Your Ultimate Guide to Sourcing Cnc Stitching Machine
Introduction: Navigating the Global Market for cnc stitching machine
In an increasingly competitive landscape, the CNC stitching machine stands as a cornerstone technology for industries ranging from textiles to automotive manufacturing. These precision-engineered machines not only enhance production efficiency but also ensure consistent quality and reduced labor costs. For international B2B buyers, particularly those in Africa, South America, the Middle East, and Europe, understanding the nuances of this market is essential for making informed sourcing decisions.
This comprehensive guide delves into the multifaceted world of CNC stitching machines, providing valuable insights into various types available, the materials they work with, and the manufacturing and quality control processes that define industry standards. We will also explore key suppliers and manufacturers across different regions, offering a comparative analysis of pricing structures, which is crucial for budget-conscious buyers.
In addition, our guide addresses common questions and concerns, empowering you to navigate potential challenges in the procurement process. By equipping yourself with this knowledge, you can streamline your sourcing strategy, optimize production capabilities, and ultimately drive your business’s growth. Whether you are looking to invest in new machinery or expand your existing capabilities, this guide is designed to be your trusted resource in the global market for CNC stitching machines.
Understanding cnc stitching machine Types and Variations
Type Name | Key Distinguishing Features | Primary B2B Applications | Brief Pros & Cons for Buyers |
---|---|---|---|
Flat Bed CNC Stitching Machine | Large, flat working area; high precision; versatile | Apparel manufacturing, upholstery | Pros: High accuracy, suitable for large fabrics. Cons: Requires significant floor space. |
Cylinder Bed CNC Stitching Machine | Curved bed design; ideal for circular stitching | Bags, shoes, and automotive sectors | Pros: Excellent for round items, adaptable. Cons: Limited for flat materials. |
Computerized Multi-Needle Machine | Multiple needles for simultaneous stitching | Quilting, heavy-duty fabric work | Pros: Increases productivity, consistent quality. Cons: Higher initial investment. |
Overlock CNC Stitching Machine | Specialized for seam finishing; serger capabilities | Garment production, textiles | Pros: Efficient seam finishing, prevents fraying. Cons: Limited to specific stitching tasks. |
Embroidery CNC Stitching Machine | Integrates embroidery functions; customizable designs | Fashion, promotional products | Pros: Versatile; adds value to products. Cons: Complex software may require training. |
Flat Bed CNC Stitching Machine
The Flat Bed CNC Stitching Machine is characterized by its expansive flat working area, which allows for high precision and versatility in handling various fabric types. This machine is particularly suitable for applications in apparel manufacturing and upholstery, where large pieces need to be stitched accurately. When considering a purchase, B2B buyers should evaluate the available floor space and the machine’s compatibility with their production volume, as these machines can take up significant real estate.
Cylinder Bed CNC Stitching Machine
Designed with a curved bed, the Cylinder Bed CNC Stitching Machine is ideal for stitching circular or tubular items such as bags and shoes. Its unique design allows for greater maneuverability around curved surfaces, making it a preferred choice in the automotive sector as well. Buyers should consider the types of products they manufacture, as this machine excels in applications requiring flexibility in stitching shapes, but may not be efficient for flat materials.
Computerized Multi-Needle Machine
The Computerized Multi-Needle Machine features multiple needles that enable simultaneous stitching, thereby increasing productivity significantly. This machine is particularly beneficial for quilting and heavy-duty fabric work, where consistent quality is paramount. B2B buyers should assess the initial investment against potential productivity gains, as this type of machine can be more costly upfront but offers substantial returns through efficiency improvements.
Overlock CNC Stitching Machine
The Overlock CNC Stitching Machine specializes in seam finishing and includes serger capabilities. It is widely used in garment production and textiles, where it efficiently finishes seams and prevents fabric fraying. Buyers should consider their specific stitching needs, as this machine is limited to finishing tasks but excels in enhancing the durability and quality of the final product.
Embroidery CNC Stitching Machine
The Embroidery CNC Stitching Machine combines traditional stitching with embroidery functions, allowing for customizable designs on various textiles. This machine is particularly popular in the fashion industry and for promotional products, where unique branding is essential. B2B buyers must evaluate the complexity of the software and the potential training required for their staff, as this machine offers versatility but may necessitate a learning curve to optimize its capabilities.
Related Video: CS 198-126: Lecture 12 – Diffusion Models
Key Industrial Applications of cnc stitching machine
Industry/Sector | Specific Application of cnc stitching machine | Value/Benefit for the Business | Key Sourcing Considerations for this Application |
---|---|---|---|
Textiles and Apparel | Automated stitching for garments and accessories | Increased production speed and uniform quality | Compatibility with various fabric types; maintenance support |
Automotive | Upholstery stitching for seats and interiors | Enhanced durability and aesthetics in vehicle interiors | Compliance with automotive standards; precision stitching capabilities |
Furniture Manufacturing | Stitching for upholstery and cushions | Cost-effective production with consistent quality | Material handling capabilities; customization options |
Footwear | Stitching for shoe construction | Improved efficiency and reduction in labor costs | Flexibility for different shoe designs; durability of stitching |
Aerospace and Defense | Stitching for protective gear and components | High precision and reliability in critical applications | Certification for aerospace standards; ability to handle specialized materials |
Textiles and Apparel
In the textiles and apparel industry, CNC stitching machines are used for automated stitching of garments and accessories. This technology addresses common issues such as inconsistent stitching quality and slow production rates. By implementing CNC stitching, businesses can achieve higher output while ensuring uniformity in stitching patterns. International buyers should consider machines that can handle various fabric types and offer robust maintenance support to minimize downtime.
Automotive
CNC stitching machines play a crucial role in the automotive sector, particularly for upholstery stitching of seats and interiors. These machines provide enhanced durability and aesthetic appeal, which are essential for consumer satisfaction and brand reputation. Buyers in this sector should focus on sourcing machines that comply with automotive standards and offer precision stitching capabilities to ensure high-quality finishes that withstand wear and tear.
Furniture Manufacturing
In furniture manufacturing, CNC stitching is employed for creating upholstery and cushions. The automation of this process leads to cost-effective production with consistent quality, reducing labor costs and material waste. Buyers should look for machines that can handle different materials and offer customization options to meet specific design needs, ensuring flexibility in production.
Footwear
The footwear industry benefits significantly from CNC stitching machines used in shoe construction. These machines enhance efficiency and reduce labor costs by automating complex stitching processes. International buyers should prioritize sourcing machines that offer flexibility for various shoe designs and ensure the durability of stitching, which is critical for product longevity and customer satisfaction.
Aerospace and Defense
In the aerospace and defense sectors, CNC stitching machines are vital for producing protective gear and components. These machines provide high precision and reliability, which are crucial in applications where safety is paramount. Buyers should ensure that sourced machines have the necessary certifications for aerospace standards and can handle specialized materials, ensuring compliance and performance in critical applications.
Related Video: The World’s Largest Bevel Gear CNC Machine- Modern Gear Production Line. Steel Wheel Manufacturing
Strategic Material Selection Guide for cnc stitching machine
When selecting materials for CNC stitching machines, it’s essential to consider various factors that affect performance, durability, and cost. Below is a detailed analysis of common materials used in CNC stitching machines, focusing on their properties, advantages, disadvantages, and specific considerations for international B2B buyers.
Aluminum Alloys
Key Properties:
Aluminum alloys are lightweight and exhibit excellent corrosion resistance. They typically have a temperature rating up to 150°C and can withstand moderate pressures, making them suitable for various stitching applications.
Pros & Cons:
The primary advantage of aluminum alloys is their lightweight nature, which enhances machine efficiency and reduces energy consumption. They are also resistant to rust and easy to machine, leading to lower manufacturing complexity. However, they may not be as durable as other metals under extreme conditions, and their cost can be higher than some alternatives.
Impact on Application:
Aluminum alloys are ideal for stitching light to medium-weight materials, such as textiles and synthetic fabrics. Their compatibility with these media ensures smooth operation and high-quality stitching.
Considerations for International Buyers:
Buyers in regions like Africa and South America should ensure compliance with local standards regarding aluminum usage. In Europe, adherence to ASTM and DIN standards is crucial, especially for aerospace and automotive applications.
Stainless Steel
Key Properties:
Stainless steel offers high strength, excellent corrosion resistance, and can withstand temperatures up to 300°C. Its pressure rating is also favorable, making it suitable for heavy-duty applications.
Pros & Cons:
The durability of stainless steel is a significant advantage, especially in environments prone to moisture and chemicals. However, the manufacturing complexity is higher due to its toughness, which can lead to increased production costs. Additionally, its weight can be a disadvantage in terms of energy efficiency.
Impact on Application:
Stainless steel is suitable for stitching heavy-duty materials like leather and thick fabrics. Its robustness ensures that the stitching remains intact under stress.
Considerations for International Buyers:
Buyers should be aware of the specific grades of stainless steel that meet local regulations. In the Middle East, for instance, compliance with JIS standards may be necessary for specific industries.
Carbon Fiber Composites
Key Properties:
Carbon fiber composites are known for their high strength-to-weight ratio and excellent thermal stability, withstanding temperatures up to 200°C. They are also resistant to corrosion and chemicals.
Pros & Cons:
The lightweight nature of carbon fiber composites allows for faster machine operation and lower energy consumption. However, they are generally more expensive than metals and can be challenging to manufacture, requiring specialized processes.
Impact on Application:
These materials are ideal for high-performance stitching applications, particularly in industries like aerospace and automotive, where weight savings are critical.
Considerations for International Buyers:
Buyers from Europe and the Middle East should ensure that the carbon fiber materials comply with industry-specific standards. The high cost may also necessitate a thorough cost-benefit analysis, especially for small to medium enterprises.
High-Performance Plastics
Key Properties:
High-performance plastics, such as PEEK and PTFE, offer excellent chemical resistance and can operate at temperatures up to 260°C. They are lightweight and provide good mechanical properties.
Pros & Cons:
These plastics are highly versatile and can be tailored for specific applications, providing significant design flexibility. However, they can be more expensive than traditional materials and may require specialized machining techniques.
Impact on Application:
High-performance plastics are suitable for stitching applications involving chemically aggressive materials or environments, such as in the medical or food industries.
Considerations for International Buyers:
International buyers should verify compliance with local regulations regarding the use of plastics, particularly in food and medical applications. Standards such as FDA regulations in the U.S. and EU directives in Europe are critical.
Summary Table
Material | Typical Use Case for cnc stitching machine | Key Advantage | Key Disadvantage/Limitation | Relative Cost (Low/Med/High) |
---|---|---|---|---|
Aluminum Alloys | Light to medium-weight textiles | Lightweight and energy-efficient | Less durable under extreme conditions | Medium |
Stainless Steel | Heavy-duty materials like leather | High strength and corrosion resistance | Higher manufacturing complexity | High |
Carbon Fiber Composites | Aerospace and automotive applications | High strength-to-weight ratio | Expensive and complex to manufacture | High |
High-Performance Plastics | Medical and food industry applications | Excellent chemical resistance | Higher cost and specialized machining | High |
This guide provides a comprehensive overview of material options for CNC stitching machines, equipping international B2B buyers with the insights needed to make informed decisions tailored to their specific market needs.
In-depth Look: Manufacturing Processes and Quality Assurance for cnc stitching machine
Manufacturing Processes for CNC Stitching Machines
The manufacturing of CNC stitching machines involves several key stages, each critical to ensuring the final product meets the required specifications and quality standards. Understanding these processes can help B2B buyers assess potential suppliers and their capabilities.
1. Material Preparation
The initial stage of manufacturing CNC stitching machines begins with material selection and preparation. Common materials include high-grade steel, aluminum, and specialized polymers. Each material is chosen based on its durability, weight, and resistance to wear and tear.
- Cutting and Shaping: Raw materials are cut into specific dimensions using techniques such as laser cutting or water jet cutting. This ensures precision and minimizes waste.
- Surface Treatment: Materials often undergo treatments like anodizing or powder coating to enhance durability and aesthetics. This is particularly important for machines exposed to harsh environments.
2. Forming
In this stage, the prepared materials are shaped into components. This is typically achieved through various forming techniques:
- CNC Machining: Advanced CNC (Computer Numerical Control) machines are used to create intricate parts with high precision. This technique allows for complex geometries that are essential in stitching machine functionality.
- Bending and Stamping: Metal components may be bent or stamped into shape using hydraulic presses. This stage is crucial for producing the machine’s frame and other structural elements.
3. Assembly
Once the components are formed, the assembly process begins. This involves the following steps:
- Component Integration: Individual parts are meticulously assembled. This may include integrating the stitching head, control panels, and feeding systems.
- Wiring and Electronics: Electrical components are installed, ensuring that all systems communicate effectively. Attention to detail here is vital to prevent future operational issues.
4. Finishing
The final stage focuses on ensuring the machine is ready for market:
- Quality Checks: Each assembled machine undergoes a series of inspections to ensure it meets design specifications. This includes functional tests to verify stitching quality and machine reliability.
- Cosmetic Finishing: Final touches such as painting and branding are applied, ensuring the machine is visually appealing and compliant with branding standards.
Quality Assurance
Quality assurance (QA) is a critical aspect of the CNC stitching machine manufacturing process, ensuring that the final product is reliable and meets international standards.
International Standards
B2B buyers should be aware of relevant quality standards that manufacturers may adhere to:
- ISO 9001: This standard ensures that manufacturers have a quality management system in place, focusing on customer satisfaction and continuous improvement.
- CE Marking: Essential for products sold in the European Economic Area (EEA), this marking indicates compliance with health, safety, and environmental protection standards.
- API Standards: For machines used in the oil and gas industries, adherence to American Petroleum Institute (API) standards may be necessary.
QC Checkpoints
Quality control (QC) involves systematic checks throughout the manufacturing process. Key checkpoints include:
- Incoming Quality Control (IQC): Inspecting raw materials upon arrival to ensure they meet specifications.
- In-Process Quality Control (IPQC): Continuous monitoring during the manufacturing process to catch defects early.
- Final Quality Control (FQC): A comprehensive inspection of the finished product, including functional testing and performance verification.
Common Testing Methods
Various testing methods are employed to ensure the quality and performance of CNC stitching machines:
- Functional Testing: Verifying that the machine operates as intended, including stitching accuracy and speed.
- Durability Testing: Simulating long-term usage to ensure the machine can withstand operational stresses.
- Safety Testing: Ensuring that safety features are effective and comply with relevant regulations.
Verifying Supplier Quality Control
For B2B buyers, particularly those from Africa, South America, the Middle East, and Europe, verifying a supplier’s quality control measures is essential to mitigate risks and ensure product reliability.
Conducting Audits
Buyers should consider conducting audits of potential suppliers. This includes:
- On-Site Visits: Inspecting manufacturing facilities to observe processes firsthand and assess quality control measures.
- Documentation Review: Evaluating quality control documentation, including certificates, inspection reports, and compliance with international standards.
Requesting Reports
B2B buyers should request detailed quality assurance reports from suppliers. These reports should include:
- Test Results: Data from functional, durability, and safety tests.
- Non-Conformance Reports: Documentation of any defects found during production and the corrective actions taken.
Engaging Third-Party Inspectors
Engaging third-party inspectors can provide an unbiased assessment of a supplier’s quality control processes. This is particularly important for buyers in regions where local regulations may differ from international standards.
Navigating QC and Certification Nuances
Understanding the nuances of quality control and certification is crucial for international B2B buyers. Each region may have specific requirements that affect the procurement process:
- Regional Compliance: Ensure that the machines comply with local regulations and standards in the buyer’s region. For instance, CE marking is mandatory for products sold in Europe.
- Cultural Considerations: Be aware of cultural differences that may influence business practices and communication styles in supplier countries.
By thoroughly understanding the manufacturing processes and quality assurance standards for CNC stitching machines, B2B buyers can make informed decisions, ensuring they source reliable and high-quality products for their operations.
**Related Video: Mesk Furniture Ergonomic Chair Quality Testing **
Comprehensive Cost and Pricing Analysis for cnc stitching machine Sourcing
When sourcing CNC stitching machines, understanding the comprehensive cost structure and pricing dynamics is crucial for international B2B buyers. This analysis will cover the essential cost components, price influencers, and provide actionable buyer tips tailored for markets in Africa, South America, the Middle East, and Europe.
Cost Components
- Materials: The primary costs arise from the raw materials used in manufacturing CNC stitching machines. This includes high-quality metals, electronic components, and specialized fabrics. Fluctuations in global commodity prices can significantly impact these costs.
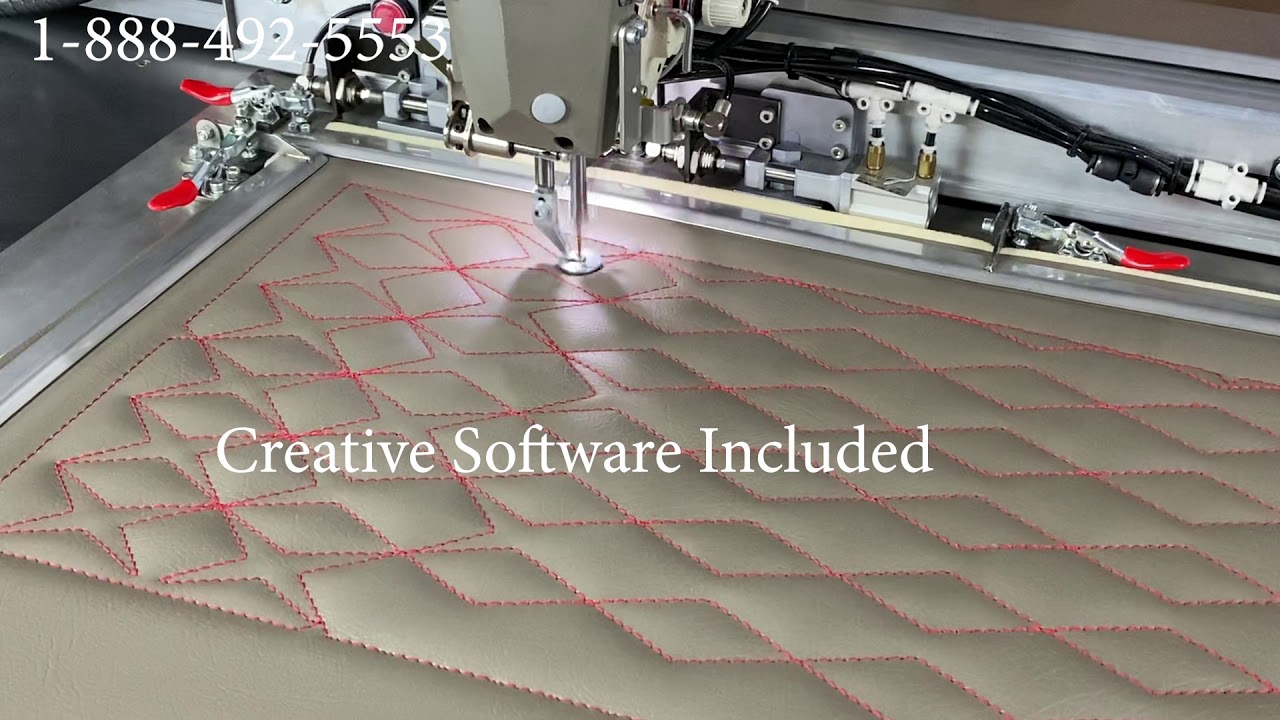
Illustrative Image (Source: Google Search)
-
Labor: Labor costs vary significantly depending on the manufacturing location. Countries with lower labor costs may offer more competitive pricing, but it’s essential to consider the trade-off in terms of skill level and quality.
-
Manufacturing Overhead: This encompasses indirect costs such as utilities, rent, and administrative expenses. Overhead can vary widely based on the supplier’s operational efficiency and location.
-
Tooling: The cost of tooling can be substantial, especially for custom CNC machines. These costs should be factored into the total procurement budget, particularly if the buyer requires specialized features.
-
Quality Control (QC): Rigorous QC processes are essential for ensuring machine reliability and performance. Buyers should account for these costs, which can be higher for suppliers that adhere to international quality standards.
-
Logistics: Shipping and handling costs are critical, particularly for international buyers. This includes freight charges, insurance, and potential tariffs or customs duties, which can add to the overall cost.
-
Margin: Suppliers typically include a profit margin in their pricing, which can vary based on market competition and demand dynamics. Understanding the average margins in different regions can aid in negotiation.
Price Influencers
-
Volume/MOQ: The minimum order quantity (MOQ) often influences pricing. Larger orders typically yield better pricing per unit due to economies of scale.
-
Specifications/Customization: Custom features or specifications can lead to higher costs. Buyers should clearly define their requirements to avoid unexpected expenses.
-
Materials and Quality Certifications: The choice of materials and adherence to international quality certifications (like ISO) can significantly influence pricing. Higher quality materials typically command a premium.
-
Supplier Factors: The supplier’s reputation, experience, and production capabilities can affect pricing. Established suppliers with a track record may charge more but often provide better reliability.
-
Incoterms: Understanding Incoterms is crucial for international transactions. They dictate the responsibilities of buyers and sellers regarding shipping, insurance, and tariffs, impacting the total landed cost.
Buyer Tips
-
Negotiation: Engage suppliers in negotiations to secure better pricing. Understanding the cost structure can provide leverage, especially if you’re placing large orders or have multiple sourcing options.
-
Cost-Efficiency: Focus on suppliers that offer a balance between cost and quality. Sometimes, the cheapest option may lead to higher long-term costs due to lower reliability or higher maintenance needs.
-
Total Cost of Ownership (TCO): Evaluate the TCO, which includes purchase price, operational costs, maintenance, and potential downtime. A higher initial investment may lead to lower TCO if the machine is more efficient.
-
Pricing Nuances: Be aware that pricing can vary significantly based on geographic location. For instance, suppliers in Europe may have higher prices due to labor and overhead costs, while those in South America might offer competitive rates but could lack certain certifications.
Disclaimer
Prices for CNC stitching machines can fluctuate based on various factors, including market conditions and supplier capabilities. It is advisable for buyers to conduct thorough market research and request multiple quotes to gain a comprehensive understanding of the current pricing landscape.
Spotlight on Potential cnc stitching machine Manufacturers and Suppliers
This section looks at several manufacturers active in the ‘cnc stitching machine’ market. This is a representative sample for illustrative purposes; B2B buyers must conduct extensive due diligence before any transaction. Information is synthesized from public sources and general industry knowledge.
Essential Technical Properties and Trade Terminology for cnc stitching machine
When considering a CNC stitching machine, understanding its essential technical properties and trade terminology is crucial for making informed purchasing decisions. This guide highlights key specifications and industry jargon that will aid international B2B buyers from regions such as Africa, South America, the Middle East, and Europe.
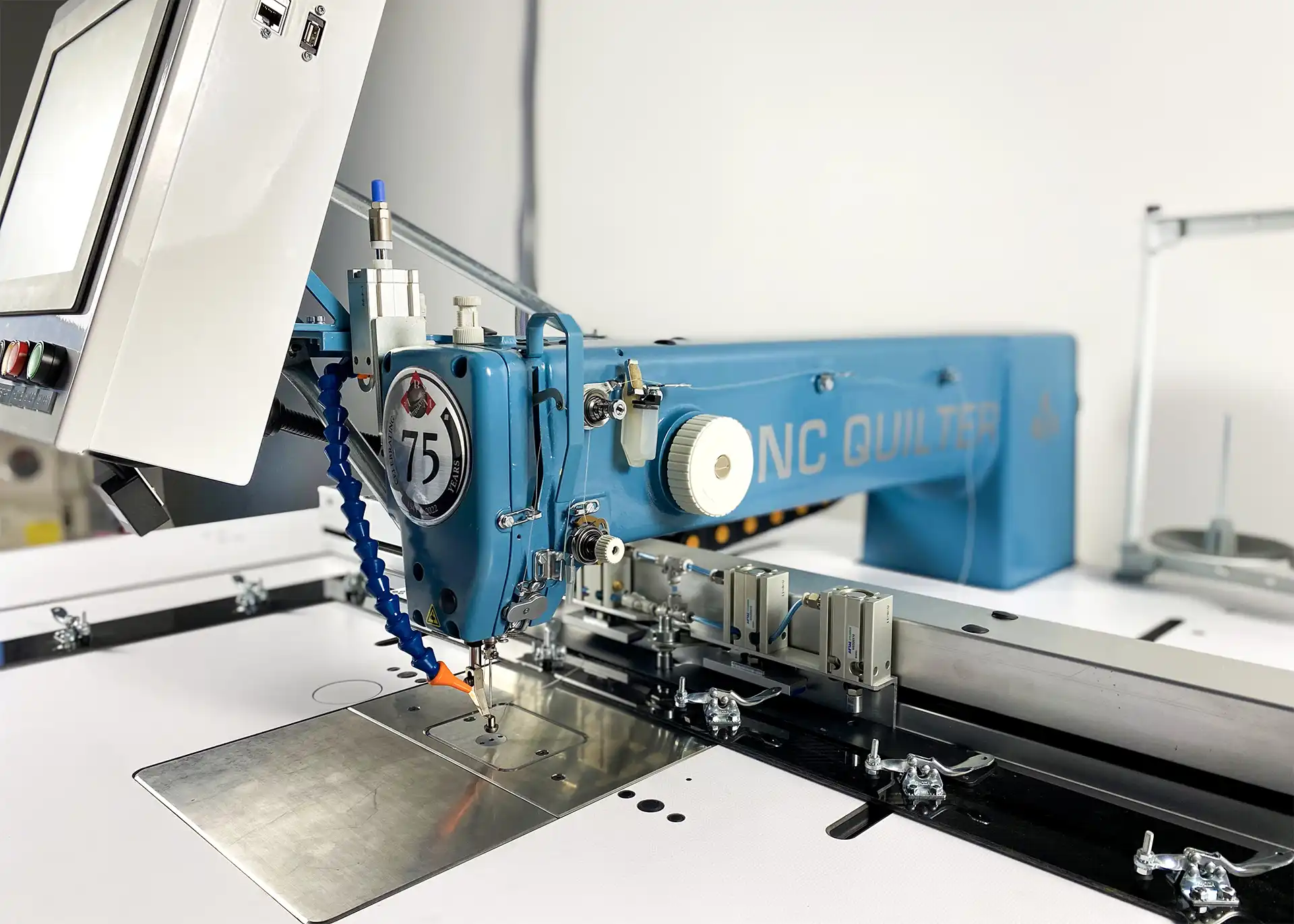
Illustrative Image (Source: Google Search)
Key Technical Properties
-
Material Grade
– Definition: Refers to the quality and type of materials used in the machine’s construction, such as aluminum, steel, or composites.
– B2B Importance: A higher material grade typically indicates better durability and performance, which can lead to lower maintenance costs and longer machine life. Buyers should assess their operational environment to choose a machine with appropriate material properties. -
Tolerance
– Definition: The allowable deviation from a specified measurement or dimension in the stitching process.
– B2B Importance: Tight tolerances ensure precision in stitching, which is critical for industries like automotive and aerospace. Buyers should evaluate the tolerance levels required for their applications to ensure product quality and compliance with industry standards. -
Stitching Speed
– Definition: The speed at which the machine can operate, usually measured in stitches per minute (SPM).
– B2B Importance: Higher stitching speeds can significantly increase production efficiency. Understanding the required speed for specific applications helps buyers choose machines that meet their production demands without sacrificing quality. -
Control System
– Definition: The technology used to operate the machine, which can be manual, semi-automated, or fully automated (CNC).
– B2B Importance: Advanced control systems can enhance precision and reduce labor costs. Buyers should consider the level of automation that aligns with their operational capabilities and workforce skills. -
Thread Compatibility
– Definition: The types and sizes of threads that the machine can effectively use.
– B2B Importance: Compatibility with various thread types can expand the range of applications for the stitching machine. Buyers should ensure that the machine can accommodate the specific threads used in their products. -
Power Consumption
– Definition: The amount of energy required for the machine to operate effectively.
– B2B Importance: Understanding power consumption is essential for cost management. Machines with lower energy requirements can lead to significant savings over time, making them more appealing for budget-conscious buyers.
Common Trade Terminology
-
OEM (Original Equipment Manufacturer)
– Definition: A company that produces parts or equipment that may be marketed by another manufacturer.
– Importance: Understanding OEM relationships is vital for buyers seeking quality components and machines. It can impact warranty, support, and overall product quality. -
MOQ (Minimum Order Quantity)
– Definition: The smallest quantity of a product that a supplier is willing to sell.
– Importance: Knowing the MOQ helps buyers plan their purchases and manage inventory levels. Negotiating MOQs can also lead to better pricing for larger orders. -
RFQ (Request for Quotation)
– Definition: A document sent to suppliers requesting pricing and other details for specific products or services.
– Importance: Submitting an RFQ allows buyers to compare offers from multiple suppliers, ensuring they get the best value for their investment. -
Incoterms (International Commercial Terms)
– Definition: A set of rules that define the responsibilities of buyers and sellers in international transactions.
– Importance: Familiarity with Incoterms helps buyers understand shipping costs, risks, and responsibilities, which can affect pricing and delivery timelines. -
Lead Time
– Definition: The total time taken from placing an order until the product is delivered.
– Importance: Knowing the lead time is essential for planning and inventory management. Buyers should factor this into their project timelines to avoid delays. -
Warranty Period
– Definition: The duration during which a manufacturer guarantees the performance of their machine.
– Importance: A longer warranty period can indicate confidence in the product quality. Buyers should review warranty terms to understand coverage and potential liabilities.
By familiarizing themselves with these essential technical properties and trade terms, international B2B buyers can make more informed decisions when sourcing CNC stitching machines, ultimately leading to better investment outcomes and operational efficiency.
Navigating Market Dynamics, Sourcing Trends, and Sustainability in the cnc stitching machine Sector
Market Overview & Key Trends
The CNC stitching machine sector is experiencing significant transformation driven by various global factors. The rise of automation and Industry 4.0 technologies is reshaping manufacturing processes, increasing efficiency, and enhancing product quality. For international B2B buyers, particularly in Africa, South America, the Middle East, and Europe, this evolution presents an opportunity to leverage advanced machinery for competitive advantage. Key trends include the integration of IoT capabilities, allowing for real-time monitoring and predictive maintenance, which reduces downtime and operational costs.
In addition, the demand for customization and small batch production is on the rise. Companies are increasingly seeking CNC stitching machines that offer flexibility and versatility, enabling them to respond swiftly to market changes. This trend is particularly relevant for buyers in regions like Mexico and France, where fashion and textile industries are vibrant and require rapid adaptation to consumer preferences. Moreover, sustainability is becoming a critical consideration, with manufacturers focusing on energy-efficient machines and processes that minimize waste.
Another noteworthy development is the shift towards digital sourcing platforms, which facilitate easier access to suppliers and enable buyers to compare products and prices from around the globe. This trend is particularly beneficial for international B2B buyers who can now explore diverse sourcing options without geographical constraints. Understanding these dynamics is essential for making informed purchasing decisions and optimizing supply chain strategies.
Sustainability & Ethical Sourcing in B2B
As environmental concerns escalate, sustainability has emerged as a key priority within the CNC stitching machine sector. Buyers are increasingly scrutinizing the environmental impact of their sourcing decisions, which includes evaluating the energy consumption and carbon footprint of manufacturing processes. Machines that utilize energy-efficient technologies not only reduce operational costs but also align with the growing demand for sustainable practices.
The importance of ethical supply chains cannot be overstated. B2B buyers are encouraged to partner with manufacturers who adhere to ethical labor practices and demonstrate transparency in their operations. This includes evaluating suppliers’ compliance with labor laws and their commitment to fair trade principles.
Moreover, certifications such as ISO 14001 (Environmental Management) and Oeko-Tex Standard 100 (Textile Safety) are becoming crucial for demonstrating a commitment to sustainability. Buyers should prioritize sourcing CNC stitching machines that are produced using eco-friendly materials and processes, as these not only contribute to environmental conservation but also enhance brand reputation among environmentally conscious consumers.
Brief Evolution/History
The CNC stitching machine has evolved significantly since its inception in the late 20th century. Initially, these machines were primarily used in large-scale production settings, offering limited flexibility. However, advancements in technology have revolutionized their capabilities, making them more accessible and adaptable for various industries, including fashion, automotive, and upholstery.
The introduction of computer numerical control (CNC) technology allowed for precise stitching patterns and automation of repetitive tasks, significantly improving efficiency and reducing labor costs. In recent years, the focus has shifted towards integrating smart technologies, such as AI and IoT, further enhancing operational capabilities. For B2B buyers, understanding this evolution is essential, as it highlights the importance of investing in modern CNC stitching machines that can meet current market demands while preparing for future challenges.
Related Video: International Trade Explained
Frequently Asked Questions (FAQs) for B2B Buyers of cnc stitching machine
-
What criteria should I use to vet suppliers of CNC stitching machines?
When vetting suppliers, focus on several key criteria: experience and expertise, manufacturing capabilities, and reputation. Research their history in the industry, production capacity, and technological advancements. Verify client testimonials and case studies that demonstrate their reliability. Additionally, look for industry certifications (like ISO) that indicate adherence to quality standards. Engaging with suppliers through trade shows or industry forums can also provide insights into their credibility and customer service. -
Can CNC stitching machines be customized to meet specific production needs?
Yes, many suppliers offer customization options to tailor CNC stitching machines to your specific production requirements. Before engaging a supplier, clearly outline your needs regarding stitching patterns, materials, and production speed. Request samples or prototypes to assess the machine’s adaptability. Be prepared to discuss technical specifications, as well as any software or integration needs with existing equipment. This will ensure that the machine aligns perfectly with your operational workflow. -
What are the typical minimum order quantities (MOQs) and lead times for CNC stitching machines?
MOQs and lead times can vary significantly based on the supplier and the complexity of the machine. Generally, MOQs can range from one unit for specialized machines to several units for standard models. Lead times typically span from 4 to 12 weeks, depending on customization and production schedules. To avoid delays, confirm these details upfront and maintain open communication throughout the manufacturing process. It’s also wise to factor in additional time for shipping and customs clearance, especially when importing to regions like Africa or South America. -
What payment terms should I expect when purchasing CNC stitching machines internationally?
Payment terms can vary widely, but common practices include 30% upfront payment and the remainder upon delivery or installation. Some suppliers may offer letters of credit or escrow services to ensure security for both parties. Always negotiate terms that align with your cash flow and risk management strategies. Additionally, consider the implications of foreign exchange rates and transaction fees, as these can impact the total cost of acquisition. -
How can I ensure quality assurance and certification for the CNC stitching machines I purchase?
Request certifications that validate the machine’s quality, such as CE marking for European markets or ISO certifications. Many suppliers will provide a Quality Assurance (QA) plan that outlines their testing procedures and standards. It’s beneficial to arrange for third-party inspections or audits, especially for large orders. Additionally, inquire about warranty terms and post-sale support, as these can be indicative of the supplier’s commitment to quality and customer satisfaction. -
What logistics considerations should I be aware of when importing CNC stitching machines?
Importing CNC stitching machines involves multiple logistics considerations. Start by researching shipping options that best suit your delivery timeline and budget, including air freight for speed or sea freight for cost savings. Ensure that you understand customs regulations in your country, as well as any tariffs or import duties that may apply. Collaborating with a freight forwarder can streamline this process and help mitigate potential delays or complications at customs. -
How should I handle disputes with suppliers during the purchasing process?
To effectively manage disputes, establish clear communication channels and documentation practices from the outset. Ensure that all agreements, including specifications, timelines, and payment terms, are documented in a contract. If a dispute arises, approach the situation diplomatically, aiming for resolution through direct dialogue. Should issues persist, consider mediation or arbitration, which can be less costly than litigation. It’s also advisable to incorporate a dispute resolution clause in contracts to outline the agreed-upon process for resolving conflicts. -
What are the best practices for post-purchase support and maintenance of CNC stitching machines?
After acquiring a CNC stitching machine, prioritize establishing a maintenance schedule to ensure optimal performance. Engage the supplier for training sessions for your operators to maximize the machine’s capabilities. Inquire about ongoing technical support and availability of spare parts, as these are critical for minimizing downtime. Additionally, consider joining industry forums or user groups for shared experiences and tips on maintenance and troubleshooting, enhancing your operational knowledge and efficiency.
Important Disclaimer & Terms of Use
⚠️ Important Disclaimer
The information provided in this guide, including content regarding manufacturers, technical specifications, and market analysis, is for informational and educational purposes only. It does not constitute professional procurement advice, financial advice, or legal advice.
While we have made every effort to ensure the accuracy and timeliness of the information, we are not responsible for any errors, omissions, or outdated information. Market conditions, company details, and technical standards are subject to change.
B2B buyers must conduct their own independent and thorough due diligence before making any purchasing decisions. This includes contacting suppliers directly, verifying certifications, requesting samples, and seeking professional consultation. The risk of relying on any information in this guide is borne solely by the reader.
Strategic Sourcing Conclusion and Outlook for cnc stitching machine
In summary, the strategic sourcing of CNC stitching machines presents a significant opportunity for international B2B buyers. Key takeaways emphasize the importance of understanding regional market dynamics, evaluating supplier capabilities, and leveraging technology to enhance operational efficiency. By focusing on quality and scalability, businesses can ensure they are well-equipped to meet increasing production demands while maintaining cost-effectiveness.
Value of Strategic Sourcing: Engaging in a comprehensive sourcing strategy not only aids in risk mitigation but also fosters long-term relationships with suppliers. This is particularly crucial for buyers in Africa, South America, the Middle East, and Europe, where varying economic conditions and technological advancements can impact sourcing decisions.
Looking ahead, it is essential for B2B buyers to remain proactive and adaptable in their sourcing strategies. As global markets evolve, staying informed about emerging trends and innovations in CNC stitching technology will be vital. We encourage you to explore partnerships that align with your business objectives, and to invest in sourcing strategies that will drive growth and competitive advantage in your respective markets. Embrace this opportunity to enhance your operational capabilities and position your business for success in the dynamic landscape of CNC stitching.