Your Ultimate Guide to Sourcing Cnc Milling Machine Projects
Introduction: Navigating the Global Market for cnc milling machine projects
CNC milling machine projects are pivotal in shaping the future of manufacturing across diverse sectors, including aerospace, automotive, and healthcare. As a cornerstone of precision engineering, CNC milling empowers businesses to produce intricate components with exceptional accuracy and efficiency. For international B2B buyers, especially those operating in rapidly evolving markets such as Africa, South America, the Middle East, and Europe, mastering the nuances of CNC milling sourcing is essential for optimizing production capabilities and reducing costs.
This comprehensive guide serves as a valuable resource, providing insights into various aspects of CNC milling that can significantly enhance your sourcing strategy. We explore the types of CNC milling technologies available and the suitable materials for different applications, ensuring you make informed decisions tailored to your specific needs. Furthermore, we delve into manufacturing and quality control standards, equipping you with the knowledge to identify suppliers who meet global benchmarks.
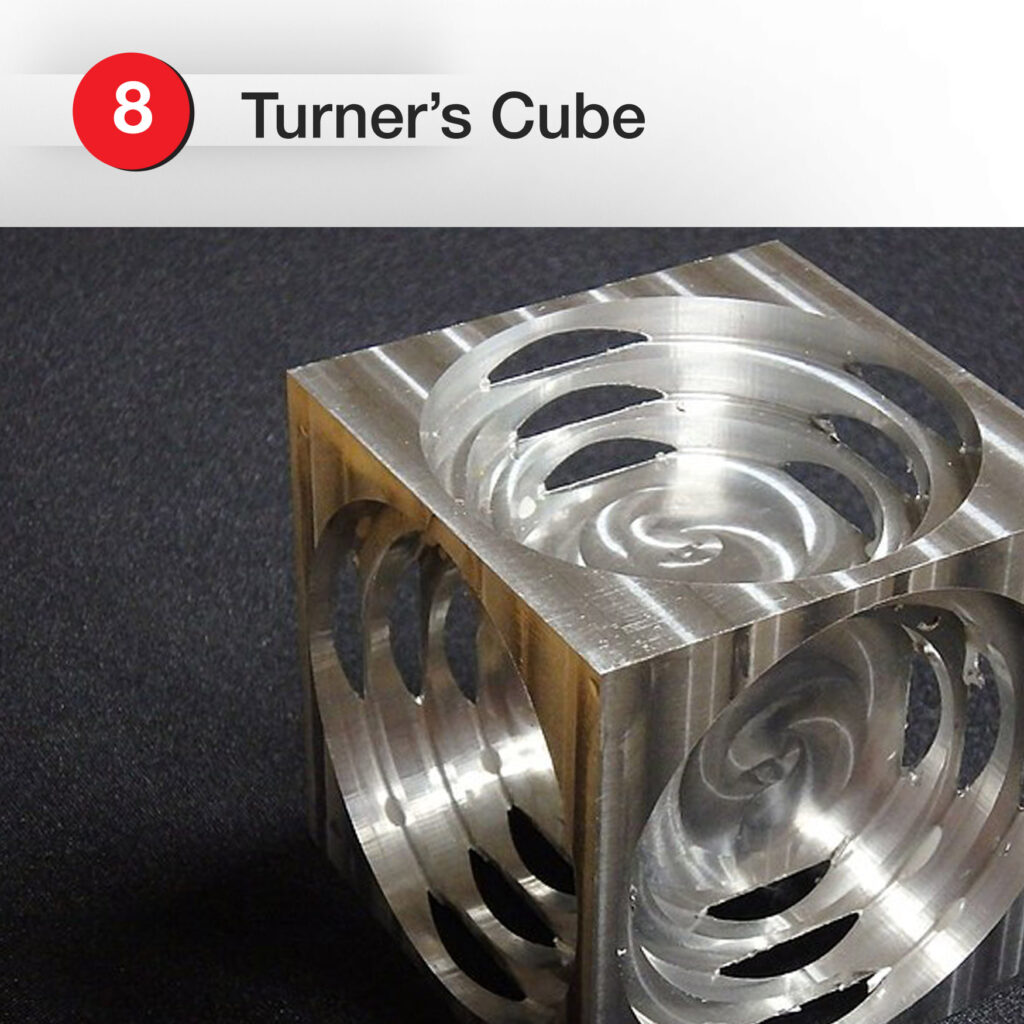
Illustrative Image (Source: Google Search)
Additionally, our guide offers strategies for supplier selection, helping you evaluate potential partners based on their capabilities and reliability. Understanding cost structures and market dynamics will enable you to navigate pricing and lead times effectively, while our Frequently Asked Questions section addresses common concerns encountered in cross-border procurement.
By leveraging the actionable insights within this guide, international B2B buyers can confidently navigate the global CNC milling landscape, mitigate sourcing risks, and forge strong supplier relationships that are critical for sustained business growth.
Understanding cnc milling machine projects Types and Variations
Type Name | Key Distinguishing Features | Primary B2B Applications | Brief Pros & Cons for Buyers |
---|---|---|---|
Vertical CNC Milling | Spindle oriented vertically; versatile 3-axis setup | Prototyping, precision components | Cost-effective, easy to operate; height limits, slower for large parts |
Horizontal CNC Milling | Spindle parallel to work table; supports larger workpieces | Automotive, heavy equipment, large runs | High removal rates, robust for tough jobs; higher cost, larger footprint |
5-Axis CNC Milling | Simultaneous movement along 5 axes for complex geometries | Aerospace, medical, advanced tooling | Complex shapes, fewer setups; higher purchase price, requires skilled operators |
Face Milling | Perpendicular cutter creates flat surfaces | Preparation for assembly, die making | Excellent surface finish; limited to surface operations, not complex profiles |
Gang Milling | Multiple cutters operate simultaneously for fast machining | Mass production, batch processing | Increases throughput; complex setup, limited flexibility for custom jobs |
Vertical CNC Milling
Vertical CNC milling machines are characterized by their spindle being positioned above the worktable, allowing for versatile three-axis operations. They are particularly suitable for projects requiring precision, such as prototyping and manufacturing small components. B2B buyers should consider their cost-effectiveness and ease of operation, making them ideal for regions with varying technical support. However, limitations in height capacity and slower processing for large parts are notable drawbacks.
Horizontal CNC Milling
Horizontal CNC milling machines orient their spindle parallel to the worktable, accommodating larger and heavier workpieces. This design is advantageous for industries like automotive and heavy equipment manufacturing, where high production volumes are common. B2B buyers should weigh the benefits of high material removal rates and robust performance against the higher capital costs and larger space requirements necessary for these machines.
5-Axis CNC Milling
5-axis CNC milling machines facilitate simultaneous movement along five axes, enabling the production of complex geometries in a single setup. This technology is crucial for sectors such as aerospace and medical device manufacturing, where precision is paramount. While the initial investment is significant and requires skilled operators, the reduced lead times and enhanced part accuracy make it a worthwhile option for B2B buyers dealing with intricate designs.
Face Milling
Face milling employs a cutter that works perpendicularly to the surface of the material, producing flat surfaces with superior finish quality. It is commonly used in preparation for assembly or in die-making processes. B2B buyers benefit from its efficiency and excellent surface finish; however, its application is limited to surface operations, which may not be suitable for more complex shapes.
Gang Milling
Gang milling involves multiple cutters working simultaneously, significantly speeding up the machining process for mass production and batch processing. This method is particularly effective for repetitive jobs, enhancing throughput. However, B2B buyers should consider the complexity of setup and limited flexibility for custom jobs, which may pose challenges for projects requiring varied specifications.
Related Video: DIY CNC Milling Machine – The Complete How to Build Video
Key Industrial Applications of cnc milling machine projects
Industry/Sector | Specific Application of CNC Milling Machine Projects | Value/Benefit for the Business | Key Sourcing Considerations for this Application |
---|---|---|---|
Aerospace | Precision components for aircraft assembly | Ensures safety and compliance with strict regulations | Supplier certifications (AS9100), material traceability |
Automotive | Engine components and transmission parts | Enhances performance and reliability of vehicles | Lead times, tooling capabilities, and cost structures |
Healthcare | Custom surgical instruments and implants | Improves patient outcomes and operational efficiency | Biocompatibility of materials, regulatory compliance |
Consumer Electronics | Enclosures and structural components for devices | Supports product durability and aesthetics | Material selection, surface finish requirements |
Industrial Equipment | Custom tooling and fixtures for manufacturing | Increases production efficiency and reduces downtime | Flexibility in production runs, precision requirements |
Aerospace Applications
In the aerospace industry, CNC milling is crucial for producing precision components such as brackets, housings, and other parts that must meet stringent safety and performance standards. These components often require tight tolerances and lightweight materials, which CNC milling can deliver efficiently. International B2B buyers must ensure that suppliers possess the necessary certifications, such as AS9100, and can provide full material traceability to comply with aviation regulations. This attention to detail not only enhances safety but also supports the overall integrity of aerospace projects.
Automotive Applications
CNC milling plays a vital role in the automotive sector, particularly in the production of engine components, transmission parts, and custom tooling. The precision achieved through CNC processes enhances the performance and reliability of vehicles, which is essential in a highly competitive market. Buyers should focus on suppliers that can demonstrate robust lead times and flexibility in tooling capabilities to adapt to changing automotive designs. Understanding cost structures is also key, as automotive projects often involve significant investment in precision manufacturing.
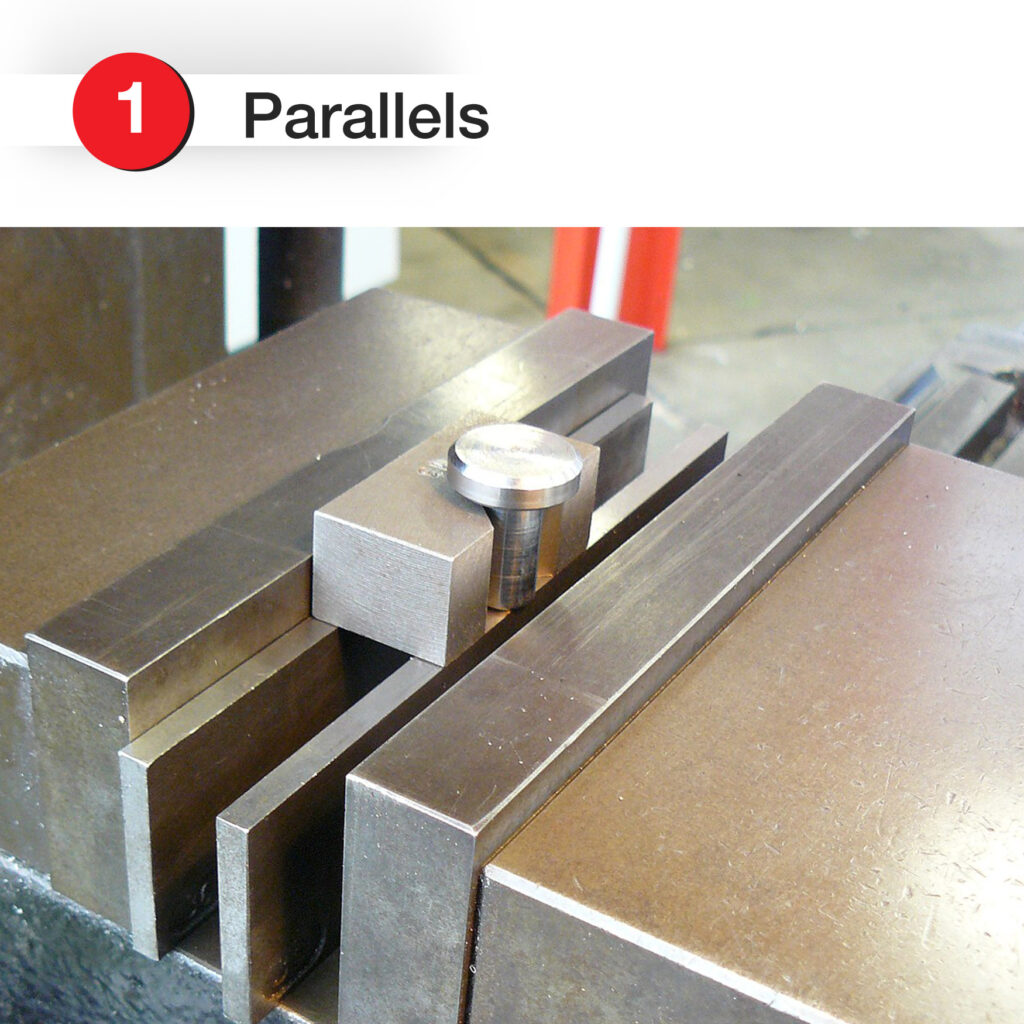
Illustrative Image (Source: Google Search)
Healthcare Applications
In healthcare, CNC milling is used to create custom surgical instruments and implants tailored to individual patient needs. The ability to produce complex geometries with high precision not only enhances surgical outcomes but also improves operational efficiency in medical facilities. B2B buyers in this sector must prioritize suppliers that comply with strict regulatory standards, particularly regarding biocompatibility of materials. This compliance ensures that products are safe for patient use and meets the evolving demands of the healthcare industry.
Consumer Electronics Applications
The consumer electronics industry relies on CNC milling for the production of enclosures and structural components that must balance durability with aesthetic appeal. CNC milling allows for intricate designs and high-quality surface finishes that are essential for modern electronic devices. Buyers should consider material selection carefully, as the right choice can impact the product’s longevity and marketability. Suppliers should also be evaluated based on their ability to meet specific surface finish requirements, ensuring that the final product aligns with consumer expectations.
Industrial Equipment Applications
CNC milling is instrumental in creating custom tooling and fixtures that enhance manufacturing processes across various industries. These components help streamline production efficiency and reduce downtime, critical factors for maintaining competitiveness. For international B2B buyers, sourcing considerations should include the flexibility of suppliers to handle varying production runs and their capabilities in meeting precision requirements. A focus on these aspects can lead to significant operational improvements and cost savings in industrial operations.
Strategic Material Selection Guide for cnc milling machine projects
When selecting materials for CNC milling machine projects, B2B buyers must consider various factors that influence performance, cost, and suitability for specific applications. Here, we analyze four common materials used in CNC milling, focusing on their properties, advantages, disadvantages, and implications for international buyers, particularly from Africa, South America, the Middle East, and Europe.
Aluminum
Key Properties:
Aluminum is lightweight, has excellent corrosion resistance, and can withstand moderate temperatures. Its thermal conductivity is high, making it suitable for applications requiring heat dissipation.
Pros & Cons:
Aluminum is known for its durability and ease of machining, resulting in lower manufacturing complexity. However, it can be more expensive than some alternatives, and its strength may not be sufficient for heavy-duty applications.
Impact on Application:
Aluminum is ideal for aerospace, automotive, and consumer electronics due to its strength-to-weight ratio and corrosion resistance. It is compatible with various media, including water and air.
Considerations for International Buyers:
Buyers should ensure compliance with international standards such as ASTM and DIN. In regions like Africa and South America, sourcing aluminum may involve navigating import tariffs and local regulations.
Steel
Key Properties:
Steel is known for its high strength, hardness, and durability. It can withstand high temperatures and pressures, making it suitable for demanding applications.
Pros & Cons:
Steel’s strength makes it a preferred choice for heavy machinery and structural components. However, it is heavier than aluminum and may require more complex machining processes, which can increase costs.
Impact on Application:
Steel is often used in automotive, construction, and heavy equipment industries. Its compatibility with various media, including oil and gas, makes it versatile for different applications.
Considerations for International Buyers:
Buyers must consider the specific type of steel (e.g., stainless, carbon) and its compliance with international standards. In regions like the Middle East, where corrosion resistance is critical, selecting the right grade of steel is essential.
Titanium
Key Properties:
Titanium is renowned for its high strength-to-weight ratio and exceptional corrosion resistance, particularly in harsh environments. It can withstand extreme temperatures and is biocompatible, making it suitable for medical applications.
Pros & Cons:
While titanium offers superior performance, it is one of the more expensive materials and can be challenging to machine, leading to higher manufacturing costs. Its applications are often limited to specialized industries.
Impact on Application:
Titanium is commonly used in aerospace, medical implants, and marine applications due to its durability and resistance to corrosion. It is compatible with various media, including seawater and chemicals.
Considerations for International Buyers:
Buyers should be aware of the stringent standards and certifications required for titanium components, especially in the aerospace and medical sectors. Compliance with ASTM and ISO standards is crucial.
Plastics (e.g., POM, Nylon)
Key Properties:
Engineering plastics like POM (Polyoxymethylene) and Nylon offer excellent strength, low friction, and good chemical resistance. They are lightweight and can operate effectively in a wide temperature range.
Pros & Cons:
Plastics are often less expensive than metals and easier to machine, resulting in lower manufacturing complexity. However, they may not be suitable for high-stress applications and can have lower thermal stability.
Impact on Application:
Plastics are widely used in consumer products, automotive components, and electrical housings. Their compatibility with various media, including water and oils, makes them versatile.
Considerations for International Buyers:
Buyers should verify the specific grades and compliance with international standards such as JIS and ASTM. In regions with developing manufacturing sectors, sourcing quality plastics may require due diligence on suppliers.
Summary Table
Material | Typical Use Case for cnc milling machine projects | Key Advantage | Key Disadvantage/Limitation | Relative Cost (Low/Med/High) |
---|---|---|---|---|
Aluminum | Aerospace, automotive components, consumer electronics | Lightweight, excellent corrosion resistance | Higher cost compared to some alternatives | Medium |
Steel | Heavy machinery, structural components, automotive | High strength and durability | Heavier and complex machining processes | Medium |
Titanium | Aerospace, medical implants, marine applications | Exceptional strength-to-weight ratio | Expensive and challenging to machine | High |
Plastics (POM, Nylon) | Consumer products, automotive components, electrical housings | Lower cost and easier to machine | Not suitable for high-stress applications | Low |
This guide provides a comprehensive overview of material selection for CNC milling projects, enabling international B2B buyers to make informed decisions that align with their operational needs and market conditions.
In-depth Look: Manufacturing Processes and Quality Assurance for cnc milling machine projects
Manufacturing Processes for CNC Milling Machine Projects
Understanding the manufacturing processes involved in CNC milling is crucial for B2B buyers aiming to optimize production quality and efficiency. The typical stages in CNC milling include material preparation, forming, assembly, and finishing. Each stage employs specific techniques and practices that contribute to the overall quality of the final product.
1. Material Preparation
Material preparation is the first critical step in the CNC milling process. It involves selecting the appropriate material based on the project specifications. Common materials used in CNC milling include metals (aluminum, steel, titanium) and engineered plastics (PVC, nylon).
- Material Selection: Buyers should consider factors such as mechanical properties, machinability, and cost. For instance, aluminum is lightweight and easy to machine, making it suitable for various applications, while titanium offers superior strength but is more challenging to work with.
- Cutting and Sizing: The material is cut to size using saws or shears before being loaded into the CNC machine. Precise sizing ensures that the material fits the machine specifications, reducing waste and improving efficiency.
2. Forming
In the forming stage, the CNC milling machine performs the actual machining process to create the desired part shapes.
- CNC Programming: This involves writing the program that dictates the machine’s movements. Effective programming is vital for achieving precision and repeatability. Buyers should ensure that suppliers utilize advanced programming software compatible with the latest CNC technologies.
- Machining Techniques: Different CNC milling techniques, such as vertical, horizontal, and 5-axis milling, are employed depending on the complexity of the components. For example, 5-axis milling allows for intricate designs and reduces the need for multiple setups, enhancing efficiency.
3. Assembly
After the parts are machined, they may require assembly, especially if they are components of a larger system.
- Sub-Assembly: Parts may be assembled into sub-units before final assembly. This process often involves additional machining or finishing processes to ensure that parts fit together correctly.
- Quality Checks: During assembly, it is essential to conduct preliminary quality checks to ensure that components meet specifications. This can include visual inspections and basic measurements.
4. Finishing
Finishing processes enhance the appearance and functionality of the machined parts.
- Surface Treatments: Techniques such as anodizing, plating, and polishing are commonly used. These not only improve aesthetics but also add protective coatings that enhance durability.
- Final Inspection: Before shipping, a final quality inspection is performed to ensure that the finished product meets all specifications.
Quality Assurance in CNC Milling
Quality assurance is paramount in CNC milling, ensuring that products not only meet customer expectations but also comply with international standards. Here are key aspects of quality control relevant to B2B buyers.
International Standards
B2B buyers should be aware of various international standards that govern manufacturing quality:
- ISO 9001: This standard focuses on quality management systems and is applicable across industries. It emphasizes a process-oriented approach and requires suppliers to demonstrate their capability to consistently provide products that meet customer and regulatory requirements.
- CE Marking: For products sold in the European Economic Area, CE marking indicates compliance with health, safety, and environmental protection standards.
- API Certification: Relevant for industries such as oil and gas, API certification ensures that products meet specific industry standards.
Quality Control Checkpoints
Effective quality control in CNC milling involves multiple checkpoints:
- Incoming Quality Control (IQC): This initial check assesses the quality of materials received from suppliers. Ensuring that raw materials meet specifications can prevent defects later in the process.
- In-Process Quality Control (IPQC): During machining, continuous monitoring and inspection of the process help identify any deviations from the expected quality standards.
- Final Quality Control (FQC): After production, the final product undergoes rigorous testing and inspection to ensure it meets all specifications before delivery.
Common Testing Methods
Several testing methods are utilized to verify the quality of machined parts:
- Dimensional Inspection: Using calipers, micrometers, or coordinate measuring machines (CMM) to measure the dimensions of the finished parts.
- Functional Testing: Assessing whether the part performs its intended function in real-world applications.
- Non-Destructive Testing (NDT): Techniques such as ultrasonic or magnetic particle testing can detect internal flaws without damaging the product.
Verifying Supplier Quality Control
For international B2B buyers, verifying a supplier’s quality control processes is essential to mitigate risks associated with sourcing.
- Supplier Audits: Conducting on-site audits allows buyers to evaluate the supplier’s manufacturing capabilities and quality management systems directly. This hands-on approach helps buyers assess compliance with international standards.
- Quality Reports: Requesting detailed quality assurance reports from suppliers can provide insights into their quality control processes, including test results and defect rates.
- Third-Party Inspections: Engaging independent inspection agencies can provide an unbiased assessment of product quality before shipment. This is particularly important for buyers in regions with varying standards of manufacturing quality.
QC and Certification Nuances for International Buyers
B2B buyers from regions like Africa, South America, the Middle East, and Europe should consider the following nuances regarding quality control and certification:
- Regional Standards: Familiarize yourself with local regulations and standards that may differ from international norms. This is crucial for ensuring compliance and avoiding costly penalties.
- Cultural Differences: Be aware of cultural differences that may influence communication and expectations regarding quality standards. Building strong relationships with suppliers can facilitate better quality assurance outcomes.
- Logistics and Supply Chain: Understand the logistics involved in transporting products, as this can impact quality. Ensure that suppliers have robust processes in place to handle products during shipping to prevent damage.
By comprehensively understanding the manufacturing processes and quality assurance practices associated with CNC milling machine projects, B2B buyers can make informed decisions that enhance product quality and ensure compliance with international standards.
Related Video: SMART Quality Control for Manufacturing
Comprehensive Cost and Pricing Analysis for cnc milling machine projects Sourcing
In the realm of CNC milling machine projects, understanding the comprehensive cost structure and pricing analysis is essential for international B2B buyers. The costs associated with sourcing CNC milling services can be broken down into several key components, each of which plays a significant role in determining the overall pricing.
Cost Components
-
Materials: The choice of materials significantly influences costs. Metals such as aluminum, steel, and titanium vary in price based on market demand and availability. Additionally, specialty materials like engineered plastics can also incur higher costs. Buyers should consider sourcing from local suppliers to reduce material costs, especially in regions like Africa and South America, where logistics can escalate expenses.
-
Labor: Skilled labor is crucial for CNC milling operations. Labor costs can vary widely depending on the region. For instance, labor costs in Europe may be higher than in some South American or African countries. Understanding local wage rates and the availability of skilled workers can help buyers negotiate better rates.
-
Manufacturing Overhead: This includes fixed costs associated with running a milling operation, such as rent, utilities, and maintenance of machinery. Overhead can be a significant percentage of total costs, particularly in countries with higher operational expenses. Buyers should inquire about the supplier’s operational efficiency to gauge how overhead is managed.
-
Tooling: Custom tooling can add a substantial expense to projects, especially when complex designs are involved. The initial investment in tooling can be high, but it is often amortized over large production runs. Buyers should assess the tooling requirements early in the project to budget accordingly.
-
Quality Control (QC): Ensuring product quality through rigorous QC processes is vital. Costs associated with QC can include testing, inspection, and certification. Buyers should seek suppliers with established quality management systems to avoid costly reworks and delays.
-
Logistics: Transportation and shipping costs can vary depending on the distance from the supplier to the buyer, as well as the chosen Incoterms. For international shipments, customs duties and taxes must also be factored into the logistics costs. Efficient logistics planning can help minimize these expenses.
-
Margin: Suppliers will typically include a profit margin in their pricing. This margin can vary based on market conditions and the supplier’s business model. Buyers should be aware of the typical margins in their industry to assess whether a supplier’s pricing is competitive.
Price Influencers
Several factors can influence pricing in CNC milling projects:
-
Volume/MOQ: Larger orders often lead to lower per-unit costs due to economies of scale. Buyers should consider consolidating orders to meet minimum order quantities (MOQ) for better pricing.
-
Specifications/Customization: Complex specifications and custom designs generally incur higher costs. Buyers should clearly define their requirements to avoid unexpected charges.
-
Materials: As mentioned, the choice of materials can significantly impact pricing. Buyers should research material options and their associated costs to make informed decisions.
-
Quality/Certifications: Suppliers with high-quality standards and certifications (such as ISO) may charge a premium. However, investing in quality can prevent future costs related to defects and rework.
-
Supplier Factors: The supplier’s location, reputation, and operational capabilities can affect pricing. Buyers should evaluate multiple suppliers to find the best balance between cost and quality.
-
Incoterms: The choice of Incoterms can influence logistics costs and risks. Buyers should select terms that align with their supply chain capabilities and risk tolerance.
Buyer Tips
-
Negotiation: Cultivating a good relationship with suppliers can enhance negotiation outcomes. Understanding their constraints and capabilities can lead to mutually beneficial agreements.
-
Cost-Efficiency: Consider the Total Cost of Ownership (TCO) rather than just the initial purchase price. This includes long-term costs such as maintenance, operational efficiency, and potential downtime.
-
Pricing Nuances: International buyers should be mindful of currency fluctuations and local economic conditions that may affect pricing. Engaging local experts can provide valuable insights into market trends.
In conclusion, a thorough understanding of the cost structure and pricing dynamics in CNC milling projects is critical for B2B buyers. By carefully considering these factors, buyers can make informed decisions that enhance their competitive edge in the global marketplace.
Spotlight on Potential cnc milling machine projects Manufacturers and Suppliers
This section looks at several manufacturers active in the ‘cnc milling machine projects’ market. This is a representative sample for illustrative purposes; B2B buyers must conduct extensive due diligence before any transaction. Information is synthesized from public sources and general industry knowledge.
Essential Technical Properties and Trade Terminology for cnc milling machine projects
In the realm of CNC milling machine projects, understanding the essential technical properties and industry terminology is crucial for international B2B buyers. This knowledge not only facilitates better communication with suppliers but also enhances decision-making processes, leading to successful project outcomes.
Key Technical Properties
-
Material Grade
– Definition: Material grade refers to the specific classification of materials based on their mechanical and chemical properties. Common grades include aluminum alloys, stainless steel, and engineering plastics.
– B2B Importance: Selecting the right material grade is vital for ensuring the end product meets the required strength, durability, and performance specifications. It impacts production costs and the overall lifecycle of the product. -
Tolerance
– Definition: Tolerance indicates the permissible limit of variation in a physical dimension, which can be expressed in millimeters or inches. Common tolerances include tight (±0.01 mm) and loose (±0.5 mm).
– B2B Importance: Accurate tolerances are critical for parts that must fit together precisely in assemblies. Understanding tolerance requirements helps buyers avoid costly rework or rejects, ensuring quality and reliability in production. -
Surface Finish
– Definition: Surface finish describes the texture of a machined surface, which can range from rough to smooth. Common finishes include Ra (roughness average) measurements.
– B2B Importance: The required surface finish can affect the part’s functionality, aesthetic appeal, and adherence to industry standards. Buyers should specify surface finish requirements to align with end-use applications. -
Machining Time
– Definition: Machining time is the duration required to produce a part from raw material to finished product, influenced by factors like material type, complexity, and machine capabilities.
– B2B Importance: Understanding machining time helps buyers manage lead times and production schedules, which is especially important for just-in-time manufacturing environments. -
Tooling Specifications
– Definition: Tooling specifications refer to the types and sizes of cutting tools required for the milling process, which can include end mills, drill bits, and inserts.
– B2B Importance: Proper tooling is essential for achieving desired precision and efficiency in machining. Buyers should collaborate with suppliers to ensure that the right tools are available for their specific milling projects.
Common Trade Terms
-
OEM (Original Equipment Manufacturer)
– Definition: An OEM is a company that produces parts or equipment that may be marketed by another manufacturer.
– Importance: Understanding OEM relationships is crucial for buyers looking to source components that meet specific quality and performance standards. -
MOQ (Minimum Order Quantity)
– Definition: MOQ is the smallest quantity of a product that a supplier is willing to sell.
– Importance: Knowing the MOQ helps buyers plan their purchasing strategies and manage inventory effectively, especially in regions with varying demand levels. -
RFQ (Request for Quotation)
– Definition: An RFQ is a document that buyers send to suppliers to request pricing and other details for specific products or services.
– Importance: Utilizing RFQs streamlines the procurement process, enabling buyers to compare offers and negotiate better terms. -
Incoterms (International Commercial Terms)
– Definition: Incoterms are a series of pre-defined commercial terms published by the International Chamber of Commerce (ICC) that clarify the responsibilities of buyers and sellers in international transactions.
– Importance: Familiarity with Incoterms helps buyers understand shipping responsibilities, costs, and risk management, which is essential for cross-border transactions. -
Lead Time
– Definition: Lead time is the total time from when an order is placed until it is fulfilled.
– Importance: Knowing the lead time for CNC milling projects aids in effective supply chain management and helps buyers align production schedules with market demands.
By mastering these technical properties and trade terms, international B2B buyers can enhance their sourcing strategies, ensuring that they select the right suppliers and materials for their CNC milling machine projects.
Navigating Market Dynamics, Sourcing Trends, and Sustainability in the cnc milling machine projects Sector
Market Overview & Key Trends
The CNC milling machine projects sector is experiencing a transformative phase driven by several global factors. Increasing demand for precision engineering and the need for rapid prototyping across industries like aerospace, automotive, and healthcare are propelling market growth. International B2B buyers, particularly in emerging markets such as Africa and South America, must stay attuned to key trends including automation, Industry 4.0 integration, and the rise of additive manufacturing techniques. These trends not only enhance production efficiency but also allow for greater customization of components, which is essential for gaining a competitive edge.
Moreover, the growing emphasis on digital transformation and data analytics is reshaping sourcing strategies. Buyers are now leveraging advanced technologies such as IoT and AI to optimize their supply chains, reduce lead times, and enhance decision-making processes. Understanding local market dynamics is crucial; for instance, in regions like the Middle East, favorable government policies are encouraging investments in advanced manufacturing technologies. As a result, international buyers can benefit from both improved access to high-quality suppliers and reduced operational costs.
Additionally, the current geopolitical climate and economic fluctuations are impacting supply chains, necessitating a more agile sourcing approach. Buyers should focus on diversifying their supplier base to mitigate risks associated with over-reliance on single sources. Engaging with suppliers who demonstrate flexibility and adaptability can lead to better negotiation power and improved supply chain resilience.
Sustainability & Ethical Sourcing in B2B
Sustainability is becoming a cornerstone in the sourcing of CNC milling projects, driven by both regulatory pressures and increasing consumer demand for responsible manufacturing practices. The environmental impact of CNC milling processes, including energy consumption and waste generation, necessitates a focus on sustainability. B2B buyers should prioritize suppliers who adopt energy-efficient technologies and practices, such as using renewable energy sources and minimizing waste through recycling initiatives.
Moreover, the importance of ethical sourcing cannot be overstated. Buyers are encouraged to establish supply chains that adhere to fair labor practices and responsible sourcing of materials. Certifications such as ISO 14001 (Environmental Management) and ISO 45001 (Occupational Health and Safety) are key indicators of a supplier’s commitment to sustainability and ethical practices. Additionally, sourcing from suppliers who utilize ‘green’ materials—such as biodegradable plastics or recycled metals—can significantly reduce the environmental footprint of milling projects.
Investing in sustainable practices not only enhances brand reputation but also opens up new market opportunities. Companies that prioritize sustainability are better positioned to comply with regulations and meet the expectations of eco-conscious customers. Therefore, international B2B buyers should integrate sustainability metrics into their supplier evaluation processes to foster long-term partnerships that align with global sustainability goals.
Brief Evolution/History
The evolution of CNC milling technology has been marked by significant advancements since its inception in the mid-20th century. Initially, milling machines were manually operated, but the introduction of computer numerical control (CNC) revolutionized the industry. This transition allowed for greater precision, repeatability, and efficiency in the manufacturing process. Over the decades, innovations in software and hardware have further enhanced the capabilities of CNC milling, leading to the development of multi-axis machines that can produce complex geometries.
As globalization intensified, the CNC milling sector saw a surge in international collaborations and outsourcing, enabling companies to leverage cost-effective production in emerging markets. Today, the integration of smart technologies, such as IoT and AI, is driving the next wave of innovation in CNC milling, making it crucial for B2B buyers to stay informed about technological advancements and market shifts to maintain a competitive edge.
Related Video: The Inside Story of the Ship That Broke Global Trade
Frequently Asked Questions (FAQs) for B2B Buyers of cnc milling machine projects
-
How do I effectively vet suppliers for CNC milling machine projects?
When vetting suppliers, prioritize those with a proven track record in your industry. Request references and case studies that demonstrate their capability to handle projects similar to yours. Investigate their certifications, such as ISO 9001, which indicates adherence to quality management standards. Conduct site visits, if possible, to assess their facilities and processes. Additionally, evaluate their responsiveness and communication style, as these factors can significantly impact collaboration throughout the project. -
Can CNC milling projects be customized to fit specific requirements?
Yes, CNC milling projects are highly customizable to meet specific needs. Most suppliers offer tailored services, allowing you to specify dimensions, tolerances, and materials. It’s essential to provide detailed specifications and design files to ensure the manufacturer understands your requirements. Early discussions about customization can help clarify capabilities and lead times, ensuring that the final product aligns with your expectations. -
What are the typical minimum order quantities (MOQs) and lead times for CNC milling projects?
Minimum order quantities (MOQs) can vary significantly based on the supplier and project complexity. While some may accept small batch sizes, others might require larger orders to justify setup costs. Lead times typically range from a few weeks to several months, depending on the project’s complexity and the supplier’s current workload. Always discuss these factors upfront to align expectations and avoid potential delays. -
What payment terms should I expect when sourcing CNC milling services internationally?
Payment terms can differ among suppliers, but common practices include upfront deposits (often 30-50%) followed by the balance upon completion or delivery. Be prepared to negotiate terms that suit both parties, considering factors like order size and relationship duration. Using secure payment methods such as letters of credit can help mitigate risks associated with international transactions. Always confirm payment details in your contract to avoid misunderstandings later. -
How can I ensure quality assurance (QA) and certifications from my CNC milling supplier?
To ensure quality, ask potential suppliers for their QA processes and certifications. Look for ISO certifications or industry-specific standards that reflect their commitment to quality control. Request regular quality reports and consider implementing periodic audits or inspections during production. Establishing clear quality expectations in your contract, including acceptable tolerances and testing methods, will further safeguard your interests. -
What logistics considerations should I keep in mind when sourcing CNC milling projects?
Logistics play a crucial role in international sourcing. Assess the supplier’s capability to manage shipping and customs, as these can impact lead times and costs. Discuss packaging requirements to ensure products arrive undamaged. Consider the total landed cost, which includes shipping, tariffs, and taxes, to make informed budgeting decisions. Collaborating with a logistics partner can streamline the process and reduce potential delays. -
How should I handle disputes with a CNC milling supplier?
Disputes can arise due to quality issues, delivery delays, or miscommunications. To minimize conflict, ensure that your contract includes clear terms regarding responsibilities, quality standards, and dispute resolution processes. If a dispute occurs, address it promptly with open communication, aiming for an amicable resolution. If necessary, involve a third-party mediator or refer to contractual clauses outlining arbitration processes to resolve the issue without damaging the relationship. -
What are the key considerations for selecting materials in CNC milling projects?
Material selection is critical and should align with your project’s functional requirements and cost constraints. Consider factors such as strength, weight, corrosion resistance, and machinability of the materials. Discuss available options with your supplier, as they can provide insights into the best materials for your specific applications. Additionally, ensure that the chosen materials comply with any relevant industry standards, especially if your products will be used in highly regulated sectors.
Important Disclaimer & Terms of Use
⚠️ Important Disclaimer
The information provided in this guide, including content regarding manufacturers, technical specifications, and market analysis, is for informational and educational purposes only. It does not constitute professional procurement advice, financial advice, or legal advice.
While we have made every effort to ensure the accuracy and timeliness of the information, we are not responsible for any errors, omissions, or outdated information. Market conditions, company details, and technical standards are subject to change.
B2B buyers must conduct their own independent and thorough due diligence before making any purchasing decisions. This includes contacting suppliers directly, verifying certifications, requesting samples, and seeking professional consultation. The risk of relying on any information in this guide is borne solely by the reader.
Strategic Sourcing Conclusion and Outlook for cnc milling machine projects
The journey through the world of CNC milling has underscored the critical importance of strategic sourcing for B2B buyers, particularly in emerging markets across Africa, South America, the Middle East, and Europe. Key takeaways include the necessity of understanding different CNC milling types, assessing supplier capabilities, and aligning procurement strategies with business objectives. Emphasizing quality control standards and leveraging global supplier networks can significantly enhance operational efficiency and reduce costs.
As the manufacturing landscape continues to evolve, staying ahead requires a proactive approach to sourcing. Engaging with suppliers who demonstrate innovation and adaptability can provide a competitive edge, enabling organizations to respond to market demands swiftly.
International buyers are encouraged to invest time in building strong partnerships and exploring diverse sourcing options. By fostering collaborative relationships with reliable manufacturers, businesses can unlock new opportunities for growth and innovation. The future of CNC milling projects is promising—embrace it by taking strategic sourcing to the next level. Your next successful project may just be a well-negotiated contract away.