Your Ultimate Guide to Sourcing Cnc Surface Grinding Machine
Introduction: Navigating the Global Market for cnc surface grinding machine
In today’s competitive manufacturing landscape, the CNC surface grinding machine has emerged as a pivotal tool for precision engineering. These machines are essential for achieving high levels of accuracy and surface finish on a variety of materials, making them indispensable in industries ranging from aerospace to automotive. As international B2B buyers increasingly seek reliable and efficient solutions, understanding the nuances of CNC surface grinding technology becomes crucial.
This comprehensive guide delves into the intricate world of CNC surface grinding machines, offering insights into various types, materials used, and manufacturing and quality control processes. It also highlights key suppliers across different regions, providing a curated overview of the market landscape. Additionally, potential cost considerations are examined, enabling buyers to make informed financial decisions that align with their operational budgets.
For buyers from regions such as Africa, South America, the Middle East, and Europe, this guide serves as a vital resource. By equipping them with knowledge about the latest technologies and market trends, it empowers these stakeholders to navigate sourcing decisions with confidence. As the global demand for precision machining continues to rise, leveraging this guide will ensure that buyers can secure the best CNC surface grinding solutions tailored to their specific needs.
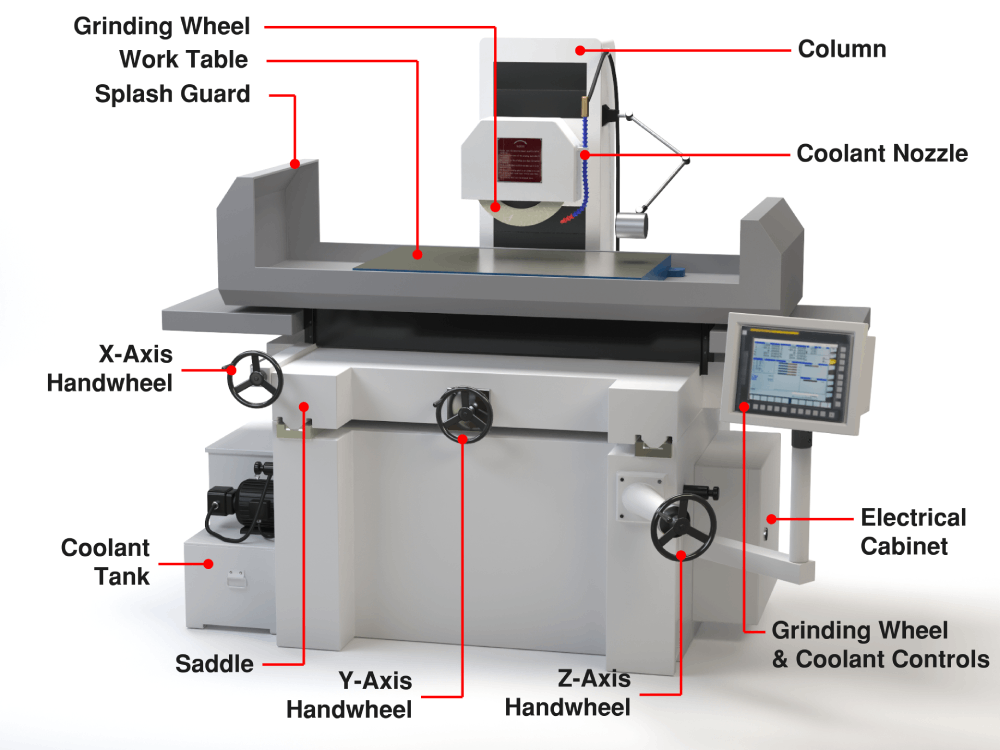
Illustrative Image (Source: Google Search)
Understanding cnc surface grinding machine Types and Variations
Type Name | Key Distinguishing Features | Primary B2B Applications | Brief Pros & Cons for Buyers |
---|---|---|---|
Horizontal CNC Surface Grinder | Flat grinding surface with a horizontal spindle | Tool and die making, precision engineering | Pros: High precision, good for larger workpieces. Cons: Requires more floor space. |
Vertical CNC Surface Grinder | Vertical spindle arrangement for compact design | Aerospace, automotive, and medical parts | Pros: Space-saving, ideal for small parts. Cons: Limited to smaller workpieces. |
CNC Rotary Surface Grinder | Features a rotating table for cylindrical parts | Manufacturing of gears, shafts, and rings | Pros: Efficient for round parts, high material removal rate. Cons: More complex setup. |
CNC Profile Grinder | Specialized for intricate shapes and profiles | Molds, dies, and complex geometries | Pros: Exceptional detail and finish quality. Cons: Higher initial investment. |
CNC Double-Sided Surface Grinder | Simultaneous grinding on both sides of a workpiece | High-volume production of flat components | Pros: Increased productivity, consistent quality. Cons: Higher operational complexity. |
Horizontal CNC Surface Grinder
Horizontal CNC surface grinders are designed with a flat grinding surface and a horizontal spindle. This configuration allows for high precision in machining larger workpieces, making it ideal for industries such as tool and die making and precision engineering. When considering a purchase, buyers should evaluate their floor space and the dimensions of their typical workpieces, as these machines require a larger footprint but offer excellent accuracy and versatility.
Vertical CNC Surface Grinder
The vertical CNC surface grinder features a vertical spindle arrangement, which allows for a more compact design, making it suitable for smaller parts. This type is widely used in sectors like aerospace and automotive for grinding intricate components. Buyers should consider their workspace constraints and the size of the parts they typically handle, as this machine excels in environments where space is limited but precision is still crucial.
CNC Rotary Surface Grinder
CNC rotary surface grinders are equipped with a rotating table that enables efficient grinding of cylindrical parts. They are particularly effective for manufacturing gears, shafts, and rings. B2B buyers should assess the complexity of their grinding tasks and the required material removal rates. While these machines provide high efficiency, the setup can be more intricate than other types, which may require specialized training for operators.
CNC Profile Grinder
CNC profile grinders are specialized machines designed for producing intricate shapes and profiles with exceptional detail. They are commonly used in the production of molds, dies, and components with complex geometries. For businesses focused on high-quality finishes and detailed work, investing in a profile grinder can yield significant benefits. However, buyers should be prepared for a higher initial investment and potentially longer setup times.
CNC Double-Sided Surface Grinder
CNC double-sided surface grinders allow for simultaneous grinding on both sides of a workpiece, significantly increasing productivity. This type is particularly beneficial for high-volume production of flat components, ensuring consistent quality and reduced cycle times. Buyers should weigh the advantages of increased output against the operational complexity and maintenance requirements, as these machines may necessitate more advanced technical support and training.
Related Video: STUDER S11 CNC Grinding Machine Configurations and Options
Key Industrial Applications of cnc surface grinding machine
Industry/Sector | Specific Application of CNC Surface Grinding Machine | Value/Benefit for the Business | Key Sourcing Considerations for this Application |
---|---|---|---|
Aerospace | Precision component manufacturing | High accuracy and surface finish for safety-critical parts | Supplier certification and compliance with aerospace standards |
Automotive | Engine component finishing | Enhanced performance and durability of engine parts | Availability of specialized grinding wheels and tooling |
Electronics | PCB and component surface preparation | Improved conductivity and performance of electronic components | Compatibility with various materials and sizes |
Tool and Die Manufacturing | Tool sharpening and maintenance | Extended tool life and reduced downtime | Precision in machine calibration and support services |
Medical Devices | Production of surgical instruments and implants | Compliance with stringent health standards | Proven track record in medical manufacturing and quality control |
Aerospace
In the aerospace industry, CNC surface grinding machines are pivotal for manufacturing precision components such as turbine blades and landing gear parts. These machines ensure high accuracy and a superior surface finish, which are essential for safety-critical applications. For international buyers, particularly in regions like Africa and the Middle East, it’s crucial to source machines that comply with aerospace standards such as AS9100. Additionally, suppliers should be certified and capable of providing documentation that attests to the quality and reliability of their equipment.
Automotive
CNC surface grinding is extensively used in the automotive sector for finishing engine components like crankshafts and camshafts. The machines enhance the performance and durability of these parts by achieving the required tolerances and surface finishes. Buyers in South America, especially in countries like Brazil and Argentina, should consider sourcing machines that offer flexibility in handling various materials, as well as those that can accommodate high production volumes without sacrificing quality.
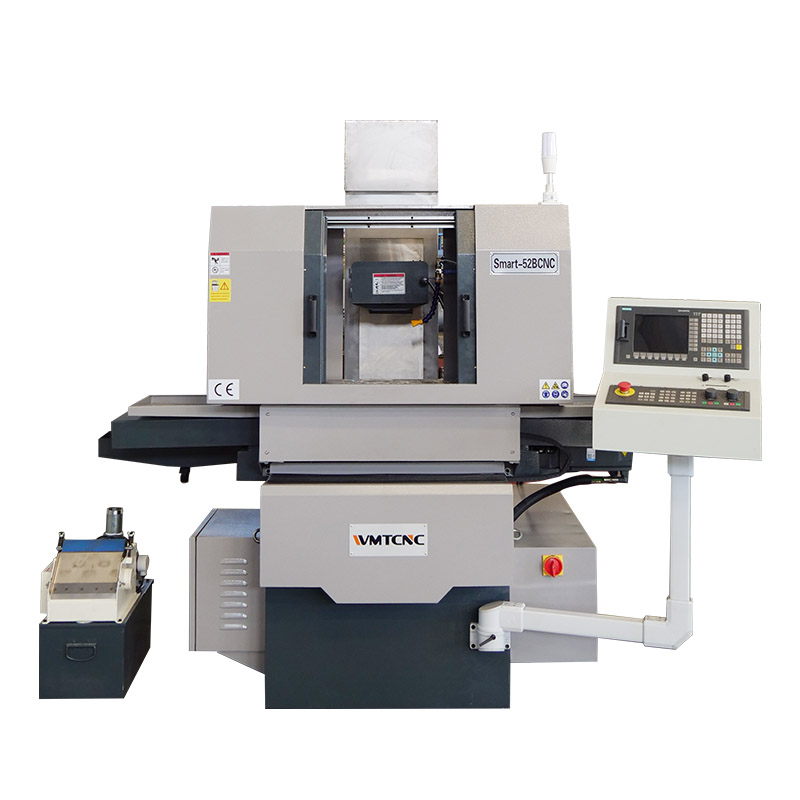
Illustrative Image (Source: Google Search)
Electronics
In the electronics industry, CNC surface grinding machines play a critical role in preparing printed circuit boards (PCBs) and other electronic components. The grinding process improves the surface characteristics, leading to better conductivity and overall performance. International buyers must ensure that the machines can handle different substrate materials and are equipped with advanced features for precision control. Additionally, sourcing from suppliers with experience in electronic applications is advisable to ensure compatibility and reliability.
Tool and Die Manufacturing
CNC surface grinding is essential in tool and die manufacturing for sharpening cutting tools and maintaining molds. This application significantly extends the life of tools and reduces downtime, which is critical for maintaining production schedules. For buyers in Europe and other regions, it is vital to source machines that offer precise calibration and robust support services to ensure optimal performance and longevity of the equipment.
Medical Devices
In the production of surgical instruments and implants, CNC surface grinding machines are used to achieve the necessary precision and compliance with stringent health standards. This application is vital for ensuring the safety and efficacy of medical devices. Buyers from Africa and the Middle East should prioritize sourcing machines from suppliers with a proven track record in the medical field, emphasizing quality control processes and certifications that meet international health regulations.
Related Video: Centerless Grinding Machine Process Animation (Parts And Functions) Surface grinding on CNC GRINDER
Strategic Material Selection Guide for cnc surface grinding machine
When selecting materials for CNC surface grinding machines, it is crucial to consider the specific properties and performance characteristics of each material. Below are analyses of four common materials used in CNC surface grinding applications, focusing on their key properties, advantages, disadvantages, and considerations for international B2B buyers.
1. High-Speed Steel (HSS)
Key Properties:
High-speed steel is known for its excellent hardness, wear resistance, and ability to maintain a sharp edge at high temperatures. It typically has a temperature rating of up to 600°C, making it suitable for high-speed applications.
Pros & Cons:
HSS offers high durability and can be ground to a fine edge, making it ideal for precision machining. However, it can be more expensive than other materials and may require more complex manufacturing processes due to its hardness.
Impact on Application:
HSS is particularly effective for grinding softer materials and can handle a range of media, including metals and plastics. It is less suitable for very hard materials, where carbide options may be preferred.
Considerations for International Buyers:
Buyers should ensure compliance with international standards such as ASTM A681 for tool steels. In regions like Africa and South America, sourcing HSS may require consideration of local suppliers’ capabilities and import regulations.
2. Carbide
Key Properties:
Carbide materials are extremely hard and can withstand high temperatures and pressures, often rated up to 1200°C. They exhibit excellent wear resistance and are less prone to deformation.
Pros & Cons:
The primary advantage of carbide is its longevity and ability to maintain precision over extended periods. However, carbide tools can be brittle and more expensive than HSS, which may lead to higher costs in case of breakage.
Impact on Application:
Carbide is well-suited for grinding hard materials, including steel and ceramics. Its hardness allows for efficient machining of tough materials, but the brittleness may limit its use in certain applications where shock resistance is critical.
Considerations for International Buyers:
Buyers should be aware of the specific grades of carbide and their applications, as different grades may comply with various international standards. For example, DIN standards in Europe and JIS standards in Japan may dictate the acceptable grades for specific applications.
3. Ceramics
Key Properties:
Ceramic materials are known for their high hardness and thermal stability, with temperature ratings exceeding 1000°C. They are also chemically inert, providing excellent corrosion resistance.
Pros & Cons:
Ceramics offer superior wear resistance and are ideal for high-speed grinding applications. However, they are generally more expensive and can be fragile, making them less suitable for applications involving heavy impacts.
Impact on Application:
Ceramics are particularly effective for grinding hard materials like hardened steel and composites. Their chemical inertness allows for compatibility with various media, including corrosive substances.
Considerations for International Buyers:
International buyers must consider the availability of ceramic materials in their regions, as sourcing can be limited. Compliance with local and international standards is essential, especially in industries with strict regulations, such as aerospace and automotive.
4. Aluminum Oxide
Key Properties:
Aluminum oxide is a versatile abrasive material known for its hardness and thermal stability. It can withstand temperatures up to 2000°C and is often used in various grinding applications.
Pros & Cons:
Aluminum oxide is cost-effective and widely available, making it a popular choice for many applications. However, its wear resistance is lower compared to carbide and ceramics, which may lead to more frequent tool replacements.
Impact on Application:
This material is suitable for grinding a variety of metals and is particularly effective for softer materials. Its affordability makes it attractive for high-volume applications, but it may not provide the precision required for high-tolerance work.
Considerations for International Buyers:
Buyers should evaluate the local market for aluminum oxide abrasives and ensure compliance with relevant standards, such as ISO 9001 for quality management. Understanding the specific needs of their operations will help in selecting the right grade and type.
Summary Table
Material | Typical Use Case for cnc surface grinding machine | Key Advantage | Key Disadvantage/Limitation | Relative Cost (Low/Med/High) |
---|---|---|---|---|
High-Speed Steel | Precision machining of softer metals | Excellent edge retention | Higher manufacturing complexity | Medium |
Carbide | Grinding hard materials like steel and ceramics | Exceptional wear resistance | Brittle, higher cost | High |
Ceramics | High-speed grinding of hard materials | Superior thermal stability | Expensive, fragile | High |
Aluminum Oxide | Grinding softer metals and general applications | Cost-effective and widely available | Lower wear resistance | Low |
This strategic material selection guide provides valuable insights for international B2B buyers, helping them make informed decisions based on material properties, application suitability, and compliance considerations.
In-depth Look: Manufacturing Processes and Quality Assurance for cnc surface grinding machine
Manufacturing Processes for CNC Surface Grinding Machines
The manufacturing of CNC surface grinding machines is a complex process that requires precision engineering and adherence to strict quality standards. Understanding these processes is vital for international B2B buyers to ensure they are sourcing high-quality machinery. Below are the main stages involved in the manufacturing process, as well as key techniques employed.
Main Stages of Manufacturing
-
Material Preparation
– Selection of Raw Materials: High-quality steel and other alloys are selected for their durability and resistance to wear. The choice of material directly impacts the machine’s performance and longevity.
– Cutting and Shaping: Raw materials are cut to specific dimensions using laser cutting or waterjet technology. This stage ensures that components are accurately sized before moving to forming. -
Forming
– Machining Processes: CNC machining centers are used to shape the components. This includes processes like milling and turning to create the intricate parts required for the grinding machine.
– Heat Treatment: Components undergo heat treatment processes to enhance their hardness and strength. This is crucial for parts that will endure high levels of stress during operation. -
Assembly
– Component Assembly: Skilled technicians assemble the various components, ensuring that tolerances and alignments are maintained. This stage often involves the use of jigs and fixtures to guarantee precision.
– Integration of Electronics: Control systems, sensors, and drives are integrated into the machine. This is where the CNC aspect comes into play, allowing for automated and precise operations. -
Finishing
– Surface Treatment: Components are subjected to surface finishing techniques such as grinding, polishing, or coating. This not only improves aesthetics but also enhances the durability and resistance to corrosion.
– Final Assembly and Calibration: The machine is fully assembled, and final calibrations are made to ensure optimal performance. This includes adjusting the grinding head and verifying the accuracy of CNC controls.
Key Techniques in Manufacturing
- CNC Machining: Utilizes computer-controlled machines to ensure high precision and repeatability in the manufacturing process.
- Additive Manufacturing: Some manufacturers are beginning to use 3D printing for prototyping and creating complex components that would be difficult to machine conventionally.
- Lean Manufacturing: Many manufacturers adopt lean principles to minimize waste and optimize efficiency throughout the production process.
Quality Assurance in CNC Surface Grinding Machines
Quality assurance is critical in ensuring that CNC surface grinding machines meet international standards and customer expectations. The following sections outline the key quality assurance practices, relevant standards, and how buyers can verify supplier quality.
International and Industry-Specific Standards
- ISO 9001: This is the most recognized quality management standard globally. Manufacturers must demonstrate their ability to provide consistent products and services that meet customer and regulatory requirements.
- CE Marking: In Europe, CE marking signifies that a product complies with EU safety, health, and environmental protection standards.
- API Certification: For manufacturers dealing with oil and gas, API certification ensures that products meet industry-specific quality and safety standards.
Quality Control Checkpoints
-
Incoming Quality Control (IQC)
– All raw materials and components are inspected upon arrival. This includes verifying material specifications and conducting initial tests for defects. -
In-Process Quality Control (IPQC)
– Throughout the manufacturing process, regular inspections are conducted to ensure that production tolerances are maintained. This often involves real-time monitoring of machining processes. -
Final Quality Control (FQC)
– Before shipment, each machine undergoes a comprehensive inspection to verify functionality, safety, and compliance with specifications. This may include operational testing and performance assessments.
Common Testing Methods
- Dimensional Inspection: Utilizing precision measuring instruments to verify that components meet specified dimensions.
- Functional Testing: Assessing the machine’s operational capabilities, including speed, accuracy, and load-bearing capacity.
- Non-Destructive Testing (NDT): Techniques such as ultrasonic testing or X-ray inspection may be employed to identify internal flaws without damaging the components.
Verifying Supplier Quality Assurance
For international B2B buyers, especially those from Africa, South America, the Middle East, and Europe, it is essential to verify the quality assurance processes of suppliers. Here are actionable strategies:
- Conduct Audits: Schedule regular audits of potential suppliers to assess their manufacturing processes and quality control systems. This can be done through third-party auditors or independent consultants.
- Request Quality Reports: Ask suppliers to provide detailed quality assurance reports, including results from IQC, IPQC, and FQC stages.
- Engage Third-Party Inspectors: Utilizing third-party inspection services can provide an unbiased evaluation of the supplier’s quality practices. This is particularly important for large orders or critical applications.
Quality Control and Certification Nuances for International Buyers
Understanding the nuances of quality control and certification is critical for international buyers. Here are some considerations:
- Cultural Differences: Be aware that quality standards and practices may vary significantly between regions. This could affect how quality assurance is implemented and perceived.
- Regulatory Compliance: Ensure that suppliers are compliant with both local and international regulations, which may differ from the buyer’s home country.
- Language Barriers: Documentation and communication regarding quality control measures may be in a different language. It is advisable to have bilingual representatives to facilitate clear communication.
By understanding the manufacturing processes and quality assurance practices for CNC surface grinding machines, international B2B buyers can make informed decisions, ensuring they partner with reliable suppliers that meet their quality standards.
Comprehensive Cost and Pricing Analysis for cnc surface grinding machine Sourcing
When sourcing CNC surface grinding machines, understanding the comprehensive cost structure and pricing dynamics is essential for international B2B buyers, especially from diverse regions like Africa, South America, the Middle East, and Europe. This analysis provides insights into the various cost components, price influencers, and buyer tips that can significantly impact sourcing decisions.
Cost Components
-
Materials: The primary raw materials for CNC surface grinding machines include high-grade steel, aluminum, and various electronic components. The quality of these materials directly affects machine durability and performance, which in turn impacts the overall cost.
-
Labor: Labor costs vary significantly by region. For manufacturers in countries with higher labor costs (e.g., parts of Europe), the price of CNC machines may be higher. Conversely, manufacturers in regions with lower labor costs can offer competitive pricing but may compromise on quality or support services.
-
Manufacturing Overhead: This includes costs related to factory operations, utilities, and administrative expenses. Effective management of overhead can lead to more competitive pricing for buyers.
-
Tooling: Specialized tooling is often required for manufacturing CNC machines, which adds to the upfront costs. Buyers should inquire about the tooling lifespan and replacement costs to gauge long-term expenses.
-
Quality Control (QC): Rigorous QC processes ensure that machines meet industry standards. While this adds to the cost, it is essential for reliability and performance, particularly for precision applications.
-
Logistics: Transportation costs can fluctuate based on shipping methods, distances, and customs duties. Understanding the logistics involved can help buyers estimate total costs more accurately.
-
Margin: Supplier margins can vary based on the manufacturer’s brand reputation, market demand, and competitive landscape. Established brands may command higher prices due to perceived value and support services.
Price Influencers
-
Volume/MOQ (Minimum Order Quantity): Bulk purchases often lead to discounts. Buyers should negotiate terms that favor larger orders when possible.
-
Specifications/Customization: Tailoring machines to specific needs can increase costs. Standard models may offer cost savings, but ensure they meet operational requirements.
-
Materials Quality/Certifications: Higher quality materials and certifications (like ISO) can lead to increased costs but are critical for ensuring machine reliability and compliance with industry standards.
-
Supplier Factors: The supplier’s location, reputation, and support capabilities can influence pricing. Buyers should assess suppliers based on their service offerings and post-sale support.
-
Incoterms: The chosen Incoterms (International Commercial Terms) affect shipping responsibilities and costs. Understanding these terms can help buyers manage risks and expenses effectively.
Buyer Tips
-
Negotiation: Leverage multiple supplier quotes to negotiate better pricing and terms. Highlighting potential long-term partnerships can also be beneficial.
-
Cost-Efficiency: Consider the Total Cost of Ownership (TCO), which includes initial purchase price, maintenance, and operational costs. A cheaper machine may lead to higher long-term costs due to frequent repairs or inefficiencies.
-
Pricing Nuances: Be aware of regional pricing differences. Suppliers in emerging markets may offer lower prices, but assess the trade-offs in quality and support.
-
Documentation and Compliance: Ensure all necessary documentation (like warranties and service agreements) is clear to avoid unexpected costs later.
Disclaimer
Prices for CNC surface grinding machines are indicative and can vary based on market conditions, supplier negotiations, and specific machine configurations. Always consult multiple sources and perform due diligence when making purchasing decisions.
Spotlight on Potential cnc surface grinding machine Manufacturers and Suppliers
This section looks at several manufacturers active in the ‘cnc surface grinding machine’ market. This is a representative sample for illustrative purposes; B2B buyers must conduct extensive due diligence before any transaction. Information is synthesized from public sources and general industry knowledge.
Essential Technical Properties and Trade Terminology for cnc surface grinding machine
Key Technical Properties of CNC Surface Grinding Machines
Understanding the essential technical properties of CNC surface grinding machines is crucial for B2B buyers, particularly when evaluating potential suppliers and making informed purchasing decisions. Here are the key specifications:
-
Material Grade
– Definition: The type of material used in the construction of the grinding machine, often steel or cast iron.
– Importance: High-quality materials ensure durability and longevity, minimizing maintenance costs. Buyers should assess the material grade to ensure that the machine can withstand operational stresses and maintain precision. -
Grinding Wheel Size
– Definition: The diameter and thickness of the grinding wheel used in the machine.
– Importance: The size affects the machine’s capability to grind different workpiece dimensions. A larger wheel can accommodate larger parts and provide a more extensive surface area for grinding, which can enhance efficiency. -
Tolerance
– Definition: The permissible limit of variation in a physical dimension, typically expressed in microns (µm).
– Importance: Tight tolerances are essential in precision machining. Understanding the tolerance specifications of a CNC surface grinding machine helps buyers ensure that their products meet industry standards and customer expectations. -
Feed Rate
– Definition: The speed at which the workpiece is fed into the grinding wheel, usually measured in mm/min.
– Importance: The feed rate impacts the quality of the surface finish and the overall machining efficiency. Buyers should evaluate this specification based on their production needs to optimize throughput without compromising quality. -
Power Consumption
– Definition: The amount of electrical power required for the machine to operate, typically measured in kilowatts (kW).
– Importance: Understanding power consumption is vital for cost analysis and energy efficiency. Machines with lower power consumption can lead to reduced operational costs, which is particularly important for businesses in regions with high energy prices. -
Control System
– Definition: The software and hardware that govern the operation of the CNC machine, often including a user interface for programming and monitoring.
– Importance: An advanced control system enhances automation, precision, and ease of use. Buyers should consider the type of control system when evaluating machine capabilities, as a user-friendly interface can significantly reduce training time and operational errors.
Common Trade Terminology
In addition to technical specifications, familiarity with industry jargon is essential for effective communication and negotiation. Here are some common terms:
-
OEM (Original Equipment Manufacturer)
– Definition: A company that produces parts or equipment that may be marketed by another manufacturer.
– Importance: Understanding OEM relationships can help buyers identify reputable suppliers and ensure the quality of replacement parts and service. -
MOQ (Minimum Order Quantity)
– Definition: The smallest quantity of a product that a supplier is willing to sell.
– Importance: Knowing the MOQ helps buyers assess budget constraints and inventory needs. It can also influence purchasing strategies, particularly for smaller companies. -
RFQ (Request for Quotation)
– Definition: A document sent to suppliers requesting a price quote for specific products or services.
– Importance: RFQs are essential for comparing prices and terms from multiple suppliers, facilitating better negotiation and decision-making. -
Incoterms (International Commercial Terms)
– Definition: A set of rules that define the responsibilities of buyers and sellers in international transactions.
– Importance: Familiarity with Incoterms helps buyers understand shipping responsibilities, risk management, and cost implications, which are crucial for cross-border trade. -
Lead Time
– Definition: The time taken from placing an order to the delivery of the product.
– Importance: Knowing the lead time is crucial for planning production schedules and inventory management, especially in industries with tight deadlines. -
Calibration
– Definition: The process of adjusting the precision of a machine to ensure accurate measurements.
– Importance: Regular calibration is vital for maintaining machine accuracy and quality. Buyers should inquire about calibration services when selecting suppliers to ensure ongoing precision in operations.
Understanding these technical properties and trade terms can significantly enhance the purchasing process for CNC surface grinding machines, enabling buyers to make informed decisions that align with their operational needs and business goals.
Navigating Market Dynamics, Sourcing Trends, and Sustainability in the cnc surface grinding machine Sector
Market Overview & Key Trends
The global market for CNC surface grinding machines is witnessing significant growth, driven by advancements in manufacturing technologies and the increasing demand for precision-engineered components. Key trends influencing this market include automation, integration of Industry 4.0 technologies, and the growing importance of high-quality surface finishes in various industries such as aerospace, automotive, and electronics. For international B2B buyers, particularly in regions like Africa, South America, the Middle East, and Europe, understanding these dynamics is crucial for making informed sourcing decisions.
Emerging technologies such as Artificial Intelligence (AI) and the Internet of Things (IoT) are reshaping the CNC grinding landscape. These innovations enhance machine performance, predictive maintenance, and operational efficiency, reducing downtime and operational costs. Buyers are encouraged to seek suppliers that offer machines with integrated smart technologies for improved productivity. Additionally, the rise of e-commerce platforms is facilitating easier access to global suppliers, allowing businesses in emerging markets to source high-quality CNC machines more efficiently.
Another noteworthy trend is the growing emphasis on customization and flexibility in CNC surface grinding solutions. Manufacturers are increasingly offering modular systems that can be tailored to specific production needs, allowing businesses to adapt quickly to changing market demands. This flexibility is particularly advantageous for companies in regions with diverse manufacturing requirements, such as Brazil and Argentina, where local industries are rapidly evolving.
Sustainability & Ethical Sourcing in B2B
Sustainability has become a pivotal concern in the CNC surface grinding machine sector, driven by both regulatory pressures and consumer demand for environmentally responsible practices. The environmental impact of manufacturing processes, including energy consumption and waste generation, necessitates a shift towards more sustainable operations. B2B buyers should prioritize suppliers that adhere to eco-friendly practices, such as energy-efficient machine designs and waste reduction strategies.
Ethical sourcing is equally important, as businesses increasingly recognize the value of transparent supply chains. Buyers should investigate potential suppliers’ sourcing practices, ensuring they comply with labor and environmental standards. Certifications such as ISO 14001 for environmental management and ISO 45001 for occupational health and safety can serve as indicators of a supplier’s commitment to sustainability.
Moreover, the adoption of ‘green’ materials and technologies is gaining traction. Suppliers that utilize recycled components or sustainable manufacturing processes not only enhance their environmental credentials but also appeal to buyers looking to bolster their own sustainability initiatives. For companies in regions like the Middle East and Africa, where resource scarcity can be a concern, sourcing machines that prioritize sustainability can lead to long-term operational benefits.
Brief Evolution/History
The CNC surface grinding machine has evolved significantly since its inception in the mid-20th century. Initially, grinding processes were manual and labor-intensive, limiting precision and efficiency. The introduction of CNC technology revolutionized the industry, allowing for automated and highly precise grinding operations. As the technology advanced, features such as programmable controls and real-time monitoring were integrated, enabling manufacturers to achieve unprecedented levels of accuracy and repeatability.
Today, the focus has shifted towards smart manufacturing solutions, where CNC surface grinding machines are part of interconnected systems that enhance overall productivity. This evolution reflects the broader trends in manufacturing, where efficiency, sustainability, and technological integration are paramount. For B2B buyers, understanding this historical context can provide valuable insights into the capabilities and future developments of CNC surface grinding technologies.
Frequently Asked Questions (FAQs) for B2B Buyers of cnc surface grinding machine
-
How can I effectively vet suppliers of CNC surface grinding machines?
Vetting suppliers is crucial for ensuring quality and reliability. Start by checking their industry experience and reputation through online reviews and testimonials. Request references from previous clients, and verify their business credentials. Additionally, assess their manufacturing capabilities by requesting a factory visit or virtual tour. Ensure they have necessary certifications, such as ISO standards, which indicate adherence to quality management systems. Lastly, inquire about their after-sales support and warranty policies to gauge their commitment to customer satisfaction. -
Can CNC surface grinding machines be customized to meet my specific requirements?
Yes, many manufacturers offer customization options for CNC surface grinding machines. When discussing your needs, provide detailed specifications, such as size, material type, and desired features. It’s beneficial to collaborate closely with the supplier during the design phase to ensure the machine meets your operational requirements. Be aware that customized machines may have longer lead times and higher costs, so plan accordingly and discuss any implications on your production schedule. -
What are the typical minimum order quantities (MOQs) and lead times for CNC surface grinding machines?
Minimum order quantities can vary significantly depending on the manufacturer and the complexity of the machine. Generally, for standard models, MOQs may range from one unit to several units for bulk orders. Lead times also differ based on customization and supplier location, typically ranging from 8 to 16 weeks. Always clarify these details upfront to align your production timelines and avoid unexpected delays. Consider discussing expedited options if you have urgent needs. -
What payment terms are common when purchasing CNC surface grinding machines internationally?
Payment terms can vary by supplier and region, but common practices include a deposit (often 30-50%) upon order confirmation, with the balance due before shipping. Some suppliers may offer letters of credit or escrow services for additional security. It’s advisable to negotiate terms that protect both parties and ensure clarity on payment methods, currencies, and any additional fees (such as import duties). Always confirm these details in the contract to avoid disputes later. -
How do I ensure quality assurance and certifications for CNC surface grinding machines?
To ensure quality, request copies of certifications that demonstrate compliance with international standards, such as ISO 9001. Additionally, inquire about the supplier’s quality control processes, including inspections and testing methods used during production. It’s also beneficial to ask for sample products or to visit the facility for firsthand evaluation. Establishing a clear quality assurance protocol within your contract can further protect your interests and ensure the machine meets your specifications. -
What logistics considerations should I keep in mind when importing CNC surface grinding machines?
Logistics can significantly impact the timely delivery of CNC machines. First, confirm the shipping method and timelines with your supplier, considering options like sea freight for cost-effectiveness or air freight for speed. Assess the total landed cost, including shipping, insurance, and customs duties, to avoid budget overruns. Additionally, ensure your supplier provides proper documentation for customs clearance, and consider working with a freight forwarder who specializes in machinery imports to streamline the process. -
What steps should I take if a dispute arises with my CNC surface grinding machine supplier?
In the event of a dispute, start by reviewing your contract to understand the terms agreed upon. Communicate directly with the supplier to express your concerns and seek a resolution. Document all interactions and keep records of correspondence. If informal negotiations fail, consider mediation or arbitration, as outlined in your contract. Engaging legal counsel familiar with international trade can provide additional support and guidance in navigating complex disputes. -
How can I assess the long-term support and service options from a CNC surface grinding machine supplier?
Assessing long-term support begins with understanding the supplier’s service offerings, such as maintenance, training, and technical support. Inquire about their response times for service requests and the availability of spare parts. A reliable supplier should provide a comprehensive warranty and clearly outline terms for repairs and replacements. Additionally, ask for customer feedback on their service experience to gauge satisfaction levels and ensure you have a partner capable of supporting your operations over time.
Important Disclaimer & Terms of Use
⚠️ Important Disclaimer
The information provided in this guide, including content regarding manufacturers, technical specifications, and market analysis, is for informational and educational purposes only. It does not constitute professional procurement advice, financial advice, or legal advice.
While we have made every effort to ensure the accuracy and timeliness of the information, we are not responsible for any errors, omissions, or outdated information. Market conditions, company details, and technical standards are subject to change.
B2B buyers must conduct their own independent and thorough due diligence before making any purchasing decisions. This includes contacting suppliers directly, verifying certifications, requesting samples, and seeking professional consultation. The risk of relying on any information in this guide is borne solely by the reader.
Strategic Sourcing Conclusion and Outlook for cnc surface grinding machine
In conclusion, the strategic sourcing of CNC surface grinding machines offers international B2B buyers a pathway to enhanced operational efficiency and competitive advantage. By prioritizing quality, supplier reliability, and technological advancements, organizations can significantly improve their manufacturing processes. The benefits of adopting CNC surface grinding technology include increased precision, reduced lead times, and the ability to handle complex geometries that traditional methods cannot achieve.
For buyers in Africa, South America, the Middle East, and Europe, understanding the regional dynamics and supplier landscapes is crucial. Engaging with local and international suppliers who offer robust support and customization options will empower businesses to meet specific market demands effectively. Furthermore, establishing long-term relationships with trusted suppliers can facilitate better pricing strategies and access to the latest innovations.
As the industry continues to evolve, now is the time for B2B buyers to invest in strategic sourcing. This proactive approach will not only safeguard current operations but also position businesses for future growth and resilience in an increasingly competitive landscape. Embrace the opportunities that CNC surface grinding machines present, and take decisive action to enhance your manufacturing capabilities today.