Unlock Efficiency: The Ultimate Gantry Crane Guide (2025)
Introduction: Navigating the Global Market for gantry crane
In the dynamic landscape of global industrial operations, sourcing the right gantry crane can be a daunting task for international B2B buyers, particularly those in Africa, South America, the Middle East, and Europe. As businesses scale their operations, the need for versatile, durable, and efficient lifting solutions becomes paramount. This guide delves into the essential aspects of gantry cranes, offering insights on various types, applications, and the nuances of supplier vetting. It addresses key challenges such as understanding load capacities, selecting between fixed and adjustable options, and evaluating cost implications.
With a comprehensive exploration of the gantry crane market, this resource empowers decision-makers to navigate their purchasing journey with confidence. It provides actionable insights that help buyers assess their unique operational needs, ensuring they select the most suitable equipment for their specific applications. From understanding the differences between aluminum and steel cranes to evaluating the benefits of mobile versus fixed systems, this guide equips B2B buyers with the knowledge necessary to make informed choices.
Moreover, by focusing on suppliers that meet international standards, buyers can mitigate risks associated with quality and compliance. This guide serves as a crucial tool for businesses looking to optimize their lifting operations, enhancing productivity and ensuring safety in their workplaces. Whether you’re in heavy manufacturing, construction, or logistics, understanding the global gantry crane market is key to driving efficiency and achieving operational excellence.
Understanding gantry crane Types and Variations
Type Name | Key Distinguishing Features | Primary B2B Applications | Brief Pros & Cons for Buyers |
---|---|---|---|
Fixed Height Gantry Crane | Non-adjustable height, sturdy construction | Manufacturing, Warehousing | Pros: Simple setup, cost-effective. Cons: Limited flexibility in height adjustments. |
Adjustable Height Gantry Crane | Height can be modified to suit different loads | Construction, Automotive Repair | Pros: Versatile, accommodates various lifting needs. Cons: Slightly more expensive and complex. |
Heavy Duty Gantry Crane | Designed for high-load capacities (up to 10 tons) | Heavy Industry, Shipbuilding, Oil & Gas | Pros: Robust design for extreme conditions. Cons: Requires significant investment and space. |
Aluminum Gantry Crane | Lightweight, portable, rust-resistant | Aerospace, Maintenance, Outdoor Applications | Pros: Easy to transport, corrosion-resistant. Cons: Lower load capacity compared to steel. |
Telescoping Gantry Crane | Adjustable span and height, versatile configurations | Logistics, Heavy Lifting in Tight Spaces | Pros: Compact storage, adaptable for various tasks. Cons: May require more frequent maintenance. |
What are the characteristics of a Fixed Height Gantry Crane?
Fixed height gantry cranes are designed with a non-adjustable height, providing a stable lifting solution for various industrial applications. Typically constructed from robust materials, they are ideal for tasks that require consistent height for lifting and transporting goods. These cranes are particularly suitable for manufacturing and warehousing where the lifting requirements do not vary significantly. Buyers should consider their need for flexibility, as fixed height models may not accommodate changing operational demands.
How does an Adjustable Height Gantry Crane enhance operational versatility?
Adjustable height gantry cranes allow users to modify the lifting height, making them highly adaptable for different applications. This feature is especially beneficial in industries such as construction and automotive repair, where the height of the load may vary. While these cranes offer greater flexibility compared to fixed models, they typically come at a higher cost and may require more complex assembly. Buyers should evaluate their specific lifting needs and budget before purchasing.
What makes Heavy Duty Gantry Cranes essential for high-load applications?
Heavy duty gantry cranes are engineered to handle substantial loads, often exceeding 10 tons, making them indispensable in heavy industries like shipbuilding and oil & gas. Their robust construction ensures safety and reliability under extreme conditions. However, the investment required for these cranes is significant, and they necessitate adequate space for operation. Buyers must assess their load requirements and operational environment to determine if a heavy-duty model is necessary.
Why choose an Aluminum Gantry Crane for specific applications?
Aluminum gantry cranes are favored for their lightweight and portable design, making them ideal for applications in aerospace and maintenance where mobility is crucial. Their rust-resistant properties also make them suitable for outdoor use. However, they generally have lower load capacities compared to steel cranes, which may limit their use in heavier industrial settings. B2B buyers should weigh the benefits of portability against the load requirements of their operations.
What advantages do Telescoping Gantry Cranes offer for logistics?
Telescoping gantry cranes provide adjustable spans and heights, making them versatile for various lifting tasks, particularly in logistics and tight spaces. Their ability to collapse for storage adds convenience for businesses with limited space. However, the need for regular maintenance and potential wear on moving parts should be taken into account by buyers. Evaluating the balance between versatility and maintenance needs is crucial for making an informed purchasing decision.
Key Industrial Applications of gantry crane
Industry/Sector | Specific Application of Gantry Crane | Value/Benefit for the Business | Key Sourcing Considerations for this Application |
---|---|---|---|
Manufacturing | Assembly Line Support | Increases efficiency in moving heavy components | Ensure load capacity matches production needs; consider mobility features. |
Construction | Heavy Equipment Lifting | Streamlines lifting and placement of machinery | Look for cranes with adjustable height and robust construction for durability. |
Shipbuilding | Vessel Assembly and Maintenance | Enhances safety and precision in heavy lifting | Evaluate corrosion resistance, especially for marine environments. |
Aerospace | Aircraft Component Handling | Facilitates safe transport of sensitive parts | Assess crane adaptability for various load types and sizes; check for custom solutions. |
Oil & Gas | Equipment Installation and Maintenance | Reduces downtime and labor costs during operations | Verify compliance with industry standards and load specifications. |
How Are Gantry Cranes Used in Manufacturing?
In the manufacturing sector, gantry cranes are essential for supporting assembly lines. They are employed to lift and move heavy components, such as machinery parts and assemblies, from one station to another. This application significantly increases operational efficiency, allowing for smoother workflows and reduced labor costs. For international buyers, particularly from regions like Africa and South America, it is crucial to consider the load capacity of the gantry crane to ensure it meets specific production requirements. Additionally, mobility features such as casters are important for flexible workspace arrangements.
What Role Do Gantry Cranes Play in Construction?
Gantry cranes are widely used in construction for lifting heavy equipment like concrete blocks and machinery. Their ability to adjust height makes them ideal for various construction projects, facilitating the precise placement of materials. This adaptability not only streamlines the construction process but also enhances safety on site. Buyers from the Middle East and Europe should prioritize cranes with robust construction materials to withstand harsh environmental conditions and heavy usage.
How Are Gantry Cranes Beneficial in Shipbuilding?
In the shipbuilding industry, gantry cranes are critical for both assembly and maintenance tasks. They allow workers to lift and position heavy components accurately, thereby enhancing safety and precision in handling large vessels. Given the exposure to marine environments, it is vital for buyers to source cranes that offer corrosion resistance and can handle the specific weight requirements of ship components. This consideration is especially pertinent for international buyers in coastal regions.
How Do Gantry Cranes Support Aerospace Operations?
Gantry cranes are utilized in the aerospace industry for handling delicate aircraft components. Their design allows for the safe transport of sensitive parts, which is crucial for maintaining the integrity of the products. Buyers in Europe and South America should look for cranes that offer customization options to adapt to various load sizes and types, ensuring they meet the stringent safety standards prevalent in aerospace manufacturing.
Why Are Gantry Cranes Important in Oil & Gas?
In the oil and gas sector, gantry cranes play a vital role in the installation and maintenance of heavy equipment. They help minimize downtime during operations, which is critical for maximizing productivity and reducing labor costs. International buyers should ensure that the cranes comply with industry standards and can handle the specific weight and load requirements typical in oil and gas operations.
3 Common User Pain Points for ‘gantry crane’ & Their Solutions
Scenario 1: Difficulty in Selecting the Right Gantry Crane Capacity
The Problem: One of the most common challenges faced by B2B buyers is selecting a gantry crane with the appropriate lifting capacity. In regions like Africa and South America, where industries may vary significantly in their operational demands, buyers often struggle to determine the correct weight specifications. Overestimating the required capacity can lead to unnecessary costs, while underestimating it can result in equipment failure and safety hazards. This confusion is exacerbated by the diverse range of available models and their specifications, making it difficult to make an informed decision.
The Solution: To effectively select the right gantry crane capacity, buyers should conduct a thorough assessment of their lifting needs. Start by listing the heaviest items you plan to lift and their dimensions. Include any potential future needs to avoid purchasing a crane that may quickly become inadequate. Consult with suppliers who offer customizable options or kits that allow for adjustments in capacity. It’s also advisable to leverage online calculators or tools provided by manufacturers to estimate the appropriate capacity. Lastly, consider the operational environment (e.g., outdoor vs. indoor use) as this can impact the crane’s performance and longevity.
Scenario 2: Challenges with Gantry Crane Mobility and Maneuverability
The Problem: Another significant pain point for buyers is the mobility and maneuverability of gantry cranes, especially in confined spaces such as warehouses or construction sites. Many businesses in the Middle East and Europe deal with tight working environments, where the ability to move heavy loads efficiently is critical. Fixed-height cranes may limit flexibility, and buyers often find themselves frustrated when they cannot easily reposition equipment as needed.
The Solution: To address mobility issues, buyers should consider investing in adjustable height gantry cranes with casters that are designed for easy maneuvering. Look for models that feature robust wheel systems, including locking casters, to secure the crane in place once positioned. Additionally, ensure that the crane’s design allows for easy disassembly and reassembly, enabling quick relocation. When selecting a gantry crane, prioritize those that offer a lightweight design without sacrificing stability. Suppliers often provide guidance on the best models for specific environments, so don’t hesitate to ask for recommendations based on your operational layout.
Scenario 3: Maintenance and Safety Concerns with Gantry Cranes
The Problem: Maintenance and safety are top concerns for international buyers, particularly in industries with stringent regulatory requirements like those found in Europe and the Middle East. Buyers often worry about the long-term durability of gantry cranes, especially in harsh environments or when lifting heavy equipment. Inadequate maintenance can lead to accidents, equipment failure, and increased downtime, which can be costly.
The Solution: To mitigate maintenance and safety issues, buyers should establish a comprehensive maintenance plan that includes regular inspections and servicing of the gantry crane. This plan should adhere to the manufacturer’s guidelines, focusing on critical components like wheels, hoists, and structural integrity. Additionally, consider investing in cranes made from durable materials such as steel or aluminum with protective coatings for outdoor use. Implementing training programs for employees on proper gantry crane operation and safety protocols will further enhance workplace safety. Finally, consider suppliers that offer warranty and support services, as having access to professional assistance can ensure that any potential issues are addressed promptly, minimizing downtime and risk.
Strategic Material Selection Guide for gantry crane
When selecting materials for gantry cranes, international B2B buyers must consider various factors such as load capacity, environmental conditions, and compliance with industry standards. Here, we analyze four common materials used in the construction of gantry cranes: steel, aluminum, stainless steel, and composite materials. Each material has unique properties and implications for performance, cost, and application suitability.
What Are the Key Properties of Steel for Gantry Cranes?
Steel is the most commonly used material for gantry cranes due to its excellent strength-to-weight ratio. It can withstand high loads and harsh conditions, making it suitable for heavy-duty applications. Steel typically has a high temperature and pressure rating, which is crucial for industrial environments.
Pros: Steel’s durability and strength make it ideal for lifting heavy loads. It is also relatively cost-effective compared to other materials, making it a popular choice for many businesses.
Cons: However, steel is prone to corrosion if not properly treated, which can lead to increased maintenance costs. Additionally, it can be heavier than alternative materials, potentially impacting mobility.
Impact on Application: Steel cranes are well-suited for environments where high load capacities are required, such as manufacturing plants and shipyards. Buyers must consider local climate conditions to ensure appropriate protective coatings are applied.
How Does Aluminum Compare as a Material for Gantry Cranes?
Aluminum is a lightweight alternative to steel, offering good strength while reducing the overall weight of the crane. This characteristic makes aluminum cranes easier to move and adjust, particularly in applications requiring frequent repositioning.
Pros: The primary advantage of aluminum is its resistance to corrosion, which reduces maintenance needs and extends the lifespan of the crane. It is also more suitable for environments where weight is a critical factor.
Cons: The downside is that aluminum generally has a lower load capacity compared to steel, making it less suitable for heavy lifting applications. Additionally, aluminum can be more expensive than steel, which may affect budget considerations.
Impact on Application: Aluminum cranes are ideal for lighter applications in industries such as automotive or electronics, where mobility and corrosion resistance are essential. Buyers should ensure compliance with local standards, as aluminum cranes may require specific certifications.
What Are the Benefits of Using Stainless Steel for Gantry Cranes?
Stainless steel is highly valued for its exceptional corrosion resistance and aesthetic appeal. It is often used in environments where exposure to moisture or chemicals is a concern, such as food processing or pharmaceuticals.
Pros: The main advantage of stainless steel is its ability to withstand harsh environments without degrading. This material also requires minimal maintenance, which can lead to long-term cost savings.
Cons: However, stainless steel is typically more expensive than both steel and aluminum, which may be a barrier for some buyers. Its weight can also be a consideration, as it may limit mobility.
Impact on Application: Stainless steel cranes are perfect for applications requiring high hygiene standards and environmental resilience. Buyers must ensure that the selected stainless steel grade meets relevant industry standards, such as ASTM or DIN.
Are Composite Materials a Viable Option for Gantry Cranes?
Composite materials, such as fiberglass or carbon fiber, are emerging as alternatives in the crane industry. These materials offer unique properties, including lightweight and high strength.
Pros: Composites are resistant to corrosion and can be engineered for specific applications, providing flexibility in design. They are also significantly lighter than metals, which enhances mobility.
Cons: The primary limitation is the cost, as composites can be substantially more expensive than traditional materials. Additionally, their load-bearing capabilities may not match those of steel or aluminum, which can limit their use in heavy lifting scenarios.
Impact on Application: Composite cranes are suitable for specialized applications where weight and corrosion resistance are critical, such as in marine or aerospace industries. Buyers should verify the material’s compliance with relevant standards and its suitability for specific lifting tasks.
Summary Table of Material Selection for Gantry Cranes
Material | Typical Use Case for gantry crane | Key Advantage | Key Disadvantage/Limitation | Relative Cost (Low/Med/High) |
---|---|---|---|---|
Steel | Heavy-duty industrial lifting | High strength and load capacity | Prone to corrosion | Medium |
Aluminum | Light-duty applications | Lightweight and corrosion-resistant | Lower load capacity | High |
Stainless Steel | Food processing, pharmaceuticals | Excellent corrosion resistance | Higher cost and weight | High |
Composite | Specialized applications (marine/aerospace) | Lightweight and customizable | High cost and limited load capacity | High |
This guide provides a comprehensive overview of the materials commonly used in gantry cranes, aiding international B2B buyers in making informed decisions tailored to their specific operational needs and environmental conditions.
In-depth Look: Manufacturing Processes and Quality Assurance for gantry crane
What Are the Key Stages in the Manufacturing Process of Gantry Cranes?
The manufacturing process for gantry cranes involves several critical stages, each designed to ensure that the end product meets the specific requirements of strength, durability, and functionality. Understanding these stages can help international B2B buyers make informed purchasing decisions.
Material Preparation: What Materials Are Used?
The first step in manufacturing gantry cranes is material preparation. Typically, high-strength steel, aluminum, or stainless steel is selected based on the crane’s intended use. The choice of material affects the crane’s load capacity, durability, and corrosion resistance. For instance, aluminum is often used for lighter, portable cranes, while steel is preferred for heavy-duty applications.
Once materials are sourced, they undergo cutting, shearing, and welding to create the necessary components. Buyers should ensure that their suppliers utilize high-quality materials and follow rigorous standards during this initial phase.
How Are Gantry Cranes Formed?
The forming stage involves shaping the prepared materials into the structural components of the crane, including the main beams, legs, and cross members. This is accomplished through various techniques such as bending, punching, and machining. Advanced CNC (Computer Numerical Control) machinery is frequently employed to ensure precision and repeatability in manufacturing.
This stage is crucial for ensuring that all parts fit together correctly, which directly impacts the crane’s stability and performance. Buyers should inquire about the machinery and techniques used by suppliers to guarantee high-quality production standards.
What Happens During the Assembly Process?
In the assembly stage, the formed components are brought together to create the complete gantry crane. This process may involve bolting, welding, or riveting the parts together, depending on the design specifications.
Quality control checkpoints are essential during assembly to confirm that every part is correctly installed and meets engineering specifications. Buyers should verify that their suppliers implement stringent assembly protocols, including detailed assembly instructions and trained personnel to oversee the process.
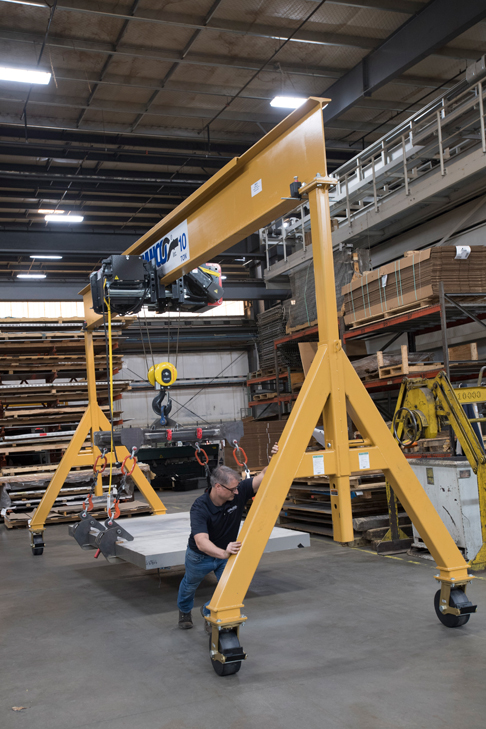
A stock image related to gantry crane.
How Is the Finishing Process Conducted?
The finishing stage of gantry crane manufacturing typically includes surface treatments such as painting, galvanizing, or applying powder coating. These processes enhance the crane’s resistance to corrosion and wear, extending its lifespan in various environments, including outdoor settings.
For international buyers, particularly those in humid or coastal regions, understanding the finishing processes can be critical. Suppliers should provide documentation on the types of finishes used and their expected performance in specific conditions.
What Quality Assurance Standards Should B2B Buyers Consider?
Quality assurance is vital in the manufacturing of gantry cranes, as it ensures that the final product meets safety and performance standards. International B2B buyers should be aware of relevant quality certifications and checkpoints throughout the manufacturing process.
Which International Standards Are Relevant for Gantry Cranes?
ISO 9001 is a widely recognized international standard for quality management systems. Suppliers who hold this certification demonstrate a commitment to maintaining quality throughout their operations. Additionally, industry-specific certifications such as CE marking (for European markets) and API (American Petroleum Institute) standards can also be significant indicators of quality and safety.
It is advisable for buyers to request evidence of these certifications from suppliers, as they reflect a commitment to quality and regulatory compliance.
What Are the Key Quality Control Checkpoints in Manufacturing?
Quality control (QC) checkpoints are established at various stages of the manufacturing process to ensure that components meet specified standards. Key checkpoints include:
- Incoming Quality Control (IQC): This involves inspecting raw materials upon arrival to confirm they meet predefined specifications.
- In-Process Quality Control (IPQC): Inspections conducted during the manufacturing process to identify any defects early on.
- Final Quality Control (FQC): A thorough examination of the finished product to ensure it adheres to quality standards before shipment.
Buyers should confirm that suppliers have established and documented QC processes, including the frequency and methodology of inspections.
How Can B2B Buyers Verify Supplier Quality Control?
Verifying a supplier’s quality control processes is essential for B2B buyers, especially those engaged in international trade. Here are several methods to ensure that your supplier meets quality standards:
What Audit Processes Should Buyers Implement?
Conducting regular audits of suppliers is an effective way to verify their adherence to quality standards. Buyers can request third-party audits or certifications to assess the supplier’s manufacturing processes, quality control measures, and compliance with international standards.
How Can Buyers Utilize Testing Methods to Ensure Quality?
Common testing methods include load testing, where the crane is subjected to its maximum load capacity to ensure it operates safely and effectively. Other methods may include non-destructive testing (NDT) to assess the integrity of welded joints and components without damaging them.
Buyers should ask suppliers for detailed reports of these tests, including methodologies and results, to gain insight into the crane’s reliability and safety.
What Are the Unique Quality Control Considerations for International Buyers?
For B2B buyers from regions such as Africa, South America, the Middle East, and Europe, understanding the nuances of quality control is crucial. Each region may have different regulations and standards that affect the manufacturing and certification of gantry cranes.
How Can Regional Standards Affect Quality Assurance?
Different countries may have specific safety regulations that affect how cranes are manufactured and certified. For instance, European buyers should ensure that their suppliers comply with CE marking requirements, which signify adherence to EU safety standards.
Understanding these regional differences can help buyers avoid potential compliance issues and ensure that their cranes meet local regulations. Always consult with local industry experts or legal advisors to navigate these complexities effectively.
Conclusion
International B2B buyers looking to procure gantry cranes should have a comprehensive understanding of the manufacturing processes and quality assurance standards involved. By focusing on material selection, manufacturing techniques, and rigorous quality control measures, buyers can ensure they select reliable suppliers that meet their operational needs. This knowledge empowers buyers to make informed decisions, ultimately leading to safer and more efficient lifting solutions for their businesses.
Practical Sourcing Guide: A Step-by-Step Checklist for ‘gantry crane’
When sourcing gantry cranes for your business, it’s essential to follow a structured approach to ensure you select the right equipment for your needs. This checklist will guide international B2B buyers, particularly from Africa, South America, the Middle East, and Europe, through the critical steps to make informed purchasing decisions.
Step 1: Define Your Technical Specifications
Before you start contacting suppliers, clearly outline your specific requirements. Determine the load capacity, height, and span of the gantry crane that will best suit your operational needs.
– Capacity: Consider the maximum weight you need to lift—options typically range from 250 lbs to over 10 tons.
– Height and Span: Adjustable height models may offer more flexibility, particularly in environments with varying load sizes.
Step 2: Research Market Prices and Options
Conduct thorough market research to understand the pricing landscape for gantry cranes. Prices can vary significantly based on the manufacturer, materials, and customization options.
– Compare Products: Look for both fixed and adjustable height options across various suppliers to find the best fit.
– Consider Total Cost of Ownership: Factor in maintenance costs, warranty, and potential shipping fees.
Step 3: Evaluate Potential Suppliers
It’s critical to vet suppliers thoroughly before making a commitment. Review their experience and reputation in the industry.
– Request Documentation: Ask for company profiles, product catalogs, and case studies that demonstrate their expertise in supplying gantry cranes.
– Seek References: Connect with other businesses in similar regions or industries that have purchased from the supplier to gain insights into their reliability and service quality.
Step 4: Verify Compliance with Safety Standards
Ensure that the gantry crane you intend to purchase meets the necessary safety and regulatory standards applicable in your region.
– Check Certifications: Look for certifications like ISO or CE marking, which signify compliance with international safety and quality standards.
– Safety Features: Inquire about built-in safety features such as overload protection and emergency stop functions.
Step 5: Request a Demonstration or Trial Period
If possible, request a demonstration of the gantry crane or a trial period to assess its performance in your specific operational environment.
– Hands-On Experience: This allows you to evaluate the crane’s ease of use, mobility, and overall functionality.
– Assess Support Services: During the trial, evaluate the supplier’s customer support responsiveness and technical assistance.
Step 6: Negotiate Terms and Conditions
Once you’ve selected a supplier, engage in negotiations to finalize the terms of the purchase.
– Discuss Payment Terms: Understand payment options and potential financing arrangements that may be available.
– Review Warranty and Service Agreements: Ensure you have clear terms regarding warranties, maintenance services, and parts replacement.
Step 7: Plan for Installation and Training
After purchase, ensure you have a plan for installation and operator training.
– Installation Support: Check if the supplier provides installation services or if you need to arrange for this separately.
– Training Programs: Proper training for your operators is crucial for safe and effective crane operation, reducing the risk of accidents and equipment damage.
By following this structured checklist, you can make informed decisions when sourcing gantry cranes, ensuring that you select the right equipment to meet your operational demands effectively and safely.
Comprehensive Cost and Pricing Analysis for gantry crane Sourcing
Gantry cranes are essential lifting solutions in various industrial applications, and understanding their cost structure is crucial for international B2B buyers. This section delves into the comprehensive cost and pricing analysis for sourcing gantry cranes, outlining the key components that influence pricing and providing actionable insights for buyers.
What Are the Key Cost Components in Gantry Crane Manufacturing?
When evaluating the cost structure of gantry cranes, several components come into play:
-
Materials: The choice of materials significantly affects the overall cost. Steel and aluminum are common materials, with steel generally being more affordable but heavier, while aluminum is lighter and more corrosion-resistant, often leading to higher costs.
-
Labor: Labor costs vary based on the region and the complexity of the gantry crane design. In regions with higher labor costs, such as Europe, the total manufacturing cost may increase.
-
Manufacturing Overhead: This includes costs related to factory operations, utilities, and equipment maintenance. Efficient manufacturing processes can reduce these overhead costs, allowing suppliers to offer more competitive pricing.
-
Tooling: The initial investment in tooling and molds can be substantial, especially for custom gantry cranes. Buyers should inquire about these costs when evaluating supplier quotes.
-
Quality Control (QC): Robust QC processes ensure that the cranes meet safety and performance standards. Enhanced QC measures can lead to higher manufacturing costs but are essential for reliability.
-
Logistics: Transportation and shipping costs can vary significantly, especially for international buyers. Understanding these costs, including customs duties and import taxes, is vital for accurate pricing.
-
Margin: Suppliers typically add a profit margin to cover their expenses and ensure business viability. This margin can fluctuate based on market demand and competition.
How Do Price Influencers Affect Gantry Crane Costs?
Several factors influence the pricing of gantry cranes, including:
-
Volume/MOQ: Bulk purchasing can lead to significant discounts. Buyers should negotiate minimum order quantities (MOQ) to secure better pricing.
-
Specifications and Customization: Customized cranes tailored to specific operational needs often come at a premium. Buyers should carefully evaluate whether customization is necessary or if standard models suffice.
-
Materials and Quality Certifications: Cranes made from higher-quality materials or those with industry certifications (such as ISO) typically command higher prices. Buyers must assess the trade-off between cost and quality.
-
Supplier Factors: Established suppliers with a reputation for quality may charge more than lesser-known brands. However, reliability and service should also be considered in the total cost assessment.
-
Incoterms: The terms of shipment (Incoterms) can significantly impact pricing. Buyers should clarify who is responsible for shipping costs and risks to avoid unexpected expenses.
What Are the Best Practices for Negotiating Gantry Crane Prices?
International B2B buyers, particularly from Africa, South America, the Middle East, and Europe, can adopt several strategies to ensure cost-efficiency when sourcing gantry cranes:
-
Conduct Market Research: Understanding market prices and competitor offerings can provide leverage during negotiations. Utilize platforms that aggregate pricing information for better insights.
-
Evaluate Total Cost of Ownership (TCO): Beyond the initial purchase price, consider maintenance, operation, and disposal costs when evaluating the overall investment in a gantry crane.
-
Negotiate Terms: Don’t hesitate to negotiate payment terms, warranty conditions, and service agreements. Flexible terms can lead to better cash flow management.
-
Assess Logistics and Delivery: Ensure that logistics costs are clearly defined in the pricing structure. Delays in delivery can lead to increased operational costs.
-
Seek Multiple Quotes: Request quotes from multiple suppliers to compare costs and services. This practice can help identify competitive pricing and potential suppliers.
Disclaimer on Indicative Prices
It is important to note that the prices mentioned for gantry cranes are indicative and may vary based on market conditions, supplier pricing strategies, and specific buyer requirements. Always confirm current pricing with suppliers before making purchasing decisions.
By understanding the cost structure, pricing influencers, and negotiation strategies, international B2B buyers can make informed decisions when sourcing gantry cranes, ensuring they receive the best value for their investment.
Alternatives Analysis: Comparing gantry crane With Other Solutions
When evaluating lifting solutions for industrial applications, it’s essential to consider various alternatives to gantry cranes. Each option presents unique benefits and potential drawbacks that can influence operational efficiency, costs, and suitability for specific tasks. Below, we explore how gantry cranes compare to two viable alternatives: Overhead Cranes and Forklifts.
Comparison Table of Gantry Cranes and Alternatives
Comparison Aspect | Gantry Crane | Overhead Crane | Forklift |
---|---|---|---|
Performance | High load capacity (up to 10 tons) | Higher load capacity (up to 50 tons) | Moderate load capacity (up to 10 tons) |
Cost | Moderate initial investment | Higher initial investment | Lower initial investment |
Ease of Implementation | Requires space for installation | Requires significant infrastructure | Quick to deploy and operate |
Maintenance | Moderate maintenance needs | Higher maintenance requirements | Low maintenance needs |
Best Use Case | Ideal for workshops and outdoor sites | Best for large-scale industrial operations | Ideal for material handling in warehouses |
What Are the Pros and Cons of Overhead Cranes Compared to Gantry Cranes?
Overhead Cranes offer a robust lifting solution for heavy loads, often exceeding the capacity of gantry cranes. They are typically fixed installations that provide a high degree of operational efficiency in large manufacturing environments. The primary advantage of overhead cranes is their ability to move loads across a broad area, making them suitable for extensive operations where space allows. However, they require a higher initial investment and significant infrastructure, which may not be feasible for all businesses, especially smaller enterprises or those operating in confined spaces.
How Do Forklifts Stack Up Against Gantry Cranes?
Forklifts are another alternative that many businesses consider for material handling tasks. They are versatile and can quickly transport loads across distances, making them a go-to solution in warehouses and distribution centers. The initial investment for a forklift is generally lower than that of a gantry crane or overhead crane, and they require minimal installation. However, forklifts have a limited lifting capacity compared to gantry cranes and are not designed for overhead lifting, which can restrict their applications. Additionally, they require skilled operators to ensure safety and efficiency during operations.
How Should B2B Buyers Choose the Right Lifting Solution?
Selecting the appropriate lifting solution hinges on various factors, including the specific lifting needs, workspace constraints, and budget considerations. For operations requiring high load capacities in a fixed location, overhead cranes may be the ideal choice. Conversely, if mobility and lower initial costs are paramount, forklifts could provide the necessary flexibility. Gantry cranes serve as a middle ground, offering a balance of mobility and lifting capacity, making them particularly suitable for workshops and outdoor applications.
Ultimately, B2B buyers should assess their operational requirements, including load types, frequency of use, and the physical layout of their facilities. Engaging with equipment experts can further assist in making an informed decision that aligns with long-term operational goals and budgetary constraints.
Essential Technical Properties and Trade Terminology for gantry crane
What Are the Key Technical Properties of Gantry Cranes?
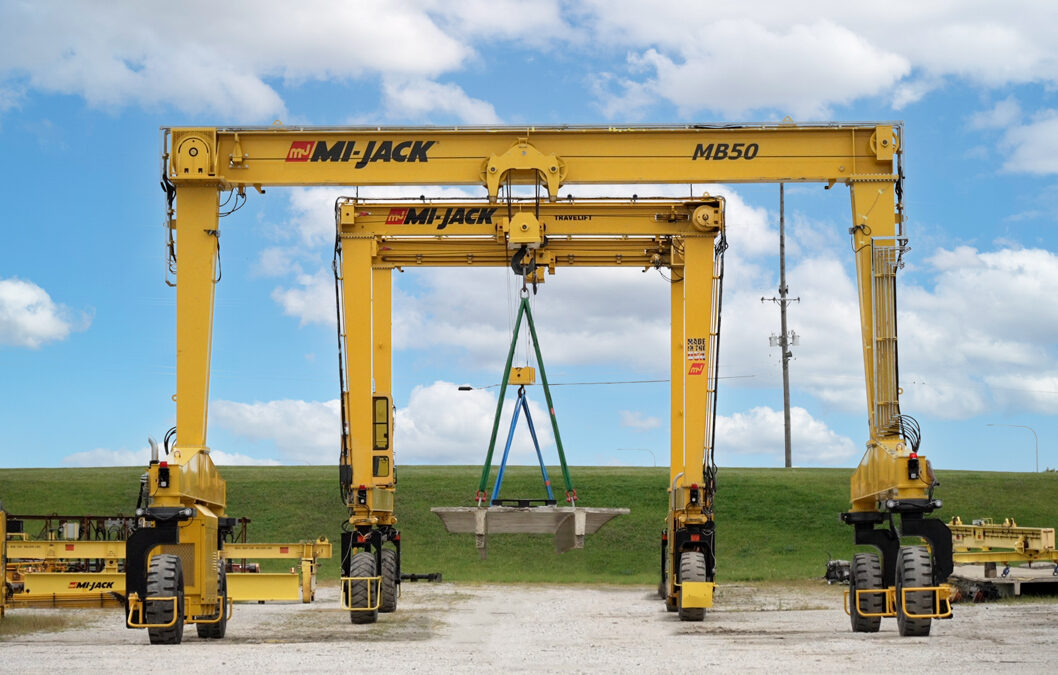
A stock image related to gantry crane.
When considering a gantry crane for your operations, understanding its technical specifications is crucial for ensuring you select the right model for your needs. Here are several essential properties to evaluate:
-
Load Capacity
The load capacity indicates the maximum weight a gantry crane can safely lift. Common capacities range from 250 lbs to over 10 tons. For B2B buyers, selecting a crane with the appropriate load capacity is vital to avoid overloading, which can lead to equipment failure and safety hazards. -
Span
The span refers to the distance between the legs of the gantry crane. It affects the area that can be covered while lifting. Depending on your workspace, you may need a wider or narrower span. Choosing the right span ensures efficient use of space and optimal lifting capability. -
Height Adjustment Range
Many gantry cranes come with adjustable heights, which allow for flexibility in lifting different loads. The height adjustment range is particularly important in environments where various load sizes are handled. For international buyers, this feature can enhance operational versatility in diverse settings. -
Material Composition
Gantry cranes are typically made from steel, aluminum, or a combination of both. Steel offers durability and strength, suitable for heavy loads, while aluminum is lightweight and portable, ideal for smaller applications. Selecting the right material is essential for balancing weight, portability, and load-bearing capacity. -
Caster and Wheel Specifications
The type of casters and wheels affects the mobility of the crane. Features such as locking mechanisms and wheel size can enhance stability and ease of movement, especially under load. B2B buyers should consider the terrain and required mobility when choosing a crane.
What Trade Terminology Should You Know When Purchasing Gantry Cranes?
Understanding industry jargon can facilitate smoother transactions and clearer communications with suppliers. Here are some common terms relevant to gantry cranes:
-
OEM (Original Equipment Manufacturer)
An OEM refers to the company that produces the original equipment. When sourcing gantry cranes, knowing whether you’re dealing with an OEM or a reseller is crucial, as it can affect warranty, service, and support options. -
MOQ (Minimum Order Quantity)
MOQ denotes the smallest quantity of units a supplier is willing to sell. This is particularly relevant for bulk purchases, as understanding MOQ helps buyers plan their budgets and inventory needs effectively. -
RFQ (Request for Quotation)
An RFQ is a formal request sent to suppliers to obtain pricing and terms for specific goods or services. Including detailed specifications in your RFQ can help ensure accurate and competitive quotes from manufacturers. -
Incoterms (International Commercial Terms)
Incoterms are a set of internationally recognized rules that define the responsibilities of buyers and sellers in shipping goods. Familiarity with Incoterms is crucial for international buyers to understand shipping costs, risks, and delivery responsibilities. -
Payload
Payload refers to the actual weight of the load being lifted. Understanding the distinction between load capacity and payload is important for ensuring that operations remain within safe limits, thus maintaining equipment integrity and worker safety. -
Customization Options
This term refers to the ability to modify certain aspects of the gantry crane to meet specific operational needs. Customization may include adjustments in height, span, or additional features like hoists and trolleys. Knowing your customization options can significantly enhance the functionality of the equipment in your operational context.
By grasping these essential technical properties and trade terms, B2B buyers can make informed decisions when selecting gantry cranes, ensuring they meet their operational needs while adhering to safety and efficiency standards.
Navigating Market Dynamics and Sourcing Trends in the gantry crane Sector
What Are the Key Market Dynamics and Trends Impacting the Gantry Crane Sector?
The gantry crane sector is witnessing significant evolution driven by various global factors. A surge in industrial automation across manufacturing and logistics sectors is propelling the demand for efficient lifting solutions. Particularly in regions like Africa and South America, rapid urbanization and infrastructure projects are creating substantial opportunities for gantry cranes. The Middle East is also experiencing growth due to ongoing investments in construction and energy sectors.
Emerging technologies such as IoT (Internet of Things) and AI (Artificial Intelligence) are influencing sourcing trends. For instance, smart gantry cranes equipped with sensors can provide real-time data on load weight, crane status, and maintenance needs, optimizing operational efficiency. Furthermore, the trend towards modular and customizable gantry crane systems allows buyers to tailor solutions to specific operational needs, enhancing flexibility and cost-effectiveness.
International B2B buyers should also be aware of fluctuating supply chain dynamics. With increased focus on local sourcing and reducing lead times, many manufacturers are diversifying their supply chains to mitigate risks associated with global disruptions. This is particularly important for buyers in Europe, where regulatory compliance and environmental considerations are becoming more stringent.
How Can Sustainability and Ethical Sourcing Influence Your Gantry Crane Purchases?
Sustainability is becoming a crucial consideration for international B2B buyers in the gantry crane sector. The environmental impact of production processes and materials used in gantry cranes can significantly affect corporate responsibility profiles. Buyers should prioritize manufacturers that demonstrate commitment to sustainability through reduced carbon footprints and responsible sourcing of raw materials.
Ethical supply chains are increasingly important, especially for buyers in Europe and the Middle East, where consumers and stakeholders demand transparency. Certifications such as ISO 14001 (Environmental Management) and adherence to sustainable practices in manufacturing and logistics can serve as indicators of a supplier’s commitment to ethical sourcing.
Additionally, using recyclable materials and eco-friendly coatings in gantry crane production not only meets environmental standards but also appeals to a growing market segment that values sustainability. B2B buyers should actively seek out suppliers who provide detailed information about their sustainability practices and materials to make informed purchasing decisions.
What Is the Brief Evolution of Gantry Cranes and Its Relevance to Current Sourcing Trends?
The gantry crane has evolved significantly since its inception in the early 20th century. Initially designed for heavy industrial use, advancements in materials science and engineering have led to the development of lighter, more versatile models, including aluminum and hybrid options that cater to a broader range of industries. The introduction of adjustable height and mobile gantry cranes has further diversified their application, making them suitable for various environments, from small workshops to large-scale industrial sites.
Understanding this evolution is essential for B2B buyers as it highlights the ongoing innovation in the sector. Modern gantry cranes are not only designed for functionality but also for adaptability, enabling businesses to optimize their operations efficiently. This evolution underscores the importance of sourcing from manufacturers who are at the forefront of these technological advancements, ensuring that buyers can leverage the latest features and capabilities in their operations.
Frequently Asked Questions (FAQs) for B2B Buyers of gantry crane
-
How do I choose the right gantry crane for my business needs?
Choosing the right gantry crane involves understanding your specific lifting requirements, including load capacity, height, and span. Evaluate the types available—fixed height, adjustable height, or mobile options—based on your workspace and operational needs. Additionally, consider the materials (steel, aluminum, or stainless steel) for durability and weight management. Consulting with suppliers about your operational environment will help ensure you select a crane that meets your safety and efficiency standards. -
What is the typical weight capacity range for gantry cranes?
Gantry cranes typically range from lifting capacities of 250 lbs to over 10 tons. Smaller models are ideal for light-duty tasks in workshops or warehouses, while heavy-duty cranes are necessary for industrial applications. When sourcing, evaluate the specific load requirements of your projects and consult with suppliers to find a crane that meets or exceeds these specifications. -
Are there customizable options for gantry cranes?
Yes, many manufacturers offer customizable options for gantry cranes, allowing you to tailor specifications such as height, span, and capacity to fit your exact needs. Customization can include features like special coatings for outdoor use or additional accessories such as hoists and trolleys. When discussing with suppliers, provide detailed descriptions of your application to explore available customization options that enhance efficiency and safety. -
What are the minimum order quantities (MOQ) for gantry cranes?
Minimum order quantities can vary significantly between suppliers. Some may offer single units for smaller operations, while others might require bulk purchases for competitive pricing. It’s advisable to directly contact potential suppliers to inquire about their MOQ policies, especially if you’re looking to establish a long-term procurement relationship or if you’re interested in negotiating pricing for larger orders. -
What payment terms should I expect when purchasing gantry cranes internationally?
Payment terms for international purchases can differ based on the supplier and your location. Common terms include upfront payment, a deposit with the balance due upon delivery, or payment upon completion of installation. It’s crucial to negotiate terms that align with your cash flow and risk management strategies. Always ensure that payment methods are secure and that contracts clearly outline all terms to avoid disputes. -
How can I ensure quality assurance (QA) when sourcing gantry cranes?
To ensure quality assurance, request certifications and compliance documents from suppliers that demonstrate adherence to international standards (e.g., ISO certifications). Conducting factory visits or audits is also beneficial if feasible. Additionally, inquire about warranties and after-sales support, which can provide reassurance about the product’s reliability and the supplier’s commitment to quality. -
What logistics considerations should I keep in mind when importing gantry cranes?
Logistics for importing gantry cranes involves understanding shipping methods, customs regulations, and potential tariffs or duties. Work with a logistics partner familiar with heavy machinery to navigate these complexities. Ensure that the supplier provides detailed shipping information, including packaging dimensions and weight, to facilitate smooth transportation. Planning for delivery timelines and local regulations will also help mitigate potential delays. -
How do I vet potential suppliers for gantry cranes in international markets?
Vetting suppliers involves researching their industry reputation, financial stability, and production capabilities. Look for reviews, testimonials, and case studies from previous clients. Verify their business licenses and any certifications relevant to manufacturing gantry cranes. Engaging in direct communication to assess responsiveness and professionalism can also provide insights into their customer service approach and reliability as a partner.
Important Disclaimer & Terms of Use
⚠️ Important Disclaimer
The information provided in this guide, including content regarding manufacturers, technical specifications, and market analysis, is for informational and educational purposes only. It does not constitute professional procurement advice, financial advice, or legal advice.
While we have made every effort to ensure the accuracy and timeliness of the information, we are not responsible for any errors, omissions, or outdated information. Market conditions, company details, and technical standards are subject to change.
B2B buyers must conduct their own independent and thorough due diligence before making any purchasing decisions. This includes contacting suppliers directly, verifying certifications, requesting samples, and seeking professional consultation. The risk of relying on any information in this guide is borne solely by the reader.
Strategic Sourcing Conclusion and Outlook for gantry crane
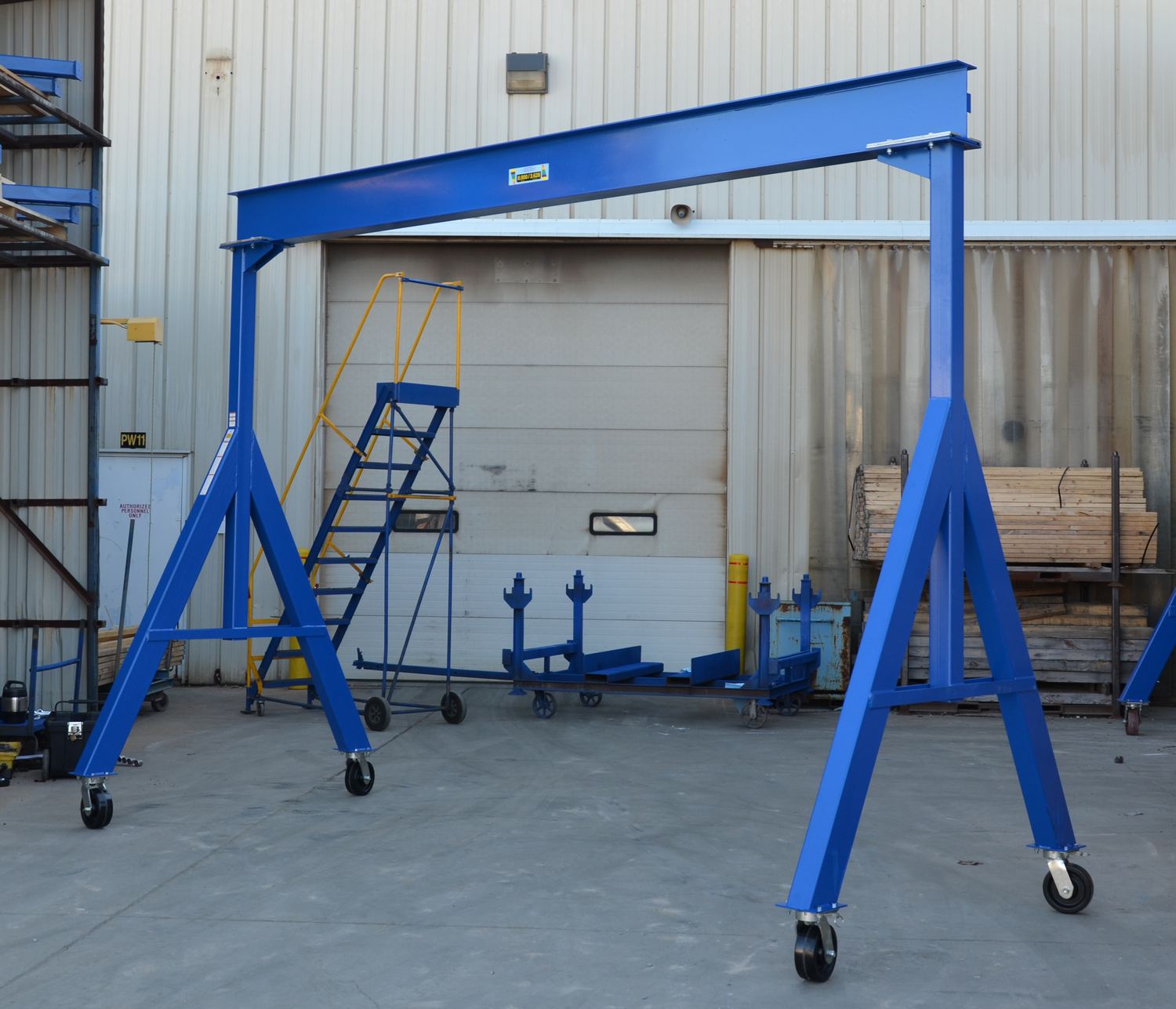
A stock image related to gantry crane.
What Are the Key Takeaways for B2B Buyers of Gantry Cranes?
In conclusion, strategic sourcing of gantry cranes is essential for international buyers aiming to enhance operational efficiency and optimize logistics. Key considerations include selecting the appropriate type of gantry crane, understanding load capacities, and choosing between fixed or adjustable height options based on specific industry needs. The versatility and cost-effectiveness of gantry cranes make them suitable for a variety of applications across sectors such as manufacturing, construction, and warehousing.
How Can International Buyers Navigate the Gantry Crane Market?
For buyers from Africa, South America, the Middle East, and Europe, establishing relationships with reputable suppliers is crucial. Considerations such as local regulations, shipping logistics, and after-sales support can significantly impact procurement success. Engaging in a thorough supplier evaluation process will ensure you partner with manufacturers that provide not only quality products but also reliable service and support.
What Is the Future Outlook for Gantry Crane Sourcing?
As industries continue to evolve, the demand for innovative lifting solutions will grow. International buyers are encouraged to stay informed about advancements in crane technology and emerging market trends. By proactively adapting to these changes, businesses can leverage strategic sourcing to gain a competitive edge in their respective markets. Investing in the right gantry crane today will position your operations for success tomorrow.