Unlock Efficiency: The Ultimate Hydraulic Lift Guide (2025)
Introduction: Navigating the Global Market for hydraulic lift
Navigating the global market for hydraulic lifts can pose significant challenges for international B2B buyers, particularly those operating in diverse regions such as Africa, South America, the Middle East, and Europe, including Poland and the UAE. With the increasing demand for efficient vertical transportation solutions, sourcing the right hydraulic lift requires not only an understanding of various types and applications but also a keen insight into supplier reliability and cost-effectiveness. This guide aims to demystify the complexities of hydraulic lift procurement by providing a thorough exploration of the different types of lifts available, their specific applications across industries, and critical factors to consider when vetting suppliers.
International buyers often face unique hurdles, from varying regulations to differing market conditions, which can complicate purchasing decisions. By leveraging this comprehensive guide, B2B buyers will be empowered to make informed decisions that align with their operational needs and budget constraints. We will delve into essential topics such as cost analysis, maintenance considerations, and the importance of after-sales support, ensuring that you are well-equipped to navigate the hydraulic lift landscape. Our goal is to facilitate a streamlined purchasing process that not only enhances operational efficiency but also contributes to long-term success in your market.
Understanding hydraulic lift Types and Variations
Type Name | Key Distinguishing Features | Primary B2B Applications | Brief Pros & Cons for Buyers |
---|---|---|---|
Two-Post Hydraulic Lift | Simple design, requires minimal space, ideal for cars | Auto repair shops, maintenance facilities | Pros: Cost-effective, easy to operate. Cons: Limited lifting height and stability for heavy vehicles. |
Four-Post Hydraulic Lift | Offers more stability, can lift heavier vehicles | Automotive service centers, storage | Pros: Greater weight capacity, excellent for alignment work. Cons: Requires more space, higher initial cost. |
Scissor Lift | Compact design, versatile in height adjustment | Warehousing, construction, automotive | Pros: Space-efficient, can reach various heights. Cons: Slower lifting speed compared to other types. |
Parking Lift | Designed for maximizing parking space | Urban garages, residential complexes | Pros: Increases parking efficiency, compact footprint. Cons: Limited to lighter vehicles, potential maintenance issues. |
Vertical Reciprocating Conveyor (VRC) | Specialized for transporting goods vertically | Manufacturing, warehousing | Pros: Efficient for moving heavy loads between floors. Cons: Requires significant maintenance, higher initial investment. |
What Are the Key Characteristics of Two-Post Hydraulic Lifts?
Two-post hydraulic lifts are characterized by their straightforward design, featuring two vertical posts that support the vehicle from its frame. These lifts are particularly suited for light to medium vehicles, making them ideal for auto repair shops and maintenance facilities. When considering a two-post lift, buyers should evaluate their space availability, as these lifts require less overhead clearance compared to four-post options. Additionally, they are typically more affordable, making them a popular choice for small businesses.
How Do Four-Post Hydraulic Lifts Differ in Usage?
Four-post hydraulic lifts provide enhanced stability and are capable of lifting heavier vehicles, which makes them a staple in automotive service centers. Their design allows for greater versatility, accommodating alignment work and storage. Buyers should consider the footprint of these lifts, as they require more space than two-post lifts. While they come with a higher initial cost, their durability and multi-functionality can justify the investment for businesses looking to handle heavier loads.
What Advantages Do Scissor Lifts Offer for B2B Buyers?
Scissor lifts are distinguished by their compact design and ability to adjust to various heights, making them versatile tools in warehouses, construction sites, and automotive services. Their design allows for efficient space utilization, which is crucial for businesses operating in limited areas. However, buyers should be aware of the slower lifting speeds and limited weight capacity compared to other hydraulic lifts. This consideration is important for businesses that require quick and heavy lifting capabilities.
Why Are Parking Lifts Important for Urban Areas?
Parking lifts are specifically designed to maximize parking space, making them ideal for urban garages and residential complexes. They allow vehicles to be stacked vertically, providing efficient use of limited space. However, they are generally limited to lighter vehicles, and potential maintenance issues could arise due to their specialized use. Buyers should assess their parking needs and vehicle types to determine if a parking lift is a suitable investment.
What Role Do Vertical Reciprocating Conveyors Play in Material Handling?
Vertical Reciprocating Conveyors (VRCs) are specialized hydraulic lifts used for transporting goods vertically within manufacturing and warehousing environments. They are particularly effective for moving heavy loads between different floor levels. However, VRCs require significant maintenance and entail a higher initial investment, which buyers must consider when evaluating their material handling solutions. The efficiency they bring to heavy load transportation can be a valuable asset for businesses with frequent vertical transport needs.
Key Industrial Applications of hydraulic lift
Industry/Sector | Specific Application of Hydraulic Lift | Value/Benefit for the Business | Key Sourcing Considerations for this Application |
---|---|---|---|
Automotive Repair | Vehicle Maintenance and Repair | Increases efficiency and safety in repairs | Capacity, lifting height, and compatibility with vehicle types |
Construction | Elevation of Heavy Materials and Equipment | Streamlines construction processes and enhances safety | Load capacity, stability, and terrain adaptability |
Manufacturing | Assembly Line Operations | Improves workflow efficiency and productivity | Customization options, maintenance support, and safety features |
Warehousing and Logistics | Loading and Unloading Goods | Reduces manual labor and minimizes injury risk | Size, lifting speed, and power requirements |
Aviation | Aircraft Maintenance and Servicing | Ensures safety and accessibility for repairs | Weight capacity, stability, and compliance with aviation standards |
How is Hydraulic Lift Used in Automotive Repair?
In the automotive sector, hydraulic lifts are essential for vehicle maintenance and repair. They allow mechanics to elevate vehicles safely, providing easy access to the undercarriage for tasks like oil changes, brake repairs, and tire rotations. The hydraulic system ensures a stable lift, reducing the risk of accidents. For international B2B buyers, it’s crucial to consider the lift’s capacity and compatibility with various vehicle types, especially in regions like Africa and South America, where vehicle diversity is high.
What Role Do Hydraulic Lifts Play in Construction?
In construction, hydraulic lifts are used to elevate heavy materials and equipment, facilitating the assembly and installation processes. They enhance safety by minimizing the risk of manual handling injuries and increasing the speed of operations. Buyers should focus on the lift’s load capacity and stability, particularly in regions like the Middle East, where construction projects often involve heavy machinery and materials. The adaptability of the lift to various terrains is also a key consideration.
How Do Hydraulic Lifts Enhance Manufacturing Operations?
Hydraulic lifts are integral to manufacturing assembly line operations. They streamline workflows by allowing for the easy movement of components between different stages of production. This efficiency can lead to increased productivity and reduced downtime. For B2B buyers in Europe, particularly Poland, sourcing lifts that offer customization options and robust maintenance support is vital to align with specific manufacturing processes and industry standards.
Why Are Hydraulic Lifts Important in Warehousing and Logistics?
In warehousing and logistics, hydraulic lifts are crucial for loading and unloading goods efficiently. They reduce manual labor, thereby minimizing the risk of injuries associated with heavy lifting. Buyers should evaluate the size and lifting speed of hydraulic lifts to ensure they meet the demands of their operations. For businesses in South America, where logistics can be challenging, selecting a lift that offers reliable performance and durability is essential.
How Are Hydraulic Lifts Used in Aviation Maintenance?
In the aviation industry, hydraulic lifts are employed for aircraft maintenance and servicing, allowing technicians to access various aircraft components safely. These lifts ensure that maintenance tasks are performed efficiently while adhering to strict safety protocols. Buyers in the aviation sector should prioritize weight capacity and stability, ensuring compliance with industry standards, especially in regions like the Middle East, where aviation is a rapidly growing sector.
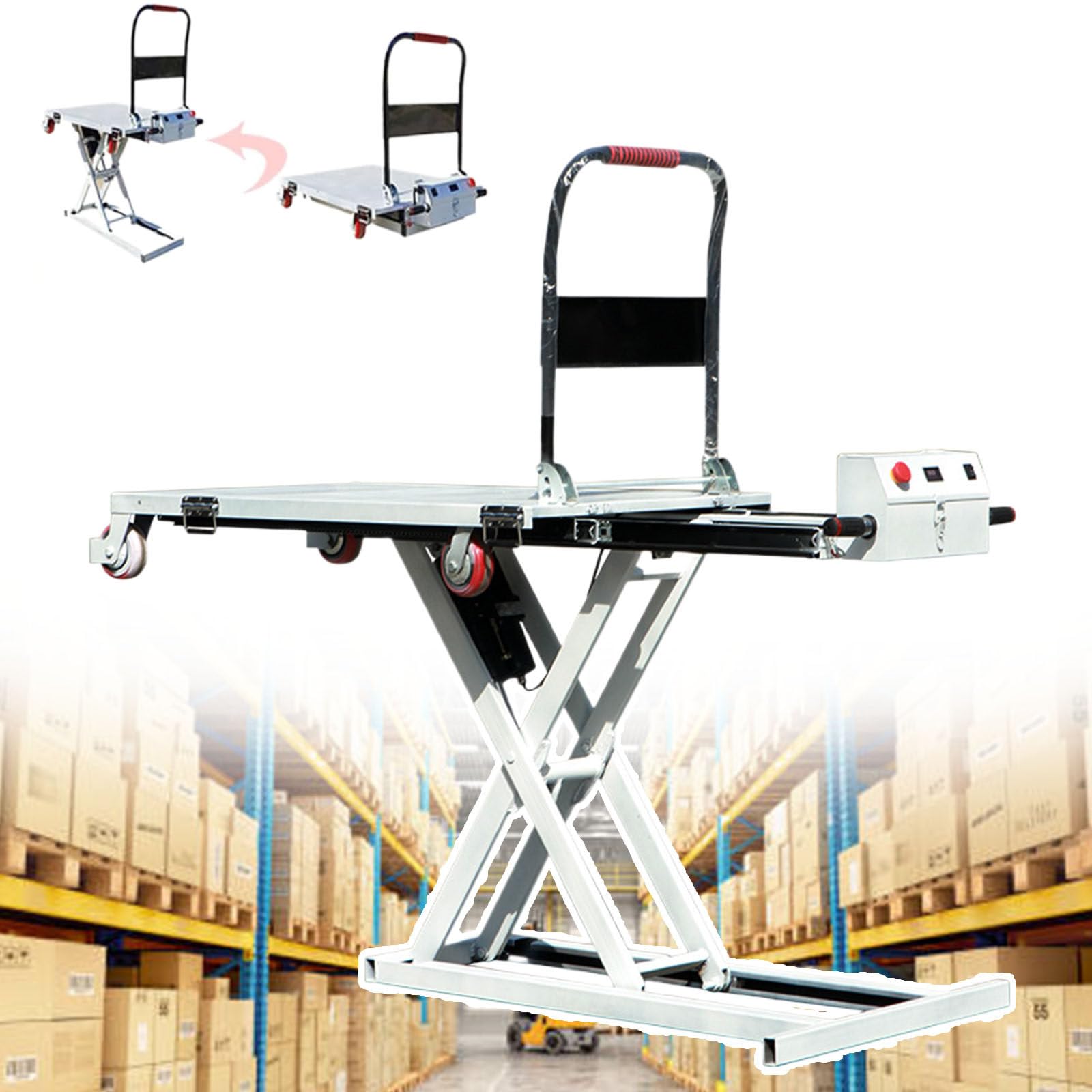
A stock image related to hydraulic lift.
3 Common User Pain Points for ‘hydraulic lift’ & Their Solutions
Scenario 1: Slow Lifting Speed Affects Efficiency in Operations
The Problem: In many B2B environments, especially within the automotive and manufacturing sectors, time is a critical resource. Buyers often find that hydraulic lifts, while cost-effective, tend to have slower lifting speeds compared to their electric counterparts. This can lead to bottlenecks in operations, particularly in busy workshops where multiple vehicles need servicing simultaneously. If a hydraulic lift takes longer to raise or lower vehicles, it can result in increased wait times for customers and decreased overall productivity.
The Solution: To mitigate the issues related to slow lifting speeds, buyers should carefully assess the specifications of hydraulic lifts before purchase. Opt for models that feature high-efficiency pumps designed to reduce lifting times. Additionally, consider investing in maintenance plans that include regular checks on hydraulic fluid quality and pump efficiency, as degraded fluid can significantly slow down lift operation. Training staff to operate the lifts efficiently and schedule maintenance can further enhance performance, ensuring that the hydraulic lift meets operational demands without causing delays.
Scenario 2: Hydraulic Oil Leakage and Environmental Concerns
The Problem: Environmental compliance is a significant concern for international B2B buyers, particularly in regions with stringent environmental regulations. Hydraulic lifts can sometimes experience oil leaks, which not only lead to operational inefficiencies but also pose a risk of soil and groundwater contamination. This can result in costly fines and damage to a company’s reputation if not managed properly.
The Solution: Buyers should prioritize sourcing hydraulic lifts that come with robust sealing systems and regular maintenance programs to minimize leakage risks. When selecting a hydraulic lift, inquire about the manufacturer’s quality control processes and certifications that ensure leak prevention. Implementing a routine inspection schedule will help identify any potential leaks early on. Additionally, consider using biodegradable hydraulic oils, which can reduce environmental impact in the event of a leak. Training staff on proper usage and maintenance will further enhance the lift’s longevity and performance.
Scenario 3: Noise Levels Disrupt Workplace Environment
The Problem: In settings such as automotive repair shops or manufacturing facilities, excessive noise from hydraulic lifts can lead to a disruptive work environment. Buyers often report that hydraulic lifts are noisier than expected, which can impact employee concentration and overall productivity. This is particularly concerning in environments where communication is essential, and noise can mask critical instructions or warnings.
The Solution: To address noise concerns, buyers should look for hydraulic lifts designed with noise-reduction features. Many manufacturers offer models with sound-dampening technology or quieter pump mechanisms that significantly reduce operational noise. Additionally, placing hydraulic lifts in designated areas away from workstations or using sound-absorbing materials in the vicinity can help minimize disruption. Investing in regular maintenance checks can also ensure that components are functioning optimally, which can reduce noise levels. Providing training for employees on best practices for using hydraulic lifts can further reduce unnecessary noise, fostering a more productive and pleasant work atmosphere.
Strategic Material Selection Guide for hydraulic lift
What Are the Key Materials Used in Hydraulic Lifts?
When selecting materials for hydraulic lifts, international B2B buyers must consider various factors, including performance, durability, and compliance with regional standards. Here, we analyze four common materials used in hydraulic lift construction: steel, aluminum, composite materials, and rubber. Each material has unique properties that can significantly impact the lift’s performance and suitability for different applications.
How Does Steel Perform in Hydraulic Lifts?
Key Properties:
Steel is renowned for its high tensile strength and durability, making it an ideal choice for hydraulic lift frames and components. It can withstand high pressure and temperature variations, withstanding loads typically exceeding 6,000 lbs. Steel also offers good corrosion resistance when treated with protective coatings.
Pros & Cons:
The primary advantage of steel is its strength and longevity, which translates to lower replacement costs over time. However, steel can be heavy, leading to increased manufacturing complexity and transportation costs. Additionally, untreated steel is prone to rusting, necessitating regular maintenance.
Impact on Application:
Steel is compatible with various hydraulic fluids, making it versatile for different lift types. However, buyers must ensure that the steel used meets specific standards like ASTM for structural steel to ensure safety and reliability.
What Are the Benefits of Using Aluminum in Hydraulic Lifts?
Key Properties:
Aluminum is lightweight yet strong, with excellent corrosion resistance. It typically has a lower temperature and pressure rating compared to steel but is still suitable for many hydraulic applications.
Pros & Cons:
The lightweight nature of aluminum makes it easier to handle and install, reducing labor costs. However, aluminum is generally more expensive than steel and may not be suitable for extremely heavy-duty applications. Additionally, it can be less durable under high-stress conditions.
Impact on Application:
Aluminum’s corrosion resistance makes it ideal for environments with high humidity or exposure to chemicals. Buyers in coastal regions or humid climates, such as parts of Africa and South America, may prefer aluminum lifts for their longevity.
Why Consider Composite Materials for Hydraulic Lifts?
Key Properties:
Composite materials, often made from a blend of fibers and resin, offer excellent strength-to-weight ratios and corrosion resistance. They can be engineered to withstand specific pressures and temperatures, making them suitable for various hydraulic applications.
Pros & Cons:
Composites are lightweight and can be molded into complex shapes, allowing for innovative designs. However, they can be more expensive to manufacture and may require specialized knowledge for repairs. Their long-term durability can also vary based on the type of resin used.
Impact on Application:
Composites are particularly useful in specialized applications where weight savings are critical. International buyers should consider the specific media compatibility of the composite materials used, ensuring they can handle the hydraulic fluids without degradation.
What Role Does Rubber Play in Hydraulic Lift Seals and Hoses?
Key Properties:
Rubber is commonly used for seals and hoses in hydraulic lifts due to its flexibility and excellent sealing properties. It can withstand moderate temperatures and pressures but has limitations compared to metals.
Pros & Cons:
Rubber is cost-effective and provides excellent sealing capabilities, preventing hydraulic fluid leaks. However, it can degrade over time due to exposure to heat, chemicals, and UV light, requiring regular replacement.
Impact on Application:
For international buyers, the choice of rubber must align with the specific hydraulic fluids used. Compliance with standards like JIS (Japanese Industrial Standards) for rubber materials is crucial to ensure reliability and safety.
Summary Table of Material Selection for Hydraulic Lifts
Material | Typical Use Case for hydraulic lift | Key Advantage | Key Disadvantage/Limitation | Relative Cost (Low/Med/High) |
---|---|---|---|---|
Steel | Structural frame and components | High strength and durability | Heavy and prone to rust without treatment | Medium |
Aluminum | Lightweight lifts and components | Lightweight and corrosion-resistant | More expensive and less durable under stress | High |
Composite | Specialized applications | Excellent strength-to-weight ratio | Higher manufacturing costs and repair complexity | High |
Rubber | Seals and hoses | Cost-effective and excellent sealing | Degrades over time and requires replacement | Low |
This strategic material selection guide provides B2B buyers with essential insights into the materials used in hydraulic lifts, allowing them to make informed decisions tailored to their specific operational needs and regional compliance requirements.
In-depth Look: Manufacturing Processes and Quality Assurance for hydraulic lift
What Are the Key Stages in the Manufacturing Process of Hydraulic Lifts?
The manufacturing process of hydraulic lifts involves several critical stages that ensure the final product meets quality and safety standards. Understanding these stages can help B2B buyers assess the capabilities of potential suppliers.
-
Material Preparation
– The first step in manufacturing hydraulic lifts is selecting high-quality raw materials, typically steel or aluminum. These materials are chosen for their strength, durability, and resistance to corrosion.
– Before processing, materials undergo inspection to verify their compliance with international standards such as ASTM or ISO. This step is crucial for ensuring the structural integrity of the lift. -
Forming
– The forming stage involves shaping the raw materials into the components required for the lift. Techniques such as cutting, welding, and bending are commonly used.
– Advanced CNC (Computer Numerical Control) machines are often employed to achieve precise dimensions and tolerances. This precision is critical in hydraulic lifts, where even minor discrepancies can affect performance and safety. -
Assembly
– After forming, components are assembled into a complete hydraulic lift. This stage includes the installation of hydraulic cylinders, pumps, valves, and control systems.
– Skilled technicians perform the assembly, often following strict protocols to ensure that each lift meets specific operational standards. Integration of electronic controls and safety mechanisms is also a key focus during assembly. -
Finishing
– The finishing stage includes surface treatments, such as painting or galvanizing, to protect the lift from environmental factors and enhance aesthetic appeal.
– Quality checks are conducted post-finishing to ensure that the protective coatings are applied uniformly and adhere to international standards.
How Is Quality Assurance Implemented in Hydraulic Lift Manufacturing?
Quality assurance (QA) is vital in the manufacturing of hydraulic lifts, as it ensures the product’s reliability, safety, and compliance with relevant regulations. B2B buyers should be aware of the QA processes that suppliers implement.
-
International Standards for Quality Assurance
– Many manufacturers adhere to ISO 9001, which outlines requirements for a quality management system. Compliance with ISO standards demonstrates a commitment to continuous improvement and customer satisfaction.
– Additionally, certifications such as CE (Conformité Européenne) for European markets or API (American Petroleum Institute) for specific hydraulic applications provide further assurance of quality and safety. -
Quality Control Checkpoints
– Incoming Quality Control (IQC): This initial stage involves inspecting raw materials and components before they enter the production process. It ensures that only materials meeting quality standards are used.
– In-Process Quality Control (IPQC): During the manufacturing process, continuous monitoring takes place. This includes checking dimensions, weld quality, and assembly accuracy to ensure compliance with specifications.
– Final Quality Control (FQC): Once assembly is complete, comprehensive testing is performed. This may include load testing, hydraulic pressure testing, and operational checks to confirm that the lift operates as intended. -
Common Testing Methods for Hydraulic Lifts
– Load testing is crucial to verify that the hydraulic lift can safely handle its maximum rated capacity. This test simulates real-world conditions and assesses the lift’s performance.
– Hydraulic fluid testing ensures that the system operates efficiently and identifies any potential leaks or contamination that could compromise safety.
How Can B2B Buyers Verify Supplier Quality Control?
B2B buyers must implement strategies to verify the quality control measures of potential hydraulic lift suppliers. Here are actionable steps to ensure compliance and reliability.
-
Conducting Supplier Audits
– Regular audits of suppliers can provide insights into their manufacturing processes and quality assurance practices. Buyers should look for suppliers who welcome audits and demonstrate transparency in their operations.
– During audits, buyers can assess the adherence to international standards and the effectiveness of quality control checkpoints. -
Requesting Quality Reports
– Buyers should request detailed quality reports, including results from IQC, IPQC, and FQC stages. These reports should outline any issues encountered during production and the corrective actions taken.
– Understanding the supplier’s historical performance can help buyers make informed decisions. -
Third-Party Inspections
– Engaging third-party inspection agencies can provide an unbiased assessment of the supplier’s quality control processes. These agencies can conduct inspections at various stages of production and offer certification of compliance with international standards.
– This step is particularly beneficial for buyers from regions like Africa and South America, where local suppliers may have varying levels of compliance with global standards.
What Are the Quality Control Nuances for International B2B Buyers?
International B2B buyers must navigate specific challenges related to quality control when sourcing hydraulic lifts. Here are some nuances to consider:
-
Understanding Regional Regulations
– Different regions may have varying regulations governing hydraulic lift safety and performance. Buyers should familiarize themselves with the specific requirements in their respective markets, such as the Machinery Directive in Europe.
– Suppliers should be able to demonstrate compliance with both local and international standards. -
Cultural and Communication Barriers
– Language differences and cultural nuances can impact the quality assurance process. Buyers should ensure that there is clear communication regarding quality expectations and standards.
– Establishing a strong relationship with suppliers can help mitigate misunderstandings and enhance collaboration on quality control efforts. -
Logistics and Supply Chain Considerations
– The logistics of transporting hydraulic lifts can introduce additional quality control challenges. Buyers should verify that suppliers have robust systems in place for handling and transporting products to prevent damage during transit.
– Inspections upon delivery can help ensure that products meet quality standards before they are put into service.
By understanding the manufacturing processes and quality assurance practices for hydraulic lifts, international B2B buyers can make informed decisions and ensure they partner with suppliers who prioritize safety and reliability.
Practical Sourcing Guide: A Step-by-Step Checklist for ‘hydraulic lift’
Introduction
Procuring a hydraulic lift can significantly enhance operational efficiency for businesses involved in automotive repair, construction, and material handling. This guide outlines a step-by-step checklist to assist international B2B buyers—especially from Africa, South America, the Middle East, and Europe—in making informed decisions when sourcing hydraulic lifts. By following these steps, you will ensure that you select a lift that meets your technical requirements and budget constraints while also considering reliability and supplier credibility.
Step 1: Define Your Technical Specifications
Before initiating your search, clearly outline the technical specifications required for your hydraulic lift. Consider factors such as load capacity, lifting height, and type of lift (e.g., two-post, four-post, or scissor lifts).
– Load Capacity: Ensure the lift can accommodate the maximum weight of the vehicles or materials you plan to lift.
– Lifting Height: Determine the required height for your specific applications, whether for vehicle maintenance or industrial use.
Step 2: Research Regulatory Compliance Requirements
Understand the local regulations and safety standards applicable to hydraulic lifts in your region. Compliance with these regulations is vital to ensure operational safety and avoid potential legal issues.
– Safety Standards: Verify that the lift adheres to standards set by organizations like ISO or ANSI.
– Environmental Regulations: Consider any environmental impacts, especially concerning hydraulic fluid leaks, which can lead to contamination.
Step 3: Evaluate Potential Suppliers
Before committing, thoroughly vet potential suppliers. Request company profiles, case studies, and references from buyers in a similar industry or region to gauge their reliability.
– Experience and Reputation: Look for suppliers with a proven track record in providing hydraulic lifts.
– Customer Reviews: Check online platforms for customer feedback to understand the supplier’s service quality and product performance.
Step 4: Assess After-Sales Support and Warranty
Evaluate the after-sales support offered by suppliers, including warranty terms and maintenance services. Reliable after-sales support can save costs and downtime in the long run.
– Warranty Coverage: Confirm the duration and extent of the warranty provided, focusing on parts and labor.
– Maintenance Services: Inquire if the supplier offers maintenance packages or service agreements to keep the hydraulic lift in optimal condition.
Step 5: Request and Compare Quotes
Once you have shortlisted suppliers, request detailed quotes outlining all costs involved, including shipping, installation, and any additional accessories or services.
– Cost Transparency: Ensure the quote is comprehensive, covering all potential hidden costs.
– Value for Money: Compare not just the price, but the overall value offered, including product quality and supplier reliability.
Step 6: Conduct Site Visits or Virtual Tours
If feasible, arrange site visits to inspect the hydraulic lifts in operation or request virtual tours. This firsthand experience can provide insight into the equipment’s functionality and reliability.
– Operational Performance: Observe how the lifts perform under typical operational conditions.
– Safety Features: Evaluate the safety mechanisms in place to protect operators and equipment.
Step 7: Finalize Your Purchase Agreement
After thorough evaluation and comparison, finalize your purchase agreement with the chosen supplier. Ensure all terms are clearly outlined, including delivery timelines, payment terms, and installation services.
– Contract Clarity: Review the contract for any ambiguous terms and ensure mutual understanding.
– Payment Security: Consider secure payment methods to protect your investment.
By following this checklist, international B2B buyers can make informed decisions when sourcing hydraulic lifts, ensuring they choose the right equipment for their operational needs while minimizing risks and maximizing value.
Comprehensive Cost and Pricing Analysis for hydraulic lift Sourcing
What Are the Key Cost Components in Hydraulic Lift Sourcing?
When sourcing hydraulic lifts for B2B purposes, understanding the cost structure is essential for making informed purchasing decisions. The primary cost components include:
-
Materials: The choice of materials significantly affects pricing. High-quality steel, hydraulic fluids, and components such as pumps and pistons can elevate costs. For instance, lifts using corrosion-resistant materials may incur higher initial costs but offer long-term savings through reduced maintenance.
-
Labor: Labor costs vary by region and can influence the overall price. Skilled labor for assembly, installation, and maintenance is crucial. Outsourcing manufacturing to regions with lower labor costs, such as Southeast Asia, can result in significant savings.
-
Manufacturing Overhead: This includes costs related to the facilities, utilities, and equipment used in the production of hydraulic lifts. Efficient manufacturing processes can help keep these costs down.
-
Tooling: The initial setup for specialized tooling can be a significant investment. Custom lifts or those with unique specifications may require additional tooling, which can increase upfront costs.
-
Quality Control (QC): Ensuring that hydraulic lifts meet safety and performance standards is vital. Companies may invest in robust QC processes, which can add to the overall cost but is essential for avoiding costly recalls or warranty claims.
-
Logistics: Transportation costs are influenced by the distance from the manufacturing facility to the buyer’s location. Import duties, tariffs, and shipping fees can add considerable costs, especially for international buyers.
-
Margin: Suppliers typically include a profit margin in their pricing. Understanding the market rates and comparing offers can help buyers negotiate better deals.
How Do Price Influencers Affect Hydraulic Lift Sourcing?
Several factors can influence the pricing of hydraulic lifts, impacting the total cost for buyers:
-
Volume/MOQ: Higher order volumes often lead to discounts. Establishing a long-term relationship with suppliers can also yield better pricing as buyers increase their order quantities.
-
Specifications and Customization: Customized hydraulic lifts to meet specific needs can significantly increase costs. Buyers should weigh the benefits of customization against the potential price increase.
-
Materials and Quality Certifications: Lifts constructed from high-grade materials or those that meet international safety certifications may command higher prices. However, investing in quality can reduce the Total Cost of Ownership (TCO) through lower maintenance and longer lifespan.
-
Supplier Factors: The reputation and reliability of suppliers can affect pricing. Established suppliers with a proven track record may charge more, but they often provide better support and product quality.
-
Incoterms: Understanding Incoterms (International Commercial Terms) is crucial for international buyers. These terms dictate the responsibilities of buyers and sellers concerning shipping, insurance, and tariffs, which can impact total costs.
What Are the Best Negotiation Tips for International Buyers?
International buyers, particularly from Africa, South America, the Middle East, and Europe, should consider the following strategies:
-
Conduct Market Research: Understanding the market and comparing prices from multiple suppliers can provide leverage during negotiations.
-
Highlight Long-Term Relationships: Emphasizing the potential for ongoing business can encourage suppliers to offer better terms and pricing.
-
Negotiate Payment Terms: Flexible payment terms can ease cash flow pressures, making higher upfront costs more manageable.
-
Consider Total Cost of Ownership (TCO): Focus on long-term savings rather than just the initial purchase price. Evaluate the costs of maintenance, energy consumption, and potential downtime.
-
Be Aware of Pricing Nuances: Different regions may have varying pricing structures based on local economic conditions, competition, and regulations. Understanding these nuances can help in negotiating effectively.
Why Is It Important to Consider Indicative Prices?
While indicative prices provide a benchmark, they can vary based on numerous factors, including market demand and supplier capabilities. Buyers should use these prices as a guideline but be prepared for fluctuations based on the specifics of their order and market conditions. Always request detailed quotes to ensure transparency and accuracy in pricing.
Alternatives Analysis: Comparing hydraulic lift With Other Solutions
Understanding Alternative Solutions to Hydraulic Lifts
When considering lifting solutions for various applications, it’s crucial to analyze alternatives to hydraulic lifts. While hydraulic lifts are widely used due to their efficiency and cost-effectiveness, other methods may suit specific operational needs better. This analysis will compare hydraulic lifts with mechanical lifts and pneumatic lifts, two viable alternatives, to help B2B buyers make informed decisions.
Comparison Table of Lifting Solutions
Comparison Aspect | Hydraulic Lift | Mechanical Lift | Pneumatic Lift |
---|---|---|---|
Performance | Moderate lifting speed (up to 150 ft/min); suitable for loads up to 6,000 lbs. | High lifting speed; unlimited vertical rise and payload capacity. | Fast lifting speed; excellent for lighter loads. |
Cost | Generally lower initial installation cost; higher long-term maintenance costs. | Higher initial cost but lower maintenance over time. | Moderate cost; installation can vary based on design. |
Ease of Implementation | Requires less space and no machine room; simpler installation. | More complex installation; often requires a dedicated machine room. | Can be installed in confined spaces; requires air supply. |
Maintenance | Requires regular oil checks; potential for leaks and overheating. | Requires minimal maintenance; very durable. | Requires periodic checks for air leaks; less frequent than hydraulic. |
Best Use Case | Ideal for automotive and low-rise applications. | Best for high-rise buildings and heavy industrial applications. | Suitable for light-duty tasks, such as in manufacturing or assembly lines. |
Detailed Breakdown of Alternatives
What Are the Advantages and Disadvantages of Mechanical Lifts?
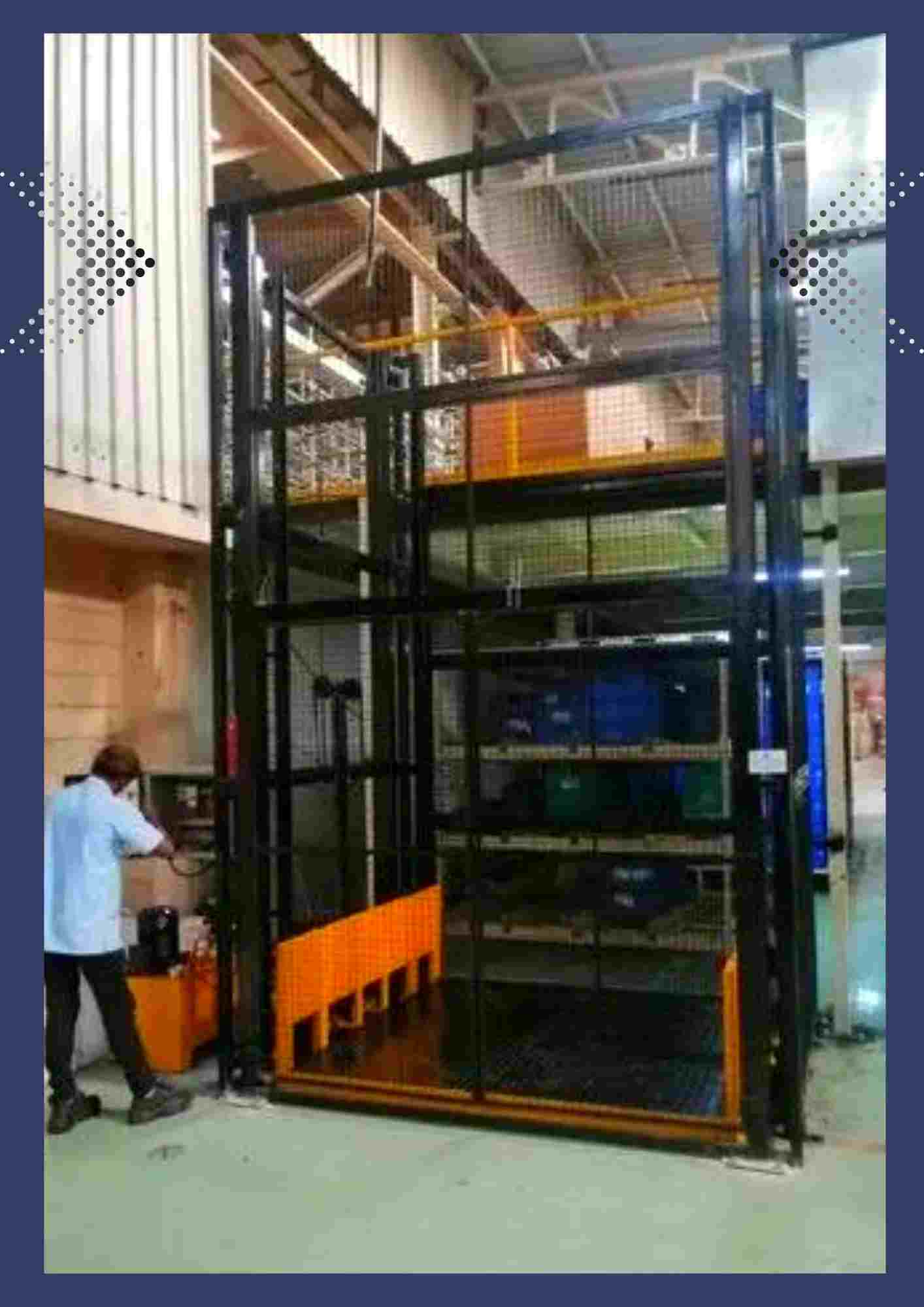
A stock image related to hydraulic lift.
Mechanical lifts utilize a system of pulleys and cables, providing an efficient lifting solution for various applications. One of their main advantages is their unlimited vertical rise, making them suitable for high-rise buildings and heavy industrial applications. They also have a higher payload capacity compared to hydraulic lifts, allowing for the lifting of heavier loads. However, they come with a higher initial cost and require a dedicated machine room for installation, which may not be feasible for smaller operations or facilities with limited space.
How Do Pneumatic Lifts Compare to Hydraulic Lifts?
Pneumatic lifts operate using compressed air to lift loads, making them a lighter and faster alternative to hydraulic systems. They are particularly effective for lighter loads and can be installed in confined spaces without the need for a dedicated machine room. Pneumatic lifts generally have a moderate cost and lower maintenance requirements compared to hydraulic lifts. However, they may not be suitable for heavy-duty applications or situations where high payload capacity is necessary, limiting their use in industrial settings.
How Can B2B Buyers Choose the Right Lifting Solution?
When selecting the appropriate lifting solution, B2B buyers should consider several factors, including the specific operational needs, budget constraints, and the physical environment of the installation site. Hydraulic lifts may be ideal for automotive shops or low-rise buildings due to their cost-effectiveness and ease of installation. In contrast, mechanical lifts are better suited for high-rise constructions where payload capacity and speed are essential. Pneumatic lifts serve well in manufacturing and assembly environments where lighter loads are common. Ultimately, the right choice will depend on balancing these factors with long-term operational goals.
Essential Technical Properties and Trade Terminology for hydraulic lift
What Are the Key Technical Properties of Hydraulic Lifts?
When selecting hydraulic lifts for your operations, understanding the essential technical properties is crucial. Here are several critical specifications to consider:
1. Load Capacity
The load capacity of a hydraulic lift defines the maximum weight it can safely handle. Typically ranging from 2,000 to 20,000 pounds, this specification is vital for ensuring that the lift can accommodate the heaviest items in your business, such as vehicles or heavy machinery. Overloading a lift can lead to mechanical failure and safety hazards.
2. Lifting Height
The lifting height indicates how high the lift can raise its load. This specification is essential for determining whether the lift will meet the vertical requirements of your workspace. Generally, hydraulic lifts can offer a lifting height of up to 14 feet, making them suitable for various applications, from automotive repair to warehouse operations.
3. Power Source
Hydraulic lifts can be powered by electricity or hydraulics. The choice of power source affects operational efficiency, installation requirements, and ongoing maintenance. Electric-powered lifts are typically more energy-efficient and easier to install, while hydraulic systems offer robust performance in heavy-duty applications. Understanding your power options can influence long-term operational costs.
4. Construction Material
The materials used in hydraulic lift construction, such as steel or aluminum, impact durability and weight. Steel lifts, while heavier, provide greater strength and load capacity, making them ideal for industrial applications. In contrast, aluminum lifts are lighter and more portable, suitable for smaller operations or mobile uses. Evaluating material grade is crucial for ensuring longevity and reliability.
5. Operational Speed
Operational speed measures how quickly a lift can raise and lower loads. While hydraulic lifts generally operate at a slower speed compared to electric lifts, which can exceed 200 feet per minute, they offer a steady and safe lifting process. This specification is important for workflow efficiency in high-volume operations.
What Are Common Trade Terms Used in Hydraulic Lift Transactions?
Familiarity with industry jargon can streamline communications and negotiations in the hydraulic lift market. Here are some essential terms:
1. OEM (Original Equipment Manufacturer)
An OEM refers to a company that produces parts and equipment that may be marketed by another manufacturer. For hydraulic lifts, sourcing from reputable OEMs ensures quality and compatibility with existing systems, which is particularly important for B2B buyers looking for reliability and warranty support.
2. MOQ (Minimum Order Quantity)
MOQ indicates the smallest quantity of a product that a supplier is willing to sell. Understanding MOQ is crucial for B2B buyers to manage inventory costs effectively. For hydraulic lifts, MOQs can vary significantly based on the supplier’s policies, making it important to clarify this term during negotiations.
3. RFQ (Request for Quotation)
An RFQ is a formal request for price quotes from suppliers for specific products or services. This document typically includes detailed specifications, quantities, and delivery timelines. Utilizing RFQs can help buyers compare prices and terms from multiple suppliers, ensuring they secure the best deal for hydraulic lifts.
4. Incoterms (International Commercial Terms)
Incoterms are standardized international trade terms that define the responsibilities of buyers and sellers. They clarify aspects such as shipping costs, risk transfer, and delivery points. Understanding Incoterms is essential for international B2B transactions involving hydraulic lifts, as they help mitigate misunderstandings and disputes.
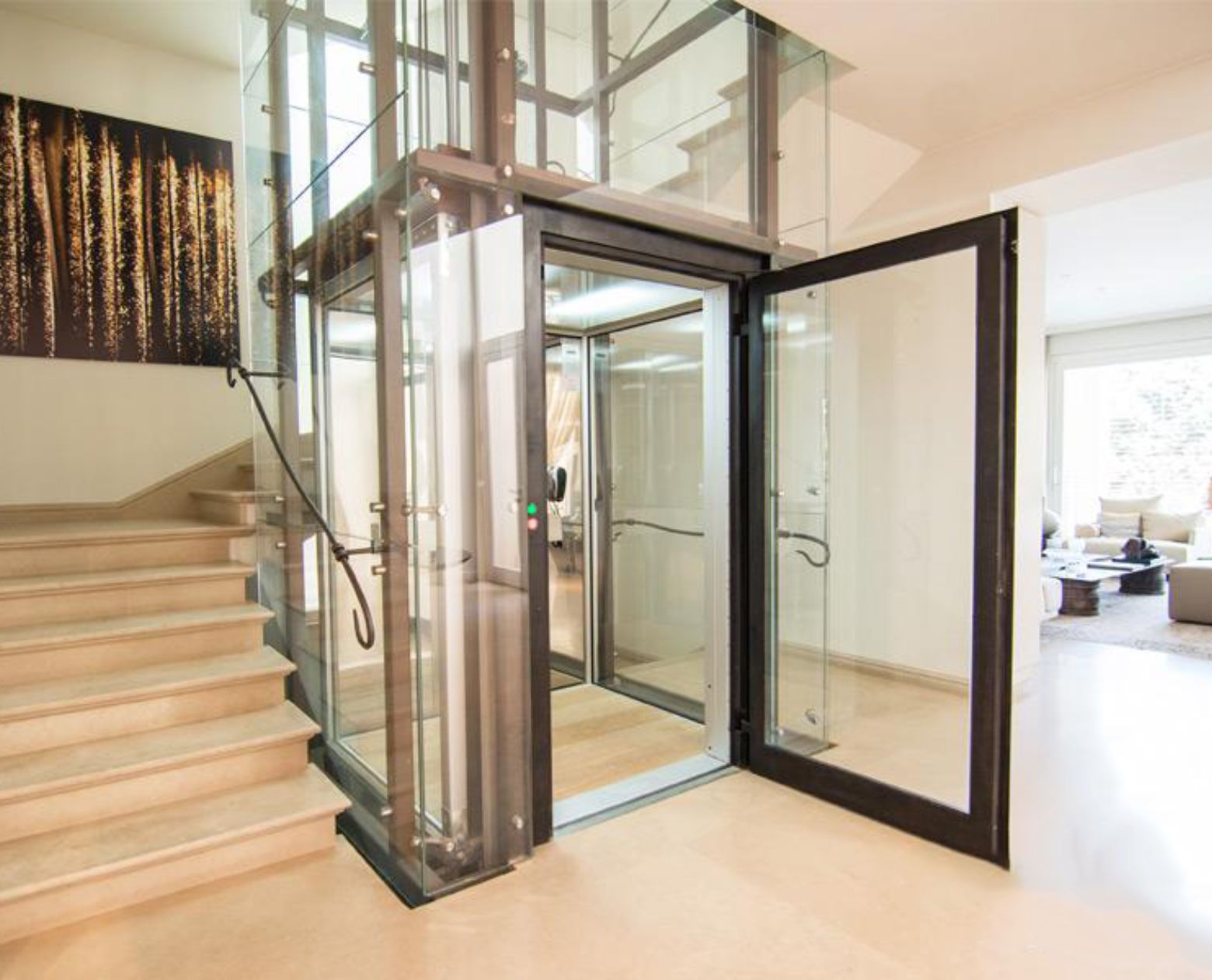
A stock image related to hydraulic lift.
5. Lead Time
Lead time refers to the time it takes from placing an order to receiving the product. For hydraulic lifts, lead times can vary based on manufacturing, shipping, and installation processes. Knowing the lead time is crucial for planning and managing operational timelines, especially in industries where equipment downtime can significantly impact productivity.
In summary, grasping these technical properties and trade terms is essential for international B2B buyers looking to make informed decisions when procuring hydraulic lifts. By understanding these factors, you can ensure that your investment aligns with operational needs while navigating the complexities of global trade.
Navigating Market Dynamics and Sourcing Trends in the hydraulic lift Sector
What Are the Current Market Dynamics and Key Trends in the Hydraulic Lift Sector?
The hydraulic lift sector is witnessing a significant transformation driven by technological advancements and changing market demands. One of the key global drivers is the increasing urbanization and the subsequent rise in construction activities, particularly in regions like Africa and the Middle East. This growth necessitates efficient vertical transportation solutions, making hydraulic lifts a preferred choice due to their space-saving designs and cost-effectiveness. Moreover, the surge in electric vehicle (EV) adoption is creating new opportunities for hydraulic lifts, particularly in automotive repair shops, as specialized lifts for EV battery replacements and maintenance become essential.
Emerging technologies such as IoT and smart lift systems are also reshaping the landscape. These innovations enable real-time monitoring and predictive maintenance, enhancing operational efficiency and reducing downtime for businesses. B2B buyers in Europe, particularly in Poland, are increasingly looking for suppliers who can provide advanced hydraulic lift systems equipped with these technologies. This trend underscores the importance of aligning with suppliers who prioritize innovation and technological integration.
Furthermore, sustainability is becoming a pivotal focus for international buyers. Hydraulic lift manufacturers are increasingly adopting eco-friendly practices, such as utilizing recyclable materials and energy-efficient hydraulic systems. This shift is particularly relevant for B2B buyers seeking to enhance their corporate social responsibility (CSR) profiles while also meeting regulatory requirements.
How Important Is Sustainability and Ethical Sourcing in the Hydraulic Lift Sector?
The environmental impact of hydraulic lifts cannot be overlooked, as traditional hydraulic systems often rely on oil-based fluids that can lead to contamination if not managed properly. Therefore, ethical sourcing and sustainability are crucial for B2B buyers in this sector. Suppliers that prioritize sustainable practices, such as using biodegradable hydraulic fluids and recyclable materials, are increasingly favored. This is particularly relevant in regions like South America and Africa, where environmental regulations are tightening.
Moreover, the importance of ethical supply chains is gaining traction. Buyers are now more inclined to partner with manufacturers who can demonstrate transparency in their sourcing and manufacturing processes. Certifications such as ISO 14001 (Environmental Management) and ISO 9001 (Quality Management) can serve as indicators of a supplier’s commitment to sustainable practices. By selecting suppliers with these certifications, B2B buyers can ensure that their hydraulic lift solutions align with global sustainability standards.
In addition, the use of “green” materials in hydraulic lift production is becoming a competitive differentiator. Manufacturers that invest in eco-friendly materials not only reduce their environmental footprint but also appeal to a growing segment of eco-conscious buyers. For B2B buyers, this means that sourcing decisions can have a significant impact on their brand reputation and customer loyalty.
What Is the Brief Evolution and History of Hydraulic Lifts?
Hydraulic lifts have a rich history that dates back to the 19th century, evolving significantly over the decades. Initially, these lifts were rudimentary and primarily used for industrial applications. However, advancements in hydraulic technology and engineering principles, particularly Pascal’s principle, have led to the development of more sophisticated systems capable of handling higher loads and speeds.
The introduction of hydraulic lifts in commercial buildings marked a turning point, making multi-level structures more accessible. Over time, innovations such as the incorporation of electric pumps and advanced safety features have further enhanced their reliability and efficiency. Today, hydraulic lifts are integral to various sectors, including automotive, construction, and logistics, providing solutions that meet the diverse needs of international B2B buyers.
As the market continues to evolve, understanding the historical context of hydraulic lifts can provide valuable insights into current trends and future developments, allowing buyers to make informed sourcing decisions.
Frequently Asked Questions (FAQs) for B2B Buyers of hydraulic lift
-
How do I choose the right hydraulic lift for my business needs?
Selecting the appropriate hydraulic lift requires a careful assessment of your specific operational requirements. Consider factors such as the weight capacity needed (most hydraulic lifts accommodate loads up to 6,000 lbs), the height you need to lift, and the available space in your facility. Additionally, evaluate the type of vehicles or equipment you will be working with, as different lifts (two-post, four-post, scissor) cater to various applications. Consulting with suppliers who understand your industry can also provide tailored recommendations. -
What are the key specifications to look for in a hydraulic lift?
When sourcing a hydraulic lift, focus on specifications such as lifting capacity, lifting height, and the type of lift (e.g., two-post, four-post, or scissor). Other important factors include the power source (electric vs. hydraulic), installation requirements, and safety features like emergency stop buttons and overload protection. It’s also wise to inquire about the warranty and service agreements offered by suppliers, ensuring you have support for maintenance and repairs. -
What are the potential shipping and logistics challenges when importing hydraulic lifts?
Importing hydraulic lifts can pose several logistical challenges, including customs clearance, shipping costs, and potential delays in transit. To mitigate these risks, work with suppliers who have experience in international shipping and can provide all necessary documentation. Consider the total landed cost, which includes shipping, duties, and taxes. It’s also advisable to choose reliable freight forwarders who can navigate potential customs hurdles and provide real-time tracking updates. -
How can I vet suppliers of hydraulic lifts effectively?
Vetting suppliers is crucial to ensure you partner with reliable manufacturers. Start by researching the supplier’s reputation through reviews and testimonials from previous clients. Request references and check their experience in exporting hydraulic lifts to your region. Additionally, confirm their compliance with international standards and certifications, such as ISO. A visit to their facility or a virtual tour can also provide insight into their manufacturing processes and quality control measures. -
What customization options are available for hydraulic lifts?
Many manufacturers offer customization options to meet specific business needs. Common customizations include adjustments in lifting capacity, modifications for specialized equipment, or the addition of unique safety features. When discussing customization, communicate your requirements clearly and ask for samples or prototypes if possible. This ensures the final product aligns with your operational demands and safety regulations. -
What are the typical payment terms for international purchases of hydraulic lifts?
Payment terms can vary significantly among suppliers. Common practices include advance payment, letters of credit, or net 30/60/90 days after shipment. It’s essential to negotiate terms that suit your cash flow while ensuring the supplier feels secure in the transaction. Be sure to clarify the currency of payment and any associated fees, as fluctuations can impact the total cost. -
What quality assurance practices should I expect from hydraulic lift suppliers?
Quality assurance is vital for ensuring safety and performance in hydraulic lifts. Reputable suppliers should have comprehensive QA processes, including material inspections, performance testing, and adherence to international standards. Inquire about their testing protocols and whether they provide certifications for their products. Additionally, ask about after-sales support and the availability of replacement parts, which are critical for maintaining the lift’s operational integrity. -
How do I ensure compliance with local regulations when installing hydraulic lifts?
Compliance with local regulations is essential for the safe operation of hydraulic lifts. Research the specific codes and standards applicable in your region, which may include building codes, safety regulations, and operational guidelines. Engage with local authorities or industry experts to understand these requirements fully. Furthermore, ensure that the lift installation is conducted by certified professionals who are familiar with local regulations to avoid legal and safety issues.
Important Disclaimer & Terms of Use
⚠️ Important Disclaimer
The information provided in this guide, including content regarding manufacturers, technical specifications, and market analysis, is for informational and educational purposes only. It does not constitute professional procurement advice, financial advice, or legal advice.
While we have made every effort to ensure the accuracy and timeliness of the information, we are not responsible for any errors, omissions, or outdated information. Market conditions, company details, and technical standards are subject to change.
B2B buyers must conduct their own independent and thorough due diligence before making any purchasing decisions. This includes contacting suppliers directly, verifying certifications, requesting samples, and seeking professional consultation. The risk of relying on any information in this guide is borne solely by the reader.
Strategic Sourcing Conclusion and Outlook for hydraulic lift
As the demand for hydraulic lifts continues to grow across various industries, international B2B buyers must prioritize strategic sourcing to maximize value. Understanding the advantages of hydraulic lifts—such as lower installation costs, space efficiency, and adaptability—can help businesses make informed purchasing decisions. However, it’s also essential to be aware of the potential drawbacks, including maintenance needs and operational limits.
By evaluating suppliers based on their product offerings, customer service, and after-sales support, buyers from Africa, South America, the Middle East, and Europe can ensure they select reliable partners. Engaging with manufacturers that provide comprehensive training and support will enhance operational efficiency and safety, ultimately leading to higher productivity.
Looking ahead, the hydraulic lift market is poised for innovation, with advancements in technology promising improved performance and sustainability. International buyers are encouraged to stay updated on industry trends and leverage strategic sourcing initiatives to secure the best solutions for their operational needs. Embrace the opportunity to enhance your business capabilities with cutting-edge hydraulic lift systems that meet both current demands and future challenges.