Your Ultimate Guide to Sourcing 7 Axis Cnc Machine
Introduction: Navigating the Global Market for 7 axis cnc machine
When it comes to modern manufacturing, 7-axis CNC machines represent a transformative leap forward, offering unparalleled precision and efficiency. For international B2B buyers, particularly from regions such as Africa, South America, the Middle East, and Europe, understanding the capabilities and advantages of these machines is critical for maintaining a competitive edge. As industries evolve, the demand for complex, high-precision parts in sectors like aerospace, automotive, and medical continues to rise, making 7-axis CNC machines indispensable for meeting these challenges.
This comprehensive guide serves as an essential resource for B2B buyers looking to navigate the global market for 7-axis CNC machines. It covers various aspects, including the different types of machines available, compatible materials, manufacturing and quality control processes, and a detailed overview of suppliers. Additionally, we delve into cost considerations and provide answers to frequently asked questions, ensuring that you are well-equipped to make informed sourcing decisions.
By leveraging the insights and knowledge contained in this guide, buyers can confidently select the right 7-axis CNC machine to enhance their manufacturing capabilities. The information provided will not only empower you to optimize production processes but also help you achieve superior quality and reduce lead times—key factors for success in today’s competitive landscape.
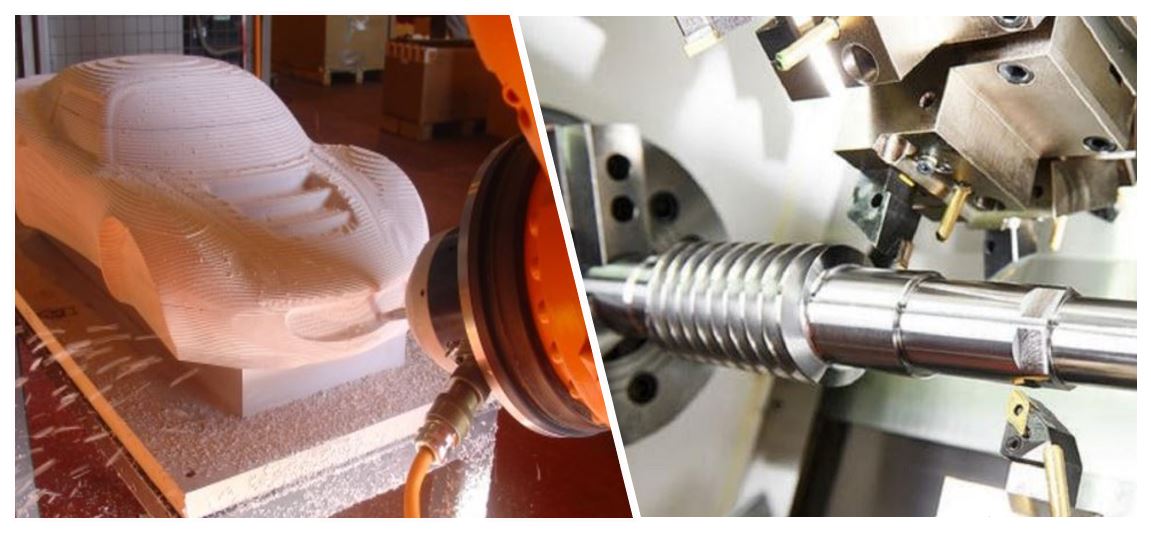
Illustrative Image (Source: Google Search)
Understanding 7 axis cnc machine Types and Variations
Type Name | Key Distinguishing Features | Primary B2B Applications | Brief Pros & Cons for Buyers |
---|---|---|---|
7-Axis CNC Mill | Combines linear and rotational axes for complex cuts | Aerospace, Automotive | Pros: High precision, reduces setup time. Cons: Higher initial investment costs. |
7-Axis CNC Lathe | Designed for turning operations with added rotation | Medical devices, Aerospace | Pros: Excellent for cylindrical parts, increased efficiency. Cons: Limited to rotationally symmetric parts. |
7-Axis CNC Router | Utilizes a large working area for various materials | Furniture, Signage, Prototyping | Pros: Versatile for different materials, cost-effective. Cons: May lack precision for intricate designs. |
7-Axis Multi-Tasking Machine | Integrates milling and turning in one setup | Aerospace, Defense, Automotive | Pros: Streamlines production, reduces handling time. Cons: Complex programming, requires skilled operators. |
7-Axis Robotic Arm | Employs robotic technology for flexible machining | Custom fabrication, Automation | Pros: High adaptability, can work in confined spaces. Cons: Potentially higher operational costs, maintenance challenges. |
7-Axis CNC Mill
The 7-axis CNC mill is characterized by its ability to perform intricate machining operations through a combination of linear (X, Y, Z) and rotational (A, B, C) movements. This machine is particularly suitable for industries that demand high precision, such as aerospace and automotive. When considering a purchase, buyers should evaluate the machine’s software compatibility, size, and the complexity of the parts they intend to produce. While the initial investment can be significant, the efficiency gains and precision offered often justify the expense.
7-Axis CNC Lathe
The 7-axis CNC lathe is specifically designed for turning operations, enabling the machining of cylindrical parts with enhanced precision. It incorporates additional rotational axes, allowing for complex geometries and features to be produced in one setup. This type of machine is ideal for applications in the medical device and aerospace sectors, where precision is paramount. Buyers should consider the materials they will be working with and the lathe’s capabilities to handle those materials, as well as the machine’s overall size and footprint.
7-Axis CNC Router
The 7-axis CNC router is distinguished by its large working area and versatility in handling various materials, from wood to plastics and metals. This machine is commonly used in industries such as furniture manufacturing, signage, and prototyping. While it offers a cost-effective solution for a wide range of applications, buyers should be aware that it may not provide the same level of precision as other types of 7-axis machines. Evaluating the specific needs of their projects and the expected tolerances will be crucial for potential buyers.
7-Axis Multi-Tasking Machine
A 7-axis multi-tasking machine integrates both milling and turning capabilities, allowing manufacturers to perform multiple operations in a single setup. This machine is particularly beneficial for sectors like aerospace, defense, and automotive, where complex parts need to be produced efficiently. Buyers should consider the machine’s programming complexity and the skill level required for operators, as these factors can impact overall productivity. The reduction in handling time and setup can lead to significant operational savings, making it an attractive option.
7-Axis Robotic Arm
The 7-axis robotic arm employs advanced robotic technology for machining tasks, offering high adaptability and flexibility in production. This type of machine is particularly useful in custom fabrication and automated processes, where space constraints may limit traditional machining options. Buyers should consider the operational costs and maintenance requirements associated with robotic systems, as they can be higher than traditional CNC machines. However, the ability to perform tasks in confined spaces and the potential for automation make this option appealing for innovative manufacturing environments.
Related Video: 7-Axis CNC Machining Robot at ZOOX – Vlog #39
Key Industrial Applications of 7 axis cnc machine
Industry/Sector | Specific Application of 7 axis cnc machine | Value/Benefit for the Business | Key Sourcing Considerations for this Application |
---|---|---|---|
Aerospace | Manufacturing complex turbine blades | Achieves high precision and reduces the need for multiple setups. | Ensure machine can handle high-strength materials and has advanced cooling systems. |
Automotive | Producing intricate engine components | Enhances efficiency by machining multiple features in one setup. | Look for machines with robust software compatibility and high-speed capabilities. |
Medical Devices | Creating custom implants and surgical instruments | Delivers superior accuracy for critical applications, reducing errors. | Verify compliance with medical standards and ensure precision tooling options. |
Military Equipment | Fabricating complex parts for defense systems | Facilitates tight tolerances and complex geometries in one process. | Check for durability and reliability in harsh operating conditions. |
Oil & Gas | Machining components for drilling and extraction tools | Improves production efficiency and reduces lead times significantly. | Assess the machine’s ability to work with tough materials and its maintenance requirements. |
Aerospace Industry Applications
In the aerospace sector, 7-axis CNC machines are pivotal for manufacturing complex turbine blades. These components require exceptional precision and intricate designs that traditional machines struggle to achieve. By utilizing a 7-axis machine, manufacturers can produce turbine blades in a single setup, eliminating the need for multiple machining processes, which significantly reduces production time and potential errors. For international buyers, especially in regions like Turkey and Kenya, sourcing machines that can handle high-strength alloys and incorporate advanced cooling systems is essential to meet stringent aerospace standards.
Automotive Sector Applications
The automotive industry benefits greatly from 7-axis CNC machining in the production of intricate engine components. These machines allow for the simultaneous machining of multiple features, enhancing efficiency and reducing cycle times. For B2B buyers in South America, selecting machines that offer robust software compatibility and high-speed capabilities is crucial, as these features can significantly improve throughput and maintain quality control in high-volume production environments.
Medical Devices Applications
In the medical field, 7-axis CNC machines are used to create custom implants and surgical instruments with superior accuracy. The ability to produce complex geometries in one setup is vital for ensuring that medical devices meet strict regulatory standards and perform reliably in critical applications. International buyers, particularly from Africa, should prioritize sourcing machines that comply with medical manufacturing regulations and offer a range of precision tooling options to cater to diverse medical needs.
Military Equipment Manufacturing
The military sector relies on 7-axis CNC machining for fabricating complex parts used in defense systems. These machines are capable of achieving tight tolerances and intricate designs, which are often required for sensitive military applications. Buyers in regions like the Middle East must ensure that the machines they source are durable and reliable, capable of functioning effectively in harsh environments while maintaining high precision.
Oil & Gas Industry Applications
In the oil and gas sector, 7-axis CNC machines are crucial for machining components used in drilling and extraction tools. The efficiency gained from producing complex parts in a single setup can lead to significant reductions in lead times and costs. For B2B buyers, particularly in regions with challenging resource environments, it is important to assess the machine’s capability to work with tough materials and its overall maintenance requirements to ensure long-term operational success.
Strategic Material Selection Guide for 7 axis cnc machine
When selecting materials for 7-axis CNC machining, it is crucial to consider properties that align with the intended application, manufacturing capabilities, and regional standards. Below is an analysis of four common materials used in 7-axis CNC machining, focusing on their properties, advantages, disadvantages, and considerations for international B2B buyers.
Aluminum Alloys
Key Properties:
Aluminum alloys are lightweight, have excellent corrosion resistance, and good thermal conductivity. They typically exhibit a temperature rating of up to 150°C, making them suitable for various applications.
Pros & Cons:
Aluminum is easy to machine, leading to lower manufacturing complexity and costs. However, while it offers good strength-to-weight ratios, it may not withstand high-pressure applications as effectively as other metals.
Impact on Application:
Aluminum is widely used in aerospace and automotive applications where weight reduction is critical. Its compatibility with various media makes it versatile for many industries.
Considerations for International Buyers:
Buyers should ensure compliance with standards like ASTM B221 for aluminum extrusions. In regions like Africa and South America, sourcing local suppliers can reduce costs and lead times.
Stainless Steel
Key Properties:
Stainless steel is known for its high strength, excellent corrosion resistance, and ability to withstand high temperatures (up to 800°C). It is often used in environments that require hygiene and durability.
Pros & Cons:
While stainless steel is highly durable and suitable for demanding applications, it can be more challenging to machine compared to aluminum, leading to higher manufacturing costs. Additionally, it is heavier, which may not be ideal for all applications.
Impact on Application:
This material is ideal for medical devices, food processing equipment, and aerospace components due to its corrosion resistance and strength.
Considerations for International Buyers:
Compliance with standards such as ASTM A240 is essential. Buyers in Europe and the Middle East should be aware of local regulations regarding food safety and medical device manufacturing.
Titanium Alloys
Key Properties:
Titanium alloys are known for their exceptional strength-to-weight ratio and excellent corrosion resistance, particularly in extreme environments. They can withstand temperatures up to 600°C.
Pros & Cons:
Titanium is highly durable and suitable for aerospace and medical applications but is more expensive and complex to machine. This can lead to increased manufacturing costs and longer lead times.
Impact on Application:
Due to its biocompatibility and strength, titanium is often used in medical implants and aerospace components where performance is critical.
Considerations for International Buyers:
Buyers should consider compliance with ASTM F136 for medical applications. In regions like Turkey and South Africa, sourcing titanium may require navigating import regulations and tariffs.
Engineering Plastics (e.g., PEEK)
Key Properties:
Engineering plastics like PEEK (Polyether Ether Ketone) offer high chemical resistance, excellent thermal stability (up to 260°C), and good mechanical properties.
Pros & Cons:
These materials are lightweight and easy to machine, making them suitable for complex geometries. However, they can be more expensive than metals and may not be suitable for high-load applications.
Impact on Application:
PEEK is often used in the aerospace and medical industries for components that require high performance in harsh environments.
Considerations for International Buyers:
Ensure compliance with relevant standards such as ASTM D638 for plastics. Buyers in Europe should be aware of REACH regulations regarding chemical safety.
Summary Table
Material | Typical Use Case for 7 axis cnc machine | Key Advantage | Key Disadvantage/Limitation | Relative Cost (Low/Med/High) |
---|---|---|---|---|
Aluminum Alloys | Aerospace, automotive components | Lightweight and easy to machine | Limited high-pressure applications | Medium |
Stainless Steel | Medical devices, food processing | High durability and corrosion resistance | More challenging to machine | High |
Titanium Alloys | Aerospace components, medical implants | Exceptional strength-to-weight ratio | Expensive and complex to machine | High |
Engineering Plastics (PEEK) | Aerospace, medical components | High chemical resistance and lightweight | Higher cost and load limitations | Medium to High |
This strategic material selection guide provides actionable insights for international B2B buyers, enabling them to make informed decisions based on material properties, application suitability, and regional considerations.
In-depth Look: Manufacturing Processes and Quality Assurance for 7 axis cnc machine
The manufacturing process for 7-axis CNC machines involves several intricate stages, each designed to ensure the highest level of precision and quality. For B2B buyers, particularly those in Africa, South America, the Middle East, and Europe, understanding these processes is critical for making informed purchasing decisions. This section provides an in-depth look at the typical manufacturing processes and quality assurance measures associated with 7-axis CNC machines.
Manufacturing Processes
1. Material Preparation
The first step in the manufacturing process involves the selection and preparation of raw materials. Common materials used in 7-axis CNC machining include aluminum, steel, titanium, and various plastics.
- Material Selection: Choosing the right material is crucial as it affects the machine’s performance and the quality of the final product. Factors to consider include tensile strength, machinability, and resistance to wear.
- Cutting and Sizing: Raw materials are cut to size using saws or lasers to ensure they fit the machine’s specifications. Proper sizing is essential to minimize waste and reduce production costs.
2. Forming
Once the materials are prepared, they undergo the forming process, where the actual machining takes place.
- CNC Programming: The design files (often in CAD format) are translated into machine language through CNC programming. This step includes defining the tool paths and machining parameters.
- Machining Operations: The 7-axis CNC machine begins to operate, utilizing its multiple axes to perform various operations such as milling, drilling, and turning. The ability to move in seven directions allows for complex geometries to be machined in a single setup, enhancing efficiency and accuracy.
3. Assembly
After the machining operations are complete, the next stage involves assembling any sub-components.
- Component Integration: Various machined parts are assembled to create the final product. This may involve the integration of electronic components, motors, and control systems.
- Alignment and Calibration: Ensuring that all components are aligned and calibrated correctly is vital for the machine’s performance. This step often requires precision tools and fixtures to guarantee that tolerances are met.
4. Finishing
The finishing process is where the machine’s surface quality is refined and any necessary treatments are applied.
- Surface Treatment: Techniques such as anodizing, plating, or polishing may be employed to enhance the machine’s durability and aesthetic appeal.
- Final Inspection: Before leaving the factory, each machine undergoes a final inspection to ensure it meets the specified quality standards.
Quality Assurance
Quality assurance is an integral part of the manufacturing process for 7-axis CNC machines. Adhering to international standards not only ensures product reliability but also helps B2B buyers mitigate risks associated with purchasing machinery.
Relevant International Standards
- ISO 9001: This quality management standard ensures that organizations meet customer and regulatory requirements consistently. Suppliers of 7-axis CNC machines should be certified to ISO 9001 to guarantee a standardized approach to quality.
- CE Marking: For buyers in Europe, ensuring that machines carry the CE marking is essential. This certification indicates conformity with health, safety, and environmental protection standards.
- API Standards: In industries such as oil and gas, compliance with American Petroleum Institute (API) standards is crucial, particularly for components that will be used in critical applications.
Quality Control Checkpoints
Quality control checkpoints are established throughout the manufacturing process to ensure that each stage meets the required standards.
- Incoming Quality Control (IQC): This initial checkpoint involves inspecting raw materials upon arrival to confirm they meet specified standards.
- In-Process Quality Control (IPQC): During the machining operations, regular checks are performed to monitor key parameters such as dimensional accuracy and surface finish.
- Final Quality Control (FQC): The final inspection involves comprehensive testing of the assembled machine to ensure it operates within defined specifications.
Common Testing Methods
B2B buyers should be aware of the following testing methods used during the quality assurance process:
- Dimensional Inspection: Utilizing tools such as calipers and coordinate measuring machines (CMM) to verify that machined parts meet dimensional tolerances.
- Functional Testing: Ensuring that all machine functions operate correctly under simulated conditions.
- Material Testing: Conducting tests such as tensile strength and hardness tests to verify material properties.
Verifying Supplier Quality Control
B2B buyers must take proactive steps to verify that their suppliers maintain rigorous quality control standards. Here are some strategies:
- Audits: Conducting on-site audits of potential suppliers can provide insight into their manufacturing processes and quality control measures.
- Quality Control Reports: Requesting detailed quality control reports can help assess a supplier’s commitment to maintaining high standards.
- Third-Party Inspections: Engaging third-party inspection services can add an additional layer of verification, ensuring that the supplier’s claims about quality are substantiated.
Quality Control Nuances for International Buyers
For international B2B buyers, particularly in regions like Africa, South America, the Middle East, and Europe, understanding the nuances of quality control is essential:
- Regulatory Compliance: Familiarize yourself with local regulations and standards that may differ from international norms. For example, CE marking is critical in Europe but may not be recognized in other regions.
- Cultural Differences: Recognize that cultural differences can influence quality perceptions and practices. Establish clear communication channels to address any concerns.
- Supply Chain Transparency: Ensure that suppliers provide transparent information about their sourcing, manufacturing, and quality control practices.
By understanding the manufacturing processes and quality assurance measures associated with 7-axis CNC machines, B2B buyers can make informed decisions that align with their operational needs and quality expectations. This knowledge not only empowers buyers to select the right suppliers but also helps mitigate risks associated with international procurement.
Related Video: The World’s Largest Bevel Gear CNC Machine- Modern Gear Production Line. Steel Wheel Manufacturing
Comprehensive Cost and Pricing Analysis for 7 axis cnc machine Sourcing
When sourcing a 7-axis CNC machine, understanding the cost structure and pricing dynamics is crucial for international B2B buyers. The costs associated with these advanced machines can be multifaceted, influenced by various components and factors. Below is a detailed analysis to aid buyers in making informed purchasing decisions.
Cost Components
-
Materials: The primary materials used in manufacturing 7-axis CNC machines include high-grade steel and aluminum for the frame, and specialized alloys for components like spindles and cutting tools. The quality of materials directly impacts both the machine’s durability and performance.
-
Labor: Skilled labor is essential in the production of 7-axis CNC machines. Labor costs vary significantly based on geographic location, with higher costs typically found in regions with stringent labor laws and higher living standards.
-
Manufacturing Overhead: This encompasses all indirect costs associated with production, such as utilities, facility maintenance, and equipment depreciation. Efficient manufacturing processes can help reduce these overhead costs.
-
Tooling: Tooling costs involve the specific equipment used for machining processes. Custom tooling can be expensive but necessary for achieving precise specifications, particularly for complex geometries.
-
Quality Control (QC): Given the precision required in 7-axis machining, robust quality control measures are mandatory. QC costs can include testing equipment, inspection processes, and certification fees, especially for industries like aerospace and medical where compliance with international standards is critical.
-
Logistics: The logistics of transporting a 7-axis CNC machine can significantly affect overall costs. This includes shipping, insurance, and handling fees, which can vary based on the origin and destination. International buyers should be aware of potential tariffs and import duties.
-
Margin: Supplier profit margins can fluctuate based on market demand, competition, and production efficiencies. Typically, margins for CNC machine manufacturers can range from 10% to 30%, influenced by the machine’s complexity and the manufacturer’s reputation.
Price Influencers
-
Volume/MOQ: Manufacturers often provide discounts for bulk purchases. Buyers should consider their production needs to negotiate favorable pricing based on Minimum Order Quantity (MOQ).
-
Specifications/Customization: Custom features and specifications can significantly affect pricing. Tailored machines for specific applications may incur higher costs, but they can provide a competitive advantage.
-
Materials: The choice of materials can influence price. Premium materials may enhance performance but at a higher cost. Buyers must balance performance needs with budget constraints.
-
Quality/Certifications: Machines that meet international quality standards (like ISO certifications) often command higher prices. However, they may reduce long-term operational risks and maintenance costs.
-
Supplier Factors: The supplier’s reputation, location, and relationship history can impact pricing. Established suppliers may charge a premium for their expertise and reliability.
-
Incoterms: Understanding Incoterms is essential for international transactions. They dictate who is responsible for shipping, insurance, and tariffs, which can significantly affect the total cost.
Buyer Tips
-
Negotiation: Always negotiate pricing, especially if purchasing multiple units. Leverage quotes from multiple suppliers to strengthen your position.
-
Cost-Efficiency: Evaluate the Total Cost of Ownership (TCO), which includes purchase price, maintenance, and operational costs. A lower initial price might not always be the most economical choice over time.
-
Pricing Nuances: Buyers from Africa, South America, the Middle East, and Europe should be aware of regional economic factors that may influence pricing, such as currency fluctuations and local demand.
-
Disclaimer for Indicative Prices: Prices for 7-axis CNC machines can vary widely based on the above factors. It is essential for buyers to conduct thorough market research and obtain detailed quotes from potential suppliers to ensure accurate budgeting.
By understanding these cost components and pricing influencers, international B2B buyers can better navigate the complexities of sourcing 7-axis CNC machines, ensuring they make informed and strategic purchasing decisions.
Spotlight on Potential 7 axis cnc machine Manufacturers and Suppliers
This section looks at several manufacturers active in the ‘7 axis cnc machine’ market. This is a representative sample for illustrative purposes; B2B buyers must conduct extensive due diligence before any transaction. Information is synthesized from public sources and general industry knowledge.
Essential Technical Properties and Trade Terminology for 7 axis cnc machine
Key Technical Properties of 7-Axis CNC Machines
When considering the acquisition of a 7-axis CNC machine, several critical technical specifications are essential for ensuring optimal performance and suitability for your specific manufacturing needs. Here are some key properties to keep in mind:
-
Material Grade
– Definition: The material grade refers to the type of materials the CNC machine can effectively process, such as aluminum, titanium, plastics, or composites.
– B2B Importance: Understanding the compatible material grades is vital for businesses that require specific materials for their products. This knowledge ensures that the machine can handle the materials required for your applications without compromising quality or performance. -
Tolerance
– Definition: Tolerance is the allowable deviation from a specified dimension in the machined part, typically expressed in millimeters or microns.
– B2B Importance: High precision is crucial in industries such as aerospace and medical devices, where even minor deviations can lead to significant issues. Knowing the machine’s tolerance capabilities helps buyers determine if it meets their exacting quality standards. -
Spindle Speed
– Definition: This refers to the rotational speed of the spindle, usually measured in revolutions per minute (RPM).
– B2B Importance: Higher spindle speeds can enhance machining efficiency and allow for finer finishes. Buyers should assess spindle speed in relation to the materials they intend to use to ensure optimal machining conditions. -
Axis Configuration
– Definition: The arrangement and type of axes (linear and rotary) that the machine can operate on.
– B2B Importance: A 7-axis CNC machine offers advanced capabilities for complex parts manufacturing. Understanding the axis configuration is crucial for buyers looking to produce intricate designs without needing multiple setups, thus improving efficiency. -
Control System
– Definition: The control system refers to the software and hardware used to operate the CNC machine, which translates CAD designs into machining instructions.
– B2B Importance: A sophisticated control system can enhance the machine’s capabilities and ease of use. Buyers should ensure that the control system is compatible with their existing design software and can handle the complexity of their projects. -
Workholding Capacity
– Definition: This is the maximum size and weight of the workpiece that the machine can securely hold during machining.
– B2B Importance: Knowing the workholding capacity is essential for ensuring that the machine can accommodate the parts your business intends to manufacture, which can influence production efficiency and safety.
Common Trade Terminology in CNC Machining
Familiarity with industry-specific jargon can facilitate better communication and negotiation with suppliers and partners. Here are several common terms related to 7-axis CNC machining:
-
OEM (Original Equipment Manufacturer)
– Definition: A company that produces parts or equipment that may be marketed by another manufacturer.
– Importance: Understanding OEM relationships can help businesses identify reliable suppliers for custom parts and components. -
MOQ (Minimum Order Quantity)
– Definition: The smallest quantity of a product that a supplier is willing to sell.
– Importance: Knowing the MOQ helps buyers plan their purchasing strategies and inventory management, especially for large-scale production. -
RFQ (Request for Quotation)
– Definition: A document that a buyer sends to suppliers to request pricing and terms for specific products or services.
– Importance: Sending an RFQ is crucial for obtaining competitive pricing and understanding the terms of service from various suppliers. -
Incoterms (International Commercial Terms)
– Definition: A set of predefined international trade terms that clarify the responsibilities of buyers and sellers.
– Importance: Familiarity with Incoterms helps businesses navigate shipping and logistics, ensuring clear agreements on costs, risks, and responsibilities. -
Lead Time
– Definition: The amount of time from the initiation of an order until its completion.
– Importance: Understanding lead times is vital for planning production schedules and managing customer expectations. -
CAM (Computer-Aided Manufacturing)
– Definition: Software used to control machine tools in the manufacturing process based on CAD (Computer-Aided Design) models.
– Importance: Knowledge of CAM systems is essential for ensuring that the CNC machine can efficiently execute designs and optimize production processes.
By grasping these essential technical properties and trade terminologies, B2B buyers can make informed decisions when investing in 7-axis CNC machines, enhancing their operational efficiency and product quality.
Navigating Market Dynamics, Sourcing Trends, and Sustainability in the 7 axis cnc machine Sector
Market Overview & Key Trends
The global market for 7-axis CNC machines is rapidly expanding, driven by the increasing demand for high-precision and complex components across various industries, including aerospace, automotive, and medical manufacturing. As industries strive for efficiency and quality, 7-axis CNC machining stands out due to its ability to produce intricate parts in a single setup, significantly reducing production time and costs. Emerging technologies such as advanced CAD/CAM software integration and automation are further enhancing the capabilities of these machines, making them more accessible to international B2B buyers.
In regions like Africa and South America, there is a growing trend toward localizing manufacturing processes. As companies seek to reduce supply chain risks and enhance responsiveness, investing in advanced machining technologies like 7-axis CNC is becoming a strategic priority. Additionally, buyers from the Middle East and Europe are increasingly focusing on machine capabilities that support complex geometries and tight tolerances, essential for sectors such as defense and high-tech manufacturing.
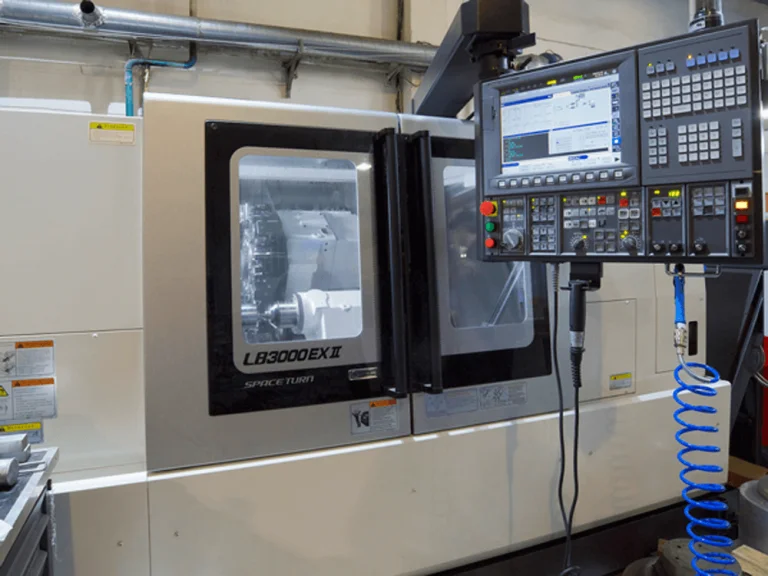
Illustrative Image (Source: Google Search)
Moreover, the rise of Industry 4.0 is reshaping the landscape, with smart manufacturing practices being adopted. This trend emphasizes connectivity, data analytics, and real-time monitoring, allowing manufacturers to optimize their operations. For B2B buyers, staying abreast of these technological advancements is crucial for making informed procurement decisions.
Sustainability & Ethical Sourcing in B2B
Sustainability is becoming a pivotal consideration for B2B buyers in the 7-axis CNC machine sector. The environmental impact of manufacturing processes, including energy consumption and waste generation, is under scrutiny. As a result, companies are increasingly seeking machines that incorporate energy-efficient technologies and sustainable manufacturing practices.
Ethical sourcing is also gaining traction, as businesses aim to build transparent supply chains that prioritize responsible sourcing of materials. Certifications such as ISO 14001 for environmental management and adherence to REACH regulations for chemical safety are becoming essential for suppliers. B2B buyers should actively seek suppliers who demonstrate a commitment to sustainability through the use of eco-friendly materials and processes, as well as adherence to ethical labor practices.
Additionally, the integration of recyclable materials in machine components and the use of biodegradable lubricants in CNC machining processes are emerging as key areas of focus. These practices not only reduce the carbon footprint but also enhance the overall sustainability profile of manufacturers. By prioritizing sustainability and ethical sourcing, international buyers can not only fulfill regulatory requirements but also align with the growing consumer demand for environmentally responsible products.
Brief Evolution/History
The evolution of CNC machining began in the 1940s with simple 2-axis machines, primarily used for basic tasks. Over the decades, advancements in technology led to the development of multi-axis machines, culminating in the introduction of 7-axis CNC machines. This innovation has enabled manufacturers to achieve unprecedented levels of precision and complexity in their parts, making it a vital tool in sectors that require detailed components, such as aerospace and medical manufacturing.
As the industry continues to evolve, the incorporation of smart technology, automation, and sustainable practices will further redefine the capabilities and applications of 7-axis CNC machines, offering significant opportunities for international B2B buyers to enhance their manufacturing processes.
Related Video: Incoterms for beginners | Global Trade Explained
Frequently Asked Questions (FAQs) for B2B Buyers of 7 axis cnc machine
-
What should I consider when vetting suppliers for 7-axis CNC machines?
When vetting suppliers, focus on their industry reputation, experience, and customer reviews. Ensure they have a proven track record of delivering high-quality machines. Request certifications such as ISO 9001, which indicates a commitment to quality management systems. Additionally, inquire about their after-sales support, including maintenance services and availability of spare parts. A reliable supplier should also be transparent about their manufacturing processes and capabilities. -
Can I customize my 7-axis CNC machine to meet specific production needs?
Yes, many suppliers offer customization options for 7-axis CNC machines. You can tailor aspects such as the machine size, spindle speed, and tooling configurations to suit your specific production requirements. Discuss your needs during initial consultations to ensure the supplier can accommodate your requests. It’s also beneficial to ask for past examples of custom machines they have built to gauge their capability in delivering tailored solutions. -
What are typical minimum order quantities (MOQ) and lead times for 7-axis CNC machines?
Minimum order quantities can vary significantly by supplier and machine type. Generally, for bespoke machines, the MOQ may be one unit, while standard models could require larger orders. Lead times typically range from 8 to 16 weeks, depending on the complexity of the machine and the supplier’s production schedule. Always confirm these details before placing an order to align your production timelines with your supplier’s capabilities. -
What payment terms are common when purchasing 7-axis CNC machines internationally?
Payment terms can differ based on the supplier’s policies and your negotiation power. Common arrangements include a deposit (often 30-50%) upfront, with the balance due upon delivery or commissioning. Some suppliers may offer financing options or letters of credit for larger purchases. Ensure you clarify payment methods accepted, such as wire transfers or credit cards, and confirm any additional costs related to international transactions. -
How can I ensure quality assurance and certifications for my machine?
Request documentation of quality assurance protocols from the supplier, including any relevant certifications like CE marking or ISO standards. It’s important to verify that the machines undergo rigorous testing before shipment. You may also consider conducting an on-site inspection or third-party audit of the manufacturing facility to assess quality control practices. Establishing clear quality benchmarks in your contract can further safeguard your investment. -
What logistics considerations should I be aware of when importing a 7-axis CNC machine?
Logistics for importing a 7-axis CNC machine involve several key factors, including shipping methods, customs clearance, and delivery timelines. Determine whether the supplier offers door-to-door delivery or if you need to arrange transportation. Understand the customs regulations in your country regarding importing machinery, including tariffs and taxes. Collaborating with a logistics provider experienced in heavy machinery can streamline the process and reduce potential delays. -
How should I handle disputes or issues with my supplier?
Establishing clear communication channels and a dispute resolution mechanism in your contract can help mitigate issues. If a problem arises, address it promptly with your supplier, providing detailed documentation of the issue. Most suppliers will have protocols in place for handling disputes, which may include mediation or arbitration. If necessary, consult with legal advisors familiar with international trade laws to explore your options for resolution. -
What additional support should I expect post-purchase of a 7-axis CNC machine?
Post-purchase support is crucial for the long-term success of your investment. Expect your supplier to provide installation assistance, training for your operators, and ongoing technical support. Inquire about warranty terms and what they cover, as well as their policy for spare parts supply. Regular maintenance services and access to technical documentation can also be vital for ensuring the longevity and optimal performance of your machine.
Important Disclaimer & Terms of Use
⚠️ Important Disclaimer
The information provided in this guide, including content regarding manufacturers, technical specifications, and market analysis, is for informational and educational purposes only. It does not constitute professional procurement advice, financial advice, or legal advice.
While we have made every effort to ensure the accuracy and timeliness of the information, we are not responsible for any errors, omissions, or outdated information. Market conditions, company details, and technical standards are subject to change.
B2B buyers must conduct their own independent and thorough due diligence before making any purchasing decisions. This includes contacting suppliers directly, verifying certifications, requesting samples, and seeking professional consultation. The risk of relying on any information in this guide is borne solely by the reader.
Strategic Sourcing Conclusion and Outlook for 7 axis cnc machine
The integration of 7-axis CNC machining into manufacturing processes represents a pivotal advancement for industries seeking precision and efficiency. By enabling the production of complex components with unmatched accuracy, these machines significantly reduce setup times and minimize the risk of errors. For international B2B buyers, particularly from regions like Africa, South America, the Middle East, and Europe, understanding the strategic sourcing of 7-axis CNC machines is crucial for maintaining a competitive edge in the global market.
Key takeaways include the importance of selecting machines that align with specific operational needs, ensuring compatibility with existing software, and investing in staff training for optimal utilization. Furthermore, regular maintenance and robust quality control systems are essential for sustaining production quality and minimizing downtime.
As the demand for intricate, high-precision parts continues to grow, the strategic sourcing of 7-axis CNC machines will become increasingly vital. Buyers are encouraged to explore partnerships with reputable suppliers who can provide not only the technology but also the necessary support and training. Embracing this technology will position businesses to capitalize on emerging opportunities in diverse sectors, ensuring a prosperous and innovative future.