Your Ultimate Guide to Sourcing Ball Screw Cnc Machine
Introduction: Navigating the Global Market for ball screw cnc machine
Navigating the global market for ball screw CNC machines is crucial for businesses seeking precision engineering solutions. As a cornerstone of modern manufacturing, ball screws facilitate the conversion of rotational motion into linear movement, ensuring high accuracy and efficiency in CNC operations. For international B2B buyers, particularly those in Africa, South America, the Middle East, and Europe—such as Germany and Turkey—understanding the nuances of ball screws is essential for optimizing their production capabilities.
This guide provides a comprehensive overview of ball screw CNC machines, covering a variety of critical aspects. From types and materials to manufacturing processes and quality control, we delve into the specifics that influence performance and cost. Buyers will gain insights into selecting the right suppliers and understanding market dynamics, empowering them to make informed sourcing decisions that align with their operational needs.
Moreover, we address frequently asked questions, offering clarity on common concerns that may arise during the purchasing process. By equipping international buyers with the knowledge needed to navigate this complex landscape, this guide serves as a valuable resource for enhancing machining precision, reducing downtime, and maximizing return on investment. Whether you are upgrading existing machinery or investing in new technology, understanding the intricacies of ball screw CNC machines is key to achieving your manufacturing goals.
Understanding ball screw cnc machine Types and Variations
Type Name | Key Distinguishing Features | Primary B2B Applications | Brief Pros & Cons for Buyers |
---|---|---|---|
Precision Ground Ball Screws | High accuracy, minimal backlash, tight tolerances | Aerospace, Medical Devices, High-Precision Manufacturing | Pros: Excellent precision, long lifespan. Cons: Higher cost. |
Rolled Ball Screws | Cost-effective, produced through rolling, higher backlash | General Manufacturing, Automation | Pros: Lower cost, easy to source. Cons: Less precision, more wear. |
Miniature Ball Screws | Compact design, suitable for small-scale applications | Robotics, Electronics, Medical Equipment | Pros: Space-saving, high performance. Cons: Limited load capacity. |
High Load Capacity Ball Screws | Designed to handle heavy loads, robust construction | Heavy Machinery, Industrial Equipment | Pros: Durable, suitable for heavy-duty applications. Cons: Bulkier design. |
Double Nut Ball Screws | Dual nut design reduces backlash, enhances stability | CNC Machining, Precision Engineering | Pros: Improved accuracy, reduced wear. Cons: More complex installation. |
Precision Ground Ball Screws
Precision ground ball screws are engineered for high accuracy and minimal backlash, often featuring tolerances as tight as 0.0001 inches. These screws are ideal for applications requiring extreme precision, such as in aerospace and medical device manufacturing. When considering a purchase, buyers should evaluate the cost versus the performance benefits, as these screws tend to be more expensive but offer enhanced durability and reliability in demanding environments.
Rolled Ball Screws
Rolled ball screws are a cost-effective alternative, manufactured by rolling the screw instead of grinding. This method results in higher backlash and slightly lower precision, making them suitable for general manufacturing and automation tasks where budget constraints are a concern. Buyers should weigh the cost savings against the potential need for more frequent maintenance or replacement due to wear over time.
Miniature Ball Screws
Miniature ball screws are designed for compact applications, providing excellent performance in limited spaces, such as robotics and electronics. Their small size does not compromise their functionality; however, they typically have a lower load capacity. B2B buyers should focus on the specific application requirements, ensuring that the miniature ball screw meets both spatial and performance needs.
High Load Capacity Ball Screws
These ball screws are specifically designed to handle heavy loads, making them essential in heavy machinery and industrial equipment applications. Their robust construction enables them to withstand significant axial forces, but this often results in a bulkier design. Buyers should consider the operational environment and the potential trade-offs in size versus load-bearing capability when selecting these screws.
Double Nut Ball Screws
Featuring a dual nut design, double nut ball screws are engineered to reduce backlash and enhance stability, making them a preferred choice in CNC machining and precision engineering applications. The complexity of installation can be a drawback, but the benefits of improved accuracy and reduced wear make them a worthwhile investment for buyers focused on high-performance machining processes.
Related Video: Ball screws in CNC machines – how they work, and what they do
Key Industrial Applications of ball screw cnc machine
Industry/Sector | Specific Application of ball screw cnc machine | Value/Benefit for the Business | Key Sourcing Considerations for this Application |
---|---|---|---|
Aerospace | Precision machining of aircraft components | Ensures high accuracy and reliability, critical for safety standards | Certification of suppliers, material quality, and lead time |
Automotive | Production of engine and transmission parts | Enhances efficiency and reduces production costs | Tolerance specifications, load capacity, and maintenance support |
Medical Devices | Manufacturing of surgical instruments | Guarantees precision and compliance with health regulations | Compliance with medical standards, customization options, and delivery times |
Industrial Equipment | Assembly of automated machinery | Increases productivity and reduces downtime | Supplier reliability, support for integration, and technical expertise |
Robotics | Production of robotic arms and automated systems | Improves performance and flexibility in manufacturing processes | Innovation in design, scalability, and post-sale service support |
Aerospace
In the aerospace industry, ball screw CNC machines are essential for the precision machining of aircraft components such as wing structures and landing gear. These components must meet stringent safety and performance standards, making accuracy a top priority. Ball screws facilitate high-speed operations with minimal backlash, ensuring that parts are manufactured to exact specifications. Buyers should consider suppliers with aerospace certifications and a proven track record in quality control to ensure compliance with industry regulations.
Automotive
Ball screw CNC machines are widely used in the automotive sector for the production of engine and transmission parts. Their ability to provide high accuracy and low friction translates to improved efficiency and reduced production costs. In this sector, buyers must focus on sourcing ball screws that can handle high axial loads and meet specific tolerance requirements. Additionally, long-term maintenance support is crucial to minimize downtime in manufacturing processes.
Medical Devices
In the medical device industry, ball screw CNC machines are utilized to manufacture surgical instruments and implantable devices. Precision is paramount, as these devices must adhere to strict health regulations. The use of ball screws ensures that components are produced with the necessary accuracy and reliability. Buyers should prioritize suppliers who understand medical compliance standards and can offer customization options to meet unique product specifications.
Industrial Equipment
Ball screw CNC machines play a vital role in the assembly of automated machinery in various industrial settings. These machines enhance productivity by allowing for rapid and accurate assembly processes, significantly reducing downtime. Buyers in this sector should evaluate suppliers based on their reliability and ability to provide support for system integration. Additionally, technical expertise from suppliers can help in optimizing the setup for specific industrial applications.
Robotics
In robotics, ball screw CNC machines are critical for producing robotic arms and other automated systems. These machines offer enhanced performance and flexibility, allowing for the creation of complex movements and tasks. Buyers should seek out innovative suppliers who can provide scalable solutions and comprehensive post-sale support. The ability to customize designs and adapt to evolving technologies will also be a key consideration for international buyers looking to stay competitive in the robotics market.
Related Video: ball screw xy-h2 linear slide cnc
Strategic Material Selection Guide for ball screw cnc machine
When selecting materials for ball screws used in CNC machines, international B2B buyers must consider several factors, including mechanical properties, application suitability, and regional compliance standards. Below, we analyze four common materials used in the manufacturing of ball screws, focusing on their key properties, advantages, disadvantages, and specific considerations relevant to buyers from Africa, South America, the Middle East, and Europe.
1. Carbon Steel
Key Properties: Carbon steel is known for its high strength and hardness, making it suitable for high-load applications. It typically has a temperature rating up to 300°C and can withstand moderate pressures.
Pros: Carbon steel offers excellent wear resistance and durability, making it ideal for heavy-duty applications. It is also relatively inexpensive compared to other materials.
Cons: Its susceptibility to corrosion requires protective coatings or treatments, which can increase manufacturing complexity and costs. Additionally, it may not perform well in high-temperature environments without proper heat treatment.
Impact on Application: Carbon steel is compatible with a variety of media, but its corrosion susceptibility can limit its use in humid or chemically aggressive environments.
Considerations for International Buyers: Buyers should ensure that the carbon steel used complies with standards such as ASTM A36 or DIN 17100, particularly in regions like Germany and Turkey where strict regulations are enforced.
2. Stainless Steel
Key Properties: Stainless steel is renowned for its corrosion resistance and can withstand temperatures up to 600°C. It is also capable of handling high pressures, making it versatile for various applications.
Pros: The primary advantage of stainless steel is its resistance to corrosion, which extends the lifespan of ball screws in challenging environments. It also offers good mechanical properties and aesthetic appeal.
Cons: Stainless steel is generally more expensive than carbon steel and can be more challenging to machine, leading to higher manufacturing costs.
Impact on Application: Its excellent corrosion resistance makes stainless steel suitable for applications involving moisture or chemical exposure, such as in the food and pharmaceutical industries.
Considerations for International Buyers: Buyers should look for compliance with standards like ASTM A276 or JIS G4303, especially in regions where quality and safety are paramount.
3. Alloy Steel
Key Properties: Alloy steel combines carbon steel with other elements like chromium, molybdenum, or nickel to enhance specific properties. It can withstand high temperatures (up to 500°C) and offers improved strength and toughness.
Pros: The addition of alloying elements provides enhanced hardness and wear resistance, making alloy steel suitable for demanding applications. It also maintains good machinability.
Cons: The manufacturing process for alloy steel can be more complex, leading to higher costs. Additionally, it may require specific heat treatment processes to achieve desired properties.
Impact on Application: Alloy steel is well-suited for high-stress applications, such as aerospace or automotive components, where performance and durability are critical.
Considerations for International Buyers: Compliance with standards such as ASTM A514 or DIN 17200 is essential, particularly in Europe, where quality assurance is strictly regulated.
4. Bronze
Key Properties: Bronze, an alloy primarily of copper and tin, offers good corrosion resistance and can operate effectively at temperatures up to 400°C. It also has excellent anti-friction properties.
Pros: Bronze provides low friction, making it ideal for applications requiring smooth motion. Its corrosion resistance is beneficial in marine or humid environments.
Cons: Bronze is typically more expensive than steel options and may not be suitable for high-load applications due to its lower tensile strength.
Impact on Application: Bronze is particularly effective in applications where lubrication is challenging, such as in marine environments or with corrosive chemicals.
Considerations for International Buyers: Buyers should ensure that bronze complies with standards like ASTM B505 or DIN 17662, particularly in regions with stringent material quality requirements.
Summary Table
Material | Typical Use Case for ball screw cnc machine | Key Advantage | Key Disadvantage/Limitation | Relative Cost (Low/Med/High) |
---|---|---|---|---|
Carbon Steel | Heavy-duty machinery | High strength and wear resistance | Susceptible to corrosion | Low |
Stainless Steel | Chemical and food processing | Excellent corrosion resistance | Higher cost and machining difficulty | High |
Alloy Steel | Aerospace and automotive components | Enhanced strength and toughness | Complex manufacturing process | Medium |
Bronze | Marine and corrosive environments | Low friction and good corrosion resistance | Lower tensile strength | High |
This strategic material selection guide provides essential insights for international B2B buyers, enabling them to make informed decisions when sourcing ball screws for CNC machines. By considering the properties, advantages, and limitations of each material, buyers can align their choices with their specific application needs and regional compliance standards.
In-depth Look: Manufacturing Processes and Quality Assurance for ball screw cnc machine
The manufacturing processes for ball screw CNC machines are intricate and require a high level of precision to ensure optimal performance and durability. This section provides an in-depth look at the typical manufacturing stages and quality assurance practices, focusing on actionable insights for B2B buyers from Africa, South America, the Middle East, and Europe.
Manufacturing Processes
1. Material Preparation
The first stage in the manufacturing of ball screws involves the careful selection and preparation of raw materials. High-quality steel is commonly used due to its strength and wear resistance.
- Material Types: Common materials include carbon steel, stainless steel, and sometimes specialized alloys for high-load applications.
- Heat Treatment: The selected steel often undergoes heat treatment to enhance hardness and fatigue resistance, which are crucial for the longevity of ball screws.
2. Forming
This stage involves shaping the prepared material into the necessary components of the ball screw.
- Machining: The raw material is machined into a screw shaft and nut. Precision machining techniques, such as CNC turning and milling, are employed to achieve the required dimensions and tolerances.
- Rolling and Grinding: For rolled ball screws, the screw is formed by rolling, which is a cost-effective method but may result in higher backlash. Precision ground ball screws are created through grinding, providing tighter tolerances and lower backlash.
3. Assembly
Once the individual components are manufactured, they are assembled into the final product.
- Ball Circulation System: The assembly includes the insertion of recirculating balls within the nut and screw. This system ensures smooth linear motion and minimizes friction.
- Ball Return Mechanism: A crucial aspect of assembly is the ball return mechanism, which allows for continuous circulation of the balls, enhancing the efficiency and lifespan of the ball screw.
4. Finishing
Finishing processes are essential for enhancing the surface quality and overall performance of the ball screws.
- Surface Treatment: Processes such as hardening, coating, and polishing are applied to improve wear resistance and reduce friction. Common surface treatments include nitriding and chrome plating.
- Final Inspection: Before packaging, a final inspection is conducted to ensure that the ball screws meet all specifications and quality standards.
Quality Assurance
Quality assurance in the manufacturing of ball screw CNC machines is critical to guarantee that the products meet international standards and customer expectations.
International Standards
B2B buyers should look for compliance with internationally recognized standards, which can significantly impact the quality and reliability of the products.
- ISO 9001: This standard outlines the criteria for a quality management system. Suppliers should have ISO 9001 certification to demonstrate their commitment to quality.
- CE Marking: For products sold in Europe, CE marking indicates conformity with health, safety, and environmental protection standards.
- API Certification: In industries such as oil and gas, API certification can be crucial for ensuring the quality of mechanical components.
Quality Control Checkpoints
Implementing robust quality control checkpoints throughout the manufacturing process ensures that any defects are identified early.
- Incoming Quality Control (IQC): This involves inspecting raw materials upon arrival to confirm they meet the required specifications.
- In-Process Quality Control (IPQC): During manufacturing, regular inspections are conducted to monitor the processes and detect any deviations from quality standards.
- Final Quality Control (FQC): After assembly, comprehensive testing is performed to ensure the final product meets all specifications.
Common Testing Methods
B2B buyers should be aware of the various testing methods employed to ensure quality:
- Dimensional Testing: Using precision measuring tools to verify that components meet specified dimensions.
- Functional Testing: Testing the ball screws under simulated operating conditions to assess performance, such as load capacity and backlash.
- Non-Destructive Testing (NDT): Methods like ultrasonic testing or magnetic particle inspection can be used to detect internal flaws without damaging the components.
Verifying Supplier Quality Control
B2B buyers can take several steps to verify the quality control processes of potential suppliers:
- Supplier Audits: Conducting audits of suppliers can provide insight into their manufacturing processes, quality control measures, and compliance with international standards.
- Quality Reports: Requesting quality assurance reports can help assess the supplier’s track record and adherence to quality standards.
- Third-Party Inspections: Engaging independent third-party inspectors to evaluate the manufacturing facility can provide an unbiased assessment of quality practices.
QC and Certification Nuances for International Buyers
International buyers, particularly from diverse regions such as Africa, South America, the Middle East, and Europe, should consider the following nuances in quality certification:
- Regional Standards: Be aware of specific regional standards that may differ from international standards. For instance, some countries may have local certifications that are crucial for compliance.
- Cultural Considerations: Understanding cultural differences in business practices can aid in building relationships with suppliers, ensuring that quality expectations are clearly communicated and met.
- Supply Chain Transparency: In regions with less stringent regulatory environments, ensuring transparency in the supply chain can help mitigate risks associated with quality.
By understanding these manufacturing processes and quality assurance practices, B2B buyers can make informed decisions when sourcing ball screw CNC machines, ensuring they partner with reliable suppliers that meet their quality expectations.
Related Video: SMART Quality Control for Manufacturing
Comprehensive Cost and Pricing Analysis for ball screw cnc machine Sourcing
In the competitive landscape of sourcing ball screw CNC machines, understanding the comprehensive cost structure and pricing dynamics is crucial for international B2B buyers. This analysis will delve into the various cost components involved, the factors that influence pricing, and practical tips for negotiation and efficient sourcing.
Cost Components
-
Materials: The primary cost driver in ball screw manufacturing is the raw materials used, which typically include high-grade steel for durability and performance. The choice of materials can significantly impact the overall price, especially if specialized alloys or coatings are required.
-
Labor: Labor costs encompass the wages of skilled workers involved in the manufacturing process. Regions with lower labor costs may offer competitive pricing, but this can come at the expense of quality. It is essential to evaluate the skill level of the workforce when considering suppliers.
-
Manufacturing Overhead: This includes costs related to facility operations, utilities, and equipment maintenance. Factories with advanced machinery may incur higher overhead but can produce higher quality and more precise components, justifying a premium price.
-
Tooling: The cost of tooling is significant, especially for custom or precision components. Buyers should be aware that initial tooling costs can be amortized over larger production runs, making bulk orders more cost-effective.
-
Quality Control (QC): Ensuring product quality is paramount, and rigorous QC processes add to the overall costs. Suppliers offering certifications (e.g., ISO 9001) often charge more due to their investment in quality assurance.
-
Logistics: Shipping and handling costs are critical, particularly for international transactions. Factors such as distance, shipping method, and customs duties can affect the final cost significantly.
-
Margin: Suppliers will apply a markup to cover their operational risks and profit expectations. Understanding typical margins in the industry can help buyers gauge whether a quoted price is fair.
Price Influencers
-
Volume/MOQ: Minimum order quantities (MOQ) and bulk purchase volumes can dramatically influence pricing. Higher volumes often lead to discounts, making it beneficial for buyers with consistent demand.
-
Specifications/Customization: Customized solutions tailored to specific needs can lead to higher costs. Buyers should clearly define their requirements to avoid unexpected price increases.
-
Material Quality/Certifications: The grade of materials and the presence of quality certifications can justify higher prices. Buyers must weigh the cost against the potential for enhanced performance and longevity.
-
Supplier Factors: Supplier reputation, reliability, and production capacity also play a role in pricing. Established suppliers may charge more due to their proven track record.
-
Incoterms: The terms of shipping and delivery (Incoterms) can significantly affect pricing. Understanding these terms helps buyers manage costs related to insurance, transportation, and customs.
Buyer Tips
-
Negotiation: Always negotiate prices and terms. Building a relationship with suppliers can lead to better pricing and terms over time.
-
Cost Efficiency: Consider the Total Cost of Ownership (TCO), which includes purchase price, operational costs, maintenance, and potential downtime. A lower upfront cost may lead to higher long-term expenses if quality is compromised.
-
Pricing Nuances for International Buyers: Buyers from Africa, South America, the Middle East, and Europe should be aware of currency fluctuations and import duties that can impact the final price. It is advisable to obtain quotes in your local currency and clarify all costs upfront.
Disclaimer
Prices for ball screw CNC machines can vary widely based on the aforementioned factors, and the figures provided in this analysis are indicative. It is crucial for buyers to conduct thorough market research and obtain multiple quotes to ensure they are making informed purchasing decisions.
Spotlight on Potential ball screw cnc machine Manufacturers and Suppliers
This section looks at several manufacturers active in the ‘ball screw cnc machine’ market. This is a representative sample for illustrative purposes; B2B buyers must conduct extensive due diligence before any transaction. Information is synthesized from public sources and general industry knowledge.
Essential Technical Properties and Trade Terminology for ball screw cnc machine
When evaluating ball screw CNC machines, understanding key technical properties and industry terminology is essential for making informed purchasing decisions. Here are the critical specifications and common jargon that B2B buyers should be familiar with.
Key Technical Properties
- Material Grade
– Definition: The quality of materials used in the construction of ball screws, typically steel or stainless steel.
– Importance: Higher-grade materials enhance durability, reduce wear, and improve overall performance. For buyers, selecting the appropriate material can directly impact the lifespan of the CNC machine and the precision of the machining processes.
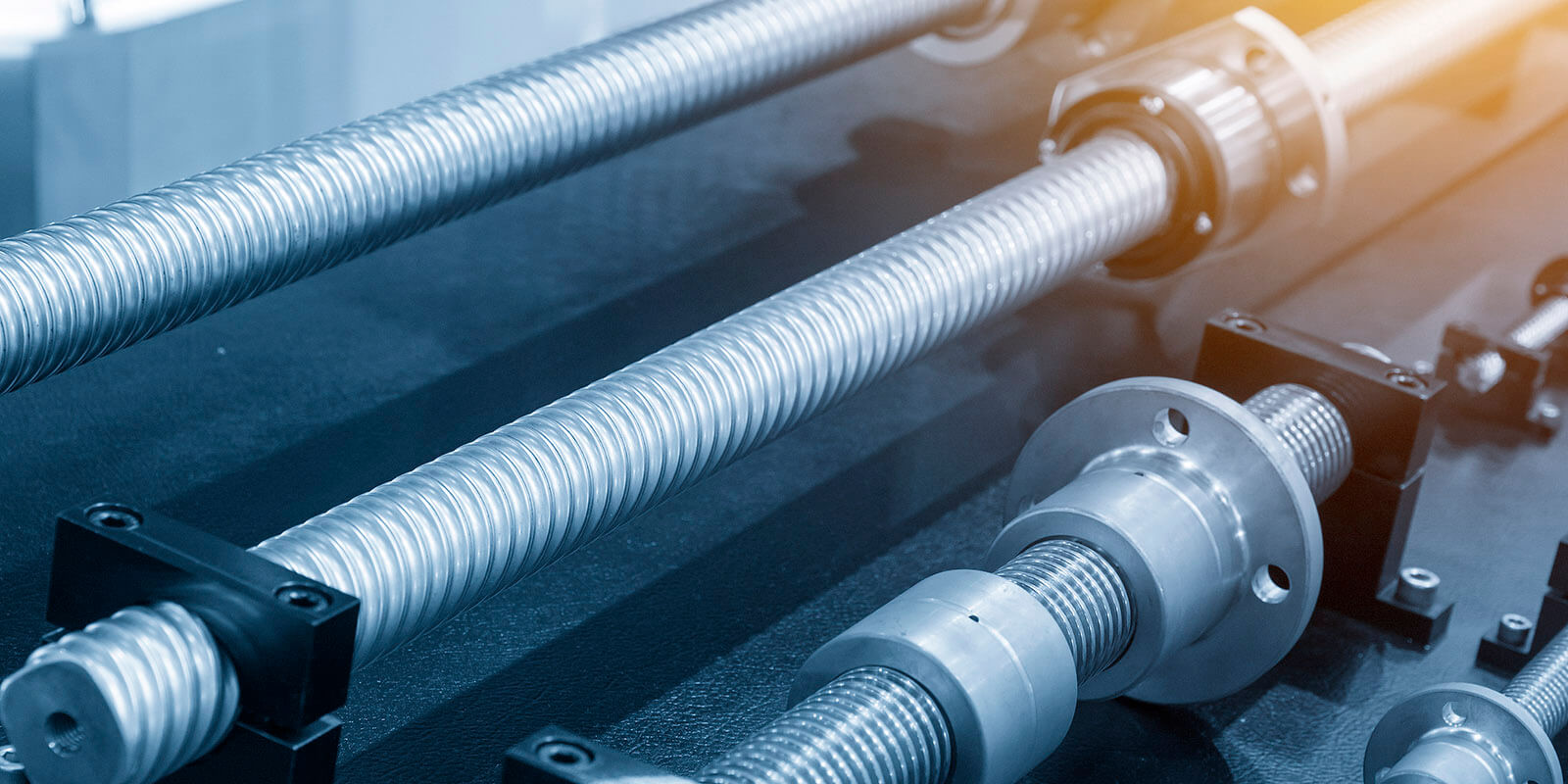
Illustrative Image (Source: Google Search)
-
Tolerance
– Definition: The allowable deviation from a specified dimension, often measured in microns (μm).
– Importance: Tight tolerances (e.g., ±0.001 mm) are crucial for precision machining. High tolerance levels ensure that the CNC machine operates smoothly and produces consistent results, which is vital in industries such as aerospace and medical devices. -
Load Capacity
– Definition: The maximum load that a ball screw can handle without failure, typically expressed in Newtons (N) or pounds (lbs).
– Importance: Understanding load capacity is essential for selecting a ball screw that can handle the specific demands of your application. Insufficient load capacity can lead to premature failure and costly downtime. -
Backlash
– Definition: The amount of play or clearance between the ball screw and the nut, often measured in millimeters or inches.
– Importance: Minimizing backlash is critical for achieving high precision in CNC operations. Buyers should look for ball screws with low backlash specifications to ensure accurate positioning and movement. -
Efficiency
– Definition: The ratio of output to input energy, often expressed as a percentage.
– Importance: Ball screws with high efficiency (over 90%) reduce energy consumption and operational costs. For B2B buyers, this can translate to significant savings in long-term operational expenses. -
Speed Rating
– Definition: The maximum rotational speed at which a ball screw can operate effectively, typically measured in revolutions per minute (RPM).
– Importance: A higher speed rating allows for faster machining cycles, improving productivity. Buyers need to consider speed ratings based on their specific machining requirements to ensure optimal performance.
Common Trade Terminology
-
OEM (Original Equipment Manufacturer)
– Definition: A company that produces parts or equipment that may be marketed by another manufacturer.
– Relevance: Understanding OEM relationships can help buyers identify quality suppliers and ensure that they are sourcing components that meet industry standards. -
MOQ (Minimum Order Quantity)
– Definition: The smallest quantity of a product that a supplier is willing to sell.
– Relevance: Knowing the MOQ is crucial for budgeting and inventory management. Buyers should negotiate MOQs that align with their operational needs to avoid excess inventory costs. -
RFQ (Request for Quotation)
– Definition: A document sent to suppliers to solicit pricing and terms for specific products or services.
– Relevance: An RFQ is an essential tool for buyers to compare prices and terms from different suppliers, ensuring they get the best deal for their CNC machine components. -
Incoterms
– Definition: International commercial terms that define the responsibilities of buyers and sellers in international trade.
– Relevance: Familiarity with Incoterms helps buyers understand shipping costs, risks, and responsibilities, facilitating smoother transactions in international procurement. -
Lead Time
– Definition: The amount of time it takes from placing an order until the product is received.
– Relevance: Understanding lead times is vital for planning and scheduling production. Buyers should factor in lead times when making purchasing decisions to ensure timely delivery and avoid production delays.
By grasping these technical properties and trade terms, international B2B buyers can make better-informed decisions when sourcing ball screw CNC machines, ultimately leading to improved operational efficiency and cost-effectiveness.
Navigating Market Dynamics, Sourcing Trends, and Sustainability in the ball screw cnc machine Sector
Market Overview & Key Trends
The global market for ball screw CNC machines is witnessing significant transformation, driven by advancements in automation, increased demand for precision engineering, and the push towards Industry 4.0. Key market drivers include the growing need for high-speed machining and the incorporation of smart technologies in manufacturing processes. This evolution is particularly relevant for international B2B buyers from Africa, South America, the Middle East, and Europe, where industries are rapidly modernizing to remain competitive.
Emerging B2B tech trends include the integration of IoT (Internet of Things) capabilities within CNC machines, enabling real-time data collection and predictive maintenance. Buyers should also consider sourcing strategies that prioritize suppliers with strong technical support and rapid response capabilities, as these factors are increasingly critical in maintaining operational efficiency. Additionally, the rise of e-commerce platforms for industrial equipment is streamlining sourcing processes, allowing buyers to compare products and prices more effectively.
Market dynamics are further influenced by regional factors. For example, European countries like Germany are at the forefront of innovation in CNC technology, while nations in Africa and South America are beginning to adopt these advanced manufacturing techniques. This presents an opportunity for B2B buyers to leverage partnerships with suppliers who can offer both cutting-edge technology and localized support.
Sustainability & Ethical Sourcing in B2B
In today’s marketplace, sustainability and ethical sourcing have become paramount considerations for B2B buyers, especially in the ball screw CNC machine sector. The environmental impact of manufacturing processes is under scrutiny, prompting companies to seek suppliers that prioritize eco-friendly practices. This includes the use of sustainable materials, energy-efficient manufacturing processes, and waste reduction initiatives.
Importance of ethical supply chains cannot be overstated. Buyers should evaluate suppliers based on their commitment to social responsibility, including fair labor practices and transparent sourcing. This not only mitigates reputational risks but also aligns with the growing consumer demand for ethically produced goods.
B2B buyers should look for green certifications such as ISO 14001 or adherence to RoHS (Restriction of Hazardous Substances) standards, which indicate a supplier’s commitment to sustainability. Additionally, using recycled or eco-friendly materials in the production of ball screws can enhance the overall sustainability profile of CNC machines, making them more attractive in an increasingly eco-conscious market.
Brief Evolution/History
The evolution of ball screw technology has been pivotal in enhancing CNC machine performance. Initially developed in the early 20th century, ball screws were designed to reduce friction and improve efficiency in linear motion applications. Over the decades, advancements in materials and manufacturing techniques have led to the creation of precision ground and rolled ball screws, each catering to different industrial needs.
The introduction of CNC technology in the 1960s marked a significant turning point, as ball screws became integral to achieving the precision and reliability required in automated machining. Today, as industries continue to innovate, ball screws remain a fundamental component, driving efficiency and accuracy in CNC operations worldwide. This historical context is essential for B2B buyers, as understanding the technology’s evolution can inform better sourcing decisions and long-term partnerships with manufacturers.
Related Video: International Trade Explained
Frequently Asked Questions (FAQs) for B2B Buyers of ball screw cnc machine
-
What should I consider when vetting suppliers for ball screw CNC machines?
When vetting suppliers, prioritize their industry experience and reputation. Look for certifications such as ISO 9001, which indicates a commitment to quality management systems. Request references from previous clients and evaluate their experience with international shipping and compliance with trade regulations. Additionally, assess their ability to provide technical support and after-sales service, as these factors are crucial for long-term partnerships. -
Can I customize the specifications of a ball screw CNC machine?
Yes, many manufacturers offer customization options to meet specific operational needs. Discuss your requirements regarding load capacity, speed, accuracy, and size with the supplier. Ensure they have experience in producing customized solutions and can provide a clear timeline for development and delivery. Request samples or prototypes to evaluate the customizations before finalizing the order. -
What are the typical minimum order quantities (MOQ) and lead times for ball screw CNC machines?
MOQs can vary significantly based on the supplier and the complexity of the machine. Generally, expect MOQs to range from 1 to 10 units for standard models, while custom designs may require larger orders. Lead times can also vary, typically ranging from 4 to 12 weeks depending on customization and production schedules. It’s essential to clarify these details upfront to manage your project timelines effectively. -
What payment methods are commonly accepted in international trade for ball screw CNC machines?
Most suppliers accept various payment methods, including wire transfers, letters of credit (LC), and PayPal. For larger transactions, a letter of credit may provide additional security for both parties. Discuss payment terms upfront, including deposits, payment schedules, and any contingencies related to delivery milestones. Always ensure that the payment method aligns with your financial risk management strategies. -
What quality assurance measures should I look for in a supplier?
Seek suppliers who implement rigorous quality assurance processes, including in-process inspections and final testing of ball screw CNC machines. Certifications like CE marking or ISO standards can indicate adherence to quality and safety regulations. Request documentation of quality control procedures and ask for reports on previous machine performance. A reliable supplier should be willing to share this information to build trust. -
How can I ensure compliance with international logistics regulations?
To navigate international logistics, collaborate with suppliers who have experience in exporting machinery. They should provide guidance on necessary documentation, such as commercial invoices, packing lists, and export licenses. Engage a freight forwarder familiar with customs regulations in your country to streamline the shipping process. Additionally, ensure that the machines are packaged securely to prevent damage during transit. -
What steps should I take in case of disputes with a supplier?
Establish clear communication channels with your supplier to address potential disputes quickly. If issues arise, document all communications and agreements, as this information will be crucial if escalation is necessary. Consider including a mediation clause in your contract to facilitate resolution without resorting to litigation. Familiarize yourself with the supplier’s country laws and regulations, as this can influence dispute resolution procedures. -
Are there specific certifications I should look for in a ball screw CNC machine?
Yes, certifications such as ISO 9001 for quality management, CE marking for European safety standards, and UL certification for electrical safety can provide assurance of compliance and quality. Depending on your industry, other certifications may be relevant, such as FDA approval for medical devices or AS9100 for aerospace applications. Verify that the supplier can provide documentation for these certifications to ensure your compliance needs are met.
Important Disclaimer & Terms of Use
⚠️ Important Disclaimer
The information provided in this guide, including content regarding manufacturers, technical specifications, and market analysis, is for informational and educational purposes only. It does not constitute professional procurement advice, financial advice, or legal advice.
While we have made every effort to ensure the accuracy and timeliness of the information, we are not responsible for any errors, omissions, or outdated information. Market conditions, company details, and technical standards are subject to change.
B2B buyers must conduct their own independent and thorough due diligence before making any purchasing decisions. This includes contacting suppliers directly, verifying certifications, requesting samples, and seeking professional consultation. The risk of relying on any information in this guide is borne solely by the reader.
Strategic Sourcing Conclusion and Outlook for ball screw cnc machine
In conclusion, strategic sourcing of ball screw CNC machines is pivotal for enhancing operational efficiency and precision in manufacturing processes. By understanding the diverse types of ball screws—such as precision ground and rolled options—international B2B buyers can make informed decisions that align with their specific needs, whether in the aerospace, automotive, or industrial sectors.
Investing in high-quality ball screws not only reduces maintenance costs but also improves machine accuracy, which is essential for competitive advantage in today’s global market. As markets in Africa, South America, the Middle East, and Europe continue to evolve, the importance of forging strong supplier relationships and leveraging innovative technologies cannot be overstated.
Looking ahead, businesses should prioritize the integration of advanced sourcing strategies and technologies to remain agile and responsive to market demands. Embrace this opportunity to enhance your CNC capabilities—connect with trusted suppliers, explore the latest advancements in ball screw technology, and position your operations for future success. The journey to excellence in CNC machining begins with the right components and partnerships.
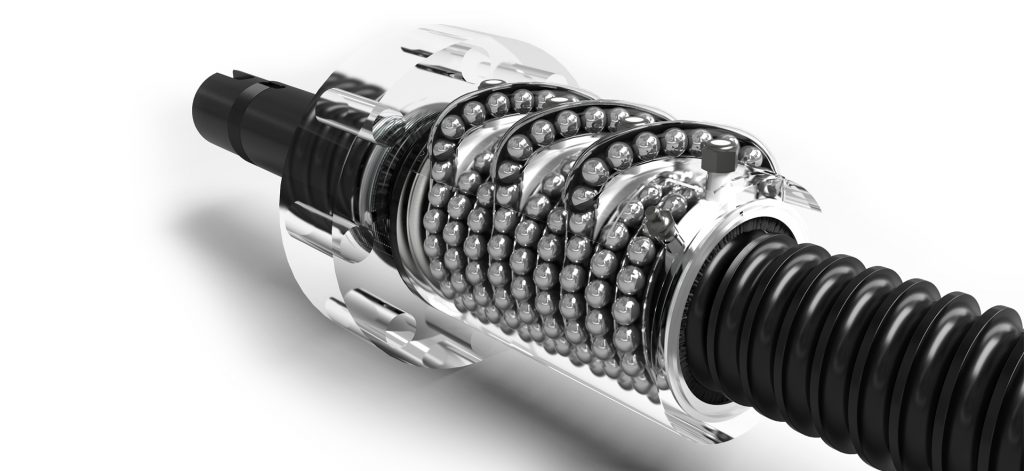
Illustrative Image (Source: Google Search)