Your Ultimate Guide to Sourcing Cnc Screw Machine
Introduction: Navigating the Global Market for cnc screw machine
Navigating the complexities of the global market for CNC screw machines is crucial for international B2B buyers seeking to enhance their manufacturing capabilities. CNC screw machines are pivotal in producing high-precision components used across various industries, including automotive, aerospace, and electronics. Their ability to automate intricate tasks not only boosts efficiency but also ensures consistent quality—an essential factor for companies aiming to maintain competitive advantage in rapidly evolving markets.
This guide provides a comprehensive overview tailored specifically for B2B buyers from Africa, South America, the Middle East, and Europe. It delves into the various types of CNC screw machines, the materials they can process, and the latest manufacturing and quality control practices. Additionally, we will explore a curated list of reputable suppliers, offering insights into cost structures and market trends that can influence your purchasing decisions.
By equipping you with detailed information and actionable insights, this guide empowers buyers to make informed sourcing decisions. Whether you are a procurement manager in South America looking for reliable suppliers or a manufacturer in Europe seeking the latest technology, understanding the nuances of the CNC screw machine market will enhance your operational efficiency and product quality. Prepare to navigate this essential segment of manufacturing with confidence and clarity.
Understanding cnc screw machine Types and Variations
Type Name | Key Distinguishing Features | Primary B2B Applications | Brief Pros & Cons for Buyers |
---|---|---|---|
Automatic CNC Screw Machine | Fully automated operations with advanced tooling systems | Mass production of screws and fasteners | Pros: High efficiency, reduced labor costs. Cons: High initial investment. |
CNC Swiss Screw Machine | Precision machining with a sliding headstock | Complex parts in aerospace and medical sectors | Pros: Excellent precision and surface finish. Cons: Limited to smaller parts. |
Multi-Spindle CNC Screw Machine | Multiple spindles for simultaneous operations | High-volume production of simple components | Pros: Increased throughput, lower cost per unit. Cons: Less flexibility in design changes. |
CNC Turning Center | Combines turning and milling capabilities | Versatile applications across various industries | Pros: Versatile machining, capable of complex shapes. Cons: Requires skilled operators. |
CNC Machining Center | Features a rotating tool holder for multi-axis machining | Custom parts manufacturing and prototyping | Pros: High precision, suitable for diverse materials. Cons: Higher maintenance costs. |
Automatic CNC Screw Machine
Automatic CNC screw machines are designed for high-volume production, enabling manufacturers to produce large quantities of screws and fasteners with minimal human intervention. They feature advanced tooling systems that enhance speed and efficiency. For B2B buyers, this type is ideal for businesses focused on mass production. However, the initial investment can be significant, so it is crucial to assess the expected return on investment based on production needs.
CNC Swiss Screw Machine
The CNC Swiss screw machine is known for its ability to produce highly precise components, particularly in industries such as aerospace and medical. Its sliding headstock allows for the machining of long, slender parts with exceptional accuracy. Buyers looking for precision in small parts will find this type advantageous. However, its specialization may limit the variety of parts that can be produced, making it essential to evaluate product range before purchasing.
Multi-Spindle CNC Screw Machine
Multi-spindle CNC screw machines are designed for high-volume production by utilizing multiple spindles to perform simultaneous operations. This capability significantly increases throughput, making it a cost-effective solution for producing simple components. B2B buyers aiming to reduce unit costs while maintaining volume should consider this type. However, its design may offer less flexibility for complex parts, which is a critical factor for businesses with diverse product lines.
CNC Turning Center
CNC turning centers combine turning and milling capabilities, making them versatile for various machining tasks. They can create complex shapes and features, making them suitable for a wide range of industries. For B2B buyers, the ability to handle multiple processes in one machine can lead to reduced lead times and cost savings. However, the requirement for skilled operators can present challenges, particularly in regions with a limited talent pool.
CNC Machining Center
CNC machining centers are equipped with rotating tool holders that allow for multi-axis machining, making them ideal for custom parts manufacturing and prototyping. Their high precision and adaptability to various materials make them a valuable asset for businesses looking to innovate. However, the higher maintenance costs associated with these machines may be a consideration for budget-conscious buyers. Understanding the total cost of ownership is vital for making informed purchasing decisions in this category.
Related Video: CS 198-126: Lecture 12 – Diffusion Models
Key Industrial Applications of cnc screw machine
Industry/Sector | Specific Application of cnc screw machine | Value/Benefit for the Business | Key Sourcing Considerations for this Application |
---|---|---|---|
Automotive | Production of precision fasteners | Enhanced production speed and quality control | Supplier certifications, material sourcing standards |
Electronics | Manufacturing of intricate components | High precision and reduced waste | Technical support, customization options |
Aerospace | Fabrication of specialized parts | Compliance with stringent safety standards | Proven track record in aerospace applications |
Medical Devices | Creation of surgical instruments and implants | Ensures high reliability and safety | Regulatory compliance, quality assurance processes |
Construction | Production of structural connectors | Improved structural integrity and project efficiency | Material specifications, lead times, and logistics |
Automotive Industry
In the automotive sector, CNC screw machines are pivotal in producing precision fasteners such as bolts, nuts, and screws. These components must adhere to strict tolerances to ensure vehicle safety and performance. By employing CNC technology, manufacturers can achieve high-speed production while maintaining quality control, significantly reducing the risk of defects. For international buyers, particularly from regions like Africa and South America, it is crucial to consider suppliers that meet industry certifications and can provide high-quality materials to withstand rigorous automotive standards.
Electronics Sector
The electronics industry benefits from CNC screw machines through the manufacturing of intricate components like connectors and housings. The precision offered by these machines minimizes waste and enhances the overall product quality, which is vital in a sector where small errors can lead to significant malfunctions. Buyers from Europe and the Middle East should prioritize suppliers that offer robust technical support and customization options to adapt to rapidly changing technology trends and product specifications.
Aerospace Industry
In aerospace manufacturing, CNC screw machines are essential for fabricating specialized parts such as brackets and fasteners that must meet stringent safety and performance standards. The use of CNC technology allows for the production of complex geometries with high precision, ensuring reliability in critical applications. Buyers in this sector need to ensure that their suppliers have a proven track record in aerospace applications and can demonstrate compliance with necessary regulations to avoid costly delays or safety issues.
Medical Devices
CNC screw machines play a crucial role in the medical device industry, particularly in the creation of surgical instruments and implants. The high reliability and safety required in medical applications necessitate the use of precision manufacturing processes. International buyers must focus on suppliers who adhere to strict regulatory compliance and quality assurance processes, ensuring that all products meet health standards and can withstand rigorous testing.
Construction Sector
In the construction industry, CNC screw machines are used to produce structural connectors that enhance the integrity of buildings and infrastructure. The efficiency gained from CNC machining translates to faster project timelines and reduced labor costs. For buyers in Africa and South America, it is vital to consider suppliers that can meet specific material specifications and provide reliable lead times, as these factors are critical for maintaining project schedules and budgets.
Related Video: What is the Difference Between CNC Swiss, Multispindle, and Screw Machining?
Strategic Material Selection Guide for cnc screw machine
When selecting materials for CNC screw machines, international B2B buyers must consider various factors, including performance properties, manufacturing complexities, and compliance with regional standards. Below is an analysis of four common materials used in CNC screw machines, focusing on their key properties, advantages, disadvantages, and specific considerations for buyers from Africa, South America, the Middle East, and Europe.
1. Stainless Steel
Key Properties: Stainless steel is known for its excellent corrosion resistance, high tensile strength, and ability to withstand elevated temperatures. It typically has a temperature rating of up to 800°C and can handle moderate pressure levels.
Pros & Cons: The durability of stainless steel makes it suitable for applications requiring longevity and resistance to harsh environments. However, it is more expensive than other materials and can be challenging to machine due to its hardness, leading to increased manufacturing complexity.
Impact on Application: Stainless steel is ideal for applications involving corrosive media, such as chemicals and saline solutions. Its compatibility with various environments makes it a preferred choice for industries like pharmaceuticals and food processing.
Considerations for International Buyers: Buyers should ensure compliance with international standards such as ASTM A276 or DIN 1.4301. Additionally, sourcing from local suppliers can mitigate costs associated with import tariffs and shipping.
2. Aluminum
Key Properties: Aluminum is lightweight, has good corrosion resistance, and offers excellent machinability. It can withstand temperatures up to 200°C and is suitable for low to moderate pressure applications.
Pros & Cons: The primary advantage of aluminum is its low weight, which can reduce overall production costs and improve energy efficiency in applications. However, it has lower tensile strength compared to stainless steel and may not be suitable for high-stress applications.
Impact on Application: Aluminum is often used in industries where weight reduction is crucial, such as aerospace and automotive. It is compatible with non-corrosive media and can be anodized for enhanced surface protection.
Considerations for International Buyers: Buyers should look for compliance with standards like ASTM B221 and consider the availability of aluminum alloys that meet specific application requirements. Local sourcing is also beneficial to avoid delays and additional costs.
3. Brass
Key Properties: Brass exhibits good machinability, moderate corrosion resistance, and a temperature rating of up to 300°C. It is also known for its excellent electrical conductivity.
Pros & Cons: The ease of machining brass makes it a popular choice for precision components. However, it is less durable than stainless steel and can corrode in certain environments, particularly in the presence of moisture.
Impact on Application: Brass is commonly used in applications that require good electrical conductivity, such as electrical connectors and fittings. It is suitable for low-pressure applications involving non-corrosive fluids.
Considerations for International Buyers: Buyers should be aware of the specific brass alloy standards, such as ASTM B16, and ensure compliance with local regulations regarding lead content. Sourcing from reputable suppliers can help avoid quality issues.
4. Carbon Steel
Key Properties: Carbon steel is known for its high strength and hardness, with temperature ratings typically up to 400°C. It is less resistant to corrosion compared to stainless steel.
Pros & Cons: The primary advantage of carbon steel is its cost-effectiveness and high tensile strength, making it suitable for heavy-duty applications. However, its susceptibility to rust and corrosion can limit its use in certain environments.
Impact on Application: Carbon steel is ideal for applications requiring high strength and durability, such as construction and heavy machinery. It is compatible with various media but requires protective coatings in corrosive environments.
Considerations for International Buyers: Compliance with standards like ASTM A36 is essential, particularly in regions with stringent quality regulations. Buyers should also consider the availability of protective coatings to enhance corrosion resistance.
Summary Table
Material | Typical Use Case for cnc screw machine | Key Advantage | Key Disadvantage/Limitation | Relative Cost (Low/Med/High) |
---|---|---|---|---|
Stainless Steel | Pharmaceutical and food processing | Excellent corrosion resistance | Higher cost and manufacturing complexity | High |
Aluminum | Aerospace and automotive applications | Lightweight and easy to machine | Lower tensile strength | Medium |
Brass | Electrical connectors and fittings | Good machinability and conductivity | Less durable and moisture-sensitive | Medium |
Carbon Steel | Construction and heavy machinery | Cost-effective and high strength | Susceptible to corrosion | Low |
This strategic material selection guide aims to assist international B2B buyers in making informed decisions about CNC screw machine materials, ensuring that their choices align with performance requirements and regional standards.
In-depth Look: Manufacturing Processes and Quality Assurance for cnc screw machine
Manufacturing Processes for CNC Screw Machines
The manufacturing of CNC screw machines involves a series of precise and methodical processes to ensure high-quality output. Understanding these stages can help B2B buyers make informed decisions regarding their suppliers and the capabilities of the machines they are considering.
1. Material Preparation
The first stage in the manufacturing process is material preparation, where raw materials such as metals (e.g., aluminum, steel, brass) are sourced and prepared for machining. Key considerations include:
- Material Selection: Choose materials based on the required mechanical properties, such as tensile strength and corrosion resistance.
- Material Inspection: Incoming materials should be inspected for defects or inconsistencies using techniques such as ultrasonic testing or visual inspections.
- Cutting and Shaping: Materials are often cut into manageable sizes for further processing, typically using saws or laser cutting technologies.
2. Forming
The forming stage involves shaping the raw materials into the desired component forms. This is where CNC (Computer Numerical Control) technology plays a crucial role:
- CNC Machining: Using CNC lathes and mills, materials are precisely cut and shaped according to programmed specifications. This process ensures high accuracy and repeatability.
- Techniques Used: Key techniques include turning, milling, drilling, and grinding. Each technique serves specific functions, such as creating threads, holes, or surface finishes.
3. Assembly
Once individual components are machined, they move to the assembly stage:
- Sub-Assembly: Components may be assembled in smaller groups before final assembly. This step helps streamline the process and allows for quality checks at multiple stages.
- Final Assembly: The final assembly combines all sub-assemblies into a complete machine. This stage often involves the use of fasteners, seals, and other components to ensure structural integrity.
4. Finishing
The finishing stage is essential for enhancing the aesthetics and functionality of the CNC screw machines:
- Surface Treatment: Techniques such as anodizing, powder coating, or plating may be applied to improve corrosion resistance and surface hardness.
- Quality Checks: Finishing processes should include rigorous quality checks to ensure that the final product meets design specifications and industry standards.
Quality Assurance in CNC Screw Machine Manufacturing
Quality assurance is critical in the manufacturing of CNC screw machines to ensure that products meet international standards and customer expectations. Here are key aspects of quality assurance that international B2B buyers should consider.
Relevant International Standards
Adherence to international quality standards is crucial for ensuring product reliability and safety. Key standards include:
- ISO 9001: This standard outlines a quality management system that can help organizations improve their processes and customer satisfaction.
- CE Marking: Required for products sold in the European Economic Area, it indicates compliance with safety, health, and environmental protection standards.
- API Certification: For companies involved in the oil and gas sector, API (American Petroleum Institute) certification ensures that products meet industry-specific standards.
Quality Control Checkpoints
Implementing a robust quality control system is essential. Common checkpoints include:
- Incoming Quality Control (IQC): This step involves inspecting raw materials and components upon arrival to ensure they meet specified standards.
- In-Process Quality Control (IPQC): Ongoing inspections during the manufacturing process help identify defects early and minimize waste.
- Final Quality Control (FQC): The final inspection ensures that the completed machines meet all specifications before shipment.
Common Testing Methods
Testing methodologies play a vital role in quality assurance:
- Dimensional Inspection: Using tools such as calipers and coordinate measuring machines (CMM) to check the accuracy of dimensions.
- Functional Testing: Ensuring that the machine operates correctly under specified conditions.
- Non-Destructive Testing (NDT): Techniques like magnetic particle inspection or dye penetrant testing help identify defects without damaging the component.
Verifying Supplier Quality Control
For B2B buyers, especially those in Africa, South America, the Middle East, and Europe, verifying the quality control processes of potential suppliers is paramount:
-
Supplier Audits: Conduct on-site audits to assess the manufacturing processes, quality management systems, and overall operational capabilities of the supplier.
-
Quality Reports: Request documentation detailing past quality performance, including defect rates and corrective actions taken.
-
Third-Party Inspections: Engage third-party inspection agencies to conduct independent assessments of the supplier’s quality control processes and product quality.
Quality Control and Certification Nuances for International Buyers
International B2B buyers must be aware of various nuances when dealing with quality control and certification:
- Cultural Considerations: Different regions may have varying approaches to quality assurance. Understanding local practices can help buyers set realistic expectations.
- Documentation Requirements: Ensure that all certifications are up-to-date and that suppliers can provide necessary documentation to facilitate customs clearance and compliance.
- Regulatory Differences: Be aware of specific regulations that may apply in different regions, such as environmental regulations in Europe or safety standards in the Middle East.
By thoroughly understanding the manufacturing processes and quality assurance protocols associated with CNC screw machines, international B2B buyers can make informed decisions, minimize risks, and ensure they receive high-quality products that meet their operational needs.
Related Video: SMART Quality Control for Manufacturing
Comprehensive Cost and Pricing Analysis for cnc screw machine Sourcing
When sourcing CNC screw machines, understanding the cost structure and pricing dynamics is crucial for international B2B buyers. The total cost can be broken down into several key components, each influencing the overall pricing strategy.
Cost Components
-
Materials: The choice of materials significantly impacts the cost. High-quality metals, such as steel or aluminum, will increase expenses but ensure durability and performance. Buyers should evaluate the material specifications based on their application needs to balance cost and quality.
-
Labor: Labor costs vary widely by region. For example, countries in Africa and South America may have lower labor costs compared to Europe, which can affect manufacturing expenses. However, higher labor costs in developed regions might correlate with better craftsmanship and quality assurance.
-
Manufacturing Overhead: This includes utilities, rent, and other operational costs associated with the manufacturing facility. Buyers should inquire about the supplier’s location to understand how overhead costs may influence pricing.
-
Tooling: Tooling costs can be substantial, especially for custom machines. It encompasses the design and production of specialized tools necessary for machining processes. Buyers should factor in these costs when requesting quotes for customized CNC screw machines.
-
Quality Control (QC): Ensuring that machines meet quality standards adds to the overall cost. Suppliers with rigorous QC processes may charge higher prices but provide better reliability and lower failure rates in the long run.
-
Logistics: Transportation and shipping costs are critical, particularly for international buyers. Factors such as distance, shipping method, and import duties can significantly alter the final price. Understanding Incoterms is essential to clarify responsibilities for shipping costs and risks.
-
Margin: Suppliers will typically include a profit margin in their pricing. This margin can vary based on the supplier’s reputation, market demand, and competitive landscape.
Price Influencers
Several factors can influence the pricing of CNC screw machines:
-
Volume/MOQ: Larger orders often lead to lower per-unit costs. Buyers should consider their purchasing power and negotiate minimum order quantities (MOQs) to achieve better pricing.
-
Specifications/Customization: Custom features or specifications can raise costs. Buyers should clearly communicate their needs to avoid unexpected charges during production.
-
Materials: The choice of material not only affects the initial price but can also influence long-term maintenance costs. High-quality materials may incur higher upfront costs but result in lower Total Cost of Ownership (TCO).
-
Quality/Certifications: Machines that meet international quality standards or possess specific certifications may cost more but can provide added assurance of reliability and performance.
-
Supplier Factors: Established suppliers with a proven track record may charge higher prices but often offer better service and support, reducing risks associated with sourcing.
-
Incoterms: Understanding Incoterms is vital for international transactions. They dictate who is responsible for shipping, insurance, and tariffs, which can significantly impact overall costs.
Buyer Tips
-
Negotiation: Effective negotiation strategies can lead to better pricing. Buyers should leverage their purchasing volume and be prepared to discuss long-term partnerships to secure favorable terms.
-
Cost-Efficiency: Assessing the Total Cost of Ownership (TCO) is critical. This includes not just the purchase price but also maintenance, operational costs, and potential downtime.
-
Pricing Nuances: International buyers should be aware of currency fluctuations and their potential impact on pricing. Establishing contracts in stable currencies can help mitigate these risks.
-
Supplier Research: Conduct thorough research on potential suppliers. Understanding their production capabilities, quality assurance processes, and customer service can help in making informed decisions.
-
Request Detailed Quotes: Always ask for detailed quotes that break down costs. This transparency helps in identifying areas for negotiation and ensures there are no hidden fees.
Disclaimer
Prices for CNC screw machines can vary widely based on specifications and supplier conditions. It is advisable to seek multiple quotes and conduct due diligence to ensure a comprehensive understanding of all associated costs before making purchasing decisions.
Spotlight on Potential cnc screw machine Manufacturers and Suppliers
This section looks at several manufacturers active in the ‘cnc screw machine’ market. This is a representative sample for illustrative purposes; B2B buyers must conduct extensive due diligence before any transaction. Information is synthesized from public sources and general industry knowledge.
Essential Technical Properties and Trade Terminology for cnc screw machine
When navigating the complexities of purchasing CNC screw machines, understanding essential technical properties and trade terminology is crucial for informed decision-making. Below is a detailed overview of key specifications and industry jargon that can significantly impact your procurement process.
Key Technical Properties
-
Material Grade
– Definition: This refers to the type of material used in manufacturing the CNC screw machine components, such as steel, aluminum, or plastic.
– Importance: Material grade directly affects the machine’s durability, strength, and suitability for specific applications. For instance, high-grade steel is essential for producing components that must withstand high stress and wear. -
Tolerance
– Definition: Tolerance indicates the permissible limits of variation in a manufactured part’s dimensions.
– Importance: In CNC machining, tight tolerances are crucial for ensuring that parts fit together correctly and function as intended. Understanding tolerance levels helps buyers assess whether a machine can meet their specific production requirements. -
Spindle Speed
– Definition: Spindle speed is the rotational speed of the spindle, usually measured in revolutions per minute (RPM).
– Importance: High spindle speeds can enhance productivity by allowing faster machining of materials. Buyers should consider the spindle speed range to ensure it aligns with their production demands. -
Axis Configuration
– Definition: This refers to the number of axes the CNC machine can operate on, commonly ranging from 3 to 5 axes.
– Importance: The axis configuration determines the machine’s capability to perform complex machining tasks. For industries requiring intricate designs, a 5-axis machine may be necessary, while simpler tasks may only need a 3-axis configuration. -
Feed Rate
– Definition: Feed rate is the speed at which the cutting tool moves through the material, typically measured in inches per minute (IPM).
– Importance: The feed rate affects both the quality of the finished part and the efficiency of the machining process. Buyers need to understand the feed rate capabilities to optimize production cycles.
Common Trade Terms
-
OEM (Original Equipment Manufacturer)
– Definition: An OEM is a company that produces parts and equipment that may be marketed by another manufacturer.
– Importance: Understanding OEM relationships can help buyers identify reliable suppliers and ensure that they are sourcing quality components tailored for specific applications. -
MOQ (Minimum Order Quantity)
– Definition: MOQ refers to the smallest quantity of a product that a supplier is willing to sell.
– Importance: Being aware of MOQs helps buyers plan their inventory and budget effectively. For international buyers, negotiating MOQs can be crucial for managing logistics and costs. -
RFQ (Request for Quotation)
– Definition: An RFQ is a document sent to suppliers to solicit price quotes for specific products or services.
– Importance: Utilizing RFQs can streamline the procurement process by providing a clear framework for comparing supplier offerings, enabling better negotiation and cost management. -
Incoterms (International Commercial Terms)
– Definition: These are a set of predefined commercial terms published by the International Chamber of Commerce (ICC) relating to international commercial law.
– Importance: Familiarity with Incoterms helps buyers understand their obligations regarding shipping, insurance, and tariffs, which is essential for managing international transactions effectively.
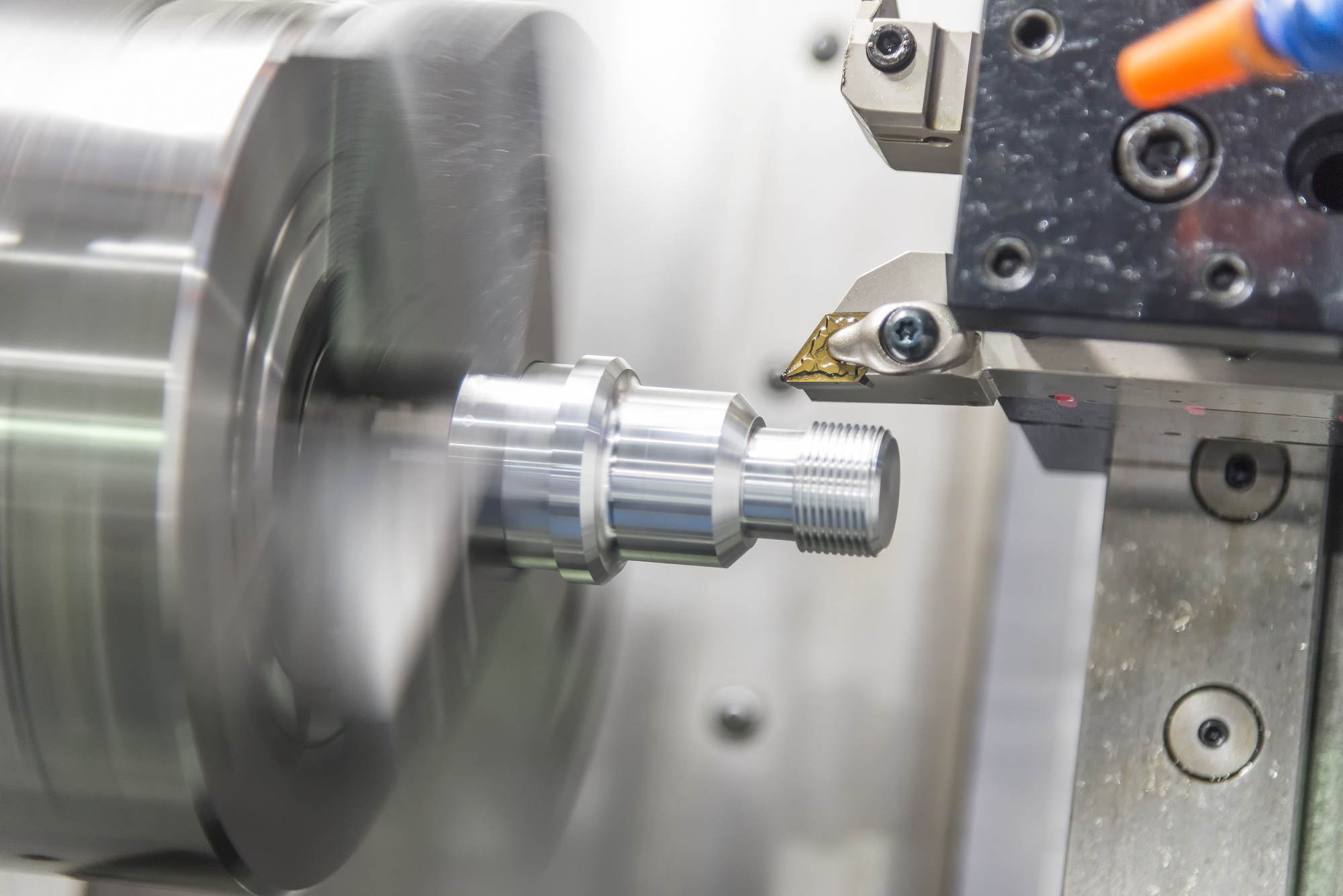
Illustrative Image (Source: Google Search)
- Lead Time
– Definition: Lead time is the amount of time it takes from placing an order to receiving the goods.
– Importance: Understanding lead times is critical for planning production schedules and ensuring timely delivery of components. This can significantly impact overall project timelines.
By grasping these essential technical properties and trade terms, international B2B buyers can navigate the complexities of the CNC screw machine market more effectively, ensuring they make informed decisions that align with their operational needs and business goals.
Navigating Market Dynamics, Sourcing Trends, and Sustainability in the cnc screw machine Sector
Market Overview & Key Trends
The CNC screw machine sector is witnessing substantial growth, driven by increased automation and demand for precision-engineered components across various industries, including automotive, aerospace, and electronics. As international B2B buyers from regions such as Africa, South America, the Middle East, and Europe seek to enhance their manufacturing capabilities, understanding the market dynamics becomes crucial. Key trends include the rise of Industry 4.0, where the integration of IoT and AI technologies into CNC machines enables real-time monitoring and predictive maintenance, thus reducing downtime and increasing efficiency.
Moreover, the push for customization has led to a growing demand for flexible manufacturing systems. This trend is particularly significant in markets like Vietnam and the UK, where buyers are looking for suppliers who can offer tailored solutions without compromising on lead times. Another critical aspect is the focus on supply chain resilience, which has been highlighted by recent global disruptions. Buyers are increasingly prioritizing suppliers with diversified sourcing strategies to mitigate risks associated with geopolitical tensions and economic fluctuations.
Sourcing trends are also evolving, with a marked shift towards local suppliers to reduce lead times and transportation costs. International buyers are encouraged to explore partnerships with regional manufacturers who not only understand local market dynamics but also comply with international standards. This approach not only enhances supply chain efficiency but also supports local economies.
Sustainability & Ethical Sourcing in B2B
Sustainability is becoming a non-negotiable aspect of sourcing strategies for international buyers in the CNC screw machine sector. The environmental impact of manufacturing processes is under scrutiny, with stakeholders demanding transparency and accountability. B2B buyers are increasingly seeking suppliers that demonstrate commitment to sustainability through eco-friendly practices, such as reduced energy consumption and waste management.
Ethical supply chains are paramount, as they ensure that materials are sourced responsibly, minimizing harm to communities and ecosystems. Certifications such as ISO 14001 for environmental management and adherence to REACH regulations for chemical safety are becoming prerequisites for suppliers aiming to engage with conscientious buyers.
Moreover, the use of ‘green’ materials—such as recycled metals or biocompatible plastics—can differentiate suppliers in a competitive market. Buyers should prioritize suppliers who can provide documentation and certifications for these materials, ensuring that their sourcing aligns with both regulatory standards and their corporate social responsibility goals.
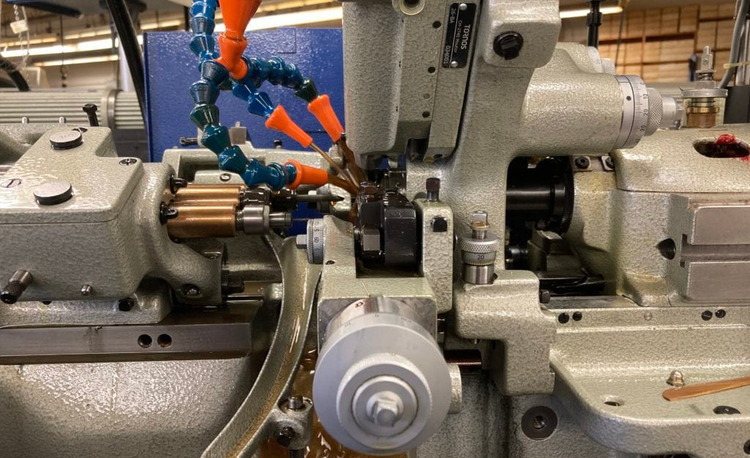
Illustrative Image (Source: Google Search)
Brief Evolution/History
The CNC screw machine has evolved significantly since its inception in the mid-20th century. Originally developed to enhance the efficiency of screw production, these machines have transformed into sophisticated systems capable of producing complex components with high precision. The introduction of computer numerical control (CNC) technology revolutionized the manufacturing landscape, allowing for greater automation and customization.
As industries continue to demand higher precision and efficiency, the CNC screw machine sector has adapted by integrating advanced technologies such as robotics and AI. This evolution not only reflects the changing needs of manufacturers but also highlights the importance of continual innovation in maintaining a competitive edge in the global market. For international B2B buyers, understanding this evolution is crucial for making informed sourcing decisions that align with both current capabilities and future trends.
Related Video: International Trade Explained
Frequently Asked Questions (FAQs) for B2B Buyers of cnc screw machine
-
What factors should I consider when vetting suppliers for CNC screw machines?
When vetting suppliers, prioritize factors such as their industry experience, production capacity, and customer reviews. Verify their certifications (ISO, CE) to ensure compliance with international standards. Request references from previous clients, particularly those in your region, to gauge reliability. Additionally, assess their communication responsiveness and willingness to provide technical support. This thorough vetting process minimizes risks associated with quality and delivery timelines, ensuring a smooth procurement experience. -
Can CNC screw machines be customized to meet specific production needs?
Yes, many suppliers offer customization options for CNC screw machines. This can include alterations in size, tooling, and software integration to cater to your specific production requirements. When discussing customization, provide detailed specifications and expected outcomes to ensure the supplier understands your needs. It’s also advisable to request prototypes or samples before full production to verify that the modifications align with your expectations. -
What are typical minimum order quantities (MOQs) and lead times for CNC screw machines?
MOQs for CNC screw machines can vary widely depending on the supplier and the complexity of the machine. Generally, MOQs range from one machine for specialized manufacturers to larger quantities for standard models. Lead times can also differ based on customization and supplier location, typically ranging from 4 to 12 weeks. Always clarify these details upfront to avoid misunderstandings and to plan your production schedule accordingly. -
What payment options are available when purchasing CNC screw machines internationally?
International transactions for CNC screw machines often involve various payment methods, including bank transfers, letters of credit, and escrow services. It’s crucial to choose a payment method that offers protection against fraud and ensures secure transactions. Negotiate payment terms upfront, considering options like partial payments during production and final payment upon delivery. This approach balances risk and cash flow management. -
What quality assurance (QA) measures should I expect from suppliers?
Reputable suppliers will implement rigorous quality assurance processes, including in-house inspections and third-party audits. Expect to receive documentation proving compliance with international standards, such as ISO certifications. Inquire about the supplier’s QA protocols, including testing procedures for precision, durability, and performance. Additionally, requesting a warranty or guarantee for the machine can provide further assurance of quality. -
How can I manage logistics when importing CNC screw machines?
Managing logistics effectively is crucial when importing CNC screw machines. Work with suppliers who have experience in international shipping and can provide guidance on customs clearance and duties. Consider partnering with a freight forwarder to navigate logistics challenges, including transportation methods and timelines. Additionally, ensure that the supplier provides proper packaging and labeling to prevent damage during transit. -
What should I do in case of disputes with a supplier?
In the event of a dispute, first attempt to resolve the issue directly with the supplier through open communication. Maintain a record of all correspondence and agreements to support your case. If resolution is not achieved, refer to the contract for dispute resolution clauses, which may include mediation or arbitration. It’s advisable to consult legal experts familiar with international trade laws to understand your rights and obligations. -
How can I ensure compliance with local regulations when importing CNC screw machines?
To ensure compliance with local regulations, research the specific import requirements for CNC screw machines in your country. This includes understanding tariffs, safety standards, and certification needs. Engage with local authorities or trade associations for guidance, and ensure your supplier provides all necessary documentation, including compliance certifications. Staying informed about regulatory changes will help you avoid costly delays or penalties.
Important Disclaimer & Terms of Use
⚠️ Important Disclaimer
The information provided in this guide, including content regarding manufacturers, technical specifications, and market analysis, is for informational and educational purposes only. It does not constitute professional procurement advice, financial advice, or legal advice.
While we have made every effort to ensure the accuracy and timeliness of the information, we are not responsible for any errors, omissions, or outdated information. Market conditions, company details, and technical standards are subject to change.
B2B buyers must conduct their own independent and thorough due diligence before making any purchasing decisions. This includes contacting suppliers directly, verifying certifications, requesting samples, and seeking professional consultation. The risk of relying on any information in this guide is borne solely by the reader.
Strategic Sourcing Conclusion and Outlook for cnc screw machine
In conclusion, strategic sourcing for CNC screw machines is not merely a procurement function; it is a vital component of a company’s overall operational strategy. Key takeaways for international B2B buyers include the importance of understanding the total cost of ownership, evaluating suppliers based on technological capabilities, and fostering strong partnerships that facilitate innovation. By leveraging data-driven insights and market intelligence, companies can identify suppliers that not only meet current demands but also align with long-term growth objectives.
The global landscape presents both challenges and opportunities, particularly for buyers in Africa, South America, the Middle East, and Europe. As industries evolve and the demand for precision manufacturing increases, investing in high-quality CNC screw machines will be crucial for maintaining competitive advantage.
Looking ahead, international B2B buyers should prioritize agility and sustainability in their sourcing strategies. This is an opportune moment to explore new markets and technologies that can enhance production efficiency. Engage with suppliers who demonstrate a commitment to innovation and customer-centric solutions. By adopting a proactive approach to strategic sourcing, you can ensure your business is well-positioned for future success in the dynamic manufacturing environment.