Your Ultimate Guide to Sourcing Cnc Wire Bending Machine
Introduction: Navigating the Global Market for cnc wire bending machine
In today’s fast-paced manufacturing landscape, CNC wire bending machines have become indispensable tools for businesses striving to enhance precision, efficiency, and productivity. These advanced machines automate the complex process of shaping metal wires, allowing manufacturers to produce intricate components with unparalleled accuracy. As global demand for such technology surges, understanding the intricacies of CNC wire bending is crucial for international B2B buyers, especially those from Africa, South America, the Middle East, and Europe, including countries like Argentina and France.
This comprehensive guide serves as an essential resource for navigating the global market for CNC wire bending machines. It covers a wide array of topics, including types of machines, suitable materials, manufacturing and quality control standards, leading suppliers, cost considerations, and market trends. Additionally, a dedicated FAQ section addresses common queries, empowering buyers with the knowledge needed to make informed decisions.
By exploring the capabilities and features of various CNC wire bending technologies, this guide equips international buyers with the insights necessary to identify the right solutions for their production needs. Whether you are looking to enhance operational efficiency or expand your manufacturing capabilities, understanding CNC wire bending machines is key to maintaining a competitive edge in the global marketplace. With this knowledge, buyers can streamline their sourcing processes, minimize risks, and ultimately drive growth in their respective industries.
Understanding cnc wire bending machine Types and Variations
Type Name | Key Distinguishing Features | Primary B2B Applications | Brief Pros & Cons for Buyers |
---|---|---|---|
Single-Axis Benders | Simple design, typically used for basic bends; low-cost entry | Automotive brackets, basic furniture | Pros: Affordable, easy to operate. Cons: Limited functionality, less precision. |
Multi-Axis Benders | Capable of bending in multiple directions; high precision | Aerospace components, complex machinery | Pros: Versatile, high accuracy. Cons: Higher initial investment, complex programming. |
Robotic Wire Bending Cells | Integrates robotics for automation; high-speed production | Mass production, custom parts manufacturing | Pros: High efficiency, reduces labor costs. Cons: Significant upfront cost, requires skilled operators. |
Hybrid Benders | Combines traditional bending methods with CNC technology | Medical device manufacturing, electronics | Pros: Flexibility in production, can handle diverse materials. Cons: Maintenance can be complex, may require specialized training. |
Synchro-Driven Benders | Eliminates mechanical adjustments; fast setup | Wire mesh production, reinforcing steel | Pros: Quick setup, consistent quality. Cons: May lack some customization options, dependent on proprietary technology. |
Single-Axis Benders
Single-axis benders are the most basic type of CNC wire bending machines, designed primarily for straightforward bending tasks. These machines are typically more affordable and user-friendly, making them ideal for small businesses or startups entering the wire bending market. However, their limited functionality means they may not be suitable for complex applications requiring precise multi-directional bends. Buyers should consider their specific production needs and potential for future growth when investing in this type.
Multi-Axis Benders
Multi-axis benders offer advanced capabilities, allowing for bends in multiple directions and creating intricate shapes with high precision. This type of machine is particularly beneficial for industries such as aerospace and automotive, where complex components are essential. While the investment is higher than single-axis benders, the versatility and accuracy can lead to significant long-term savings and efficiency improvements. Buyers must evaluate their production volume and design complexity to justify the investment.
Robotic Wire Bending Cells
Robotic wire bending cells integrate advanced robotics with CNC technology to automate the bending process, significantly increasing production speed and efficiency. These systems are ideal for mass production environments where high output and low labor costs are priorities. However, they require a larger upfront investment and skilled operators for setup and maintenance. B2B buyers should assess their production scale and labor resources to determine if this high-tech solution aligns with their operational goals.
Hybrid Benders
Hybrid benders combine traditional wire bending techniques with modern CNC technology, offering flexibility in production processes. They are particularly well-suited for industries such as medical device manufacturing, where diverse materials and intricate designs are common. While they provide versatility, maintenance can be more complex, and operators may need specialized training to manage the hybrid systems effectively. B2B buyers should consider their product range and the potential need for skilled labor when evaluating this option.
Synchro-Driven Benders
Synchro-driven benders are known for their innovative design that eliminates mechanical adjustments, allowing for quick setups and consistent quality in production. This type is particularly effective in wire mesh production and reinforcing steel applications. While they offer speed and reliability, buyers should be aware that they may lack some customization options and could be dependent on proprietary technology. Evaluating the specific production needs and potential limitations of synchro-driven systems is essential for making an informed purchasing decision.
Related Video: CNC wire bending machine DH40 | BLM GROUP
Key Industrial Applications of cnc wire bending machine
Industry/Sector | Specific Application of CNC Wire Bending Machine | Value/Benefit for the Business | Key Sourcing Considerations for this Application |
---|---|---|---|
Automotive | Production of brackets, frames, and exhaust systems | High precision and repeatability reduce material waste and enhance product quality | Compatibility with existing manufacturing lines and flexibility for various designs |
Aerospace | Manufacturing of lightweight components for aircraft | Improved performance and fuel efficiency through precision-engineered parts | Certifications and compliance with industry standards (e.g., FAA, EASA) are critical |
Electronics | Creation of wiring harnesses and connectors | Enhanced reliability and performance of electronic devices | Ability to handle various wire gauges and types, as well as programmable features for different designs |
Furniture Design | Custom metal frames for furniture | Unique designs and faster production times lead to competitive advantage | Material specifications (e.g., steel, aluminum) and aesthetic finishes should align with market trends |
Construction | Fabrication of rebar and mesh structures | Increased structural integrity and reduced labor costs through automation | Sourcing from manufacturers with robust support and service capabilities for maintenance |
CNC wire bending machines play a pivotal role in the automotive industry by enabling the production of complex components such as brackets, frames, and exhaust systems. These machines allow manufacturers to achieve high precision and repeatability, which significantly reduces material waste and enhances the overall quality of the products. For international buyers, particularly in regions like South America and Africa, sourcing machines that are compatible with existing manufacturing lines and offer flexibility for various designs is crucial to optimizing production efficiency.
In the aerospace sector, CNC wire bending machines are essential for crafting lightweight components that contribute to better aircraft performance and fuel efficiency. The high precision of these machines ensures that parts meet stringent safety and quality standards. Buyers from the Middle East and Europe must consider the necessary certifications and compliance with industry regulations, such as those mandated by the FAA and EASA, when sourcing these machines to ensure they meet operational requirements.
The electronics industry benefits from CNC wire bending machines in the production of wiring harnesses and connectors. These machines provide enhanced reliability and performance for electronic devices by allowing for the creation of intricate designs with exact specifications. International buyers should look for machines that can handle various wire gauges and types, along with programmable features that can accommodate different design requirements to stay competitive in the fast-paced electronics market.
In furniture design, CNC wire bending machines facilitate the creation of custom metal frames that add unique aesthetic appeal to products. The ability to produce intricate designs quickly not only enhances creativity but also leads to faster production times, giving businesses a competitive edge. When sourcing machines, buyers should ensure that material specifications, such as the ability to work with steel or aluminum, align with current market trends and customer preferences.
Finally, in the construction industry, CNC wire bending machines are instrumental in fabricating rebar and mesh structures that provide increased structural integrity. Automation of this process leads to reduced labor costs and improved efficiency on construction sites. Buyers should prioritize sourcing from manufacturers that offer robust support and service capabilities to ensure seamless integration into their operations and minimize downtime.
Related Video: 3D CNC Wire Bending Machine – Straight Cut to Length Wire
Strategic Material Selection Guide for cnc wire bending machine
When selecting materials for CNC wire bending machines, international B2B buyers should consider the properties, advantages, and limitations of common materials used in the manufacturing process. This analysis focuses on four materials: stainless steel, carbon steel, aluminum, and copper. Each material has unique characteristics that can significantly impact performance and suitability for specific applications.
Stainless Steel
Key Properties: Stainless steel is known for its excellent corrosion resistance, high strength, and ability to withstand high temperatures. It typically has a temperature rating of up to 800°C and can handle various environmental conditions without degrading.
Pros & Cons: The durability of stainless steel makes it ideal for applications where longevity is essential. However, it tends to be more expensive than other materials, which can increase the overall cost of the CNC wire bending machine. Additionally, its manufacturing complexity can lead to longer production times.
Impact on Application: Stainless steel is particularly suited for industries that require hygiene and corrosion resistance, such as food processing and pharmaceuticals. Its compatibility with various media makes it a versatile choice.
Considerations for International Buyers: Buyers from regions like Europe and the Middle East should ensure compliance with standards such as ASTM A240 or DIN 1.4301. The higher cost may be justified by the material’s longevity and performance.
Carbon Steel
Key Properties: Carbon steel is characterized by its high tensile strength and hardness, making it suitable for heavy-duty applications. It generally has a lower corrosion resistance compared to stainless steel but can be treated to improve this property.
Pros & Cons: The primary advantage of carbon steel is its cost-effectiveness and ease of manufacturing. However, its susceptibility to rust and corrosion can limit its use in certain environments unless adequately coated.
Impact on Application: Carbon steel is widely used in automotive and construction applications where strength is prioritized over corrosion resistance. Its suitability for high-stress applications makes it a common choice.
Considerations for International Buyers: Buyers should be aware of the need for protective coatings in humid or corrosive environments. Compliance with standards like ASTM A36 can also be essential for ensuring quality.
Aluminum
Key Properties: Aluminum is lightweight, corrosion-resistant, and has good thermal conductivity. It can withstand temperatures up to 600°C, making it suitable for various applications.
Pros & Cons: The lightweight nature of aluminum allows for easier handling and installation, reducing labor costs. However, it is generally less strong than steel, which may limit its use in high-stress applications.
Impact on Application: Aluminum is often used in the aerospace and automotive industries due to its excellent strength-to-weight ratio. It is also suitable for applications requiring non-magnetic properties.
Considerations for International Buyers: Buyers should consider compliance with standards such as ASTM B221. The cost of aluminum can vary significantly based on market conditions, so budgeting for potential price fluctuations is advisable.
Copper
Key Properties: Copper is known for its excellent electrical conductivity and corrosion resistance. It can handle high temperatures, typically up to 400°C, and is often used in electrical applications.
Pros & Cons: The primary advantage of copper is its superior conductivity, making it ideal for electrical components. However, it is relatively expensive and can be prone to tarnishing, which may affect its aesthetic appeal.
Impact on Application: Copper is widely used in electrical wiring and electronic components. Its compatibility with various media makes it suitable for specialized applications in electronics.
Considerations for International Buyers: Buyers should check for compliance with standards such as ASTM B170. The higher cost of copper may be a consideration, especially for large-scale applications.
Material | Typical Use Case for cnc wire bending machine | Key Advantage | Key Disadvantage/Limitation | Relative Cost (Low/Med/High) |
---|---|---|---|---|
Stainless Steel | Food processing, pharmaceuticals | Excellent corrosion resistance | Higher cost, complex manufacturing | High |
Carbon Steel | Automotive, construction | Cost-effective, strong | Susceptible to rust | Low |
Aluminum | Aerospace, automotive | Lightweight, good thermal conductivity | Less strong than steel | Medium |
Copper | Electrical wiring, electronics | Superior electrical conductivity | Expensive, prone to tarnishing | High |
This material selection guide provides international B2B buyers with actionable insights to make informed decisions when investing in CNC wire bending machines. By understanding the properties, advantages, and limitations of each material, buyers can better align their choices with their specific industry needs and compliance requirements.
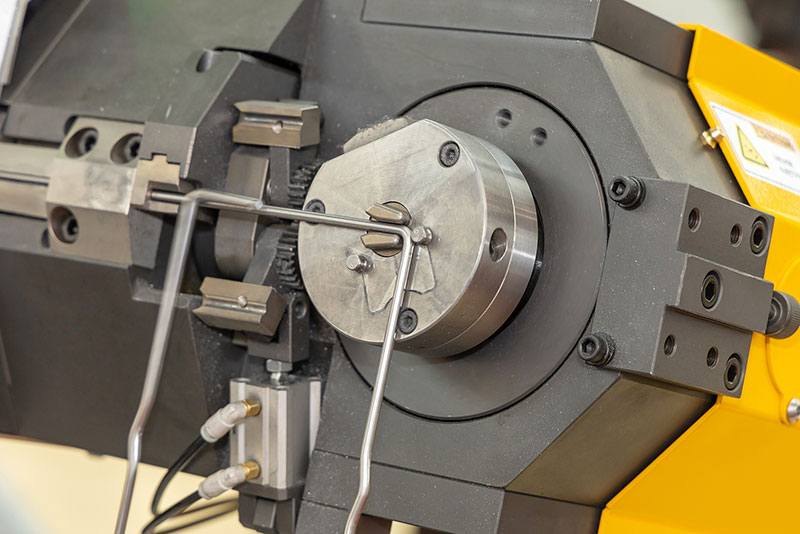
Illustrative Image (Source: Google Search)
In-depth Look: Manufacturing Processes and Quality Assurance for cnc wire bending machine
The manufacturing process of CNC wire bending machines is critical for ensuring high quality and performance. Understanding the various stages of production and the quality assurance measures in place can help international B2B buyers make informed purchasing decisions. This section delves into the typical manufacturing processes and quality control measures that are essential for CNC wire bending machines, particularly for buyers from Africa, South America, the Middle East, and Europe.
Manufacturing Process
The manufacturing of CNC wire bending machines generally involves several key stages, each crucial for achieving the desired level of precision and reliability.
1. Material Preparation
Material selection is the first and most critical step in the manufacturing process. High-quality steel or aluminum is often used for the construction of CNC wire bending machines due to its strength and durability.
- Material Sourcing: Suppliers should ideally provide certifications verifying the quality and origin of the materials used.
- Cutting and Shaping: Raw materials are cut to size using laser or plasma cutting methods to ensure precision. This is followed by shaping processes such as bending or machining to prepare the components for assembly.
2. Forming
The forming stage involves transforming the prepared materials into functional parts of the machine. This is where CNC technology truly shines.
- CNC Programming: Each machine is programmed with specific designs and bending parameters. This process utilizes advanced software, allowing for high levels of customization and complex geometries.
- Bending Operations: Using servo motors and hydraulic systems, the machine executes precise bends as per the programmed instructions. This stage often includes multiple passes to ensure accuracy.
3. Assembly
Once the individual components are formed, they are assembled into a complete machine.
- Sub-Assembly: Components such as the bending arm, control panel, and drive systems are first assembled separately.
- Final Assembly: The sub-assemblies are then brought together, and connections are made. This step may also involve the installation of safety features and user interfaces.
4. Finishing
The finishing process is essential for both aesthetics and functionality.
- Surface Treatment: Components may undergo treatments such as painting, anodizing, or powder coating to enhance durability and appearance.
- Final Inspection: Before leaving the manufacturing facility, each machine is subjected to a thorough inspection to ensure it meets specified tolerances and quality standards.
Quality Assurance
Quality assurance (QA) is a fundamental aspect of manufacturing CNC wire bending machines. It ensures that every unit produced meets international and industry-specific standards.
Relevant International Standards
Buyers should look for compliance with recognized quality standards:
- ISO 9001: This standard outlines the requirements for a quality management system (QMS) and is crucial for ensuring consistent product quality.
- CE Marking: For machines sold in Europe, CE marking indicates compliance with health, safety, and environmental protection standards.
- API Standards: For industries such as oil and gas, adherence to API standards can be a requirement.
Quality Control Checkpoints
The QA process typically includes several checkpoints:
- Incoming Quality Control (IQC): Materials received from suppliers are inspected for quality and compliance with specifications.
- In-Process Quality Control (IPQC): During manufacturing, regular checks are conducted to ensure that processes are executed correctly, minimizing defects.
- Final Quality Control (FQC): Once the machine is fully assembled, a comprehensive test is performed to verify functionality and performance.
Common Testing Methods
Testing methods may include:
- Functional Testing: Verifying that all machine functions operate as intended under various conditions.
- Dimensional Inspection: Using precision measuring tools to ensure that all components adhere to specified tolerances.
- Load Testing: Assessing the machine’s ability to perform under maximum load conditions.
Verifying Supplier Quality Control
For international B2B buyers, particularly those from diverse regions, verifying a supplier’s quality control practices is essential to ensure product reliability.
- Supplier Audits: Conducting on-site audits can provide insights into the supplier’s manufacturing processes and QA protocols.
- Quality Reports: Requesting detailed quality reports can help assess the consistency of the supplier’s quality management.
- Third-Party Inspections: Engaging third-party inspection agencies can offer an unbiased evaluation of the supplier’s quality assurance processes.
Quality Control and Certification Nuances for International Buyers
Understanding the nuances of quality control and certifications is vital for B2B buyers operating in different regions:
- Regional Compliance: Buyers must be aware of specific regulations and standards applicable in their markets. For instance, European buyers may prioritize CE marking, while those in Africa and South America may focus on local certifications.
- Language Barriers: Documentation and communication can sometimes be challenging due to language differences. It is advisable to ensure that all quality reports and certification documents are available in a language that is easily understood by the buyer.
- Cultural Considerations: Building relationships with suppliers may require an understanding of cultural nuances, which can influence negotiations and quality expectations.
In conclusion, the manufacturing processes and quality assurance measures for CNC wire bending machines play a critical role in determining their performance and reliability. By understanding these processes and verifying supplier quality, international B2B buyers can make informed decisions that lead to successful investments in CNC technology.
Related Video: CNC wire benders | BLM GROUP
Comprehensive Cost and Pricing Analysis for cnc wire bending machine Sourcing
Understanding the cost structure and pricing dynamics for CNC wire bending machines is crucial for international B2B buyers, especially those from regions such as Africa, South America, the Middle East, and Europe. This analysis will provide insights into the various cost components, price influencers, and practical tips for negotiation and sourcing.
Cost Components
-
Materials: The primary raw materials used in CNC wire bending machines include high-quality steel, aluminum, and various alloys. The choice of material directly influences durability and performance, affecting overall costs. Suppliers often offer different grades of materials, which can vary significantly in price.
-
Labor: Labor costs encompass both skilled workers involved in the manufacturing process and those required for assembly and quality control. In regions with higher labor costs, such as parts of Europe, buyers may find that this impacts the final price of the machine.
-
Manufacturing Overhead: This includes costs related to factory operation, utilities, maintenance, and administrative expenses. Overhead can vary greatly depending on the manufacturer’s location and operational efficiency.
-
Tooling: Tooling costs are related to the machinery and equipment used in the production of CNC wire bending machines. Custom tooling may be required for specialized machines, which can add to the overall cost.
-
Quality Control (QC): Quality assurance processes ensure that machines meet specified standards. QC costs can increase the price, but they are essential for maintaining product reliability and performance, which is particularly important for industries like aerospace and automotive.
-
Logistics: Shipping and handling costs can be significant, especially for international buyers. These costs can vary based on the shipping method, distance, and current freight rates.
-
Margin: Manufacturers typically include a profit margin in their pricing. This margin can be influenced by market demand, competition, and the perceived value of the machine.
Price Influencers
-
Volume/MOQ: The minimum order quantity (MOQ) often affects pricing. Larger orders typically yield better pricing due to economies of scale.
-
Specifications/Customization: Custom features or specifications can significantly increase costs. Buyers should clearly define their requirements to avoid unexpected expenses.
-
Materials: The choice of materials can lead to substantial price variations. Higher-quality materials may incur higher initial costs but can offer better longevity and performance.
-
Quality/Certifications: Machines that comply with international standards or possess certifications may command higher prices due to the assurance of quality and reliability.
-
Supplier Factors: The reputation and reliability of the supplier can influence pricing. Established manufacturers may charge a premium for their machines but often provide better support and warranty services.
-
Incoterms: Understanding the terms of delivery (e.g., FOB, CIF) is crucial. They affect pricing by determining who bears the shipping and insurance costs.
Buyer Tips
-
Negotiation: Engage in negotiations to explore discounts for bulk purchases or long-term contracts. Be prepared to discuss your requirements in detail to justify your position.
-
Cost-Efficiency: Consider the total cost of ownership (TCO), which includes not just the purchase price but also maintenance, operation, and potential downtime costs. Cheaper machines may lead to higher operational costs in the long run.
-
Pricing Nuances: International buyers should be aware of currency fluctuations and local tariffs that can affect the final price. Additionally, consider the implications of import duties and local taxes when calculating total expenses.
-
Research and Compare: Thoroughly research different suppliers and compare their offerings. Look for reviews or case studies that demonstrate the performance and reliability of their machines.
Disclaimer
Prices for CNC wire bending machines can vary widely based on the factors outlined above. It is advisable for buyers to request detailed quotes and consider all associated costs before making a purchasing decision.
Spotlight on Potential cnc wire bending machine Manufacturers and Suppliers
This section looks at several manufacturers active in the ‘cnc wire bending machine’ market. This is a representative sample for illustrative purposes; B2B buyers must conduct extensive due diligence before any transaction. Information is synthesized from public sources and general industry knowledge.
Essential Technical Properties and Trade Terminology for cnc wire bending machine
Key Technical Properties of CNC Wire Bending Machines
When considering the purchase of a CNC wire bending machine, understanding its essential technical properties is crucial for making an informed decision. Here are some of the critical specifications to consider:
-
Material Grade
The material grade of the wire that can be processed is a vital specification. High-quality machines can handle various materials, including stainless steel, copper, and aluminum. The choice of material affects the machine’s durability, the quality of the final product, and its suitability for specific applications. Buyers should ensure that the machine can accommodate the types of materials they intend to use. -
Bending Radius
The bending radius indicates the smallest curve that the machine can produce on a wire. This specification is important because it determines the machine’s flexibility in creating complex shapes. A smaller bending radius allows for more intricate designs, which can be a significant advantage in industries such as automotive and aerospace where precision is critical. -
Tolerance
Tolerance refers to the permissible limit of variation in a physical dimension. High-precision CNC wire bending machines can achieve tolerances as tight as ±0.1 mm. This capability is essential for industries where accuracy is non-negotiable, as even minor deviations can lead to product failure or increased costs due to rework. -
Production Speed
Production speed measures how quickly the machine can complete a bending cycle. This is particularly crucial for businesses aiming to maximize throughput and meet tight deadlines. A machine that offers high-speed operation can significantly enhance productivity, allowing manufacturers to fulfill larger orders more efficiently. -
Programmability
The programmability of the machine affects how easily it can be adapted for different designs and specifications. Advanced CNC machines feature user-friendly interfaces and software that allow operators to quickly input parameters, which reduces setup times and increases operational efficiency. -
Energy Consumption
Energy efficiency is increasingly important for manufacturers looking to minimize operational costs and reduce their environmental footprint. Machines with lower energy consumption not only save costs but also reflect a company’s commitment to sustainability, which can be a significant selling point in today’s market.
Common Trade Terminology in CNC Wire Bending
Understanding trade terminology is essential for effective communication with manufacturers and suppliers. Here are some commonly used terms in the CNC wire bending industry:
-
OEM (Original Equipment Manufacturer)
An OEM refers to a company that produces parts or equipment that may be marketed by another manufacturer. In the context of CNC machines, buying from an OEM often ensures high-quality components and better support services. -
MOQ (Minimum Order Quantity)
MOQ is the smallest quantity of a product that a supplier is willing to sell. Understanding the MOQ is crucial for buyers to manage inventory and costs effectively, especially when entering new markets or launching new products. -
RFQ (Request for Quotation)
An RFQ is a document sent to suppliers requesting a price quote for specific products or services. It is an essential part of the procurement process, allowing buyers to compare offers and negotiate better terms. -
Incoterms (International Commercial Terms)
Incoterms are a set of rules that define the responsibilities of buyers and sellers in international transactions. Familiarity with Incoterms helps buyers understand shipping costs, insurance, and delivery responsibilities, which can significantly impact the total cost of acquiring machinery. -
Lead Time
Lead time is the duration between placing an order and receiving the product. Understanding lead times is vital for effective planning and inventory management, especially in industries where timely delivery is critical.
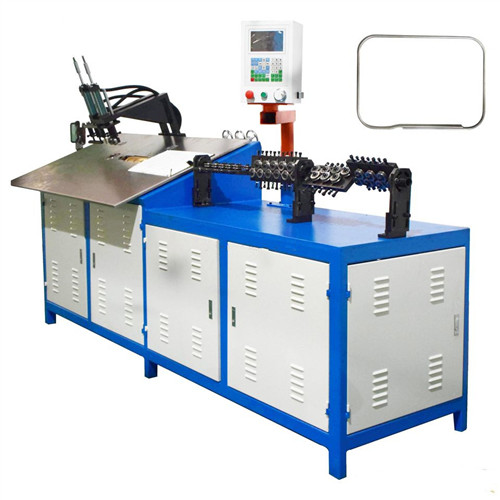
Illustrative Image (Source: Google Search)
- Service Level Agreement (SLA)
An SLA is a contract that outlines the expected service levels between a provider and a client. In the context of CNC wire bending machines, it may include maintenance schedules, response times for repairs, and quality expectations, helping to ensure that buyers receive the support they need for optimal machine performance.
By grasping these technical properties and trade terms, B2B buyers can make more informed decisions when investing in CNC wire bending machines, ensuring they choose the right equipment for their specific manufacturing needs.
Navigating Market Dynamics, Sourcing Trends, and Sustainability in the cnc wire bending machine Sector
Market Overview & Key Trends
The CNC wire bending machine sector is experiencing significant growth driven by advancements in automation, increasing demand for precision manufacturing, and the rising trend of custom production. Key markets in Africa, South America, the Middle East, and Europe are actively pursuing technology that enhances operational efficiency, reduces lead times, and improves product quality. For international B2B buyers, understanding the local market dynamics is crucial; for instance, in Argentina, manufacturers are shifting towards automation to enhance productivity, while in France, sustainability and energy efficiency are pivotal concerns.
Emerging technologies such as AI and IoT are becoming integral in optimizing CNC operations, allowing for real-time monitoring and predictive maintenance. Buyers should look for machines equipped with advanced software that facilitates easier programming and faster setup times, which is essential for adapting to fluctuating market demands. Furthermore, the trend towards modular machine designs, as seen with manufacturers like Bihler, offers flexibility and customization, enabling businesses to tailor their equipment to specific needs without extensive re-investment.
International sourcing trends are also evolving, with an increasing preference for manufacturers that provide comprehensive after-sales support and training. This is particularly relevant in regions with less technical expertise, as it ensures the efficient utilization of complex machinery. Buyers should prioritize suppliers that emphasize technological innovation and customer service, as these factors will significantly influence long-term operational success.
Sustainability & Ethical Sourcing in B2B
As global awareness of environmental issues increases, sustainability has become a key factor in sourcing CNC wire bending machines. The manufacturing process of these machines can have significant environmental impacts, including energy consumption and waste generation. Therefore, buyers are encouraged to seek out manufacturers who prioritize eco-friendly practices, such as utilizing energy-efficient technologies and sustainable materials in their machine production.
Ethical sourcing is equally important, as it reflects a company’s commitment to social responsibility. Buyers should consider suppliers that are transparent about their supply chains and adhere to ethical labor practices. Certifications such as ISO 14001 for environmental management systems and other “green” certifications can serve as indicators of a manufacturer’s commitment to sustainability.
In addition, materials used in CNC wire bending machines should be recyclable or made from recycled content, reducing the overall environmental footprint. For example, manufacturers like Schnell are adopting eco-sustainable materials and energy-saving technologies in their products, which not only benefit the environment but also help buyers reduce operational costs in the long run.
Brief Evolution/History
CNC wire bending technology has evolved significantly since its inception, transitioning from manual bending techniques to sophisticated computer-controlled machines. Initially, wire bending was a labor-intensive process fraught with inefficiencies and inaccuracies. The introduction of CNC technology in the late 20th century revolutionized this sector by enabling precise and repeatable wire shaping, essential for industries such as automotive and aerospace.
Over the years, advancements in software and control systems have further enhanced the capabilities of CNC wire bending machines. Features like programmable controls and real-time feedback mechanisms have allowed manufacturers to produce complex designs with minimal human intervention. As a result, the market has seen a surge in demand for machines that not only improve productivity but also align with evolving trends in customization and sustainability, making it crucial for B2B buyers to stay informed about these developments.
Related Video: International Trade Explained
Frequently Asked Questions (FAQs) for B2B Buyers of cnc wire bending machine
-
What criteria should I use to vet potential suppliers of CNC wire bending machines?
When vetting suppliers, prioritize manufacturers with a proven track record in CNC technology and strong customer testimonials. Investigate their certifications, such as ISO 9001, which indicates a commitment to quality management. Additionally, assess their production capabilities, technology used, and whether they provide after-sales support and service. Engage in direct communication to gauge their responsiveness and willingness to customize solutions for your specific needs. -
Can I customize the CNC wire bending machine to fit my specific production requirements?
Yes, many manufacturers offer customization options for their CNC wire bending machines. This can include adjusting the machine’s size, bending capacity, or integrating specific software features to align with your production processes. Discuss your requirements with potential suppliers to understand the extent of customization available, and request samples or demonstrations if possible to ensure the machine meets your expectations. -
What are the typical minimum order quantities (MOQ) and lead times for CNC wire bending machines?
MOQs for CNC wire bending machines can vary significantly among suppliers, often depending on the complexity of the machine and the level of customization required. Standard lead times typically range from 6 to 12 weeks, but this can be affected by factors such as order volume and the supplier’s production schedule. Always clarify these details in advance to avoid unexpected delays in your production timeline. -
What payment terms should I expect when purchasing a CNC wire bending machine?
Payment terms can vary widely based on the supplier’s policies and your relationship with them. Common arrangements include a deposit (usually 30-50%) upfront, with the balance due upon delivery or installation. Some suppliers may also offer financing options or payment through letters of credit. Ensure you discuss payment terms upfront to establish clear expectations and minimize the risk of disputes. -
How can I verify the quality assurance processes and certifications of a CNC wire bending machine supplier?
To verify a supplier’s quality assurance processes, request documentation of their quality management system, including any relevant certifications like ISO 9001 or CE marking. Ask for details about their testing procedures, including how they ensure machine accuracy and reliability. Additionally, consider visiting their manufacturing facility or requesting third-party audits to gain a deeper understanding of their quality control measures. -
What logistical considerations should I keep in mind when importing CNC wire bending machines?
Importing CNC wire bending machines involves several logistical considerations, including shipping methods, customs regulations, and import duties. Work with a reliable freight forwarder familiar with machinery imports to navigate these complexities efficiently. Ensure that the supplier provides necessary documentation, such as a bill of lading and customs invoices, to facilitate smooth clearance through customs. -
How can I resolve disputes with a supplier regarding the quality or performance of a CNC wire bending machine?
To effectively resolve disputes, maintain clear communication with your supplier from the outset. Document all agreements, specifications, and performance benchmarks. If issues arise, approach the supplier directly to discuss your concerns and seek a resolution. Consider involving a third-party mediator if necessary, and refer to any contractual agreements that outline dispute resolution processes to guide your discussions. -
What should I do if the CNC wire bending machine does not meet my expectations upon delivery?
If the machine does not meet your expectations, immediately contact the supplier to address the issue. Document the discrepancies with photos and detailed descriptions to support your case. Depending on the supplier’s policies, you may be entitled to a replacement, repair, or refund. Always refer to your purchase agreement for warranty terms and conditions, which will guide your next steps in addressing the situation.
Important Disclaimer & Terms of Use
⚠️ Important Disclaimer
The information provided in this guide, including content regarding manufacturers, technical specifications, and market analysis, is for informational and educational purposes only. It does not constitute professional procurement advice, financial advice, or legal advice.
While we have made every effort to ensure the accuracy and timeliness of the information, we are not responsible for any errors, omissions, or outdated information. Market conditions, company details, and technical standards are subject to change.
B2B buyers must conduct their own independent and thorough due diligence before making any purchasing decisions. This includes contacting suppliers directly, verifying certifications, requesting samples, and seeking professional consultation. The risk of relying on any information in this guide is borne solely by the reader.
Strategic Sourcing Conclusion and Outlook for cnc wire bending machine
In conclusion, strategic sourcing of CNC wire bending machines is a pivotal step for businesses aiming to enhance manufacturing efficiency and precision. By understanding the unique features and capabilities of leading manufacturers, such as AIM, Bihler, and EUROBEND, international buyers can make informed decisions that align with their specific production needs. Prioritizing flexibility, automation, and sustainability will not only optimize operations but also contribute to cost reduction and improved product quality.
Key Takeaways:
– Evaluate machine specifications against industry demands to ensure optimal fit.
– Leverage advanced features like intuitive software and energy-efficient designs to enhance productivity.
– Consider the long-term benefits of building relationships with reputable suppliers for ongoing support and innovation.
As the global market for CNC wire bending technology continues to grow, now is the time for businesses in Africa, South America, the Middle East, and Europe to invest strategically in these advanced machines. Embrace the opportunity to elevate your production capabilities and stay competitive in an increasingly dynamic landscape. Engage with trusted suppliers today to explore the best solutions tailored to your operational goals.