Your Ultimate Guide to Sourcing Cnc Pipe Bending Machine
Introduction: Navigating the Global Market for cnc pipe bending machine
In today’s competitive manufacturing landscape, CNC pipe bending machines are indispensable tools that drive efficiency and precision in metal forming processes. For international B2B buyers in regions such as Africa, South America, the Middle East, and Europe, understanding the nuances of these machines can significantly enhance operational capabilities. Industries ranging from automotive and construction to energy and aerospace rely on the ability to bend pipes and tubes with accuracy, directly impacting project timelines, cost management, and product quality.
This comprehensive guide serves as a vital resource for navigating the diverse global market of CNC pipe bending machines. It delves into the various types of machines available—each tailored to specific applications and material requirements—ensuring buyers can select the right technology for their needs. The guide further explores critical aspects such as manufacturing best practices, quality control measures, and strategic sourcing tips for identifying reputable suppliers.
Moreover, it provides insights into real-world cost factors, risk mitigation strategies, and return on investment considerations, enabling informed decision-making. With actionable market intelligence and a focus on regional specifics, this guide empowers buyers to make strategic investments that unlock efficiency, expand market reach, and future-proof their manufacturing operations. By leveraging the information within, you can confidently approach your procurement strategy for CNC pipe bending systems, ensuring you remain competitive in an ever-evolving global marketplace.
Understanding cnc pipe bending machine Types and Variations
Type Name | Key Distinguishing Features | Primary B2B Applications | Brief Pros & Cons for Buyers |
---|---|---|---|
CNC Electric Pipe Bender | Precision electromechanical actuation, quiet operation | Automotive, aerospace, lightweight fabrication | High accuracy, low energy use; limited for thick wall |
CNC Hydraulic Pipe Bender | Hydraulic-powered movement, strong force for heavy-walled pipes | Construction, oil & gas, power infrastructure | Bends thick pipes, powerful; higher maintenance |
CNC Induction Pipe Bender | Utilizes precise induction heating for bend forming | Large-diameter pipelines, structural beams | Preserves material integrity, large diameters; cost |
CNC Mandrel Bender | Features internal mandrel for tight-radius bends | Shipbuilding, HVAC, furniture manufacturing | Tight, precise bends; higher setup cost |
CNC Multi-Stack Bender | Multiple tooling stacks for rapid size/shape changes | Plumbing, production lines, process industry | Boosts productivity, versatile; skilled setup needed |
CNC Electric Pipe Bender
CNC Electric Pipe Benders are characterized by their precision electromechanical actuation, which allows for highly accurate and repeatable bends. These machines are particularly suited for applications in the automotive and aerospace industries, where lightweight materials are commonly used. Buyers should consider the lower energy consumption and maintenance costs, although the limitations in bending thicker materials may restrict their use in heavy industries.
CNC Hydraulic Pipe Bender
Hydraulic Pipe Benders are known for their robust power and capability to handle heavy-walled pipes, making them essential in sectors like construction and oil & gas. The hydraulic system provides significant force, allowing for precise bends in larger diameters. However, prospective buyers must weigh the benefits of high performance against the need for more complex maintenance and the availability of skilled technicians, especially in regions with limited technical resources.
CNC Induction Pipe Bender
This type of bender employs induction heating technology, allowing for large-radius and large-diameter bends with minimal material distortion. It is ideal for infrastructure projects, such as pipelines and structural steel applications, where maintaining the integrity of the material is crucial. While the initial investment is typically higher, the long-term benefits of producing complex, distortion-free bends make it a valuable option for buyers focused on quality and efficiency.
CNC Mandrel Bender
CNC Mandrel Benders are designed to create tight-radius bends without compromising the internal structure of the pipe. This technology is particularly beneficial in industries such as shipbuilding and HVAC, where precision and surface finish are paramount. Buyers should consider the higher upfront costs and tooling flexibility, as well as the necessary training for operators to maximize the machine’s capabilities.
CNC Multi-Stack Bender
CNC Multi-Stack Benders are equipped with multiple tooling stacks that allow for rapid changes in size and shape, making them ideal for high-volume production environments like plumbing and process industries. The ability to quickly adapt to different specifications boosts productivity significantly. However, buyers must ensure they have the skilled personnel required for setup and operation, as the complexity of the machine can pose challenges in less experienced hands.
Related Video: High-performance hydraulic CNC pipe bending machine.tube bending machine – 6-axis all-rounder
Key Industrial Applications of cnc pipe bending machine
Industry/Sector | Specific Application of CNC Pipe Bending Machine | Value/Benefit for the Business | Key Sourcing Considerations for this Application |
---|---|---|---|
Automotive | Manufacturing exhaust systems and chassis components | High precision and repeatability in complex shapes | Supplier’s experience with automotive standards and certifications |
Construction | Fabricating structural steel for buildings | Enhanced structural integrity and reduced material waste | Availability of technical support and local spare parts |
Oil & Gas | Bending pipes for pipelines and drilling equipment | Increased efficiency in transport and installation | Assessment of machine durability in harsh environments |
HVAC | Creating ductwork and piping systems | Improved energy efficiency and air quality management | Compliance with regional regulations and energy standards |
Furniture Manufacturing | Producing intricate metal furniture designs | Ability to create unique designs and reduce lead time | Flexibility of machine for different materials and designs |
In the automotive industry, CNC pipe bending machines are essential for manufacturing exhaust systems and chassis components. These applications require high precision to ensure parts fit correctly and perform optimally. International buyers must consider suppliers who comply with automotive industry standards and can provide documentation of certifications, as quality assurance is critical in this sector.
In construction, CNC pipe bending machines are used to fabricate structural steel components for buildings. This process not only enhances the structural integrity of the projects but also minimizes material waste, which is particularly beneficial in cost-sensitive markets. Buyers should evaluate suppliers based on their ability to provide technical support and the availability of spare parts locally, ensuring minimal downtime during production.
The oil and gas sector relies heavily on CNC pipe bending machines for creating pipelines and drilling equipment. The efficiency of these machines in producing high-quality bends translates to reduced transport and installation times. For international buyers, understanding the durability of the machines in harsh environments is crucial, as well as the supplier’s capacity to provide ongoing maintenance and support.
In the HVAC industry, CNC pipe bending machines facilitate the production of ductwork and piping systems, which are vital for effective heating, ventilation, and air conditioning solutions. By improving energy efficiency and air quality management, these machines play a key role in modern building designs. Buyers should ensure that suppliers adhere to regional regulations and energy efficiency standards, which can vary significantly across different markets.
Lastly, in furniture manufacturing, CNC pipe bending machines enable the creation of intricate metal designs that enhance aesthetic appeal. The ability to produce unique pieces quickly can significantly reduce lead times and cater to custom orders. Buyers should focus on sourcing machines that offer flexibility in terms of material types and design capabilities, ensuring they can adapt to market trends and customer preferences.
Related Video: CNC Pipe Bending Machine – CH42CN1 / CLR80 | AMOB
Strategic Material Selection Guide for cnc pipe bending machine
When selecting materials for CNC pipe bending machines, it is essential to consider various factors that influence performance, cost, and application suitability. Below is a detailed analysis of four common materials used in CNC pipe bending, focusing on their properties, advantages, disadvantages, and implications for international B2B buyers, particularly from regions such as Africa, South America, the Middle East, and Europe.
Carbon Steel
Key Properties: Carbon steel is known for its high tensile strength and good machinability. It typically has a temperature rating of up to 400°C and can withstand moderate pressure, making it suitable for various applications.
Pros & Cons: Carbon steel is durable and relatively low-cost compared to other materials, which makes it a popular choice for many industries. However, it is prone to corrosion if not properly treated, which can limit its lifespan in harsh environments.
Impact on Application: Carbon steel is compatible with a wide range of media, including water, oil, and gas, making it suitable for construction and infrastructure projects. However, its susceptibility to rust necessitates protective coatings or galvanization, especially in humid climates.
Considerations for Buyers: Buyers should ensure compliance with relevant standards such as ASTM A53 or DIN 2440. In regions like Africa and South America, where corrosion can be a significant issue, selecting a corrosion-resistant treatment is advisable.
Stainless Steel
Key Properties: Stainless steel is highly resistant to corrosion and oxidation, with temperature ratings exceeding 800°C. Its chemical composition provides excellent durability against various media.
Pros & Cons: The primary advantage of stainless steel is its long lifespan and low maintenance requirements. However, it comes at a higher cost compared to carbon steel and may present challenges in machining due to its hardness.
Impact on Application: Stainless steel is ideal for applications involving food processing, pharmaceuticals, and chemical transport due to its non-reactive nature. It is also suitable for high-pressure applications.
Considerations for Buyers: Buyers must consider compliance with standards such as ASTM A312 or JIS G3463. In Europe, the preference for stainless steel in food-related applications is particularly strong, necessitating adherence to stringent hygiene standards.
Aluminum
Key Properties: Aluminum is lightweight yet strong, with excellent corrosion resistance. It has a lower temperature rating than steel, typically around 300°C, and is not suitable for high-pressure applications.
Pros & Cons: The lightweight nature of aluminum allows for easier handling and transport, making it cost-effective for projects requiring mobility. However, its lower strength compared to steel may limit its use in heavy-duty applications.
Impact on Application: Aluminum is commonly used in automotive and aerospace applications where weight reduction is critical. Its compatibility with various media is good, but it may not be suitable for high-pressure systems.
Considerations for Buyers: Buyers should be aware of the need for compliance with standards such as ASTM B221 or EN AW-6060. In regions like the Middle East, where lightweight structures are favored, aluminum can be a preferred choice.
Copper
Key Properties: Copper has excellent thermal and electrical conductivity, with a temperature rating of up to 200°C. It is also resistant to corrosion, particularly in non-oxidizing environments.
Pros & Cons: The primary advantage of copper is its conductivity, making it ideal for electrical applications. However, it is more expensive than steel and can be challenging to bend without specialized equipment.
Impact on Application: Copper is widely used in plumbing and electrical applications due to its excellent conductivity and resistance to corrosion in water systems. However, its cost can be a limiting factor in large-scale projects.
Considerations for Buyers: Buyers should ensure compliance with standards such as ASTM B280 or EN 1057. In Europe, where plumbing systems often utilize copper, understanding local regulations regarding material use is crucial.
Material | Typical Use Case for cnc pipe bending machine | Key Advantage | Key Disadvantage/Limitation | Relative Cost (Low/Med/High) |
---|---|---|---|---|
Carbon Steel | Construction, infrastructure | Durable and cost-effective | Prone to corrosion | Low |
Stainless Steel | Food processing, pharmaceuticals | Corrosion resistant and durable | Higher cost and machining issues | High |
Aluminum | Automotive, aerospace | Lightweight and easy to handle | Lower strength | Medium |
Copper | Plumbing, electrical applications | Excellent conductivity | Expensive and bending challenges | High |
This strategic material selection guide aims to empower international B2B buyers by providing critical insights into the properties and implications of various materials used in CNC pipe bending applications. Understanding these factors will facilitate informed purchasing decisions and enhance operational efficiency across diverse markets.
In-depth Look: Manufacturing Processes and Quality Assurance for cnc pipe bending machine
Manufacturing Processes for CNC Pipe Bending Machines
Understanding the manufacturing processes behind CNC pipe bending machines is essential for B2B buyers, particularly in diverse markets across Africa, South America, the Middle East, and Europe. The production of these machines involves several key stages, each contributing to the overall quality, efficiency, and precision of the final product.
Main Stages of Manufacturing
-
Material Preparation
– Selection of Raw Materials: The manufacturing process begins with selecting high-quality raw materials, typically including various grades of steel (carbon, stainless, alloy) based on the machine’s intended applications.
– Cutting and Shaping: Raw materials are cut into specified dimensions using precision cutting tools. This stage often employs advanced techniques such as laser cutting or plasma cutting to ensure accuracy. -
Forming
– Bending Process: The core function of a CNC pipe bending machine is to bend pipes with high precision. This is achieved through various techniques, including rotary draw bending, induction bending, and mandrel bending. Each method is selected based on the material type and the desired bend radius.
– Machining: Additional machining processes, such as drilling or milling, may be performed to create specific features or improve surface finishes on the pipe components. -
Assembly
– Component Integration: After forming, various machine components (like motors, hydraulics, and electronics) are assembled. This stage requires skilled technicians to ensure that all parts fit and function together seamlessly.
– Electrical Wiring and Control Systems: The assembly of electrical components is crucial for the operation of CNC machines. This includes integrating control panels and programming the CNC software. -
Finishing
– Surface Treatment: To enhance durability and resistance to corrosion, the machine undergoes surface treatments such as powder coating, galvanizing, or painting.
– Final Assembly and Calibration: The final assembly stage includes calibrating the machine to ensure it meets specified tolerances. This step is critical for achieving the high precision required in CNC operations.
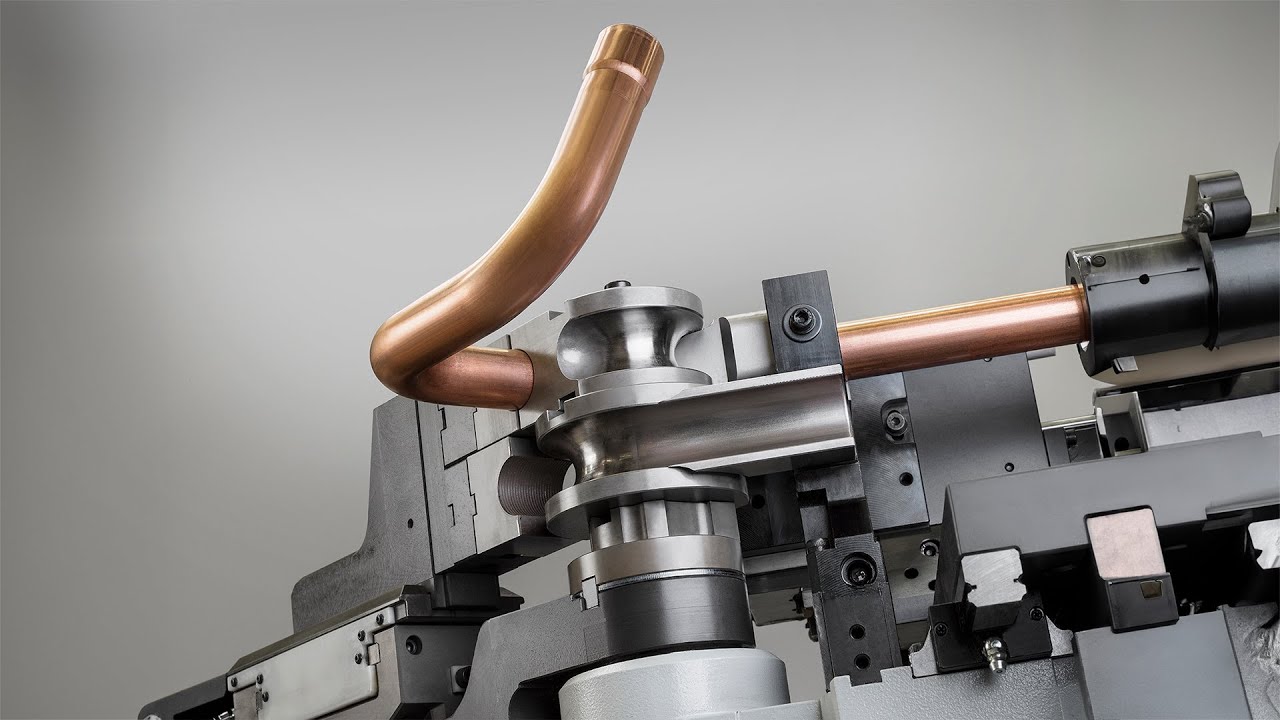
Illustrative Image (Source: Google Search)
Quality Assurance in CNC Pipe Bending Machine Manufacturing
Quality assurance (QA) is a vital aspect of manufacturing CNC pipe bending machines, as it ensures that products meet international standards and customer expectations. Effective QA processes help mitigate risks and enhance the reliability of machines.
Relevant International Standards
- ISO 9001: This widely recognized standard sets out the criteria for a quality management system. Compliance with ISO 9001 ensures that manufacturers maintain consistent quality in their products and services.
- CE Certification: For machines sold in Europe, CE marking indicates conformity with health, safety, and environmental protection standards.
- API Certification: For applications in the oil and gas industry, API (American Petroleum Institute) certification is crucial for ensuring that equipment meets industry-specific standards.
Key QC Checkpoints
-
Incoming Quality Control (IQC)
– Material Inspection: Raw materials are inspected upon arrival to verify compliance with specifications. This includes checks for material grade, dimensions, and surface conditions. -
In-Process Quality Control (IPQC)
– Monitoring During Manufacturing: Regular inspections during the manufacturing process help identify defects early. Techniques such as dimensional checks, visual inspections, and operational testing are common. -
Final Quality Control (FQC)
– End-of-Line Testing: Before shipping, machines undergo rigorous testing to ensure they operate correctly. This includes functional tests, safety checks, and performance assessments against predefined metrics.
Common Testing Methods
- Dimensional Inspection: Using precision measurement tools to ensure that all components meet specified tolerances.
- Functional Testing: Verifying that the machine operates as intended under various conditions.
- Performance Testing: Assessing the machine’s ability to handle specified loads and speeds.
Verifying Supplier Quality Control
For B2B buyers, especially those in emerging markets, verifying a supplier’s quality control processes is crucial. Here are actionable steps to ensure supplier compliance:
- Supplier Audits: Conducting on-site audits allows buyers to assess manufacturing processes, quality control measures, and overall operational standards.
- Requesting Quality Reports: Buyers should ask suppliers for detailed quality reports that document the results of IQC, IPQC, and FQC.
- Third-Party Inspections: Engaging third-party inspection services can provide an unbiased assessment of a supplier’s quality control measures and product reliability.
Quality Control and Certification Nuances for International Buyers
International buyers face unique challenges when sourcing CNC pipe bending machines. Here are some nuances to consider:
- Understanding Local Regulations: Each region may have specific regulations that impact machine certification. For example, while CE marking is essential for European markets, other regions may have different standards.
- Cultural and Communication Barriers: Buyers should be aware of potential language and cultural differences that may affect negotiations and quality assurance discussions.
- Logistics and After-Sales Support: Assessing a supplier’s logistics capabilities and after-sales support is essential, especially in remote areas where access to spare parts and service may be limited.
By understanding the manufacturing processes and quality assurance measures in the production of CNC pipe bending machines, international B2B buyers can make informed decisions, ensuring they invest in reliable, high-quality equipment that meets their operational needs.
Related Video: CNC PLC conroller pipe bending machine programme and operation
Comprehensive Cost and Pricing Analysis for cnc pipe bending machine Sourcing
In the intricate landscape of CNC pipe bending machine sourcing, understanding the comprehensive cost structure and pricing dynamics is essential for international B2B buyers. This analysis focuses on the key cost components, price influencers, and actionable tips for navigating procurement effectively.
Cost Components
-
Materials: The primary material used in CNC pipe bending machines significantly impacts costs. Common materials include carbon steel, stainless steel, and various alloys. Prices fluctuate based on market conditions and availability, influencing the overall machine cost.
-
Labor: Labor costs encompass both direct and indirect expenses. Skilled labor is crucial for manufacturing, assembly, and maintenance. In regions with higher wage standards, such as Europe, labor may represent a more substantial portion of the overall cost compared to areas with lower labor costs, like parts of Africa and South America.
-
Manufacturing Overhead: This includes facility costs, utilities, and administrative expenses associated with production. Efficient operations can help minimize overhead, but buyers should ensure that suppliers maintain quality standards despite cost-cutting measures.
-
Tooling: Tooling costs vary based on the complexity and customization of the bending machine. Specialized tooling for specific applications can drive prices higher, but investing in quality tooling can lead to better performance and longevity.
-
Quality Control (QC): Implementing rigorous QC processes ensures that machines meet industry standards and specifications. While this adds to the upfront costs, it mitigates risks related to machine failure and operational inefficiencies.
-
Logistics: Shipping costs can be significant, especially for international buyers. Factors such as distance, shipping mode, and tariffs must be considered. Incoterms (International Commercial Terms) can influence logistics costs and responsibilities.
-
Margin: Supplier profit margins vary widely based on market positioning, brand reputation, and service offerings. Understanding these margins can help buyers negotiate better pricing.
Price Influencers
-
Volume/MOQ (Minimum Order Quantity): Larger orders typically yield lower per-unit costs. Buyers should negotiate volume discounts when feasible.
-
Specifications/Customization: Custom features or specialized machines usually come at a premium. Buyers must assess whether the added functionality justifies the cost.
-
Materials: The choice of materials directly influences pricing. Premium materials may offer better durability and performance but at a higher price point.
-
Quality/Certifications: Machines that meet international quality standards and possess certifications may carry higher costs. However, such investments often result in lower maintenance and operational costs over time.
-
Supplier Factors: Established suppliers with a reputation for quality may charge more, but they often provide better support and reliability. Newer or less-known suppliers might offer lower prices but could come with higher risks.
-
Incoterms: Understanding the implications of different Incoterms can help buyers calculate total landed costs, including shipping, duties, and insurance.
Buyer Tips
-
Negotiation: Leverage your purchasing power by negotiating terms and prices. Be prepared to discuss volume and long-term partnerships for better deals.
-
Cost-Efficiency: Analyze the Total Cost of Ownership (TCO), not just the initial purchase price. Consider maintenance, operational costs, and potential downtime when evaluating machine options.
-
Pricing Nuances: Be aware of regional pricing differences. For instance, prices may be higher in Europe due to stricter regulations and labor costs compared to emerging markets.
-
Market Research: Conduct thorough market research to identify competitive pricing and reputable suppliers. Utilize industry networks and trade shows to gather insights and make informed decisions.
Disclaimer
Prices can fluctuate based on market dynamics, supplier negotiations, and regional economic conditions. Always seek multiple quotes and conduct due diligence before making procurement decisions to ensure the best value for your investment.
Spotlight on Potential cnc pipe bending machine Manufacturers and Suppliers
This section looks at several manufacturers active in the ‘cnc pipe bending machine’ market. This is a representative sample for illustrative purposes; B2B buyers must conduct extensive due diligence before any transaction. Information is synthesized from public sources and general industry knowledge.
Essential Technical Properties and Trade Terminology for cnc pipe bending machine
CNC pipe bending machines are complex tools that play a vital role in various industries, from construction to automotive manufacturing. Understanding their essential technical properties and familiarizing oneself with trade terminology is critical for international B2B buyers, especially those in Africa, South America, the Middle East, and Europe. This section outlines the key specifications and jargon that will aid decision-making and procurement processes.
Key Technical Properties
-
Material Grade
– Definition: This refers to the type of material that can be processed by the CNC pipe bending machine, such as carbon steel, stainless steel, or aluminum.
– B2B Importance: Selecting the right material grade is crucial for ensuring the durability and performance of the final product. Buyers must consider the specific requirements of their projects, as different materials offer varying levels of strength, corrosion resistance, and cost. -
Bend Radius
– Definition: The minimum radius that a pipe can be bent without compromising its integrity.
– B2B Importance: A smaller bend radius allows for more complex designs in confined spaces, which is often necessary in industries like HVAC and automotive. Understanding the bend radius capabilities of a machine helps buyers ensure it meets their design specifications. -
Tolerance
– Definition: The allowable deviation from a specified dimension, typically expressed in millimeters or inches.
– B2B Importance: High precision is essential for applications where parts must fit together accurately. Buyers should seek machines that can achieve tight tolerances to minimize waste and rework, thereby enhancing efficiency and reducing costs. -
Capacity
– Definition: This refers to the maximum wall thickness and diameter of the pipes that the machine can handle.
– B2B Importance: Understanding the capacity of a CNC pipe bending machine ensures that it can accommodate the specific needs of projects, particularly in sectors such as oil and gas, where large-diameter pipes are common. Overestimating capacity can lead to equipment failure and increased operational costs. -
Control System
– Definition: The technology used to operate the machine, including software for programming bends and monitoring processes.
– B2B Importance: Advanced control systems enhance accuracy and repeatability. Buyers should evaluate the user-friendliness and compatibility of the control system with their existing processes to facilitate smoother operations.
Common Trade Terminology
-
OEM (Original Equipment Manufacturer)
– Definition: A company that produces parts and equipment that may be marketed by another manufacturer.
– Importance: Understanding OEM relationships helps buyers identify reliable suppliers and ensures that they are purchasing high-quality components. -
MOQ (Minimum Order Quantity)
– Definition: The smallest quantity of a product that a supplier is willing to sell.
– Importance: Knowing the MOQ is essential for budget planning and inventory management. Buyers should negotiate MOQs to align with their production needs without overcommitting resources. -
RFQ (Request for Quotation)
– Definition: A document sent by a buyer to suppliers requesting pricing and other details for specific products or services.
– Importance: An RFQ allows buyers to gather competitive pricing and evaluate options. This process is crucial for informed decision-making and cost-effective procurement. -
Incoterms (International Commercial Terms)
– Definition: A set of predefined international rules that clarify the responsibilities of buyers and sellers in international transactions.
– Importance: Familiarity with Incoterms helps buyers understand shipping costs, risks, and responsibilities, aiding in smoother negotiations and transactions. -
Lead Time
– Definition: The amount of time it takes from placing an order until it is fulfilled.
– Importance: Understanding lead times is critical for project planning and inventory management. Buyers should factor in lead times when coordinating with suppliers to ensure timely delivery of machinery and materials.
By grasping these technical properties and trade terms, international B2B buyers can make more informed choices, ensuring that their investments in CNC pipe bending machines yield optimal returns and meet the demands of their respective markets.
Navigating Market Dynamics, Sourcing Trends, and Sustainability in the cnc pipe bending machine Sector
In the rapidly evolving landscape of CNC pipe bending machines, several key market dynamics are shaping the procurement strategies of international B2B buyers, particularly in regions like Africa, South America, the Middle East, and Europe.
Market Overview & Key Trends
The global CNC pipe bending machine market is driven by the increasing demand for precision and efficiency across various industries, including automotive, construction, and energy. Notably, the shift towards automation and Industry 4.0 is pushing manufacturers to adopt advanced technologies, such as IoT-enabled machines, which enhance operational efficiency and data analytics capabilities. Additionally, the growing emphasis on reducing lead times and optimizing production processes is leading buyers to explore flexible and customizable machine solutions.
Emerging sourcing trends highlight a preference for local suppliers, especially in regions like Africa and South America, where businesses seek to minimize shipping costs and lead times. Moreover, the focus on vertical integration is gaining traction, as buyers look to engage directly with manufacturers to ensure quality control and reduce dependency on intermediaries. In Europe, there is an increasing trend towards purchasing machines with enhanced energy efficiency features to comply with stringent environmental regulations.
The market is also witnessing the rise of second-hand and refurbished CNC machines as a cost-effective solution for small to medium enterprises. This trend is particularly prevalent in emerging markets, where budget constraints often dictate procurement decisions. Buyers are advised to carefully evaluate the condition and warranty of used machines to mitigate risks.
Sustainability & Ethical Sourcing in B2B
Sustainability is becoming a critical consideration for B2B buyers in the CNC pipe bending machine sector. The environmental impact of manufacturing processes, particularly in terms of energy consumption and waste generation, is under scrutiny. As a result, many buyers are prioritizing suppliers that demonstrate a commitment to sustainable practices, such as using energy-efficient machines and implementing waste reduction strategies.
Ethical sourcing is equally important, as businesses seek to ensure their supply chains are transparent and socially responsible. This includes verifying that suppliers adhere to fair labor practices and environmental standards. Certifications such as ISO 14001 for environmental management and ISO 9001 for quality management are increasingly sought after by buyers as indicators of a supplier’s commitment to sustainability and ethical practices.
Furthermore, the use of ‘green’ materials, such as recyclable metals and eco-friendly coatings, is gaining popularity. Buyers are encouraged to engage with suppliers who prioritize these materials, not only to enhance their own sustainability credentials but also to meet the evolving demands of environmentally-conscious customers.
Brief Evolution/History
The CNC pipe bending machine has evolved significantly since its inception in the mid-20th century. Initially, pipe bending was a manual and labor-intensive process, often resulting in inconsistencies and inaccuracies. The introduction of CNC technology in the late 1970s revolutionized the industry by enabling precise and repeatable bends, thus enhancing productivity and quality. Over the years, advancements in software and automation have further refined these machines, allowing for complex geometries and integration with other manufacturing processes. This evolution has made CNC pipe bending machines indispensable in modern manufacturing, catering to a diverse range of industries with varying requirements.
As B2B buyers navigate this dynamic landscape, understanding these market trends, sustainability factors, and the historical context of CNC pipe bending technology will empower them to make informed procurement decisions that align with their operational goals and corporate values.
Frequently Asked Questions (FAQs) for B2B Buyers of cnc pipe bending machine
- What criteria should I use to vet suppliers of CNC pipe bending machines?
When vetting suppliers, prioritize their industry experience, reputation, and customer reviews. Request references from past clients to gauge satisfaction levels. Evaluate their production capabilities, including technology and capacity, to ensure they can meet your specific needs. Additionally, check for compliance with international quality standards, such as ISO certifications, which demonstrate reliability and adherence to best practices. Consider visiting their facilities if possible, or utilize virtual tours to better understand their operations.
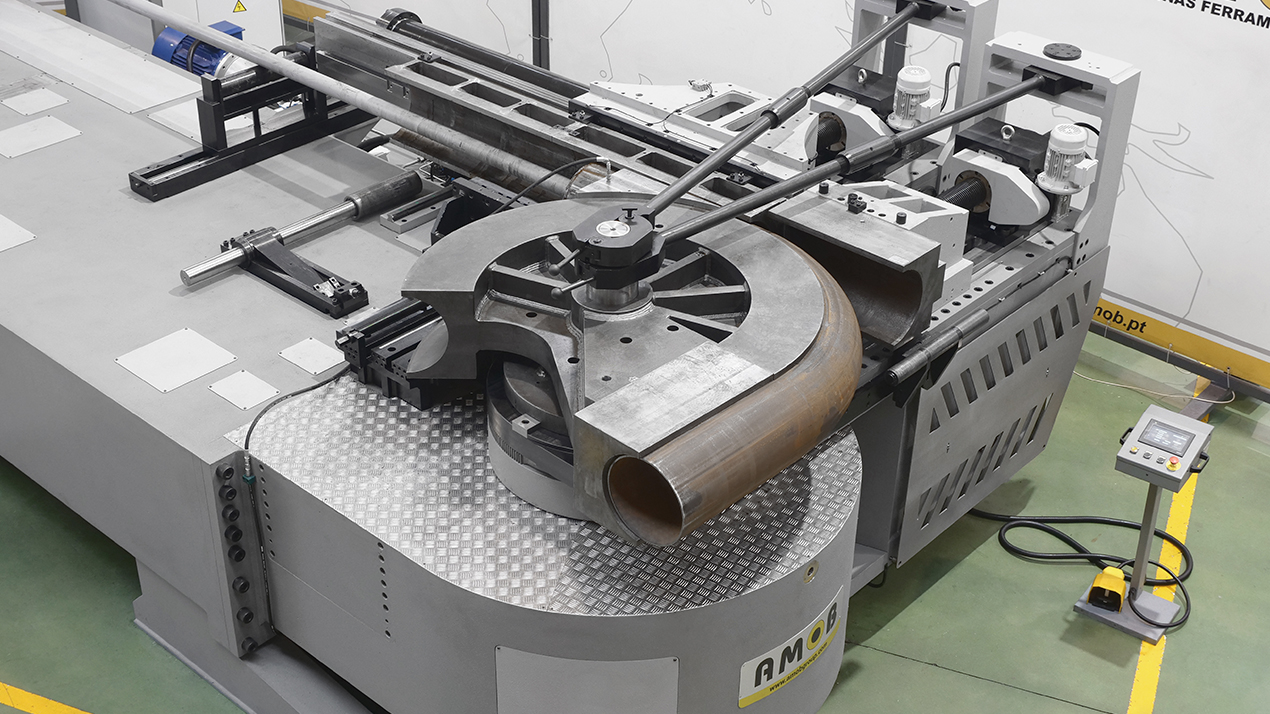
Illustrative Image (Source: Google Search)
-
Can I customize CNC pipe bending machines to suit my specific requirements?
Yes, many suppliers offer customization options for CNC pipe bending machines. This could include specific configurations for different materials, sizes, or bending angles. When discussing customization, clearly outline your operational needs and project specifications. Ensure that the supplier provides detailed documentation on the modifications, as well as guarantees that the machine will perform as expected. Be aware that customization may impact lead times and costs, so factor this into your procurement planning. -
What are the typical minimum order quantities (MOQs) and lead times for CNC pipe bending machines?
MOQs and lead times can vary significantly based on the supplier and the complexity of the machine. Generally, for standard models, MOQs may range from one to several units, while lead times can be anywhere from 4 to 12 weeks depending on customization and production schedules. It’s advisable to discuss these details upfront with suppliers to align expectations. Additionally, inquire about their capacity for rush orders in case of urgent project needs. -
What payment options and terms should I expect when purchasing CNC pipe bending machines?
Most suppliers will offer various payment terms, including upfront deposits and installment payments. Common options include wire transfers, letters of credit, or escrow services, especially for international transactions. It’s crucial to clarify payment terms before finalizing agreements to avoid misunderstandings. Consider negotiating terms that align with your cash flow and project timelines. Always ensure that the payment method chosen provides adequate protection against fraud or non-delivery. -
What quality assurance measures and certifications should I look for?
Look for suppliers that adhere to international quality standards, such as ISO 9001, which ensures consistent quality management processes. Request documentation of their quality control practices, including testing protocols and inspection reports. A reputable supplier should provide certifications for the machines, indicating they meet safety and performance standards. Additionally, inquire about warranty policies and after-sales support to understand their commitment to quality and customer service. -
How can I manage logistics when importing CNC pipe bending machines?
Managing logistics involves coordinating shipping, customs clearance, and transportation to your facility. Work closely with your supplier to understand their shipping methods and timelines. Engage a freight forwarder experienced in handling machinery imports to navigate customs regulations and ensure compliance with local laws. Prepare for potential delays by allowing ample time for shipping and customs clearance, especially if the machine requires specialized handling or documentation. -
What should I do in case of disputes with my CNC pipe bending machine supplier?
In the event of a dispute, first, attempt to resolve the issue directly with the supplier through open communication. Document all correspondence and agreements as evidence. If a resolution cannot be reached, refer to the terms outlined in your purchase contract regarding dispute resolution processes, such as mediation or arbitration. It may also be helpful to consult legal counsel familiar with international trade laws to explore your options for escalation or legal recourse. -
Are there specific regional considerations I should be aware of when sourcing from different continents?
Yes, regional considerations can significantly impact your sourcing strategy. For buyers in Africa and South America, consider potential challenges with infrastructure and logistics, which may affect delivery times. In the Middle East and Europe, regulations may differ, especially regarding compliance and safety standards. Stay informed about trade agreements that may facilitate or hinder import processes. Establishing strong relationships with local representatives can also provide valuable insights into regional market nuances and help navigate potential challenges effectively.
Important Disclaimer & Terms of Use
⚠️ Important Disclaimer
The information provided in this guide, including content regarding manufacturers, technical specifications, and market analysis, is for informational and educational purposes only. It does not constitute professional procurement advice, financial advice, or legal advice.
While we have made every effort to ensure the accuracy and timeliness of the information, we are not responsible for any errors, omissions, or outdated information. Market conditions, company details, and technical standards are subject to change.
B2B buyers must conduct their own independent and thorough due diligence before making any purchasing decisions. This includes contacting suppliers directly, verifying certifications, requesting samples, and seeking professional consultation. The risk of relying on any information in this guide is borne solely by the reader.
Strategic Sourcing Conclusion and Outlook for cnc pipe bending machine
In conclusion, the strategic sourcing of CNC pipe bending machines presents a transformative opportunity for international B2B buyers. By understanding the diverse machine types—ranging from electric to hydraulic and mandrel benders—buyers can align their investments with specific project requirements, ensuring optimal performance and cost-effectiveness.
Key takeaways include the importance of assessing machine capabilities, operational costs, and maintenance needs, particularly in regions with unique challenges such as Africa, South America, the Middle East, and Europe. Engaging with reputable suppliers and leveraging market intelligence can significantly mitigate risks associated with procurement and enhance overall operational efficiency.
As global demand for precision and efficiency in manufacturing continues to rise, now is the time to invest in cutting-edge CNC pipe bending technology. Actively explore partnerships with suppliers who understand your regional context and can offer tailored solutions to meet your business needs. By prioritizing strategic sourcing, you will not only improve your production capabilities but also position your company for long-term success in an increasingly competitive landscape.