Unlock Savings: The Ultimate Guide to Locks and Latches (2025)
Introduction: Navigating the Global Market for locks and latches
In the dynamic landscape of global commerce, sourcing high-quality locks and latches poses significant challenges for international B2B buyers. With diverse markets across Africa, South America, the Middle East, and Europe, decision-makers often grapple with varying standards, regulatory requirements, and supplier reliability. This comprehensive guide aims to equip you with the insights necessary to navigate these complexities, focusing on the diverse types and applications of locks and latches, effective supplier vetting strategies, and understanding cost implications.
Understanding the nuances of different locking mechanisms, from traditional deadbolts to innovative smart locks, is crucial for making informed purchasing decisions. This guide will delve into the specifications that matter most—such as security ratings, durability, and compatibility with existing infrastructure—ensuring you can select the right products for your projects. Furthermore, we will explore the best practices for vetting suppliers to mitigate risks associated with international transactions, including assessing their certifications and customer feedback.
Ultimately, this guide empowers B2B buyers by providing actionable insights that facilitate strategic sourcing decisions, fostering confidence in the procurement process. Whether you are based in the bustling markets of Italy, the vibrant economies of Argentina, or any region in between, our goal is to enhance your understanding of the global locks and latches market, paving the way for successful and secure transactions.
Understanding locks and latches Types and Variations
Type Name | Key Distinguishing Features | Primary B2B Applications | Brief Pros & Cons for Buyers |
---|---|---|---|
Deadbolts | High security, typically requires a key for locking. | Commercial buildings, residential doors | Pros: Enhanced security; Cons: Can be more expensive and complex to install. |
Mortise Locks | Integrated into the door, offering a sleek appearance. | High-end residential, offices | Pros: Aesthetically pleasing; Cons: Requires precise installation and may need professional help. |
Padlocks | Portable, available in various sizes and security levels. | Storage units, construction sites | Pros: Versatile and easy to use; Cons: Less secure than fixed locks, vulnerable to cutting. |
Latch Locks | Simple mechanism, often used in conjunction with other locks. | Interior doors, cabinets | Pros: Cost-effective and easy to install; Cons: Limited security, primarily for low-risk applications. |
Smart Locks | Keyless entry, can be controlled via smartphone apps. | Modern offices, residential buildings | Pros: Convenience and remote access; Cons: Reliance on technology and battery life concerns. |
What are Deadbolts and Their B2B Suitability?
Deadbolts are one of the most secure types of locks available, requiring a key for locking and unlocking. They are commonly used in commercial buildings and residential doors, providing a significant upgrade in security over traditional spring bolt locks. When considering a purchase, B2B buyers should evaluate the level of security needed for their premises, as well as the installation complexity, which may necessitate professional services.
How Do Mortise Locks Benefit Businesses?
Mortise locks are installed within the door itself, offering a clean and sophisticated look. They are particularly suitable for high-end residential properties and office environments, where aesthetics and security are paramount. B2B buyers should consider the installation requirements, as mortise locks demand precise fitting and may require skilled labor, impacting overall project timelines and costs.
Why Choose Padlocks for Temporary Security Needs?
Padlocks are highly versatile and can be used in various settings, including storage units and construction sites. They come in different sizes and security levels, making them suitable for both low-risk and higher-security applications. Buyers should assess the level of security required, as padlocks can be more vulnerable to tampering compared to fixed locks. Their portability is a significant advantage for businesses needing temporary solutions.
What Are Latch Locks and Their Limitations?
Latch locks feature a simple mechanism that is often used in conjunction with other locking systems. They are ideal for interior doors and cabinets, making them cost-effective and easy to install. However, B2B buyers should recognize that latch locks offer limited security and are best suited for low-risk areas. Understanding the specific application can help businesses make informed decisions about their security needs.
How Do Smart Locks Enhance Security for Modern Businesses?
Smart locks provide the convenience of keyless entry and can be managed via smartphone applications. They are increasingly popular in modern offices and residential buildings, where flexibility and remote access are valued. B2B buyers should consider the technological infrastructure required for installation and maintenance, as well as the potential for battery life issues. The advanced features of smart locks can justify the higher upfront costs for businesses prioritizing modern security solutions.
Key Industrial Applications of locks and latches
Industry/Sector | Specific Application of locks and latches | Value/Benefit for the Business | Key Sourcing Considerations for this Application |
---|---|---|---|
Manufacturing | Secure access control for production areas | Enhances safety and prevents unauthorized access | Look for ANSI-certified locks; consider durability and resistance to tampering. |
Hospitality | Locking systems for guest room doors | Improves guest security and enhances customer trust | Prioritize ease of use, compatibility with existing systems, and aesthetic appeal. |
Retail | Latches for display cases and storage areas | Protects merchandise and reduces theft risk | Focus on lock reliability, quick installation, and maintenance needs. |
Education | Locks for classrooms and administrative offices | Ensures safety for students and staff | Consider compliance with safety regulations and user-friendly designs. |
Healthcare | Access control for sensitive areas (pharmacies) | Protects sensitive information and controlled substances | Look for high-security options and compatibility with electronic access systems. |
How Are Locks and Latches Used in Manufacturing?
In the manufacturing sector, locks and latches play a critical role in securing production areas, machinery, and sensitive materials. They ensure that only authorized personnel can access restricted zones, significantly reducing the risk of theft and accidents. International B2B buyers should prioritize sourcing ANSI-certified locks that offer high durability and resistance to tampering, as these features are essential for maintaining operational integrity and safety.
What Role Do Locks and Latches Play in the Hospitality Industry?
In the hospitality sector, secure locking systems for guest room doors are paramount for ensuring guest safety and privacy. High-quality locks not only enhance the customer experience but also foster trust in the establishment. Buyers from regions like Europe and South America should consider ease of use, compatibility with existing systems, and aesthetic appeal when sourcing locks and latches, as these factors directly impact guest satisfaction and operational efficiency.
How Are Locks and Latches Used in Retail Environments?
Retail environments utilize locks and latches for securing display cases and storage areas, protecting merchandise from theft and damage. The effectiveness of these locking systems can directly influence a retailer’s bottom line. When sourcing locks for retail applications, businesses should focus on reliability, quick installation, and maintenance needs to ensure smooth operations and safety.
Why Are Locks and Latches Important in Educational Institutions?
In educational settings, locks for classrooms and administrative offices are essential for ensuring the safety of students and staff. Effective locking mechanisms can prevent unauthorized access during school hours and during after-school activities. Buyers in this sector should consider compliance with safety regulations, user-friendly designs, and the ability to integrate with existing security systems when sourcing locks and latches.
How Are Locks and Latches Used in Healthcare Settings?
In healthcare facilities, locks and latches are crucial for maintaining access control in sensitive areas such as pharmacies and patient records rooms. These locking systems protect sensitive information and controlled substances, ensuring compliance with regulatory standards. B2B buyers in the healthcare sector should look for high-security options that can seamlessly integrate with electronic access systems, enhancing overall security and operational efficiency.
3 Common User Pain Points for ‘locks and latches’ & Their Solutions
Scenario 1: Inconsistent Quality Across Suppliers
The Problem: A B2B buyer sourcing locks and latches for a large-scale construction project often encounters a frustrating issue: inconsistent quality across different suppliers. This inconsistency can lead to frequent replacements, project delays, and increased costs. For instance, a supplier may provide high-quality latches for one order but deliver subpar replacements for the next. This unpredictability not only disrupts timelines but also affects the overall integrity of the project.
The Solution: To mitigate this risk, buyers should implement a robust supplier evaluation process that includes quality certifications and performance reviews. Start by requesting samples and conducting thorough testing before placing large orders. Additionally, consider establishing long-term relationships with a select few suppliers known for their reliability and product consistency. Tools like quality management systems can help track supplier performance over time. By prioritizing suppliers who adhere to international quality standards such as ISO 9001, you can ensure a more consistent supply of high-quality locks and latches, reducing the likelihood of project delays and unexpected costs.
Scenario 2: Security Concerns with Lock Systems
The Problem: Security is paramount for businesses, and a B2B buyer may face challenges when selecting locks and latches that provide adequate protection against unauthorized access. For example, a facility manager in the Middle East may find that standard locks are inadequate for high-security areas, leading to potential breaches and losses. The fear of theft or vandalism can create a significant burden, especially in regions with high crime rates.
The Solution: To enhance security, buyers should consider investing in advanced locking systems that offer features such as smart technology, access control, and tamper resistance. When sourcing locks, look for products that have been tested against industry standards for security, such as ANSI/BHMA grades. Additionally, integrating electronic locks with keyless entry systems can provide increased security and flexibility. Educate staff on the importance of security measures and conduct regular audits to assess the effectiveness of the locks in place. By taking a proactive approach to security, businesses can protect their assets and maintain peace of mind.
Scenario 3: Difficulty in Sizing and Compatibility
The Problem: Many B2B buyers encounter difficulties when it comes to sizing and compatibility of locks and latches with existing doors and frameworks. A common scenario is a buyer in Europe who discovers that the new locks they ordered do not fit standard door sizes or the existing latch systems. This oversight can lead to delays in installation, increased labor costs, and a backlog of projects waiting for compatible hardware.
The Solution: To avoid sizing and compatibility issues, buyers should meticulously assess the specifications of their doors and existing hardware before making a purchase. Create a detailed inventory that includes measurements and types of doors, as well as any existing latch systems. When sourcing locks and latches, look for suppliers that provide comprehensive product specifications, including dimensions, compatibility notes, and installation instructions. It can also be beneficial to consult with a technical expert or a product representative to ensure that the selected products will meet the specific requirements. By investing time in accurate assessments and communication with suppliers, buyers can streamline their procurement process and minimize installation complications.
Strategic Material Selection Guide for locks and latches
What Are the Key Materials Used in Locks and Latches?
When selecting locks and latches for various applications, the choice of material is critical. The material not only affects the performance and durability of the product but also influences compliance with international standards and market preferences. Here, we analyze four common materials used in locks and latches: stainless steel, brass, plastic, and zinc alloy.
How Does Stainless Steel Perform in Lock and Latch Applications?
Stainless steel is renowned for its exceptional corrosion resistance and strength, making it a preferred choice for locks and latches used in outdoor or humid environments. Its temperature rating is generally high, allowing it to withstand extreme conditions without compromising functionality.
Pros: Stainless steel is durable and resistant to rust, which is essential for applications exposed to moisture. It also has a sleek, modern appearance that appeals to many buyers.
Cons: The manufacturing process can be more complex and costly compared to other materials. Additionally, while it is strong, it may not be as malleable as brass, which can limit design options.
Impact on Application: Stainless steel is suitable for high-security applications, such as commercial buildings and outdoor gates, where weather resistance is crucial.
Considerations for International Buyers: Buyers from regions like Europe may prioritize stainless steel due to stringent corrosion resistance standards (e.g., DIN EN 10088). In contrast, buyers in Africa and the Middle East might consider the material’s performance in extreme heat and humidity.
Why Choose Brass for Locks and Latches?
Brass is a traditional material known for its excellent machinability and aesthetic appeal. It offers good corrosion resistance and is often used in decorative applications.
Pros: Brass is easy to work with, allowing for intricate designs and finishes. It also has natural antimicrobial properties, making it suitable for environments where hygiene is a concern.
Cons: While brass is durable, it is softer than stainless steel, which may lead to wear over time, especially in high-traffic areas. Additionally, brass can tarnish, requiring regular maintenance to maintain its appearance.
Impact on Application: Brass is commonly used in residential locks and latches, particularly in decorative hardware. Its warm color adds a touch of elegance to interior spaces.
Considerations for International Buyers: In Europe, brass products must often meet specific standards (e.g., EN 1670 for corrosion resistance). Buyers in South America may prefer brass for its aesthetic qualities in residential applications.
What Role Does Plastic Play in Locks and Latches?
Plastic is increasingly used in locks and latches, especially in lightweight and cost-sensitive applications. It offers a range of properties depending on the type of plastic used.
Pros: Plastic is lightweight, resistant to corrosion, and can be produced at a lower cost than metal options. It also allows for a variety of colors and finishes.
Cons: Plastic may not provide the same level of security as metal, making it less suitable for high-security applications. Additionally, some plastics can degrade under UV exposure, limiting their use in outdoor settings.
Impact on Application: Plastic locks and latches are often used in residential settings, such as interior doors or cabinets, where high security is not a primary concern.
Considerations for International Buyers: Buyers in regions with lower security needs may find plastic options appealing due to their affordability. However, compliance with safety standards should still be verified.
How Does Zinc Alloy Compare in Locks and Latches?
Zinc alloy is a versatile material often used for die-casting locks and latches. It provides a good balance of strength and cost-effectiveness.
Pros: Zinc alloy is durable and can be manufactured into complex shapes, making it suitable for various designs. It also has decent corrosion resistance when coated properly.
Cons: While it is more affordable than stainless steel, it may not offer the same level of durability and can be prone to corrosion if not properly finished.
Impact on Application: Zinc alloy is often used in commercial applications where cost is a significant factor but decent durability is still required.
Considerations for International Buyers: Buyers in South America may appreciate the cost-effectiveness of zinc alloy products, while European buyers might focus on the quality of the finish to ensure compliance with local standards.
Summary Table of Material Properties
Material | Typical Use Case for locks and latches | Key Advantage | Key Disadvantage/Limitation | Relative Cost (Low/Med/High) |
---|---|---|---|---|
Stainless Steel | High-security outdoor applications | Exceptional corrosion resistance and strength | Higher manufacturing complexity and cost | High |
Brass | Decorative residential locks | Aesthetic appeal and machinability | Softer, prone to wear and tarnishing | Medium |
Plastic | Lightweight interior applications | Low cost and lightweight | Lower security and UV degradation | Low |
Zinc Alloy | Cost-sensitive commercial applications | Good balance of strength and cost | Prone to corrosion without proper finishing | Medium |
This guide provides actionable insights for international B2B buyers, helping them make informed decisions based on material properties, application suitability, and regional considerations.
In-depth Look: Manufacturing Processes and Quality Assurance for locks and latches
What Are the Main Stages in the Manufacturing Process of Locks and Latches?
The manufacturing process of locks and latches involves several key stages, each crucial for ensuring the final product meets quality and performance standards. Here’s an overview of the typical stages involved:
1. Material Preparation
The first step in manufacturing locks and latches is selecting the right materials. Common materials include stainless steel, brass, and zinc alloys, chosen for their durability and resistance to corrosion. Manufacturers often source materials from certified suppliers to ensure quality. Pre-treatment processes such as cleaning and surface preparation are essential to remove impurities and enhance adhesion for subsequent coatings.
2. Forming
Once materials are prepared, they undergo forming processes, which can include casting, forging, or machining.
- Casting involves pouring molten metal into molds, which is suitable for complex shapes.
- Forging is a process where metal is shaped under high pressure, enhancing its strength.
- Machining is used for precision parts, where material is removed to achieve specific dimensions.
Each technique has its advantages, and the choice often depends on the design complexity and material properties.
3. Assembly
After forming, components are assembled. This may involve mechanical fastening or welding, depending on the design. For instance, locks may require intricate assembly of multiple parts like the latch bolt, strike plate, and locking mechanism. Automated assembly lines are often employed to enhance efficiency and precision, especially for high-volume production.
4. Finishing
The finishing stage is critical for both aesthetics and functionality. Processes such as plating, anodizing, or powder coating provide corrosion resistance and improve the appearance of the locks and latches. Quality control checks are conducted at this stage to ensure that finishes are applied uniformly and meet specified thickness standards.
How Is Quality Assurance Managed in the Locks and Latches Industry?
Quality assurance is integral to the manufacturing of locks and latches, ensuring products meet international standards and customer expectations. Here are some critical aspects of quality assurance in this industry:
Relevant International Standards for Locks and Latches
International standards such as ISO 9001 play a crucial role in ensuring consistent quality management processes. Additionally, industry-specific certifications like CE marking in Europe indicate compliance with health, safety, and environmental protection standards. For B2B buyers from regions like Africa and South America, understanding these certifications can help in assessing the credibility of suppliers.
What Are the Key QC Checkpoints?
Quality control checkpoints are established throughout the manufacturing process:
- Incoming Quality Control (IQC) involves inspecting raw materials upon arrival to ensure they meet specified standards.
- In-Process Quality Control (IPQC) monitors production processes and parameters, ensuring adherence to specifications during manufacturing.
- Final Quality Control (FQC) is conducted on finished products, where they are tested for functionality, durability, and compliance with specifications.
These checkpoints help in identifying and rectifying defects at various stages, thus minimizing wastage and ensuring product quality.
What Common Testing Methods Are Used?
Several testing methods are employed to validate the quality and performance of locks and latches:
- Functional Testing assesses the operational capabilities of locks, ensuring they lock and unlock smoothly.
- Durability Testing simulates long-term use, evaluating how well locks withstand wear and tear.
- Corrosion Resistance Testing checks the effectiveness of finishes and coatings against environmental factors.
B2B buyers should inquire about the specific testing methods used by suppliers to ensure they meet their quality requirements.
How Can B2B Buyers Verify Supplier Quality Control?
For international buyers, particularly from Africa, South America, the Middle East, and Europe, verifying a supplier’s quality control processes is essential. Here are actionable steps:
1. Conduct Supplier Audits
Regular audits can provide insights into the supplier’s manufacturing processes and quality control practices. Buyers should request access to audit reports and certifications to evaluate compliance with international standards.
2. Request Quality Assurance Documentation
Suppliers should provide documentation detailing their quality assurance processes, including inspection records, testing results, and certifications. This transparency can help buyers assess the reliability of the supplier.
3. Utilize Third-Party Inspection Services
Engaging third-party inspection services can provide an unbiased assessment of the supplier’s quality practices. These services can conduct inspections at various stages of production, ensuring compliance with specified standards.
What Are the Quality Control and Certification Nuances for International Buyers?
When dealing with international suppliers, particularly from diverse regions, buyers should be aware of specific nuances in quality control and certification:
- Regional Compliance: Different regions may have varying compliance requirements. For instance, European buyers may prioritize CE marking, while those in the Middle East might focus on local compliance standards.
- Language Barriers: Documentation may be in different languages, which could lead to misunderstandings. Buyers should ensure that all quality assurance documents are provided in a language they understand.
- Cultural Differences in Business Practices: Different regions may have varying approaches to quality assurance and business ethics. Building strong relationships and understanding local practices can enhance collaboration and trust.
Conclusion
Understanding the manufacturing processes and quality assurance mechanisms for locks and latches is vital for international B2B buyers. By focusing on material preparation, forming, assembly, and finishing stages, along with rigorous quality control practices and relevant certifications, buyers can make informed decisions. Engaging in thorough supplier verification processes, including audits and third-party inspections, ensures that the products sourced meet the necessary quality and performance standards. This approach not only minimizes risks but also fosters long-term partnerships in the locks and latches industry.
Practical Sourcing Guide: A Step-by-Step Checklist for ‘locks and latches’
In the competitive landscape of international B2B procurement, particularly for locks and latches, a systematic approach can streamline the sourcing process and mitigate risks. This checklist serves as a practical guide for buyers from Africa, South America, the Middle East, and Europe, ensuring that you make informed decisions when selecting suppliers and products.
Step 1: Define Your Technical Specifications
Establishing clear technical specifications is the foundation of your sourcing process. Consider the specific requirements for your application, such as latch types (deadbolts, mortise, surface-mounted), materials (stainless steel, brass), and security ratings (ANSI grades). This clarity helps in aligning your needs with supplier offerings and ensures compatibility with existing systems.
Step 2: Research Market Trends and Innovations
Understanding current market trends and technological innovations in locks and latches can provide a competitive edge. Look for advancements such as smart locks, keyless entry systems, and enhanced security features. This knowledge not only informs your procurement strategy but also positions your business as a leader in adopting new technologies.
Step 3: Evaluate Potential Suppliers
Before making commitments, it’s essential to vet potential suppliers thoroughly. Request company profiles, product catalogs, and references from other clients, especially those in similar markets or industries. Assess their capacity to meet your volume requirements and their track record regarding product quality and delivery reliability.
Step 4: Verify Certifications and Compliance
Ensure that suppliers meet relevant industry standards and certifications. This may include ISO certifications, compliance with local regulations, and adherence to security standards. Validating these credentials mitigates risks associated with product quality and safety, particularly in international transactions.
Step 5: Request Samples for Quality Assessment
Before finalizing any bulk orders, request samples of the locks and latches you intend to purchase. This allows you to assess the quality, functionality, and aesthetics of the products firsthand. Pay attention to details such as ease of installation, durability, and finish, which are critical to overall customer satisfaction.
Step 6: Negotiate Terms and Pricing
Effective negotiation can lead to favorable terms and pricing. Discuss bulk order discounts, payment terms, and delivery timelines. Understanding the total cost of ownership, including shipping and potential duties, is essential for budgeting and financial forecasting.
Step 7: Establish a Communication Plan
Clear communication with your suppliers is vital for successful procurement. Establish regular check-ins and updates to discuss order status, potential delays, or changes in specifications. A robust communication plan fosters a collaborative relationship and helps address any issues proactively.
By following this structured checklist, B2B buyers can navigate the complexities of sourcing locks and latches more effectively, ensuring that they select the right products and partners for their business needs.
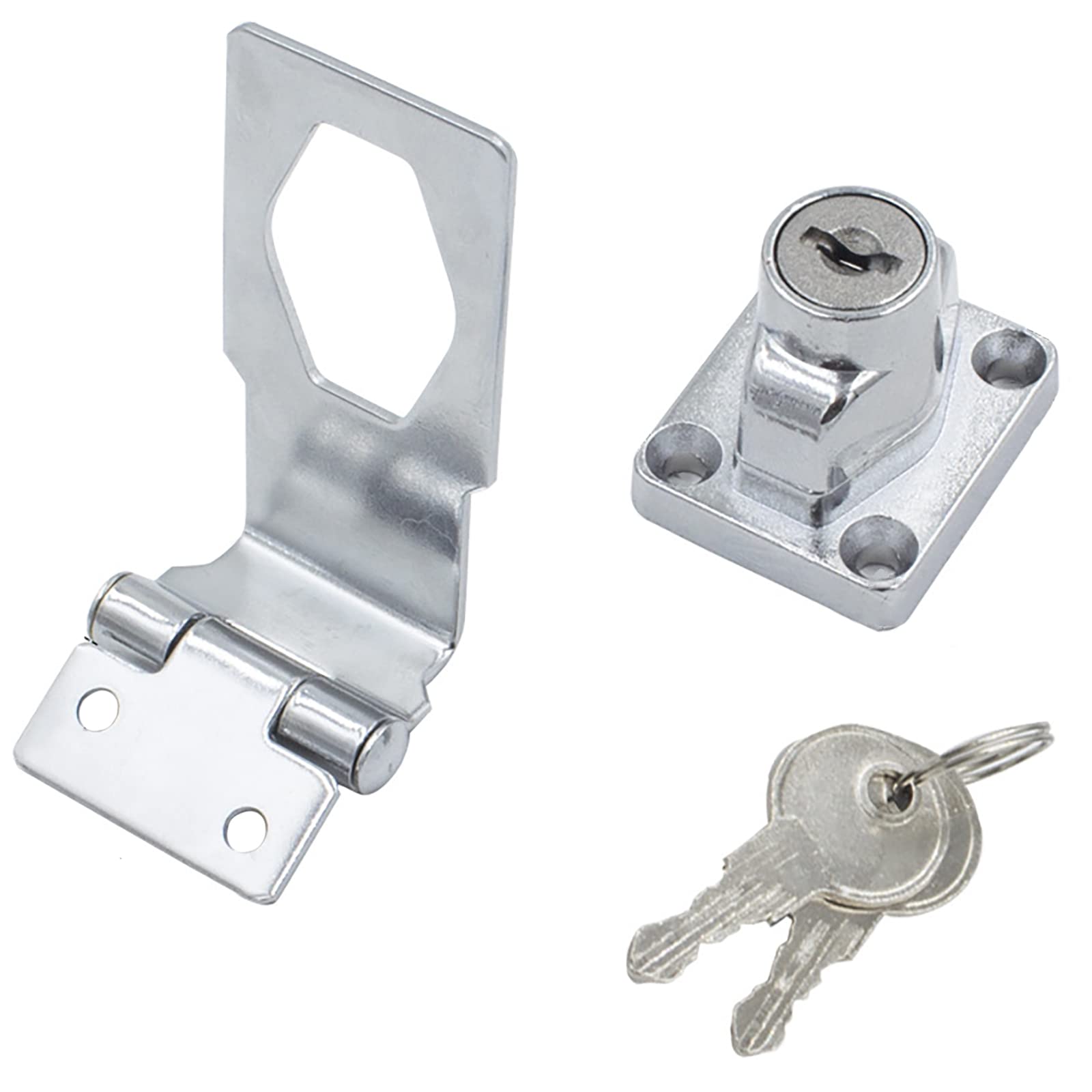
A stock image related to locks and latches.
Comprehensive Cost and Pricing Analysis for locks and latches Sourcing
What Are the Key Cost Components in Locks and Latches Sourcing?
When sourcing locks and latches, understanding the cost structure is critical for international B2B buyers. The main cost components include:
-
Materials: The type of materials used significantly impacts the pricing. Common materials include stainless steel, brass, and plastic, each with varying costs. High-quality materials often lead to higher prices but can enhance durability and security.
-
Labor: Labor costs vary by region, influenced by local wage standards and the complexity of manufacturing processes. Regions with lower labor costs may offer competitive pricing but could compromise on quality.
-
Manufacturing Overhead: This includes costs related to factory maintenance, utilities, and administrative expenses. Efficient operations can reduce overhead and subsequently lower pricing.
-
Tooling: Initial costs associated with molds and tooling for custom designs can be substantial. However, these costs may be amortized over larger production runs, making it crucial to consider the Minimum Order Quantity (MOQ).
-
Quality Control (QC): Implementing rigorous QC processes ensures product reliability, impacting overall costs. Suppliers with strong QC practices may charge higher prices but can reduce the risk of defects.
-
Logistics: Shipping costs are influenced by the weight and volume of the products, as well as the distance from the supplier. It’s essential to factor in logistics, especially for international shipments, which may involve customs duties and tariffs.
-
Margin: Suppliers will include their profit margin in the final pricing. This can vary widely based on market demand, competition, and the uniqueness of the product.
How Do Price Influencers Affect Locks and Latches Costs?
Several factors can influence the pricing of locks and latches:
-
Volume/MOQ: Purchasing in larger quantities typically allows buyers to negotiate better prices. Suppliers are often willing to offer discounts for bulk orders, which can significantly reduce the unit cost.
-
Specifications and Customization: Customized locks and latches will incur higher costs due to additional tooling and production complexities. Buyers should balance their needs for customization against the potential for increased expenses.
-
Materials: The choice of materials not only affects the initial cost but also the longevity and maintenance of the product. Higher-quality materials may lead to lower Total Cost of Ownership (TCO) over time.
-
Quality and Certifications: Products that meet international quality standards or certifications (such as ISO or ANSI grades) may command higher prices. These certifications can be crucial for buyers in regulated industries.
-
Supplier Factors: The supplier’s reputation, location, and market position can influence pricing. Established suppliers with proven track records may charge more but provide better reliability and service.
-
Incoterms: The terms of delivery agreed upon can impact overall costs. Buyers should understand the implications of different Incoterms (e.g., FOB, CIF) on shipping responsibilities and costs.
What Tips Can Help Buyers Negotiate Better Prices?
For international buyers, particularly in regions like Africa, South America, the Middle East, and Europe, here are actionable tips for negotiating better pricing:
-
Conduct Thorough Market Research: Understanding the market rates for locks and latches can empower buyers during negotiations. This includes knowing the average costs based on materials and specifications.
-
Leverage Total Cost of Ownership: When evaluating suppliers, consider not only the initial price but also the long-term costs associated with maintenance, durability, and warranties. This perspective can justify a higher upfront cost if it leads to savings over time.
-
Build Relationships: Establishing strong relationships with suppliers can lead to better terms and pricing. Regular communication and feedback can foster trust and encourage suppliers to offer favorable conditions.
-
Be Flexible with Specifications: If possible, being flexible with specifications can open the door to cost-saving alternatives. Consider standard designs that may have lower tooling costs.
-
Negotiate Payment Terms: Discussing extended payment terms can ease cash flow issues. Suppliers might be more willing to negotiate on price if they perceive a commitment to a long-term partnership.
In conclusion, understanding the comprehensive cost structure and pricing influencers, combined with effective negotiation strategies, can significantly enhance the purchasing process for locks and latches in international markets. Buyers should remain vigilant and informed to achieve the best value for their investments.
Alternatives Analysis: Comparing locks and latches With Other Solutions
Understanding Alternative Solutions to Locks and Latches
In the realm of security solutions, locks and latches are traditional methods for safeguarding properties and assets. However, with advancements in technology, several alternative solutions have emerged that can offer enhanced security, convenience, and cost-effectiveness. This section explores the comparative aspects of locks and latches against two notable alternatives: electronic access control systems and biometric security solutions.
Comparison Table of Locks and Latches Against Alternatives
Comparison Aspect | Locks And Latches | Electronic Access Control Systems | Biometric Security Solutions |
---|---|---|---|
Performance | Reliable for basic security; varies by type (e.g., deadbolts offer higher security). | High-security with audit trails; can be integrated with other systems. | Offers high accuracy and quick access; resistant to unauthorized duplication. |
Cost | Generally low upfront cost; replacement required over time. | Higher initial investment; ongoing costs for maintenance and updates. | Can be expensive due to technology and installation; cost-effective over time. |
Ease of Implementation | Simple installation; minimal training required. | Requires professional installation; user training needed for optimal use. | Installation can be complex; training necessary for effective use. |
Maintenance | Low maintenance; periodic lubrication and replacement needed. | Regular software updates and hardware maintenance required. | Requires regular calibration and updates; potential for malfunction if not maintained. |
Best Use Case | Suitable for residential and small commercial applications. | Ideal for large enterprises or facilities needing controlled access. | Best for high-security environments such as government buildings and data centers. |
Detailed Breakdown of Alternatives
What Are the Benefits of Electronic Access Control Systems?
Electronic access control systems utilize keycards, fobs, or mobile applications to grant access. These systems often include features like time-sensitive access and monitoring capabilities, allowing businesses to track who enters and exits a facility. The main advantage is enhanced security through the ability to revoke access instantly without needing to replace locks. However, the initial investment and ongoing maintenance can be significant, making it a better fit for larger organizations with a high volume of access management needs.
How Do Biometric Security Solutions Compare?
Biometric security solutions use unique biological traits such as fingerprints or facial recognition to grant access. These systems offer superior security as they are difficult to replicate or bypass. They are particularly beneficial in environments where security is paramount, such as banks or data centers. However, they come with a higher price tag and require regular maintenance and calibration to ensure accuracy. Additionally, they can face challenges in extreme environmental conditions, which could affect performance.
How Can B2B Buyers Choose the Right Security Solution?
When selecting the appropriate security solution, B2B buyers should consider their specific needs, budget constraints, and the environment where the solution will be implemented. For businesses focused on basic security needs and low upfront costs, traditional locks and latches might suffice. However, those requiring advanced security features, audit trails, or flexibility should explore electronic access control systems or biometric solutions. Ultimately, the decision should align with the organization’s operational goals and security requirements, ensuring both safety and efficiency in their operations.
Essential Technical Properties and Trade Terminology for locks and latches
What Are the Essential Technical Properties of Locks and Latches?
Understanding the technical specifications of locks and latches is crucial for international B2B buyers, especially when sourcing products from diverse markets such as Africa, South America, the Middle East, and Europe. Here are the key properties to consider:
1. Material Grade: What Should You Look For?
The material used in locks and latches significantly affects their durability and security. Common materials include stainless steel, brass, and zinc alloy. Stainless steel offers high corrosion resistance and strength, making it suitable for outdoor applications. Brass is often used for its aesthetic appeal and natural resistance to corrosion. Understanding material grades helps buyers select products that meet specific environmental and security needs, particularly in regions with varying climates.
2. Security Rating: How Is It Determined?
Security ratings, such as ANSI/BHMA grades (1-3), indicate the strength and durability of locks and latches. Grade 1 locks are the most secure and are typically used in commercial applications, while Grade 2 is suitable for residential use. Buyers should assess the security rating based on the application to ensure adequate protection, especially in high-risk areas.
3. Tolerance: Why Is It Important?
Tolerance refers to the permissible limit of variation in dimensions, which is vital for ensuring proper fit and function. A tight tolerance ensures that locks and latches operate smoothly and securely. In B2B transactions, understanding tolerance can help avoid compatibility issues during installation, which can lead to increased costs and delays.
4. Backset Measurement: What Does It Mean?
The backset measurement is the distance from the edge of the door to the center of the lock. Common backset sizes are 2-3/8 inches and 2-3/4 inches. Buyers must ensure that the backset matches their door specifications to avoid installation complications. Inaccurate measurements can lead to product returns and additional shipping costs.
5. Finish and Coating: How Do They Affect Performance?
The finish of a lock or latch not only contributes to its aesthetic appeal but also its performance. Common finishes include polished brass, satin nickel, and oil-rubbed bronze. These coatings can enhance resistance to wear, tarnishing, and corrosion. Buyers should consider both the functional and visual aspects of finishes, especially when outfitting commercial spaces or high-end residential properties.
What Are the Key Trade Terminologies in Locks and Latches?
Familiarizing yourself with common trade terms can streamline the procurement process and improve communication with suppliers.
1. OEM (Original Equipment Manufacturer): What Does It Signify?
An OEM is a company that produces parts or equipment that may be marketed by another manufacturer. In the locks and latches industry, understanding whether a product is OEM can inform buyers about its quality and compatibility with existing systems. This is particularly important for companies looking to maintain brand integrity.
2. MOQ (Minimum Order Quantity): Why Is It Crucial?
MOQ refers to the smallest quantity of a product that a supplier is willing to sell. This term is essential for B2B buyers to understand as it can affect budgeting and inventory management. Suppliers with high MOQs may not be suitable for smaller companies or those testing new products.
3. RFQ (Request for Quotation): How Should It Be Used?
An RFQ is a document sent to suppliers asking for pricing on specific products. It is a critical step in the purchasing process, allowing buyers to compare costs, terms, and availability. Crafting a precise RFQ can lead to better pricing and terms from suppliers.
4. Incoterms: What Are They and Why Do They Matter?
Incoterms are international commercial terms that define the responsibilities of buyers and sellers in international transactions. They clarify shipping costs, risk, and responsibilities, which is particularly important when sourcing locks and latches across different continents. Familiarity with Incoterms can help avoid disputes and ensure smooth delivery.
By understanding these essential technical properties and trade terminologies, international B2B buyers can make informed decisions when sourcing locks and latches, ensuring they select the right products for their specific needs and markets.
Navigating Market Dynamics and Sourcing Trends in the locks and latches Sector
What Are the Current Market Dynamics and Key Trends in the Locks and Latches Sector?
The locks and latches market is increasingly influenced by globalization, technological advancements, and evolving consumer preferences. International B2B buyers, especially from regions like Africa, South America, the Middle East, and Europe, are observing a shift toward smart locking solutions and electronic access control systems. These innovations not only enhance security but also offer convenience and integration with smart home systems. For instance, the rise of IoT (Internet of Things) has led to the development of locks that can be controlled via smartphones or voice assistants, catering to a tech-savvy clientele.
Furthermore, the demand for customizable solutions is surging. Buyers are seeking products that can be tailored to specific security needs or architectural styles, prompting manufacturers to offer a broader range of designs and functionalities. In addition, the market is witnessing a trend toward modular locking systems, which allow for easy upgrades and maintenance, appealing to property managers and commercial buyers looking for long-term value.
Economic conditions and regional stability also play critical roles in shaping market dynamics. Buyers in emerging markets, such as those in Africa and South America, are increasingly prioritizing cost-effective solutions that do not compromise on quality. This has led to a rise in local manufacturing and sourcing initiatives, as companies seek to minimize costs and support local economies.
How Is Sustainability Influencing Sourcing Practices in the Locks and Latches Sector?
Sustainability is becoming a central theme in the sourcing strategies of B2B buyers in the locks and latches sector. As environmental concerns gain prominence, companies are increasingly focusing on the environmental impact of their products and supply chains. This includes a shift toward using recycled materials and sustainable manufacturing processes. For instance, locks and latches made from recycled metals not only reduce waste but also appeal to environmentally-conscious consumers.
Moreover, ethical sourcing practices are gaining traction. Buyers are demanding transparency in the supply chain, ensuring that materials are sourced responsibly and that labor practices meet ethical standards. Certifications such as Forest Stewardship Council (FSC) and ISO 14001 are becoming essential for suppliers aiming to establish credibility in the market.
Investing in ‘green’ certifications is not just a compliance measure; it can also serve as a competitive advantage. Buyers are increasingly inclined to partner with manufacturers who demonstrate a commitment to sustainability, as this aligns with their corporate social responsibility goals. As a result, companies that prioritize sustainability in their sourcing practices can enhance their brand reputation and appeal to a broader customer base.
What Is the Historical Context of Locks and Latches Development?
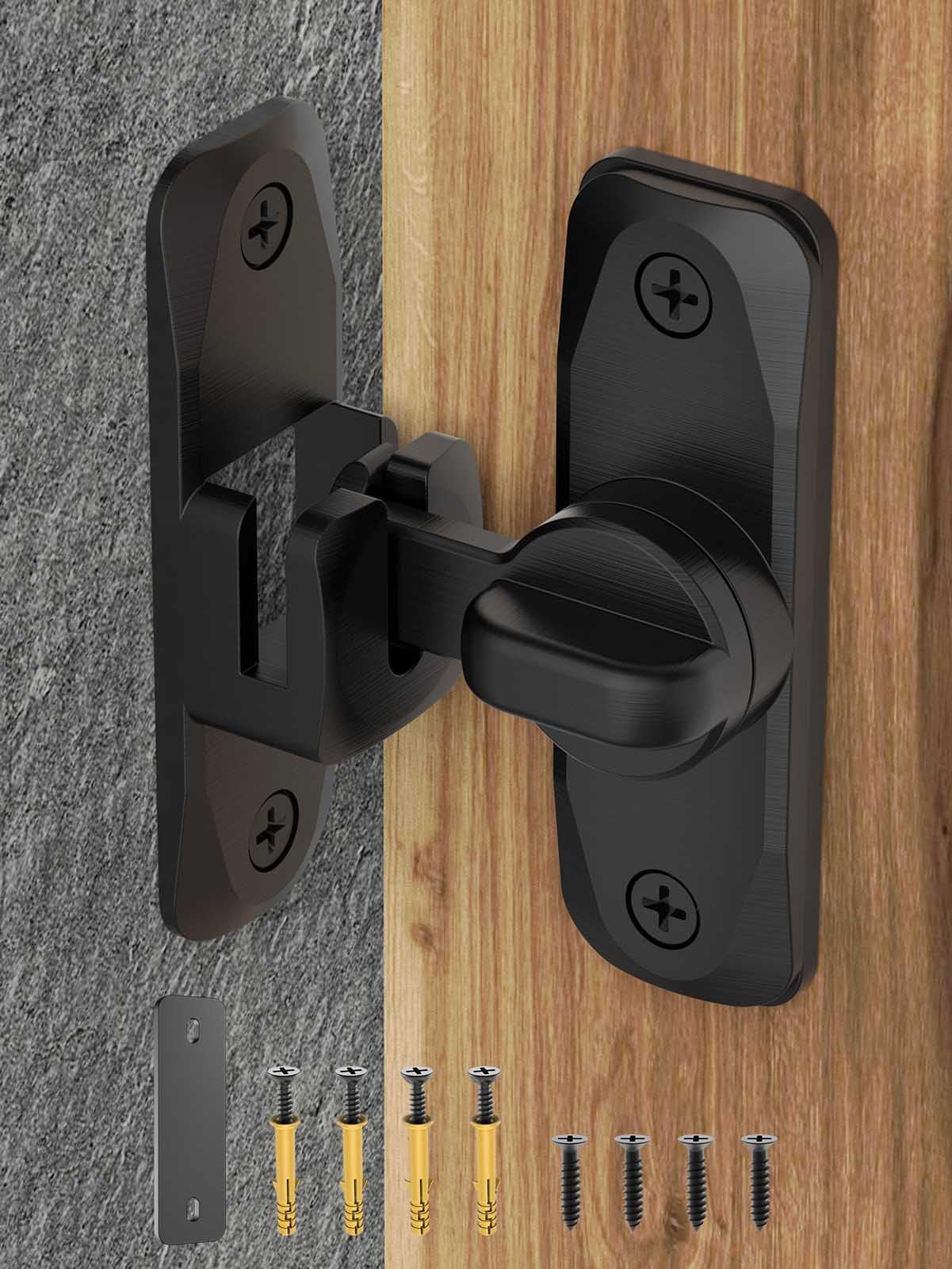
A stock image related to locks and latches.
The evolution of locks and latches dates back thousands of years, with early forms emerging in ancient civilizations such as Egypt and Rome. Initially, locks were crafted from wood and metal, serving primarily to secure doors and possessions. The introduction of more sophisticated locking mechanisms in the 19th century, such as the pin tumbler lock, revolutionized the industry, providing enhanced security and reliability.
In recent decades, technological advancements have further transformed the sector. The advent of electronic locks, smart technology, and integrated access control systems has changed how consumers and businesses approach security. Today, the locks and latches market is not only about physical security but also about integrating technology to meet modern demands, shaping the future of security solutions in both residential and commercial applications.
By understanding these market dynamics, sustainability trends, and historical contexts, international B2B buyers can make informed decisions that align with current industry standards and future developments in the locks and latches sector.
Frequently Asked Questions (FAQs) for B2B Buyers of locks and latches
-
How do I choose the right locks and latches for my business needs?
Choosing the right locks and latches involves assessing the specific security requirements of your operations. Consider factors such as the type of door (interior vs. exterior), the frequency of use, and the level of security needed. For commercial applications, ANSI grades can help determine the reliability of the lock. It’s also essential to evaluate the materials used in the locks, especially in humid or corrosive environments common in regions like Africa and South America. Consulting with suppliers who offer customized solutions can provide additional insights tailored to your business. -
What are the best types of locks and latches for international shipping?
When sourcing locks and latches for international shipping, opt for products that are durable, tamper-resistant, and compliant with international security standards. Deadbolts and electronic locks often provide higher security levels, while latches with a robust locking mechanism are ideal for shipping containers. Ensure that your chosen locks are also lightweight and easy to install, as this can significantly reduce shipping costs and installation time in your target markets across Europe and the Middle East. -
What customization options should I consider when sourcing locks and latches?
Customization options can include specific finishes, sizes, and locking mechanisms tailored to your operational needs. Some manufacturers offer branding options, allowing you to add your logo to the products. Additionally, consider whether you require features such as keyless entry, smart technology integration, or specialized locking systems for unique applications. Discussing these options early in the sourcing process can help align the product specifications with your operational requirements. -
What is the minimum order quantity (MOQ) for locks and latches from suppliers?
Minimum order quantities (MOQs) can vary significantly among suppliers and are often influenced by the type of product and the level of customization required. Many manufacturers have standard MOQs ranging from 100 to 1,000 units, while others may offer flexibility for bulk orders. It’s advisable to negotiate MOQs, especially if you are a smaller business or looking to test a new product line before committing to larger quantities. -
How do I vet suppliers of locks and latches for international trade?
Vetting suppliers involves assessing their credibility, product quality, and compliance with international standards. Start by checking reviews and testimonials from other B2B buyers, and request samples to evaluate product quality firsthand. Verify certifications, such as ISO or ANSI, which can indicate adherence to industry standards. Additionally, consider suppliers who have experience exporting to your target regions, as they will be familiar with local regulations and logistics challenges. -
What payment terms should I negotiate when sourcing locks and latches?
Negotiating payment terms is crucial for managing cash flow and reducing risk. Common terms include a percentage upfront, with the balance due upon delivery or after a specific period post-delivery. Consider using escrow services for larger orders to ensure security for both parties. It’s also beneficial to inquire about payment methods accepted by the supplier, as some may offer discounts for early payments or specific payment methods. -
How can I ensure quality assurance when purchasing locks and latches?
Quality assurance (QA) can be ensured through several strategies, including requesting detailed product specifications, third-party inspections, and certifications. Establishing clear quality control processes with your supplier can help mitigate risks. Additionally, consider implementing a return policy that allows for returns in case of defects or non-compliance with agreed specifications. Regular audits and supplier assessments can also contribute to maintaining high standards. -
What logistics considerations should I keep in mind when importing locks and latches?
Logistics considerations include shipping methods, customs regulations, and delivery timelines. It’s essential to work with a freight forwarder experienced in handling hardware products to navigate any specific import regulations in your target market. Ensure that your supplier can provide the necessary documentation for customs clearance, and consider the potential for delays in shipping. Additionally, assess warehousing options if you plan to hold inventory before distribution to your customers.
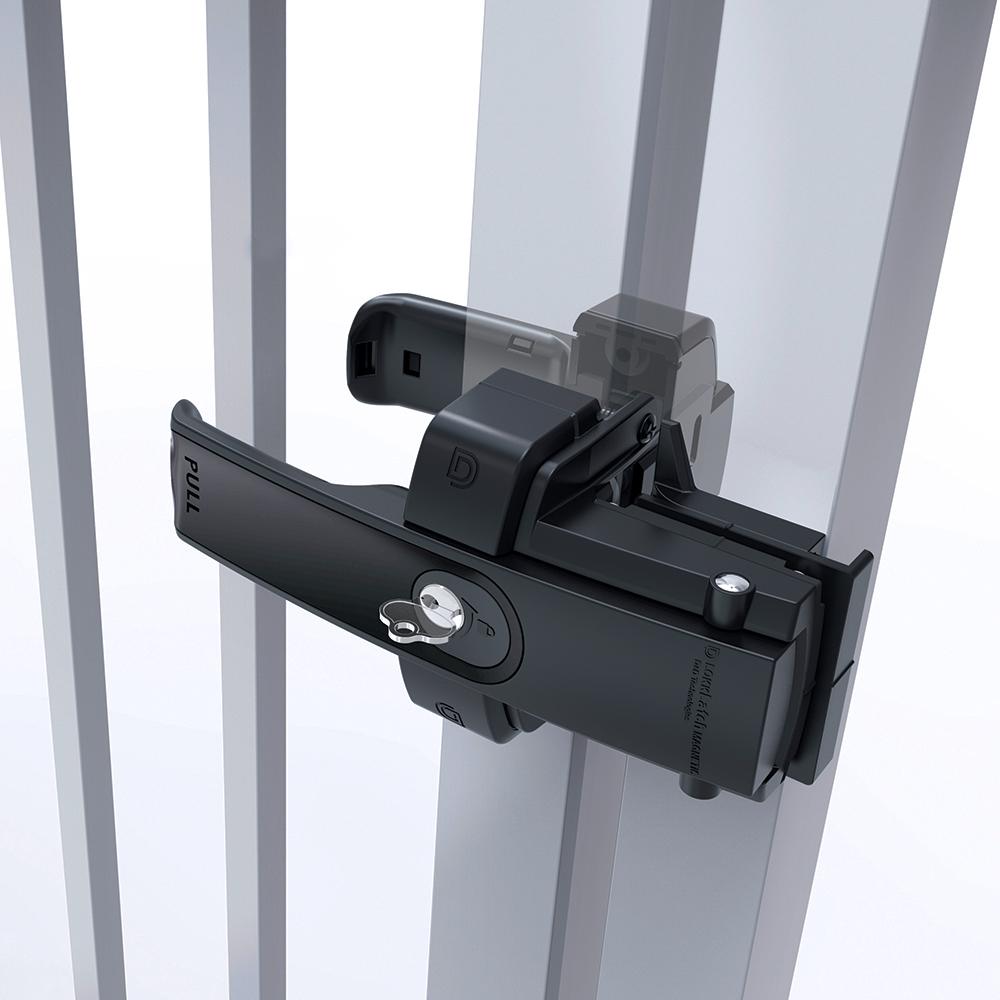
A stock image related to locks and latches.
Important Disclaimer & Terms of Use
⚠️ Important Disclaimer
The information provided in this guide, including content regarding manufacturers, technical specifications, and market analysis, is for informational and educational purposes only. It does not constitute professional procurement advice, financial advice, or legal advice.
While we have made every effort to ensure the accuracy and timeliness of the information, we are not responsible for any errors, omissions, or outdated information. Market conditions, company details, and technical standards are subject to change.
B2B buyers must conduct their own independent and thorough due diligence before making any purchasing decisions. This includes contacting suppliers directly, verifying certifications, requesting samples, and seeking professional consultation. The risk of relying on any information in this guide is borne solely by the reader.
Strategic Sourcing Conclusion and Outlook for locks and latches
What Are the Key Takeaways for B2B Buyers in Locks and Latches?
In summary, strategic sourcing in the locks and latches market is essential for ensuring quality, cost-effectiveness, and reliability. B2B buyers must prioritize suppliers that offer a comprehensive range of products, including traditional and smart locking solutions, while also focusing on the latest security technologies. Understanding the unique requirements of your market—whether in Africa, South America, the Middle East, or Europe—can help tailor your purchasing decisions to meet local demands effectively.
How Can Buyers Enhance Their Sourcing Strategy?
Investing time in supplier evaluations, comparing product specifications, and analyzing pricing structures will empower buyers to make informed decisions. Leverage data analytics to forecast trends in security needs and anticipate future demands. Establishing strong relationships with manufacturers can also lead to better pricing, exclusive offers, and priority access to new innovations.
What Does the Future Hold for Locks and Latches?
Looking ahead, the locks and latches industry is poised for growth driven by advancements in technology and increasing security concerns. As smart locking systems gain popularity, buyers should remain adaptable and open to integrating new solutions into their offerings. Engage with suppliers who can provide insights into emerging trends and technologies to stay competitive in this evolving landscape. Now is the time to take proactive steps in your sourcing strategy to secure the best products for your business.