Unlock Efficiency: The Complete NEMA Connector Chart (2025)
Introduction: Navigating the Global Market for nema connector chart
Navigating the global market for NEMA connectors can be a daunting task for international B2B buyers, especially when considering the diverse applications and specifications required across different regions. Understanding the NEMA connector chart is crucial for sourcing the right connectors that meet your operational needs, whether you’re in the industrial sector in South America or managing commercial projects in Europe. This guide serves as a comprehensive resource, covering various types of NEMA connectors, their applications, and critical factors such as supplier vetting and cost considerations.
International buyers face unique challenges, including compatibility issues, safety standards, and sourcing reliable suppliers in their regions. By delving into this guide, you will gain insights into the different configurations of NEMA connectors, both locking and non-locking, along with their respective voltage and current ratings. Additionally, we provide actionable tips on how to evaluate suppliers effectively and ensure that you are investing in quality products that adhere to local regulations.
This guide is designed to empower B2B buyers from Africa, South America, the Middle East, and Europe, equipping you with the knowledge needed to make informed purchasing decisions. Whether you are operating in Kenya, Australia, or any other part of the world, understanding the intricacies of NEMA connectors will enhance your procurement strategy and ultimately drive operational efficiency.
Understanding nema connector chart Types and Variations
Type Name | Key Distinguishing Features | Primary B2B Applications | Brief Pros & Cons for Buyers |
---|---|---|---|
Non-Locking Plugs | Simple plug-in design, typically used in residential settings. Voltage ratings of 125V to 250V, current ratings up to 60A. | Household appliances, light commercial use. | Pros: Easy to use, widely available. Cons: Less secure connection, may disconnect under vibration. |
Locking Plugs | Twist-and-lock mechanism for a secure connection. Available in voltages up to 480V and current ratings up to 50A. | Industrial applications, outdoor equipment. | Pros: High safety, prevents accidental disconnections. Cons: More complex installation, potentially higher cost. |
Straight Blade Connectors | Flat, easily connected blades, versatile for various amperages and voltages. Commonly seen in NEMA 1-15 to NEMA 5-50 configurations. | General-purpose applications, from home to light industrial. | Pros: Versatile and compatible with many devices. Cons: Lower amperage limits compared to locking types. |
Multi-Pole Connectors | Designed for three-phase systems, typically rated for higher voltages and currents. Common configurations include NEMA L14-30 and L18-30. | Heavy machinery, industrial power supply. | Pros: Supports higher loads and complex systems. Cons: More expensive, requires careful installation. |
Weatherproof Connectors | Enhanced protection against environmental factors, often used in outdoor settings. Includes locking features and higher voltage ratings. | Outdoor equipment, construction sites. | Pros: Durable and reliable in harsh conditions. Cons: Bulkier design, may require specialized installation. |
What Are Non-Locking Plugs and Their B2B Relevance?
Non-locking plugs are characterized by their straightforward plug-in design, making them ideal for residential and light commercial applications. They typically support voltage ratings between 125V and 250V and have current ratings that can reach up to 60A. These connectors are widely available and easy to use, making them a go-to choice for many B2B buyers looking for reliable solutions for household appliances or light machinery. However, their less secure connection may lead to accidental disconnections, particularly in high-vibration environments.
Why Choose Locking Plugs for Industrial Applications?
Locking plugs offer a twist-and-lock mechanism that ensures a secure connection, making them suitable for industrial applications and outdoor equipment. They can handle voltages up to 480V and current ratings up to 50A, providing a safe solution for high-demand environments. B2B buyers may prefer these connectors due to their high safety standards, which prevent accidental disconnections. However, the complexity of installation and potentially higher costs might be a consideration for some businesses.
How Do Straight Blade Connectors Serve Diverse Applications?
Straight blade connectors feature flat blades and are versatile enough to accommodate various amperages and voltages, ranging from NEMA 1-15 to NEMA 5-50 configurations. Their general-purpose nature makes them suitable for a wide array of applications, from household devices to light industrial equipment. Buyers appreciate their compatibility with many devices and ease of use, although the lower amperage limits compared to locking types may restrict their use in heavy-duty applications.
What Are the Benefits of Multi-Pole Connectors in Heavy Machinery?
Multi-pole connectors are specifically designed for three-phase systems and are commonly used in industrial settings, supporting higher voltages and currents. Configurations like NEMA L14-30 and L18-30 are typical in heavy machinery and industrial power supplies. These connectors are ideal for B2B buyers needing to support substantial loads and complex electrical systems. However, their higher cost and the requirement for careful installation may be factors to consider.
How Do Weatherproof Connectors Enhance Outdoor Equipment Reliability?
Weatherproof connectors provide enhanced protection against environmental factors, making them suitable for outdoor applications like construction sites. They often feature locking mechanisms and can handle higher voltage ratings. B2B buyers benefit from their durability and reliability in harsh conditions, ensuring that outdoor equipment remains operational. However, their bulkier design and specialized installation requirements may pose challenges for some businesses.
Key Industrial Applications of nema connector chart
Industry/Sector | Specific Application of NEMA Connector Chart | Value/Benefit for the Business | Key Sourcing Considerations for this Application |
---|---|---|---|
Manufacturing | Power supply for machinery and equipment | Ensures reliable and safe connections for high-load operations | Compliance with local electrical standards and certifications |
Construction | Temporary power distribution for construction sites | Facilitates quick and safe connections for tools and machinery | Durability and weather resistance for outdoor applications |
Renewable Energy | Interconnection of solar panels and inverters | Supports efficient energy transfer and system performance | Compatibility with various voltage and amperage requirements |
Transportation | Charging stations for electric vehicles | Enhances accessibility and reliability of charging infrastructure | Adaptability to different vehicle types and charging standards |
Data Centers and IT Facilities | Power distribution for servers and networking equipment | Minimizes downtime and ensures continuous operation of critical systems | High-quality connectors to withstand constant use and vibration |
How is the NEMA Connector Chart Utilized in Manufacturing?
In the manufacturing sector, the NEMA connector chart is critical for ensuring that machinery and equipment receive the appropriate power supply. Many industrial machines require high amperage and specific voltage configurations, making it essential for buyers to select the right NEMA connectors. This chart helps mitigate risks associated with electrical mismatches, which can lead to equipment failure or safety hazards. Buyers should prioritize sourcing connectors that comply with local electrical standards to ensure safety and reliability in their operations.
What Role Does the NEMA Connector Chart Play in Construction?
Construction sites often require temporary power distribution to run various tools and machinery. The NEMA connector chart provides essential guidance on selecting the right connectors for these applications, ensuring that power supply is both safe and efficient. By using the correct configurations, businesses can minimize downtime and enhance productivity. Sourcing considerations should include the durability and weather resistance of connectors, especially since they are frequently exposed to harsh environmental conditions.
How is the NEMA Connector Chart Beneficial for Renewable Energy Projects?
In the renewable energy sector, particularly solar energy, the NEMA connector chart assists in the interconnection of solar panels and inverters. Correctly configured connectors facilitate efficient energy transfer, which is crucial for maximizing system performance. Buyers must consider compatibility with various voltage and amperage requirements, ensuring that connectors can handle the specific demands of solar installations. This attention to detail can significantly impact energy efficiency and system reliability.
Why is the NEMA Connector Chart Important for Electric Vehicle Charging Stations?
The rise of electric vehicles has necessitated the establishment of reliable charging infrastructure. The NEMA connector chart aids in the design and implementation of charging stations, ensuring that they meet the varied power requirements of different vehicle types. By selecting the appropriate connectors, businesses can improve the accessibility and reliability of their charging stations. Key sourcing considerations include the adaptability of connectors to various vehicle types and compliance with international charging standards.
How Does the NEMA Connector Chart Enhance Data Center Operations?
In data centers and IT facilities, the NEMA connector chart is vital for the power distribution of servers and networking equipment. Ensuring that the right connectors are used minimizes the risk of downtime, which is critical for maintaining operational continuity. Buyers should focus on sourcing high-quality connectors designed to withstand constant use and vibration, as these environments are often demanding. This careful consideration can lead to improved reliability and efficiency in data management operations.
3 Common User Pain Points for ‘nema connector chart’ & Their Solutions
Scenario 1: Incompatibility Between Equipment and NEMA Connectors
The Problem: A B2B buyer in the Middle East is tasked with sourcing electrical equipment for a new manufacturing facility. Upon reviewing the NEMA connector chart, they realize that the connectors used in their equipment do not align with standard NEMA configurations. This misalignment leads to delays, as the buyer must find adapters or alternative solutions, increasing project timelines and costs. Additionally, the potential for mismatched connections raises safety concerns, especially in an industrial environment where equipment reliability is critical.
The Solution: To avoid such compatibility issues, B2B buyers should conduct a thorough analysis of their equipment’s electrical requirements before making a purchase. This includes checking the voltage, amperage, and the specific NEMA configuration used in each piece of machinery. When consulting the NEMA connector chart, buyers should note the configuration codes and corresponding specifications, ensuring they match their equipment. It is advisable to maintain a list of required NEMA configurations that can be easily referenced during procurement. Buyers can also reach out to manufacturers or distributors for guidance on the best-fit connectors for their specific equipment, ensuring that all components work seamlessly together, thereby avoiding any costly modifications or delays.
Scenario 2: Lack of Knowledge on NEMA Connector Ratings
The Problem: An electrical contractor in South America is responsible for installing power systems for several commercial buildings. However, they find themselves overwhelmed by the variety of NEMA configurations and their respective current ratings. This confusion leads to the risk of selecting connectors that cannot handle the required load, potentially resulting in equipment failures or safety hazards. The contractor’s lack of understanding of how to interpret the NEMA connector chart correctly creates significant anxiety and uncertainty.
The Solution: Education is crucial in overcoming this knowledge gap. B2B buyers should invest time in training sessions or workshops that focus on understanding NEMA configurations, their ratings, and applications. Additionally, creating a quick-reference guide or a cheat sheet that summarizes the most common NEMA configurations, their voltage ratings, and typical applications can be incredibly beneficial. This resource can help contractors quickly identify the correct connectors needed for various installations. Moreover, buyers should leverage online resources, including webinars and instructional videos, to reinforce their understanding of the NEMA connector chart, ensuring they can confidently select the right products for their projects without compromising safety or efficiency.
Scenario 3: Difficulty in Sourcing NEMA Connectors
The Problem: A company in Europe faces challenges in sourcing specific NEMA connectors for a unique application in a renewable energy project. Due to the specialized nature of the equipment and connectors required, local suppliers do not stock the necessary parts. This situation leads to extended lead times and potential project delays, which can jeopardize contracts and relationships with clients.
The Solution: To mitigate sourcing challenges, B2B buyers should adopt a proactive approach by establishing relationships with multiple suppliers, including international vendors. Utilizing the NEMA connector chart, buyers can identify the exact specifications needed and communicate these requirements clearly to potential suppliers. Additionally, it is advisable to explore online marketplaces that specialize in electrical components, as they may offer a wider range of NEMA connectors. Joining industry forums or groups can also provide insights into where others have successfully sourced specific connectors. Lastly, buyers should consider ordering in bulk or setting up consignment agreements with suppliers to ensure they have the necessary components on hand for future projects, thus reducing lead times and maintaining project momentum.
Strategic Material Selection Guide for nema connector chart
What Are the Key Materials Used in NEMA Connectors?
When selecting NEMA connectors for various applications, the choice of materials is crucial for ensuring optimal performance, durability, and compliance with international standards. Here, we analyze four common materials used in NEMA connectors: thermoplastic, thermoset, metal alloys, and rubber. Each material has unique properties that influence its suitability for specific applications.
How Do Thermoplastic Materials Impact NEMA Connectors?
Thermoplastic materials, such as nylon and polycarbonate, are widely used in NEMA connectors due to their excellent electrical insulation properties and resistance to moisture. They typically have a temperature rating of up to 105°C (221°F) and can withstand moderate mechanical stress.
Pros:
– Lightweight and cost-effective, making them suitable for mass production.
– Good chemical resistance, which is beneficial in various environments.
Cons:
– Limited high-temperature performance compared to thermoset materials.
– Susceptible to UV degradation unless treated.
Application Impact:
Thermoplastics are ideal for indoor applications where exposure to harsh environmental conditions is minimal. They are commonly used in residential and light commercial settings.
Considerations for International Buyers:
Buyers should ensure compliance with local electrical safety standards, such as IEC or UL, and verify that the thermoplastic used meets ASTM or DIN specifications.
What Are the Advantages of Thermoset Materials for NEMA Connectors?
Thermoset materials, like epoxy and phenolic resin, are known for their high-temperature resistance (up to 200°C or 392°F) and superior mechanical strength. These materials undergo a curing process that enhances their structural integrity.
Pros:
– Excellent thermal stability and resistance to deformation under load.
– High resistance to chemicals and moisture, making them suitable for harsh environments.
Cons:
– Generally more expensive than thermoplastics.
– Manufacturing complexity can lead to longer lead times.
Application Impact:
Thermosets are ideal for industrial applications where connectors may be exposed to extreme temperatures or corrosive environments, such as manufacturing plants or outdoor installations.
Considerations for International Buyers:
Ensure that thermoset materials comply with relevant standards like JIS or ASTM. Buyers should also consider the environmental impact of manufacturing processes.
Why Are Metal Alloys Important in NEMA Connectors?
Metal alloys, particularly those made from copper, aluminum, or brass, are essential for the conductive components of NEMA connectors. They provide excellent conductivity and mechanical strength.
Pros:
– High durability and resistance to mechanical wear.
– Excellent electrical conductivity, which is crucial for efficient power transmission.
Cons:
– Prone to corrosion if not properly treated or coated.
– Heavier than plastic materials, which can be a consideration for portable applications.
Application Impact:
Metal alloys are typically used in high-load applications, such as industrial machinery and heavy-duty equipment, where reliable electrical connections are paramount.
Considerations for International Buyers:
Buyers should be aware of local regulations regarding the use of metals, especially in environments where corrosion is a concern. Compliance with RoHS directives may also be necessary.
How Does Rubber Contribute to NEMA Connector Performance?
Rubber materials, including silicone and neoprene, are often used for gaskets and seals in NEMA connectors. They provide excellent insulation and protection against moisture and dust.
Pros:
– High flexibility and resilience, allowing for effective sealing.
– Good resistance to environmental factors such as UV light and ozone.
Cons:
– Limited temperature range compared to thermoplastics and thermosets.
– Can degrade over time if exposed to harsh chemicals.
Application Impact:
Rubber is particularly beneficial in outdoor applications where connectors are exposed to moisture and dust, such as in construction or agricultural settings.
Considerations for International Buyers:
It is important to ensure that rubber materials meet local environmental regulations and standards for safety and durability.
Summary Table of Material Selection for NEMA Connectors
Material | Typical Use Case for NEMA Connector Chart | Key Advantage | Key Disadvantage/Limitation | Relative Cost (Low/Med/High) |
---|---|---|---|---|
Thermoplastic | Residential and light commercial | Lightweight and cost-effective | Limited high-temperature performance | Low |
Thermoset | Industrial applications | High thermal stability | More expensive and complex to manufacture | High |
Metal Alloys | High-load industrial machinery | Excellent electrical conductivity | Prone to corrosion | Medium |
Rubber | Outdoor applications | Effective sealing against moisture and dust | Limited temperature range | Medium |
This analysis provides international B2B buyers with actionable insights into the material selection process for NEMA connectors, ensuring they make informed decisions that align with their specific application requirements and regional standards.
In-depth Look: Manufacturing Processes and Quality Assurance for nema connector chart
What Are the Typical Manufacturing Processes for NEMA Connectors?
The manufacturing of NEMA connectors involves several critical stages, each designed to ensure the final product meets stringent performance and safety standards. Understanding these processes is essential for international B2B buyers, particularly those from Africa, South America, the Middle East, and Europe, as it enables them to make informed purchasing decisions.
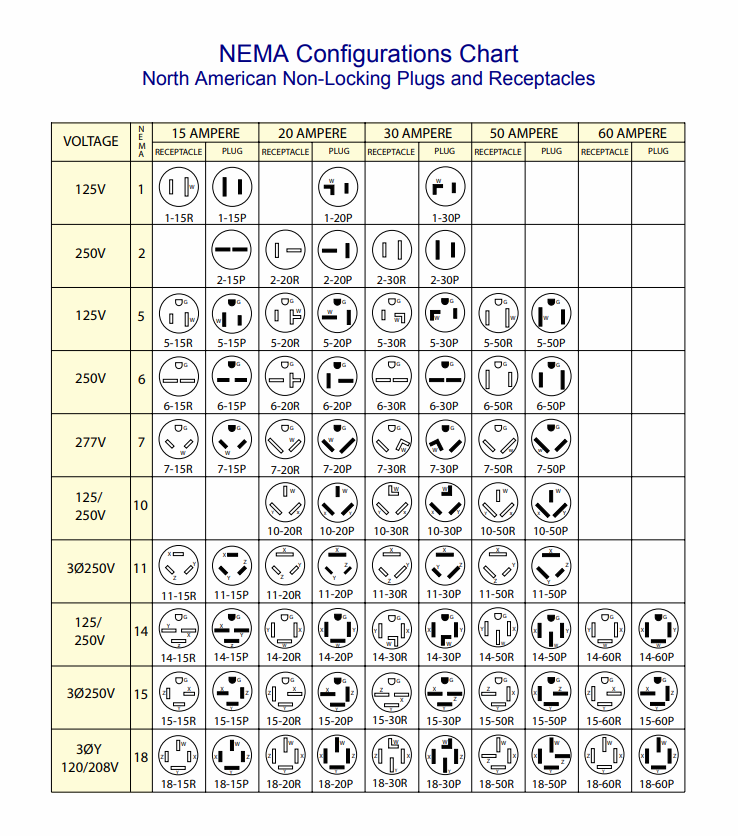
A stock image related to nema connector chart.
How Is Material Prepared for NEMA Connector Production?
Material preparation is the initial step in the manufacturing process. High-quality materials, such as copper for electrical contacts and thermoplastic or thermoset materials for housings, are selected based on their conductive properties and durability. Suppliers often conduct tests to verify material compliance with industry standards, including UL and IEC certifications.
Before production, materials undergo inspection to ensure they meet specifications. This includes checking for impurities, dimensions, and conductivity. Buyers should inquire about suppliers’ material sourcing practices and whether they have certifications to ensure compliance with international standards.
What Are the Key Forming Techniques Used in Manufacturing NEMA Connectors?
The forming stage involves shaping materials into the desired connector components. Common techniques include:
- Stamping: Metal sheets are stamped into specific shapes for contacts and terminal ends. This process is efficient and allows for high-volume production.
- Injection Molding: Thermoplastic materials are melted and injected into molds to create the connector housings. This technique enables complex shapes and precise dimensions, essential for fitting and safety.
- Die Casting: For connectors requiring higher strength and durability, die casting is used, particularly for metal housings. This process allows for intricate designs and high-quality finishes.
The choice of forming technique can impact the performance and longevity of NEMA connectors. B2B buyers should ask suppliers about their forming techniques to ensure they align with their quality expectations.
How Is Assembly Conducted for NEMA Connectors?
Assembly combines all components into a finished product. This stage involves:
- Component Integration: Electrical contacts are inserted into the housing, followed by securing mechanisms like screws or snaps.
- Soldering and Welding: For certain designs, soldering or welding techniques are used to ensure electrical continuity and mechanical strength.
- Quality Checks: Throughout the assembly process, visual inspections and automated checks are performed to ensure proper alignment and secure connections.
Buyers should consider suppliers with robust assembly processes and inquire about the level of automation used, as this often correlates with consistency and quality.
What Finishing Processes Are Applied to NEMA Connectors?
Finishing processes enhance both the aesthetic and functional qualities of NEMA connectors. These processes may include:
- Surface Treatment: Techniques such as plating (e.g., nickel or gold plating) enhance corrosion resistance and conductivity.
- Coating: Protective coatings may be applied to safeguard against environmental factors, particularly for connectors used in outdoor or industrial settings.
- Final Inspection: A thorough inspection is conducted to ensure that all connectors meet specified quality standards before packaging.
B2B buyers should request information about the finishing processes used by suppliers, as these can significantly impact product performance and longevity.
What Quality Assurance Measures Are Implemented for NEMA Connectors?
Quality assurance is critical in manufacturing NEMA connectors to ensure safety, reliability, and compliance with international standards. Understanding these measures can help international B2B buyers select trustworthy suppliers.
Which International Standards Should B2B Buyers Consider?
Suppliers of NEMA connectors typically adhere to several international standards, including:
- ISO 9001: This standard specifies requirements for a quality management system, ensuring that manufacturers consistently provide products that meet customer and regulatory requirements.
- CE Marking: For European buyers, CE marking indicates that the product complies with EU safety, health, and environmental protection legislation.
- UL Certification: In North America, Underwriters Laboratories (UL) certification is crucial for electrical safety.
Buyers should verify that their suppliers possess relevant certifications, as this reflects their commitment to quality and safety.
What Are the Key Quality Control Checkpoints in NEMA Connector Production?
Quality control (QC) checkpoints are integrated throughout the manufacturing process. Key checkpoints include:
- Incoming Quality Control (IQC): Materials and components are inspected upon arrival to ensure they meet specifications.
- In-Process Quality Control (IPQC): Ongoing inspections during manufacturing help catch defects early. This may involve automated testing for electrical continuity and mechanical integrity.
- Final Quality Control (FQC): The final product undergoes rigorous testing, including electrical performance tests, insulation resistance tests, and environmental stress tests.
B2B buyers should inquire about the QC processes of suppliers to ensure they follow stringent protocols at every stage of production.
How Can B2B Buyers Verify Supplier Quality Control Practices?
International B2B buyers can take several steps to ensure that suppliers maintain high-quality standards:
- Conduct Audits: Regular audits of suppliers can provide insights into their manufacturing practices and adherence to quality standards.
- Request Quality Reports: Suppliers should provide documentation of their quality control processes, including test results and compliance certifications.
- Engage Third-Party Inspectors: Using third-party inspection services can offer an unbiased assessment of product quality and manufacturing practices.
By actively engaging in these verification processes, buyers can mitigate risks associated with purchasing NEMA connectors.
What Are the Unique Quality Control Considerations for International B2B Buyers?
International buyers face additional challenges in ensuring product quality due to differences in regulations and standards across regions. Here are some considerations:
- Cultural and Regulatory Differences: Understanding local standards and practices is essential, as they can vary significantly from one region to another.
- Logistical Challenges: Shipping and handling can affect product integrity, particularly for sensitive electrical components. Ensuring that suppliers have robust packaging and shipping protocols is crucial.
- Language Barriers: Clear communication regarding quality expectations and standards is vital. Buyers may benefit from translators or local representatives who understand both the language and industry standards.
By being proactive and informed, B2B buyers from Africa, South America, the Middle East, and Europe can confidently navigate the complexities of sourcing NEMA connectors, ensuring they receive products that meet their high standards for quality and performance.
Practical Sourcing Guide: A Step-by-Step Checklist for ‘nema connector chart’
To successfully procure NEMA connectors for your business, following a structured approach is essential. This guide provides a step-by-step checklist to ensure that you make informed decisions while sourcing NEMA connectors, particularly beneficial for international B2B buyers from Africa, South America, the Middle East, and Europe.
Step 1: Define Your Technical Specifications
Before initiating the sourcing process, it is crucial to determine the specific technical requirements for the NEMA connectors you need. This includes identifying the voltage, amperage, and whether you require locking or non-locking configurations.
– Voltage and Current Ratings: Ensure you understand the operational environment and electrical needs of your equipment.
– Connector Type: Decide between locking and non-locking connectors based on your application.
Step 2: Research Reputable Suppliers
Conduct thorough research to identify suppliers who specialize in NEMA connectors. A reputable supplier will have a proven track record and positive reviews from previous clients.
– Supplier Directories: Use online directories and industry-specific platforms to find certified suppliers.
– Trade Shows and Expos: Attend industry events to network with potential suppliers and assess their products firsthand.
Step 3: Evaluate Potential Suppliers
Once you have a shortlist of suppliers, evaluate them rigorously. Request documentation such as company profiles, product catalogs, and references from other B2B buyers.
– Certifications: Verify that suppliers hold relevant certifications, such as ISO or UL, to ensure product quality and safety.
– Case Studies: Look for case studies that demonstrate the supplier’s capability in fulfilling similar orders.
Step 4: Request Samples for Testing
Before finalizing your order, request samples of the NEMA connectors. Testing samples in your actual application environment is critical to ensure compatibility and performance.
– Functionality Testing: Assess the connectors for their electrical performance under load conditions.
– Durability Evaluation: Check the physical robustness, especially if the connectors will be used in high-vibration or outdoor environments.
Step 5: Negotiate Terms and Pricing
Engage in negotiations with your selected suppliers to establish favorable terms and pricing. This step is vital for optimizing your procurement budget.
– Volume Discounts: Inquire about bulk purchase discounts or loyalty programs that could reduce costs.
– Payment Terms: Discuss payment options that align with your cash flow needs.
Step 6: Confirm Shipping and Delivery Logistics
Once you have agreed on terms, clarify the shipping and delivery processes. Understanding logistics is essential, especially when sourcing internationally.
– Shipping Options: Evaluate various shipping methods and their associated costs and delivery times.
– Customs and Import Duties: Familiarize yourself with any customs regulations or import duties that may apply to your shipments.
Step 7: Implement Quality Control Measures
After receiving your NEMA connectors, implement quality control measures to ensure they meet your specifications and industry standards.
– Inspection Protocols: Establish a routine for inspecting connectors upon arrival.
– Feedback Loop: Create a process for documenting any issues to inform future orders and maintain supplier accountability.
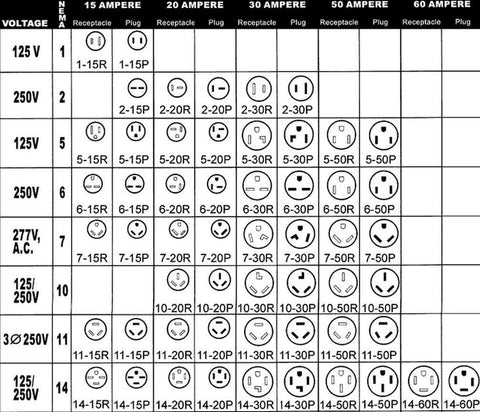
A stock image related to nema connector chart.
Following this checklist will help you navigate the complexities of sourcing NEMA connectors effectively, ensuring that you select the right products for your business needs while minimizing risks associated with procurement.
Comprehensive Cost and Pricing Analysis for nema connector chart Sourcing
What Are the Key Cost Components in NEMA Connector Sourcing?
When sourcing NEMA connectors, understanding the cost structure is critical for international B2B buyers. The primary cost components include:
-
Materials: The type of materials used in manufacturing NEMA connectors significantly affects the price. High-quality metals, plastics, and insulation materials tend to increase costs but can enhance durability and performance.
-
Labor: Labor costs vary based on the manufacturing location. Countries with higher labor rates may reflect this in the pricing, while regions with lower labor costs can offer competitive pricing but may compromise on quality.
-
Manufacturing Overhead: This includes costs related to utilities, equipment maintenance, and factory management. Efficient production processes can help minimize overhead costs, which can be beneficial for both suppliers and buyers.
-
Tooling: The initial investment in tooling for custom or specialized NEMA connectors can be substantial. Buyers should consider these upfront costs when evaluating supplier quotes.
-
Quality Control (QC): Implementing rigorous QC processes ensures that connectors meet industry standards. While this may add to costs, it helps avoid long-term expenses associated with failures and recalls.
-
Logistics: Shipping costs, including freight, insurance, and customs duties, can significantly impact the total cost. Buyers should account for these when negotiating prices.
-
Margin: Supplier margins vary widely based on market conditions, competition, and perceived value. Understanding these factors can aid in negotiations.
How Do Price Influencers Affect NEMA Connector Costs?
Several factors influence the pricing of NEMA connectors, making it essential for buyers to consider these variables:
-
Volume and Minimum Order Quantity (MOQ): Larger orders typically lead to lower per-unit costs. Buyers should negotiate MOQs that align with their purchasing needs to maximize cost savings.
-
Specifications and Customization: Custom designs or specific certifications can drive up costs. Buyers should clarify their requirements to avoid unexpected expenses during the production process.
-
Materials and Quality Certifications: Connectors made from premium materials with recognized quality certifications may command higher prices but can offer better performance and safety.
-
Supplier Factors: The reputation, location, and production capabilities of the supplier can affect pricing. Established suppliers with a track record of reliability may charge a premium.
-
Incoterms: The agreed Incoterms (International Commercial Terms) dictate the responsibilities of buyers and sellers regarding shipping and logistics costs. Understanding these terms is crucial for accurate budgeting.
What Tips Can International B2B Buyers Use to Optimize Costs?
For buyers from Africa, South America, the Middle East, and Europe, several strategies can enhance cost efficiency:
-
Negotiate Effectively: Engage suppliers in discussions about pricing structures, especially regarding bulk orders or long-term contracts. Highlighting your purchasing potential may yield better terms.
-
Consider Total Cost of Ownership (TCO): Evaluate the complete lifecycle cost of NEMA connectors, including installation, maintenance, and potential downtime. This broader view can justify higher upfront costs for higher-quality products.
-
Understand Pricing Nuances: International buyers should be aware of currency fluctuations and their impact on pricing. Engaging in forward contracts can mitigate risks associated with currency changes.
-
Leverage Local Suppliers: Whenever possible, consider sourcing from local manufacturers to reduce shipping costs and lead times. This can also facilitate better communication and support.
-
Request Samples: Before finalizing large orders, requesting samples can help verify quality and compatibility, preventing costly mistakes.
Disclaimer for Indicative Prices
Pricing for NEMA connectors can vary widely based on the aforementioned factors and market conditions. The information provided here is intended for guidance and should be verified with suppliers for the most accurate and current pricing. Always conduct thorough market research to ensure you are making informed purchasing decisions.
Alternatives Analysis: Comparing nema connector chart With Other Solutions
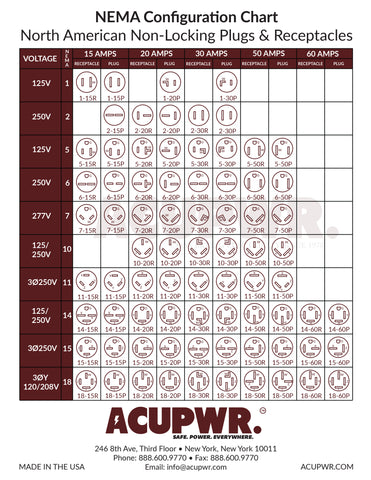
A stock image related to nema connector chart.
Understanding Alternative Solutions to NEMA Connector Charts
When selecting electrical connectors for industrial or commercial applications, it’s vital to consider various solutions available in the market. NEMA connector charts provide a standardized way to understand the configurations and specifications of plugs and receptacles, but there are alternatives that may better suit specific needs. This analysis will compare the NEMA connector chart with two viable alternatives: IEC (International Electrotechnical Commission) connector systems and custom connector solutions.
Comparison Table of NEMA Connector Chart and Alternatives
Comparison Aspect | NEMA Connector Chart | IEC Connector Systems | Custom Connector Solutions |
---|---|---|---|
Performance | High reliability; standardized | High safety ratings; versatile | Tailored to specific needs; flexible |
Cost | Generally cost-effective | Moderate to high cost | Potentially higher due to design |
Ease of Implementation | Easy due to standardization | Requires additional training | May require engineering expertise |
Maintenance | Low; standardized parts available | Moderate; parts may vary | Variable; depends on design |
Best Use Case | Residential and light commercial | Industrial and medical applications | Specialized applications requiring custom features |
Detailed Breakdown of Alternatives
IEC Connector Systems
IEC connector systems are widely recognized for their international standards and safety features. These connectors are designed for high-performance applications, particularly in environments where safety and versatility are critical, such as in industrial or medical settings. The primary advantage of IEC connectors is their high safety ratings, which often exceed those of NEMA connectors. However, the cost can be higher, and implementing these systems may require additional training for staff to understand the different configurations and standards. They are best suited for global operations where compatibility with international standards is necessary.
Custom Connector Solutions
Custom connector solutions offer flexibility that standard connectors cannot. These connectors can be tailored to specific applications, providing unique specifications that meet the particular needs of a project. The main advantage is their adaptability; they can be designed to fit various environments and requirements, ensuring optimal performance. However, this flexibility often comes at a higher cost, and the design process may require significant engineering expertise. Custom solutions are ideal for specialized applications, such as high-tech industries or unique industrial setups where standard connectors may not suffice.
Conclusion: How to Choose the Right Solution
When evaluating which solution is best for your needs, consider the specific requirements of your application. If your focus is on standardization and cost-effectiveness for residential or light commercial use, the NEMA connector chart remains a strong choice. Conversely, if you operate in a global context or require high safety ratings, IEC connectors could be the better option. For specialized applications that demand tailored solutions, custom connectors provide the flexibility necessary to meet those unique requirements. Ultimately, the decision should align with your operational needs, budget constraints, and the level of expertise available within your organization.
Essential Technical Properties and Trade Terminology for nema connector chart
What Are the Essential Technical Properties of NEMA Connectors?
When navigating the complexities of NEMA connectors, understanding their technical properties is crucial for ensuring compatibility and safety in electrical applications. Here are the key specifications that international B2B buyers should consider:
1. Voltage Rating
Voltage ratings indicate the maximum voltage a connector can safely handle. Common ratings include 125V, 250V, and 480V. For buyers, selecting the correct voltage rating is essential to prevent electrical failures and ensure compliance with regional electrical standards. Mismatched voltage ratings can lead to equipment damage or safety hazards.
2. Current Rating
Current ratings, measured in amperes (A), specify the maximum current a connector can carry. Options typically range from 15A to 60A. This specification is critical for buyers as it dictates the load the connector can support, directly affecting the performance and safety of electrical systems. Choosing a connector with insufficient current rating can result in overheating and potential fire risks.
3. Material Grade
The materials used in the construction of NEMA connectors—such as thermoplastics for housings and copper for blades—impact durability and conductivity. For B2B buyers, understanding material grades helps in evaluating the longevity and reliability of connectors, particularly in harsh environments. High-quality materials can enhance performance and reduce maintenance costs over time.
4. Blade Configuration
Blade configuration refers to the physical arrangement and shape of the connector blades. This includes straight or curved designs, which affect how connectors engage with receptacles. Buyers should consider the blade design to ensure compatibility with existing equipment and to prevent accidental disconnections, especially in high-vibration applications.
5. Grounding Mechanism
Grounding pins are vital for safety, ensuring that electrical faults are safely redirected. NEMA connectors often include specific designs where the ground pin connects first. For B2B buyers, understanding the grounding mechanism is critical for compliance with safety regulations and minimizing shock hazards.
6. Environmental Ratings
Environmental ratings (like IP ratings) indicate the connector’s resistance to dust and moisture. These ratings are especially important for outdoor or industrial applications where exposure to the elements is common. Buyers should assess these ratings to ensure that the connectors will perform reliably in their specific operating environments.
What Trade Terminology Should B2B Buyers Understand?
Familiarity with industry terminology can enhance communication and negotiation in the procurement process. Here are some essential terms related to NEMA connectors:
1. OEM (Original Equipment Manufacturer)
OEM refers to companies that manufacture products that are sold under another company’s brand name. Understanding this term is crucial for buyers sourcing connectors that need to integrate seamlessly with existing equipment.
2. MOQ (Minimum Order Quantity)
MOQ is the smallest quantity of a product that a supplier is willing to sell. Knowing the MOQ helps buyers manage inventory levels and budgeting effectively, especially when sourcing connectors for large projects.
3. RFQ (Request for Quotation)
An RFQ is a formal document requesting price quotes from suppliers for specific products. For B2B buyers, issuing an RFQ can streamline the procurement process by ensuring that all vendors provide comparable pricing and terms for NEMA connectors.
4. Incoterms (International Commercial Terms)
Incoterms are standardized terms that define the responsibilities of buyers and sellers in international transactions. Familiarity with these terms helps buyers understand shipping costs, risks, and responsibilities associated with importing connectors from different regions.
5. Lead Time
Lead time refers to the time taken from placing an order to the product’s delivery. Understanding lead times is critical for project planning and ensuring that connectors arrive when needed to avoid delays in operations.
6. Certification Standards
Certification standards, such as UL (Underwriters Laboratories) and CSA (Canadian Standards Association), indicate that products have been tested for safety and performance. Buyers should prioritize connectors that meet relevant certification standards to ensure compliance with local regulations and enhance safety.
By comprehensively understanding these technical properties and trade terms, B2B buyers can make informed decisions when sourcing NEMA connectors, ultimately enhancing their operational efficiency and safety.
Navigating Market Dynamics and Sourcing Trends in the nema connector chart Sector
What Are the Key Market Dynamics and Trends in the NEMA Connector Sector?
The global NEMA connector market is witnessing significant growth, driven by increasing industrial automation, the rise of renewable energy projects, and a growing demand for reliable electrical connections across various sectors. International B2B buyers, particularly those in Africa, South America, the Middle East, and Europe, should note the surge in smart technology integration, which necessitates advanced NEMA configurations for enhanced connectivity and safety. For instance, in regions like Kenya and South America, the expansion of manufacturing and infrastructure development is elevating the need for robust electrical solutions that comply with international standards.
Emerging trends also indicate a shift towards customization of NEMA connectors to meet specific application requirements, such as those in industrial settings, where high power and durability are crucial. Buyers should be aware of the growing importance of locking connectors, which provide secure connections in high-vibration environments, such as construction sites or factories. Moreover, the market is increasingly influenced by technological advancements, such as the development of smart connectors that can monitor and report electrical performance, thereby enhancing operational efficiency.
How Are Sustainability and Ethical Sourcing Affecting the NEMA Connector Market?
As global awareness of environmental issues rises, sustainability is becoming a key factor in the sourcing of NEMA connectors. International buyers are increasingly prioritizing suppliers who demonstrate a commitment to ethical sourcing practices and minimize their environmental impact. This includes the use of recyclable materials and adherence to ‘green’ certifications, such as RoHS (Restriction of Hazardous Substances) and REACH (Registration, Evaluation, Authorisation and Restriction of Chemicals).
For B2B buyers, understanding the environmental footprint of NEMA connectors is critical. The production processes of these components can involve significant energy consumption and material waste; thus, suppliers that implement sustainable practices can provide a competitive advantage. Ethical supply chains not only enhance brand reputation but also align with the corporate social responsibility goals of many businesses, particularly those in Europe and the Middle East, where regulatory frameworks increasingly mandate sustainable practices.
Moreover, as demand for renewable energy sources grows, the need for NEMA connectors that facilitate green energy applications, such as solar and wind power, is on the rise. Buyers should seek out products that are designed for energy efficiency and durability, ensuring they meet the rigorous demands of environmentally friendly projects.
What is the Historical Context of NEMA Connectors in B2B Sourcing?
The National Electrical Manufacturers Association (NEMA) was established in 1926 to standardize electrical connectors, which has significantly shaped the landscape of electrical connectivity. Initially focused on the North American market, NEMA connectors have gained international recognition due to their reliability and safety features. Over the decades, advancements in materials and technology have led to the development of various NEMA configurations, catering to a wide array of applications, from residential to industrial.
As global trade expanded, NEMA connectors began to be recognized as vital components in various sectors, including manufacturing, construction, and renewable energy. This evolution has positioned NEMA connectors as a benchmark for electrical connectivity, influencing sourcing decisions for international B2B buyers. Understanding this historical context can help buyers appreciate the reliability and safety standards that NEMA connectors provide, ensuring they make informed purchasing decisions that meet both operational needs and regulatory requirements.
Frequently Asked Questions (FAQs) for B2B Buyers of nema connector chart
-
How do I select the right NEMA connector for my specific application?
Choosing the correct NEMA connector depends on your voltage and current requirements, as well as the environment in which it will be used. For residential applications, standard non-locking connectors like the NEMA 5-15P are commonly used. In contrast, industrial settings may require locking configurations (e.g., L14-30) to ensure a secure connection against vibrations. Always refer to the NEMA configuration chart to match the connector type with the electrical specifications of your equipment. -
What are the key differences between locking and non-locking NEMA connectors?
Locking connectors, identified by an “L” in their designation, provide a secure twist-and-lock mechanism, making them ideal for industrial applications where disconnection risks are high. Non-locking connectors, on the other hand, are easier to plug and unplug, making them suitable for residential use. Understanding these differences helps in selecting the right type based on the application’s safety and performance needs. -
What should I consider when sourcing NEMA connectors internationally?
When sourcing NEMA connectors from international suppliers, consider factors such as compliance with local electrical standards, shipping regulations, and import duties. Verify the supplier’s reputation and track record in delivering quality products. Additionally, assess the availability of technical support and after-sales service, which can be critical for resolving issues post-purchase. -
How can I vet suppliers for NEMA connectors to ensure quality?
To vet suppliers, start by checking their certifications and compliance with relevant standards like UL or CE. Request samples to evaluate the quality of the connectors. Additionally, review customer testimonials and case studies to gauge their reliability. Engaging in direct communication to discuss your specific needs can also reveal their customer service responsiveness. -
What are common minimum order quantities (MOQ) for NEMA connectors?
MOQs for NEMA connectors can vary significantly depending on the supplier and the specific type of connector. Typically, MOQs may range from 50 to several hundred units. It’s advisable to inquire directly with suppliers about their MOQs and negotiate terms that align with your purchasing strategy, especially if you’re looking to test the market with smaller quantities initially. -
What payment terms should I expect when purchasing NEMA connectors internationally?
Payment terms can vary widely among suppliers, but common options include upfront payment, partial payment upon order confirmation, or payment on delivery. It’s essential to clarify these terms before finalizing the order. Consider using secure payment methods, such as letters of credit or escrow services, especially for larger transactions to protect your investment. -
How can I ensure quality assurance (QA) for NEMA connectors?
Implement a QA process by requiring suppliers to provide test reports and certifications for their connectors. Conduct inspections at different stages of production and before shipment. You may also consider third-party inspection services to validate the quality of the connectors. Establishing clear quality criteria in your purchase agreement can help ensure you receive products that meet your specifications. -
What logistics considerations should I keep in mind when importing NEMA connectors?
When importing NEMA connectors, consider shipping methods, lead times, and customs clearance processes. Opt for reliable freight forwarding services that can handle the complexities of international shipping. Be aware of potential delays at customs, and ensure all documentation is accurate and complete to avoid additional costs. Planning for proper warehousing upon arrival can also help streamline your operations.
Important Disclaimer & Terms of Use
⚠️ Important Disclaimer
The information provided in this guide, including content regarding manufacturers, technical specifications, and market analysis, is for informational and educational purposes only. It does not constitute professional procurement advice, financial advice, or legal advice.
While we have made every effort to ensure the accuracy and timeliness of the information, we are not responsible for any errors, omissions, or outdated information. Market conditions, company details, and technical standards are subject to change.
B2B buyers must conduct their own independent and thorough due diligence before making any purchasing decisions. This includes contacting suppliers directly, verifying certifications, requesting samples, and seeking professional consultation. The risk of relying on any information in this guide is borne solely by the reader.
Strategic Sourcing Conclusion and Outlook for nema connector chart
In navigating the complexities of the NEMA connector landscape, strategic sourcing emerges as a critical component for international B2B buyers. Understanding the distinctions between non-locking and locking configurations allows companies to tailor their electrical solutions to specific applications, enhancing safety and efficiency. For instance, while non-locking connectors are ideal for residential and light commercial use, locking configurations are essential for industrial applications where high-vibration environments are common.
Buyers should consider voltage classifications, current capacities, and the unique requirements of their operations when selecting NEMA connectors. By leveraging the insights from the NEMA configuration charts, businesses can mitigate risks associated with incompatible electrical equipment and streamline their procurement processes.
As the global market continues to evolve, staying informed about technological advancements and regulatory changes will empower B2B buyers from Africa, South America, the Middle East, and Europe to make informed purchasing decisions. Embrace the value of strategic sourcing today; it not only safeguards your investments but also positions your business for sustainable growth in a competitive marketplace.