaround and lower unit costs. Buyers should seek suppliers that utilize 3D-printed master patterns to minimize tooling expenses and lead times. When sourcing urethane services, inquire about their material options and capabilities to ensure they can meet specific project requirements. By leveraging urethane molding, businesses can maintain a competitive edge while managing costs effectively.
Scenario 2: Inconsistent Quality and Finish of Parts
The Problem:
In industries such as medical devices and consumer electronics, the quality and finish of produced parts are critical. Buyers often experience frustration when parts produced through urethane molding lack the desired consistency in surface finish or mechanical properties. Variability can lead to product failures, compliance issues, or increased costs due to rework or replacement.
The Solution:
To ensure consistent quality, buyers should establish clear specifications and quality standards with their urethane molding suppliers. This includes defining tolerances, surface finishes, and material properties upfront. It’s beneficial to request samples or prototypes before committing to larger orders, allowing for adjustments based on performance and aesthetics. Additionally, working with experienced suppliers who use advanced quality control methods, such as automated inspection and testing, can help ensure that the final products meet the required standards. Implementing a robust quality assurance process will mitigate risks and enhance overall product quality.
Scenario 3: Difficulty in Selecting the Right Material for Application
The Problem:
Choosing the appropriate urethane material can be daunting for buyers unfamiliar with the nuances of material properties and applications. For instance, a company producing components for harsh environments may struggle to determine which urethane formulation offers the best resistance to abrasion, chemicals, or temperature variations. Making the wrong choice can lead to product failures and increased liability.
The Solution:
To navigate material selection effectively, B2B buyers should engage in thorough research and consultation with their suppliers. It’s essential to clearly understand the specific performance requirements of the application, such as hardness, flexibility, and environmental resistance. Suppliers should provide comprehensive material data sheets that outline the properties of different urethane formulations, enabling informed decision-making. Collaborating with suppliers who offer material testing and validation services can also ensure that the chosen material meets the necessary performance criteria. By leveraging expert insights and detailed specifications, buyers can select the optimal material for their urethane molding needs, reducing the risk of product failure.
Strategic Material Selection Guide for urethane molding
When selecting materials for urethane molding, international B2B buyers must consider a variety of factors that impact performance, cost, and compliance with regional standards. Here, we analyze four common urethane materials, focusing on their properties, advantages and disadvantages, and specific considerations for buyers from Africa, South America, the Middle East, and Europe.
What Are the Key Properties of General Purpose Urethane?
General Purpose Urethane is a versatile material characterized by its Shore hardness of 76-80D, making it impact-resistant and suitable for a range of applications. It can mimic the properties of ABS plastic, providing a balance between rigidity and flexibility. This material typically performs well under moderate temperatures and is resistant to abrasion, making it suitable for products that require durability.
Pros & Cons: The primary advantage of general-purpose urethane is its cost-effectiveness and ease of manufacturing, allowing for quick turnaround times. However, its limitations include lower temperature resistance compared to specialized materials, which may restrict its use in high-heat applications.
Impact on Application: This material is ideal for prototypes and low-volume production runs, particularly in industries like consumer goods and automotive. However, it may not be suitable for applications requiring high chemical resistance.
Considerations for International Buyers: Buyers should ensure that the material complies with local standards such as ASTM or DIN, especially in industries like automotive and electronics where safety regulations are stringent.
How Does Rigid Clear Urethane Perform in Urethane Molding?
Rigid Clear Urethane features a Shore hardness of 80D and offers excellent optical clarity, making it suitable for applications where aesthetics are essential. This material is also resistant to UV light and can withstand moderate temperatures.
Pros & Cons: One of the key advantages is its ability to provide a high-gloss finish, making it ideal for cosmetic applications. However, it can be more expensive than general-purpose urethane and may require additional finishing processes to achieve the desired clarity.
Impact on Application: This material is often used in the production of clear housings, lenses, and display components. Its UV resistance makes it suitable for outdoor applications, but it may not perform well in environments with extreme temperatures.
Considerations for International Buyers: Buyers should verify that the material meets local optical clarity standards and consider the implications of shipping costs for high-value materials.
What Are the Benefits of Using Flame Retardant Urethane?
Flame Retardant Urethane has a Shore hardness of 78-82D and is UL Listed, making it suitable for applications where fire safety is a concern. This material is designed to withstand high temperatures and has excellent mechanical properties.
Pros & Cons: The primary advantage is its compliance with safety standards, which can be crucial for industries such as construction and transportation. However, flame retardant urethane can be more costly and may have a more complex manufacturing process due to its specialized properties.
Impact on Application: This material is ideal for electronic housings, automotive parts, and other applications where fire resistance is critical. Its performance in high-temperature environments makes it a preferred choice for safety-critical components.
Considerations for International Buyers: Buyers should ensure compliance with local fire safety regulations and standards, which may vary significantly between regions, especially in Europe and the Middle East.
How Does Rubber-Like Polyurethane Compare in Urethane Molding?
Rubber-Like Polyurethane features a Shore hardness range of 25-95A, providing high flexibility and elongation properties. This material is particularly useful in applications requiring soft-touch surfaces and high resilience.
Pros & Cons: The main advantage is its versatility in applications such as seals, gaskets, and soft-touch products. However, its softness may limit its use in load-bearing applications, and it can be more expensive than harder urethanes.
Impact on Application: This material is ideal for applications in the medical device industry, automotive interiors, and consumer products where a soft feel is desired. Its flexibility allows for better performance in dynamic applications.
Considerations for International Buyers: Buyers should consider the availability of this material in their region and ensure compliance with medical and safety standards, particularly in the healthcare sector.
Summary Table of Urethane Materials
Material | Typical Use Case for urethane molding | Key Advantage | Key Disadvantage/Limitation | Relative Cost (Low/Med/High) |
---|---|---|---|---|
General Purpose Urethane | Prototypes, consumer goods | Cost-effective, easy to manufacture | Limited temperature resistance | Low |
Rigid Clear Urethane | Clear housings, lenses | High optical clarity | Higher cost, requires finishing | Medium |
Flame Retardant Urethane | Electronic housings, automotive parts | Compliance with fire safety standards | Complex manufacturing, higher cost | High |
Rubber-Like Polyurethane | Seals, gaskets, soft-touch products | High flexibility and resilience | Limited load-bearing capacity | Medium |
This strategic material selection guide aims to equip international B2B buyers with the insights necessary to make informed decisions in urethane molding, ensuring compliance with local standards and optimizing product performance.
In-depth Look: Manufacturing Processes and Quality Assurance for urethane molding
What Are the Main Stages of the Urethane Molding Manufacturing Process?
The manufacturing process for urethane molding consists of several critical stages that ensure the production of high-quality components. Understanding these stages is vital for B2B buyers to effectively engage with suppliers and ensure the final products meet their specifications.
1. Material Preparation
The first step in the urethane molding process is material preparation. This involves selecting the appropriate polyurethane resin based on the desired properties, such as hardness, durability, and flexibility. Manufacturers often categorize these materials by their Shore hardness ratings, which can range from soft elastomers to rigid plastics. This selection is crucial as it directly impacts the performance of the final product.
Once the materials are chosen, they undergo thorough mixing, where the resin is combined with hardeners and any additives required for specific applications, such as colorants or fillers. Accurate measurement and mixing are essential to achieve the desired chemical reaction and material properties.
2. Forming
After the materials are prepared, the next stage is forming. This typically involves creating molds that will shape the urethane into the desired form. Modern techniques often leverage 3D printing to produce master patterns, which can then be used to create silicone or urethane molds. This method allows for faster turnaround times and lower tooling costs compared to traditional methods, making it an attractive option for low to medium volume production.
The casting process itself involves pouring the mixed urethane into the mold and allowing it to cure. This curing process can take from a few hours to several days, depending on the material and environmental conditions. Manufacturers must closely monitor temperature and humidity levels during this stage to ensure consistent curing and prevent defects.
3. Assembly
In cases where the final product consists of multiple components, assembly becomes a necessary stage. This could involve adhering different urethane parts together or integrating other materials, such as metal inserts or electronic components. The assembly process often requires precision to maintain the quality and integrity of the final product, particularly for applications in industries like aerospace or medical devices.
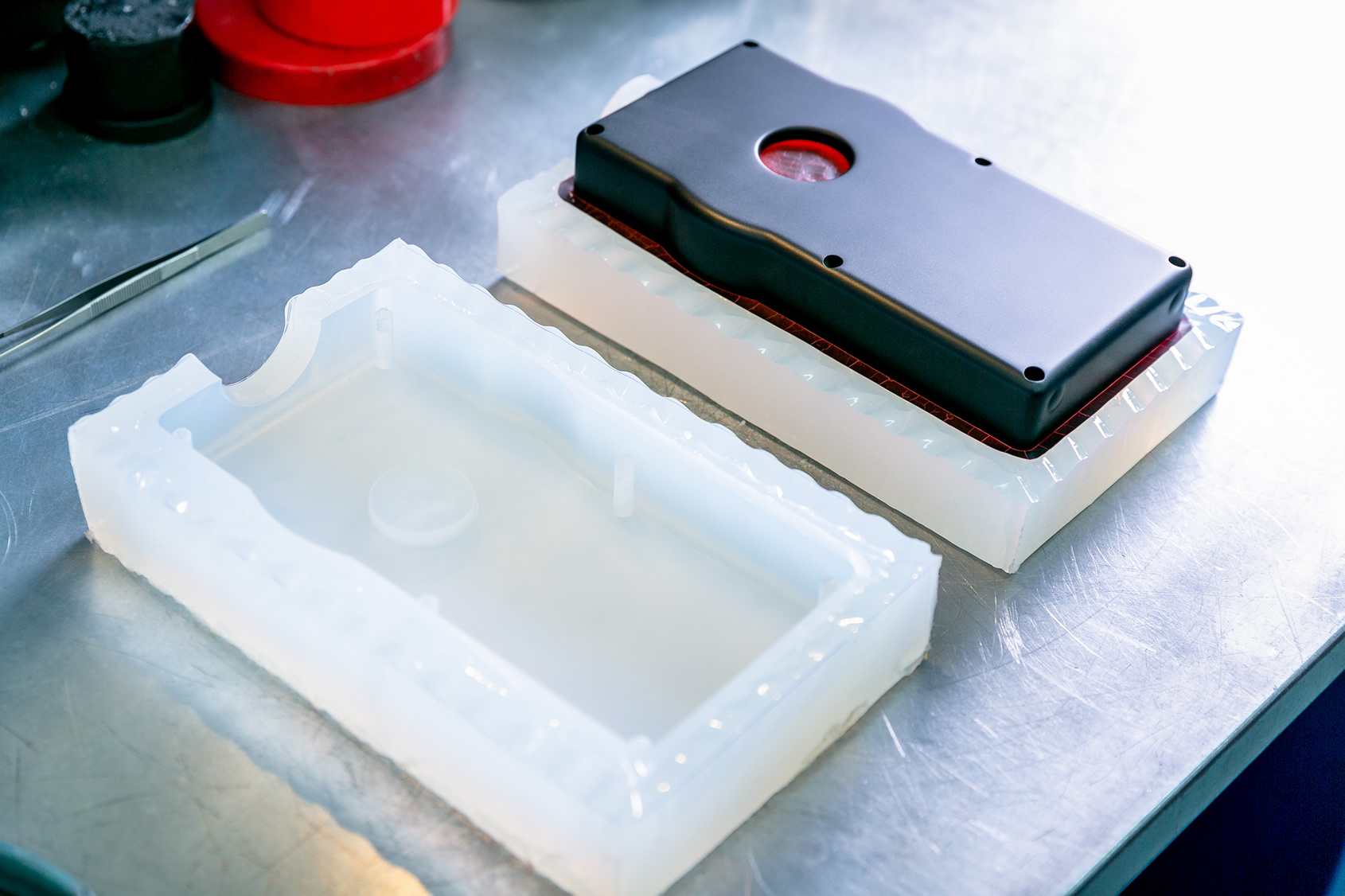
A stock image related to urethane molding.
4. Finishing
The final stage in the manufacturing process is finishing. This may include surface treatments, painting, or applying textures to enhance the product’s aesthetic and functional qualities. Various finishes, such as matte, semi-gloss, or high-gloss, can be applied based on the client’s specifications. Proper finishing is essential for achieving the desired look and feel, as well as for functional requirements, such as reducing friction or enhancing grip.
How Is Quality Assurance Implemented in Urethane Molding?
Quality assurance (QA) is a critical aspect of urethane molding that ensures products meet industry standards and customer expectations. For international B2B buyers, understanding the QA processes can significantly influence procurement decisions.
Relevant International Standards
Adhering to recognized international standards is essential for maintaining quality in manufacturing processes. ISO 9001 is one of the most widely recognized quality management standards, focusing on ensuring consistent quality and continuous improvement. Additionally, industry-specific certifications may be required, such as CE marking for products sold in Europe or API standards for oil and gas equipment. Buyers should inquire about these certifications to ensure compliance with regulatory requirements.
What Are the Key Quality Control Checkpoints?
Quality control (QC) in urethane molding involves several checkpoints throughout the manufacturing process:
-
Incoming Quality Control (IQC): This initial checkpoint involves inspecting raw materials before they are used in production. Suppliers must provide material certifications and test reports to verify the quality of the urethane materials.
-
In-Process Quality Control (IPQC): During the manufacturing stages, continuous monitoring is conducted to ensure that processes align with established standards. This includes checking the mixing ratios and monitoring environmental conditions during curing.
-
Final Quality Control (FQC): After the products are completed, they undergo final inspections and testing. This may involve dimensional checks, visual inspections, and functional testing to ensure the parts perform as intended.
What Testing Methods Are Commonly Used for Urethane Molded Parts?
Various testing methods are employed to verify the quality of urethane molded parts:
-
Mechanical Testing: This includes tensile strength, impact resistance, and hardness tests to ensure that the material properties meet specifications.
-
Thermal Testing: Evaluating the thermal stability and resistance of the urethane parts is crucial, especially for applications in high-temperature environments.
-
Chemical Resistance Testing: This is particularly important for parts exposed to harsh chemicals or solvents, ensuring that the materials will not degrade under operational conditions.
-
Visual Inspection: Regular visual checks can help identify surface defects, color inconsistencies, or other anomalies that may affect product quality.
How Can B2B Buyers Verify Supplier Quality Control?
For international B2B buyers, verifying a supplier’s quality control measures is vital to ensuring product reliability. Here are several strategies to consider:
-
Supplier Audits: Conducting on-site audits allows buyers to assess the manufacturing processes, quality management systems, and compliance with international standards. This firsthand evaluation can provide insights into the supplier’s commitment to quality.
-
Requesting Quality Reports: Buyers should request documentation of quality control procedures, including IQC, IPQC, and FQC reports. These documents should detail the results of tests conducted and any corrective actions taken.
-
Third-Party Inspections: Engaging third-party inspectors can provide an impartial assessment of the supplier’s quality control practices. These inspectors can perform audits and testing to ensure that the products meet the required standards.
What Are the QC and Certification Nuances for International B2B Buyers?
Navigating quality control and certification nuances can be challenging for B2B buyers, especially when dealing with suppliers from different regions. Here are some considerations:
-
Regional Standards: Buyers must be aware of regional regulations and standards that may differ from international norms. For example, CE marking is essential for products sold in Europe, while other regions may have different certification requirements.
-
Cultural Differences: Understanding the cultural context of suppliers in regions such as Africa, South America, and the Middle East can help buyers build stronger partnerships. This includes recognizing varying approaches to quality management and compliance.
-
Language Barriers: Clear communication is essential for ensuring quality. Buyers should ensure that technical specifications and quality requirements are well-understood by the supplier, potentially employing bilingual staff or translation services if necessary.
By comprehensively understanding the manufacturing processes and quality assurance protocols in urethane molding, international B2B buyers can make informed decisions that enhance their supply chain effectiveness and product quality.
Practical Sourcing Guide: A Step-by-Step Checklist for ‘urethane molding’
To effectively navigate the procurement of urethane molding services, international B2B buyers must follow a systematic approach. This checklist is designed to streamline the sourcing process, ensuring that your final selection aligns with your project requirements and business goals.
Step 1: Define Your Technical Specifications
Establishing clear technical specifications is crucial for successful sourcing. Identify the characteristics your urethane parts must possess, such as hardness, flexibility, and thermal resistance. This clarity will help you communicate effectively with potential suppliers and ensure that they can meet your specific needs.
- Consider end-use requirements: Different applications may require varying levels of durability and resistance to chemicals or heat.
- Specify dimensions and tolerances: Accurate measurements will help avoid costly errors during production.
Step 2: Research Potential Suppliers
Conduct thorough research to identify suppliers with a strong reputation in the urethane molding sector. Focus on companies that have experience in your industry and can demonstrate expertise in producing parts similar to your requirements.
- Look for industry certifications: Certifications like ISO 9001 can indicate a commitment to quality.
- Read customer reviews: Testimonials from past clients can provide insight into the supplier’s reliability and service quality.
Step 3: Evaluate Supplier Capabilities
Assess the capabilities of each supplier to ensure they can deliver on your specifications. This evaluation should include an examination of their production processes, available materials, and technology used in urethane molding.
- Ask about tooling options: Inquire whether they utilize soft tooling or hard tooling, as this can impact lead times and costs.
- Check material variety: A diverse range of urethane materials can provide flexibility in achieving desired properties.
Step 4: Request Samples and Prototypes
Before finalizing your supplier, request samples or prototypes of their work. This step allows you to evaluate the quality of the parts they produce and ensure they align with your expectations.
- Assess surface finish and detail: High-quality urethane parts should exhibit excellent surface finish and detail.
- Test performance: If possible, conduct performance tests to verify that the samples meet your functional requirements.
Step 5: Verify Compliance with Regulations
Ensure that your potential suppliers comply with relevant regulations and standards, especially if you are in industries like medical or food production. Compliance is critical for avoiding legal issues and ensuring product safety.
- Check for material safety data sheets (MSDS): These documents provide information on the materials used and their safety.
- Inquire about testing protocols: Understanding the testing procedures can give you confidence in the supplier’s quality assurance practices.
Step 6: Discuss Pricing and Lead Times
Openly discuss pricing structures and lead times with your shortlisted suppliers. Understanding the cost implications and timelines involved will help you make an informed decision.
- Request detailed quotes: Ensure that quotes include all potential costs, including shipping and tariffs.
- Negotiate terms: Don’t hesitate to negotiate pricing or lead times based on your project requirements.
Step 7: Establish Clear Communication Channels
Finally, establish clear communication channels with your selected supplier. Effective communication is key to ensuring that any issues are addressed promptly and that the project stays on track.
- Set regular check-ins: Regular updates can help keep the project aligned with expectations.
- Utilize project management tools: Consider using tools that facilitate collaboration and transparency throughout the production process.
By following this comprehensive checklist, international B2B buyers can effectively source urethane molding services that meet their operational needs while minimizing risks and ensuring quality.
Comprehensive Cost and Pricing Analysis for urethane molding Sourcing
What Are the Key Cost Components in Urethane Molding?
When sourcing urethane molding services, understanding the cost structure is crucial for B2B buyers. The primary cost components include:
-
Materials: The choice of polyurethane or silicone significantly impacts costs. Premium materials with specialized properties, such as flame retardance or high elasticity, can increase the overall expense. Buyers should evaluate material requirements based on the application to avoid overspending.
-
Labor: Skilled labor is necessary for both the molding process and quality control (QC). Labor costs can vary by region, so international buyers should consider sourcing from areas with lower labor rates while ensuring the required skill level is met.
-
Manufacturing Overhead: This includes expenses related to facility maintenance, utilities, and equipment depreciation. Efficient production processes can help minimize these costs, making it important to choose suppliers with modern facilities and technology.
-
Tooling: Initial tooling costs can be significant, especially for custom designs. However, urethane molding typically requires less investment in tooling compared to injection molding, making it an attractive option for lower volume production runs.
-
Quality Control: Ensuring the final product meets specified tolerances and quality standards incurs costs. Certifications, especially for industries like medical or automotive, may require additional testing and documentation, impacting the overall price.
-
Logistics: Shipping costs can vary widely based on destination, volume, and chosen Incoterms. Buyers should factor in import duties and taxes, especially when sourcing from overseas suppliers.
-
Margin: Suppliers will include a profit margin, which can be influenced by demand, competition, and perceived value of the service provided.
How Do Price Influencers Affect Urethane Molding Costs?
Several factors can influence pricing in urethane molding, including:
-
Volume/MOQ: Minimum order quantities (MOQs) often dictate pricing. Larger orders typically result in lower per-unit costs, making it beneficial for buyers to consolidate orders when possible.
-
Specifications/Customization: Custom designs and specific performance requirements can lead to increased costs. Buyers should assess whether standard options can meet their needs to optimize pricing.
-
Material Choices: The selection of materials can substantially affect costs. For example, high-performance or specialty materials will drive up expenses compared to standard options.
-
Quality and Certifications: Products requiring compliance with industry standards will incur additional costs for testing and certification. Buyers should clarify these requirements upfront to avoid unexpected expenses.
-
Supplier Factors: The reputation and reliability of the supplier can influence pricing. Established suppliers may charge a premium for their expertise, while new entrants may offer lower prices to gain market share.
-
Incoterms: Understanding Incoterms is vital for managing logistics costs. They dictate the responsibilities of buyers and sellers in shipping, which can significantly affect overall pricing.
What Are Effective Buyer Tips for Negotiating Urethane Molding Costs?
International B2B buyers should consider the following strategies to enhance cost-efficiency in sourcing urethane molding:
-
Negotiate Bulk Discounts: Engage suppliers in discussions about volume discounts, especially if you can commit to larger orders over time.
-
Evaluate Total Cost of Ownership: Look beyond the initial price and consider long-term costs, including maintenance, durability, and performance of the molded parts.
-
Request Detailed Quotes: Ensure that all components, including tooling, QC, and logistics, are clearly outlined in supplier quotes. This transparency can help identify areas for negotiation.
-
Leverage Regional Opportunities: Buyers from Africa, South America, and the Middle East should explore local suppliers to reduce shipping costs and lead times. European buyers, particularly from Italy, can benefit from regional manufacturing hubs that specialize in urethane molding.
-
Understand Pricing Nuances: Be aware of fluctuations in material costs and labor rates due to economic factors. This knowledge can empower buyers to negotiate more effectively.
Disclaimer on Indicative Prices
Prices for urethane molding services can vary widely based on the factors mentioned above. Buyers should consult multiple suppliers to obtain a range of quotes tailored to their specific needs and circumstances. Always ensure that price estimations account for regional differences, material availability, and any additional requirements that may affect overall costs.
Alternatives Analysis: Comparing urethane molding With Other Solutions
When considering manufacturing solutions, it’s essential for B2B buyers to evaluate various alternatives to urethane molding. Each method has its own strengths and weaknesses, which can significantly impact production timelines, costs, and the quality of the final product. Below, we provide a comparative analysis of urethane molding against two viable alternatives: injection molding and 3D printing.
Comparison Aspect | Urethane Molding | Injection Molding | 3D Printing |
---|---|---|---|
Performance | High-quality surface finish; good for low to medium volumes; simulates various plastic properties. | Excellent for high-volume production; consistent quality; complex geometries achievable. | Good for prototyping; intricate designs possible; limited material properties. |
Cost | Lower initial costs; economical for small runs; no need for expensive molds. | High upfront costs for mold creation; lower cost per unit for large volumes. | Low setup costs; cost-effective for small batches; higher per-unit cost for larger quantities. |
Ease of Implementation | Quick lead times with soft tooling; suitable for rapid prototyping. | Longer lead times due to mold fabrication; setup complexity. | Very fast setup; straightforward for design modifications; limited by printer capabilities. |
Maintenance | Minimal; molds can wear out over time but are generally durable. | High maintenance for molds; requires significant upkeep. | Low maintenance; issues typically arise from machine performance rather than material. |
Best Use Case | Ideal for low to medium production runs; prototypes; applications needing high detail and finish. | Best for mass production; high-precision parts; durable consumer goods. | Excellent for prototyping; custom parts; low-volume production; complex geometries. |
What Are the Pros and Cons of Injection Molding Compared to Urethane Molding?
Injection molding is a dominant manufacturing method for high-volume production. It offers consistent quality and is capable of producing complex geometries. However, the initial setup costs for molds can be significantly higher than those for urethane molding. This makes injection molding less economical for low-volume runs, where urethane molding shines due to its lower initial costs and quicker turnaround times. While injection molding produces high-quality parts, the long lead times for mold creation can delay time-to-market for new products.
How Does 3D Printing Stack Up Against Urethane Molding?
3D printing is a rapidly evolving technology that excels in producing intricate designs and prototypes. It has a low setup cost and allows for quick modifications to designs. However, 3D printing can struggle with material properties and surface finishes compared to urethane molding. While it’s cost-effective for small batches, the per-unit cost can rise significantly with larger volumes, making it less suitable for mass production. Urethane molding, on the other hand, provides a better balance of quality, cost, and versatility, especially for applications requiring durability and a high-quality finish.
How Can B2B Buyers Choose the Right Solution for Their Needs?
When selecting a manufacturing method, B2B buyers should consider their specific needs, such as production volume, budget constraints, and required part characteristics. For projects that involve low to medium volumes where quality and detail are paramount, urethane molding is often the best choice. If mass production is the goal and upfront investment is justified, injection molding may be the way to go. Conversely, for rapid prototyping and highly customized designs, 3D printing offers flexibility that other methods may not. Ultimately, evaluating these factors will help international buyers from regions like Africa, South America, the Middle East, and Europe make informed decisions that align with their operational goals.
Essential Technical Properties and Trade Terminology for urethane molding
What Are the Key Technical Properties of Urethane Molding?
Understanding the essential technical properties of urethane molding is crucial for B2B buyers, especially those looking to optimize production processes and ensure product quality. Here are some key specifications to consider:
-
Material Grade
Material grade refers to the specific formulation of urethane used, which can significantly affect performance characteristics. Common grades include general-purpose urethane, which is versatile and impact-resistant, and specialized grades like flame-retardant or rubber-like urethane. Selecting the right material grade is vital for meeting application-specific requirements, such as durability, flexibility, or compliance with industry standards. -
Shore Hardness
Shore hardness measures the material’s resistance to indentation, indicating its flexibility or rigidity. Urethanes can vary from soft Shore A values (25-95) for rubber-like applications to hard Shore D values (76-86) for more rigid parts. Understanding Shore hardness helps buyers select materials that will perform as required in their specific applications, ensuring longevity and reliability. -
Tolerance
Tolerance defines the allowable deviation in dimensions during manufacturing. Urethane molding typically achieves tolerances of ±0.005 inches, depending on the complexity of the part and the mold design. Accurate tolerances are crucial for applications where precise fit and function are necessary, such as in automotive or medical devices. -
Mechanical Properties
Mechanical properties include tensile strength, elongation at break, and impact resistance. These factors determine how well a urethane part can withstand physical stress and environmental conditions. For international buyers, understanding these properties ensures that the selected materials can endure the specific challenges posed by their markets, whether in extreme temperatures or high-stress applications. -
Chemical Resistance
Urethanes have varying degrees of resistance to chemicals, including oils, solvents, and acids. This property is particularly important for applications in industries like automotive or food processing, where exposure to harsh substances is common. Assessing chemical resistance helps prevent premature failure of components, safeguarding investments.

A stock image related to urethane molding.
- Finish Quality
The finish quality of urethane parts can greatly influence their aesthetic and functional attributes. Options range from matte to high-gloss finishes, which can impact the part’s usability and appeal. For B2B buyers, the ability to specify finish quality ensures that products meet both performance and branding standards.
What Trade Terminology Should B2B Buyers Know for Urethane Molding?
Familiarizing oneself with industry-specific terminology can enhance communication and negotiation in the urethane molding sector. Here are some common terms that are essential for B2B transactions:
-
OEM (Original Equipment Manufacturer)
An OEM is a company that produces parts or equipment that may be marketed by another manufacturer. Understanding OEM relationships is crucial for buyers seeking reliable suppliers who can meet specific quality and production standards. -
MOQ (Minimum Order Quantity)
MOQ refers to the minimum number of units a supplier is willing to produce or sell. Knowing the MOQ is essential for buyers to manage inventory and budget effectively, especially in low-volume production scenarios typical in urethane molding. -
RFQ (Request for Quotation)
An RFQ is a formal document requesting price quotes from suppliers for specific products or services. This process enables buyers to compare costs and terms, facilitating informed purchasing decisions in the competitive urethane market. -
Incoterms (International Commercial Terms)
Incoterms are standardized trade terms that define the responsibilities of buyers and sellers in international transactions. Familiarity with Incoterms helps buyers understand shipping costs, insurance, and risk management, which is critical when sourcing urethane products across borders. -
Lead Time
Lead time refers to the time taken from placing an order to receiving the finished product. In urethane molding, shorter lead times can provide a competitive advantage, allowing companies to respond quickly to market demands. -
Soft Tooling
Soft tooling refers to the use of less expensive materials (like silicone) for creating molds in low-volume production. This approach is particularly beneficial for companies looking to prototype or test designs without incurring the higher costs associated with traditional hard tooling methods.
By understanding these essential technical properties and trade terms, international B2B buyers can make more informed decisions, optimize their procurement strategies, and ultimately enhance their product offerings in the global market.
Navigating Market Dynamics and Sourcing Trends in the urethane molding Sector
What are the Current Market Dynamics and Key Trends in Urethane Molding?
The urethane molding sector is experiencing notable growth driven by several global factors. Increasing demand for customized and durable parts in industries such as automotive, aerospace, and medical devices is propelling the market forward. International B2B buyers, particularly those from Africa, South America, the Middle East, and Europe, are increasingly seeking flexible manufacturing solutions that offer rapid prototyping and low-volume production capabilities. The rise of e-commerce and online marketplaces has also facilitated easier access to suppliers, allowing businesses to source urethane products without geographical constraints.
Emerging technologies such as 3D printing are revolutionizing the urethane casting process. Companies are now utilizing 3D-printed master patterns to create molds more efficiently and cost-effectively. This trend not only shortens lead times but also enhances the ability to produce intricate designs and custom finishes that meet specific client needs. Furthermore, the growth of Industry 4.0, characterized by smart manufacturing and digital supply chains, is enabling better transparency and responsiveness in sourcing strategies.
Another trend is the increasing focus on low-cost, high-quality production. Urethane molding provides a cost-effective alternative to traditional injection molding for small to medium batch sizes, making it an attractive option for businesses looking to balance quality with budget constraints. As a result, B2B buyers are advised to consider suppliers that leverage these technologies to optimize their sourcing processes.
How Can B2B Buyers Address Sustainability and Ethical Sourcing in Urethane Molding?
Sustainability is becoming a crucial factor for B2B buyers in the urethane molding sector. The environmental impact of manufacturing processes is under scrutiny, and companies are increasingly pressured to adopt sustainable practices. This includes sourcing materials that are recyclable or derived from renewable resources. Ethical supply chains are gaining importance, with buyers looking for transparency in sourcing and production practices to ensure compliance with environmental regulations.
Many suppliers are now offering ‘green’ certifications or using eco-friendly materials in their urethane products. These materials not only minimize environmental impact but also appeal to a growing consumer base that prioritizes sustainability. B2B buyers should actively seek out suppliers who demonstrate commitment to sustainable practices, such as using low-VOC (volatile organic compounds) urethane formulations or implementing energy-efficient manufacturing processes.
Additionally, understanding the lifecycle impact of urethane products—from production to disposal—can help businesses make informed decisions. Buyers should engage with suppliers who provide data on the environmental footprint of their products and offer take-back or recycling programs. By prioritizing sustainability and ethical sourcing, B2B buyers can enhance their brand reputation and meet the expectations of environmentally conscious consumers.
What is the Brief Evolution and History of Urethane Molding?
The history of urethane molding dates back to the mid-20th century when polyurethane was first developed as a versatile material. Initially used in foam applications, the unique properties of polyurethane led to its adoption in various industrial applications, including coatings, adhesives, and elastomers. The introduction of urethane casting techniques allowed manufacturers to create complex shapes and high-quality finishes with relative ease.
Over the decades, advances in material science and manufacturing technology have refined urethane molding processes, making them more efficient and accessible. The ability to produce low-volume, high-quality parts has transformed the industry, allowing businesses to innovate rapidly and meet market demands. Today, urethane molding stands as a critical component in numerous sectors, reflecting its evolution from a niche application to a mainstream manufacturing solution for international B2B buyers.
Frequently Asked Questions (FAQs) for B2B Buyers of urethane molding
-
How do I solve quality issues with urethane molded parts?
To address quality issues in urethane molded parts, first, ensure that the supplier conducts thorough quality assurance (QA) checks throughout the production process. Look for suppliers who utilize advanced testing methods, such as tensile strength and hardness tests, to validate material properties. Additionally, consider implementing a detailed inspection plan that includes pre-production samples and regular quality audits. Open communication with your supplier about any defects or inconsistencies will also help resolve issues promptly, ensuring that the final products meet your specifications. -
What is the best type of urethane material for my application?
The best urethane material for your application depends on the specific performance requirements, such as hardness, flexibility, and chemical resistance. For instance, if you need a tough and durable part, a rigid urethane with a Shore hardness of 80 or higher may be suitable. Conversely, if flexibility is paramount, consider rubber-like polyurethanes with lower Shore hardness values. Evaluate your application’s demands alongside your budget and desired lead times, and consult with suppliers who can provide samples or prototypes for testing. -
How can I customize urethane molded parts to fit my design needs?
Customization of urethane molded parts can be achieved through various methods, including adjusting material properties, colors, and surface finishes. Most suppliers offer the option to select from different urethane formulations, allowing you to tailor the part’s performance. Additionally, you can specify custom colors and finishes, such as matte, semi-gloss, or high-gloss options. Engaging in early discussions with your supplier about design requirements and potential modifications will ensure that your final product aligns with your vision. -
What are the minimum order quantities (MOQ) for urethane molding?
Minimum order quantities (MOQ) for urethane molding can vary significantly between suppliers and depend on factors such as the complexity of the part and the materials used. Typically, MOQs can range from as low as 10 to several hundred units. When sourcing from international suppliers, ensure to clarify the MOQ upfront to avoid any misunderstandings. If you require a smaller quantity, some suppliers may offer prototyping services or low-volume production runs to accommodate your needs. -
How do I vet potential suppliers for urethane molding?
Vetting suppliers for urethane molding involves assessing their capabilities, quality standards, and reliability. Start by checking their certifications, such as ISO 9001, which indicates adherence to quality management practices. Request samples of previous work to evaluate the quality and precision of their molded parts. Additionally, read customer testimonials and reviews to gauge their reputation in the market. Establishing direct communication with potential suppliers can also help you understand their production processes and responsiveness to client needs. -
What payment terms should I expect when sourcing urethane molded parts internationally?
Payment terms for international sourcing of urethane molded parts can vary widely based on the supplier’s policies and your relationship with them. Common terms include a deposit (usually 30-50%) upfront, with the balance due upon completion or delivery of the order. Some suppliers may offer net terms (e.g., net 30 or net 60) for established clients. It’s essential to discuss and agree on payment terms before finalizing contracts, ensuring that they align with your cash flow and operational needs. -
What logistics considerations should I keep in mind for international shipping of urethane molded parts?
When planning logistics for the international shipping of urethane molded parts, consider factors such as shipping methods, customs clearance, and delivery timelines. Choose a reliable logistics partner familiar with the shipping regulations of your destination country to minimize delays. Ensure that the supplier provides accurate documentation, including invoices and packing lists, to facilitate smooth customs processes. Additionally, factor in shipping costs and potential tariffs, which can significantly impact your overall budget. -
How do I ensure compliance with international standards for urethane molded parts?
To ensure compliance with international standards for urethane molded parts, familiarize yourself with relevant regulations specific to your industry and target market. Depending on your application, you may need to adhere to standards such as ISO, ASTM, or specific industry certifications (e.g., medical or automotive). Work closely with your supplier to confirm that they implement quality control measures and testing protocols that align with these standards. Regular audits and reviews of your supplier’s compliance status can also help maintain adherence throughout the production process.
Important Disclaimer & Terms of Use
⚠️ Important Disclaimer
The information provided in this guide, including content regarding manufacturers, technical specifications, and market analysis, is for informational and educational purposes only. It does not constitute professional procurement advice, financial advice, or legal advice.
While we have made every effort to ensure the accuracy and timeliness of the information, we are not responsible for any errors, omissions, or outdated information. Market conditions, company details, and technical standards are subject to change.
B2B buyers must conduct their own independent and thorough due diligence before making any purchasing decisions. This includes contacting suppliers directly, verifying certifications, requesting samples, and seeking professional consultation. The risk of relying on any information in this guide is borne solely by the reader.
Strategic Sourcing Conclusion and Outlook for urethane molding
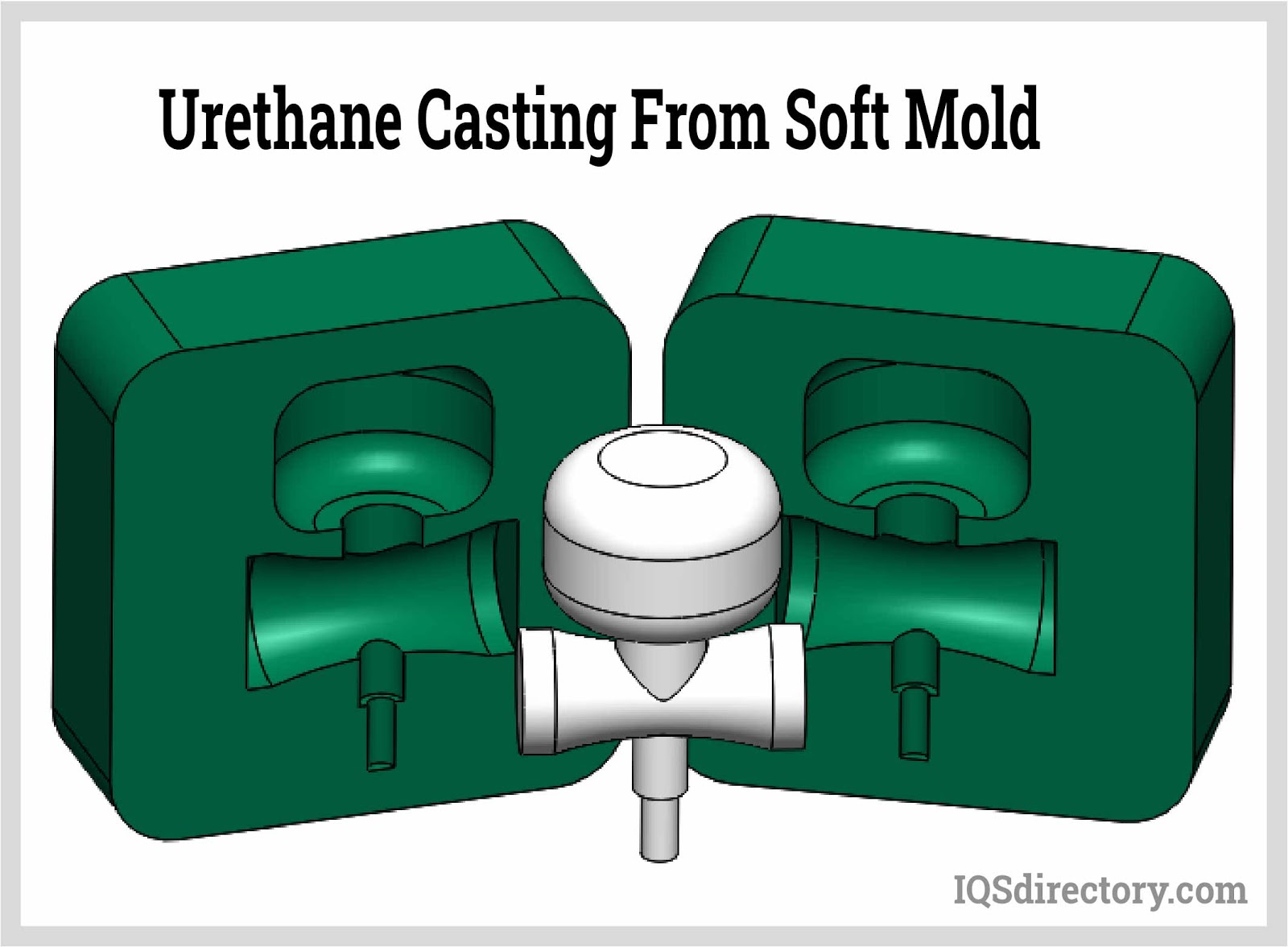
A stock image related to urethane molding.
What Are the Key Takeaways for B2B Buyers in Urethane Molding?
In conclusion, urethane molding presents a strategic advantage for international B2B buyers looking to optimize their production processes. Its flexibility in handling low to medium volume runs allows businesses from Africa, South America, the Middle East, and Europe to bridge the gap between rapid prototyping and full-scale production without the high costs associated with injection molding. Urethane casting can deliver production-quality parts quickly, making it an ideal solution for industries ranging from electronics to medical devices.
How Can Strategic Sourcing Enhance Your Urethane Molding Capabilities?
Strategic sourcing is crucial for maximizing the benefits of urethane molding. By partnering with reliable suppliers who offer diverse material options and advanced manufacturing technologies, businesses can ensure high-quality outcomes tailored to their specific needs. Understanding material properties, such as Shore hardness and finish options, empowers buyers to make informed decisions that align with their project requirements.
What Does the Future Hold for Urethane Molding in Global Markets?
Looking ahead, the demand for urethane molding is expected to grow as industries increasingly seek cost-effective and versatile manufacturing solutions. International B2B buyers should actively explore partnerships with suppliers who can adapt to emerging trends and technological advancements. By doing so, companies can position themselves competitively in the global marketplace and capitalize on the benefits of urethane molding for their product development strategies. Engaging with knowledgeable suppliers can unlock new opportunities and drive innovation within your operations.