Unlock Efficiency: The Ultimate Electric Motor Buying Guide (2025)
Introduction: Navigating the Global Market for electric motor
In the rapidly evolving landscape of industrial technology, sourcing the right electric motor can be a significant challenge for international B2B buyers, especially those operating in Africa, South America, the Middle East, and Europe. With diverse applications spanning from manufacturing to renewable energy, understanding the nuances of different electric motor types—such as AC, DC, and servo motors—is crucial for optimizing operational efficiency. This comprehensive guide delves into the essential aspects of electric motors, providing insights into their construction, functionality, and applications.
Moreover, we will explore effective strategies for supplier vetting, ensuring that buyers can confidently navigate the complexities of global sourcing. Cost considerations, including initial investment and long-term energy efficiency, will also be thoroughly examined to aid in budget planning. By empowering B2B buyers with knowledge about market trends, technological advancements, and best practices, this guide aims to facilitate informed purchasing decisions.
Whether you’re a procurement manager in Mexico seeking reliable suppliers or a project engineer in Saudi Arabia looking for high-performance motors, the insights presented here will help you make strategic choices that align with your business goals. Embrace the opportunity to enhance your operational capabilities and drive success in your projects through informed sourcing of electric motors.
Understanding electric motor Types and Variations
Type Name | Key Distinguishing Features | Primary B2B Applications | Brief Pros & Cons for Buyers |
---|---|---|---|
Induction Motors | Operate on electromagnetic induction; robust design | Manufacturing, HVAC systems | Pros: Durable, low maintenance; Cons: Less efficient at low speeds. |
DC Motors | Use direct current; can be easily controlled | Robotics, electric vehicles | Pros: High starting torque; Cons: Requires maintenance due to brushes. |
Synchronous Motors | Rotor moves in sync with the stator’s magnetic field | Power generation, precision machinery | Pros: Constant speed, efficient; Cons: More complex control systems needed. |
Permanent Magnet Motors | Use permanent magnets for rotor; high efficiency | Consumer electronics, automotive | Pros: Compact, high torque density; Cons: Higher initial cost. |
Servomotors | Provide precise control of angular position and speed | CNC machines, robotics | Pros: High accuracy, responsive; Cons: More expensive and complex. |
What Are Induction Motors and Their Key Applications?
Induction motors are widely recognized for their robustness and simplicity, making them a staple in various industries. They operate on the principle of electromagnetic induction, which allows them to convert electrical energy into mechanical energy efficiently. Commonly used in manufacturing and HVAC systems, these motors are ideal for applications requiring continuous operation. When purchasing induction motors, buyers should consider factors such as efficiency ratings, operating conditions, and load requirements to ensure optimal performance.
How Do DC Motors Work and Where Are They Used?
DC motors are favored for their ease of control and high starting torque, making them suitable for applications like robotics and electric vehicles. They operate on direct current and can be easily adjusted for speed and torque, which is crucial for dynamic applications. However, buyers must be aware of the maintenance requirements associated with brushes in traditional DC motors. Exploring brushless options may provide a solution to reduce maintenance downtime.
What Are the Advantages of Synchronous Motors?
Synchronous motors are unique in that their rotor rotates in synchrony with the magnetic field of the stator, providing a constant speed regardless of the load. This characteristic makes them particularly valuable in power generation and precision machinery applications. While they offer high efficiency, the complexity of their control systems can be a barrier for some buyers. Understanding the specific speed and torque requirements of your application is essential when considering synchronous motors.
Why Choose Permanent Magnet Motors?
Permanent magnet motors are known for their high efficiency and compact design, often found in consumer electronics and automotive applications. By utilizing permanent magnets for the rotor, these motors achieve high torque density and reduced energy consumption. Although they come with a higher initial cost, their long-term operational efficiency can offset this investment. Buyers should assess the total cost of ownership, including energy savings, when evaluating permanent magnet motors.
What Are Servomotors and Their Key Benefits?
Servomotors are engineered for precision control over angular position and speed, making them essential in applications like CNC machines and robotics. They provide high accuracy and responsiveness, which is crucial in automated processes. However, their complexity and higher price point may deter some buyers. When considering servomotors, it is important to evaluate the specific performance requirements of your application to justify the investment.
Key Industrial Applications of electric motor
Industry/Sector | Specific Application of Electric Motor | Value/Benefit for the Business | Key Sourcing Considerations for this Application |
---|---|---|---|
Manufacturing | Conveyor Systems | Improved efficiency and reduced labor costs | Motor durability, compatibility with existing systems |
Agriculture | Irrigation Pumps | Enhanced water management and crop yield | Energy efficiency, maintenance support, local service availability |
Transportation | Electric Vehicles | Lower operational costs and reduced emissions | Battery compatibility, motor performance specifications |
HVAC | Air Conditioning Systems | Energy savings and improved indoor air quality | Energy ratings, installation support, warranty terms |
Mining | Hoists and Crushers | Increased productivity and safety | Load capacity, environmental certifications, reliability |
How Are Electric Motors Used in Manufacturing?
In manufacturing, electric motors are integral to conveyor systems, driving the movement of materials and products through production lines. This application enhances operational efficiency by automating processes that were previously labor-intensive. For international B2B buyers, particularly those in Africa and South America, sourcing motors with high durability and compatibility with existing systems is crucial to minimize downtime and maintenance costs.
What Role Do Electric Motors Play in Agriculture?
Electric motors are vital in agricultural irrigation systems, powering pumps that manage water distribution effectively. This technology solves issues related to water scarcity and inefficient irrigation practices, thereby increasing crop yields. Buyers from the Middle East and Europe should prioritize energy-efficient motors with robust maintenance support to ensure sustainable agricultural practices in varying climates.
How Do Electric Motors Enhance Transportation?
In the transportation sector, electric motors are essential for electric vehicles (EVs), providing a cleaner alternative to traditional fuel engines. They contribute to significant cost savings in fuel and maintenance, while also reducing environmental impact. B2B buyers in Europe and the Middle East should focus on sourcing motors that offer high performance and compatibility with modern battery technologies to maximize efficiency.
In What Ways Do Electric Motors Benefit HVAC Systems?
Electric motors are crucial in air conditioning systems, where they drive compressors and fans. This application leads to energy savings and improved indoor air quality, making it a strategic investment for businesses. Buyers from all regions should consider the energy ratings of motors, installation support, and warranty terms to ensure long-term reliability and efficiency.
How Are Electric Motors Essential in Mining Operations?
In the mining industry, electric motors power hoists and crushers, enhancing productivity and safety in operations. By automating heavy lifting and material processing, businesses can achieve higher output with reduced labor risks. International buyers should evaluate load capacity, environmental certifications, and the reliability of motors to ensure they meet the demanding conditions often found in mining environments.
3 Common User Pain Points for ‘electric motor’ & Their Solutions
Scenario 1: High Energy Costs from Inefficient Electric Motors
The Problem: Many B2B buyers face the challenge of rising operational costs due to inefficient electric motors. This inefficiency often stems from outdated technology or poorly maintained equipment. For companies in industries like manufacturing and agriculture, where electric motors are critical for operations, the impact can be substantial. Not only do these inefficiencies lead to increased energy bills, but they can also result in higher maintenance costs and reduced productivity, ultimately affecting the bottom line.
The Solution: To address this issue, buyers should prioritize the procurement of energy-efficient electric motors, such as those that comply with international efficiency standards like IE3 or IE4. When sourcing these motors, it’s essential to assess the total cost of ownership rather than just the initial purchase price. Engage with suppliers who can provide detailed efficiency ratings and performance data. Additionally, consider implementing a predictive maintenance program that leverages IoT technologies to monitor motor performance continuously. This approach will not only optimize energy consumption but also extend the lifespan of the motors, leading to lower overall costs.
Scenario 2: Difficulty in Finding Compatible Electric Motor Parts
The Problem: B2B buyers often encounter compatibility issues when sourcing replacement parts for electric motors. This is especially true for companies operating in regions with limited access to a wide variety of suppliers. Incompatible or substandard parts can lead to prolonged downtime and increased repair costs, significantly impacting operational efficiency. Buyers may also struggle with understanding the specifications required for their motors, leading to costly mistakes in procurement.
The Solution: To overcome this pain point, buyers should develop a robust parts management strategy that includes maintaining an updated inventory of motor specifications and compatible parts. Collaborating with reputable suppliers who provide comprehensive catalogs can also be beneficial. Buyers should request technical documentation and compatibility charts to ensure they are sourcing the correct parts. Additionally, investing in training for staff on understanding motor specifications can significantly reduce errors. Establishing a partnership with a local distributor who specializes in electric motors can streamline the sourcing process, ensuring timely availability of compatible parts.
Scenario 3: Challenges in Electric Motor Installation and Integration
The Problem: Installing and integrating new electric motors into existing systems can be a daunting task for many B2B buyers, particularly in sectors like construction and energy. Inadequate installation can lead to operational inefficiencies, safety hazards, and even damage to the equipment. Moreover, buyers may lack the technical expertise required to ensure proper integration with existing machinery and control systems, leading to delays and increased labor costs.
The Solution: To mitigate these challenges, buyers should prioritize working with suppliers that offer comprehensive installation support and technical training. Before purchasing, inquire about the availability of installation services and technical assistance. Consider investing in motors that come with detailed installation manuals and online resources, such as video tutorials. Additionally, forming a partnership with engineering consultants can provide the necessary expertise for successful integration. This collaborative approach will help ensure that installations are completed efficiently, minimizing downtime and enhancing operational safety.
Strategic Material Selection Guide for electric motor
What Are the Key Materials Used in Electric Motors?
When selecting materials for electric motors, it is crucial to consider their properties, advantages, disadvantages, and overall impact on performance. Here, we analyze four common materials: copper, aluminum, steel, and composite materials.
How Does Copper Contribute to Electric Motor Performance?
Copper is widely recognized for its excellent electrical conductivity, making it a preferred choice for windings in electric motors. Its high thermal conductivity allows for efficient heat dissipation, which is essential for maintaining optimal performance under load. Copper also exhibits good corrosion resistance, particularly when coated or treated.
Pros: Copper’s durability and conductivity lead to enhanced motor efficiency and longevity. It is relatively easy to work with during manufacturing, allowing for intricate designs.
Cons: The primary downside of copper is its cost, which can be significantly higher than alternatives like aluminum. Additionally, its weight can be a consideration in applications where weight reduction is critical.
Impact on Application: Copper is compatible with various media, including oils and coolants, making it suitable for diverse industrial applications.
Considerations for International Buyers: Compliance with standards such as ASTM B170 (copper wire) is essential. Buyers from regions like the Middle East and Europe may also need to consider local sourcing options due to fluctuating copper prices.
What Role Does Aluminum Play in Electric Motors?
Aluminum is often used as a cost-effective alternative to copper in motor windings and casings. It has a lower density, which contributes to weight savings in applications where weight is a concern.
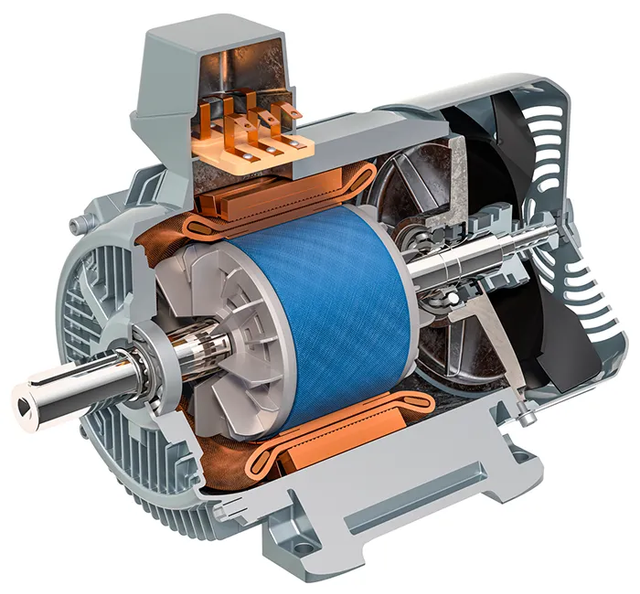
A stock image related to electric motor.
Pros: Aluminum is less expensive than copper and offers a good strength-to-weight ratio. It is also resistant to corrosion, especially when anodized.
Cons: While aluminum conducts electricity, it is not as efficient as copper, leading to potential losses in performance. Additionally, aluminum’s mechanical properties can be inferior in high-temperature applications.
Impact on Application: Aluminum is suitable for environments where weight savings are prioritized, but its lower conductivity may limit its use in high-performance motors.
Considerations for International Buyers: Buyers should ensure compliance with standards such as ASTM B221 (aluminum extrusions). In regions like Africa and South America, sourcing aluminum locally may be advantageous due to lower shipping costs.
Why Is Steel a Common Choice for Electric Motors?
Steel is primarily used in the construction of motor cores and frames due to its magnetic properties and strength. Various grades of steel, such as silicon steel, are specifically designed to enhance magnetic performance.
Pros: Steel’s magnetic properties improve motor efficiency and torque. It is also relatively inexpensive and widely available.
Cons: Steel can be prone to corrosion if not properly treated, which may lead to reduced lifespan in harsh environments. It is also heavier than aluminum, which may be a disadvantage in certain applications.
Impact on Application: Steel is suitable for high-torque applications but may require protective coatings in corrosive environments.
Considerations for International Buyers: Compliance with standards such as DIN 10088 (stainless steel) is crucial. Buyers in Europe may prefer specific grades of steel that meet EU regulations.
How Do Composite Materials Enhance Electric Motor Design?
Composite materials, such as fiberglass and carbon fiber, are increasingly used in electric motors for their lightweight and strength properties. These materials can be tailored for specific applications, providing flexibility in design.
Pros: Composites offer excellent resistance to corrosion and thermal expansion, making them suitable for a variety of environments. They also contribute to significant weight savings.
Cons: The manufacturing complexity of composites can lead to higher costs and longer production times. Additionally, their electrical properties may not be as favorable as metals.
Impact on Application: Composites are ideal for specialized applications where weight and corrosion resistance are critical, such as in aerospace or marine environments.
Considerations for International Buyers: Buyers should be aware of the specific manufacturing standards for composites, such as ASTM D3039. In regions like the Middle East, where extreme temperatures can affect material performance, selecting the right composite is vital.
Summary Table of Material Selection for Electric Motors
Material | Typical Use Case for Electric Motor | Key Advantage | Key Disadvantage/Limitation | Relative Cost (Low/Med/High) |
---|---|---|---|---|
Copper | Motor windings | Excellent conductivity | High cost, heavier | High |
Aluminum | Motor casings and windings | Lightweight, cost-effective | Lower conductivity than copper | Medium |
Steel | Motor cores and frames | Strong magnetic properties | Prone to corrosion | Low |
Composite | Specialized applications | Lightweight, corrosion-resistant | Higher manufacturing complexity | Medium to High |
This strategic material selection guide provides actionable insights for international B2B buyers, ensuring informed decisions that align with specific application requirements and regional considerations.
In-depth Look: Manufacturing Processes and Quality Assurance for electric motor
What Are the Key Stages in the Manufacturing Process of Electric Motors?
The manufacturing of electric motors involves several critical stages, each designed to ensure the performance, durability, and efficiency of the final product. Understanding these stages can help B2B buyers make informed decisions when selecting suppliers.
Material Preparation: How Is the Right Material Selected for Electric Motors?
The manufacturing process begins with material preparation. Key materials include:
- Copper and Aluminum: Used for windings due to their excellent electrical conductivity.
- Magnetic Materials: Such as silicon steel, which is used for the stator and rotor to enhance magnetic performance.
- Insulation Materials: Essential for winding insulation, which helps prevent short circuits and enhances motor lifespan.
Suppliers should provide material certifications to verify the quality and type of materials used. Buyers should request documentation such as Material Safety Data Sheets (MSDS) and Certificates of Compliance.
Forming: What Techniques Are Used to Shape Electric Motor Components?
In this stage, the raw materials are shaped into specific components. Key techniques include:
- Stamping: Used for creating the laminations of the stator and rotor. Precision in stamping is vital to reduce energy losses and improve efficiency.
- Winding: Involves winding copper or aluminum wire around the stator and rotor cores. Automated winding machines are often used for consistency and precision.
- Casting: Sometimes employed for rotor fabrication, particularly in squirrel-cage rotors.
Quality during forming is crucial, as any defects can lead to performance issues. B2B buyers should verify the use of high-precision machinery and techniques, as well as the training of personnel involved in these processes.
Assembly: How Are Electric Motor Components Brought Together?
The assembly stage is where all the components come together. This includes:
- Component Integration: Involves fitting the rotor into the stator and connecting the winding to the commutator or terminals.
- Alignment: Proper alignment of components is essential for minimizing friction and wear during operation.
- Mechanical Fastening: Use of bolts, screws, or adhesive bonding to secure the motor assembly.
During this phase, buyers should ensure that suppliers follow a stringent assembly protocol, which includes checks for component compatibility and alignment.
Finishing: What Processes Ensure the Electric Motor Is Ready for Use?
Finishing processes are critical for enhancing the durability and performance of electric motors. These include:
- Surface Treatment: Techniques such as painting or anodizing protect against corrosion and improve aesthetic appeal.
- Balancing: Dynamic balancing of the rotor is performed to minimize vibrations during operation, which can lead to premature failure.
- Final Inspection: A comprehensive check to ensure all specifications and tolerances are met.
Buyers should inquire about the finishing processes used and request information on any environmental or safety compliance certifications.
What Quality Assurance Standards Should B2B Buyers Look For?
Quality assurance (QA) is crucial in the manufacturing of electric motors to ensure reliability and performance. Buyers should be familiar with international standards and industry-specific certifications.
Which International Standards Are Relevant for Electric Motor Manufacturing?
- ISO 9001: This standard focuses on quality management systems and is essential for suppliers aiming to ensure consistent quality and customer satisfaction.
- CE Marking: Particularly relevant for products sold in the European market, indicating compliance with health, safety, and environmental protection standards.
- API Certifications: If applicable, particularly in industries like oil and gas, where electric motors are used in critical applications.
What Are the Key Quality Control Checkpoints in Electric Motor Manufacturing?
Quality control checkpoints are integrated at various stages of the manufacturing process:
- Incoming Quality Control (IQC): Inspection of raw materials upon arrival to verify compliance with specifications.
- In-Process Quality Control (IPQC): Continuous monitoring during manufacturing to catch defects early.
- Final Quality Control (FQC): Comprehensive testing of the finished product, including performance tests, thermal imaging, and vibration analysis.
B2B buyers should seek suppliers that implement these checkpoints rigorously and provide detailed reports on quality metrics.
How Can B2B Buyers Verify Supplier Quality Control Practices?
Ensuring the integrity of a supplier’s quality control processes is vital for international B2B buyers. Here are actionable strategies:
What Steps Can Be Taken to Conduct Supplier Audits?
- On-Site Audits: Conducting physical inspections of the manufacturing facility to assess compliance with quality standards and practices.
- Documentation Review: Requesting access to quality assurance documents, such as inspection reports, process flows, and corrective action logs.
- Third-Party Inspections: Engaging independent organizations to conduct audits can provide an objective assessment of the supplier’s quality control processes.
How Can B2B Buyers Utilize Testing Methods to Ensure Quality?
Common testing methods include:
- Electrical Testing: To verify insulation resistance, winding resistance, and operational performance.
- Mechanical Testing: Assessing mechanical strength and durability through stress tests.
- Environmental Testing: Evaluating performance under extreme conditions (temperature, humidity, etc.).
B2B buyers should seek suppliers that routinely perform these tests and are willing to share the results.
What Unique Quality Control Considerations Exist for International Buyers?
For buyers from regions such as Africa, South America, the Middle East, and Europe, understanding the nuances of quality control is essential. Key considerations include:
- Regulatory Compliance: Understanding local regulations and ensuring that suppliers comply with them can prevent legal and operational issues.
- Cultural Differences: Being aware of different standards and practices in various regions can facilitate smoother negotiations and partnerships.
- Supply Chain Transparency: Ensuring that suppliers maintain transparency throughout the supply chain can help mitigate risks associated with product quality.
By being informed about these aspects, B2B buyers can make strategic decisions that enhance their procurement processes and ensure they receive high-quality electric motors.
Practical Sourcing Guide: A Step-by-Step Checklist for ‘electric motor’
To successfully procure electric motors, international B2B buyers must follow a strategic and detailed approach. This practical sourcing guide outlines essential steps to ensure you make informed decisions, minimize risks, and maximize value in your procurement process.
Step 1: Define Your Technical Specifications
Clearly outline the technical requirements for the electric motors you need. This includes voltage type (AC or DC), power rating, size, and application-specific features like torque and speed control. Precise specifications help you streamline the selection process and ensure compatibility with your existing systems.
- Consider application needs: Identify if the motors are for industrial machinery, HVAC systems, or other applications, as each may require different specifications.
- Evaluate energy efficiency: Specify the efficiency class (e.g., IE3, IE4) to ensure compliance with energy regulations and cost-effectiveness.
Step 2: Research and Identify Potential Suppliers
Conduct thorough research to identify potential suppliers specializing in electric motors. Look for manufacturers with a strong reputation and experience in your target market, particularly in Africa, South America, the Middle East, and Europe.
- Use industry directories: Resources like ThomasNet or Alibaba can help you find qualified suppliers.
- Check for regional expertise: Suppliers familiar with your region’s regulations and market dynamics may provide better support and compliance.
Step 3: Evaluate Supplier Certifications and Standards
Verify that potential suppliers meet relevant international and regional standards. Certifications such as ISO 9001 for quality management and CE marking for compliance with EU regulations are critical indicators of reliability.
- Request documentation: Ask suppliers for copies of their certifications to ensure they adhere to quality and safety standards.
- Assess environmental compliance: Check if the supplier follows eco-friendly practices, as this is increasingly important in global markets.
Step 4: Request and Compare Quotations
Once you have a shortlist of suppliers, request detailed quotations. This should include pricing, delivery timelines, warranty terms, and after-sales support.
- Break down costs: Ensure that quotations detail all costs, including shipping and taxes, to avoid unexpected expenses.
- Compare value, not just price: Look for suppliers that offer comprehensive support, including installation and maintenance services.
Step 5: Conduct Supplier Visits or Virtual Inspections
If possible, visit the supplier’s facilities to assess their manufacturing capabilities and quality control processes. If an in-person visit is not feasible, consider scheduling a virtual inspection.
- Evaluate production capacity: Ensure the supplier can meet your demand without compromising quality.
- Assess quality assurance practices: Look for robust testing procedures that ensure the motors meet specified standards.
Step 6: Negotiate Terms and Conditions
Once you have selected a supplier, negotiate terms and conditions that protect your interests. This includes payment terms, delivery schedules, and penalty clauses for non-compliance.
- Discuss payment options: Consider secure payment methods that protect against potential fraud.
- Establish clear delivery expectations: Ensure that delivery timelines are realistic and include contingencies for delays.
Step 7: Monitor Performance Post-Purchase
After procurement, continuously monitor the performance of the electric motors and the supplier’s service. Establish feedback mechanisms to assess efficiency, reliability, and overall satisfaction.
- Gather performance data: Track operational efficiency and maintenance needs to identify any issues early.
- Build a long-term relationship: Foster communication with your supplier for ongoing support and future procurement needs.
By following these steps, B2B buyers can navigate the complexities of sourcing electric motors effectively, ensuring that their investment yields optimal performance and reliability.
Comprehensive Cost and Pricing Analysis for electric motor Sourcing
What are the Key Cost Components in Electric Motor Sourcing?
When sourcing electric motors, international B2B buyers must consider various cost components that contribute to the overall pricing structure. Understanding these components can aid in making informed purchasing decisions.
-
Materials: The primary materials used in electric motors include copper, steel, aluminum, and insulation materials. The prices of these raw materials can fluctuate based on global market conditions, making it essential to monitor commodity prices regularly.
-
Labor: Labor costs vary significantly across regions. In countries with lower labor costs, such as some in Africa and South America, the manufacturing cost per motor may be reduced. However, the quality and skill level of the labor force can also impact the final product’s reliability.
-
Manufacturing Overhead: This includes costs related to utilities, equipment maintenance, and factory operations. Efficient manufacturing processes can lower overhead costs, which is crucial for competitiveness in pricing.
-
Tooling: The initial investment in tooling and machinery is substantial. Buyers should consider whether suppliers have the capacity to accommodate custom specifications without incurring excessive tooling costs.
-
Quality Control (QC): Implementing stringent QC measures is vital to ensure the motors meet specified performance standards. The costs associated with QC can vary based on the complexity of the motors and the certifications required.
-
Logistics: Transportation costs can significantly affect the total cost of acquisition. Factors such as distance, mode of transportation, and shipping terms (Incoterms) play a critical role in logistics costs.
-
Margin: Suppliers typically add a profit margin to cover their operating expenses and investment risks. Understanding the average market margins can help buyers negotiate better prices.
How Do Price Influencers Affect Electric Motor Sourcing?
Several factors influence the pricing of electric motors, and being aware of these can help buyers optimize their purchasing strategies.
-
Volume/MOQ: Bulk purchasing often leads to lower per-unit costs. Buyers should negotiate minimum order quantities (MOQs) that align with their operational needs to benefit from economies of scale.
-
Specifications and Customization: Custom specifications can lead to increased costs. Buyers must weigh the benefits of customization against the potential price increases, ensuring that the specifications align with operational requirements.
-
Materials: The choice of materials impacts not only the performance but also the cost. High-quality materials may lead to higher upfront costs but can reduce the total cost of ownership (TCO) through improved efficiency and longevity.
-
Quality and Certifications: Motors that meet international quality standards and certifications often come at a premium. Buyers should assess whether the additional cost aligns with their operational needs and regulatory requirements.
-
Supplier Factors: The reputation, reliability, and financial stability of suppliers can affect pricing. Long-term relationships with reputable suppliers may yield better pricing and terms.
-
Incoterms: The chosen Incoterms define the responsibilities of buyers and sellers in terms of shipping costs and risks. Understanding these terms can help buyers negotiate better shipping arrangements and avoid unexpected costs.
What Tips Can Help B2B Buyers Optimize Costs?
International B2B buyers can adopt several strategies to maximize cost-efficiency when sourcing electric motors:
-
Negotiation: Building a good rapport with suppliers can lead to more favorable pricing and terms. Engaging in open discussions about pricing structures can uncover potential cost-saving opportunities.
-
Focus on Total Cost of Ownership (TCO): Instead of just considering the initial purchase price, buyers should evaluate the TCO, which includes maintenance, energy consumption, and potential downtime costs. This holistic view can lead to more strategic purchasing decisions.
-
Pricing Nuances for International Buyers: Buyers from regions such as Africa, South America, the Middle East, and Europe should be aware of regional pricing differences and potential tariffs or trade barriers that could affect the final cost.
-
Conduct Market Research: Understanding market trends and competitor pricing can provide leverage in negotiations. Buyers should stay informed about the latest developments in the electric motor industry.
-
Request Multiple Quotes: Obtaining quotes from various suppliers can help buyers gauge the market rate and negotiate better terms. This practice encourages competitive pricing and transparency.
Disclaimer
Prices mentioned in this analysis are indicative and may vary based on market conditions, supplier negotiations, and specific project requirements. Always consult with suppliers for accurate pricing tailored to your needs.
Alternatives Analysis: Comparing electric motor With Other Solutions
Understanding Alternatives to Electric Motors
In the evolving landscape of industrial machinery, electric motors have long been the standard for converting electrical energy into mechanical energy. However, as international B2B buyers seek more efficient and sustainable solutions, it’s crucial to explore viable alternatives. These alternatives can offer unique advantages depending on the specific application, budget constraints, and operational environments. Below, we delve into a comparative analysis of electric motors against two prominent alternatives: pneumatic systems and hydraulic systems.
Comparison Table of Electric Motors and Alternatives
Comparison Aspect | Electric Motor | Pneumatic System | Hydraulic System |
---|---|---|---|
Performance | High efficiency, precise control over speed and torque | Quick response, suitable for repetitive tasks | High force output, excellent for heavy loads |
Cost | Moderate initial investment, low operational costs | Lower initial costs, but higher energy costs | Higher initial investment, but cost-effective for heavy-duty applications |
Ease of Implementation | Generally straightforward, requires electrical infrastructure | Easy to implement in existing systems, requires air compressor | More complex setup, requires hydraulic pumps and reservoirs |
Maintenance | Low maintenance, occasional need for brush replacement | Moderate maintenance, filters and hoses need regular checks | High maintenance, potential for leaks and requires regular fluid changes |
Best Use Case | Robotics, conveyor systems, HVAC | Assembly lines, tools, and light machinery | Construction equipment, heavy lifting applications |
Detailed Breakdown of Alternatives
What Are the Advantages and Disadvantages of Pneumatic Systems?
Pneumatic systems utilize compressed air to perform work and are often favored for their quick response times. They excel in applications requiring rapid movement and repetitive tasks, such as in assembly lines or packaging. The initial investment in pneumatic technology can be lower than electric motors, but operational costs can be higher due to energy consumption and the need for an air compressor. Additionally, pneumatic systems can be less precise than electric motors, which may be a drawback for applications requiring fine control.
How Do Hydraulic Systems Compare to Electric Motors?
Hydraulic systems are another alternative that operates using pressurized fluid to transmit power. They are particularly advantageous in applications requiring high force output, such as construction equipment and heavy machinery. While hydraulic systems can handle significant loads efficiently, they typically involve a higher initial investment and more complex installation compared to electric motors. Maintenance can also be a challenge due to potential leaks and the need for regular fluid changes. However, for heavy-duty applications, the power-to-weight ratio of hydraulic systems makes them an attractive option.
How Should B2B Buyers Choose the Right Solution?
Selecting the appropriate solution for your operational needs requires a thorough understanding of each technology’s strengths and weaknesses. B2B buyers should consider factors such as the specific application, budget constraints, and the required level of precision. Electric motors may be the ideal choice for tasks demanding high efficiency and precision control, while pneumatic systems are suitable for rapid, repetitive tasks. Conversely, hydraulic systems shine in applications involving heavy lifting and force. Ultimately, aligning the choice with the operational goals and infrastructure will yield the best long-term results.
Essential Technical Properties and Trade Terminology for electric motor
What Are the Essential Technical Properties of Electric Motors?
Understanding the technical properties of electric motors is crucial for B2B buyers, especially when sourcing motors for various applications. Here are some key specifications that should be considered:
1. Power Rating (Horsepower or Kilowatts)
The power rating indicates the motor’s capacity to perform work. It is typically measured in horsepower (HP) or kilowatts (kW). For B2B buyers, selecting a motor with the appropriate power rating is essential for ensuring it meets the operational demands of their applications. An undersized motor may lead to overheating and failure, while an oversized motor can be inefficient and costly.
2. Efficiency Class (IE Ratings)
Electric motors are rated for efficiency, often categorized by the International Electrotechnical Commission (IEC) as IE1, IE2, IE3, etc. Higher efficiency ratings correspond to lower energy consumption and reduced operating costs. For international buyers, particularly in regions facing energy challenges, investing in higher efficiency motors can lead to significant long-term savings and sustainability benefits.
3. Torque Rating
Torque is a measure of rotational force and is critical for applications requiring specific movement capabilities. Torque ratings can be categorized as starting torque, running torque, or peak torque. For B2B buyers, understanding the torque requirements of their applications will help in selecting the right motor, ensuring optimal performance and longevity.
4. Frame Size and Mounting Type
The physical dimensions and mounting configuration of a motor are vital for integration into existing machinery or systems. Frame size affects the motor’s thermal performance and compatibility with mounting systems. Buyers should ensure that the selected motor fits within the specified space constraints and aligns with the existing infrastructure.
5. Insulation Class
Insulation class indicates the thermal tolerance of the motor’s windings, impacting its operational lifespan. Common classes include A, B, F, and H, with higher classes suitable for more demanding environments. For B2B buyers, selecting a motor with the appropriate insulation class can prevent premature failure due to overheating, particularly in harsh operating conditions.
What Are Common Trade Terminologies Related to Electric Motors?
Familiarity with industry jargon is essential for effective communication and negotiation in B2B transactions. Here are several key terms that buyers should know:
1. OEM (Original Equipment Manufacturer)
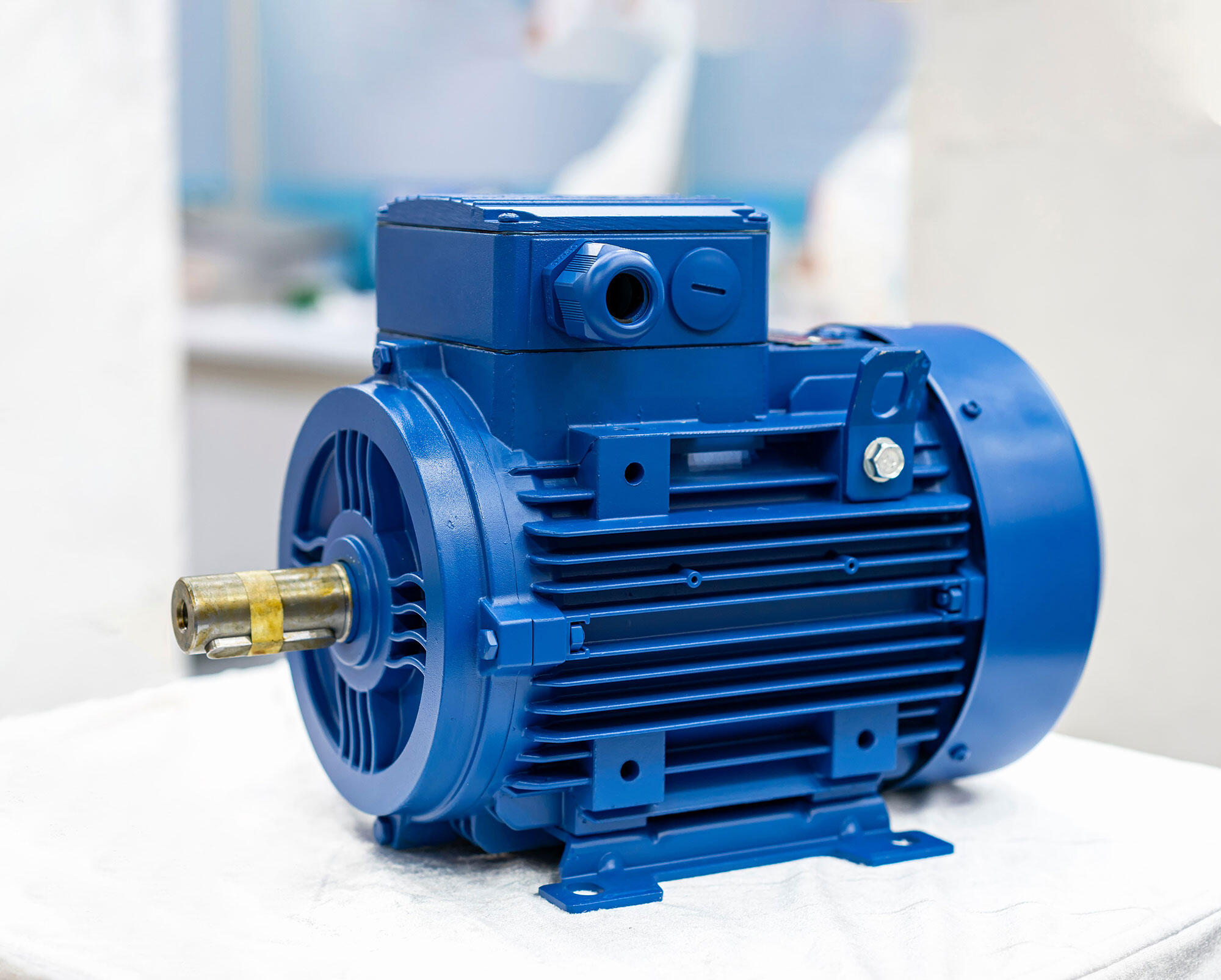
A stock image related to electric motor.
OEM refers to companies that produce parts or equipment that may be marketed by another manufacturer. When sourcing electric motors, buyers should consider OEMs for reliable quality and compatibility with their existing systems. OEM relationships can also provide better warranty support and service options.
2. MOQ (Minimum Order Quantity)
MOQ indicates the smallest quantity of a product that a supplier is willing to sell. Understanding MOQ is crucial for B2B buyers to manage inventory and cost effectively. Negotiating favorable MOQs can help in reducing initial investment while ensuring adequate supply.
3. RFQ (Request for Quotation)
An RFQ is a document that buyers send to suppliers to request pricing and availability for a specific quantity of products. Issuing an RFQ is an essential step in the procurement process, as it allows buyers to compare offers and select the best supplier based on price, quality, and delivery terms.
4. Incoterms (International Commercial Terms)
Incoterms are internationally recognized rules that define the responsibilities of buyers and sellers in the transportation of goods. Understanding Incoterms is vital for B2B transactions, as they dictate who bears the risk and costs associated with shipping, insurance, and customs clearance. This knowledge helps buyers avoid unexpected expenses and delays.
5. Lead Time
Lead time refers to the time taken from placing an order to receiving the goods. For B2B buyers, understanding lead times is critical for project planning and ensuring that operations run smoothly. Longer lead times may necessitate earlier order placements to avoid disruptions.
By familiarizing themselves with these technical specifications and trade terminologies, international B2B buyers can make informed decisions, ensuring they select the right electric motors for their specific needs.
Navigating Market Dynamics and Sourcing Trends in the electric motor Sector
What Are the Key Market Dynamics and Trends in the Electric Motor Sector?
The electric motor market is experiencing robust growth driven by several global factors. The increasing demand for energy-efficient solutions, driven by both regulatory frameworks and corporate sustainability goals, is a significant market driver. Electric motors are integral to various applications, from industrial machinery to consumer electronics, making them vital for operational efficiency. As international B2B buyers from Africa, South America, the Middle East, and Europe explore sourcing opportunities, understanding the dynamics of this market is crucial.
Emerging technologies, such as the Internet of Things (IoT) and advanced manufacturing techniques like 3D printing, are reshaping the electric motor landscape. IoT integration allows for real-time monitoring and predictive maintenance, enhancing the lifespan and efficiency of motors. In addition, the push towards automation in manufacturing sectors across these regions is leading to increased demand for high-performance electric motors. Buyers should pay attention to suppliers that leverage these technologies to ensure they are sourcing innovative and competitive products.
Moreover, the shift towards renewable energy sources is influencing the types of motors in demand. Synchronous motors and those designed for variable speed applications are becoming increasingly popular, especially in regions investing heavily in green technologies. For B2B buyers, aligning with suppliers that prioritize these trends can provide a competitive edge in their respective markets.
How Can Sustainability and Ethical Sourcing Impact Electric Motor Procurement?
Sustainability is no longer a mere trend; it has become a necessity in the procurement of electric motors. The environmental impact of motor production, including energy consumption and waste generation, necessitates a focus on sustainable practices. Buyers must evaluate suppliers based on their commitment to reducing their carbon footprint and implementing eco-friendly manufacturing processes.
Ethical sourcing is equally important. The sourcing of raw materials, such as rare earth metals used in permanent magnets, should be conducted responsibly. B2B buyers should prioritize suppliers that are transparent about their supply chains and have certifications for ethical practices. This includes adherence to standards such as ISO 14001 for environmental management and SA8000 for social accountability.
Additionally, ‘green’ certifications for electric motors, such as Energy Star or similar energy efficiency labels, can guide buyers in selecting products that meet sustainability criteria. By emphasizing sustainability and ethical sourcing, businesses can not only comply with regulations but also enhance their brand reputation and appeal to environmentally-conscious consumers.
What Is the Historical Context of Electric Motors Relevant to Today’s B2B Market?
The evolution of electric motors dates back to the early 19th century, with significant contributions from inventors like Nikola Tesla and Michael Faraday. The advent of alternating current (AC) technology revolutionized the electric motor industry, enabling the widespread use of electric motors in various applications. This historical context is vital for today’s B2B buyers as it highlights the ongoing innovation in motor technology.
The transition from simple DC motors to advanced induction and synchronous motors reflects a broader trend towards efficiency and performance. Understanding this evolution can help buyers appreciate the complexities and advancements in electric motor technology, enabling them to make informed sourcing decisions. As the market continues to innovate, staying abreast of these historical advancements can provide valuable insights into future trends and supplier capabilities.
Frequently Asked Questions (FAQs) for B2B Buyers of electric motor
-
How do I solve compatibility issues when sourcing electric motors for my machinery?
To address compatibility issues, first, clearly define the specifications of your existing machinery, including voltage, phase, and horsepower requirements. Consult with suppliers who can provide detailed technical information and support. It’s crucial to engage in discussions about the intended application, environmental conditions, and any industry standards that must be met. Request samples or prototypes for testing, and consider using adaptable motor mounts or couplings to ensure seamless integration. -
What is the best type of electric motor for industrial applications?
The best type of electric motor for industrial applications depends on your specific needs. Generally, three-phase induction motors are favored for their efficiency and reliability in high-power applications. For precision control, servomotors or stepper motors are ideal. Evaluate factors such as torque requirements, operating environment, and available power supply to make an informed decision. Engaging with suppliers who specialize in industrial motors can also provide insights tailored to your application. -
How can I ensure the quality of electric motors from international suppliers?
To ensure quality, it’s essential to conduct thorough supplier vetting. Look for manufacturers with ISO certifications, and request references or case studies from previous clients. Conduct factory audits, if possible, to observe production processes. Additionally, ask for quality assurance documentation, including test reports and warranties. Establishing clear quality expectations in your contracts will also help in maintaining product standards. -
What are typical minimum order quantities (MOQs) for electric motors?
Minimum order quantities (MOQs) for electric motors can vary significantly by supplier and motor type. Generally, MOQs may range from a few units for standard motors to hundreds for specialized or custom designs. Discuss your requirements with suppliers to negotiate MOQs that align with your procurement strategy. Consider pooling orders with other buyers or scheduling regular purchases to meet MOQ requirements while minimizing inventory costs.
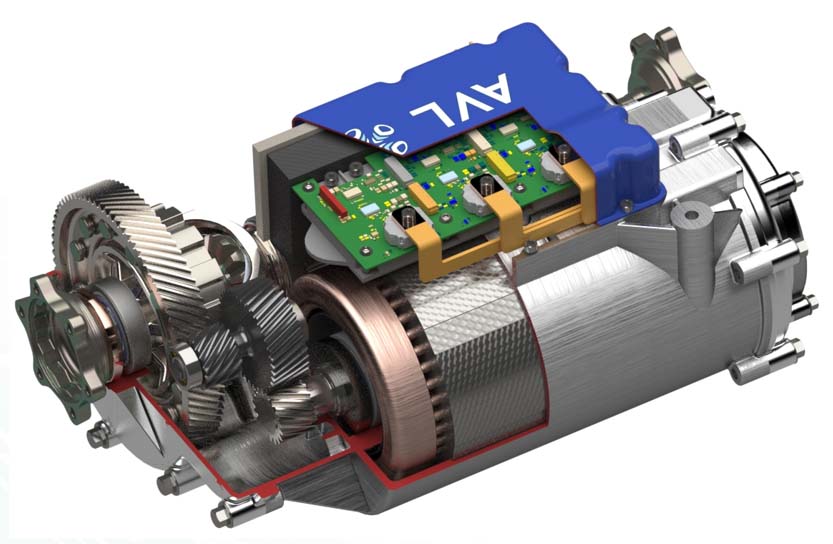
A stock image related to electric motor.
-
What payment terms should I expect when sourcing electric motors internationally?
Payment terms vary widely by supplier and region. Common arrangements include partial upfront payments (e.g., 30%) with the balance due upon delivery, or payment via letter of credit to ensure security for both parties. Always clarify payment methods accepted, such as bank transfers, credit terms, or escrow services. Negotiating favorable terms can enhance cash flow while ensuring timely delivery of products. -
How do I handle logistics and shipping for electric motors from overseas suppliers?
Effective logistics management is crucial when sourcing electric motors internationally. Work with suppliers who have experience in global shipping and understand local regulations. Ensure that the packaging is suitable for transportation to prevent damage. Consider using freight forwarders to navigate customs and import duties. It’s also wise to clarify delivery timelines and responsibilities for shipping costs to avoid unexpected expenses. -
What certifications should I look for when sourcing electric motors?
When sourcing electric motors, look for relevant certifications that indicate compliance with international standards. Common certifications include CE marking for compliance with European safety directives, UL certification for safety in North America, and ISO 9001 for quality management systems. Depending on your industry, additional certifications may be necessary, such as ATEX for explosive environments or RoHS for restriction of hazardous substances. -
How can I customize electric motors to fit my specific application needs?
Customization options for electric motors can include modifications to size, power rating, voltage, and speed. Engage with your supplier early in the design process to discuss your specific requirements. Many manufacturers offer custom solutions, but be prepared to provide detailed specifications and possibly commit to larger orders for unique designs. Collaborating closely with engineers from the supplier can streamline the process and ensure that the final product meets your operational needs.
Important Disclaimer & Terms of Use
⚠️ Important Disclaimer
The information provided in this guide, including content regarding manufacturers, technical specifications, and market analysis, is for informational and educational purposes only. It does not constitute professional procurement advice, financial advice, or legal advice.
While we have made every effort to ensure the accuracy and timeliness of the information, we are not responsible for any errors, omissions, or outdated information. Market conditions, company details, and technical standards are subject to change.
B2B buyers must conduct their own independent and thorough due diligence before making any purchasing decisions. This includes contacting suppliers directly, verifying certifications, requesting samples, and seeking professional consultation. The risk of relying on any information in this guide is borne solely by the reader.
Strategic Sourcing Conclusion and Outlook for electric motor
What Are the Key Takeaways for B2B Buyers in Electric Motors?
In the evolving landscape of electric motors, strategic sourcing has emerged as a critical component for international B2B buyers. Understanding the distinction between AC and DC motors, along with their respective applications, is vital for making informed purchasing decisions. Prioritizing energy efficiency and sustainability will not only reduce operational costs but also align with global environmental standards, particularly in regions like Europe and parts of South America.
How Can Strategic Sourcing Enhance Your Supply Chain?
Effective strategic sourcing can significantly enhance supply chain resilience by diversifying supplier bases and mitigating risks associated with geopolitical tensions and economic fluctuations, especially relevant for buyers in Africa and the Middle East. By fostering strong partnerships with manufacturers and suppliers, businesses can secure better pricing and more favorable terms, ultimately enhancing their competitive edge in the marketplace.
What’s Next for B2B Buyers in the Electric Motor Market?
Looking ahead, international B2B buyers should remain vigilant about technological advancements in electric motors, such as the rise of smart motors and IoT integration. Embracing these innovations can provide a substantial advantage in optimizing performance and efficiency. As you navigate this dynamic market, consider leveraging your sourcing strategies to not only meet current demands but also to anticipate future trends. The time to act is now—align your sourcing strategies with the future of electric motors to drive your business forward.