Unlock Efficiency: The Complete Hydraulic Valve Guide (2025)
Introduction: Navigating the Global Market for hydraulic valve
In today’s interconnected world, sourcing high-quality hydraulic valves can be a daunting challenge for international B2B buyers, especially those operating in diverse markets such as Africa, South America, the Middle East, and Europe. With numerous types and specifications available, including directional control valves and solenoid-operated options, navigating this complex landscape requires more than just a basic understanding of hydraulic systems. This guide aims to provide a comprehensive overview of hydraulic valves, covering essential aspects such as types, applications, supplier vetting, and cost considerations.
By delving into the specific needs of various industries—from agriculture to construction—this guide empowers B2B buyers to make informed purchasing decisions that align with their operational requirements. Whether you’re in Poland seeking reliable suppliers or in Colombia evaluating competitive pricing, the insights offered here will help you identify the right hydraulic valve solutions tailored to your unique needs.
Additionally, we’ll explore how to effectively vet suppliers, ensuring that you partner with reputable manufacturers who prioritize quality and compliance with international standards. Armed with this knowledge, you can confidently navigate the global market for hydraulic valves, ultimately enhancing your operations and driving business success.
Understanding hydraulic valve Types and Variations
Type Name | Key Distinguishing Features | Primary B2B Applications | Brief Pros & Cons for Buyers |
---|---|---|---|
Directional Control Valves | Control the direction of hydraulic fluid flow | Construction, Agriculture, Manufacturing | Pros: Versatile in operation; Cons: May require calibration for optimal performance. |
Ball Valves | Simple on/off control with minimal pressure drop | Oil & Gas, Water Treatment | Pros: Durable and reliable; Cons: Limited flow control. |
Solenoid Operated Valves | Electrically controlled for precise operation | Automation, Robotics | Pros: High precision; Cons: Dependency on electrical supply. |
Modular Valves | Customizable configurations for specific applications | Mobile Equipment, Industrial Machinery | Pros: Flexible design; Cons: More complex installation. |
Cartridge Valves | Compact design integrated into larger systems | Aerospace, Heavy Machinery | Pros: Space-saving; Cons: Higher initial cost. |
What are the Characteristics of Directional Control Valves?
Directional control valves are essential in hydraulic systems, as they manage the flow direction of hydraulic fluid. Typically available in multiple spool configurations, they can operate one or more hydraulic actuators. These valves are widely used in sectors such as construction and agriculture, where they facilitate the movement of heavy machinery. When purchasing, buyers should consider the valve’s flow rate, pressure rating, and compatibility with existing systems to ensure optimal functionality.
Why Choose Ball Valves for Your B2B Operations?
Ball valves offer a straightforward solution for on/off control, making them suitable for applications requiring minimal pressure drop. They are commonly utilized in oil and gas industries and water treatment facilities due to their durability and reliability. B2B buyers should assess the valve’s material compatibility with the fluid being handled and consider installation space, as ball valves can be bulkier compared to other options.
How Do Solenoid Operated Valves Enhance Automation?
Solenoid operated valves are favored in automated systems due to their ability to provide precise control over hydraulic flow. These valves respond quickly to electrical signals, making them ideal for applications in robotics and automation. Buyers should ensure that the electrical specifications align with their operational needs and consider the potential requirement for backup power sources to maintain functionality during outages.
What are the Advantages of Modular Valves?
Modular valves offer flexibility and customization, allowing businesses to tailor their hydraulic systems to specific applications. These valves can be reconfigured or expanded as operational needs change, making them suitable for mobile equipment and industrial machinery. When selecting modular valves, buyers should evaluate the ease of installation and the potential for future modifications to maximize return on investment.
Why Consider Cartridge Valves for Space-Constrained Applications?
Cartridge valves are compact and designed to be integrated into larger hydraulic systems, making them ideal for applications in aerospace and heavy machinery. Their space-saving design can help optimize system layout while maintaining performance. However, buyers should be aware of the higher initial costs associated with cartridge valves and ensure that the long-term benefits justify the investment.
Key Industrial Applications of hydraulic valve
Industry/Sector | Specific Application of Hydraulic Valve | Value/Benefit for the Business | Key Sourcing Considerations for this Application |
---|---|---|---|
Agriculture | Control of hydraulic systems in tractors and harvesters | Enhanced efficiency in crop production and reduced downtime | Compatibility with existing machinery and local regulations |
Construction | Operation of excavators and cranes | Improved lifting capacity and operational precision | Durability under extreme conditions and maintenance support |
Manufacturing | Automation of assembly lines | Increased throughput and lower labor costs | Customization options and integration with existing systems |
Mining | Control of hydraulic drills and loaders | Enhanced safety and productivity in harsh environments | High-pressure ratings and reliable performance under load |
Transportation | Hydraulic braking systems in commercial vehicles | Improved safety and compliance with international standards | Sourcing from certified manufacturers with quality assurance |
How Are Hydraulic Valves Used in Agriculture?
In the agriculture sector, hydraulic valves are pivotal for controlling the hydraulic systems in tractors and harvesters. These valves enable precise control over various functions, such as lifting, lowering, and tilting attachments, thus enhancing operational efficiency. For B2B buyers in Africa and South America, sourcing hydraulic valves that meet local agricultural standards and environmental conditions is crucial. Compatibility with existing machinery and ease of maintenance are key considerations to ensure minimal downtime during peak agricultural seasons.
What Role Do Hydraulic Valves Play in Construction?
Hydraulic valves are essential in the construction industry, where they operate heavy machinery like excavators and cranes. These valves facilitate the smooth operation of hydraulic cylinders, allowing for precise lifting and lowering of materials. Buyers in Europe, especially in regions like Poland, should prioritize valves that offer durability and reliability, as construction sites often expose equipment to harsh conditions. Additionally, understanding local regulations regarding equipment safety can guide sourcing decisions, ensuring compliance and operational safety.
How Are Hydraulic Valves Applied in Manufacturing?
In manufacturing, hydraulic valves automate assembly lines, controlling the flow of hydraulic fluid to power machinery. This automation leads to increased throughput and reduced labor costs, making it a critical component for manufacturers aiming for efficiency. For international buyers, particularly from the Middle East, sourcing customizable hydraulic valves that can integrate seamlessly with existing systems is vital. Buyers should also consider the availability of local support and spare parts to minimize operational disruptions.
What Are the Applications of Hydraulic Valves in Mining?
Mining operations rely heavily on hydraulic valves to control drills and loaders, which are essential for excavation and material handling. These valves help enhance safety and productivity in challenging environments. Buyers from Africa and South America must focus on sourcing high-pressure-rated valves that can withstand extreme conditions, such as dust and moisture. Ensuring reliable performance under heavy loads is a priority, as equipment failure can lead to significant downtime and safety hazards.
How Do Hydraulic Valves Enhance Transportation Safety?
In the transportation sector, hydraulic valves are integral to the braking systems of commercial vehicles. They ensure precise control over braking, enhancing safety and compliance with international standards. B2B buyers in Europe should consider sourcing valves from certified manufacturers to guarantee quality and reliability. Additionally, understanding the specific requirements of different vehicle models can aid in selecting the right hydraulic valves, ensuring optimal performance and safety on the roads.
3 Common User Pain Points for ‘hydraulic valve’ & Their Solutions
Scenario 1: Inconsistent Performance of Hydraulic Valves in Heavy Machinery
The Problem:
Many B2B buyers, particularly in sectors like agriculture and construction, face the issue of inconsistent performance from hydraulic valves, which can lead to reduced machinery efficiency. For instance, a buyer may find that the hydraulic valve used in a tractor or excavator does not provide a consistent flow rate, causing the equipment to operate erratically. This inconsistency can lead to increased downtime, affecting productivity and profitability, particularly in competitive markets such as South America and Africa.
The Solution:
To mitigate this issue, buyers should prioritize sourcing high-quality hydraulic valves that meet the specific demands of their machinery. It is crucial to evaluate the specifications such as maximum flow rates (GPM) and pressure ratings (PSI). Look for valves that feature robust construction and are designed for the specific environmental conditions of your region—valves that can withstand high dust or moisture levels are essential in harsh climates. Additionally, consider working with reputable suppliers who offer comprehensive warranties and support. Engaging with local distributors can also provide insights into which valves perform best in your specific applications, ensuring you choose products that enhance the reliability and efficiency of your operations.
Scenario 2: Difficulty in Sourcing Compatible Hydraulic Valves
The Problem:
B2B buyers often encounter challenges in sourcing hydraulic valves that are compatible with their existing systems. This issue is especially prevalent in regions like the Middle East and Europe, where machinery may have been imported from various manufacturers, leading to a patchwork of components that do not easily fit together. A buyer might discover that a valve designed for a specific machine model has different thread sizes or flow specifications, causing delays in repairs and increasing maintenance costs.
The Solution:
To avoid compatibility issues, buyers should conduct thorough research on their existing systems before purchasing new hydraulic valves. This includes documenting the specifications of current valves, such as inlet and outlet port sizes, and understanding the system’s flow requirements. When sourcing new valves, utilize a reliable hydraulic selection guide provided by manufacturers, which can help identify suitable replacements. Additionally, collaborating with engineering consultants or hydraulic specialists can help ensure that the selected valves meet compatibility criteria, thus streamlining the procurement process and minimizing operational disruptions.
Scenario 3: High Maintenance Costs Due to Valve Failures
The Problem:
Frequent valve failures can lead to high maintenance costs, which can be particularly burdensome for B2B buyers operating in industries like mining and manufacturing. Buyers may find that their hydraulic systems experience increased wear and tear, leading to unplanned downtime and costly repairs. For example, a poorly designed valve may fail under pressure, causing fluid leaks and requiring immediate replacement, which disrupts operations and escalates costs.
The Solution:
To address high maintenance costs, it is essential to invest in high-quality hydraulic valves from reputable manufacturers that adhere to international quality standards. Buyers should look for valves with features such as built-in pressure relief mechanisms and enhanced seals that can withstand high-pressure environments. Regular maintenance schedules should also be implemented, including inspections for wear and potential leaks, which can catch issues before they escalate. Additionally, training staff on proper valve operation and maintenance can further reduce the risk of failures, ensuring that the hydraulic systems run efficiently and reliably, ultimately lowering long-term maintenance costs.
Strategic Material Selection Guide for hydraulic valve
What Are the Common Materials Used in Hydraulic Valves?
When selecting hydraulic valves, the material of construction is crucial for ensuring optimal performance and longevity. Here, we analyze four common materials used in hydraulic valve manufacturing: Cast Iron, Aluminum, Stainless Steel, and Brass. Each material has distinct properties, advantages, and limitations that can significantly impact the application and operational efficiency of hydraulic systems.
How Does Cast Iron Perform in Hydraulic Valve Applications?
Key Properties: Cast iron is known for its excellent wear resistance and ability to withstand high pressure and temperature. It typically has a pressure rating of up to 3,600 PSI and can operate effectively in temperatures ranging from -20°F to 400°F.
Pros & Cons: The primary advantage of cast iron is its durability and strength, making it suitable for heavy-duty applications. However, it is relatively heavy, which can complicate installation and increase shipping costs. Additionally, cast iron is prone to corrosion unless properly coated.
Impact on Application: Cast iron valves are often used in industrial applications involving hydraulic fluids with moderate corrosive properties. However, they may not be suitable for aggressive chemicals, limiting their use in specific industries.
Considerations for International Buyers: Buyers should ensure compliance with local standards such as ASTM A48 or DIN 1691. In regions like Africa and South America, where corrosive environments may be prevalent, additional protective coatings may be necessary.
Why Choose Aluminum for Hydraulic Valves?
Key Properties: Aluminum is lightweight and offers good corrosion resistance, making it suitable for applications with lower pressure ratings (typically up to 2,500 PSI) and temperatures up to 250°F.
Pros & Cons: The key advantage of aluminum is its low weight, which simplifies installation and reduces shipping costs. However, it is less durable than cast iron and may not withstand high-pressure applications as effectively. Additionally, aluminum can be more expensive than cast iron.
Impact on Application: Aluminum valves are ideal for mobile equipment and applications where weight savings are critical. However, they may not be suitable for high-pressure hydraulic systems.
Considerations for International Buyers: Buyers should verify compliance with standards such as ASTM B211 or EN 573. In Europe, aluminum valves are often preferred for their lightweight properties in automotive and aerospace applications.
What Benefits Does Stainless Steel Offer in Hydraulic Valve Manufacturing?
Key Properties: Stainless steel is highly resistant to corrosion and can handle extreme temperatures (up to 1,500°F) and pressures (up to 5,000 PSI), making it versatile for various applications.
Pros & Cons: The primary advantage of stainless steel is its longevity and resistance to rust and corrosion, making it suitable for harsh environments. However, it is more expensive than other materials and can be challenging to machine, increasing manufacturing complexity.
Impact on Application: Stainless steel valves are commonly used in food processing, pharmaceuticals, and chemical industries where hygiene and corrosion resistance are paramount.
Considerations for International Buyers: Buyers should ensure compliance with standards such as ASTM A312 or JIS G4303. In the Middle East and Europe, where stringent hygiene standards are enforced, stainless steel is often the preferred choice.
When is Brass the Right Choice for Hydraulic Valves?
Key Properties: Brass offers good corrosion resistance and is suitable for moderate pressure applications (up to 2,000 PSI) and temperatures up to 300°F.
Pros & Cons: The main advantage of brass is its excellent machinability and aesthetic appeal. However, it is less durable than stainless steel and can be more susceptible to dezincification in certain environments.
Impact on Application: Brass valves are often used in plumbing and low-pressure hydraulic systems, particularly where aesthetics matter, such as in decorative fixtures.
Considerations for International Buyers: Buyers should check for compliance with standards such as ASTM B16 or EN 12164. In regions like South America, brass is commonly used in residential applications due to its favorable properties.
Summary Table of Material Selection for Hydraulic Valves
Material | Typical Use Case for Hydraulic Valve | Key Advantage | Key Disadvantage/Limitation | Relative Cost (Low/Med/High) |
---|---|---|---|---|
Cast Iron | Industrial hydraulic systems | High durability and strength | Heavy and prone to corrosion | Medium |
Aluminum | Mobile equipment and lightweight applications | Lightweight and corrosion-resistant | Lower pressure rating | High |
Stainless Steel | Food processing and chemical industries | Excellent corrosion resistance | Higher cost and machining complexity | High |
Brass | Plumbing and low-pressure systems | Good machinability and aesthetics | Susceptible to dezincification | Medium |
This analysis provides a comprehensive overview of the materials used in hydraulic valve manufacturing, helping international B2B buyers make informed decisions based on their specific application needs and regional considerations.
In-depth Look: Manufacturing Processes and Quality Assurance for hydraulic valve
What Are the Main Stages in the Manufacturing Process of Hydraulic Valves?
The manufacturing of hydraulic valves involves several critical stages, each designed to ensure precision and reliability. The main stages include material preparation, forming, assembly, and finishing.
Material Preparation: What Materials Are Used in Hydraulic Valve Manufacturing?
The initial stage in hydraulic valve manufacturing is the selection and preparation of materials. Common materials include high-strength steel, aluminum, and various alloys that can withstand high pressures and corrosive environments. Material selection is crucial as it impacts the valve’s durability and performance.
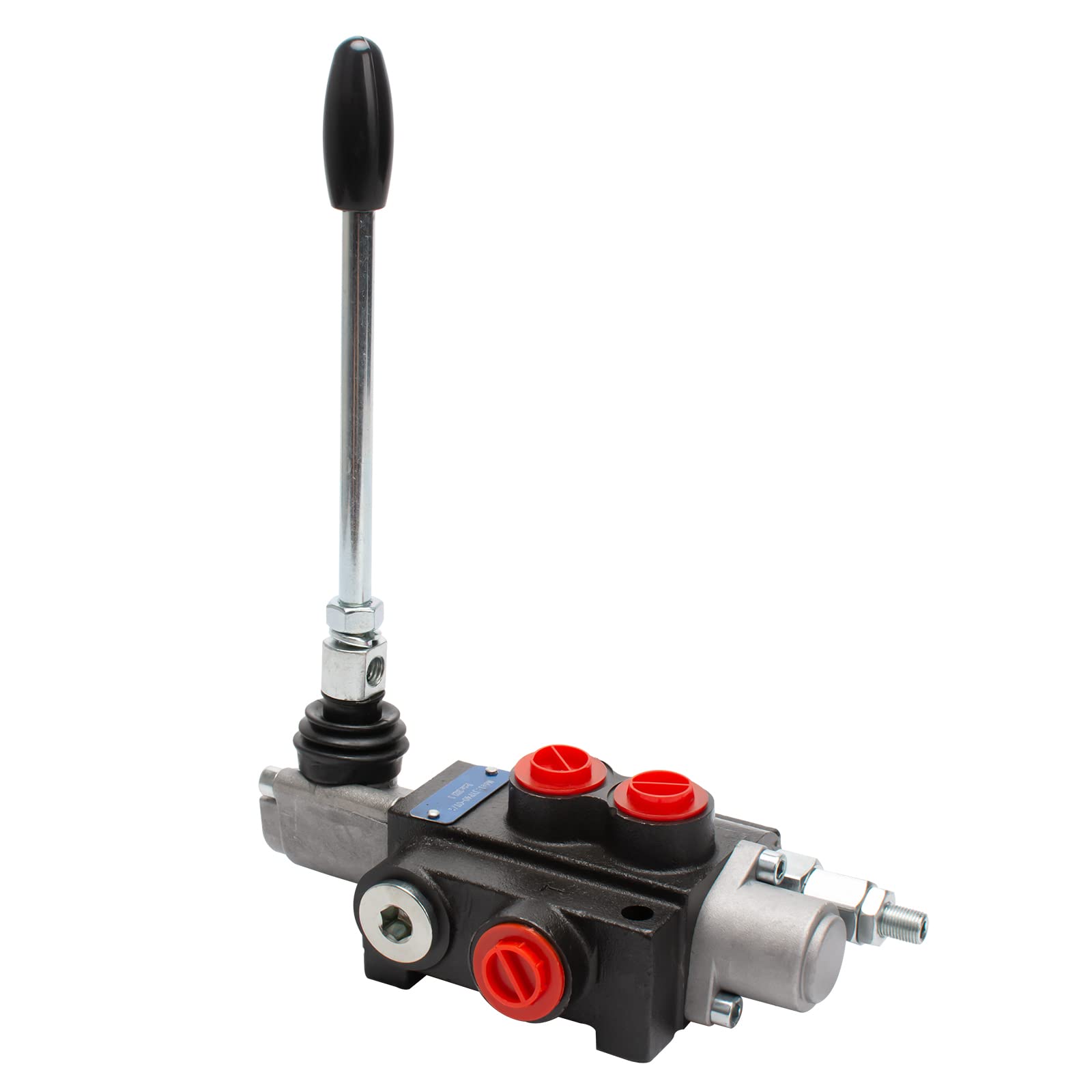
A stock image related to hydraulic valve.
Once the materials are selected, they undergo rigorous quality checks to ensure they meet industry standards. This may include chemical composition analysis and mechanical property testing. Proper material preparation lays the foundation for a reliable hydraulic valve.
How Are Hydraulic Valves Formed?
The forming stage involves shaping the prepared materials into the required components. This can be achieved through various techniques such as machining, casting, and forging. Machining is often used for precision components, while casting may be more suitable for complex shapes.
In addition to traditional methods, advanced technologies like Computer Numerical Control (CNC) machining are increasingly used. CNC machines allow for high precision and repeatability, which are essential for the functionality of hydraulic valves. The formed components must then be checked for dimensional accuracy and surface finish.
What Does the Assembly Process Entail for Hydraulic Valves?
During the assembly stage, the individual components, such as spools, springs, and seals, are brought together to create the final hydraulic valve. This process requires skilled technicians who understand the importance of precision and attention to detail. Each assembly line may have specific protocols to ensure that every valve is assembled according to the design specifications.
Quality checks are integral to the assembly process, including inspections of the assembled components for proper fit and function. Any discrepancies must be addressed before proceeding to the next stage.
Which Finishing Techniques Are Commonly Used in Hydraulic Valve Production?
The finishing stage focuses on enhancing the valve’s surface and preparing it for operational conditions. Common finishing techniques include anodizing, plating, and painting. These processes not only improve aesthetics but also provide corrosion resistance and wear protection.
After finishing, the valves undergo additional quality checks to confirm that the surface treatments meet industry standards. This is crucial for maintaining the longevity and performance of the hydraulic valves in various applications.
What Quality Assurance Measures Are Implemented in Hydraulic Valve Manufacturing?
Quality assurance (QA) is a vital aspect of hydraulic valve production, ensuring that each product meets stringent performance and safety standards.
What Are the Relevant International Standards for Hydraulic Valve Quality Assurance?
Manufacturers often adhere to international quality management standards such as ISO 9001, which provides a framework for consistent quality across all manufacturing processes. In addition, industry-specific certifications like CE marking for European markets and API standards for the oil and gas sector are crucial for compliance.
These standards not only enhance the manufacturer’s credibility but also provide assurance to B2B buyers regarding the quality and safety of the products they are purchasing.
What Are the Key Quality Control Checkpoints in Hydraulic Valve Production?
Quality control (QC) checkpoints are strategically placed throughout the manufacturing process. Key checkpoints include:
- Incoming Quality Control (IQC): This involves inspecting raw materials for compliance with specifications before they enter the production line.
- In-Process Quality Control (IPQC): During the manufacturing stages, random samples are tested for dimensional accuracy and functional performance.
- Final Quality Control (FQC): After assembly, the finished valves undergo rigorous testing, including pressure tests, functional tests, and leak tests to ensure they meet performance criteria.
By incorporating these checkpoints, manufacturers can identify and rectify issues early in the production process, minimizing defects and enhancing overall product quality.
How Can B2B Buyers Verify Supplier Quality Control Practices?
As an international B2B buyer, particularly from regions like Africa, South America, the Middle East, and Europe, verifying a supplier’s quality control practices is crucial for ensuring the reliability of hydraulic valves.
What Methods Can Buyers Use to Audit Supplier Quality Control?
Buyers can conduct supplier audits to assess the manufacturing processes and quality control measures in place. During an audit, buyers should review the supplier’s documentation, including quality manuals, inspection reports, and compliance certifications. Engaging a third-party inspection service can provide an unbiased evaluation of the supplier’s capabilities and adherence to quality standards.
What Documentation Should Buyers Request from Suppliers?
Buyers should request comprehensive quality assurance documentation, including:
- Certificates of compliance with relevant international and industry standards.
- Detailed quality control reports from each production stage.
- Test results from FQC, including pressure and performance tests.
This documentation not only provides assurance of the product’s quality but also helps in making informed purchasing decisions.
What Are the Specific Quality Control Considerations for International B2B Buyers?
International buyers must consider additional factors when evaluating quality control in hydraulic valve manufacturing. These may include:
- Cultural and Regulatory Differences: Understanding local manufacturing practices and regulatory requirements can help buyers navigate potential quality issues.
- Logistics and Supply Chain Management: Assessing the supplier’s logistics capabilities ensures that products can be delivered on time and in compliance with quality standards.
- After-Sales Support and Warranty Policies: Buyers should inquire about warranty coverage and support services to address any potential quality concerns post-purchase.
By taking these considerations into account, B2B buyers can make more informed decisions and build strong partnerships with reliable suppliers in the hydraulic valve industry.
Practical Sourcing Guide: A Step-by-Step Checklist for ‘hydraulic valve’
In the competitive landscape of B2B procurement, sourcing hydraulic valves requires careful consideration and strategic planning. This guide provides a step-by-step checklist to assist international buyers, particularly from Africa, South America, the Middle East, and Europe, in making informed purchasing decisions.
Step 1: Define Your Technical Specifications
Start by clearly outlining the technical requirements of the hydraulic valves needed for your applications. Consider factors such as flow rate (GPM), pressure ratings (PSI), and the number of spools required.
– Flow Rate: Ensure that the valve can handle the maximum flow needed for your machinery.
– Pressure Ratings: Match the valve’s pressure capabilities with your system’s operational pressures to avoid failures.
Step 2: Research Different Valve Types
Familiarize yourself with various hydraulic valve types available in the market, such as directional control valves, ball valves, and solenoid-operated valves. Understanding the distinctions will help you select the right type for your specific application.
– Directional Control Valves: Ideal for controlling the direction of hydraulic fluid.
– Ball Valves: Suitable for on/off applications where flow control is not critical.
Step 3: Evaluate Potential Suppliers
Before making a purchase, conduct thorough due diligence on potential suppliers. Request information such as company profiles, certifications, and client references to assess their reliability.
– Certifications: Check for industry-standard certifications to ensure compliance with safety and quality regulations.
– Client References: Speak to other customers in your industry to gauge their satisfaction with the supplier’s products and services.
Step 4: Compare Pricing and Warranty Options
Gather quotes from multiple suppliers and compare not only the prices but also the warranty options provided. A lower price might not always equate to better value if the warranty coverage is inadequate.
– Warranty Terms: Ensure that the warranty covers defects and provides support for a reasonable period.
– Total Cost of Ownership: Consider long-term costs, including maintenance and potential downtime.
Step 5: Assess Shipping and Delivery Times
Evaluate the logistics capabilities of your chosen suppliers, particularly their shipping options and delivery timelines. Timely delivery is crucial for maintaining production schedules.
– Shipping Methods: Confirm if they offer expedited shipping options if needed.
– Lead Times: Understand the expected lead times for both standard and custom orders.
Step 6: Verify After-Sales Support
After purchasing, reliable after-sales support can significantly impact your operational efficiency. Assess the level of support your supplier provides post-purchase.
– Technical Support: Ensure that the supplier offers technical assistance for installation and troubleshooting.
– Replacement Parts Availability: Check if they provide easy access to replacement parts to minimize downtime.
Step 7: Finalize the Purchase Agreement
Once you have completed your due diligence, finalize the purchase agreement with clear terms and conditions. Ensure that all aspects of the transaction are documented to avoid any misunderstandings later.
– Payment Terms: Clarify payment schedules and methods.
– Return Policy: Understand the return policy in case the product does not meet your specifications.
By following this checklist, B2B buyers can confidently navigate the procurement process for hydraulic valves, ensuring that they select products that meet their operational needs while fostering strong supplier relationships.
Comprehensive Cost and Pricing Analysis for hydraulic valve Sourcing
What are the Key Cost Components in Hydraulic Valve Sourcing?
When sourcing hydraulic valves, understanding the cost structure is essential for international B2B buyers. The primary components include:
-
Materials: The choice of materials, such as steel, aluminum, or specialized alloys, significantly affects the cost. High-quality materials often lead to increased durability and performance but come at a higher price point.
-
Labor: Labor costs can vary by region. For example, manufacturing in countries with lower labor costs can result in significant savings. However, the expertise required for precision engineering in hydraulic valves may necessitate skilled labor, impacting overall expenses.
-
Manufacturing Overhead: This includes costs associated with running manufacturing facilities, such as utilities, rent, and administrative expenses. Efficient production processes can reduce these overhead costs, benefiting the buyer.
-
Tooling: Custom tooling for specific valve designs can be a substantial upfront investment. Buyers should consider whether the supplier has the necessary tooling capabilities to avoid additional costs later.
-
Quality Control (QC): Implementing strict QC measures ensures product reliability but may increase costs. Buyers should assess the value of these measures against potential failure costs.
-
Logistics: Shipping, customs duties, and transportation costs can significantly affect pricing, especially for international buyers. Understanding Incoterms is crucial to anticipating total logistics expenses.
-
Margin: Suppliers typically include a profit margin in their pricing. This can vary based on the supplier’s market position, competitive landscape, and perceived value of their products.
How Do Pricing Influencers Impact Hydraulic Valve Costs?
Several factors influence the pricing of hydraulic valves, particularly for international buyers:
-
Volume/MOQ: Purchasing in larger volumes can lead to price reductions. Many suppliers offer tiered pricing based on Minimum Order Quantities (MOQs), which can significantly lower the cost per unit.
-
Specifications and Customization: Custom designs or specific performance criteria may increase costs. Buyers should clearly define their requirements to avoid unnecessary expenses.
-
Materials and Quality Certifications: Valves made from premium materials or those that meet specific industry certifications (e.g., ISO, ANSI) often command higher prices. Ensure that the investment aligns with operational needs.
-
Supplier Factors: The reputation and reliability of the supplier can influence costs. Established suppliers may charge more due to their track record, while emerging suppliers might offer competitive rates to gain market share.
-
Incoterms: Understanding shipping terms can help in estimating total costs. For instance, FOB (Free on Board) pricing may seem lower than CIF (Cost, Insurance, and Freight), but the latter includes transportation costs, which can add up significantly.
What Buyer Tips Can Help Optimize Hydraulic Valve Sourcing?
To enhance cost-efficiency in sourcing hydraulic valves, international buyers should consider the following strategies:
-
Negotiate Effectively: Leverage volume commitments or long-term contracts to negotiate better pricing. Building a relationship with suppliers can also yield better terms and conditions.
-
Evaluate Total Cost of Ownership (TCO): Beyond the initial purchase price, consider maintenance, operational costs, and potential downtime when evaluating suppliers. A higher upfront cost may be justified by lower long-term operational costs.
-
Understand Pricing Nuances: Be aware of regional pricing differences. For instance, hydraulic valves sourced from Europe may come with higher labor costs but offer superior quality. In contrast, products from South America or Africa might be more competitively priced but vary in quality.
-
Seek Multiple Quotes: Always obtain quotes from multiple suppliers to ensure competitive pricing. This practice not only aids in cost comparison but also provides insights into market standards.
-
Stay Informed on Market Trends: Regularly review market conditions, material costs, and technological advancements. This knowledge can provide leverage in negotiations and help anticipate price changes.
Disclaimer on Indicative Prices
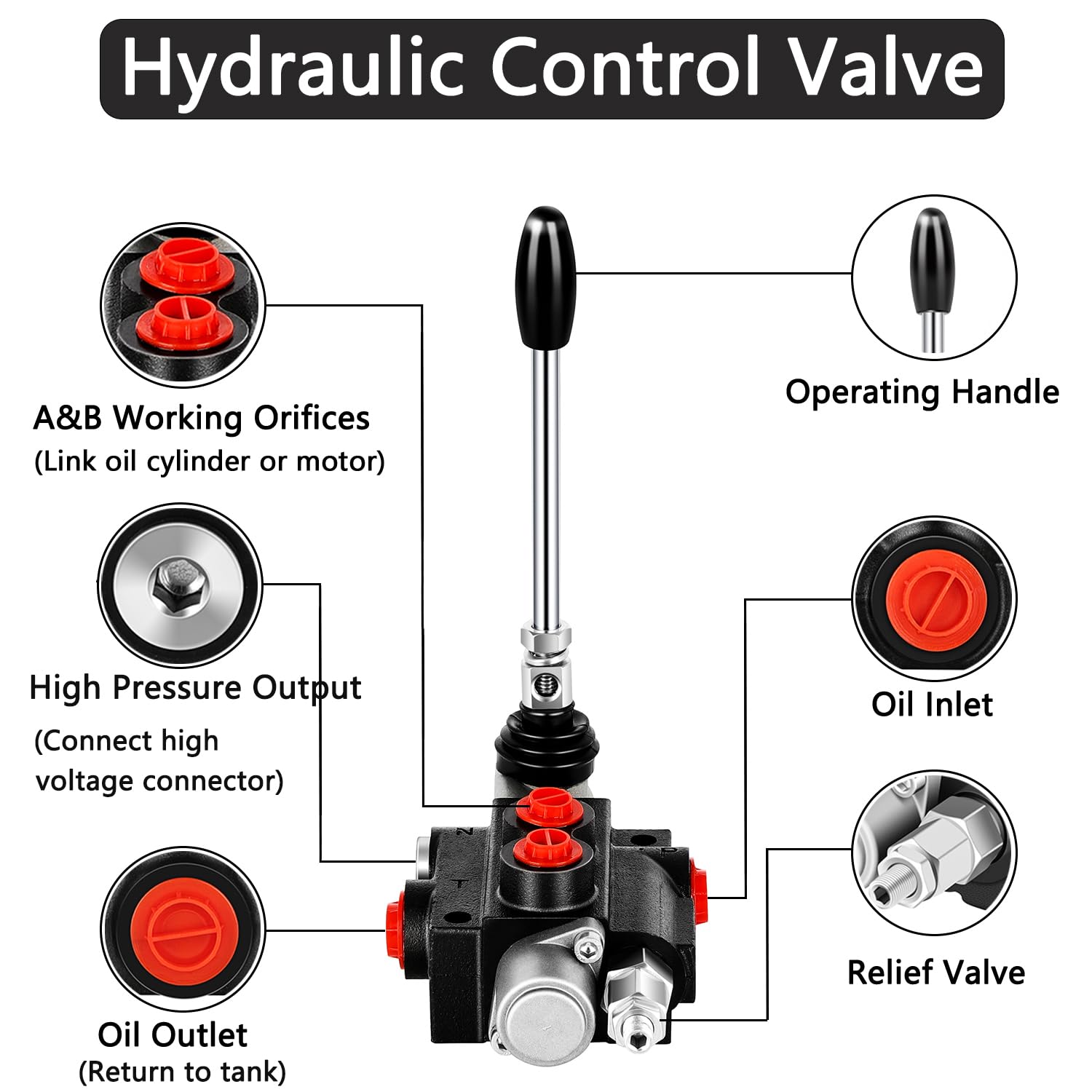
A stock image related to hydraulic valve.
Prices for hydraulic valves can fluctuate based on market conditions, supplier changes, and raw material costs. The figures referenced in this guide are indicative and should be confirmed with suppliers for accurate quotations tailored to specific needs.
Alternatives Analysis: Comparing hydraulic valve With Other Solutions
Understanding Alternative Solutions to Hydraulic Valves
In the realm of fluid control and motion, hydraulic valves are a common choice due to their efficiency and reliability. However, various alternative solutions exist that can meet similar operational needs. This section explores the comparative aspects of hydraulic valves against two viable alternatives: Pneumatic Valves and Electric Actuators. Each of these options has unique advantages and disadvantages that can influence a B2B buyer’s decision based on specific operational requirements.
Comparison Table of Hydraulic Valves and Alternatives
Comparison Aspect | Hydraulic Valve | Pneumatic Valves | Electric Actuators |
---|---|---|---|
Performance | High pressure and flow control | Rapid response, lower pressure | Precise control, low speed |
Cost | Moderate initial cost | Generally lower cost | Higher initial investment |
Ease of Implementation | Requires hydraulic system setup | Easier integration into existing systems | Complex wiring may be needed |
Maintenance | Regular maintenance required | Lower maintenance needs | Minimal maintenance, but complex |
Best Use Case | Heavy machinery, construction | Packaging, food processing | Robotics, automated systems |
Detailed Breakdown of Alternatives
What Are the Advantages and Disadvantages of Pneumatic Valves?
Pneumatic valves utilize compressed air to operate and are known for their quick response times. They are typically less expensive than hydraulic valves and are easier to integrate into existing systems without the need for extensive hydraulic setups. However, their performance is limited to lower pressures compared to hydraulic systems, making them less suitable for heavy-duty applications. Industries such as packaging and food processing often favor pneumatic solutions due to their cleanliness and speed, but they may not provide the necessary force required in heavy machinery.
How Do Electric Actuators Compare to Hydraulic Valves?
Electric actuators convert electrical energy into mechanical motion, offering precise control over movement. They are particularly advantageous in applications where accuracy and repeatability are essential, such as in robotics and automated systems. While they require a higher initial investment and may involve complex wiring, electric actuators demand minimal maintenance compared to hydraulic systems. However, they typically operate at lower speeds and may not handle the same heavy loads as hydraulic valves, making them less ideal for construction or heavy machinery applications.
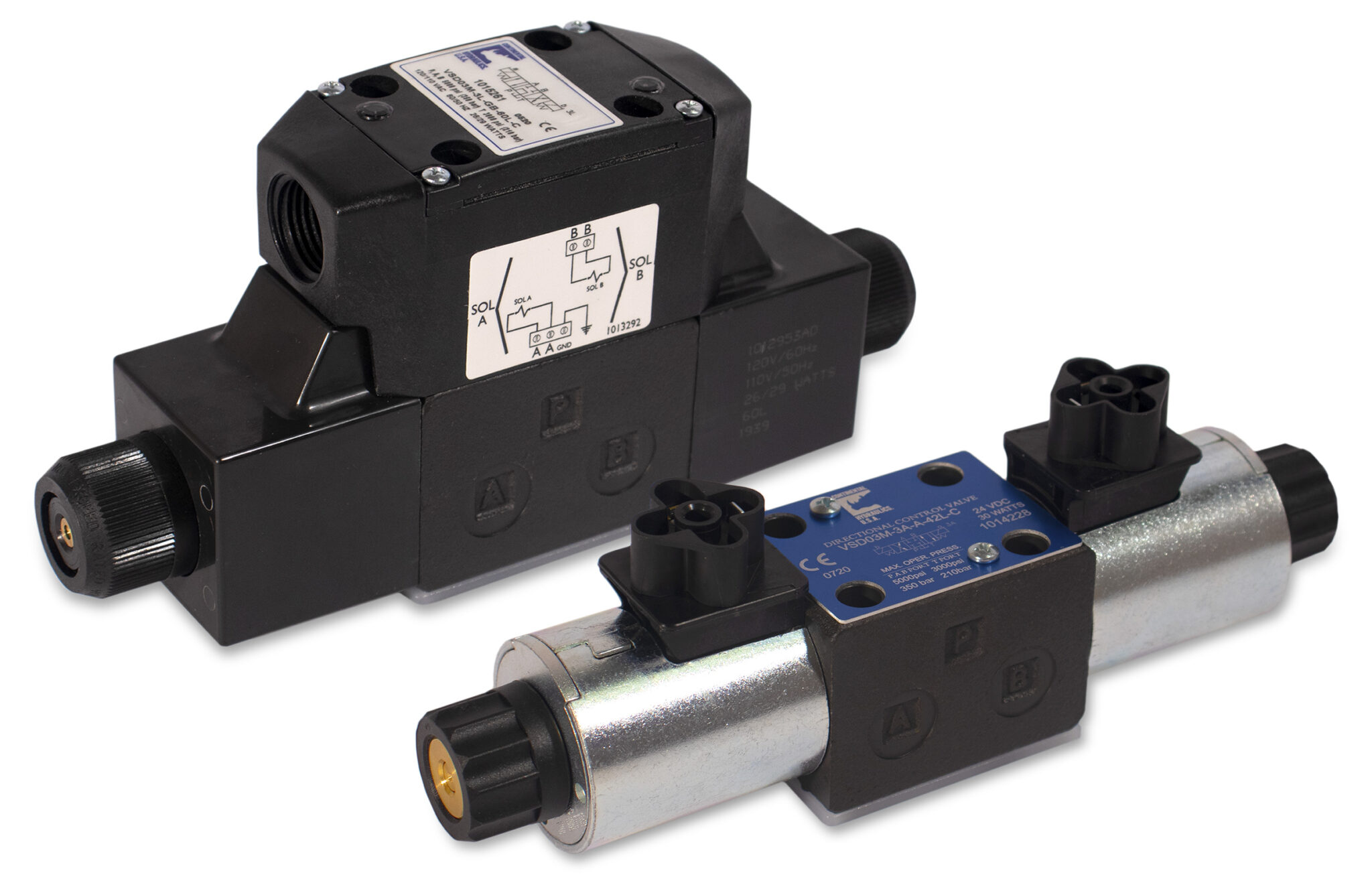
A stock image related to hydraulic valve.
How Can B2B Buyers Choose the Right Solution?
When selecting between hydraulic valves, pneumatic valves, and electric actuators, B2B buyers should carefully assess their operational needs. Considerations should include the specific application requirements, budget constraints, and the existing infrastructure. Hydraulic valves may be the best choice for heavy-duty applications requiring high pressure and flow control, while pneumatic valves offer a cost-effective and efficient solution for lighter tasks. Electric actuators provide precision for automated processes but at a higher initial cost. By evaluating these factors, buyers can make informed decisions that align with their operational goals.
Essential Technical Properties and Trade Terminology for hydraulic valve
What Are the Essential Technical Properties of Hydraulic Valves?
When sourcing hydraulic valves, international B2B buyers must understand the critical specifications that dictate performance and compatibility. Here are some essential technical properties to consider:
1. Maximum Flow Rate (GPM)
The maximum flow rate, measured in gallons per minute (GPM), indicates how much hydraulic fluid can pass through the valve. This property is crucial for ensuring that the hydraulic system can operate efficiently under various loads. Buyers should assess their system’s requirements to select a valve that meets or exceeds the necessary flow rate to prevent performance bottlenecks.
2. Maximum Pressure Rating (PSI)
The maximum pressure rating, expressed in pounds per square inch (PSI), indicates the highest pressure the valve can withstand without failure. Selecting a valve with an appropriate pressure rating is vital to ensure safety and reliability in high-stress applications. Buyers must consider the operational pressure of their systems to avoid costly failures or downtime.
3. Number of Spools
The number of spools on a hydraulic valve determines how many cylinders or motors can be controlled simultaneously. Each spool corresponds to a specific function, such as extending or retracting a cylinder. Understanding the number of spools required for your application is essential for optimizing system performance and ensuring proper functionality.
4. Inlet and Outlet Port Sizes
Inlet and outlet port sizes dictate how the valve connects to the hydraulic system. Common sizes include SAE thread specifications, which must align with the existing components in the hydraulic circuit. Ensuring compatibility in port sizes is critical to avoid leaks and inefficiencies, making this a significant consideration during procurement.
5. Material Grade
The material grade of a hydraulic valve influences its durability, corrosion resistance, and overall performance. Common materials include steel and aluminum, each suited for different environments and applications. Buyers should evaluate the operating conditions, such as temperature and exposure to chemicals, to choose a valve made from the appropriate material.
6. Tolerance and Precision
Tolerance refers to the allowable variation in the dimensions of the valve components. High precision and tight tolerances are crucial for the valve’s performance, particularly in applications requiring exact fluid control. Buyers should prioritize valves with appropriate tolerances to ensure seamless integration and operation within their hydraulic systems.
What Common Trade Terms Should B2B Buyers Know?
Understanding industry jargon is essential for effective communication and negotiation in the hydraulic valve market. Here are some common terms:
1. OEM (Original Equipment Manufacturer)
An OEM is a company that produces parts or equipment that may be marketed by another manufacturer. In the context of hydraulic valves, buyers often seek OEM parts to ensure compatibility and reliability within their systems.
2. MOQ (Minimum Order Quantity)
MOQ refers to the smallest quantity of a product that a supplier is willing to sell. This term is crucial for buyers to understand as it impacts inventory management and overall purchasing costs. Buyers should negotiate MOQs that align with their operational needs.
3. RFQ (Request for Quotation)
An RFQ is a document sent to suppliers to request pricing information for specific products or services. This process helps buyers compare costs and terms from multiple suppliers, facilitating informed purchasing decisions in the hydraulic valve market.
4. Incoterms
Incoterms are international commercial terms that define the responsibilities of buyers and sellers in shipping agreements. Familiarity with these terms is essential for international B2B buyers to understand shipping costs, risk transfer, and delivery obligations.
5. Lead Time
Lead time is the duration between placing an order and receiving the product. Understanding lead times is critical for B2B buyers to manage project timelines and avoid delays in their operations.
6. Certification Standards
Certification standards ensure that hydraulic valves meet specific quality and safety requirements. Common certifications include ISO and CE marks, which can be essential for buyers to verify compliance and reliability in their procurement processes.
By grasping these essential technical properties and trade terms, B2B buyers can make informed decisions that enhance the efficiency and reliability of their hydraulic systems.
Navigating Market Dynamics and Sourcing Trends in the hydraulic valve Sector
What Are the Current Market Dynamics and Key Trends in the Hydraulic Valve Sector?
The hydraulic valve market is experiencing significant growth driven by increased demand in industries such as construction, agriculture, and manufacturing. Global drivers include the rise in automation and the need for efficient hydraulic systems to enhance productivity. In regions like Africa and South America, infrastructure development and urbanization are propelling the demand for hydraulic solutions. Meanwhile, in Europe and the Middle East, there is a strong push toward modernizing existing hydraulic systems to improve efficiency and reduce operational costs.
Emerging B2B technologies such as IoT (Internet of Things) and Industry 4.0 are transforming how hydraulic systems are designed and operated. These advancements enable real-time monitoring and predictive maintenance, which can significantly minimize downtime and enhance productivity. Additionally, suppliers are increasingly adopting e-commerce platforms to streamline the procurement process, making it easier for international buyers to source hydraulic valves. For instance, digital marketplaces allow buyers from Poland or Colombia to compare products and prices from various manufacturers quickly.
Another noteworthy trend is the shift towards modular designs in hydraulic valves, which facilitates easier integration and customization. This trend is particularly beneficial for B2B buyers looking to optimize their hydraulic systems for specific applications, thereby enhancing their operational efficiency. As sustainability becomes a priority, manufacturers are also focusing on producing energy-efficient hydraulic valves that reduce energy consumption and emissions.
How Can Sustainability and Ethical Sourcing Impact B2B Buyers in the Hydraulic Valve Market?
Sustainability is increasingly influencing purchasing decisions in the hydraulic valve sector. B2B buyers must consider the environmental impact of their sourcing choices, as industries are under growing pressure to reduce their carbon footprint. This includes evaluating the lifecycle of hydraulic valves, from material sourcing to manufacturing processes and end-of-life disposal.
Ethical supply chains are becoming essential for international buyers, particularly in Africa and South America, where local communities are affected by industrial activities. Buyers are encouraged to seek suppliers who adhere to fair labor practices and environmental regulations. Furthermore, certifications such as ISO 14001 for environmental management and ISO 45001 for occupational health and safety are indicators of a supplier’s commitment to sustainable practices.
The use of eco-friendly materials in hydraulic valve production is gaining traction. Manufacturers are exploring alternatives to traditional materials that are more sustainable and recyclable. For example, valves made from composite materials may provide the same performance with a lower environmental impact. B2B buyers who prioritize these factors not only enhance their corporate social responsibility (CSR) profiles but also align with global sustainability goals.
What Is the Brief Evolution of the Hydraulic Valve Industry?
The hydraulic valve industry has evolved significantly over the past century. Initially, hydraulic systems were primarily mechanical, relying on simple valve designs that offered limited control and efficiency. The introduction of hydraulic fluid technology in the early 20th century revolutionized the industry, allowing for more precise control of fluid dynamics.
As industrial needs grew, so did the complexity and functionality of hydraulic valves. The late 20th century saw the emergence of electronic controls and smart valves, enabling advanced automation and integration with computer systems. Today, the industry is at the forefront of innovation, focusing on digital solutions and sustainable practices. This evolution not only improves performance but also meets the increasing demands for energy efficiency and eco-friendliness in hydraulic systems.
In summary, B2B buyers navigating the hydraulic valve market must stay informed about current trends, prioritize sustainability, and understand the historical context to make informed purchasing decisions.
Frequently Asked Questions (FAQs) for B2B Buyers of hydraulic valve
-
How do I choose the right hydraulic valve for my application?
Selecting the right hydraulic valve involves considering several factors: flow rate, pressure rating, valve type (e.g., directional control, pressure relief), and compatibility with your hydraulic system. Evaluate the maximum flow (GPM) and pressure (PSI) your application requires. Additionally, consider whether you need a manual or solenoid-operated valve. Consulting with suppliers about your specific needs can help you make an informed decision and ensure optimal performance. -
What is the best hydraulic valve for heavy-duty applications?
For heavy-duty applications, look for valves that can handle higher flow rates and pressures, such as those rated above 3,000 PSI. Options like proportional valves or robust directional control valves with multiple spools are often ideal. Brands with a proven track record in industrial applications, such as Danfoss or Bailey Hydraulics, typically provide valves designed for durability and reliability under extreme conditions. -
What should I consider when sourcing hydraulic valves internationally?
When sourcing hydraulic valves internationally, consider factors such as supplier reputation, product certifications, and compliance with local regulations. It’s also essential to assess the supplier’s ability to provide technical support and after-sales service. Evaluate logistics aspects, including shipping times, import duties, and warranty terms. Engaging in communication with potential suppliers can clarify these points and help you establish a trustworthy partnership. -
How can I vet potential suppliers for hydraulic valves?
To vet suppliers, start by checking their industry reputation through reviews, testimonials, and case studies. Request references from other clients, especially those in your region. Verify their certifications, such as ISO or CE compliance, to ensure quality standards. Conduct a factory visit if possible, or utilize third-party inspection services to assess their manufacturing capabilities. This due diligence can mitigate risks associated with international sourcing. -
What customization options are available for hydraulic valves?
Customization options for hydraulic valves often include modifications in flow rates, pressure settings, valve sizes, and spool configurations. Some manufacturers offer tailored solutions to meet specific application needs, such as special coatings for corrosion resistance or unique port sizes for compatibility with existing systems. Discuss your requirements with suppliers early in the procurement process to explore available customization options. -
What are the minimum order quantities (MOQs) for hydraulic valves?
Minimum order quantities (MOQs) for hydraulic valves can vary significantly among suppliers, typically ranging from a few units to several hundred. Smaller suppliers might accommodate lower MOQs to attract new customers, while larger manufacturers often set higher thresholds to optimize production efficiency. Always clarify MOQs during negotiations to ensure they align with your purchasing strategy and budget. -
What payment terms should I negotiate with suppliers?
Negotiating favorable payment terms is crucial for international transactions. Common terms include partial upfront payments, letters of credit, or net 30/60 terms. Aim for terms that provide a balance between cash flow management and supplier security. Additionally, consider the currency exchange risks and ensure that payment methods align with your company’s financial policies and capabilities. -
How can I ensure quality assurance for hydraulic valves?
To ensure quality assurance, inquire about the supplier’s quality control processes, including testing and inspection protocols. Request documentation such as material certifications, test reports, and compliance certificates. Establish clear acceptance criteria and consider third-party quality inspections before shipment. Building a quality assurance plan in collaboration with your supplier can significantly enhance the reliability of the hydraulic valves you procure.
Important Disclaimer & Terms of Use
⚠️ Important Disclaimer
The information provided in this guide, including content regarding manufacturers, technical specifications, and market analysis, is for informational and educational purposes only. It does not constitute professional procurement advice, financial advice, or legal advice.
While we have made every effort to ensure the accuracy and timeliness of the information, we are not responsible for any errors, omissions, or outdated information. Market conditions, company details, and technical standards are subject to change.
B2B buyers must conduct their own independent and thorough due diligence before making any purchasing decisions. This includes contacting suppliers directly, verifying certifications, requesting samples, and seeking professional consultation. The risk of relying on any information in this guide is borne solely by the reader.
Strategic Sourcing Conclusion and Outlook for hydraulic valve
In navigating the complex landscape of hydraulic valve sourcing, international B2B buyers must prioritize strategic sourcing practices to enhance operational efficiency and cost-effectiveness. Understanding the various types of hydraulic valves—such as directional control, ball, and modular valves—enables buyers to align their specific needs with the right product features. Key considerations include flow rates, pressure ratings, and compatibility with existing systems, which are crucial for ensuring optimal performance in diverse applications across sectors like agriculture and construction.
How Can Buyers Optimize Their Hydraulic Valve Procurement?
To maximize value, buyers should engage with suppliers who offer transparency in pricing, warranty policies, and delivery timelines. Establishing relationships with reputable manufacturers can lead to better negotiation leverage and access to innovative solutions tailored to regional challenges. Additionally, exploring local and international suppliers can enhance sourcing flexibility and reduce lead times, especially in markets like Africa and South America, where logistics can present unique challenges.
What’s Next for International Buyers in the Hydraulic Valve Market?
As the global demand for hydraulic systems continues to grow, international buyers must stay abreast of industry trends and technological advancements. Emphasizing the importance of strategic sourcing will not only improve procurement outcomes but also position businesses for future success. Take the next step by evaluating your sourcing strategies today—ensure you are equipped to meet the evolving demands of your industry while fostering sustainable partnerships that drive innovation and efficiency.