Unlock Efficiency: The Ultimate Worm and Wheel Gear Guide (2025)
Introduction: Navigating the Global Market for worm and wheel gear
Navigating the global market for worm and wheel gear can be a daunting task for international B2B buyers, especially when sourcing reliable components that meet specific operational needs. Worm gears, renowned for their unique ability to provide high torque and compact design, are essential in various applications ranging from automotive power steering to robotics. However, buyers often face challenges in understanding the various types, lubrication requirements, and supplier options available in diverse markets, particularly in regions such as Africa, South America, the Middle East, and Europe.
This comprehensive guide serves as a vital resource, addressing critical aspects of worm and wheel gear procurement. It delves into the different types of worm gears, their applications, and the importance of selecting the right materials to ensure longevity and efficiency. Additionally, the guide offers actionable insights on vetting suppliers, understanding cost structures, and evaluating the performance metrics that matter most in your industry.
By leveraging this guide, international B2B buyers will be empowered to make informed purchasing decisions, ensuring they select high-quality worm gears that align with their operational goals. Whether you are in Italy or Indonesia, understanding the global landscape of worm and wheel gear will enhance your sourcing strategy and drive business success.
Understanding worm and wheel gear Types and Variations
Type Name | Key Distinguishing Features | Primary B2B Applications | Brief Pros & Cons for Buyers |
---|---|---|---|
Cylindrical Worm Gear | Features a cylindrical thread; compact design | Speed reducers, conveyors | Pros: High reduction ratio, compact. Cons: Lower efficiency (30-60%). |
Drum-Shaped Worm Gear | Has a drum-shaped thread; allows for smooth operation | Elevators, machine tools | Pros: Smooth operation, good for tight spaces. Cons: Higher wear rates. |
Dual-Lead Worm Gear | Two different lead angles for adjusting backlash | Robotics, automated systems | Pros: Adjustable backlash, versatile. Cons: More complex design. |
Self-Locking Worm Gear | Prevents reverse motion due to low lead angle | Lifts, winches, automotive power steering | Pros: Increased safety, no back drive. Cons: Not entirely reliable; may need additional mechanisms. |
Small Module Worm Gear | Smaller modules suited for precision applications | Medical equipment, high-tech robotics | Pros: Ideal for precision, space-efficient. Cons: Limited torque capacity. |
What are the Characteristics of Cylindrical Worm Gears?
Cylindrical worm gears are characterized by their cylindrical threads, which mesh with a worm wheel at a right angle. This design allows for a significant speed reduction in a compact form. They are commonly used in applications such as speed reducers and conveyors. When considering a purchase, buyers should note their relatively low efficiency, which typically ranges from 30% to 60%. It’s crucial to evaluate the application requirements against the potential energy loss due to friction.
How Do Drum-Shaped Worm Gears Operate?
Drum-shaped worm gears feature a drum-like thread that provides smoother operation compared to their cylindrical counterparts. This design minimizes vibration and noise, making them suitable for elevators and machine tools. Buyers should consider the potential for higher wear rates due to the increased contact area, which can lead to more frequent maintenance. Evaluating the operational environment and expected load can help determine if this type meets specific needs.
What Advantages Do Dual-Lead Worm Gears Offer?
Dual-lead worm gears utilize two different lead angles, allowing for precise backlash adjustments without altering the center distance between the worm and wheel. This feature makes them particularly versatile for robotics and automated systems where precision is critical. However, the complexity of their design may lead to higher manufacturing costs. Buyers should assess the need for adjustability against the potential for increased maintenance and operational challenges.
Why Choose Self-Locking Worm Gears?
Self-locking worm gears are designed with a small lead angle, which prevents reverse motion. This makes them ideal for safety-critical applications like lifts and automotive power steering. While they provide enhanced safety by eliminating back drive, their reliability can vary, necessitating supplementary mechanisms for complete assurance. Buyers should weigh the benefits of safety against the complexity and potential costs of additional systems.
What are the Benefits of Small Module Worm Gears?
Small module worm gears are tailored for high-tech applications, such as medical equipment and robotics, where precision and compactness are paramount. Their smaller size allows for integration into tight spaces, but they typically have a limited torque capacity. Buyers should consider the specific requirements of their applications, such as the need for precision versus the potential limitations in power transmission. Choosing the right size and module is crucial for optimal performance in specialized settings.
Key Industrial Applications of worm and wheel gear
Industry/Sector | Specific Application of worm and wheel gear | Value/Benefit for the Business | Key Sourcing Considerations for this Application |
---|---|---|---|
Manufacturing | Machine Tools | High precision and compact design for efficient operation | Material compatibility, load capacity, and lubrication requirements |
Construction | Elevators | Reliable vertical transportation with minimal space usage | Self-locking features, durability, and maintenance needs |
Automotive | Power Steering Systems | Enhanced control and responsiveness in vehicle handling | Weight, size, and efficiency of gear ratios for specific models |
Robotics | Actuation Systems | Precise motion control in robotic applications | Miniaturization, backlash adjustments, and material selection |
Entertainment | Fishing Reels | Smooth and reliable gear engagement for optimal performance | Corrosion resistance, gear ratio options, and ease of maintenance |
How is Worm and Wheel Gear Used in Manufacturing Machine Tools?
In the manufacturing sector, worm and wheel gears are commonly employed in machine tools, providing a high degree of precision in the movement of components. These gears facilitate compact designs that save space while delivering significant torque and speed reduction. For international buyers, particularly in regions like Africa and South America, sourcing gears made from compatible materials is crucial to ensure longevity. Additionally, understanding the specific lubrication needs is essential, as inadequate lubrication can lead to increased wear and reduced efficiency.
What Role Does Worm and Wheel Gear Play in Construction Elevators?
Worm and wheel gears are essential in construction elevators, where they ensure reliable vertical transportation of materials and personnel. Their self-locking feature prevents reverse motion, enhancing safety in high-rise buildings. Buyers from the Middle East and Europe must consider factors such as the durability of materials used in the gears and the ease of maintenance, given the harsh environmental conditions in some construction sites. Ensuring the right gear ratio for the load requirements is also vital for optimal performance.
How is Worm and Wheel Gear Integrated into Automotive Power Steering Systems?
In the automotive industry, worm and wheel gears are integral to power steering systems, providing enhanced control and responsiveness. Their design allows for a compact assembly, crucial in modern vehicles where space is at a premium. Buyers should focus on sourcing gears that meet specific weight and size requirements, as well as efficiency ratings to match vehicle performance standards. Additionally, considering the gear’s resistance to wear and tear is important for maintaining long-term functionality.
How Does Worm and Wheel Gear Contribute to Robotics Actuation Systems?
In robotics, worm and wheel gears are used in actuation systems to achieve precise motion control, essential for tasks requiring high accuracy. These gears allow for compact designs, which are beneficial in applications where space is limited. International buyers, especially in Europe and Africa, should prioritize sourcing gears that allow for backlash adjustments to enhance performance. Material selection is also critical, as gears must withstand repetitive motion and varying loads without failure.
What Advantages Do Worm and Wheel Gears Offer in Fishing Reels?
Worm and wheel gears are widely used in fishing reels, providing smooth and reliable gear engagement for optimal line retrieval and casting. Their design minimizes backlash, ensuring a seamless user experience. Buyers in regions like South America, where fishing is a significant industry, should look for gears with corrosion-resistant properties to withstand exposure to water and salt. Additionally, considering the available gear ratio options can greatly influence the performance of the reel, making it essential for buyers to choose wisely.
3 Common User Pain Points for ‘worm and wheel gear’ & Their Solutions
Scenario 1: Inefficient Lubrication Leading to Gear Failure
The Problem: Many B2B buyers encounter the challenge of inadequate lubrication in worm and wheel gear systems. Due to the unique sliding friction mechanism in these gears, proper lubrication is critical. If the lubrication is insufficient or the wrong type is used, it can lead to excessive wear, overheating, and ultimately, gear failure. This issue is particularly concerning for manufacturers and machinery operators in industries such as manufacturing and automotive, where downtime can lead to significant production losses.
The Solution: To effectively combat lubrication issues, buyers should prioritize selecting high-viscosity lubricants specifically formulated for worm gear applications. Look for mineral-based gear oils with viscosity ratings of ISO 460 or higher, as these can withstand the sliding conditions better than standard oils. Additionally, consider investing in specialized lubrication systems that ensure consistent application and circulation of the lubricant. Regular monitoring and maintenance schedules should be implemented to check lubricant levels and conditions, ensuring that the gears remain well-lubricated at all times. Training your maintenance staff on the specific lubrication needs of worm gears can further enhance the longevity and efficiency of your gear systems.
Scenario 2: High Heat Generation Reducing Gear Efficiency
The Problem: A common pain point for B2B buyers is the high heat generation associated with worm and wheel gears. The sliding motion between the worm and the wheel generates significant friction, which can lead to overheating and decreased operational efficiency. This is particularly problematic in regions with high ambient temperatures, such as parts of Africa and the Middle East, where heat management is crucial for machinery longevity and performance.
The Solution: To address heat generation, consider implementing heat dissipation strategies such as installing cooling systems or using heat-resistant materials for gear construction. Additionally, selecting gears with appropriate thread designs can enhance the efficiency of power transmission, thereby reducing excess heat. Buyers should also evaluate the operational environment and adjust workloads accordingly to minimize excessive strain on the gear system. Regular maintenance checks should be scheduled to identify any signs of overheating early, allowing for timely interventions and adjustments.
Scenario 3: Limited Compatibility with Existing Systems
The Problem: International B2B buyers often face challenges regarding compatibility when integrating worm and wheel gears into existing machinery. The diversity of gear specifications and the unique requirements of different applications can make it difficult to find suitable replacements or upgrades. This is especially true for companies in regions with less standardized manufacturing practices, such as South America and parts of Europe.
The Solution: To ensure compatibility, buyers should conduct thorough compatibility assessments before purchasing worm and wheel gears. This involves analyzing existing gear specifications, including dimensions, load capacities, and materials. Engage with suppliers who offer customizable solutions or a broad range of stock gears that can be adapted to various applications. Additionally, consider collaborating with a gear manufacturer that provides detailed product specifications and technical support. This proactive approach can help mitigate compatibility issues and streamline the integration process, ultimately saving time and costs associated with trial and error in sourcing. Regularly updating your inventory and keeping an eye on emerging gear technologies can also help future-proof your operations against compatibility challenges.
Strategic Material Selection Guide for worm and wheel gear
What Are the Key Materials for Worm and Wheel Gears?
When selecting materials for worm and wheel gears, it is essential to consider the specific application requirements, environmental conditions, and mechanical properties. Here, we analyze four common materials used in the manufacturing of worm and wheel gears: carbon steel, stainless steel, bronze, and engineering plastics. Each material has unique properties that can significantly impact performance and suitability for various applications.
How Does Carbon Steel Perform in Worm and Wheel Gear Applications?
Key Properties: Carbon steel, particularly grades like S45C and SCM440, offers excellent strength and hardness. It can withstand high temperatures and pressures, making it suitable for demanding applications.
Pros & Cons: The primary advantage of carbon steel is its durability and cost-effectiveness. However, it is prone to corrosion, which can limit its use in humid or corrosive environments. Additionally, manufacturing processes for carbon steel can be complex, requiring heat treatment for optimal performance.
Impact on Application: Carbon steel is compatible with a variety of lubricants and is often used in heavy machinery, automotive applications, and industrial equipment. Buyers should ensure that the gear is adequately protected against corrosion, especially in regions with high humidity.
Considerations for International Buyers: Compliance with standards such as ASTM A36 or JIS G4051 is crucial. Buyers from regions like Africa and South America should consider local availability and cost implications of carbon steel.
What Advantages Does Stainless Steel Offer for Worm and Wheel Gears?
Key Properties: Stainless steel, particularly grades like 304 and 316, is known for its excellent corrosion resistance and high-temperature performance. It maintains strength even in extreme conditions.
Pros & Cons: The main advantage of stainless steel is its longevity and resistance to rust and corrosion, making it ideal for marine and chemical applications. However, it is generally more expensive than carbon steel and can be more challenging to machine.
Impact on Application: Stainless steel gears are suitable for applications involving exposure to water, chemicals, or high temperatures. They are commonly used in food processing, pharmaceuticals, and marine industries.
Considerations for International Buyers: Buyers should be aware of compliance with standards such as ASTM A240 or DIN 17440. In Europe, preferences for stainless steel may be higher due to stringent regulations on corrosion resistance.
Why Choose Bronze for Worm and Wheel Gears?
Key Properties: Bronze, especially phosphor bronze, offers excellent wear resistance and low friction properties. It is also resistant to corrosion, particularly in seawater.
Pros & Cons: The primary advantage of bronze is its self-lubricating properties, which reduce maintenance needs. However, bronze can be more expensive than steel and may not handle high loads as effectively.
Impact on Application: Bronze gears are often used in applications where lubrication is difficult, such as marine equipment, pumps, and valves. They are also suitable for low-speed applications.
Considerations for International Buyers: Compliance with standards like ASTM B150 or JIS H3250 is essential. Buyers in the Middle East and Africa should consider the availability of bronze materials and their cost implications.
How Do Engineering Plastics Compare for Worm and Wheel Gears?
Key Properties: Engineering plastics, such as nylon and acetal, offer lightweight, high strength, and excellent wear resistance. They also have good chemical resistance and can operate in a wide temperature range.
Pros & Cons: The main advantage of engineering plastics is their lower weight and noise reduction during operation. However, they may not be suitable for high-load applications and can be more expensive than traditional materials.
Impact on Application: Engineering plastics are ideal for applications in robotics, medical devices, and consumer products where weight and noise are critical factors. They also provide good electrical insulation.
Considerations for International Buyers: Compliance with standards such as ASTM D638 or ISO 527 is important. Buyers from Europe may prefer plastics due to lightweight requirements in automotive applications.
Summary Table of Material Selection for Worm and Wheel Gears
Material | Typical Use Case for worm and wheel gear | Key Advantage | Key Disadvantage/Limitation | Relative Cost (Low/Med/High) |
---|---|---|---|---|
Carbon Steel | Heavy machinery, automotive applications | Durable and cost-effective | Prone to corrosion | Medium |
Stainless Steel | Food processing, marine applications | Excellent corrosion resistance | Higher cost and machining complexity | High |
Bronze | Marine equipment, pumps | Self-lubricating, low maintenance | More expensive, lower load capacity | Medium |
Engineering Plastics | Robotics, medical devices | Lightweight, noise reduction | Not suitable for high-load applications | Medium to High |
This strategic material selection guide provides international B2B buyers with valuable insights into the various materials available for worm and wheel gears, helping them make informed decisions based on their specific applications and regional considerations.
In-depth Look: Manufacturing Processes and Quality Assurance for worm and wheel gear
What Are the Key Stages in the Manufacturing Process of Worm and Wheel Gears?
Worm and wheel gears are precision components essential in various mechanical systems. The manufacturing process typically encompasses several critical stages: material preparation, forming, assembly, and finishing.
Material Preparation: What Materials Are Used for Worm and Wheel Gears?
The choice of materials is vital for ensuring the durability and efficiency of worm and wheel gears. Common materials include:
- Worms: Generally made from high-strength steels (like S45C and SCM440) or stainless steel to withstand wear and stress.
- Worm Wheels: Often constructed from softer materials such as phosphor bronze, cast iron, or aluminum bronze, which facilitate smoother interaction with the harder worm.
Before manufacturing, raw materials are subjected to quality checks to confirm they meet specific mechanical properties and standards. This includes verifying chemical composition, hardness, and tensile strength.
How Are Worm and Wheel Gears Formed?
The forming stage involves various techniques to shape the raw materials into functional gears. Key techniques include:
- Machining: Precision machining processes like CNC turning and milling are used to create the worm’s helical threads and the wheel’s teeth. This ensures high accuracy in dimensions and tooth profiles.
- Hobbing: This is a common method for producing worm wheels, where a cutting tool (hob) shapes the gear teeth with precision.
- Broaching: Often used for internal gear teeth, broaching provides a highly accurate and efficient means of achieving the desired tooth profile.
These methods help achieve the necessary tolerances and surface finishes required for optimal gear performance.
What Does the Assembly Process Involve?
The assembly of worm and wheel gears requires meticulous attention to detail. Key steps include:
- Alignment: Proper alignment of the worm and wheel is crucial to ensure smooth operation and minimize wear. This may involve the use of jigs and fixtures during the assembly process.
- Backlash Adjustment: This is particularly important in worm gears. Adjustments may be made using shims to maintain the appropriate distance between the worm and wheel, ensuring efficient power transmission.
- Lubrication Application: High-viscosity lubricants are applied at this stage to reduce friction and enhance performance. The selection of lubricant is essential to prevent sliding wear, which is prevalent in worm gear systems.
What Quality Assurance Measures Are Essential for Worm and Wheel Gear Production?
Quality assurance (QA) is critical in ensuring that worm and wheel gears meet industry standards and customer expectations. The QA process typically involves adherence to international and industry-specific standards.
Which International Standards Are Relevant for Worm and Wheel Gears?
International standards such as ISO 9001 are fundamental for manufacturers aiming to establish a quality management system (QMS). Compliance with ISO 9001 helps ensure that products consistently meet customer and regulatory requirements. Other industry-specific certifications might include:
- CE Marking: Indicating conformity with health, safety, and environmental protection standards for products sold within the European Economic Area.
- API Standards: Particularly relevant for gears used in the oil and gas industry, ensuring they meet stringent operational requirements.
What Are the Key Quality Control Checkpoints in the Manufacturing Process?
Quality control (QC) is typically divided into several checkpoints throughout the manufacturing process:
- Incoming Quality Control (IQC): Raw materials undergo inspection for compliance with specifications before production begins.
- In-Process Quality Control (IPQC): During manufacturing, ongoing checks are performed to monitor tolerances and dimensions.
-
Final Quality Control (FQC): Once manufacturing is complete, finished gears are subjected to rigorous testing, including:
-
Dimensional Inspection: Verifying the accuracy of gear dimensions and tooth profiles.
- Functional Testing: Assessing the performance under operational conditions to ensure reliability and efficiency.
How Can B2B Buyers Verify Supplier Quality Control Practices?
For international B2B buyers, particularly from Africa, South America, the Middle East, and Europe, verifying supplier QC practices is essential for ensuring the reliability of products. Here are actionable strategies:
What Methods Can Buyers Use to Audit Supplier QC Processes?
- Supplier Audits: Conducting on-site audits allows buyers to evaluate the manufacturing processes, equipment, and adherence to quality standards.
- Reviewing Quality Reports: Requesting detailed quality reports from suppliers can provide insights into their QC practices and any issues encountered during production.
- Third-Party Inspections: Engaging third-party inspection services can provide an unbiased assessment of the manufacturing process and product quality.
What Are the Specific QC and Certification Nuances for International Buyers?
International buyers should be aware of specific nuances, including:
- Regulatory Compliance: Understanding local regulations in both the supplier’s and buyer’s regions can impact product acceptance.
- Cultural Considerations: Different regions may have varying standards of quality and expectations for QC practices. Buyers must communicate their quality requirements clearly to avoid misunderstandings.
By adhering to these guidelines, international B2B buyers can ensure they source high-quality worm and wheel gears that meet their operational needs and industry standards, thus enhancing their supply chain reliability.
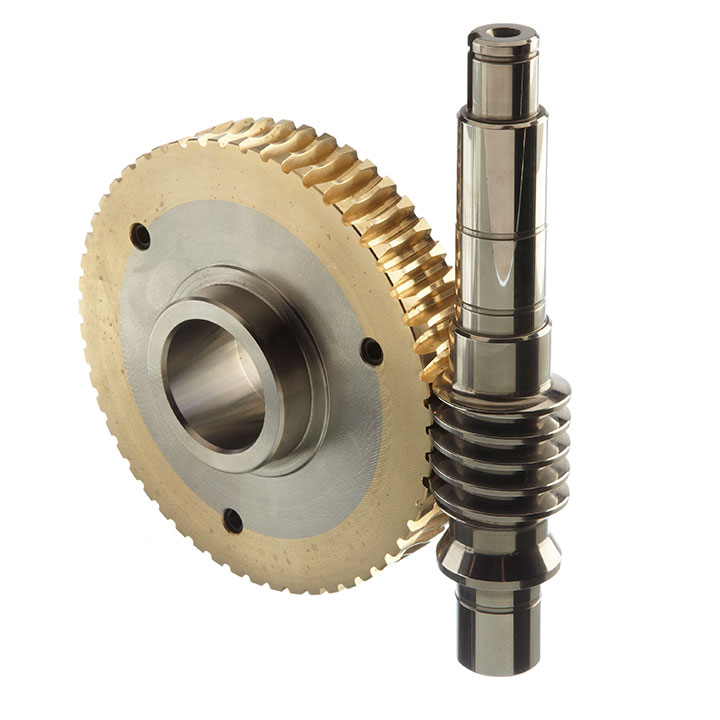
A stock image related to worm and wheel gear.
Practical Sourcing Guide: A Step-by-Step Checklist for ‘worm and wheel gear’
Introduction
Sourcing worm and wheel gears can be a complex process, particularly for international B2B buyers looking for reliable suppliers across diverse regions such as Africa, South America, the Middle East, and Europe. This checklist provides actionable steps to guide buyers through the procurement process, ensuring they select the right components that meet their technical requirements and operational needs.
Step 1: Define Your Technical Specifications
Before reaching out to suppliers, clearly outline the technical specifications required for your worm and wheel gears. This includes the gear ratio, material preferences (such as steel or bronze), and the operating environment (temperature, humidity, etc.).
- Key Considerations: Specify load capacity, dimensions, and any necessary certifications (like ISO standards) to ensure compliance with industry regulations.
Step 2: Research Potential Suppliers
Conduct thorough research to identify potential suppliers who specialize in worm and wheel gears. Look for manufacturers with a proven track record in your specific industry.
- Where to Look: Utilize platforms such as industry trade shows, online directories, and recommendations from industry peers.
Step 3: Evaluate Supplier Certifications and Quality Assurance
Before making a commitment, it’s essential to verify that your chosen suppliers hold relevant certifications and adhere to quality assurance practices.
- What to Check: Look for ISO certifications, compliance with international standards, and any third-party quality endorsements. This ensures that the products will meet your specifications and reduce the risk of defects.
Step 4: Request Samples and Technical Documentation
Request samples of the worm and wheel gears along with technical documentation, such as material specifications and load capacity charts.
- Why This Matters: Testing samples allows you to assess the quality and performance of the gears in your applications, while documentation provides crucial insights into compatibility with your systems.
Step 5: Discuss Customization Options
Engage with suppliers about potential customization options that could better suit your operational needs. Many manufacturers offer bespoke solutions that can enhance efficiency.
- Customization Examples: Inquire about specific gear ratios, materials, or dimensions that may not be available in standard offerings. Discuss any unique operational challenges you face and how they might tailor solutions.
Step 6: Review Pricing and Payment Terms
Once you have narrowed down your options, compare pricing structures and payment terms among suppliers.
- Important Considerations: Look beyond just the price; assess the total cost of ownership, including shipping, handling, and any potential tariffs. Favor suppliers who offer flexible payment terms that align with your cash flow needs.
Step 7: Establish Communication and Support Channels
Ensure that your supplier has robust communication and support systems in place. This is vital for ongoing collaboration and issue resolution.
- What to Look For: Confirm that the supplier offers reliable customer support and technical assistance. Establish clear lines of communication to facilitate timely responses to any inquiries or issues that may arise during the procurement process.
By following this checklist, international B2B buyers can navigate the complexities of sourcing worm and wheel gears, ensuring they make informed decisions that align with their operational requirements and business goals.
Comprehensive Cost and Pricing Analysis for worm and wheel gear Sourcing
What are the Key Cost Components in Worm and Wheel Gear Sourcing?
When sourcing worm and wheel gears, understanding the various cost components is essential for making informed purchasing decisions. The primary cost elements include:
-
Materials: The choice of materials significantly impacts the cost. Worms are typically made from harder materials like carbon steel or stainless steel, while worm wheels may be constructed from bronze, cast iron, or engineering plastics. The material selection should align with the application requirements, balancing cost and durability.
-
Labor: Labor costs can vary widely depending on the manufacturing region. In regions with lower labor costs, such as some parts of Africa and South America, buyers may find more competitive pricing. However, it is crucial to ensure that the quality of workmanship meets industry standards.
-
Manufacturing Overhead: This includes indirect costs associated with production, such as utilities, rent, and administrative expenses. Higher overhead can lead to increased prices, so buyers should inquire about the supplier’s operational efficiency.
-
Tooling: Custom tooling for specific gear designs can add to the initial costs. However, investing in high-quality tooling may reduce long-term production costs and improve product quality.
-
Quality Control (QC): Rigorous QC processes ensure the reliability and performance of worm gears. Suppliers with stringent QC measures may charge higher prices, but this can lead to lower failure rates and maintenance costs over time.
-
Logistics: Transportation costs can fluctuate based on distance, shipping method, and local regulations. Buyers should consider logistics as a vital component of the total cost, especially when sourcing from international suppliers.
-
Margin: Supplier profit margins vary based on market conditions, competition, and product demand. Understanding the market landscape can help buyers gauge whether pricing is fair or inflated.
How Do Pricing Influencers Affect the Cost of Worm and Wheel Gears?
Several factors influence the pricing of worm and wheel gears, which can vary based on buyer specifications and supplier capabilities:
-
Volume and Minimum Order Quantity (MOQ): Larger orders typically lead to lower per-unit costs due to economies of scale. Buyers should negotiate MOQs to optimize pricing.
-
Specifications and Customization: Custom designs or specifications can increase costs. Buyers should clearly define their requirements to avoid unexpected price hikes.
-
Material Quality and Certifications: Higher-quality materials and certifications (e.g., ISO standards) enhance performance but also increase costs. Buyers should assess the necessity of certifications based on their application needs.
-
Supplier Factors: The supplier’s reputation, experience, and geographical location can affect pricing. Established suppliers may charge a premium for their reliability and expertise.
-
Incoterms: Understanding Incoterms is crucial for international transactions. They dictate the responsibilities of buyers and sellers regarding shipping, insurance, and tariffs, which can impact the overall cost.
What Buyer Tips Can Help Achieve Cost-Efficiency in Worm and Wheel Gear Sourcing?
To maximize value in worm and wheel gear procurement, buyers should consider the following strategies:
-
Negotiation: Engage suppliers in open discussions about pricing, especially for larger orders. Leverage volume commitments to negotiate better rates.
-
Total Cost of Ownership (TCO): Evaluate not just the purchase price but also the long-term costs associated with maintenance, reliability, and potential downtime. Investing in higher-quality gears may result in lower TCO.
-
Pricing Nuances for International Buyers: International buyers should be aware of currency fluctuations, tariffs, and import duties that may affect final costs. Building relationships with suppliers in target regions can also facilitate smoother transactions.
-
Request for Quotes (RFQs): Solicit quotes from multiple suppliers to compare prices and service offerings. This process can provide insights into market rates and help identify competitive pricing.
Disclaimer on Indicative Prices
Prices for worm and wheel gears can vary significantly based on the factors mentioned above. It is advisable for buyers to conduct thorough market research and obtain multiple quotes to ensure they are making cost-effective purchasing decisions tailored to their specific needs.
Alternatives Analysis: Comparing worm and wheel gear With Other Solutions
When evaluating mechanical solutions for motion transmission, it is crucial to consider various alternatives to worm and wheel gears. Each alternative offers distinct advantages and disadvantages that can significantly impact performance, cost, and application suitability. Below is a detailed comparison of worm and wheel gears with two other prevalent gear solutions: helical gears and bevel gears.
Comparison Aspect | Worm And Wheel Gear | Helical Gear | Bevel Gear |
---|---|---|---|
Performance | High reduction ratios; self-locking ability; lower efficiency due to sliding contact (30-60%). | Smooth operation; high efficiency (up to 90%); can transmit power at various angles. | Excellent for changing axis direction; offers high torque capacity. |
Cost | Moderate initial cost; higher long-term lubrication costs. | Generally higher initial cost due to complexity; lower maintenance costs. | Moderate cost; dependent on material and manufacturing precision. |
Ease of Implementation | Simple design; requires precise alignment; lubrication challenges. | More complex assembly; requires careful alignment for optimal performance. | Installation can be straightforward; requires precise machining for best fit. |
Maintenance | High maintenance due to lubrication needs; susceptible to wear. | Lower maintenance; lubrication is easier due to rolling contact. | Moderate maintenance; lubrication needs depend on application. |
Best Use Case | Ideal for applications needing high torque at low speeds (e.g., elevators, conveyors). | Best for applications requiring efficiency and speed control (e.g., automotive, robotics). | Suitable for applications needing a change in drive direction (e.g., power tools, automotive differentials). |
What Are the Pros and Cons of Helical Gears Compared to Worm and Wheel Gears?
Helical gears utilize angled teeth that allow for smoother and quieter operation compared to worm gears. They offer higher efficiency levels and can handle greater loads, making them suitable for high-speed applications. However, their design complexity may lead to higher initial costs and require precise alignment during installation. In environments where noise and vibration are a concern, helical gears might be the preferred choice, especially in automotive and industrial machinery applications.
How Do Bevel Gears Compare with Worm and Wheel Gears in Terms of Performance?
Bevel gears are designed to transmit power between shafts at angles, typically 90 degrees. They excel in applications requiring high torque and can handle significant loads, making them ideal for power tools and automotive differentials. However, bevel gears can also be more expensive to manufacture due to the precision required in their construction. Their maintenance needs are moderate, and they can operate efficiently with proper lubrication. For applications that necessitate a change in direction of power transmission, bevel gears can often outperform worm gears.
Conclusion: How to Choose the Right Gear Solution for Your Needs
In selecting the right gear solution, international B2B buyers should assess their specific operational requirements, including torque, speed, and the operational environment. Worm and wheel gears may be ideal for low-speed, high-torque applications, but their lubrication demands and efficiency limitations must be considered. Conversely, helical and bevel gears offer higher efficiencies and smoother operation at the cost of increased complexity and potential higher initial investment. Evaluating these factors will ensure that businesses make informed decisions that align with their operational goals and budget constraints.
Essential Technical Properties and Trade Terminology for worm and wheel gear
What Are the Essential Technical Properties of Worm and Wheel Gears?
When considering the procurement of worm and wheel gears, several technical specifications are crucial for ensuring optimal performance and longevity in applications. Here are some key properties to focus on:
1. Material Grade: Why Does It Matter?
The materials used in worm and wheel gears significantly affect their durability and efficiency. Common materials include mechanical structural carbon steel (S45C), stainless steel, and various bronzes for the worm wheel. The choice of material influences wear resistance, load capacity, and lubrication requirements. For international buyers, understanding material specifications ensures compatibility with local standards and enhances equipment longevity.
2. Gear Ratio: What Should You Look For?
The gear ratio defines the relationship between the rotational speeds of the worm and the wheel. High gear ratios (up to 1/120 for some models) allow for significant speed reduction and torque multiplication. This is particularly beneficial in applications where space is limited and high torque is needed. Buyers should assess their operational needs to select gears with suitable ratios for efficient performance.
3. Tolerance Levels: How Do They Impact Performance?
Tolerance refers to the permissible limit of variation in a physical dimension. In worm and wheel gears, tight tolerances ensure smooth engagement and minimize backlash, which enhances accuracy in applications such as robotics and machine tools. Buyers should prioritize suppliers who can provide precise tolerance specifications to ensure optimal functionality.
4. Lubrication Requirements: What Are the Implications?
Worm gears typically require high-viscosity lubricants (ISO 320 and above) due to their sliding contact nature. The lubrication type affects heat generation and wear rates. Buyers must understand the specific lubrication needs to avoid premature gear failure and ensure operational efficiency, especially in regions with extreme temperatures.
5. Efficiency Ratings: What Are the Expected Levels?
Efficiency ratings indicate how well the gear transmits power without excessive losses. Worm gears generally exhibit efficiencies ranging from 30% to 60%. Buyers should consider these ratings when selecting gears for applications where energy efficiency is critical, such as in manufacturing and transportation systems.
What Trade Terminology Should You Understand in the Worm Gear Industry?
Familiarity with industry terminology is essential for smooth transactions and effective communication with suppliers. Here are some common terms:
1. OEM (Original Equipment Manufacturer): What Does It Signify?
An OEM is a company that manufactures products that are sold under another company’s brand. Understanding OEM relationships is crucial for buyers looking for reliable gear suppliers who maintain high-quality standards in their products.
2. MOQ (Minimum Order Quantity): How Does It Affect Your Purchasing?
MOQ refers to the smallest quantity of a product that a supplier is willing to sell. This term is critical for budgeting and inventory management, especially for international buyers who may need to balance costs with storage capabilities.
3. RFQ (Request for Quotation): Why Is It Important?
An RFQ is a formal document that solicits price bids from suppliers for specific products or services. For B2B buyers, submitting an RFQ helps clarify requirements and obtain competitive pricing, ensuring informed purchasing decisions.
4. Incoterms: What Are They and Why Should You Care?
Incoterms (International Commercial Terms) are predefined commercial terms that clarify the responsibilities of buyers and sellers in international transactions. Understanding these terms is vital for managing shipping costs and liabilities, particularly for buyers from different continents.
5. Backlash: How Does It Impact Gear Functionality?
Backlash refers to the slight movement between gears when they are engaged. It can affect precision in applications requiring high accuracy. Buyers should consider the allowable backlash in gear specifications to ensure compatibility with their operational needs.
By understanding these essential technical properties and trade terminologies, international B2B buyers can make informed decisions when procuring worm and wheel gears, ultimately enhancing their operational efficiency and product performance.
Navigating Market Dynamics and Sourcing Trends in the worm and wheel gear Sector
What Are the Current Market Dynamics and Key Trends in the Worm and Wheel Gear Sector?
The global worm and wheel gear market is currently experiencing several transformative dynamics driven by technological advancements and evolving buyer needs. One of the primary drivers is the increasing demand for high-efficiency power transmission systems across various sectors, including automotive, manufacturing, and robotics. The advent of Industry 4.0 has spurred the adoption of smart manufacturing technologies, leading to a heightened focus on precision and reliability in gear systems. This trend is particularly notable in regions like Europe and North America, where advanced manufacturing techniques are being integrated into traditional practices.
In Africa and South America, the market is witnessing growth fueled by infrastructural development and modernization of manufacturing facilities. These regions are increasingly investing in automated systems, which often require specialized gear solutions, such as worm gears, due to their compact design and high torque capabilities. Additionally, the Middle East is focusing on energy-efficient solutions, which further enhances the demand for worm and wheel gears that can effectively handle high loads while maintaining energy efficiency.
Emerging B2B sourcing trends include a shift towards online procurement platforms, enabling international buyers to access a broader range of suppliers and streamline their sourcing processes. This digital transformation allows for real-time comparison of product specifications, pricing, and delivery times, which is critical for buyers from diverse geographical backgrounds like Italy and Indonesia. As such, international buyers should focus on leveraging technology to enhance their procurement strategies and capitalize on market opportunities.
How Are Sustainability and Ethical Sourcing Addressed in the Worm and Wheel Gear Sector?
Sustainability is becoming an integral aspect of sourcing in the worm and wheel gear sector, driven by increasing regulatory pressures and consumer demand for environmentally responsible products. The manufacturing process of these gears typically involves significant energy consumption and the use of raw materials, which can have a considerable environmental impact. Consequently, international B2B buyers are now prioritizing suppliers that demonstrate a commitment to sustainable practices, such as reducing waste and optimizing energy usage.
Ethical sourcing is equally important, as buyers are increasingly scrutinizing their supply chains for compliance with labor standards and environmental regulations. This is particularly relevant for buyers from Africa and South America, where local sourcing can significantly impact community development and sustainability. Suppliers that can provide certifications such as ISO 14001 (Environmental Management) or ISO 45001 (Occupational Health and Safety) are becoming more attractive to buyers seeking to align their purchasing decisions with corporate social responsibility (CSR) goals.
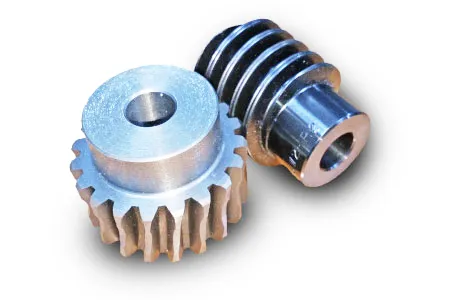
A stock image related to worm and wheel gear.
Additionally, the use of eco-friendly materials in the production of worm and wheel gears, such as recycled metals or low-impact lubricants, is gaining traction. Buyers should actively seek out suppliers who can demonstrate their commitment to sustainability through certifications and transparent reporting on their environmental practices. By prioritizing sustainability and ethical sourcing, international B2B buyers can not only meet regulatory requirements but also enhance their brand reputation and customer loyalty.
What Is the Historical Context of Worm and Wheel Gears Relevant to Today’s Market?
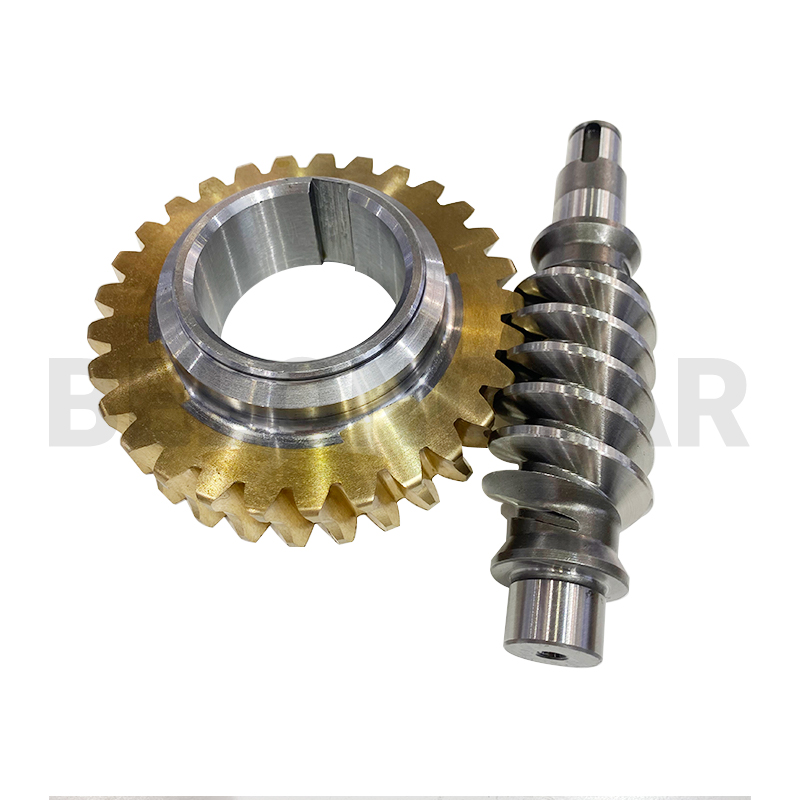
A stock image related to worm and wheel gear.
The history of worm and wheel gears dates back to ancient times, with Archimedes first describing their use around 250 BC. Initially employed in simple machines, these gears have evolved significantly over the centuries, becoming integral components in various applications due to their unique ability to transmit motion between non-parallel shafts at a right angle. The compact design and high reduction ratios made worm gears particularly valuable in machinery where space constraints and torque requirements are critical.
Over the years, advancements in materials and manufacturing processes have led to the development of more robust and efficient worm gear systems. Today, modern materials such as carbon steel and advanced composites are used to enhance durability and performance. This evolution not only reflects technological progress but also highlights the growing importance of precision engineering in meeting the demands of contemporary industries. Understanding this historical context can help international B2B buyers appreciate the value and potential applications of worm and wheel gears in their operations, guiding them in making informed purchasing decisions.
Frequently Asked Questions (FAQs) for B2B Buyers of worm and wheel gear
-
1. How do I solve lubrication issues with worm and wheel gears?
Proper lubrication is crucial for the performance and longevity of worm and wheel gears due to the sliding friction involved in their operation. To solve lubrication issues, select a high-viscosity lubricant specifically designed for worm gears, such as ISO 460 or ISO 680 oils. Ensure that your lubrication system includes adequate filtering and pumping capabilities, as high-viscosity oils can be challenging to manage. Regularly monitor lubricant levels and condition to prevent wear and overheating, and consider implementing a maintenance schedule that includes lubricant changes and inspections. -
2. What is the best material for worm and wheel gears?
The choice of material for worm and wheel gears significantly impacts performance. Typically, worms are made from harder materials like mechanical structural carbon steel or alloy steel, while worm wheels are often constructed from softer materials like cast iron or brass. For applications requiring reduced wear and increased durability, consider using phosphor bronze for the wheel. Evaluate the specific demands of your application, such as load capacity and environmental conditions, to select the most suitable material for optimal performance. -
3. How can I customize worm and wheel gears for my specific application?
Customization of worm and wheel gears can be achieved by specifying dimensions, material types, and gear ratios that meet your application’s unique requirements. Communicate your needs clearly to suppliers, including parameters like shaft angles, reduction ratios, and backlash tolerances. Many manufacturers offer custom solutions, allowing you to modify gear designs to fit specialized applications, such as robotics or automotive systems. It’s essential to collaborate with experienced engineers or manufacturers who can guide you through the customization process to ensure compatibility. -
4. What are the minimum order quantities (MOQs) for worm and wheel gears?
Minimum order quantities for worm and wheel gears vary by supplier and can depend on factors like the complexity of the gear design and production capacity. Generally, MOQs can range from a few pieces for standard items to larger quantities for custom orders. To find the best supplier for your needs, inquire directly about MOQs and negotiate terms that align with your purchasing strategy. Consider consolidating orders with other components to meet MOQ requirements while optimizing your supply chain. -
5. What payment terms should I expect when sourcing worm and wheel gears internationally?
Payment terms for international transactions can vary widely depending on the supplier and the nature of the agreement. Common payment options include upfront payments, letters of credit, or payment upon delivery. It’s advisable to establish clear terms regarding payment schedules, currency, and any potential fees associated with international transactions. Ensure that you understand the risks involved with each payment method, especially when dealing with suppliers in different regions, and consider using trusted payment platforms to enhance security. -
6. How can I vet suppliers of worm and wheel gears effectively?
Vetting suppliers involves assessing their credibility, quality standards, and production capabilities. Start by reviewing their certifications, such as ISO standards, which indicate adherence to quality management systems. Request references or case studies from previous clients to gauge their reliability. Additionally, consider visiting their manufacturing facilities if possible, or utilizing third-party inspection services. Engaging in detailed discussions about their manufacturing processes, lead times, and customer support can also help ensure you select a reputable supplier. -
7. What logistics considerations should I keep in mind when importing worm and wheel gears?
When importing worm and wheel gears, consider logistics factors such as shipping methods, customs regulations, and lead times. Choose a reliable freight forwarder experienced in handling industrial components to navigate international shipping complexities. Understand the customs duties and taxes applicable in your region, and ensure compliance with local regulations to avoid delays. Additionally, plan for potential supply chain disruptions by allowing extra time for shipping and customs clearance, especially if sourcing from regions with unpredictable logistics. -
8. What quality assurance (QA) measures are important when sourcing worm and wheel gears?
Implementing robust quality assurance measures is essential for ensuring the reliability of worm and wheel gears. Request documentation of the supplier’s QA processes, including material inspections, dimensional checks, and performance testing. Consider requiring third-party inspections for critical components to verify compliance with specifications. Establish a clear agreement on warranty terms and post-sale support to address any potential quality issues that may arise after purchase. Regular communication with suppliers regarding quality expectations can help mitigate risks in the procurement process.
Important Disclaimer & Terms of Use
⚠️ Important Disclaimer
The information provided in this guide, including content regarding manufacturers, technical specifications, and market analysis, is for informational and educational purposes only. It does not constitute professional procurement advice, financial advice, or legal advice.
While we have made every effort to ensure the accuracy and timeliness of the information, we are not responsible for any errors, omissions, or outdated information. Market conditions, company details, and technical standards are subject to change.
B2B buyers must conduct their own independent and thorough due diligence before making any purchasing decisions. This includes contacting suppliers directly, verifying certifications, requesting samples, and seeking professional consultation. The risk of relying on any information in this guide is borne solely by the reader.
Strategic Sourcing Conclusion and Outlook for worm and wheel gear
Why Is Strategic Sourcing Essential for Worm and Wheel Gears?
In the ever-evolving landscape of manufacturing and engineering, strategic sourcing for worm and wheel gears is critical for optimizing performance and reducing operational costs. By understanding the unique attributes of worm gears, such as their high reduction ratios and self-locking capabilities, international B2B buyers can make informed decisions that enhance machinery efficiency. Additionally, recognizing the challenges associated with lubrication and wear can guide buyers in selecting the right materials and lubricants, ultimately prolonging equipment lifespan.
What Are the Key Takeaways for International Buyers?
For buyers in Africa, South America, the Middle East, and Europe, prioritizing suppliers who offer high-quality materials—like mechanical structural alloy steel for worms and phosphor bronze for wheels—can significantly impact performance. Furthermore, considering manufacturers who provide tailored solutions, such as dual-lead worm gears for adjustable backlash, can lead to enhanced operational flexibility.
How to Prepare for Future Trends in Worm Gear Technology?
As industries increasingly shift towards automation and precision engineering, the demand for compact and efficient worm gear solutions will continue to rise. Buyers should stay informed about emerging technologies and innovations in gear design, including advancements in lubrication techniques and material science, to maintain a competitive edge.
Call to Action for Strategic Partnerships
Engaging in strategic partnerships with reputable manufacturers and suppliers can unlock new opportunities and drive success in your operations. Now is the time to explore these options and ensure your sourcing strategies are aligned with future industry trends.