Unlock Quality Gains: The Complete 316 Stainless Composition (2025)
Introduction: Navigating the Global Market for 316 stainless composition
In today’s competitive landscape, international B2B buyers face the critical challenge of sourcing 316 stainless composition that meets both quality and cost-effectiveness requirements. With its superior corrosion resistance and versatile applications, 316 stainless steel has become a preferred choice across various industries, including marine, chemical, and food processing. However, navigating the complexities of global suppliers can be daunting, especially for buyers from Africa, South America, the Middle East, and Europe.
This comprehensive guide is designed to empower B2B buyers by detailing the nuances of 316 stainless composition, including its chemical makeup, mechanical properties, and specific applications. We will explore various grades of stainless steel, supplier vetting techniques, and cost analysis strategies, ensuring that buyers can make informed decisions tailored to their operational needs.
By understanding the unique characteristics and applications of 316 stainless steel, buyers can select the right materials for their projects, minimize risks, and enhance operational efficiency. Whether you are sourcing for industrial equipment, architectural projects, or specialized manufacturing processes, this guide provides actionable insights to streamline your procurement process and ensure you achieve the best value in your purchases. As we delve into the world of 316 stainless composition, you will gain the knowledge necessary to navigate the global market confidently.
Understanding 316 stainless composition Types and Variations
Type Name | Key Distinguishing Features | Primary B2B Applications | Brief Pros & Cons for Buyers |
---|---|---|---|
316 Stainless Steel | Contains molybdenum for enhanced chloride resistance | Marine, chemical processing, food | Pros: Excellent corrosion resistance; versatile. Cons: Higher cost than lower grades. |
316L Stainless Steel | Low carbon content to reduce carbide precipitation in welding | Pharmaceuticals, nuclear, food | Pros: Better weldability; suitable for high-purity applications. Cons: Slightly lower strength than standard 316. |
316Ti Stainless Steel | Titanium addition for improved high-temperature stability | Aerospace, high-temperature environments | Pros: Enhanced stability at elevated temperatures. Cons: More expensive due to titanium content. |
316N Stainless Steel | Nitrogen addition for improved strength and corrosion resistance | Oil and gas, marine applications | Pros: High strength; excellent resistance to pitting. Cons: Limited availability compared to standard grades. |
316F Stainless Steel | Free-machining variant with added sulfur for better machinability | Automotive, manufacturing | Pros: Easier to machine; good surface finish. Cons: Slightly lower corrosion resistance than standard 316. |
What Are the Key Characteristics of 316 Stainless Steel?
316 stainless steel is the standard grade in the 316 family, recognized for its superior resistance to corrosion, particularly in chloride-rich environments. Its composition includes 16-18% chromium, 10-14% nickel, and 2-3% molybdenum, which enhances its durability and makes it suitable for a wide range of applications such as marine and chemical processing. Buyers should consider its versatility and reliability, although they may face higher costs compared to lower grades like 304 stainless steel.
How Does 316L Stainless Steel Differ from Standard 316?
316L stainless steel features a lower carbon content, which significantly reduces the risk of carbide precipitation during welding. This makes it ideal for applications in the pharmaceutical and nuclear sectors where high purity is critical. Its enhanced weldability is a major advantage for projects requiring extensive fabrication. However, buyers should note that while it offers excellent corrosion resistance, its strength is slightly lower than that of standard 316.
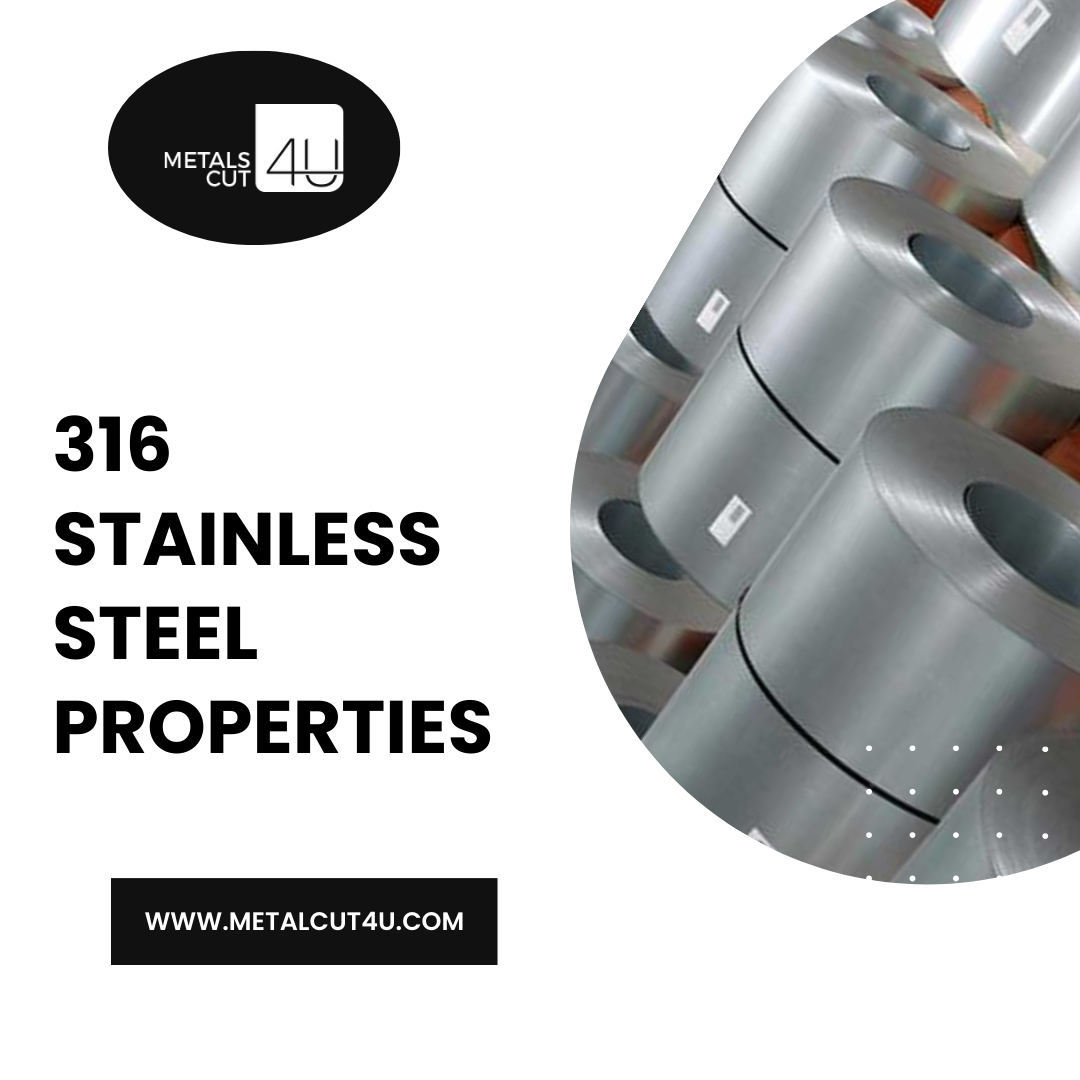
A stock image related to 316 stainless composition.
Why Choose 316Ti Stainless Steel for High-Temperature Applications?
316Ti stainless steel incorporates titanium, providing improved stability at high temperatures. This variant is particularly beneficial in aerospace and other high-temperature environments where material integrity is crucial. While it offers enhanced performance, the inclusion of titanium raises the cost, making it a consideration for buyers focused on long-term durability and performance in extreme conditions.
What Advantages Does 316N Stainless Steel Offer for Industrial Use?
316N stainless steel is enhanced with nitrogen, which improves both strength and corrosion resistance. It is particularly suited for demanding environments in the oil and gas industry and marine applications where pitting corrosion is a concern. While it provides excellent mechanical properties, its availability can be more limited than standard grades, which may affect procurement timelines for international buyers.
How Does 316F Stainless Steel Improve Machinability?
316F stainless steel is designed for improved machinability due to the addition of sulfur. This variant is particularly useful in automotive and manufacturing applications where ease of machining is a priority. While it allows for better surface finishes and reduced tool wear, buyers should be aware that it may not offer the same level of corrosion resistance as standard 316, necessitating careful consideration based on the application’s specific environmental conditions.
Key Industrial Applications of 316 stainless composition
Industry/Sector | Specific Application of 316 stainless composition | Value/Benefit for the Business | Key Sourcing Considerations for this Application |
---|---|---|---|
Chemical Processing | Storage tanks for corrosive chemicals | Enhanced durability and safety in handling hazardous materials | Ensure compliance with international safety standards |
Marine Engineering | Shipbuilding and offshore structures | Superior resistance to saltwater corrosion | Evaluate local suppliers with marine-grade certifications |
Food and Beverage | Food processing equipment and storage solutions | Maintains hygiene and prevents contamination | Verify certifications for food safety regulations |
Pharmaceutical Industry | Equipment for drug manufacturing | Ensures product purity and compliance with health regulations | Source from suppliers with a proven track record in pharma |
Oil and Gas | Pipeline systems and fittings | Reliable performance in extreme environments | Assess material certifications for high-pressure applications |
How is 316 Stainless Steel Used in Chemical Processing?
In the chemical processing sector, 316 stainless steel is commonly used for storage tanks and piping systems that handle corrosive substances. The alloy’s exceptional resistance to pitting and crevice corrosion makes it ideal for environments where chemicals may react with standard materials. International B2B buyers should prioritize suppliers who can demonstrate compliance with global safety standards, ensuring their products can withstand the rigors of chemical storage without compromising safety.
What Role Does 316 Stainless Steel Play in Marine Engineering?
In marine engineering, 316 stainless steel is favored for shipbuilding and offshore structures due to its superior resistance to saltwater corrosion. This property is crucial in preventing structural failures and extending the lifespan of marine vessels. Buyers from regions with extensive coastlines, such as Africa and the Middle East, should consider sourcing from suppliers who specialize in marine-grade materials, ensuring they meet the rigorous demands of maritime applications.
Why is 316 Stainless Steel Essential in Food and Beverage Applications?
The food and beverage industry relies on 316 stainless steel for processing equipment and storage solutions, as it maintains hygiene and prevents contamination. Its non-reactive nature ensures that food products remain untainted by metals, making it a preferred choice for manufacturers. B2B buyers must verify that their suppliers comply with food safety regulations, such as FDA standards, to ensure the quality and safety of their products.
How is 316 Stainless Steel Utilized in the Pharmaceutical Industry?
In the pharmaceutical industry, 316 stainless steel is utilized in the manufacturing of equipment that requires high levels of cleanliness and product purity. This alloy helps prevent contamination, ensuring that drugs produced meet stringent health regulations. International buyers should seek suppliers with a proven track record in pharmaceutical applications, focusing on those who can provide documentation of compliance with relevant industry standards.
What Benefits Does 316 Stainless Steel Offer in Oil and Gas Applications?
In the oil and gas sector, 316 stainless steel is commonly used for pipeline systems and fittings due to its reliable performance in extreme environments. The alloy’s durability and corrosion resistance are crucial for maintaining system integrity and safety. B2B buyers should assess the material certifications of potential suppliers, ensuring they can withstand high-pressure applications and meet industry-specific requirements.
3 Common User Pain Points for ‘316 stainless composition’ & Their Solutions
Scenario 1: Inconsistent Quality of 316 Stainless Steel Supply
The Problem:
B2B buyers often struggle with the inconsistent quality of 316 stainless steel from various suppliers. Variability in chemical composition, such as the percentages of nickel and molybdenum, can lead to significant differences in corrosion resistance and mechanical properties. This inconsistency can jeopardize the integrity of the end products, particularly in industries like pharmaceuticals, food processing, and marine applications, where precision and reliability are critical.
The Solution:
To mitigate the risk of quality inconsistency, B2B buyers should establish strict quality assurance processes when selecting suppliers. It’s crucial to request detailed certificates of compliance that specify the chemical composition and mechanical properties of the steel. Engage suppliers who adhere to recognized standards such as ASTM A240 or AMS 5524, which ensure that the material meets industry specifications. Additionally, consider conducting regular audits of suppliers to verify their manufacturing processes and material quality. By fostering long-term relationships with trusted suppliers who prioritize quality, buyers can ensure they receive reliable 316 stainless steel that meets their operational needs.
Scenario 2: High Costs Due to Improper Material Selection
The Problem:
Many international buyers, especially those in emerging markets, face the challenge of escalating costs due to improper selection of materials. Opting for lower-grade stainless steels to save costs can lead to premature failure, increased maintenance, and ultimately higher replacement expenses. This is particularly relevant in industries like chemical processing, where equipment must withstand harsh environments without compromising safety or performance.
The Solution:
To avoid the pitfalls of improper material selection, it’s essential to conduct a comprehensive needs assessment before purchasing. B2B buyers should evaluate the specific environmental conditions their equipment will face, including temperature fluctuations, exposure to corrosive substances, and mechanical stress. Investing in 316 stainless steel, known for its superior corrosion resistance and durability, may have higher upfront costs but will yield long-term savings by reducing maintenance and replacement needs. Collaborating with engineering consultants can also provide insights into the best material choices based on operational requirements, ensuring that buyers make informed decisions that align with their budgetary constraints while optimizing performance.
Scenario 3: Difficulty in Fabrication and Welding of 316 Stainless Steel
The Problem:
Buyers often encounter challenges during the fabrication and welding of 316 stainless steel due to its specific composition, which can complicate these processes. Inadequate welding techniques or equipment can lead to issues like carbide precipitation, resulting in decreased corrosion resistance and structural integrity. This is particularly problematic in industries such as construction and shipbuilding, where the reliability of welded joints is paramount.
The Solution:
To overcome fabrication and welding challenges, buyers should prioritize training and education for their workforce on the specific requirements of working with 316 stainless steel. Implementing best practices, such as preheating the material and using appropriate filler metals, can significantly enhance the quality of welds. Additionally, sourcing 316 stainless steel from suppliers who offer technical support and fabrication services can provide invaluable assistance. Many suppliers have in-house experts who can advise on the best welding techniques and processes to use, ensuring that buyers achieve optimal results. By focusing on proper training and utilizing supplier resources, buyers can enhance their fabrication processes, ensuring strong and durable applications of 316 stainless steel.
Strategic Material Selection Guide for 316 stainless composition
What are the Key Materials in 316 Stainless Composition?
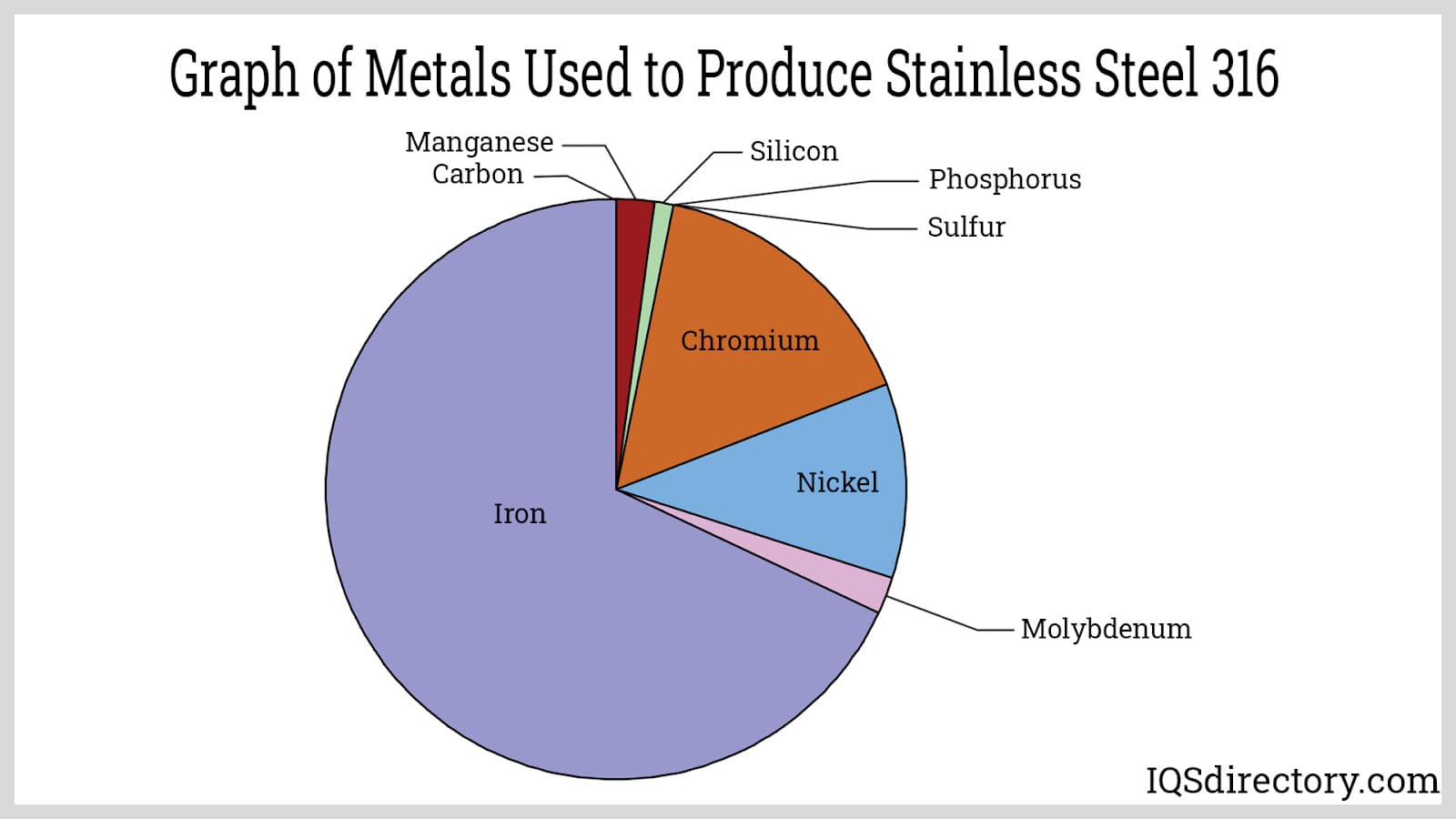
A stock image related to 316 stainless composition.
When selecting materials for applications involving 316 stainless steel, it’s essential to understand the various components that contribute to its properties. The following analysis focuses on the key materials that define 316 stainless composition, their characteristics, and their implications for international B2B buyers.
Nickel (Ni): Enhancing Corrosion Resistance
Key Properties:
Nickel is a crucial alloying element in 316 stainless steel, typically comprising 10-14% of the total composition. It significantly enhances corrosion resistance, particularly in acidic environments and against chlorides. Nickel also contributes to the alloy’s toughness and ductility, making it suitable for applications requiring high strength.
Pros & Cons:
The inclusion of nickel improves the material’s resistance to pitting and crevice corrosion, which is vital for marine and chemical processing applications. However, nickel is relatively expensive, which can increase the overall cost of 316 stainless steel. Additionally, sourcing nickel can be challenging due to supply chain fluctuations.
Impact on Application:
Nickel’s properties make 316 stainless steel ideal for environments exposed to harsh chemicals, such as the pharmaceutical and food processing industries. Its ability to withstand high temperatures also makes it suitable for applications in the oil and gas sector.
Considerations for International Buyers:
Buyers from regions like Africa and the Middle East should ensure compliance with international standards such as ASTM and DIN, particularly in industries like oil and gas where safety is paramount. The fluctuating price of nickel may also affect procurement strategies.
Molybdenum (Mo): Critical for Marine Applications
Key Properties:
Molybdenum, typically present at 2-3% in 316 stainless steel, enhances the alloy’s resistance to localized corrosion, particularly in chloride environments. This property is essential for marine applications, where exposure to saltwater is common.
Pros & Cons:
The addition of molybdenum significantly improves the durability of 316 stainless steel in aggressive environments. However, the cost of molybdenum can be high, impacting the overall expense of the material. The manufacturing complexity may also increase due to the specific processes required to incorporate molybdenum effectively.
Impact on Application:
Molybdenum’s corrosion resistance makes 316 stainless steel an excellent choice for marine equipment, chemical tanks, and other applications exposed to corrosive substances.
Considerations for International Buyers:
B2B buyers should be aware of the specific regulatory standards in their regions, such as those set by the EU for marine applications. Understanding local compliance can prevent costly delays in product deployment.
Carbon (C): Balancing Strength and Ductility
Key Properties:
Carbon content in 316 stainless steel is typically limited to 0.08% to avoid carbide precipitation during welding. This balance is crucial for maintaining the alloy’s mechanical properties.
Pros & Cons:
Lower carbon content enhances weldability, making 316 stainless steel easier to fabricate. However, this can also limit the material’s hardness, which may be a disadvantage in applications requiring high wear resistance.
Impact on Application:
The controlled carbon content is beneficial for applications in the food and pharmaceutical industries, where cleanliness and integrity are critical.
Considerations for International Buyers:
Buyers should ensure that their suppliers adhere to international standards that specify carbon limits in stainless steel, particularly in applications requiring stringent hygiene and safety measures.
Summary Table of Key Materials in 316 Stainless Composition
Material | Typical Use Case for 316 stainless composition | Key Advantage | Key Disadvantage/Limitation | Relative Cost (Low/Med/High) |
---|---|---|---|---|
Nickel (Ni) | Food processing, chemical tanks | Enhances corrosion resistance and toughness | High cost and supply chain challenges | High |
Molybdenum (Mo) | Marine applications, chemical processing | Excellent resistance to localized corrosion | Expensive and increases manufacturing complexity | High |
Carbon (C) | Pharmaceutical equipment, food industry | Improves weldability and fabrication | Limits hardness and wear resistance | Medium |
This strategic material selection guide provides international B2B buyers with a comprehensive overview of the key components in 316 stainless steel, helping them make informed decisions tailored to their specific industry needs.
In-depth Look: Manufacturing Processes and Quality Assurance for 316 stainless composition
What Are the Main Stages in the Manufacturing Process of 316 Stainless Steel?
The manufacturing process of 316 stainless steel involves several crucial stages, ensuring that the final product meets the high standards required for its diverse applications. Understanding these stages is essential for international B2B buyers seeking reliable suppliers.
Material Preparation
The first step in manufacturing 316 stainless steel is material preparation, which includes selecting high-quality raw materials. The primary alloying elements, chromium, nickel, and molybdenum, are sourced from reputable suppliers to ensure consistency and quality. The materials undergo rigorous testing for chemical composition and purity, often adhering to international standards like ASTM and ISO.
Forming Techniques
Once the materials are prepared, the next stage is forming, which can involve various techniques such as:
-
Hot and Cold Rolling: These methods are used to shape the metal into sheets, plates, or coils. Hot rolling involves shaping the metal at high temperatures, while cold rolling is done at room temperature, providing better surface finish and dimensional accuracy.
-
Forging: This process is utilized to create complex shapes and enhance mechanical properties. Forged products often display improved strength and durability, making them suitable for high-stress applications.
-
Welding: Due to its lower carbon content, 316 stainless steel can be easily welded. Techniques such as TIG (Tungsten Inert Gas) and MIG (Metal Inert Gas) welding are commonly employed, allowing for strong joints that maintain the alloy’s integrity.
Assembly and Finishing
After forming, the components are assembled. This may involve additional machining to achieve precise dimensions and tolerances. The finishing stage includes processes like polishing and passivation, which enhance corrosion resistance and aesthetic appeal. Passivation involves treating the surface to remove free iron and other contaminants, ensuring the longevity of the material in challenging environments.
What Quality Assurance Measures Are Essential for 316 Stainless Steel?
Quality assurance (QA) is critical in the production of 316 stainless steel, particularly given its applications in industries such as aerospace, marine, and pharmaceuticals. B2B buyers must understand the QA measures employed by manufacturers to ensure product reliability.
Relevant International Standards for Quality Assurance
Manufacturers of 316 stainless steel should comply with various international standards, including:
-
ISO 9001: This standard focuses on quality management systems and ensures that manufacturers consistently provide products that meet customer and regulatory requirements.
-
CE Marking: For products sold in Europe, CE marking indicates compliance with European health, safety, and environmental protection standards.
-
API Standards: For applications in the petroleum and natural gas industries, adherence to American Petroleum Institute (API) standards is critical.
Key Quality Control Checkpoints
Quality control (QC) is implemented at several checkpoints throughout the manufacturing process:
-
Incoming Quality Control (IQC): This involves inspecting raw materials upon receipt to verify compliance with specified standards. Tests may include chemical analysis and physical inspection.
-
In-Process Quality Control (IPQC): During manufacturing, various checks are performed to ensure that processes remain within specified parameters. This includes monitoring temperature and pressure during forming processes.
-
Final Quality Control (FQC): Before shipment, finished products undergo thorough inspections, including dimensional checks, surface quality assessment, and corrosion resistance tests.
What Testing Methods Are Commonly Used in Quality Assurance?
B2B buyers should be familiar with the testing methods that manufacturers utilize to ensure the quality of 316 stainless steel:
-
Chemical Analysis: This is performed using techniques such as spectroscopy to confirm the alloy’s composition matches specified standards.
-
Mechanical Testing: Tensile strength, yield strength, and elongation tests are conducted to determine the material’s mechanical properties.
-
Corrosion Testing: Salt spray tests and immersion tests evaluate the alloy’s resistance to various corrosive environments, essential for applications in marine and chemical processing.
How Can B2B Buyers Verify Supplier Quality Control?
International B2B buyers must take proactive measures to verify the quality control systems of their suppliers:
-
Audits: Conducting on-site audits of potential suppliers allows buyers to assess manufacturing processes, quality control measures, and overall compliance with international standards.
-
Quality Reports: Requesting detailed quality reports can provide insights into a supplier’s QC practices. These reports should outline testing methods, results, and any corrective actions taken in case of deviations.
-
Third-Party Inspections: Engaging third-party inspection agencies can provide an unbiased assessment of the supplier’s manufacturing and quality assurance processes, ensuring compliance with industry standards.
What Are the Nuances of Quality Control for International B2B Buyers?
For B2B buyers from regions such as Africa, South America, the Middle East, and Europe, understanding the nuances of quality control in international trade is vital:
-
Regulatory Compliance: Buyers must be aware of the specific regulatory requirements in their regions, which may differ significantly from those in the supplier’s country.
-
Cultural Differences: Communication and cultural differences can impact quality expectations. Establishing clear specifications and standards from the outset is crucial.
-
Logistics and Supply Chain Considerations: Delays in shipping or customs can affect product quality. Implementing thorough inspection protocols before shipment can mitigate risks associated with transportation.
By understanding the manufacturing processes and quality assurance measures for 316 stainless steel, international B2B buyers can make informed decisions when sourcing materials. Prioritizing suppliers with robust QA systems not only ensures product quality but also enhances the overall reliability of supply chains.
Practical Sourcing Guide: A Step-by-Step Checklist for ‘316 stainless composition’
The following practical sourcing guide provides essential steps for B2B buyers aiming to procure 316 stainless steel composition. This checklist is designed to ensure that your sourcing process is thorough, efficient, and aligned with your specific needs, especially for buyers from Africa, South America, the Middle East, and Europe.
Step 1: Define Your Technical Specifications
Before reaching out to suppliers, clearly define the technical specifications of the 316 stainless steel you require. This includes understanding the desired mechanical properties, chemical composition, and applicable standards (e.g., ASTM, AMS).
– What to Consider: Ensure you specify the required corrosion resistance, especially if the material will be used in harsh environments.
Step 2: Research Potential Suppliers
Conduct comprehensive research to identify potential suppliers who specialize in 316 stainless steel. Look for manufacturers with a proven track record in your industry, as well as those who comply with international standards.
– Where to Look: Utilize online directories, trade shows, and industry publications to find reputable suppliers that align with your sourcing needs.
Step 3: Evaluate Supplier Certifications
Verify that your chosen suppliers hold relevant certifications that demonstrate their compliance with quality standards. Common certifications include ISO 9001, ISO 14001, and specific product certifications like ASTM A240.
– Why It Matters: Certifications assure you of the supplier’s commitment to quality control and environmental management, which is critical for long-term partnerships.
Step 4: Request Samples for Testing
Once you narrow down your options, request samples of the 316 stainless steel for testing. This step is crucial for assessing the material’s quality and suitability for your applications.
– Testing Parameters: Evaluate samples for mechanical properties, corrosion resistance, and compliance with your specified standards.
Step 5: Compare Pricing and Payment Terms
Collect quotes from multiple suppliers and compare their pricing structures. Pay attention not only to the base price but also to payment terms, shipping costs, and potential bulk discounts.
– Value Over Cost: While price is important, also consider the total cost of ownership, which includes quality, reliability, and supplier service.
Step 6: Assess Lead Times and Delivery Options
Inquire about lead times for production and delivery from your shortlisted suppliers. Understanding their timelines is essential for planning your project schedules.
– Flexibility: Look for suppliers that can accommodate urgent orders or provide alternatives in case of delays.
Step 7: Establish Communication and Support Channels
Finally, establish clear communication channels with your selected supplier. Good communication is key to resolving issues quickly and efficiently.
– Support Availability: Ensure that the supplier provides timely support and has a dedicated team to assist with your inquiries and potential after-sales needs.
By following this step-by-step checklist, you can enhance your sourcing strategy for 316 stainless steel composition, ensuring that your procurement process is streamlined and effective.
Comprehensive Cost and Pricing Analysis for 316 stainless composition Sourcing
What Are the Key Cost Components in Sourcing 316 Stainless Composition?
When sourcing 316 stainless steel, international B2B buyers must consider a variety of cost components that contribute to the overall price. The primary elements include:
-
Materials: The cost of raw materials (chromium, nickel, molybdenum) fluctuates based on global market conditions. Prices can vary significantly based on purity and sourcing location.
-
Labor: Labor costs depend on the region and the complexity of manufacturing processes. Countries with lower labor costs may offer competitive pricing, but this can affect quality and delivery times.
-
Manufacturing Overhead: This includes expenses related to factory maintenance, utilities, and administrative costs. Efficient production facilities tend to have lower overhead costs, which can be passed on to buyers.
-
Tooling: Specialized tools may be required for custom orders, impacting the initial investment and, subsequently, the pricing structure.
-
Quality Control (QC): Ensuring product quality involves additional costs for testing and certification, particularly for industries like food processing and pharmaceuticals where compliance is critical.
-
Logistics: Transportation and shipping costs are influenced by the distance from the supplier, shipping method, and import duties. Incoterms can significantly affect these logistics costs.
-
Margin: Suppliers typically add a profit margin that can vary based on market competition and perceived value.
How Do Price Influencers Affect the Cost of 316 Stainless Steel?
Several factors can influence the pricing of 316 stainless steel, including:
-
Volume/MOQ: Larger orders often lead to discounts due to economies of scale. Establishing a minimum order quantity (MOQ) can help negotiate better prices.
-
Specifications and Customization: Tailored solutions often incur additional costs. Standardized products may be less expensive compared to customized alternatives.
-
Material Quality and Certifications: Higher quality materials and certifications (like ASTM or ISO standards) command a premium price. Buyers should ensure that the supplier meets necessary standards to avoid future costs related to compliance.
-
Supplier Factors: The supplier’s reputation, location, and reliability can impact pricing. Established suppliers with a history of quality may charge more due to their proven track record.
-
Incoterms: Understanding the implications of Incoterms is crucial. They dictate the responsibilities of buyers and sellers regarding shipping, risk, and costs, affecting the total landed cost of products.
What Tips Can Help International B2B Buyers Optimize Costs?
For international buyers, particularly from Africa, South America, the Middle East, and Europe, optimizing costs in sourcing 316 stainless steel is vital. Here are several actionable tips:
-
Negotiate Terms: Engage in negotiations not just on price but also on payment terms, delivery schedules, and after-sales service. Building a strong relationship with suppliers can lead to better terms over time.
-
Focus on Total Cost of Ownership (TCO): Assess all costs associated with the product over its lifespan, including maintenance, downtime, and disposal costs. A lower initial price may lead to higher TCO if quality is compromised.
-
Consider Local Suppliers: Sourcing from regional suppliers can reduce logistics costs and lead times. Local suppliers may also better understand regional regulations and requirements.
-
Stay Informed on Market Trends: Keep abreast of global market conditions affecting raw material prices. Timing your purchase during favorable market conditions can lead to significant savings.
-
Evaluate Alternative Materials: In some cases, exploring similar alloys or grades may provide cost-effective solutions without compromising quality.
Conclusion
Understanding the comprehensive cost structure and pricing dynamics of 316 stainless steel is essential for international B2B buyers. By evaluating cost components, recognizing price influencers, and implementing strategic sourcing tips, buyers can enhance their procurement process, ensuring both cost-efficiency and product quality. Always remember to seek multiple quotes and conduct thorough supplier evaluations before finalizing agreements. Prices are subject to change and should be confirmed with suppliers to ensure accuracy.
Alternatives Analysis: Comparing 316 stainless composition With Other Solutions
When considering material options for various industrial applications, B2B buyers often evaluate alternatives to 316 stainless steel. This analysis aims to provide a detailed comparison of 316 stainless composition against viable alternatives, enabling informed decision-making for businesses in Africa, South America, the Middle East, and Europe.
Comparison Aspect | 316 Stainless Composition | Alternative 1: 304 Stainless Steel | Alternative 2: Duplex Stainless Steel |
---|---|---|---|
Performance | Excellent corrosion resistance, especially in chloride environments. | Good corrosion resistance, but inferior to 316 in marine settings. | Superior strength and corrosion resistance, particularly in acidic environments. |
Cost | Higher cost due to molybdenum content. | More affordable and widely available. | Generally higher cost due to complex metallurgy. |
Ease of Implementation | Easy to fabricate and weld. | Very easy to work with; widely used. | Requires specialized techniques for welding and fabrication. |
Maintenance | Low maintenance due to durability and corrosion resistance. | Moderate maintenance; may require protective coatings in harsh environments. | Low maintenance but may require monitoring for corrosion in specific conditions. |
Best Use Case | Ideal for marine, chemical, and food processing industries. | Suitable for kitchenware, architectural applications, and general-purpose use. | Best for oil and gas applications, pulp and paper industries, and environments requiring high strength. |
What Are the Advantages and Disadvantages of 304 Stainless Steel as an Alternative?
304 stainless steel is often considered a more cost-effective alternative to 316 due to its lower alloying elements. It possesses good corrosion resistance but is significantly less resistant to chlorides, making it less suitable for marine environments. It is widely used in applications such as kitchen equipment and architectural structures. Its ease of fabrication and lower cost make it a popular choice, but it may require additional protective measures in more corrosive settings.
How Does Duplex Stainless Steel Compare?
Duplex stainless steel, which combines austenitic and ferritic structures, offers enhanced strength and corrosion resistance compared to both 316 and 304 stainless steels. This makes it particularly effective in applications exposed to harsh environments, such as oil and gas extraction. However, it typically comes at a higher cost and requires specialized fabrication techniques. While its superior properties can justify the investment, buyers must consider the added complexity in working with this material.
Conclusion: How Should B2B Buyers Decide Between These Materials?
When selecting the right stainless steel for specific applications, B2B buyers should assess their operational requirements, including environmental conditions, budget constraints, and the desired longevity of the materials. If the application involves exposure to corrosive environments, 316 stainless steel may be worth the investment despite its higher cost. Conversely, for less demanding applications, 304 stainless steel may suffice, providing a more economical solution. Duplex stainless steel, while more expensive, is ideal for high-strength requirements and challenging environments. By carefully evaluating the unique properties and costs of each option, buyers can make informed choices that align with their operational goals and budget.
Essential Technical Properties and Trade Terminology for 316 stainless composition
What Are the Key Technical Properties of 316 Stainless Steel Composition?
Understanding the technical properties of 316 stainless steel is crucial for B2B buyers, especially those involved in industries such as chemical processing, marine applications, and food manufacturing. Here are some essential specifications that define its performance and suitability for various applications:
-
Material Grade
316 stainless steel is classified as an austenitic stainless steel, distinguished by its significant chromium, nickel, and molybdenum content. The presence of molybdenum (2-3%) enhances its resistance to pitting and crevice corrosion, making it ideal for harsh environments. Buyers should prioritize this grade for applications that require superior corrosion resistance. -
Tensile Strength
The tensile strength of 316 stainless steel is approximately 515 MPa (75 ksi). This property indicates the maximum stress the material can withstand while being stretched or pulled before failing. For B2B buyers, high tensile strength is essential for ensuring structural integrity in demanding applications, such as in construction or machinery. -
Yield Strength
With a yield strength of around 205 MPa (30 ksi), 316 stainless steel can endure significant stress without permanent deformation. This property is particularly important for industries that require materials to maintain their shape under load, such as in manufacturing heavy machinery or structural components. -
Corrosion Resistance
One of the standout features of 316 stainless steel is its exceptional resistance to corrosion, particularly in chloride-rich environments. This property is vital for B2B buyers in sectors like marine, chemical, and food processing, where equipment is often exposed to corrosive substances. The ability to resist corrosion not only extends the lifespan of products but also reduces maintenance costs. -
Weldability
Due to its lower carbon content compared to other stainless steel grades, 316 is highly weldable. This characteristic is crucial for manufacturers who need to fabricate complex structures or components. Ensuring that the material can be easily welded can significantly reduce production time and costs. -
Density
The density of 316 stainless steel is approximately 8.03 g/cm³ (0.290 lbs/in³). Understanding the density is important for B2B buyers when calculating shipping costs and handling requirements, especially in large-scale projects where weight can significantly impact logistics.
What Are Common Trade Terms Used in the Stainless Steel Industry?
Navigating the trade terminology in the stainless steel industry can enhance communication and facilitate smoother transactions. Here are some essential terms that B2B buyers should be familiar with:
-
OEM (Original Equipment Manufacturer)
This term refers to companies that produce parts or equipment that may be marketed by another manufacturer. Understanding OEM relationships can help buyers identify reliable suppliers for their specific needs. -
MOQ (Minimum Order Quantity)
MOQ refers to the smallest quantity of a product that a supplier is willing to sell. Buyers need to be aware of MOQ requirements to manage inventory effectively and avoid overcommitting to large orders that may not be necessary. -
RFQ (Request for Quotation)
An RFQ is a document sent to suppliers requesting pricing and terms for specific products or services. It is a crucial step in the procurement process, allowing buyers to compare offers and negotiate better deals. -
Incoterms (International Commercial Terms)
These are a series of pre-defined commercial terms published by the International Chamber of Commerce (ICC) that are widely used in international commercial transactions. Understanding Incoterms helps buyers clarify responsibilities regarding shipping, insurance, and tariffs, ensuring smooth logistics operations. -
Certification Standards
Various certification standards, such as ASTM, ISO, and EN, are essential for ensuring that materials meet specific quality and safety criteria. Buyers should verify that their suppliers comply with these standards to ensure product reliability.
By grasping these technical properties and trade terms, B2B buyers can make more informed purchasing decisions when sourcing 316 stainless steel for their projects. This knowledge not only aids in selecting the right materials but also enhances negotiation strategies and supplier relationships.
Navigating Market Dynamics and Sourcing Trends in the 316 stainless composition Sector
What Are the Key Market Drivers for 316 Stainless Composition?
The global demand for 316 stainless steel is primarily driven by its exceptional corrosion resistance and durability, making it the material of choice for various industries, including marine, chemical, food processing, and pharmaceuticals. As urbanization accelerates in regions like Africa and South America, there is a growing need for infrastructure that can withstand harsh environmental conditions. Moreover, the increasing focus on sustainability in manufacturing processes is pushing companies to adopt materials like 316 stainless steel, which not only enhance product longevity but also minimize maintenance costs.
Emerging B2B technologies are also reshaping the sourcing landscape. Digital platforms for procurement are gaining traction, allowing international buyers to connect with suppliers more efficiently. Technologies like blockchain are enhancing transparency in supply chains, ensuring that material origins and compositions are accurately tracked. Additionally, advanced analytics are being utilized to forecast demand and optimize inventory levels, allowing buyers from Europe and the Middle East to manage their sourcing strategies effectively.
How Is Sustainability Shaping the Sourcing of 316 Stainless Steel?
Sustainability has become a paramount concern for B2B buyers, particularly in Europe and the Middle East, where regulations are increasingly stringent. The environmental impact of sourcing materials is under scrutiny, making it crucial for companies to consider the lifecycle of their materials. Ethical sourcing practices are not only essential for compliance but also for maintaining a positive brand image.
Buyers should prioritize suppliers who demonstrate a commitment to sustainable practices, such as using recycled materials or engaging in responsible mining. Certifications such as ISO 14001 (Environmental Management) and LEED (Leadership in Energy and Environmental Design) can serve as indicators of a supplier’s dedication to sustainability. By opting for “green” materials and certified suppliers, companies can significantly reduce their environmental footprint while ensuring compliance with global standards.
What Is the Historical Context of 316 Stainless Steel?
The development of 316 stainless steel can be traced back to the early 20th century, when the need for more resilient materials in demanding environments became apparent. Originally developed for use in the marine industry, its unique composition—featuring molybdenum—enhanced its resistance to chloride-induced corrosion. Over the decades, 316 stainless steel has evolved and found applications in diverse sectors, including food processing, pharmaceuticals, and construction.
As industries continue to innovate and expand, the historical significance of 316 stainless steel serves as a reminder of the material’s adaptability and importance in modern manufacturing. Understanding its evolution can provide valuable insights for international B2B buyers looking to leverage its properties for their specific applications.
Frequently Asked Questions (FAQs) for B2B Buyers of 316 stainless composition
-
How do I solve the issue of corrosion in marine environments when using 316 stainless steel?
To mitigate corrosion in marine environments, ensure you select high-quality 316 stainless steel, as it is specifically designed to resist chloride-induced corrosion. Additionally, consider applying protective coatings or using cathodic protection systems to enhance durability. Regular maintenance and inspections can also help identify early signs of corrosion, allowing for timely interventions. -
What is the best type of 316 stainless steel for food processing applications?
For food processing, opt for 316L stainless steel, which features lower carbon content, reducing the risk of carbide precipitation during welding. This grade is ideal for sanitary applications, providing superior corrosion resistance and ease of cleaning. It’s essential to ensure that the material meets FDA and other regulatory standards for food safety. -
What are the key factors to consider when sourcing 316 stainless steel suppliers?
When sourcing suppliers for 316 stainless steel, evaluate their industry certifications, such as ISO 9001, which indicates a commitment to quality management. Look for suppliers with a proven track record in your industry, competitive pricing, and reliable delivery schedules. Request samples to assess material quality and ensure they can meet your specific technical requirements. -
What customization options are available for 316 stainless steel products?
Many suppliers offer customization options, including specific dimensions, finishes, and surface treatments for 316 stainless steel products. Discuss your requirements with potential suppliers to understand their capabilities. Some may provide additional services such as machining, welding, or fabrication, allowing for tailored solutions that fit your application needs. -
What is the minimum order quantity (MOQ) for 316 stainless steel, and how does it affect pricing?
The MOQ for 316 stainless steel can vary significantly between suppliers, typically ranging from a few kilograms to several tons. A higher MOQ may lead to lower per-unit costs due to economies of scale. However, it’s crucial to assess your project requirements and budget before committing to large orders. Negotiate terms to find a balance that meets your needs without excessive inventory. -
What payment terms should I expect when purchasing 316 stainless steel internationally?
Payment terms can vary by supplier and region. Common terms include upfront payments, net 30 or net 60 days, and letters of credit for larger transactions. Be prepared to negotiate terms that align with your cash flow needs. It’s advisable to conduct due diligence on the supplier’s financial stability and reputation to minimize risks associated with international trade. -
How can I ensure quality assurance for my 316 stainless steel orders?
To ensure quality assurance, request certifications that verify the chemical composition and mechanical properties of the 316 stainless steel. Suppliers should provide mill test reports (MTRs) or certificates of compliance. Consider third-party inspections, especially for large or critical orders, to ensure the materials meet your specifications and industry standards. -
What logistics considerations should I keep in mind when importing 316 stainless steel?
When importing 316 stainless steel, consider shipping methods, lead times, and customs regulations in your region. Engage with logistics providers experienced in handling industrial materials to ensure timely delivery. Familiarize yourself with import duties and tariffs that may apply, and ensure proper documentation is prepared to avoid delays at customs.
Important Disclaimer & Terms of Use
⚠️ Important Disclaimer
The information provided in this guide, including content regarding manufacturers, technical specifications, and market analysis, is for informational and educational purposes only. It does not constitute professional procurement advice, financial advice, or legal advice.
While we have made every effort to ensure the accuracy and timeliness of the information, we are not responsible for any errors, omissions, or outdated information. Market conditions, company details, and technical standards are subject to change.
B2B buyers must conduct their own independent and thorough due diligence before making any purchasing decisions. This includes contacting suppliers directly, verifying certifications, requesting samples, and seeking professional consultation. The risk of relying on any information in this guide is borne solely by the reader.
Strategic Sourcing Conclusion and Outlook for 316 stainless composition
In conclusion, the strategic sourcing of 316 stainless steel presents significant advantages for international B2B buyers, especially those in Africa, South America, the Middle East, and Europe. This alloy’s superior corrosion resistance, particularly against chlorides, makes it a vital choice for industries ranging from marine applications to pharmaceuticals and food processing. Understanding the composition—12% nickel, 17% chromium, and 2.5% molybdenum—enables buyers to select materials that meet their specific operational requirements while ensuring durability and longevity.
Why is Strategic Sourcing Essential for 316 Stainless Steel?
Strategic sourcing not only enhances supply chain efficiency but also reduces costs and mitigates risks associated with material quality and availability. Buyers are encouraged to develop robust relationships with suppliers who understand the nuances of 316 stainless steel and can provide insights on market trends and pricing fluctuations.
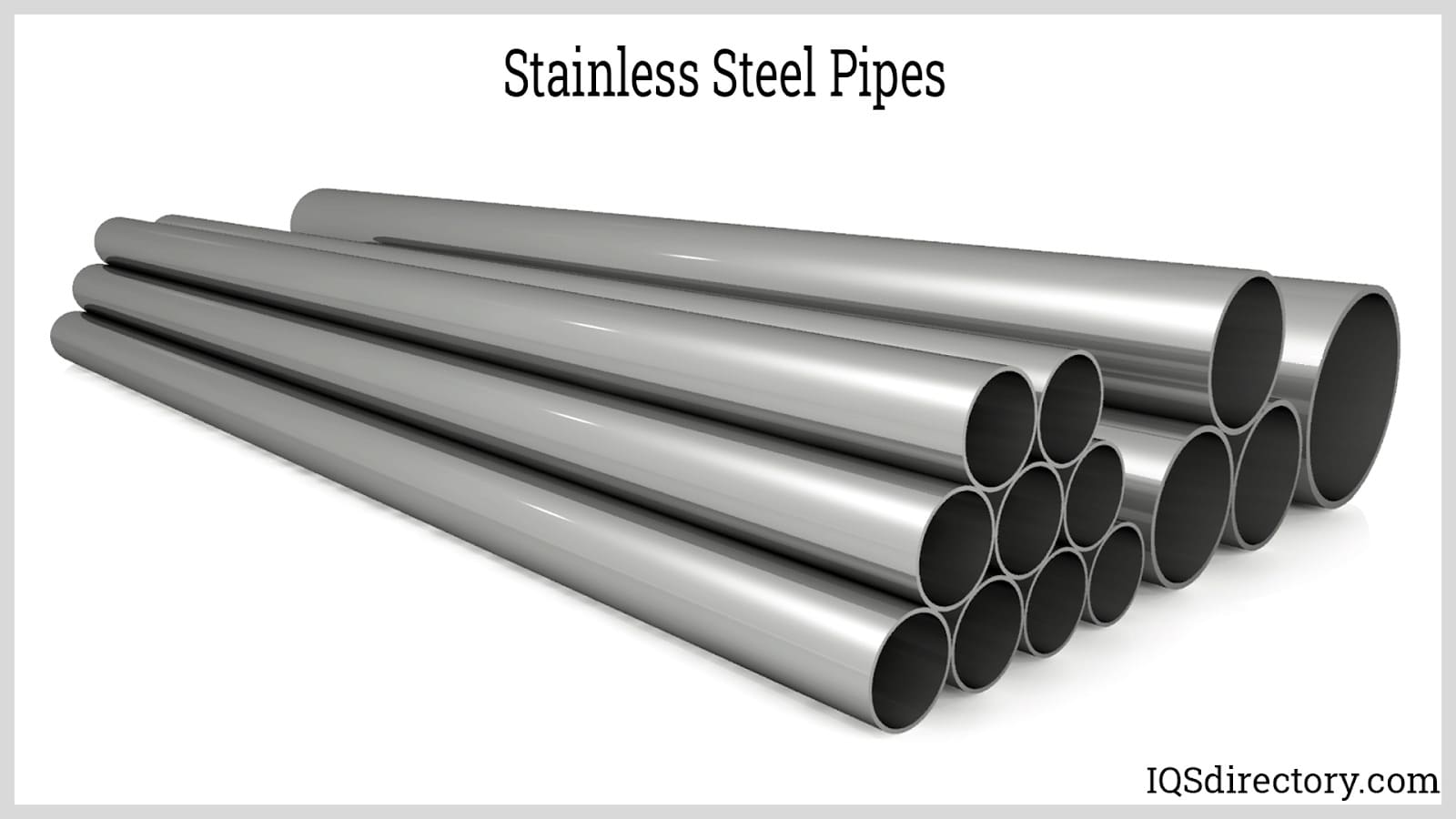
A stock image related to 316 stainless composition.
What Does the Future Hold for 316 Stainless Steel Buyers?
Looking ahead, the demand for 316 stainless steel is expected to grow as industries seek materials that can withstand harsher environments and comply with stringent regulatory standards. B2B buyers should proactively engage with suppliers to secure favorable terms and leverage insights into emerging technologies and applications. By staying informed and adaptable, businesses can capitalize on the opportunities presented by this versatile alloy.