Unlock Savings: The Complete Door Latch Buying Guide (2025)
Introduction: Navigating the Global Market for door latch
In today’s global market, sourcing high-quality door latches poses a significant challenge for international B2B buyers, especially in dynamic regions like Africa, South America, the Middle East, and Europe. With a myriad of options available, from mortise and surface-mounted latches to specialty designs for unique applications, the decision-making process can be overwhelming. This guide aims to simplify your purchasing journey by providing a comprehensive overview of door latch types, their various applications, and essential supplier vetting criteria.
You will discover insights into the latest trends in door latch technology, including security features and material selections that cater to diverse market needs. Moreover, we will delve into cost considerations, helping you evaluate pricing structures and identify potential cost-saving opportunities without compromising quality. By the end of this guide, you will be equipped with the knowledge to make informed purchasing decisions that align with your business requirements and regional standards.
Whether you’re sourcing for commercial projects in Turkey, residential developments in Germany, or industrial applications in South Africa, this guide empowers you to navigate the complexities of the door latch market with confidence. Your ability to identify reliable suppliers and understand the nuances of product specifications will enhance your procurement strategy and ultimately support your business’s growth in the competitive global landscape.
Understanding door latch Types and Variations
Type Name | Key Distinguishing Features | Primary B2B Applications | Brief Pros & Cons for Buyers |
---|---|---|---|
Deadbolt Latch | High security, requires a key, often heavy-duty | Commercial buildings, residential | Pros: Enhanced security; Cons: Higher cost, complex installation. |
Roller Latch | Smooth operation, retracts when the door closes | Interior doors, cabinets | Pros: Easy to use; Cons: Less secure than deadbolts. |
Surface-Mounted Latch | Mounted on the surface of the door, visible | Screen doors, storm doors | Pros: Easy installation; Cons: Aesthetically less pleasing. |
Cabin Hook Latch | Simple hook mechanism, often decorative | Barn doors, outdoor settings | Pros: Versatile and stylish; Cons: Limited security. |
Security Chain Latch | Chain mechanism for added security | Gates, doors requiring extra security | Pros: Affordable and effective; Cons: Less convenient for frequent use. |
What Are the Characteristics of a Deadbolt Latch?
Deadbolt latches are renowned for their high-security features, making them a preferred choice for commercial and residential properties. They require a key or a thumb turn to operate, providing an extra layer of protection against unauthorized access. When considering a deadbolt latch, buyers should focus on the ANSI grade, which indicates the quality and durability of the latch. Additionally, installation complexity and cost can vary significantly, so it’s essential to evaluate these aspects based on the specific security needs of the property.
How Does a Roller Latch Function?
Roller latches are designed for smooth operation, making them ideal for interior doors and cabinetry. The latch retracts automatically when the door is closed, ensuring a snug fit without the need for manual operation. B2B buyers should consider the material and design of roller latches to ensure compatibility with their door types. While they offer ease of use and installation, it’s important to note that they may not provide the same level of security as deadbolt latches, making them better suited for low-security applications.
Why Choose a Surface-Mounted Latch?
Surface-mounted latches are installed directly onto the door’s surface, making them visible and easy to install. These latches are commonly used on screen and storm doors where aesthetics may be less of a concern. Buyers should evaluate the latch’s durability and resistance to weather conditions, especially in outdoor applications. While surface-mounted latches are convenient and cost-effective, their visibility may detract from the overall appearance of the door.
What Are the Benefits of a Cabin Hook Latch?
Cabin hook latches utilize a simple hook mechanism, often adding a decorative touch to barn doors and outdoor settings. They are easy to install and can be used in various applications, making them a versatile choice for buyers. However, it’s important to recognize that cabin hooks do not provide significant security, so they are best used in situations where security is not the primary concern. Buyers should consider the latch’s material and finish to ensure it complements the door design.
How Do Security Chain Latches Work?
Security chain latches feature a chain mechanism that provides an additional layer of security, commonly used on gates and doors requiring extra protection. They are relatively affordable and easy to install, appealing to budget-conscious buyers. However, the convenience factor may be a drawback, as they can be cumbersome for frequent access. Buyers should assess the chain’s strength and the latch’s overall durability to ensure it meets their security requirements.
Key Industrial Applications of door latch
Industry/Sector | Specific Application of Door Latch | Value/Benefit for the Business | Key Sourcing Considerations for this Application |
---|---|---|---|
Construction | Use in residential and commercial doors | Enhances security and functionality of entry points | Compliance with local building codes and standards |
Hospitality | Application in hotel room doors | Provides guest privacy and security | Durability and ease of use for both guests and staff |
Manufacturing | Integration in factory access points | Controls access to sensitive areas, ensuring safety | Must meet industrial safety regulations and standards |
Retail | Installation in store entrance and exit doors | Improves customer flow and security | Aesthetic appeal and functionality for high-traffic areas |
Transportation | Use in shipping containers and vehicle doors | Secures cargo and enhances safety during transit | Weather resistance and tamper-proof features are essential |
How is Door Latch Used in the Construction Industry?
In the construction sector, door latches play a crucial role in both residential and commercial buildings. They are essential for securing entry points, ensuring that doors can be easily locked and unlocked while maintaining safety and accessibility. International B2B buyers should consider local building codes and standards, as regulations may vary significantly by region, especially in Africa and South America. Additionally, the choice of materials can impact durability and compliance with safety requirements.
What are the Applications of Door Latches in the Hospitality Sector?
In the hospitality industry, door latches are primarily used in hotel room doors to provide guests with privacy and security. These latches must be reliable and easy to operate, as they directly affect the guest experience. For B2B buyers in Europe, particularly in Germany and Turkey, sourcing high-quality latches that meet durability standards is essential. Furthermore, aesthetic appeal can enhance the overall look of hotel interiors, making it a key consideration during the procurement process.
How Do Door Latches Function in Manufacturing Facilities?
Manufacturing facilities often require specialized door latches to control access to sensitive areas, such as production lines or storage rooms. These latches help maintain safety by restricting entry to authorized personnel only. B2B buyers in this sector must ensure that the latches comply with industrial safety regulations, which can differ by country. Materials that withstand wear and tear, as well as environmental conditions, are critical for long-term functionality.
Why are Door Latches Important in Retail Environments?
In retail settings, door latches are vital for both entrance and exit doors, facilitating customer flow while enhancing security. Effective latching systems can deter theft and unauthorized access, which is crucial for maintaining a secure shopping environment. For buyers in South America and the Middle East, it’s important to consider the aesthetic design of latches, as they contribute to the overall customer experience. Additionally, the functionality and ease of use are paramount, particularly in high-traffic areas.
How are Door Latches Utilized in Transportation?
In the transportation sector, door latches are essential for securing shipping containers and vehicle doors. They ensure that cargo remains safe during transit, which is crucial for logistics companies operating internationally. Buyers should prioritize latches that offer weather resistance and tamper-proof features, especially when dealing with long-distance transportation across varying climates. Understanding the specific requirements for different transport modes can help in selecting the most suitable latching systems.
3 Common User Pain Points for ‘door latch’ & Their Solutions
Scenario 1: Difficulty in Sourcing Quality Door Latches for Diverse Applications
The Problem: International B2B buyers often struggle to find high-quality door latches that meet specific requirements for various applications. For example, a company in South America may need latches that withstand humid conditions for outdoor installations, while a buyer in Europe might be looking for latches that comply with strict safety regulations. This challenge is compounded by the lack of local suppliers who can provide the necessary variety and quality, leading to potential delays and increased costs.
The Solution: To effectively source quality door latches, buyers should prioritize working with established manufacturers who offer a wide range of products tailored to specific environmental conditions and regulatory standards. Conduct thorough market research to identify suppliers that specialize in the type of latches needed—be it for residential, commercial, or industrial use. Utilize platforms that showcase supplier certifications and product specifications. When reaching out to suppliers, clearly communicate your unique requirements and inquire about their experience with similar projects. This proactive approach can streamline procurement and ensure that you receive latches that are reliable and compliant with local standards.
Scenario 2: Incompatibility with Existing Door Hardware
The Problem: Another common pain point arises when new door latches are incompatible with existing door hardware, leading to costly modifications or replacements. This issue can occur particularly in regions with older infrastructure, such as in parts of Africa or the Middle East, where door dimensions and hardware specifications may differ significantly from modern standards.
The Solution: To mitigate compatibility issues, it is crucial to conduct a comprehensive audit of the existing door hardware before making any purchases. Measure door thickness, latch sizes, and the type of locking mechanism currently in use. When selecting new latches, opt for adjustable or universal models that can be adapted to various door types. Communicate with suppliers to understand the compatibility of their products with older systems. Additionally, consider working with local contractors who can assist in the installation process, ensuring that the new latches fit seamlessly with existing hardware without requiring extensive modifications.
Scenario 3: Security Concerns with Standard Latches
The Problem: In an increasingly security-conscious environment, many B2B buyers are apprehensive about the effectiveness of standard door latches. Buyers, especially those in commercial sectors across Europe and the Middle East, often find themselves questioning whether their current latches provide adequate protection against unauthorized access.
The Solution: To address security concerns, it is essential to invest in high-security door latches that meet industry standards for strength and durability. Look for products that feature tamper-resistant designs, reinforced materials, and advanced locking mechanisms such as deadbolts or smart technology options. When sourcing these latches, consult with security experts who can provide insights into the latest trends in door security solutions. Additionally, consider conducting a risk assessment of your facilities to identify vulnerable areas where enhanced security measures may be necessary. By investing in specialized latches, buyers can significantly improve their security posture and reduce the risk of break-ins or unauthorized access.
Strategic Material Selection Guide for door latch
What Are the Key Properties of Common Materials Used in Door Latches?
When selecting door latches for international markets, understanding the properties of various materials is crucial. Here, we analyze four common materials: brass, stainless steel, zinc alloy, and plastic. Each material has unique characteristics that can influence product performance, durability, and suitability for specific applications.
How Does Brass Perform in Door Latch Applications?
Key Properties: Brass is known for its excellent corrosion resistance and mechanical strength. It can withstand moderate temperature variations, making it suitable for various climates. Additionally, brass has good machinability, allowing for precise manufacturing.
Pros & Cons: The primary advantage of brass is its durability and aesthetic appeal, often featuring a polished finish that enhances visual appeal. However, it can be more expensive than other materials, which might be a concern for budget-sensitive projects. Brass also requires regular maintenance to prevent tarnishing.
Impact on Application: Brass is particularly suitable for residential applications, where aesthetic considerations are paramount. Its compatibility with various environments makes it a versatile choice.
Considerations for International Buyers: Buyers from regions like Europe and the Middle East should ensure that brass latches comply with local standards such as DIN and EN. In Africa and South America, the availability of brass may vary, affecting procurement strategies.
What Are the Benefits of Stainless Steel in Door Latch Manufacturing?
Key Properties: Stainless steel is renowned for its high corrosion resistance and strength, even in harsh environments. It can withstand high temperatures and pressures, making it ideal for both residential and commercial applications.
Pros & Cons: The main advantage of stainless steel is its longevity and low maintenance requirements. However, it is generally more expensive than brass and zinc alloy. Its manufacturing process can also be more complex, potentially leading to higher production costs.
Impact on Application: Stainless steel latches are well-suited for commercial applications where durability is critical. They are often used in environments exposed to moisture, such as coastal areas.
Considerations for International Buyers: Compliance with ASTM standards is crucial for buyers in North America, while European buyers should consider EN standards. The demand for stainless steel is growing in Africa and South America due to its durability in humid conditions.
Why Choose Zinc Alloy for Door Latches?
Key Properties: Zinc alloy offers a good balance of strength, corrosion resistance, and cost-effectiveness. It can be cast into complex shapes, which allows for innovative designs.
Pros & Cons: Zinc alloy latches are generally less expensive than brass and stainless steel, making them an attractive option for budget-conscious buyers. However, they may not be as durable as brass or stainless steel, particularly in high-stress applications.
Impact on Application: These latches are ideal for residential and light commercial applications where cost is a primary concern. They are suitable for indoor use but may not perform well in extreme outdoor conditions.
Considerations for International Buyers: Buyers should check for compliance with local standards, as zinc alloy may not be as widely accepted in certain markets compared to brass or stainless steel.
How Does Plastic Compare as a Material for Door Latches?
Key Properties: Plastic latches are lightweight and resistant to corrosion, making them suitable for various environments. They can be molded into intricate designs, providing flexibility in aesthetics.
Pros & Cons: The primary advantage of plastic is its low cost and lightweight nature. However, plastic latches may not offer the same level of durability as metal options, particularly in high-traffic areas.
Impact on Application: Plastic latches are often used in residential settings and for temporary installations. They are less suitable for heavy-duty applications.
Considerations for International Buyers: Compliance with safety standards is essential, especially in Europe, where regulations are stringent. In Africa and South America, the availability of quality plastic materials can vary.
Summary Table of Material Properties for Door Latches
Material | Typical Use Case for Door Latch | Key Advantage | Key Disadvantage/Limitation | Relative Cost (Low/Med/High) |
---|---|---|---|---|
Brass | Residential applications | Excellent durability and aesthetics | Higher cost and maintenance needs | High |
Stainless Steel | Commercial applications | High strength and corrosion resistance | More expensive and complex to manufacture | High |
Zinc Alloy | Residential/light commercial | Cost-effective and versatile | Less durable than metals | Medium |
Plastic | Temporary and residential uses | Lightweight and low cost | Limited durability in high-stress areas | Low |
This comprehensive analysis equips international B2B buyers with the necessary insights to make informed decisions regarding material selection for door latches, ensuring compliance with local standards and suitability for their specific applications.
In-depth Look: Manufacturing Processes and Quality Assurance for door latch
What Are the Key Stages in the Manufacturing Process of Door Latches?
The manufacturing of door latches involves several critical stages that ensure the final product meets quality and functionality standards. Understanding these stages is essential for B2B buyers to assess potential suppliers effectively.
Material Preparation: What Materials Are Commonly Used in Door Latch Manufacturing?
The first step in the manufacturing process is material preparation. Common materials for door latches include:
- Steel: Known for its strength and durability, steel is often used for commercial latches. It can be treated for corrosion resistance.
- Brass: Popular for residential applications, brass offers aesthetic appeal and natural corrosion resistance.
- Aluminum: Lightweight and resistant to rust, aluminum is gaining popularity in various applications.
- Plastic: Used in lightweight and budget-friendly latches, plastic can offer versatility in design.
The choice of material significantly affects the latch’s performance, cost, and market suitability. Suppliers must source high-quality materials that comply with international standards.
How Are Door Latches Formed During the Manufacturing Process?
Once materials are prepared, the next stage is forming. This involves shaping the materials into the required components of the door latch. Common techniques include:
- Stamping: Metal sheets are cut and shaped using dies, allowing for mass production of latch components with high precision.
- Casting: Used primarily for complex shapes, molten metal is poured into molds and cooled to form the desired part.
- Machining: This technique involves removing material from a solid block to create precise dimensions, often used for high-quality latches.
Each method has its pros and cons, and the choice depends on the design specifications and production volume.
What Are the Assembly and Finishing Processes for Door Latches?
After forming, the components are assembled. This step includes:
- Sub-assembly: Individual parts like the latch mechanism and housing are assembled into sub-units before final assembly.
- Final Assembly: All components are put together to create the complete door latch, ensuring that moving parts operate smoothly.
Finishing processes, such as plating, painting, or anodizing, are then applied to enhance the product’s durability and aesthetic appeal. For example, zinc plating can prevent rust, while powder coating provides a durable finish that resists scratches and fading.
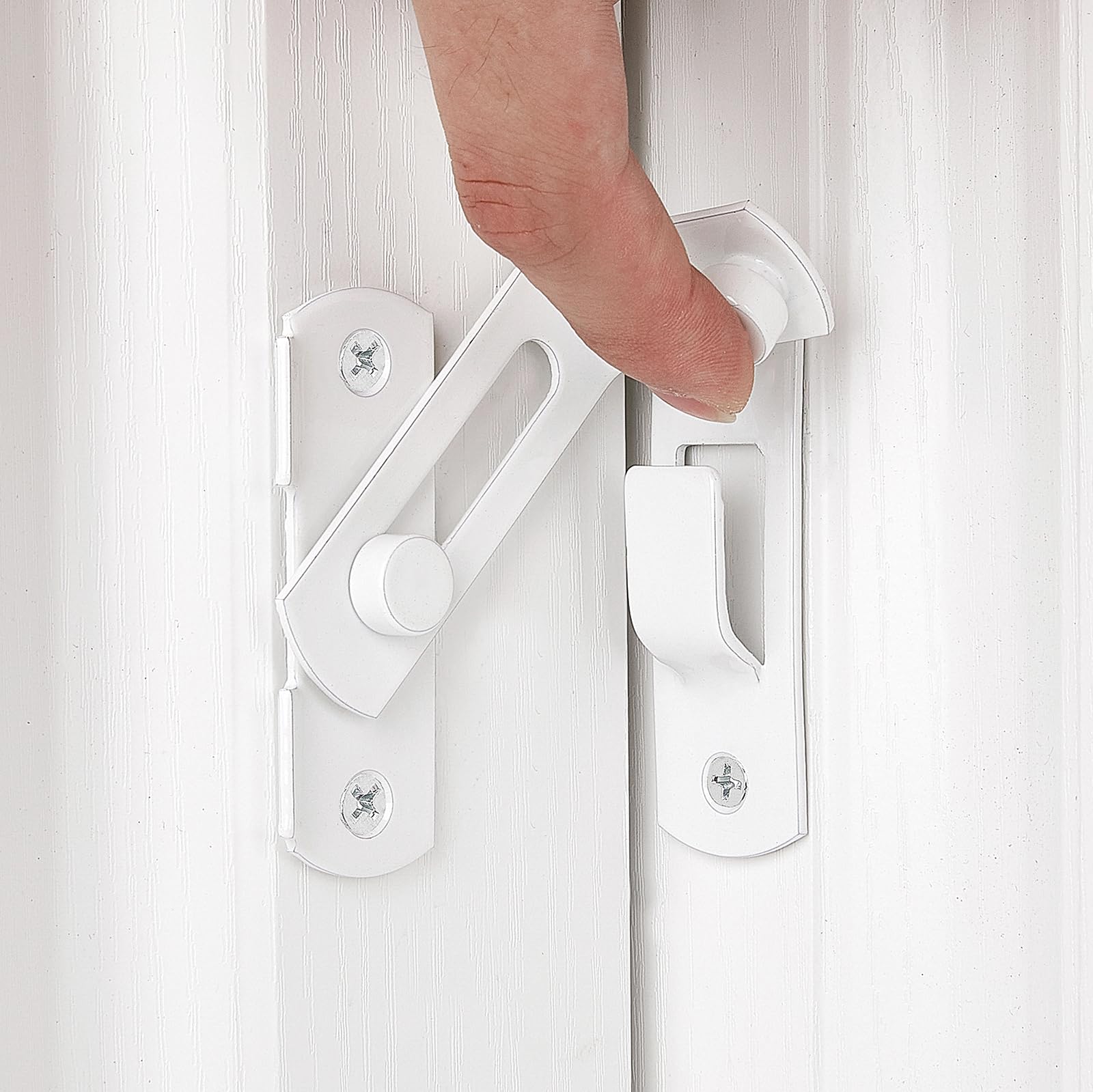
A stock image related to door latch.
What Quality Assurance Practices Should B2B Buyers Expect?
Quality assurance (QA) is crucial in ensuring that the door latches meet industry standards and customer expectations. Buyers should be aware of the following practices:
Which International Standards Should Door Latch Manufacturers Comply With?
International standards play a vital role in the quality assurance process. Key standards include:
- ISO 9001: This standard outlines the criteria for a quality management system, ensuring consistent product quality and customer satisfaction.
- CE Marking: Required for products sold within the European Economic Area, CE marking indicates compliance with health, safety, and environmental protection standards.
- API Standards: For latches used in oil and gas applications, adherence to American Petroleum Institute (API) standards ensures safety and reliability.
Manufacturers should be able to demonstrate compliance with these standards through certifications and documentation.
What Are the Checkpoints in the Quality Control Process?
Quality control (QC) involves multiple checkpoints throughout the manufacturing process to identify and rectify defects. Common QC checkpoints include:
- Incoming Quality Control (IQC): This is the first line of defense where raw materials are inspected upon arrival to ensure they meet specifications.
- In-Process Quality Control (IPQC): Inspections during the manufacturing process help catch defects early, minimizing waste and rework.
- Final Quality Control (FQC): The finished product undergoes rigorous testing to ensure it meets design specifications and quality standards before shipping.
These checkpoints are critical for ensuring that only high-quality products reach the market.
What Testing Methods Are Commonly Used for Door Latches?
Various testing methods are employed to verify the performance and durability of door latches:
- Functional Testing: Ensures that the latch operates correctly under normal use.
- Durability Testing: Simulates wear and tear over time to assess the latch’s lifespan.
- Environmental Testing: Checks the latch’s performance under different environmental conditions, such as humidity and temperature extremes.
Understanding these methods allows B2B buyers to request specific tests relevant to their needs.
How Can B2B Buyers Verify Supplier Quality Control Practices?
For international buyers, verifying the quality control practices of potential suppliers is essential. Here are some actionable steps:
- Supplier Audits: Conducting on-site audits can provide valuable insights into a manufacturer’s production processes and quality assurance measures.
- Quality Reports: Requesting detailed quality reports can help assess a supplier’s commitment to maintaining high standards.
- Third-Party Inspections: Engaging third-party inspection agencies can provide an unbiased evaluation of a supplier’s quality control processes.
These measures can help mitigate risks associated with sourcing door latches from international suppliers.
What Are the Quality Control Nuances for International B2B Buyers?
When sourcing door latches from different regions, B2B buyers must be aware of specific nuances:
- Cultural Differences: Different countries may have varying approaches to quality management and customer service. Understanding these cultural differences can aid in building strong supplier relationships.
- Regulatory Compliance: Ensure that suppliers are compliant with both local and international regulations, as this can affect product quality and safety.
- Supply Chain Transparency: Buyers should seek suppliers who are transparent about their supply chain practices, as this can impact the quality and reliability of the final product.
By considering these factors, international B2B buyers can make informed decisions and establish partnerships with reputable suppliers.
Practical Sourcing Guide: A Step-by-Step Checklist for ‘door latch’
In the competitive landscape of international B2B procurement, sourcing door latches requires a systematic approach to ensure quality, reliability, and compliance. This guide provides a step-by-step checklist tailored for buyers from Africa, South America, the Middle East, and Europe, focusing on critical factors that will enhance your procurement process.
Step 1: Define Your Technical Specifications
Understanding the specific requirements of the door latches you need is crucial. Consider factors such as:
– Latch Type: Identify whether you require deadlatches, roller latches, or surface-mounted options based on the intended use (commercial vs. residential).
– Material Requirements: Assess whether you need brass, steel, or plastic materials based on durability and aesthetic preferences.
Clarifying these specifications will streamline your search and ensure you acquire products that meet your operational needs.
Step 2: Research Market Trends and Standards
Stay informed about the latest trends in door latch technology and compliance standards. This involves:
– Regulatory Compliance: Ensure that the latches adhere to local and international safety standards, such as ANSI or ISO certifications.
– Market Trends: Explore emerging features like smart locks or tamper-resistant designs, which could enhance security.
Being aware of these trends can inform your purchasing decisions and future-proof your investment.
Step 3: Evaluate Potential Suppliers
Before committing to a supplier, conduct thorough evaluations. This includes:
– Company Background Checks: Request company profiles, product catalogs, and case studies that showcase their experience in the industry.
– References and Reviews: Look for testimonials or reviews from other businesses in similar regions or sectors.
A diligent supplier evaluation helps mitigate risks associated with quality and delivery reliability.
Step 4: Request Samples for Quality Assurance
Before placing a large order, always request samples of the door latches. This step is vital to:
– Assess Quality: Inspect the material, finish, and functionality of the latches firsthand to ensure they meet your standards.
– Fit and Compatibility: Verify that the samples fit your door specifications and are compatible with existing hardware.
Testing samples can prevent costly mistakes and ensure that the product aligns with your expectations.
Step 5: Negotiate Terms and Pricing
Once you have identified potential suppliers, engage in negotiations to secure favorable terms. Consider:
– Pricing Structures: Discuss bulk pricing options, discounts for long-term contracts, or payment terms that suit your cash flow.
– Delivery Times and Shipping Costs: Clarify lead times and shipping arrangements to avoid delays in your operations.
Effective negotiation can lead to significant cost savings and better service from suppliers.
Step 6: Verify Supplier Certifications and Quality Control
Ensure that your chosen supplier has the necessary certifications and quality control measures in place. This includes:
– ISO Certification: Look for suppliers with ISO 9001 certification, indicating they adhere to international quality management standards.
– Quality Control Processes: Ask about their quality assurance protocols to ensure consistent product quality.
Validating these credentials is essential to building a reliable supply chain.
Step 7: Plan for Logistics and Distribution
Finally, consider the logistics involved in the procurement process. Pay attention to:
– Shipping Methods: Determine the most efficient shipping methods for your location, considering cost and delivery time.
– Customs and Import Duties: Understand the customs regulations and import duties applicable to your region to avoid unexpected costs.
Effective logistics planning ensures that your door latches arrive on time and within budget, facilitating smooth operations.
By following this comprehensive checklist, international B2B buyers can enhance their procurement process for door latches, ensuring quality, compliance, and efficiency in their sourcing activities.
Comprehensive Cost and Pricing Analysis for door latch Sourcing
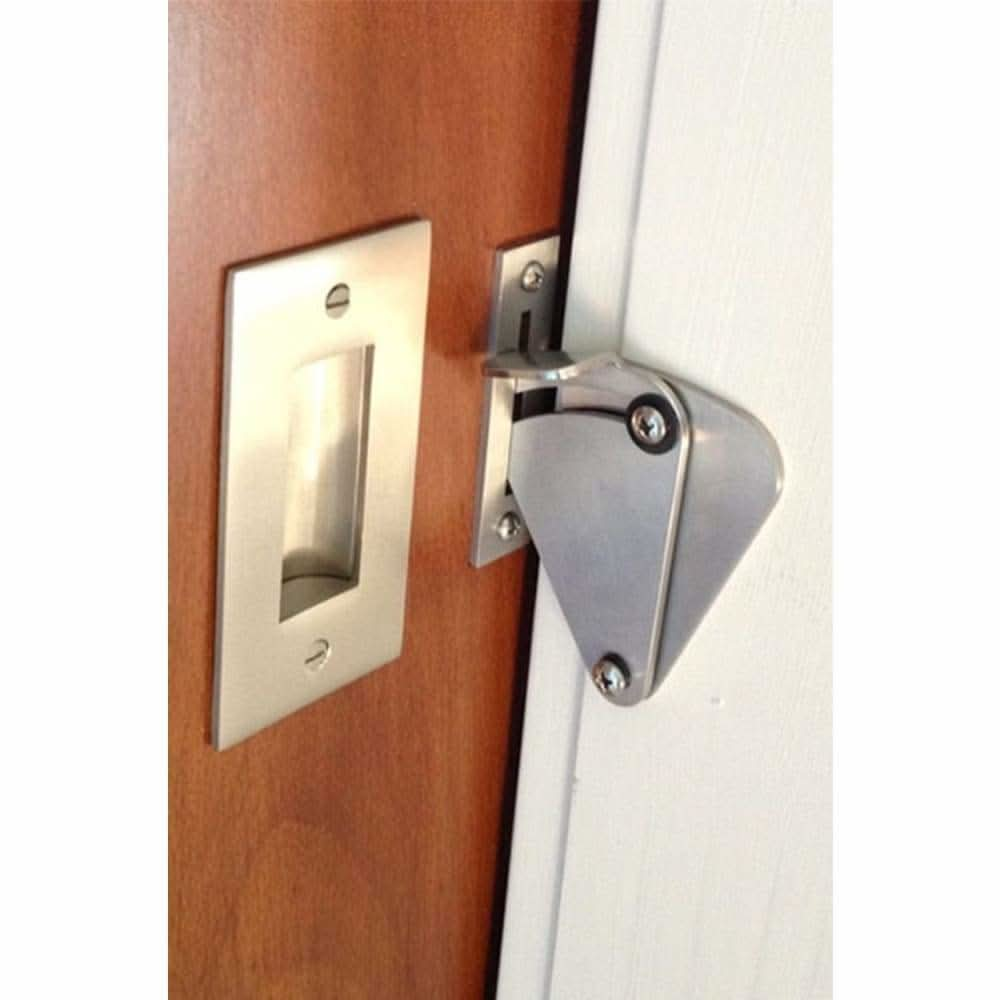
A stock image related to door latch.
When sourcing door latches, understanding the comprehensive cost structure and pricing dynamics is crucial for international B2B buyers. This section delves into the various cost components, price influencers, and buyer strategies to optimize sourcing decisions, particularly for buyers from Africa, South America, the Middle East, and Europe.
What Are the Key Cost Components in Door Latch Manufacturing?
The cost structure of door latches is influenced by several components:
-
Materials: The choice of materials significantly affects the overall cost. Common materials include brass, stainless steel, and plastic, with brass typically being more expensive due to its durability and aesthetic appeal. Custom or specialty materials can further increase costs.
-
Labor: Labor costs vary based on the region and the complexity of the latch design. Regions with lower labor costs may offer competitive pricing, but this can sometimes come at the expense of quality.
-
Manufacturing Overhead: This includes costs associated with facilities, utilities, and administrative expenses. Efficient manufacturing processes can help minimize these costs.
-
Tooling: Initial tooling costs for custom designs can be significant. Buyers should consider these costs when planning for long-term sourcing, as they can be amortized over larger production runs.
-
Quality Control (QC): Investing in QC processes is essential to ensure that the latches meet safety and performance standards. Buyers should inquire about the supplier’s QC procedures and certifications, which can affect pricing.
-
Logistics: Shipping and handling costs can vary widely based on the supplier’s location and the chosen Incoterms. These costs should be factored into the total cost of ownership.
-
Margin: Suppliers typically add a markup to cover their costs and profit. Understanding the supplier’s margin expectations can provide insights into potential negotiation points.
How Do Price Influencers Impact Door Latch Sourcing?
Several factors influence the pricing of door latches, including:
-
Volume/MOQ (Minimum Order Quantity): Larger orders can lead to significant discounts. Buyers should negotiate MOQs that align with their demand to optimize costs.
-
Specifications and Customization: Custom designs or specific specifications often incur higher costs. Buyers should assess whether customization is essential or if standard products can meet their needs.
-
Quality and Certifications: Higher-quality latches often come with certifications that validate their performance and safety. Buyers should weigh the benefits of certified products against their budget constraints.
-
Supplier Factors: The reputation, reliability, and location of suppliers can influence pricing. Established suppliers may charge a premium for their reliability, while newer suppliers may offer lower prices to attract customers.
-
Incoterms: Understanding the implications of different Incoterms (e.g., FOB, CIF) is critical for managing logistics costs and responsibilities in international transactions.
What Are Effective Buyer Tips for Cost-Efficient Door Latch Sourcing?
To maximize value in door latch sourcing, consider the following strategies:
-
Negotiate with Suppliers: Build relationships with multiple suppliers and leverage competitive bids to negotiate better pricing. Highlighting your purchasing volume can strengthen your position.
-
Focus on Total Cost of Ownership (TCO): Evaluate not just the upfront costs but also the long-term costs associated with maintenance, durability, and potential replacements. This holistic view can lead to more informed purchasing decisions.
-
Understand Pricing Nuances for International Markets: Be aware of regional pricing trends and currency fluctuations that may affect costs. Buyers from Africa, South America, the Middle East, and Europe should also consider the impact of tariffs and trade agreements on pricing.
-
Request Samples: Before committing to large orders, request samples to assess quality. This can prevent costly mistakes and ensure that the product meets your specifications.
Disclaimer for Indicative Prices
Prices for door latches can vary widely based on the factors mentioned above. The figures provided in supplier catalogs are indicative and may not reflect the final costs after negotiations, shipping, and other logistical considerations. Always seek updated quotes and detailed breakdowns from suppliers to ensure accurate budgeting.
Alternatives Analysis: Comparing door latch With Other Solutions
When considering door security and functionality, it’s important for B2B buyers to evaluate various solutions. While traditional door latches have been a go-to option, other alternatives may offer unique advantages depending on the specific requirements of a business. Below, we compare door latches with two alternatives: electronic locks and sliding bolt locks. This analysis will help international B2B buyers, particularly from regions like Africa, South America, the Middle East, and Europe, to make informed decisions.
Comparison Table of Door Latch and Alternatives
Comparison Aspect | Door Latch | Electronic Locks | Sliding Bolt Locks |
---|---|---|---|
Performance | Reliable for basic security | High security, customizable access | Good for added security |
Cost | Low-cost (typically $5 – $50) | Higher initial investment ($100 – $500) | Moderate ($20 – $100) |
Ease of Implementation | Simple installation | Requires technical knowledge | Easy to install |
Maintenance | Low maintenance | Moderate (battery changes) | Low maintenance |
Best Use Case | Residential and light commercial | Commercial, high-security areas | Storage rooms, sheds |
What Are the Advantages and Disadvantages of Electronic Locks?
Electronic locks provide enhanced security features, including keyless entry and access control systems that can be integrated with security management software. These locks often allow businesses to manage access remotely, making them ideal for high-security environments such as offices or warehouses. However, they come with a higher upfront cost and require technical expertise for installation and maintenance. Additionally, reliance on batteries or power sources can be a drawback in areas with unreliable electricity supply.
How Do Sliding Bolt Locks Compare to Door Latches?
Sliding bolt locks are a robust alternative that offers an additional layer of security. They are particularly effective in securing storage areas, gates, or doors that require a more substantial locking mechanism. The installation is relatively straightforward, making them a popular choice for businesses looking to enhance security without significant investment. However, they may not be as aesthetically pleasing and can be cumbersome in high-traffic areas, limiting their use in commercial settings.
Conclusion: How Should B2B Buyers Choose the Right Door Security Solution?
Selecting the right door security solution depends on various factors, including the level of security required, budget constraints, and the specific application of the door. For businesses prioritizing cost-effectiveness and basic security, traditional door latches remain a reliable choice. However, if the focus is on advanced security features and access management, electronic locks might be the better option. Sliding bolt locks can serve as a middle ground, offering solid security for areas that require frequent access but may not need high-tech solutions. Understanding the unique needs of your operation will guide you in making the best choice for your security strategy.
Essential Technical Properties and Trade Terminology for door latch
What Are the Key Technical Properties of Door Latches?
When sourcing door latches for commercial applications, it’s crucial to understand the technical specifications that can impact performance, security, and compliance. Here are some essential properties to consider:
1. Material Grade
The material from which a door latch is made significantly affects its durability and security. Common materials include brass, stainless steel, and zinc alloys. For example, brass offers corrosion resistance and aesthetic appeal, while stainless steel provides strength and is ideal for high-traffic areas. Understanding material grades helps in choosing latches suitable for specific environmental conditions and usage levels.
2. Security/ANSI Grade
The American National Standards Institute (ANSI) provides grading for locks and latches based on their resistance to unauthorized access. Grades range from 1 (highest security) to 3 (standard security). For B2B buyers, selecting a higher grade latch is vital for applications requiring enhanced security, such as commercial properties or sensitive areas.
3. Latch Type
Door latches come in various types, including deadlatches, spring latches, and electronic latches. Each type has specific functionalities; for instance, deadlatches are more secure as they prevent the door from being forced open. Knowing the type of latch required can streamline procurement and installation processes.
4. Finish and Aesthetic Appeal
The finish of a door latch not only affects its appearance but also its resistance to wear and corrosion. Common finishes include polished brass, satin nickel, and oil-rubbed bronze. B2B buyers should consider the finish in relation to the overall design of the facility, ensuring that the latch complements the architectural style while providing necessary durability.
5. Tolerance Levels
Tolerance refers to the permissible limit of variation in a latch’s dimensions. High precision is crucial in applications where a latch must fit seamlessly with other hardware. Understanding tolerance levels can prevent installation issues and ensure the latch operates correctly, thus reducing maintenance costs.
What Are Common Trade Terms Related to Door Latches?
Understanding industry terminology is essential for effective communication and negotiation in B2B transactions. Here are some common terms that buyers should be familiar with:
1. OEM (Original Equipment Manufacturer)
An OEM refers to a company that produces parts or equipment that may be marketed by another manufacturer. When sourcing door latches, buyers often look for OEM products to ensure compatibility with existing hardware and adherence to quality standards.
2. MOQ (Minimum Order Quantity)
MOQ is the smallest quantity of a product that a supplier is willing to sell. This term is crucial for buyers to understand as it can affect inventory levels and cost structures. Negotiating MOQs can lead to more favorable pricing and terms, especially for bulk purchases.
3. RFQ (Request for Quotation)
An RFQ is a document sent to suppliers to invite them to provide pricing and terms for a specific quantity of goods. Issuing an RFQ for door latches can help buyers compare costs from different suppliers, ensuring they get the best value.
4. Incoterms (International Commercial Terms)
Incoterms define the responsibilities of buyers and sellers in international trade. They clarify who is responsible for shipping, insurance, and tariffs. Familiarity with Incoterms is essential for B2B buyers engaging in cross-border transactions, as it helps prevent misunderstandings regarding delivery and costs.
5. Lead Time
Lead time is the period between placing an order and receiving the goods. Understanding lead times for door latches can help buyers manage their inventory and project timelines effectively, ensuring that they have the necessary hardware when needed.
By grasping these technical properties and trade terms, international B2B buyers can make informed decisions that enhance their procurement processes and ensure they select the right door latches for their specific needs.
Navigating Market Dynamics and Sourcing Trends in the door latch Sector
What Are the Current Market Dynamics and Key Trends in the Door Latch Sector?
The door latch market is experiencing significant transformation driven by technological advancements, consumer preferences, and changing regulatory environments. International B2B buyers should note that the global demand for door latches is primarily fueled by the construction and renovation industries, which have seen a resurgence post-pandemic. Key trends include the increasing adoption of smart locking systems and enhanced security features, which are becoming essential in both residential and commercial settings. Buyers from regions like Africa and South America are increasingly interested in affordable yet innovative solutions, while European markets, particularly Germany and Turkey, show a growing preference for high-security and aesthetically appealing designs.
Moreover, sustainability is becoming a significant driver in the door latch sector. Buyers are increasingly seeking suppliers that prioritize eco-friendly materials and processes. The rise of e-commerce is also influencing sourcing strategies, as B2B buyers can now easily compare products and suppliers online, facilitating more informed purchasing decisions. Emerging technologies, such as IoT-enabled devices, are expected to dominate the market, offering enhanced convenience and security features. Buyers should keep an eye on these innovations to remain competitive in their respective markets.
How Can Sustainability and Ethical Sourcing Impact Your B2B Buying Decisions?
Sustainability and ethical sourcing are becoming non-negotiable factors in B2B purchasing decisions. The environmental impact of manufacturing processes, particularly concerning resource extraction and waste generation, is under increasing scrutiny. Buyers in the door latch sector should prioritize suppliers who utilize sustainable materials, such as recycled metals or sustainably sourced wood, to align with global sustainability goals.
Certifications like ISO 14001 (Environmental Management) or LEED (Leadership in Energy and Environmental Design) can serve as indicators of a supplier’s commitment to sustainability. Additionally, ethical sourcing practices, including fair labor conditions and transparency in supply chains, are increasingly important to buyers in Europe and the Middle East. By choosing suppliers who adhere to these principles, businesses can enhance their brand reputation and appeal to environmentally conscious consumers.
What Is the Brief Evolution of Door Latches and Its Relevance to Today’s B2B Market?
The evolution of door latches can be traced back to ancient civilizations, where simple mechanisms were developed for security. Initially, these were rudimentary devices made of wood or metal, but advancements during the Industrial Revolution led to the creation of more sophisticated locking mechanisms. The introduction of mass production techniques in the 20th century further transformed the market, making door latches more accessible and affordable.
Today, the focus has shifted towards smart technology and enhanced security features, reflecting the changing needs of consumers and businesses alike. Understanding this evolution is crucial for B2B buyers, as it highlights the importance of innovation and adaptability in supplier offerings. By recognizing historical trends, buyers can better anticipate future developments and make informed decisions that align with their strategic goals.
Frequently Asked Questions (FAQs) for B2B Buyers of door latch
-
How do I choose the right door latch for my business needs?
Choosing the right door latch involves assessing the specific application and security requirements. Consider factors such as the latch type (e.g., deadbolt, sliding, or surface-mounted), material durability, and finish that aligns with your brand aesthetics. Ensure the latch meets local building codes and security standards relevant to your region, particularly in countries with stringent regulations like Germany or Turkey. Additionally, evaluate the latch’s ease of installation and maintenance, which can impact your operational efficiency. -
What are the key features to look for in a commercial door latch?
For commercial applications, prioritize latches that offer high security, durability, and resistance to tampering. Look for features like ANSI grading, which indicates the quality and security level of the latch. Consider latches with weather-resistant materials for outdoor installations, as well as those that provide additional safety features like anti-pick or anti-drill designs. Aesthetic options such as customizable finishes can also enhance your business’s branding while maintaining functionality. -
How can I ensure the quality of door latches when sourcing internationally?
To ensure quality when sourcing door latches internationally, thoroughly vet suppliers through certifications and quality assurance standards, such as ISO 9001. Request samples to evaluate the latch’s performance and durability firsthand. Establish clear quality control measures, including inspections during production and before shipping. Engaging with suppliers who have a proven track record in your target regions (like Africa or South America) can also mitigate risks associated with quality discrepancies. -
What are the minimum order quantities (MOQ) for door latches when importing?
Minimum order quantities (MOQ) can vary significantly by supplier and product type. Typically, MOQs for door latches range from 100 to 1,000 units, depending on the manufacturer’s production capabilities and your specific requirements. When negotiating with suppliers, inquire about flexible MOQs, especially if you are testing new products or entering a new market. Additionally, consider the implications of bulk orders on your cash flow and inventory management. -
What payment terms should I negotiate with international suppliers for door latches?
Negotiating favorable payment terms is crucial for managing cash flow in international transactions. Common options include letters of credit, advance payments, or payment upon delivery. Aim for a 30% upfront payment with the remainder due upon shipment or delivery, as this balances risk for both parties. Ensure that payment methods are secure and consider using escrow services for high-value orders to protect your investment. -
How do I handle logistics and shipping for door latch imports?
When importing door latches, coordinate closely with your supplier and logistics provider to ensure timely and cost-effective shipping. Choose between air freight for speed or sea freight for cost efficiency, depending on your urgency and budget. Understand customs regulations in your importing country, particularly for regions like the Middle East or Europe, to avoid unexpected delays. Establish a reliable supply chain that includes tracking shipments and managing delivery timelines to ensure smooth operations. -
What customization options are available for door latches?
Many suppliers offer customization options for door latches, allowing you to tailor products to meet specific needs. Customization can include size variations, unique finishes, branding elements like logos, and modifications to latch mechanisms. When discussing customization, clarify lead times and any impact on pricing and MOQs. This flexibility can be a competitive advantage, particularly in diverse markets across Africa and South America. -
What are the common compliance standards for door latches in international markets?
Compliance standards for door latches vary by region and can include safety, security, and material regulations. In Europe, for instance, latches may need to comply with CE marking requirements, while in the Middle East, you should consider local building codes. Research the specific standards applicable to your target market, and ensure your suppliers can provide documentation proving compliance. This diligence helps avoid legal issues and enhances your product’s marketability.
Important Disclaimer & Terms of Use
⚠️ Important Disclaimer
The information provided in this guide, including content regarding manufacturers, technical specifications, and market analysis, is for informational and educational purposes only. It does not constitute professional procurement advice, financial advice, or legal advice.
While we have made every effort to ensure the accuracy and timeliness of the information, we are not responsible for any errors, omissions, or outdated information. Market conditions, company details, and technical standards are subject to change.
B2B buyers must conduct their own independent and thorough due diligence before making any purchasing decisions. This includes contacting suppliers directly, verifying certifications, requesting samples, and seeking professional consultation. The risk of relying on any information in this guide is borne solely by the reader.
Strategic Sourcing Conclusion and Outlook for door latch
In the evolving landscape of door latch sourcing, international B2B buyers must prioritize strategic sourcing to enhance operational efficiency and quality assurance. By understanding the diversity of door latch types—ranging from residential to commercial applications—buyers can tailor their procurement strategies to meet specific project needs. Leveraging supplier relationships across different regions, such as Africa, South America, the Middle East, and Europe, allows for competitive pricing and access to innovative designs that cater to local market preferences.
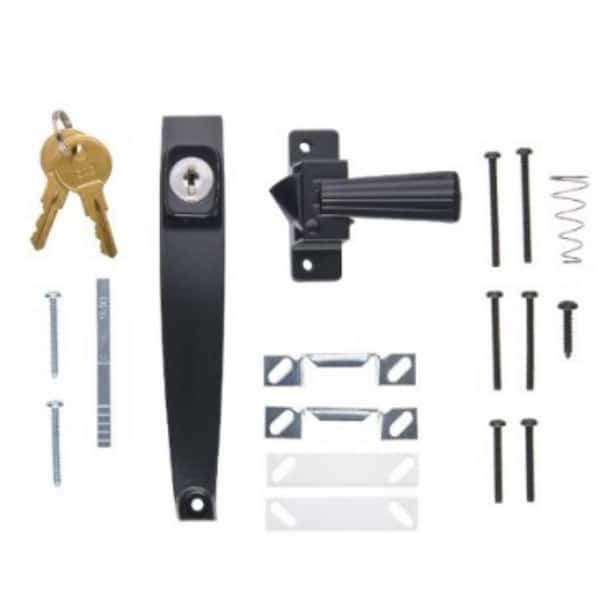
A stock image related to door latch.
How Can Strategic Sourcing Enhance Your Procurement Process?
Implementing a strategic sourcing approach not only mitigates risks associated with supply chain disruptions but also fosters collaboration with manufacturers who understand regional compliance and quality standards. Buyers are encouraged to conduct thorough market research to identify reliable suppliers and to utilize platforms that offer comprehensive product specifications and customer reviews.
What’s Next for International B2B Buyers in the Door Latch Market?
Looking ahead, the demand for high-quality, durable door latches will continue to grow, particularly as construction and renovation projects expand globally. By staying informed about emerging trends and technological advancements, B2B buyers can position themselves at the forefront of the market. Engage with industry experts, attend trade shows, and explore digital marketplaces to seize new opportunities in door latch sourcing. The future is promising—make your next move count!