Unlock Efficiency: The Complete CNC Machine G Code Guide (2025)
Introduction: Navigating the Global Market for cnc machine g code
In the fast-evolving landscape of global manufacturing, understanding CNC machine G code is crucial for international B2B buyers looking to optimize their production processes. Sourcing high-quality G code programming can pose significant challenges, especially when navigating different machines, applications, and standards prevalent across regions such as Africa, South America, the Middle East, and Europe. This guide offers a comprehensive overview of CNC machine G code, detailing various types and their applications, while also providing insights into supplier vetting, cost considerations, and best practices for effective implementation.
As the demand for precision engineering grows, so does the complexity of CNC operations. Buyers will benefit from a thorough exploration of essential G codes, such as G00 for rapid travel and G01 for linear interpolation, as well as more advanced commands that facilitate intricate machining tasks. Additionally, this guide empowers businesses to make informed purchasing decisions by outlining critical factors to consider when selecting CNC suppliers, ensuring compatibility with existing machinery, and evaluating long-term costs versus benefits.
By leveraging the insights provided in this guide, B2B buyers can streamline their procurement processes, enhance their operational efficiency, and ultimately drive greater value in their manufacturing endeavors. Whether you are based in Spain, the UAE, or beyond, this resource serves as an essential tool for navigating the complexities of CNC machine G code in the global market.
Understanding cnc machine g code Types and Variations
Type Name | Key Distinguishing Features | Primary B2B Applications | Brief Pros & Cons for Buyers |
---|---|---|---|
G00 – Rapid Travel | Quick movement without cutting; used for positioning. | Tool changes, setup operations | Pros: Increases efficiency; Cons: Risk of collisions if not careful. |
G01 – Linear Interpolation | Cutting along a straight line; requires feed rate. | Milling, drilling operations | Pros: High precision; Cons: Requires careful speed management. |
G02/G03 – Circular Interpolation | For machining arcs; G02 clockwise, G03 counterclockwise. | Complex shapes, curved profiles | Pros: Essential for intricate designs; Cons: More complex programming. |
G04 – Dwell | Introduces pauses in machining to improve finish quality. | Drilling operations, finishing cuts | Pros: Enhances surface finish; Cons: Slower cycle times. |
G90/G91 – Positioning Modes | G90 for absolute positioning, G91 for incremental. | General machining applications | Pros: Flexibility in programming; Cons: Can lead to errors if misunderstood. |
What Are the Key Features of G00 – Rapid Travel in CNC G Code?
G00 is essential for rapid positioning of the tool without engaging in cutting. It is commonly used during tool changes or when moving to a new starting point. This command enables quick transitions, which is crucial for maintaining productivity in high-volume operations. However, buyers should consider the potential risks associated with rapid movements, such as collisions with workpieces or fixtures. Effective training and careful programming can mitigate these risks.
How Does G01 – Linear Interpolation Benefit B2B Operations?
G01 allows for cutting along a straight line and requires a specified feed rate. This command is fundamental for operations such as milling and drilling, where precision is paramount. It enables machinists to control the speed of the tool, ensuring optimal material removal rates. Buyers should assess their machining needs to determine the appropriate feed rates and cutting speeds, as incorrect settings can lead to tool wear or damage.
Why Are G02 and G03 – Circular Interpolation Important for Complex Machining?
G02 and G03 facilitate the machining of arcs and circles, which are critical for producing complex shapes and profiles. These commands allow for smooth transitions in cutting, enhancing the quality of the finished product. In B2B contexts, this capability is vital for industries that require intricate designs, such as automotive and aerospace. However, the complexity of programming these commands necessitates skilled operators and robust training programs.
What Role Does G04 – Dwell Play in Enhancing Machining Quality?
The G04 command introduces a pause in the machining process, which can be beneficial for improving surface finishes, especially when using flat-bottom drills. This dwell time allows the tool to clean up the surface before proceeding, which is particularly useful in precision machining applications. While this can enhance quality, buyers must weigh the trade-off of slower cycle times against the benefits of improved finish quality.
How Do G90 and G91 – Positioning Modes Affect CNC Programming?
G90 and G91 define the positioning mode of the CNC machine, with G90 using absolute positioning and G91 using incremental positioning. This flexibility allows operators to choose the most efficient method based on the job requirements. For B2B buyers, understanding these modes is critical, as incorrect usage can lead to significant errors in machining. Proper training and documentation are essential to ensure operators are well-versed in the implications of each mode.
Key Industrial Applications of cnc machine g code
Industry/Sector | Specific Application of CNC Machine G Code | Value/Benefit for the Business | Key Sourcing Considerations for this Application |
---|---|---|---|
Aerospace | Precision component manufacturing | High accuracy and repeatability in complex geometries | Supplier certifications, quality control processes |
Automotive | Tooling and prototyping | Faster production cycles and reduced material waste | Advanced machining capabilities, lead times |
Medical Devices | Custom surgical instruments | Tailored solutions for specific surgical needs | Compliance with medical standards, material sourcing |
Construction Equipment | Fabrication of structural components | Enhanced durability and performance of machinery | Robustness of machinery, customization options |
Electronics | PCB prototyping and manufacturing | Higher precision in electronic component production | Precision machining capabilities, rapid prototyping |
How is CNC Machine G Code Used in Aerospace Manufacturing?
In the aerospace industry, CNC machine G Code is essential for manufacturing precision components such as turbine blades and fuselage parts. The high accuracy and repeatability required in this sector ensure that components meet stringent safety standards. International buyers should prioritize suppliers with robust quality control processes and certifications, as these are critical for maintaining compliance with aviation regulations.
What are the Applications of CNC Machine G Code in Automotive Tooling?
CNC machine G Code is widely utilized in the automotive sector for tooling and prototyping. This application allows manufacturers to create complex shapes and components more efficiently, resulting in faster production cycles and reduced material waste. Buyers from regions like South America and Europe should consider suppliers that offer advanced machining capabilities and can deliver on time to meet the fast-paced demands of the automotive market.
How is CNC Machine G Code Beneficial for Medical Device Manufacturing?
In the medical devices sector, CNC machine G Code facilitates the production of custom surgical instruments tailored to specific surgical needs. This level of customization ensures that medical professionals have the right tools for various procedures, improving patient outcomes. B2B buyers in this field must focus on suppliers that comply with medical standards and can source high-quality materials to ensure safety and efficacy.
What Role Does CNC Machine G Code Play in Construction Equipment Fabrication?
CNC machine G Code is crucial in the fabrication of structural components for construction equipment. The use of CNC technology enhances the durability and performance of machinery by allowing for precise cuts and shapes. Buyers should evaluate the robustness of the machinery used by suppliers, as well as their ability to offer customization options to meet specific project requirements.
How is CNC Machine G Code Applied in Electronics Manufacturing?
In the electronics industry, CNC machine G Code is utilized for PCB prototyping and manufacturing. This application requires high precision to ensure that electronic components function correctly. International buyers should prioritize suppliers that possess precision machining capabilities and can provide rapid prototyping services to keep pace with the fast-evolving electronics market.
3 Common User Pain Points for ‘cnc machine g code’ & Their Solutions
Scenario 1: Navigating G-Code Compatibility Across Different CNC Machines
The Problem: B2B buyers often encounter difficulties when trying to implement G-code across various CNC machines, especially when dealing with different manufacturers. Each machine may have unique interpretations or extensions of G-code, leading to errors in machining processes and increased downtime. This inconsistency can be particularly challenging for companies operating in regions like Africa and South America, where access to standardized training and resources may be limited.
The Solution: To effectively manage G-code compatibility, buyers should invest in training programs that cover the nuances of G-code for specific CNC machines. This includes understanding the core G-codes that are commonly used across most machines, such as G00 for rapid positioning and G01 for linear interpolation. Additionally, utilizing simulation software that can replicate the specific CNC environment will allow operators to test their G-code before actual machining. Engaging with vendors that offer robust technical support can also ensure that any discrepancies in G-code interpretation are addressed promptly, minimizing production delays and enhancing operational efficiency.
Scenario 2: Overcoming the Complexity of G-Code Programming for Beginners
The Problem: Many businesses, especially startups in the Middle East and Europe, face a steep learning curve when training staff to program CNC machines using G-code. New employees often struggle with the syntax and logic required to write effective G-code, leading to increased error rates and reduced productivity. This complexity can deter companies from fully utilizing their CNC capabilities and can hamper their competitive edge.
The Solution: To simplify the learning process, businesses should consider implementing structured training programs that utilize both hands-on workshops and online resources. Investing in comprehensive training materials that break down G-code commands into digestible segments can demystify the programming process. Furthermore, partnering with educational institutions or CNC training centers can provide employees with practical experience. Using user-friendly G-code editors with built-in error-checking features can also assist beginners in developing their programming skills without the risk of significant mistakes.
Scenario 3: Ensuring Accuracy with G-Code in Precision Machining
The Problem: Precision is paramount in CNC machining, and inaccuracies in G-code can lead to defective parts and costly rework. This issue is prevalent among international buyers, especially in industries like aerospace and automotive, where stringent specifications must be met. G-code errors can stem from manual entry mistakes, miscommunication in design specifications, or improper tool settings, causing frustration and financial losses.
The Solution: To mitigate the risk of inaccuracies, it is crucial to adopt a robust quality assurance process that incorporates G-code verification tools. Implementing software that can simulate G-code execution prior to machining can catch errors early in the process. Additionally, establishing a standardized workflow for G-code generation, including checks for unit consistency (metric vs. imperial) and tool offsets, can enhance accuracy. Regular audits and cross-training among team members involved in programming and machining can also foster a culture of precision, significantly reducing the occurrence of errors and ensuring high-quality output.
Strategic Material Selection Guide for cnc machine g code
When selecting materials for CNC machining, particularly in the context of G-code programming, it is crucial for international B2B buyers to understand the properties, advantages, and limitations of various materials. This understanding aids in optimizing performance, ensuring compliance with regional standards, and enhancing the overall quality of the end product.
What Are the Key Properties of Aluminum in CNC Machining?
Aluminum is one of the most commonly used materials in CNC machining due to its favorable properties. It boasts a high strength-to-weight ratio, excellent corrosion resistance, and good thermal conductivity. These characteristics make aluminum suitable for a wide range of applications, from automotive components to aerospace parts.
Pros & Cons:
– Pros: Lightweight, easy to machine, and has excellent corrosion resistance. It can be anodized for additional surface protection.
– Cons: While generally durable, aluminum can be softer than other metals, making it less suitable for high-wear applications. It can also be more expensive than some alternatives.
Impact on Application:
Aluminum is compatible with various media, including water and oils, making it suitable for hydraulic applications. However, it may not perform well in high-temperature environments without special treatments.
Considerations for International Buyers:
Buyers from regions like Africa and the Middle East should be aware of local suppliers that comply with ASTM standards for aluminum alloys. Understanding the specific alloy grades that are commonly used in their industry can help in making informed purchasing decisions.
How Does Steel Compare as a Material for CNC Machining?
Steel is another prevalent material in CNC machining, known for its durability and strength. It offers a wide range of grades, including carbon steel, stainless steel, and tool steel, each tailored for specific applications.
Pros & Cons:
– Pros: High tensile strength, excellent wear resistance, and good machinability. Stainless steel, in particular, offers excellent corrosion resistance.
– Cons: Heavier than aluminum, which may not be suitable for weight-sensitive applications. It can also be more challenging to machine due to its hardness.
Impact on Application:
Steel is ideal for applications requiring high strength and durability, such as automotive and industrial machinery. However, its weight can be a disadvantage in applications where weight reduction is critical.
Considerations for International Buyers:
Buyers in Europe, particularly in Spain, must consider compliance with European standards (EN) for steel grades. Understanding the specific requirements for different applications can guide buyers in selecting the appropriate steel grade.
What Are the Benefits of Using Plastics in CNC Machining?
Plastics, such as polycarbonate and nylon, are increasingly popular in CNC machining due to their versatility and lightweight nature. They are particularly useful in applications where corrosion resistance and electrical insulation are essential.
Pros & Cons:
– Pros: Lightweight, corrosion-resistant, and can be molded into complex shapes. They are often less expensive than metals.
– Cons: Generally not as strong or durable as metals, making them unsuitable for high-stress applications. They can also be sensitive to temperature variations.
Impact on Application:
Plastics are compatible with various media and are often used in electrical components and consumer products. However, their lower thermal resistance can limit their use in high-temperature environments.
Considerations for International Buyers:
Buyers from South America should be aware of local regulations regarding the use of certain plastics, especially in food and medical applications. Understanding local standards can help ensure compliance and safety.
How Does Titanium Enhance CNC Machining Applications?
Titanium is a high-performance material known for its exceptional strength-to-weight ratio and corrosion resistance. It is commonly used in aerospace, medical, and high-end automotive applications.
Pros & Cons:
– Pros: Extremely strong, lightweight, and highly resistant to corrosion and heat. Ideal for demanding applications.
– Cons: More expensive than other materials and can be challenging to machine due to its hardness.
Impact on Application:
Titanium is suitable for high-performance applications, including aerospace components and medical implants. Its unique properties make it ideal for environments that require both strength and resistance to harsh conditions.
Considerations for International Buyers:
Buyers in the UAE should consider the specific grades of titanium that meet industry standards, such as ASTM or ISO. Understanding the cost implications and sourcing options can help in budget planning.
Summary Table of Material Selection for CNC Machining
Material | Typical Use Case for cnc machine g code | Key Advantage | Key Disadvantage/Limitation | Relative Cost (Low/Med/High) |
---|---|---|---|---|
Aluminum | Automotive components, aerospace parts | Lightweight and corrosion-resistant | Softer than some metals | Medium |
Steel | Industrial machinery, automotive parts | High strength and durability | Heavier and harder to machine | Medium to High |
Plastics | Electrical components, consumer products | Lightweight and cost-effective | Lower strength and thermal resistance | Low |
Titanium | Aerospace components, medical implants | Exceptional strength and corrosion resistance | High cost and machining difficulty | High |
This strategic material selection guide provides valuable insights for international B2B buyers, enabling them to make informed decisions based on material properties, applications, and compliance with regional standards.
In-depth Look: Manufacturing Processes and Quality Assurance for cnc machine g code
What Are the Main Stages of Manufacturing Processes for CNC Machine G Code?
Understanding the manufacturing processes involved in CNC machine G code is essential for B2B buyers looking to optimize their operations and ensure quality output. The typical stages of CNC manufacturing include material preparation, forming, assembly, and finishing. Each stage has its specific techniques and quality assurance checkpoints.
How is Material Prepared for CNC Machining?
Material preparation is the first step in CNC machining. It involves selecting the right raw material, which could range from metals like aluminum and steel to plastics. Key techniques during this stage include:
- Material Selection: Choose materials that meet the specifications of the final product. Buyers should consider properties like strength, machinability, and resistance to wear.
- Cutting and Shaping: Raw materials are cut to size using saws or lasers before being loaded into CNC machines. This initial shaping is critical to ensure that the material fits within the CNC machine’s work envelope.
B2B buyers should engage suppliers who have robust material sourcing strategies and can provide certificates of material compliance, ensuring that the materials meet specific standards.
What Techniques are Used in the Forming Stage of CNC Machining?
The forming stage involves the actual machining process where G code comes into play. This stage is crucial for creating the desired shapes and dimensions. Techniques include:
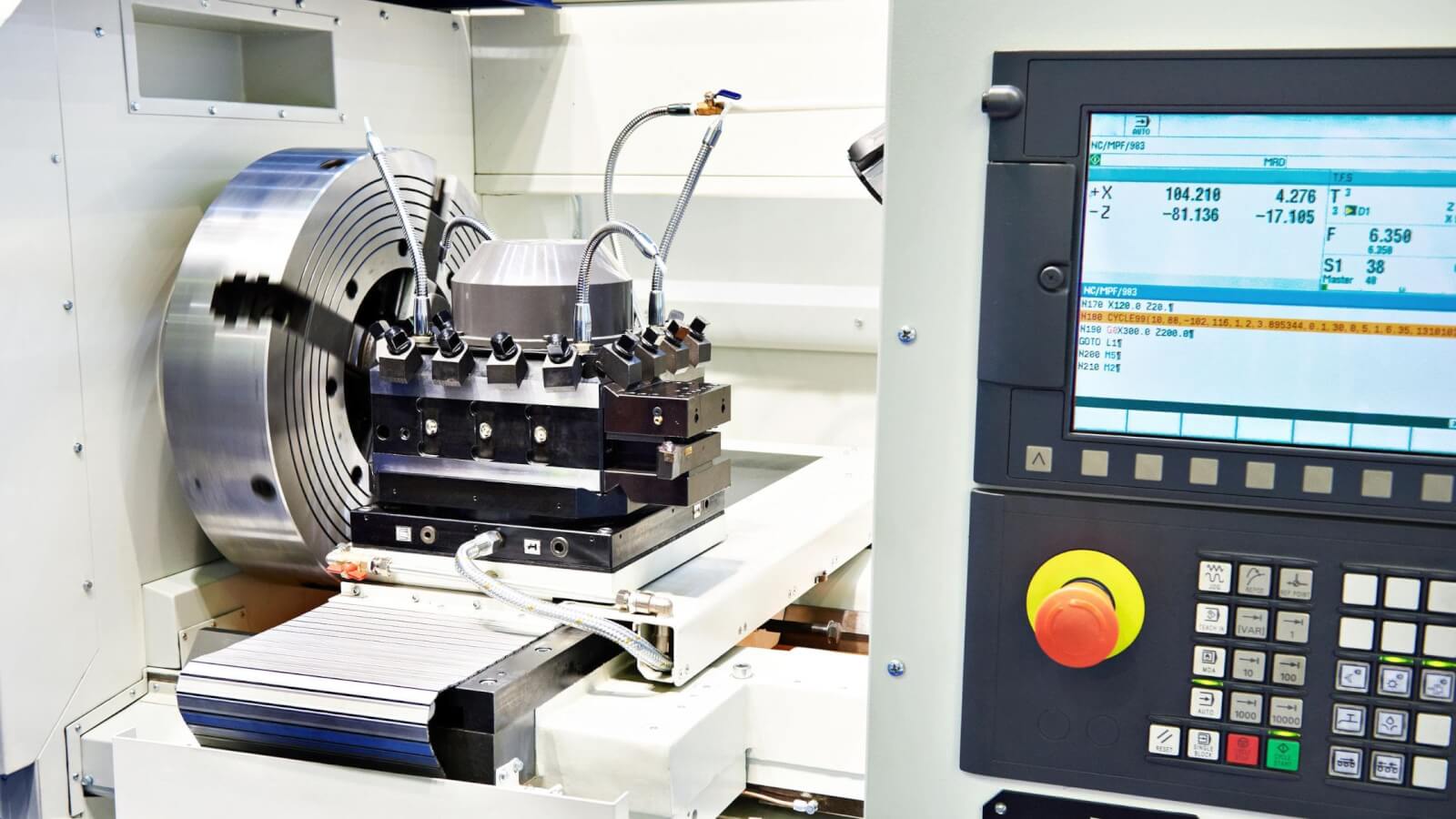
A stock image related to cnc machine g code.
- Milling and Turning: CNC milling machines and lathes utilize G code commands such as G01 for linear interpolation and G02/G03 for circular interpolation to create complex geometries.
- 5-Axis Machining: For intricate designs, 5-axis CNC machines allow for more complex cuts and angles, increasing precision. This capability is particularly beneficial for industries like aerospace and automotive.
B2B buyers should inquire about the specific machining capabilities of their suppliers to ensure they can meet complex project requirements.
What Are the Key Processes in Assembly and Finishing?
Once the parts are machined, assembly and finishing are crucial for ensuring the product meets quality standards. The processes involved include:
- Assembly: If the product consists of multiple machined parts, precise assembly is essential. This may involve manual assembly or automated processes, depending on the scale of production.
- Finishing: Techniques such as anodizing, powder coating, or polishing enhance the product’s appearance and durability. G code may also dictate specific finishing processes.
B2B buyers should ensure that their suppliers have a clear plan for assembly and finishing processes, including any post-processing treatments that may be required.
How is Quality Assurance Maintained in CNC Machining?
Quality assurance (QA) is vital in ensuring that CNC machined parts meet international standards and customer specifications. Buyers should understand the various quality control (QC) checkpoints and standards applicable to CNC machining.
What Are the International Standards for CNC Machining Quality Control?
Several international standards govern quality assurance in CNC machining. The most notable include:
- ISO 9001: This standard focuses on quality management systems and is applicable across various industries. Suppliers should be certified to ISO 9001 to ensure they follow consistent quality practices.
- CE Marking: For products sold in the European Union, CE marking indicates compliance with safety, health, and environmental protection standards.
- API Standards: In industries such as oil and gas, API standards ensure that products meet specific safety and operational criteria.
B2B buyers should request certifications from their suppliers to verify compliance with these standards.
What Are the Key Quality Control Checkpoints in CNC Manufacturing?
Quality control in CNC manufacturing typically involves several checkpoints:
- Incoming Quality Control (IQC): This involves inspecting raw materials upon receipt to ensure they meet specifications before production begins.
- In-Process Quality Control (IPQC): During the machining process, continuous monitoring is necessary. This may include measurements of critical dimensions and checks for machining errors.
- Final Quality Control (FQC): After machining and finishing, products undergo final inspections to verify that they meet all specifications before delivery.
B2B buyers should establish clear expectations with suppliers regarding the frequency and methods of inspections at each checkpoint.
How Can B2B Buyers Verify Supplier Quality Control?
It is crucial for B2B buyers to verify the quality control processes of their suppliers to ensure reliability and consistency in production.
What Methods Can Be Used for Supplier Audits and Inspections?
- Supplier Audits: Conducting regular audits helps buyers assess suppliers’ manufacturing processes and quality control systems. This can be done through on-site visits or comprehensive reports.
- Quality Reports: Suppliers should provide detailed quality reports, including inspection results and any corrective actions taken. This transparency builds trust and ensures accountability.
- Third-Party Inspections: Engaging third-party inspection services can provide an unbiased assessment of the supplier’s quality control practices. This is particularly important for international transactions where buyers may not have direct oversight.
What Are the Quality Control Nuances for International Buyers?
For international B2B buyers, understanding quality control nuances is essential. Factors to consider include:
- Cultural Differences: Different regions may have varying standards and practices in manufacturing. Buyers should familiarize themselves with local customs and regulations.
- Logistics and Compliance: International shipments may require additional inspections and compliance checks. Buyers should ensure that suppliers are knowledgeable about customs regulations and documentation.
- Language Barriers: Clear communication is crucial. Buyers should ensure that suppliers can provide documentation in the buyer’s preferred language to avoid misunderstandings.
By understanding these manufacturing processes and quality assurance protocols, B2B buyers can make informed decisions when sourcing CNC machined products, ensuring they receive high-quality components that meet their specific needs.
Practical Sourcing Guide: A Step-by-Step Checklist for ‘cnc machine g code’
To effectively procure CNC machine G-code for your manufacturing needs, it is essential to follow a structured approach. This checklist serves as a practical guide for international B2B buyers from regions such as Africa, South America, the Middle East, and Europe, ensuring you make informed decisions that align with your operational goals.
Step 1: Define Your Technical Specifications
Clearly outline the specifications of the CNC machine you intend to use. This includes the types of G-codes compatible with your equipment, the required precision, and the specific machining tasks you aim to accomplish. Understanding these technical details is crucial for ensuring that the G-code you source will work effectively with your machinery.
- Considerations:
- Identify the machine model and manufacturer.
- List the primary operations (e.g., milling, turning) that will utilize the G-code.
Step 2: Research and Identify Reputable Suppliers
Conduct thorough research to identify suppliers that specialize in CNC G-code programming. Look for suppliers with a proven track record in your industry and those who understand the specific requirements of international markets.
- Key Actions:
- Check supplier reviews and testimonials.
- Look for case studies or examples of previous work relevant to your needs.
Step 3: Evaluate Supplier Certifications and Compliance
Ensure that potential suppliers hold relevant certifications and comply with international standards. Certifications such as ISO 9001 can indicate a commitment to quality management practices.
- What to Look For:
- Certification validity and scope.
- Compliance with regional regulations, especially if you are importing.
Step 4: Request Samples and Demonstrations
Before finalizing any agreements, request samples of the G-code or demonstrations of their programming capabilities. This will help you assess the quality and suitability of the code for your specific applications.
- Sample Requests:
- Ask for a trial run on a sample part to evaluate performance.
- Review the coding style and commentaries for clarity and usability.
Step 5: Discuss Support and Training Options
Inquire about the support and training options available from your suppliers. This is particularly important if your team is new to G-code programming or if you are integrating new machinery.
- Support Considerations:
- Availability of technical support post-purchase.
- Training programs for your staff on using the G-code effectively.
Step 6: Negotiate Terms and Pricing
Engage in negotiations to establish favorable terms and pricing structures. Consider not just the initial costs but also long-term value, including updates and support.
- Negotiation Tips:
- Explore bulk purchase discounts.
- Discuss the potential for ongoing support contracts.
Step 7: Finalize the Purchase Agreement
Once all due diligence is completed, finalize your purchase agreement. Ensure that all terms are clearly outlined, including delivery timelines, payment schedules, and warranty information.
- Important Elements:
- Clearly defined responsibilities for both parties.
- Contingencies for delays or discrepancies in G-code performance.
By following this step-by-step checklist, B2B buyers can ensure a more streamlined and effective procurement process for CNC machine G-code, ultimately leading to improved productivity and quality in manufacturing operations.
Comprehensive Cost and Pricing Analysis for cnc machine g code Sourcing
What Are the Key Cost Components in CNC Machine G-Code Sourcing?
When sourcing CNC machine G-Code, various cost components come into play. Understanding these elements can help international B2B buyers from regions like Africa, South America, the Middle East, and Europe (including Spain and the UAE) make informed purchasing decisions.
-
Materials: The primary material costs involve the software and hardware necessary for CNC operations. This includes licenses for G-Code programming software and the cost of the CNC machines themselves. Additionally, the type of machine (e.g., 3-axis vs. 5-axis) can significantly affect material costs.
-
Labor: Skilled labor is essential for creating and optimizing G-Code. Labor costs can vary dramatically based on geographic location and the availability of trained machinists. In regions with a shortage of skilled labor, prices may be higher, impacting overall project costs.
-
Manufacturing Overhead: This includes utilities, equipment maintenance, and facility costs associated with CNC machining operations. Buyers should consider how these overheads influence the pricing structure of suppliers, especially when sourcing from different countries.
-
Tooling: The cost of tooling, including cutting tools and fixtures, must also be accounted for. The choice of tooling can affect the longevity and performance of the machine, making it a critical factor in the overall cost structure.
-
Quality Control (QC): Implementing QC measures to ensure that the G-Code produced meets specified standards can add to costs. Buyers should inquire about the QC processes of potential suppliers and how these might affect pricing.
-
Logistics: Shipping and handling costs can vary significantly based on the supplier’s location and the chosen shipping method. Understanding Incoterms is crucial, as they define responsibilities and risks between buyers and sellers during transportation.
-
Margin: Suppliers typically include a profit margin in their pricing. This margin can vary based on the supplier’s market position, reputation, and the uniqueness of their offerings.
What Influences Pricing for CNC Machine G-Code?
Several factors can influence the pricing of CNC machine G-Code, particularly for international buyers.
-
Volume and Minimum Order Quantity (MOQ): Larger orders often lead to lower per-unit costs due to economies of scale. Buyers should negotiate for favorable terms based on their expected order volumes.
-
Specifications and Customization: Custom G-Code solutions tailored to specific projects can incur additional costs. Buyers should clearly define their needs to avoid unexpected charges.
-
Quality and Certifications: Products that come with industry certifications or guarantees of quality may command higher prices. Buyers should weigh the benefits of certified products against their costs.
-
Supplier Factors: The reputation and reliability of a supplier can affect pricing. Established suppliers may charge more due to their proven track record, while newer suppliers may offer lower prices to attract business.
-
Incoterms: Different shipping terms can significantly impact the total cost. Buyers should understand the implications of terms like FOB (Free on Board) or CIF (Cost, Insurance, and Freight) when budgeting for their purchases.
What Tips Can Help B2B Buyers Optimize Costs in CNC Machine G-Code Sourcing?
-
Negotiation: Engaging in negotiation can yield better pricing terms. Buyers should be prepared to discuss volume discounts, payment terms, and delivery timelines.
-
Cost-Efficiency: Focus on total cost of ownership rather than just upfront costs. This includes evaluating long-term operational costs associated with different G-Code solutions.
-
Pricing Nuances for International Buyers: Understand the economic conditions and market dynamics of the supplier’s country. Currency fluctuations, trade tariffs, and local market competition can all influence pricing.
-
Research and Compare: Conduct thorough research on multiple suppliers to compare pricing, quality, and service levels. This can help identify the best value for money.
-
Leverage Technology: Utilize software solutions for G-Code generation and optimization to minimize labor costs and improve efficiency.
Disclaimer
Prices mentioned in this analysis are indicative and can fluctuate based on market conditions, supplier negotiations, and specific project requirements. Buyers should conduct their own research and due diligence when sourcing CNC machine G-Code.
Alternatives Analysis: Comparing cnc machine g code With Other Solutions
Introduction: Exploring Alternatives to CNC Machine G Code
In the realm of CNC machining, G Code is widely recognized as the standard language for programming CNC machines. However, as technology advances, various alternative solutions have emerged that offer different functionalities and efficiencies. Understanding these alternatives can help B2B buyers, especially in diverse markets such as Africa, South America, the Middle East, and Europe, make informed decisions based on their specific operational needs and budget constraints.
Comparison Table of CNC Machine G Code and Alternatives
Comparison Aspect | CNC Machine G Code | CAD/CAM Software | M-Code |
---|---|---|---|
Performance | High precision and control | Varies with software quality | High precision and control |
Cost | Low to moderate | Moderate to high | Low to moderate |
Ease of Implementation | Requires programming skills | User-friendly interfaces | Requires programming skills |
Maintenance | Low maintenance | Regular updates needed | Low maintenance |
Best Use Case | General CNC machining | Complex designs and workflows | Specific machine functions |
What Are the Advantages and Disadvantages of CAD/CAM Software?
CAD/CAM software integrates computer-aided design (CAD) and computer-aided manufacturing (CAM), allowing for seamless design-to-production workflows. One major advantage is its ability to handle complex geometries that may be cumbersome to program manually with G Code. Additionally, these software solutions often provide user-friendly interfaces that reduce the learning curve for operators. However, the costs can be significant, and ongoing software updates may be necessary to ensure compatibility with the latest machine technology. This option is ideal for businesses that require intricate designs and value efficiency in transitioning from design to production.
How Does M-Code Compare to CNC Machine G Code?
M-Code, or miscellaneous code, complements G Code by controlling machine-specific functions such as spindle rotation and coolant flow. While it is not a standalone programming language like G Code, it is essential for comprehensive machine operation. The primary advantage of M-Code is its ability to manage non-motion-related tasks effectively, enhancing the overall efficiency of CNC operations. However, M-Code requires operators to have a solid understanding of machine-specific codes and their applications, which can be a barrier for some users. This alternative is best suited for manufacturers looking to optimize specific machine operations without the need for extensive programming.
Conclusion: Choosing the Right Solution for Your CNC Needs
When considering alternatives to CNC machine G Code, B2B buyers must evaluate their specific operational requirements, budget constraints, and the complexity of the tasks at hand. While G Code remains a robust and widely used programming language, alternatives like CAD/CAM software and M-Code offer unique benefits that can enhance productivity and precision. By carefully analyzing the performance, cost, ease of implementation, maintenance, and best use cases of each option, businesses can make informed decisions that align with their manufacturing goals and technological capabilities.
Essential Technical Properties and Trade Terminology for cnc machine g code
What Are the Essential Technical Properties of CNC Machine G-Code?
Understanding the essential technical properties of CNC machine G-code is crucial for B2B buyers looking to optimize their manufacturing processes. Here are some critical specifications that every buyer should consider:
1. Precision and Tolerance Levels
Precision in CNC machining refers to how closely a manufactured part meets its specified dimensions. Tolerance levels dictate the acceptable range of deviation from these dimensions. In industries such as aerospace or medical devices, where safety and functionality are paramount, tight tolerances (e.g., ±0.01 mm) are often required. Buyers should ensure that their CNC machines can achieve the necessary precision to meet their specific applications, thereby reducing waste and enhancing product quality.
2. Material Compatibility
CNC machines can work with a variety of materials, including metals, plastics, and composites. Understanding the material compatibility with specific G-codes is essential for buyers to ensure that their machines are capable of processing the desired materials effectively. For instance, harder materials like titanium may require slower feed rates and specialized tooling to prevent damage, impacting production efficiency.
3. Axis Configuration
CNC machines typically operate on three axes (X, Y, and Z), but advanced configurations can include additional axes (A, B, C) for more complex machining operations. Buyers need to consider the axis configuration that best suits their production needs. A five-axis machine allows for more intricate shapes and reduced setup times, which can be a competitive advantage in industries requiring complex geometries.
4. Feed Rates and Speeds
Feed rates determine how quickly the tool moves through the material, while spindle speeds affect the cutting action. These parameters are vital for achieving optimal cutting performance and surface finish. Buyers should examine the machine’s capabilities in terms of maximum feed rates and spindle speeds to ensure they align with their production requirements, particularly for high-volume operations.
5. Control Software Compatibility
The G-code used in CNC machines is often dependent on the control software. Compatibility with industry-standard software can streamline operations and improve workflow. Buyers should verify that the machines they are considering can effectively integrate with their existing CAD/CAM systems to facilitate smoother programming and operation.
What Are Common Trade Terms Associated with CNC G-Code?
Familiarity with industry jargon can significantly enhance communication and negotiation processes for B2B buyers. Here are some common terms related to CNC G-code:
1. OEM (Original Equipment Manufacturer)
An OEM is a company that produces parts and equipment that may be marketed by another manufacturer. In the context of CNC machines, buyers should look for OEMs that provide reliable machinery and support, ensuring long-term operational efficiency.
2. MOQ (Minimum Order Quantity)
MOQ refers to the smallest quantity of a product that a supplier is willing to sell. Understanding MOQ is vital for buyers to optimize inventory levels and manage costs effectively, especially when sourcing components or machines from manufacturers across different regions.
3. RFQ (Request for Quotation)
An RFQ is a document that buyers send to suppliers requesting pricing for specific quantities of products or services. This is a crucial step in the procurement process, allowing buyers to compare costs and negotiate better deals.
4. Incoterms (International Commercial Terms)
Incoterms are a set of rules that define the responsibilities of sellers and buyers regarding the delivery of goods. Understanding these terms is essential for international transactions, as they clarify who is responsible for shipping, insurance, and tariffs, reducing the risk of misunderstandings.
5. CNC (Computer Numerical Control)
CNC refers to the automated control of machining tools through a computer program. This technology is at the core of modern manufacturing, enabling high precision and repeatability in production processes, which is essential for maintaining quality standards.
By grasping these technical properties and trade terminology, B2B buyers can make informed decisions when procuring CNC machinery and components, ultimately leading to improved operational efficiency and competitiveness in the global market.
Navigating Market Dynamics and Sourcing Trends in the cnc machine g code Sector
What are the Current Market Dynamics and Key Trends in the CNC Machine G-Code Sector?
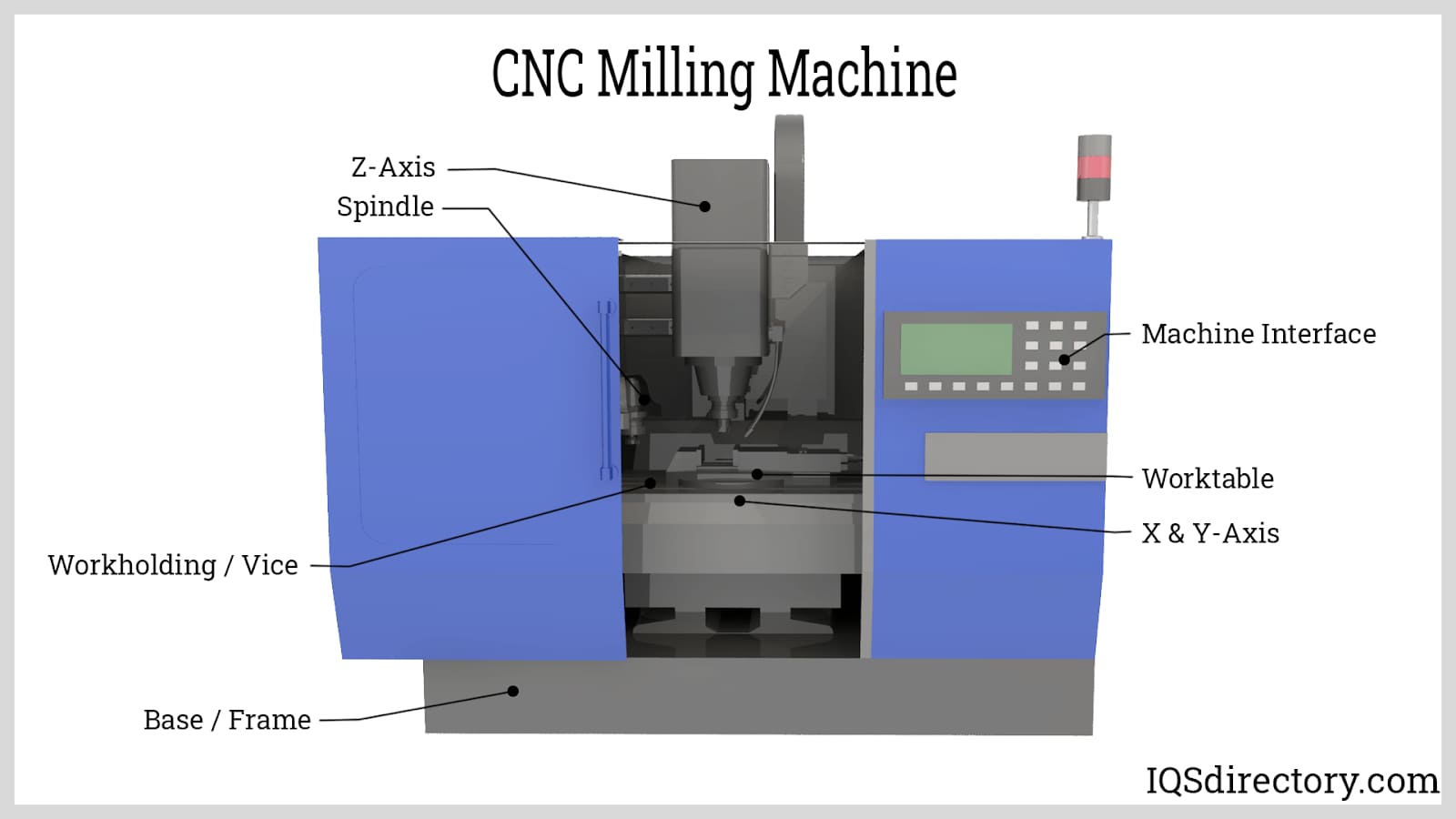
A stock image related to cnc machine g code.
The CNC machine G-Code sector is undergoing significant transformation driven by advancements in technology and the growing demand for precision manufacturing. Key global drivers include the increasing adoption of Industry 4.0 technologies, which integrate IoT and AI into CNC machining processes, enhancing efficiency and accuracy. As international B2B buyers from regions such as Africa, South America, the Middle East, and Europe look to optimize their manufacturing capabilities, they are increasingly sourcing CNC machines equipped with advanced G-Code functionalities that facilitate complex machining tasks.
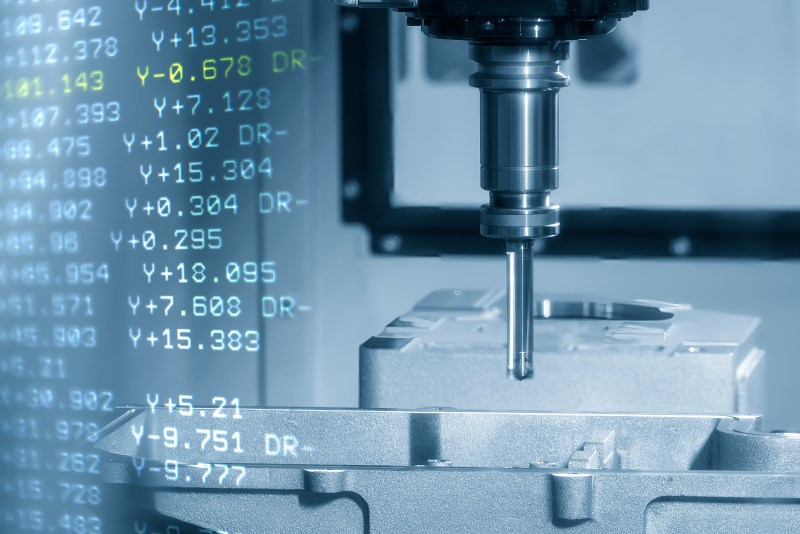
A stock image related to cnc machine g code.
Emerging trends indicate a shift towards automation and smart manufacturing solutions. The incorporation of cloud-based software for G-Code programming and simulation is gaining traction, allowing for real-time adjustments and remote monitoring. This trend not only streamlines the production process but also reduces downtime, making it essential for companies aiming to maintain competitiveness in a fast-paced market. Additionally, as buyers become more environmentally conscious, there is a growing emphasis on sourcing machines that offer energy-efficient operations and reduced material waste.
Moreover, the rise of additive manufacturing techniques, such as 3D printing, is influencing G-Code applications, as hybrid machines that can perform both subtractive and additive processes are becoming more prevalent. This opens new avenues for innovation and product development, particularly in sectors like aerospace and automotive where precision is paramount.
How Can Sustainability and Ethical Sourcing Impact B2B Buyers in the CNC Machine G-Code Sector?
Sustainability is becoming a critical factor for international B2B buyers in the CNC machine G-Code sector. As manufacturers face increasing pressure to minimize their environmental impact, the demand for sustainable practices in sourcing and production is on the rise. Ethical supply chains are not only a moral obligation but also a market differentiator. Buyers should prioritize suppliers who demonstrate a commitment to sustainability through certifications such as ISO 14001, which focuses on effective environmental management systems.
The use of ‘green’ materials and technologies in CNC machining can significantly reduce the ecological footprint of operations. For instance, sourcing machines that utilize biodegradable lubricants or energy-efficient motors can help companies lower their energy consumption and waste output. Additionally, implementing a circular economy approach—whereby materials are reused and recycled—can lead to cost savings and improved resource efficiency.
International buyers should also consider the social aspects of sustainability, such as fair labor practices and community engagement, when selecting suppliers. Collaborating with manufacturers that prioritize ethical practices can enhance brand reputation and appeal to a growing segment of consumers who value corporate responsibility.
What is the Evolution and History of CNC Machine G-Code?
The evolution of CNC machine G-Code has been a pivotal development in the manufacturing sector since its inception in the 1950s. Initially, CNC machining was a manual process where operators used punch cards and basic programming to control machine tools. The introduction of G-Code simplified this process by providing a standardized language for controlling CNC machines, enabling operators to execute complex machining tasks with greater precision.
Over the years, G-Code has evolved to support multi-axis machining and advanced functionalities, such as tool path optimization and automated error correction. This evolution has been driven by the need for increased efficiency and accuracy in manufacturing, particularly as industries demand higher-quality components with tighter tolerances.
As technology continues to advance, the future of G-Code is likely to include further integration with AI and machine learning algorithms, allowing for predictive maintenance and self-optimizing machining processes. This ongoing evolution presents exciting opportunities for international B2B buyers to enhance their manufacturing capabilities and remain competitive in an increasingly globalized market.
Frequently Asked Questions (FAQs) for B2B Buyers of cnc machine g code
-
How do I solve common issues when programming CNC machine G-code?
To troubleshoot programming issues with G-code, start by reviewing the code for syntax errors, incorrect commands, or missing parameters. Ensure that you are using the correct G-code set for your machine, as variations exist among manufacturers. Conduct dry runs without material to observe tool movements and identify potential crashes. If problems persist, consult your machine’s manual or reach out to technical support for guidance tailored to your specific model. -
What is the best G-code library for CNC programming?
The ideal G-code library depends on the specific CNC machine type and its manufacturer. However, universally recognized resources like G-code Tutor or Tormach offer extensive libraries and tutorials suitable for various applications. Additionally, consider libraries that provide examples for different machining processes such as milling, turning, or 3D printing. Always ensure the library is compatible with your machine’s firmware to avoid operational issues. -
How can I verify the quality of G-code before execution?
To ensure the quality of G-code, use simulation software that can visualize the toolpath and movements before executing the program on the machine. This allows you to identify errors or collisions in a virtual environment. Additionally, implementing a peer review process where experienced machinists evaluate the code can enhance quality assurance. Regularly updating your software tools and keeping abreast of best practices in G-code programming also contributes to improved accuracy. -
What are the common customization options for CNC G-code?
Customization options for CNC G-code often include modifying feed rates, tool paths, and setting specific parameters for different machining operations. Many machines allow for user-defined macros, enabling operators to create reusable code snippets for repetitive tasks. Always consult your machine’s documentation for specific commands and options available for customization, as these can vary significantly between different CNC models. -
What minimum order quantity (MOQ) should I expect when sourcing CNC G-code?
The MOQ for CNC G-code services can vary widely based on the supplier and the complexity of the code required. Typically, custom programming services may have a MOQ of one complete project, while bulk G-code files or libraries might require a minimum of 10 or more units. It is advisable to discuss your specific needs with potential suppliers to find a flexible arrangement that suits your production scale. -
What payment terms are standard for international CNC G-code suppliers?
Payment terms for international suppliers can differ, but common arrangements include partial upfront payments (20-50%) with the balance due upon delivery or after successful project completion. Some suppliers may offer payment via letters of credit or escrow services for added security. Always clarify payment options and timelines before finalizing agreements to avoid misunderstandings that could delay your project. -
How can I effectively vet suppliers for CNC G-code services?
To vet suppliers for CNC G-code services, start by assessing their experience and expertise in your specific industry. Request samples of previous work and client references to evaluate their coding quality and reliability. Additionally, verify certifications and compliance with international standards, which can assure you of their operational integrity. Engaging in preliminary conversations about your project can also provide insight into their responsiveness and willingness to collaborate. -
What logistics should I consider when sourcing CNC G-code internationally?
When sourcing CNC G-code internationally, consider shipping times, customs regulations, and potential tariffs that could affect delivery schedules and costs. Ensure that your supplier has a clear logistics plan and provides tracking for your orders. It’s also beneficial to discuss support for potential issues that may arise during transit, such as damage to digital files or delays in delivery. Establishing a reliable communication channel with your supplier can help address logistical challenges promptly.
Important Disclaimer & Terms of Use
⚠️ Important Disclaimer
The information provided in this guide, including content regarding manufacturers, technical specifications, and market analysis, is for informational and educational purposes only. It does not constitute professional procurement advice, financial advice, or legal advice.
While we have made every effort to ensure the accuracy and timeliness of the information, we are not responsible for any errors, omissions, or outdated information. Market conditions, company details, and technical standards are subject to change.
B2B buyers must conduct their own independent and thorough due diligence before making any purchasing decisions. This includes contacting suppliers directly, verifying certifications, requesting samples, and seeking professional consultation. The risk of relying on any information in this guide is borne solely by the reader.
Strategic Sourcing Conclusion and Outlook for cnc machine g code
In navigating the complexities of CNC machine G-code, international B2B buyers must prioritize strategic sourcing to enhance operational efficiency and productivity. Understanding the fundamental G-codes—such as G00 for rapid positioning and G01 for linear interpolation—equips manufacturers with the knowledge to optimize machining processes. Buyers should also consider the compatibility of G-code across various machine brands, ensuring that their investments align with industry standards while facilitating smoother integration into existing workflows.
How Can Strategic Sourcing Enhance Your CNC Operations?
Strategic sourcing not only streamlines procurement but also fosters partnerships with suppliers who can provide technical support, training, and updates on the latest advancements in CNC technology. For businesses in Africa, South America, the Middle East, and Europe, leveraging local suppliers can reduce lead times and shipping costs, enhancing overall supply chain agility.
What Lies Ahead for CNC G-code in Global Markets?
As the demand for precision manufacturing continues to rise, the future of CNC machining looks promising. Investing in G-code training and advanced CNC systems will position companies to capitalize on emerging market opportunities. International buyers are encouraged to engage with technology providers and industry experts to stay ahead of the curve. By prioritizing strategic sourcing in their CNC operations, businesses can not only improve their production capabilities but also drive sustainable growth in an increasingly competitive landscape.