Your Ultimate Guide to Sourcing Cnc Welding Machine
Introduction: Navigating the Global Market for cnc welding machine
Precision and efficiency are paramount in today’s global manufacturing landscape, and CNC (Computer Numerical Control) welding machines play a crucial role in achieving these goals. As industries across Africa, South America, the Middle East, and Europe strive to enhance productivity and maintain competitive advantages, CNC welding technology emerges as a vital investment. These machines not only streamline the welding process but also ensure consistent quality, reducing labor costs and material waste while increasing throughput.
This comprehensive guide serves as an essential resource for international B2B buyers looking to navigate the complexities of sourcing CNC welding machines. It covers various machine types, including robotic welders, TIG, MIG, and spot welding systems, tailored to specific applications and materials. The guide also delves into manufacturing and quality control best practices, providing insights into compatible materials and compliance standards essential for operational success.
Moreover, buyers will find critical information on selecting reliable suppliers, understanding pricing models, and analyzing the broader CNC welding market landscape. Addressing common queries and concerns, this guide empowers procurement professionals with actionable insights to make informed decisions. By leveraging this knowledge, businesses can enhance their operational capabilities, ensure return on investment, and drive growth in diverse markets, ultimately positioning themselves for success in a competitive global environment.
Understanding cnc welding machine Types and Variations
Type Name | Key Distinguishing Features | Primary B2B Applications | Brief Pros & Cons for Buyers |
---|---|---|---|
MIG (Metal Inert Gas) Welder | Uses a continuous wire feed and inert gas for shielding | Automotive, construction, and fabrication | Fast welding speed; less effective for thicker materials. |
TIG (Tungsten Inert Gas) Welder | Provides precise control with a non-consumable tungsten electrode | Aerospace, piping, and art metalwork | High-quality welds; slower process requiring skilled operators. |
Spot Welder | Joins metal sheets by applying heat and pressure at specific points | Automotive assembly and HVAC systems | High efficiency for mass production; limited to sheet metal. |
Laser Welding Machine | Uses focused laser beams to melt and join materials | Electronics, medical devices, and aerospace | Exceptional precision; high setup costs and requires skilled labor. |
Plasma Arc Welder | Utilizes plasma to create a high-temperature arc for welding | Heavy machinery and shipbuilding | Effective for thick materials; higher operational costs. |
MIG (Metal Inert Gas) Welder
MIG welding is favored for its speed and versatility, making it ideal for applications in automotive and construction sectors. This method uses a continuous wire feed and an inert gas shield, which protects the weld pool from contamination. B2B buyers should consider the machine’s duty cycle, wire feed speed, and compatibility with various materials. While MIG welding is efficient, it may not be suitable for thicker materials, requiring buyers to evaluate their specific welding needs and production volumes.
TIG (Tungsten Inert Gas) Welder
TIG welding is known for producing high-quality, precise welds, making it a go-to choice in industries such as aerospace and piping. This technique uses a non-consumable tungsten electrode and requires more skill than MIG welding. Buyers should assess the machine’s amperage range, ease of use, and available accessories. Although TIG welding offers superior finish quality, it is slower and demands a higher level of operator expertise, which can affect training and operational costs.
Spot Welder
Spot welding is commonly used in automotive assembly and HVAC systems, where it joins overlapping metal sheets by applying localized heat and pressure. This method is highly efficient for mass production, allowing for quick and repetitive welding tasks. B2B buyers should focus on the machine’s electrode life, power output, and ease of maintenance. While spot welders are excellent for sheet metal applications, their limitations in joining thicker materials must be considered during procurement.
Laser Welding Machine
Laser welding machines utilize focused laser beams to achieve high precision in joining materials, making them suitable for applications in electronics and aerospace. This method offers exceptional control over the weld pool, resulting in minimal thermal distortion. Buyers should evaluate the machine’s power settings, material compatibility, and the need for skilled operators. While laser welding provides unparalleled accuracy, the initial setup costs and operational requirements can be significant, necessitating a thorough cost-benefit analysis.
Plasma Arc Welder
Plasma arc welding is effective for working with thick materials, making it ideal for heavy machinery and shipbuilding applications. This technique employs a high-temperature arc created by ionizing gas, allowing for deep penetration and strong welds. B2B buyers should consider the machine’s power capacity, arc stability, and consumable costs. Although plasma welding can handle demanding projects, the higher operational costs and potential need for specialized training should be factored into purchasing decisions.
Related Video: CNC machining – What is it and How Does it Work? (Must Know Basics)
Key Industrial Applications of cnc welding machine
Industry/Sector | Specific Application of cnc welding machine | Value/Benefit for the Business | Key Sourcing Considerations for this Application |
---|---|---|---|
Automotive | Frame and chassis assembly | Enhanced precision and structural integrity | Compatibility with various materials; support for complex geometries |
Construction | Steel structure fabrication | Faster assembly and reduced labor costs | Durability of equipment; local technical support availability |
Aerospace | Component welding for aircraft | High-strength joints for safety and performance | Compliance with stringent industry standards; skilled operator training |
Oil & Gas | Pipeline and equipment fabrication | Improved efficiency and reduced downtime | Resistance to harsh environments; after-sales service reliability |
Heavy Machinery | Assembly of large machinery components | Increased productivity and reduced waste | Machine size and capacity; sourcing of spare parts and maintenance support |
Automotive
In the automotive industry, CNC welding machines are crucial for assembling frames and chassis, where precision and structural integrity are paramount. These machines allow for automated, consistent welding that meets strict safety standards, reducing the risk of human error. For international buyers, particularly from emerging markets, sourcing machines that can handle diverse materials and complex geometries is essential. Additionally, ensuring access to local training and support services can facilitate smoother integration into existing workflows.
Construction
CNC welding machines play a significant role in the fabrication of steel structures used in construction projects. By automating the welding process, businesses can achieve faster assembly times and lower labor costs, which is vital for meeting project deadlines. Buyers should consider the durability of the equipment to withstand harsh working conditions and assess the availability of local technical support. This is especially important in regions where skilled labor may be limited, ensuring that operations can continue without interruption.
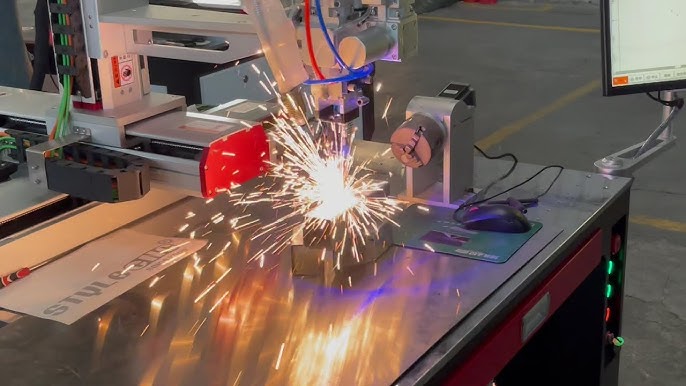
Illustrative Image (Source: Google Search)
Aerospace
In the aerospace sector, CNC welding machines are employed to create high-strength joints in aircraft components. The precision offered by these machines is critical, as even minor imperfections can compromise safety and performance. B2B buyers must prioritize sourcing machines that comply with stringent aerospace standards, ensuring that they can produce parts that meet regulatory requirements. Additionally, investing in skilled operator training is essential to fully leverage the capabilities of these advanced machines.
Oil & Gas
CNC welding machines are extensively used in the fabrication of pipelines and equipment in the oil and gas industry. Their ability to deliver high-quality welds quickly enhances operational efficiency and minimizes downtime during critical projects. Buyers should focus on sourcing machines that are resistant to harsh environments and can handle various materials typically used in the sector. Furthermore, establishing a reliable after-sales service is crucial for maintaining equipment and ensuring long-term operational success.
Heavy Machinery
In heavy machinery manufacturing, CNC welding machines are integral to assembling large components. These machines boost productivity by allowing for precise, repeatable welds, which reduces material waste and enhances overall production efficiency. When sourcing, buyers should evaluate the machine’s size and capacity to ensure it meets their specific production needs. Additionally, the availability of spare parts and maintenance support is essential to avoid operational disruptions, particularly in regions with limited access to technical resources.
Strategic Material Selection Guide for cnc welding machine
When selecting materials for CNC welding machines, understanding the properties and applications of various materials is crucial for international B2B buyers. This section analyzes four common materials used in CNC welding, providing insights into their performance characteristics, pros and cons, and specific considerations for buyers from diverse regions, including Africa, South America, the Middle East, and Europe.
Steel
Key Properties: Steel is known for its high tensile strength and durability, making it suitable for a wide range of applications. It typically has excellent weldability, allowing for strong joints. Depending on the alloy, steel can also exhibit varying levels of corrosion resistance.
Pros & Cons: Steel is relatively cost-effective and widely available, which makes it a popular choice for many manufacturing processes. However, its susceptibility to rust without proper treatment can be a drawback in humid or corrosive environments. The complexity of manufacturing can increase with the use of specialized alloys.
Impact on Application: Steel is compatible with various media, including gases and liquids, making it suitable for structural applications, automotive components, and machinery parts.
Considerations for Buyers: Buyers should ensure compliance with local standards such as ASTM or DIN for steel grades. Additionally, understanding the local market’s availability of specific steel types can aid in procurement efficiency.
Aluminum
Key Properties: Aluminum is lightweight, non-corrosive, and possesses good thermal and electrical conductivity. It is also known for its ability to withstand high temperatures, making it ideal for applications requiring heat resistance.
Pros & Cons: The primary advantage of aluminum is its low weight, which can enhance the performance of end products in applications such as aerospace and automotive. However, it can be more expensive than steel and may require specialized welding techniques, increasing manufacturing complexity.
Impact on Application: Aluminum’s corrosion resistance makes it suitable for outdoor applications and environments where exposure to moisture is a concern. It is often used in the production of frames, casings, and components that require a lightweight yet strong material.
Considerations for Buyers: B2B buyers should be aware of the specific aluminum alloys required for their applications and ensure that suppliers can meet these specifications. Compliance with international standards such as JIS for aluminum can also be critical.
Stainless Steel
Key Properties: Stainless steel is renowned for its exceptional corrosion resistance and high-temperature performance. It maintains structural integrity under various conditions, making it ideal for demanding environments.
Pros & Cons: While stainless steel offers superior durability and aesthetic appeal, it is generally more expensive than carbon steel and can be more challenging to weld due to its thermal properties. This can lead to increased manufacturing complexity and costs.
Impact on Application: Its resistance to corrosion and staining makes stainless steel suitable for food processing, medical equipment, and marine applications, where hygiene and durability are paramount.
Considerations for Buyers: Buyers should consider the specific grades of stainless steel (e.g., 304, 316) that comply with local regulations and industry standards. Understanding the local market’s supply chain for stainless steel can also impact procurement strategies.
Titanium
Key Properties: Titanium is known for its high strength-to-weight ratio and excellent corrosion resistance, particularly in harsh environments. It can withstand extreme temperatures and is non-magnetic.
Pros & Cons: Titanium’s primary advantages include its lightweight nature and superior performance in corrosive environments. However, it is one of the most expensive materials, and its welding requires specialized skills and equipment, increasing manufacturing complexity.
Impact on Application: Titanium is often used in aerospace, medical implants, and high-performance automotive components due to its strength and resistance to corrosion.
Considerations for Buyers: B2B buyers should evaluate the availability of titanium in their region and consider compliance with international standards for aerospace or medical applications. The cost and technical expertise required for welding titanium should also be factored into the decision-making process.
Summary Table
Material | Typical Use Case for cnc welding machine | Key Advantage | Key Disadvantage/Limitation | Relative Cost (Low/Med/High) |
---|---|---|---|---|
Steel | Structural components, automotive parts | Cost-effective and durable | Susceptible to corrosion without treatment | Low |
Aluminum | Aerospace frames, automotive casings | Lightweight and corrosion-resistant | Higher cost and requires specialized welding | Medium |
Stainless Steel | Food processing, medical equipment | Exceptional durability and hygiene | More expensive and challenging to weld | High |
Titanium | Aerospace, medical implants | High strength-to-weight ratio | Very expensive and requires specialized welding | High |
This analysis provides a comprehensive overview of the materials commonly used in CNC welding machines, equipping international B2B buyers with the knowledge needed to make informed purchasing decisions.
In-depth Look: Manufacturing Processes and Quality Assurance for cnc welding machine
CNC welding machines represent a critical component in modern manufacturing, enabling high-precision welding across various industries. Understanding the manufacturing processes and quality assurance protocols for these machines is essential for B2B buyers, particularly those in regions like Africa, South America, the Middle East, and Europe. This section details the key stages of production and the quality control measures that ensure reliability and compliance with international standards.
Manufacturing Process for CNC Welding Machines
The manufacturing of CNC welding machines typically involves several key stages, each critical to the machine’s overall performance and durability.
1. Material Preparation
The first stage involves selecting and preparing raw materials, which commonly include high-grade steel, aluminum, and other alloys. Material quality directly impacts the machine’s strength and longevity. Key techniques in this stage include:
- Cutting and Shaping: Materials are cut to required dimensions using laser cutting, plasma cutting, or traditional machining methods.
- Surface Treatment: Processes such as sandblasting or acid cleaning are applied to enhance the material’s surface quality, ensuring better adhesion for welding.
2. Forming
In this stage, the prepared materials are shaped into components that will make up the CNC welding machine. Techniques employed include:
- Bending and Forming: Using hydraulic presses or CNC bending machines to create complex shapes.
- Welding: Components are welded together using MIG (Metal Inert Gas) or TIG (Tungsten Inert Gas) welding techniques, ensuring strong joints that can withstand operational stresses.
3. Assembly
Once the individual components are fabricated, the next step is assembly. This involves:
- Integration of Electronic Components: Installing control systems, sensors, and wiring that allow for CNC operation.
- Mechanical Assembly: Fitting together various parts, including frames, motors, and gears, ensuring proper alignment and function.
4. Finishing
Finishing processes enhance both the aesthetic and functional qualities of the CNC welding machine. Common finishing techniques include:
- Painting and Coating: Applying protective coatings to prevent corrosion and improve durability.
- Final Inspection and Testing: Conducting thorough inspections to ensure that all components meet specified tolerances and operational requirements.
Quality Assurance for CNC Welding Machines
Ensuring quality throughout the manufacturing process is paramount. B2B buyers should be well-versed in the relevant international and industry-specific standards that govern the quality assurance of CNC welding machines.
International Standards
ISO 9001 is the most widely recognized quality management standard, focusing on meeting customer expectations and delivering satisfaction. Compliance with this standard is a strong indicator of a supplier’s commitment to quality.
Additional certifications may include:
- CE Marking: Indicates compliance with European safety, health, and environmental protection standards, essential for machines sold in Europe.
- API Standards: Relevant for companies in the oil and gas sector, ensuring that equipment meets specific industry requirements.
Quality Control Checkpoints
Quality control in the manufacturing of CNC welding machines typically involves several checkpoints:
- Incoming Quality Control (IQC): Ensures that raw materials meet specified quality standards before production begins.
- In-Process Quality Control (IPQC): Monitors the manufacturing process at various stages to catch defects early. This includes regular checks during welding and assembly.
- Final Quality Control (FQC): Conducts comprehensive tests on the finished machine, including functionality tests and dimensional checks to ensure conformity with specifications.
Common Testing Methods
B2B buyers should be aware of several testing methods commonly employed during the quality assurance process:
- Non-Destructive Testing (NDT): Techniques such as ultrasonic testing or magnetic particle inspection to detect internal and surface defects without damaging the components.
- Functional Testing: Ensuring that all CNC capabilities operate as intended, including movement accuracy and control responses.
- Load Testing: Assessing the machine’s performance under typical operational loads to confirm structural integrity.
Verifying Supplier Quality Control
Buyers must take proactive steps to verify the quality control practices of potential suppliers. Here are effective strategies:
- Supplier Audits: Conducting on-site audits can provide insight into a supplier’s manufacturing practices and adherence to quality standards. This is particularly important for international suppliers.
- Requesting Quality Reports: Suppliers should be able to provide documentation on their quality control processes and test results, showcasing their commitment to standards.
- Third-Party Inspection: Engaging independent inspection services can provide an unbiased evaluation of the machine’s quality before shipment, ensuring compliance with specified standards.
Quality Control Nuances for International Buyers
For B2B buyers in Africa, South America, the Middle East, and Europe, several nuances must be considered when dealing with international suppliers:
- Understanding Regional Standards: Different regions may have varying compliance requirements. Buyers should familiarize themselves with both local and international standards applicable to their markets.
- Language and Communication Barriers: Clear communication is crucial. Ensure that all specifications and quality expectations are clearly defined and understood by both parties.
- Logistical Considerations: International shipping can complicate quality assurance. Buyers should account for potential risks during transport and verify that the machine arrives in optimal condition.
Conclusion
Investing in a CNC welding machine is a significant commitment for B2B buyers, and understanding the manufacturing processes and quality assurance protocols is essential for ensuring a successful purchase. By familiarizing themselves with the production stages, relevant quality standards, and verification techniques, buyers can make informed decisions that enhance their operational efficiency and competitiveness in the global marketplace.
Related Video: CNC Machine Working Process 5 Axis Machining Metal & Aluminium Aerospace
Comprehensive Cost and Pricing Analysis for cnc welding machine Sourcing
When sourcing CNC welding machines, international B2B buyers must navigate a complex cost structure and pricing landscape. Understanding the various cost components, price influencers, and negotiation tactics can empower buyers to make informed decisions that align with their operational needs and budget constraints.
Cost Components
-
Materials: The choice of materials used in the CNC welding machine significantly impacts the overall cost. High-grade steel and specialized alloys will increase the machine’s durability but also its price. Buyers should assess the material quality in relation to their production requirements to ensure a balance between cost and longevity.
-
Labor: Labor costs are another critical factor. Skilled technicians are required for assembly, programming, and maintenance. In regions with higher labor costs, such as parts of Europe, the overall expenditure on CNC machines may be elevated. Conversely, emerging markets may offer lower labor costs, affecting the pricing dynamics favorably for buyers.
-
Manufacturing Overhead: This includes costs related to factory operations, utilities, and equipment depreciation. Understanding a supplier’s manufacturing overhead can provide insights into their pricing strategy. Buyers should inquire about these costs to gauge how they affect final pricing.
-
Tooling: The tooling required for CNC welding machines, including fixtures and jigs, can add significant costs. Custom tooling designed for specific applications can escalate expenses, so buyers should evaluate whether standard tooling options can meet their needs without incurring excessive costs.
-
Quality Control (QC): Rigorous QC processes are essential for ensuring the reliability and performance of CNC machines. Suppliers with stringent QC protocols may charge higher prices, but this investment often translates into better long-term value. Buyers should consider the implications of QC on overall operational efficiency.
-
Logistics: Shipping and handling costs can vary widely based on the machine’s size and weight, as well as the distance from the supplier. International buyers should be aware of potential tariffs and taxes that could further affect the final cost. An understanding of Incoterms is crucial to clarifying responsibilities and costs related to logistics.
-
Margin: Supplier margins can fluctuate based on market conditions and competition. Buyers should research market prices to ensure they are not overpaying and can negotiate effectively.
Price Influencers
Several factors can influence the pricing of CNC welding machines:
-
Volume/MOQ (Minimum Order Quantity): Bulk purchases typically lead to lower per-unit costs. Buyers should assess their production needs and consider negotiating for better pricing with higher volumes.
-
Specifications/Customization: Custom features and specifications can raise the cost. Buyers should define their requirements clearly to avoid unnecessary expenses on features that may not be essential.
-
Materials and Quality Certifications: Machines with specific certifications (e.g., ISO, CE) may come at a premium but often provide assurance of quality and reliability. Buyers should weigh these benefits against their budget.
-
Supplier Factors: The reputation and reliability of the supplier can significantly influence pricing. Established suppliers with a proven track record may charge more, but the added value of support and reliability can justify the cost.
Buyer Tips
-
Negotiation: Engage in discussions with multiple suppliers to understand pricing structures better and leverage competitive offers. Highlighting potential long-term relationships can also yield favorable terms.
-
Cost-Efficiency: Evaluate the Total Cost of Ownership (TCO), which includes purchase price, maintenance, operational costs, and potential downtime. A higher initial investment may be justified if it leads to lower operational costs over time.
-
Pricing Nuances for International Buyers: Buyers from regions like Africa, South America, the Middle East, and Europe should be mindful of currency fluctuations and international shipping costs, which can affect overall pricing. Understanding local market conditions can also provide leverage in negotiations.
Disclaimer
Prices for CNC welding machines can vary widely based on specifications, supplier, and market conditions. Buyers should conduct thorough research and obtain multiple quotes to ensure they are making informed purchasing decisions.
Spotlight on Potential cnc welding machine Manufacturers and Suppliers
This section looks at several manufacturers active in the ‘cnc welding machine’ market. This is a representative sample for illustrative purposes; B2B buyers must conduct extensive due diligence before any transaction. Information is synthesized from public sources and general industry knowledge.
Essential Technical Properties and Trade Terminology for cnc welding machine
When sourcing CNC welding machines, understanding key technical properties and industry terminology is essential for making informed purchasing decisions. Below, we outline the critical specifications that define these machines, as well as common trade terms that every B2B buyer should know.
Key Technical Properties
-
Material Compatibility
– Definition: The range of materials a CNC welding machine can effectively process, including metals (steel, aluminum, etc.), plastics, and composites.
– Importance: Buyers must ensure that the machine can handle the specific materials relevant to their production needs. This compatibility can significantly impact the quality of the weld and the overall efficiency of the manufacturing process. -
Welding Speed
– Definition: The rate at which the machine can perform welding operations, typically measured in inches per minute (IPM) or millimeters per minute (mm/min).
– Importance: Faster welding speeds can enhance productivity and reduce cycle times, which is crucial for meeting tight deadlines in competitive markets. Buyers should assess the balance between speed and weld quality to ensure optimal performance. -
Power Output
– Definition: The total wattage or amperage that the machine can deliver during welding operations.
– Importance: Higher power output allows for welding thicker materials and achieving stronger joints. Buyers should consider their specific applications to ensure the machine’s power capabilities align with their production requirements. -
Precision and Tolerance
– Definition: The degree of accuracy in the welding process, often specified in millimeters or microns.
– Importance: High precision and tight tolerances are critical in industries like aerospace and automotive, where even minor deviations can lead to significant quality issues. Buyers should evaluate their projects’ specifications to select a machine that meets these standards. -
Cooling System
– Definition: The method employed to dissipate heat generated during the welding process, which can include water-cooled or air-cooled systems.
– Importance: An effective cooling system prolongs the machine’s lifespan and maintains consistent performance. Buyers should consider the implications of cooling systems on maintenance and operational costs. -
Control System
– Definition: The software and hardware that manage the welding process, including programming languages, user interfaces, and automation features.
– Importance: A user-friendly and advanced control system enhances operational efficiency and reduces the learning curve for operators. Buyers should look for systems that integrate well with existing workflows and provide robust support.
Common Trade Terms
-
OEM (Original Equipment Manufacturer)
– Definition: A company that produces parts or equipment that may be marketed by another manufacturer.
– Relevance: Understanding OEM relationships can help buyers identify reputable suppliers and ensure they are sourcing quality equipment that meets industry standards. -
MOQ (Minimum Order Quantity)
– Definition: The smallest quantity of a product that a supplier is willing to sell.
– Relevance: Buyers must consider MOQ when planning their purchases to avoid excessive inventory costs or insufficient supply for production needs.
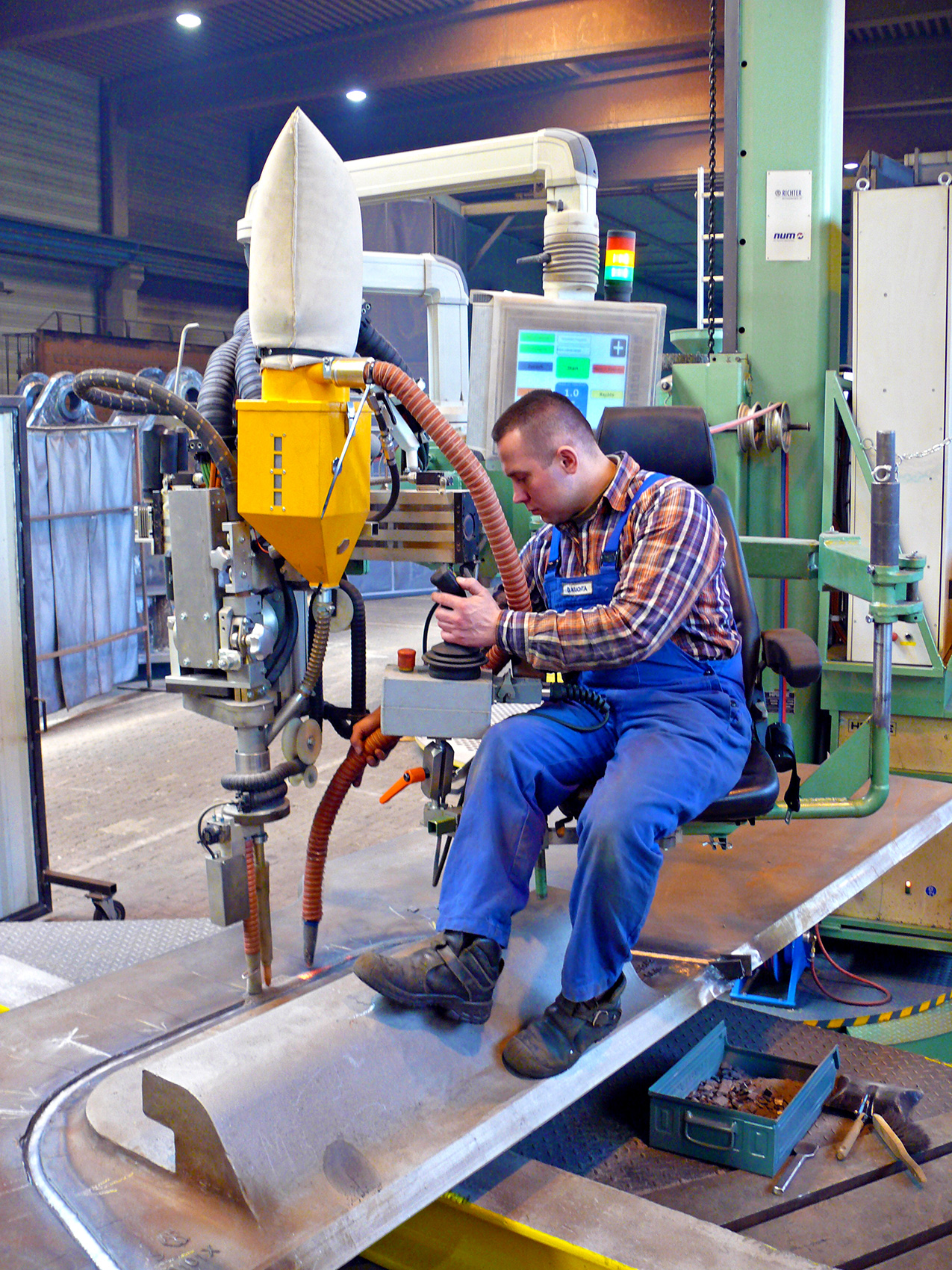
Illustrative Image (Source: Google Search)
-
RFQ (Request for Quotation)
– Definition: A document sent to suppliers asking for pricing and terms for specific products or services.
– Relevance: Submitting an RFQ allows buyers to compare quotes from multiple suppliers, ensuring they secure the best deal for their CNC welding machine. -
Incoterms (International Commercial Terms)
– Definition: A set of international rules that define the responsibilities of sellers and buyers in international trade.
– Relevance: Familiarity with Incoterms helps buyers understand their shipping costs, risks, and responsibilities, facilitating smoother transactions across borders. -
TIG and MIG Welding
– Definition: Types of welding processes; TIG (Tungsten Inert Gas) is known for precision, while MIG (Metal Inert Gas) is favored for speed and versatility.
– Relevance: Understanding these processes allows buyers to choose the right CNC welding machine based on their specific welding needs and production goals. -
Warranty and After-Sales Support
– Definition: Guarantees offered by suppliers regarding the machine’s performance and the availability of technical assistance.
– Relevance: A strong warranty and reliable after-sales support are critical for minimizing downtime and ensuring operational continuity. Buyers should prioritize suppliers that provide comprehensive support packages.
By familiarizing themselves with these technical properties and trade terms, B2B buyers can navigate the complexities of sourcing CNC welding machines more effectively, ensuring that their investments align with their strategic manufacturing goals.
Navigating Market Dynamics, Sourcing Trends, and Sustainability in the cnc welding machine Sector
Market Overview & Key Trends
The CNC welding machine sector is experiencing robust growth driven by several global factors. The increasing demand for precision welding in diverse industries—such as automotive, aerospace, and construction—is propelling investments in advanced CNC technologies. International B2B buyers, particularly in Africa, South America, the Middle East, and Europe, are focusing on automation and technological integration to enhance productivity and reduce operational costs.
Emerging trends include the adoption of Industry 4.0 principles, such as IoT-enabled machines that allow for real-time monitoring and predictive maintenance. This capability is particularly appealing to buyers in regions like Saudi Arabia, where large-scale infrastructure projects necessitate reliable and efficient machinery. Additionally, the rise of hybrid welding technologies, which combine traditional welding methods with CNC automation, is gaining traction, offering versatility and improved weld quality.
Sourcing trends are also evolving. Buyers are increasingly favoring suppliers that offer comprehensive after-sales support, including training and maintenance services. As the market becomes more competitive, there is a growing emphasis on supplier reliability and the ability to provide customized solutions tailored to specific manufacturing needs. Buyers should also be aware of regional regulations and standards that may affect machine selection, ensuring compliance and operational efficiency in their markets.
Sustainability & Ethical Sourcing in B2B
Sustainability has become a critical consideration for B2B buyers in the CNC welding machine sector. The environmental impact of manufacturing processes, including energy consumption and waste generation, necessitates a shift towards more sustainable practices. Buyers are encouraged to seek out CNC welding machines that incorporate energy-efficient technologies and are compatible with eco-friendly materials.
Ethical sourcing is equally important, as businesses face increasing scrutiny regarding their supply chains. Buyers should prioritize suppliers who demonstrate a commitment to ethical labor practices and environmental stewardship. Certifications such as ISO 14001 (Environmental Management) and OHSAS 18001 (Occupational Health and Safety) can serve as indicators of a supplier’s dedication to sustainability.
Moreover, the use of “green” materials—such as recycled metals and low-emission welding consumables—can enhance the sustainability profile of manufacturing operations. As consumers and governments push for greener practices, aligning procurement strategies with sustainability goals can not only mitigate risks but also enhance brand reputation and market competitiveness.
Brief Evolution/History
The evolution of CNC welding machines began in the late 20th century with the integration of computer technology into traditional welding processes. Initially, these machines were primarily used for simple tasks, but advancements in technology have led to the development of sophisticated CNC systems capable of executing complex welding tasks with precision.
As industries expanded and the demand for high-quality welding increased, manufacturers began adopting CNC welding to enhance productivity and consistency. Today, CNC welding machines are equipped with features such as automated welding parameters, real-time monitoring, and adaptive control systems, making them essential tools for modern manufacturing. This evolution has enabled businesses across various sectors to achieve higher efficiency and quality in their welding operations, positioning CNC welding as a cornerstone of industrial automation.
Related Video: Incoterms for beginners | Global Trade Explained
Frequently Asked Questions (FAQs) for B2B Buyers of cnc welding machine
-
What key factors should I consider when vetting suppliers for CNC welding machines?
When vetting suppliers, prioritize their industry experience, reputation, and the range of products they offer. Look for suppliers with a proven track record in manufacturing CNC welding machines, supported by customer testimonials and case studies. Ensure they provide comprehensive after-sales support, including training and maintenance. Additionally, verify their compliance with international quality standards, such as ISO certifications, which can indicate reliability and adherence to best practices. -
Can CNC welding machines be customized to meet specific operational needs?
Yes, many suppliers offer customization options for CNC welding machines to fit unique production requirements. This can include adjustments in machine size, welding parameters, and software configurations. When discussing customization, provide detailed specifications of your operational needs and inquire about the potential impacts on lead times and costs. Ensure that the supplier has the capability to implement these changes without compromising quality or delivery timelines. -
What is the typical minimum order quantity (MOQ) and lead time for CNC welding machines?
The MOQ for CNC welding machines varies by supplier and may range from one unit for standard models to larger quantities for custom machines. Lead times can also differ significantly based on the supplier’s production capacity and the complexity of the order, typically ranging from 4 to 12 weeks. Discuss your requirements upfront with potential suppliers to understand their capabilities and negotiate terms that align with your production schedule. -
What payment terms are commonly offered by suppliers for CNC welding machines?
Payment terms can vary widely among suppliers, but many offer options such as a deposit upon order confirmation followed by the balance upon delivery or installation. Other arrangements may include financing options or extended payment terms for larger orders. It is essential to negotiate terms that provide security for both parties and consider using escrow services for high-value transactions to mitigate risks. -
How can I ensure quality assurance and certifications for CNC welding machines?
To ensure quality, request documentation of certifications such as ISO 9001, CE marking, or other relevant industry standards from your supplier. Conduct a factory audit if possible, or ask for references from other clients who have purchased similar machines. Additionally, inquire about the supplier’s quality control processes, including testing protocols, and request samples or demonstrations to verify the machine’s performance before finalizing the purchase. -
What logistical considerations should I be aware of when importing CNC welding machines?
When importing CNC welding machines, consider shipping methods, customs duties, and local regulations that may affect delivery. Engage with freight forwarders experienced in heavy machinery to facilitate the shipping process and ensure compliance with import regulations. Additionally, plan for potential delays in customs clearance and arrange for proper handling and installation at your facility to avoid operational disruptions. -
What steps can I take to resolve disputes with suppliers during the procurement process?
To minimize disputes, establish clear communication channels and document all agreements in writing, including specifications, delivery schedules, and payment terms. If a dispute arises, attempt to resolve it through direct negotiation with the supplier. If that fails, consider mediation or arbitration as alternative dispute resolution methods. Ensure your contracts include clauses specifying the process for handling disputes to protect your interests and facilitate a smoother resolution. -
How can I assess the long-term support and service capabilities of a CNC welding machine supplier?
Evaluate a supplier’s long-term support by asking about their service level agreements (SLAs) and the availability of spare parts. Inquire about the technical support offered post-purchase, including response times for service requests and the expertise of their service personnel. Additionally, consider suppliers that provide training programs for your staff to ensure they can effectively operate and maintain the CNC welding machines, contributing to the longevity and efficiency of your investment.
Important Disclaimer & Terms of Use
⚠️ Important Disclaimer
The information provided in this guide, including content regarding manufacturers, technical specifications, and market analysis, is for informational and educational purposes only. It does not constitute professional procurement advice, financial advice, or legal advice.
While we have made every effort to ensure the accuracy and timeliness of the information, we are not responsible for any errors, omissions, or outdated information. Market conditions, company details, and technical standards are subject to change.
B2B buyers must conduct their own independent and thorough due diligence before making any purchasing decisions. This includes contacting suppliers directly, verifying certifications, requesting samples, and seeking professional consultation. The risk of relying on any information in this guide is borne solely by the reader.
Strategic Sourcing Conclusion and Outlook for cnc welding machine
Strategic sourcing for CNC welding machines is a pivotal factor in enhancing operational efficiency and competitiveness for international B2B buyers across Africa, South America, the Middle East, and Europe. The complexity of sourcing these machines—ranging from understanding various types, such as MIG, TIG, and robotic welding systems, to evaluating supplier reliability and after-sales support—demands a strategic approach. Buyers should focus on aligning their procurement strategies with local market needs while considering the total cost of ownership, including maintenance and training requirements.
Key Takeaways:
– Assess Compatibility: Ensure the selected CNC welding machine is compatible with your specific materials and production processes.
– Evaluate Supplier Credentials: Prioritize suppliers with proven track records in quality assurance, technical support, and customer service.
– Invest in Training: Equip your team with the necessary skills to operate advanced CNC welding systems efficiently.
Looking ahead, the global market for CNC welding machines is expected to grow, driven by advancements in technology and increasing demand for precision manufacturing. As you embark on your sourcing journey, leverage the insights gained from this guide to make informed decisions that will not only meet your immediate needs but also position your business for future success in an evolving landscape. Embrace the opportunity to enhance your manufacturing capabilities and stay competitive in a dynamic global market.