Your Ultimate Guide to Sourcing Cnc Metal Cutting Machine
Introduction: Navigating the Global Market for cnc metal cutting machine
In today’s rapidly evolving manufacturing landscape, CNC metal cutting machines stand as pivotal tools that define precision, efficiency, and competitiveness across various sectors. For international B2B buyers, particularly in regions like Africa, South America, the Middle East, and Europe, understanding the nuances of sourcing these machines is crucial. The ability to fabricate metal components with accuracy not only enhances product quality but also drives operational efficiency and innovation, making it essential for industries ranging from automotive to aerospace and beyond.
This guide serves as a comprehensive resource designed to empower buyers with actionable insights into the global CNC metal cutting market. It covers a variety of CNC cutting processes—including milling, turning, laser cutting, and plasma cutting—along with their specific applications and advantages. Additionally, it delves into material selection, manufacturing and quality control best practices, and supplier evaluation criteria, enabling buyers to make informed decisions.
Understanding cost structures and emerging market trends is also vital, as these factors directly impact budgeting and long-term sourcing strategies. The guide addresses frequently asked questions that often arise during the procurement process, ensuring that buyers are well-equipped to navigate potential challenges. By leveraging the knowledge presented in this guide, B2B buyers can confidently enhance their sourcing strategies, optimize supplier relationships, and ultimately achieve greater success in their manufacturing endeavors.
Understanding cnc metal cutting machine Types and Variations
Type Name | Key Distinguishing Features | Primary B2B Applications | Brief Pros & Cons for Buyers |
---|---|---|---|
CNC Turning | Rotates workpiece; cuts via fixed single-point tool | Shafts, bushings, fittings (automotive, aerospace) | High precision for cylindrical parts; limited for complex shapes |
CNC Milling | Multi-axis movement with rotary cutting tools | Complex housings, brackets, plates, molds | Highly versatile; initial investment is high, requires skilled operators |
CNC Laser Cutting | Focused laser beam for precise, contactless cutting | Sheet metal fabrication, prototyping | Exceptional precision; higher maintenance and energy costs |
CNC Plasma Cutting | Uses ionized gas plasma to cut thicker metal at high speeds | Structural steel, automotive frames | Fast cutting; less precise for detailed work |
CNC Waterjet Cutting | High-pressure water (with/without abrasives) for cold cutting | Sensitive alloys, architectural panels | No heat-affected zone; slower for thick metals, higher operating costs |
CNC Turning
CNC turning is ideal for producing symmetrical components such as shafts and bushings. This method utilizes a rotating workpiece and a stationary cutting tool, allowing for high precision and repeatability in mass production. For B2B buyers, it’s crucial to consider the geometrical requirements of parts, as this method is less suited for complex shapes. Additionally, evaluating the expected production volume and ensuring the availability of compatible tooling can optimize the investment.
CNC Milling
CNC milling machines are renowned for their versatility, capable of producing intricate geometries by moving a rotating tool across multiple axes. This makes them suitable for applications in industries like aerospace and automotive, where precision is critical. Buyers should assess the machine’s axis capabilities and the skill level of available operators, as these factors can significantly influence lead times and production costs. The initial investment may be higher, but the potential for increased production capabilities often justifies this expense.
CNC Laser Cutting
CNC laser cutting is distinguished by its ability to deliver precise cuts with minimal material waste. This method is widely used for applications such as metal sheet fabrication and prototyping in sectors like electronics and HVAC. B2B buyers should weigh the benefits of exceptional cutting quality against the ongoing operational costs, including maintenance and energy consumption. Additionally, confirming local technical support availability is essential, especially in regions with emerging markets.
CNC Plasma Cutting
CNC plasma cutting is favored for its speed and efficiency in cutting through thick metals, making it a popular choice in heavy fabrication and construction. This method uses an ionized gas stream to achieve rapid cuts, which can lower initial costs for buyers. However, it’s important to note that plasma cutting may not provide the same level of precision on thinner materials. Buyers should carefully evaluate the machine’s capabilities in relation to their specific project requirements to ensure optimal performance.
CNC Waterjet Cutting
CNC waterjet cutting employs high-pressure water to achieve cold cutting without affecting the material’s properties. This method is particularly suitable for sensitive alloys and applications in food processing. While it offers the advantage of no heat-affected zone, it tends to be slower for thicker metals and has higher operational costs. B2B buyers must consider the types of materials they will be working with and the expected production volume to make an informed decision on whether this technology aligns with their needs.
Related Video: CNC Working High Speed Milling – iMachining Cutting Metal – CNC Machine Process
Key Industrial Applications of cnc metal cutting machine
Industry/Sector | Specific Application of CNC Metal Cutting Machine | Value/Benefit for the Business | Key Sourcing Considerations for this Application |
---|---|---|---|
Automotive | Precision components manufacturing (e.g., engine parts, transmission housings) | Enhanced performance and reliability of vehicles | Supplier capabilities, precision standards, lead times |
Aerospace | Fabrication of structural components and tooling | High safety standards and weight reduction | Certification (e.g., AS9100), material traceability, cost |
Electronics | Production of enclosures and heat sinks | Improved thermal management and device longevity | Material compatibility, precision requirements, volume needs |
Construction and Heavy Machinery | Custom metal frameworks and structural supports | Increased durability and project adaptability | Material sourcing, local regulations, fabrication capabilities |
Medical Devices | Manufacturing of surgical instruments and implants | Compliance with stringent health regulations | Quality certifications (ISO 13485), precision, biocompatibility |
Automotive Industry
CNC metal cutting machines are crucial in the automotive sector for manufacturing precision components such as engine parts and transmission housings. These components must meet stringent performance and safety standards. For international buyers, particularly in Africa and South America, sourcing from reliable suppliers with advanced capabilities is essential to ensure quality and compliance. Buyers should prioritize suppliers that can demonstrate high precision and repeatability, as well as the ability to manage large production volumes efficiently.
Aerospace Sector
In aerospace, CNC metal cutting is utilized for fabricating structural components and tooling that must adhere to rigorous safety standards. The lightweight nature of these components is critical for fuel efficiency and performance. Buyers in the Middle East and Europe should seek suppliers with certifications like AS9100 to ensure compliance with aerospace industry standards. Additionally, the ability to provide traceability for materials used is vital for maintaining safety and quality assurance throughout the supply chain.
Electronics Industry
The electronics sector leverages CNC metal cutting for producing enclosures and heat sinks that enhance thermal management and extend the lifespan of devices. Precision is paramount, as even minor deviations can lead to product failures. B2B buyers should consider material compatibility and specific precision requirements when sourcing CNC services. Ensuring that suppliers can handle various metal types and provide rapid prototyping capabilities is crucial for meeting the fast-paced demands of the electronics market, especially for companies in emerging markets.
Construction and Heavy Machinery
CNC metal cutting machines are employed in the construction industry for creating custom metal frameworks and structural supports. These components must be durable and adaptable to various project requirements. Buyers should focus on local regulations regarding construction materials and safety standards when sourcing. Additionally, evaluating a supplier’s fabrication capabilities and material sourcing options can lead to significant cost savings and increased project efficiency.
Medical Devices Sector
In the medical device industry, CNC metal cutting is vital for manufacturing surgical instruments and implants that must meet strict health regulations. Compliance with quality certifications such as ISO 13485 is essential for international buyers. Precision is critical, as any inaccuracies can compromise device safety and effectiveness. Buyers should ensure that their suppliers have the necessary expertise in biocompatibility and can provide detailed documentation to support regulatory compliance.
Strategic Material Selection Guide for cnc metal cutting machine
Analysis of Common Materials for CNC Metal Cutting Machines
When selecting materials for CNC metal cutting applications, international B2B buyers must consider properties that affect performance, durability, and cost. Here, we analyze four common materials: Aluminum, Stainless Steel, Carbon Steel, and Titanium. Each material has unique characteristics that impact its suitability for various applications.
Aluminum
Key Properties: Aluminum is lightweight, corrosion-resistant, and has excellent thermal and electrical conductivity. It typically performs well under moderate temperature and pressure conditions.
Pros & Cons: The primary advantage of aluminum is its low density, which makes it easy to machine and reduces transportation costs. However, it is less durable than steel and may not withstand high-stress applications. The cost of aluminum is generally moderate, but prices can fluctuate based on market demand.
Impact on Application: Aluminum is widely used in automotive, aerospace, and consumer electronics due to its favorable strength-to-weight ratio. It is compatible with various media, including air and water, but may not be suitable for high-pressure applications without reinforcement.
Considerations for International Buyers: Buyers should ensure compliance with international standards such as ASTM B221 or DIN 1725. In regions like Africa and South America, sourcing aluminum may involve navigating local regulations regarding import duties and material certifications.
Stainless Steel
Key Properties: Stainless steel is known for its high corrosion resistance, strength, and ability to withstand elevated temperatures. It maintains structural integrity under varying environmental conditions.
Pros & Cons: Its durability makes stainless steel ideal for demanding applications in the food, medical, and chemical industries. However, it can be more challenging to machine than aluminum, leading to higher manufacturing costs. The relative cost of stainless steel is typically high compared to other metals.
Impact on Application: Stainless steel is compatible with a wide range of media, including corrosive substances, making it suitable for applications in harsh environments. Its strength and resistance to oxidation ensure longevity in critical components.
Considerations for International Buyers: Buyers should verify compliance with standards such as ASTM A240 or JIS G4303. In Europe, the preference for specific grades (e.g., 304, 316) may influence sourcing decisions, while buyers in the Middle East should consider local availability and pricing.
Carbon Steel
Key Properties: Carbon steel offers high tensile strength and hardness, making it suitable for high-stress applications. However, it is less resistant to corrosion compared to stainless steel.
Pros & Cons: Carbon steel is relatively inexpensive and easy to machine, making it a popular choice for structural components and heavy machinery. The downside is its susceptibility to rust, which can necessitate protective coatings or treatments, adding to overall costs.
Impact on Application: This material is commonly used in construction, automotive, and manufacturing applications where strength is paramount. It is compatible with various media but requires careful consideration of environmental factors to prevent corrosion.
Considerations for International Buyers: Buyers should be aware of standards such as ASTM A36 or DIN 17100. In regions like Africa, where moisture levels can be high, the need for protective coatings should be factored into procurement decisions.
Titanium
Key Properties: Titanium is renowned for its high strength-to-weight ratio and exceptional corrosion resistance, especially in harsh environments. It performs well at high temperatures and has a low thermal expansion coefficient.
Pros & Cons: The primary advantage of titanium is its durability and lightweight nature, making it ideal for aerospace and medical applications. However, it is expensive and can be difficult to machine, leading to higher manufacturing costs.
Impact on Application: Titanium is suitable for applications requiring high performance, such as aerospace components and medical implants. Its compatibility with aggressive media makes it a preferred choice in chemical processing.
Considerations for International Buyers: Compliance with standards such as ASTM F136 or JIS T 2001 is crucial. Buyers from Europe and the Middle East should consider the availability of titanium and its cost implications, as sourcing can be more complex than for other metals.
Summary Table
Material | Typical Use Case for CNC Metal Cutting Machine | Key Advantage | Key Disadvantage/Limitation | Relative Cost (Low/Med/High) |
---|---|---|---|---|
Aluminum | Automotive parts, electronics | Lightweight and easy to machine | Less durable than steel | Medium |
Stainless Steel | Food processing, medical devices | High corrosion resistance | More challenging to machine | High |
Carbon Steel | Construction, heavy machinery | Inexpensive and strong | Susceptible to rust | Low |
Titanium | Aerospace components, medical implants | High strength-to-weight ratio | Expensive and difficult to machine | High |
By understanding the properties, advantages, and limitations of these materials, international B2B buyers can make informed decisions that align with their operational needs and market conditions.
In-depth Look: Manufacturing Processes and Quality Assurance for cnc metal cutting machine
The manufacturing processes and quality assurance for CNC metal cutting machines are vital aspects that international B2B buyers must understand to make informed purchasing decisions. This section will explore the main stages of manufacturing, key techniques, international standards, and quality control checkpoints.
Manufacturing Processes
The production of CNC metal cutting machines typically involves several key stages:
- Material Preparation
– Selection of Raw Materials: The process begins with sourcing high-quality raw materials, such as structural steel, aluminum, and other alloys. Buyers should ensure that the materials meet industry specifications for strength, durability, and machinability.
– Cutting and Shaping: The raw materials are initially cut into rough shapes using saws or plasma cutters. This stage is crucial for ensuring that the components fit together correctly in later stages.
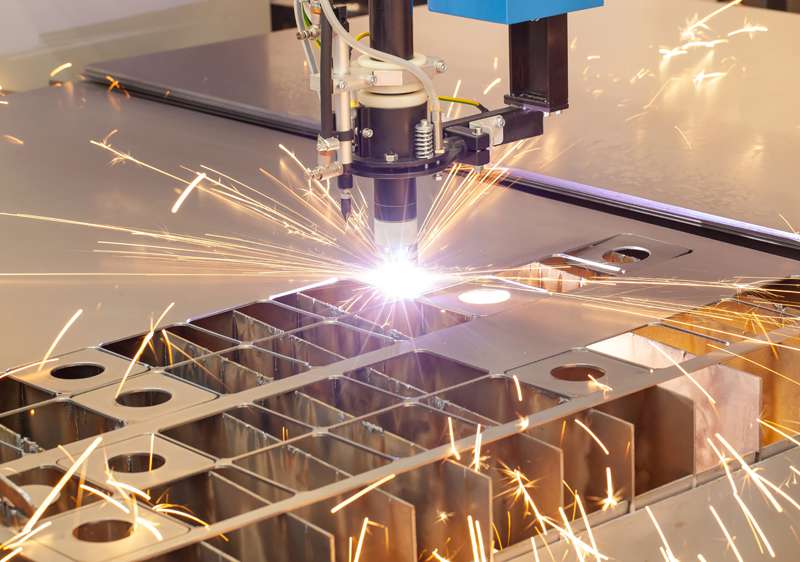
Illustrative Image (Source: Google Search)
-
Forming
– Machining: CNC machines utilize various machining processes like milling, turning, and grinding to achieve precise dimensions and surface finishes. Advanced CNC technology allows for multi-axis operations, enhancing the complexity of shapes that can be manufactured.
– Welding and Assembly: Components are welded together or assembled using bolts and fasteners. Buyers should inquire about the welding techniques used (e.g., MIG, TIG) as they impact the structural integrity of the machine. -
Finishing
– Surface Treatments: After assembly, machines undergo surface treatments such as anodizing, painting, or powder coating to enhance durability and corrosion resistance. These treatments are essential for machines operating in harsh environments.
– Quality Finishing: Precision finishing processes, such as grinding and polishing, ensure that all surfaces meet the required tolerances and provide the necessary finish for operational efficiency.
Key Techniques in Manufacturing
- CNC Programming: The efficiency of the CNC machine relies heavily on the programming of the control software. Skilled programmers develop and optimize the G-code that dictates the machine’s movements and operations.
- Automation: Many manufacturers incorporate automation technologies, such as robotic arms and automated tool changers, to improve production speed and reduce human error.
- Lean Manufacturing: Adopting lean principles helps manufacturers minimize waste and enhance productivity. This approach is particularly beneficial for international buyers looking for cost-effective solutions.
Quality Assurance
Quality assurance in the manufacturing of CNC metal cutting machines is crucial for ensuring that the final product meets both industry standards and customer expectations. Key elements include:
-
International Standards
– ISO 9001: This globally recognized standard focuses on quality management systems. Suppliers should be certified to ISO 9001 to demonstrate their commitment to maintaining high-quality manufacturing processes.
– CE Marking: For buyers in Europe, CE marking indicates that the machine complies with EU safety, health, and environmental protection standards. Ensuring that the supplier provides machines with this certification is essential for market entry. -
Industry-Specific Standards
– API Certification: For manufacturers supplying the oil and gas sector, API (American Petroleum Institute) standards ensure that products meet rigorous safety and performance requirements.
– ASTM Standards: Various ASTM standards apply to materials and components used in CNC machines, ensuring consistency and reliability. -
Quality Control Checkpoints
– Incoming Quality Control (IQC): This stage verifies the quality of raw materials before they enter the manufacturing process. Buyers should ensure that suppliers have strict IQC protocols to filter out subpar materials.
– In-Process Quality Control (IPQC): Regular inspections during the machining and assembly phases help catch defects early. This includes monitoring dimensions, surface finishes, and tolerances.
– Final Quality Control (FQC): A comprehensive review of the finished product occurs before shipping. This includes functional testing, performance evaluations, and compliance checks against specifications.
Common Testing Methods
- Dimensional Inspection: Utilizing calipers, micrometers, and coordinate measuring machines (CMM) to ensure components meet specified tolerances.
- Non-Destructive Testing (NDT): Techniques such as ultrasonic testing and magnetic particle inspection assess the integrity of welds and materials without damaging the components.
- Performance Testing: Machines may undergo operational tests to verify that they perform as intended under load and operational conditions.
Verifying Supplier Quality Control
For B2B buyers, verifying a supplier’s quality control processes is essential to mitigate risks associated with machine failure or non-compliance. Here are some actionable steps:
- Supplier Audits: Conduct on-site audits to assess the manufacturing environment, quality control systems, and adherence to standards. This provides firsthand insight into the supplier’s operations.
- Request Quality Reports: Ask suppliers for detailed quality control reports that outline testing methods, results, and corrective actions taken for any non-conformances.
- Third-Party Inspections: Engage independent third-party inspection agencies to evaluate the machines before shipment. These inspections can provide an unbiased assessment of quality and compliance.
Quality Control Nuances for International Buyers
International buyers, particularly from Africa, South America, the Middle East, and Europe, must navigate additional complexities in quality control:
- Cultural Differences: Understanding local manufacturing practices and cultural attitudes toward quality can aid in building effective supplier relationships.
- Logistics and Shipping: Ensure that quality control checks are integrated into the shipping process to prevent damage during transit. Buyers should consider insurance options for high-value equipment.
- Regulatory Compliance: Be aware of specific regulations in the buyer’s home country that may affect machine specifications, safety standards, and importation processes.
By comprehensively understanding these manufacturing processes and quality assurance measures, international B2B buyers can make informed decisions that not only enhance operational efficiency but also ensure the reliability and longevity of their CNC metal cutting machines.
Related Video: CNC Machine Working Process 5 Axis Machining Metal & Aluminium Aerospace
Comprehensive Cost and Pricing Analysis for cnc metal cutting machine Sourcing
When sourcing CNC metal cutting machines, understanding the comprehensive cost structure and pricing dynamics is crucial for international B2B buyers, particularly from Africa, South America, the Middle East, and Europe. The following analysis outlines the key cost components, price influencers, and actionable buyer tips to facilitate informed purchasing decisions.
Cost Components
-
Materials: The cost of raw materials, including metal types (steel, aluminum, etc.), plays a significant role in the overall price of CNC machines. High-quality materials can enhance durability and precision but may also increase initial costs.
-
Labor: Skilled labor is essential for operating CNC machines and ensuring high-quality output. Labor costs can vary significantly based on geographical location, experience level, and the complexity of the tasks involved.
-
Manufacturing Overhead: This includes indirect costs such as utilities, facility rent, and equipment maintenance. Understanding the overhead structure of suppliers can provide insights into their pricing strategies.
-
Tooling: Custom tooling may be required for specific machining processes, which can add to the total cost. Buyers should inquire about tooling costs and whether they are included in the quoted price.
-
Quality Control (QC): Implementing robust QC measures ensures that the machines meet the required standards and specifications. This may involve additional costs for testing and certification, which are essential for maintaining product integrity.
-
Logistics: Shipping and handling costs are crucial, especially for international buyers. Factors such as distance, mode of transport, and customs duties can significantly affect the final price.
-
Margin: Supplier profit margins can vary, often depending on their market position, brand reputation, and service offerings. Buyers should compare margins across different suppliers to identify the most cost-effective options.
Price Influencers
-
Volume/MOQ: Bulk purchases often come with discounts. Understanding the minimum order quantities (MOQ) can help buyers negotiate better pricing structures.
-
Specifications/Customization: Custom specifications may increase costs due to the additional engineering and production requirements. Buyers should assess whether standard options can meet their needs to minimize expenses.
-
Materials: The choice of materials not only influences the machine’s performance but also its price. High-performance materials typically command higher prices.
-
Quality/Certifications: Machines that meet international quality standards (ISO, CE, etc.) may be priced higher due to the added assurance of quality. Buyers should weigh the benefits of certifications against their budgets.
-
Supplier Factors: Reputation, location, and service capabilities of the supplier can affect pricing. Established suppliers may charge a premium for their reliability and after-sales support.
-
Incoterms: Understanding the terms of shipping (FOB, CIF, etc.) is vital as they dictate who bears the shipping costs and risks, directly impacting the total expenditure.
Buyer Tips
-
Negotiation: Leverage your purchasing power by negotiating terms, particularly for volume purchases. Suppliers may offer flexibility in pricing or additional services.
-
Cost-Efficiency: Evaluate the total cost of ownership (TCO), which includes purchase price, maintenance, and operational costs over the machine’s lifespan. This holistic view helps identify the most cost-effective option.
-
Pricing Nuances: Be aware of regional pricing differences. Suppliers in emerging markets may offer competitive pricing, but consider potential trade-offs in quality and service.
-
Research and Compare: Conduct thorough market research to compare prices and specifications from multiple suppliers. Utilize industry contacts and trade shows for insights into reputable manufacturers.
-
Understand Local Regulations: Familiarize yourself with import duties, taxes, and compliance requirements in your region to avoid unexpected costs.
By considering these components, influences, and strategic tips, international B2B buyers can navigate the complexities of CNC metal cutting machine sourcing effectively, ensuring they make informed and cost-efficient decisions.
Disclaimer: Prices are indicative and may vary based on market conditions, supplier negotiations, and specific project requirements. Always seek multiple quotes for accurate pricing.
Spotlight on Potential cnc metal cutting machine Manufacturers and Suppliers
This section looks at several manufacturers active in the ‘cnc metal cutting machine’ market. This is a representative sample for illustrative purposes; B2B buyers must conduct extensive due diligence before any transaction. Information is synthesized from public sources and general industry knowledge.
Essential Technical Properties and Trade Terminology for cnc metal cutting machine
Key Technical Properties of CNC Metal Cutting Machines
Understanding the essential specifications of CNC metal cutting machines is critical for B2B buyers to ensure that they select the right equipment for their manufacturing needs. Here are some of the most important technical properties:
-
Material Grade
Material grade refers to the specific type of metal being cut, such as steel, aluminum, or titanium. Each material has distinct properties, including hardness, tensile strength, and machinability. For buyers, choosing the right machine that can handle the specific material grade is essential for achieving desired outcomes and ensuring durability in the final products. -
Tolerance
Tolerance indicates the allowable variation in a part’s dimensions. For CNC machining, tolerances can range from ±0.01 mm to ±0.5 mm, depending on the complexity of the part and the capabilities of the machine. High-precision applications, such as aerospace components, often require tighter tolerances. B2B buyers must understand the tolerances their projects require to select machines capable of meeting those specifications. -
Cutting Speed
Cutting speed is the speed at which the cutting tool moves through the material, typically measured in meters per minute (m/min). Faster cutting speeds can improve productivity but may affect the quality of the cut and the tool’s lifespan. Buyers should consider their production volume and the specific materials being processed when evaluating cutting speeds to balance efficiency with quality. -
Axis Configuration
CNC machines can have different axis configurations, such as 3-axis, 4-axis, or even 5-axis. The number of axes affects the machine’s ability to create complex geometries. For buyers, understanding the axis configuration is vital for ensuring that the machine can produce the required part shapes without the need for extensive re-fixturing, thus optimizing production time. -
Power Rating
The power rating of a CNC machine indicates its capability to cut through various materials. Higher power ratings allow for deeper cuts and the ability to handle tougher materials. B2B buyers should assess the power needs based on their anticipated workloads to avoid underperformance in production.
Common Trade Terminology
Familiarity with industry-specific jargon is crucial for effective communication and negotiation in the CNC metal cutting market. Here are some essential terms:
-
OEM (Original Equipment Manufacturer)
An OEM is a company that produces parts or equipment that may be marketed by another manufacturer. In the CNC industry, working with OEMs can ensure the quality and compatibility of components, which is important for maintaining production standards. -
MOQ (Minimum Order Quantity)
MOQ refers to the smallest quantity of a product that a supplier is willing to sell. Understanding MOQs is vital for B2B buyers to ensure that they can meet their production needs without overcommitting financially, especially when sourcing from international suppliers. -
RFQ (Request for Quotation)
An RFQ is a document that a buyer sends to suppliers requesting pricing and terms for specific goods or services. It is a critical step in the procurement process, allowing buyers to compare costs and negotiate better terms with potential suppliers.
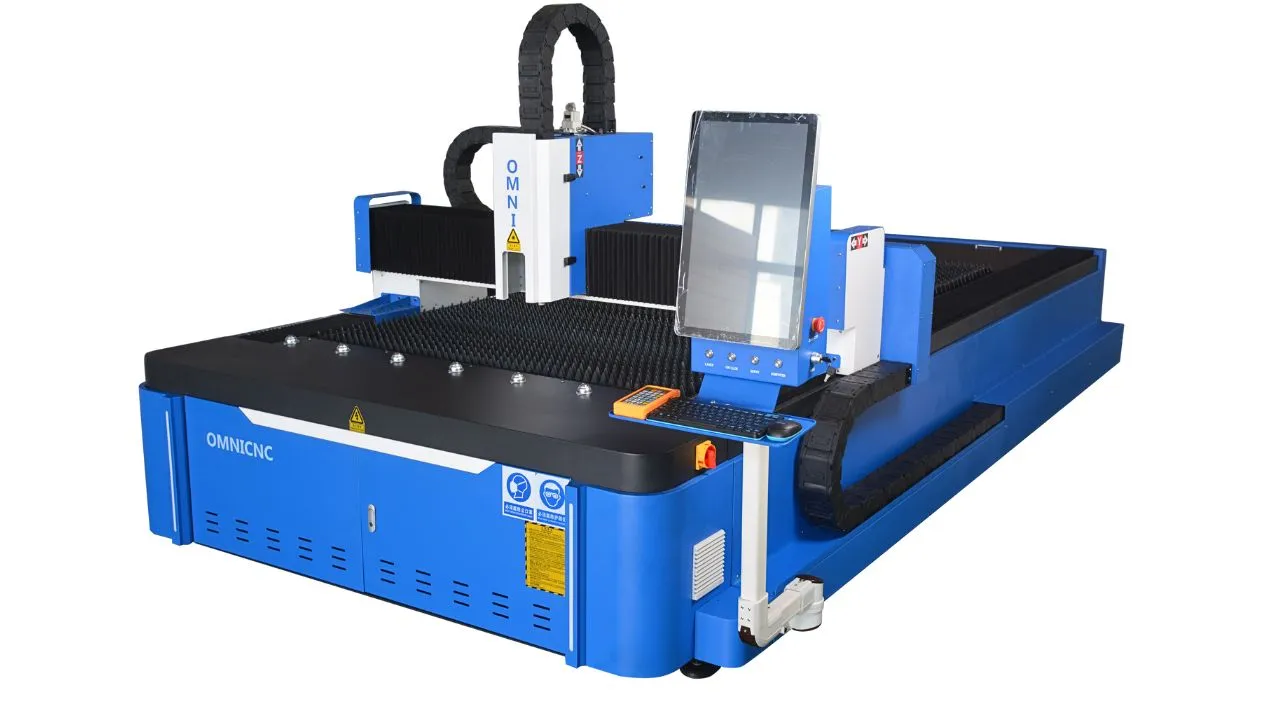
Illustrative Image (Source: Google Search)
-
Incoterms
Incoterms are international commercial terms that define the responsibilities of buyers and sellers in international transactions. Understanding these terms helps B2B buyers clarify shipping responsibilities, risks, and costs, ensuring smoother logistics and compliance. -
Lead Time
Lead time refers to the time it takes from placing an order to receiving the finished product. This is a crucial factor for B2B buyers to consider, as longer lead times can impact project schedules and customer satisfaction. Buyers should discuss lead times upfront to align expectations with suppliers. -
After-sales Support
After-sales support encompasses the services provided by suppliers after a purchase, including maintenance, training, and troubleshooting. Reliable after-sales support is essential for maximizing the efficiency and longevity of CNC machines, making it a critical consideration for buyers in their supplier evaluations.
Navigating Market Dynamics, Sourcing Trends, and Sustainability in the cnc metal cutting machine Sector
Market Overview & Key Trends
The CNC metal cutting machine sector is currently experiencing significant transformation driven by globalization, technological advancements, and evolving buyer expectations. Key global drivers include the increasing demand for precision manufacturing across various industries such as automotive, aerospace, and electronics. Emerging markets in Africa and South America are becoming attractive hubs for manufacturing, offering both cost-effective production and a growing skilled workforce.
International B2B buyers are witnessing trends such as the rise of Industry 4.0, where smart manufacturing technologies like IoT and AI are integrated into CNC operations. This not only enhances operational efficiency but also enables real-time monitoring and predictive maintenance, reducing downtime and operational costs. Additionally, the trend towards automation is reshaping sourcing practices, with buyers increasingly seeking suppliers who can provide advanced, automated CNC solutions.
Furthermore, sustainability is becoming a pivotal consideration in the sourcing process. Buyers are looking for suppliers that prioritize eco-friendly practices and materials, as regulatory pressures and consumer expectations shift towards greener manufacturing. The demand for higher-quality, longer-lasting products is also influencing market dynamics, as businesses strive to minimize waste and maximize resource efficiency.
In summary, international B2B buyers should stay informed about these trends to leverage opportunities in sourcing CNC metal cutting machines that align with both operational goals and sustainability objectives.
Sustainability & Ethical Sourcing in B2B
Sustainability is no longer just a trend; it has become a vital component of strategic sourcing in the CNC metal cutting machine sector. The environmental impact of manufacturing processes, including energy consumption and waste generation, is under scrutiny from both regulators and consumers. Consequently, B2B buyers must prioritize suppliers who demonstrate a commitment to reducing their carbon footprint through energy-efficient technologies and sustainable practices.
Ethical supply chains are also gaining prominence, as buyers increasingly seek transparency in sourcing materials and components. This includes verifying that suppliers adhere to ethical labor practices and responsible sourcing of raw materials. Certifications such as ISO 14001 for environmental management and ISO 45001 for occupational health and safety can serve as indicators of a supplier’s commitment to sustainability.
Moreover, the use of “green” materials—such as recycled metals and eco-friendly lubricants—can significantly enhance a company’s sustainability profile. B2B buyers should actively seek partnerships with suppliers who are certified for using sustainable materials and are willing to invest in environmentally friendly manufacturing processes. By prioritizing sustainability and ethical sourcing, buyers can not only fulfill regulatory obligations but also enhance brand reputation and customer loyalty.
Brief Evolution/History
The CNC metal cutting machine industry has evolved significantly since the introduction of computer numerical control technology in the 1940s and 1950s. Initially developed for military applications, CNC technology quickly expanded into commercial manufacturing, revolutionizing the metalworking sector. The introduction of automation in the 1980s allowed for enhanced precision and efficiency, leading to widespread adoption across various industries.
Today, the evolution continues with the integration of advanced technologies such as IoT, AI, and machine learning. These innovations are transforming traditional CNC operations into smart manufacturing environments, enabling real-time data analysis and improved decision-making. For B2B buyers, understanding this evolution is crucial in making informed sourcing decisions that align with modern manufacturing practices and market demands.
Frequently Asked Questions (FAQs) for B2B Buyers of cnc metal cutting machine
-
What key factors should I consider when vetting suppliers of CNC metal cutting machines?
When vetting suppliers, prioritize their experience and reputation in the industry. Check for certifications such as ISO 9001, which indicates a commitment to quality management. Evaluate their technical capabilities, including machine specifications and customization options, to ensure they meet your production needs. Additionally, assess their after-sales support and service availability, as reliable maintenance is crucial for operational efficiency. Lastly, consider their financial stability and customer references to gauge their reliability and trustworthiness. -
Can CNC metal cutting machines be customized to meet specific project requirements?
Yes, many manufacturers offer customization options for CNC metal cutting machines. This may include tailored machine specifications, additional tooling, or software adaptations to suit unique production needs. When discussing customization, provide detailed specifications and applications to ensure that the supplier fully understands your requirements. Be prepared for potential adjustments in lead times and costs, as custom solutions often require additional engineering and production time. -
What are the typical minimum order quantities (MOQs) and lead times for CNC metal cutting machines?
Minimum order quantities can vary significantly based on the supplier and the type of machine. Generally, for standard CNC machines, MOQs might range from one unit for small-scale buyers to several units for bulk orders. Lead times typically depend on the complexity of the machine and customization requirements, ranging from a few weeks for off-the-shelf models to several months for bespoke solutions. Always confirm these details upfront to align your production schedule with supplier capabilities. -
How can I ensure the quality of CNC metal cutting machines and their compliance with industry standards?
To ensure quality, request documentation of compliance with relevant industry standards, such as CE marking in Europe or ANSI in the United States. Inspecting machines before purchase, if feasible, is ideal to evaluate their condition and performance. Additionally, inquire about the supplier’s quality control processes, including testing protocols and certifications. Establishing clear quality expectations in your contract can also mitigate risks associated with non-compliance or substandard products. -
What payment terms are common in international trade for CNC metal cutting machines?
Payment terms can vary widely among suppliers. Common practices include a deposit (typically 30-50%) upfront, with the balance due upon delivery or installation. Some suppliers may offer letters of credit or escrow services to secure transactions, which can be beneficial for large orders. It’s essential to clarify payment methods (bank transfer, credit card, etc.) and currency considerations, as fluctuations can impact final costs. Establishing clear terms in the purchase agreement is crucial for protecting your investment. -
What logistics considerations should I keep in mind when importing CNC metal cutting machines?
Logistics for importing CNC machines require careful planning. Consider shipping methods (air freight vs. sea freight), as this will affect costs and delivery times. Ensure that you understand customs regulations and duties in your country to avoid unexpected fees. Additionally, work with a logistics partner experienced in machinery imports to navigate complexities such as packaging, insurance, and transport safety. Finally, confirm that the supplier can assist with documentation needed for customs clearance. -
How can I handle disputes with suppliers effectively?
To manage disputes effectively, establish clear communication channels and maintain a record of all interactions. When issues arise, attempt to resolve them amicably through direct dialogue. If necessary, refer to the terms outlined in your contract, including warranties and return policies. Mediation or arbitration can be effective alternatives to litigation, often resolving disputes more quickly and cost-effectively. Additionally, consider including a clause in your contract that specifies the jurisdiction for resolving disputes to avoid confusion later. -
What are the common challenges faced when sourcing CNC metal cutting machines internationally?
Common challenges include language barriers, differing quality standards, and varying lead times that can disrupt production schedules. Cultural differences may also impact negotiation styles and business practices. To mitigate these issues, conduct thorough research on potential suppliers and consider working with local intermediaries who understand the market. Establishing clear specifications and expectations from the outset can also help minimize misunderstandings and ensure a smoother sourcing process.
Important Disclaimer & Terms of Use
⚠️ Important Disclaimer
The information provided in this guide, including content regarding manufacturers, technical specifications, and market analysis, is for informational and educational purposes only. It does not constitute professional procurement advice, financial advice, or legal advice.
While we have made every effort to ensure the accuracy and timeliness of the information, we are not responsible for any errors, omissions, or outdated information. Market conditions, company details, and technical standards are subject to change.
B2B buyers must conduct their own independent and thorough due diligence before making any purchasing decisions. This includes contacting suppliers directly, verifying certifications, requesting samples, and seeking professional consultation. The risk of relying on any information in this guide is borne solely by the reader.
Strategic Sourcing Conclusion and Outlook for cnc metal cutting machine
In conclusion, effective strategic sourcing of CNC metal cutting machines is essential for international B2B buyers looking to enhance their manufacturing capabilities and drive competitive advantage. By understanding the various types of CNC machines—such as milling, turning, laser, and plasma cutting—buyers can make informed decisions that align with their specific industry needs. Key takeaways include the importance of evaluating supplier capabilities, assessing material compatibility, and considering total cost of ownership, including maintenance and support.
As you navigate the global market, remember that the right machine can significantly impact product quality, operational efficiency, and ultimately, profitability. For buyers in Africa, South America, the Middle East, and Europe, leveraging local knowledge while exploring international partnerships can lead to fruitful collaborations and innovative solutions.
Looking ahead, stay attuned to evolving technologies and market trends that will shape the future of CNC machining. Embrace the opportunity to invest strategically in CNC equipment that not only meets current demands but also positions your business for long-term success. Take action today—evaluate your options, seek expert advice, and embark on a journey toward manufacturing excellence.